烧结返矿粒度范围的研究与应用资料
几种粉料的粒度和用途

水泥组分
• 水泥生料:一般的,水泥生料应当磨至90µm的筛余量为 15%,而300um的筛余量为1.5%~2.5%。大多数企业已经 掌握的技术; • 高炉矿渣:①是一种冶炼生铁时从高炉中排出得废渣。当 炉温达到1400℃~1600℃时,助溶剂与铁矿石发生高温反 应生成生铁和矿渣,而高炉渣是由脉石,灰粉,助溶剂和 其它不能进入生铁中的杂志组成的混合物,从化学成分上 看,高炉矿渣属于硅酸盐质材料。②因为是硅酸盐质材料, 又是在1400℃~1600℃高温下形成的熔融体,所以便于加 工成多种建筑材料,水淬成粒状矿渣(水渣)可显出它
几种粉料的粒 度和用途
铁精粉
• 钢铁厂要求的铁精粉的粒度是小于75um的要达到 70%以上; • 炼铁行业中,入高炉的矿料(球团矿,烧结矿,焦 ) 5~35mm 5mm 炭)的粒度在5~35mm中,小于5mm的不能直接入 高炉; • 铁精粉的密度:2.2~2.4g/cm3 褐红色铁精粉堆积密度:1.14g/cm3 含铁55%-65%铁粉比重在4.55-4.9左右
Байду номын сангаас
煤粉和粉煤灰
• 煤粉炉:①主要用于电厂的大型锅炉中,要求粒度为 74um以下的占80%以上;②现在电厂主要用立磨和球磨; ③烧结矿块用的焦炭粉在1~2mm左右; • 水泥回转窑中的煤粉:粒度应在80um,筛余为6%~8%; • 粉煤灰:是从煤燃烧后的烟气中收捕下来的细灰;主要成 分是SiO2,Al2O3,Fe2O3等等;粉煤灰以颗粒形态存在, 在混凝土中掺和粉煤灰可以节约大量的水泥和细骨料; • 粉煤灰的物理性质:密度:1.9~2.9g/cm3 均值: 2.1g/cm3 堆积密度:0.531~1.261g/cm3 均值: 0.780g/cm3
潜在的水硬胶凝性能,生产水泥的优质原料。可作为水 泥混合料使用,也可制成无熟料水泥。因为它对水泥的抗 压强度影响小,对抗拉强度影响更小,所以其掺入量可达 到水泥质量的20%~80%,对提高水泥质量,降低水泥成 本十分有利。 物理性质 普通水泥:密度 3.0~3.15g/cm3 堆积密度 1.0~1.6g/cm3 矿渣水泥:密度 ≥2.8g/cm3 堆积密度 1.0~1.2/cm3 火山灰水泥:密度 2.8~3.1g/cm3 堆积密度 0.9~1.0g/cm3 粉煤灰水泥:密度 2.8~3.1g/cm3 堆积密度 0.9~1.0g/cm3
精益管理在提高烧结矿产质量中的应用研究

精益管理在提高烧结矿产质量中的应用研究作者:郑文祥来源:《科学与信息化》2020年第10期摘要在当下,社会竞争越来越激烈,与此同时钢材价格波动频繁使得很多国内的钢铁行业都在艰难的维持着运作,也有不少的企业甚至在亏损的情况下运作。
为了打破这一局面,使它往可持续的方向发展,国内钢铁企业都在积极的思考。
关键词烧结矿;质量;精益管理如何运用好精益管理为企业最大程度的优化成本投入,转化出更大的效益,提升自身的企业竞争力。
那么到底什么是精益管理呢?烧结矿产质量是衡量一个企业经济效益好坏的重要因素,在平时的生产操作过程中起到了非常重要的作用。
那么该如何在提高烧结矿产质量中展现出精益管理的作用呢?本文我们将对这两点做一个简单的分析与研究。
1 精益管理的定义精益管理简单来讲就是要培养一种运用“精益思维”来管理企业的各活动的管理思维。
“精益思维”的定义就是用最小的资源投入,将资源浪费降到最低,从而获得最大的效益。
对于企业来讲,最小的资源投入即在人力支出,设备支出,资金支出和材料支出等方面,将不该有的消耗降到最低程度,同等资源下尽可能的创造出更多的价值,同时不影响顾客的满意度。
2 精益管理的重要性精益思维所体现的精益管理,在越来越多企业的实践下,已经被认为是在不影响质量的情况下,降低成本,带来效益的有效的举措。
在提高烧结矿产质量中,如果运用精益管理方法,在同一种烧结工艺状态下,通过稳定烧结原料的性质,对影响烧结矿产质量的因素进行优化,就可以很好的解决长久以来因为烧结新矿石而不断摸索和反复实验的问题,从而达到用最小的损耗来实现矿产质量最优化的指标。
所以在提高烧结矿产质量中,将精益管理同实际的生产操作结合起来,对提高烧结矿产质量,带来经济效益奠定了坚实的基础。
3 精益管理的应用3.1 稳定烧结矿化学成分随着进口铁矿石的可选择性越来越多,各大企业的原料不再单一,这样多种原料混合会使原料的性能因为互相混合而不稳定。
混合料成分的稳定,就可以运用精益管理结合多次取样分析混匀粉的化学成分明细,然后通过结合烧结矿产质量变化的特点,来稳定烧结原料的性质,将原料成分的波动控制在一个合理的范围内,可以有利的促进高炉的顺利运转,从而大大提高烧结矿质量。
