转炉冶炼出钢挡渣
转炉挡渣出钢

转炉挡渣出钢——让钢水更“洁净”随着我国国民经济的发展,对钢材的消费结构正在发生变化,加之众多企业日益关注转炉生产特殊钢,这些都对低成本生产高洁净度钢水提出了越来越高的要求。
就转炉炼钢生产企业而言,为生产IF钢(超低碳钢)、石油管线钢、硅钢、轴承钢、弹簧钢等高附加值产品,减少转炉出钢时的下渣量是提高钢水洁净度,从而提高转炉钢产品的质量和档次,降低其生产成本最有效的途径。
有效挡渣亟待引起高度重视有效防止钢水回磷、回硫。
在转炉出钢时采取有效的挡渣操作,是改善钢水质量的重要举措,既可以减少钢水回磷、回硫,提高合金收得率,减少钢水中夹杂物,提高钢水洁净度,还可为后续精炼创造条件。
当在精炼过程进行造渣脱硫时,因钢水钢渣中含有10%~13%的SiO2和0.8%~1.0%的P2O5,钢水极易发生回硫和回磷现象,导致钢水成分超标形成废品。
减少脱氧剂及合金消耗。
在转炉出钢时采取有效的挡渣操作,不仅可以减少脱氧剂及合金消耗,减少钢包粘渣,延长钢包使用寿命,还可提高转炉出钢口区域耐材的使用寿命,降低炼钢产品的生产成本。
转炉出钢后钢包的钢渣成分与终渣成分基本一致。
若转炉出钢时挡渣效果不好,将导致钢包钢渣量加大。
如果钢水精炼过程中不对钢渣进行脱氧改性,则精炼后钢渣中的氧会扩散到钢中,造成钢中成分烧损,导致成分变差;或在钢中形成新的夹杂物,污染钢水使其质量恶化。
当对钢渣进行脱氧改性时,较大的顶渣量会消耗大量脱氧剂。
钢包钢渣中FeO含量通常为1O%~17%(平均按13%计算),钢水精炼时,以使用铝脱氧剂为例,每100公斤顶渣消耗的铝脱氧剂为3.8公斤。
对于每天产钢100炉的炼钢厂,如果每炉出钢少出200公斤渣,则每年可节省脱氧剂消耗440万元。
挡渣塞成为挡渣产品主流多年来,国内外众多冶金工作者研究开发将钢渣进入量降到最低的技术和方法,除少渣、无渣冶炼工艺外,主要开发了各种挡渣技术和产品,以尽量减少转炉出钢后期涡流带出的钢渣量。
浅谈转炉滑板挡渣出钢技术

来越高的要求。就转炉炼钢生产企业而言 ,为 生产 I F钢( 超低碳钢) 、石油管线钢、硅钢 、轴承钢、弹簧钢等高附加值产 品,减少 转炉出钢 时的下渣量是提高钢水 洁净庹 ,从而提高转炉钢产 品的质量和档次 ,降低其 生产成本最有效 的途径 。
暑 棼
一
转 炉 挡 渣 出 钢 技 术 方 法
一
绪 的正 向变 化 ,对于学生 的缺点 和不 足 ,最好不直接提 出批评 ,而采用 正面提 出要求为好 ,这样做 ,有利于防止负面作用的产生 ,避免产生消极影 响。 作为一名语 文教师 ,应迅速抓住学生 思想行为 ,充分暴露的有利时机 ,因 势利导 ,引导学生正确地看待成 功与失 败 、长处与短处 、顺利与挫折 ,激励他 们 勇于战胜困难 ,克服不健康 的心理障碍 ,提高 自尊心 和自信心 ;培养学生 良 好 的心理调节能力 ;促使学 生经过失败 ,保持稳定 的情绪 、乐观 的心境 ,这样 ,即使在逆境中也能成才。 总而言之 ,建立教育 “ 情感场” ,营造积极健康的学习环境是优化课堂教学 的良药。包含真情 的语文教 师一定深受学生的喜爱 。学生喜欢在充 满爱和愉快 的环境 中成长 , 世间没有真正不需要友爱和感情 的学生。 于漪有一句 口头禅 : “ 教 师 的天职就是爱学生 。 ”⑤夏丐尊说 :没有情感 ,没有爱 ,就没有教育。的确如 此 ,语 文教 师只有全身心地投 入,在教学中渗透情感教育 ,才能上好 每一节语 文课 , 从而成 为优 秀的语文教 师。
转炉挡渣 出钢 “ 提质降耗” 滑动水 口及机构操作和评 判人员水平也提 出更苛刻 的要求 。因此 ,应针对不同 在转炉炼钢生产 中 ,炉内冶炼时产生 大量熔融状态 的炉渣 。这些炉渣会随 钢企 客户的实际炼钢环境 和滑板寿命 需求进行成本测算 ,综合权衡 性价比和利 着 转炉的 出钢 流人 钢包中 ,进而影响钢包 耐火材料的寿命 ;造 成钢水 回硫 、回 润 空间,选用合适 的材质 。 磷 ,影响钢水质量 ;增加炉后铁合金 的消耗 ,增加后续工 序合 成渣的用量 ,延 此外 ,市场上亦出现过 少量 重烧镁碳质 、低温烧成铝碳质 、中温烧 结尖晶 长精炼工序处理 时间。f 习此 ,在转炉 出钢 时 ,应采用挡渣 出钢 技术以严格控制 石碳 质等出钢 口滑板 。然 而这几种材质均非市场主流 ,且对转 炉炼 钢环境均存 转 炉的下渣量。 在较 大不适应性 。
转炉炼钢挡渣工艺简介
