常见焊接缺陷及控制
焊接中出现的问题和解决方案
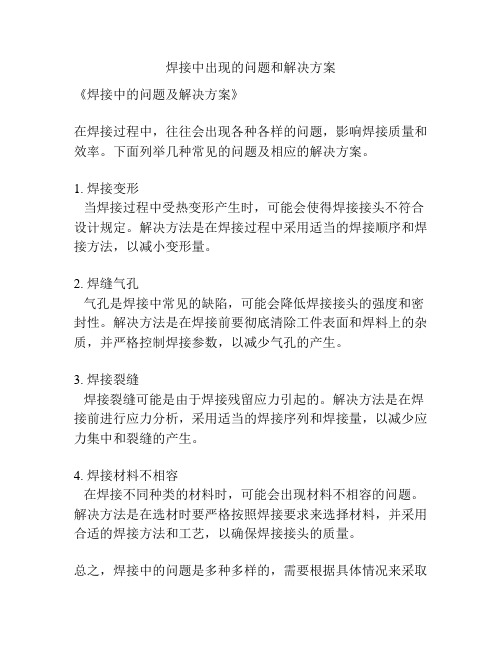
焊接中出现的问题和解决方案
《焊接中的问题及解决方案》
在焊接过程中,往往会出现各种各样的问题,影响焊接质量和效率。
下面列举几种常见的问题及相应的解决方案。
1. 焊接变形
当焊接过程中受热变形产生时,可能会使得焊接接头不符合设计规定。
解决方法是在焊接过程中采用适当的焊接顺序和焊接方法,以减小变形量。
2. 焊缝气孔
气孔是焊接中常见的缺陷,可能会降低焊接接头的强度和密封性。
解决方法是在焊接前要彻底清除工件表面和焊料上的杂质,并严格控制焊接参数,以减少气孔的产生。
3. 焊接裂缝
焊接裂缝可能是由于焊接残留应力引起的。
解决方法是在焊接前进行应力分析,采用适当的焊接序列和焊接量,以减少应力集中和裂缝的产生。
4. 焊接材料不相容
在焊接不同种类的材料时,可能会出现材料不相容的问题。
解决方法是在选材时要严格按照焊接要求来选择材料,并采用合适的焊接方法和工艺,以确保焊接接头的质量。
总之,焊接中的问题是多种多样的,需要根据具体情况来采取
相应的解决方法。
只有不断积累经验、改进技术,才能够提高焊接质量和效率。
常见焊接缺陷及焊接质量检验资料
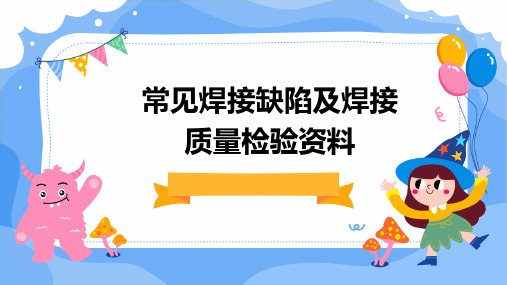
02
不同的焊接方法和应用领域有不同的质量检验标准,应选择适
用的标准进行检验。
焊接质量检验标准应定期更新,以适应技术发展和提高质量要
03
求。
焊接质量检验记录
焊接质量检验记录是对焊接质量进行跟踪和追溯的重 要手段,应详细记录检验时间、检验人员、检验方法、
检验结果等信息。
焊接质量检验记录应保持真实、完整、准确,以便对 焊接质量问题进行分析和改进。
05
结论
焊接缺陷对焊接质量的影响
01
焊接缺陷如气孔、夹渣、未熔合等会导致焊接接头的强度、塑 性和韧性下降,影响焊接结构的承载能力和使用寿命。
02
焊接缺陷会导致焊接接头的疲劳强度降低,增加疲劳断裂 的风险。
03
焊接缺陷会影响焊接结构的耐腐蚀性能,降低其耐腐蚀性。
焊接质量检验的重要性和作用
焊接质量检验是确保焊接结构安全可靠的重要手段,能够及时发现和消除 焊接缺陷,防止因焊接缺陷导致的安全事故。
焊接工艺评定
焊接工艺评定是确保焊接质量的重要环节,通 过对焊接工艺参数、焊接材料、焊接方法等进 行评估,确定焊接工艺的可行性和可靠性。
焊接工艺评定应遵循相关标准和规范,确保评 定的科学性和准确性。
焊接工艺评定结果应记录在评定报告中,并作 为后续焊接工作的依据。
焊接质量检验标准
01
焊接质量检验标准是衡量焊接质量的依据,规定了焊接接头的 外观质量、无损检测、力学性能等方面的要求。
详细描述
夹渣通常是由于焊接电流过小、焊接速度过快、坡口清理不干净等原因造成的。 在焊接过程中,熔渣未能及时浮出表面或被排除,就会残留在焊缝金属中形成夹 渣。夹渣可能导致焊接接头的强度下降,甚至引发断裂。
气孔
焊接——焊接缺陷及防治措施
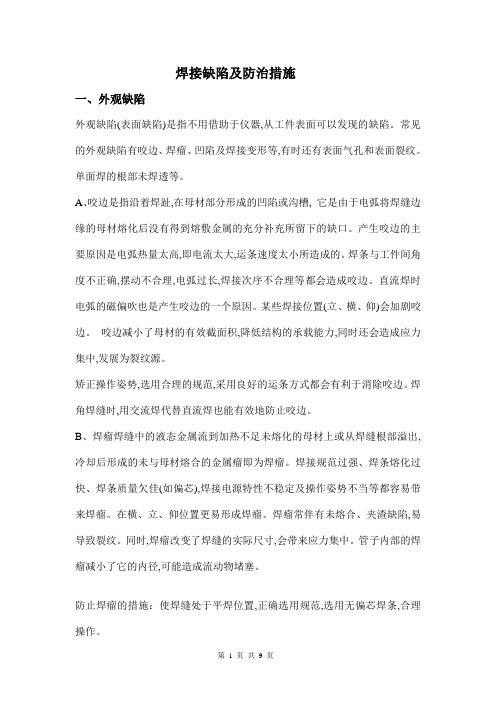
焊接缺陷及防治措施一、外观缺陷外观缺陷(表面缺陷)是指不用借助于仪器,从工件表面可以发现的缺陷。
常见的外观缺陷有咬边、焊瘤、凹陷及焊接变形等,有时还有表面气孔和表面裂纹。
单面焊的根部未焊透等。
A、咬边是指沿着焊趾,在母材部分形成的凹陷或沟槽, 它是由于电弧将焊缝边缘的母材熔化后没有得到熔敷金属的充分补充所留下的缺口。
产生咬边的主要原因是电弧热量太高,即电流太大,运条速度太小所造成的。
焊条与工件间角度不正确,摆动不合理,电弧过长,焊接次序不合理等都会造成咬边。
