柴油加氢工艺流程-班长
生物柴油加氢工艺流程
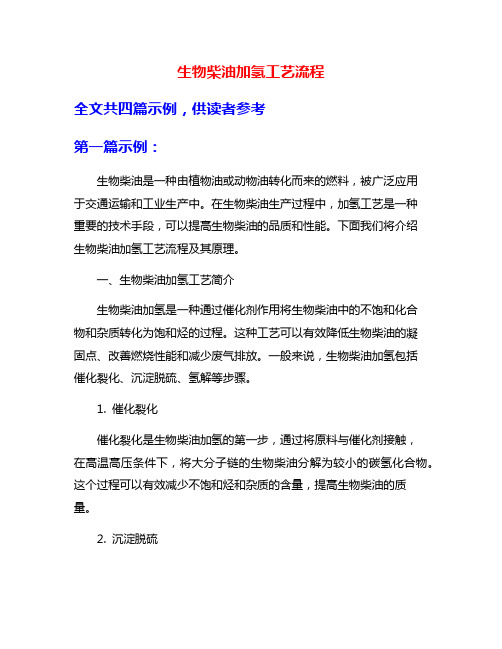
生物柴油加氢工艺流程全文共四篇示例,供读者参考第一篇示例:生物柴油是一种由植物油或动物油转化而来的燃料,被广泛应用于交通运输和工业生产中。
在生物柴油生产过程中,加氢工艺是一种重要的技术手段,可以提高生物柴油的品质和性能。
下面我们将介绍生物柴油加氢工艺流程及其原理。
一、生物柴油加氢工艺简介生物柴油加氢是一种通过催化剂作用将生物柴油中的不饱和化合物和杂质转化为饱和烃的过程。
这种工艺可以有效降低生物柴油的凝固点、改善燃烧性能和减少废气排放。
一般来说,生物柴油加氢包括催化裂化、沉淀脱硫、氢解等步骤。
1. 催化裂化催化裂化是生物柴油加氢的第一步,通过将原料与催化剂接触,在高温高压条件下,将大分子链的生物柴油分解为较小的碳氢化合物。
这个过程可以有效减少不饱和烃和杂质的含量,提高生物柴油的质量。
2. 沉淀脱硫沉淀脱硫是生物柴油加氢工艺的第二步,用于去除生物柴油中的硫化物。
硫化物是生物柴油中的一种有害物质,容易损坏催化剂和污染环境。
通过将生物柴油与脱硫剂反应,可以将硫化物转化为不溶于油中的硫酸盐或硫代硼酸盐,然后通过沉淀分离的方式将其去除。
3. 氢解1. 提高生物柴油的品质和性能,减少废气排放。
2. 可以降低生物柴油的凝固点,提高其在低温条件下的流动性。
3. 减少生物柴油的不饱和烃和杂质含量,减少燃料的积炭和系统堵塞。
4. 延长动力系统和催化转化器的使用寿命,降低维护成本。
生物柴油加氢工艺是一种有效的技术手段,可以提高生物柴油的品质和性能,减少废气排放,符合现代工业生产和环境保护的要求。
未来随着生物能源技术的不断发展,生物柴油加氢工艺将在全球范围内得到更广泛的应用。
第二篇示例:生物柴油是一种由植物油或动物油经过一系列化学反应加工而成的燃料,与传统石油燃料相比,生物柴油具有低碳排放、可再生资源等优点,因此备受关注。
而加氢工艺是生物柴油生产过程中的关键环节,通过加氢反应可以改善生物柴油的质量,提高其燃烧效率,减少有害物质排放。
柴油加氢工艺流程精

柴
油
延迟焦化柴油
加 氢
催化裂化柴油
改
质
装
置
燃料气 石脑油 加氢柴油
总厂燃料气管网 催化重整预分馏 油品调合罐区
加工原理:在柴油加氢精制改质装置,除了发生了加氢脱除杂质的反应, 还发生了改质反应,即使柴油中低十六烷值的组分在高压氢气和催化剂存在 的条件下转化成较高十六烷值的组分,进而提高整体柴油的十六烷值。
职业教育应用化工技术专业教学资源库《汽柴油生产操作》课程
柴油加氢装置工艺流程
郑哲奎
承德石油高等专科学校
职业教育应用化工技术专业教学资源库《汽柴油生 冷却器
排放氢
1
2
原料泵
加热炉
高
低分气
分
罐
低
污水
分 罐
精制油去分馏塔 污水
冷氢
柴油加氢精制装置反应系统工艺流程图 (1 精制反应器 2 改质反应器)
职业教育应用化工技术专业教学资源库《汽柴油生产操作》课程
氢气
高
低分气
分
罐
低
污水
分 罐
精制油去分馏塔 污水
高分罐内分离 三相是氢气、油相和 污水
低分罐内分离 三相是低分气、精制 油和污水
职业教育应用化工技术专业教学资源库《汽柴油生产操作》课程
分馏单元的任务是做好柴油 轻组分含量的控制,即50%蒸发 温度的控制。
馏
反应油从低分罐来
塔
原料泵
回流罐
瓦斯气 石脑油
柴油出装置
柴油加氢精制装置分馏系统工艺流程图
分馏塔底泵
职业教育应用化工技术专业教学资源库《汽柴油生产操作》课程
分离塔顶的气体产出量不应 有变化,如果其产量增高,说明 在反应器内发生的加氢裂化量增 加,需要调整反应温度、压力、 剂油比、空速等因素。
石油催化加氢—催化加氢工艺流程
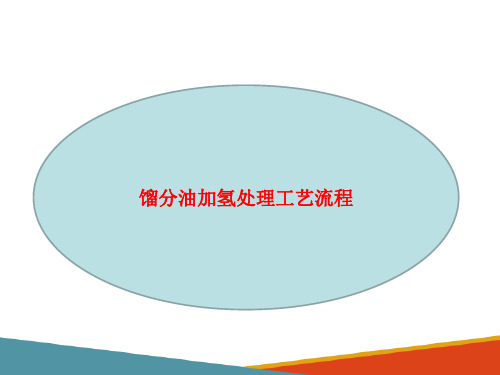
一段串联全循环加氢裂化流程图
• 渣油加氢处理工艺流程与有一般馏分油加氢处理流程有 以下几点不同:
• ①原料油首先经过微孔过滤器,以除去夹带的固体微粒 ,防止反应器床层压降过快;
• ②加氢生成油经过热高压分离器与冷高压分离器,提高 气液分离效果,防止重油带出;
• ③由于一般渣油含硫量较高,故循环氢需要脱除H2S,防 止或减轻高压反应系统腐蚀。
二段加氢裂化工艺原理流程
缺点:工艺流程复杂,装置 投资和操作费用高。
一段加氢裂化工艺流程
一段加氢裂化工艺流程
一、一段一次通过流程 一段一次通过流程的加氢裂化装置主要是以直
馏减压馏分油为原料生产喷气燃料、低凝柴为主, 裂化尾油作高黏度指数、低凝点润滑油料。
高压一段一次通过加氢裂化典型工艺流程图
二.一段串联循环流程 一段串联循环流程是将尾油全部返
馏分油加氢处理工艺流程
馏分油加氢处理工艺流程
馏分油加氢处理,主要应用于二次加工汽油、柴油的精制和含硫、芳烃高的 直馏煤油馏分精制。
汽油馏分加氢:焦化汽油与热裂化汽油中硫、氮及烯烃含量较高,安定性差,辛 烷值低,需要通过加氢处理,才能作为汽油调合组分、重整原料,或乙烯裂解原 料。
煤油馏分加氢:直馏煤油加氢处理,主要是对含硫、氮和芳烃高的煤油馏 分进行加氢脱硫、脱氮及部分芳烃饱和,以改善其燃烧性能,生产合格的 喷气燃料或灯用煤油。
柴油馏分加氢:柴油加氢精制主要是焦化柴油与催化裂化柴油的 加氢精制。加氢脱氮是柴油加氢处理改质的首要目的。
馏分油加氢处理典型工艺流程提
1—加热炉 2—反应器 3—冷却器 4—高压分离器 5—低压分离器 6—新氢储罐 7—循环氢储罐
化工厂班长实习心得

