零件加工工艺过程
典型零件机械加工工艺过程(共29张PPT)精选

第十九页,共29页。
接盘(jiē pán)加工工艺规 程卡片
工序号 工种 工 序 内 容
加工简图
设备
1
锻
锻造毛坯
三爪自定心卡盘夹
小端,粗车大端面
2
车 见平,粗车大外圆
至Ø96。
车床
第二十页,共29页。
工序号 工种 工 序 内 容
加工简图
调头夹大端,粗车
小端面保证总长52,
3
第三页,共29页。
传动轴工艺规程
(guīchéng)卡片
工 序
工 种
工序内容
加工简 图
设 备
1
下 料
圆钢ø60×265
锯 床
车一端面见平;调 2 车 头,车另一端面保
证总长259。
车 床
3
车
钻一端中心孔;钻 另一端中心孔。
车 床
第四页,共29页。
工工 序种
工序内容
加工简 图
设 备
用尾架顶尖顶住,粗
10
铣
深度比图样规定尺 寸多铣0. 25mm,作
为磨削的余量。
加工简图
设 备
铣 床
11 钳 修研两端中心孔
车 床
第九页,共29页。
工工 序种
工序内容
加工简图
设 备
磨外圆Q,M,并用砂
轮端面靠磨台肩H,1,
12 磨 调头,磨外圆N,尸, 靠磨台肩G。
外 圆 磨 床
13 检
检验
第十页,共29页。
2.中间轴机械加工工艺规程 中间轴的材料(cáiliào)为45号钢,生 产批量为600件,中间轴如下图:
第十三页,共29页。
工序号 工序名称
典型零件机械加工工艺过程

典型零件机械加工工艺过程1轴类零件加工分析(1)轴类零件加工的工艺路线1)基本加工路线外圆加工的方法很多,基本加工路线可归纳为四条。
①粗车—半精车—精车对于一般常用材料,这是外圆表面加工采用的最主要的工艺路线。
②粗车—半精车—粗磨—精磨对于黑色金属材料,精度要求高和表面粗糙度值要求较小、零件需要淬硬时,其后续工序只能用磨削而采用的加工路线。
③粗车—半精车—精车—金刚石车对于有色金属,用磨削加工通常不易得到所要求的表面粗糙度,因为有色金属一般比较软,容易堵塞沙粒间的空隙,因此其最终工序多用精车和金刚石车。
④粗车—半精—粗磨—精磨—光整加工对于黑色金属材料的淬硬零件,精度要求高和表面粗糙度值要求很小,常用此加工路线。
2)典型加工工艺路线轴类零件的主要加工表面是外圆表面,也还有常见的特特形表面,因此针对各种精度等级和表面粗糙度要求,按经济精度选择加工方法。
对普通精度的轴类零件加工,其典型的工艺路线如下:毛坯及其热处理—预加工—车削外圆—铣键槽—(花键槽、沟槽)—热处理—磨削—终检。
(1)轴类零件的预加工轴类零件的预加工是指加工的准备工序,即车削外圆之前的工艺。
校直毛坯在制造、运输和保管过程中,常会发生弯曲变形,为保证加工余量的均匀及装夹可靠,一般冷态下在各种压力机或校值机上进行校值,(2)轴类零件加工的定位基准和装夹1)以工件的中心孔定位在轴的加工中,零件各外圆表面,锥孔、螺纹表面的同轴度,端面对旋转轴线的垂直度是其相互位置精度的主要项目,这些表面的设计基准一般都是轴的中心线,若用两中心孔定位,符合基准重合的原则。
中心孔不仅是车削时的定为基准,也是其它加工工序的定位基准和检验基准,又符合基准统一原则。
当采用两中心孔定位时,还能够最大限度地在一次装夹中加工出多个外圆和端面。
2)以外圆和中心孔作为定位基准(一夹一顶)用两中心孔定位虽然定心精度高,但刚性差,尤其是加工较重的工件时不够稳固,切削用量也不能太大。
典型零件的加工工艺
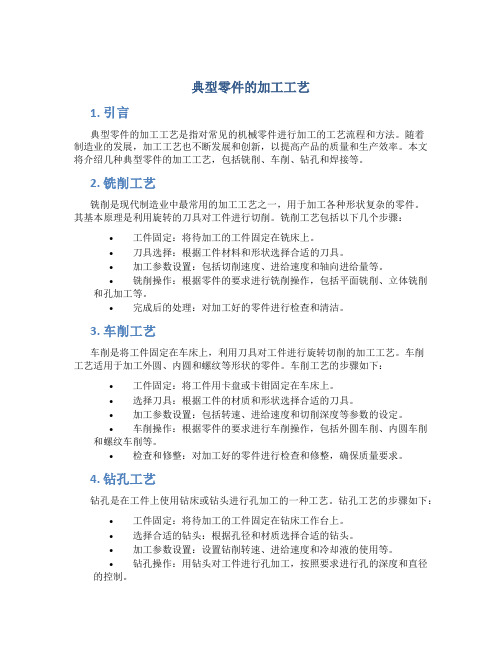
典型零件的加工工艺1. 引言典型零件的加工工艺是指对常见的机械零件进行加工的工艺流程和方法。
随着制造业的发展,加工工艺也不断发展和创新,以提高产品的质量和生产效率。
本文将介绍几种典型零件的加工工艺,包括铣削、车削、钻孔和焊接等。
2. 铣削工艺铣削是现代制造业中最常用的加工工艺之一,用于加工各种形状复杂的零件。
其基本原理是利用旋转的刀具对工件进行切削。
铣削工艺包括以下几个步骤:•工件固定:将待加工的工件固定在铣床上。
•刀具选择:根据工件材料和形状选择合适的刀具。
•加工参数设置:包括切削速度、进给速度和轴向进给量等。
•铣削操作:根据零件的要求进行铣削操作,包括平面铣削、立体铣削和孔加工等。
•完成后的处理:对加工好的零件进行检查和清洁。
3. 车削工艺车削是将工件固定在车床上,利用刀具对工件进行旋转切削的加工工艺。
车削工艺适用于加工外圆、内圆和螺纹等形状的零件。