转炉炼钢过程中烧结返矿应用的生产实践
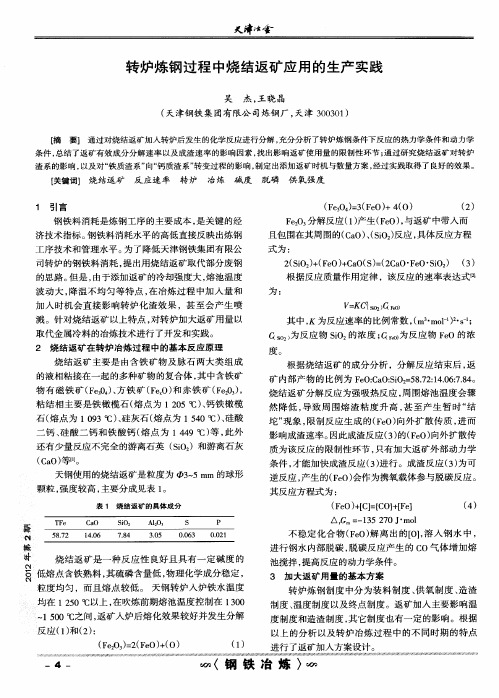
矿 内部产物 的 比例 为 F O C OSO = 87 : .6 . 。 e :a : 5 .21 0 : 8 i 4 74
烧结返 矿分解反应 为强吸热反 应 , 围熔池 温度会骤 周
然 降低 , 导致 周 围熔 渣粘 度 升高 , 至 产 生 暂 时“ 甚 结
坨” 现象 , 限制反 应生成 的( e 向外扩 散传 质 , 而 F O) 进
C O a
1 o 4.6
S O2 i
7.4 8
A103 2
3.5 O
S
0.6 0 3
P
0.21 0
不 稳 定化 合物 (e 解 离 出 的[]溶 人 钢水 中 , F O) O,
进行 钢水 内部脱碳 , 碳反应 产生 的 C 脱 O气体 增加熔
蚌
烧 结返 矿是 一种 反应 性 良好 且 具有 一定 碱度 的
天. 4 i幺 : 牵 -
转炉 炼 钢 过 程 中烧 结 返矿 应 用 的生产 实践
吴 杰 , 晓 晶 王
( 津钢 铁 集 团有 限公 司炼钢 厂 , 天 天津 300 ) 03 1
【 摘 要】 通过对烧结返矿加入转炉后发 生的化学 反应 进行 分解 , 充分分析 了转炉炼钢条件下反应 的热力学条件 和动 力学
条件 , 总结了返矿有效成分分解 速率 以及成渣速率 的影 响因素 , 找出影响返矿使用量 的限制性环节 ; 通过研究烧结返矿对 转炉 渣系 的影 响, 以及对“ 铁质渣 系” 钙 质渣 系” 向“ 转变过程 的影 响, 制定出添加返矿时机与数量方案 , 经过实践取得 了 良好 的效果 。
【 关键词】 烧 结返矿
池搅拌 , 提高反应 的动力学条件 。
3 加大返பைடு நூலகம்用量 的基 本方案
铁矿石碎矿粒度对烧结养分性能影响的研究

铁矿石碎矿粒度对烧结养分性能影响的研究随着全球经济的不断发展,矿山资源的开采和利用也日益受到关注。
铁矿石作为重要的工业原料之一,被广泛运用于水泥、钢铁等行业中。
在铁矿石的加工过程中,碎矿是必不可少的环节,其粒度也对烧结养分性能有重要影响。
本文将探讨铁矿石碎矿粒度对烧结养分性能的影响,并借助相关研究解释其原因。
铁矿石烧结过程中,养分性能表现为烧结矿的质量和机械强度等指标。
烧结矿的质量受到铁矿石粉末矿物成分、颗粒大小和形态、烧结温度、煤粉性质等因素的影响。
其中,铁矿石粉末的粒度是影响烧结养分性能的关键因素之一。
研究表明,铁矿石碎矿粒度对烧结养分性能有重要影响。
在一定范围内,铁矿石粉末的粒度越细,烧结矿的质量和机械强度越高。
这是由于粉末颗粒大小的变化会导致颗粒间的空隙率、表面积和孔隙度发生变化,从而影响到烧结过程中矿石的结合和转化。
粉末颗粒大小越小,其表面积越大,颗粒之间的空隙率也越小,因此,烧结矿的质量和机械强度也就越高。
除了粉末颗粒大小的影响外,铁矿石碎矿粒度对烧结养分性能的影响还与铁矿石的矿物成分和结构有关。
铁矿石的矿物组成复杂,不同矿物对烧结过程中的结合、转化和热分解有不同的影响。
在粒径相同的情况下,矿物成分不同的铁矿石其热分解温度和转化速率也会有较大的差异,进而影响到烧结矿的质量和机械强度。
因此,铁矿石碎矿粒度的作用是与其矿物成分和结构相互交织并共同作用的。
另外,铁矿石的碎矿粒度对于烧结过程中的烧损率也有很大的影响。
烧损率是指烧结过程中铁矿石的挥发分和焦炭的消耗率,其大小直接影响到冶金品质和成本。
一般来说,碎矿粒度较细的铁矿石在烧结过程中,因其表面积大,热传递效率高,所需焦炭量相对较少,从而减小烧损率。
另外,铁矿石粒度过细会导致料层透气性不足,从而增加焦炭的消耗和烧损率。
因此,铁矿石碎矿粒度的选择必须兼顾铁矿石烧结特性和冶金经济成本。
综合来看,铁矿石碎矿粒度直接影响烧结养分性能。
在烧结工程实践中,在保证烧结质量稳定和产品质量的前提下,应该根据铁矿石的矿物成分、结构特点和冶金成本等因素,综合考虑碎矿粒度的选择。
烧结返矿粒度范围的研究与应用共61页PPT

•
46、寓形宇内复几时,曷不委心任去 留。
•
47、采菊东篱下,悠然见南山。
•
48、啸傲东日 有所长 。
•
50、环堵萧然,不蔽风日;短褐穿结 ,箪瓢 屡空, 晏如也 。
▪
26、要使整个人生都过得舒适、愉快,这是不可能的,因为人类必须具备一种能应付逆境的态度。——卢梭
▪
27、只有把抱怨环境的心情,化为上进的力量,才是成功的保证。——罗曼·罗兰
▪
28、知之者不如好之者,好之者不如乐之者。——孔子
▪
29、勇猛、大胆和坚定的决心能够抵得上武器的精良。——达·芬奇
▪
30、意志是一个强壮的盲人,倚靠在明眼的跛子肩上。——叔本华
谢谢!
