气体辅助注射成型技术在汽车内饰件上的应用
《气辅成型模具》课件

操作后检查
检查成型件是否符合要求,对不合格 品进行修整或报废处理。
操作注意事项
严格遵守操作规程,确保安全操作, 防止意外事故发生。
模具维护保养方法
01
02
03
日常保养
保持模具表面清洁,定期 检查密封件、气路、电路 等是否正常,对易损件进 行更换。
定期保养
对模具进行全面检查和维 护,清洗或更换冷却水路 ,对损坏部件进行维修或 更换。
05
案例分析
某公司气辅成型模具应用案例
案例概述
某公司在生产过程中面临成型困难的问题,通过引入气辅 成型模具技术,成功解决了问题并提高了生产效率。
技术应用
该公司采用了气辅成型模具技术,通过引入气体来辅助塑 料的成型过程,提高了产品的质量和生产效率。
经验教训
在应用气辅成型模具技术时,该公司遇到了一些技术难题 和挑战,但通过不断尝试和改进,最终成功实现了技术的 稳定应用。
绿色化
采用环保材料和节能技术,降低气辅成型模具的生产能耗和排放,满 足可持续发展要求。
气辅成型模具的市场需求预测
行业应用拓展
随着气辅成型技术的不断成熟, 气辅成型模具在汽车、家电、航 空航天等领域的应用将进一步拓
展。
定制化需求增长
随着个性化消费的兴起,气辅成型 模具的定制化需求将逐渐增长,对 模具的设计和制造能力提出更高要 求。
准备图纸
根据设计要求,制作详细的模 具图纸。
组装与调试
将各部分组装在一起,并进行 初步调试。
抛光与验收
对模具表面进行抛光处理,确 保表面质量,并进行最终验收 。
03
气辅成型模具的使用与维护
模具操作规程
操作前准备
检查气辅成型模具是否完好,确认气 源、电源是否正常,准备好所需材料 。
气体辅助注射成型技术原理及应用

气体辅助注射成型技术原理及应用
气体辅助注射成型技术的应用
● 管状和棒状零件,如门把手、转椅支座、吊 钩、扶手、导轨、衣架等。这是因为,管状结 构设计使现存的厚截面适于产生气体管道,利 用气体的穿透作用形成中空,从而可消除表面 成型缺陷,节省材料并缩短成型周期。
气体辅助注射成型技术原理及应用
在进行模具设计之前,利用MoldFlow MPI 5.0对设计方案进行了模拟。 分析模型如图8所示,在该分析模型中确定了浇口及进气口位置。在模拟中, 设定预注射量为70%,熔体温度为230℃,注射时间为3s,延迟时间为1.5s, 气体压力为20MPa。
气体辅助注射成型技术原理及应用
● 可通过气体的穿透减轻制品重量,节省原材料 用量,并缩短成型周期,提高生产率。
● 该技术可适用于热塑性塑料、一般工程塑料及 其合金以及其他用于注射成型的材料。
气体辅助注射成型技术原理及应用
气体辅助注射成型技术的缺点是:
●需要增加供气和回收装置及气体压力控制单元, 从而增加了设备投资;对注射机的注射量和注射 压力的精度要求有所提高;制品中接触气体的表 面与贴紧模壁的表面会产生不同的光泽;制品质 量对工艺参数更加敏感,增加了对工艺控制的精 度要求。
气体辅助注射成型CAE分析的主要作用是:
1.分析产品的成型工艺性 2.评价模具的设计是否合理 3.优化成型工艺参数 4.预测制品可能出现的缺陷