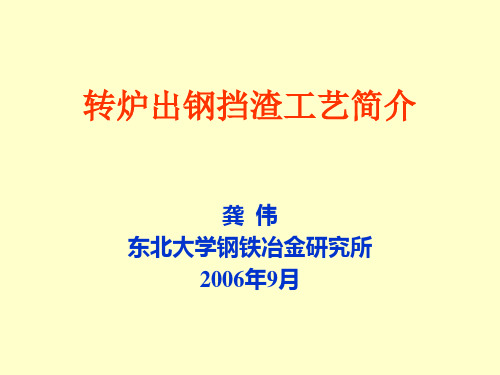
龚 伟 东北大学钢铁冶金研究所 2006年9月 年 月
转炉出钢挡渣的必要性
可以减少钢水回磷,提高合金收得率 可以减少钢水回磷 提高合金收得率; 提高合金收得率 减少钢中夹杂物,提高钢水清洁度 提高钢水清洁度; 减少钢中夹杂物 提高钢水清洁度 可以减少钢包粘渣,提高钢包包龄 提高钢包包龄; 可以减少钢包粘渣 提高钢包包龄 同时可减少耐材消耗; 同时可减少耐材消耗 也可为钢水精炼提供良好的条件。 也可为钢水精炼提供良好的条件。
挡渣塞法
该装置呈陀螺形,粗端有 3个凹槽、6个棱角,能够 破坏钢水涡流,减少涡流 卷渣。其比重与挡渣球 相近,在4.5 ~ 4.7 g/cm3之 间,能浮于钢渣界面,伴随 着出钢过程,逐渐堵住出 钢口,实现抑制涡流和挡 渣的作用。
能抑制涡流的挡渣塞
挡渣料法
• 原理:此法也称硬吹或干渣吹炼法。 原理:此法也称硬吹或干渣吹炼法。 它是在吹炼结束时喷射一种固态混合 提高渣稠度,使渣局部或全部凝固 物,提高渣稠度 使渣局部或全部凝固 提高渣稠度 使渣局部或全部凝固, 以改变渣的流动性来挡渣;或在出钢 以改变渣的流动性来挡渣 或在出钢 口上部渣面投入粒状耐火材料,形成 口上部渣面投入粒状耐火材料 形成 块状堵塞物,防止渣流出 防止渣流出。 块状堵塞物 防止渣流出。
挡渣棒法
• 1983年日新制钢研究成功挡渣棒法。 • 挡渣棒吊在支臂上在炉内可以自由移动, 在即将出完钢时从转炉内部将出钢口塞 住,以挡住炉渣,如再配以荷重器、高频电 流信号,效果更佳。该装置操作与维护较 复杂。
其他Байду номын сангаас法
• • • • 出钢口吹气干扰涡流法 转动悬壁法 挡渣罐挡渣法 均流出钢口法
带保护外壳的红外摄像仪
转炉出钢挡渣改进生产实践

阳春新钢铁有限责任公司,广东阳春 529600摘要:转炉挡渣工艺是高洁净钢生产工艺中重要的一环, 挡渣效果不好会直接造成钢水杂质含量高、回磷量大成分出格、后续精炼处理难度增加、钢铁料消耗高等问题,影响钢水质量。
本文结合目前实际挡渣情况进一步探索研究影响转炉挡渣合格率的因素,制订相应对策,提高挡渣合格率,减少转炉出钢下渣量,从而达到改善钢水质量、减少废品的目的。
关键词:转炉、挡渣、高挡渣率1 前言随着我国国民经济的发展,钢材的消费结构正在不断地发生变化,对钢水的洁净度提出了越来越高的要求。
在实际生产中,要求转炉在出钢过程中最大限度地减少下渣量、降低钢水的氧化性及提高炉外精炼的冶金效果,相对于成本较高的精炼过程,转炉挡渣出钢是生产低成本洁净钢的最简单有效途径[1]。
国内某炼钢厂(120吨转炉)2021年5-12月平均挡渣合格率95.6%(下渣≤50mm炉数占比),平均每月因下渣导致磷超国标判废2炉,每炉重量180吨,每月360吨,吨钢加工费用500元,平均每月因成分出格损失18万元。
2 挡渣塞挡渣原理现在国内钢厂转炉挡渣法有挡渣球法,挡渣塞法,气动挡渣,滑板挡渣法,各有利弊[2]。
某炼钢厂采用挡渣塞法挡渣,具有操作简便,使用成本低等优点。
挡渣塞呈陀螺形,粗端有4个凹槽、8个棱角,能够破坏钢水涡流,减少涡流卷渣。
其比重在3.4~ 4.0 g/cm3之间,能浮于钢渣界面,出钢时用专用机械将挡渣塞吊置出钢口上方,缓缓加到钢水面上,随钢水流尽,挡渣塞能堵住出钢口而阻挡炉渣流出,实现抑制涡流和挡渣的作用。
挡渣塞简图及挡渣原理见图1。
图1挡渣塞简图及挡渣原理3 分析影响挡渣成功的因素根据挡渣塞挡渣原理、相关文献及现场生产实践,分析影响挡渣合格率的因素有:1、挡渣塞的工艺参数,如比重、形状、流钢槽的数量、宽度、形状等;2、挡渣塞耐材质量的稳定性,是否受潮,在出钢时是否炸裂;3、挡渣塞的制作质量:挡渣塞整套装置是由挡渣塞,导向杆组成,在使用时将导向杆套在挡渣塞上,出钢至1/2∽2/3时通过挡渣塞投放装置,对准出钢口,插入钢水中,当导向杆卡子松动、衔接不紧密在加挡渣塞时导向杆易掉落、熔化与出钢口定位不准;4、出钢口的形状,当出钢口内口有钢渣堆积时会呈现不规则形状,与挡渣塞配合存在间隙,有漏渣的风险;5、加挡渣塞的时机,挡渣时出钢口的角度与夹持机构上挡渣棒的位置配合不好,加挡渣塞过早或过晚都会影响挡渣效果;6、转炉炉型的控制,出钢口周边及炉帽的日常维护做好有利于挡渣率的提高。
【技术】典型的转炉挡渣方法
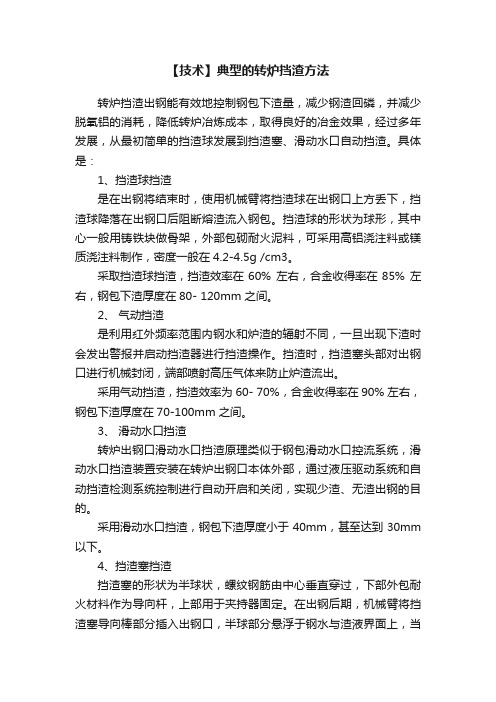
