控制臂的受力分析与改进
机械臂的动力学分析与控制

机械臂的动力学分析与控制近年来,随着科学技术的不断进步,机械臂在工业领域得到了广泛的应用。
机械臂以其优异的精度和灵活性,成为自动化生产的得力助手。
而要实现机械臂的高效工作,动力学分析与控制是不可或缺的关键。
动力学分析是研究机械臂在特定条件下的力学行为和运动规律。
通过对机械臂的动力学进行分析,可以深入了解机械臂在不同工作状态下的力学特性,有助于优化机械臂的设计和控制算法。
首先,动力学分析需要建立机械臂的动力学模型。
机械臂由多个关节和执行器组成,关节是机械臂的运动连接部件,执行器负责驱动机械臂的运动。
通过对机械臂的关节和执行器进行建模,可以得到机械臂的几何结构,质量分布以及关节间的连接关系。
接下来,动力学分析需要考虑机械臂的力学特性。
机械臂在工作时会受到多种力的作用,如重力、惯性力和外部负载力等。
这些力的作用会导致机械臂的加速度、速度和位置的变化。
通过对这些力进行分析,可以确定机械臂在特定工作状态下的动力学特性。
在动力学分析的基础上,控制机械臂的运动是十分重要的。
控制机械臂的目的是使其按照预设的路径和姿态进行精准的操作。
控制机械臂的方法有很多种,其中常用的是PID控制器和模糊控制器。
PID控制器是一种基于比例、积分和微分的控制策略。
通过对机械臂的误差进行测量和反馈,PID控制器可以根据误差的大小来调整机械臂的输出,从而使机械臂的位置和姿态接近预期值。
而模糊控制器则是一种基于模糊逻辑推理的控制方法,它可以处理复杂和模糊的输入条件,从而实现对机械臂的精确控制。
除了基本的控制方法,机械臂的轨迹规划也是控制的重要一环。
轨迹规划是指确定机械臂运动的路径和速度,使机械臂在运动过程中保持平稳和高效。
常见的轨迹规划方法有插值法和最小时间法。
插值法通过对机械臂的离散点进行插值,得到机械臂的路径和速度。
最小时间法则是通过确定机械臂的加速度、速度和位置的变化,使机械臂在最短时间内完成运动。
总结起来,机械臂的动力学分析与控制是实现机械臂高效工作的重要一环。
汽车控制臂检查和维修:松动和磨损问题

汽车控制臂检查和维修:松动和磨损问题汽车控制臂是汽车悬挂系统的重要组成部分,负责连接车身和车轮,支撑和控制车辆的悬挂运动。
车辆行驶过程中,控制臂承受着很大的压力和震动,因此经常会出现松动和磨损的问题。
正确的检查和维修控制臂是保证车辆行驶安全和悬挂系统正常工作的关键。
下面将详细介绍控制臂的检查和维修步骤。
1. 工具准备检查和维修控制臂需要准备一些基本工具,例如扳手、扭矩扳手、千斤顶、千斤顶垫、安全支撑架和润滑油等。
确保工具齐全,并按照使用说明正确使用。
2. 提升车辆在进行控制臂的检查和维修前,需要将车辆提升至适当的高度。
使用千斤顶提升车辆,然后使用安全支撑架稳固车辆。
确保车辆离地面足够高,以便工作更加方便和安全。
3. 检查控制臂的松动首先,检查控制臂是否出现松动现象。
通过尝试摇晃控制臂,如果存在明显的松动,则表明控制臂连接螺栓可能已松动。
使用扳手或扭矩扳手,逐一检查并拧紧连接螺栓。
确保所有的连接螺栓都牢固可靠。
4. 检查控制臂的磨损然后,检查控制臂是否出现磨损现象。
仔细观察控制臂表面是否存在明显的划痕、变形或裂纹。
如果发现控制臂有磨损迹象,则需要进行更加详细的检查。
使用手掌轻轻拍打控制臂,观察是否有异常声响。
如果有声响,则可能是球形关节或橡胶套筒磨损,需要进行维修或更换。
5. 润滑控制臂如果控制臂正常且无磨损问题,可以考虑润滑控制臂,以保持其良好的工作状态。
使用润滑油或润滑剂,涂抹在控制臂的连接螺栓和球形关节上。
确保润滑油涂抹均匀,并避免过量使用。
6. 定期检查和维护控制臂的检查和维修不仅限于一次,应定期进行检查和维护。
建议每隔一定的行驶里程或一定的时间间隔,对控制臂进行检查。
特别是在长时间行驶或经常在恶劣路况下行驶的情况下,应更加重视控制臂的检查和维修。
总结:通过以上步骤,可以对汽车的控制臂进行全面的检查和维修。
正确的检查和维修可以保证车辆的行驶安全和悬挂系统的正常运行。
同时,定期检查和维护也可以延长控制臂的使用寿命,减少潜在的故障和损坏。
《某型汽车前悬架控制臂的结构分析与优化》
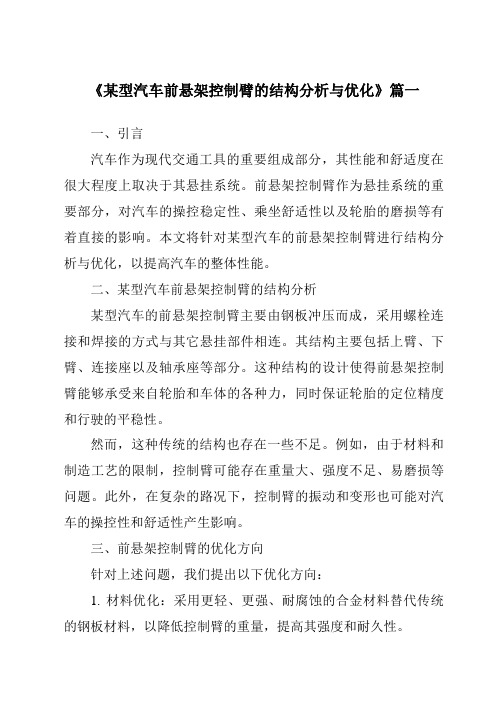
《某型汽车前悬架控制臂的结构分析与优化》篇一一、引言汽车作为现代交通工具的重要组成部分,其性能和舒适度在很大程度上取决于其悬挂系统。
前悬架控制臂作为悬挂系统的重要部分,对汽车的操控稳定性、乘坐舒适性以及轮胎的磨损等有着直接的影响。
本文将针对某型汽车的前悬架控制臂进行结构分析与优化,以提高汽车的整体性能。
二、某型汽车前悬架控制臂的结构分析某型汽车的前悬架控制臂主要由钢板冲压而成,采用螺栓连接和焊接的方式与其它悬挂部件相连。
其结构主要包括上臂、下臂、连接座以及轴承座等部分。
这种结构的设计使得前悬架控制臂能够承受来自轮胎和车体的各种力,同时保证轮胎的定位精度和行驶的平稳性。
然而,这种传统的结构也存在一些不足。
例如,由于材料和制造工艺的限制,控制臂可能存在重量大、强度不足、易磨损等问题。
此外,在复杂的路况下,控制臂的振动和变形也可能对汽车的操控性和舒适性产生影响。
三、前悬架控制臂的优化方向针对上述问题,我们提出以下优化方向:1. 材料优化:采用更轻、更强、耐腐蚀的合金材料替代传统的钢板材料,以降低控制臂的重量,提高其强度和耐久性。
2. 结构优化:通过有限元分析等方法,对控制臂的结构进行优化设计,减少振动和变形,提高其动态性能。
3. 制造工艺优化:采用先进的制造工艺,如激光焊接、机器人焊接等,提高制造精度和效率,同时降低制造成本。
四、具体优化措施1. 材料优化:选用高强度铝合金作为主要材料,其具有轻质、高强度、耐腐蚀等优点,能够有效降低控制臂的重量,提高其强度和耐久性。
2. 结构优化:a) 通过有限元分析方法对控制臂进行受力分析,找出潜在的应力集中和变形区域,对其进行优化设计。
b) 采用多轴向加强筋的设计,提高控制臂的局部刚度和强度。
c) 对连接座和轴承座进行优化设计,提高其连接强度和稳定性。
3. 制造工艺优化:a) 采用激光焊接和机器人焊接等先进工艺,提高制造精度和效率。
b) 对关键部位进行表面处理,如喷涂防腐涂料等,以提高其耐腐蚀性能。
《某型汽车前悬架控制臂的结构分析与优化》范文

《某型汽车前悬架控制臂的结构分析与优化》篇一一、引言汽车作为现代交通工具的重要组成部分,其性能和舒适度在很大程度上取决于其悬挂系统。
前悬架控制臂作为悬挂系统的重要部分,其结构设计和性能对汽车的行驶稳定性和乘坐舒适性具有重要影响。
本文将针对某型汽车的前悬架控制臂进行结构分析,并提出相应的优化方案。
二、某型汽车前悬架控制臂的结构分析某型汽车的前悬架控制臂主要由支撑臂、连接臂和调节臂等部分组成。