车削工艺的步骤如下:•工件固定:将工件用卡盘或卡钳固定在车床上。
•选择刀具:根据工件的材质和形状选择合适的刀具。
•加工参数设置:包括转速、进给速度和切削深度等参数的设定。
•车削操作:根据零件的要求进行车削操作,包括外圆车削、内圆车削和螺纹车削等。
•检查和修整:对加工好的零件进行检查和修整,确保质量要求。
4. 钻孔工艺钻孔是在工件上使用钻床或钻头进行孔加工的一种工艺。
钻孔工艺的步骤如下:•工件固定:将待加工的工件固定在钻床工作台上。
•选择合适的钻头:根据孔径和材质选择合适的钻头。
•加工参数设置:设置钻削转速、进给速度和冷却液的使用等。
•钻孔操作:用钻头对工件进行孔加工,按照要求进行孔的深度和直径的控制。
•清洁和检查:对加工好的孔进行清理和检查,确保孔的质量。
5. 焊接工艺焊接是将两个或多个工件通过熔化和凝固的过程连接在一起的工艺。
焊接工艺的步骤如下:•工件准备:准备待焊接的工件,包括清洁和坡口处理等。
•焊接机器设置:根据材料和焊接方式设置焊接机器的参数,包括电流、电压和焊接速度等。
零件加工工艺流程

零件加工工艺流程零件加工是指将原材料经过一系列工艺加工,将其转化为具有特定形状和尺寸的产品。
下面是一篇关于零件加工工艺流程的介绍。
零件加工工艺流程是一个基于设计图纸的生产流程,它通常包括以下几个步骤:设计分析、工艺规划、加工准备、加工操作和质量控制。
首先是设计分析。
在这一步骤中,工艺师会仔细分析设计图纸,并确定零件的材料、工艺特点、尺寸和形状等关键要素。
他们还会进行模拟分析,以确保加工过程的可行性和结果的准确性。
接下来是工艺规划。
基于设计分析的结果,工艺师会制定出零件加工的具体方案。
这个方案包括选择适当的加工设备、工艺参数和工艺顺序。
工艺规划还涉及到工艺的经济性和工期的控制,以确保加工过程的效率和成本的可控性。
然后是加工准备。
在这一步骤中,工艺师会准备好所需的加工设备和工装夹具。
他们会检查和调整设备的性能,并进行所需的维护。
此外,他们还会准备好所需的刀具、磨具和润滑剂等加工工具和辅助材料。
接下来是加工操作。
在这一步骤中,工艺师会根据工艺规划的要求,进行具体的加工操作。
这包括将设备和工装夹具设置到合适的位置和状态,安装和调整刀具和磨具,控制加工参数,进行零件的切削、成型、抛光和检测等操作。
最后是质量控制。
在加工过程中,工艺师会进行各种质量控制措施,以确保加工结果的准确性和一致性。
这包括对加工后的零件进行尺寸和形状的测量和检测,并与设计要求进行比较。
如果发现问题,工艺师会采取相应的纠正措施,以确保零件的质量和性能达到要求。
总结起来,零件加工工艺流程是一个严谨而复杂的过程,它需要工艺师具备扎实的专业知识和技能。
通过设计分析、工艺规划、加工准备、加工操作和质量控制等环节的有效协作,可以实现零件加工过程的高效、高质和可控。
零件的加工工艺流程
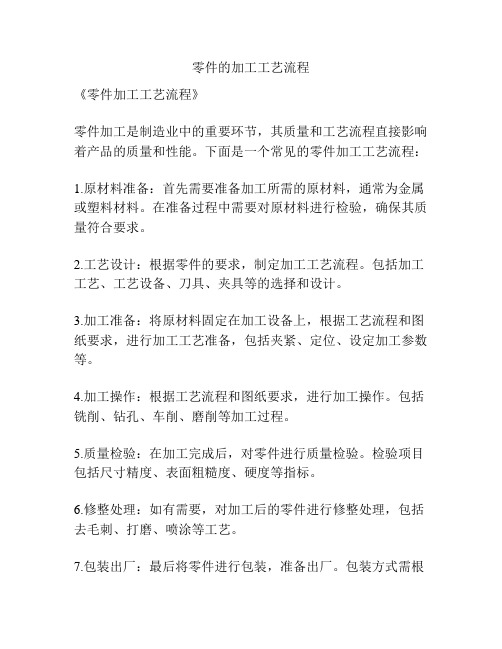
零件的加工工艺流程
《零件加工工艺流程》
零件加工是制造业中的重要环节,其质量和工艺流程直接影响着产品的质量和性能。
下面是一个常见的零件加工工艺流程:
1.原材料准备:首先需要准备加工所需的原材料,通常为金属或塑料材料。
在准备过程中需要对原材料进行检验,确保其质量符合要求。
2.工艺设计:根据零件的要求,制定加工工艺流程。
包括加工工艺、工艺设备、刀具、夹具等的选择和设计。
3.加工准备:将原材料固定在加工设备上,根据工艺流程和图纸要求,进行加工工艺准备,包括夹紧、定位、设定加工参数等。
4.加工操作:根据工艺流程和图纸要求,进行加工操作。
包括铣削、钻孔、车削、磨削等加工过程。
5.质量检验:在加工完成后,对零件进行质量检验。
检验项目包括尺寸精度、表面粗糙度、硬度等指标。
6.修整处理:如有需要,对加工后的零件进行修整处理,包括去毛刺、打磨、喷涂等工艺。
7.包装出厂:最后将零件进行包装,准备出厂。
包装方式需根
据零件的尺寸、重量和特性来选择,确保运输过程中不被损坏。
以上就是一个典型的零件加工工艺流程。
在实际生产中,还要根据零件的特性和要求进行具体的调整和处理,以确保生产出具有优良质量和性能的零件。
零件加工的步骤怎么做_零件加工的步骤有哪些

零件加工的步骤怎么做_零件加工的步骤有哪些零件加工的,这中间要走什么样一个流程或者是步骤,那么你对关于零件加工的步骤到底要怎么做有兴趣吗?下面就由店铺为你带来零件加工的步骤怎么做分析,希望你喜欢。