【技术】典型的转炉挡渣方法转炉挡渣出钢能有效地控制钢包下渣量,减少钢渣回磷,并减少脱氧铝的消耗,降低转炉冶炼成本,取得良好的冶金效果,经过多年发展,从最初简单的挡渣球发展到挡渣塞、滑动水口自动挡渣。
具体是:1、挡渣球挡渣是在出钢将结束时,使用机械臂将挡渣球在出钢口上方丢下,挡渣球降落在出钢口后阻断熔渣流入钢包。
挡渣球的形状为球形,其中心一般用铸铁块做骨架,外部包砌耐火泥料,可采用高铝浇注料或镁质浇注料制作,密度一般在4.2-4.5g /cm3。
采取挡渣球挡渣,挡渣效率在60% 左右,合金收得率在85% 左右,钢包下渣厚度在80- 120mm 之间。
2、气动挡渣是利用红外频率范围内钢水和炉渣的辐射不同,一旦出现下渣时会发出警报并启动挡渣器进行挡渣操作。
挡渣时,挡渣塞头部对出钢口进行机械封闭,端部喷射高压气体来防止炉渣流出。
采用气动挡渣,挡渣效率为60- 70%,合金收得率在90% 左右,钢包下渣厚度在70-100mm 之间。
3、滑动水口挡渣转炉出钢口滑动水口挡渣原理类似于钢包滑动水口控流系统,滑动水口挡渣装置安装在转炉出钢口本体外部,通过液压驱动系统和自动挡渣检测系统控制进行自动开启和关闭,实现少渣、无渣出钢的目的。
采用滑动水口挡渣,钢包下渣厚度小于40mm,甚至达到30mm 以下。
4、挡渣塞挡渣挡渣塞的形状为半球状,螺纹钢筋由中心垂直穿过,下部外包耐火材料作为导向杆,上部用于夹持器固定。
在出钢后期,机械臂将挡渣塞导向棒部分插入出钢口,半球部分悬浮于钢水与渣液界面上,当钢水流尽时,半球形部分适时堵住出钢口,从而防止熔渣流入钢包。
因半球体上有导流槽,可以抑制钢水发生涡流卷渣,当挡渣塞本体堵住出钢口后,残钢仍能通过导流槽流至钢包,故提高了钢水收得率。
采用挡渣塞工艺,挡渣效率可以达到90%以上,合金收得率可以达到95% 以上,钢包下渣厚度在40- 70mm 之间。
氧气顶吹转炉炼钢挡渣出钢
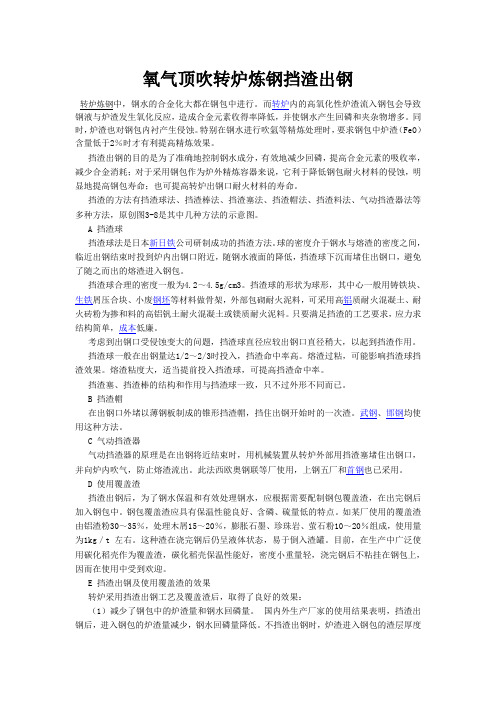
氧气顶吹转炉炼钢挡渣出钢转炉炼钢中,钢水的合金化大都在钢包中进行。
而转炉内的高氧化性炉渣流入钢包会导致钢液与炉渣发生氧化反应,造成合金元素收得率降低,并使钢水产生回磷和夹杂物增多。
同时,炉渣也对钢包内衬产生侵蚀。
特别在钢水进行吹氩等精炼处理时,要求钢包中炉渣(FeO)含量低于2%时才有利提高精炼效果。
挡渣出钢的目的是为了准确地控制钢水成分,有效地减少回磷,提高合金元素的吸收率,减少合金消耗;对于采用钢包作为炉外精炼容器来说,它利于降低钢包耐火材料的侵蚀,明显地提高钢包寿命;也可提高转炉出钢口耐火材料的寿命。
挡渣的方法有挡渣球法、挡渣棒法、挡渣塞法、挡渣帽法、挡渣料法、气动挡渣器法等多种方法,原创图3-8是其中几种方法的示意图。
A 挡渣球挡渣球法是日本新日铁公司研制成功的挡渣方法。
球的密度介于钢水与熔渣的密度之间,临近出钢结束时投到炉内出钢口附近,随钢水液面的降低,挡渣球下沉而堵住出钢口,避免了随之而出的熔渣进入钢包。
挡渣球合理的密度一般为4.2~4.5g/cm3。
挡渣球的形状为球形,其中心一般用铸铁块、生铁屑压合块、小废钢坯等材料做骨架,外部包砌耐火泥料,可采用高铝质耐火混凝土、耐火砖粉为掺和料的高铝钒土耐火混凝土或镁质耐火泥料。
只要满足挡渣的工艺要求,应力求结构简单,成本低廉。
考虑到出钢口受侵蚀变大的问题,挡渣球直径应较出钢口直径稍大,以起到挡渣作用。
挡渣球一般在出钢量达1/2~2/3时投入,挡渣命中率高。
熔渣过粘,可能影响挡渣球挡渣效果。
熔渣粘度大,适当提前投入挡渣球,可提高挡渣命中率。
挡渣塞、挡渣棒的结构和作用与挡渣球一致,只不过外形不同而已。
B 挡渣帽在出钢口外堵以薄钢板制成的锥形挡渣帽,挡住出钢开始时的一次渣。
武钢、邯钢均使用这种方法。
C 气动挡渣器气动挡渣器的原理是在出钢将近结束时,用机械装置从转炉外部用挡渣塞堵住出钢口,并向炉内吹气,防止熔渣流出。
此法西欧奥钢联等厂使用,上钢五厂和首钢也已采用。
转炉挡渣出钢技术应用
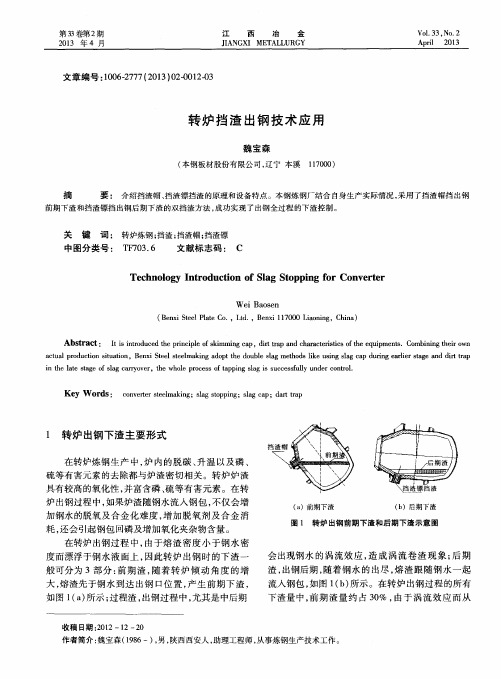
Ke y Wo r d s: c o n v e  ̄e r s t e e l ma k i n g ;s l a g s t o p p i n g ;s l a g c a p;d a r t t r a p
1 转炉 出钢下渣主要形式
