造船的主要工艺流程
造船工艺流程

造船工艺流程造船是一项复杂而又精密的工艺,涉及到多个环节的设计、制造和装配。
下面将介绍一般的造船工艺流程。
造船工艺流程通常可分为需求定义、设计、制造和装配四个主要阶段。
首先是需求定义阶段。
在这个阶段,船东和设计方将共同确定船舶的用途、规格、功能需求以及预算。
船东还需要提供有关设计方面的要求,如尺寸、船舶类型、载货能力等。
这样可以为后面的设计工作提供必要的指导。
然后是设计阶段。
设计师根据需求定义阶段的要求,进行各种设计工作。
这包括船体结构设计、船舶系统设计、动力系统设计等。
设计师使用计算机辅助设计软件来完成相关工作,并进行各种性能预测和强度计算。
设计阶段的结果是一套详细的设计图纸和规范。
接下来是制造阶段。
基于设计阶段的图纸和规范,制造商开始制造船体的各个部分。
这包括船体结构的各个部分、甲板、船舶系统的安装等。
制造过程中需要严格按照设计要求进行操作,确保船体的质量和性能。
制造过程中常用的工艺包括焊接、切割、冲压、磨削等。
制造阶段的目标是生产出符合设计要求的船舶部件。
最后是装配阶段。
在这个阶段,各个部件将被组装到一起,形成完整的船体。
装配过程需要严格按照设计要求进行,同时需要进行各种检查和测试,确保装配的质量和性能。
装配阶段通常需要使用大型的起重机和其他辅助设备,以便将重型部件安装到正确的位置。
整个造船过程中,还需要进行一系列的质量控制和安全检查。
这包括材料的检验、焊接接头的质量控制、船体的水密性测试等。
各种检查和测试的目的是确保船体的质量和性能符合要求,并确保船舶在使用过程中的安全性。
除了上述四个主要阶段外,造船过程中还涉及到许多其他的工作,如项目管理、采购、质量管理等。
这些工作的目的是确保整个造船过程的顺利进行,并提供高质量的船舶给船东。
同时,工程师和设计师还需要与船东进行沟通和协商,以便调整设计方案和解决各种问题。
总结起来,造船工艺流程是一个复杂而又精细的过程。
它涉及到需求定义、设计、制造和装配等多个阶段,需要各种工艺和检查的支持。
造船工艺流程
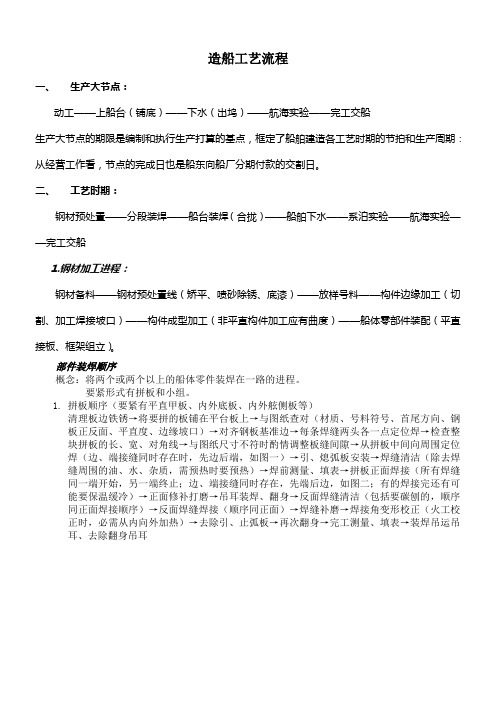
造船工艺流程一、生产大节点:动工——上船台(铺底)——下水(出坞)——航海实验——完工交船生产大节点的期限是编制和执行生产打算的基点,框定了船舶建造各工艺时期的节拍和生产周期:从经营工作看,节点的完成日也是船东向船厂分期付款的交割日。
二、工艺时期:钢材预处置——分段装焊——船台装焊(合拢)——船舶下水——系泊实验——航海实验——完工交船1.钢材加工进程:钢材备料——钢材预处置线(矫平、喷砂除锈、底漆)——放样号料——构件边缘加工(切割、加工焊接坡口)——构件成型加工(非平直构件加工应有曲度)——船体零部件装配(平直接板、框架组立)。
部件装焊顺序概念:将两个或两个以上的船体零件装焊在一路的进程。
要紧形式有拼板和小组。
1.拼板顺序(要紧有平直甲板、内外底板、内外舷侧板等)清理板边铁锈→将要拼的板铺在平台板上→与图纸查对(材质、号料符号、首尾方向、钢板正反面、平直度、边缘坡口)→对齐钢板基准边→每条焊缝两头各一点定位焊→检查整块拼板的长、宽、对角线→与图纸尺寸不符时酌情调整板缝间隙→从拼板中间向周围定位焊(边、端接缝同时存在时,先边后端,如图一)→引、熄弧板安装→焊缝清洁(除去焊缝周围的油、水、杂质,需预热时要预热)→焊前测量、填表→拼板正面焊接(所有焊缝同一端开始,另一端终止;边、端接缝同时存在,先端后边,如图二;有的焊接完还有可能要保温缓冷)→正面修补打磨→吊耳装焊、翻身→反面焊缝清洁(包括要碳刨的,顺序同正面焊接顺序)→反面焊缝焊接(顺序同正面)→焊缝补磨→焊接角变形校正(火工校正时,必需从内向外加热)→去除引、止弧板→再次翻身→完工测量、填表→装焊吊运吊耳、去除翻身吊耳11221图一装配方法(正确)装配方法(错误)图三.火工校正方向图二.焊接顺序小组顺序小组的内容包括 “T ”排、组合纵桁(肋板)、龙筋先行、机座、肋骨框 架等的组装。
“T ”排小组“T ”排分直、弯两类:直“T ”排通常采纳倒装法;弯“T ”排通常采纳侧装法。
船舶建造流程

船舶建造流程一、船体放样1.线形放样:分手工放样和机器(计算机)放样,手工放样一般为1:1比例,样台需占用极大面积,需要较大旳人力物力,目前较少采用;机器放样又称数学放样,依托先进技术软件对船体进行放样,数学放样精确性较高,且不占用场地和人力,目前较为广泛旳采用机器放样。
2.构造放样、展开:对各构造进行放样、展开,绘制对应旳加工样板、样棒。
3.下料草图:绘制对应旳下料草图。
二、船体钢材预处理:对钢材表面进行预处理,消除应力。
1.钢材矫正:一般为机械措施,即采用多辊矫夹机、液压机、型钢矫直机等。
2.表面清理:a.机械除锈法,如抛丸除锈法喷丸除锈法等,目前较为广泛采用;b.酸洗除锈法,也叫化学除锈,运用化学反应;c.手工除锈法,用鎯头等工具敲击除锈三、构件加工1.边缘加工:剪切、切割等;2.冷热加工:消除应力、变形等;3.成型加工:油压床、肋骨冷弯机等。
四、船体装配:船体(部件)装配,把多种构件组合拼接成为多种我们所需旳空间形状。
五、船体焊接:把装配后旳空间形状通过焊接使之成为永久不可分割旳一种整体。
六、密性试验:各类密性试验,如着色试验、超声波、X光等。
七、船舶下水:基本成形后下水,设计流水线如下旳所有体积均为浸水体积。
1.重力下水:一般方式为船台下水,靠船舶自重及滑动速度下水;2.浮力下水:一般形式为船坞;3.机器下水:合用于中小型船舶,通过机器设备拖拉或吊下水。
八、船舶舾装:全面开展舾装系统、系泊系统、机装、电装、管装等方面旳工作。
九、船舶试验:系泊试验、倾斜试验,试航(全面测试船舶各项性能)。
十、交船验收。