零件加工的步骤怎么做以下面做例子:一、加工要求加工如下图所示零件。
零件材料为 LY12 ,单件生产。
零件毛坯已加工到尺寸。
选用设备: V-80 加工中心二、准备工作加工以前完成相关准备工作,包括工艺分析及工艺路线设计、刀具及夹具的选择、程序编制等。
三、操作步骤及内容1、开机,各坐标轴手动回机床原点2、刀具准备根据加工要求选择Φ20 立铣刀、Φ5中心钻、Φ8麻花钻各一把,然后用弹簧夹头刀柄装夹Φ20立铣刀,刀具号设为T01,用钻夹头刀柄装夹Φ5中心钻、Φ8麻花钻,刀具号设为T02、T03,将对刀工具寻边器装在弹簧夹头刀柄上,刀具号设为 T04 。
3 、将已装夹好刀具的刀柄采用手动方式放入刀库,即1 )输入“T01 M06” ,执行2 )手动将 T01 刀具装上主轴3 )按照以上步骤依次将 T02 、 T03 、 T04 放入刀库4、清洁工作台,安装夹具和工件将平口虎钳清理干净装在干净的工作台上,通过百分表找正、找平虎钳,再将工件装正在虎钳上。
5、对刀,确定并输入工件坐标系参数1 )用寻边器对刀,确定 X 、 Y 向的零偏值,将 X 、 Y 向的零偏值输入到工件坐标系 G54 中, G54 中的 Z 向零偏值输为 0 ;2 )将 Z 轴设定器安放在工件的上表面上,从刀库中调出 1 号刀具装上主轴,用这把刀具确定工件坐标系 Z向零偏值,将 Z 向零偏值输入到机床对应的长度补偿代码中,“+” 、“-” 号由程序中的 G43 、G44 来确定,如程序中长度补偿指令为 G43 ,则输入“-” 的 Z 向零偏值到机床对应的长度补偿代码中;3 )以同样的步骤将 2 号、 3 号刀具的 Z 向零偏值输入到机床对应的长度补偿代码中。
典型的零件加工工艺过程
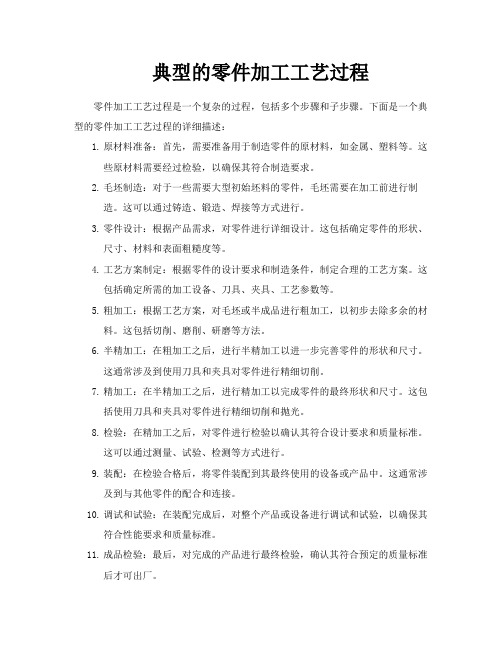
典型的零件加工工艺过程零件加工工艺过程是一个复杂的过程,包括多个步骤和子步骤。
下面是一个典型的零件加工工艺过程的详细描述:1.原材料准备:首先,需要准备用于制造零件的原材料,如金属、塑料等。
这些原材料需要经过检验,以确保其符合制造要求。
2.毛坯制造:对于一些需要大型初始坯料的零件,毛坯需要在加工前进行制造。
这可以通过铸造、锻造、焊接等方式进行。
3.零件设计:根据产品需求,对零件进行详细设计。
这包括确定零件的形状、尺寸、材料和表面粗糙度等。
4.工艺方案制定:根据零件的设计要求和制造条件,制定合理的工艺方案。
这包括确定所需的加工设备、刀具、夹具、工艺参数等。
5.粗加工:根据工艺方案,对毛坯或半成品进行粗加工,以初步去除多余的材料。
这包括切削、磨削、研磨等方法。
6.半精加工:在粗加工之后,进行半精加工以进一步完善零件的形状和尺寸。
这通常涉及到使用刀具和夹具对零件进行精细切削。
7.精加工:在半精加工之后,进行精加工以完成零件的最终形状和尺寸。
这包括使用刀具和夹具对零件进行精细切削和抛光。
8.检验:在精加工之后,对零件进行检验以确认其符合设计要求和质量标准。
这可以通过测量、试验、检测等方式进行。
9.装配:在检验合格后,将零件装配到其最终使用的设备或产品中。
这通常涉及到与其他零件的配合和连接。
10.调试和试验:在装配完成后,对整个产品或设备进行调试和试验,以确保其符合性能要求和质量标准。
11.成品检验:最后,对完成的产品进行最终检验,确认其符合预定的质量标准后才可出厂。
除了以上提到的加工工艺过程,还有热处理、表面处理等附加处理步骤。
这些步骤是为了改变零件内部的微观结构和性能,以满足特定的工作要求和使用环境。
例如,热处理可以提高材料的强度、硬度和耐磨性;表面处理可以增强材料的耐腐蚀性和美观性,同时提高其工作性能和使用寿命。
需要注意的是,零件加工工艺过程是一个复杂的过程,需要专业的技术人员和先进的设备来保证其质量和效率。
典型零件机械加工工艺过程
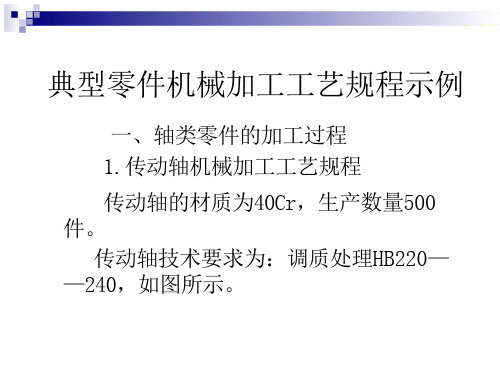
1
下料
工序内容 圆钢下料
机床和刀具 锯床、铁锯
工序 简图
工序号 2
工序名称
工序内容
车端面见平,钻中心孔;粗车四个台阶;
粗车 掉头车端面保证总长,钻中心孔;粗车 一个台阶。
机床和刀具
车床 车刀、中心
钻
工序 简图
工序号 3
工序名称
工序内容
半精车
半精车三个台阶;切槽三个,倒角三个; 调头半精车一个台阶;切槽一个,倒角 一个。
工种 工 序 内 容 划Ø32支承孔两端
