典型零件加工工艺齿轮
基于典型齿轮零件的数控工艺分析与加工
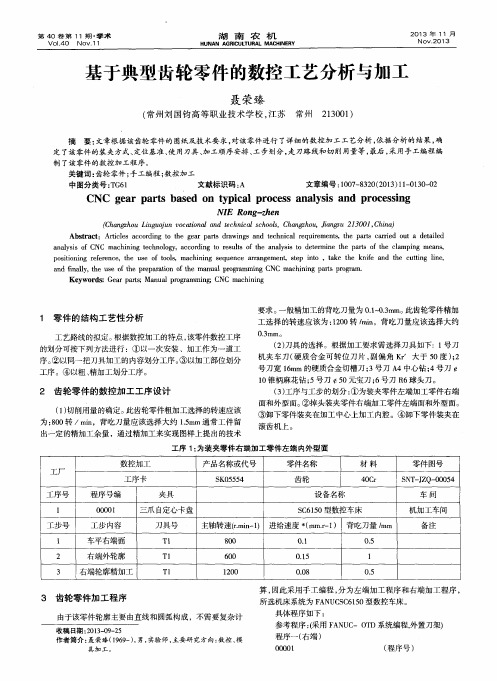
Ab s t r a c t :A r t i c l e s a c c o r d i n g t o t h e g e a r p a ts r d r a wi n g s a n d t e c h n i c a l r e q u i r e me n t s ,t h e p a r t s c a r r i e d o u t a d e t a i l e d
第 4 0卷 第 1 1期 ・ 学 术
VoI . 40 NO V. 1 1
湖
南
农
机
2 O1 3年 1 1 月
N OV. 201 3
HUNAN AGRI CUL TURAL MACHI NER Y
基于典型齿轮零件 的数控 工艺 分析 与加工
聂 荣臻
( 常 州刘 国钧 高等 职业技 术学 校 , 江苏 常 州 2 1 3 0 0 1 )
Nl E Ron g一 e n
( C h a n g z h o u L i u g u o j u n v o c a t i o n a l a n d t e c h n i c l a s c h o o l s ,C h a n g z h o  ̄J i ng a s u 2 1 3 0 0 1 , C h i n a )
齿轮工艺流程

齿轮工艺流程
齿轮是机械传动中常见的零部件,其工艺流程对于齿轮的质量和性能起着至关
重要的作用。
下面将介绍齿轮的工艺流程,包括材料选择、加工工艺、热处理和精加工等内容。
首先,齿轮的材料选择至关重要。
常见的齿轮材料包括碳素钢、合金钢和不锈
钢等。
在选择材料时,需要考虑到齿轮的使用环境、传动功率和工作温度等因素,以确保齿轮具有足够的强度和耐磨性。
接下来是齿轮的加工工艺。
齿轮的加工工艺通常包括车削、铣削、磨削和齿轮
切削等工艺。
在进行加工时,需要根据齿轮的尺寸、精度要求和齿轮的类型选择合适的加工工艺,以确保齿轮的加工质量。
然后是齿轮的热处理工艺。
热处理是提高齿轮硬度和耐磨性的重要工艺环节。
常见的热处理工艺包括淬火、渗碳和表面强化等。
在进行热处理时,需要控制好加热温度、保温时间和冷却速度,以确保齿轮具有良好的组织结构和性能。
最后是齿轮的精加工工艺。
精加工是保证齿轮精度和表面质量的关键环节。
常
见的精加工工艺包括滚齿、磨齿和齿面修形等。
在进行精加工时,需要控制好加工参数,确保齿轮的精度和表面质量达到要求。
总的来说,齿轮的工艺流程包括材料选择、加工工艺、热处理和精加工等环节,每个环节都对齿轮的质量和性能起着至关重要的作用。
只有严格控制每个环节,才能保证齿轮具有良好的工艺性能,满足不同工况下的使用要求。
传动齿轮加工工艺

传动齿轮加工工艺主要包括以下步骤:
1.铣齿:采用盘形模数铣刀或指状铣刀铣齿,属于成形法加工。
2.滚齿:属于展成法加工,其工作原理相当于一对螺旋齿轮啮合。
3.剃齿:在大批量生产中剃齿是非淬硬齿面常用的精加工方法。
剃齿还可形成鼓形齿,用以改善齿面接触区位置。
4.插齿:插齿是除滚齿以外常用的一种利用展成法的切齿工艺。
5.珩齿:珩齿原理与剃齿相似,珩轮与工件类似于一对螺旋齿轮
呈无侧隙啮合,利用啮合处的相对滑动,并在齿面间施加一定
的压力来进行珩齿。
链条、齿轮等七个机械零件的加工工艺
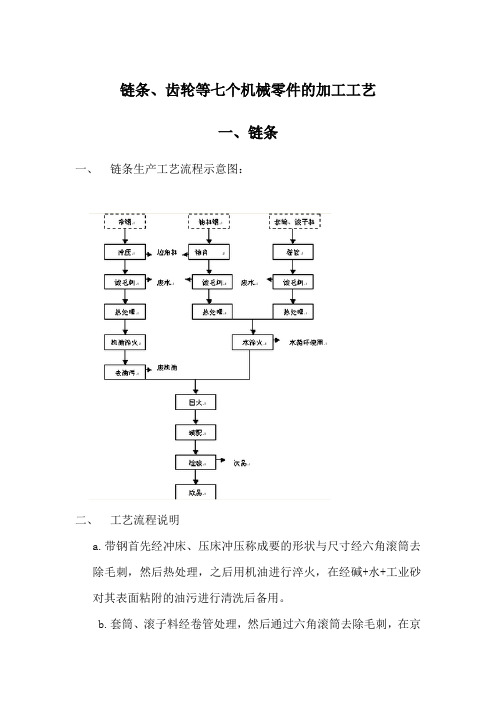
链条、齿轮等七个机械零件的加工工艺一、链条一、链条生产工艺流程示意图:二、工艺流程说明a.带钢首先经冲床、压床冲压称成要的形状与尺寸经六角滚筒去除毛刺,然后热处理,之后用机油进行淬火,在经碱+水+工业砂对其表面粘附的油污进行清洗后备用。
b.套筒、滚子料经卷管处理,然后通过六角滚筒去除毛刺,在京哈热处理之后用水淬火,然后对其表面的油污进行去除。
c.轴料钢首先经轴销机处理制成需要的形状与尺寸,然后通过六角滚筒去除毛刺,再经热处理后用水淬火,然后对其表面的油污进行去除。
d.最后将个零件进行回火,最后装配成型。
经检验合格后即为成品。
三、工艺1、热处理:在热处理设备中,在高温下采用各种辅助介质,改善零件的组织结构,提高各种物品性能。
2、渗碳:将零件置在热处理设备中加热至一定温度并保温一定时间,再通入含碳介质,将碳渗入零件表面,以提高链条硬度和耐磨性能。
3、淬火:零件在热处理设备中加热到一定温度后,保温一定时间,然后按照要求在不同的介质中冷却,从而提高零件硬度。
4、回火:经过淬火后的零件在热处理设备中以一定的温度进行加热,并保温一定时间后冷却。
零件经过回火可以降低淬火硬度,消除淬火应力,提高韧性。
5、发黑:采用高分子有机聚合原理,利用热处理工艺过程中回火余热成膜发黑。
发黑后工件带有光泽,耐腐蚀,防锈性能强;降低劳动强度,改善生产环境。
6、发蓝:把零件加热至一定的温度后,经过化学水溶液冷却,皂化,使零件表面颜色呈现蓝色。
经过发蓝处理的链条外观美观,还有防锈的作用。
不足之处就是这些化学水溶液对环境造成很大的污染。
7、磷化:将零件浸置在一定温度的磷化液内,使零件表面形成磷化层,可使零件表面颜色呈现黑色或灰色,提高链条美观的同时达到防腐的目的。
这些磷化液可循环利用,对环境污染较轻。
8、镀镍:采用电镀或化学镀镍的方法,在零件表面形成镀镍层,镀镍层既可以美观链条,又可以防腐。
镀镍链条一般用在露天场合。
9、镀锌:采用电镀或化学镀锌的方法,在零件表面形成镀锌层,镀锌层既可以美观链条,又可以防腐。
齿轮类零件加工工艺分析及夹具设计
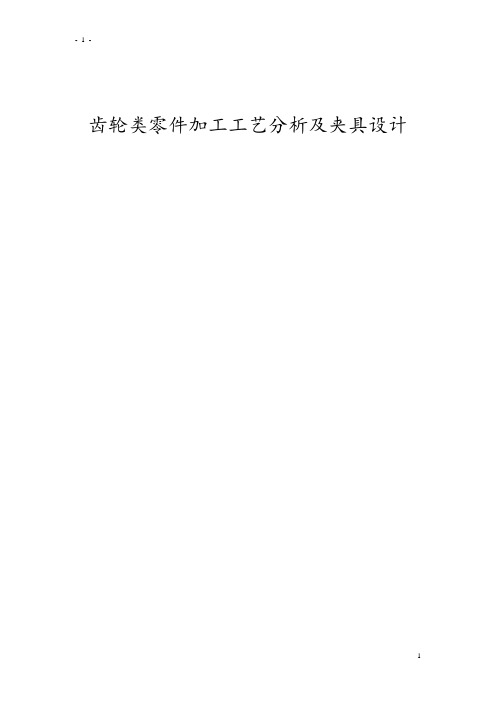
