车削加工中毛刺的产生及控制
《机械制造工艺学》教案 影响加工表面粗糙度的工艺因素及其改善措施
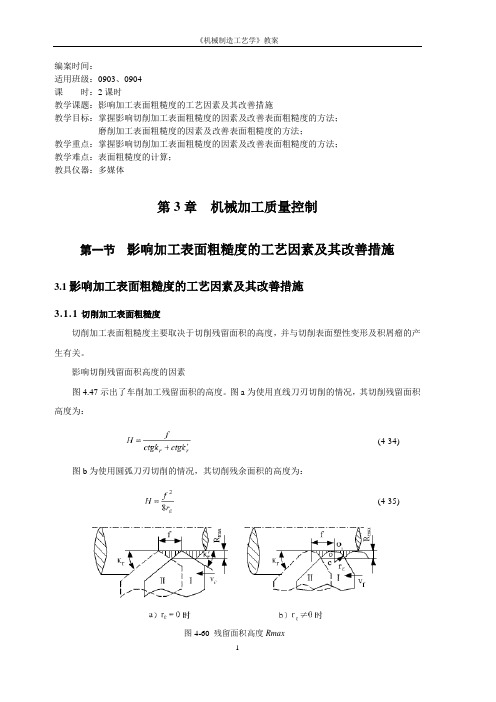
编案时间:适用班级:0903、0904课时:2课时教学课题:影响加工表面粗糙度的工艺因素及其改善措施教学目标:掌握影响切削加工表面粗糙度的因素及改善表面粗糙度的方法;磨削加工表面粗糙度的因素及改善表面粗糙度的方法;教学重点:掌握影响切削加工表面粗糙度的因素及改善表面粗糙度的方法;教学难点:表面粗糙度的计算;教具仪器:多媒体第3章机械加工质量控制第一节影响加工表面粗糙度的工艺因素及其改善措施3.1影响加工表面粗糙度的工艺因素及其改善措施3.1.1切削加工表面粗糙度切削加工表面粗糙度主要取决于切削残留面积的高度,并与切削表面塑性变形及积屑瘤的产生有关。
影响切削残留面积高度的因素图4.47示出了车削加工残留面积的高度。
图a为使用直线刀刃切削的情况,其切削残留面积高度为:(4-34) 图b为使用圆弧刀刃切削的情况,其切削残余面积的高度为:(4-35)图4-60 残留面积高度Rmax从上面两式可知,影响切削残留面积高度的因素主要包括:刀尖圆弧半径、主偏角、副偏角及进给量f等。
影响切削表面塑性变形和积屑瘤的因素图4-61示出了加工塑性材料时切削速度对表面粗糙度的影响。
切削速度v处于20~50m/min 时,表面粗糙度值最大,这是由于此时容易产生积屑瘤或鳞刺。
积屑瘤已在3.4节中介绍,鳞刺是指切削加工表面在切削速度方向产生的鱼鳞片状的毛刺。
在切削低碳钢、中碳钢、铬钢、不锈钢、铝合金、紫铜等塑性金属时,无论是车、刨、钻、插、滚齿、插齿和螺纹加工工序中都可能产生鳞刺。
积屑瘤和鳞刺均使表面粗糙度值加大。
当切削速度超100m/min时,表面粗糙度值下降,并趋于稳定。
在实际切削时,选择低速宽刀精切和高速精切,往往可以得到较小的表面粗糙度值。
图4-61 切削45钢时切削速度与粗糙度关系一般说,材料韧性越大或塑性变形趋势越大,被加工表面粗糙度就越大。
切削脆性材料比切削塑性材料容易达到表面粗糙度的要求。
对于同样的材料,金相组织越是粗大,切削加工后的表面粗糙度值也越大。
车削螺纹时常见故障及解决方法

车削螺纹时常见故障及解决方法螺纹车削是机械加工中的一项重要工艺,常用于制作螺栓、螺母等产品。
在车削螺纹过程中,有时会遇到一些常见的故障,如螺纹断裂、螺纹毛刺等问题。
本文将针对这些常见故障,给出相应的解决方法。
一、螺纹断裂螺纹断裂是车削螺纹中最常见的故障之一,主要原因有以下几点:1. 切削量过大。
车削螺纹时,如果一次性切削量过大,容易导致螺纹切削力过大,从而造成螺纹断裂。
2. 车削速度过高。
车削速度过高,会使螺纹材料在车削过程中产生过热现象,从而影响螺纹强度,导致断裂。
3. 切削刃磨损严重。
切削刃磨损严重会导致螺纹车削时切削力不均匀,从而容易引起断裂。
解决方法:1. 合理控制切削量。
在车削螺纹时,应根据工件的材料和尺寸,选择合适的切削量,避免一次性过大的切削力。
2. 控制切削速度。
根据螺纹材料的硬度和热处理情况,选择合适的切削速度,避免过高的车削速度造成螺纹断裂。
3. 及时更换刀具。
定期检查和更换切削刃,保证切削刃的锐利度,避免因刀具磨损产生过大的切削力。
二、螺纹毛刺螺纹毛刺是车削螺纹常见的表面缺陷之一,主要原因有以下几点:1. 加工精度不高。
车削螺纹时,如果刀具偏斜、工件夹紧不稳定等,容易导致精度不高,从而产生毛刺。
2. 切削液不合适。
切削液在车削螺纹时起到冷却、润滑的作用,选用不合适的切削液容易造成毛刺。
3. 刀具磨损严重。
刀具磨损严重会导致切削力不均匀,从而产生毛刺。
解决方法:1. 提高加工精度。
在车削螺纹前,检查刀具和夹持装置,确保工艺参数设置正确,以提高加工精度。
2. 合理选择切削液。
根据螺纹材料的特性和切削条件,选择合适的切削液,保证切削液的冷却和润滑效果,减少毛刺。
3. 及时更换刀具。
定期检查和更换刀具,保证刀具的切削锋利度,减少切削力不均匀引起的毛刺问题。
三、螺纹尺寸不准确螺纹尺寸不准确是车削螺纹常见的质量问题之一,主要原因有以下几点:1. 刀具磨损不均匀。
刀具磨损不均匀会导致切削力不均匀,从而影响螺纹尺寸的精度。
轴类零件外圆的加工方法
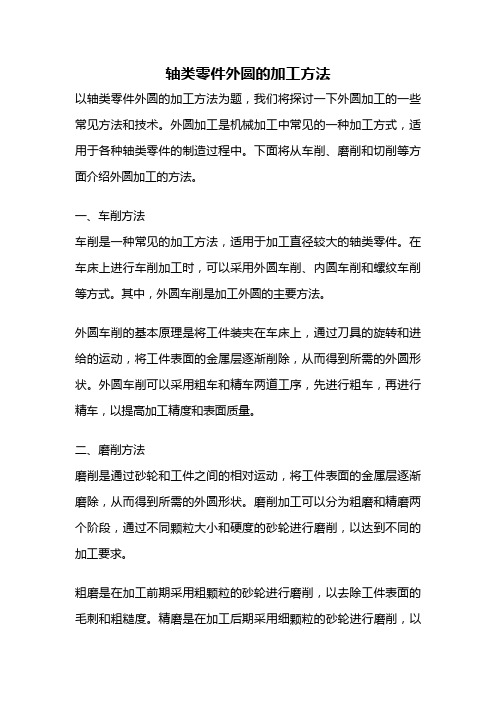
轴类零件外圆的加工方法以轴类零件外圆的加工方法为题,我们将探讨一下外圆加工的一些常见方法和技术。
外圆加工是机械加工中常见的一种加工方式,适用于各种轴类零件的制造过程中。
下面将从车削、磨削和切削等方面介绍外圆加工的方法。
一、车削方法车削是一种常见的加工方法,适用于加工直径较大的轴类零件。
在车床上进行车削加工时,可以采用外圆车削、内圆车削和螺纹车削等方式。
其中,外圆车削是加工外圆的主要方法。
外圆车削的基本原理是将工件装夹在车床上,通过刀具的旋转和进给的运动,将工件表面的金属层逐渐削除,从而得到所需的外圆形状。
