铝板带连续铸轧
铝合金杆(电缆)连铸连轧工序

铝合金杆(电缆)连铸连轧工序铝连铸连轧生产属于热加工工艺。
是电工用铝加工的第一道生产工序,也是公司生产中的重要生产工序。
它的主要生产功能是把电工用铝锭加工成φ9.5大小的圆铝杆。
连轧机的主要控制参数有:保温炉铝液温度、浇铸下浇煲铝液温度、铸锭温度、冷却水温度、冷却水压力、乳化液温度、乳化液压力、浇铸电机反馈电压、连轧、电机反馈电压、连轧电机反馈电流等主要参数。
铝连铸连轧生产共分为9个生产工序,由3个操作机台来完成。
9个工序为:装料、熔化、保温、精炼、过滤、连续浇铸、剪头、连续轧制、成圈。
3个操作机台是:熔化、浇铸、轧制。
其中装料、熔化、精炼工序为熔化机台部分;过滤、连续浇铸工序为浇铸机台部分;剪头、连续轧制工序为轧制机台部分。
一、装料工序1、电线电缆使用的电工铝纯度一般要求不低于99.70%,并符合GB/T1196—93规定。
为了防止铝单线出现裂纹倾向和单线机械强度不达标,必须使Fe含量大于Si含量,其中Fe含量和Si的比例应控制在1.3~2.0之间。
2.配方2.1若铝锭中Fe含量和Si含量比例达不到1.3或Fe含量小于Si含量时,在尽量少降低铝导电率的条件下为了保证铝线的强度,应对铝进行控铁处理,在铝中加入适当的铝铁合金。
2.2若铝锭中V、Mn、Ti、Cr4种微量元素总量大于0.01%时,需加入铝硼合金。
硼在铝中可以降低V、Mn、Ti、Cr微量元素杂质对导电率的影响。
另外硼的加入可以起细化晶粒的作用。
2.3若Si含量在0.09~0.13%时,在加料过程中加入一定的铝稀土合金,使硅与稀土结合形成化合物,减少游离硅对铝组织结构的危害,提高铝杆的导电性能与机械性能。
2.4对优质产品的化学成分应控制为:Fe<0.15%, Si<0.12%, Cu<0.01%。
杂质总和小于0.29%。
开始上料时,应连续上料到炉满为止,炉膛上部空炉端不允许超过400mm,防止火焰外冲,也不允许装料过满。
采用铝稀土、铝硼和铝铁中间合金作为辅助材料加入,根据原材料和可能的配料结果以及生产实践经验,可以采用一种或几种处理方法,以保证取得最佳的技术经济效果。
铝铸轧工艺及质量研究

第一章铸轧的基本原理第一节铸轧原理的简单介绍连续铸轧工艺是液体铝连续通过旋转的结晶器(铸轧机)制成毛坯同时轧制成为板带的一种金属铸轧方法。
铝带坯连续铸轧工艺是八十年代从国外引进的一种先进的生产工艺连续铸轧即铸造和轧制的过程,通过供料嘴从铸轧辊的一侧源源不段地供应液体金属铝,经过铸轧辊的连续冷却,铸造,轧制,从铸轧辊的另一侧铸轧出铸轧板,同时进,出铸轧区的金属量始终保持平衡,使之达到连续铸轧的稳定过程,具体内容如下。
液体金属铝通过供料嘴进入到铸轧区时,立即与两个相转动的铸轧辊相遇,液体金属铝的热量不段从垂直于铸轧辊辊面的方向传递到铸轧辊中,使附着在铸轧辊表面的液体金属铝的温度急剧下降,因此,液体金属铝在铸轧辊表面被冷却、结晶,凝固。
随着铸轧辊的不段转动,液体金属铝的热量继续向铸轧辊中传递,并不段被铸轧辊中的冷却水带走,晶体不段向液体中生长,凝固层随之增厚。
液体金属铝与两个铸轧辊基本同时接触,同时结晶,其结晶过程和条件相同,形成凝固层的速度和厚度相同,当两侧凝固层厚度随着铸轧辊的转动逐渐增加,并在两个铸轧辊中心线以下相遇时,即完成了铸造过程,并随之受到这两个铸轧辊对其凝固组织的轧制作用,并给以一定的轧制加工率,使液体金属铝被铸造,轧制成铸轧板,这就是连续铸轧的基本原理。
第二节铸轧的工艺流程铝水→静置保温炉→除气箱→过滤箱→供流系统→铸轧机→喷涂系统→剪床→卷取。
1.2.1 熔炼铝锭装入圆炉中,加以高温融化,待熔融后有一定温度时在其中加入金属溶剂并搅拌,使金属溶剂达到一定的含量既可倒炉,将铝水倒到静置炉内。
1.2.2 保温静置炉内的液态铝并不是马上就进入下一道工序需要一点点流过去,因此在静置炉内保温。
1.2.3 除气铝水从静置炉流出在除气箱内除气保温,继续流往下一工序。
除气箱有两个腔体,一个是除气用一个是加热或保温。
1.2.4 过滤过滤是在过滤箱内完成的,过滤箱腔中安装有过滤片,有来过滤,此工序的质量直接关系铸轧板的质量,过滤彻底则无夹渣,不彻底则会有质量问题。
我国铝加工轧制设备未来几年的发展预测
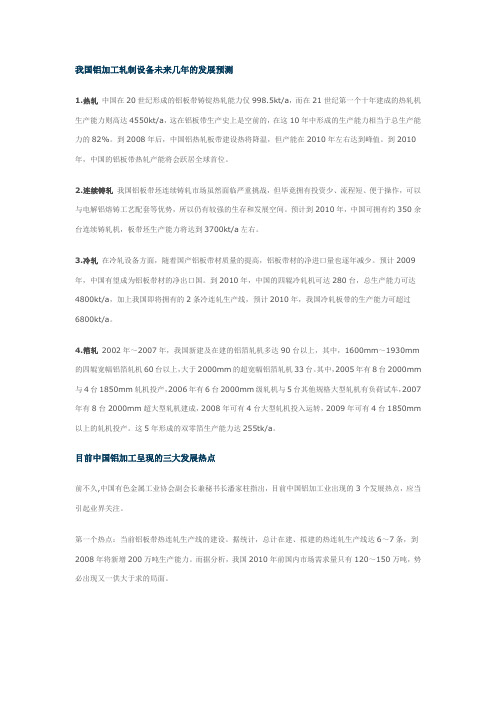
我国铝加工轧制设备未来几年的发展预测1.热轧中国在20世纪形成的铝板带铸锭热轧能力仅998.5kt/a,而在21世纪第一个十年建成的热轧机生产能力则高达4550kt/a,这在铝板带生产史上是空前的,在这10年中形成的生产能力相当于总生产能力的82%。
到2008年后,中国铝热轧板带建设热将降温,但产能在2010年左右达到峰值。
到2010年,中国的铝板带热轧产能将会跃居全球首位。
2.连续铸轧我国铝板带坯连续铸轧市场虽然面临严重挑战,但毕竟拥有投资少、流程短、便于操作,可以与电解铝熔铸工艺配套等优势,所以仍有较强的生存和发展空间。
预计到2010年,中国可拥有约350余台连续铸轧机,板带坯生产能力将达到3700kt/a左右。
3.冷轧在冷轧设备方面,随着国产铝板带材质量的提高,铝板带材的净进口量也逐年减少。
预计2009年,中国有望成为铝板带材的净出口国。
到2010年,中国的四辊冷轧机可达280台,总生产能力可达4800kt/a,加上我国即将拥有的2条冷连轧生产线,预计2010年,我国冷轧板带的生产能力可超过6800kt/a。
4.箔轧2002年~2007年,我国新建及在建的铝箔轧机多达90台以上,其中,1600mm~1930mm 的四辊宽幅铝箔轧机60台以上,大于2000mm的超宽幅铝箔轧机33台。
其中,2005年有8台2000mm 与4台1850mm轧机投产,2006年有6台2000mm级轧机与5台其他规格大型轧机有负荷试车,2007年有8台2000mm超大型轧机建成,2008年可有4台大型轧机投入运转,2009年可有4台1850mm 以上的轧机投产。
这5年形成的双零箔生产能力达255tk/a。
目前中国铝加工呈现的三大发展热点前不久,中国有色金属工业协会副会长兼秘书长潘家柱指出,目前中国铝加工业出现的3个发展热点,应当引起业界关注。
第一个热点:当前铝板带热连轧生产线的建设。
据统计,总计在建、拟建的热连轧生产线达6~7条,到2008年将新增200万吨生产能力。
铝带坯连续铸轧技术新发展——四辊式连续铸轧机