直流焊时电弧的磁偏吹也是产生咬边的一个原因。
某些焊接位置(立、横、仰)会加剧咬边。
咬边减小了母材的有效截面积,降低结构的承载能力,同时还会造成应力集中,发展为裂纹源。
矫正操作姿势,选用合理的规范,采用良好的运条方式都会有利于消除咬边。
焊角焊缝时,用交流焊代替直流焊也能有效地防止咬边。
B、焊瘤焊缝中的液态金属流到加热不足未熔化的母材上或从焊缝根部溢出,冷却后形成的未与母材熔合的金属瘤即为焊瘤。
焊接规范过强、焊条熔化过快、焊条质量欠佳(如偏芯),焊接电源特性不稳定及操作姿势不当等都容易带来焊瘤。
在横、立、仰位置更易形成焊瘤。
焊瘤常伴有未熔合、夹渣缺陷,易导致裂纹。
同时,焊瘤改变了焊缝的实际尺寸,会带来应力集中。
管子内部的焊瘤减小了它的内径,可能造成流动物堵塞。
防止焊瘤的措施:使焊缝处于平焊位置,正确选用规范,选用无偏芯焊条,合理操作。
C、凹坑凹坑指焊缝表面或背面局部的低于母材的部分。
凹坑多是由于收弧时焊条(焊丝)未作短时间停留造成的(此时的凹坑称为弧坑),仰立、横焊时,常在焊缝背面根部产生内凹。
凹坑减小了焊缝的有效截面积,弧坑常带有弧坑裂纹和弧坑缩孔。
防止凹坑的措施:选用有电流衰减系统的焊机,尽量选用平焊位置,选用合适的焊接规范,收弧时让焊条在熔池内短时间停留或环形摆动,填满弧坑。
D、未焊满未焊满是指焊缝表面上连续的或断续的沟槽。
填充金属不足是产生未焊满的根本原因。
焊接常见缺陷产生的原因及其预防措施
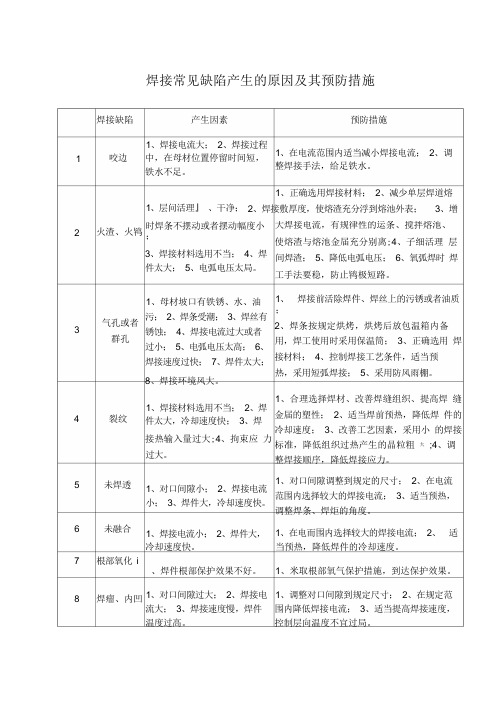
焊接常见缺陷产生的原因及其预防措施1 2 3 45 6 7 8 焊接缺陷咬边火渣、火鸨气孔或者群孔裂纹未焊透未融合根部氧化i焊瘤、内凹产生因素1、焊接电流大;2、焊接过程中,在母材位置停留时间短,铁水不足。
预防措施1、在电流范围内适当减小焊接电流;2、调整焊接手法,给足铁水。
1、正确选用焊接材料;2、减少单层焊道熔1、层问活理』、干净;2、焊接敷厚度,使熔渣充分浮到熔池外表;3、增时焊条不摆动或者摆动幅度小;3、焊接材料选用不当;4、焊件太大;5、电弧电压太局。
1、母材坡口有铁锈、水、油污;2、焊条受潮;3、焊丝有锈蚀;4、焊接电流过大或者过小;5、电弧电压太高;6、焊接速度过快;7、焊件太大;8、焊接环境风大。
1、焊接材料选用不当;2、焊件太大,冷却速度快;3、焊接热输入量过大;4、拘束应力过大。
1、对口间隙小;2、焊接电流小;3、焊件大,冷却速度快。
1、焊接电流小;2、焊件大,冷却速度快。
、焊件根部保护效果不好。
1、对口间隙过大;2、焊接电流大;3、焊接速度慢,焊件温度过高。
大焊接电流,有规律性的运条、搅拌熔池、使熔渣与熔池金届充分别离;4、子细活理层间焊渣;5、降低电弧电压;6、氧弧焊时焊工手法要稳,防止鸨极短路。
1、焊接前活除焊件、焊丝上的污锈或者油质;2、焊条按规定烘烤,烘烤后放包温箱内备用,焊工使用时采用保温筒;3、正确选用焊接材料;4、控制焊接工艺条件,适当预热,采用短弧焊接;5、采用防风雨棚。
1、合理选择焊材、改善焊缝组织、提高焊缝金届的塑性;2、适当焊前预热,降低焊件的冷却速度;3、改善工艺因素,采用小的焊接标准,降低组织过热产生的晶粒粗大;4、调整焊接顺序,降低焊接应力。
1、对口间隙调整到规定的尺寸;2、在电流范围内选择较大的焊接电流;3、适当预热,调整焊条、焊炬的角度。
1、在电而围内选择较大的焊接电流;2、适当预热,降低焊件的冷却速度。
1、米取根部氧气保护措施,到达保护效果。
常见焊接缺点与避免办法
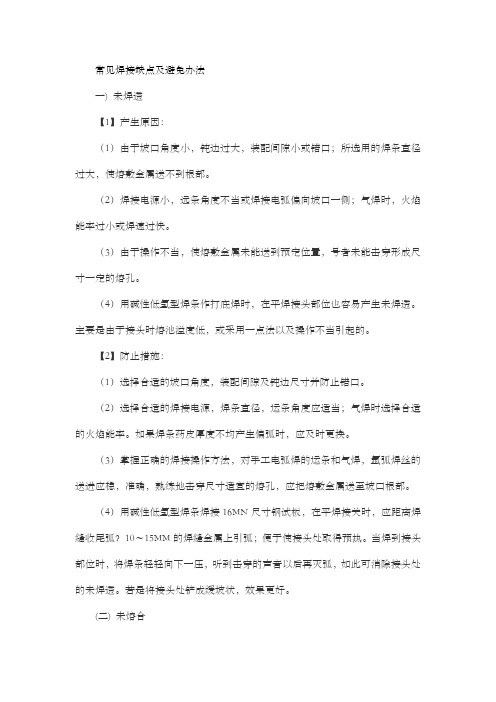