齿轮类零件加工工艺分析及夹具设计目录摘要 (4)第一章齿轮类零件加工工艺规程编制概述 (5)1.1工艺编制的总体步骤 (5)第二章对齿轮类零件的加工工艺编制及分析 (6)2.1分析齿轮类零件的技术要求 (6)2.2明确毛坯尺寸 (8)2.3拟定工艺路线 (8)2.4设计工序内容 (10)2.5填写工艺文件 (10)第三章对齿轮类零件加工工艺进行合理性分析 (11)第四章夹具设计的要求 (11)4.1 了解夹具设计的总体要求 (11)第五章夹具设计的特点 (12)5.1确定夹具的类型 (12)5.2钻模的主要类型 (12)第六章工件夹紧计算及选择 (13)6.1工件的夹紧 (13)6.2 夹紧力的选择 (13)6.3夹紧力的计算及精度分析 (14)第七章夹具的结构分析及设计 (16)7.1夹具的夹紧和定位 (16)7.2夹具的导向 (17)第八章夹具的总体分析 (17)第九章致谢 (18)摘要齿轮类零件是典型零件之一,它在机械主要用于传动,齿轮类零件主要有齿轮.齿轮轴,涡轮涡杆,在机械领域运用很广泛。
按传动形式分圆柱类齿轮、锥齿轮、齿条等。
按齿形状分:齿轮、齿、字齿等。
按制作方法分:铸造齿轮、烧结齿轮、轧制齿轮等。
我以齿轮加工工艺编制分析齿轮的加工要求,在生产实际中阐述齿轮的工艺过程,及工艺的合理性。
夹具在机械加工中有举足轻重的作用,好的夹具才是保障零件加工的方法。
我从夹具的分析、设计、计算、使用方面概述夹具的用途。
按专业化程度可分为通用夹具、专用夹具、可调夹具、组合夹具、成组夹具、标准夹具、随行夹具、组合机床夹具等。
我这次设计的是盖板式钻夹具。
这是一种专用夹具,专为一工件的一道工序而设计的夹具。
关键词:齿轮、夹具、工艺、设计1.1工艺编制的总体步骤1.分析零件的结构和技术要求(1)分析图样资料①加工工艺表面的尺寸精度和形状精度②各加工表面之间以及加工表面和不加工表面之间的位置精度③加工表面的粗糙度及表面的其他要求④热处理及其他要求(2)零件的结构工艺分析。
锥齿轮的工艺加工

摘要轴是组成机械的重要零件,也是机械加工中常见的典型零件之一。
它支撑着其它转动件回转并传递扭矩,同时又通过轴承与机器的机架连接。
但在职业学校机械加工实习课中,轴类零件的加工是学生练习车削技能的最基本也最重要的项目,但学生最后完工工件的质量总是很不理想,经过分析主要是学生对轴类零件的工艺分析工艺规程制订不够合理。
轴类零件中工艺规程的制订,直接关系到工件质量、劳动生产率和经济效益。
一零件可以有几种不同的加工方法,但只有某一种较合理,在制订机械加工工艺规程中,须注意以下几点。
1.零件图工艺分析中,需理解零件结构特点、精度、材质、热处理等技术要求,且要研究产品装配图,部件装配图及验收标准。
2.渗碳件加工工艺路线一般为:下料→锻造→正火→粗加工→半精加工→渗碳→去碳加工(对不需提高硬度部分)→淬火→车螺纹、钻孔或铣槽→粗磨→低温时效→半精磨→低温时效→精磨。
3.粗基准选择:有非加工表面,应选非加工表面作为粗基准。
对所有表面都需加工的铸件轴,根据加工余量最小表面找正。
且选择平整光滑表面,让开浇口处。
选牢固可靠表面为粗基准,同时,粗基准不可重复使用。
关键词:工艺分析;基准选择;工艺路线;粗糙度AbstractThe axis is composes the machinery the important components, also is in the machine-finishing one of common typical supports other rotors to rotate and to transmit the torque, simultaneously through bearing and machine rack in the vocational school machine-finishing practicum, the axis class components processing is the student practices the turning skill the most basic also most important project, but the student finally finishes the work piece quality very not to be always ideal, the process analysis mainly is the student countershaft class components craft analysis technological process making insufficiently is reasonable.In the axis class components the technological process making, relates the work piece quality, the labor productivity and the economic efficiency may have several different processing methods, but only then some one kind reasonable, in the making machine-finishing technological process, must pay attention to following several.1. detail drawing craft analysis, must understand components specifications and so on unique feature, precision, material quality, heat treatment, also need to study the product assembly drawing, the part assembly drawing