61
烧结杯试验
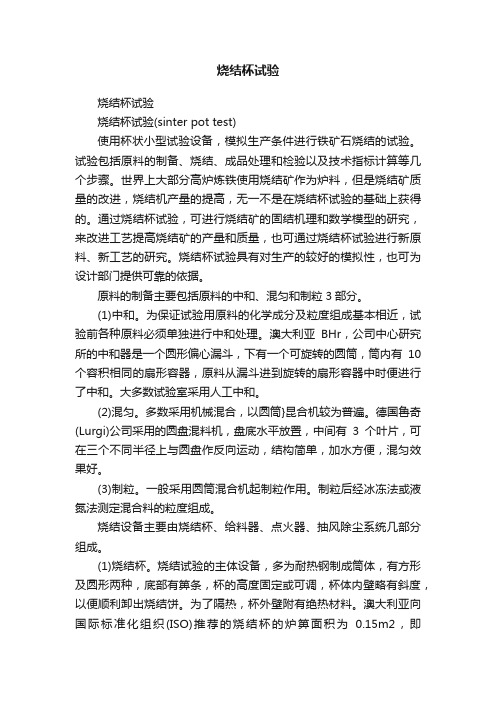
烧结杯试验烧结杯试验烧结杯试验(sinter pot test)使用杯状小型试验设备,模拟生产条件进行铁矿石烧结的试验。
试验包括原料的制备、烧结、成品处理和检验以及技术指标计算等几个步骤。
世界上大部分高炉炼铁使用烧结矿作为炉料,但是烧结矿质量的改进,烧结机产量的提高,无一不是在烧结杯试验的基础上获得的。
通过烧结杯试验,可进行烧结矿的固结机理和数学模型的研究,来改进工艺提高烧结矿的产量和质量,也可通过烧结杯试验进行新原料、新工艺的研究。
烧结杯试验具有对生产的较好的模拟性,也可为设计部门提供可靠的依据。
原料的制备主要包括原料的中和、混匀和制粒3部分。
(1)中和。
为保证试验用原料的化学成分及粒度组成基本相近,试验前各种原料必须单独进行中和处理。
澳大利亚BHr,公司中心研究所的中和器是一个圆形偏心漏斗,下有一个可旋转的圆筒,筒内有10个容积相同的扇形容器,原料从漏斗进到旋转的扇形容器中时便进行了中和。
大多数试验室采用人工中和。
(2)混匀。
多数采用机械混合,以圆筒}昆合机较为普遍。
德国鲁奇(Lurgi)公司采用的圆盘混料机,盘底水平放置,中间有3个叶片,可在三个不同半径上与圆盘作反向运动,结构简单,加水方便,混匀效果好。
(3)制粒。
一般采用圆筒混合机起制粒作用。
制粒后经冰冻法或液氮法测定混合料的粒度组成。
烧结设备主要由烧结杯、给料器、点火器、抽风除尘系统几部分组成。
(1)烧结杯。
烧结试验的主体设备,多为耐热钢制成筒体,有方形及圆形两种,底部有箅条,杯的高度固定或可调,杯体内壁略有斜度,以便顺利卸出烧结饼。
为了隔热,杯外壁附有绝热材料。
澳大利亚向国际标准化组织(ISO)推荐的烧结杯的炉箅面积为0.15m2,即φ400mm的圆杯或400mm×400mm的方杯,料层高度为500mm。
此外,世界各国还有为不同研究目的而设计的各种特殊结构的烧结杯。
(2)给料器。
作用是将混合料装入烧结杯中。
大烧结杯采用机械装料,小烧结杯则用人工装料。
烧结混合料粒度标准

烧结混合料粒度标准
烧结混合料粒度标准是指在烧结生产过程中,为了保证烧结矿块的质量,对原
料矿石的粒度进行规定的标准。
粒度标准旨在确保原料矿石的成分和性质满足烧结生产的要求,进而保证烧结矿块的质量和生产效益。
对于烧结混合料的粒度标准来说,一般有两个方面的要求:一是对于原料矿石
的最大粒径进行限制;二是对于原料矿石的分级要求。
首先,烧结混合料需要限制原料矿石的最大粒径。
原料矿石的最大粒径过大会
导致烧结过程中的物理反应和化学反应不充分,影响矿石的烧结性能和产品的质量。
因此,烧结混合料的粒度标准通常会规定原料矿石的最大允许粒径,以确保矿石的烧结效果。
其次,烧结混合料的粒度标准还包括对原料矿石的分级要求。
原料矿石的分级
是指将原料矿石按照一定的粒度范围进行划分,以保证矿石的成分和性质在一定范围内稳定。
分级要求通常通过筛分实验来确定,烧结混合料的粒度标准会规定不同粒度级别的矿石所占的比例范围,以确保混合料中的矿石能够达到稳定的成分和性质,从而提高烧结生产的效果。
总之,烧结混合料粒度标准是为了保证烧结生产的质量和效益,对于原料矿石
的粒度进行规定的标准。
标准主要包括对原料矿石的最大粒径进行限制以及对原料矿石的分级要求。
这些标准的制定有助于确保矿石的烧结效果和产品的质量,提高烧结生产过程中的效率和经济效益。
烧结返矿粒度要求
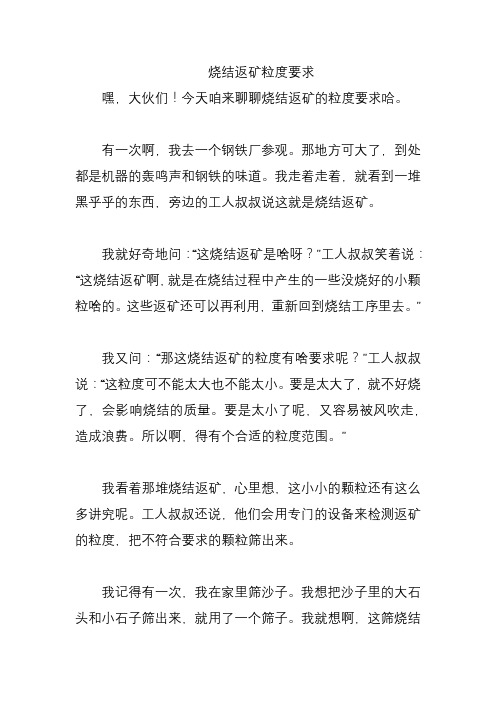
烧结返矿粒度要求
嘿,大伙们!今天咱来聊聊烧结返矿的粒度要求哈。
有一次啊,我去一个钢铁厂参观。
那地方可大了,到处都是机器的轰鸣声和钢铁的味道。
我走着走着,就看到一堆黑乎乎的东西,旁边的工人叔叔说这就是烧结返矿。
我就好奇地问:“这烧结返矿是啥呀?”工人叔叔笑着说:“这烧结返矿啊,就是在烧结过程中产生的一些没烧好的小颗粒啥的。
这些返矿还可以再利用,重新回到烧结工序里去。
”