技术开发 铝带坯连续铸轧技术新发展——○四○辊○式○连○续○铸○轧○机 50年代初,由美国亨特公司研制的双辊式铝连续铸轧技术投入工业应用。
由于该技术具有带坯生产流程短,投资少(仅为热轧法的1 3),节能(能耗仅为传统热轧法的40%)等突出特点,因此,一直受到世界各国的重视。
特别是70年代的能源危机使该技术更倍受青睐。
目前世界上铝连续铸轧设备发展到230多台套,它已成为铝板带箔材生产的重要供坯方法。
我国从70年代初研制成功铝连续铸轧技术以来,也有了很大的发展。
目前,我国铝连续铸轧机发展到48台套(包括引进),其供带坯量已占我国铝板带箔材产量的一半左右,已成为我国铝板带箔材生产的主要供坯方法。
但由于该技术的单机产能低,铸轧材料的品种少(目前主要铸轧纯铝)以及存在一定的产品质量问题,影响该技术与传统的热轧开坯技术的竞争。
因此,世界各国都在致力于该技术的新发展或突破。
最近英国的戴维(D aV y)公司研制开发的四辊式铝簿带坯快速连续铸轧技术,就是这些新突破的例证之一。
这台四辊连续铸轧机于1996年末安装在卢森堡的Eu rofo il厂。
这台铸轧机的设计是在经过牛津大学的研究试验并结合瑞典的格兰斯(Granges)公司的F in spong厂的连续铸轧机的发展经验基础上提出的。
他们的研究和经验认为,随着铝的连续铸轧带坯加宽和变薄,连续铸轧的材料向合金方向发展和铸轧速度增加,铸轧机的单位受载力可达1. 25~1.35t mm带宽。
这样高的单位载荷带来如下问题:1.为了铸轧出合格带坯,铸轧辊的辊径要超过1200mm,铸轧辊的总装重量达40t。
这将给铸轧机的安装和起动带来不便,同时使制造费和装运费提高。
铸轧辊属于消费件,这样大的消费件,会给生产成本带来影响。
2.高的单位载荷会使铸轧辊的挠曲和压扁增加,结果造成铸轧带坯的板型变坏和带坯的厚度偏差增大。
为了解决这一问题,往往要给铸轧辊磨成一定的凸度,但是,一定凸度只能适应生产一定的正常板型的带坯。
铝板铸轧工艺

铝板铸轧工艺
铝板铸轧工艺是指将铝合金材料通过铸造、轧制等工艺加工而成的铝板产品。
铝板广泛应用于航空航天、汽车、建筑、电子等领域,具有轻量、耐腐蚀、导热性能好等特点。
铝板铸造工艺包括连续铸造、半连续铸造和离散铸造等,常用的是连续铸造。
铸造时,铝合金材料先通过加热熔化成液态,然后借助铸造机械设备,将铝液注入模具中,在模具内部形成铝板原形。
经过冷却固化后,取出铝板原形,进行下一步的加工工艺。
铝板轧制工艺包括热轧和冷轧两种方式。
热轧适用于铝板材料厚度较大的情况,先将铝板加热至高温,然后通过轧机将铝板辊压成所需要的尺寸。
冷轧适用于铝板材料厚度较薄的情况,先将铝板加热至较低的温度,然后通过辊压机将铝板轧制成所需要的尺寸。
铝板铸轧工艺生产出的铝板产品质量优良,广泛应用于各行各业。
随着科技的不断发展,铝板铸轧工艺也在不断改进和完善,为满足市场需求提供了更多样化的选择。
- 1 -。
铝连铸连轧环评报告

铝连铸连轧环评报告
铝连铸连轧环评报告应由本人根据自身实际情况书写,以下仅供参考,请您根据自身实际情况撰写。
铝连铸连轧环评报告
一、项目概述
本项目为铝连铸连轧生产线建设项目,旨在提高铝材的产量和品质,满足市场需求。
项目位于某工业园区内,总占地面积为100亩,总投资额为2亿元人民币。
二、建设内容
本项目主要建设内容包括:
1. 铝连铸生产线:采用先进的连铸技术,生产高品质的铝材。
2. 铝连轧生产线:采用先进的轧制技术,对铝材进行连续轧制,提高铝材的尺寸精度和表面质量。
3. 辅助设施:包括原料仓库、成品仓库、办公楼、宿舍楼等设施。
三、环境保护
为了保护环境,本项目采取了以下措施:
1. 废气治理:采用活性炭吸附和燃烧法处理生产过程中产生的废气,确保废气达标排放。
2. 废水治理:建立污水处理设施,对生产过程中产生的废水进行处理,确保废水达标排放。
3. 噪声治理:采用低噪声设备,对高噪声设备进行减振降噪处理,确保噪声达标排放。
4. 固废治理:建立固废仓库,对生产过程中产生的固废进行分类处理和处置,确保固废得到合理利用和处置。
四、经济效益
本项目建成后,预计年产值可达到5亿元人民币,年利润可达到1亿元人民币。
同时,本项目的建设还将带动相关产业的发展,增加就业机会,促进当地经济的可持续发展。
五、结论
综上所述,本项目的建设符合国家产业政策和地方经济发展需要,具有良好的市场前景和经济效益。
同时,本项目采取了有效的环境保护措施,确保对环境的影响降到最低。
因此,本环评报告认为本项目的建设是可行的。
铝材连续铸轧工艺技术操作详细说明