化工厂班长实习心得从某件事情上得到收获以后,就很有必要写一篇心得体会,这样能够培养人思考的习惯。
那么如何写心得体会才能更有感染力呢?以下是本店铺为大家收集的化工厂班长实习心得,希望对大家有所帮助。
化工厂班长实习心得(篇1)时间如梭转瞬即逝,来到山东新和成已经有三个月的时间了,在工作中,经历了很多酸甜苦辣,认识了很多良师益友,获得了很多经验教训,感谢领导给了我成长的空间、勇气和信心,让我从一个懵懂的大学生成长为一名合格的员工。
在这段时间里,通过自身的不懈努力,在工作上取得了长足的进步,但也存在了诸多不足。
回顾即将逝去的三个月,有如下总结:一、在工作中从最基本最简单的离心岗位干起离心顾名思义就是通过加速旋转起到分离的作用。
在离心的工作中我了解了化工生产中的基本操作流程,懂得了什么是操作、为什么操作、该怎样操作。
在工作中我了解了公司的规章制度、安保设施、日常行为规范。
通过岗前培训我知道了公司的企业文化、安全生产法律法规、后勤管理制度、职业病防治、设备知识、TMP培训、质量管理、环保知识等。
企业文化对我影响深远,我最喜欢其中的老师文化,提倡在工作中人人都是我的老师,跟孔老夫子的三人行必有我师不谋而合。
在工作中我是个新手也就是职场菜鸟,需要我学习的还有很多很多只有虚心学习才能不断进步。
在第二个月我调到了缩合岗位。
这对我来说是一个全新的工作,但工作就需要不断的挑战与征服。
缩合反应占据整个生产的龙头地位,只有将反应控制好才能继续下面的操作。
在师父的代领下我首先了解了缩合的工艺流程,在理论的指引下我很快就胜任了这个岗位。
缩合重在控温只有将温度控制在适宜的温度范围内才能增加产量与纯度,如何将温度控制在一度范围内成为我的难题,但在师父的耐心指点与自己的不断总结下终于将温度控制在要求的温度以内。
二、在工作中主要存在的问题1、工作的条理性不够清晰;在工作时间很仓促的情况下,事情多了就要有主次分明的计划,哪些需要立即完成,哪些可以稍后完成,虽然在计划上自己进步很大,但在这方面还有很大的优化空间。
柴油加氢工艺流程
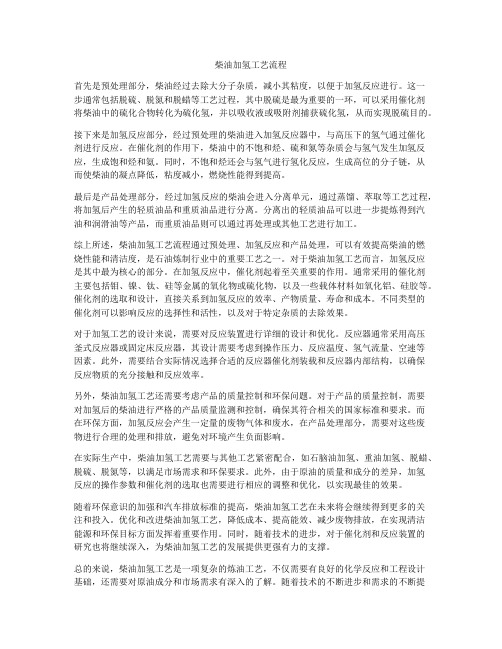
柴油加氢工艺流程首先是预处理部分,柴油经过去除大分子杂质,减小其粘度,以便于加氢反应进行。
这一步通常包括脱硫、脱氮和脱蜡等工艺过程,其中脱硫是最为重要的一环,可以采用催化剂将柴油中的硫化合物转化为硫化氢,并以吸收液或吸附剂捕获硫化氢,从而实现脱硫目的。
接下来是加氢反应部分,经过预处理的柴油进入加氢反应器中,与高压下的氢气通过催化剂进行反应。
在催化剂的作用下,柴油中的不饱和烃、硫和氮等杂质会与氢气发生加氢反应,生成饱和烃和氨。
同时,不饱和烃还会与氢气进行氢化反应,生成高位的分子链,从而使柴油的凝点降低,粘度减小,燃烧性能得到提高。
最后是产品处理部分,经过加氢反应的柴油会进入分离单元,通过蒸馏、萃取等工艺过程,将加氢后产生的轻质油品和重质油品进行分离。
分离出的轻质油品可以进一步提炼得到汽油和润滑油等产品,而重质油品则可以通过再处理或其他工艺进行加工。
综上所述,柴油加氢工艺流程通过预处理、加氢反应和产品处理,可以有效提高柴油的燃烧性能和清洁度,是石油炼制行业中的重要工艺之一。
对于柴油加氢工艺而言,加氢反应是其中最为核心的部分。
在加氢反应中,催化剂起着至关重要的作用。
通常采用的催化剂主要包括钼、镍、钛、硅等金属的氧化物或硫化物,以及一些载体材料如氧化铝、硅胶等。
催化剂的选取和设计,直接关系到加氢反应的效率、产物质量、寿命和成本。
不同类型的催化剂可以影响反应的选择性和活性,以及对于特定杂质的去除效果。
对于加氢工艺的设计来说,需要对反应装置进行详细的设计和优化。
反应器通常采用高压釜式反应器或固定床反应器,其设计需要考虑到操作压力、反应温度、氢气流量、空速等因素。
此外,需要结合实际情况选择合适的反应器催化剂装载和反应器内部结构,以确保反应物质的充分接触和反应效率。
另外,柴油加氢工艺还需要考虑产品的质量控制和环保问题。
对于产品的质量控制,需要对加氢后的柴油进行严格的产品质量监测和控制,确保其符合相关的国家标准和要求。
柴油加氢工艺流程(精)ppt课件
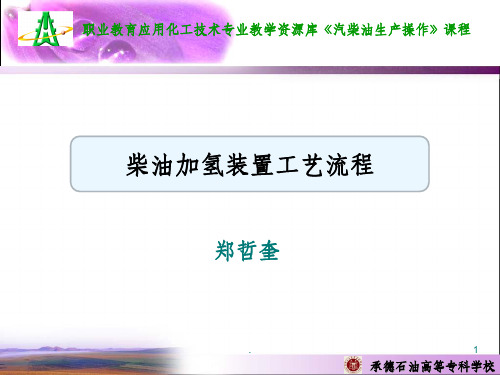
应。或者作为化工洁净原料。
分
馏
塔
反应油从低分罐来
原料泵
回流罐
瓦斯气 石脑油
柴油出装置
柴油加氢精制装置分馏系统工艺流程图
分馏塔底泵
.
6
职业教育应用化工技术专业教学资源库《汽柴油生产操作》课程
分离塔顶的气体产出量不应有
变化,如果其产量增高,说明在
反应器内发生的加氢裂化量增加,
需要调整反应温度、压力、剂油
.
2
职业教育应用化工技术专业教学资源库《汽柴油生产操作》课程
柴油加氢装置加氢精制反应器内发生的反应:
一、加氢脱硫反应: 三、加氢脱氧反应: 五、烯烃饱和反应:
二、加氢脱氮反应: 四、加氢脱金属反应:
但是与催化重整预加氢反应器不同的是,柴油加氢精制反应器内的 反应压力更高,约在8.6MPa左右。
这是因为精制反应器与后面的改质反应器是串联,改质反应是芳烃 开环的反应,需要较高的反应压力。
延迟焦化柴油 催化裂化柴油
装柴 置油
加 氢 改 质
燃料气 石脑油 加氢柴油
总厂燃料气管网 催化重整预分馏 油品调合罐区
加工原理:在柴油加氢精制改质装置,除了发生了加氢脱除杂质的反应,
还发生了改质反应,即使柴油中低十六烷值的组分在高压氢气和催化剂存在
的条件下转化成较高十六烷值的组分,进而提高整体柴油的十六烷值。
炉温的控制有何要求?