在转 炉炼 钢 生 产 中 , 炉 内的 脱 碳 、 升 温 以及 磷 、 硫等 有害 元素 的去 除都 与炉 渣密 切相 关 。转 炉 炉 渣 具有较 高 的氧化 性 , 并 富含磷 、 硫 等有 害 元 素 。在转 炉 出钢过 程 中 , 如果 炉渣 随 钢水 流入 钢包 , 不 仅 会 增 加钢 水 的脱 氧及 合 金 化难 度 , 增 加 脱 氧 剂及 合 金 消 耗, 还会 引起 钢包 回磷及 增 加氧 化夹 杂物 含量 。 在转 炉 出钢过 程 中 , 由于 熔 渣 密 度 小 于 钢 水 密
位置时, 打 开滑 动水 口 , 进行 出钢 操作 。此 法 能较 好 地 解 决挡 渣帽 挡 渣法 存 在 的摩 擦 力 不 足 等 问题 , 实 现 了对 出钢 前期 下 渣 的有效控 制 。
2 . 2 出钢 过程 中涡 流卷 渣 的控 制
2 挡渣 工艺介绍
为 了有针 对性 地 控 制 不 同 阶段 的 下 渣 , 本 钢 炼 钢厂 1 8 0 t 转 炉生 产采 用 双挡 渣法 工艺 , 即采 用挡 渣 帽挡 出钢 开始 时 的前 期 下 渣 , 再 用 挡 渣 镖 挡 出 钢 快 结 束 时 的后期 下 渣 。 这 两种 挡 渣 方 法 综 合 使 用 , 使 挡渣 效果 明显 提 高 , 出钢 后 钢 包 渣 厚 一 般 可 控 制 在 8 0— 9 0 m m, 有 效 降 低 了钢 水 回磷 并 为 精 炼 处 理 等 后 续工 序 创造 了 良好条 件 。 2 . 1 转 炉 出钢 前期 的挡 渣 技术 转 炉 出钢前 期 , 由于熔 渣密 度小 于钢 水 密度 , 熔 渣 漂 浮于 钢水 之 上 , 随着 出钢 时 摇 炉 角 度 的逐 渐 增 大, 熔渣 会 先于 钢水 到达 出钢 口区域 进 入 钢包 , 造成 下 渣危 害 。针 对这 情 况 , 本 钢 炼 钢 厂 采 用 挡 渣 帽 挡 渣 法 阻挡这 部分 渣 进入 钢包 。该 法是 在 出钢 前用 钢
转炉冶炼出钢挡渣

出钢挡渣随着用户对钢材质量要求的日益提高,需要不断提高钢水质量。
减少转炉出钢时的下渣量是改善钢水质量的一个重要方面。
在转炉出钢过程中进行有效的挡渣操作,不仅可以减少钢水回磷,提高合金收得率,还能减少钢中夹杂物,提高钢水清洁度,并可减少钢包粘渣,延长钢包使用寿命。
与此同时亦可减少耐材消耗,相应提高转炉出钢口耐火材料的使用寿命,还可为钢水精炼提供良好的条件。
转炉吹炼结束向盛钢桶(钢包)内放出钢水而把氧化渣留在炉内的操作。
出钢时使氧化性渣和钢水分离是炉外精炼的要求。
钢包内的二次精炼适于在还原条件下进行。
采用挡渣出钢,避免出钢带渣对提高炉外精炼效果是重要保证。
出钢时,随着钢水面的下降,当钢水深度低于某一临界值时,在出钢口上方会形成漏斗状的汇流旋涡,部分渣子在钢水出完以前就由出钢口流出,这是渣、钢分离不清的根本原因。
另外摇炉过快,有部分渣子由炉口涌出;但这可通过细心操作而避免。
挡渣出钢技术主要是针对汇流旋涡下渣而开发的。
有挡渣球、挡渣塞、高压气挡渣、挡渣阀门、下渣信号检测等各种方法。
挡渣球挡渣球由耐火材料包裹在铁芯外面制成,其密度大于炉渣而小于钢水,因而能浮在渣钢界面处。
出钢时,当钢水已倾出3/4~4/5时,用特定工具伸入炉内将挡渣球放置于出钢口上方。
钢水临近出完时,旋涡将其推向出钢口,将出钢口堵住而阻挡渣子流出。
(图1)为了提高挡渣球的抗急冷急热性能,提高挡渣效率,又研制了石灰质挡渣球。
先在铁芯外包一层耐火纤维,用于起缓冲作用;球的外壳以白云石、石灰等作原料,用合成树脂或沥青等作黏接剂制造。
挡渣球法成功的关键:一是球的密度恰当,即4.3~4.4g/cm3;二是出钢口维护好,保持圆形;三是放置球的位置对准出钢口。
但由于挡渣球的体形,极易随钢流飘浮而离开出钢口,从而失去挡渣作用。
挡渣出钢挡渣塞将挡渣物制成上为倒锥体下为棒状的塞(图2a)。
由于其形状接近于漏斗形,可配合出钢时的钢水流,故比挡渣球效率高。
有的在挡渣塞上部锥体增加小圆槽而下部改为六角锥形(图2b),以增加抑制旋涡的能力。
转炉炼钢挡渣工艺的应用及效益

为 提 高转 炉 挡渣 效 果 . 国内外 在 挡 渣技 术 方 面 进 行 了深 入研 究 。 自 17 9 0年 日本 发 明挡渣 球 挡 渣 出钢 以来 , 国 为 完善 挡 渣 技 术 . 明 了 十 几 种 挡 各 发 渣 方法 。挡 渣 出钢 的方法 有 :1 出钢前期 挡渣 ;2 () ()
2挡 渣 工 艺 和 挡 渣 设 备 的 选 择
21挡 渣 出钢的 必要 性 .