其中,支撑臂负责承受车辆重量和路面冲击,连接臂将控制臂与转向系统连接,调节臂则用于调整车轮的定位参数。
在结构上,该型汽车的前悬架控制臂采用了高强度钢材制造,以保证其足够的强度和刚度。
同时,控制臂的各个部分都经过了精密的加工和焊接,以确保其尺寸精度和连接强度。
然而,尽管该型汽车的前悬架控制臂在结构和材料上具有一定的优势,但仍存在一些潜在的问题和改进空间。
三、前悬架控制臂存在的问题及原因经过实际使用和测试,发现该型汽车的前悬架控制臂存在以下问题:1. 耐磨性不足:由于道路状况复杂,控制臂在使用过程中容易出现磨损,导致尺寸精度下降,影响行驶稳定性。
2. 抗冲击性能有待提高:在遇到颠簸路面时,控制臂容易受到较大的冲击力,导致损坏或变形。
3. 制造工艺复杂:控制臂的制造过程需要多道工序,包括切割、加工、焊接等,导致制造成本较高。
造成这些问题的原因主要包括材料选择、结构设计、制造工艺等方面。
例如,选用的材料虽然具有较高的强度和刚度,但在耐磨性和抗冲击性能方面仍有待提高。
此外,结构设计上可能存在一些不合理之处,导致在使用过程中容易出现磨损或变形。
制造工艺方面,复杂的加工和焊接过程也可能影响制件的质量和成本。
四、前悬架控制臂的优化方案针对上述问题,提出以下优化方案:1. 改进材料选择:选用具有更高耐磨性和抗冲击性能的材料制造前悬架控制臂,以提高其使用寿命和抗损性能。
2. 优化结构设计:对前悬架控制臂的结构进行优化设计,使其在承受重量和冲击力的同时,减少应力集中和磨损现象。
浅谈汽车悬架控制臂有限元分析与结构优化
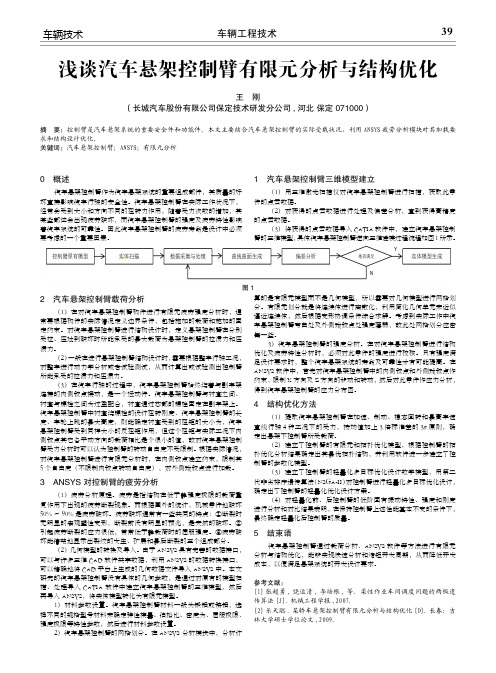
车辆工程技术39车辆技术0 概述汽车悬架控制臂作为汽车悬架系统的重要组成部件,其质量的好坏直接影响汽车行驶的安全性。
汽车悬架控制臂在实际工作状况下,经常会受到大小和方向不同的扭转力作用,随着受力次数的增加,其某些部位会出现疲劳破坏,而汽车悬架控制臂的强度及疲劳特性影响着汽车系统的可靠性。
因此汽车悬架控制臂的疲劳寿命是设计中必须要考虑的一个重要因素。
1 汽车悬架控制臂三维模型建立(1)用三维激光扫描仪对汽车悬架控制臂进行扫描,获取此零件的点云数据。
(2)对获得的点云数据进行处理及偏差分析,直到获得高精度的点云数据。
(3)将获得的点云数据导入CATIA 软件中,建立汽车悬架控制臂的三维模型,具体汽车悬架控制臂逆向三维建模过程流程如图1所示。
浅谈汽车悬架控制臂有限元分析与结构优化王 刚(长城汽车股份有限公司保定技术研发分公司,河北 保定 071000)摘 要:控制臂是汽车悬架系统的重要安全件和功能件。
本文主要结合汽车悬架控制臂的实际受载状况,利用ANSYS 疲劳分析模块对其加载要求和结构设计优化。
关键词:汽车悬架控制臂;ANSYS;有限元分析图12 汽车悬架控制臂载荷分析(1)在对汽车悬架控制臂构件进行有限元疲劳强度分析时,通常要根据构件的实际情况定义边界条件,包括施加的载荷和施加的固定约束。
对汽车悬架控制臂进行结构设计时,定义悬架控制臂在分别受拉、压达到破坏时所能承受的最大载荷为悬架控制臂的拉溃力和压溃力。
(2)一般在进行悬架控制臂结构设计时,需要根据整车行驶工况,对整车进行动力学分析或者试验测试,从而计算出或试验测出控制臂所能承受的拉溃力和压溃力。
(3)在汽车行驶的过程中,汽车悬架控制臂始终绕着与副车架连接的内侧铰点摆动,是一个运动件。
汽车悬架控制臂与衬套之间、衬套与螺栓之间为过盈配合,衬套通过芯部的螺栓固定在副车架上。
汽车悬架控制臂中衬套绕螺栓的设计扭转刚度、汽车悬架控制臂的长度、车轮上跳的最大高度,则能确定衬套受到的扭矩的大小为,汽车悬架控制臂受到同样大小的反扭矩作用,但这个扭矩与实际工况下内侧铰点其它各平动方向的载荷相比是个很小的值,故对汽车悬架控制臂受力分析时可以认为控制臂的转动自由度不受限制。
《2024年某型汽车前悬架控制臂的结构分析与优化》范文

《某型汽车前悬架控制臂的结构分析与优化》篇一一、引言随着汽车行业的不断发展,车辆的性能、舒适性和安全性逐渐成为了消费者购车时的重要考量因素。
作为汽车底盘系统的重要组成部分,前悬架控制臂的设计与制造对汽车的操控性能、稳定性和行驶安全性起着至关重要的作用。
本文将对某型汽车的前悬架控制臂的结构进行深入分析,并提出相应的优化方案。
二、某型汽车前悬架控制臂的结构分析某型汽车的前悬架控制臂主要采用铸铁材料,通过锻造和机械加工而成。
其结构主要包括连接部分、支撑部分和安装部分。
连接部分负责将控制臂与转向节和减震器连接;支撑部分则负责支撑车身并传递路面反馈;安装部分则用于固定控制臂在车身上的位置。
此外,为满足各种行驶需求,前悬架控制臂在设计上还需考虑到多角度的弯折和扭力承受能力。
三、当前结构存在的问题虽然某型汽车的前悬架控制臂在常规使用条件下表现出色,但在长期使用和高强度驾驶环境中仍存在一定的问题。
如,某些部位易发生疲劳裂纹,影响行车安全;控制臂重量较大,导致整车重量增加,影响燃油经济性;某些结构细节的设计不够合理,可能导致车辆操控性能和稳定性的降低。
四、结构优化方案针对上述问题,我们提出以下结构优化方案:1. 材料优化:采用轻质材料替代铸铁,如铝合金或高强度钢材,以降低控制臂的重量,提高燃油经济性。
2. 结构改进:在易发生疲劳裂纹的部位增加加强筋或改变结构形式,以提高其抗疲劳性能和强度。
同时,对安装部分和支撑部分进行优化设计,以提高车辆操控性能和稳定性。
3. 细节优化:对控制臂的细节设计进行优化,如优化连接部分的形状和尺寸,使其更符合力学原理,提高其传递力和扭矩的效率。
五、结论通过对某型汽车前悬架控制臂的结构分析与优化,我们找到了其存在的问题并提出了相应的解决方案。
这些优化措施不仅有助于提高车辆的操控性能、稳定性和安全性,还能降低整车重量,提高燃油经济性。
未来,我们将继续深入研究汽车底盘系统,为消费者提供更加优质、高效的汽车产品。
车辆控制臂疲劳损伤分析与寿命预测探讨
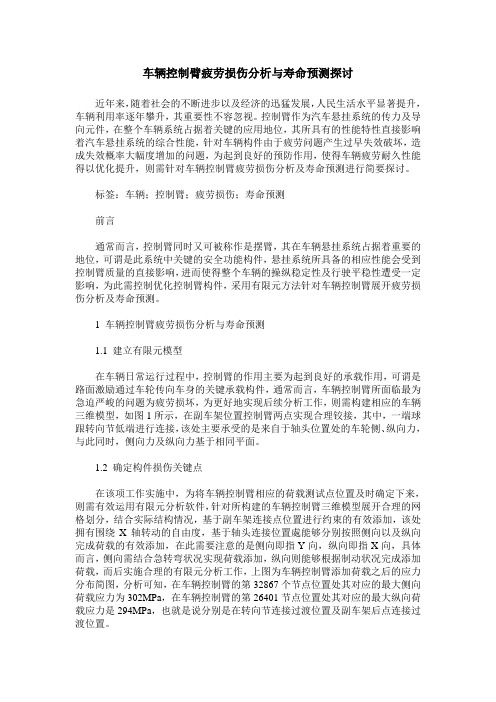
车辆控制臂疲劳损伤分析与寿命预测探讨近年来,随着社会的不断进步以及经济的迅猛发展,人民生活水平显著提升,车辆利用率逐年攀升,其重要性不容忽视。
控制臂作为汽车悬挂系统的传力及导向元件,在整个车辆系统占据着关键的应用地位,其所具有的性能特性直接影响着汽车悬挂系统的综合性能,针对车辆构件由于疲劳问题产生过早失效破坏,造成失效概率大幅度增加的问题,为起到良好的预防作用,使得车辆疲劳耐久性能得以优化提升,则需针对车辆控制臂疲劳损伤分析及寿命预测进行简要探讨。
标签:车辆;控制臂;疲劳损伤;寿命预测前言通常而言,控制臂同时又可被称作是摆臂,其在车辆悬挂系统占据着重要的地位,可谓是此系统中关键的安全功能构件,悬挂系统所具备的相应性能会受到控制臂质量的直接影响,进而使得整个车辆的操纵稳定性及行驶平稳性遭受一定影响,为此需控制优化控制臂构件,采用有限元方法针对车辆控制臂展开疲劳损伤分析及寿命预测。