气体辅助注射成型技术原理及应用
下面以成型把手为例,介绍气体辅助注射成型 CAE分析的过程。
如图7所示的把手材料为ABS,手柄位置壁厚为14mm。由于是外观件,对 其成型要求很高。
气体辅助注塑成型技术
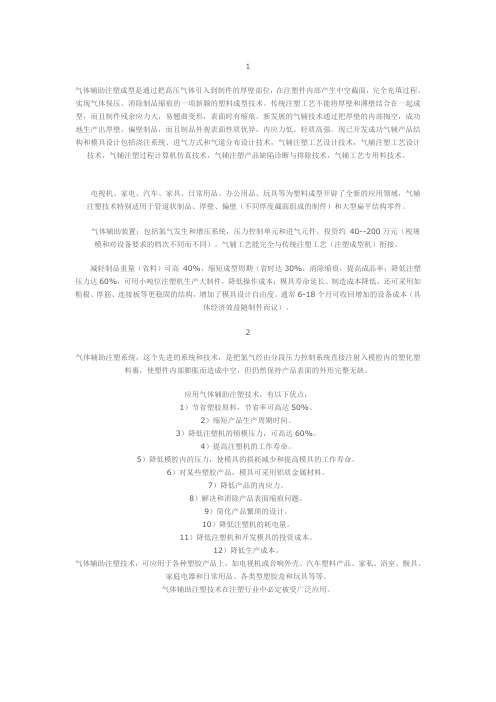
1气体辅助注塑成型是通过把高压气体引入到制件的厚壁部位,在注塑件内部产生中空截面,完全充填过程、实现气体保压、消除制品缩痕的一项新颖的塑料成型技术。
传统注塑工艺不能将厚壁和薄壁结合在一起成型,而且制件残余应力大,易翘曲变形,表面时有缩痕。
新发展的气辅技术通过把厚壁的内部掏空,成功地生产出厚壁、偏壁制品,而且制品外观表面性质优异,内应力低。
轻质高强。
现已开发成功气辅产品结构和模具设计包括浇注系统、进气方式和气道分布设计技术,气辅注塑工艺设计技术,气辅注塑工艺设计技术,气辅注塑过程计算机仿真技术,气辅注塑产品缺陷诊断与排除技术,气辅工艺专用料技术。
电视机、家电、汽车、家具、日常用品、办公用品、玩具等为塑料成型开辟了全新的应用领域,气辅注塑技术特别适用于管道状制品、厚壁、偏壁(不同厚度截面组成的制件)和大型扁平结构零件。
气体辅助装置:包括氮气发生和增压系统,压力控制单元和进气元件。
投资约40--200万元(视规模和对设备要求的档次不同而不同)。
气辅工艺能完全与传统注塑工艺(注塑成型机)衔接。
减轻制品重量(省料)可高40%,缩短成型周期(省时达30%,消除缩痕,提高成品率;降低注塑压力达60%,可用小吨位注塑机生产大制件,降低操作成本;模具寿命延长、制造成本降低,还可采用如粗根、厚筋、连接板等更稳固的结构,增加了模具设计自由度。
通常6-18个月可收回增加的设备成本(具体经济效益随制件而议)。
2气体辅助注塑系统,这个先进的系统和技术,是把氮气经由分段压力控制系统直接注射入模腔内的塑化塑料裹,使塑件内部膨胀而造成中空,但仍然保持产品表面的外形完整无缺。
应用气体辅助注塑技术,有以下优点:1)节省塑胶原料,节省率可高达50%。
2)缩短产品生产周期时间。
3)降低注塑机的锁模压力,可高达60%。
4)提高注塑机的工作寿命。
5)降低模腔内的压力,使模具的损耗减少和提高模具的工作寿命。
6)对某些塑胶产品,模具可采用铝质金属材料。
(完整版)气辅注射成型及设计要点

气辅注射成型及设计要点气辅注射成型GRIM( Gas-Assisted Injection Mold-ing)为一种新型的注射成型工艺,近几年已在国外得到广泛的应用,国内的使用也越来越多。
其原理是利用压力相对低的惰性气体(氮气因为价廉安全又兼具冷却剂的作用而被常用,压力为0.5一300 MPa)代替传统模塑过程中型腔内的部分树脂来保压,以达到制品成型性能更加优良的目的。
1气辅注射成型的优点气辅注射成型克服了传统注射成型和发泡成型的局限性,具有以下优点:1.1制件性能良好 (1)消除气孔和凹陷在制件不同壁厚连接处所设的加强筋和凸台中合理开设气道,欠料注射后气体导入,补偿了因熔体在冷却过程中的收缩,避免气孔和凹陷的产生。
