曲柄摇杆机构优化设计
曲柄摇杆机构综合优化设计及其软件开发
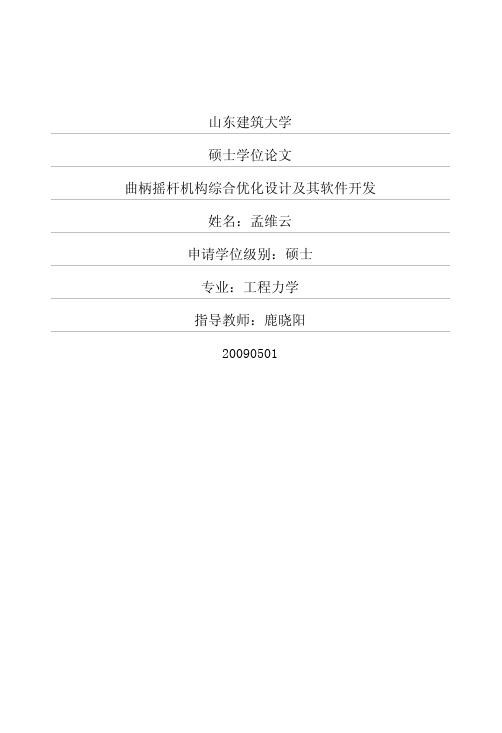
transmission efficiency.
First,the best transmission angle to be optimization designed.knowing rocker length,
rocker largest Swinging angle,the limit position angle,taking other bars as Design variables,taking the best transmission angle to Optimize the crank-rocker mechanism,from
山东建筑大学硕士学位论文
图1.1缝纫机 图1.2颚式破碎机
山东建筑大学硕士学位论文
图1.3搅拌机 (1)机构分析就是根据给定的机构简图,研究机构的运动特性和动力特性。机构分 析着重于机构结构学、运动学及动力学特性的研究,揭示机构结构组成、运动学与动力 学规律及其相互联系,但其更重要的是为机构综合提供理论依据。 (2)机构综合的实质就是按照给定的运动特性对机构进行系统的设计,其综合内容 包括尺度综合和类型综合。 1)类型综合又分为数综合与型综合。数综合就是指在满足机构预定自由度的条件下, 确定组成该机构的构件数目和不同类型的运动副数目的过程。型综合是指在给定构件数 目、运动副数目及其类型的条件下,通过不同的组合方式,确定机构不同结构型式的过 程,从理论上讲,同一结构类型的机构组合方案有无穷多种,这就给尺度综合的方案优 选带来了困难。机构尺寸型的研究是机构尺度综合的基础。 2)尺度综合是指当机构的结构型式选定后,在满足其执行构件运动要求的条件下, 确定出机构尺度参数的过程。对于给定运动特性要求条件下进行结构综合方面己有大量 的文献发表[18讲】。尺度综合的任务就是为选定了类型的机构确定实际尺寸和原动件的起 始位置。 目前在国内外关于机构尺度综合的方法可分为:几何作图法、代数法、图谱法,这 三种方法既有联系又有区别。下面将这三种方法分别进行归纳综述: 几何作图法【251是传统的机构尺度综合方法。它是建立在机构运动和几何分析基础上 的一种方法,其最大特点是直观、概念清楚。几何作图法也是平面四杆机构设计的一种
曲柄摇杆机构优化设计

课程作业曲柄摇杆优化设计姓名:宋*学号:29班级:三峡大学机械与动力学院・程序代码进程 (1)1目录1・曲柄摇杆机构优化设计题目要求要求设计一曲柄摇杆机构,当曲柄山©转到久+90。
时,摇杆的输岀角实现如下给定的函数关系:(1) 置时曲柄和摇杆的位置角,它们是机架杆h为原线逆时针气宇的角度,见图1。
要求在该区间的运动进程中的最小传动角不得小于45° , B|J:式中%和0o别离为对应于摇杆在右极限位/min^[/l = 45°通常把曲柄的长度当做单位长度,即/l = lo另外,按照机构在机械中的许可空间,可以适当预选机架杆的长度,现取/4=5O2・课题描述在曲柄输入角从0()到久+彳的进程中,使摇杆输岀角P尽可能知足一个给定的函数办(0)即公式(1)o对此我将%到%+兰等分为m分,固然输出角(也将对应的分为m分,然后我将输出角对应的数值与期望函数进行拟合,若是误差降到最小,那么取得的结果将会是优化的解,这是将持续型函数转化为离散型的问题,利用matalab编程计算,从而求解。
运动模型如图(1)所示3 •数学模型的成立设计变量的肯定概念:设计变量是除设计常数之外的大体参数,在优化设计进程中不断地进行修改、调整、一直处于转变的状态,这些大体参数都叫做设计变量。
对于本课题,设计常量为厶丿2长度,别离为1和5。
决定机构部份杆长尺寸厶,厶,和摇杆依照已知运动规律开始运动时曲柄所处的位置角%应该列为设计变量即为X 二k %2 AjJ =[/2厶%『% = arc co.0()=(2)(3) 山于整个机构的杆长都是按比例来设计的,他们都是1的倍数,依照题U要求曲柄的初始位置为极位角,即%。
则可以按照曲柄摇杆机构各杆长度关系取得%和相应的摇杆?3位置角00的函数,关系式为由已知条件可知厶上长度别离为1和5,而按照公式(2)(3)可知,%%是lli/2J3的长度来决定,所以厶厶为独立变量,则可以肯定本课题的设计变量X=[.v, xj =[/2厶『,这是一个二维优化问题。
曲柄摇杆机构的最优设计

曲柄摇杆机构的最优设计[摘要] 图解法设计曲柄摇杆机构时为了满足传力性能,往往需要重复进行,结果也不唯一。
本文采用0.618法,在给定行程速比系数k、摇杆摆角φ、长度l4等前提下,采用机械最优设计,使γmin最大,得到了设计最优解。
并讨论了行程速比系数k、摇杆摆角φ的取值范围。
[关键词] 曲柄摇杆机构机械最优设计0.618法1 引言机械最优设计是在给定的载荷或环境条件下,在机械产品的性态、几何尺寸关系或其他因素的限制范围内,选取设计变量,建立目标函数并使其获得最优值的一种新的设计方法。
设计变量、目标函数和约束条件这三者在设计空间(以设计变量为坐标轴组成的实空间)的几何表示中构成设计问题[1]。
最优设计是保证设计合理性、提高设计效率的一种有效方法。
曲柄摇杆机构中,传动角γ越大,对机构的传力愈有利,故常用传动角的大小及变化情况来衡量机构传力性能的好坏。
考虑到机构运动过程中传动角γ是变化的,为了保证机构传力性能良好,必须使最小传动角γmin≥[γ]。