外圆车削可以采用粗车和精车两道工序,先进行粗车,再进行精车,以提高加工精度和表面质量。
二、磨削方法磨削是通过砂轮和工件之间的相对运动,将工件表面的金属层逐渐磨除,从而得到所需的外圆形状。
磨削加工可以分为粗磨和精磨两个阶段,通过不同颗粒大小和硬度的砂轮进行磨削,以达到不同的加工要求。
粗磨是在加工前期采用粗颗粒的砂轮进行磨削,以去除工件表面的毛刺和粗糙度。
精磨是在加工后期采用细颗粒的砂轮进行磨削,以提高工件的尺寸精度和表面质量。
三、切削方法切削加工是通过刀具与工件之间的相对运动,将工件表面的金属层逐渐切削掉,从而得到所需的外圆形状。
切削加工可以采用车削切削、铣削切削和车铣复合切削等方式。
车削切削是通过车床上的刀具进行切削加工,根据工件的形状和加工要求选择合适的刀具进行切削。
铣削切削是通过铣床上的刀具进行切削加工,将刀具按照预定的路径进行旋转和进给运动,从而形成所需的外圆形状。
车铣复合切削是将车床和铣床的功能进行组合,通过车床上的主轴旋转和铣床上的进给运动,实现对外圆形状的加工。
总结:以上是轴类零件外圆的加工方法,包括车削、磨削和切削等多种方式。
在实际加工过程中,根据工件的形状、尺寸和加工要求选择合适的加工方法,以确保外圆加工的精度和质量。
此外,还需要注意刀具的选择、刀具的磨损与更换、加工参数的控制等方面的问题,以提高加工效率和质量。
某壳体组件机械加工过程中的多余物控制方法
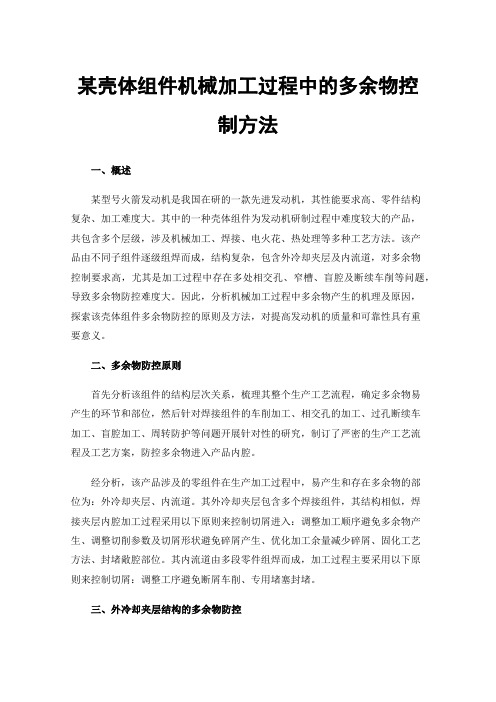
某壳体组件机械加工过程中的多余物控制方法一、概述某型号火箭发动机是我国在研的一款先进发动机,其性能要求高、零件结构复杂、加工难度大。
其中的一种壳体组件为发动机研制过程中难度较大的产品,共包含多个层级,涉及机械加工、焊接、电火花、热处理等多种工艺方法。
该产品由不同子组件逐级组焊而成,结构复杂,包含外冷却夹层及内流道,对多余物控制要求高,尤其是加工过程中存在多处相交孔、窄槽、盲腔及断续车削等问题,导致多余物防控难度大。
因此,分析机械加工过程中多余物产生的机理及原因,探索该壳体组件多余物防控的原则及方法,对提高发动机的质量和可靠性具有重要意义。
二、多余物防控原则首先分析该组件的结构层次关系,梳理其整个生产工艺流程,确定多余物易产生的环节和部位,然后针对焊接组件的车削加工、相交孔的加工、过孔断续车加工、盲腔加工、周转防护等问题开展针对性的研究,制订了严密的生产工艺流程及工艺方案,防控多余物进入产品内腔。
经分析,该产品涉及的零组件在生产加工过程中,易产生和存在多余物的部位为:外冷却夹层、内流道。
其外冷却夹层包含多个焊接组件,其结构相似,焊接夹层内腔加工过程采用以下原则来控制切屑进入:调整加工顺序避免多余物产生、调整切削参数及切屑形状避免碎屑产生、优化加工余量减少碎屑、固化工艺方法、封堵敞腔部位。
其内流道由多段零件组焊而成,加工过程主要采用以下原则来控制切屑:调整工序避免断屑车削、专用堵塞封堵。
三、外冷却夹层结构的多余物防控该产品的外冷却夹层包含的焊接组件主要为:静子组件、锥管组件、弯管组件。
针对以上组件及部位的多余物防控制要求制定以下措施:1.静子零件及组件静子零件外形余量大,在后续静子组件状态需车除,其中需过整周的径向小孔进行断续车削,车削产生的碎屑易进入径向孔内,原始方法是采用黄油、蜂蜡等进行封堵,存在封堵困难、不易清理的问题,容易残留多余物。
为此,在后续产品加工过程中通过调整零件及组件之间的加工顺序及加工余量,在不影响产品结构的前提下,将静子组件状态小孔所在部位的外形加工余量调整至静子零件状态加工,从而避免在静子组件状态产生过孔断续车削现象,杜绝了多余物进入的风险。
车削加工切屑形状分析及合理断屑方法
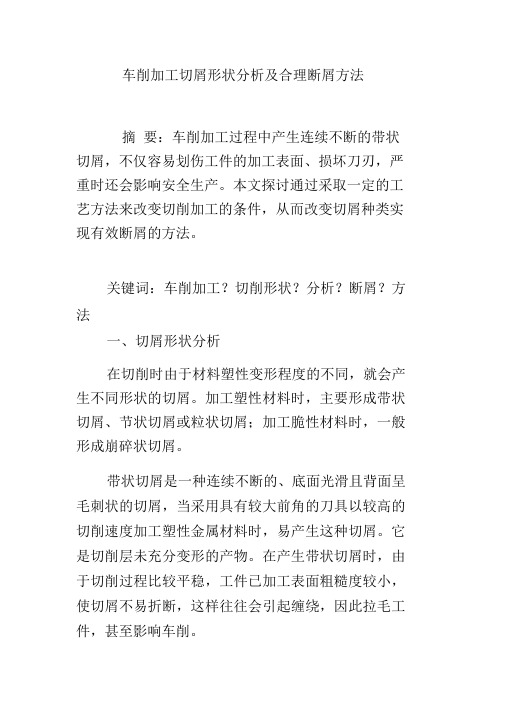
车削加工切屑形状分析及合理断屑方法摘要:车削加工过程中产生连续不断的带状切屑,不仅容易划伤工件的加工表面、损坏刀刃,严重时还会影响安全生产。
本文探讨通过采取一定的工艺方法来改变切削加工的条件,从而改变切屑种类实现有效断屑的方法。
关键词:车削加工?切削形状?分析?断屑?方法一、切屑形状分析在切削时由于材料塑性变形程度的不同,就会产生不同形状的切屑。
加工塑性材料时,主要形成带状切屑、节状切屑或粒状切屑;加工脆性材料时,一般形成崩碎状切屑。
带状切屑是一种连续不断的、底面光滑且背面呈毛刺状的切屑,当采用具有较大前角的刀具以较高的切削速度加工塑性金属材料时,易产生这种切屑。
它是切削层未充分变形的产物。
在产生带状切屑时,由于切削过程比较平稳,工件已加工表面粗糙度较小,使切屑不易折断,这样往往会引起缠绕,因此拉毛工件,甚至影响车削。
节状切屑是一种底面光滑、背面有明显裂纹且裂纹较深的切屑。
当采用具有减小前角的刀具,以较低的切削速度加工塑性金属材料时,易产生这种切屑。
它是切屑层较为充分变形的产物,已达到剪裂程度。