常见焊接缺点及避免办法一) 未焊透【1】产生原因:(1)由于坡口角度小,钝边过大,装配间隙小或错口;所选用的焊条直径过大,使熔敷金属送不到根部。
(2)焊接电源小,远条角度不当或焊接电弧偏向坡口一侧;气焊时,火焰能率过小或焊速过快。
(3)由于操作不当,使熔敷金属未能送到预定位置,号者未能击穿形成尺寸一定的熔孔。
(4)用碱性低氢型焊条作打底焊时,在平焊接头部位也容易产生未焊透。
主要是由于接头时熔池溢度低,或采用一点法以及操作不当引起的。
【2】防止措施:(1)选择合适的坡口角度,装配间隙及钝边尺寸并防止错口。
(2)选择合适的焊接电源,焊条直径,运条角度应适当;气焊时选择合适的火焰能率。
如果焊条药皮厚度不均产生偏弧时,应及时更换。
(3)掌握正确的焊接操作方法,对手工电弧焊的运条和气焊,氩弧焊丝的送进应稳,准确,熟练地击穿尺寸适宜的熔孔,应把熔敷金属送至坡口根部。
(4)用碱性低氢型焊条焊接16MN尺寸钢试板,在平焊接关时,应距离焊缝收尾弧?10~15MM的焊缝金属上引弧;便于使接头处取得预热。
当焊到接头部位时,将焊条轻轻向下一压,听到击穿的声音以后再灭弧,如此可消除接头处的未焊透。
若是将接头处铲成缓坡状,效果更好。
(二) 未熔合【1】产生原因:(1)手工电弧焊时,由于运条角度不当或产生偏弧,电弧不能良好地加热坡口两侧金属,导致坡口面金属未能充分熔化。
(2)在焊接时由于上侧坡口金属熔化后产生下坠,影响下侧坡口面金属的加热熔化,造成“冷接”。
(3)横接操作时,在上、下坡口面击穿顺序不对,未能先击穿下坡口后击穿上坡口,或者在上、下坡口面上击穿熔孔位置未能错开一定的距离,使上坡口熔化金属下坠产生粘接,造成未熔合。
(4)气悍时火焰能率小,氩弧焊时电弧两侧坡口的加热不均,或者坡口面存在污物等。
【2】防止措施:(1)选择适宜的运条角度,焊接电弧偏弧时应及时更换焊条。
(2)操作时注意观察坡口两侧金属熔化情况,使之熔合良好。
焊接质量缺陷原因分析及预防、治理措施
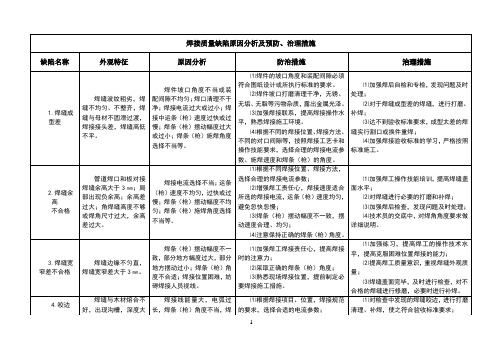
⑷根据自己的操作技能,选择合适的线能量、焊接速度和操作手法。
厚度符合标准要求;
⑵加强打底练习,熟练掌握操作手法以及对应的焊接线能量及焊接速度等。
18.管道焊口根部焊瘤、凸出、凹陷
⑷注意周围焊接施工环境,搭设防风设施,管子焊接无穿堂风;
⑸氩弧焊时,氩气纯度不低于%,氩气流量合适;
⑹尽量采用短弧焊接,减少气体进入熔池的机会;
⑺焊工操作手法合理,焊条、焊枪角度合适;
⑻焊接线能量合适,焊接速度不能过快;
⑼按照工艺要求进行焊件预热。
⑴严格按照预防措施执行;
⑵加强焊工练习,提高操作水平和责任心;
⑴严格按照规程和作业指导书的要求准备各种焊接条件;
⑵提高焊接操作技能,熟练掌握使用的焊接方法;
⑶采取合理的焊接顺序等措施,减少焊接应力等。
⑴针对每种产生裂纹的具体原因采取相应的对策;
⑵对已经产生裂纹的焊接接头,采取挖补措施处理。
11.焊缝表面不清理或清理不干净,电弧擦伤焊件
焊缝焊接完毕,焊接接头表面药皮、飞溅物不清理或清理不干净,留有药皮或飞溅物;焊接施工过程中不注意,电弧擦伤管壁等焊件造成弧疤。
⑶发现问题及时采取必要措施。
14.气孔
在焊缝中出现的单个、条状或群体气孔,是焊缝内部最常见的缺陷。
根本原因是焊接过程中,焊接本身产生的气体或外部气体进入熔池,在熔池凝固前没有来得及溢出熔池而残留在焊缝中。
⑴焊条要求进行烘培,装在保温筒内,随用随取;
⑵焊丝清理干净,无油污等杂质;
⑶焊件周围10~15㎜范围内清理干净,直至发出金属光泽;
⑴焊件的坡口角度和装配间隙必须符合图纸设计或所执行标准的要求。
焊接缺陷及预防措施
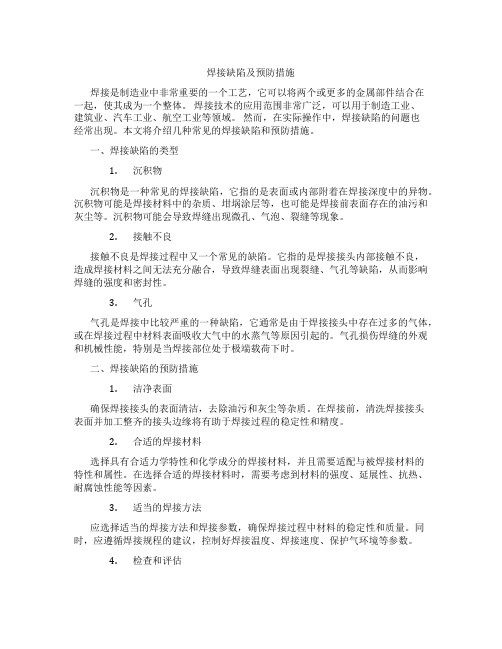