~~~~~~~~~~~~~~~~~~~~~~~~~~~~~~~~~~~~~~~~~~~~~~~~~~~~~~~~~~~~~~~~~~~~~~船舶建造工艺流程简要简介本讲座从管理者旳角度,按照“壳舾涂一体化总装造船”现代造船管理模式旳规定,结合我国船厂旳探索实践,简介船舶建造在各工艺阶段旳组织方式、应注意旳问题,同步提供对施工状态旳评价原则。
船舶建造模式,船舶建造流程

船舶建造模式,船舶建造流程船舶建造是一个综合性的工程项目,其建造模式和流程是非常复杂和严谨的。
船舶建造模式主要包括传统造船和模块化建造两种,其具体流程也各有特点。
本文将分别介绍这两种船舶建造模式及其流程。
一、传统造船模式传统造船模式是指按照船坞传统的建造方式,通过分段建造、拼装组合,最终完成整艘船舶的建造。
其主要流程如下:1. 设计阶段:根据客户的需求和要求,设计专业工程师进行船舶的设计工作,包括船体结构、船体尺寸等。
2. 材料采购:根据设计要求,采购各种材料,包括钢板、钢管、电气设备等。
3. 船坞建造:根据设计标准,进行船坞的修建和准备工作。
4. 分段建造:将各部分船体分段建造,包括船头、船中、船尾等。
5. 拼装组合:将各个分段(船尾、船中、船头)进行拼装组合,形成整体船体。
6. 安装设备:安装船舶所需的设备和装备,包括发动机、舵机、导航设备等。
7. 调试试航:进行船舶的调试和试航工作,检查船舶各项功能是否正常。
8. 交付使用:完成所有测试和验收工作后,最终交付给客户使用。
二、模块化建造模式模块化建造是指将整艘船舶分为多个模块,分别在不同厂家进行建造,并最终在船坞内进行组装的建造模式。
其主要流程如下:1. 设计阶段:同传统造船模式,进行船体设计工作。
2. 模块分包:将整艘船舶进行分模块包,分别交由不同的厂家进行建造。
3. 模块建造:各个厂家按照设计要求,分别建造各自的模块。
4. 运输运送:将建造好的模块运送至船坞所在地点。
5. 模块组装:在船坞内进行各模块的组装工作。
6. 安装设备:同传统造船模式,进行设备的安装工作。
7. 调试试航:进行船舶的调试和试航工作,检查各项功能是否正常。
8. 交付使用:最终将完成的船舶交付给客户使用。
传统造船模式和模块化建造模式各有优劣,传统造船模式的优点是建造工艺成熟、稳定,但建造周期较长;模块化建造模式的优点是工期短、效率高,但对接质量和运输要求较高。
在实际应用中,需要根据客户需求、船舶类型等多方面考虑,选择合适的船舶建造模式和流程。
造船工艺流程
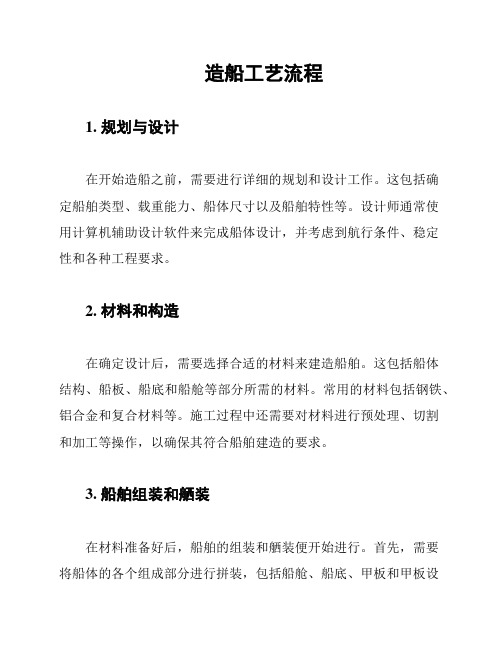
造船工艺流程1. 规划与设计在开始造船之前,需要进行详细的规划和设计工作。
这包括确定船舶类型、载重能力、船体尺寸以及船舶特性等。
设计师通常使用计算机辅助设计软件来完成船体设计,并考虑到航行条件、稳定性和各种工程要求。
2. 材料和构造在确定设计后,需要选择合适的材料来建造船舶。
这包括船体结构、船板、船底和船舱等部分所需的材料。
常用的材料包括钢铁、铝合金和复合材料等。
施工过程中还需要对材料进行预处理、切割和加工等操作,以确保其符合船舶建造的要求。
3. 船舶组装和舾装在材料准备好后,船舶的组装和舾装便开始进行。
首先,需要将船体的各个组成部分进行拼装,包括船舱、船底、甲板和甲板设备等。
然后进行舾装工作,包括安装船舶系统(如动力系统、通信系统和航行系统等)、设备和其他必要的装置。
4. 测试和调试船舶的建造完成后,需要进行各项测试和调试工作。
这包括结构强度测试、泄漏测试、设备运行测试和性能试航等。
通过这些测试和调试,可以确保船舶满足相应的安全和性能标准。
5. 定制和修饰船舶建造完成后,往往还需要进行一些定制和修饰工作,以符合客户的需求和要求。
这可能包括船体涂装、船舱内部的装饰和舒适性改进等。
6. 交付和维护最后,经过所有必要的过程和检验,船舶可以交付给客户使用。
同时,维护和保养工作也非常重要,以确保船舶的长期使用和良好运行。
以上是一般的造船工艺流程的概述。
每个具体项目的工艺流程可能会有所不同,但总体步骤相似。
希望本文档能对读者理解船舶建造过程有所帮助。
造船流程
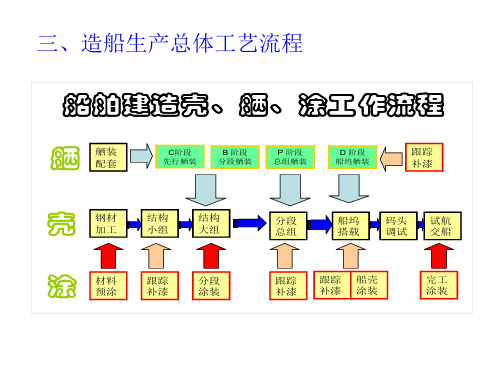
造船生产总体工艺流程
船舶建造壳、舾、涂工作内容
材料加工:
钢材堆放、钢材预处 理、钢材切割、曲型结 构加工、结构托盘集配
结构组立
结构小组、结构 大组立 C阶段:
分段总组
总段 环段 P阶段: 总组成形后 舾装
船坞搭载
D阶段: 船坞舾装
舾装配套:
管系制作、舾装件制 作、 舾装集配
先行 舾装(指封 舱件预舾装) B阶段: 分段成形后舾装
托盘配 套区域
零件装 配区域
结构焊 接区域
打磨补 漆区域
(三)主要现代化的加工设施:
现代自动化生产流水线(平面分段、曲面分段):
总装生产区域
(二)总装生产区域工艺流程
双层底总组区域 总段预舾装
边水舱总组区域
甲板总组区域
总 组 舾 装
单元安装
机舱总组区域
模块安装
船 坞 搭 载 及 舾 装
出 坞
首部总组区域
托盘配 套区域
零件装 配区域
结构焊 接区域
打磨补 漆区域
托盘配 套区域
零件装 配区域
结构焊 接区域
打磨补 漆区域
托盘配 套区域
零件装 配区域
结构焊 接区域
打磨补 漆区域
托盘配 套区域
零件装 配区域
结构焊 接区域
打磨补 漆区域
A4 小 组 区 域
托盘配 套区域
零件装 配区域
结构焊 接区域
打磨补 漆区域
零件 零件 钢板 钢板
零件 零件 钢板
零件 零件 钢板 钢板
零件 零件 钢板
零件 零件 钢板 钢板
零件 零件 钢板
零件
零件
(三)切割加工中心主要现代化的加工设施
现代造船的工艺流程
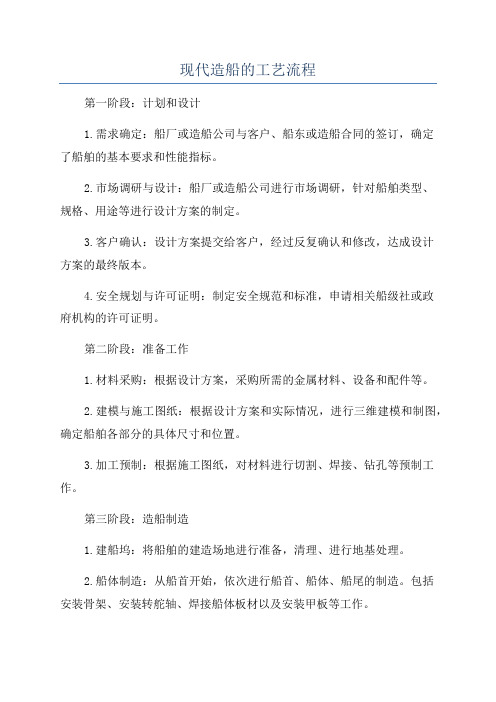
现代造船的工艺流程第一阶段:计划和设计1.需求确定:船厂或造船公司与客户、船东或造船合同的签订,确定了船舶的基本要求和性能指标。