在产生节状切屑时,切屑工作不平稳,工件已加工表面粗糙度较大。
粒状切屑是一种均匀的颗粒状切屑。
当使用具有较小前角的刀具,以很低的切削速度加工塑性金属材料时,易产生这种切屑。
它是切削层充分变形的产物,其材料已产生剪切破坏,已使切屑沿厚度断裂。
在产生粒状切屑时,切削工作不平稳,工件已加工表面粗糙度大。
崩碎状切屑是一种不规则的细粒状切屑。
它是在切削脆性材料时,切削层弹性变形,几乎不经过塑性变形阶段,经突然崩裂而产生的切屑。
在产生崩碎状切屑时,切削工作不稳定,刀刃受到较大的冲击力,工件已加工表面粗糙不平。
切屑的形状随工件材料和切削条件的不同而不同。
因此,在加工过程中,我们可以通过观察切屑的形状来判断切屑条件是否合适,也可以通过转化切削条件改变切屑的形状,改进加工方法。
二、断屑方法切屑断与不断的根本原因在于切屑形成过程中材料的变形和所受应力的大小。
电连接器多余物的预防和控制

电连接器多余物的预防和控制摘要:多余物作为电连接器的一种常见故障现象,它往往会影响电连接器的可靠性,从而危害整个系统的安全。
文章重点分析总结了电连接器在整个生产过程中常见的多余物失效案例,阐述了多余物产生的原因并提出了预防和控制措施。
主题词:电连接器、多余物、预防和控制1 引言多余物是产品存在的由外部进入或内部产生的与产品规定状态不符的物质。
按这些物质的实质属性,通常可以分为金属多余物和非金属多余物两大类。
其中一些多余物是可以自由活动的,一旦进入到一些电连接器的关键部位,非金属多余物可能会造成产品的接触不通或接触电阻增大等失效模式,金属多余物则会引起电连接器短路或击穿。
电连接器作为电流或信号连接的基础元器件,在电缆与电缆之间、或电缆与设备之间起电流或信号传输的作用,广泛应用于航空、航天、国防等军用系统,其可靠性和质量优劣直接关系到整个系统的安全。
因此,总结分析电连接器多余物的失效案例,研究相关检查方法及控制标准,提出预防改进措施,对电连接器质量和可靠性具有十分重要的意义。
2失效案例及预防控制措施2.1设计不合理引起的金属多余物案例1:某型号连接器在外观检验时发现壳体内腔存在黑色多余物。
经过分析发现,该型号接触件的设计不合理,其装配位置存在尖角,在与绝缘体装配时,将绝缘体刮伤造成多余物。
产品的设计方案作为预防和控制多余物的源头,应把预防多余物作为产品质量的设计准则之一。
产品的设计结构应便于检查和清除多余物,避免尖角、窄缝、死角等;合理选用材料,充分考虑材料由于磨损或咬死产生的多余物,不选用易腐蚀、蜕皮、龟裂、氧化、易产生静电、吸附性强的材料。
另外制定合理的工艺流程也十分重要,工艺流程应尽量减少装配过程的再机械加工,若确实需要再加工(包含返工),必须规定专门的工艺措施、加工场地、检验方法等,以确保不产生多余物或多余物能得到清除;工艺流程对关键部位和重点环节,应规定控制多余物的操作方法和检验措施。
2.2机加工质量差引起的金属多余物案例2:某型号连接器在性能测试时发现产品短路。
车削加工危险和防护

车削加工危险和防护1、车削加工危险(1)车削加工最主要的不安全因素是切屑的飞溅,以及车床的附带工件造成的伤害。
(2)切削过程中形成的切屑卷曲、边缘锋利,特别是连续而且成螺旋状的切屑,易缠绕操作者的手或身体造成的伤害。
(3)崩碎屑飞向操作者。
(4)车削加工时暴露在外的旋转部分,钩住操作者的衣服或将手卷入转动部分造成的伤害事故。
长棒料、异性工件加工更危险。
(5)车床运转中用手清除切屑、测量工件或用砂布打磨工件毛刺,易造成手与运动部件相撞。
(6)工件及装夹附件没有夹紧,就开机工作,易使工件等飞出伤人。
工件、半成品几手用工具、量具、夹具、量具放置不当,造成扳手飞落、工件弹落伤人事故。
(7)机床局部照明不足或灯光刺眼,不利操作者观察切削过程,而产生错误操作,导致伤害事故。
(8)车床周围布局不合理、卫生条件不好、切屑堆放不当,也易造成事故。
(9)车床技术状态不好、缺乏定期检修、保险装置失灵等,也会造成机床事故而引起的伤害事故。
2、安全防护措施(1)采取断屑措施:断屑器、断屑槽等。
(2)在车床上安装活动式透明挡板。
用气流或乳化液对切屑进行冲洗,改变切屑的射出方向。
(3)使用防护罩式安全装置将其危险部分罩住。
如安全鸡心夹、安全拨盘等。
(4)对切削下来的带状切屑,应用钩子进行清除,切勿用手拉。
(5)除车床上装有自动测量的量具外,均应停车测量工件,并将刀架到安全位置。
(6)用纱布打磨工件表面时,要把刀具移到安全位置,并注意不要让手和衣服接触到工件表面。
(7)磨内孔时,不可用手指支持砂布,应用木棍代替,同时车速不宜过快。
(8)禁止把工具、夹具或工件放在车床身上和主轴变速箱上。
车间作业指导书

车间作业指导书篇一:车间作业指导书车间作业指导书对车间生产、行政工作进行全面领导和管理;对车间生产活动进行统筹规划、组织、控制和协调;组织车间员工按时、保质、保量地完成生产任务一、召开早会车间早会有两种,分别是负责召开车间员工早会和召开所有指导工与收发员的早会。