焊接缺陷及预防措施焊接是制造业中非常重要的一个工艺,它可以将两个或更多的金属部件结合在一起,使其成为一个整体。
焊接技术的应用范围非常广泛,可以用于制造工业、建筑业、汽车工业、航空工业等领域。
然而,在实际操作中,焊接缺陷的问题也经常出现。
本文将介绍几种常见的焊接缺陷和预防措施。
一、焊接缺陷的类型1.沉积物沉积物是一种常见的焊接缺陷,它指的是表面或内部附着在焊接深度中的异物。
沉积物可能是焊接材料中的杂质、坩埚涂层等,也可能是焊接前表面存在的油污和灰尘等。
沉积物可能会导致焊缝出现微孔、气泡、裂缝等现象。
2.接触不良接触不良是焊接过程中又一个常见的缺陷。
它指的是焊接接头内部接触不良,造成焊接材料之间无法充分融合,导致焊缝表面出现裂缝、气孔等缺陷,从而影响焊缝的强度和密封性。
3.气孔气孔是焊接中比较严重的一种缺陷,它通常是由于焊接接头中存在过多的气体,或在焊接过程中材料表面吸收大气中的水蒸气等原因引起的。
气孔损伤焊缝的外观和机械性能,特别是当焊接部位处于极端载荷下时。
二、焊接缺陷的预防措施1.洁净表面确保焊接接头的表面清洁,去除油污和灰尘等杂质。
在焊接前,清洗焊接接头表面并加工整齐的接头边缘将有助于焊接过程的稳定性和精度。
2.合适的焊接材料选择具有合适力学特性和化学成分的焊接材料,并且需要适配与被焊接材料的特性和属性。
在选择合适的焊接材料时,需要考虑到材料的强度、延展性、抗热、耐腐蚀性能等因素。
3.适当的焊接方法应选择适当的焊接方法和焊接参数,确保焊接过程中材料的稳定性和质量。
同时,应遵循焊接规程的建议,控制好焊接温度、焊接速度、保护气环境等参数。
4.检查和评估在焊接过程中,应定期检查和评估焊接质量和焊缝的特征。
检查焊缝的外观、尺寸和形状等特征,以确保焊接的质量和完整性。
结论在焊接过程中,焊接缺陷的出现是非常常见的。
要预防焊接缺陷,需要实施一系列的措施,例如保持表面干净,选择合适的焊接材料和方法以及定期检查焊接质量等。
焊接质量缺陷原因分析及预防、治理措施
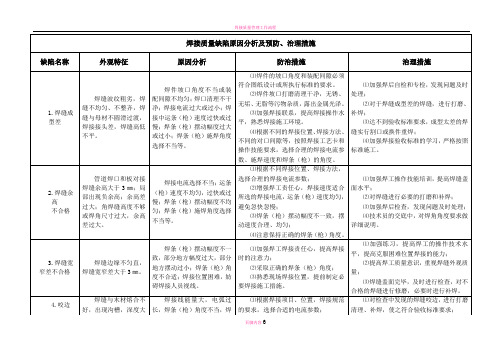
⑵加强质量标准的学习,提高焊工质量意识;
⑶加强练习,提高防止咬边缺陷的操作技能。
5.错口
表现为焊缝两侧外壁母材不在同一平面上,错口量大于10%母材厚度或超过4㎜。
焊件对口不符合要求,焊工在对口不合适的情况下点固和焊接。
⑴加强安装工的培训和责任心;
⑴焊接材料、母材打磨清理等严格按照规定执行;
⑵加强焊工练习,提高操作水平和操作经验;
⑶对有表面气孔的焊缝,机械打磨清除缺陷,必要时进行补焊。
9表面夹渣
在焊接过程中,主要是在层与层间出现外部看到的药皮夹渣。
⑴多层多道焊接时,层间药皮清理不干净;
⑵焊接线能量小,焊接速度快;
⑶焊接操作手法不当;
⑷前一层焊缝表面不平或焊件表面不符合要求。
焊接线能量大,电弧过长,焊条(枪)角度不当,焊条(丝)送进速度不合适等都是造成咬边的原因。
⑴根据焊接项目、位置,焊接规范的要求,选择合适的电流参数;
⑵控制电弧长度,尽量使用短弧焊接;
⑶掌握必要的运条(枪)方法和技巧;
⑷焊条(丝)送进速度与所选焊接电流参数协调;
⑸注意焊缝边缘与母材熔化结合时的焊条(枪)角度。
⑴加强焊后自检和专检,发现问题及时处理;
⑵对于焊缝成型差的焊缝,进行打磨、补焊;
⑶达不到验收标准要求,成型太差的焊缝实行割口或换件重焊;
⑷加强焊接验收标准的学习,严格按照标准施口和板对接焊缝余高大于3㎜;局部出现负余高;余高差过大;角焊缝高度不够或焊角尺寸过大,余高差过大。
焊接电流选择不当;运条(枪)速度不均匀,过快或过慢;焊条(枪)摆动幅度不均匀;焊条(枪)施焊角度选择不当等。
⑴根据不同焊接位置、焊接方法,选择合理的焊接电流参数;