传统的图解设计方法往往需要重复进行,结果也不唯一。
本文采用0.618法,在给定行程速比系数k、摇杆摆角φ、长度l4等前提下,运用机械最优设计,使γmin最大,得到了设计最优解。
并讨论了行程速比系数k、摇杆摆角φ的取值范围。
在实现过程中,本文采用C 语言实现优化过程编程,从而使结果更加精确、直观。
2 曲柄摇杆机构的最优设计(1)寻优目标函数的确定曲柄摇杆机构γmin出现在主动曲柄与机架共线的两位置之一处[2]。
以γmin 最大为寻优目标函数,即:maxf(x)=γmin=(γ1, γ3)min其中,γ1=arccosγ2= arccos(2)设计变量的选择如图1所示,考虑到一旦曲柄支点A确定,则机架l1=AD,其他设计参数l2、l3也随之确定。
因此,只需取曲柄为设计变量即可,即x=l2。
图1设计参数间的几何关系(3)设计参数间的几何关系若已知曲柄x时,有:l3=l1=其中,C1C2=2l4sin(Φ/2)∠AC2D=90°-arcsin+Φ/2(4)设计变量的取值范围根据文献[3]所述,寻优区间起始点xmin= C1C2(1-cosθ)/2sinθ;寻优区间终点xmax= C1C2/2。
优化设计-曲柄摇杆机构优化设计

优化设计-曲柄摇杆机构优化设计1. 引言曲柄摇杆机构被广泛应用于机械工程中,它具有转换旋转运动为往复直线运动的功能。
随着技术的发展,对曲柄摇杆机构的性能要求也越来越高。
为了满足这些要求,需要对曲柄摇杆机构进行优化设计,以提高其工作效率、减小体积和降低功耗。
本文将通过优化设计的方法,对曲柄摇杆机构进行改进,以期达到更好的性能。
2. 优化目标优化设计的目标是在保持曲柄摇杆机构原有功能的基础上,提高其工作效率、减小体积和降低功耗。
具体目标如下:1. 提高工作效率:通过优化设计,减小摩擦阻力和能量损失,提高能量传递效率。
2. 减小体积:通过优化结构,减小曲柄摇杆机构的整体体积,使其更适用于空间有限的应用场景。
3. 降低功耗:通过优化设计,减小机构的运动阻力,达到减少功耗的效果。
3. 优化方法为了实现上述优化目标,可以采用以下方法:优化材料选择:选择适合曲柄摇杆机构的高强度、低摩擦系数的材料,减小摩擦阻力和能量损失。
优化结构设计:通过对曲柄摇杆机构的结构进行改进,减小机构的摩擦面积和摩擦阻力,提高运动效率。
优化润滑方式:采用适当的润滑方式,减小曲柄摇杆机构的摩擦和磨损,以达到降低功耗的效果。
优化运动轨迹:通过对曲柄摇杆机构的运动轨迹进行优化设计,减小运动阻力和摩擦损失,提高能量传递效率。
优化配合间隙:适当调整曲柄摇杆机构的配合间隙,减小摩擦和磨损,提高工作效率。
4. 优化设计实施方案基于以上优化方法,可以实施以下具体的优化设计方案:1. 材料选择:选择高强度、低摩擦系数的材料,如高强度钢材和涂有低摩擦涂层的表面。
2. 结构设计:减小曲柄摇杆机构的摩擦面积,采用滚动轴承等减小摩擦阻力的结构设计。
3. 润滑方式:采用润滑油或固体润滑剂等适当的润滑方式,减小摩擦和磨损。
4. 运动轨迹优化:分析曲柄摇杆机构的运动特点,优化运动轨迹,减小摩擦阻力和能量损失。
5. 配合间隙优化:通过调整曲柄摇杆机构的配合间隙,减小摩擦和磨损,提高工作效率。
优化设计-曲柄摇杆机构优化设计

优化设计-曲柄摇杆机构优化设计优化设计-曲柄摇杆机构优化设计1:引言1.1 背景在机械工程中,曲柄摇杆机构是常用的传动机构之一,具有转动-直线运动转换的功能。
然而,由于曲柄摇杆机构的结构复杂性以及不同工况下的性能要求,如何对曲柄摇杆机构进行优化设计成为一项重要的工作。
1.2 目的本文旨在对曲柄摇杆机构进行优化设计,以提高其运动精度、工作效率和使用寿命。
2:功能需求分析2.1 运动要求根据使用场景和应用需求,分析曲柄摇杆机构需要实现的运动要求,包括速度、加速度、行程等方面的要求。
2.2 负载要求确定曲柄摇杆机构在工作过程中所承受的负载要求,包括静载荷和动载荷。
2.3 精度要求根据实际应用场景,分析曲柄摇杆机构需要达到的运动精度要求,如定位精度、重复定位精度等。
3:结构设计优化3.1 曲柄摇杆机构的结构形式选择根据运动要求和负载要求,结合现有的曲柄摇杆机构结构形式,选择合适的结构形式来满足设计要求。
3.2 关键部件的优化设计对曲柄摇杆机构的关键部件进行优化设计,如曲柄轴、摇杆、连杆等,提高其强度和刚度,减小重量和惯性。
4:润滑与密封设计4.1 润滑系统设计根据工作条件和运动要求,设计曲柄摇杆机构的润滑系统,确保关键部件的摩擦副有足够的润滑。
4.2 密封设计对曲柄摇杆机构的关键部位进行密封设计,防止润滑剂泄漏或外界杂质进入,保证机构的工作正常。
5:动力学分析与优化5.1 运动学分析通过运动学分析,研究曲柄摇杆机构的运动规律和轨迹,为后续的动力学分析提供基础。
5.2 动力学分析根据负载要求和运动要求,进行曲柄摇杆机构的动力学分析,考虑受力分布和扭矩传递,优化曲柄摇杆机构的结构参数和材料选择。
6:工艺制造优化6.1 工艺优化针对曲柄摇杆机构的结构特点和制造工艺要求,进行工艺优化,提高制造精度和工艺可行性。
6.2 制造工艺选择根据实际情况,选择适合曲柄摇杆机构的制造工艺,如铸造、锻造、加工等。
7:仿真与试验验证7.1 仿真分析使用计算机辅助工程技术,对曲柄摇杆机构进行有限元分析、动力学仿真等,验证优化设计方案的可行性。
基于DFM的曲柄摇杆机构的优化设计