钳 面线。
平口钳装夹工件;
7
铣 粗铣两个端面长
32㎜。
加工简图
设备
铣床
三面 刃 铣刀
工序号 工种 工 序 内 容
划Ø32支承孔的十
8
钳
字线及圆孔线。
花盘-弯板装夹工
件,参照十字线钻
孔;
半精车两端面及支
9
车
承孔、倒角;
精车两端面及支承
孔。
10
检
检查
加工简图
设备
典型零件机械加工工艺规程示例
一、轴类零件的加工过程 1.传动轴机械加工工艺规程
传动轴的材质为40Cr,生产数量500 件。
传动轴技术要求为:调质处理HB220— —240,如图所示。
传动轴工艺规程卡片
工工 序种
工序内容
设
加工简 图
备
下
锯
1 料 圆钢ø60×265
床
车一端面见平;调
2 车 头,车另一端面保 证总长259。
7
检
工序内容 最终检查。
机床和刀具
工序 简图
二、盘套类零件的加工过程 1. 接盘机械加工工艺规程。 接盘材质为45钢,生产数量500件。 接盘技术要求为:调质处理HB220—— 240,如图所示。
轴类零件加工工艺的过程
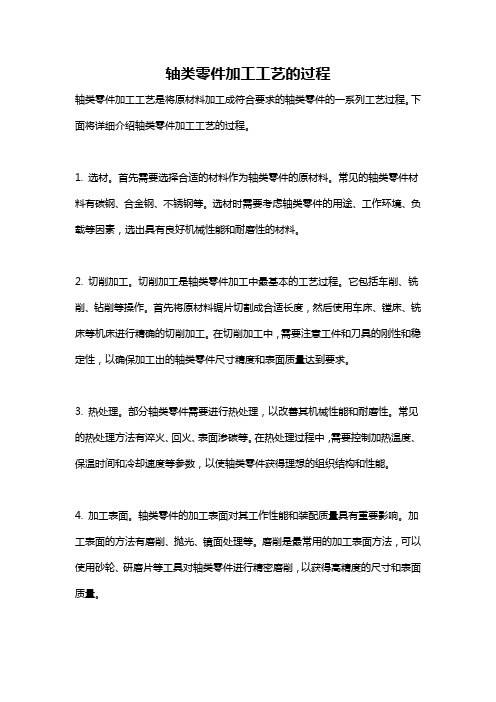
轴类零件加工工艺的过程轴类零件加工工艺是将原材料加工成符合要求的轴类零件的一系列工艺过程。
下面将详细介绍轴类零件加工工艺的过程。
1. 选材。
首先需要选择合适的材料作为轴类零件的原材料。
常见的轴类零件材料有碳钢、合金钢、不锈钢等。
选材时需要考虑轴类零件的用途、工作环境、负载等因素,选出具有良好机械性能和耐磨性的材料。
2. 切削加工。
切削加工是轴类零件加工中最基本的工艺过程。
它包括车削、铣削、钻削等操作。
首先将原材料锯片切割成合适长度,然后使用车床、镗床、铣床等机床进行精确的切削加工。
在切削加工中,需要注意工件和刀具的刚性和稳定性,以确保加工出的轴类零件尺寸精度和表面质量达到要求。
3. 热处理。
部分轴类零件需要进行热处理,以改善其机械性能和耐磨性。
常见的热处理方法有淬火、回火、表面渗碳等。
在热处理过程中,需要控制加热温度、保温时间和冷却速度等参数,以使轴类零件获得理想的组织结构和性能。
4. 加工表面。
轴类零件的加工表面对其工作性能和装配质量具有重要影响。
加工表面的方法有磨削、抛光、镜面处理等。
磨削是最常用的加工表面方法,可以使用砂轮、研磨片等工具对轴类零件进行精密磨削,以获得高精度的尺寸和表面质量。
5. 组装。
在零件加工完成后,需要进行零件的组装。
轴类零件的组装通常需要与其他零件配合使用,如轴套、轴承、齿轮等。
在组装过程中,需要注意零件的配合间隙和装配顺序,以确保零件的配合精度和工作可靠性。
6. 检测。
最后,对加工完成的轴类零件进行检测。
常见的检测方法有尺寸测量、硬度测量、外观检查等。
通过检测,可以判断轴类零件是否达到要求,并进行必要的修正和改进。
综上所述,轴类零件加工工艺的过程包括选材、切削加工、热处理、加工表面、组装和检测等环节。
每个环节都需要严格控制,以确保加工出的轴类零件具有良好的机械性能、尺寸精度和表面质量,能够满足工程需求。
零件加工的工艺流程
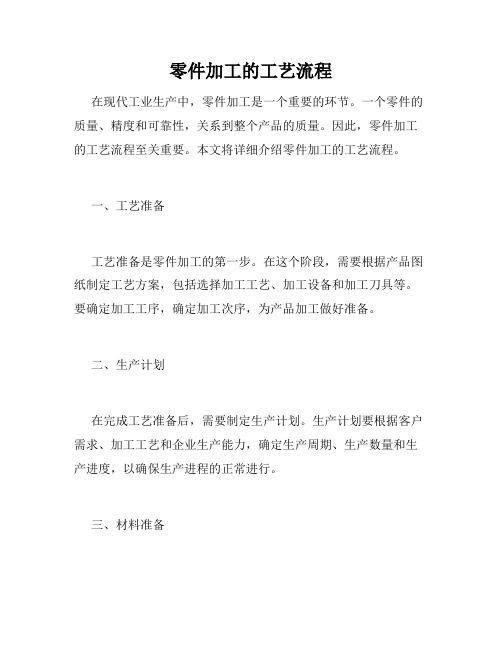
零件加工的工艺流程在现代工业生产中,零件加工是一个重要的环节。
一个零件的质量、精度和可靠性,关系到整个产品的质量。
因此,零件加工的工艺流程至关重要。
本文将详细介绍零件加工的工艺流程。
一、工艺准备工艺准备是零件加工的第一步。
在这个阶段,需要根据产品图纸制定工艺方案,包括选择加工工艺、加工设备和加工刀具等。
要确定加工工序,确定加工次序,为产品加工做好准备。
二、生产计划在完成工艺准备后,需要制定生产计划。
生产计划要根据客户需求、加工工艺和企业生产能力,确定生产周期、生产数量和生产进度,以确保生产进程的正常进行。
三、材料准备在进行零件加工之前,需要准备原材料。
原材料的品质将直接影响到零件加工的质量和成本。
通常情况下,选用的加工材料包括铁、铜、铝、钢等金属材料,以及塑料、橡胶、陶瓷等非金属材料。
四、数控编程数控编程是当代数字化加工的重要步骤。
数控编程是将加工工艺参数编写到计算机中,通过计算机控制加工设备进行精确加工。
数控编程需要具备精准计算、画图等技能,以确保零件加工的精度和可靠性。
五、加工加工是零件加工的核心步骤。
加工过程中需要运用多种加工方法和设备,包括车床、磨床、钻床、锯床、铣床等机床加工方式。
