烧结焙烧鼓风炉熔炼 工艺流程图
炼铁工艺设计流程图描述

熔炼工艺流程及简介熔炼炉生产概况 1熔炼炉是制铁工艺流程的主体,它是由耐火砖砌筑的竖立圆筒炉体,外壳钢枝制作,外壳3熔炼炉冷却壁共有348块,共分450m12层冷却壁;一层与耐火砖之间有冷却设备,我公司冷却板;1-3层为光板冷却壁、材质耐热铸铁冷却壁;4-12层为镶砖冷却壁材质是铁素体球墨铸铁冷却壁;6-7层冷却壁之间有一层冷却板,炉喉有18块水冷炉喉钢砖,炉缸有一个铁口、2个渣口、14个风口;从其上部装入矿石,熔剂和燃料向下运动,下部鼓入被加热的空气。
熔炼炉生产的主要产品是生铁,副产品有炉渣和煤气,炉渣可用来制作水泥,保温材料、建筑材料和肥料,煤气可以做为燃料供给各用户。
熔炼炉生产的主要工艺过程:1.11.1.1供料熔炼炉冶炼用的主要原燃料:块矿、烧结矿、石灰石、焦炭,有K1、J1皮带机把原燃料送到1#转运站,经K2、J2皮带机、分料车运到指定的矿槽。
1.1.2上料由料仓输出的原料,燃料和熔剂,经仓下给料机、振动筛、经筛分、称量后,用料车按一定比例一批一批有序地送到熔炼炉炉顶,并卸入炉顶受料斗。
1.1.3装料炉顶装料设备的任务就是把提升到炉顶的炉料,按一定的工作制度装入熔炼炉炉喉。
1.1.4冶炼熔炼炉冶炼主要是还原过程,把铁氧化物还原成含有碳、硅、锰、硫、磷、镍、铬等杂质的铁合金。
由鼓风机连续不断地把冷风送到热风炉加热到1100~1250℃,再通过炉缸周围的风口进入熔炼炉,由炉顶加入的焦炭和风口鼓入的热空气燃烧燃料,产生大量的煤气和热量,使矿石源源不断地熔化还原,产生的铁水和熔渣贮存在熔炼炉炉缸内,定期地由铁口和渣口排出。
1.1.5产品处理在渣铁处理中,出铁前先从渣口放出溶渣,流入冲渣沟进行粒化后,以脱水器脱水,有皮带运到渣仓。
设有一个应急用干渣坑,出铁时,用液压开口机打开铁口,使铁水流入铁水罐车运到铸铁机铸成铁块,出完铁后用液压泥炮把铁口堵上。
经熔炼炉顶部导出的煤气通过重力除尘器、布袋除尘过滤后,经调压阀组调压后输往各煤气用户使用,从重力除尘器、布袋除尘器排出的炉尘,经过处理回收运往焙烧厂作为烧结原料。
烧结作业区工艺流程图

烧结作业区工艺流程图一、 管理步骤来料验收-----卸车储备-----混匀布料、混匀供料-----烧结生产二、 流程图1、 验收2、 储备3、混匀布料、供料工艺a 、铁料4、烧结工艺石灰石(0-3 mm)焦粉(0-3 mm)作业区以创建“书香型”作业区、全力打造视觉文化为目标,提出“科学管理、管理科学”的全新理念,统筹安排生产工作,坚持纵向贯穿、横向协同的管理思路,加强生产协调的核心作用,操纵好各生产工序的稳固,服务好其它作业区的保供、做到各工序间的无缝连接,保证产品质量,并与先进行业指标对标挖潜,寻找差距、降低成本、创新工艺、提升产品质量。
打造烧结先进的指标,构建与谐顺畅的生产流程,使烧结机利用系数突破1.30 t/㎡·h已达1.482t/㎡·h,年产量163万吨,且各项指标都在接近全国最高指标水平,基本满足高炉正常生产。