(h a x Is tt o c n eadT c n l y H n hn 2 0 3 C ia S a n intue f i c n e h oo , a zo g 3 0 , hn ) i Se g 7
【 摘
要】 以最小传动角取得最大值为条件,对曲柄摇杆机构进行 了机构优化设计 ,在不考虑重
陈应 舒
( 陕西理 工学院 , 中 730 ) 汉 20 3
An Op I m sg f a k Ro k r e h ns Ba e n DFM t mu De in o n — c e c a im s d o Cr M
C HE n — h N Yi g— u s
机 械 设 计 与 制 造
3 6
第 1 0期 21 0 2年 1 0月
Ma h n r De i n c ie y sg
&
Ma u a t r n f cu e
文章编 号:0 13 9 (0 2 1— 0 6 0 10 — 9 7 2 1 )0 0 3 — 2
基 于 D M 的 曲柄 摇 杆机 构 的优 化 设 计 F : l =
i ii m t nmsinagei tepeeuseo nt osdr gw i tr t nloc dtese t mnmu as i o l, rrq it f o cniei e h,ii afrea — s r s n nh i n g fco n h p cafr c mbrw i eemi srt nl ete uci , o t it odt nadbu ay i m o e hm lo f a e e, hc dtr n ai a 0 ci ntn cn r n n io onr h e o vf o s a c i n d
曲柄摇杆机构的优化设计
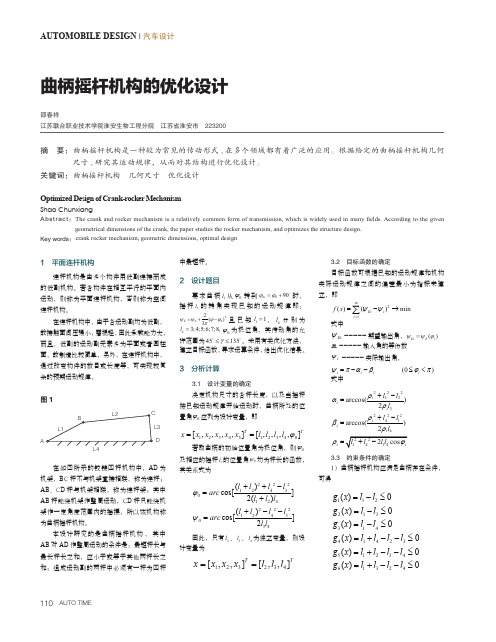
AUTOMOBILE DESIGN | 汽车设计曲柄摇杆机构的优化设计邵春祥江苏联合职业技术学院淮安生物工程分院 江苏省淮安市 223200摘 要: 曲柄摇杆机构是一种较为常见的传动形式,在多个领域都有着广泛的应用。
根据给定的曲柄摇杆机构几何尺寸,研究其运动规律,从而对其结构进行优化设计。
关键词:曲柄摇杆机构 几何尺寸 优化设计1 平面连杆机构连杆机构是由多个构件用低副连接而成的低副机构。
若各构件在相互平行的平面内运动,则称为平面连杆机构,否则称为空间连杆机构。
在连杆机构中,由于各运动副均为低副,故接触面间压强小,磨损轻,因此承载能力大,而且,低副的运动副元素多为平面或者圆柱面,故制造比较简单,另外,在连杆机构中,通过改变构件的数目或长度等,可实现较复杂的预期运动规律。
图1AL1L4L2L3DCB在如图所示的铰链四杆机构中,AD为机架,BC杆不与机架直接相联,称为连杆;AB、CD杆与机架相联,称为连杆架;其中AB杆能绕机架作整周运动,CD杆只能绕机架作一定角度范围内的摇摆,所以该机构称为曲柄摇杆机构。
本设计研究的是曲柄摇杆机构, 其中AB对AD作整周运动的条件是:最短杆长与最长杆长之和,应小于或等于其他两杆长之和;组成运动副的两杆中必须有一杆为四杆中最短杆。
2 设计题目要求曲柄1l从0ϕ转到090mϕϕ=+ 时,摇杆3l的转角实现已知的运动规律即:2002()3Eψψϕϕπ=+−且已知11l=,4l分别为43;4;5;6;7;8,l=ϕ为极位角,其传动角的允许范围为45135γ≤≤。
采用有关优化方法,建立目标函数,寻求运算条件,给出优化结果。
3 分析计算3.1 设计变量的确定决定机构尺寸的各杆长度,以及当摇杆按已知运动规律开始运动时,曲柄所处的位置角0ϕ应列为设计变量,即1234512340[,,,,][,,,,]T Tx x x x x x l l l lϕ=若取曲柄的初始位置角为极位角,则0ϕ及相应的摇杆3l的位置角0ψ均为杆长的函数,其关系式为2221243124222124334()cos[]2()()cos[]2l l l larcl l ll l l larcl lϕψ++−=++−−=因此,只有2l、3l、4l为独立变量,则设计变量为123234[,,][,,]T Tx x x x l l l=3.2 目标函数的确定目标函数可根据已知的运动规律和机构实际运动规律之间的偏差最小为指标来建立,即21()()minmEi iif xψψ==−→∑式中Eiψ-----期望输出角,()Ei E iψψϕ=m-----输入角的等份数iψ-----实际输出角,i i iψπαβ=−− (0)iϕπ≤<式中222323222414221414arccos()2arccos()22cosiiiiiii il lll lll l l lραρρβρρϕ+−=+−=+−3.3 约束条件的确定1)曲柄摇杆机构应满足曲柄存在条件,可得112213314414235123461324()0()0()0()0()0()0g x l lg x l lg x l lg x l l l lg x l l l lg x l l l l=−≤=−≤=−≤=+−−≤=+−−≤=+−−≤Optimized Design of Crank-rocker MechanismShao ChunxiangAbstract: T he crank and rocker mechanism is a relatively common form of transmission, which