而常用的加工方式包括切削加工、折弯加工、热加工等。
通常情况下,需要多次加工和检验,以满足客户要求和企业内部质量控制标准。
六、细节处理在加工完成之后,需要进行细节处理。
这个步骤包括研磨、清洗、防锈等处理。
这些处理步骤将有助于提高产品的质量和性能,保证产品使用寿命和稳定性。
七、检验检验是零件加工的最后步骤。
在检验中需要对加工出的零件进行多次严密检验,以确保零件的精度和质量达到标准要求。
检验手段包括物理检验、化学检验、光学检验、三坐标检测等技术手段。
如果零件未过检验,则需要返工或废品处理,以确保加工出来的产品符合标准质量。
结论在现代数字化生产的环境下,零件加工已经成为了一项复杂且精细的工作。
而且随着人工智能的发展,数字化生产也将更加自主和高效。
零件加工工艺流程_零件加工工序过程【详解】
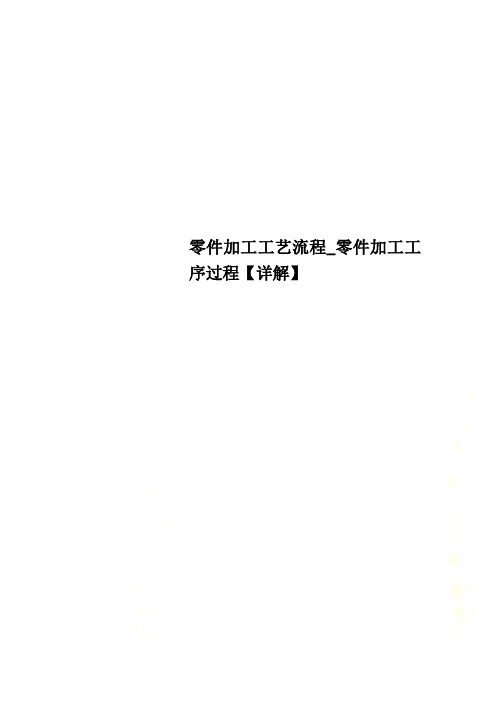
零件加工工艺流程_零件加工工序过程【详解】零件加工工艺流程_零件加工工序过程内容来源网络,由深圳机械展收集整理!零件加工工艺过程的基本知识在制造生产过程中,由于零件的要求和生产条件等不同,其制造工艺方案也不相同。
相同的零件采用不同的工艺方案生产时,其生产效率、经济效益也是不相同的。
在确保零件质量的前提下,拟定具有良好的综合技术经济效益、合理可行的工艺方案的过程称为零件的工艺过程设计。
一、生产过程和工艺过程1. 生产过程由设计图纸变为产品,要经过一系列的制造过程。
通常将原材料或半成品转变成为产品所经过的全部过程称作生产过程。
生产过程通常包括:(1)技术准备过程包括产品投产前的市场调查、预测、新产品鉴定、工艺设计、审查等。
(2) 或工艺过程指直接改变原材料半成品的尺寸、形状、表面的相互位置、表面粗糙度或性能,使之成为成品的过程。
例如液态成形、塑变成形、焊接、粉末成形、切削加工、热处理、表面处理、装配等,都属于工艺过程。
将合理的工艺过程编写成用以指导生产的技术文件,这份技术文件称作工艺规程。
(3)辅助生产过程指为了基本生产过程的正常进行所必须的辅助生产活动。
(4)生产服务过程指原材料的组织、运输、保管、储存、供应及产品包装、销售等过程。
2. 工艺过程的组成零件的切削加工工艺过程由许多工序组合而成,每个工序又由工位、工步、走刀和安装组成。
(1)工序指在一台机床上或在同一个工作地点对一个或一组工件连续完成的那部分工艺过程。
划分工序的依据是工作地点是否变化和工作是否连续。
图2-1所示阶梯轴的加工工艺过程见表2-1。
表2一1工序的划分,是由一个人在一台车床上连续完成车两端面、钻两顶尖孔后,便换一个工件加工,重复以上内容,则这部分工艺过程为一个工序。
该人又在同一台车床上连续完成粗车各外圆、半精车各外圆、倒角后,便换一个工件加工,重复以上内容,则这部分工艺过程又为一个工序。
如果是由一个人在一台车床上连续完成车两端面、钻两顶尖孔、粗车各外圆、半精车各外圆、倒角后再换第二个工件重复这些内容,则这部分工艺过程是一个工序,而不是两个工序。
轴类零件加工工艺的过程
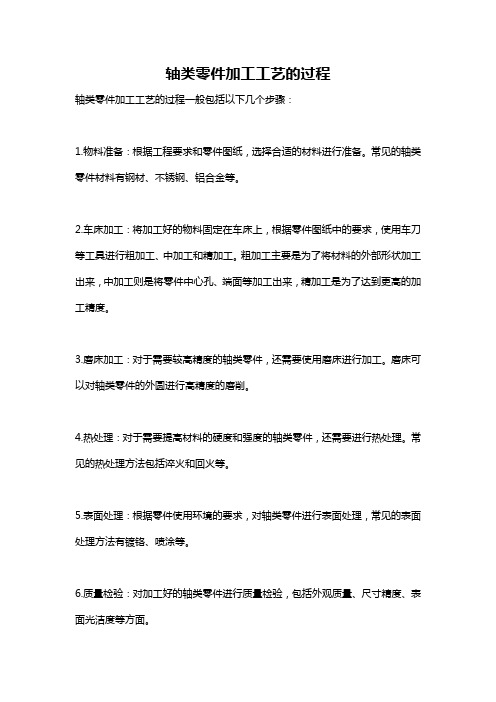
轴类零件加工工艺的过程
轴类零件加工工艺的过程一般包括以下几个步骤:
1.物料准备:根据工程要求和零件图纸,选择合适的材料进行准备。
常见的轴类零件材料有钢材、不锈钢、铝合金等。
2.车床加工:将加工好的物料固定在车床上,根据零件图纸中的要求,使用车刀等工具进行粗加工、中加工和精加工。
粗加工主要是为了将材料的外部形状加工出来,中加工则是将零件中心孔、端面等加工出来,精加工是为了达到更高的加工精度。
3.磨床加工:对于需要较高精度的轴类零件,还需要使用磨床进行加工。
磨床可以对轴类零件的外圆进行高精度的磨削。
4.热处理:对于需要提高材料的硬度和强度的轴类零件,还需要进行热处理。
常见的热处理方法包括淬火和回火等。
5.表面处理:根据零件使用环境的要求,对轴类零件进行表面处理,常见的表面处理方法有镀铬、喷涂等。
6.质量检验:对加工好的轴类零件进行质量检验,包括外观质量、尺寸精度、表面光洁度等方面。
7.包装出库:将通过质量检验的轴类零件进行包装,并进行出库准备,便于交付给客户或下一道工序使用。
以上是轴类零件加工工艺的基本过程,实际操作中还需要根据具体情况进行调整和改进。
同时,为了确保加工质量和效率,还需要合理选择和使用适当的加工设备和工具。
典型零件加工工艺过程PPT课件

.