转 炉炼 钢 中 ,钢水 的合 金 化 大 都 在 钢包 中 进
行 , 转 炉 内 的高 氧化 性渣 流 入钢 包 会 导致 钢 液 与 而
它采 用 电子示 渣 器对 钢 流监 测 . 根 据检 测 信 号用 并
气 动装置 将耐 火材料 塞 子封堵 出钢 口 挡 渣设 备处 于 炉 口极 为 恶劣 的高 温 状 态 下 . 于 损 坏 . 便 维 易 不
钢 渣 发生 氧化 反 应 ,造 成 合金 元 素收 得 率 降低 。 并
使 钢水 产 生 回磷 和夹 杂 物增 多 。同时 . 炉渣 也 对 钢 包 内衬 产 生侵 蚀 , 别在 钢 水进 行 吹 氩 等精 炼 处 理 特 时 ,要 求钢 包 中炉 渣 F O重量 低 于 2 e %时才 有利 于 提高 精炼 效果
钢 包 中的渣 量 )
出钢后 期 挡 渣 的方 法 有 : 1 ( )气 动 挡渣 ; 2 滑 ()
板 法挡渣 ( 称液 压挡 渣 闸) 也 。
出钢 后挡 渣有 : 挡渣 罐挡 渣法 。 另外 , 有 一 些 挡 渣方 法 , : 孔 出 钢 法 、 还 如 三 真 空 吸渣法 、 动撇渣 法 、 气 扒渣法 等 , 未能 广泛应 用 。 目前 常用 的挡 渣 出钢 法 是 ( ) 1 耐材 制 品 挡 渣 ; () 2 气动挡 渣 ;3 液 压挡 渣 闸挡渣 。 () 气动挡渣是 8 0年 代 中期 奥 钢 联 开 发 成 功 的
转炉的挡渣出钢技术探讨

Ma L 2 01 3
冶
金
能
源
l 3
E NE RG Y F OR ME TA I 上UR GI C AL I NDUS T R Y
转 炉 的挡 渣 出钢 技 术 探 讨
魏 宝森
( 本钢板 材股份 有 限公 司 )
摘 要 简述了转炉出钢 下渣 的危害 ,结合本钢 炼钢厂生 产实践 ,有 针对性 的提 出具 体的控
增大 , 熔渣先于钢水到达出钢 口位置 ,产生前期 下渣;过程渣 ,出钢过程中,尤其是中后期会出
现 钢水 的 涡 旋 效 应 ,造成 涡 流 卷 渣 现 象 ;后 期
在转炉炼钢生产中 ,炉内的脱碳、升温以及 磷、硫等有害元素的去除都与炉渣密切相关。转 炉炉渣具有较高的氧化性 ,并富含磷、硫等对钢 水质量有害的元素。在转炉出钢过程中,如果炉
渣随 钢水一 并流人 钢包 ,不 仅会 增加钢 水 的脱 氧
收稿 日期 : 2 0 1 2—1 0— 2 9 魏宝森 ( 1 9 8 6一 ) , 助理工程师 ; 1 1 7 0 0 0 辽宁省本溪市。
渣 ,出钢后期 ,随着钢水的出尽 , 熔渣随钢水一 并 流人钢 包 。在 整 个 转 炉 出钢 过 程 的下 渣 量 中 , 前期渣量 大体 占 3 0 % ,涡流效应从钢水表面带 下的渣量约为 3 0 % ,后期渣约为4 0 %D J 。
t h e s t e e l s l g a c o n t r o 1 .