为什么是全回流?
组成有哪些?
.
17
职业教育应用化工技术专业教学资源库《汽柴油生产操作》课程
工艺操作参数与常减 压装置常压塔顶回流罐 相同么?
.
18
职业教育应用化工技术专业教学资源库《汽柴油生产操作》课程
柴油加氢精制工艺流程
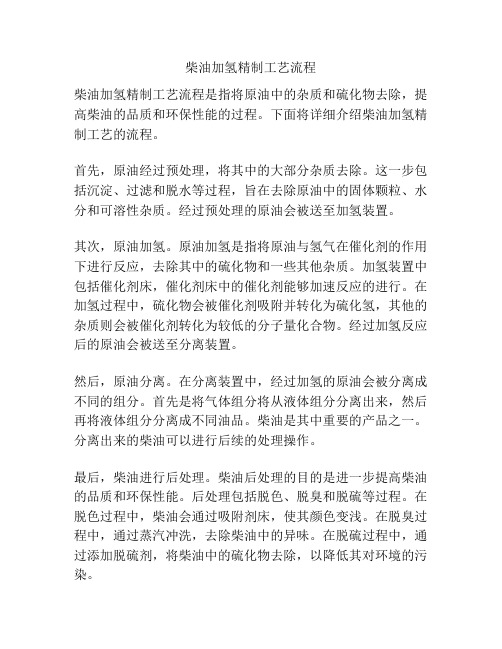
柴油加氢精制工艺流程柴油加氢精制工艺流程是指将原油中的杂质和硫化物去除,提高柴油的品质和环保性能的过程。
下面将详细介绍柴油加氢精制工艺的流程。
首先,原油经过预处理,将其中的大部分杂质去除。
这一步包括沉淀、过滤和脱水等过程,旨在去除原油中的固体颗粒、水分和可溶性杂质。
经过预处理的原油会被送至加氢装置。
其次,原油加氢。
原油加氢是指将原油与氢气在催化剂的作用下进行反应,去除其中的硫化物和一些其他杂质。
加氢装置中包括催化剂床,催化剂床中的催化剂能够加速反应的进行。
在加氢过程中,硫化物会被催化剂吸附并转化为硫化氢,其他的杂质则会被催化剂转化为较低的分子量化合物。
经过加氢反应后的原油会被送至分离装置。
然后,原油分离。
在分离装置中,经过加氢的原油会被分离成不同的组分。
首先是将气体组分将从液体组分分离出来,然后再将液体组分分离成不同油品。
柴油是其中重要的产品之一。
分离出来的柴油可以进行后续的处理操作。
最后,柴油进行后处理。
柴油后处理的目的是进一步提高柴油的品质和环保性能。
后处理包括脱色、脱臭和脱硫等过程。
在脱色过程中,柴油会通过吸附剂床,使其颜色变浅。
在脱臭过程中,通过蒸汽冲洗,去除柴油中的异味。
在脱硫过程中,通过添加脱硫剂,将柴油中的硫化物去除,以降低其对环境的污染。
综上所述,柴油加氢精制工艺流程包括预处理、加氢、分离和后处理等几个步骤。
通过这些步骤,原油中的杂质和硫化物可以被有效去除,从而提高柴油的品质和环保性能。
这是炼油行业中非常重要的一个工艺流程,也是保障柴油质量的关键步骤之一。
柴油加氢工艺流程

柴油加氢工艺流程
概述
柴油加氢是一种重要的燃料精制工艺,通过加氢反应将柴油中的不饱和烃和有
害杂质转化为饱和烃,提高柴油的燃烧性能和清洁度。
本文将介绍柴油加氢工艺的流程及其原理。
工艺流程
原料准备
1.柴油进料
–原料柴油需提前进行预处理,去除水分、固体杂质和硫等杂质。
2.氢气供应
–大量的高纯度氢气是柴油加氢反应中不可或缺的反应气体。
加氢反应器
1.加氢反应器
–将预处理后的柴油和高纯度氢气送入加氢反应器进行反应。
2.催化剂
–通常使用铑、钼等金属催化剂催化反应,将柴油中的不饱和烃加氢成为饱和烃。
催化剂再生
1.再生装置
–催化剂在反应中会因为积聚杂质而失活,需定期送入再生装置进行再生处理。
产品分离
1.产品分离装置
–将加氢反应得到的产品分离出来,其中包括提炼后的高品质柴油及产生的废弃物。
产品处理
1.柴油处理
–对提炼出的高品质柴油进行后续处理,以满足燃料标准和市场需求。
原理解析
柴油加氢工艺利用氢气在催化剂的作用下,将柴油中的不饱和烃和杂质加氢转化为饱和烃。
这一过程中,发生了加氢裂解、加氢饱和等一系列反应,最终得到更高品质的柴油产品。
结语
柴油加氢工艺是一项重要的能源精制技朧,通过对原料柴油进行加氢处理,可以得到更高品质的柴油产品。
随着环保意识的提升,柴油加氢工艺在提高柴油清洁度和燃烧性能方面具有重要意义。
生物柴油加氢工艺流程
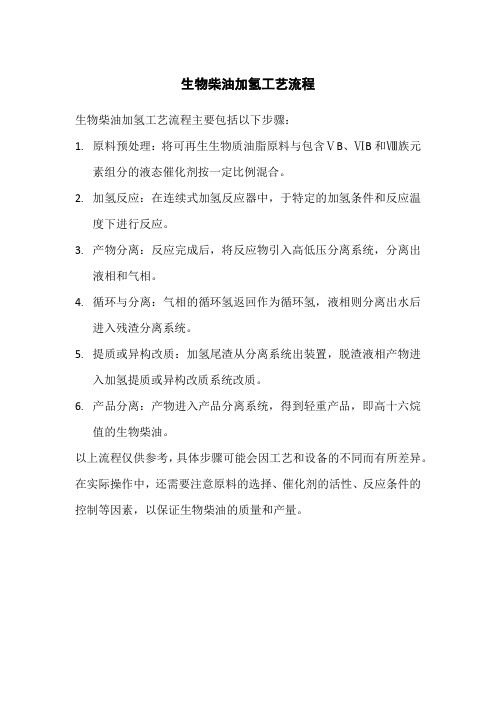
生物柴油加氢工艺流程
生物柴油加氢工艺流程主要包括以下步骤:
1.原料预处理:将可再生生物质油脂原料与包含ⅤB、ⅥB和Ⅷ族元
素组分的液态催化剂按一定比例混合。
2.加氢反应:在连续式加氢反应器中,于特定的加氢条件和反应温
度下进行反应。
3.产物分离:反应完成后,将反应物引入高低压分离系统,分离出
液相和气相。
4.循环与分离:气相的循环氢返回作为循环氢,液相则分离出水后
进入残渣分离系统。
5.提质或异构改质:加氢尾渣从分离系统出装置,脱渣液相产物进
入加氢提质或异构改质系统改质。
6.产品分离:产物进入产品分离系统,得到轻重产品,即高十六烷
值的生物柴油。
以上流程仅供参考,具体步骤可能会因工艺和设备的不同而有所差异。
在实际操作中,还需要注意原料的选择、催化剂的活性、反应条件的控制等因素,以保证生物柴油的质量和产量。
柴油加氢—典型柴油加氢生产工艺(石油加工课件)
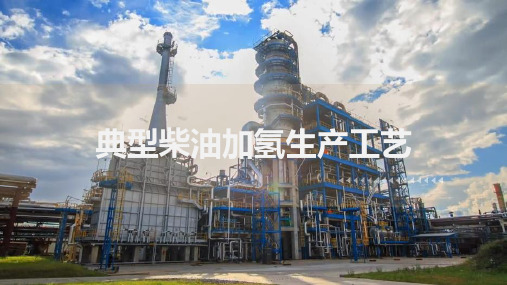
典型柴油加氢生产工艺
二段加氢裂化工艺
在这种工艺流程中有两个反应器,分别装有不同性能的催化剂。第一个反应 器中主要进行原料油的精制;第二个反应器中主要进行加氢裂化反应,形成独立 的两段流程体系。
典型柴油加氢生产工艺
二段加氢裂化工艺
在这种工艺流程中有两个反应器,分别装有不同性能的催化剂。
第一个反应器中主要进行原料油的精制;第二个反 应器中主要进行加氢裂化反应,形成独立的两段流程体 系。二段加氢裂化工艺适合处理高硫、高氮减压渣油, 催化裂化循环油,焦化蜡油或这些油的混合油。