is widely used in many fi elds. According to the given geometrical dimensions of the crank, the paper studies the rocker mechanism, and optimizes the structure design.Key words:crank rocker mechanism, geometric dimensions, optimal design110AUTO TIMEAUTO TIME111AUTOMOBILE DESIGN | 汽车设计时代汽车 2)曲柄摇杆机构的传动角应在min γ和max γ之间,可得22223147max 2322223418min 23()()arccos()02()()arccos()02l l l l g x l l l l l l g x l l γγ+−+=−≤+−−=−≤计算时分别将1l 、4l 的数值代入即可,其中,2132,l x l x ==。
优化设计-曲柄摇杆机构优化设计

ri l12 l42 2l1l4 cos i 26 10cos i
曲柄摇杆机构的设计
3. 约束条件的确定
① 曲柄存在条件
l1≤l2;l1≤l3;l1+l4≤l2+l3 l2≤(l4-l1)+l3;l3≤(l4-l1)+l2 ② 曲柄与机架共线位置时的传动角(连杆BC 和摇杆CD 之 间的夹角) 最小传动角γmin=min∠BCD≥45° 最大传动角γmax=max∠BCD≤135°
ADAMS仿真
检验优化结果
图4 为测量曲柄旋转角和传动角位移图,它表 明主动杆AB 由φ0=26.4738°转到φ0=386.4738°, 杆AB 可以旋转一周,进而说明设计的曲柄正确。 当曲柄旋转一周,传动角的变化范围70°≤γ≤135° ,所以满足传动角45°≤γ≤135°设计要求。
图3 曲柄转角与传动角位移图
用MATLAB 工具箱优化计算结果
④ 运行结果
连杆机构实现函数优化设计最优解 连杆相对长度 a=4.1286 摇杆相对长度 b=2.3226 输出角平方误差之和 f*=0.0076 最优点的性能约束函数值 最小传动角约束函数值 g1*=-7.1214 最大传动角约束函数值 g2*=-0.0000
用MATLAB 工具箱优化计算结果
用MATLAB 工具箱优化计算结果
将输入角分成30 等分(m=30),经过转化为标准形式得
到曲柄摇杆机构优化设计标准数学模型为:
min f ( x) (Ei i ) 2
i 1
m
x [l2 l3 ]T [ x1 x2 ]T
优化设计:曲柄摇杆机构
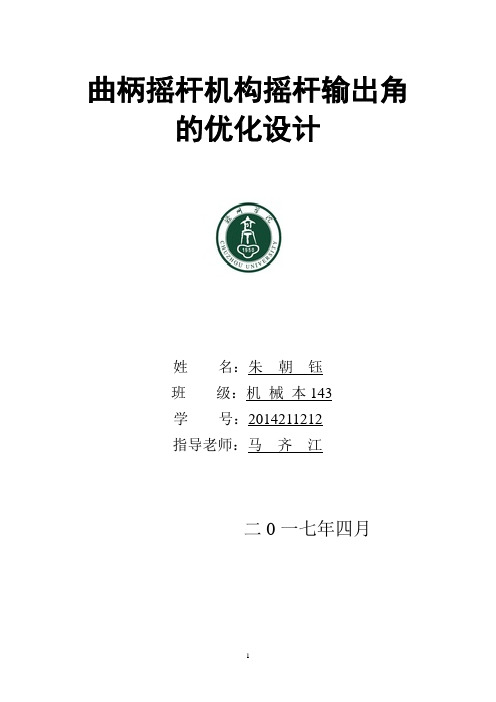
曲柄摇杆机构摇杆输出角的优化设计姓名:朱朝钰班级:机械本143学号:2014211212指导老师:马齐江二0一七年四月目录一、问题描述 (3)二、优化分析 (3)1.约束提取 (3)2.目标函数 (4)3.标准形式 (5)三、优化求解 (6)四、结论 (7)一、问题描述作业:设计曲柄摇杆机构。
要求:曲柄从0ϕ转到20πϕ+时,摇杆的输出角最优地实现一个给定的运动规律;()()πϕϕψϕψ3200-+==--f 曲柄与机架共线位置时的转角满足:︒≥︒≤45,135min max γγ图1二、优化分析1.约束提取a.杆长条件:最长杆与最短杆之和小于等于其他两杆之和{}0,,m ax 21432432≤+---l l l l l l lb.曲柄机构存在条件:任意三杆长之和必须大于另一杆长{}0,,,m ax 214324321<----l l l l l l l lc.曲柄摇杆条件:曲柄最短10132≤-≤-l ld.传动角⎪⎪⎩⎪⎪⎨⎧︒≤-+=+-+=︒≥-+=--+=1352362)(arccos 452162)(arccos322322322142322max 322322322142322min l l l l l l l l l l r l l l l l l l l l l r 2.目标函数首先根据已知的运动规律与机构实际运动规律之间的最小偏差指标来建立目标函数:21)(min ∑=-⎪⎭⎫⎝⎛-=ni i i x F ψψ设置初始位置如下图图2其中:⎩⎨⎧︒=︒=→⎭⎬⎫==090350032ϕψl l 对于任意位置,如下图所示图3根据几何关系可得出一下公式:ii i ii i i i i i l l l ϕϕβϕϕαπϕαβπψcos 1026cos 5arccoscos 10262cos 1026arccos0;32223--=--+-=≤≤--= 3.标准形式目标函数:21)(min ∑=-⎪⎭⎫⎝⎛-=ni i i x F ψψ约束条件:{}{}⎪⎪⎪⎪⎪⎩⎪⎪⎪⎪⎪⎨⎧≤---=≤--+=≤---=≤---=≤-=≤-=====0414.1360414.116065,,,1max 2045,,max 2010151..32232263223225323243232332214211l l l l g l l l l g l l l l g l l l l g l g l g l h l h t s三、优化求解根据以上条件,使用Excel进行优化分析,得知结果如下。
机械优化设计实例
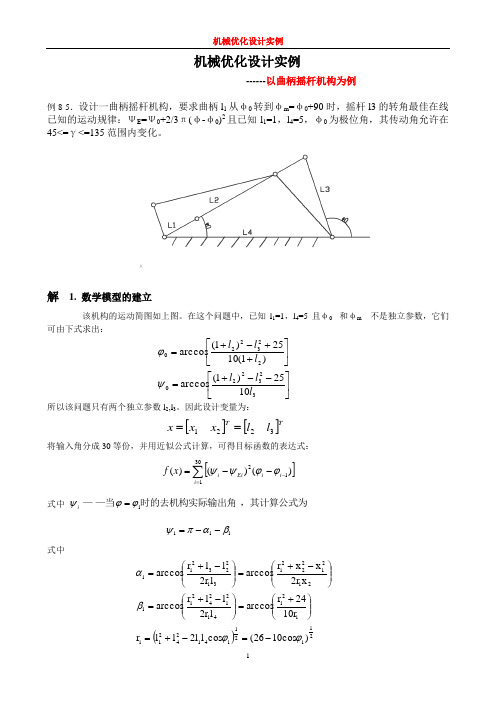