先将各流程做一简单的介绍:1、从PL-2皮带把混匀矿打到配料室1#、2#、3#、4#铁料仓;2、从白灰窑把-3mm粒级大于85%以上的生石灰通过手动葫芦吊打入配料室11#生石灰仓;3、通过PL-6皮带将-3mm粒级大于85%的石灰石打入配料室9#、10#仓;4、通过PL-3皮带将-3mm粒级在80%-85%的焦粉打入配料室7#、8#仓;5、按正常配比将混匀矿、焦粉、石灰石、生石灰、烧结返矿通过PL-12、Z4-1、H-1运输到一次混合机里面,在混合机加水、混匀通过ZL-1皮带运输到制粒机,在制粒机配加蒸汽以提高料温;物料(混合料)在制粒机里面混匀制粒6分钟通过Z5-1、S-1皮带,在通过梭布小车均匀布料到烧结小矿槽。
6、在烧结机上先布一层粒级10-20mm的烧结矿10mm作为底料,混合料在通过圆辊及六辊布料到烧结机,料层布到650mm,在通过圧料器把料通过点火器点火烧结。
7、混合料在烧结机上烧结50分钟左右,通过单齿辊破碎到环冷机,在环冷机冷却1个小时左右,通过Z6-1、LS-1在成品筛分室通过振动筛将-5mm 烧结返矿通过Z2-1、PL-9、PL-10皮带运输到配料室5#、6#仓内;将10-20mm烧结矿通过Z5-2、Z7-1、S-2皮带打到底料仓;将大于20mm粒级烧结矿通过Z8-1输送到高炉8、在烧结上料之前先开启机头、机尾电场及主抽风机。
烧结生产工艺流程图

烧结生产工艺流程图烧结工艺流程一、我厂烧结机概况:我厂90M2带式抽风机是有冶金设计研究总院设计。
设计利用系数为1.57t/m·h。
(设备能力为2.0 t/m·h)作业率90.4%,年产烧结矿224万吨。
产品为冷烧结矿;温度小于120℃;粒度5—150mm;0—5mm粉末含量小于5%;TFe55%;FeO小于10%;碱度2.0倍。
配料采用自动重量配料强化制粒烧结工艺。
厚料层烧结、环式鼓风冷却机冷却烧结矿。
冷烧结矿经整粒筛分;分出冷返矿及烧结机铺底料和成品烧结矿。
选用了高效主抽风机等节能设备,电器控制及自动化达到国同类厂先进水平,采用以PLC为核心的EIC控制系统,构成仪电合一的计算机控制系统。
仪表选用性能良好的电动单元组合仪表智能型数字显示仪表等,对生产过程的参数进行指示;记录;控制;自动调节,对原料成品及能源进行计量,在环境保护方面采用静电除尘器,排放浓度小于100mg/m3,生产水循环使用,实现全厂污水零排放。
采取多项措施对薄弱环节设备采用加强型及便于检修的设备,关键部位设电动桥式吊车,有储存时间8小时的成品矿槽以提高烧结机作业率,使烧结和高炉生产互不影响。
二、什么叫烧结工艺:烧结工艺就是按高炉冶炼的要求把准备好的铁矿粉、熔剂、燃料及代用品,按一定比例经配料、混料、加水润滑湿。
再制粒、布料点火、借助风机的作用,使铁矿粉在一定的高温作用下,部分颗粒表面发生软化和熔化,产生一定的液相,并与其他末熔矿石颗粒作用,冷却后,液相将矿粉颗粒粘成块这个过程为烧结工艺。
三.烧结的方法按照烧结设备和供风方式的不同烧结方法可分为:1)鼓风烧结如:烧结锅、平地吹;2)抽风烧结:①连续式如带式烧结机和环式烧结机等;②间歇式如固定式烧结机有盘式烧结机和箱式烧结机,移动式烧结机有步进式烧结机;3)在烟气中烧结如回转窑烧结和悬浮烧结。
四.烧结矿的种类:CaO/SiO2小于1为非自熔性烧结矿;碱度为1-1.5是自熔性烧结.矿碱度为1.5~2.5是高碱度烧结矿;大于2.5是超高或熔剂性烧结矿。
炼铁工艺流程图描述

熔炼工艺流程及简介1 熔炼炉生产概况熔炼炉是制铁工艺流程的主体.它是由耐火砖砌筑的竖立圆筒炉体.外壳钢枝制作.外壳与耐火砖之间有冷却设备.我公司450m3熔炼炉冷却壁共有348块.共分12层冷却壁;一层冷却板;1-3层为光板冷却壁、材质耐热铸铁冷却壁;4-12层为镶砖冷却壁材质是铁素体球墨铸铁冷却壁;6-7层冷却壁之间有一层冷却板.炉喉有18块水冷炉喉钢砖.炉缸有一个铁口、2个渣口、14个风口;从其上部装入矿石.熔剂和燃料向下运动.下部鼓入被加热的空气。