(2)减少内应力和翘曲变形在制件冷却过程中,从气体喷嘴到料流末端形成连续气体通道,无压力损失,各处气压一致,因而降低了残余应力,防止制件翘曲变形。
(3)增加制件的强度制件上中空的加强筋和凸台的设计,使强度重量比比同类实心制件高出大约5,制件的惯性矩工大幅度提高,从而提高制件使用强度。
(4)提高设计的灵活性气辅注射可用来成型壁厚不均的制品,使原来必须分为几个部分单独成型的制品实现一次成型,便于制件的装配。
例如国外一家公司原来生产的以几十个金属零件为主体、形状复杂的汽车门板,通过GAI M技术并采用塑料合金材料实现了一次成型。
1.2 成本低 (1)节约原材料气辅注射成型在制品较厚部位形成空腔,可减少成品重量达10%一50% (2)降低设备费用气辅注射较普通注射成型需要较小的注射压力和锁模力(可节省25%一50%),同时节约能量达30% (3)相对缩短成型周期由于去除了较厚部位芯料,缩短冷却时间可达50%正是基于这些优点,气辅注射适用于成型大型平板状制品如桌面、门、板等;大型柜体如家用电器壳体、电视机壳、办公机械壳体等;结构部件如底座、汽车仪表板、保险杠、汽车大前灯罩等汽车内外饰件。
气辅注塑工艺的应用和工艺过程
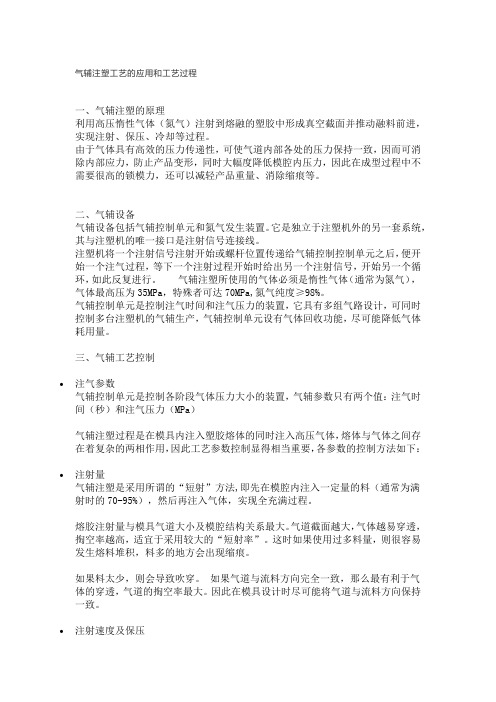
气辅注塑工艺的应用和工艺过程一、气辅注塑的原理利用高压惰性气体(氮气)注射到熔融的塑胶中形成真空截面并推动融料前进,实现注射、保压、冷却等过程。
由于气体具有高效的压力传递性,可使气道内部各处的压力保持一致,因而可消除内部应力,防止产品变形,同时大幅度降低模腔内压力,因此在成型过程中不需要很高的锁模力,还可以减轻产品重量、消除缩痕等。
二、气辅设备气辅设备包括气辅控制单元和氮气发生装置。
它是独立于注塑机外的另一套系统,其与注塑机的唯一接口是注射信号连接线。
注塑机将一个注射信号注射开始或螺杆位置传递给气辅控制控制单元之后,便开始一个注气过程,等下一个注射过程开始时给出另一个注射信号,开始另一个循环,如此反复进行。
气辅注塑所使用的气体必须是惰性气体(通常为氮气),气体最高压为35MPa,特殊者可达70MPa,氮气纯度≥98%。
气辅控制单元是控制注气时间和注气压力的装置,它具有多组气路设计,可同时控制多台注塑机的气辅生产,气辅控制单元设有气体回收功能,尽可能降低气体耗用量。
三、气辅工艺控制•注气参数气辅控制单元是控制各阶段气体压力大小的装置,气辅参数只有两个值:注气时间(秒)和注气压力(MPa)气辅注塑过程是在模具内注入塑胶熔体的同时注入高压气体,熔体与气体之间存在着复杂的两相作用,因此工艺参数控制显得相当重要,各参数的控制方法如下:•注射量气辅注塑是采用所谓的“短射”方法,即先在模腔内注入一定量的料(通常为满射时的70-95%),然后再注入气体,实现全充满过程。
熔胶注射量与模具气道大小及模腔结构关系最大。
气道截面越大,气体越易穿透,掏空率越高,适宜于采用较大的“短射率”。
这时如果使用过多料量,则很容易发生熔料堆积,料多的地方会出现缩痕。
如果料太少,则会导致吹穿。
如果气道与流料方向完全一致,那么最有利于气体的穿透,气道的掏空率最大。
因此在模具设计时尽可能将气道与流料方向保持一致。