22
CA6140. 车床主轴图
23
主轴的机械加工工艺过程
➢主轴加工工艺过程制订的依据 主轴的结构;技术要求;生产批量;
设备条件 ➢主轴加工工艺过程 批量:大批;材料:45钢;毛坯:模
锻件
.
24
➢工艺过程: 分为三个阶段(参见表5-5):
粗加工:工序 1~6 半精加工:工序 7~13(7为预备) 精加工:工序 14~26(14为预备)
.
63
箱孔与孔的位置精度 引起轴安装歪斜,致使主轴径向跳动 和轴向窜动,加剧轴承磨损 同一轴线上各孔的同轴度误差 孔端面对轴线垂直度误差
.
64
孔和平面的位置精度
主要是规定主要孔和主轴箱安装基 面的平行度
主要平面的精度
影响主轴箱与床身的连接刚度
规定底面和导向面必须平直和相互 垂直
平面度、垂直度公差等级为5级
第二节
典型零件加工 工艺过程
机械制造工程——第五章
.
1
一、轴(杆)类零件的加工
1.轴类零件的分类、技术要求
➢轴类零件的作用 支撑传动零件; 承受载荷; 传递扭矩。
.
2
➢轴类零件的特点 长度大于直径; 加工表面为内外圆柱面、圆锥面、
螺纹、花键、沟轴 阶梯轴 空心轴 异形轴(曲轴、齿轮轴、偏心轴、
.
38
➢加工顺序的安排和工序的确定
三种方案
粗加工外圆→钻深孔→精加工外圆→ 粗加工锥孔→精加工锥孔
粗加工外圆→钻深孔→粗加工锥孔→ 精加工锥孔→精加工外圆
粗加工外圆→钻深孔→粗加工锥孔→ 精加工外圆→精加工锥孔
.
39
工序确定的两个原则
➢工序中所用的基准应在该工序前加工
零件加工工艺流程
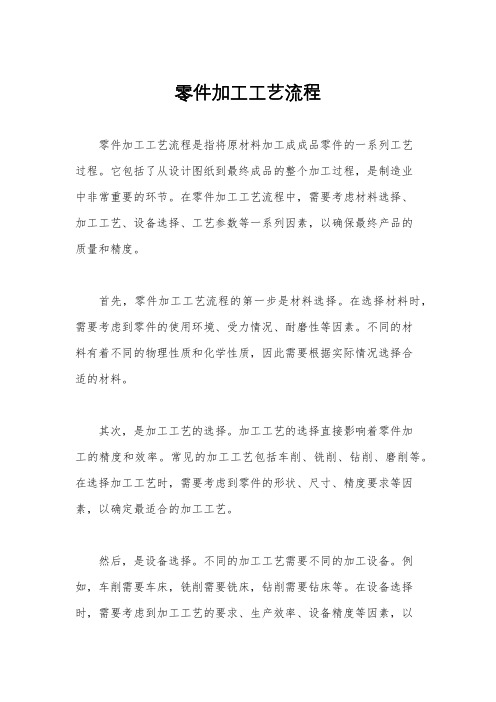
零件加工工艺流程零件加工工艺流程是指将原材料加工成成品零件的一系列工艺过程。
它包括了从设计图纸到最终成品的整个加工过程,是制造业中非常重要的环节。
在零件加工工艺流程中,需要考虑材料选择、加工工艺、设备选择、工艺参数等一系列因素,以确保最终产品的质量和精度。
首先,零件加工工艺流程的第一步是材料选择。
在选择材料时,需要考虑到零件的使用环境、受力情况、耐磨性等因素。
不同的材料有着不同的物理性质和化学性质,因此需要根据实际情况选择合适的材料。
其次,是加工工艺的选择。
加工工艺的选择直接影响着零件加工的精度和效率。
常见的加工工艺包括车削、铣削、钻削、磨削等。
在选择加工工艺时,需要考虑到零件的形状、尺寸、精度要求等因素,以确定最适合的加工工艺。
然后,是设备选择。
不同的加工工艺需要不同的加工设备。
例如,车削需要车床,铣削需要铣床,钻削需要钻床等。
在设备选择时,需要考虑到加工工艺的要求、生产效率、设备精度等因素,以选择最合适的加工设备。
接着,是工艺参数的确定。
在进行零件加工时,需要确定一系列工艺参数,如切削速度、进给速度、切削深度等。
这些工艺参数直接影响着加工效率和零件质量,因此需要根据实际情况进行合理的确定。
最后,是加工过程中的质量控制。
在零件加工过程中,需要进行质量检测和控制,以确保加工出来的零件符合设计要求。
常见的质量控制手段包括尺寸测量、表面质量检查、材料成分分析等。
综上所述,零件加工工艺流程是一个复杂而严谨的过程,需要考虑到诸多因素。
只有在材料选择、加工工艺选择、设备选择、工艺参数确定和质量控制等方面做到科学合理,才能够保证最终加工出的零件质量和精度。
在今后的工作中,我们需要不断学习和积累经验,以提高零件加工工艺的水平,为企业的发展做出贡献。
零件的加工工艺包括哪些

零件的加工工艺包括哪些零件的加工工艺是指将原材料经过一系列的工艺操作,按照要求对其进行切削、打磨、镗孔、车削等加工,以便使其达到使用要求的过程。
下面将详细介绍零件加工工艺的主要环节。
1. 零件的设计与规划:首先,在零件加工之前必须进行零件的设计与规划,确定零件的材料、尺寸、形状、加工要求等。
2. 材料的准备与切割:根据零件的要求,选择合适的材料并对其进行切割。
通常使用锯床、火焰切割机等设备进行切割。
3. 粗加工:粗加工是指在工件上去除大量剩余材料的加工过程。
常见的粗加工方法有铣削、钻孔、镗削等。
4. 精加工:精加工是指在零件上进一步去除较少量的剩余材料,以达到更高的尺寸精度和表面质量要求。
常见的精加工方法有车削、铣削、磨削、钻孔等。
5. 零件的热处理:在必要的情况下,对零件进行热处理,以改变其组织结构和性能。
常见的热处理方法有淬火、回火、退火等。
6. 表面处理:根据零件的要求,对其进行表面处理,以提高其耐腐蚀性、装饰性或降低摩擦系数等。
常见的表面处理方法有电镀、喷涂、氮化等。
7. 安装与装配:根据零件的使用要求,进行零件的组装与安装。
根据零件的不同形状和功能,装配过程可能包括焊接、螺纹连接、插接等。
8. 检验与测试:在零件加工完成后,对其进行质量检验与测试,以确保其达到设计要求。