焊接中常见的缺陷及预防措施
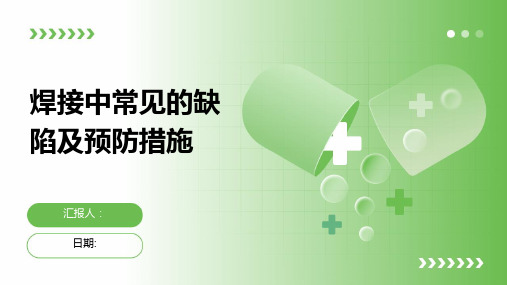
合理选择焊接顺序
避免在结构中产生过大的 拘束度。
夹渣的预防措施
1 2
选用合适的焊接电流和焊接速度
确保熔池充分熔化,避免熔渣残留。
清除杂质
焊接前彻底清除坡口边缘和焊丝上的杂质。
3
多层焊接
每层焊接完成后,彻底清除熔渣再进行下一层焊 接。
未焊透与未熔合的预防措施
选用合适的坡口和焊接参数
根据母材厚度和焊接位置选择合适的坡口形状和焊接参数 。
裂纹
总结词
裂纹是焊接中危险的缺陷,表现为焊缝中的开裂部分。
详细描述
裂纹的产生主要是由于焊接过程中热应力、材料质量、结构设计等因素的影响, 焊缝中的应力超过材料的强度极限,导致焊缝开裂。裂纹的存在会严重影响焊接 的强度和稳定性。
夹渣
总结词
夹渣是焊接中常见的缺陷,表现为焊缝中存在的杂质和夹杂 物。
详细描述
电弧太长使得热量分散过大,不利于 熔池的保持和气体的排除,容易形成 气孔。
裂纹的产生原因
碳当量过高
预热温度不足
对于一些高碳钢或合金钢,其碳当量过高 ,焊接时易产生裂纹。
对于一些大厚度的焊件,预热温度不足导 致焊缝冷却速度过快,产生裂纹。
应力集中
焊缝处理不当
由于结构或工件形状的原因,焊缝处存在 较大的应力集中,易产生裂纹。
焊接中常见的缺 陷及预防措施
汇报人: 日期:
目录
• 引言 • 焊接缺陷的分类与识别 • 焊接缺陷的产生原因 • 焊接缺陷的预防措施 • 焊接缺陷的修复方法 • 结论
01
引言
焊接的定义与重要性
• 焊接是一种通过加热或加压金属接头,使其原子间相互结合, 达到连接金属的方法。焊接在工业制造中扮演着至关重要的角 色,包括桥梁、建筑、汽车、船舶、飞机等。
常见焊接缺陷及预防措施
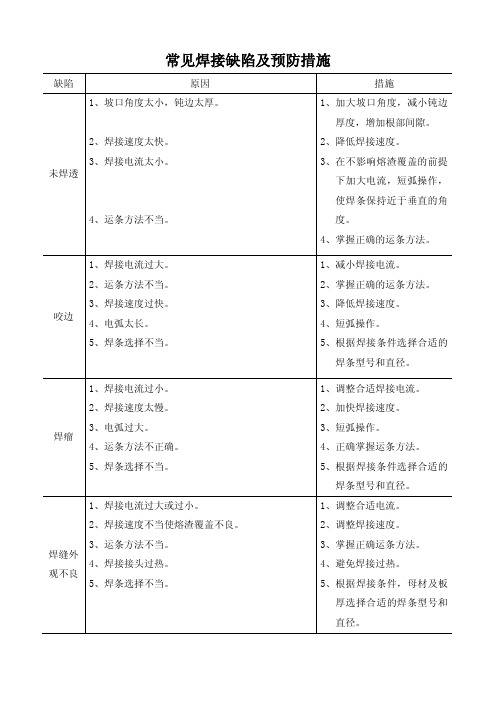
缺陷 原因 1、坡口角度太小,钝边太厚。 措施 1、加大坡口角度,减小钝边 厚度,增加根部间隙。 2、焊接速度太快。 3、焊接电流太小。 未焊透 2、降低焊接速度。 3、在不影响熔渣覆盖的前提 下加大电流,短弧操作, 使焊条保持近于垂直的角 4、运条方法不当。 度。 4、掌握正确的运条方法。 1、焊接电流过大。 2、运条方法不当。 3、焊接速度过快。 咬边 4、电弧太长。 5、焊条选择不当。 1、减小焊接电流。 2、掌握正确的运条方法。 3、降低焊接速度。 4、短弧操作。 5、根据焊接条件选择合适的 焊条型号和直径。 1、焊接电流过小。 2、焊接速度太慢。 焊瘤 3、电弧过大。 4、运条方法不正确。 5、焊条选择不当。 1、调整合适焊接电流。 2、加快焊接速度。 3、短弧操作。 4、正确掌握运条方法。 5、根据焊接条件选择合适的 焊条型号和直径。 1、焊接电流过大或过小。 2、焊接速度不当使熔渣覆盖不良。 焊缝外 观不良 3、运条方法不当。 4、焊接接头过热。 5、焊条选择不当。 1、调整合适电流。 2、调整焊接速度。 3、掌握正确运条方法。 4、避免焊接过热。 5、根据焊接条件,母材及板 厚选择合适的焊条型号和 直径。
4、焊条吸潮。
规范。 4、焊前焊条烘干,选用难吸
ห้องสมุดไป่ตู้