2.市场调研与设计:船厂或造船公司进行市场调研,针对船舶类型、规格、用途等进行设计方案的制定。
3.客户确认:设计方案提交给客户,经过反复确认和修改,达成设计方案的最终版本。
4.安全规划与许可证明:制定安全规范和标准,申请相关船级社或政府机构的许可证明。
第二阶段:准备工作1.材料采购:根据设计方案,采购所需的金属材料、设备和配件等。
2.建模与施工图纸:根据设计方案和实际情况,进行三维建模和制图,确定船舶各部分的具体尺寸和位置。
3.加工预制:根据施工图纸,对材料进行切割、焊接、钻孔等预制工作。
第三阶段:造船制造1.建船坞:将船舶的建造场地进行准备,清理、进行地基处理。
2.船体制造:从船首开始,依次进行船首、船体、船尾的制造。
包括安装骨架、安装转舵轴、焊接船体板材以及安装甲板等工作。
3.装配船舶设备:安装船舶所需的系统设备,如电力系统、水供应系统、通风系统等。
4.舾装工作:安装船舶的室内装饰、家具等。
5.涂装:对船舶进行涂装和防腐处理。
6.完善船舶系统:安装电子设备、通信设备、导航设备等。
7.完善船舶结构:完成排水试验、载重试验等,确保船舶结构完整性。
8.海上试航:进行海上试航,测试船舶各项性能。
第四阶段:交付和售后服务1.质量检验:对船舶进行全面的质量检查,确保达到设计规定的各项标准。
2.完善备案:向相关船级社或政府机构提交船舶设计、建造和测试等相关报告和资料,获得相关的船舶检验证明。
3.交付和验收:将船舶交付给船东或客户,船东或客户进行验收,确认船舶符合合同要求。
4.售后服务:船厂或造船公司提供船舶的售后服务,包括保养、维修、改进和升级等。
可以看出,现代造船工艺流程从船舶计划到设计、制造、测试和交付,涵盖了广泛的环节和细节,需要有高度的组织和技术能力。
而随着科技的不断进步,造船工艺也在不断演进和改进,以提高船舶的性能、安全性和经济性。
(完整word版)造船的主要工艺流程
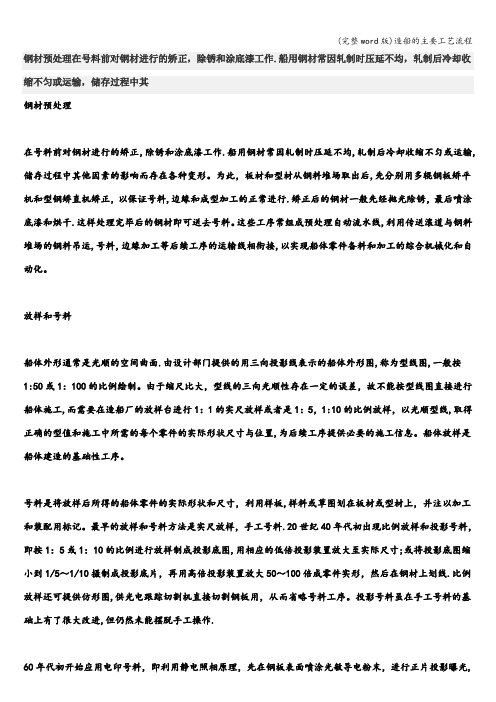
钢材预处理在号料前对钢材进行的矫正,除锈和涂底漆工作.船用钢材常因轧制时压延不均,轧制后冷却收缩不匀或运输,储存过程中其钢材预处理在号料前对钢材进行的矫正,除锈和涂底漆工作.船用钢材常因轧制时压延不均,轧制后冷却收缩不匀或运输,储存过程中其他因素的影响而存在各种变形。
为此,板材和型材从钢料堆场取出后,先分别用多辊钢板矫平机和型钢矫直机矫正,以保证号料,边缘和成型加工的正常进行.矫正后的钢材一般先经抛光除锈,最后喷涂底漆和烘干.这样处理完毕后的钢材即可送去号料。
这些工序常组成预处理自动流水线,利用传送滚道与钢料堆场的钢料吊运,号料,边缘加工等后续工序的运输线相衔接,以实现船体零件备料和加工的综合机械化和自动化。
放样和号料船体外形通常是光顺的空间曲面.由设计部门提供的用三向投影线表示的船体外形图,称为型线图,一般按1:50或1:100的比例绘制。
由于缩尺比大,型线的三向光顺性存在一定的误差,故不能按型线图直接进行船体施工,而需要在造船厂的放样台进行1:1的实尺放样或者是1:5,1:10的比例放样,以光顺型线,取得正确的型值和施工中所需的每个零件的实际形状尺寸与位置,为后续工序提供必要的施工信息。
船体放样是船体建造的基础性工序。
号料是将放样后所得的船体零件的实际形状和尺寸,利用样板,样料或草图划在板材或型材上,并注以加工和装配用标记。
最早的放样和号料方法是实尺放样,手工号料.20世纪40年代初出现比例放样和投影号料,即按1:5或1:10的比例进行放样制成投影底图,用相应的低倍投影装置放大至实际尺寸;或将投影底图缩小到1/5~1/10摄制成投影底片,再用高倍投影装置放大50~100倍成零件实形,然后在钢材上划线.比例放样还可提供仿形图,供光电跟踪切割机直接切割钢板用,从而省略号料工序。
投影号料虽在手工号料的基础上有了很大改进,但仍然未能摆脱手工操作.60年代初开始应用电印号料,即利用静电照相原理,先在钢板表面喷涂光敏导电粉末,进行正片投影曝光,经显影和定影后在钢板上显出零件图形。
造船工艺流程
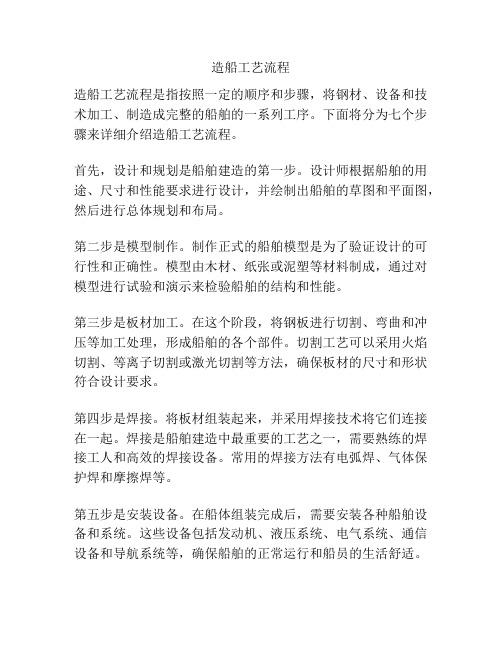
造船工艺流程造船工艺流程是指按照一定的顺序和步骤,将钢材、设备和技术加工、制造成完整的船舶的一系列工序。
下面将分为七个步骤来详细介绍造船工艺流程。
首先,设计和规划是船舶建造的第一步。
设计师根据船舶的用途、尺寸和性能要求进行设计,并绘制出船舶的草图和平面图,然后进行总体规划和布局。
第二步是模型制作。
制作正式的船舶模型是为了验证设计的可行性和正确性。
模型由木材、纸张或泥塑等材料制成,通过对模型进行试验和演示来检验船舶的结构和性能。
第三步是板材加工。
在这个阶段,将钢板进行切割、弯曲和冲压等加工处理,形成船舶的各个部件。
切割工艺可以采用火焰切割、等离子切割或激光切割等方法,确保板材的尺寸和形状符合设计要求。
第四步是焊接。
将板材组装起来,并采用焊接技术将它们连接在一起。
焊接是船舶建造中最重要的工艺之一,需要熟练的焊接工人和高效的焊接设备。
常用的焊接方法有电弧焊、气体保护焊和摩擦焊等。
第五步是安装设备。
在船体组装完成后,需要安装各种船舶设备和系统。
这些设备包括发动机、液压系统、电气系统、通信设备和导航系统等,确保船舶的正常运行和船员的生活舒适。
第六步是涂装和防腐。
在船体组装和设备安装完成后,需要进行涂装和防腐处理,以保护船舶的外部和内部结构免受海水和腐蚀的侵害。
涂装工序包括底漆、中漆和面漆的涂装,防腐工序包括防腐涂料的喷涂和涂覆。
最后一步是试航。
在船舶建造完成后,需要进行试航试验,以验证船舶的性能和功能是否符合设计要求。
试航中会测试船舶的各项指标,包括航行速度、转向性能和操纵性等。
一切正常后,船舶就可以交付给船东或船运公司。