常见的检验方法有尺寸测量、硬度测试、金相分析等。
9. 包装与运输:对加工完成的零件进行包装,以防止在运输过程中的损坏。
通常使用适当的包装材料和方法,如木箱、泡沫垫等。
10. 质量控制与记录:对零件加工过程中的质量进行控制与记录,以便追溯和改进生产工艺。
通过质量控制和记录,可以及时发现并纠正加工中的问题,提高产品质量。
总结:零件的加工工艺包括设计与规划、材料准备与切割、粗加工、精加工、热处理、表面处理、装配、检验与测试、包装与运输以及质量控制与记录等环节。
每个环节都是零件加工中必不可少的步骤,只有经过一系列工艺的处理,才能在形状、尺寸和性能上满足使用要求。
轴类零件加工工艺过程
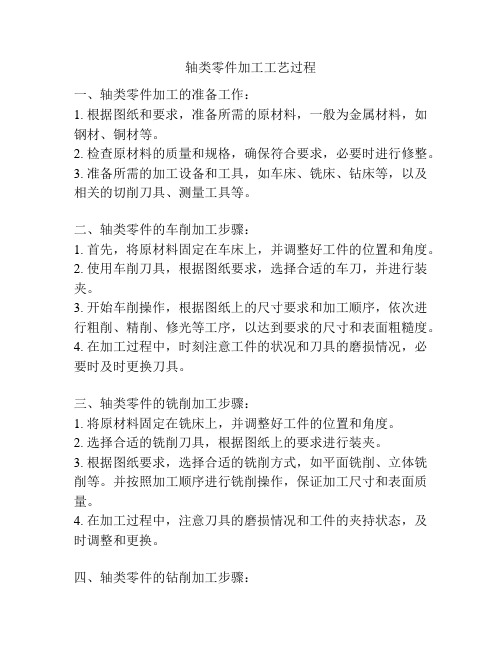
轴类零件加工工艺过程一、轴类零件加工的准备工作:1. 根据图纸和要求,准备所需的原材料,一般为金属材料,如钢材、铜材等。
2. 检查原材料的质量和规格,确保符合要求,必要时进行修整。
3. 准备所需的加工设备和工具,如车床、铣床、钻床等,以及相关的切削刀具、测量工具等。
二、轴类零件的车削加工步骤:1. 首先,将原材料固定在车床上,并调整好工件的位置和角度。
2. 使用车削刀具,根据图纸要求,选择合适的车刀,并进行装夹。
3. 开始车削操作,根据图纸上的尺寸要求和加工顺序,依次进行粗削、精削、修光等工序,以达到要求的尺寸和表面粗糙度。
4. 在加工过程中,时刻注意工件的状况和刀具的磨损情况,必要时及时更换刀具。
三、轴类零件的铣削加工步骤:1. 将原材料固定在铣床上,并调整好工件的位置和角度。
2. 选择合适的铣削刀具,根据图纸上的要求进行装夹。
3. 根据图纸要求,选择合适的铣削方式,如平面铣削、立体铣削等。
并按照加工顺序进行铣削操作,保证加工尺寸和表面质量。
4. 在加工过程中,注意刀具的磨损情况和工件的夹持状态,及时调整和更换。
四、轴类零件的钻削加工步骤:1. 将原材料固定在钻床上,并调整好工件的位置和角度。
2. 选择合适的钻孔刀具,根据图纸要求进行装夹。
3. 根据图纸上的孔径要求,选择合适的钻头,并进行设定,调整钻头的速度和进给量。
4. 开始钻削操作,根据图纸上的孔径位置进行钻孔,保证加工尺寸和孔壁的质量。
5. 在加工过程中,注意刀具的磨损情况和冷却液的使用,及时调整和更换。
五、轴类零件加工的后续工序:1. 进行工件的检验,包括尺寸测量、表面质量等,确保符合要求。
2. 进行必要的热处理、表面处理等工艺,以提高工件的性能和耐用度。
3. 进行最后的整理和打磨工作,使工件达到最终的要求。
4. 进行产品的包装和出库。
以上就是轴类零件加工的基本工艺过程,通过严格按照要求进行加工操作,可以确保加工出高质量的轴类零件。
加工过程中需要密切关注工件的状况和刀具的磨损情况,及时调整和更换,以保证加工质量和工艺效率。
典型零件机械加工工艺过程

典型零件机械加工工艺过程
典型零件的机械加工工艺过程通常包括选择工艺路线、准备工作、粗加工、半精加工、精加工和装配等几个主要阶段。
首先,在选择工艺路线中,需要根据零件的形状、材料和加工要求等因素,确定合适的工艺路线。
选择工艺路线时需要考虑到加工效率、加工质量和加工成本等因素。
接下来是准备工作阶段。
首先,需要准备所需的设备、工具和材料,确保工艺过程中的各种资源和条件得到满足。
然后,对零件进行工艺分析和加工工艺规程编制,确定加工的方法、工序和工艺参数等。
在粗加工阶段,一般采用先粗后精的原则,首先对零件进行粗加工。
粗加工的目的是通过去除多余的材料,使零件逐渐接近最终形状,并为后续的半精加工和精加工提供参考形位。
半精加工是在粗加工的基础上,进一步去除材料并修整加工表面。
半精加工的目的是为了进一步减少精加工的量和提高整体加工质量。
精加工是最后一道工序,主要通过切削或磨削等工艺方法,使零件达到最终的外形、尺寸和表面质量要求。
精加工要求高精度和良好的表面质量。
最后是装配阶段,在完成零件的加工后,根据装配图纸或要求,将零件按照一定的顺序进行组合,形成最终的产品。
装配过程中需要注意配合面的精度和技术要求,确保零件的装配精度和装配质量。
总结起来,典型零件的机械加工工艺过程包括选择工艺路线、准备工作、粗加工、半精加工、精加工和装配。
每个阶段都有其特定的目标和要求,通过合理的工艺安排和优化的加工方法,可以实现高质量的零件加工。
机械零部件加工的流程和步骤

机械零部件加工的流程和步骤机械零部件加工的流程和步骤在现代制造业中,机械零部件加工是一个非常重要的环节。
机械零部件加工过程中,需要经历多个步骤和流程,以确保最终产品的质量和性能。
本文将深入探讨机械零部件加工的流程和步骤,并分享我对这个主题的观点和理解。