典型柴油加氢生产工艺
单段一次通过流程的加氢裂化装置主要是以直馏减压馏分油为原料生产喷 气燃料、低凝柴油,裂化尾油作高黏度指数、低凝点润滑油料。
工艺流程简单,体积空速相对较高。
所采用的催化剂应具有较强的耐S、N、O等化合物的性能。 原料油的氮含量不宜过高,馏分不能太重,以加工常压瓦斯 油(AGO)/轻减压瓦斯油(LVGO)为宜。 反应温度相对较高,运转周期相对较短。
典型柴油加氢生产工艺
二段加氢裂化工艺特点
二段加氢裂化工艺适合处 理高硫、高氮减压渣油,催化 裂化循环油,焦化蜡油或这些 油的混合油。
第一、二段的反应器、高压分离器和 循环氢(含循环压缩机)自成体系。
补充氢增压机、产品分馏塔两段公用。
工艺流程复杂、投资及能耗相对较高。
对原料油的适应性强,生产灵活性大, 操作运转周期长。 与一段工艺相比,气体产率低、干气少、 目的产品收率高、液体总收率高;产品 质量好,特别是产品中芳烃含量非常低; 氢耗较低。
思政小课堂
随着我国工业化进程的加 快和人们环保意识的不断增长, 对柴油产品的质量提出了更高 的要求,柴油加氢技术不断进 步,不断丰富生产工艺。
柴油加氢工艺流程
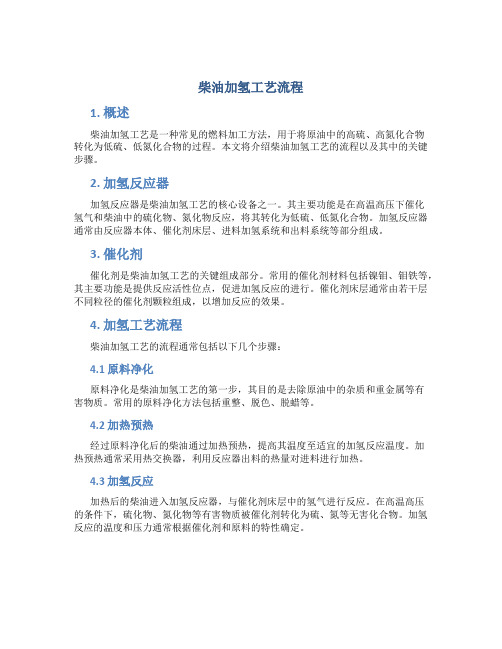
柴油加氢工艺流程1. 概述柴油加氢工艺是一种常见的燃料加工方法,用于将原油中的高硫、高氮化合物转化为低硫、低氮化合物的过程。
本文将介绍柴油加氢工艺的流程以及其中的关键步骤。
2. 加氢反应器加氢反应器是柴油加氢工艺的核心设备之一。
其主要功能是在高温高压下催化氢气和柴油中的硫化物、氮化物反应,将其转化为低硫、低氮化合物。
加氢反应器通常由反应器本体、催化剂床层、进料加氢系统和出料系统等部分组成。
3. 催化剂催化剂是柴油加氢工艺的关键组成部分。
常用的催化剂材料包括镍钼、钼铁等,其主要功能是提供反应活性位点,促进加氢反应的进行。
催化剂床层通常由若干层不同粒径的催化剂颗粒组成,以增加反应的效果。
4. 加氢工艺流程柴油加氢工艺的流程通常包括以下几个步骤:4.1 原料净化原料净化是柴油加氢工艺的第一步,其目的是去除原油中的杂质和重金属等有害物质。
常用的原料净化方法包括重整、脱色、脱蜡等。
4.2 加热预热经过原料净化后的柴油通过加热预热,提高其温度至适宜的加氢反应温度。
加热预热通常采用热交换器,利用反应器出料的热量对进料进行加热。
4.3 加氢反应加热后的柴油进入加氢反应器,与催化剂床层中的氢气进行反应。
在高温高压的条件下,硫化物、氮化物等有害物质被催化剂转化为硫、氮等无害化合物。
加氢反应的温度和压力通常根据催化剂和原料的特性确定。
4.4 冷却分离加氢反应后的柴油通过冷却分离,将气相和液相分离。
常用的冷却分离设备包括冷凝器、分离器等。
通过冷却分离,可以将氢气收集回收,减少资源浪费。
4.5 气液分离冷却分离后,得到的液相为加氢后的柴油产品,而气相则包含未反应的氢气、碳氢化合物等。
气液分离的目的是将氢气进行回收,同时将其他气态组分进行处理。
4.6 产品处理加氢后得到的柴油产品需要进行进一步处理,以满足燃料标准要求。
产品处理通常包括脱硫、脱氮、脱氧等步骤,以降低产物中的硫、氮和氧含量。
4.7 产品贮存与装运经过处理后的柴油产品可以进行贮存和装运。
加氢裂化车间安全生产岗位责任制

加氢裂化车间安全生产岗位责任制加氢裂扮装置是我公司180万吨/年加氢裂化项目的一部分,是生产国V柴油和重整原料的重要生产装置,生产过程具有高温、高压、易燃易爆、有毒等特点,同时典型的量段式加氢裂化设备多、流程简单,装置平安平稳生产的要求更高。
另外,本装置原料和产品、氢源、蒸汽动力等重要生产条件受外界因素影响较大。
因此,为了实现装置平安高效平稳生产,实现车间日常管理规范化,特制定本制度。
本制度适用于山东****加氢裂化车间的日常管理。
1、负责组织车间生产管理,完成生产任务,负责新装置的试车,车间工艺的优化、成熟。
2、负责平安、质量管理,保质保量、平安生产。
3、负责生产设备各产品间的协调工作。
4、负责车间的工艺、平安、劳动纪律、文明卫生的考核工作;搞好技术学习和岗位练兵,结合生产现状提出改进工艺、设备和管理的合理化建议。
5、娴熟把握本车间的操作规程和平安防护措施;处理车间突发性事故。
6、加强设备维护保养。
7、负责贯彻执行各项规章制度;组织车间成员学习,提高操作技能,对下属人员检查、督促、考核、激励。
8、准时参与、召开车间各会议,仔细传达、通报公司各项政策和打算9、协调与本车间生产相关的各部门,保证生产进度。
10、完成领导交办的其他任务。
1、建立健全车间生产装置工艺技术管理制度。
组织制(修)订生产装置的工艺操作规程、工艺卡片、开停工方案,并监督检查执行状况。
负责各种生产运行原始记录的管理。
2、负责生产过程的工艺技术管理、工艺纪律检查和考核;组织生产装置工艺技术标定,组织技术攻关工作。
3、组织质量事故、组织生产事故调查,并将调查报告报平安环保部备案。
参加生产、设备事故等其他相关事故的调查处理。