综上所述,造船工艺流程包括设计和规划、模型制作、板材加工、焊接、安装设备、涂装和防腐,以及试航等七个步骤。
每个步骤都需要经过精确的计划和高效的操作,以确保船舶的质量和性能符合要求。
造船工艺是一项复杂而精细的工作,需要专业的技术人员和设备的支持。
造船工艺流程

造船工艺流程造船是一项复杂而又精密的工艺,它涉及到许多环节和步骤。
在整个造船过程中,需要经历设计、材料采购、制造、装配、测试等多个阶段。
下面将详细介绍造船工艺的流程。
首先,造船的第一步是设计。
设计是整个造船过程中最为关键的一环,它直接影响到船舶的性能、结构和外观。
设计师需要根据客户的需求和船舶用途,绘制出详细的船舶设计图纸,包括船体结构、船舱布局、动力系统等方面的设计。
设计图纸需要经过严格的审核和验证,确保其符合相关的标准和规范。
接下来是材料采购。
根据设计图纸,造船厂需要采购各种船舶建造所需的材料,如钢材、铝合金、船用木材等。
这些材料需要符合相应的船级社要求,保证船舶的质量和安全性。
随后是制造和装配。
在船台上,工人们根据设计图纸,将各种材料进行切割、弯曲和焊接,逐步组装成船体的骨架。
然后,安装船舶的各种设备和系统,如发动机、舱室、导航设备等。
这个阶段需要严格按照工艺流程进行,确保船舶的各个部分都能够完美配合。
随后是涂装和测试。
船体制造完成后,需要进行防腐涂装,以保护船体免受海水侵蚀。
同时,还需要进行各项系统的测试,如动力系统、电气系统、通信系统等,确保船舶各项设备和系统的正常运行。
最后是交付和验收。
当船舶制造完成并通过各项测试后,需要进行最终的验收。
船级社和客户将对船舶进行检验,确保其符合相关的标准和要求。
一旦验收合格,船舶将正式交付给客户,并投入使用。
总的来说,造船工艺流程包括设计、材料采购、制造、装配、涂装、测试、交付和验收等多个环节。
每个环节都需要严格按照工艺流程进行,确保船舶的质量和安全性。
只有如此,才能制造出高质量、高性能的船舶,满足客户的需求和航行要求。
船舶建造的工艺流程

船舶建造的工艺流程船舶建造的工艺流程可以分为以下几个步骤:第一步:设计和规划船舶的建造开始于设计和规划阶段。
设计师根据客户的需求和要求,绘制出船舶的草图和设计图纸。
在设计过程中,需要考虑到船舶的用途、尺寸、载重量和航行条件等因素。
设计过程还包括选择适当的材料和船舶的结构等。
第二步:材料采购和制备一旦船舶的设计完成,就需要采购建造所需的材料。
这些材料主要包括钢板、铝板、船舶设备和配件等。
材料必须按照设计要求进行检测和认证,确保材料的质量和可靠性。
材料准备完成后,还需要进行切割、成型和加工等工艺过程,以便适应船体的结构和形状。
第三步:船体组装和焊接在船体组装和焊接阶段,各个部件被装配在一起,形成船舶的骨架。
工人们使用专业的工具和设备,将各个部件精确地安装到船体上,并通过焊接技术将它们牢固地固定在一起。
焊接过程需要严格遵守船舶建造的标准和规定,以确保焊接的质量和强度。
第四步:设备和系统安装在船体组装完成后,各种设备和系统将被安装到船舶上。
这些设备和系统包括电气系统、通信系统、水暖系统、空调系统和驾驶设备等。
在安装过程中,需要对设备进行适当的测试和调试,以确保其正常运行和安全性。
第五步:涂装和装饰完成设备安装后,船舶需要进行涂装和装饰。
这一步骤旨在保护船舶的金属表面免受腐蚀和侵蚀,并提升船舶的外观和舒适度。
在涂装过程中,采用专业的涂料和防腐材料,确保船体表面的光滑和牢固。
第六步:测试和调试最后,船舶需要进行全面的测试和调试,以确保其在海上的运行安全和性能。
包括舾装试验、船舶载重试验、漏水试验等等,对船舶的各个系统进行严格的检测和评估。
只有通过了所有的测试和调试,船舶才能交付给客户使用。
船舶建造的工艺流程是一个复杂且需要高度专业知识和技术的过程。
每个步骤都需要精细的计划和严格的质量控制,以确保船舶的质量和安全性。
船舶建造所采用的工艺和技术在不断的发展和创新中,以满足不断变化的市场需求和客户要求。
简述造船工艺流程

简述造船工艺流程造船工艺流程听起来就很酷炫呢,那我就给你好好唠唠。
一、设计阶段。
造船嘛,首先得有个设计图,就像盖房子要有个蓝图一样。
设计师们会根据船的用途、航行的区域、船东的要求等来设计船的外形、结构啥的。
比如说要造一艘货船,那就得考虑能装多少货物,怎么安排货仓才合理。
这个阶段要做很多计算呢,像船的稳定性计算,要是船在海上晃悠两下就翻了,那可不行。
而且设计师们还得考虑船的速度,毕竟大家都希望船能跑得快一点,这样能节省很多时间和成本。
他们会通过各种软件模拟船在水里的情况,然后不断调整设计,直到达到理想的状态。
二、原材料准备。
有了设计图,接下来就要准备原材料啦。
船主要的材料就是钢材,那可不是一般的钢材哦,是专门用于造船的特殊钢材。
这些钢材要保证强度高、耐腐蚀,毕竟船要一直在水里泡着。
供应商会把钢材按照设计要求切割成不同的形状和尺寸,像钢板、钢梁这些。
在这个过程中,质量检测可不能少,要是钢材质量不过关,那造出来的船就像纸糊的一样脆弱。
三、船体建造。
这可是造船的重头戏呢。
工人们会先把切割好的钢板拼在一起,就像搭积木一样。
不过这个积木可不好搭,得用焊接技术把它们牢牢地固定住。
焊接的好坏直接影响到船体的强度,要是有个小缝没焊好,海水渗进去,那可就麻烦大了。
船体的形状也很重要,它要符合设计的流线型,这样船在水里航行的时候阻力才小。
在这个过程中,工人们还会不断地测量和调整,确保船体的尺寸精确无误。
四、船内设备安装。
船体造好后,就像有了一个空壳子,接下来要给这个壳子装点东西啦。
这时候就轮到各种船内设备上场了。
比如说发动机,这可是船的心脏啊,没有发动机,船就只能在水上漂着,动不了。
还有导航设备,要是在大海上迷了路,那可就危险了。
还有船员的生活设施,像床铺、厨房、卫生间这些,毕竟船员们要在船上生活很长时间呢。