熔炼炉生产的主要产品是生铁.副产品有炉渣和煤气.炉渣可用来制作水泥.保温材料、建筑材料和肥料.煤气可以做为燃料供给各用户。
1.1熔炼炉生产的主要工艺过程:1.1.1供料熔炼炉冶炼用的主要原燃料:块矿、烧结矿、石灰石、焦炭.有K1、J1皮带机把原燃料送到1#转运站.经K2、J2皮带机、分料车运到指定的矿槽。
1.1.2上料由料仓输出的原料.燃料和熔剂.经仓下给料机、振动筛、经筛分、称量后.用料车按一定比例一批一批有序地送到熔炼炉炉顶.并卸入炉顶受料斗。
1.1.3装料炉顶装料设备的任务就是把提升到炉顶的炉料.按一定的工作制度装入熔炼炉炉喉。
1.1.4冶炼熔炼炉冶炼主要是还原过程.把铁氧化物还原成含有碳、硅、锰、硫、磷、镍、铬等杂质的铁合金。
由鼓风机连续不断地把冷风送到热风炉加热到1100~1250℃.再通过炉缸周围的风口进入熔炼炉.由炉顶加入的焦炭和风口鼓入的热空气燃烧燃料.产生大量的煤气和热量.使矿石源源不断地熔化还原.产生的铁水和熔渣贮存在熔炼炉炉缸内.定期地由铁口和渣口排出。
1.1.5产品处理在渣铁处理中.出铁前先从渣口放出溶渣.流入冲渣沟进行粒化后.以脱水器脱水.有皮带运到渣仓。
设有一个应急用干渣坑.出铁时.用液压开口机打开铁口.使铁水流入铁水罐车运到铸铁机铸成铁块.出完铁后用液压泥炮把铁口堵上。
经熔炼炉顶部导出的煤气通过重力除尘器、布袋除尘过滤后.经调压阀组调压后输往各煤气用户使用.从重力除尘器、布袋除尘器排出的炉尘.经过处理回收运往焙烧厂作为烧结原料。
烧结工艺流程图之欧阳理创编

烧结工艺流程图:图片:烧结工艺流程图:烧结是钢铁生产工艺中的一个重要环节,它是将铁矿粉、粉(无烟煤)和石灰按一定配比混匀。
经烧结而成的有足够强度和粒度的烧结矿可作为炼铁的熟料。
利用烧结熟料炼铁对于提高高炉利用系数、降低焦比、提高高炉透气性保证高炉运行均有一定意义。
由于烧结技术具体的作用和应用太广泛了, 以下介绍一下烧结生产在钢铁工业粉矿造块的意义和作用我国的铁矿石大部分都是贫矿,贫矿直接入炉炼铁是很不合算b,因此必须将贫矿进行破碎、选出高品位的精矿后,再将精矿粉造块成为人造富矿才能入高炉冶炼。
所以,粉矿造块是充分合理利用贫矿的不可缺少的关控环节。
富矿的开采过程中要产生粉矿,为了满足高炉的粒度要兔在整较过程中也会产生粉矿,粉矿直接入炉会51起高炉不顺。
恶化高炉技术经济指标,因此粉矿也必须经过造块才能入炉。
粉矿经过迭决后,可以进一步控制相改善合铁原料的性肠获得气孔串高、还原性好、强度合适、软熔温度较高、成份稳定的优质冶金原料,有助于炉况的稳定和技术经济指标的改善。
粒矿造块过程中,还可以除去部份有害杂质,如硫、氟、砷、锌等,有利于提高生铁的质量。
因为人造富矿比天然富矿更具有优越性,成为了现代商炉原料的主要来源。
粉矿迭块还可综合利用含铁、合被、台钙的粉状工业废料,如高炉炉尘、钢迢、轧钢皮、均热炉渣、硫酸渣、染料铁红、电厂烟尘灰笔适当配入可以成为廉价的高炉好原料,又可以减少环境污染,取得良好的经济效益和社会效益。
粉矿造铁是现代高炉冶炼并获得优质高产的基础,对于高炉冶炼有君十分重要的意义,是钢铁工业生产必不可少的重要工序,对钢铁生产的发展起着重要作用。