1、负责召开车间员工早会,可以采取两种方式进行:站队集合和广播两种方式,时间一般在早上7:50开始,会议时间一般控制在5—10分钟,若事情多则可适当延长,若认为无须召开车间员工早会,则各班组必须召开班组员工早会,会议基本相同,大致的内容有以下几个方面,可以选择几个方面的话题来展开:1)、公司的政策与制度;2)、车间的生产任务情况;3)、车间的重大事件和活动;4)、车间卫生、物料摆放、安全生产和设备维护等情况或不足;5)、员工关心的话题,包括生活等方面;6)、员工的提问而需要集体说明回答的;7)、总结前一天生产完成的进度情况,表扬做得好的,批评做得不好的;8)、总结前一天产品的质量情况,表扬质量好的,今后产品质量须加强的。
2、负责召开指导工和收发员的早会,会议采取在车间办公室召开,时间在7:40开始,时间是10分钟,早会的内容有以下几个方面:1)、车间的生产安排与各组生产任务;2)、产品生产质量注意事项;3)、当日开货技术质量指导与说明;4)、生产日常管理注意的几个方面:人员、成本、安全、5S 等方面;5)、公司的政策与制度;6)、车间的总的生产任务情况;7)、车间的重大事件和活动;8)、解答各指导工和收发员提出的问题而且是认为有必要开会说明的。
二、生产调度按生产计划合理安排各班组的生产任务,根据需要对本车间人员、设备、材料等进行调配;依照生产均衡原则对车间各班组的生产进行有效调度,负责生产计划完成率能达到百分九十以上。
1、产能统计1)、预估产能:在生产接到定单的时候,由生产计划员与车间主管豫估每一工序的人均产能;2)、初步产能:在车产前版的过程中要根据车版的情况向各指导工了解大货产能,若与预估产能有差异则需与计划员反馈,及时调整生产安排;3)、产能调整:在车货的过程中要对车位的产能情况进行跟踪与统计,建立产能档案。
车床工件表面粗糙度的原因及措施
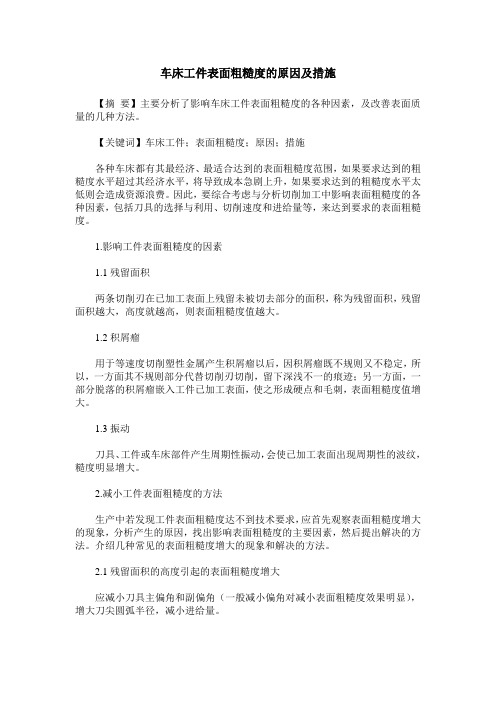
车床工件表面粗糙度的原因及措施【摘要】主要分析了影响车床工件表面粗糙度的各种因素,及改善表面质量的几种方法。
【关键词】车床工件;表面粗糙度;原因;措施各种车床都有其最经济、最适合达到的表面粗糙度范围,如果要求达到的粗糙度水平超过其经济水平,将导致成本急剧上升,如果要求达到的粗糙度水平太低则会造成资源浪费。
因此,要综合考虑与分析切削加工中影响表面粗糙度的各种因素,包括刀具的选择与利用、切削速度和进给量等,来达到要求的表面粗糙度。
1.影响工件表面粗糙度的因素1.1残留面积两条切削刃在已加工表面上残留未被切去部分的面积,称为残留面积,残留面积越大,高度就越高,则表面粗糙度值越大。
1.2积屑瘤用于等速度切削塑性金属产生积屑瘤以后,因积屑瘤既不规则又不稳定,所以,一方面其不规则部分代替切削刃切削,留下深浅不一的痕迹;另一方面,一部分脱落的积屑瘤嵌入工件已加工表面,使之形成硬点和毛刺,表面粗糙度值增大。
1.3振动刀具、工件或车床部件产生周期性振动,会使已加工表面出现周期性的波纹,糙度明显增大。
2.减小工件表面粗糙度的方法生产中若发现工件表面粗糙度达不到技术要求,应首先观察表面粗糙度增大的现象,分析产生的原因,找出影响表面粗糙度的主要因素,然后提出解决的方法。
介绍几种常见的表面粗糙度增大的现象和解决的方法。
2.1残留面积的高度引起的表面粗糙度增大应减小刀具主偏角和副偏角(一般减小偏角对减小表面粗糙度效果明显),增大刀尖圆弧半径,减小进给量。
2.2工件表面产生毛刺引起表面粗糙度增大工件表面上产生毛刺,一般是由于积屑瘤引起的,这时可用改变切削速度的方法来抑制积屑瘤的产生和长大,如用高速钢车刀时应降低切削速度,使其小于5m/min,并加注切削液;用硬质合金车刀时应增大切削速度,避开最易产生积屑瘤的中速范围(15-30-m/min)。
因此,应尽量减小前、后刀面的表面粗糙度,及时重磨或更换刀具,经常保持刀具的锋利。
2.3切屑擦毛工件表面切屑擦毛的工件表面一般是无规则的很浅的划纹,这时应选用负值刃倾角的车刀,使切屑流向工件待加工表面,并采用断屑或卷屑措施。
车削过程中工件表面粗糙度值的控制
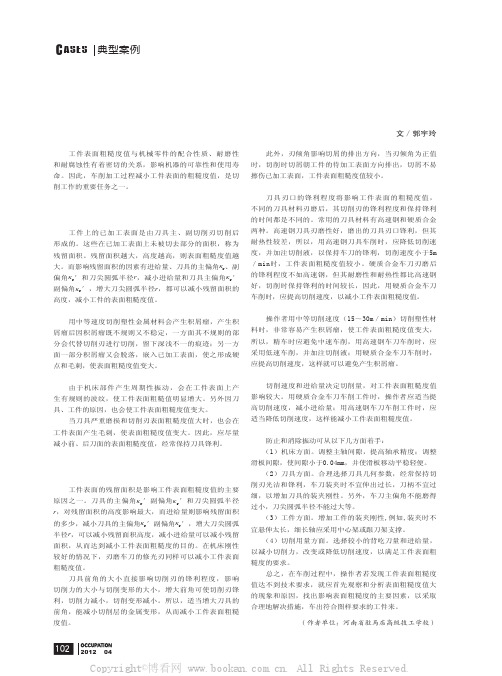
C OCCUPATION2012 04102典型案例ASES车削过程中工件表面粗糙度值的控制文/郭宇玲工件表面粗糙度值与机械零件的配合性质、耐磨性和耐腐蚀性有着密切的关系,影响机器的可靠性和使用寿命。
因此,车削加工过程减小工件表面的粗糙度值,是切削工作的重要任务之一。
一、切削过程中影响工件表面粗糙度的因素1.残留面积 工件上的已加工表面是由刀具主、副切削刃切削后形成的。
这些在已加工表面上未被切去部分的面积,称为残留面积。
残留面积越大,高度越高,则表面粗糙度值越大。
而影响残留面积的因素有进给量、刀具的主偏角κr 、副偏角κr ′和刀尖圆弧半径r ,减小进给量和刀具主偏角κr ′副偏角κr ′,增大刀尖圆弧半径r ,都可以减小残留面积的高度,减小工件的表面粗糙度值。