3.11、倒炉时铝液温度控制在740℃~750℃(测量前应充分搅拌熔体, 保证炉内熔体温度均匀),温度测量采用在两个炉门分别取三点的平均 值。 3.12、倒炉过程中导流流槽要加盖一层石棉毯,以防热量损失。 3.13、倒炉前后要对熔炼、保温炉导流口、导流竖管及倒流流槽进行检 查清理,倒流流槽内刷滑石粉。 3.14、倒炉结束后应清理炉内铝渣。 3.15、倒炉时间不大于30分钟。 3.16、精炼完毕静置10~15分钟将表面浮渣扒净,扒渣应干净彻底,然 后均匀撒入一层覆盖剂用量为20kg。 3.17、保温炉熔体温度控制在730℃~740℃之间。 3.18、保温炉采用一天一小清三天一大清,保证炉内容积。 3.19、保温炉扒渣、精炼、搅拌时必须进行停电。 4 精练工艺技术规程 4.1、配料完毕后进行精炼,精炼前首先向炉内撒入打渣剂用量 1kg/t.Al.精炼时首先开启氮气阀门(氮气阀门不能过大以防止铝液剧 烈翻腾),再缓慢开启精炼剂阀门,待稳定后将精炼管伸入铝液中,根 据情况调整氮气流量,精炼时精炼管沿“Z”字形进行,到边到沿,精
按照国标要求,如生产卡片中有特殊说明,则按照卡片执行。 9.2 轧辊磨削工艺技术要求 9.2.1新辊生产纯铝时,轧辊磨削凸度:0.20-0.22mm,随着辊径的减 小,凸度增加,每车磨一次,凸度增加0.01-0.02mm 。生产合金时适当 将凸度加大。 9.2.2轧辊磨削粗糙度不大于0.4µm。 9.2.3配对辊直径差:0.005mm。 9.3 烘炉制度 9.3.1 新炉和大修后的炉子必须按照图纸要求验收.
连续铸轧工艺技术操作规程 1 目的及适用范围 1.1 目的:规范工艺操作,保证产品质量。 1.2 适用范围:
本规程适用于Ø960X1850mm倾斜式铸轧机连续铸轧工艺技术规程。 2 连续铸轧工艺流程
铝材连续铸轧工艺技术操作详细说明祥解

连续铸轧工艺技术规程目录1.目的及适用范围2.连续铸轧工艺流程3.熔炼工艺技术规程4.精练工艺技术规程5.铸轧工艺技术规程6.供料嘴组装工艺技术规程7.液化气喷涂工艺技术规程8.炉外除气工艺技术规程9.附件:9.1化学成分控制标准9.2轧辊磨削工艺技术要求9.3烘炉制度、洗炉制度9.4废料分级标准9.5试样切取要求连续铸轧工艺技术操作规程1目的及适用范围1.1 目的:规范工艺操作,保证产品质量。
1.2 适用范围:本规程适用于Ø960X1850mm倾斜式铸轧机连续铸轧工艺技术规程。
2 连续铸轧工艺流程连续铸轧的原料为:铝锭、铝水、待回炉废料,成品为铸轧带材。
其生产工艺流程如下:铝锭、铝水、待回炉废料---熔炼及配料——精练—铸轧—成品铸轧卷3 熔炼工艺技术规程3.1、连续铸轧的原料为:铝水、铝锭、待回炉废料、中间合金、易挥发合金。
3.2、熔炼炉装炉顺序为:小片料---板片料----难熔难挥发合金---铝水---易挥发合金。
3.3、各种炉料应均匀平坦分布在炉子中央或稍靠近烟道及烧咀大火交叉处,同时不可堵住喷嘴。
3.4、使用电解铝水时必须配入30%~35%的冷料。
3.5、装炉炉料应干净,无油污、无杂质、无水分等。
3.6、按要求进行配料和装炉。
加料要迅速,以尽量减少炉内热量损失,同时计算各种牌号废杂料的化学成分及用量。
3.7、当炉料化平后应立即对熔体进行搅拌,加快固体料熔化速度并向炉内均匀撒入一层覆盖剂,用量为1kg/t.Al.3.8、炉料完全融化完毕后进行取样分析,式样在炉子中间部位舀取,取样勺距炉底约100mm,式样在两个炉门共取两个,进行炉前分析,(最终试样以溜槽中所取为准)如果计算值与试样成份差值大于20%时应重新搅拌取样。
3.9、根据炉前分析结果进行配料,加入合金时要分别在两个炉门向不同位置加入,加入合金时铝液温度不得低于720℃。
3.10、向表面撒一层覆盖剂用量为20 kg,关闭炉门进行保温,准备倒炉。
铝板铸轧工艺
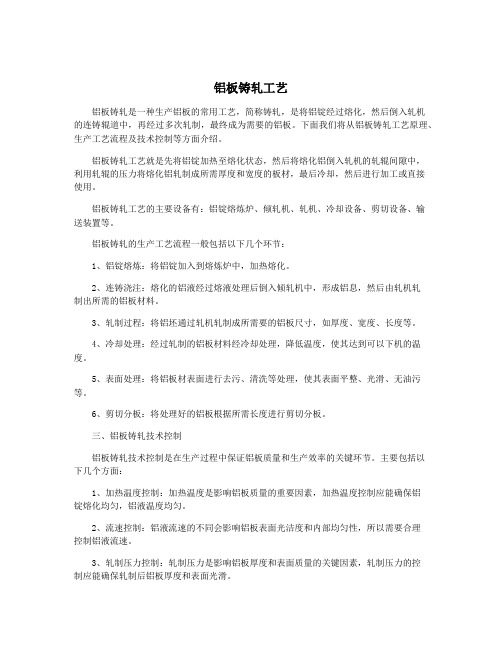
铝板铸轧工艺铝板铸轧是一种生产铝板的常用工艺,简称铸轧,是将铝锭经过熔化,然后倒入轧机的连铸辊道中,再经过多次轧制,最终成为需要的铝板。
下面我们将从铝板铸轧工艺原理、生产工艺流程及技术控制等方面介绍。
铝板铸轧工艺就是先将铝锭加热至熔化状态,然后将熔化铝倒入轧机的轧辊间隙中,利用轧辊的压力将熔化铝轧制成所需厚度和宽度的板材,最后冷却,然后进行加工或直接使用。
铝板铸轧工艺的主要设备有:铝锭熔炼炉、倾轧机、轧机、冷却设备、剪切设备、输送装置等。
铝板铸轧的生产工艺流程一般包括以下几个环节:1、铝锭熔炼:将铝锭加入到熔炼炉中,加热熔化。
2、连铸浇注:熔化的铝液经过熔液处理后倒入倾轧机中,形成铝息,然后由轧机轧制出所需的铝板材料。
3、轧制过程:将铝坯通过轧机轧制成所需要的铝板尺寸,如厚度、宽度、长度等。
4、冷却处理:经过轧制的铝板材料经冷却处理,降低温度,使其达到可以下机的温度。
5、表面处理:将铝板材表面进行去污、清洗等处理,使其表面平整、光滑、无油污等。
6、剪切分板:将处理好的铝板根据所需长度进行剪切分板。
三、铝板铸轧技术控制铝板铸轧技术控制是在生产过程中保证铝板质量和生产效率的关键环节。
主要包括以下几个方面:1、加热温度控制:加热温度是影响铝板质量的重要因素,加热温度控制应能确保铝锭熔化均匀,铝液温度均匀。
2、流速控制:铝液流速的不同会影响铝板表面光洁度和内部均匀性,所以需要合理控制铝液流速。
3、轧制压力控制:轧制压力是影响铝板厚度和表面质量的关键因素,轧制压力的控制应能确保轧制后铝板厚度和表面光滑。
4、冷却水温度和速度控制:冷却是保证铝板质量的关键环节,冷却水温度和速度的不同会影响铝板的冷却效果,所以需要合理控制冷却水温度和速度。
5、表面质量控制:铝板的表面质量是影响其用途的重要因素,应注意表面处理,减少表面缺陷,确保铝板表面质量。
总之,铝板铸轧工艺是一种常用的铝板生产工艺,对铝板的质量和生产效率有重要影响。
铸轧技术概况