Ke y wo r d s c o n v e r t e r s l g — a — s t o p p i n g s l a g— — s t o p p i n g c a p s l a g— — s t o p p i n g d a r t
转炉滑动水口挡渣出钢工艺的研发与应用

转炉滑动水口挡渣出钢工艺的研发与应用福建三钢闽光股份有限公司一炼钢系统(以下简称三钢)拥有100吨转炉两座、LF炉两座、6机6流小方坯机组一台、板坯连铸机两台。
随着三钢产品结构的不断优化调整,转炉钢水的纯净度已经成为部分品种钢开发的限制因素,而如何控制和减少转炉出钢过程中的下渣量是提高钢水纯净度的一个重要环节。
有效的挡渣操作,不仅改善钢水质量、减少钢水回磷、降低钢中夹杂物含量、提高合金的收得率、降低生产成本,而且还可为钢水精炼提供良好的条件。
为此,三钢提出了利用滑动水口结合下渣自动检测的挡渣技术,提高挡渣的成功率,控制下渣量,并用于生产实践。
经过多次改进,目前控渣效果良好。
工作原理分析转炉滑动水口挡渣的工作原理是:在转炉出钢口末端设计闸阀系统,与自动下渣检测系统相结合,通过执行系统,采用液压控制的方式开启或关闭闸板,通过上下闸板之间流钢孔的错位实现挡渣的目的。
挡渣系统由检测、控制和挡渣3部分组成。
在转炉出钢口末端安装滑动水口系统,通过自动下渣检测系统来控制液压滑动水口快速开启或关闭,达到挡渣的目的。
附图所示为挡渣系统示意图。
挡渣系统通过离线安装机构卸载或安装滑板和内水口,检测机构内部的安全性,降低劳动强度,提高机构的使用安全。
新更换滑板机构离线安装后,要在上滑板与内水口接触面涂抹火泥和防黏剂,避免内水口的凸台黏结冷钢,以及清理冷钢过程中的凸台剥落影响安全使用。
技术开发的主要内容挡渣闸阀设计。
三钢采用轮式滑动框的门式机构,主要特点是:闸阀机构在线整体更换,离线更换机构闸板砖及检修调试,减轻劳动强度,缩短更换时间。
工作原理是通过水冷油缸推动轮式滑动框,开启或关闭下闸板,达到出钢和挡渣目的。
由于闸阀机构要能够承受高温烘烤且不易变形,机构本体应选择抗氧化、耐热性较好的钢件。
耐材材质与寿命选用。
耐火材料是转炉出钢口闸阀系统中的关键性材料,其材质的合理选定是出钢口闸阀系统安全使用的重要保证。
出钢口闸阀机构用的耐火材料由出钢口砖、内水口砖、内闸板砖、外闸板砖和外水口砖5块砖组成,同时砖与砖间采用凹凸连接方式。
浅谈转炉滑板挡渣出钢技术

浅谈转炉滑板挡渣出钢技术随着我国国民经济的发展,对钢材的消费结构正在发生变化,加之众多企业日益关注转炉生产特殊钢,这些都对低成本生产高洁净度钢水提出了越来越高的要求。
就转炉炼钢生产企业而言,为生产IF钢(超低碳钢)、石油管线钢、硅钢、轴承钢、弹簧钢等高附加值产品,减少转炉出钢时的下渣量是提高钢水洁净度,从而提高转炉钢产品的质量和档次,降低其生产成本最有效的途径。
转炉挡渣出钢技术方法一、转炉挡渣出钢“提质降耗”在转炉炼钢生产中,炉内冶炼时产生大量熔融状态的炉渣。
这些炉渣会随着转炉的出钢流入钢包中,进而影响钢包耐火材料的寿命;造成钢水回硫、回磷,影响钢水质量;增加炉后铁合金的消耗,增加后续工序合成渣的用量,延长精炼工序处理时间。
因此,在转炉出钢时,应采用挡渣出钢技术以严格控制转炉的下渣量。
自1970年日本新日铁发明了挡渣球以来,为了提高转炉出钢过程的挡渣效果,减少下渣量,国内外有关工作者在挡渣技术方面进行了大量的探索,相继发明了挡渣球法、挡渣塞法、挡渣料法、滑板法、气动挡渣法、出钢口吹气干扰涡流法等几十种挡渣方法,并结合炼钢生产实际情况不断加以改进,挡渣效果逐渐优化。
实践证明,转炉出钢口滑动水口挡渣技术以机械或液压方式开启或关闭出钢口,以达到挡渣目的,可以有效控制前期和后期下渣,挡渣成功率可以达到100%,相对其他挡渣技术,挡渣效果最优。
二、转炉出钢口滑动水口应合理选材转炉出钢口内水口:铝锆碳质性能较优。
考虑到转炉的特殊冶炼环境,目前市场上转炉出钢口内水口材质主要以不烧镁碳质为主,其成分大体类似于转炉出钢口砖,其使用寿命在30炉~80炉。
已有科研工作者开始尝试研究镶嵌氧化锆复合内水口,其使用寿命有望达到120炉以上,甚至与转炉出钢口耐火砖同步。
有研究曾将不烧铝锆碳材质的内水口与不烧镁碳材质的内水口在某钢企120吨转炉进行使用对比,结果发现相同使用寿命的情况下,铝锆碳质内水口使用效果明显好于镁碳质的内水口,主要表现在扩孔小且均匀,用后子母口端面放射状裂纹相对少而小。
- 1、下载文档前请自行甄别文档内容的完整性,平台不提供额外的编辑、内容补充、找答案等附加服务。
- 2、"仅部分预览"的文档,不可在线预览部分如存在完整性等问题,可反馈申请退款(可完整预览的文档不适用该条件!)。
- 3、如文档侵犯您的权益,请联系客服反馈,我们会尽快为您处理(人工客服工作时间:9:00-18:30)。
出钢挡渣随着用户对钢材质量要求的日益提高,需要不断提高钢水质量。
减少转炉出钢时的下渣量是改善钢水质量的一个重要方面。
在转炉出钢过程中进行有效的挡渣操作,不仅可以减少钢水回磷,提高合金收得率,还能减少钢中夹杂物,提高钢水清洁度,并可减少钢包粘渣,延长钢包使用寿命。