我又问:“那这烧结返矿的粒度有啥要求呢?”工人叔叔说:“这粒度可不能太大也不能太小。
要是太大了,就不好烧了,会影响烧结的质量。
要是太小了呢,又容易被风吹走,造成浪费。
所以啊,得有个合适的粒度范围。
”
我看着那堆烧结返矿,心里想,这小小的颗粒还有这么多讲究呢。
工人叔叔还说,他们会用专门的设备来检测返矿的粒度,把不符合要求的颗粒筛出来。
我记得有一次,我在家里筛沙子。
我想把沙子里的大石头和小石子筛出来,就用了一个筛子。
我就想啊,这筛烧结
返矿应该也差不多吧。
不过,钢铁厂的筛子可大多了,也更先进。
工人叔叔还告诉我,控制好烧结返矿的粒度,不仅能提高烧结的质量,还能节约能源呢。
因为合适的粒度能让烧结过程更顺利,少浪费一些燃料。
总之呢,烧结返矿的粒度要求可不能马虎。
要控制在一个合适的范围内,这样才能让烧结工序更高效,也更环保。
希望大家都能了解一下烧结返矿的粒度要求,这样我们就能更好地理解钢铁生产啦。
嘿嘿,大伙们觉得咋样?。
烧结矿al2o3
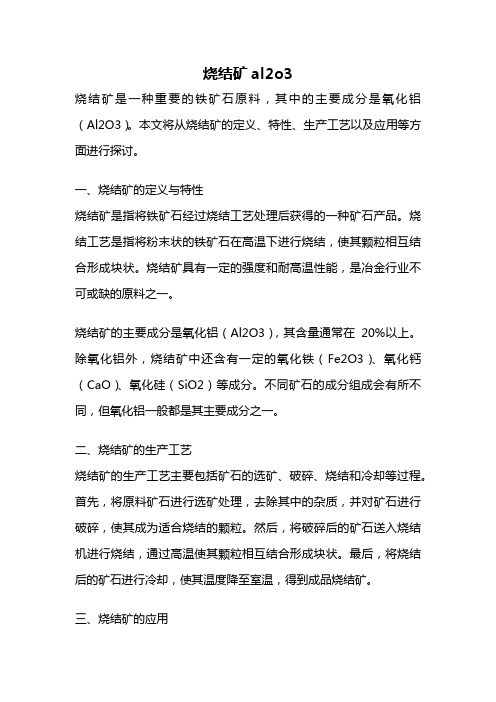
烧结矿al2o3烧结矿是一种重要的铁矿石原料,其中的主要成分是氧化铝(Al2O3)。
本文将从烧结矿的定义、特性、生产工艺以及应用等方面进行探讨。
一、烧结矿的定义与特性烧结矿是指将铁矿石经过烧结工艺处理后获得的一种矿石产品。
烧结工艺是指将粉末状的铁矿石在高温下进行烧结,使其颗粒相互结合形成块状。
烧结矿具有一定的强度和耐高温性能,是冶金行业不可或缺的原料之一。
烧结矿的主要成分是氧化铝(Al2O3),其含量通常在20%以上。
除氧化铝外,烧结矿中还含有一定的氧化铁(Fe2O3)、氧化钙(CaO)、氧化硅(SiO2)等成分。
不同矿石的成分组成会有所不同,但氧化铝一般都是其主要成分之一。
二、烧结矿的生产工艺烧结矿的生产工艺主要包括矿石的选矿、破碎、烧结和冷却等过程。
首先,将原料矿石进行选矿处理,去除其中的杂质,并对矿石进行破碎,使其成为适合烧结的颗粒。
然后,将破碎后的矿石送入烧结机进行烧结,通过高温使其颗粒相互结合形成块状。
最后,将烧结后的矿石进行冷却,使其温度降至室温,得到成品烧结矿。
三、烧结矿的应用烧结矿作为一种重要的冶金原料,具有广泛的应用领域。
首先,烧结矿是炼铁过程中的重要原料之一。
在高炉冶炼中,烧结矿与其他铁矿石混合使用,可以提高炉渣的流动性和炉渣的还原性,从而提高炉渣的脱硫能力,减少炉渣对铁液的冶炼影响。
其次,烧结矿还可用于生产铁合金。
在铁合金冶炼中,烧结矿作为还原剂和熔剂,可与其他原料混合使用,使得反应更加充分,提高铁合金的产率和质量。
此外,烧结矿还可用于制备耐火材料、陶瓷材料等。
总结:烧结矿是一种重要的冶金原料,其中的主要成分是氧化铝(Al2O3)。
烧结矿具有一定的强度和耐高温性能,是冶金行业不可或缺的原料之一。
烧结矿的生产工艺包括选矿、破碎、烧结和冷却等过程。
烧结矿在炼铁、铁合金生产以及耐火材料、陶瓷材料等领域都有广泛的应用。
通过对烧结矿的深入了解,可以更好地应用于实际生产中,提高冶金产品的质量和产量。
小粒度烧结矿回收利用研究及生产实践

223 料 批 的确定 .. 保 持正 常 矿 批 ( 3t 右 ) 变 , 常矿 批 的 布 1 左 不 正
中 ≤5m 的 比例 较 高 , 到 1% ~1%, 虑 到 这 m 达 0 5 考 些 因素 , 合 其他 企 业小 粒 度烧 结 矿 运用 的成 功 经 结 验 和 我公 司实 际情 况 , 们 制定 了小 粒度 烧 结 矿使 我
收 稿 日期 :0 2 0 — 3 2 1— 5 1 作者 简介 : 志伟 (9 8 , , 南许 昌人 , 学本科 , 理工程 李 17 一) 男 河 大 助
用 好 小 粒 度 烧 结 矿 的前 提 是 保 证 小 粒 度 烧 结
矿 的入 炉粒 级 , 免大 量粉 末 人炉 。我公 司的 炉料 避
结 构 是烧 结 矿较 碎 和 高球 团 比例 , 因此整 体 炉料 粒 级较 小 ;同 时原 料 入 炉 只 有 槽 下 一 道 筛分 ,炉 料