1.2 粉矿造块的方法粉矿造块方法很多,主要是烧结矿和球团矿。
此外,还有压制方团矿、辊压团矿、蒸养球团t碳酸化球团,其成球方式和固结方法与球团矿不同,还有小球烧结,国外称为HPs球团化挠结矿,界于球团和烧结之间;还有铁焦生产,是炼焦和粉矿造块相结合。
球团矿的焙烧方法主要乞竖队带式焙烷仇链蓖机—回转窃。
炼铁工艺流程图

炼铁工艺流程图炼铁工艺流程图炼铁厂质量监视和测量过程一、高炉系统(一)工艺流程图(图1)焦炭烧结矿球团矿块矿辅料喷煤高炉★富氧、鼓风水渣煤气、炉尘铸铁铁水图1炼钢(二)监视和测量过程:1.监控入炉原燃料成分:对焦炭、烧结矿、球团矿、块矿、辅料的粒度、水份、含粉率、化学成分及原料配比进行监控。
2.对喷煤的粒度、水份、化学成分进行监控。
3.对铸块尺寸进行监控。
4.对煤气含尘、含水进行监控。
5.对高炉的生铁中含[Si]、[S]及炉渣碱度进行控制,使生铁质量符合标准要求。
(三)工艺参数:1.高炉炉缸安全容铁量炉容:380m3、449m3、329m3、402m3。
安全容铁量:112t、144t、97t、116t。
炉缸存铁量接近安全容铁量时禁止放上渣,并采取相应措施,防止事故发生。
2.炉顶温度不大于500℃,气密箱温度不大于70℃。
3.风、渣口冷却水压应高出热风压力0.05Mpa,水压下降低于0.1Mpa时高炉应立即组织休风。
4.铁水罐内最高铁水面应低于罐沿300mm。
6.休风时冷风管道及煤气系统应保持正压。
7.打水空料面时,H2含量应不大于6%,并至少每小时测定一次煤气成分。
当H2含量大于6%,O2含量大于2%时,应停止回收煤气。
8.高炉热风压力小于0.05Mpa时,必须关闭混风切断阀。
9.煤粉水分<2%,最好在1%以下;筛分粒度:粒度级<60μm<50%粒度级<100μm<80%粒度级<500μm<20%粒度级<200μm<0%二、竖炉系统(一)竖炉系统工艺流程图(图2)配料混合造球筛分焙烧★球团矿仓高炉矿槽图2(二)监视和测量过程:1.监控生球水分、粒度、抗压强度和落下强度。
2.监控和测量球团矿转鼓指数。
3.监控焙烧过程的焙烧时间和温度,燃烧室温度和压力。
4.监控球团矿FeO含量。
(三)工艺参数:1.燃烧室压力≤19000Pa,压力超标,调整时间不超过15分钟。
1.燃烧室温度900℃~1050℃,温度超标,调整时间不超过60分钟。
硫化锌精矿的焙烧_图文
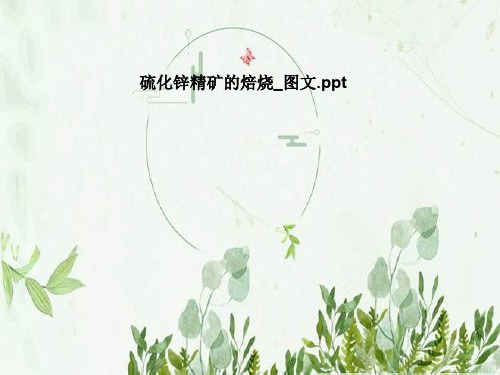
当PSO2=0.1 atm , PO2=10132.5~20265 Pa 时,
当 T > 1203K( 930℃)时,ZnO稳定 。
当 T < 1203K( 930℃)时, ZnO·2ZnSO4稳定。
Zn-Fe-S-O系氧势-温度平衡图 (PSO2=0.1 atm)
1203K
火法炼锌的焙烧温度一般控制在1000 ℃以上
2.5.2 硫化锌精矿沸腾焙烧的工艺和设备
2.5.2 硫化锌精矿沸腾 焙烧的工艺和设备
3、沸腾焙烧炉的结构
内衬耐火材料的炉身 装有风帽的空气分布板 下部的钢壳送风斗 上部的炉顶和炉气出口 侧边的加料装置和焙砂溢流排料口
锌冶金学
Zinc Metallurgy
当气相组成不变 ,改变焙烧温度时, 也可改变焙烧产物中 锌存在的形态。
提高温度有利于 ZnO的生成!