4、搞好生产方案指标的分降落实工作、负责月度生产方案的实施。
依据公司生产作业方案和领导布置,准时下达各生产装置的生产方案修改的指令,通知并督促各装置提降处理量,确保生产方案的完成。
5、负责处理生产过程中消失的问题,重大问题准时向有关领导汇报。
柴油加氢流程

柴油加氢流程
柴油加氢是一种常见的炼油工艺,通过加氢反应可以提高柴油
的品质,减少硫、氮等有害物质的含量,提高燃烧效率,降低环境
污染。
下面我们将介绍柴油加氢的流程。
首先,原料柴油通过预处理单元进行预处理,去除其中的杂质
和硫、氮等有害物质。
在预处理单元中,柴油会被加热至一定温度,然后进入加氢反应器。
在加氢反应器中,柴油与氢气在催化剂的作用下发生加氢反应,硫、氮等有害物质被还原成相对无害的化合物,同时分子结构也发
生改变,提高了柴油的品质。
加氢反应的温度、压力和催化剂的选
择都对反应的效果有着重要影响。
经过加氢反应后的柴油进入分离装置,通过升温、蒸馏等操作,将加氢后的柴油与副产物进行分离,得到提质后的柴油产品。
同时,副产物中的氢气也会被回收利用,提高了资源利用效率。
最后,提质后的柴油产品需要经过一系列的检测和处理,确保
其符合相关的质量标准,然后可以被用于各种柴油发动机的燃烧,
提供动力。
总的来说,柴油加氢流程是一种重要的炼油工艺,通过加氢反
应可以提高柴油的品质,减少环境污染,对于能源的可持续发展具
有重要意义。
加氢流程的优化和改进也是炼油企业不断努力的方向,希望能够在未来为社会提供更加清洁、高效的柴油产品。
柴油加氢工艺流程-班长

装置简介
设计能力
装置公称规模为120×104t/a,实际处理量为113.43×104t/a,投产于2003年7月,原 设计能力为120万吨/年,主要产品有粗汽油、精制柴油,副产品为加氢干气。2004年6月 进行掺炼焦化汽油改造,装置实际加工能力为104×104t/a。装置主要由反应和分馏两部 分组成。
CnH2n + H2→CnH2n+2 烯烃饱合也为耗氢和放热反应,原料油溴价每降低一个单位,放热8.11×103焦/ 公斤进料,耗氢量约为1.07-1.42NM3/M3原料。
d 脱氧反应:
加氢原料油中含有酚、过氧化物、酮等化合物,它们在加氢精制条件下发生下列 反应。
工艺流程
反应部分
原料油自装置外来,在原料油缓冲罐(V1101)液面控制下,通过原料 油过滤器(FI1101)进行过滤,除去原料中大于25μm的颗粒。过滤后的原料 油进入原料油缓冲罐,然后经加氢进料泵(P1101A、B)升压后,在流量控制 下,与混合氢混合作为反应进料,依次与反应流出物经两个台位的反应流出 物/反应进料换热器(E1103A、B和E110l)换热后,进入反应进料加热炉 (F1101)加热至反应所需温度,再进入加氢精制反应器(R1101),在催化 剂作用下进行脱硫、脱氮、烯烃饱和、芳烃饱和等反应。该反应器设置两个 催化剂床层,床层间设有注急冷氢设施。来自R1101的反应流出物,经反应流 出物/反应进料换热器(E1101、E1103A,B)、反应流出物/分馏塔进料换 热器(E1102)依次与反应进料、分馏塔进料、反应进料换热,然后经反应流 出物空冷器(A1101)冷却至49℃进入高压分离器(V1102)。为了防止反应 流出物中的铵盐在低温部位析出,通过注水泵(P1102A、B)将脱盐水注至 A1101上游侧的管道中。冷却后的反应流出物在高压分离器(V1102)中进行 油、气、水三相分离。高分气进入循环氢压缩机(C1101)升压后分两路:一 路作为急冷氢进入反应器;一路与来自新氢压缩机(C1102A、B)的新氢混合, 混合氢与原料油混合作为反应进料。含硫、含氨污水自V1102底部排出,至装 置外酸性水汽提装置处理。高分油相在液位控制下经调节阀减压后进入低压 分离器(V1103)。V1103闪蒸出的低分气至分馏部分与脱硫化氢汽提塔顶气 合并送出装置进行脱硫处理。低分油经柴油/低分油换热器(E1106A~D)与
柴油加氢工艺流程(精)
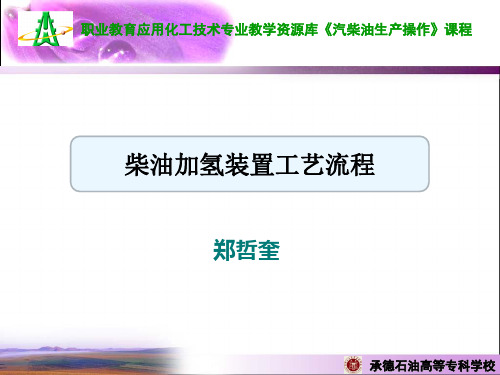
瓦斯气
分馏单元的任务是做好柴油 轻组分含量的控制,即50%蒸发 温度的控制。
具体轻组分控制量为多少? 要看油库待调和的直馏柴油的情 况而定。
反应油从低分罐来
回流罐
石脑油
分 馏 塔
原料泵 柴油出装置
柴油加氢精制装置分馏系统工艺流程图
分馏塔底泵
职业教育应用化工技术专业教学资源库《汽柴油生产操作》课程
瓦斯气 回流罐
燃料气 石脑油 加氢柴油
延迟焦化柴油 催化裂化柴油
加工原理:在柴油加氢精制改质装置,除了发生了加氢脱除杂质的反应, 还发生了改质反应,即使柴油中低十六烷值的组分在高压氢气和催化剂存在 的条件下转化成较高十六烷值的组分,进而提高整体柴油的十六烷值。
职业教育应用化工技术专业教学资源库《汽柴油生产操作》课程
工艺操作参数与常减 压装置常压塔顶回流罐 相同么?
职业教育应用化工技术专业教学资源库《汽柴油生产操作》课程
航煤汽提塔
组成特点?