师, 主要从事设备技术与管理工作 。
・
4 ・ 0
2 0 箜 塑
李志 马 丽, 娟, 强,志 .粒 烧 矿 收 用 究 生 实 伟,军 黄 柴 王 刚/ 度 结 回 利 研 及 产 践 J 、
要求 ;同时在机头旁制作安装一个小粒 回收专料
仓 , 大于 3 将 的小粒 矿存 入 回收仓 , 独加 入 高 mm 单 炉 。< 的粉 末返 回烧 结车 间 。小 粒度烧 结矿 回 3 mm
收工艺 流程 见 图 1 。 22 小粒度 烧结矿 入 炉操 作 参数 的确 定 .
筛 分 ,结果 导 致烧 结返 矿 中的大 于 3m 的小 粒 矿 m 很 多 , 烧结 产 量 40 0t 按 0 d计 , 天 筛 分 出 的返 矿 / 每
铸造设备与工艺
平衡烧结内部返矿率技术分析
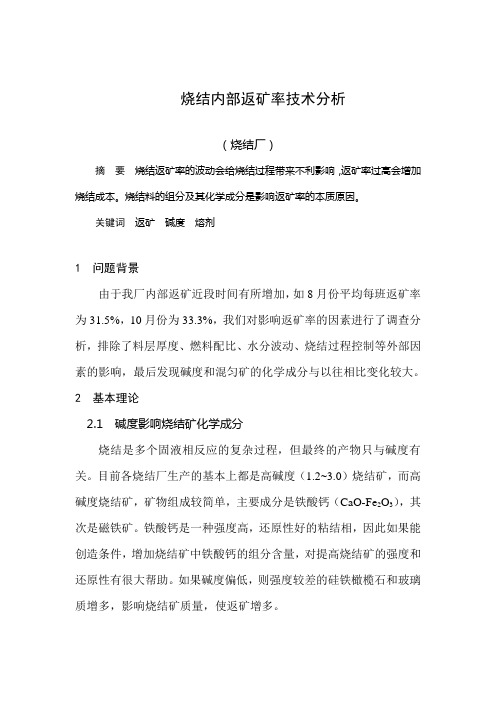
烧结内部返矿率技术分析(烧结厂)摘要烧结返矿率的波动会给烧结过程带来不利影响,返矿率过高会增加烧结成本。
烧结料的组分及其化学成分是影响返矿率的本质原因。
关键词返矿碱度熔剂1 问题背景由于我厂内部返矿近段时间有所增加,如8月份平均每班返矿率为31.5%,10月份为33.3%,我们对影响返矿率的因素进行了调查分析,排除了料层厚度、燃料配比、水分波动、烧结过程控制等外部因素的影响,最后发现碱度和混匀矿的化学成分与以往相比变化较大。
2 基本理论2.1 碱度影响烧结矿化学成分烧结是多个固液相反应的复杂过程,但最终的产物只与碱度有关。
目前各烧结厂生产的基本上都是高碱度(1.2~3.0)烧结矿,而高碱度烧结矿,矿物组成较简单,主要成分是铁酸钙(CaO-Fe2O3),其次是磁铁矿。
铁酸钙是一种强度高,还原性好的粘结相,因此如果能创造条件,增加烧结矿中铁酸钙的组分含量,对提高烧结矿的强度和还原性有很大帮助。
如果碱度偏低,则强度较差的硅铁橄榄石和玻璃质增多,影响烧结矿质量,使返矿增多。
2.2 熔剂的活性和粒度影响烧结矿质量铁酸钙的形成有一个前提条件:那就是要有足够多的CaO与Fe2O3充分接触。
我们通过在混合料中添加熔剂来生产高碱度烧结矿,以提供大量的CaO。
熔剂的活性和粒度很重要。
生石灰的反应活性远远大于其他熔剂,用生石灰取代其他熔剂能增强反应效果。
但如果生石灰的粒度较大或分布不均,CaO与Fe2O3接触不够充分,CaO就能与烧结料中的SiO2生成正硅酸钙,正硅酸钙在冷却时能发生β-型到γ-型的晶型转变,该转变使其体积增大10%,从而发生膨胀,致使烧结矿在冷却时自行粉碎。
返矿的增加,本质是因为烧结过程中液相的质量和数量不够,使得最终的烧结矿强度下降而造成的。
3 现状分析3.1 碱度影响由于高炉炉料结构调整,我厂生产的烧结矿碱度从以往的2.0左右调整到目前的1.65左右。
从以上基本理论可知,碱度下降,对烧结矿的强度产生一定的影响,使返矿率有所增加。
烧结矿质量及其对高炉冶炼主要操作指标的影响

烧结矿质量及其对高炉冶炼主要操作指标的影响摘要:烧结矿质量对高炉炼铁产量、能耗、生铁质量、高炉寿命起着决定性的作用。
基于此,本文重点分析了烧结矿质量及其对高炉冶炼主要操作指标的影响。
关键词:烧结矿质量;高炉冶炼;操作指标;影响目前,在高炉炼铁过程中,烧结矿的质量作为影响炼铁燃料消耗的重要因素之一,应进行有效的优化完善,以有效提高烧结矿的性能,为高炉炼铁过程奠定坚实的物质基础,从而在一定程度上促进炼铁工艺节能降耗的发展。
一、烧结矿产量与质量的影响因素1、燃料粒度影响。
合适的固体燃料粒度等级和粒度分布能提烧结机利用系数,使烧结矿成品率、转鼓指数、平均粒径等指标明显改善,同时也能降低固体燃料消耗和高炉返矿率。
2、烧结熔剂结构影响。
自熔性烧结矿要满足高炉所需各项理化指标,必须在混合料中配加一定量生石灰、石灰石和白云石等熔剂。
配加熔剂结构的不同会对烧结矿强度、碱度、还原性、低温还原粉化率和混匀料粒级分布等各项理化指标产生影响,这些指标会直接关系到高炉冶炼的稳定顺行,从而对生铁产量及炼铁成本产生影响。