Zn-S-O系等温平衡状态图
1300K
当温度一定时,ZnS 氧化顺序是:
ZnO->ZnO·2ZnSO4 ->ZnSO4
Zn-Fe-S-O系氧势-温度平衡图 (PSO2=0.1 atm)
火法炼锌空气过剩系数为 1.05~1.10。 湿法炼锌空气过剩系数为 1.20~1.30。
(6) 硫化镉 镉在锌精矿中常以硫化镉的形式存在,在焙烧时被
氧化生成CdO和CdSO4。CdSO4在高温下分解生成CdO ,与CdS挥发进入烟尘有硫砷铁矿(即毒
砂 FeAsS)、硫化砷(As2S3)、辉锑矿(Sb2S3),在焙烧过 程中生成 As2O3、Sb2O3以及砷酸盐和锑酸盐。 As2S3 、 Sb2S3 、As2O3、Sb2O3容易挥发进入烟尘,砷酸盐和锑酸 盐是稳定化合物残留于焙砂中。
当进行硫酸化焙烧时,进行下列反应: ZnSO4 = ZnO + SO3 ZnO·2ZnSO4 = 3ZnO + 2SO3 SO2 + 1/2O2 = SO3
高炉、烧结、球团工艺流程

炼铁工艺是将含铁原料(烧结矿、球团矿或铁矿)、燃料(焦炭、煤粉等)及其它辅助原料(石灰石、白云石、锰矿等)按一定比例装入高炉,并由热风炉向高炉内鼓入热风助焦炭燃烧,原料、燃料随着炉内熔炼等过程的进行而下降。
在炉料下降和煤气上升过程中,先后发生传热、还原、溶化、脱炭作用而生成生铁,铁矿石原料中的杂质与加入炉内的溶剂相结合而成渣,炉底铁水间断地放出装入铁水罐,送往炼钢厂。
同时产生高炉煤气、炉渣两种副产品,高炉渣水淬后全部作为水泥生产原料。
高炉是用焦炭、铁矿石和熔剂炼铁的一种竖式的反应炉(如图2-3)。
高炉是一个竖立的圆筒形炉子,其内部工作空间的形状称为高炉内型,即通过高炉中心线的剖面轮廓。
现代高炉内型一般由圆柱体和截头圆锥体组成,由下而上分为炉缸、炉腹、炉腰、炉身和炉喉五段。
由于高炉炼铁是在高温下进行的,所以它的工作空间是用耐火材料围砌而成,外面再用钢板作炉壳。
1-炉底耐火材料;2-炉壳;3-生产后炉内砖衬侵蚀线;4-炉喉钢砖;5-煤气导出管;6-炉体夸衬;7-带凸台镶砖冷却壁;8-镶砖冷却壁;9-炉底碳砖;10-炉底水冷管;11-光面冷却壁;12-耐热基墩;13-基座l图2-3 高炉的结构在高炉炉顶设有装料装置,通过它将冶炼用的炉料(由焦炭和矿石按一定比例组成)按批装入炉内。
在高炉下部炉缸的上沿,沿圆周均匀地布置了若干个风口(100m3小高炉有 8-10个,4000m3以上的大高炉则有36-42 个)。
加热到1000℃以上的热风,经铜质水冷风口送入炉内,供焦炭燃烧形成高温煤气。
在炉缸的底部设有铁口,可周期性或连续性地排放出液态生铁和炉渣。
在风口和铁口之间还设有渣口以排放部分炉渣,减轻铁口负担。
l现代高炉采用优质耐火材料,例如炉底、炉缸部位用微碳孔碳砖,炉身下部和炉腰部位用铝碳砖或碳化硅砖,其它部位用优质高铝砖和高致密度的粘土砖等作炉衬。
炉壳用含锰的高强度低合金钢制作,安装有性能好的含铬耐热铸铁、球墨铸铁或铜质立式冷却器,或铜质的卧式冷却器。
RKEF工艺教育训练资料
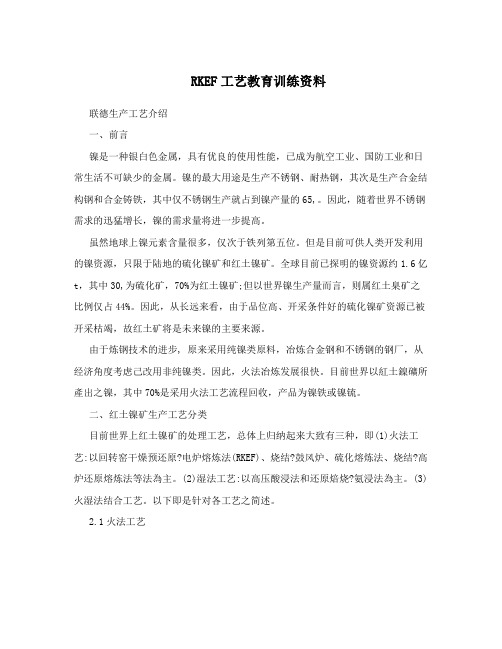
RKEF工艺教育训练资料联德生产工艺介绍一、前言镍是一种银白色金属,具有优良的使用性能,已成为航空工业、国防工业和日常生活不可缺少的金属。