第一章铸轧技术概况双辊铸轧是一种用双辊的表面来冷却液态钢水并使之凝固以生产薄带钢的方法,其工艺特点是液体金属在结晶凝固的同时承受压力加工和塑性变形,在很短的时间内完成从液体金属到固态薄带的全过程]1[。
双辊铸轧的平均冷却速度接近100℃/s,因此,其凝固速度要比常规工艺大约快1000倍左右,并能够铸轧出厚度约为常规铸坯1/100的薄带,取消了热轧过程,由于双辊式铸轧冷却速度快,因此,用这种方法有可能生产具有特殊性能的产品。
1.1我国铝连铸连轧机列开发和发展动向铝连铸连轧是把铝的熔炼至热轧六道完全不同的工艺合并为两道的新的铝加工工艺技术,使铝液结晶并产生一定的变形率,从而实现铝及铝合金熔融液态的金属铸轧成6mm~10mm铸轧板材,形成铸轧卷带材的工艺过程。
20世纪60年代,随着这种新的铝加工工艺技术在美国、前苏联等国家先后研制成功,与之匹配的生产设备 --铝连铸连轧机列开始在世界上许多国家进行装备,用这种机列生产铝卷带材,为冷轧薄板和铝箔提供坯料。
由于这种加工工艺的简化,带来了生产设备的大大简化。
用连铸连轧机列生产铝卷带材,具有投资少、见效快、操作简便等一系列优点。
对中小企业,特别是对轻工、民用材极为适用。
正是由于铝连铸连轧工艺及其设备具有上述突出的特点和优势,在今天蓬勃发展的铝加工技术中,特别是在“ 1+3”、“1+4”铝热连轧技术不断应用于工业生产的情况下,连铸连轧工艺依然具有旺盛的生命力,其工艺革新和设备优化具有广阔的空间。
涿神公司作为中国铝加工专用设备的开发研制基地,在20世纪80年代通过与日本株式会社神户制钢所、神钢商事株式会社的合资,积极引进日本神户制钢的先进技术和先进管理经验,成功研制的从Φ650mm到Φ1023m m、辊身长度从1350mm到1900mm的系列连续铸轧机,基本上涵盖了国内铝加工行业所有的规格类型。
公司在1 995年开发研制成功的Φ960 ×1550mm超型连续铸轧机的性能、技术指标都达到甚至超过国际同类设备的水平。
铝带连续铸轧工艺的现状及研究进展