机械优化设计实例------以曲柄摇杆机构为例例8-5.设计一曲柄摇杆机构,要求曲柄l 1从φ0转到φm =φ0+90时,摇杆l3的转角最佳在线已知的运动规律:ΨE =Ψ0+2/3π(φ-φ0)2且已知l 1=1,l 4=5,φ0为极位角,其传动角允许在45<=γ<=135范围内变化。
解 1. 数学模型的建立该机构的运动简图如上图。
在这个问题中,已知l 1=1,l 4=5且φ和φm 不是独立参数,它们可由下式求出:⎥⎦⎤⎢⎣⎡--+=⎥⎦⎤⎢⎣⎡++-+=3232202232201025)1(arccos )1(1025)1(arccos l l l l l l ψϕ所以该问题只有两个独立参数l 2,l 3。
因此设计变量为:[][]TTl l x x x 3221==将输入角分成30等份,并用近似公式计算,可得目标函数的表达式:[]∑=---=30112)()()(i i i Ei i x f ϕϕψψ式中 ,其计算公式为时的去机构实际输出角—当—i ϕϕψ=ii i i βαπψ--=式中()21i 21i412421i i 2i 4i 21242i i 2i 21222i 3i 2232i i )10cos 26(cos l 2l l l r 10r 24r arccos l 2r l l r arccos x 2r x x r arccos l 2r l l r arccos ϕϕβα-=-+=⎪⎪⎭⎫ ⎝⎛+=⎪⎪⎭⎫ ⎝⎛-+=⎪⎪⎭⎫ ⎝⎛-+=⎪⎪⎭⎫ ⎝⎛-+=20i 0Eii Ei 32)(由下式计算时的理想输出角,其值为当ϕϕπψψϕϕψ-+==约束函数按曲柄存在条件对传动角的限制来建立,得g1(x)=-x1<=0 g2(x)=-x2<=0 g3(x)=6-x1-x2<=0 g4(x)=x1-x2-4<=0 g5(x)=x2-x1-4<=0g6(x)=x1^2+x2^2-1.414x1*x2-16<=0 g7(x)=36-x1^2-x2^2-1.414 x1*x2<=02.程序代码根据上述数学模型写出其程序代码 (1)function y=f(x) Pi=3.1416;c0=acos(((1+x(1))^2-x(2)^2+25)/(10*(1+x(1)))); d0=acos(((1+x(1))^2-x(2)^2-25)/(10*x(2))); y=0; for i=0:30;c=c0+Pi*i/60;r=(26-10*cos(c))^0.5;a=acos((r^2+x(2)^2-x(1)^2)/(2*r*x(2))); b=acos((r^2+24)/(10*r)); d=Pi-a-b;de=d0+2*(c-c0)^2/(3*Pi); y0=(d-de)^2*(Pi/60); y=y0+y;end………………………………….%建立f 文件计算目标函数的表达式(2)function [c1,c2]=nonlin(x)c1=[x(1)^2+x(2)^2-1.414*x(1)*x(2)-16;36-x(1)^2-x(2)^2-1.414*x(1)*x(2)]; c2=[];………………………..%建立nonlin 文件(3)A=[-1 -1;1 -1;-1 1];b=[-6;4;4]; lb=[0 0]; ub=[];Aeq=[]; beq=[];x0=[4 3];……………………….%给定初始搜索点[x,fval]=f mincon(@f,x0,A,b,Aeq,beq,lb,ub,@nonlin)…………..%建立约束优化条件并求最优解三运算结果及说明运用MA TLAB计算出结果跟课本运算结果最优解大致相同,但最优解的值有所区别,通过分析我认为其原因:由于Pi的值取的精度不同,初始点取得不同,导致运算的结果会有所区别,同时函数值即最优解的值比较小,而函数值变化浮动比较大。
优化设计-曲柄摇杆机构优化设计本月修正简版

优化设计-曲柄摇杆机构优化设计优化设计-曲柄摇杆机构优化设计引言曲柄摇杆机构是一种常见的工程设备,常用于转换旋转运动为往复运动。
在实际应用中,为了提高机构的性能和效率,需要进行优化设计。
本文将详细介绍曲柄摇杆机构的优化设计方法和步骤。
1. 优化设计的背景和目标曲柄摇杆机构在工程应用中具有广泛的应用,例如内燃机、泵浦系统、机械手和纺织机械等。
在实际应用中,曲柄摇杆机构存在一些问题,例如能量损失、噪音和振动等。
进行优化设计,以改善机构的性能和效率,是非常必要和重要的。
2. 优化设计的方法和步骤2.1. 问题分析和需求定义,需要对已有的曲柄摇杆机构进行问题分析,确定需要改进的性能指标和需求。
例如,可以考虑降低摇杆机构的能耗、减少振动、提高工作效率和稳定性等。
2.2. 理论分析和模拟仿真在优化设计的初期阶段,可以使用理论分析和模拟仿真的方法,对曲柄摇杆机构进行分析和评估。
通过建立模型,计算和模拟机构的运动学和动力学特性,可以快速评估不同设计参数对机构性能的影响。
2.3. 设计参数的选择和优化根据理论分析和模拟仿真的结果,可以选择关键的设计参数进行优化。
例如,可以考虑曲柄长度、连杆长度和转动角度等。
通过改变这些参数的值,可以对机构的性能进行改善。
2.4. 结构改进和优化在选择和优化设计参数的基础上,可以对曲柄摇杆机构的结构进行改进和优化。
例如,可以改变曲柄和连杆的形状和材料,以提高机构的刚度和耐久性。
还可以考虑添加减振装置和降噪措施等。
2.5. 实验验证和性能评估完成结构改进和优化后,需要进行实验验证和性能评估。