一、零部件加工的流程概述机械零部件加工的流程可以大致分为以下几个步骤:设计和规划、材料准备、加工工艺选择、数控编程、设备调试和加工、质量检验与测试。
1. 设计和规划在加工零部件之前,设计和规划阶段非常关键。
在这个阶段,工程师需要根据产品的要求和规范,绘制详细的图纸和设计方案。
这些设计图纸包括了零部件的尺寸、结构和加工要求等信息。
2. 材料准备在加工零部件之前,需要准备相应的材料。
材料的选择取决于零部件的具体要求,因此需要根据设计图纸中的要求,选择材料的类型和规格。
3. 加工工艺选择在零部件加工过程中,选择适当的加工工艺非常重要。
加工工艺的选择取决于材料的性质和零部件的形状。
常见的加工工艺包括铣削、车削、钻削、磨削等。
4. 数控编程对于采用数控机床进行加工的零部件,需要进行数控编程。
数控编程是指根据设计图纸和加工工艺,将加工路径和切削参数等信息输入数控机床控制系统,以指导机床完成具体的加工操作。
5. 设备调试和加工一切准备就绪后,需要将加工设备进行调试,确保其正常运行和稳定性。
根据数控程序进行加工操作,包括刀具装夹、工件装夹和加工参数的设置等。
6. 质量检验与测试在零部件加工完成后,需要进行质量检验与测试。
这包括对零部件的尺寸、表面粗糙度和形位公差等进行测量和评估,以确保加工质量符合设计要求。
二、我的观点和理解机械零部件加工是一个复杂而又精细的过程,需要严格按照规范和要求进行操作。
在我的观点和理解中,我认为以下几个方面是十分重要的。
设计和规划阶段是整个加工过程中最关键的一步。
合理的设计和规划能够为后续的加工提供准确的依据,避免出现尺寸和结构上的错误。
典型零件加工工艺过程

强化质量管理体系:建立完善的质量管理体系,对加工过程进行全面监控和管理, 确保每个环节的质量控制。
引入先进技术和设备:积极引入先进的加工技术和设备,提高加工效率和精度,提 升零件加工质量。
感谢您的观看
检验环节:对加工 完成的零件进行检 验,包括尺寸、形 状、表面质量等方 面的检查,确保零 件符合设计要求
检验标准:制定明 确的检验标准,为 检验人员提供依据 ,确保零件质量稳 定可靠
质量记录:对加工 过程监控和检验结 果进行记录,便于 后续追溯和分析, 为持续改进提供数 据支持
05
零件加工后的质量检测 与评估
案例分析:具体零 件加工过程中的形 位公差控制实例
表面粗糙度控制
影响因素:切削参数、刀具 类型、材料性质等
定义:表面粗糙度是指零件 表面微观不平度的程度
控制方法:选择合适的切削 参数和刀具类型,采用先进
的加工工艺
检测方法:采用表面粗糙度 测量仪进行测量
加工过程监控与检验
加工过程监控:对 零件加工过程中的 关键工序进行实时 监控,确保加工质 量符合要求
结论:总结箱体类零件加工工艺的重要性和发展趋势,强调其在机械制造领域的重要地位和作用
其他典型零件加工工艺案例
轴类零件加工工艺 案例
盘套类零件加工工 艺案例
叉架类零件加工工 艺案例
箱体类零件加工工 艺案例
07 总结与展望
典型零件加工工艺过程总结
零件加工工艺过程概述 零件加工工艺流程 零件加工工艺特点 零件加工工艺发展趋势
度等
检测方法:采 用各种量具、 仪器进行测量
检测数据记录: 详细记录每个 零件的检测数
- 1、下载文档前请自行甄别文档内容的完整性,平台不提供额外的编辑、内容补充、找答案等附加服务。
- 2、"仅部分预览"的文档,不可在线预览部分如存在完整性等问题,可反馈申请退款(可完整预览的文档不适用该条件!)。
- 3、如文档侵犯您的权益,请联系客服反馈,我们会尽快为您处理(人工客服工作时间:9:00-18:30)。
矿产资源开发利用方案编写内容要求及审查大纲
矿产资源开发利用方案编写内容要求及《矿产资源开发利用方案》审查大纲一、概述
㈠矿区位置、隶属关系和企业性质。
如为改扩建矿山, 应说明矿山现状、
特点及存在的主要问题。
㈡编制依据
(1简述项目前期工作进展情况及与有关方面对项目的意向性协议情况。
(2 列出开发利用方案编制所依据的主要基础性资料的名称。
如经储量管理部门认定的矿区地质勘探报告、选矿试验报告、加工利用试验报告、工程地质初评资料、矿区水文资料和供水资料等。
对改、扩建矿山应有生产实际资料, 如矿山总平面现状图、矿床开拓系统图、采场现状图和主要采选设备清单等。
二、矿产品需求现状和预测
㈠该矿产在国内需求情况和市场供应情况
1、矿产品现状及加工利用趋向。
2、国内近、远期的需求量及主要销向预测。
㈡产品价格分析
1、国内矿产品价格现状。
2、矿产品价格稳定性及变化趋势。
三、矿产资源概况
㈠矿区总体概况
1、矿区总体规划情况。
2、矿区矿产资源概况。
3、该设计与矿区总体开发的关系。
㈡该设计项目的资源概况
1、矿床地质及构造特征。
2、矿床开采技术条件及水文地质条件。