二、烧结矿质量对高炉冶炼主要操作指标的影响1、烧结矿主要化学成分的影响①品位及SiO2含量影响。
在正常情况下,入炉矿品位1%变动将导致高炉燃料比1~1.5%变动,产量2~2.5%变动,一旦确定了烧结矿在炉料结构中比例,就可计算出烧结矿品位变动1%对高炉燃料比及产量的影响。
入炉矿SiO2含量1%变动将影响30~35kg/t渣铁比,100kg渣量将影响3.0~3.5%燃料、产量。
有了烧结矿入炉比例,乘以该比例将决定烧结矿SiO2含量变动对高炉主操作指标的影响。
②烧结矿碱度的影响。
生产实践表明,烧结矿最佳碱度范围为1.9~2.3,当低于1.85时,碱度每降低0.1,燃料比与产量将分别影响3.0~3.5%。
据了解,实际生产中,降低碱度对高炉燃料比影响远高于3.5%的比例。
近年来,一些生产企业的烧结矿碱度低于1.80甚至低于1.70,应该认识到,碱度对烧结矿质量和高炉主要操作指标都有影响。
返矿对烧结过程和烧结矿质量影响的研究

返矿对烧结过程和烧结矿质量影响的研究一、返矿的基本情况返矿呢,就是在烧结过程中产生的一种东西啦。
它可不是个小角色哦,在整个烧结的世界里,有着很重要的影响呢。
咱们先来说说它是怎么来的吧。
在烧结的过程中,由于各种原因,比如说矿石的特性啊,烧结的工艺条件之类的,就会产生返矿。
它就像是一个调皮的小跟班,虽然是从主要的烧结过程里“跑出来”的,但却有着自己独特的影响力。
二、返矿对烧结过程的影响1. 透气性方面返矿的存在就像是在烧结的道路上开了一些小通道。
它可以改善烧结料层的透气性哦。
你想啊,如果把烧结料层比作是一条拥挤的小路,返矿就像是在小路上清理出了一些小缝隙,让空气可以更顺畅地通过。
这样的话,燃料燃烧就会更充分,烧结的速度也会受到影响呢。
如果返矿的量合适,就像是给烧结过程加了个小助手,能让烧结过程顺利地向前推进。
但要是返矿太多或者太少,那就麻烦啦。
太多的话,就像是小缝隙开得太大,整个烧结料层的结构可能就不稳定了;太少呢,空气就又不够顺畅了,就像小路还是很拥挤一样。
2. 热量传递方面返矿还会影响热量的传递哦。
它就像一个小小的热量储存器。
当热量在烧结过程中传递的时候,返矿会吸收和释放热量。
如果返矿的比例合适,它能很好地调节热量的分布,让整个烧结过程的温度更加均匀。
可是如果返矿的量或者性质不合适,就可能会造成热量传递的不均匀。
比如说有的地方热量太多,矿石都烧结过头了,有的地方热量又不够,还没烧结好呢。
三、返矿对烧结矿质量的影响1. 强度方面烧结矿的强度可是很重要的质量指标呢。
返矿对它有着不小的影响。
合适的返矿加入,可以让烧结矿的结构更加紧密,强度也就更好啦。
就像盖房子一样,返矿就像是一些特殊的小砖块,把其他的砖块更好地连接在一起。
但是如果返矿的成分或者量有问题,那烧结矿的强度可能就会大打折扣。
比如说返矿里如果有一些杂质,就会破坏烧结矿的结构,让它变得脆弱,在后续的运输或者使用过程中就容易破碎。
2. 化学成分方面返矿的化学成分也会影响烧结矿的质量。
承钢外矿烧结性能研究与应用

在烧 结生 产 中 , 烧 结 配料 结 构是 否 合 理 将 直 接 影 响烧结 矿显 微 组织 形 态 和冶 金 性 能 , 进而 对 烧 结 矿 质量 和生产 成本产 生重要 影响 。通过 烧结 杯试 验
研 究承 钢使用 主 要外 矿 的 烧结 性 能 , 确 定 其 与本 地 钒 钛粉搭 配使 用适宜 的配加 比例 。根据 烧结杯 试验 及工业 试验 结果 , 对 外 矿性 能 进 行 综合 评 价 、 排序 ,
粉” 结构 , 目前外 矿配 加 比例 已经达 到 3 0 %, 外 矿 在
满 足资源需 求 、 改善烧 结矿性 能方 面起 到积极 作 用 。
随 着原料 结构 的 变化 , 烧 结 矿 显微 组 织 形 态 和冶 金
( 1 ) 通过 分 析 承 钢 使 用 主要 外 矿 的 理 化 指 标 、
C) 的最 低 同化温 度较低 , 均 属 于 同化 性 较高 的铁 矿 粉, 而 巴西粉 D 铁 矿 粉 的最 低 同化 温 度 最 高 , 高 于