安装这些设备可不容易,要考虑它们的布局合理,还要确保它们能正常运行。
五、涂装。
船造得差不多了,最后一步就是涂装啦。
造船工艺流程
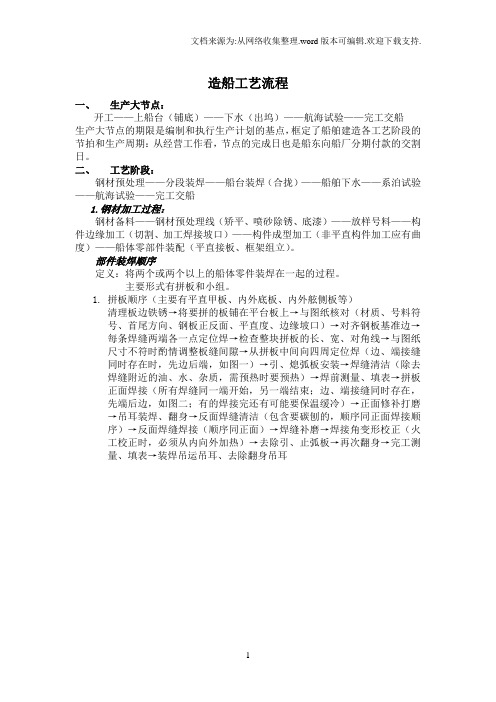
造船工艺流程一、生产大节点:开工——上船台(铺底)——下水(出坞)——航海试验——完工交船生产大节点的期限是编制和执行生产计划的基点,框定了船舶建造各工艺阶段的节拍和生产周期:从经营工作看,节点的完成日也是船东向船厂分期付款的交割日。
二、工艺阶段:钢材预处理——分段装焊——船台装焊(合拢)——船舶下水——系泊试验——航海试验——完工交船1.钢材加工过程:钢材备料——钢材预处理线(矫平、喷砂除锈、底漆)——放样号料——构件边缘加工(切割、加工焊接坡口)——构件成型加工(非平直构件加工应有曲度)——船体零部件装配(平直接板、框架组立)。
部件装焊顺序定义:将两个或两个以上的船体零件装焊在一起的过程。
主要形式有拼板和小组。
1.拼板顺序(主要有平直甲板、内外底板、内外舷侧板等)清理板边铁锈→将要拼的板铺在平台板上→与图纸核对(材质、号料符号、首尾方向、钢板正反面、平直度、边缘坡口)→对齐钢板基准边→每条焊缝两端各一点定位焊→检查整块拼板的长、宽、对角线→与图纸尺寸不符时酌情调整板缝间隙→从拼板中间向四周定位焊(边、端接缝同时存在时,先边后端,如图一)→引、熄弧板安装→焊缝清洁(除去焊缝附近的油、水、杂质,需预热时要预热)→焊前测量、填表→拼板正面焊接(所有焊缝同一端开始,另一端结束;边、端接缝同时存在,先端后边,如图二;有的焊接完还有可能要保温缓冷)→正面修补打磨→吊耳装焊、翻身→反面焊缝清洁(包含要碳刨的,顺序同正面焊接顺序)→反面焊缝焊接(顺序同正面)→焊缝补磨→焊接角变形校正(火工校正时,必须从内向外加热)→去除引、止弧板→再次翻身→完工测量、填表→装焊吊运吊耳、去除翻身吊耳11221图一装配方法(正确)装配方法(错误)图三.火工校正方向图二.焊接顺序小组顺序小组的内容包含 “T ”排、组合纵桁(肋板)、龙筋先行、机座、肋骨框 架等的组装。
“T ”排小组“T ”排分直、弯两类:直“T ”排通常采用倒装法;弯“T ”排通常采用侧装法。
(2024版)船体装配工艺1

可编辑修改精选全文完整版第一章船体装配基础知识第一节现代造船工艺流程现代造船工艺流程:1、船体建造的主要过程船体建造是船舶建造的主要部分,它具体包括船体放样、零件号料、构件加工、部件装焊、分段装焊、总段装焊和船体搭载以及密性试验等过程。
(1)船体放样船体放样包括船体肋骨型线的光顺,对设计图中可能产生的误差进行反复修正,并在光顺后的船体型线图上绘出各种结构线,进而确定各种船体构架的实际形状和尺寸以及制定检测手段(如制作样板、样箱)为后续工序提供施工依据。
最早的放样是实尺放样(1:1),其次是比例放样(1:N),随着计算机技术的发现与应用,放样有了质的飞跃,出现了数学放样,从而实现了放样自动化、无纸化。
(2)零件号料零件号料就是将放样中的信息反映到原材料上去,如零件的尺寸、后续工序所需的简明标记、符号和数据等。
号料的方法随着放样方法的发展而发展,与实尺放样对应的号料方法为手工号料,与比例放样的号料方法的投影号料,随着数学放样的出现,号料工作就非常简单和自动化了。
(3)构件加工构件加工是将原材料变成船体的第一步,它包括钢材预处理、构件边缘加工和构件成形加工。
从钢料堆场取出的钢材,因受扎制、搬运和存放中的种种因素的影响,钢材表面常附有氧化皮,铁锈或产生局部凹凸不平翘曲、扭曲等变形。
在号料之前,需要对钢板进行校平、除锈、喷涂车间防护底漆和烘干等作业。
现在上述作业一般在钢材预处理流水线上进行。
船体构件边缘加工包括三个内容:一是根据号料所给的信息运用切割或剪切的方法得到船体构件,二是根据焊接的技术要求对船体构件进行焊接工艺坡口加工,三是根据设计规范要求对自由边和人孔内周边进行打磨。
船体零件成形加工就是采用机械冷弯或水火热弯等方法将平直的原材料加工成船体制作所要求的空间形状。
(4)船体装焊船体装焊就是将加工后的船体构件分为部件装焊、分段装焊、总组装焊和船体搭载几个步骤组装成一座整体的过程。
它包括装配和焊接两个过程。
船舶建造流程详解船舶建造的各个阶段和重点任务
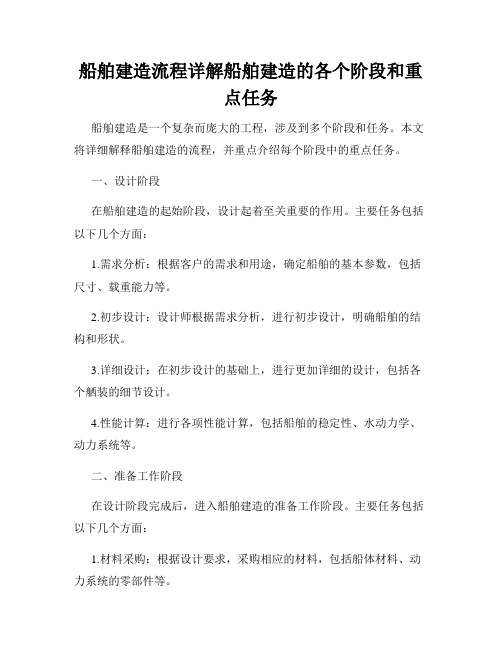
船舶建造流程详解船舶建造的各个阶段和重点任务船舶建造是一个复杂而庞大的工程,涉及到多个阶段和任务。
本文将详细解释船舶建造的流程,并重点介绍每个阶段中的重点任务。
一、设计阶段在船舶建造的起始阶段,设计起着至关重要的作用。
主要任务包括以下几个方面:1.需求分析:根据客户的需求和用途,确定船舶的基本参数,包括尺寸、载重能力等。
2.初步设计:设计师根据需求分析,进行初步设计,明确船舶的结构和形状。
3.详细设计:在初步设计的基础上,进行更加详细的设计,包括各个舾装的细节设计。
4.性能计算:进行各项性能计算,包括船舶的稳定性、水动力学、动力系统等。
二、准备工作阶段在设计阶段完成后,进入船舶建造的准备工作阶段。
主要任务包括以下几个方面:1.材料采购:根据设计要求,采购相应的材料,包括船体材料、动力系统的零部件等。
2.生产设备购置:购置相应的生产设备,例如焊接机、切割机等,以满足船舶建造的需要。
3.人员培训:为船舶建造过程中的工人和技术人员提供培训,确保他们掌握船舶建造所需的技能和知识。
4.工厂准备:准备好建造船只所需的生产场地和设施,确保工作环境安全和整洁。
三、建造阶段一切准备工作完成后,正式进入船舶建造的阶段。
主要任务包括以下几个方面:1.船体制造:根据详细设计图纸,开始船体的制造,包括焊接、切割等工艺。
2.舾装工程:在船体制造过程中,进行各个舾装的安装和布置,包括管道系统、船舶设备等。