铝带连续铸轧工艺的现状及研究进展高性能铝板带材广泛用于航天、交通运输、信息、包装、印刷、建筑等领域,市场需求巨大.铝板带材坯料主要生产方式为热轧和连续铸轧<1> .热轧产品深加工性能好,可轧制各系铝合金,其最先进的方式是热连轧,但投资巨大,我国尚无铝热连轧生产线,已有的最好的生产方式为双机架热轧,在产品精度、性能上均有一定局限.相比热轧,连续铸轧投资大幅减少,流程短、能耗低.二十世纪八十年代以来在我国迅速发展,成为我国主要的铝板带材坯料生产方式.但是常规铸轧板组织不均匀、深加工性能差,可铸轧的合金品种少,主要用于铝箔毛料和对深加工性能要求不高的部分薄板.我国高性能铝板带材仍需大量进口.1 连续铸轧工艺所面临的关键问题铝带坯连续铸轧是一种低投入、低成本、节能型的短流程生产工艺,其铸轧区的熔体受到激烈的冷却,冷却速度可达10 2~1 0 3℃s,比常规水冷半连续铸锭约高2个数量级<1> .它的组织具有快速凝固与定向结晶的特点,晶体生长的方向性很强.目前用这种方法生产的铝板带各向异性严重,深加工性能远比热轧板差,这就限制了铸轧板的使用范围.连续铸轧是一个很复杂的过程,金属一方面连续散热与凝固,另一方面还受到轧制,而不是铸造过程与热轧过程的简单混合,它们互相影响着.在连续铸轧过程中金属凝固涉及到的学科有材料学、热力学、动力学、振动理论、流体理论、晶体生长理论等问题.它们涉及到两个重大科学问题:(1)铝在连续轧制过程中的凝固规律;(2 )金属凝固过程中的晶体生长与控制.金属凝固过程主要由两部分组成,一是形核过程,它对金属材料晶粒的大小起着至关重要的作用.受金属熔体结构复杂性以及人们对其认识程度的限制,形核理论与控制形核过程的手段还没有达到人们所想象的程度,故金属凝固中的形核问题仍然是金属凝固行为研究的前沿课题之一.金属凝固过程中另一个重要问题是形核后的晶体生长,它关系到凝固后金属组织组成物的形态.由于组成金属材料的晶体形态直接与金属材料的性能有关,如何控制晶体生长,已经成为控制金属材料性能的一个重要手段<2> .因此研究在铸轧过程中铝溶液的晶体凝固规律,对提高铝带材的组织性能与机械性能都具有非常重要的意义.铝带坯连铸技术作为冶金及材料研究领域内的一项前沿技术,目前在工业化应用方面面临的一个主要间题是薄带的质量较差和质量不稳定.其中,薄带的凝固组织对薄带的质量有非常重要的影响,但目前国内外还不能定量阐明工艺因素变化对薄带凝固组织的影响.由于双辊薄带连铸过程中工艺参数间的匹配较复杂,如果采用实验的方法来研究工艺因素变化对薄带凝固组织的影响,则难度高、工作量大.而采用数值模拟的办法,则可以大幅度减少工作量.此外,双辊薄带的凝固组织结构(晶区的几何特征)以及不同晶区内晶粒的几何特征还在很大程度上决定着薄带的工艺性能和使用性能.因此,对双辊薄带凝固组织的数值模拟和薄带凝固组织中各晶区的分布特征、晶区内晶粒几何特征的尺寸表征展开研究具有重要的理论意义和实用意义.2国内外研究现状195 1年,美国亨特—道格拉斯(Hunter-Douglas)公司首次铸轧成了铝带坯,制成了双辊式连续铸轧机.随后,法国彼西涅(Pechiney)公司研制的3C水平式双辊铸轧机也获得成功,从那以后,铝带坯双辊连续铸轧技术和设备得到了迅速的发展.根据Frishchknecht和Maiwald统计目前世界上约有20 %的铝带材的坯料由双辊连续铸轧法生产,大约有1 70多台双辊铸轧机正在工业上应用,其中约有60 %是在北美和欧洲<3> .在2 0世纪70年代以前,铸轧机多为标准型,铸轧辊直径为Φ60 0~70 0mm ,铸轧带坯厚度7mm 左右,铸轧速度小于1 .5m min .80年代以后出现了超型铸轧机,铸轧辊直径可达1 0 0 0mm ,带坯厚度5~1 2mm ,铸轧速度3m min左右,铸轧合金已有纯铝扩大到3 0 0 0系列、5 0 0 0系列软合金.90年代初出现了改进型超型铸轧机,铸轧带坯厚度3mm ,铸轧速度5mm min .由于铸轧带坯尺寸薄和铸轧速度快能进一步发挥快速凝固的特点,使铸轧带坯的晶粒细化,从而获得更好的冶金质量,使这一生产方式为人类带来更大的效益.从90年代以来,国际上开展了对快速超薄铸轧技术的研究<4~6> ,主要有意大利的法塔—亨特(Fata-Hunter)公司、法国的彼西涅(Pechiney )公司、英国的戴维(Davy)公司以及挪威的海德洛(Hydro)公司,他们共同的做法是先在研究开发中心与大学合作进行小型试验,在取得一定成果和经验后,进行中试和大型工业试验,英国Davy公司和牛津(Oxford)大学合作,于1991年推出了第一台快速超薄铝带坯铸轧试验机.1 996年以来,意大利Fata -Hunter 公司、英国Davy公司以及法国Pechiney公司都相继研制出超薄铸轧工业样机<7> ,能铸轧出1mm厚的铸带坯,铸轧速度达1 5m min ,应该说,这是铸轧技术发展中的又一次飞跃.但是由于各国(美国、英国、法国、意大利、挪威) 对快速超薄技术的研究均处于工业试验阶段,试验条件(如装备参数、功能、工艺环境条件等)各不相同,所得结果也有差别,甚至相反,如:Fata-Hunter的试验与Hydro-Lauener公司的试验,对快速超薄铸轧的组织与性能的认识与结果几乎完全相反;在快速超薄铸轧的铸轧机型选择上也存在不同的主张:如Fata-Hunter 采用二辊铸轧机型,英国Davy公司则采用四辊铸轧机型,同时各试验铸轧机的工艺环境条件、设备参数及其范围的确定也不一致(力学参数、辊径、有无外部冷却、铸轧区长度、大小、铸咀开口度大小等).在主要技术规律上尚未形成共识.我国铝带坯连续铸轧技术研究开发工作始于2 0世纪60年代<16 > ,1 964年初进行了双辊下注式铝带坯连续铸轧模拟实验,并于同年铸轧出厚8mm ,宽 2 5 0mm和40 0mm的铝板,1 965年铸轧出宽70 0mm的铝带坯,1 971年由东北轻合金加工厂研制成我国第一台80 0mm水平式下注式双辊铸轧机,1 975年,用铝带坯生产的冷轧板基本上满足了一般深冲制品和箔材毛料的性能要求.1 979年由华北铝加工厂研制成65 0mm×1 3 0 0mm我国第一台亨特式倾斜铸轧机,并于1 981年和1 983年相继研制成65 0mm×1 60 0mm和980mm×1 60 0mm 铸轧机,并通过部级鉴定,标志着我国铸轧技术进入成熟阶段.1 984年中日诼神有色金属加工专用设备有限公司成立,并于1 993年诼神公司为其母公司华北铝业有限公司试制成功我国第一台仿3C 960mm×1 5 5 0mm超型铸轧机.至此国产铸轧机发展成为具有标准型和超型这两种机型,而且铸轧机逐步实现标准化、系列化.随着我国微电子、信息、机械、食品、包装、建筑产业的迅猛发展,我国已成为铝材生产及消费大国,如何提高铝材生产率、降低生产成本、提高我国铝材质量、扩大铝材使用范围已成为迫在眉睫的问题.而快速超薄铸轧的冷却速度远高于现有常规铸轧,铸坯结晶组织的晶粒度和枝晶间距将明显减少,溶质元素在固熔体中的过饱和度提高,因此板带的深冲性能和机械性能得到改善,可生产出具有优良冶金组织和表面质量的优质板带材;同时,可铸轧合金范围也可拓展(如30 0 0系列等铝合金) ,可使铸轧产品的应用市场范围扩大.例如:高精度PS版基,计算机硬盘的铝质基板,高层建筑幕墙板,高精烟箔以及空调箔等.另外,由于铸轧板厚度减薄后,不仅大大减轻了对后面工序———冷轧的压力,解放冷轧机的生产力,大大节省了铝箔生产的投资和能源,而且提高了生产效率,增加了产品的市场竞争力.我国科技界和国际铝加工同行一样已认识到快速超薄铸轧代表了新一代铝加工发展的重要方向和铝加工技术的制高点,我国必须加入到这一研究领域中去.由国内学者钟掘院士担纲技术指导的“铝及铝合金铸轧新技术及设备研制开发”作为国家计委的重大科研项目于1999年初启动,经过以钟掘为首的科研课题组经过一年多的攻关,于2 0 0 0年7月在实验机上成功地铸轧出铸速为1 3 .2m min ,厚度为2mm的铸坯,并开发了铜基合金新型辊套材料、具有在线布流控制技术的新型铸咀、新型复合外冷润滑技术等一系列相关的新技术、新装置、新材料,这些都标志着我国在快速超薄铸轧技术领域已经达到世界领先水平,填补了国内空白.目前用连续铸轧法生产的铝板带在国内已占铝板带生产总量的70% ,在国际上约占铝板带生产总量的40 %左右<7> .国内的连续铸轧设备已由十多年前的3 0多台套,增至目前的5 0多台套.但是,常规的连续铸轧生产工艺目前还只局限于1 系列和3 系列、8 系列的一部分,连续铸轧板带的深拉性能明显地低于热轧开坯板带.这是目前连续铸轧生产工艺必须解决的技术难题.显然,能突破这一难题,将使铝带坯的生产结构发生根本型变化,带来巨大的社会效益与经济效益.对金属凝固规律,国内外都已进行了比较多的研究,如50年代初Tiller,Jackson和Rutter提出的成分过冷理论<8> ,首次将传质和传热因素耦合起来分析凝固过程的组织形态问题,以后发展起来的理论有Jacks on和Hunt提出的枝晶和共晶合金凝固过程扩散场的理论解,Flemings提出局部溶质再分配方程等理论模型,这些理论为控制金属组织奠定了基础,20世纪60年代以来形成了快速凝固技术、定向凝固技术、半固态铸造等先进铸造工艺和技术<9> .3国内开展相关研究的基础与条件据统计,我国现有的铝带坯连续铸轧生产线已超过1 1 0条,总生产能力超过90万吨/年.其中有引进的生产线1 2条,合计生产铝箔毛料质量的重要性和技术标准要求铝箔毛料质量的重要性和技术标准要求Technology Standard and Qualitative Importance of Aluminium Foil Stock黄金法张学平HUANG Jin-fa ZHANG Xue-ping(兰州铝业股份有限公司西北铝业加工有限公司,甘肃陇西748111)摘要:从四个方面阐述铝箔毛料质量对生产高质量铝箔的重要性;指出了在订购铝箔毛料时应提出的技术要求内容。
铝板的铸轧工艺

铝板的铸轧工艺
铝板的铸轧工艺是指将铝合金熔化后,通过铸造和轧制工艺制成不同尺寸和形状的铝板,以满足不同领域的使用需求。
铝板的铸造工艺包括连铸和直铸两种,其中连铸工艺是通过将熔化的铝合金倒入连续铸造机中进行连续铸造,制成厚度较薄的板材;而直铸工艺则是通过将熔化的铝合金倒入铸模中进行单次铸造,制成厚度较厚的板材。
铝板的轧制工艺包括热轧和冷轧两种,其中热轧工艺是将连铸或直铸的铝板在高温下进行轧制,以减小板材厚度并提高其力学性能;而冷轧工艺则是将热轧后的铝板在常温下进行轧制,以提高其表面质量和精度。
此外,还可以采用涂层、拉伸等工艺对铝板进行进一步加工,以满足特定的使用需求。
总的来说,铝板的铸轧工艺是一个复杂的过程,需要精密的设备和技术,并需要根据不同的需求和使用环境选择适合的工艺和材料。
铝板的应用范围广泛,包括航空航天、汽车制造、建筑装饰、电子产品等多个领域。
- 1 -。
5 连续铸轧