1 车辆控制臂疲劳损伤分析与寿命预测1.1 建立有限元模型在车辆日常运行过程中,控制臂的作用主要为起到良好的承载作用,可谓是路面激励通过车轮传向车身的关键承载构件,通常而言,车辆控制臂所面临最为急迫严峻的问题为疲劳损坏,为更好地实现后续分析工作,则需构建相应的车辆三维模型,如图1所示,在副车架位置控制臂两点实现合理铰接,其中,一端球跟转向节低端进行连接,该处主要承受的是来自于轴头位置处的车轮侧、纵向力,与此同时,侧向力及纵向力基于相同平面。
1.2 确定构件损伤关键点在该项工作实施中,为将车辆控制臂相应的荷载测试点位置及时确定下来,则需有效运用有限元分析软件,针对所构建的车辆控制臂三维模型展开合理的网格划分,结合实际结构情况,基于副车架连接点位置进行约束的有效添加,该处拥有围绕X轴转动的自由度,基于轴头连接位置處能够分别按照侧向以及纵向完成荷载的有效添加,在此需要注意的是侧向即指Y向,纵向即指X向,具体而言,侧向需结合急转弯状况实现荷载添加,纵向则能够根据制动状况完成添加荷载,而后实施合理的有限元分析工作,上图为车辆控制臂添加荷载之后的应力分布简图,分析可知,在车辆控制臂的第32867个节点位置处其对应的最大侧向荷载应力为302MPa,在车辆控制臂的第26401节点位置处其对应的最大纵向荷载应力是294MPa,也就是说分别是在转向节连接过渡位置及副车架后点连接过渡位置。
《某型汽车前悬架控制臂的结构分析与优化》范文
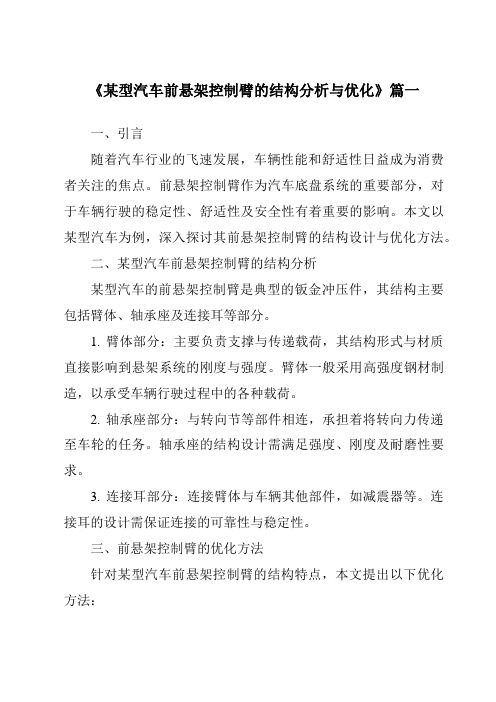
《某型汽车前悬架控制臂的结构分析与优化》篇一一、引言随着汽车行业的飞速发展,车辆性能和舒适性日益成为消费者关注的焦点。
前悬架控制臂作为汽车底盘系统的重要部分,对于车辆行驶的稳定性、舒适性及安全性有着重要的影响。
本文以某型汽车为例,深入探讨其前悬架控制臂的结构设计与优化方法。
二、某型汽车前悬架控制臂的结构分析某型汽车的前悬架控制臂是典型的钣金冲压件,其结构主要包括臂体、轴承座及连接耳等部分。
1. 臂体部分:主要负责支撑与传递载荷,其结构形式与材质直接影响到悬架系统的刚度与强度。
臂体一般采用高强度钢材制造,以承受车辆行驶过程中的各种载荷。
2. 轴承座部分:与转向节等部件相连,承担着将转向力传递至车轮的任务。
轴承座的结构设计需满足强度、刚度及耐磨性要求。
3. 连接耳部分:连接臂体与车辆其他部件,如减震器等。
连接耳的设计需保证连接的可靠性与稳定性。
三、前悬架控制臂的优化方法针对某型汽车前悬架控制臂的结构特点,本文提出以下优化方法:1. 材料优化:采用高强度、轻质材料替代传统钢材,以降低整体重量,提高刚度与强度。
同时,采用热处理工艺提高材料的抗疲劳性能。
2. 结构优化:通过有限元分析等方法,对控制臂进行结构分析与优化设计。
针对应力集中、易磨损等部位进行结构改进,提高整体结构的可靠性与耐久性。
3. 工艺优化:采用先进的冲压、焊接等工艺技术,提高控制臂的制造精度与质量。
同时,采用自动化生产线,提高生产效率与降低成本。
4. 润滑与防护:对轴承座等易磨损部位进行润滑处理,延长使用寿命。
对整体结构进行防腐、防锈处理,提高耐候性能。
四、优化效果分析经过对某型汽车前悬架控制臂的结构分析与优化,可以预期达到以下效果:1. 提高车辆行驶的稳定性与舒适性:优化后的控制臂具有更高的刚度与强度,可有效抵抗各种载荷,提高车辆行驶的稳定性。
同时,优化后的结构能够更好地吸收路面冲击,提高乘坐舒适性。
2. 降低油耗与排放:优化后的控制臂重量更轻,可降低车辆的整备质量,从而降低油耗与排放。
《某型汽车前悬架控制臂的结构分析与优化》范文
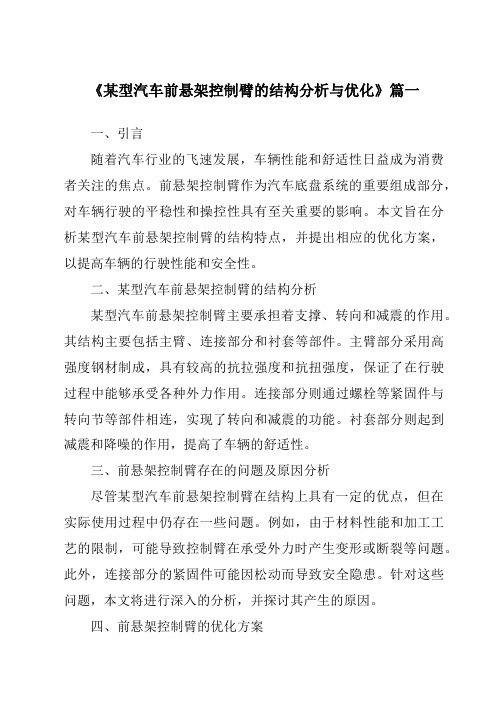
《某型汽车前悬架控制臂的结构分析与优化》篇一一、引言随着汽车行业的飞速发展,车辆性能和舒适性日益成为消费者关注的焦点。
前悬架控制臂作为汽车底盘系统的重要组成部分,对车辆行驶的平稳性和操控性具有至关重要的影响。
本文旨在分析某型汽车前悬架控制臂的结构特点,并提出相应的优化方案,以提高车辆的行驶性能和安全性。
二、某型汽车前悬架控制臂的结构分析某型汽车前悬架控制臂主要承担着支撑、转向和减震的作用。
其结构主要包括主臂、连接部分和衬套等部件。
主臂部分采用高强度钢材制成,具有较高的抗拉强度和抗扭强度,保证了在行驶过程中能够承受各种外力作用。
连接部分则通过螺栓等紧固件与转向节等部件相连,实现了转向和减震的功能。
衬套部分则起到减震和降噪的作用,提高了车辆的舒适性。
三、前悬架控制臂存在的问题及原因分析尽管某型汽车前悬架控制臂在结构上具有一定的优点,但在实际使用过程中仍存在一些问题。
例如,由于材料性能和加工工艺的限制,可能导致控制臂在承受外力时产生变形或断裂等问题。
此外,连接部分的紧固件可能因松动而导致安全隐患。
针对这些问题,本文将进行深入的分析,并探讨其产生的原因。
四、前悬架控制臂的优化方案针对某型汽车前悬架控制臂存在的问题,本文提出以下优化方案:1. 材料优化:选用更高强度、更轻量化的材料替代原有的高强度钢材,以提高控制臂的抗拉强度和抗扭强度。
同时,采用先进的加工工艺,提高材料的利用率和加工精度。
2. 结构优化:对控制臂的结构进行优化设计,减小应力集中和振动产生的可能性。
例如,可以改进连接部分的形状和布局,提高其承载能力和抗疲劳性能。
此外,还可以在控制臂上增加加强筋等结构,提高其整体刚度和稳定性。
3. 紧固件优化:对连接部分的紧固件进行升级,采用更先进的防松技术和紧固方法,确保在各种路况下都能保持紧固状态,从而提高车辆的安全性。
4. 减震降噪优化:改进衬套部分的材料和结构,提高其减震和降噪性能。
例如,可以采用粘弹性材料或液态衬套等新型减震元件,提高车辆的舒适性和静谧性。
《2024年某型汽车前悬架控制臂的结构分析与优化》范文
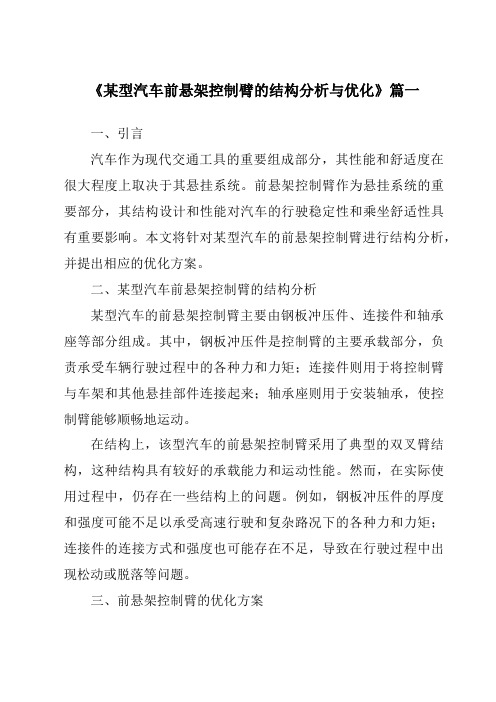
《某型汽车前悬架控制臂的结构分析与优化》篇一一、引言汽车作为现代交通工具的重要组成部分,其性能和舒适度在很大程度上取决于其悬挂系统。
前悬架控制臂作为悬挂系统的重要部分,其结构设计和性能对汽车的行驶稳定性和乘坐舒适性具有重要影响。
本文将针对某型汽车的前悬架控制臂进行结构分析,并提出相应的优化方案。
二、某型汽车前悬架控制臂的结构分析某型汽车的前悬架控制臂主要由钢板冲压件、连接件和轴承座等部分组成。
其中,钢板冲压件是控制臂的主要承载部分,负责承受车辆行驶过程中的各种力和力矩;连接件则用于将控制臂与车架和其他悬挂部件连接起来;轴承座则用于安装轴承,使控制臂能够顺畅地运动。