and the approval standard.2. cementation processing craft route is generally: The yummy treats -> forging -> fire -> rough machining -> semi-finishing -> cementation -> decarbonization processing (to does not have to enhance degree of hardness part) -> the quenching -> cutting thread, the drill hole or the milling -> rough grinding -> low temperature effectiveness -> half correct grinding -> low temperature effectiveness -> correct grinding.3. thick datum choices: Has the non-processing surface, the elected non-processing surface takes the thick axis all must process which to all surfaces, adjusts according to the processing remainder smallest the choice smooth smooth surface, makes way the runner the reliable reliable surface is the thick datum, simultaneously, the thick datum cannot duplicate uses.Keywords: Craft analysis; datum choice; craft route;roughness目录引言........................................................ 错误!未定义书签。
圆柱齿轮制造基本工艺过程

滚切直、斜齿轮交换齿轮的调整公式见下表:
交换齿轮 速度交换齿轮 分度交换齿
名称
轮
公式 表公式中:
i An 0
n0
1000v da0
滚齿机是加工圆柱齿轮、蜗轮等零件的主要工艺装备。滚齿机按布局形式 和结构特点,可分为立式和卧式滚齿机,常用的是立式滚齿机。按JB/T6344.1— 1999的规定,滚齿机的型式有工作台移动式和立柱移动式两种,滚齿机的系列 由万能滚齿机、高效滚齿机和数控滚齿机构成。
滚齿是目前世界上在齿轮加工中应用最广的切齿方法,目前国际上精滚齿 的加工精度(主要指周节偏差)可以达到5~7级(GB/T10095),国内的滚齿机 (数控)精滚齿的加工精度也可以达到6~8级(GB/T10095)。CNC滚齿机是目 前国际上已广泛采用的设备,国内齿轮生产厂家的使用也越来越多。为了达到 最大可能的静刚度和动刚度,滚齿机部件都尽可能以封闭箱形的铸造结构制造, 采用减震性能良好的铸铁,有经过验证的热补偿系统。
滚齿原理图
10
二、齿轮的加工方法
1,滚齿 1),滚齿原理
根据滚齿加工原理,滚切齿轮时滚齿机必须 具有以下几种运动: (1)切削运动 即滚刀轴1的转速,借助于切削 速度交换齿轮或变速箱2,滚刀的转速为:
n0
1000v
da0
式中:—切削速度 (m/min)
—滚刀齿顶圆直径(mm)
2)分度运动 随着滚刀的转动,齿坯也要相应n地w
13
二、齿轮的加工方法
1,滚齿 常见的机械式传动链滚齿机很多,技术性能不尽相同,但均具备切削运动、
典型零件的选材与工艺路线分析.

2. 汽车齿轮
汽车齿轮功能—在变速箱中,通过它改变发动机、曲轴和主轴齿轮的速比; 在差速器中,齿轮增加扭矩,并调节左右轮的转速。全部 发动机动力均通过齿轮传给车轴,推动汽车运行。 工作条件—汽车齿轮受力较大,受冲击频繁,其耐磨性、疲劳强度、 心部强度以及冲击韧性等,均要求比机床齿轮高。 选材—用低碳钢进行渗碳处理来作重要齿轮。我国应用最多的 是合金渗碳钢20CrMnTi,
三、齿轮材料的性能要求
1.高的弯曲疲劳强度; 2. 高的接触疲劳强度和耐磨性;
3. 较高强度和冲击韧性。
还要求有较好的热处理工艺性能,例如热处理变形小,或变形有一定规律等。
四、典型齿轮选材举例
1.机床齿轮
机床变速箱齿轮担负传递动力,改变运动速度和方向的任务。 工作条件较好,转速中等,载荷不大,工作平稳无强烈冲击。 一般可选中碳钢制造,为了提高淬透性,也可选用中碳合金钢。
喷丸—增大表层压应力,提高疲劳强度,并清除氧化皮。
第八章 典型零件的选材与工艺路线分析
8.1齿轮选材
单元34- 1
第八章 典型零件的选材与工艺路线分析 8.1 齿轮选材 齿轮主要用于传递扭矩和调节速度, 一. 齿轮的工作条件
1.由于传递扭矩,齿根承受很大的变弯曲应力;
2.换挡、启动或啮合不均时,齿部承受一定冲击载荷;
3.齿面相互滚动或滑动接触,承受很大的接触压应力及摩擦力的作用。
第八章 典型零件的选材与工艺路线分析
8.1齿轮选材
单元34- 4
工艺路线:下料→锻造→正火→切削加工→渗碳→、淬火 及低温回火→喷丸→磨削加工 正火—可消除锻造应力,均匀组织,改善切削加工性, 改善齿轮表面加工质量。
渗碳、淬火及低温回火—得到表面高硬度、高耐磨性和接触疲劳抗力。 由于合金元素提高淬透性,淬火、回火后可 使心部获得较高的强度和足够的冲击韧性。
齿轮典型零件的加工工艺过程
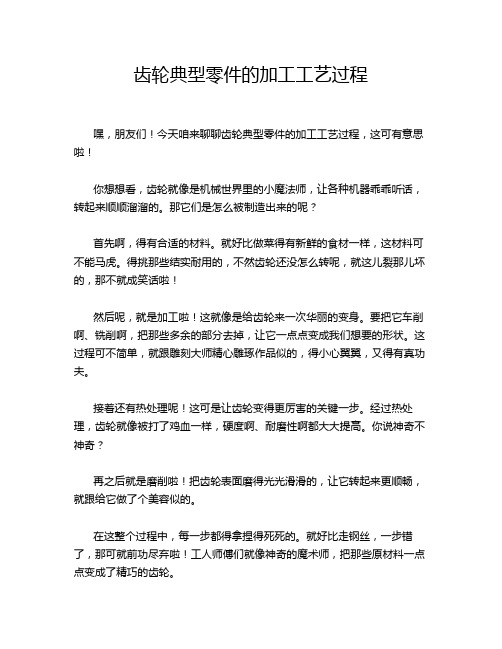
齿轮典型零件的加工工艺过程
嘿,朋友们!今天咱来聊聊齿轮典型零件的加工工艺过程,这可有意思啦!