镍的最大用途是生产不锈钢、耐热钢,其次是生产合金结构钢和合金铸铁,其中仅不锈钢生产就占到镍产量的65,。
因此,随着世界不锈钢需求的迅猛增长,镍的需求量将进一步提高。
虽然地球上镍元素含量很多,仅次于铁列第五位。
但是目前可供人类开发利用的镍资源,只限于陆地的硫化镍矿和红土镍矿。
全球目前已探明的镍资源约1.6亿t,其中30,为硫化矿,70%为红土镍矿;但以世界镍生产量而言,则属红土臬矿之比例仅占44%。
因此,从长远来看,由于品位高、开采条件好的硫化镍矿资源已被开采枯竭,故红土矿将是未来镍的主要来源。
由于炼钢技术的进步, 原来采用纯镍类原料,冶炼合金钢和不锈钢的钢厂,从经济角度考虑己改用非纯镍类。
因此,火法冶炼发展很快。
目前世界以紅土鎳礦所產出之镍,其中70%是采用火法工艺流程回收,产品为镍铁或镍锍。
二、红土镍矿生产工艺分类目前世界上红土镍矿的处理工艺,总体上归纳起来大致有三种,即(1)火法工艺:以回转窑干燥预还原?电炉熔炼法(RKEF)、烧结?鼓风炉、硫化熔炼法、烧结?高炉还原熔炼法等法為主。
(2)湿法工艺:以高压酸浸法和还原焙烧?氨浸法為主。
(3)火湿法结合工艺。
以下即是针对各工艺之简述。
2.1火法工艺火法工艺主要冶炼方法包括回转窑干燥预还原?电炉熔炼法(RKEF)、烧结?鼓风炉硫化熔炼法、烧结?高炉还原熔炼法等,产品主要为镍铁合金和镍锍产品。
镍铁合金可直接供生产不锈钢,而镍锍则须经进一步精炼等程序,始得高纯镍之产品。
(1) 回转窑干燥预还原?电炉熔炼法(RKEF)顾名思义即是红土镍矿经回转窑进行干燥与预还原后,再投入电炉熔炼成粗制镍铁。
此法工艺较适合处理高品位的氧化镍矿,而其生产规模更可依据原料供应情况、矿石贮量等等决定。
此法亦是现行生产镍铁的主流,表一即是目前全世界采用回转窑-电炉熔炼法的代表性生产厂家及基本情况。
烧结机工艺流程图
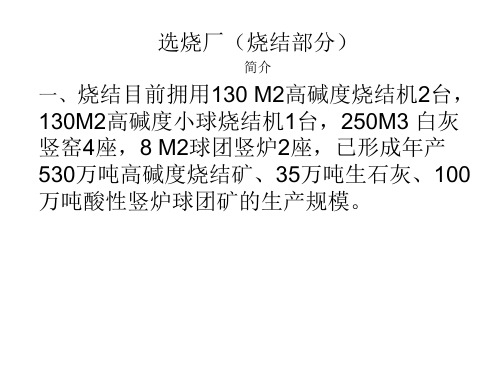
与布入生球量基本平衡
• 焙烧过程:由冷却带进行热交换所产生的约 300~500℃的热风通过导风墙对布在竖炉烘干 床上的生球进行干燥脱水,再经热废气预热氧 化后以一定的速度向下移动到焙烧带,设在竖 炉两侧的燃烧室燃烧高炉煤气产生1000±20℃ 高温气体从火口喷入炉内对生球进行高温氧化 焙烧,Fe3O4氧化焙烧过程放热,使焙烧带温 度高达1200~1300℃,进行高温固结,再经过 均热带进行均热定型后完成全部固结过程,固 结后的球团进入到冷却带与由下往上鼓入的冷 却风进行热交换而得到冷却,冷却到约500℃ 后的球团矿从竖炉底部经齿辊卸料机排出
• 工艺流程图ห้องสมุดไป่ตู้
铁料 粘结剂
配料
混匀干燥
润磨
造球
高炉
冷却
竖炉
生球筛分
粉
• 原料系统:原料有磁铁精矿、粘结剂(膨润土) 和燃料。 • 配料系统:将一种或两种磁铁精矿和膨润土按 一定比例进行配合 。 • 混匀干燥系统 :由于受到来料条件的限制,运 至球团生产的精矿水份往往要高于造球所需的 适宜水份,精矿水份较大的情况下,会给球团 矿生产的造球作业带来不利的影响,生球粒度 偏大且强度差;水份太大时甚至无法造球。为 了获得合格的生球,必须在球团生产工艺中设 置烘干系统,以保证精矿在造球时达到适宜的 水份,以提高生球的产质量