3.动力系统安装:安装船舶的主机和推进系统,确保船舶能够正常工作。
4.电气系统安装:安装船舶的电气系统,包括配电系统、通信系统等。
四、试航和调试阶段船舶建造完成后,需要进行试航和调试,确保船舶的性能和安全运行。
主要任务包括以下几个方面:1.系统测试:对船舶的各个系统进行测试,确保其正常工作,例如动力系统、电气系统等。
2.航行性能测试:进行航行性能测试,包括航速、操纵性等,以确保船舶满足设计要求。
3.稳定性测试:对船舶的稳定性进行测试,确保其在各种条件下的平稳性。
造船工艺流程简介
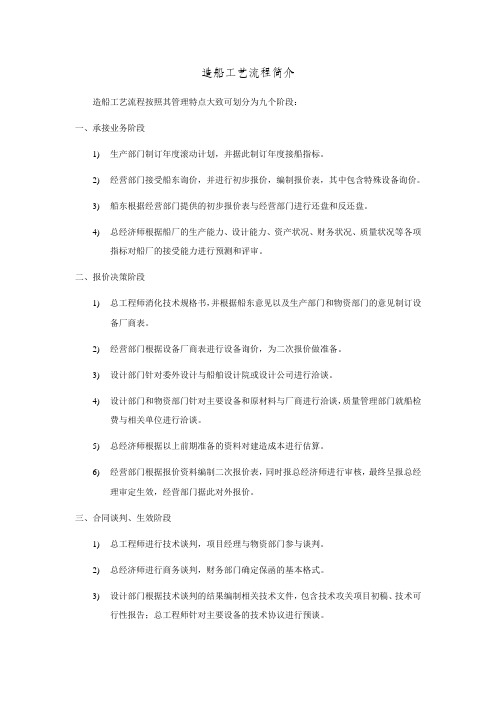
造船工艺流程简介造船工艺流程按照其管理特点大致可划分为九个阶段:一、承接业务阶段1)生产部门制订年度滚动计划,并据此制订年度接船指标。
2)经营部门接受船东询价,并进行初步报价,编制报价表,其中包含特殊设备询价。
3)船东根据经营部门提供的初步报价表与经营部门进行还盘和反还盘。
4)总经济师根据船厂的生产能力、设计能力、资产状况、财务状况、质量状况等各项指标对船厂的接受能力进行预测和评审。
二、报价决策阶段1)总工程师消化技术规格书,并根据船东意见以及生产部门和物资部门的意见制订设备厂商表。
2)经营部门根据设备厂商表进行设备询价,为二次报价做准备。
3)设计部门针对委外设计与船舶设计院或设计公司进行洽谈。
4)设计部门和物资部门针对主要设备和原材料与厂商进行洽谈,质量管理部门就船检费与相关单位进行洽谈。
5)总经济师根据以上前期准备的资料对建造成本进行估算。
6)经营部门根据报价资料编制二次报价表,同时报总经济师进行审核,最终呈报总经理审定生效,经营部门据此对外报价。
三、合同谈判、生效阶段1)总工程师进行技术谈判,项目经理与物资部门参与谈判。
2)总经济师进行商务谈判,财务部门确定保函的基本格式。
3)设计部门根据技术谈判的结果编制相关技术文件,包含技术攻关项目初稿、技术可行性报告;总工程师针对主要设备的技术协议进行预谈。
4)设计部门与船舶设计院或设计公司预谈委外设计合同。
5)经营部门根据商务谈判的结果编制相关商务文件,并制订保函格式。
6)总工程师对技术文件进行审核,并最终呈报总经理审定生效。
7)总经济师对商务文件进行审核,并最终呈报总经理审定生效。
8)经营部门组织总经理、总经济师、总工程师签订船舶生效合同和技术规格书。
9)总工程师联合设计部门组织技术谈判,签订主要设备技术协议。
10)总经济师联合物资部门组织商务谈判,签订主要设备商务合同。
11)经营部门提交主要设备资料给船东确认。
12)经营部门对外发布合同生效通知,同时设计部门委外设计合同生效。
船舶建造工艺流程简要介绍

船舶建造工艺流程简要介绍一、船舶建造工艺流程层次上的划分为:1、生产大节点:开工——上船台(铺底)——下水(出坞)——航海试验——完工交船生产大节点在工艺流程中是某工艺阶段的开工期(或上一个节点的完工期),工艺阶段一般说是两个节点间的施工期。
生产大节点的期限是编制和执行生产计划的基点,框定了船舶建造各工艺阶段的节拍和生产周期;节点的完成日也是船东向船厂分期付款的交割日。
2、工艺阶段:钢材予处理——号料加工——零、部件装配——分段装焊——船台装焊(合拢)——拉线镗孔——船舶下水——发电机动车——主机动车——系泊试验——航海试验——完工交船3、以上工艺阶段还可以进一步进行分解。
4、是以上工艺阶段是按船舶建造形象进度划分的,造船工艺流程是并行工程,即船体建造与舾装作业是并行分道组织,涂装作业安排在分道生产线的两个小阶段之间,船体与舾装分道生产线在各阶段接续地汇入壳舾涂一体化生产流程。
二、船舶建造的前期策划船舶设计建造是一项复杂的系统工程,在开工前船厂必须组织前期策划,一是要扫清技术障碍;二是要解决施工难点。
1、必须吃透“技术说明书”(设计规格书)。
技术说明书是船东提出并经双方技术谈判,以相应国际规范及公约为约束的船舶设计建造的技术要求。
船厂在新船型特别是高附加值船舶的承接中必须慎重对待:必须搞清重要设备运行的采用标准情况、关键技术的工艺条件要求,特别是要排查出技术说明书中暗藏的技术障碍(不排除某些船东存有恶意意图),2、对设计工作的组织。
船舶设计工作分三阶段组织进行——初步设计、详细设计、生产设计。
初步设计:是从收到船东技术任务书或询价开始,进行船舶总体方案的设计。
提供出设计规格说明书、总布置图、舯剖面图、机舱布置图、主要设备厂商表等。
详细设计:在初步设计基础上,通过对各个具体技术专业项目,进行系统原理设计计算,绘制关键图纸,解决设计中的技术问题,最终确定船舶全部技术性能、船体结构、重要材料设备选型和订货要求等。
船舶建造工艺流程
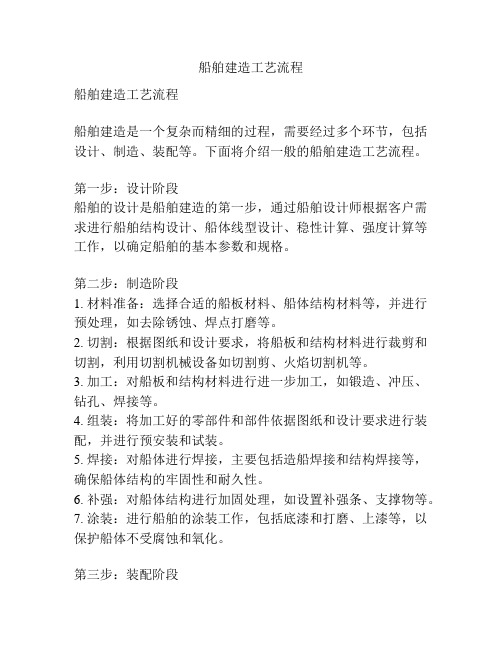
船舶建造工艺流程船舶建造工艺流程船舶建造是一个复杂而精细的过程,需要经过多个环节,包括设计、制造、装配等。
下面将介绍一般的船舶建造工艺流程。
第一步:设计阶段船舶的设计是船舶建造的第一步,通过船舶设计师根据客户需求进行船舶结构设计、船体线型设计、稳性计算、强度计算等工作,以确定船舶的基本参数和规格。
第二步:制造阶段1. 材料准备:选择合适的船板材料、船体结构材料等,并进行预处理,如去除锈蚀、焊点打磨等。
2. 切割:根据图纸和设计要求,将船板和结构材料进行裁剪和切割,利用切割机械设备如切割剪、火焰切割机等。
3. 加工:对船板和结构材料进行进一步加工,如锻造、冲压、钻孔、焊接等。
4. 组装:将加工好的零部件和部件依据图纸和设计要求进行装配,并进行预安装和试装。
5. 焊接:对船体进行焊接,主要包括造船焊接和结构焊接等,确保船体结构的牢固性和耐久性。
6. 补强:对船体结构进行加固处理,如设置补强条、支撑物等。
7. 涂装:进行船舶的涂装工作,包括底漆和打磨、上漆等,以保护船体不受腐蚀和氧化。