通过在实际工作环境中和评估机构的性能和效果,可以验证优化设计的有效性和可行性。
根据实验结果,可以进一步优化设计,以达到最佳性能。
3. 优化设计的挑战和注意事项在进行曲柄摇杆机构的优化设计时,需要注意以下挑战和注意事项:- 保持设计的可靠性和稳定性,避免引入新的故障点。
- 在优化设计中,需要考虑材料成本、制造成本和可维护性等因素。
曲柄摇杆机构的运动分析及快速优化设计
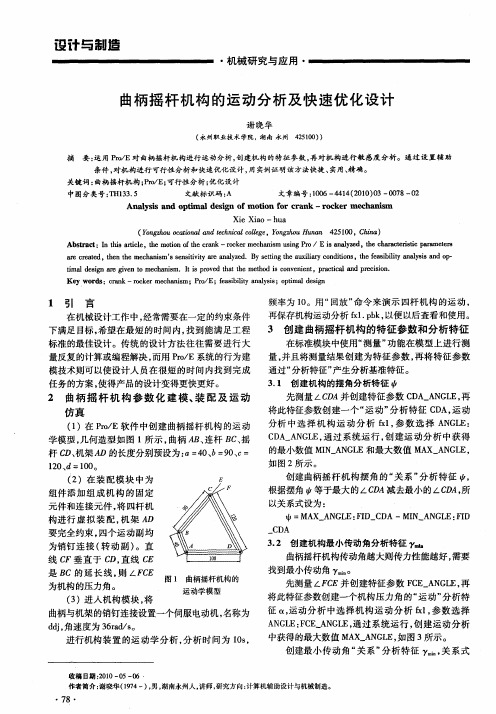
的最小数值 M N A G E和最大数值 M X A G E I_ N L A —NL , 如 图 2所示 。 创建曲柄摇杆 机构摆角的“ 系” 析特征 , 关 分 根据摆角 等于最大的 C A减去最小的 C A 所 D D ,
以关 系式设 为 :
=
( )在 装 配 模 块 中 为 2
设 计 与制 造
・
机 械 研 究 与应 用 ・
曲柄 摇 杆 机 构 的 运 动分 析 及 快 速优 化 设 计
谢 晓 华
( 州职业技术学院,湖南 永州 永 4 50 ) 2 10 )
摘
要 : 用 Po E对曲柄摇杆机 构进行运动分析 , 运 r/ 创建机 构的特征参数 , 对机构进行敏 感度分析 。通 过设置 辅助 再
Ab t a t n t i r ce, h t n o e c a k—rc e c a im sn r sr c :I h sa t l t e mo o ft r n i i h o k rme h n s u ig P o/ E i n l z d, e c a a t r t a a t r a ay e t h r ce s c p me es s h ii r ae c e td。t e e me h n s ss n i vt r n l z d r rae h n t c a im e st i a e a ay e .B et gt e a x l r o d t n ,t ef a i i t ay i n h i y y s t n h u i a yc n i o s l e s bl a l ssa d叩 - i i i l i n y t ld s n a eg v n t c a im.I i rv a h to s c n e in .p a t a d p e iin i e i r i e ome h n s ma g t sp o e t tt eme d i o v n e t r c i la r c s 。 d h h c n o
机械优化设计实验设计报告

实验设计连杆设计优化问题的解决:问题:设计一曲柄摇杆机构要求曲柄L1从A0转到Ai=A0+90时,摇杆L3的转角再次恢复到初始值B0,已知道Bi的运动规律为:)2(AiBi2π+=,且B03-/(A0)已知L1=1,机架L4=5,L2为连杆长度,A0为极位角,其允许传动角[γ]=︒45一、建立数学模型并设定变量:选取设计变量决定机构尺寸的各杆长度以及曲柄所处的初始角A0,均应列为设计变量。
但若取曲柄的初始位置角为极位角,则A0及相应的摇杆L3位置角B0均为杆长的函数,其关系式为;A0=arcos{[(l1+l2)^2+l4^2-l3^2]/[2(l1+l2)*l4]}B0= arcos{[(l1+l2)^2-l4^2-l3^2]/(2*l3*l4)}量,则设计变量X=[x1,x2]=[l2,l3]二、建立目标函数目标函数可根据已知的运动规律与机构实际运动规律之间的偏差最小为指标来建立,表达式为:2=BBiBixf(∑-)()期望的输出角Bi---摇杆L3期望的输出角;BBi---摇杆L3实际输出角,BBi=PI-a-ba= arcos[(r^2+L3^2-L2^2)/(2*r*L3)]b= arcos[(r^2+L4^2-L1^2)/(2*r*L4)]r =(L1^2+L4^2-2L1*L4cos(ai))^0.5确定约束条件:杆长非负条件:L2>0,L3>0曲柄存在条件: L1+L4-L2-L3>0 L1+L2-L3-L4>0 L1+L3-L2-L4>0机构传动角的限制:︒135>[γ]>=︒45jama= arcos([L2^2+L3^2-(L1+L4)^2]/(2*L2*L3))>=45 jama= arcos([L2^2+L3^2-(L4-L2)^2]/(2*L2*L3))<=135此为非线性约束优化问题,首先编写目标函数(角度偏差量)取名为myfun.m M 文件如下:function f=myfun(x) 该函数的输入为L2,L3 f=0a0=acos(((x(1)+1)^2-x(2)^2+25)/(10*(1+x(1)))) a0的初始值 b0=acos(((x(1)+1)^2-x(2)^2-25)/(10*x(2)))b0的初始值for a=a0:pi/18:(a0+1.5707) 以pi/18为步长测试a 不同值的情况 b=b0+2*(a-a0)^2/(3*pi) 测试b 不同值的情况 r=sqrt(26-10*cos(a))r 为A0所对的边m=acos((r^2+x(2)^2-x(1)^2)/(2*r*x(2))) n=acos((r^2+24)/(10*r)) bb=pi-m-n i=(bb-b)^2 f=f+i end 循环结束接着再编写非线性约束函数M 文件取名为mycon.m 文件如下: function [c,ceq]=mycon(x)c=[x(1)^2+x(2)^2-1.414*x(1)*x(2)-16; 36-x(1)^2-x(2)^2-1.414*x(1)*x(2)];ceq=[]最后在MATLAB命令窗口调用主程序:format long ; 以长数据格式显示x0=[6,3]; 给x0赋初值A=[-1 -1;1 -1;-1 1]; 给A赋值b=[-6;4;4];lb=zeros(2,1); 创建lb变量为两行一列的零阵options=optimset('largescale','off');[x,fval]=fmincon(@myfun,x0,A,b,[],[],lb,[],@mycon,options) 调用优化函数显示结果如下所示:f =0.00115968643895ceq =[]Optimization terminated: Magnitude of directional derivative in searchdirection less than 2*options.TolFun and maximum constraint violationis less than options.TolCon.Active inequalities (to within options.TolCon = 1e-006):lower upper ineqlin ineqnonlinx =4.06504526388845 2.39243572364663fval =0.00115968641518如下是相关截屏约束函数的M文件目标函数myfun在主程序窗口的运行结果。
基于MATLAB的曲柄摇杆机构的机械优化设计
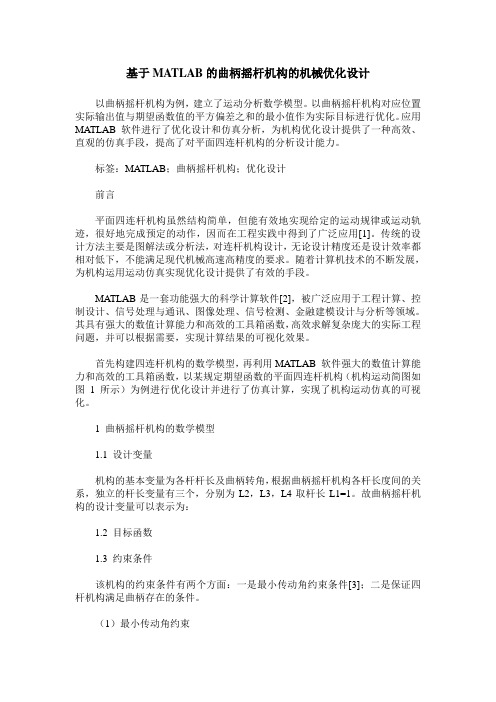
基于MATLAB的曲柄摇杆机构的机械优化设计以曲柄摇杆机构为例,建立了运动分析数学模型。
以曲柄摇杆机构对应位置实际输出值与期望函数值的平方偏差之和的最小值作为实际目标进行优化。
应用MATLAB软件进行了优化设计和仿真分析,为机构优化设计提供了一种高效、直观的仿真手段,提高了对平面四连杆机构的分析设计能力。
标签:MATLAB;曲柄摇杆机构;优化设计前言平面四连杆机构虽然结构简单,但能有效地实现给定的运动规律或运动轨迹,很好地完成预定的动作,因而在工程实践中得到了广泛应用[1]。
传统的设计方法主要是图解法或分析法,对连杆机构设计,无论设计精度还是设计效率都相对低下,不能满足现代机械高速高精度的要求。
随着计算机技术的不断发展,为机构运用运动仿真实现优化设计提供了有效的手段。
MATLAB是一套功能强大的科学计算软件[2],被广泛应用于工程计算、控制设计、信号处理与通讯、图像处理、信号检测、金融建模设计与分析等领域。
其具有强大的数值计算能力和高效的工具箱函数,高效求解复杂庞大的实际工程问题,并可以根据需要,实现计算结果的可视化效果。
首先构建四连杆机构的数学模型,再利用MATLAB 软件强大的数值计算能力和高效的工具箱函数,以某规定期望函数的平面四连杆机构(机构运动简图如图1 所示)为例进行优化设计并进行了仿真计算,实现了机构运动仿真的可视化。
1 曲柄摇杆机构的数学模型1.1 设计变量机构的基本变量为各杆杆长及曲柄转角,根据曲柄摇杆机构各杆长度间的关系,独立的杆长变量有三个,分别为L2,L3,L4取杆长L1=1。
故曲柄摇杆机构的设计变量可以表示为:1.2 目标函数1.3 约束条件该机构的约束条件有两个方面:一是最小传动角约束条件[3];二是保证四杆机构满足曲柄存在的条件。
(1)最小传动角约束或对应的约束函数为:(2)曲柄存在的条件按曲柄存在条件,由机械原理可知:2 结果比较文章的算例是四连杆机构的一个经典案例,常被研究四连杆机构的学者进行引用,但是很多人研究的都是已知曲柄和机架的参数优化设计,而把机架也作为未知量求解的程序较少,也就是研究的多是两参数的问题,一般把曲柄设置为1,机架设置为5,然后编程进行优化,结果如表1。
曲柄摇杆机构的综合优化设计
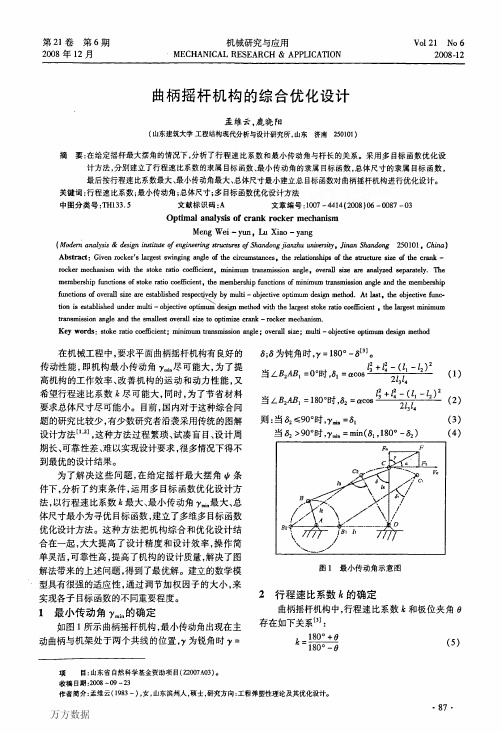
图1最小传动角示意图
2行程速比系数IjI的确定
曲柄摇杆机构中,行程速比系数蠡和极位夹角口 存在如下关系‘3l:
盂:黑等
万一1800—p
(~5J,)
项
目:山东省自然科学基金资助项目(Z2007A03)。
收稿日期:2008一09—23
3≥南≥l
建立数学模型时需注意:①口。,毛的大小可以根 据实际情况来定;②∞。,甜:根据工作要求来定。 3.5算例
设计一平面曲柄摇杆机构。已知给定摆角谚,
[y]=40。,最大杆长nD=400咖,‰=60mm。要求
y。h尽可能的大,.i}也尽可能大,总体尺寸尽可能小。 分别按以下三种情况来设计:
(1)甜l=0.5,山2=0.5,∞3=O (2)’∞1=O.5,∞2=0,∞3=O.5
在机械工程中,要求平面曲柄摇杆机构有良好的 传动性能,即机构最小传动角y。;。尽可能大,为了提 高机构的工作效率、改善机构的运动和动力性能,又 希望行程速比系数五尽可能大,同时,为了节省材料 要求总体尺寸尽可能小。目前,国内对于这种综合问 题的研究比较少,有少数研究者沿袭采用传统的图解 设计方法【l’2】,这种方法过程繁琐、试凑盲目、设计周 期长、可靠性差、难以实现设计要求,很多情况下得不 到最优的设计结果。
计与箭造,2005(8):86—87.