• 冷却系统 :由振动给料机排到的竖 炉热球团矿温度一般在500~700℃, 不便于皮带的运输和储存,需采用 36m2轻型带式冷却机进行二次冷却 到150℃以下,然后由耐热胶带运 输至成品矿槽进行储存,再送至高 炉进行冶炼
白灰窑
• 工艺原理:石灰竖窑生产冶金石灰是通过 焦碳的燃烧提供大量的热量,将石灰石加 热至1150~1200℃进行煅烧,使石灰石中 的碳酸钙产生分解,放出二氧化碳,生成 氧化钙的过程
重金属冶金学-新-铅冶金--铅烧结矿的鼓风炉还原熔炼

铅烧结矿的鼓风炉还原熔炼
一、概述 1、鼓风炉还原熔炼目的
使铅的氧化物还原,并与贵金属和铋等聚集进入粗铅,而 使各种造渣成分(包括SiO2、CaO、FeO、Fe3O4等)及锌等进 入炉渣,以达到相互分离。
1
1、鼓风炉还原熔炼目的
目的:使铅的氧化物还原,并与贵金属和铋等聚集进入粗 铅,而使各种造渣成分(包括SiO2、CaO、FeO、Fe3O4等)及 锌等进入炉渣,以达到相互分离。
由图可见,在1000℃时金属氧化 物还原的先后顺序是: Cu2O、PbO、NiO、CdO、SnO2、 Fe3O4、FeO、ZnO、Cr2O3、MnO。
图3-2 金属氧化物还原曲线比较
11
2)金属氧化物的固体碳还原(直接还原)
固体碳还原反应可用下式表示:
MeO+C=Me+CO
(3-4)
固体氧化物的直接还原,实质上是下列
• 铅烧结块中的铅主要以PbO(包括结合态的硅酸铅) 和少量的PbS、金属Pb及PbSO4等形态存在,此外还 含有伴存的Cu、Zn、Bi等有价金属和贵金属Ag、Au 以及一些脉石氧化物。
5
2) 焦炭
• 焦炭在铅鼓风炉还原熔炼过程中的作用: ①发热剂。焦炭燃烧放出的热量为吸热化学反应和
炉料熔化造渣提供充足的热量,保证熔体过热所必需的 温度;
氧化物的理论开始还原温度。
图3-3 金属氧化物的固体碳还原 平衡曲线图
12
4、铅的还原反应△Go-T 图
氧化铅和硅酸铅的直接还原和间接还原反应的吉布斯标准自由能变化与 温度的关系可用图2-15 的△Go-T 图表示(P96)。
图2-15 铅化合物还原反应的△G--T图
13
对同一类型的还原 反应,直接还原的吉 布斯标准自由能变化 的负值总比间接还原 时要大。
铅冶炼技术
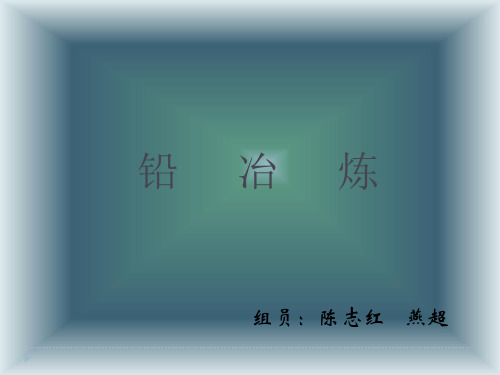
从上自下共分为五个区域:
1)炉料预热区(100~400℃).炉料被烘干,表面水被蒸发, 易还原的氧化物被还原。
2)上还原区(400~700℃).在此去结晶水开始脱除,碳酸 盐及硫酸盐开始分解,还原过程近一倍加强。铁的高价氧化 物被还原成低价氧化物。
3)下还原区(700~900℃).在此区CO还原作用强烈,硫酸 铅呈熔融状态并开始被还原。
在7.5-15%之间的矿床占 24.1%,铅+锌平均品位大于15%的 矿床仅占4.3%。 根据多年经验,铅锌品位小于7.5%的矿床,开采的经济 效益不甚理想,生产成本高,利润微薄甚至亏损。这就限制
了铅资源的利用。
我国铅锌的主要生产基地
我国铅锌业经过这么多年的发展,现已经形成了东北、 湖南、两广,滇川、西北等五大铅锌采选冶和加工配套的 生产基地。其铅产量占全国产量的85%以上。锌产量占全国 的95%。 东北铅锌生产基地