职业教育应用化工技术专业教学资源库《汽柴油生产操作》课程
如果没有航煤生产任料 中, 正十六烷的体积百分数。
正十六烷 α-甲基萘
十六烷值为100
十六烷值为0
碳链越直,结构越简单的烃类,其十六烷值越高。
职业教育应用化工技术专业教学资源库《汽柴油生产操作》课程
循环氢压缩机 排放氢 新氢 冷却器 高分罐 低分气 1
2
稳
低分罐
定 塔
原料泵 加热炉 精制油去分馏塔
这里的石脑油,杂质含量很 少,可以作为精制油直接进入催 化重整装置重整反应系统发生重 整反应。或者作为化工洁净原料。
石脑油
分 馏
反应油从低分罐来
塔
原料泵 柴油出装置
加氢精制基础知识

加氢精制1、加氢(也称氢化)是指在催化剂的存在下,某种化学物质与氢的加和反应,即称之为加氢反应。
2、加氢技术主要是在炼厂加工过程中以石油馏分为原料的加氢反应,其又可分为加氢精制和加氢裂化两个领域。
3、“加氢裂化”的概念是指通过加氢反应,使原料油中大于或等于10%以上的分子变小的一些加氢过程。
如典型的高压加氢裂化、缓和加氢裂化和中压加氢改质等反应。
4“加氢处理”属于加氢精制的范畴,它所指的是某些反应仍以加氢精制为主,允许有轻度的裂解,可以为下游工艺过程提供优质进料为主的反应。
显然可以广义地称之为加氢精制,但为了与定义的加氢精制有所区别,将此过程成为“加氢处理”,也可以把加氢处理理解为稍有些加氢裂化的加氢精制过程。
5、“加氢精制”过程则是在保持原油分子骨架结构不发生变化或变化很小的情况下,将杂质脱除,以达到改善油品质量为目的的加氢反应。
即“在有催化剂和氢气存在的条件下,将石油馏分中含硫、氮、氧及金属的非烃类组分加氢脱除以及烯烃、芳烃发生加氢饱和反应”。
加氢精制是改善和提高石油产品质量的主要手段之一。
加氢精制的主要目的是脱除油品中的硫、氮、氧等杂原子以及油品中的金属。
加氢精制主要用于油品的精制,通过精制来改善油品的性能;此外,加氢精制还用来处理性能较差的馏分油、重油和渣油等,以使其满足催化裂化、催化重整等工艺对原料的要求。
(1) 加氢精制的化学反应加氢精制的主要反应有加氢脱硫、加氢脱氮、加氢脱氧、加氢脱金属和烯烃饱和等。
①加氢脱硫。
在加氢精制条件下,石油馏分中的硫化物进行氢解,转化成相应的烃和H2S,从而使硫杂原子脱除。
硫醇、硫醚、二硫化物等链状硫化物宜在比较缓和的条件下进行反应,而噻吩、苯并噻吩等环状硫化物加氢脱硫比较困难,需要较为苛刻的反应条件。
②加氢脱氮。
石油馏分中的氮化物可分为三类:脂肪胺及芳香胺,吡啶、喹啉类型的碱性杂环化合物,吡咯、茚及咔唑类型的非碱性杂环化合物。
其中,脂肪胺类的反应能力最强,芳香胺(烷基苯胺)比较难反应。
柴油加氢装置工艺流程4篇
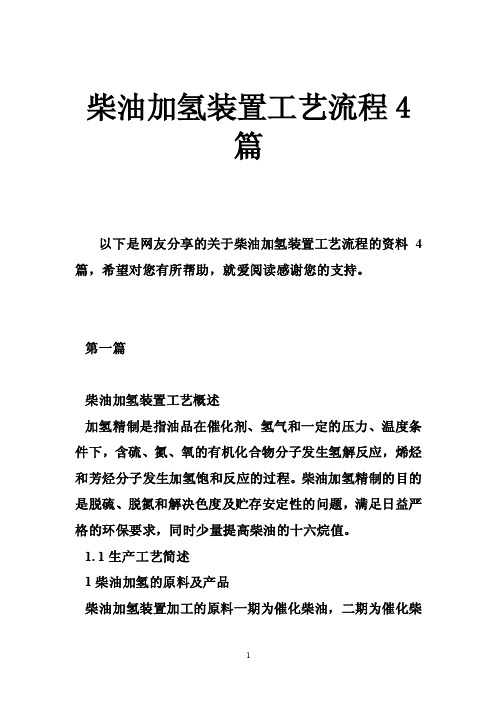
柴油加氢装置工艺流程4篇以下是网友分享的关于柴油加氢装置工艺流程的资料4篇,希望对您有所帮助,就爱阅读感谢您的支持。
第一篇柴油加氢装置工艺概述加氢精制是指油品在催化剂、氢气和一定的压力、温度条件下,含硫、氮、氧的有机化合物分子发生氢解反应,烯烃和芳烃分子发生加氢饱和反应的过程。
柴油加氢精制的目的是脱硫、脱氮和解决色度及贮存安定性的问题,满足日益严格的环保要求,同时少量提高柴油的十六烷值。
1. 1生产工艺简述1柴油加氢的原料及产品柴油加氢装置加工的原料一期为催化柴油,二期为催化柴油、焦化柴油和焦化汽油的混合油,混合原料的硫含量和溴价均较高。
根据加工原料的情况和用户对产品质量的要求,本1.1. 2柴油加氢工艺1.1.2.1反应系统自罐区来的原料油在原料油缓冲罐的液面和流量控制下,通过原料油过滤器除去原料中大于25微米的颗粒后,进入原料油缓冲罐,原料油缓冲罐用燃料气气封。
自原料油缓冲罐来的原料油经加氢进料泵增压后,在流量控制下,经反应流出物/原料油换热器换热后,与混合氢混合进入反应流出物/反应进料换热器,然后经反应进料加热炉加热至反应所需温度,进入加氢精制反应器。
该反应器设置两个催化剂床层,床层间设有注急冷氢设施。
自加氢精制反应器出来的反应流出物经反应流出物/反应进料换热器、反应流出物/低分油换热器、反应流出物/原料油换热器依次与反应进料、低分油、原料油换热,然后经反应流出物空冷器及水冷器冷却至45℃,进入高压分离器。
为了防止反应流出物中的铵盐在低温部位析出,通过注水泵将脱氧水注到反应流出物空冷器上游侧的管道中。
冷却后的反应流出物在高压分离器中进行油、气、水三相分离。
高分气(循环氢)经循环氢压缩机入口分液罐分液后,进入循环氢压缩机升压,然后分两路:一路作为急冷氢进反应器;一路与来自新氢压缩机的新氢混合,混合氢与原料油混合作为反应进料。
含硫、含氨污水自高压分离器底部排出至酸性水汽提装置处理。
高分油相在液位控制下经减压调节阀进入低压分离器,其闪蒸气体排至工厂燃料气管网。
精选范文--加氢裂化车间安全生产岗位责任制

加氢裂化车间安全生产岗位责任制加氢裂化装置是我公司180万吨/年加氢裂化项目的一部分,是生产国V柴油和重整原料的重要生产装置,生产过程具有高温、高压、易燃易爆、有毒等特点,同时典型的量段式加氢裂化设备多、流程复杂,装置安全平稳生产的要求更高。
另外,本装置原料和产品、氢源、蒸汽动力等重要生产条件受外界因素影响较大。
因此,为了实现装置安全高效平稳生产,实现车间日常管理规范化,特制定本制度。
本制度适用于山东****加氢裂化车间的日常管理。
1、负责组织车间生产管理,完成生产任务,负责新装置的试车,车间工艺的优化、成熟。
2、负责安全、质量管理,保质保量、安全生产。
3、负责生产设备各产品间的协调工作。
4、负责车间的工艺、安全、劳动纪律、文明卫生的考核工作;搞好技术学习和岗位练兵,结合生产现状提出改进工艺、设备和管理的合理化建议。
5、熟练掌握本车间的操作规程和安全防护措施;处理车间突发性事故。
6、加强设备维护保养。
7、负责贯彻执行各项规章制度;组织车间成员学习,提高操作技能,对下属人员检查、督促、考核、激励。
8、及时参加、召开车间各会议,认真传达、通报公司各项政策和决定9、协调与本车间生产相关的各部门,保证生产进度。
10、完成领导交办的其他任务。
1、建立健全车间生产装置工艺技术管理制度。
组织制(修)订生产装置的工艺操作规程、工艺卡片、开停工方案,并监督检查执行情况。
负责各种生产运行原始记录的管理。
2、负责生产过程的工艺技术管理、工艺纪律检查和考核;组织生产装置工艺技术标定,组织技术攻关工作。
3、组织质量事故、组织生产事故调查,并将调查报告报安全环保部备案。
参与生产、设备事故等其他相关事故的调查处理。
4、搞好生产计划指标的分解落实工作、负责月度生产计划的实施。
根据公司生产作业计划和领导安排,及时下达各生产装置的生产方案修改的指令,通知并督促各装置提降处理量,确保生产计划的完成。
5、负责处理生产过程中出现的问题,重大问题及时向有关领导汇报。