潮焊条或超低氢焊条。 1、坡口形状不良。 1、减小根部间隙及加大钝边 高度。 2、焊接电流过大。 烧穿 3、焊接速度过慢。 4、母材过热。 5、电弧过长。 1、焊接接头设计不当。 2、使用较小的电流或选用电 弧吹力小的焊条。 3、适当加快焊接速度。 4、避免接头过热。 5、短弧操作。 1、设计时预先考虑到接头的 膨胀、收缩。 2、接头下部过热。 2、使用小电流、选用熔深浅 的焊条。 变形 3、焊接速度过慢。 4、焊接顺序不当。 5、缺乏约束的条件。 3、适当加快焊接速度。 4、正确安排焊接顺序。 5、使 用 夹 具 等 进 行 充 分 约 束,但必须注意防止产生 裂缝。 1、焊条吸潮。 2、焊接区表面赃物太多。 3、焊条过热发红。 凹坑 4、母材含硫过高。 5、母材的碳、锰过高。 1、焊前焊条烘干。 2、清除表面油、锈、油漆等 污物。 3、使用小电流、避免焊条过 热。 4、使用低氢型焊条。 5、使用碱度高的焊条。 1、电流过大。 2、焊接时产生磁偏吹。 飞溅 3、碱性焊条错用正极性。 4、焊条吸潮。 5、电弧过大。 1、使用合适的电流。 2、尽量防止磁偏吹。 3、改 用 反 接 ( 即 焊 条 接 正 极) 。 4、焊前焊条烘干。 5、用短弧施焊。
常见焊接缺陷
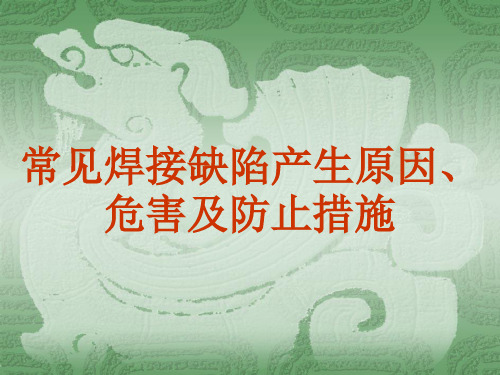
6、未熔合:熔焊时,焊道与母材之间或焊 道之间未能完全熔化熔化结合在一起的部 分,称为未熔合。也称为“假焊”常见的 未熔合部位有三处;坡口边缘未熔合、焊 缝金属层间未熔合。
危害:是一种比较危险的焊接缺陷,焊缝 出现间断和突变部位,使得焊接接头的强 度ቤተ መጻሕፍቲ ባይዱ大降低。未熔合部位还存在尖劈间隙, 承载后应力集中严重,极易由此处产生裂 纹。
c.焊件表面及坡口有水、油、锈等污物存在, 这些污物在电弧高温作用下,分解出来的 一氧化碳、氢和水蒸气等,进入熔池后往 往形成一氧化碳气孔和氢气孔。
d.焊接电流偏低或焊接速度过快,熔池存 在的时间短,以致于气体来不及从熔池金 属中逸出。
e.电弧长度过长,使熔池失去了气体的保护, 空气很容易侵入熔池,焊接电流过大,焊 条发红,药皮脱落,而失去了保护作用, 电弧偏吹,运条手法不稳等。
常见焊接缺陷产生原因、 危害及防止措施
★★焊接缺陷的分类:
焊接缺陷可分为外部缺陷和内部缺陷两种 1.外部缺陷分为: 1外观形状和尺寸不符合要求;2表面裂纹;3表面
气孔;4咬边;5凹陷;6满溢;7焊瘤;8弧坑;9电 弧擦伤;10明冷缩孔;11烧穿;12过烧。 2.内部缺陷分为: 1焊接裂纹:a.冷裂纹;b.层状撕裂;c.热裂纹; d.再热裂纹。 2气孔;3夹渣;4未焊透;5未熔合;6夹钨;7夹珠。
产生原因:焊件坡口角度不对,装配 间隙不匀,点固焊时未对正,焊接电 流过大或过小,运条速度过快或过慢, 焊条的角度选择不合适或改变不当, 埋弧焊焊接工艺选择不正确等。
防止措施:选择合适的坡口角度,按 标准要求点焊组装焊件,并保持间隙 均匀,编制合理的焊接工艺流程,控 制变形和翘曲,正确选用焊接电流, 合适地掌握焊接速度,采用恰当的运 条手法和角度,随时注意适应焊件的 坡口变化,以保证焊缝外观成形均匀 一致。
焊接中常见的缺陷及预防措施

焊接中常见的缺陷及预防措施焊接作为一种常见的金属连接技术,广泛应用于许多领域,如汽车、建筑、机械、航空等。
在焊接过程中,由于多种因素的影响,可能会产生各种焊接缺陷,这些缺陷如果不能及时检测和修补,将会导致焊接接头的质量下降,从而影响产品的性能和安全。
因此,掌握焊接缺陷的类型,了解它们的形成原因和特征,并采取相应的预防措施是非常必要的。
一、焊接中常见的缺陷类别1.焊接裂纹焊接裂纹是指在焊接接头中形成的一些裂缝,通常会引起焊接接头的破裂和开裂。
其主要原因是焊接时产生的应力过高,而焊接接头的塑性或韧性低于应力水平,导致裂纹形成。
2.气孔气孔是指在焊接接头中形成的一些气体孔隙,通常会引起焊接接头的承载能力下降和腐蚀敏感性增加。
其主要原因是焊接过程中气体没有得到完全排放,或焊接材料中含有氧化物等杂质,导致产生气孔。
3.未焊透未焊透是指在焊接接头中存在未完全焊透的情况,通常会导致焊接接头的强度下降和腐蚀敏感性增加。