2.积屑瘤 用中等速度切削塑性金属材料会产生积屑瘤,产生积屑瘤后因积屑瘤既不规则又不稳定,一方面其不规则的部分会代替切削刃进行切削,留下深浅不一的痕迹;另一方面一部分积屑瘤又会脱落,嵌入已加工表面,使之形成硬点和毛刺,使表面粗糙度值变大。
3.机床部件振动 由于机床部件产生周期性振动,会在工件表面上产生有规则的波纹,使工件表面粗糙值明显增大。
另外因刀具、工件的原因,也会使工件表面粗糙度值变大。
当刀具严重磨损和切削刃表面粗糙度值大时,也会在工件表面产生毛刺,使表面粗糙度值变大。
因此,应尽量减小前、后刀面的表面粗糙度值,经常保持刀具锋利。
二、减小工件表面粗糙度值的方法1.合理刃磨刀具角度 工件表面的残留面积是影响工件表面粗糙度值的主要原因之一。
刀具的主偏角κr ′副偏角κr ′和刀尖圆弧半径r ,对残留面积的高度影响最大,而进给量则影响残留面积的多少,减小刀具的主偏角κr ′副偏角κr ′,增大刀尖圆弧半径r ,可以减小残留面积高度,减小进给量可以减小残留面积,从而达到减小工件表面粗糙度的目的。
在机床刚性较好的情况下,刃磨车刀的修光刃同样可以减小工件表面粗糙度值。
车削加工中毛刺的产生及控制

车削加工中毛刺的生成因素的控制金属切削中产生的切削毛刺严重的影响了被加工工件的尺寸精度和形位精度,并在一定程度上成为后续加工工序作业的障碍(例如在滑动管一序切断过程中产生的端面毛刺若处理不当会影响到滑动管与滑动板焊接工序时的定位),甚至还影响到零件的使用性能和寿命。
因此,弄清切削加工毛刺的生成过程、生成机理及影响因素,对开发切削加工中毛刺的抑制与去除方法,保证和提高切削加工质量具有重要的理论意义和实用价值。
按照以切削运动和道具切削刃为基础的切削毛刺分类方法,车削加工中产生的切削毛刺可分为进给方向毛刺(沿进给运动方向产生的切入毛刺和切出毛刺,例如在座管外圆车削中由于刀具的磨损、程序说设定的切削用量、刀具的磨损、切削液和对切屑的控制表面过于粗糙,)和两侧毛刺(沿刀具的主、副切削刃两侧流动所产生的切削毛刺,例如在导向套镗孔后需配备倒角刀倒角已去除边缘毛刺)两类。
一般情况下,沿进给运动方向产生切入进给方向毛刺的尺寸很小。
沿刀具主切削刃产生的两侧毛刺只能部分地增大切出进给方向毛刺的高度尺寸,对工件已加工表面质量多无多大影响。
但沿刀具副切削刃产生的两侧毛刺一流在工件的已加工表面上,增大其表面粗糙度值,破坏工件的尺寸精度,对切削加工质量产生直接的影响。
当加工精度要求不太高时其影响可以忽略。
而沿进给运动方向产生的切出进给方向毛刺尺寸最大,去除困难,去除作业量大,它往往成为增大加工成本、降低切削效率的主要原因之一。
金属切削加工中影响切削毛刺的主要因素有被加工工件材料的物理机械性能、刀具的几何参数、切削用量及工件终端部的形态等。
车削加工中进给方向毛刺形成过程:由于各种因素的影响,车削加工中可形成一次毛刺和二次毛刺,一次毛刺的形成大体上经过正常切削、端部变形、继续切削和毛刺形成四个阶段:1、正常切削从刀具切入工件被切削层后,切削沿着前刀面流出,切削加工顺利进行,在正常切削阶段中,沿这刀具的主、副切削刃产生两侧毛刺,并且沿刀具副切削刃产生的两次毛刺部分的遗留在工件的已加工表面上,影响其质量。
车床加工提高断屑的方法

车床加工提高断屑的方法在车床加工中,提高断屑的质量和数量,是保证加工质量和效率的关键之一。
断屑是在车削过程中由切削刀具切削工件时剥离出的金属屑,其质量和数量直接影响着工件表面的光洁度、加工精度和加工效率。
因此,合理选择加工参数和采取有效的方法,提高断屑的质量和数量,对于提升车床加工的质量和效率具有重要意义。
1. 优化刀具和切削参数在车床加工中,选择合适的刀具和切削参数是提高断屑质量和数量的关键。
首先要根据工件材料和加工要求选择合适的切削刀具,确保刀具材料和刀具几何形状适合加工材料的特性。
同时,合理选择切削速度、进给速度和切削深度,避免切削过程中出现过大的切削力和温度,从而影响断屑的形成和排出。
2. 控制冷却润滑在车床加工中,冷却润滑是非常重要的一环。
通过适量的切削液冷却工件和刀具,可以有效减少切削温度,降低切削力,提高加工表面质量和断屑的排出。
此外,良好的冷却润滑还能延长刀具的使用寿命,减少刀具磨损,提高加工效率。
3. 加工去毛刺在车床加工中,去除工件表面的毛刺对于提高断屑质量非常重要。
通过采用合适的去毛刺工艺和工具,可以有效地去除工件表面的毛刺,减少毛刺对切削刀具的干扰,提高断屑的排出和加工表面的光洁度。
4. 保持车床整洁保持车床清洁整洁也是提高断屑质量和数量的关键之一。
定期清理车床上的切屑和油污,保持刀具和工件的清洁,可以有效减少切削过程中产生的摩擦和磨损,提高断屑的排出和加工表面的质量。
通过以上几点方法的有效应用,可以提高车床加工中断屑的质量和数量,进而提升加工质量和效率。
只有不断优化加工工艺,注重细节,才能达到更好的加工效果。
切割过程中如何避免产生毛刺?