在结构上,该型汽车的前悬架控制臂采用了典型的双叉臂结构,这种结构具有较好的承载能力和运动性能。
然而,在实际使用过程中,仍存在一些结构上的问题。
例如,钢板冲压件的厚度和强度可能不足以承受高速行驶和复杂路况下的各种力和力矩;连接件的连接方式和强度也可能存在不足,导致在行驶过程中出现松动或脱落等问题。
三、前悬架控制臂的优化方案针对某型汽车前悬架控制臂的结构问题,我们可以从以下几个方面进行优化:1. 材料选择与强度提升:为了提高控制臂的承载能力和耐久性,可以选择更高强度、更轻质的材料。
如使用高强度钢材或铝合金材料替代传统的钢板冲压件,以减轻重量、提高强度。
同时,对关键部位的厚度进行适当增加,确保其能够承受更大的力和力矩。
2. 连接方式优化:对连接件进行重新设计,采用更可靠的连接方式。
如使用高强度的螺栓和螺母进行连接,并增加防松装置,确保在行驶过程中连接件不会出现松动或脱落等问题。
此外,还可以考虑采用一体式设计,减少连接点的数量,提高整体结构的刚性。
3. 结构优化:对控制臂的结构进行进一步优化,使其更加符合力学原理。
如通过有限元分析等方法对控制臂进行仿真分析,找出结构上的薄弱环节并进行改进。
同时,还可以借鉴其他先进车型的悬挂系统设计经验,对双叉臂结构进行改进,提高其运动性能和承载能力。
车辆控制臂优化设计
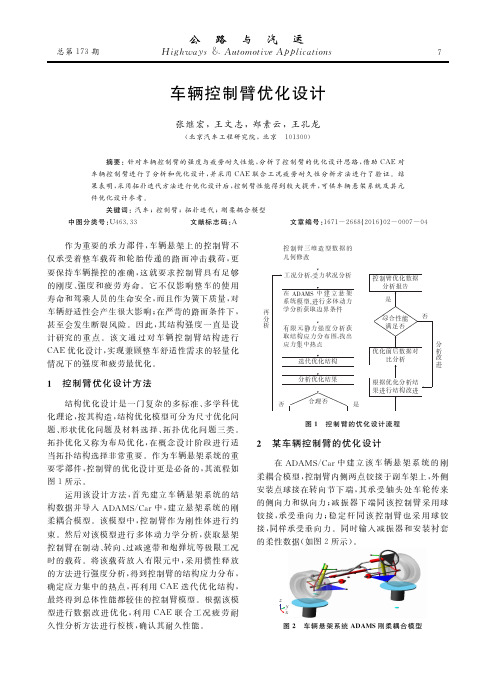
7
制 动 767_
767 #6#
7
反向制动#6;_ 8#6; #6#
7
反向制动7_ 876# #6#
7
加 速 #6;_
8#6; #6#
7
加速和转向#6;_ 8#6; #6;
7
对 角 扭 9_
#6# #6#
9
""注&7_ Va6: P'29%下同%
""&I&%*依据标准工况提取控制臂载荷加 载到 控 制 臂 上 各 个 硬 点 !如 图 " 所 示 "%
图#"车辆悬架系统 %9%$)刚柔耦合模型
:
" " " " " 公 路 与 汽 运 " " " " " "9#75 年 " 月 "
根 据 对 试 验 场 路 谱 采 集 数 据 的 分 析$确 定 控 制 臂 的 标 准 工 况 和 载 荷 !如 表 7 所 示 "%
"""""公路与汽运
"总第7$"期"""""""!"#$%&'( D )*+,-,+"./)001"2&+",3("""""""""" $
车辆控制臂优化设计
张 继 宏 王 文 志 郑 素 云 王 孔 龙
北 京 汽 车 工 程 研 究 院 北 京 "7#7"##
汽车悬架控制臂的可靠性拓扑优化
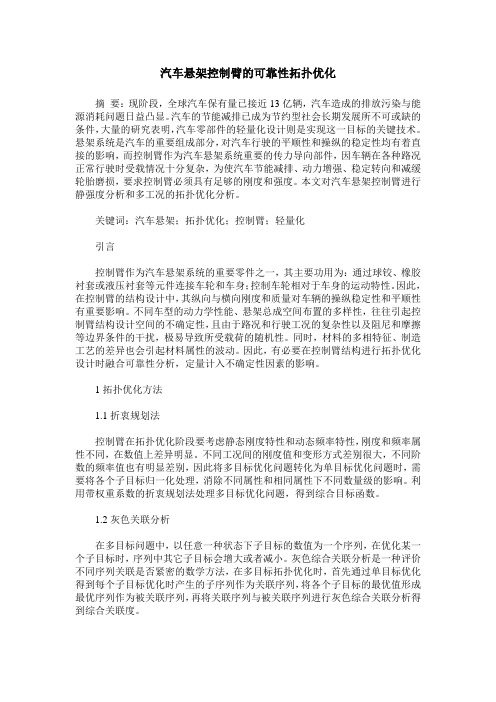
汽车悬架控制臂的可靠性拓扑优化摘要:现阶段,全球汽车保有量已接近13亿辆,汽车造成的排放污染与能源消耗问题日益凸显。
汽车的节能减排已成为节约型社会长期发展所不可或缺的条件,大量的研究表明,汽车零部件的轻量化设计则是实现这一目标的关键技术。
悬架系统是汽车的重要组成部分,对汽车行驶的平顺性和操纵的稳定性均有着直接的影响,而控制臂作为汽车悬架系统重要的传力导向部件,因车辆在各种路况正常行驶时受载情况十分复杂,为使汽车节能减排、动力增强、稳定转向和减缓轮胎磨损,要求控制臂必须具有足够的刚度和强度。
本文对汽车悬架控制臂进行静强度分析和多工况的拓扑优化分析。
关键词:汽车悬架;拓扑优化;控制臂;轻量化引言控制臂作为汽车悬架系统的重要零件之一,其主要功用为:通过球铰、橡胶衬套或液压衬套等元件连接车轮和车身;控制车轮相对于车身的运动特性。
因此,在控制臂的结构设计中,其纵向与横向刚度和质量对车辆的操纵稳定性和平顺性有重要影响。
不同车型的动力学性能、悬架总成空间布置的多样性,往往引起控制臂结构设计空间的不确定性,且由于路况和行驶工况的复杂性以及阻尼和摩擦等边界条件的干扰,极易导致所受载荷的随机性。
同时,材料的多相特征、制造工艺的差异也会引起材料属性的波动。
因此,有必要在控制臂结构进行拓扑优化设计时融合可靠性分析,定量计入不确定性因素的影响。
1拓扑优化方法1.1折衷规划法控制臂在拓扑优化阶段要考虑静态刚度特性和动态频率特性,刚度和频率属性不同,在数值上差异明显。
不同工况间的刚度值和变形方式差别很大,不同阶数的频率值也有明显差别,因此将多目标优化问题转化为单目标优化问题时,需要将各个子目标归一化处理,消除不同属性和相同属性下不同数量级的影响。
利用带权重系数的折衷规划法处理多目标优化问题,得到综合目标函数。
1.2灰色关联分析在多目标问题中,以任意一种状态下子目标的数值为一个序列,在优化某一个子目标时,序列中其它子目标会增大或者减小。
《某型汽车前悬架控制臂的结构分析与优化》范文

《某型汽车前悬架控制臂的结构分析与优化》篇一一、引言汽车作为现代交通工具的重要组成部分,其性能和舒适度在很大程度上取决于其悬挂系统。
前悬架控制臂作为悬挂系统的重要部分,对汽车的操控稳定性、乘坐舒适性以及轮胎的磨损情况有着直接的影响。
本文将针对某型汽车的前悬架控制臂进行结构分析与优化,旨在提高汽车的整体性能。
二、某型汽车前悬架控制臂的结构分析某型汽车的前悬架控制臂主要由钢板冲压而成,采用焊接工艺连接各部分。
其结构主要包括主臂、副臂、连接点等部分。
主臂和副臂通过特定的角度和位置关系相互连接,形成一个稳定的支撑结构。
连接点则是连接主臂与汽车底盘的纽带,其设计和安装对汽车的悬挂性能和行驶稳定性具有重要影响。
三、前悬架控制臂存在的问题虽然某型汽车的前悬架控制臂在设计和制造上已经达到了相当高的水平,但在实际使用过程中仍存在一些问题。
例如,由于材料和制造工艺的限制,控制臂在长期使用过程中可能会出现疲劳断裂、磨损等问题,这将对汽车的行驶安全性和舒适性产生不良影响。
此外,控制臂的结构设计也需要进一步优化,以提高汽车的操控性能和乘坐舒适性。
四、前悬架控制臂的优化方案针对某型汽车前悬架控制臂存在的问题,本文提出以下优化方案:1. 材料优化:采用更高强度、更耐磨损的材料制造控制臂,以提高其耐久性和可靠性。
例如,可以采用高强度钢或铝合金等材料,以减轻控制臂的重量,提高其抗疲劳性能。
2. 结构设计优化:通过改进控制臂的结构设计,提高其操控性能和乘坐舒适性。
例如,可以优化主臂和副臂的角度和位置关系,使其更加符合汽车行驶的力学原理;同时,可以改进连接点的设计,使其更加稳固和耐用。
3. 制造工艺优化:采用先进的制造工艺和技术,如精密铸造、机器人焊接等,以提高控制臂的制造精度和一致性。
这不仅可以提高控制臂的质量和可靠性,还可以降低制造成本和制造周期。
五、优化后的效果评估通过实施《某型汽车前悬架控制臂的结构分析与优化》篇二一、引言随着汽车行业的迅猛发展,车辆性能及驾驶舒适度的要求逐渐提升,前悬架控制臂作为汽车底盘的重要组成部分,其结构设计与性能优化显得尤为重要。
某轿车悬架控制臂有限元分析与结构优化.