13
烧
结
图2.1 烧结机实物图 机 台 车ຫໍສະໝຸດ 带 式 烧 烧 机14
1.1.1 烧结焙烧的目的 (1)氧化脱硫:将精矿中PbS和其他金属硫化物氧化成PbO
等金属氧化物,同时除去矿石中的砷、锑。 (2)将细粒炉料烧结成适合鼓风炉熔炼的,具有一定孔隙 度的烧结矿。 1.1.2 烧结焙烧的方法 工业上采用两次焙烧和一次焙烧两种方法。
➢ 铅锌密切共生,单一的铅矿较少; ➢ 锌品位高于铅,锌、铅比值平均为2.5; ➢ 铅锌矿床物质成分复杂,共伴生组分多,尤以白银、黄金、
我国铅资源的特点
铜、镉、铋、铟、锗等综合利用价值大。其中白银回收量在
全国白银总产量中占到65-70% ; 就铅锌矿品位而言,呈现出如下特点:
➢ 矿贫矿多、富矿少,结构构造和矿物组成复杂; ➢ 中国铅锌矿床的平均品位铅为1.99%,锌为4.49%, ➢ 铅+锌平均品位小于9.5%的矿床占71.6%,铅+锌平均品位
铅冶炼工艺及用能特点
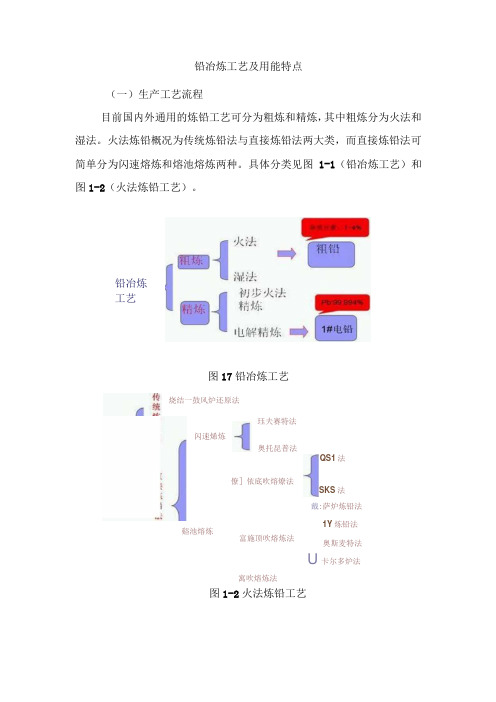
铅冶炼工艺及用能特点(一)生产工艺流程目前国内外通用的炼铅工艺可分为粗炼和精炼,其中粗炼分为火法和湿法。
火法炼铅概况为传统炼铅法与直接炼铅法两大类,而直接炼铅法可简单分为闪速熔炼和熔池熔炼两种。
具体分类见图1-1(铅冶炼工艺)和图1-2(火法炼铅工艺)。
图17铅冶炼工艺U 卡尔多炉法寓吹熔炼法图1-2火法炼铅工艺珏夫赛特法SKS 法戴:萨炉炼铅法谿池熔炼 富施顶吹熔炼法 1Y 炼铅法奥斯麦特法铅冶炼工艺烧结一鼓风炉还原法闪速烯炼奥托昆普法QS1法僚]依底吹熔燎法1.传统炼铅法传统炼铅法即烧结一鼓风炉还原熔炼工艺,其主要设备为烧结机和鼓风炉,分两段分别完成氧化和还原过程,该工艺本身存在一些缺陷:烧结过程中SO2浓度偏低,烟气SO2转换率只能达90%左右,SCh利用率低;烧结过程产生的反应热不能有效回收利用,鼓风炉熔炼时需消耗大量冶金焦,能耗较高;烧结烟气中浓度低,不能有效夹带粉尘量大,烧结返料约80%,烧结成本高;鼓风炉烟气SO2回收,环保压力大;工作、卫生及操作环境差,难以实现清洁生产,对职工健康危害大。
由于该工艺较为成熟,且投资小,目前在国外铅生产仍占有重要作用,而国内该工艺己经列入《产业结构调整指导目录(2011年版)》淘汰类,属于淘汰类工艺。
2.直接炼铅法直接炼铅法分为闪速熔炼和熔池熔炼:闪速熔炼的典型代表有基夫赛特法、奥托昆普法;溶池熔炼的典型代表有QS1法、水口山法(SKS).艾萨炉、卡尔多法等。
(1)基夫赛特法的关键设备为基夫赛特炉,主要由反应塔、电热还原区、铜水套和包括余热锅炉在内的直升烟道组成,该法在反应塔内完成氧化过程和80%左右的还原过程,在电热还原区完成20%左右还原过程。
该炼铅方法有以下特点:原料适应性强,对原料品位没有过多要求,可处理铅精矿、多金属金矿、锌渣、铅烟尘和二次铅物料等;炉子运行稳定、连续,炉体寿命长,维修费用低,作业率可高达95%以上;主金属回收率高,铅回收率98%,金银回收率99%,锌回收率60%以上;工作环境卫生条件好,烟尘率低,炉体密闭,烟尘烟气逸散少,工艺环保性好;烟气中S02浓度高,制酸成本低;自动化程度高,工人劳动强度低,所需员工数量少。