切割过程中如何避免产生毛刺?在进行切割工作时,往往会面临一种常见的问题——毛刺的产生。
毛刺不仅会影响切割效果,还可能导致工件表面不光滑,甚至造成安全隐患。
为了避免这一问题,下面将介绍一些有效的方法。
一、选择合适的切割工具使用合适的切割工具是避免产生毛刺的首要步骤。
对于不同材料的切割,需要选择不同形状和材质的刀具。
同时,还需要考虑刀具的刃口尺寸和材质硬度等因素,以确保切割过程中刃口能够充分贴合工件表面,减少毛刺的产生。
二、调整切割参数切割过程中的切削速度、进给速度和切割深度等参数的合理调整,也是避免毛刺产生的关键。
通过降低切割速度和进给速度,可以减少刀具对工件表面的冲击力,降低毛刺的概率。
另外,适当减小切割深度,也有助于减少毛刺的产生。
三、保持切削工具的锐利切削工具的锋利程度对切割效果有着重要影响。
当刀具变钝时,切削力会增大,导致切割时产生较大的振动和毛刺。
因此,定期检查和及时磨削切割工具是保持切割效果的重要手段之一。
四、采用适当的切割技术合理选择切割技术是避免产生毛刺的另一个关键因素。
例如,对于一些容易产生毛刺的薄板材料,可以采用倾角切割法,使刀具的进给方向与工件表面的倾角相吻合,从而减少毛刺的产生。
此外,使用夹具固定工件,以减少振动和位移,也是一种有效的方法。
五、加工前进行预处理对于一些容易产生毛刺的特殊材料,如不锈钢、铝合金等,可以在切割之前进行预处理,如表面抛光或涂覆保护膜等。
这些预处理方法能够降低材料表面的粗糙度,减少毛刺的产生。
总结起来,在进行切割工作时,为了避免产生毛刺,我们可以从选择合适的切割工具、调整切割参数、保持切削工具的锐利、采用适当的切割技术以及进行预处理等方面来着手。
只有综合运用这些方法,才能有效地提高切割质量,确保工件表面的平整度和质量。
切割过程中的毛刺问题将不再困扰我们。
铝合金切削加工过程中毛刺形成机理与控制

上海交通大学硕士学位论文铝合金切削加工过程中毛刺形成机理与控制姓名:董洪艳申请学位级别:硕士专业:机械工程指导教师:邵华;张其然20080601BURR FORMATION MECHANISM AND CONTROLIN MILLING OF 2A12 ALUMINUM ALLOYABSTRACTBurr formed during metal cutting process,is harmful to both function and quality of mechanical components. In this thesis, based on FEM analysis and cutting experiment in milling of 2A12(LY12) aluminum-alloy,burr formation mechanism and the impact of cutting parameters on burr dimensions were explored. FEM analysisⅠdemonstrated that when cutting 2A12(LY12) aluminum-alloy ,the type burr was formed in cutting out direction due to chip bending at theⅡend of the work piece and the burr is big ;The type burr is formedⅠdue to the breakage of type burr with further plastic bending at the endof the work piece and the burr is relatively small. FEM analysis and cutting experiment showed that the bigger the depth of cut is,the larger the formed burr is; the increase the cutting velocity decreases the burr dimensions,and the impact of feed rate on burr dimension depends on the machining system. The orthogonal experiments of the two machining system indicated that the optimized cutting conditions of the first machining system are : depth of cut 0.1mm,feed per tooth 0.05mm/z,spindle speed 250m/min and corresponding burr height was about 0.02mm;the optimization cutting conditions of the second machiningsystem are :depth of cut 0.2mm,feed per tooth 0.2mm/z,spindle speed 4000r/min, and corresponding burr height was around 0.01mm. In this thesis machinability of 2A12(LY12) aluminum alloy was further explored. The work is of some practical value to the machining of the material.KEY WORDS:2A12(LY12) aluminum alloy,milling,burr,metal cutting,machinability, FEA上海交通大学学位论文原创性声明本人郑重声明:所呈交的学位论文,是本人在导师的指导下,独立进行研究工作所取得的成果。