1 3 0 0 ℃, 属于 同化 性 较 低 的难 烧 铁矿 粉 。黑 山精 粉 也 属 于 同化 性 较 差 的矿 粉 , 普 通 粉 稍好 些 。7种 铁
( I r o n wo r k s , C h e n g d e I r o n a n d S t e e l Co mp a n y , He b e i I r o n a n d S t e e l Gr o u p, C h e n g d e , He b e i , 0 6 7 1 0 2 )
对改善烧结矿强度和粒度的资料

对改善烧结矿强度和粒度的资料烧结矿品位的提高和Si02含量的降低.出现了成品矿强度降低和小粒级 (10—5mm)比例增大的质量问题不同程度地影响着烧结和高炉生产1 磁铁矿的主要成分是Fe3O4 , 赤铁矿的主是要成分是Fe2O3 , 在烧结反应过程中, 前者比后者更易形成含FeO 的矿相。
因而, 随着磁铁矿配比的提高, 烧结矿的FeO 含量亦提高。
对高碱度烧结矿而言,它的主要矿物相为赤铁矿(Fe2o3 )和铁酸钙,随FeO 升高(配C增加),会造成Fe2o3分解为Fe3o4十FeO使得矿物组成中Fe3o4增加,铁酸钙含量降低,从而造成成品矿的强度下降。
2 Si02含量高低对成品矿的强度和性能有举足轻重的影响。
,高sio2含量矿石,特别是使用含量在10%一12%时的磁选铁精矿,在一定碱度时,由于正硅酸钙(2Ca0"S102)在冷却过程中的相变体积膨胀,会造成严重的自然粉化和降低烧结矿的强度。
混合料的Si02降低到<5%的水平时,烧结矿的强度就会出现问题3由于MgO的熔点高达2799°,在烧结过程中,部分固溶于磁铁矿形成镁磁铁矿,MgO含量高后会降低烧结矿中铁酸钙的含量,从而不利于烧结矿的冷强度,提高MgO含量会降低烧结矿的转鼓指数4Al2o3的熔点为2042°,在烧结过程中除了生成复合的铁、钙、硅、铝复合铁酸盐外,不能单独熔化,烧结矿的合理含量应低于1.8%,高了会降低烧结矿的冷强度,还会恶化烧结矿的还原粉比指数。
5热返矿是最容易被忽视而又最不能忽视的一个因素,热返矿粒度和热返矿量大后,均会引起混合料水分的波动和成球率下降,从而影响成品矿的强度下降和粒度变小6 燃料的粒度过粗或过细,降低烧结矿的强度和成品率,因此适宜的燃料粒度也是成品矿强度和粒度组成的一个重要条件。
烧结生产适宜的焦粉粒度应为0.5~3 mm90%以上。
如果粒度太细, 一方面会使料层的透气性恶化, 烧结速度降低, 另一方面,细颗粒燃料燃烧速度过快, 烧结矿液相发展不充分, 使强度变差。
【管理资料】烧结返矿粒度范围的研究与应用资料汇编
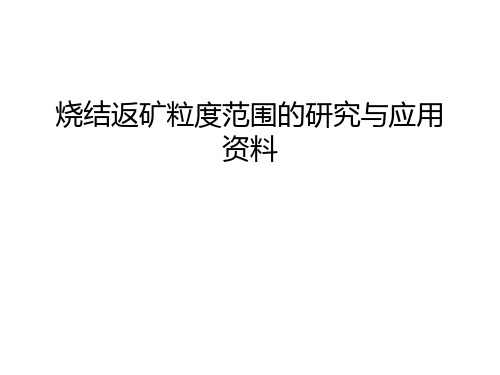
一、文献综述
返矿作为烧结矿闭路循环物料是整粒工艺筛 下物(粒度0-5mm),又是小颗粒烧结矿和少部 分未烧透的夹生料所组成,俗称“烧结循环下脚 料”。但由于其粒度相对较粗,在混合料制粒过 程中,易成为成球的“核心”,加上其具有疏松 多孔的结构,可明显改善烧结料的透气性,加快 烧结速度。同时,由于返矿中含有烧结过程中的 低熔点物质,有助于熔融物生成,增加烧结液相 量,改善烧结矿强度,提高成品率,从而提高烧 结矿产质量。
2020/7/5
5
1、优化原料条件,执行科学配比
主要种类:进口精粉主要有巴西精粉、智力
精粉、新西兰精粉等;国内精粉主要有梅山精粉 和其他各类地方小矿。目前常用精粉有巴精、梅 精和各类小矿种。特性分析:精粉是经过选矿球 磨后的高品位含铁原料(与原始矿比较而言), 颗粒细小,在混匀料混合过程中填充在大颗粒矿 料之间的缝隙中,阻碍抽风气流的流动,使氧气 流分布不均匀,燃料燃烧出现偏析,在一定程度 上降低了烧结料的透气性。常用精粉中,巴精品 位较高,梅精含近50%左右的褐铁矿,地方小矿 成分极不稳定且杂质较多。
二、降低烧结返矿的措施