你想想看,齿轮就像是机械世界里的小魔法师,让各种机器乖乖听话,转起来顺顺溜溜的。
那它们是怎么被制造出来的呢?
首先啊,得有合适的材料。
就好比做菜得有新鲜的食材一样,这材料可不能马虎。
得挑那些结实耐用的,不然齿轮还没怎么转呢,就这儿裂那儿坏的,那不就成笑话啦!
然后呢,就是加工啦!这就像是给齿轮来一次华丽的变身。
要把它车削啊、铣削啊,把那些多余的部分去掉,让它一点点变成我们想要的形状。
这过程可不简单,就跟雕刻大师精心雕琢作品似的,得小心翼翼,又得有真功夫。
接着还有热处理呢!这可是让齿轮变得更厉害的关键一步。
经过热处理,齿轮就像被打了鸡血一样,硬度啊、耐磨性啊都大大提高。
你说神奇不神奇?
再之后就是磨削啦!把齿轮表面磨得光光滑滑的,让它转起来更顺畅,就跟给它做了个美容似的。
在这整个过程中,每一步都得拿捏得死死的。
就好比走钢丝,一步错了,那可就前功尽弃啦!工人师傅们就像神奇的魔术师,把那些原材料一点点变成了精巧的齿轮。
你说这加工工艺是不是很了不起?没有这些精湛的工艺,哪来那些厉害的机器呀!那些大机器能轰隆隆地转起来,可都多亏了这些小小的齿轮和背后的加工工艺呢!咱得好好感谢那些默默付出的工人师傅们,是他们让这一切成为可能。
所以啊,可别小看了这齿轮典型零件的加工工艺过程,这里面的学问大着呢!它就像是机械世界的基石,支撑着整个庞大的体系。
下次你再看到那些复杂的机器,可别忘了想想它们里面的齿轮是怎么被制造出来的哟!这真的是太神奇,太让人惊叹啦!。
典型机械零件的加工工艺尺寸链计算例题及习题

基本尺寸计算:43.6=A+20-19. 8mm
A=43.4
上偏差计算:+0. 34=Bs(A)+0. 025-0
Bs (A)=+0. 315mm
下偏差计算:0=B,(A)+0-0. 05
Bx (A)=+0. 05mm
所以
A=43.4+0.05+0.315mm
按入体原则标注为:A=43.450+0.265mm
磨内孔至 Ø144.760+0.04mm;
2)渗氮,深度t1;
3)磨内孔至 Ø145+0.04mm,并保留 渗层深度t0=0. 3~0. 5mm 。
试求渗氮时的深度t1。
解 在孔的半径方向上画尺寸链如图2-28d 所示,显然t0=0. 3~0.5=0. 3+0.2mm是间接 获得,为封闭环。t1的求解如下:
解先列出尺寸链如图2-21b。要注意的是,当有直径尺寸时,
一般应考虑用半径尺寸来列尺寸链。因最后工序是直接保证 Ø40+0.05mm,间接保证43. 60+0.34mm,故43.6+0.3434 mm为封闭环,尺寸A和20+0.025mm为增环,19. 8+0.05mm为减环。利用基本公式计算可得
4.保证渗氮、渗碳层深度的工艺计 算
有些零件的表面需进行渗氮或渗碳 处理,并且要求精加工后要保持一 定的渗层深度。为此,必须确定渗 前加工的工序尺寸和热处理时的渗 层深度。
例 如图 所示某零件内孔, 材料为38CrMoAlA,孔径 为Ø145+0.04 mm内孔表 面需要渗氮,渗氮层深度 为0. 3~0. 5mm。其加工 过程为
典型零件的选材及加工工艺路线分析讲解材料

轻量化
减轻材料重量,提高产品机动性,降低能源 消耗和排放。
环保化
发展可再生、可回收、可降解的材料,减少 对环境的污染。
智能化
研究具有自适应、自修复、自感应等功能的 智能材料。
新材料的研究与开发
碳纤维复合材料
具有高强度、轻质、耐高温等优点,广 泛应用于航空航天、汽车等领域。
高分子合成材料
具有优良的化学稳定性、绝缘性、耐 磨性等,在建筑、电子、化工等领域
03
材料的应用与发展趋势
材料的应用领域
01
航空航天
用于制造飞机、火箭等高强度、轻 质材料。
建筑领域
用于制造桥梁、高层建筑等高强度、 高耐久性材料。
03
02
汽车工业
用于制造发动机、变速器等耐磨、 耐高温材料。
电子产品
用于制造集成电路、晶体管等精密、 小型化材料。
04
材料的发展趋势
高性能化
提高材料的强度、硬度、耐高温等性能,以 满足更高要求的工业应用。