其主要原因是焊接温度不够高或焊接时间不够长,没有完成全部焊接。
4.冷焊接冷焊接是指在焊接接头中因火焰不足或焊材量不足等因素,导致接头不够热,未能产生彻底结合而形成的缺陷,通常会导致焊接接头的强度下降和腐蚀敏感性增加。
5.夹渣夹渣是指在焊接接头中因焊丝或焊条的表面有杂质或内部含气,而导致未能将渣完全浮于熔池表面,而与熔池结合形成的缺陷,通常会引起焊接接头的强度下降和腐蚀敏感性增加。
6.焊接变形焊接变形是指焊接接头在焊接中由于受到热应力和冷却收缩的影响,而发生形变的现象。
其主要原因是焊接温度和焊接速度不合适,或使用的焊接方法错误。
二、焊接中常见缺陷的预防措施1.焊接裂纹的预防(1)控制焊接热量,采用适当的预热和后热措施,以减少焊接接头的热应力;(2)选择适当的材料和焊接方法,以提高焊接接头的塑性和韧性;(3)严格执行焊接规程,防止焊接接头产生一些质量问题,如缺陷、气孔等。
2.气孔的预防(1)使用干燥的焊材和基材,以减少水分和氧化物等杂质的含量;(2)控制焊接过程中的熔池气氛,以避免氧和氮等气体的侵入;(3)严格执行焊接规程和焊接参数的标准,以保证焊接接头的质量。
焊接缺陷产生原因及防止措施

焊接缺陷产生原因及防止措施焊接缺陷是指焊接工艺过程中产生的不符合要求的缺陷,会导致焊接接头的强度、密封性和耐腐蚀性等性能下降。
产生焊接缺陷的原因很多,包括焊接工艺参数不合理、材料质量不良、操作不当等。
为了避免焊接缺陷的产生,需要采取一系列防止措施。
1.工艺参数不合理:焊接工艺参数的选择与设置非常重要,如电流、电压、焊接速度等。
如果选择不当或设置不合理,容易导致焊缝结构不良、焊接接头强度降低等缺陷的产生。
因此,在焊接前应对工艺参数进行正确的评估,根据焊接件的要求和材料特性选择合适的参数。
2.材料质量不良:焊接材料的质量对焊接接头的质量有很大的影响。
材料存在裂纹、氧化物、夹杂物等缺陷时,焊接过程中很容易产生焊接缺陷。
因此,在选材过程中应选择质量良好的焊接材料,并进行必要的预处理,如清洗、除锈等。
3.焊接操作不当:焊接操作人员的技术水平和操作经验对产生焊接缺陷起着决定性的作用。
操作不当、不熟练或粗心大意容易导致焊接缺陷的产生。
因此,操作人员应具备良好的焊接技术和严谨的工作态度,严格按照焊接规程进行操作。
下面是预防焊接缺陷的措施:1.合理选择焊接工艺参数:根据焊件的材料特性和焊接要求,选择合适的焊接工艺参数,如适当的电流、电压、焊接速度等。
并进行试焊,通过试焊找出最佳的焊接参数,以保证焊接接头的质量。
2.选择质量良好的焊接材料:在选择焊接材料时,应选择质量可靠的材料,并进行必要的预处理,如清洗、除锈等。
同时,根据焊接件的材料特性和要求选择合适的焊接材料。
3.提高焊接操作人员的技术水平:培训焊接操作人员,提高其焊接技术水平和操作经验。
引导焊接操作人员积极参加焊接技能比赛和培训班,不断提高操作技能,增强工作责任心和自我监督能力。
4.制定严格的焊接规程:对于一些复杂的焊接工艺,应制定详细的焊接规程,并严格执行。
规程中要包括焊接参数、焊接顺序、焊接方法、检验标准等内容,以保证焊接接头的质量。
5.加强质量控制和检验:建立完善的焊接质量控制体系,加强对焊接工艺过程的监控和控制。
焊接中常见的缺陷及防治措施
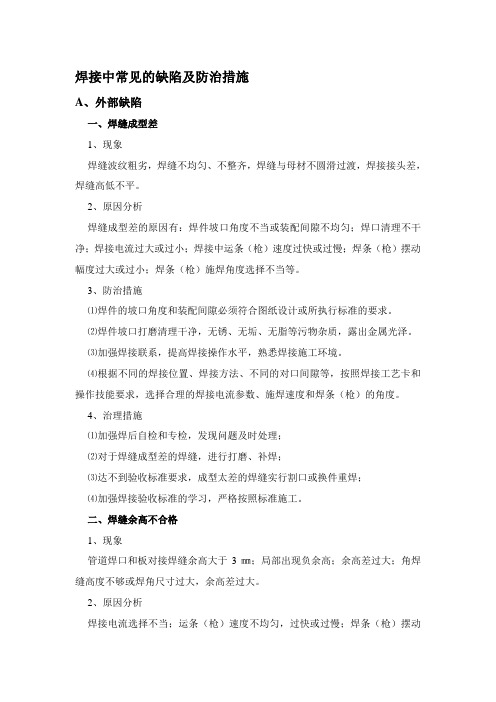
焊接中常见的缺陷及防治措施A、外部缺陷一、焊缝成型差1、现象焊缝波纹粗劣,焊缝不均匀、不整齐,焊缝与母材不圆滑过渡,焊接接头差,焊缝高低不平。
2、原因分析焊缝成型差的原因有:焊件坡口角度不当或装配间隙不均匀;焊口清理不干净;焊接电流过大或过小;焊接中运条(枪)速度过快或过慢;焊条(枪)摆动幅度过大或过小;焊条(枪)施焊角度选择不当等。