5. 连续铸轧5.1 概述现代冶金工业正向着短流程、节能型、连续化、自动化、高质量方向发展。
连铸作为冶金和轧制成形的中间环节,起到承上启下的重要作用。
随着连铸技术的进一步发展,出现了连铸坯热送热装、直接轧制技术和薄板坯连铸连轧技术,使连铸和轧制这两个原先独立存在的工艺过程更加紧密地衔接在一起,因此连铸已不再是一个纯粹的冶金和凝固过程,而是在连铸、凝固的同时伴随着轧制过程。
原来的全凝固压力加工规律和塑性变形本构关系,也发生了相应的变化,该项技术已经成为一种新的边缘科学。
直接将金属熔体“轧制”成半成品带坯或成品带材的工艺称为连续铸轧。
这种工艺的显著特点是其结晶器为两个带水冷系统的旋转铸轧辊,熔体在其辊缝间完成凝固和热轧两个过程,而且在很短的时间内(2~3s)完成的。
它也不同于薄板坯连铸连轧,后者实质上将薄锭坯铸造与热轧连续进行,即金属熔体在连铸机结晶器中凝固成厚约50~90mm的坯后,再在后续的连轧机上连续轧成板材,其铸造和轧制是两道独立的工序。
5.1.1铝带铸轧连续铸轧技术具有投资省、成本低、流程短等优点,从20世纪50年代以来一直在有色金金,特别是铝带的生产上得到了广泛的应用。
该技术可直接铸轧厚度为几毫米的近净形状(near net shape )带材,并且铸轧带无需热轧开坯就可冷轧成更薄的带材或箔材。
1951年美国亨特·道格拉斯(Hunter-Dougalss)公司设计制造成功全球首台工业生产用双辊式铝带坯连续铸轧机。
使这种技术进人工业化生产阶段;1981年中国冶金工业部铝加工试验厂(即现在的华北铝业有限公司的前身)制成φ650m m×1600mm双辊倾斜式铸轧机,并投入试生产。
经过50多年的发展,铝合金带坯的连续铸轧技术取得了长足进展,截止2000年底,全球约有400台连续铸轧机在运转,其中最多的是:法塔亨特铸轧机约135台普基铝业工程公司3C式铸轧机约120台中国的双辊式铸轧机超过60台高速薄带坯铸轧机27台无机架铸轧机约10台这些铸轧机的总生产能力达3600kt/a。
铝及铝合金板带热连轧生产工艺及工程建设浅析
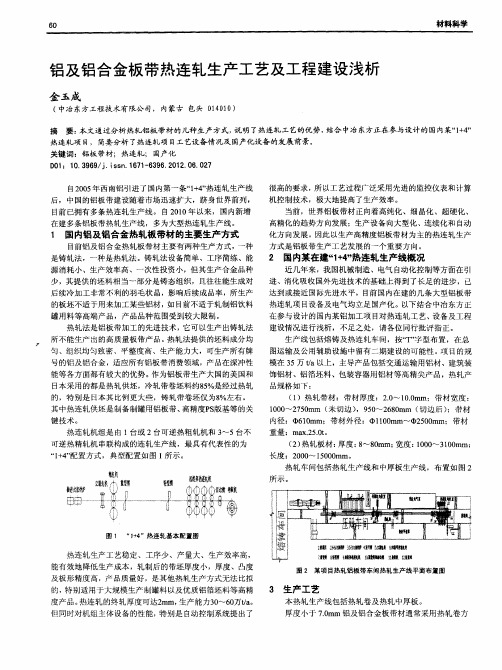
热连轧机组是 由 1台或 2台可逆热粗轧机和 3 ~5台不 可逆热精轧机 串联构成 的连轧生产线 ,最具有代表性的为
“+ ” 置 方 式 , 典 型 配 置 如 图 I 示 。 1 4配 所
图 1 “ + ”热连 轧基 本配 置图 4
愫 一
图 2 某 项 且热轧铝 板 带车 间热 轧生产 线 平面 布置 图
6 0
材料科学
铝及铝合金板带热连轧生产工艺及工程建设浅析
金 玉成
( 中冶 东方工程技术有限公 司,内蒙古 包头 0 1 ) 1 0 4 0 摘 要 : 文通过分析热轧铝板 带材的几种 生产 方式, 本 说明 了热连轧工艺的优 势, 结合 中冶 东方正在参与设 计的 国内某“+ ” 14
差 :< 5 。 士 ℃
热 轧 自动 化使用世界先进的软硬件和网络配置,自动化 系统具有 开放 性、安全可靠 。采用二级方式控 制:一级系统 完成 自动板形 控制、工作辊弯辊控制 、厚度控制 、偏心补偿 控制等功 能;二级控制 系统完成一级系统参考 值设定、轧制 跟踪 、轧制数收集 、报表、轧制分析、系统测试 、产 品分类 、
热连 轧项 目,简要 分析 了热连轧 项 目工艺设备 情况及 国产化设备 的发展前景 。 关键 词:铝板 带材;热连轧;国产化
D : 1 3 6 / . s . 6 1 6 9 . 0 2 0 . 2 0l 0. 9 9 j i n 1 7 — 3 6 2 1 . 6 0 7 s
自2 0 年西南铝引进 了国 内第一条“ + ” 05 1 4 热连轧生产线
洁 除 尘 的 目的 。
4 热连轧主要工艺设备及装备特点
4 1铣 面机 .
型式 :带侧铣装 置的铸锭 铣床 ;生产能力:6 块m。 ~8 4 2立推式推进 式加 热/ . 均热炉 最 高炉气温度 :6 0 5 ℃;最高工作温度 : 5 ℃; 5 0 装炉 量: 6 0、5 0;加热方 式:天然气加热:出料铸锭端各部位温 6t 3 t
铝板带连铸连轧工艺装备及工程建设综述
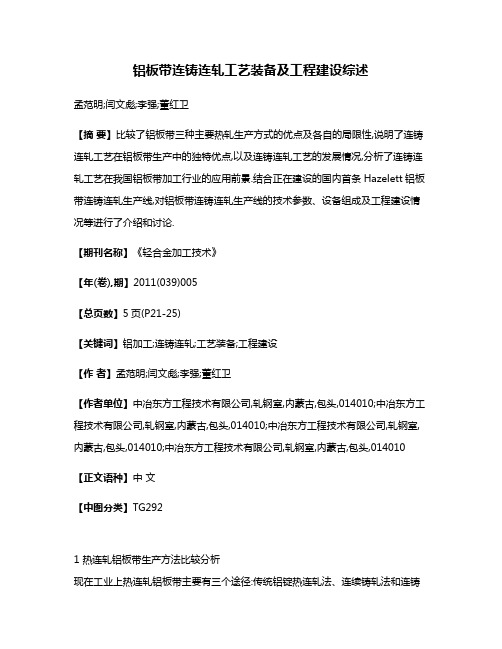
铝板带连铸连轧工艺装备及工程建设综述孟范明;闫文彪;李强;董红卫【摘要】比较了铝板带三种主要热轧生产方式的优点及各自的局限性,说明了连铸连轧工艺在铝板带生产中的独特优点,以及连铸连轧工艺的发展情况,分析了连铸连轧工艺在我国铝板带加工行业的应用前景.结合正在建设的国内首条Hazelett铝板带连铸连轧生产线,对铝板带连铸连轧生产线的技术参数、设备组成及工程建设情况等进行了介绍和讨论.【期刊名称】《轻合金加工技术》【年(卷),期】2011(039)005【总页数】5页(P21-25)【关键词】铝加工;连铸连轧;工艺装备;工程建设【作者】孟范明;闫文彪;李强;董红卫【作者单位】中冶东方工程技术有限公司,轧钢室,内蒙古,包头,014010;中冶东方工程技术有限公司,轧钢室,内蒙古,包头,014010;中冶东方工程技术有限公司,轧钢室,内蒙古,包头,014010;中冶东方工程技术有限公司,轧钢室,内蒙古,包头,014010【正文语种】中文【中图分类】TG2921 热连轧铝板带生产方法比较分析现在工业上热连轧铝板带主要有三个途径:传统铝锭热连轧法、连续铸轧法和连铸连轧法。
1.1 传统铝锭热连轧法传统铝锭热连轧法生产的板带材成分均匀、组织致密、平整度好、产品档次高,这也是其他热轧生产方法无法比拟的。
综合性铝板带生产企业,其坯料大多采用热轧卷,热连轧供坯是制备制罐用铝板带、高精度PS版基材等的主要方法。
但从经济效益上看,热连轧法需要批量生产高档产品才会有比其他两种方法更明显的经济优势。
铝锭热连轧法起点高、成本高,各方面都需要很高的投资。
国内拥有热连轧生产线的只有东北轻合金有限责任公司、西南铝业(集团)公司、南山铝业公司等实力较强的企业[1-2]。
1.2 连续铸轧法连续铸轧法的设备简单、投资小,对于某些铝合金牌号的板带材生产可取代投资大、成本高的传统铝锭热连轧方法;可铸轧出用铝锭轧制法得不到的精细微观组织,从而更适合于某些特殊用途铝材的生产,如散热片、空调铝箔和计算机用磁盘基材等[3-4]。
铝连续铸轧立板工艺研究