可加工性原则
材料应具有良好的可加工性, 以便于零件的制造和加工。
可维修性原则
材料应易于维修和更换,以提 高零件的使用寿命和降低维修 成本。
常用材料介绍
钢铁
钢铁是机械制造业中应用最广泛的材料之一,具 有高强度、良好的韧性和耐磨性。
铜及铜合金
铜及铜合金具有良好的导电性、导热性、耐腐蚀 性和加工性能,广泛应用于电气、电子、化工等 领域。
实例二:齿轮类零件的选材与加工工艺
灰铸铁
用于制造一般用途的齿轮,如减速器齿轮等。
球墨铸铁
用于制造高强度、高耐磨性的齿轮,如汽车变速毛坯准备
根据零件材料和尺寸要求,准备毛坯。
粗加工
零件的加工工艺路线

零件的加工工艺路线1、轴类零件典型工艺路线对于7级精度、表面粗糙度Ra0.8~0.4μm的一般传动轴,其典型工艺路线是:正火-车端面钻中心孔-粗车各表面-精车各表面-铣花键、键槽-热处理-修研中心孔-粗磨外圆-精磨外圆-检验。
轴类零件一般采用中心孔作为定位基准,以实现基准统一的方案。
在单件小批生产中钻中心孔工序常在普通车床上进行。
在大批量生产中常在铣端面钻中心孔专用机床上进行。
中心孔是轴类零件加工全过程中使用的定位基准,其质量对加工精度有着重大影响。
所以必须安排修研中心孔工序。
修研中心孔一般在车床上用金刚石或硬质合金顶尖加压进行。
对于空心轴(如机床主轴),为了能使用顶尖孔定位,一般均采用带顶尖孔的锥套心轴或锥堵。
若外圆和锥孔需反复多次、互为基准进行加工,则在重装锥堵或心轴时,必须按外圆找正或重新修磨中心孔。
轴上的花键、键槽等次要表面的加工,一般安排在外圆精车之后,磨削之前进行。
因为如果在精车之前就铣出键槽,在精车时由于断续切削而易产生振动,影响加工质量,又容易损坏刀具,也难以控制键槽的尺寸。
但也不应安排在外圆精磨之后进行,以免破坏外圆表面的加工精度和表面质量。
在轴类零件的加工过程中,应当安排必要的热处理工序,以保证其机械性能和加工精度,并改善工件的切削加工性。
一般毛坯锻造后安排正火工序,而调质则安排在粗加工后进行,以便消除粗加工后产生的应力及获得良好的综合机械性能。
淬火工序则安排在磨削工序之前。
2、齿轮的加工工艺路线(以45号钢为例):(1)、毛坯下料(2)、粗车(3)、调质处理(提高齿轮轴的韧性和轴的刚度)(4)、精车齿坯至尺寸(5)、磨齿(6)、若轴上有键槽时,可先加工键槽等(7)、滚齿(8)、齿面中频淬火(小齿轮用高频淬火),淬火硬度HRC48-58(具体硬度值需要依据工况、载荷等因素而定)(9)、成品的最终检验3、箱体的加工工艺路线箱壳体要求加工的表面很多。
在这些加工表面中,孔系加工精度是工艺关键问题。
典型齿轮零件加工工艺分析
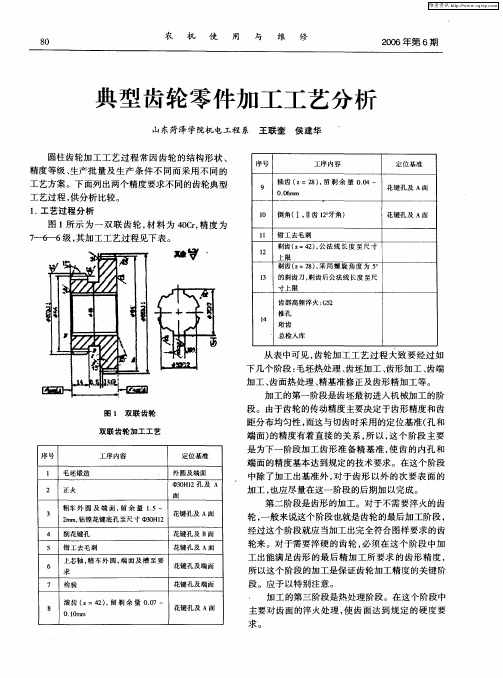
工序 内容
毛 坯 锻造
正 火
是 为下一 阶段 加工 齿 形准 备 精 基 准 , 齿 的 内孔 和 使
端面的精度基本达到规定的技术要求。在这个 阶段
中除 了加工 出基准 外 , 于 齿 形 以外 的次 要 表 面 的 对
加工 , 应尽 量在 这一 阶段 的后期加 以完 成 。 也 第 二 阶段是齿 形 的加工 。对 于不需 要淬 火 的齿 轮, 一般 来 说这个 阶段 也就 是齿轮 的最 后加 工阶 段 , 经过这 个 阶段就 应 当加工 出完全 符合 图样 要求 的齿 轮来 。对 于需 要淬 硬 的齿 轮 , 须 在 这个 阶段 中加 必
3 4
粗车 外 圆 及 端 面, 余 量 15~ 留 . 2 m, m 钻镗花键底孔至尺寸  ̄ 0 1  ̄ H2 3
削花 键 孔
花键 孔 及 A面 花 键孔 及 B面
5 6
7
钳 工去毛刺
花键孔及 A面
上芯轴 , 精车 外 圆、 面及槽 至 要 端 求 花键孔及端面
的。以修整过的基准面定 位进行齿形精加工, 可以 使定位准确可靠 , 余量分布也 比较均匀 , 以便达到精 加 工 的 目的。
2 定位 基准 的确定 .
图 3 齿 端 倒 圆 加 工形 式
4 精 基准修 正 .