3、防治措施⑴焊件的坡口角度和装配间隙必须符合图纸设计或所执行标准的要求。
⑵焊件坡口打磨清理干净,无锈、无垢、无脂等污物杂质,露出金属光泽。
⑶加强焊接联系,提高焊接操作水平,熟悉焊接施工环境。
⑷根据不同的焊接位置、焊接方法、不同的对口间隙等,按照焊接工艺卡和操作技能要求,选择合理的焊接电流参数、施焊速度和焊条(枪)的角度。
4、治理措施⑴加强焊后自检和专检,发现问题及时处理;⑵对于焊缝成型差的焊缝,进行打磨、补焊;⑶达不到验收标准要求,成型太差的焊缝实行割口或换件重焊;⑷加强焊接验收标准的学习,严格按照标准施工。
二、焊缝余高不合格1、现象管道焊口和板对接焊缝余高大于3㎜;局部出现负余高;余高差过大;角焊缝高度不够或焊角尺寸过大,余高差过大。
2、原因分析焊接电流选择不当;运条(枪)速度不均匀,过快或过慢;焊条(枪)摆动幅度不均匀;焊条(枪)施焊角度选择不当等。
3、防治措施⑴根据不同焊接位置、焊接方法,选择合理的焊接电流参数;⑵增强焊工责任心,焊接速度适合所选的焊接电流,运条(枪)速度均匀,避免忽快忽慢;⑶焊条(枪)摆动幅度不一致,摆动速度合理、均匀;⑷注意保持正确的焊条(枪)角度。
4、治理措施⑴加强焊工操作技能培训,提高焊缝盖面水平;⑵对焊缝进行必要的打磨和补焊;⑶加强焊后检查,发现问题及时处理;⑷技术员的交底中,对焊角角度要求做详细说明。
三、焊缝宽窄差不合格1、现象焊缝边缘不匀直,焊缝宽窄差大于3㎜。
2、原因分析焊条(枪)摆动幅度不一致,部分地方幅度过大,部分地方摆动过小;焊条(枪)角度不合适;焊接位置困难,妨碍焊接人员视线。
常见焊接缺陷及控制

焊接缺陷及防止措施1、外观缺陷:外观缺陷(表面缺陷)是指不用借助于仪器,从工件表面可以发现的缺陷。
常见的外观缺陷有咬边、焊瘤、凹陷及焊接变形等,有时还有表面气孔和表面裂纹。
单面焊的根部未焊透等。
A、咬边是指沿着焊趾,在母材部分形成的凹陷或沟槽, 它是由于电弧将焊缝边缘的母材熔化后没有得到熔敷金属的充分补充所留下的缺口。
产生咬边的主要原因是电弧热量太高,即电流太大,运条速度太小所造成的。
焊条与工件间角度不正确,摆动不合理,电弧过长,焊接次序不合理等都会造成咬边。
直流焊时电弧的磁偏吹也是产生咬边的一个原因。
某些焊接位置(立、横、仰)会加剧咬边。
咬边减小了母材的有效截面积,降低结构的承载能力,同时还会造成应力集中,发展为裂纹源。
矫正操作姿势,选用合理的规范,采用良好的运条方式都会有利于消除咬边。
焊角焊缝时,用交流焊代替直流焊也能有效地防止咬边。
B、焊瘤焊缝中的液态金属流到加热不足未熔化的母材上或从焊缝根部溢出,冷却后形成的未与母材熔合的金属瘤即为焊瘤。
焊接规范过强、焊条熔化过快、焊条质量欠佳(如偏芯),焊接电源特性不稳定及操作姿势不当等都容易带来焊瘤。
在横、立、仰位置更易形成焊瘤。
焊瘤常伴有未熔合、夹渣缺陷,易导致裂纹。
同时,焊瘤改变了焊缝的实际尺寸,会带来应力集中。
管子内部的焊瘤减小了它的内径,可能造成流动物堵塞。
防止焊瘤的措施:使焊缝处于平焊位置,正确选用规范,选用无偏芯焊条,合理操作。
C、凹坑凹坑指焊缝表面或背面局部的低于母材的部分。
凹坑多是由于收弧时焊条(焊丝)未作短时间停留造成的(此时的凹坑称为弧坑),仰立、横焊时,常在焊缝背面根部产生内凹。
凹坑减小了焊缝的有效截面积,弧坑常带有弧坑裂纹和弧坑缩孔。
防止凹坑的措施:选用有电流衰减系统的焊机,尽量选用平焊位置,选用合适的焊接规范,收弧时让焊条在熔池内短时间停留或环形摆动,填满弧坑。
D、未焊满未焊满是指焊缝表面上连续的或断续的沟槽。
填充金属不足是产生未焊满的根本原因。