钳工毛刺工作总结
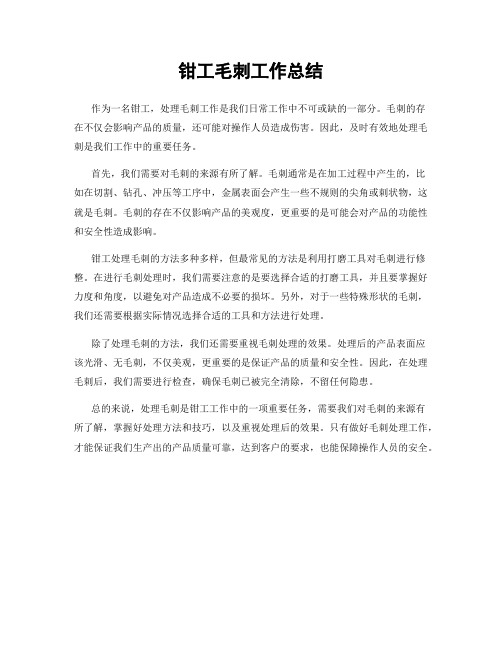
钳工毛刺工作总结
作为一名钳工,处理毛刺工作是我们日常工作中不可或缺的一部分。
毛刺的存
在不仅会影响产品的质量,还可能对操作人员造成伤害。
因此,及时有效地处理毛刺是我们工作中的重要任务。
首先,我们需要对毛刺的来源有所了解。
毛刺通常是在加工过程中产生的,比
如在切割、钻孔、冲压等工序中,金属表面会产生一些不规则的尖角或刺状物,这就是毛刺。
毛刺的存在不仅影响产品的美观度,更重要的是可能会对产品的功能性和安全性造成影响。
钳工处理毛刺的方法多种多样,但最常见的方法是利用打磨工具对毛刺进行修整。
在进行毛刺处理时,我们需要注意的是要选择合适的打磨工具,并且要掌握好力度和角度,以避免对产品造成不必要的损坏。
另外,对于一些特殊形状的毛刺,我们还需要根据实际情况选择合适的工具和方法进行处理。
除了处理毛刺的方法,我们还需要重视毛刺处理的效果。
处理后的产品表面应
该光滑、无毛刺,不仅美观,更重要的是保证产品的质量和安全性。
因此,在处理毛刺后,我们需要进行检查,确保毛刺已被完全清除,不留任何隐患。
总的来说,处理毛刺是钳工工作中的一项重要任务,需要我们对毛刺的来源有
所了解,掌握好处理方法和技巧,以及重视处理后的效果。
只有做好毛刺处理工作,才能保证我们生产出的产品质量可靠,达到客户的要求,也能保障操作人员的安全。
关于铝合金材料的螺纹加工的毛刺及铝屑的原理及解决方案

关于铝合金材料的内螺纹加工的方法及产生毛刺及铝屑的解决方案内螺纹加工有车削螺纹、攻丝、挤压、铣削,车削、攻丝加工是传统加工工艺,挤压螺纹、铣削螺纹是现代制造业中的先进技术。
挤压内螺纹主要适用延伸率大于10%钢材的薄板及铝合金材料,钢材薄板厚度一般在3mm。
铣削螺纹是用螺纹销在数控机床通过圆弧插补加工成形的螺纹。
由于铣削螺纹是通过刀具的侧刃铣削,刀具会受到侧向力作用,如果材料较硬,会产生让刀现象,导致螺纹上下大小不一。
所以小直径(直径20以内)的螺纹铣削一般不适用钢材,一般适用于铝合金材料。
挤压螺纹时原理是通过材料塑性变形形成的螺纹,用挤压丝锥挤压螺纹时,不会产生切削,也就是说没有把材料切除,所以不会切削物产生。
而切削丝锥加攻螺纹是通过吧材料切除,形成螺纹,所以会产生切削物。
挤压螺纹的加工预钻孔直径和切削丝锥不一样,切削丝锥的加工螺纹时的预钻孔直径就是螺纹的小径,挤压丝锥的预钻孔直径要比螺纹的小径大,具体公式是:预钻孔直径=D-0.2P-0.00403Pf1+0.0127n ,D:标准大径,P:螺距,f1:螺纹接触高度比(%),n:RH(OSG标准,此标准能与国标对应)的精度号,例如:M10×1.5RH7P2级内螺纹,螺纹接触高度比为90%,预钻孔直径=10-0.2×1.5-0.00403×1.5×90+0.0127×7=9.24铣削螺纹的预钻孔是和切削丝锥的螺纹预钻孔直径一样,其原理螺纹铣刀在数控机床走一个圆弧插补,刀具的进一个螺距的深度。
切削丝锥的切削齿是按照螺距螺旋的,在丝锥的每个截面圆上是按照一个螺距在上升的。
螺纹铣刀的切削齿刃不是按照螺距螺旋的,每个齿形在刀具的一个截面圆上的。
金属切削时,由于材料有延伸性,所以被切削材料容易在被切处的棱边、孔等的相交线处形成毛刺。
铝合金材料的延伸性好,所以在加工铝合金材料是更容易产生毛刺,特别是在加工铝合金材料的内螺纹时,会在螺纹的牙尖形成毛刺和铝屑。
浅谈提高普通车削加工表面粗糙度的方法
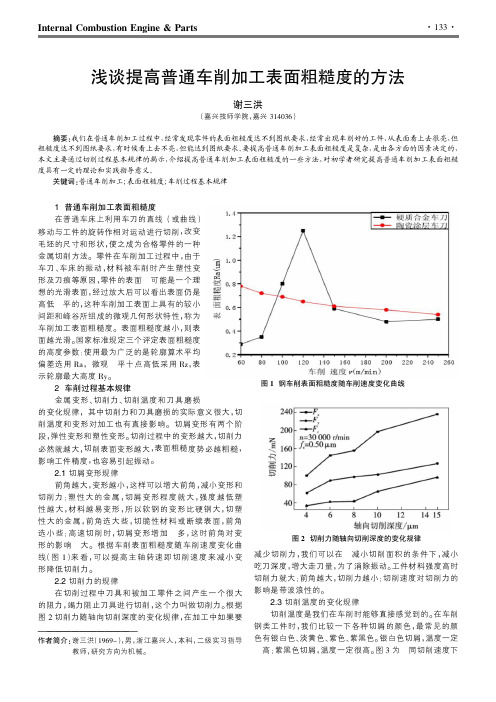
图1钢车削表面粗糙度随车削速度变化曲线
的变化规律,其中切削力和刀具磨损的实际意义很大,切
削温度和变形对加工也有直接影响。
切屑变形有两个阶
切削过程中的变形越大,切削力
表面粗糙度势必越粗糙,
图2切削力随轴向切削深度的变化规律
减少切削力,我们可以在不减小切削面积的条件下,减小
吃刀深度,增大走刀量,为了消除振动。
工件材料强度高时
切削力就大;前角越大,切削力越小;切削速度对切削力的
影响是带波浪性的。
2.3切削温度的变化规律
切削温度是我们在车削时能够直接感觉到的。
在车削
钢类工件时,我们比较一下各种切屑的颜色,最常见的颜
色有银白色、淡黄色、紫色、紫黑色。
银白色切屑,温度一定
图3不同切削速度下切削温度的对比
切削温度的对比,根据切屑温度的这一规律性,必须控制切削速度。
2.4刀具磨损的变化规律
一把车刀使用一段时间以后,刀具的切削刃变钝了,甚至无法使用;经过重新刃磨后,使切削刃恢复锋利。
从开始使用到磨钝后的有效实际工作时间叫做车刀耐用用T表示。
车刀从工具库领出后到完全不能再刃磨,好报废的这个使用期限叫刀具寿命,用W表示。
车刀正常磨损的原因有:①机械擦伤磨损;②粘结磨损;③金相组织变化磨损;④元素扩散磨损。
一般车刀的磨损主要是由高温而引起的。
切削速度增大时,车刀耐用度T急剧降低。
- 1、下载文档前请自行甄别文档内容的完整性,平台不提供额外的编辑、内容补充、找答案等附加服务。