与此同时亦可减少耐材消耗,相应提高转炉出钢口耐火材料的使用寿命,还可为钢水精炼提供良好的条件。
转炉吹炼结束向盛钢桶(钢包)内放出钢水而把氧化渣留在炉内的操作。
出钢时使氧化性渣和钢水分离是炉外精炼的要求。
钢包内的二次精炼适于在还原条件下进行。
采用挡渣出钢,避免出钢带渣对提高炉外精炼效果是重要保证。
出钢时,随着钢水面的下降,当钢水深度低于某一临界值时,在出钢口上方会形成漏斗状的汇流旋涡,部分渣子在钢水出完以前就由出钢口流出,这是渣、钢分离不清的根本原因。
另外摇炉过快,有部分渣子由炉口涌出;但这可通过细心操作而避免。
挡渣出钢技术主要是针对汇流旋涡下渣而开发的。
有挡渣球、挡渣塞、高压气挡渣、挡渣阀门、下渣信号检测等各种方法。
挡渣球挡渣球由耐火材料包裹在铁芯外面制成,其密度大于炉渣而小于钢水,因而能浮在渣钢界面处。
出钢时,当钢水已倾出3/4~4/5时,用特定工具伸入炉内将挡渣球放置于出钢口上方。
钢水临近出完时,旋涡将其推向出钢口,将出钢口堵住而阻挡渣子流出。
(图1)为了提高挡渣球的抗急冷急热性能,提高挡渣效率,又研制了石灰质挡渣球。
先在铁芯外包一层耐火纤维,用于起缓冲作用;球的外壳以白云石、石灰等作原料,用合成树脂或沥青等作黏接剂制造。
挡渣球法成功的关键:一是球的密度恰当,即4.3~4.4g/cm3;二是出钢口维护好,保持圆形;三是放置球的位置对准出钢口。
但由于挡渣球的体形,极易随钢流飘浮而离开出钢口,从而失去挡渣作用。
挡渣出钢挡渣塞将挡渣物制成上为倒锥体下为棒状的塞(图2a)。
由于其形状接近于漏斗形,可配合出钢时的钢水流,故比挡渣球效率高。
有的在挡渣塞上部锥体增加小圆槽而下部改为六角锥形(图2b),以增加抑制旋涡的能力。
出钢时用专用机械将挡渣塞吊置在出钢口上方,缓缓加到钢水面上。
挡渣塞能堵住出钢口而阻挡炉渣流出。
挡渣出钢高压气挡渣是奥钢联开发的技术。
如图3所示,当有出渣信号时即将一铸铁喷嘴插入出钢口,向出钢口喷射高压(1~1.6MPa)氮或氩,喷嘴与出钢口耐火材料间的缝隙可将空气抽引进入,喷射的气流和吸入的空气共同将渣堵住。
挡渣出钢挡渣塞图2挡渣塞及其挡渣过程“一挡渣位置;6一改进的挡渣塞图3高压气挡渣示意图1一转炉;2一出钢口;3高压气体(Ar或N2)4炉渣信号检测器;5一气动挡渣器挡渣阀门在转炉出钢口外安装耐火材料制造的滑动阀板,其结构和钢包底部的滑动水口相类似。
(图4)当有下渣信号时,将阀门插上阻止渣子流下。
但出钢口环境条件比钢包恶劣,阀板滑动性能不易保证。
电弧炉炉底出钢时应用开闭式阀门,结构如图5,当钢水放出后用旋转臂关闭阀门阻止下渣。
挡渣出钢挡渣出钢下渣信号检测由于汇流旋涡的作用,在钢水没有出完时,部分渣子已在钢流内流出。
因此靠肉眼观察不能准确判断开始下渣时间。
应用电磁式渣信号检测器能早判断渣子流出信号,及时启动各种挡渣设施。
检测器原理如图6。
将线圈埋在出钢口外,在出钢口形成电磁场,由于金属和渣的透磁性不同,影响线圈内感应电流。
信号放大后可判断是否有渣出现。
挡渣出钢转炉出钢挡渣方法1 前言随着用户对钢材质量要求的日益提高,需要不断的提高钢水质量。
减少转炉出钢时的下渣量是提高钢水质量的一个重要方面。
转炉出钢时进行有效的挡渣,可以减少钢水回磷,提高合金收得率;减少钢中夹杂物,提高钢水清洁度;可以减少钢包粘渣,提高钢包包龄;同时可减少耐材消耗;也可为钢水精炼提供良好的条件。
为提高转炉挡渣效果,国外在挡渣技术方面作了深入研究,自1970年日本发明挡渣球出钢挡渣方法以来,各国为完善挡渣技术,发明了几十种挡渣方法。
本文对国内外转炉出钢挡渣的一些主要方法作一介绍。
2 转炉出钢挡渣的方法2.1 挡渣球法1970年新日铁发明了挡渣球,利用其比重介于钢、渣之间,在出钢将完时堵住出钢口以阻断渣流入钢包内。
但由于挡渣球通常是以随波逐流的方式到达出钢口,而由于钢渣粘性大,挡渣球有时不能顺利到达出钢口,或者不能有效地在钢水将流尽时堵住出钢口;另外又由于圆形挡渣球完全落到出钢口上,出钢口过早封堵的几率显著增加,降低了钢水收得率,故挡渣球法的可靠性难以令人满意。
但由于挡渣球法操作简单,故目前国内多数钢厂仍都采用挡渣球挡渣。
2.2 挡渣塞法1987年Michael bate总结了西德挡渣棒在美国使用的经验,发明了具有挡渣和抑制涡流双重功能的挡渣塞[1],见图1。
该装置呈陀螺形,粗端有3个凹槽、6个棱角,能够破坏钢水涡流,减少涡流卷渣。
其比重与挡渣球相近,在4.5~4.7 g/cm3之间,能浮于钢渣界面,伴随着出钢过程,逐渐堵住出钢口,实现抑制涡流和挡渣的作用。
图1 能抑制涡流的挡渣塞挡渣塞为一带杆的可以导向的圆锥体耐材,该法挡渣成功率可达95%左右。
西德曼内斯曼胡金根厂在220 t转炉上用挡渣塞挡渣。
武钢1996年开发设计了类似的陀螺形挡渣塞[2],见图2。
其上部为组合式空心结构,下部为带导向杆的陀螺形,与挡渣球类装置相比,具有可灵活调节比重、且能自动而准确地到达预定位置、成本低、成功率高的特点。
图2 陀螺形挡渣塞1.导向杆2.挡渣塞本体3.耐火材料4.杆芯5.芯片座板6.芯片7.芯片盖8.耐火材料国内外不少钢厂在挡渣器件的结构、形状及其投放方式等方面都进行了不少探索和改进,都取得了一定效果。