某轿车悬架控制臂有限元分析与结构优化
在轿车悬架系统的优化设计中,为保证整车的行驶安全性和燃油经济性,需要全面考虑悬架零件的结构强度、刚度和重量等。
对于具有复杂形状和边界条件的悬架零件而言,以往单纯基于有限元方法的结构改进设计往往带有盲目性。
因此,本文结合某轿车底盘开发项目,综合使用多体动力学、有限元和结构优化方法,进行悬架某控制臂概念设计方案的有限元分析和结构优化研究。
全文围绕该解决方案,首先进行了悬架控制臂的载荷分析,在对比并选择了具体的载荷获取方法之后,对载荷分析的典型极限工况进行了总结和分析,并计算得到各工况的轮胎接地力,然后以此作为输入条件,用该车的ADAMS悬架模型加载仿真,并提取悬架控制臂各工况下的载荷。
其次,利用HyperWorks软件对选取的悬架控制臂的概念设计方案进行有限元建模,然后,以之前提取的载荷为边界条件对其进行结构强度分析,并作了自由模态分析。
最后,结合结构工艺性要求,对概念设计方案先后进行了拓扑优化和形状优化共两轮优化设计以及相应的改进设计,并对比了两轮优化前后的控制臂结构强度、刚度、质量、固有频率等,最终优化结果基本实现了减轻零件重量而不牺牲关键性能的目标。
机械手臂力与力矩的控制与分析研究

机械手臂力与力矩的控制与分析研究引言机械手臂力与力矩的控制与分析是现代自动化领域中的一个重要课题。
随着工业自动化水平的不断提高,机械手臂在生产线上的应用日益广泛。
为了实现机械手臂的精确操作,需要对其力与力矩进行有效控制与分析。
本文将探讨机械手臂力与力矩的控制原理、应用场景以及相关研究进展。
一、机械手臂力与力矩的控制原理1.1 力与力矩的概念与表示力是物体之间相互作用所产生的效应,它可以改变物体的运动状态或形状。
力矩是力绕某个轴产生的旋转效应,它是用来描述物体围绕某一点的旋转能力。
在机械手臂的控制中,力和力矩通常通过传感器来实时测量。
1.2 机械手臂力与力矩的控制策略机械手臂力与力矩的控制策略可以分为两种类型:力控制和力矩控制。
力控制是指在机械手臂的末端施加一个恒定的力,在这个力的作用下,机械手臂可以移动或保持在某个位姿。
力矩控制则是在机械手臂的末端施加一个恒定的力矩,用于旋转或扭转物体。
1.3 机械手臂力与力矩的控制方法机械手臂力与力矩的控制可以通过多种方法实现,常见的包括基于PID控制器的反馈控制方法、基于模型的前馈控制方法以及基于增量式学习控制方法。
这些方法各自有其特点和适用场景,可以根据具体需求选择合适的控制方法。
二、机械手臂力与力矩的应用场景2.1 工业制造领域机械手臂在工业制造领域中广泛应用,例如装配线上的自动化装配、焊接、喷涂等任务。
对于一些需要保持一定力度的操作,如螺丝焊接时的力控制,机械手臂的力与力矩控制显得尤为关键。
2.2 医疗领域机械手臂在医疗领域中的应用也逐渐增多。
例如,在微创手术中,机械手臂可以模拟人类手的运动,并通过力与力矩的控制实现对患者的精细操作。
对于一些需要精确控制力度的手术,机械手臂的力与力矩控制能够帮助医生提高手术的安全性和精准度。
三、相关研究进展3.1 机械手臂力矩控制算法的研究近年来,学术界对于机械手臂力矩控制算法的研究一直处于热点。
一些学者提出了基于非线性动力学模型的控制算法,在保持系统稳定性的同时,实现对机械手臂力矩的高精度控制。
力臂调节装置故障分析与改进

工 业 科 技
2 0 1 4 年( 第4 3 卷) 第1 期
力臂 调节装置故 障分析 与改进
栾 日涛 孙 波
( 海军装备部 , 甘肃 兰州 7 3 0 0 7 0 )
摘
要: 本文对某型飞机配装 的力臂调 节装 置的工作原理 、 重要性进行 了简要介绍 , 针对在某特技 飞行 过程 中出现 的技术
的输入信号和 回输 电位计 的反馈 信号进行 比较后 , 差
动作 。当回输 电位计 的反馈信号电压与输入信号 电压
的差值为规定值时 , 单片机输出控制信号 , 停止电机工
作 ,完成一次调节。当产品到达大臂或小臂极限位置
后, 单片机控制盒给 出到位控制信号 , 在大臂端同时点 亮大臂灯 。 如产品的某一部件发生故障时, 单片机控制 盒向大臂灯发出闪烁告警信号。其功能方框 图见 图 1 。
簧载荷机构之间的传动比,从而保证 飞机在不 同的飞
行高度和飞行速度上都有一致的操纵性能 。
在某次特技飞行 中,力臂 自动调节装置大臂灯闪 烁两次后 , “ 自动” 状态停止工作 , 操纵杆力变重 , 但是 产品没有报故。由于该力臂调节装置的特殊作用 , 其工 作状态的好坏直接影响飞机 的飞行安全 。经综合分析 及测试后 , 查明故 障原 因是 , 特技飞行时 , 空速快速变
行 安全 。
化 ,动静压传感器的值和力臂位置反馈 的差值大于失
某乘用车悬架控制臂早期断裂原因分析及改进
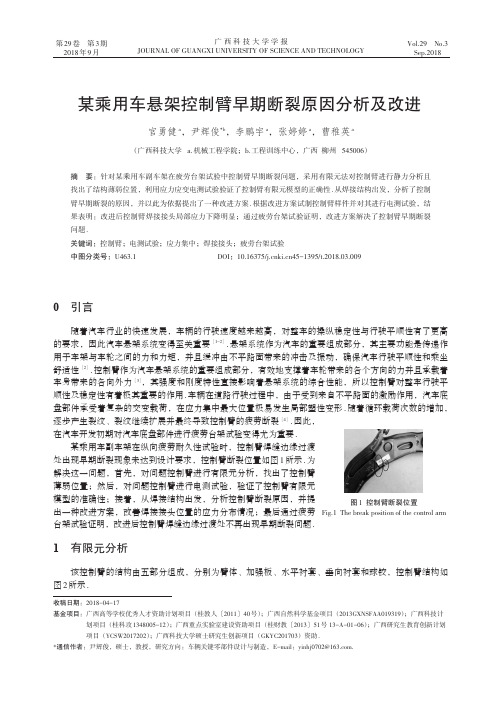
第29卷第3期2018年9月广西科技大学学报JOURNAL OF GUANGXI UNIVERSITY OF SCIENCE AND TECHNOLOGY Vol.29No.3Sep.2018某乘用车悬架控制臂早期断裂原因分析及改进官勇健a ,尹辉俊*b ,李鹏宇a ,张婷婷a ,曹稚英a(广西科技大学 a.机械工程学院;b.工程训练中心,广西柳州545006)摘要:针对某乘用车副车架在疲劳台架试验中控制臂早期断裂问题,采用有限元法对控制臂进行静力分析且找出了结构薄弱位置,利用应力应变电测试验验证了控制臂有限元模型的正确性.从焊接结构出发,分析了控制臂早期断裂的原因,并以此为依据提出了一种改进方案.根据改进方案试制控制臂样件并对其进行电测试验,结果表明:改进后控制臂焊接接头局部应力下降明显;通过疲劳台架试验证明,改进方案解决了控制臂早期断裂问题.关键词:控制臂;电测试验;应力集中;焊接接头;疲劳台架试验中图分类号:U463.1DOI :10.16375/45-1395/t.2018.03.0090引言随着汽车行业的快速发展,车辆的行驶速度越来越高,对整车的操纵稳定性与行驶平顺性有了更高的要求,因此汽车悬架系统变得至关重要[1-2].悬架系统作为汽车的重要组成部分,其主要功能是传递作用于车架与车轮之间的力和力矩,并且缓冲由不平路面带来的冲击及振动,确保汽车行驶平顺性和乘坐舒适性[2].控制臂作为汽车悬架系统的重要组成部分,有效地支撑着车轮带来的各个方向的力并且承载着车身带来的各向外力[3],其强度和刚度特性直接影响着悬架系统的综合性能,所以控制臂对整车行驶平顺性及稳定性有着极其重要的作用.车辆在道路行驶过程中,由于受到来自不平路面的激励作用,汽车底盘部件承受着复杂的交变载荷,在应力集中最大位置极易发生局部塑性变形.随着循环载荷次数的增加,逐步产生裂纹、裂纹继续扩展并最终导致控制臂的疲劳断裂[4].因此,在汽车开发初期对汽车底盘部件进行疲劳台架试验变得尤为重要.某乘用车副车架在纵向疲劳耐久性试验时,控制臂焊缝边缘过渡处出现早期断裂现象未达到设计要求,控制臂断裂位置如图1所示.为解决这一问题,首先,对问题控制臂进行有限元分析,找出了控制臂薄弱位置;然后,对问题控制臂进行电测试验,验证了控制臂有限元模型的准确性;接着,从焊接结构出发,分析控制臂断裂原因,并提出一种改进方案,改善焊接接头位置的应力分布情况;最后通过疲劳台架试验证明,改进后控制臂焊缝边缘过渡处不再出现早期断裂问题.1有限元分析该控制臂的结构由五部分组成,分别为臂体、加强板、水平衬套、垂向衬套和球铰,控制臂结构如图2所示.收稿日期:2018-04-17基金项目:广西高等学校优秀人才资助计划项目(桂教人〔2011〕40号);广西自然科学基金项目(2013GXNSFAA019319);广西科技计划项目(桂科攻1348005-12);广西重点实验室建设资助项目(桂财教〔2013〕51号13-A-01-06);广西研究生教育创新计划项目(YCSW2017202);广西科技大学硕士研究生创新项目(GKYC201703)资助.*通信作者:尹辉俊,硕士,教授,研究方向:车辆关键零部件设计与制造,E-mail :yinhj0702@.图1控制臂断裂位置Fig.1The break position of the controlarm第29卷广西科技大学学报1.1有限元模型建立此控制臂为薄板冲压焊接结构,故在有限元分析过程中以壳单元[5]对其进行建模.采用刚性单元通过对自由度的限制来模拟控制臂和副车架衬套及球铰处的连接[6].T 型焊接接头可使用实体单元或者壳单元进行建模.由于采用实体单元计算得到的结构应力集中系数同采用壳单元求解出的结构应力集中系数非常接近[7],而采用壳单元建模大大减少了网格数量,可适用于各种形状复杂的焊接接头建模,故采用壳单元模拟臂体与加强板连接的T 型焊接接头.其余焊缝采用实体单元模拟,长度与实际焊缝长度一致.建立控制臂有限元模型如图3所示.1.2材料属性此控制臂材料为SAPH440汽车结构钢,其出厂状态如下:屈服强度为305MPa ,抗拉强度为440MPa.