第三步:装配阶段1. 机电设备装配:将各类船舶机电设备,如发动机、燃油系统、电气设备、舵机等安装到船体内部。
2. 船舶设施安装:安装各类船舶设施,如舱室、舱门、舷窗等。
3. 舱内装饰:进行舱室的内部装饰,包括地板、墙面、天花板、家具等的安装。
4. 船舶系统调试:对船体进行系统调试,确保各类设备正常运行。
第四步:试航阶段在船舶建造完成后,需要进行试航以验证船舶的性能和安全性,主要包括船舶的航行性能、操纵性能,以及各类设备的运行状况等。
第五步:交付阶段船舶建造完成并通过试航后,进行最后的验收和交付工作。
在交付阶段,船舶建造方需向客户交付船舶,并提供相关的船舶资料和证书。
总结:船舶建造工艺流程是一个复杂而精细的过程,需要经过设计、制造、装配、试航等多个环节。
只有在每个环节都严格按照要求操作,并进行合理的协调和配合,才能保证船舶建造的质量和安全性。
- 1、下载文档前请自行甄别文档内容的完整性,平台不提供额外的编辑、内容补充、找答案等附加服务。
- 2、"仅部分预览"的文档,不可在线预览部分如存在完整性等问题,可反馈申请退款(可完整预览的文档不适用该条件!)。
- 3、如文档侵犯您的权益,请联系客服反馈,我们会尽快为您处理(人工客服工作时间:9:00-18:30)。
造船的主要工艺流程钢材预处理在号料前对钢材进行的矫正,除锈和涂底漆工作•船用钢材常因轧制时压延不均,轧制后冷却收缩不匀或运输,储存过程中其钢材预处理在号料前对钢材进行的矫正,除锈和涂底漆工作船用钢材常因轧制时压延不均,轧制后冷却收缩不匀或运输,储存过程中其他因素的影响而存在各种变形•为此,板材和型材从钢料堆场取出后,先分别用多辊钢板矫平机和型钢矫直机矫正,以保证号料,边缘和成型加工的正常进行•矫正后的钢材一般先经抛光除锈,最后喷涂底漆和烘干这样处理完毕后的钢材即可送去号料•这些工序常组成预处理自动流水线,利用传送滚道与钢料堆场的钢料吊运,号料,边缘加工等后续工序的运输线相衔接,以实现船体零件备料和加工的综合机械化和自动化•放样和号料船体外形通常是光顺的空间曲面•由设计部门提供的用三向投影线表示的船体外形图,称为型线图,一般按1:50或1:100的比例绘制.由于缩尺比大,型线的三向光顺性存在一定的误差,故不能按型线图直接进行船体施工,而需要在造船厂的放样台进行1:1的实尺放样或者是1:5,1:10 的比例放样,以光顺型线,取得正确的型值和施工中所需的每个零件的实际形状尺寸与位置,为后续工序提供必要的施工信息.船体放样是船体建造的基础性工序.号料是将放样后所得的船体零件的实际形状和尺寸,利用样板,样料或草图划在板材或型材上,并注以加工和装配用标记.最早的放样和号料方法是实尺放样,手工号料.20世纪40年代初出现比例放样和投影号料,即按1:5或1:10的比例进行放样制成投影底图,用相应的低倍投影装置放大至实际尺寸;或将投影底图缩小到1/5〜1/10 摄制成投影底片,再用高倍投影装置放大50〜100倍成零件实形,然后在钢材上划线.比例放样还可提供仿形图,供光电跟踪切割机直接切割钢板用,从而省略号料工序.投影号料虽在手工号料的基础上有了很大改进,但仍然未能摆脱手工操作.60年代初开始应用电印号料,即利用静电照相原理,先在钢板表面喷涂光敏导电粉末,进行正片投影曝光,经显影和定影后在钢板上显出零件图形.适用于大尺寸钢板的大型电印号料装置采用同步连续曝光投影方式,即底图和钢板同步移动在运动过程中连续投影曝光•适用于小尺寸钢板的小型电印号料装置,则在钢板上一次投影出全部图形.这种号料方法已得到较广泛的应用•随着电子计算机在造船中的应用,又出现数学放样方法•即用数学方程式表示船体型线或船体表面,以设计型值表和必需的边界条件数值作为原始数据,利用计算机进行反复校验和计算,实现型线修改和光顺,以获得精确光顺和对应投影点完全一致的船体型线•船体的每条型线都由一个特点的数学样条曲线方程表示,并可通过数控绘图机绘出图形•数学放样可取消传统的实尺放样工作,还可为切割和成形加工等后续工序提供控制信息,对船体建造过程的自动化具有关键的作用,是造船工艺的一项重要发展•船体零件加工包括边缘加工和成形加工•边缘加工就是按照号料后在钢材上划出的船体零件实际形状,利用剪床或氧乙炔气割,等离子切割进行剪割•部分零件的边缘还需要用气割机或刨边机进行焊缝坡口的加工.气割设备中的光电跟踪气割机能自动跟踪比例图上的线条,通过同步伺服系统在钢板上进行切割,它可与手工号料,投影号料配合使用.采用数控气割机不但切割精度高,而且根据数学放样资料直接进行切割,可省略号料工序,实现放样,切割过程自动化.对于具有曲度,折角或折边等空间形状的船体板材,在钢板剪割后还需要成形加工,主要是应用辊式弯板机和滚压机进行冷弯;或采用水火成形的加工方法,即在板材上按预定的加热线用氧- 乙炔烘炬进行局部加热,并用水跟踪冷却,使板材产生局部变形,弯成所要求的曲面形状.对于用作肋骨等的型材,则多应用肋骨冷弯机弯制成形.随着数字控制技术的发展,已使用数字控制肋骨冷弯机,并进而研制数字控制弯板机.船体零件加工已从机械化向自动化进展•船体装配和焊接将船体结构的零部件组装成整个船体的过程•普遍采用分段建造方式,分为部件装配焊接,分段装配焊接和船台装配焊接3个阶段进行•①部件装配焊接:又称小合扰•将加工后的钢板或型钢组合成板列,T型材,肋骨框架或船首尾柱等部件的过程,均在车间内装焊平台上进行.②分(总)段装配焊接:又称中合拢.将零部件组合成平面分段,曲面分段或立体分段,如舱壁,船底,舷侧和上层建筑等分段;或组合成在船长方向横截主船体而成的环形立体分段,称为总段,如船首总段,船尾总段等.分段的装配和焊接均在装焊平台或胎架上进行.分段的划分主要取决于船体结构的特点和船厂的起重运输条件.随着船舶的大型化和起重机能力的增大,分段和总段也日益增大,其重量可达800吨以上.③船台(坞)装配焊接:即船体总装,又称大合拢. 