例如:用倒四面体、立方体的挡渣体、陶瓷挡渣块以及四周开槽的标枪式浮动芯棒等器件取代挡渣球挡渣,挡渣效果都好于挡渣球。
用投放车并不断改进来取代人工投放挡渣体,减轻了操作者的劳动强度,提高投放准确率,从而提高了挡渣效果。
2.3 挡渣料法此法也称硬吹或干渣吹炼法。
它是在吹炼结束时喷射一种固态混合物,提高渣稠度,使渣局部或全部凝固,以改变渣的流动性来挡渣;或在出钢口上部渣面投入粒状耐火材料,形成块状堵塞物,防止渣流出。
如:加古川制铁所在1978年试验过喷吹石灰法挡渣[3],新日铁曾用过固化炉渣法来挡渣。
2.4 避渣罩法1988年美国阿.勒德隆钢铁公司发明避渣罩挡渣法[4]见图3。
避渣罩砌筑在出钢口处,出钢时,钢水经耐材制成的避渣罩侧孔流入出钢口出钢,由于避渣罩顶部呈封闭形式,阻碍了出钢口上方涡流形成的条件,能有效地防止涡流卷渣图3 避渣罩挡渣法2.5 滑板法卢森堡、西德、日本在转炉上用大型钢包滑动水口挡渣,和一些示渣法相结合,可以有效控制下渣量,并能准确控制出钢时间。
其原理是将类似盛钢桶滑动水口耐火材料系统移植安装到转炉出钢口部位,通过操作系统以机械或液压控制的方式开启或关闭出钢口,以达到挡渣的目的。
这种装置挡渣效果较好,但其成本较高。
同时由于出钢口所在的特定位置,使得安装与拆卸均不方便,且易受吹炼期间喷溅的影响。
德国G.Bocher等人的文章介绍了Salzgitter钢厂210 t转炉使用一种在出钢口末端用液压闸门的挡渣装置[5],见图4。
该装置由3部分组成:驱动连接件、带保护箱的闸门、液压驱动系统。
转炉装料时闸门为开启位置,转炉到出钢位置时闸门关上,出钢前闸门重新开启,闸门开关仅0.3 s,操作安全可靠。
与挡渣球相比,钢包下渣量减少了70%,挡渣效果显著。
但该装置设备复杂、成本较高。
图4 闸板挡渣装置示意图2.6 气动挡渣法奥地利、瑞典等国家研究成功了气动挡渣法,见图5。
日本神户钢铁公司80年代末也使用了气动挡渣法,效果显著。
图5 气动挡渣法示意图该法主要设备包括封闭出钢口用的挡渣塞和用来喷吹气体、起动气缸以及对主体设备进行冷却保护等所用的供气设备。
挡渣时,挡渣塞头对出钢口进行机械封闭,塞头端部喷射高压气体来防止炉渣流出。
即使塞头与出钢口之间有缝隙,高速气流也能实现挡渣的效果。
这种挡渣法还采用了炉渣流出检测装置,由发送和接送信号的元件以及信号处理器件构成,通过二次线圈产生电压的变化,即可测出钢水通过出钢口的流量变化,能准确控制挡渣的时间。
此法在迅速性、可靠性和费用等方面都有明显优点。
比利时Forges de Clabecq的LD—LBE厂在85 t转炉也采用气动挡渣塞和炉渣自动检测系统实现挡渣出钢,可手动或自动控制[6]。
挡渣和气缸驱动挡渣塞头所用气体为高压压缩空气,设备冷却用低压压缩空气。
加古川制铁所从奥钢联引进的气动挡渣塞,挡渣时喷吹气体为氮气,气缸驱动和设备冷却用压缩空气。
另外还有不少钢厂采用了气动挡渣法,如:土耳其埃雷利(Erdemir)公司[7]、德国蒂森钢厂等。
宝钢第二炼钢厂转炉也采用了气动挡渣法[8],配有炉渣检测装置,实现了自动挡渣出钢。
2.7 电磁挡渣法日本钢管公司发明了电磁挡渣法[9],在转炉出钢口外围安装电磁泵,出钢时启动电动泵,通过产生的磁场使钢流直径变细,使在出钢口上方钢液面上发生的吸入涡流的高度减低,可以有效的防止炉渣通过出钢口流出。
该公司在250 t转炉上安装了能产生约1 500 G磁场的电磁泵,挡渣效果显著,出钢时间约20 min,钢水温度几乎不降低。
2.8 出钢口吹气干扰涡流法日本钢管公司经多年研究发现,从出钢口流出的钢流中混入熔渣的原因,主要是出钢口上方引起的钢流吸入漩涡,这种吸入漩涡愈高,愈容易将熔渣带走,因此如降低通过出钢口流出钢水的相对流速,即可减低所产生的吸入漩涡的高度,因而能防止熔渣的流出。
根据这些研究成果,日本钢管公司提出了这种方法,即在出钢口周围安装隋性气体吹管,当出钢时,通过惰性气体吹管往炉内喷吹惰性气流,可有效地阻止炉渣流出。
韩国光阳厂也研制了类似的方法,即出钢时向出钢口上方的钢液面吹氩,吹散钢液面上的炉渣,同时形成一个“刚性”凹坑,抑制熔池涡流在出钢口上方形成,凹坑形状对阻止炉渣随钢水流入出钢口起重要作用。
采用本法钢包内渣层厚度20~50 mm,而采用挡渣球法渣层厚度为70~90 mm。
加拿大伊利湖钢铁公司研究认为[10],230 t转炉当出钢口上方钢水高度为125 mm时,开始出现涡流卷渣现象。
为防止涡流卷渣,在出钢口设置多孔透气砖,通过吹气来干扰涡流,使钢包渣层厚度小于75 mm。
2.9 转动悬壁法瑞典斯堪的纳维亚兰舍斯钢公司设计了一种转动式悬臂木塞挡渣器,可使出钢带渣减到最低限度,欧洲许多厂采用该挡渣法[11]。
2.10 挡渣棒法1983年日新制钢研究成功挡渣棒法,挡渣棒吊在支臂上在炉内可以自由移动,在即将出完钢时从转炉内部将出钢口塞住,以挡住炉渣,如再配以荷重器、高频电流信号,效果更佳。
该装置操作与维护较复杂。
2.11 挡渣罐挡渣法川崎钢铁公司研制了挡渣罐挡渣法,它能在转炉出钢时将熔渣分离。