齿轮淬 火 后基 准 孔产 生 变 形 , 保 证 齿形 精 加 为 工质 量 , 基准 孔必须 给予修正 。 对 对外 径定 心 的花键 孔齿 轮 , 常 用 花键 推刀 修 通
钳 工 去 毛 刺
1 2
剃齿( z=4 ) 公法线 长 度 至尺寸 2,
上 限
剃齿 ( z=2 ) 采用 螺旋 角度 为 5 8, 。
汽车典型零部件制造工艺

• 2)盘形齿轮 • 当齿轮较大时,为了减轻重量和机械加工量,常设计成有凹槽的、带
轮毂式的,如图7-3所示。 • 3)改变盘形齿轮的结构形式 • 如图7 -4 (b)图所示,这样不仅方便多件加工,又能提高生产率,增
强了工件在机床上的安装强度。若用图7 -4 (a)所示结构,则安装刚 度差,且增加了滚刀行程长度,降低了生产率。 • 4)主动锥齿轮(主减速器轴齿轮) • 其结构形式有悬臂式和骑马式(如图7-5所示)两种。其中悬臂式的两个 轴颈位于齿轮的同一侧。
上一页 下一页 返回
7. 1齿轮制造工艺
• 端面跳动量视齿轮精度和分度圆直径不同而异,对于精度等级为6~7 级的齿轮,规定为0. 011~0. 022 mm。基准端面的表面粗糙度Ra的 值为0. 40~0. 80 μm,非定位和非工作端面的表面粗糙度Ra值为6. 3~25 μm。
• 4)齿轮外圆尺寸公差 • 当齿轮外圆不作为加工、测量的基准时,其尺寸公差一般为IT 11,
必须对基准孔予以修整。修整的方法是内孔和端面一般用内圆磨床磨 削,花键孔则用推刀加工。轴齿轮中心孔用硬质合金顶尖加磨料研磨。 另外,对于汽车后桥的主动、被动锥齿轮齿面的最后加工,是将大小 齿轮成对地进行对研,对研后打上标记,以便配对装配。
上一页 下一页 返回
7. 1齿轮制造工艺
• 5.典型汽车齿轮的机械加工工艺过程 • 1)汽车变速器第一速及倒车齿轮零件的加工工艺过程 • 汽车变速器第一速及倒车齿轮零件加工工艺过程如表7-1所示。 • 2)汽车后桥主减速器主动锥齿轮零件的加工工艺 • 汽车后桥主减速器主动锥齿轮零件结构如图7-6所示。两端面及定位
大多数汽油发动机的连杆都是以垂直于杆身轴线的平面作为连杆体和连杆盖的接合面有些柴油发动机的曲轴由于提高强度刚度和减小轴承比压的需要增大了连杆轴颈因此连杆大头的外部尺寸略大于气缸直径致使连杆大头不能从气缸孔中抽出
浅析高精度齿轮的加工工艺分析

浅析高精度齿轮的加工工艺分析发布时间:2021-06-03T08:24:20.264Z 来源:《中国科技人才》2021年第9期作者:李清潮[导读] 目前,汽车齿轮机械加工过程中,通常采用的加工工艺为:车削锻造毛坯→切齿(滚齿/插齿)→剃齿→渗碳淬火→磨齿,滚齿和磨齿工艺过程如图1所示。
弗兰德传动系统有限公司天津 300400摘要:目前,齿轮加工工艺已经发展出了完善的加工流水线,齿轮加工的质量与产量也实现巨大的提升。
然而,伴随着现代工业的发展,对于齿轮加工精度提出了新型的要求。
传统的齿轮加工技艺,已经不能满足日益增长的生产需求。
因此,相关的人员需要在现有的齿轮加工技艺基础之上,进一步结合新型的科学技术手段,对齿轮加工工艺进行优化与改进,实现现代齿轮加工精度的有效提升,为现代工业技术的发展与建设奠定坚实的基础。
关键词:高精度;齿轮;加工工艺1汽车齿轮典型加工工艺分析目前,汽车齿轮机械加工过程中,通常采用的加工工艺为:车削锻造毛坯→切齿(滚齿/插齿)→剃齿→渗碳淬火→磨齿,滚齿和磨齿工艺过程如图1所示。
齿轮毛坯为模锻而成;采用数控车床在一次装夹的条件下完成毛坯的外圆表面、内孔表面和端面的车削,保证齿坯具有较好的精度,为后序的高质量加工提供基础;采用滚齿的方法进行齿形的粗加工(滚齿机的加工精度为IT10~IT7级);剃齿一般应用于未进行淬火热处理齿轮齿形的精加工(精度可达IT7~IT6级),但是剃齿不能修正分齿误差,剃齿后的精度只能比剃齿前提高一级;汽车齿轮的工作任务比机床齿轮要繁重得多,因此在耐磨性、抗疲劳强度、心部强度和冲击韧性等方面的要求均比机床齿轮要高,选用渗碳钢制造并经渗碳热处理才能满足其性能要求;最后以磨削加工的方法对经过热处理的齿轮内孔、端面、轴的外径等部分进行精加工,进而提高尺寸精度和减小形位公差,磨削加工可达的经济精度为IT6~IT4级,表面粗糙度为Ra0.2~0.8μm。
珩磨作为一种特殊的磨削加工技术,是精加工中的一种高效加工方式,可以安排为最后加工工序,划分为光整加工阶段,具有加工精度高、表面质量好、加工效率高等特点,可将表面粗糙度降低到Ra0.20~0.05μm。
典型零件的加工工艺

图4-1
二、轴类零件的材料、毛坯和热处理
• 轴类零件的毛坯常用棒料和锻件。光滑轴、直径相差不大 的非重要阶梯轴宜选用棒料,一般比较重要的轴大都采用 锻件作为毛坯,只有某些大型的、结构复杂的轴采用铸件。 • 根据生产规模的不同,毛坯的锻造方式有自由锻和模锻两 种。中小批生产多采用自由锻,大批大量生产时通常采用 模锻。 • 45钢是轴类零件的常用材料,它价格便宜,经过调质(或 正火)后,可得到较好的切削性能,而且能够获得较高的 强度和韧性,淬火后表面硬度可达45~52HRC。 • 40Cr等合金结构钢适用于中等精度而转速较高的轴类零 件。这类钢经调质和淬火,具有较好的综合力学性能。
3.主轴的检验
• 主轴的最终检验要按一定顺序进 行,先检验各个外圆的尺寸精度、 素线平行度和圆度,再用外观比 较法检验各表面的粗糙度和表面 缺陷,最后再用专用检具检验各 表面之间的位置精度,这样可以 判明和排除不同性质误差之间对 测量精度的干扰。 • 检验前、后支承轴径对公共基准 的同轴度误差,通常采用如图4-6 所示的方法。 • C6150型车床主轴上其他各表面 相对于支承轴径位置精度的检验 常在图4-7所示的专用检具上进行。
6加工方法和加工设备的选择
More to learn
定位基准选择
(1)精基准的选择 精基准选择时应尽量符合“基准重合” 和“基准统一”原则,保证主要加工表面(主要轴径的支 承孔)的加工余量均匀,同时定位基面应形状简单、加工 方便,以保证定位质量和夹紧可靠。此外,精基准的选择 还与生产批量的大小有关。箱体零件典型的定位方案有两 种:
图4-11
(2)粗基准的选择 箱体零件加工面较多,粗基准选择时 主要考虑各加工面能否分配到合理的加工余量,以及加工 面与非加工面之间是否具有准确的相互位置关系。箱体零 件上一般有一个(或几个)主要的大孔,为了保证孔加工 的余量均匀,应以该毛坯孔作为粗基准。箱体零件上的不 加工面以内腔为主,它和加工面之间有一定的相互位置关 系。箱体中往往装有齿轮等传动件,它们与不加工的内壁 之间只有不大的间隙,如果加工出的轴承孔与内腔壁之间 的误差太大,就有可能使齿轮安装时与箱体壁相碰。从这 一要求出发,应选内壁为粗基准,但这将使夹具结构十分 复杂。考虑到铸造时内壁与主要孔都是由同一个泥芯浇铸 的,因此实际生产中常以孔为主要粗基准,限制4个自由 度,而辅之以内腔或其他毛坯孔为次要基准面,以实现完 全定位。