按照材料的实际属性,将控制臂有限元模型的泊松比取为0.3,材料密度为7.8×10-9t/mm 3,杨氏模量取为2.1×105MPa.不考虑焊接处材料的特性变化,认为焊接处的材料属性与母材的材料属性相同[8].1.3边界约束及载荷施加副车架的极限工况为加速工况和制动工况,其中加速工况尤为恶劣.根据某企业《乘用车前后副车架台架疲劳耐久试验规范》,控制臂在加速工况下纵向拉伸8000N.此工况约束副车架与车身安装点(③、④、⑤、⑥、⑦、⑧、⑨、⑩点)的X 、Y 、Z 三个方向移动自由度[9],依此工况的受力情况在控制臂球铰处(①、②点)X 负方向施加8000N 作用力,螺栓及衬套均以刚性单元模拟,控制臂与副车架有限元模型及边界条件如图4所示.1.4应力分析利用有限元软件Hypermesh 对控制臂进行前置处理,以Optistruct 为求解器,对控制臂进行加速工况下的有限元分析,得到应力分布云图如图5所示.分析应力云图,加强板与臂体焊缝边缘过渡处应力较大,约为230MPa ,离开该位置应力急剧减小并趋于稳定.2应力测试2.1测试介绍为验证控制臂有限元模型的正确性,对控制臂进行应力应变电测试验.根据疲劳台架试验中的控制臂1—球铰;2—臂体;3—加强板;4—水平衬套;5—垂向衬套图2控制臂结构示意图Fig.2The structure of the controlarm 图3控制臂有限元模型Fig.3The finite element model of the control arm图4控制臂与副车架有限元模型及边界条件Fig.4The finite element model and boundary conditions of control arms andsub-frame 图5加速工况下控制臂应力云图Fig.5Stress nephogram of the control arm underacceleration workingcondition 58第3期断裂情况,再结合有限元分析结果[10],分别在左右臂体两侧设立测点1、测点2,加强板上设立测点3、测点4,测点分布情况见图6.使用东华DH3816静态应变仪进行测试,根据加速工况下的载荷条件,借助疲劳台架测试系统对控制臂纵向施加8000N 作用力,测试其应力值,测试现场如图7所示.2.2测试数据处理与分析控制臂在加速工况下有限元计算数据与电测测试数据进行对比,对比结果见表1.对比结果表明,测点1和测点2两处误差相对较大,最大误差为13.12%.其原因为:测点1和测点2在模型中的位置为曲面,应力梯度变化较大,且模型网格大小统一,以致在曲面上网格稀疏,产生物理离散误差影响模型计算精度.根据经验认为此计算模型和分析方法基本可靠.3控制臂断裂分析及结构改进控制臂为冲压焊接件.由于焊缝形状与焊缝位置分布不同,在外力作用下,焊接接头位置应力分布不均匀,通常使用应力集中来表示应力分布不均匀程度.应力集中是指接头局部位置应力最大值比平均应力值高的现象,常用应力集中系数[11]来表示.如图8所示,焊缝被截断分成两条不连续焊缝,不连续处形成I 型槽.在拉伸应力作用下,局部会产生应力集中现象.在靠近槽局部区域,应力急剧增加;离开槽边缘稍远处应力迅速减小,并趋于均匀.应力集中程度的大小,常用理论应力集中系数ασ[12]表示:ασ=σmax σ0(1)式中:σmax ——最大局部应力;σ0——平均应力.理论应力集中系数反映了应力集中的程度,焊接结构的应力集中现象越为严重,它的数值就越大,对焊接结构的影响越大.根据有限元分析结果,控制臂臂体与加强板连接的焊缝边缘过渡处应力较大,约为230MPa.离开焊缝边缘过渡处应力迅速下降趋于平缓,约为170MPa.由式(1)可知,该处理论应力集中系数较大,应力集中现象较为严重.焊接接头的基本形式主要分为角接接头、T 型接头、对接接头和搭接接头等4种.由于焊缝的形状不同,接头的应力集中系数也不相同,对焊接接头的疲劳性能影响亦不同.臂体与加强板之间使用T 型接头连接.T 型接头焊缝向母材过渡较为急剧,接头在应力作用下力线扭曲较大,应力分布极不均匀,在焊缝边缘过渡处易产生很大的应力集中[11],T 型接头焊缝边缘过渡处疲劳极限相对较低.(a )控制臂正面(b )控制臂反面图6控制臂测点布置示意图Fig.6Arrangement of measuring points on the control arms 图7控制臂电测试验Fig.7The stress-strain test of the controlarms表1控制臂电测数据与有限元分析数据对比Tab.1The data contrast of stress-strain test and finite element analysis of control arms 测点1234有限元模拟值/MPa 220.52231.8793.27101.31电测试验值/MPa 202.17204.9895.9798.14误差/%9.0613.122.813.23图8焊缝结构的应力集中Fig.8The stress concentration of weldstructure 59第29卷广西科技大学学报工程实际中,有些运动构件在工作时其内部的应力常常会随时间做周期性变化,这种随时间做周期变化的应力称为交变应力.实践表明,金属材料在交变应力作用下引起的失效与因静力引起的失效完全不同.交变应力引起的失效特征为疲劳极限远低于材料静载荷强度极限或甚至低于屈服极限[13],随着循环次数的增加,进而产生裂纹最终导致疲劳断裂.控制臂为汽车底盘零部件,承受着复杂的交变应力,故其疲劳极限相对较低.由于零件的疲劳极限降低程度不能直接通过理论应力集中系数进行判断,工程上通常用有效应力集中系数K σ来表示疲劳极限真实降低程度[12],即:K σ=σ-1σ′-1(2)式中:σ-1——光滑试样疲劳极限;σ′-1——缺口试样疲劳极限.由式(2)可知:提高缺口试样疲劳极限可使有效应力集中系数减小,降低应力集中程度,进而提高工件的疲劳寿命.控制臂为汽车底盘零部件,承受着复杂的交变应力,故其疲劳极限相对较低.在交变应力作用下,T 型接头焊缝边缘过渡处疲劳极限较低,有效应力集中系数过大,随着加载次数的增加进而发生疲劳断裂现象.通过以上分析可知:将焊缝1、焊缝2合并并延长成焊缝4,可提高了焊缝的疲劳极限,降低了应力集中程度,从而提高控制臂疲劳寿命.控制臂改进图如图9所示.4改进方案的验证4.1加速工况的静力分析按上述材料属性及边界条件建立改进控制臂有限元模型,对控制臂进行加速工况下的静力分析,得到应力分布云图如图10所示.改进后的控制臂应力分布均匀,应力集中现象得到显著改善.4.2应力测试根据改进方案试制样件,按前述测试方法对改进后的控制臂进行应力应变电测试验,测点布置与改进前相同,借助疲劳台架系统对控制臂纵向施加8000N 作用力.将电测试验数据与有限元计算数据进行对比,改进后的数据对比结果见表2.由表2可知,加速工况下有限元分析数据与电测试验数据基本吻合,最大误差为12.09%.(a )改进前(b )改进后图9控制臂改进图Fig.9The improvement of the controlarm 图10改进后控制臂在加速工况下应力云图Fig.10The stress nephogram of improved control arm under acceleration workingcondition60第3期4.3电测数据对比分析与评价根据表2电测试验数据,将控制臂焊接结构改进前与改进后电测试验数据进行对比,对比结果见表3.由表3可知:改进控制臂在测点1、测点2处应力分别为171.67MPa 、172.48MPa ,相比改进前试验值最大降低15.86%;测点3、测点4处应力稍有增加,各点应力朝着一个中间值进行靠拢,应力集中现象得到改善.4.4疲劳台架试验验证疲劳台架试验采用双通道电液伺服疲劳试验机,按某企业《乘用车前后副车架台架疲劳耐久试验规范》,在左右控制臂球铰处纵向施加8000N 交变载荷,以模拟加速和制动工况.图11为疲劳台架试验工作图.根据某厂家设计要求,控制臂在加速工况下正常工作12万次,不发生明显地永久变形或出现裂纹.对改进控制臂进行多批次疲劳台架试验,改进后控制臂未出现早期断裂问题,进一步验证了改进方案的可行性.5结论1)对问题控制臂进行有限元静力分析,并对关键点进行了应力应变电测试验.试验结果表明:电测试验数据与有限元分析数据基本吻合,误差最大为13.12%,验证了控制臂有限元分析的正确性,为后续控制臂结构改进提供参考.2)从焊接结构出发,分析了控制臂早期断裂原因并提出一种改进方案.对改进后控制臂进行电测试验,相比改进前试验值最大降低15.86%;测点3、测点4处应力稍有增加,各点应力朝着一个中间值进行靠拢,应力集中现象得到改善,为汽车相关零部件的焊缝结构布置提供了可行的参考方案.3)采用双通道电液伺服疲劳试验机,根据疲劳试验规范,对改进控制臂进行疲劳台架试验.