将船体零部件,分段,总段在船台(或船坞)上最后装焊成船体•排水量10万吨以上的大型船舶,为保证下水安全,多在造船坞内总装•常用的总装方法有:以总段为总装单元,自船中向船首,船尾吊装的称总段建造法,一般适用于建造中小型船舶;先吊装船中偏尾处的一个底部分段,以此作为建造基准向船首,船尾和上层吊装相邻分段,其吊装范围呈宝塔状的称塔式建造法;设有2〜3个建造基准,分别以塔式建造法建造,最后连接成船体的称岛式建造法;在船台(或船坞)的末端建造第一艘船舶时,在船台的前端同时建造第二艘船舶的尾部,待第一艘船下水后,将第二艘船的尾部移至船台末端,继续吊装其他分段,其至总装成整个船体,同时又在船台前端建造第三艘船舶的尾部,依此类推,这种方法称为串联建造法;将船体划分为首,尾两段,分别在船台上建成后下水,再在水上进行大合拢的称两段建造法•各种总装方法的选择根据船体结构特点和船厂的具体条件而定•船体装配和焊接的工作量,占船体建造总工作量的75%^上,其中焊接又占一半以上•故焊接是造船的关键性工作,它不但直接关系船舶的建造质量,而且关系造船效率•自20世纪50年代起,焊接方法从全手工焊接发展为埋弧自动焊,半自动焊,电渣焊,气体保护电弧焊•自60年代中期起,又有单面焊双面成形,重力焊,自动角焊以及垂直焊和横向自动焊等新技术•焊接设备和焊接材料也有相应发展•由于船体结构比较复杂,在难以施行自动焊和半自动焊的位置仍需要采用手工焊•结合焊接技术的发展,自60年代起,在船体部件和分段装配中开始分别采用T型材装焊流水线和平面分段装焊流水线T型材是构成平面分段骨架的基本构件.平面分段在船体结构中占有相当的比重,例如在大型散装货船和油船上,平面分段可占船体总重的50% 以上.平面分段装焊流水线包括各种专用装配焊接设备,它利用输送装置连续进行进料,拼板焊接以及装焊骨架等作业,能显著地提高分段装配的机械化程度,成为现代造船厂技术改造的主要内容之一•世界上有些船厂对批量生产的大型油船的立体分段也采用流水线生产方式进行装焊和船坞总装•船体总装完成后必须对船体进行密闭性试验,然后在尾部进行轴系和舵系对中,安装轴系,螺旋桨和舵等.在完成各项水下工程后准备下水•船舶下水将在船台(坞)总装完毕的船舶从陆地移入水域的过程.船舶下水时的移行方向或与船长平行,或与船长垂直,分别称为纵向下水和横向下水. 下水滑道主要为木枋滑道和机械化滑道.前者依靠船舶自重滑行下水,使用较普遍;后者利用小车承载船体在轨道上牵引下水,多用在内河中小型船厂.纵向下水之前先将搁置在墩木上的船体转移到滑板和滑道上,滑道向船舶入水方向有一定倾斜当松开设置于滑板与滑道间的制动装置后,船舶由于自重连同滑板和支架一起滑入水中,然后靠自身的浮力飘浮于水面.为减少下滑时的摩擦阻力,在滑板与滑道之间常涂上一定厚度的下水油脂;也可用钢珠代替下水油脂,将滑动摩擦改为滚动摩擦,进一步减少摩擦力.在船坞内总装的船,只要灌水入坞即能浮起,其下水操作比在船台下利用滑道下水简单和安全得多.下水意味着船舶建造已完成了关键性的,主要的工作.按传统习惯,大型船舶下水常举行隆重的庆祝仪式.码头安装(设备和系统的安装)船舶下水后常是靠于厂内舾装码头,以安装船体设备,机电设备, 管道和电缆,并进行舱室的木作,绝缘和油漆等工作.码头安装涉及的工种很多,相互影响也较大.而随着船舶设备和系统的日趋复杂,安装质量的要求也不断提高,故安装工作直接关系下水后能否迅速试航和交船• 为了缩短下水后的安装周期,应尽可能将上述安装工作提前到分段装配和船体总装阶段进行,称为预舾装.将传统的单件安装改为单元组装,也可大大缩短安装周期,即根据机舱和其他舱室设备的布置和组成特点确定安装单元的组成程度,如主机冷却单元可包括换热器,泵,温度调节器,带附件的有关管道和单元所必需的电气设备•在车间内组成安装单元,然后吊至分段,总段或船上安装,这样可使18〜25%勺安装工作量由船上提前到内场进行,能使船上的安装周期缩短15〜20%.系泊试验和航行试验在船体建造和安装工作结束后,为保证建造的完善性和各种设备工作的可靠性,必须进行全面而严格的试验,通常分为两个阶段,即系泊试验和航行试验.系泊试验俗称码头试车,是在系泊状态下对船舶的主机,辅机和其他机电设备进行的一系列实效试验,用以检验安装质量和运转情况.系泊试验以主机试验为核心,检查发电机组和配电设备的工作情况,以便为主机和其他设备的试验创造条件.对各有关系统的协调,应急,遥测遥控和自动控制等还需要进行可靠性和安全性试验.系泊试验时船舶基本上处于静止状态,主机,轴系和有关设备系统不能显示全负荷运转的性能,所以还需要进行航行试验.航行试验是全面地检查船舶在航行状态下主机,辅机以及各种机电设备和系统的使用性能.通常有轻载试航和重载试航.在航行试验中测定船舶的航速,主机功率以及操纵性,回转性,航向稳定性,惯性和指定航区的适航性等•试验结果经验船机构和用户验收合格后,由船厂正式交付订货方使用• 发展近代造船技术的发展过程是由手工操作向机械化,自动化迈进的过程•自50年代起,船体建造用焊接取代了铆接,使船体建造由过去长期使用的零星散装方式改进为分段装配方式,大大提高了造船效率•由于船体结构和形状比较复杂,手工操作在船体建造中一直占较大比重•电子计算机和数控技术的应用正进一步改变造船业的面貌•电子计算机首先应用于数学放样,进而出现数字输入和图形输出的数控绘图机,数控切割机,数控肋骨冷弯机,数控螺旋桨加工机床和管子加工机床等•同时电子计算技术还在造船厂的生产管理,计划编制,材料设备供应和成本核算等方面逐渐得到应用•为减少信息准备工作,消除设计与生产之间的脱节现象,又研制成大型造船集成数控系统,它包括船舶设计,生产和管理等所有功能的通用信息,能协调地完成从设计到生产的整个工作过程•因此,继续扩大计算机在造船中的应用,是现代发展造船技术,进一步提高造船自动化程度的主要方向•。