锥齿轮的工艺加工

锥齿轮的工艺加工摘要轴是组成机械的重要零件,也是机械加工中常见的典型零件之一。
它支撑着其它转动件回转并传递扭矩,同时又通过轴承与机器的机架连接。
但在职业学校机械加工实习课中,轴类零件的加工是学生练习车削技能的最基本也最重要的项目,但学生最后完工工件的质量总是很不理想,经过分析主要是学生对轴类零件的工艺分析工艺规程制订不够合理。
轴类零件中工艺规程的制订,直接关系到工件质量、劳动生产率和经济效益。
一零件可以有几种不同的加工方法,但只有某一种较合理,在制订机械加工工艺规程中,须注意以下几点。
1.零件图工艺分析中,需理解零件结构特点、精度、材质、热处理等技术要求,且要研究产品装配图,部件装配图及验收标准。
2.渗碳件加工工艺路线一般为:下料→锻造→正火→粗加工→半精加工→渗碳→去碳加工(对不需提高硬度部分)→淬火→车螺纹、钻孔或铣槽→粗磨→低温时效→半精磨→低温时效→精磨。
3.粗基准选择:有非加工表面,应选非加工表面作为粗基准。
对所有表面都需加工的铸件轴,根据加工余量最小表面找正。
且选择平整光滑表面,让开浇口处。
选牢固可靠表面为粗基准,同时,粗基准不可重复使用。
关键词:工艺分析;基准选择;工艺路线;粗糙度AbstractThe axis is composes the machinery the important components, also is in the machine-finishing one of common typical components.It supports other rotors to rotate and to transmit the torque, simultaneously through bearing and machine rack connection.But in the vocational school machine-finishing practicum, the axis class components processing is the student practices the turning skill the most basic also most important project, but the student finally finishes the work piece quality very not to be always ideal, the process analysis mainly is the student countershaft class components craft analysis technological process making insufficiently is reasonable.In the axis class components the technological process making, relates the work piece quality, the labor productivity and the economic efficiency ponents may have several different processing methods, but only then some one kind reasonable, in the making machine-finishing technological process, must pay attention to following several.1. detail drawing craft analysis, must understand components specifications and so on unique feature, precision, material quality, heat treatment, also need to study the product assembly drawing, the part assembly drawing and the approval standard.2. cementation processing craft route is generally: The yummy treats -> forging -> fire -> rough machining -> semi-finishing -> cementation -> decarbonization processing (to does not have to enhance degree of hardness part) -> the quenching -> cutting thread, the drill hole or the milling -> rough grinding -> low temperature effectiveness -> half correct grinding -> low temperature effectiveness -> correct grinding.3. thick datum choices: Has the non-processing surface, the elected non-processing surface takes the thick datum.Casting axis all must process which to all surfaces, adjusts according to the processing remainder smallest surface.Also the choice smooth smooth surface, makes way the runner place.Chooses the reliable reliable surface is the thick datum, simultaneously, the thick datum cannot duplicate uses.Keywords: Craft analysis;datum choice;craft route;roughness目录引言 (4)第一章零件的分析 (5)1.1 零件的作用 (5)1.2 零件的工艺分析 (7)第二章确定毛坯及加工余量 (12)第三章零件的工艺安排 (15)3.1 定位基准的选择 (15)3.2 制定工艺路线 (15)3.3 工艺装备的选择 (16)3.4 加工工序设计 (16)3.5 填写机械加工工序卡 (18)第四章数控加工程序 (20)参考文献 (22)致谢 (23)引言这次工艺学课程毕业设计是我们对所学各课程的一次深入的综合性的复习,也是一次理论联系实际的训练。