改进方案经多批次疲劳台架试验证实,控制臂未出现早期断裂问题,进一步验证了改进方案的可行性.综上所采用的方法对解决控制臂早期断裂问题有较好的实用价值,对其他车型底盘零件结构强度的提升有一定的指导意义.参考文献[1]蒋翠翠,上官文斌,愈宏.汽车悬架控制臂[J ].现代零部件,2008(2):90-92.[2]李碧军.基于刚柔耦合的非线性悬架汽车的平顺性研究[D ].长沙:湖南大学,2008.[3]薛建奇,王宝中.控制臂的受力分析与改进[J ].机械工程与自动化,2017(2):84-86.[4]KIM Y S ,KIM J G.Evaluation of corrosion fatigue and life prediction of lower arm for automotive suspension component [J ].Met⁃als and Materials International ,2017,23(1):98-105.[5]尹辉俊,黄贵东,黄昶春,等.重型自卸车车架早期断裂原因的研究[J ].汽车工程,2006,28(12):1133-1135.图11控制臂台架试验图Fig.11The fatigue bench test of the controlarm表2控制臂改进后的电测数据与有限元分析数据对比Tab.2The data contrast of stress-strain test and finite elementanalysis of improved control arms测点1234有限元模拟值/MPa 193.62196.21124.15123.63电测试验值/MPa 171.67172.48122.42128.04误差/%11.3412.091.393.57表3控制臂改进前后的电测试验数据对比Tab.3The data contrast of stress-strain test before and after improvement of control arms 测点1234改进前试验值/MPa 202.17204.9895.9798.14改进后试验值/MPa 171.67172.48122.42128.04变化率/%15.0815.8627.5628.43(下转第88页)6188广西科技大学学报第29卷Contrast enhancement of color image based on spatial transformation and expertfuzzy methodCHEN Zhixuan(School of Vocational and Technical Education,Guangxi University of Science and Technology,Liuzhou545006,China)Abstract:The existing image enhancement algorithms have some disadvantages such as large computation,poor re⁃al-time performance,parameter selection difficulty,color drift,convergence guarantee and so on.As far as the effect of image enhancement is concerned,we mainly consider the visual perception of human eyes.And it is diffi⁃cult to process the image with accurate standards and methods.Therefore,fuzzy technology based on imprecise concept and expert experience is an effective method to solve the problem of image enhancement.In this paper,a color image contrast enhancement technique is proposed.Firstly,the color space of color image is transformed from RGB color space to the color space of hue,saturation and gray scale,and then the image enhancement is pro⁃cessed by expert fuzzy technology.The algorithm does not change the hue and saturation of the original color image. The contrast experiment shows that the method can improve the visual effect of the image significantly,and the computation is small and the real-time performance is excellent.Key words:image enhancement;contrast ratio;space transformation;fuzzy technology;color image(学科编辑:黎娅)(上接第61页)[6]尹辉俊,王雨,姜美姣.某乘用车后轴的疲劳分析及结构改进[J].机械设计,2015,32(3):33-36.[7]DONG P.A robust structural stress method for fatigue analysis of offshore/marine structures[J].Journal of Offshore Mechanics and Arctic Engineering,2003,127(1):68-74.[8]廖金深,沈光烈,林圣存.对某微型客车车身结构的有限元分析[J].广西科技大学学报,2016,27(1):58-61.[9]张婷婷,尹辉俊,刘赟,等.某燃油箱边界约束对应力分析精度的影响研究[J].广西科技大学学报,2018.29(1):49-54.[10]尹辉俊,姜美姣,王雨,等.某乘用车后轴扭杆早期断裂原因分析及改进[J].机械设计,2014,31(9):86-88.[11]周瑾,祁文军,薛强.浅析应力集中对焊接接头疲劳强度的影响[J].机械工程与自动化,2010(2):212-213,216.[12]赵子豪,刘德刚.焊接结构疲劳失效的产生原因与预防措施[J].现代机械,2012(1):64-67.[13]屈本宁,张曙红.工程力学[M].2版.北京:科学出版社,2008.Analysis of early fracture of suspension control arms of a passenger car and itsimprovementGUAN Yongjian a,YIN Huijun*b,LI Pengyu a,ZHANG Tingting a,CAO Zhiying a (a.School of Mechanical Engineering;b.Engineering Training Center,Guangxi University of Science andTechnology,Liuzhou545006,China)Abstract:Aimed at the control arms’early fatigue fracture in a passenger car’s sub-frame fatigue bench test,a method of linear static analysis was applied to locate the weak points of the structure of control arms.Then,the ac⁃curacy of the finite element model was verified by a stress-strain test.According to the welding structure of the con⁃trol arm,the reasons of the control arms’early fractures were analyzed and the solution was put forward.Based on the improved scheme,samples of the control arm were made,on which stress-strain test was conducted.The test shows that the local stress of the welding joints of the control arms decreases significantly.Finally,the fatigue test shows that improved scheme solves the problem of the early fracture of control arm.Key words:control arm;stress-strain test;stress concentration;welding joint;fatigue bench test(学科编辑:黎娅)。