炼油厂采用的主流石油加工工艺——催化加氢工艺详解

3、反应空速
空速的大小反映了反应器的处理能力和反应时间。空速越大,装置的 处理能力越大,但原料与催化剂的接触时间则越短,相应的反应时间 也就越短。因此,空速的大小最终影响原料的转化率和反应的深度。
1、加氢处理催化剂 加氢处理催化剂中常用的加氢活性组分有铂、钯、镍等金属和钨、钼、 镍、钴的混合硫化物,它们对各类反应的活性顺序为: 加氢饱和 Pt,Pb﹥Ni﹥W-Ni﹥Mo-Ni﹥Mo-Co﹥W-Co 加氢脱硫 Mo-Co﹥Mo-Ni﹥W-Ni﹥W-Co 加氢脱氮 W-Ni﹥Mo-Ni﹥Mo-Co﹥W-Co 加氢活性主要取决于金属的种类、含量、化合物状态及在载体表面的 分散度等。 活性氧化铝是加氢处理催化剂常用的载体。
目前炼油厂采用的加氢过程主要分为两类:一类是加氢处理,一 类是加氢裂化。
用这种技术的目的在于脱除油品中的硫、氮、氧及金属等杂质, 同时还使烯烃、二烯烃、芳烃和稠环芳烃选择加氢饱和,从而改善原 料的品质和产品的使用性能。此外,加氢裂化的目的在于将大分子裂 化为小分子以提高轻质油收率,同时还除去一些杂志。其特点是轻质 油收率高,产品饱和度高,杂质含量少。 作用机理 吸附在催化剂上的氢分子生成活泼的氢原子与被催化剂削弱了键的 烯、炔加成。烯烃在铂、钯或镍等金属催化剂的存在下,可以与氢加 成而生成烷烃。加氢过程可分为两大类:
4、催化剂再生 国内加氢装置一般采用催化剂器内再生方式,有蒸汽-空气烧焦法和 氮气-空气烧焦法两种。 再生过程包括以下两个阶段: ①再生前的预处理 在反应器烧焦之前,需先进行催化剂脱油与加热炉清焦。 ②烧焦再生 通过逐步提高烧焦温度和降低氧浓度,并控制烧焦过程分三个阶段完 成。
柴油加氢工艺流程

柴油加氢工艺流程柴油加氢工艺流程柴油加氢是一种常用的炼油工艺,通过将柴油与氢气在催化剂的存在下进行反应,可以降低柴油中的硫、氮等杂质含量,提高柴油的质量和清洁度。
下面将介绍柴油加氢的工艺流程。
首先,在柴油加氢工艺中,需要收集原料柴油。
原料柴油一般是从炼油厂的蒸馏塔中分离出来的,含有一定的硫、氮等杂质。
为了确保柴油加氢的效果,原料柴油需要进行预处理。
预处理主要是通过加热和混合来去除柴油中的杂质和水分。
经过预处理后的柴油进入加氢反应器。
加氢反应器是柴油加氢工艺的核心部分。
在加氢反应器中,原料柴油与氢气通过催化剂进行反应。
催化剂的选择非常重要,通常使用的是铜、铁或锌等金属的氧化物。
氢气在催化剂的作用下与柴油中的硫、氮等杂质发生反应,生成硫化氢和氨等无害物质。
同时,催化剂还可以去除柴油中的饱和度较低的分子,使柴油的分子结构更加稳定。
反应过程需要控制温度和压力,一般温度在300℃至400℃之间,压力在20MPa至40MPa之间。
反应后的柴油气体混合物进入分离器。
在分离器中,将气体和液体分离。
气体中主要是未被反应的氢气和反应生成的硫化氢和氨等物质。
气体经过脱除硫器进行二次处理,以去除硫化氢和氨等有害物质。
液体中则主要是经过加氢反应后的柴油。
分离器将气体和液体分别收集。
最后,收集到的柴油经过一系列的处理步骤,如蒸馏和过滤等,以达到对柴油的进一步提纯。
经过处理后的柴油可以用于各种柴油动力设备和柴油发动机,提高动力设备的效率和清洁度。
总之,柴油加氢工艺是一种常用的炼油工艺,可以降低柴油中的硫、氮等杂质含量,提高柴油的质量和清洁度。
工艺流程包括预处理、加氢反应、分离和提纯等步骤。
通过精确的操作和控制,柴油加氢工艺可以生产出高质量的柴油,为各种柴油动力设备提供可靠的燃料。
- 1、下载文档前请自行甄别文档内容的完整性,平台不提供额外的编辑、内容补充、找答案等附加服务。
- 2、"仅部分预览"的文档,不可在线预览部分如存在完整性等问题,可反馈申请退款(可完整预览的文档不适用该条件!)。
- 3、如文档侵犯您的权益,请联系客服反馈,我们会尽快为您处理(人工客服工作时间:9:00-18:30)。
加氢反应系统
▪ 反应系统操作原则
加氢反应原料为催化、焦化柴油和焦化汽油
a 原料要求: 装置加工的焦化柴油和焦化汽油杂质和烯烃含量较高,原料先经过滤器脱除大于25µ的杂
质颗粒,为保证脱除效果降低过滤器的过滤负荷,要求罐区控制较高的柴油罐存,确保沉降 时间,汽油罐维持较低的汽油罐存,缩短停留时间,减少烯烃氧化生成胶质。
6 仪表第四维护班
工艺流程
▪ 分馏部分
从反应部分来的低分油与T1102底油换热后进入脱硫化氢汽提塔(T1101),塔底通入220℃汽提蒸 汽,塔顶油气经汽提塔顶空冷器(A1102)、汽提塔顶后冷器(E1107)冷凝冷却至40℃,进入汽提塔顶 回流罐(V1104)进行气、油、水三相分离。闪蒸出的气体与低分气合并送至装置外;V1104含硫含氨污 水与高分、低分酸性水一起送出装置;油相经汽提塔顶回流泵(P1103A,B)升压后全部作为塔顶回流 。为了抑制硫化氢对塔顶管道和冷换设备的腐蚀,在塔顶管道注入缓蚀剂。脱硫化氢汽提塔底油经 E1102与反应流出物换热后进入产品分馏塔(T1102),T1102设有29层浮阀塔盘,塔底设蒸汽汽提,塔 顶油气经产品分馏塔顶空冷器(A1103)、产品分馏塔顶后冷器(E1105)冷凝冷却40℃后进入产品分馏 塔回流罐(V1105),回流罐压力通过燃料气控制。回流罐液相经产品分馏塔塔顶回流泵(P1104A、B) 升压后,一部分作为分馏塔的回流,另一部分作为粗汽油产品出装置。V1105分水包排出的含油污水自 流出装置由工厂统一处理。产品分馏塔底油经柴油泵(P1105A、B)升压后先经E1106A~D换热,后经柴 油空冷器(A1104)冷却至50℃,再经过柴油聚集器(V1108)脱水后,精制柴油送出装置
控制方式:PIC-8102与TRCA-8133A串级控制,TRCA-8133A为主调,PIC-8102为副调,控制入炉瓦斯 压力来控制反应器入口温度TRCA-8133A。提高反应温度可促进加氢反应,有利于杂质脱除,但是温度过 高,会促进裂化反应,而使液收降低,而且催化剂积碳速度加快,缩短催化剂的寿命。另外反应温度必 须足够高,使得进入反应器的物料100%的汽化,以保证物料在催化剂床层的均匀分配,在保证原料精制 效果的情况下,为得到最长的催化剂寿命,反应器入口温度应尽量的低。反应器温度随催化剂的活性不 断下降而逐渐提高。
4 仪表第四维护班
工艺原理
▪ c 烯烃饱合
烯烃饱合生成烷烃,其加氢反应速度比脱硫反应略慢,原料由于烯烃的存在,会增加催化剂上的积碳,缩短生 产周期。化学反应方程式:
CnH2n + H2→CnH2n+2 烯烃饱合也为耗氢和放热反应,原料油溴价每降低一个单位,放热8.11×103焦/公斤进料,耗氢量约为1.07- 1.42NM3/M3原料。
2014.07
装置简介
▪ 设计能力