- 1、下载文档前请自行甄别文档内容的完整性,平台不提供额外的编辑、内容补充、找答案等附加服务。
- 2、"仅部分预览"的文档,不可在线预览部分如存在完整性等问题,可反馈申请退款(可完整预览的文档不适用该条件!)。
- 3、如文档侵犯您的权益,请联系客服反馈,我们会尽快为您处理(人工客服工作时间:9:00-18:30)。
齿标题轮加工工艺分析
(二)定位基准的确定 定位基准的精度对齿形加工精度有直接的影响。轴类齿
轮的齿形加工一般选择顶尖孔定位,某些大模数的轴类齿轮 多选择齿轮轴颈和一端面定位。盘套类齿轮的齿形加工常采 用两种定位基准。
1)内孔和端面定位 选择既是设计基准又是测量和装 配基准的内孔作为定位基准,既符合“基准重合”原则,又 能使齿形加工等工序基准统一,只要严格控制内孔精度,在 专用芯轴上定位时不需要找正。故生产率高,广泛用于成批 生产中。
(3)辅助基准 有些工件为了装夹方便、定位稳定或易于实现基
准统一,常常人为地造成一种定位基准,这种基准就是辅 助基准。如凸台、中心孔等。
标现题场常用工艺文件---机加工序卡片
现标题场常用工艺文件---可视化工艺
现标题场常用工艺文件---可视化工艺
齿标题轮加工工艺分析
圆柱齿轮加工工艺过程常因齿轮的结构形状、精度等级 、生产批量及生产条件不同而采用不同的工艺方案。下面列出 两个材料、结构、精度要求不同的齿轮典型工艺过程供分析比 较。 一、双联齿轮加工
14 剃齿(z=28),采用螺旋角度为5°的剃
齿刀,剃齿后公法线长度至尺寸上限
16 齿部高频淬火:G52
17 推孔
18 珩齿
19 总检入库
定位基准 花键孔及A 面 花键孔及A 面
花键孔及A 面
花键孔及A 面
齿标题轮加工工艺分析
从表中可见,齿轮加工工艺过程大致要经过如下五个 阶段:
材料制备——齿坯加工——齿形加工——热处 理——精基准修正及齿形精加工
工艺分析
(一)工艺过程分析 右图所示为
一双联齿轮,材料 为40Cr,精度为 7级。
齿标题轮加工工艺分析
齿号
Ⅰ
Ⅱ
齿号
Ⅰ
Ⅱ
模数
2
2 基节偏差 ±0.016 ±0.016
齿数
28
42 齿形公差 0.017 0.018
精度等级
公法线长 度变动量 齿圈径向
跳动
7GK 0.039 0.050
7JL 齿向公差 0.017 0.017
0.024
公法线平 21.36 均长度 -0.05
27.60 -0.05
0.042 跨齿数
4
5
齿标题轮加工工艺分析
表1-1 双联齿轮加工工艺过程
序号
工序内容
定位基准
1 毛坯锻造
外圆及端面
2 正火
3 粗车外圆及端面,留余量1.5~2mm 外圆及端面
4 钻、车花键底孔至尺寸φ30H12
外圆及A面
5 拉花键孔
齿标题轮加工工艺分析
加工的第四阶段是热处理阶段。 在这个阶段中主要对齿面的淬火处理,使齿面达到规定
的硬度要求。 加工的最后阶段是齿形的精加工阶段。
这个阶段的目的,在于修正齿轮经过淬火后所引起的齿 形变形,进一步提高齿形精度和降低表面粗糙度,使之达到 最终的精度要求。在这个阶段中首先应对定位基准面(孔和 端面)进行修整,因淬火以后齿轮的内孔和端面均会产生变 形,如果在淬火后直接采用这样的孔和端面作为基准进行齿 形精加工,是很难达到齿轮精度的要求的。以修整过的基准 面定位进行齿形精加工,可以使定位准确可靠,余量分布也 比较均匀,以便达到精加工的目的。
按照标准格式和要求编制工艺文件。
相标题关概念
1. 基准及其分类 (1)设计基准
在设计图样上所采用的基准,称为设计基准。 (2)工艺基准
可以分为装配基准、测量基准、定位基准及工序基准。 2. 定位基准的选择
定位基准分为粗基准、精基准和辅助基准等。 (1)粗基准的选择原则
1)余量均匀原则 2)保证不加工面位置正确的原则 3)粗基准平整光洁,定位可靠原则。 4)粗基准只能有效使用一次原则
相标题关概念
(2)精基准的选择原则 主要应考虑减少定位误差和装夹方 便。 1)基准重合原则。选用设计基准作为定位基准。 2)基准统一原则。选用统一的定位基准加工各表面。 3)自为基准原则。有些零件的精加工工序,要求余量小 而均匀,可用加工表面本身作为精基准。 4)互为基准,反复加工的原则。 对于精密零件,如齿轮加工有时还先以齿圈为基 准磨内孔,再以内孔为基准磨齿圈,齿圈与内孔互为 基准,反复加工。
孔及A面
6 钳工去毛刺
花键孔及A面
7 上芯轴,精车外圆,端面及槽至要求 花键孔及A面
工序内容
9 滚齿(z=42),留剃余量0.07~0.10 mm
10 插齿(z=28),留剃余量0.04~0.06 mm
11 倒角(Ⅰ、Ⅱ齿12°牙角)
12 钳工去毛刺
13 剃齿(z=42),公法线长度至尺寸上限
标题
标题
标题
标题
标题
相标题关概念
影响毛坯选择的因素是:生产规模的大小;工件结构 形状和尺寸;零件的力学性能要求;本厂现有设备和技术 水平。 3、拟定工艺过程
包括划分工艺过程的组成、选择定位基准、选择零件 表面的加工方法、安排加工顺序和组合工序等。 4、工艺设计
包括选择机床和工艺装备,确定加工余量、计算工序 尺寸及其公差,确定切削用量及计算工时定额等。 5、编制工艺文件
齿坯加工必须保证基准面精度 热处理直接决定轮齿的内在质量 齿形加工和热处理后精加工是制造的关键,也反映 齿轮制造水平。
材料制备直接影响齿轮的可靠性和成本,它是齿轮 加工第一阶段
齿标题轮加工工艺分析
加工的第二阶段是齿坯最初进入机械加工的阶段。 由于齿轮的传动精度主要决定于齿形精度和齿距分布均匀 性,而这与切齿时采用的定位基准(孔和端面)的精度有着直 接的关系,所以,这个阶段主要是为下一阶段加工齿形准备精 基准,使齿的内孔和端面的精度基本达到规定的技术要求。在 这个阶段中除了加工出基准外,对于齿形以外的次要表面的加 工,也应尽量在这一阶段的后期加以完成 第三阶段是齿形的加工。 对于不需要淬火的齿轮,一般来说这个阶段也就是齿轮的 最后加工阶段,经过这个阶段就应当加工出完全符合图样要求 的齿轮来。对于需要淬硬的齿轮,必须在这个阶段中加工出能 满足齿形的最后精加工所要求的齿形精度,所以这个阶段的加 工是保证齿轮加工精度的关键阶段。应予以特别注意。
2)外圆和端面定位 齿坯内孔在通用芯轴上安装,用 找正外圆来决定孔中心位置,故要求齿坯外圆对内孔的径向 跳动要小。因找正效率低,一般用于单件小批生产。
齿标题轮加工工艺分析
(三)齿端加工 如图1-2 所示,齿轮的齿端加工有倒圆、倒尖、倒棱,