铝连续铸轧立板工艺研究铝连续铸轧立板工艺,这个听起来像是个高深的技术名词,但其实它和我们日常生活息息相关。
你知道吧,咱们生活中用的很多铝制品,比如铝合金门窗、厨房用具、汽车配件,背后都有一个“铝连续铸轧立板工艺”的功劳。
这不只是一个技术上的名词,它代表着铝材从原材料到最终成品的一个神奇过程。
要是你想了解它,那咱们就一起聊聊,看看这个工艺是如何把原料变成各种各样的铝制成品的,顺便聊聊它的奥秘。
这个工艺的名字就已经说明了很多事情。
你看,“铝”这个字,是不是一下就能联想到很多东西?铝是非常轻的金属,硬度适中,耐腐蚀,常常用来制造各种产品。
再看“连续铸轧”,别看这俩字很专业,其实它的意思也不复杂。
连续铸造,就是通过一个持续不断的过程,把铝的液态金属慢慢地冷却成固态,这样就能得到铝板的形态。
而“轧”这个字,指的就是压制、碾压的意思,就是通过机械的力量把铝板压得更薄,压出你需要的形状。
“立板”嘛,就是说这整个过程出来的是“板”状的铝材料。
说到这里,大家可能会问,为什么要用这么复杂的方式来处理铝呢?其实呀,这背后可有大大的学问。
铝的生产过程中,温度、压力、冷却速度,甚至是每一个环节的小小差异,都能决定最终铝板的质量。
想想看,铝合金材料应用的地方多了去了,稍微一点点的瑕疵,可能就会影响到产品的使用性能。
所以,必须得精细控制每一个环节。
这就像做菜一样,你控制好了火候,菜肴就鲜香可口;如果火候把握不好,菜肴就可能变味。
好啦,那这个铝连续铸轧立板工艺,怎么就能把一堆铝矿石变成我们手里轻巧的铝板呢?首先是要把铝矿石经过提炼处理,得到纯铝。
然后,将这种纯铝通过高温熔化,变成液态的铝水。
这个液态铝水就像是刚从锅里倒出来的热汤一样,温度高得让人望而生畏。
这些液态铝会被送进铸造设备,冷却下来,变成铝板的雏形。
你能想象吗?这些铝水一滴滴落到模具里,然后迅速凝固,变成一块块长条形的铝锭。
有了铝锭之后,接下来的“轧”工艺就开始了。
这时,铝锭就得接受一对强力的“轧辊”压制了。
节能降耗——哈兹列特铝板带连铸连轧工艺的优势

第2卷 7
第l 期
. 治 痛 色 它 属 f :
S HANGH AINONFERROUS METAL S
V 0 .7 12
NO 1 .
200 6 年 3月
Ma . 2 O O 6 r
文章编 号 :10 05—24 2 0 ) 1 0 8 4 06(0 6 0 —0 1 —0
( )通 常 安装熔 化 炉并在 其 中配 置合 金 ,但 2
亦有 将 熔化 炉与 静止 炉合 并使 用 。 ( )在线 处 理包括 净化 、过滤 、脱氢 及 晶粒 3 细化 等 ,与 直冷 基本 相 同。
1 哈 兹 列 特 工 艺 与直 冷 工 艺 的 比较
欲 阐明 哈 氏工 艺在 节能 降耗 方面 的优 势 ,必
D ai r e m il uigoes n i i ti r Cc n po s s g c s( a y s n t dwt t n o es)adH zl t p cs,teavn gso n n a hw l n ae e r es h da t e f lt o a
连铸 一 l 一3机架 热连 轧一卷 取
哈 氏工 艺 的主要 工艺 参数 及说 明 :
“ 轧开坯 ” 当指 直 冷 铸 坯 的 热 轧 开 坯 。本 文 因 热
篇 幅有 限 ,只从 节能 降耗一个 侧 面作 一定 量 的描 述 ,以阐明 哈 氏工 艺 在这方 面 的 巨大 优势 。
()用 于 熔化 的铝 料可 主要 为原 生铝 锭 ,亦 1 可 主要 为经分 拣 及处 理过 的 旧铝料 。在 与铝 冶炼 厂相 连 时则 主要 采用 电解 铝。
的经 济效益 和社 会效 益。
关键词 :连 续铸 造 ;直冷铸 造 ;铝 板 带 ;节能 ;降耗
浅析连续铸轧法生产铝带坯的现状
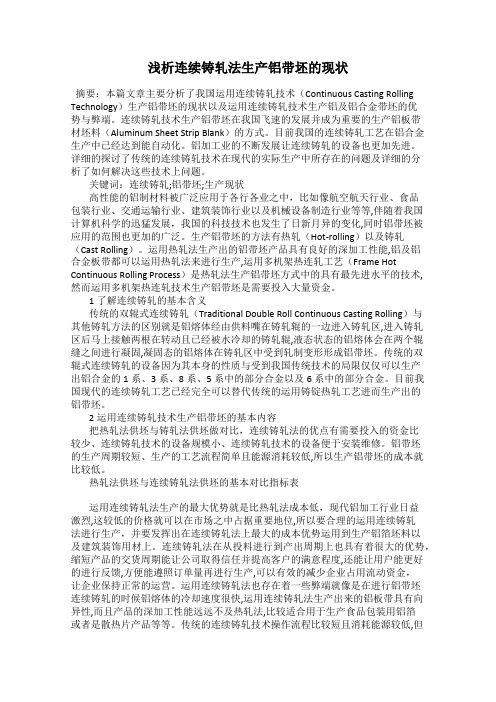
浅析连续铸轧法生产铝带坯的现状摘要:本篇文章主要分析了我国运用连续铸轧技术(Continuous Casting Rolling Technology)生产铝带坯的现状以及运用连续铸轧技术生产铝及铝合金带坯的优势与弊端。
连续铸轧技术生产铝带坯在我国飞速的发展并成为重要的生产铝板带材坯料(Aluminum Sheet Strip Blank)的方式。
目前我国的连续铸轧工艺在铝合金生产中已经达到能自动化。
铝加工业的不断发展让连续铸轧的设备也更加先进。
详细的探讨了传统的连续铸轧技术在现代的实际生产中所存在的问题及详细的分析了如何解决这些技术上问题。
关键词:连续铸轧;铝带坯;生产现状高性能的铝制材料被广泛应用于各行各业之中,比如像航空航天行业、食品包装行业、交通运输行业、建筑装饰行业以及机械设备制造行业等等,伴随着我国计算机科学的迅猛发展,我国的科技技术也发生了日新月异的变化,同时铝带坯被应用的范围也更加的广泛。
生产铝带坯的方法有热轧(Hot-rolling)以及铸轧(Cast Rolling)。
运用热轧法生产出的铝带坯产品具有良好的深加工性能,铝及铝合金板带都可以运用热轧法来进行生产,运用多机架热连轧工艺(Frame Hot Continuous Rolling Process)是热轧法生产铝带坯方式中的具有最先进水平的技术,然而运用多机架热连轧技术生产铝带坯是需要投入大量资金。
1了解连续铸轧的基本含义传统的双辊式连续铸轧(Traditional Double Roll Continuous Casting Rolling)与其他铸轧方法的区别就是铝熔体经由供料嘴在铸轧辊的一边进入铸轧区,进入铸轧区后马上接触两根在转动且已经被水冷却的铸轧辊,液态状态的铝熔体会在两个辊缝之间进行凝固,凝固态的铝熔体在铸轧区中受到轧制变形形成铝带坯。
传统的双辊式连续铸轧的设备因为其本身的性质与受到我国传统技术的局限仅仅可以生产出铝合金的1系、3系、8系、5系中的部分合金以及6系中的部分合金。
铝板带轧制过程