装置公称规模为120×104t/a,实际处理量为113.43×104t/a,投产于2003年7月,原设计能力为120万吨/年,主要产 品有粗汽油、精制柴油,副产品为加氢干气。2004年6月进行掺炼焦化汽油改造,装置实际加工能力为104×104t/a。装置 主要由反应和分馏两部分组成。
7 仪表第四维护班
工艺流程
▪ 含氢尾气膜分离提氢部分
由芳烃装置、加氢裂化装置和柴油加氢装置提供异构化富氢、100#酸性气、加氢裂化、柴油加氢干气等四股富 含氢原料气汇集混合后输送到氢气压缩机入口缓冲罐(V102)。混合原料气通过氢气压缩机升压至6.8MPa(G),经氢气 压缩机冷却器(E102)冷却后进入氢气压缩机出口分液罐(V103),先脱除所含液态烃,然后进入膜分离系统。膜分离 氢提纯工艺流程主要由两部分组成,即预处理和膜分离。预处理的目的是除去原料气中的固体微粒和重烃,并将气 体加热到比露点温度高10~20℃,从而得到既干净又温热的气体。该气体可直接进行膜分离。膜分离的目的是提纯 氢气。含氢尾气经稳流后, 以6.8MPa 、40 ℃进入膜分离装置界区, 此气体先经一除雾器(X-101),除去较大水滴和 油滴。再由高效联合过滤器(X-102 )除去大于0.01μm 的粒子, 可冷凝的液沫及雾滴被捕集形成液体后, 通过过 滤器底部的阀门排出界区。联合过滤器分两组,一组在线,一组备用。分别为两级串联。然后原料气经过一套管式 加热器(E-101 )加热至83 ℃, 使原料气远离露点, 不至于因为氢气渗透后滞留气烃类含量升高,冷凝形成液膜而 影响分离性能。 用一蒸汽流量调节阀TV-101 和温度变送器TT-101 实现原料气温度控制,指示报警和联锁。原料气 经过加热器(E-101 )加热至83 ℃后,经一管道过滤器(SP-101 ), 再进入PRISM®膜分离器(M101A/B/C )进行 分离。膜分离器M-101A 与M-101B 并联,然后与M-101C 串联运行。 每个PRISM®膜分离器外型类似一管壳式热交换 器,膜分离器壳内由成千上万根中空纤维束填充,类似于管束。原料气从下端侧面进入PRISM®膜分离器。由于各种 气体组分在透过中空纤维膜时的溶解度和扩散系数不同,导致不同气体在膜中的相对渗透速率不同,在加氢尾气的 各组分中氢气的相对渗透速率最快,从而可将氢气分离提纯。在原料气沿PRISM®膜分离器长度方向流动时,更多的 氢气扩散进入中空纤维。在中空纤维芯侧得到92%的富氢产品,称为渗透气,压力为2.3MPa; 在壳程得到富含惰性气 体的物流,称为非渗透气。 其压力由HV-101 控制, 并减压至1.0 Mpa ,进入燃料气管网。PRISM®膜分离器可以根
烃类分子的骨架结构发生极小的变化。
▪ a 脱硫反应:
在加氢条件下,石油馏份中的各种含硫化合物转化为相当的烃和H2S,从而脱除了硫。 硫醇加氢:R-SH+H2→RH+H2S 硫醚加氢:R-S-R`+2H2→RH+R`H+H2S 二硫化物加氢:R-S-S-R`+3H2→RH+R`H+2H2S
3 仪表第四维护班
蒸汽、凝结水及采暖水系统:
a 3.5MPa蒸汽自厂中压蒸汽管网来,进入循环氢压缩机透平做功,做功后蒸汽并入厂1.0MPa蒸汽管网。 b 1.0MPa蒸汽作为分馏系统T1101、T1102的汽提用汽。1.0MPa蒸汽也作为各处消防伴热及抽空器的动力,各管 架的吹扫接头及塔、容器底部的吹扫用蒸汽。 c 凝结水来自装置1.0MPa蒸汽低点排凝及各蒸汽伴热点回水,经疏水器疏水后进入注水罐V1109。 d 采暖水系统与厂热水伴热系统相连,作为装置伴热及采暖用水。
▪ 原料及产品
原料为焦化汽油、焦化柴油和催化柴油的混合油,产品为精制柴油和精制汽油,副产品为干气,至装置外脱硫后作燃 料使用
2 仪表第四维护班
工艺原理
▪ 加氢精制
加氢精制是指在催化剂和氢气存在下,石油馏份中含硫、氮、氧的非烃类组份和有机金属化合物分 子发生脱除硫、氮、氧和金属的氢解反应,烯烃和芳烃分子发生加氢反应,被处理的原料平均分子量及
据原料气流量的变化,用渗透气侧的截止阀将其隔离或投入运行。
8 仪表第四维护班
工艺流程
▪ 主要系统流程说明
风系统:
风系统包括净化风与非净化风,两者都自装置外来,净化风进入V1113,其底部可排凝,顶部进入仪表用风部位 。非净化风与软管站相连做吹扫、气密用。
水系统:
a 新鲜水自装置外来,进入泵房及压缩机房做日常清洗用水,进入分馏系统做开工冲洗用水。 b 循环水自装置外来,进凝汽器及E1104、E1105、E1107作循环冷却水,冷却后出装置回供排水车间。 c 除盐水自锅炉车间来,主要作为反应系统注水用,用来溶解氨盐,防止换热设备堵塞。
工艺原理
▪ b 脱氮反应
在加氢精制条件下,氮化物在氢作用下,转化为NH3和烃,几种含氮化合物反应如下: 胺类:R-NH2+H2→RH+NH3
加氢原料油中氮化物大部分是环状化合物,加氢时首先是杂环结构被氢饱和生成氢化衍生物,然后氢化环在不 同位置上断裂生成胺,胺进一步加氢分解,转化为氨和相应的饱和烃和烷基芳烃。例如喹啉的反应:
对流段吹扫蒸汽
TRCA 8133A
爆炸气采样点
十
二
组
喷
嘴
风机挡板
辐射段吹扫蒸汽 爆炸气采样点
b 反应成份: 反应流出物主要是加氢后的汽柴油,反应生成硫化氢以及加氢干气。当原料改变而引起
的硫、氮等杂质含量升高,则加氢反应条件应适当的提高,以确保精制产品符合要求。
10 仪表第四维护班
加氢反应系统
▪ 加氢反应温度TRCA-8133A
控制范围:反应器入口温度TRCA-8133A:210-280℃ 控制目标:指令反应温度±2℃ 相关参数:加热炉出口温度点TRCA-8133B高高联锁温度为328℃。
▪ 装置特点
a 原料油过滤装置内设置原料自动反冲洗过滤器,脱除大于25微米的固体颗粒。 b 原料油惰性气体保护原料油缓冲罐采用燃料气覆盖措施,以防止原料被氧化生成胶质。 c 高压空冷前注水在反应流出物进入空冷前注水,来溶解铵盐,避免铵盐结晶析出堵塞管路。 d 采用双壳程、螺纹锁紧环换热器,提高换热效率,减少换热面积,节省投资。 e 采用炉前混氢方案 ,提高换热效率和减缓结焦程度。 f 采用板焊结构热壁反应器,内设两个催化剂床层,中间设置了冷氢箱。 g 采用冷高分流程 h 分馏部分采用双塔蒸汽汽提流程。
瓦斯系统:
装置外来的瓦斯进V1111,一路去反应加热炉,另一路做为原料缓冲罐V1101的充压用气,以维持罐内压力稳定。 V1111底部有加热盘管,瓦斯中的凝缩液可以再次汽化,不汽化部分排到污水系统,也可排至液体放空线进入火炬放 空罐V1112并入厂火炬管网。
氮气系统:
自空分来的低压氮气进入装置各部分,作为压缩机干气密封用气、事故氮气,吹扫及其它用处。
11 仪表第四维护班
加氢反应系统
氢气 燃料气
氮气
PV 8115A
FT 8402
火炬 12 仪表Байду номын сангаас四维护班