(上接第86页) 分的托板20用4个螺钉固定在导料板上。卸料板 12上各凸模穿过的孔处均采用lmm的间隙,卸料板 用6根拉杆lo拉住,拉杆下端用螺纹与卸料板连接, 上部台肩挂住上模板10内孔台肩。7个冲孔凸模均 从上方位后,将落料凸模15穿过凸模固定板6上的孑L,用 4个M8的内六角螺钉固定在上垫板7上,再用8个 MlO的内六角螺钉和2个定位销将凸模固定板、上垫 板、上模座固定在一起,各凸模上平面处被压紧。模 柄“与上模座孔为过盈配合,并由上垫板平面压紧。 定位销18、19安装在凹模相应孔中。
优化设计课程设计

1.ψ=式中0ϕ杆l4︒=≥45][m in γγ2.建立连杆机构设计的优化数学模型2.1确定设计变量由机械原理知识可知,铰链四杆机构按主、从动杆给定的角度对应关系进行设计时,独立参数有五个:三根杆长和主、从动杆的输入和输出起始位置角。
通常把曲柄的长度当成单位长度,即l1=1。
其它三杆的长度l2、l3、l4表示为实际杆长l1的倍数。
这是因为铰链四杆机构的各构件长若按同一比例缩放时,不会影响到主、从动杆的转角对应关系。
由本题题意,0ϕ和0ψ规定为摇杆在右极限位置时曲柄和摇杆的位置角。
在这种特定的条件下,0ϕ和0ψ也不再是独立参数,而是杆长的函数。
按图1不难写出如下关系式:()()⎥⎥⎦⎤⎢⎢⎣⎡++-+=421242322102arccos l l l l l l l ϕ;()⎥⎥⎦⎤⎢⎢⎣⎡--+=43242322102arccos l l l l l l ψ (1)另外,根据机构在机器中的许可空间,可以适当预选机架杆的长度,现取l4 =5。
经上述分析,该优化问题的设计变量是:X=[l2 l3]T =[x1 x2]T所以该优化问题是一个二维优化问题。
2.2建立目标函数由设计变量的分析可知,对于平面机构可供自由选择的独立参数是有限的。
对于实现给定运动规律的铰链四杆机构,独立参数最多为五个,而本题的情况只有两个。
因此利用平面连杆机构只能近似地实现给定的运动规律。
对于该机构设计问题,可取以机构输出角的平方偏差最小为目标函数,则它的表达形式可写成:∑=-=s i si i X F 02)()(ψψ (2)式中i ψ为期望输出角。
按给定的运动规律计算: 200)(32ϕϕπψψ-+=i i (3)i s i ⋅⋅+=120πϕϕ (i = 0,1,…,s) si ψ为机构实际输出角,计算式为:⎩⎨⎧≤<+-≤<--=)2()0(πϕπβαππϕβαπψi i i i i i si (4) 式中i α、i β可利用三角关系求出:⎪⎪⎭⎫ ⎝⎛-+=2212222arccos x r x x r i i i α;⎪⎪⎭⎫ ⎝⎛+=i i i r r 1024arccos 2β;i i r ϕcos 1026-= (5)i 是对应于曲柄从0ϕ转到20πϕ+角度内各等分点的标号。
优化设计-曲柄摇杆机构优化设计
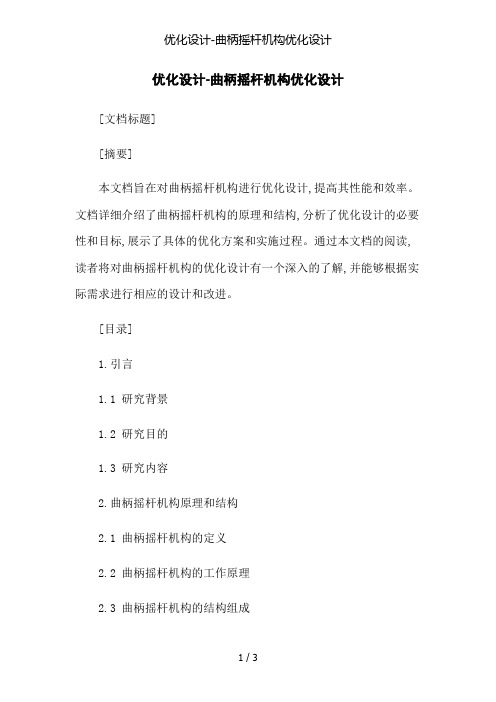
优化设计-曲柄摇杆机构优化设计
[文档标题]
[摘要]
本文档旨在对曲柄摇杆机构进行优化设计,提高其性能和效率。
文档详细介绍了曲柄摇杆机构的原理和结构,分析了优化设计的必要性和目标,展示了具体的优化方案和实施过程。
通过本文档的阅读,读者将对曲柄摇杆机构的优化设计有一个深入的了解,并能够根据实际需求进行相应的设计和改进。
[目录]
1.引言
1.1 研究背景
1.2 研究目的
1.3 研究内容
2.曲柄摇杆机构原理和结构
2.1 曲柄摇杆机构的定义
2.2 曲柄摇杆机构的工作原理
2.3 曲柄摇杆机构的结构组成
3.优化设计的必要性
3.1 现有曲柄摇杆机构存在的问题
3.2 优化设计的目标
4.优化设计方案
4.1 参数分析和优化目标的确定
4.2 设计方案的制定
4.3 仿真分析和评估
5.优化设计的实施过程
5.1 实施步骤和流程
5.2 设计实验和数据分析
5.3 结果和效果评估
6.结论
6.1 实施结果总结
6.2 存在的问题和进一步改进方向[附件]
- 附件1:曲柄摇杆机构优化设计报告- 附件2:仿真分析数据表格
- 附件3:设计实验原始数据
[法律名词及注释]
1.专利法:指国家对某项新的技术或技术方案所给予的一种专
门的权利保护。
2.商标法:指用于表示特定商品来源的某种标志的法律规定和
制度。
3.著作权法:指对于某种独立的创作作品,其作者取得的权利。
4.侵权:指在未取得相应权利人同意的情况下,侵犯他人在专利、商标、著作权等方面的合法权益的行为。
[全文结束]。
- 1、下载文档前请自行甄别文档内容的完整性,平台不提供额外的编辑、内容补充、找答案等附加服务。
- 2、"仅部分预览"的文档,不可在线预览部分如存在完整性等问题,可反馈申请退款(可完整预览的文档不适用该条件!)。
- 3、如文档侵犯您的权益,请联系客服反馈,我们会尽快为您处理(人工客服工作时间:9:00-18:30)。
矿产资源开发利用方案编写内容要求及审查大纲
矿产资源开发利用方案编写内容要求及《矿产资源开发利用方案》审查大纲一、概述
㈠矿区位置、隶属关系和企业性质。
如为改扩建矿山, 应说明矿山现状、
特点及存在的主要问题。
㈡编制依据
(1简述项目前期工作进展情况及与有关方面对项目的意向性协议情况。
(2 列出开发利用方案编制所依据的主要基础性资料的名称。
如经储量管理部门认定的矿区地质勘探报告、选矿试验报告、加工利用试验报告、工程地质初评资料、矿区水文资料和供水资料等。
对改、扩建矿山应有生产实际资料, 如矿山总平面现状图、矿床开拓系统图、采场现状图和主要采选设备清单等。
二、矿产品需求现状和预测
㈠该矿产在国内需求情况和市场供应情况
1、矿产品现状及加工利用趋向。
2、国内近、远期的需求量及主要销向预测。
㈡产品价格分析
1、国内矿产品价格现状。
2、矿产品价格稳定性及变化趋势。
三、矿产资源概况
㈠矿区总体概况
1、矿区总体规划情况。
2、矿区矿产资源概况。
3、该设计与矿区总体开发的关系。
㈡该设计项目的资源概况
1、矿床地质及构造特征。
2、矿床开采技术条件及水文地质条件。