《2024年某型汽车前悬架控制臂的结构分析与优化》范文
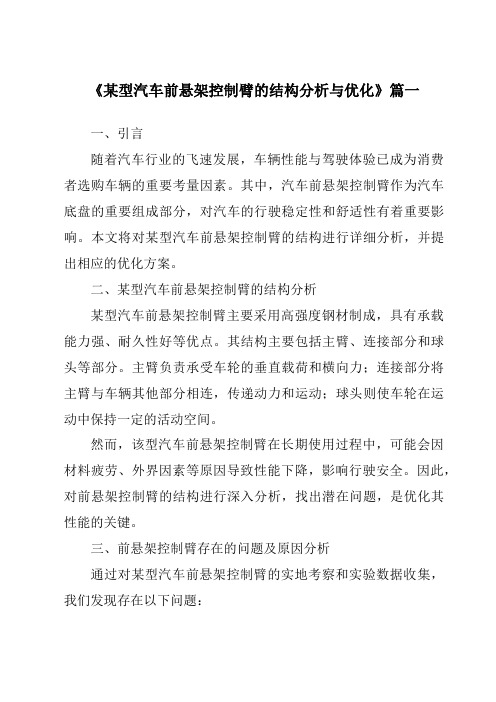
《某型汽车前悬架控制臂的结构分析与优化》篇一一、引言随着汽车行业的飞速发展,车辆性能与驾驶体验已成为消费者选购车辆的重要考量因素。
其中,汽车前悬架控制臂作为汽车底盘的重要组成部分,对汽车的行驶稳定性和舒适性有着重要影响。
本文将对某型汽车前悬架控制臂的结构进行详细分析,并提出相应的优化方案。
二、某型汽车前悬架控制臂的结构分析某型汽车前悬架控制臂主要采用高强度钢材制成,具有承载能力强、耐久性好等优点。
其结构主要包括主臂、连接部分和球头等部分。
主臂负责承受车轮的垂直载荷和横向力;连接部分将主臂与车辆其他部分相连,传递动力和运动;球头则使车轮在运动中保持一定的活动空间。
然而,该型汽车前悬架控制臂在长期使用过程中,可能会因材料疲劳、外界因素等原因导致性能下降,影响行驶安全。
因此,对前悬架控制臂的结构进行深入分析,找出潜在问题,是优化其性能的关键。
三、前悬架控制臂存在的问题及原因分析通过对某型汽车前悬架控制臂的实地考察和实验数据收集,我们发现存在以下问题:1. 材料疲劳:由于长期承受重载和振动,高强度钢材容易出现疲劳裂纹,导致控制臂强度降低。
2. 连接部分松动:连接部分的紧固件可能因振动而松动,导致连接失效。
3. 球头磨损:球头与转向节之间的摩擦可能导致球头磨损,影响车轮的运动轨迹。
针对上述问题,我们进行了深入的原因分析,发现除了材料本身的使用寿命限制外,设计上的不足、制造工艺的缺陷以及使用环境的影响都是导致这些问题的原因。
四、前悬架控制臂的优化方案针对上述问题,我们提出以下优化方案:1. 材料优化:采用更高强度、耐疲劳的材料,以提高控制臂的使用寿命。
2. 设计优化:改进连接部分的紧固方式,增加防松装置,以提高连接的稳定性。
同时,优化球头的设计,减少摩擦和磨损。
3. 制造工艺优化:采用先进的制造工艺,如热处理、表面强化等,提高控制臂的耐久性和抗腐蚀性。
五、结论通过对某型汽车前悬架控制臂的结构分析与优化,我们不仅提高了其性能和寿命,还为汽车行业的发展提供了有益的参考。
- 1、下载文档前请自行甄别文档内容的完整性,平台不提供额外的编辑、内容补充、找答案等附加服务。
- 2、"仅部分预览"的文档,不可在线预览部分如存在完整性等问题,可反馈申请退款(可完整预览的文档不适用该条件!)。
- 3、如文档侵犯您的权益,请联系客服反馈,我们会尽快为您处理(人工客服工作时间:9:00-18:30)。
中 间 孔
MP a ,峰 值 位 移 减 少 0 . 0 1 5 2 5 7 mm,进 一 步保 障 了悬 架 系 统 的 安 全 性 , 为 悬 架 控 制 臂 的 结 构 改 进 提 供 了一
定 的 参考 依 据 。
关 键 词 : 电 动 汽 车 ;控 制 臂 ;有 限元 ; 刚度 ;强 度
控 制 臂 的受力 分析 与改进
薛建 奇 ,王 宝 中
( 华北理X - 大 学 机 械 工 程 学 院 ,河 北 唐 山 0 6 3 0 0 9 )
摘 要 :为 了提 高 悬 架 系 统 的综 合 性 能 ,对 自主 研 发 的 电动 汽 车 悬 架 控 制 臂 进 行 了分 析 与 改 进 。 首先 ,建 立 控 制 臂 的 三维 模 型 并 通 过 AD AMS提 取 控 制 臂 3个 铰 接 点 的受 力 作 为 边 界 条 件 ,并 利 用 A NS Y S对 控 制 臂 进 行 了有 限元 分 析 ,得 到 了其 变 形 和 应 力 云 图 ;其 次 , 改进 现 有 控 制 臂 的 几 何 形 状 以减 小 控 制 臂 的 峰值 应 力 和 峰 值 位 移 ; 最后 ,对 改进 前 后 的 控 制 臂 进 行 了对 比 分 析 。结 果 表 明 , 改 进 后 的 控 制 臂 峰 值 应 力 减 少 6 . 2 0 9
第 2期 ( 总第 2 0 1 期)
2 0 1 7年 4 月
机 械 工 程 与 自 动 化
M ECHANI CAl ENGI NEERI NG & AUTOM ATI ON
No. 2
Ap r .
文章编号 : 1 6 7 2 — 6 4 1 3 ( 2 0 1 7 ) 0 2 — 0 0 8 4 — 0 3
表 1 样 车 性 能 参 数
参 数 整备质量( k g ) 前、 后轮距( mm) 数 值 7 8 O 1 2 0 0 参 数 最大总质量( k g ) 驱 动 电机 数 值 1 4 O O 直 流 无刷 电机
越高, 同时 驾驶者对 车辆 的操控 稳 定 性 与 舒 适 性有 了 更 高 的要 求 , 因此 汽车 的悬 架 系统 变得 至关 重 要l 1 _ 。 ~ 。 控 制臂 是悬 架 系统 中传 力 和导 向 的重 要 机构 , 其 强度 和 刚度 是否 合理直 接影 响着 悬架 性能 。悬架 系统 是连 接 车架 ( 或 车身 ) 与 车轮 间的装 置 , 是汽 车 中重 要 的组 成 部分 , 车 轮和 车架 间所 有 的力 和 力矩 都 是 通 过 悬架 传 递 的 。控 制 臂 作 为 汽 车 悬 架 系 统 的 重 要 组 成 部 分[ 3 ] , 有 效 提供车 轮 所需 的各 向支 撑 力 以及 承 担 着 车 轮对 车身各 个方 向的外 力 , 因此 控 制 臂对 整 个 汽 车 的 安 全性 有着 关键 性 的 作 用 。作 为重 要 的承 力 部件 , 车 辆 悬 架系统 上 的控制 臂不 仅承 受着整 车 载荷 和轮胎传 递 的路面 冲击 载荷 , 更 要 保 持 车辆 操 控 的准 确 性 。张 海波 等为 了验证 汽 车悬架 系统 控制 臂在受 载状 况 下 的可 靠 性 , 通 过 ANS YS分 析 软件 对 悬 架 控 制 臂 刚度 进行 了分 析 ; K r i s h n a 等 和 L a x ma n 等 阐明了悬架控 制臂 的轻 量 化 设 计 过 程 ; S o n g B - C 等[ 7 利 用 铝 合 金 A1 6 0 6 1 M6代替钢作 为材料进行 了控制臂 轻量化设计 。 本文 以 自主研 发 的 场 区 电动 车 悬 架为 研 究 对 象 ,
架, 本 文样 车采 用前 驱麦 弗逊式 非独 立悬架 , 悬架 由车
轮连 接点 橡胶 吊耳 、 转 向拉 杆 、 减 震器 、 螺旋 弹簧 、 减震 器 上 端 和 下 端 的橡 胶 衬 垫、 副 车 架 和 稳 定 杆 组
成 一 。 1 . 2 控 制 臂 参 数
该控 制臂 取 自自主研 发 的 电动汽 车 , 材料 为 4 0 C r 钢, 密度 为 7 8 5 0 k g / m。 , 弹 性模量 为 2 1 0 0 0 0 MP a , 泊 松 比为 0 . 3 , 屈服 极 限为 ' 7 8 5 MP a 。通 过 C r e o软 件绘 制 控制 臂 的三维 图 , 如图 1 所示 。
轴距( mm)
空 载最 大 行 驶 速 度
k m/ h
2 1 O O
3 9
.
电机 功 率 ( k W)
满载 最 大 行 驶 速 度
k m/ h
4 . 5
3 5
3
I 最小外侧转弯半径( mm ) 4 5 O 0
驱动 悬 架 系 统 包 括 独立 悬 架 和非 独 立 悬
中 图分 类 号 :U4 6 3 . 3 3: T P 3 9 1 . 7 文 献 标 识 码 :A
0 引言
随着汽 车产业 的快 速 发展 , 汽 车 的行 驶 速 度越 来
本 文研究 的 车辆 为 自主制 造 的场 区 电动 实验 车 。 样 车部 分参 数如 表 1 所示。
在 现有几 何模 型基 础上 , 利 用 AD AMS建 立悬 架 系统 控 制臂 模 型 , 然 后进 行 动力 学 仿 真实 验, 最 后 通 过 ANS YS分析 悬 架系 统控 制 臂应 力 分布 和 位移 分 布情
况, 并对 其进 行适 当改 进 。
1 样 车与控 制臂 参数 1 . 1 样 车参数