冷轧机主要工艺参数简介
轧制速度:500m/min,高速轧机 1000m/min以上,箔轧机比冷轧机速度快
加工率:视合金成分确定,如3102一般加 工率在40%-60%
张力:生产过程中前后卷取机所给的拉应 力
轧制力:生产过程中,轧辊作用于金属的 压力,一般在500t左右
a
25
五、精整生产流及其简介
铝板带生产过程简介
一、熔铸 二、热轧 三、铸轧 四、冷轧 五、精整
a
1
铝合金牌号简介
1系:99.00%以上工业纯铝,电导性、耐腐蚀性、焊 接性能好、强度低
2系:Al——Cu合金,强度高、耐热性能和加工性能 良好
3系:Al——Mn合金,耐腐蚀性能、焊接性能好、塑 性好
4系:Al——Si合金,耐磨性、高温性能好 5系:Al——Mg合金,耐腐蚀性焊接性能好、抗疲劳
边)
>2.5mm卷材
纵剪
热轧坯料 9.5*1000-
1300mm 6.07.0*1100mm -1300mm
冷连轧
1#/2#清洗
(厚度>3.2mm
冷轧
卷材切边,板
材切边至成品
宽度)
中退
a
板材
1#/2#/3#横 切
冷轧
≤2.5mm卷材
2#拉矫 (拉伸+ 矫直+切
边)
入库
>2.5mm卷材
纵剪
18
本厂3004 合金热轧
润滑采用煤气不完全燃烧的C粉进行润滑, 这也是导致铸轧料表a面比较脏的原因之一 14
铸轧机示意图
a
15
铸轧机
a
16
四、冷轧生产流程及其简介
冷轧指在再结晶温度以下的轧制生产方式
铝合金连续铸轧和连铸连轧技术

铝合金连续铸轧和连铸连轧技术
铝合金连续铸轧和连铸连轧技术
铝合金连续铸轧和连铸连轧技术是一种新兴的材料加工技术,它结合
了铸造和轧制的技术,可以实现铝合金材料的连续加工。
连续铸轧工艺,是把铝合金浇液料加热熔融,然后将熔体倒入熔体模,经过一段时间冷却固化后即可得到铸件,并经过轧制加工,从而提高
了铝合金的力学性能和外观质量。
连铸连轧技术,则是将熔体倒入铸轧机中,一次完成浇注和轧制,实
现熔体的连续加工,从而提高了产量和效率,并可以直接改变铸件的
尺寸和形状,并可以提高质量,降低生产成本。
连续铸轧和连铸连轧技术,不仅可以改善铝合金的力学性能,提高外
观质量,而且可以提高产量,降低成本,一定程度上满足大批量生产
的要求。
它已经被广泛应用于车辆制造、航空航天、电力行业等众多
领域,受到了社会的广泛认可。
总之,铝合金连续铸轧和连铸连轧技术是一种新兴的材料加工技术,
它的应用范围广泛,可以改善铝合金的力学性能,提高外观质量,提
高产量,降低成本,有助于提高生产能力和效率,更好地满足社会对
高品质铝合金产品的需求。
- 1、下载文档前请自行甄别文档内容的完整性,平台不提供额外的编辑、内容补充、找答案等附加服务。
- 2、"仅部分预览"的文档,不可在线预览部分如存在完整性等问题,可反馈申请退款(可完整预览的文档不适用该条件!)。
- 3、如文档侵犯您的权益,请联系客服反馈,我们会尽快为您处理(人工客服工作时间:9:00-18:30)。
铝板带连续铸轧
铝博士网站
液体铝连续通过旋转的结晶器制成毛坯同时轧制成为板带的一种金属铸轧方法(见连续铸轧)。
轻合金连续铸造的工业性试验是20世纪30年代进行的。
1955年美国制成第一台铝带坯连续铸轧机。
后来出现了多种其他类型的连续铸轧机。
与传统的铸锭热轧- 冷轧方法相比,连续铸轧法的主要优点是:能源消耗少、一般可节省40%左右,设备投资小,生产周期短,有利于回收废料,运输费用少等,使生产成本低得很多。
缺点是产品的力学性能较差,质量不如传统方法生产的产品;铸轧品种少;每台机组产量小等。
连续铸轧的产品主要用于食品、建筑、汽车等民用工业。
连续铸轧大多使用工业纯铝和含镁量低的铝镁合金为原料,生产带坯厚度一般为6~10毫米,再经冷轧生产出成品板带及箔材。
连续铸轧工艺有多种类型。
主要差别在于结晶方法不同和结晶器的构造不同,因此,辅助工序和设备结构也就不同。
连续铸轧工艺是指液态金属在辊式结晶器中凝固并进行塑性加工(轧制);而连铸连轧工艺则是金属在结晶器中凝固后,在后续的轧机上进行轧制。
但一般并不严格区分这两个名词,时有混同。
典型的双辊倾斜侧注式工艺流程见图1[ 双辊倾斜侧注式连续铸轧工艺流程示意]。
液体金属由静止炉通过流槽进入可控制液面高度的前箱中。
前箱底部设有联通横浇道,使液体金属经过分配器进入铸嘴,并使金属均匀分布成所要求的宽度。
液体金属由铸嘴流出即与铸轧机冷却的辊面接触。
开始结晶,同时发生15%左右变形,随后经过矫直,卷取成卷。
图2[ 二辊铸轧金属铸轧区示意]
是二辊铸轧金属铸轧区示意图。
铸轧时两辊之间有一个近似梯形的区间。
在此区间要瞬时完成铸和轧两个过程,因此必须严格控制铸轧区长度、浇铸温度、冷却和铸造速度、结晶瞬间液体金属的供给量和液体金属的膨胀压力等工艺因
素,才能使铸轧正常进行。
铝合金的各种连续铸轧方法正在研究发展中。
新型履带式连铸连轧机列已用于工业生产,连续铸轧成厚1425毫米、宽1750毫米带坯,经两机架四辊轧机连轧轧到3~6毫米厚,卷取成卷供冷轧厂作坯料。
可制造包括硬铝合金在内的各种合金。