- 2、"仅部分预览"的文档,不可在线预览部分如存在完整性等问题,可反馈申请退款(可完整预览的文档不适用该条件!)。
- 3、如文档侵犯您的权益,请联系客服反馈,我们会尽快为您处理(人工客服工作时间:9:00-18:30)。
车削加工中毛刺的生成因素的控制
金属切削中产生的切削毛刺严重的影响了被加工工件的尺寸精度和形位精度,并在一定程度上成为后续加工工序作业的障碍(例如在滑动管一序切断过程中产生的端面毛刺若处理不当会影响到滑动管与滑动板焊接工序时的定位),甚至还影响到零件的使用性能和寿命。
因此,弄清切削加工毛刺的生成过程、生成机理及影响因素,对开发切削加工中毛刺的抑制与去除方法,保证和提高切削加工质量具有重要的理论意义和实用价值。
按照以切削运动和道具切削刃为基础的切削毛刺分类方法,车削加工中产生的切削毛刺可分为进给方向毛刺(沿进给运动方向产生的切入毛刺和切出毛刺,例如在座管外圆车削中由于刀具的磨损、程序说设定的切削用量、刀具的磨损、切削液和对切屑的控制表面过于粗糙,)和两侧毛刺(沿刀具的主、副切削刃两侧流动所产生的切削毛刺,例如在导向套镗孔后需配备倒角刀倒角已去除边缘毛刺)两类。
一般情况下,沿进给运动方向产生切入进给方向毛刺的尺寸很小。
沿刀具主切削刃产生的两侧毛刺只能部分地增大切出进给方向毛刺的高度尺寸,对工件已加工表面质量多无多大影响。
但沿刀具副切削刃产生的两侧毛刺一流在工件的已加工表面上,增大其表面粗糙度值,破坏工件的尺寸精度,对切削加工质量产生直接的影响。
当加工精度要求不太高时其影响可以忽略。
而沿进给运动方向产生的切出进给方向毛刺尺寸最大,去除困难,去除作业量大,它往往成为增大加工成本、降低切削效率的主要原因之一。
金属切削加工中影响切削毛刺的主要因素有被加工工件材料的物理机械性能、刀具的几何参数、切削用量及工件终端部的形态等。
车削加工中进给方向毛刺形成过程:由于各种因素的影响,车削加工中可形成一次毛刺和二次毛刺,一次毛刺的形成大体上经过正常切削、端部变形、继续切削和毛刺形成四个阶段:
1、正常切削从刀具切入工件被切削层后,切削沿着前刀面流出,切削加工顺利进行,在正常切削阶段中,沿这刀具的主、副切削刃产生两侧毛刺,并且沿刀具副切削刃产生的两次毛刺部分的遗留在工件的已加工表面上,影响其质量。
2、端部变形当刀具逐渐接近工件的终端面时在进给分力的作用下,工件终端部开始产生变形其变形量随刀具接近工件终端部的距离缩小而缩小。
3、继续切削随着刀具逐渐接近工件的终端面,工件终端部材料的变形量逐渐增大。
由于被加工材料属于非完全刚塑体,具有一定的弹性,尽管工件被切削层与刀具相接触的最外缘点的变形量大于进给量,并依次逐渐的脱离切削,致使实际切削层向刀具的刀尖部位集中。
但由于与刀具刀尖相接触部位的被切削层材料的变形量小于进给量,所以仍能维持切削加工的继续进行。
4、当刀具的刀尖即将抵达工件终端面时,刀尖部位的被切削层金属材料的变形量大于进给量。
虽然此时刀具仍然沿着进给方向进行,但其切削
工作已经停止,刀具只能将变形很大的部分工件材料推到,使其遗留在工件终端面上形成进给方向毛刺。
一般情况下,一次毛刺的尺寸大,去除作业困难,去除作业量较大。
车削加工中二次毛刺的形成大体上经过正常切削、端部变形、裂纹扩展和脱落形成四个阶段。
正常切削和端部变形情况和一次毛刺形成下的情况相同,当刀具继续进行逼近工件终端部时,与刀尖相接触的被切削层金属,在进给分力的作用下产生裂纹,并随刀具的继续进行使裂纹加大、扩展,,促使已经形成的一次毛刺在其极限根部与工件终端部脱落,从而形成二次毛刺。
二次毛刺的尺寸较小。
当加工精度要求不太搞时,一般不需要进行去除作业,但当加工精度要求较高时也需要进行去除毛刺,但其去除容易,去除作业量也较一次毛刺小得多。
切削深度对毛刺影响。
随着切削深度的增加,毛刺的高度增大,但当切削深度达到某一数值时,毛刺的高度急剧减小,及形成的毛刺由一次毛刺转变为二次毛刺。
此时的切削深度成为临界切削深度,但切削毛刺的根部厚度仍随切削深度的增加而逐步增大,并未因一次毛刺转换层二次毛刺而发生很大的变化。
刀具主偏角、切削用量和刀尖圆弧半径的影响。
随着刀具主偏角的增加临界切削深度减小,并且毛刺的根部厚度也相应减小,改变车削加工中的仅给量和刀具的刀尖圆弧半径后,临界切削深度随着进给量的增加,临界切削深度值增大,一次毛刺越不易转换成二次毛刺,因为随这进给量的增加切削厚度增大,刀具对产生形变的工件终端部材料的推挤力增大,易于形成一次毛刺的缘故,粗车时应选一个尽可能大的背吃刀量,然后选择一个比较大的进给量,最后再根据刀具允许的寿命选一个合适的切削速度。
随着刀尖圆弧半径的增加,临界切削深度逐渐减小,因为随着刀尖圆弧边检的增加,刀尖部平均正盈利下降,致使工件终端材料的支持刚度相对提高,加速了一次毛刺向二次毛刺的转换。
车削加工中,通过部分地调整切削参数,提高切削速度,减小进给量,增大刀具前角、刀具刃倾角,刀具主偏角、刀尖圆弧半径,提高工件终端部的支持强度和刚度,合理的使用切削液。
促使工件终端部材料的脆化,进而抑制或减小车削加工中的毛刺,保证加工资料,提高切削加工效率。
此外,在实际生产加工过程中往往由于毛坯的改换、程序的改动对切削用量的改变等因素,对刀具的磨损、工具的损伤产生影响,例如在毛坯变厚的情况下,切削深度会相应增大,对刀具的磨损加剧,改变主偏角,致使工件毛刺量增大,因此在一个在生产过程中需按照一个合理的步骤进行规范生产,使工件的加工效率、对工具的折损、工人的生产加工工时达到一个合理的平衡点形成一个价值的最大化。