烧结矿粒级是烧结矿的主要属性之一。这种属性 不仅决定了高炉内料柱的气体动力状况,而且也对炉内 的化学反应有很大影响。烧结矿成品粒度均匀,可以增 加粒柱孔隙度,提高透气性和改善气流分布,有利于高 炉冶炼增铁节焦。烧结矿中<10 mm粒级含量越多炉内 煤气利用率越低,高炉焦比越高。高炉生产实践表明: 烧结矿含粉率每升高10%,高炉产量降低6%一8%, 焦比升高0.5%。因此,提高烧结矿强度,减少烧结矿 中5—10 mm粒级含量,最大限度地降低<5 mm粉末, 是高炉强化冶炼、稳定顺行、高产低耗的重要保证。
烧结新技术

烧结返矿控制的研究与实践摘要基于烧结返矿平衡的研究,描述了烧结返矿控制的依据及操作原则。
关键词烧结返矿控制1前言烧结返矿是烧结过程中的重要因素,一方面它对烧结过程的水碳波动产生直接影响,直接影响到烧结过程的优质、高产、低耗;另一方面返矿量的波动形态是非随机的,是烧结过程中不可预知的重要因素之一,因而对它的控制还是十分困难的。
为了保证烧结过程控制的有效性,基于武钢烧结矿原料的实际,对返矿的控制及其影响因素进行了研究,并将控制效果应用于生产现场的实践。
2返矿平衡的研究烧结理论告诉我们,返矿的稳定对稳定烧结混合料的水碳乃至保证烧结矿的产量质量都是至关重要的。
正因为如此,配入的返矿量(RE)和产生的返矿量(RA)如能达到平衡(即B=RA/RE=1),必然对提高烧结矿的产量质量有不可忽视的作用。
生产过程中,返矿量在过高或过低的情况下达到平衡,虽然烧结过程也能进行,但是将达不到降低能耗和提高产量质量指标要求的生产目的。
例如RA高、RE随之也高,则B=RA/RE=1或者接近1,这时烧结矿的产量一定会低而能耗高,质量也会受到影响(因为返矿的化学成分即使在配料相当准确的情况下,由于返矿的波动,烧结矿的成分也难免受到影响)。
当RA很低、RE随之也很低时,B值也会等于或者接近1,此时混合粒度细(除单烧粉矿或粉矿比例较大外),烧结过程透气性差,机速过慢,产量也会低。
只有在适当的返矿配加范围内达到平衡,才能获得优质高产的烧结矿。
因为在烧结混合料中配入适当的返矿量,一方面能改善料层的透气性特别是细精矿烧结时更为明显;另一方面由于返矿中含有已经烧结的低熔点物质,在烧结过程中有助于液相的生成,并能提高烧结矿的机械强度。
但当配入的返矿量超过了一定的限度后,引起水碳较大的波动致使生产率和强度下降。
图1是我们利用生产现场的原料条件,在试验室所作的返矿量与产量质量的变化关系图。
图1返矿量对烧结矿的生产率与机械强度的影响从图1可以看出,返矿量控制在30%~40%之间较为合适,适宜的返矿量根据原料的性质不同而有所差别。
- 1、下载文档前请自行甄别文档内容的完整性,平台不提供额外的编辑、内容补充、找答案等附加服务。
- 2、"仅部分预览"的文档,不可在线预览部分如存在完整性等问题,可反馈申请退款(可完整预览的文档不适用该条件!)。
- 3、如文档侵犯您的权益,请联系客服反馈,我们会尽快为您处理(人工客服工作时间:9:00-18:30)。
矿产资源开发利用方案编写内容要求及审查大纲
矿产资源开发利用方案编写内容要求及《矿产资源开发利用方案》审查大纲一、概述
㈠矿区位置、隶属关系和企业性质。
如为改扩建矿山, 应说明矿山现状、
特点及存在的主要问题。
㈡编制依据
(1简述项目前期工作进展情况及与有关方面对项目的意向性协议情况。
(2 列出开发利用方案编制所依据的主要基础性资料的名称。
如经储量管理部门认定的矿区地质勘探报告、选矿试验报告、加工利用试验报告、工程地质初评资料、矿区水文资料和供水资料等。
对改、扩建矿山应有生产实际资料, 如矿山总平面现状图、矿床开拓系统图、采场现状图和主要采选设备清单等。
二、矿产品需求现状和预测
㈠该矿产在国内需求情况和市场供应情况
1、矿产品现状及加工利用趋向。
2、国内近、远期的需求量及主要销向预测。
㈡产品价格分析
1、国内矿产品价格现状。
2、矿产品价格稳定性及变化趋势。
三、矿产资源概况
㈠矿区总体概况
1、矿区总体规划情况。
2、矿区矿产资源概况。
3、该设计与矿区总体开发的关系。
㈡该设计项目的资源概况
1、矿床地质及构造特征。
2、矿床开采技术条件及水文地质条件。