•注射速度及保压在保证制品表现不出现缺陷的情况下,尽可能使用较高的注射速度,使熔料尽快充填模腔,这时熔料温度仍保持较高,有利于气体的穿透及充模。
氮气辅助成型技术讲义
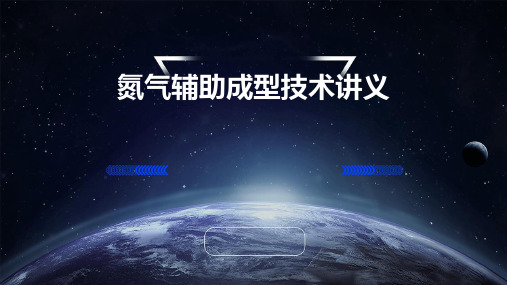
能够缩短成型周期,提高生产效率。
氮气辅助成型技术的优势与局限性
• 低成本:能够降低原材料和能源消耗,降 低生产成本。
氮气辅助成型技术的优势与局限性
技术门槛高
需要专业的技术人员和设备,增加技 术难度和成本。
应用范围有限
目前主要应用于塑料制品的成型,对 于其他材料的成型仍需进一步研究。
02
氮气辅助成型技术的基本原理
防止氧化
在高温成型过程中,氮气可以替代空气中的氧气, 避免产品氧化和烧焦。
降低成型温度
由于氮气的热导率较低,可以降低成型温度,减 少能源消耗。
氮气辅助成型技术的工艺流程
注入氮气
在模具型腔内注入 高纯度氮气,确保 气体分布均匀。
冷却和脱模
将模具冷却至适当 温度,然后打开模 具取出成型产品。
准备材料
根据产品需求准备 合适的材料和模具。
氮气的性质与特点
01
氮气是一种无色、无味、无毒的 气体,在标准条件下密度约为 1.25kg/m^3,大约是空气的 78%。
02
氮气的化学性质相对稳定,不 易与其他物质发生化学反应。
03
氮气的热导率低,具有良好的 隔热性能。
氮气在成型过程中的作用
保护环境
氮气辅助成型技术可以减少生产过程中的有害气 体排放,降低对环境的污染。
时间控制
合理安排成型时间,确保材料完全固化,提高产品性能和稳定性。
04
氮气辅助成型技术的应用案例
汽车制造业的应用
总结词
氮气辅助成型技术在汽车制造业中广泛应用于制造复杂零部件,如保险杠、仪表 盘和座椅骨架等。
详细描述
通过氮气辅助成型技术,汽车零部件能够以较低的成本和较短的生产周期实现高 质量、高强度和复杂形状的成型。该技术有助于提高汽车的安全性能和外观质量 ,同时降低生产成本和减少废料。
内饰塑料件工艺方法介绍

内饰塑料件工艺方法介绍汽车内饰塑料件成型方法主要有以下7种:1)注射成型注射成型简称注塑,是指物料在注射机加热料筒中塑化后,由螺杆或注塞注射入闭合模具的模腔中经过冷却形成制品的成型方法。
它广泛用于热塑性塑料的成型,也用于某些热固性塑料(如酚醛塑料、氨基塑料)的成型。
注射成型的优点是能一次成型外观复杂、尺寸精确、带有金属或非金属嵌件、甚至可充以气体形成空芯结构的塑料模制品;生产效率高,自动化程度高。
新型注射方法的出现更加巩固了其在汽车塑料加工中的地位。
各种车上的硬质仪表板一般采用PP、PC、ABS、ABS/PC等一次性注射成型。
就注射技术而言,已经开发了适应性很广的很多新技术。
如采用微型注射成型自动化生产毫克级的高尺寸精度制品,如汽车传感器等自动控制和电子控制部件。
注射成型细分,还可以分成以下几类。
(1)气体辅助注射成型。
气体辅助注射成型技术是一项新兴的塑料注射成型技术,其原理是利用高压气体在塑件内部产生中空截面,利用气体保压代替塑料注射保压,消除制品缩痕完成注射成型过程。
传统注射工艺不能将厚壁和薄壁结合在一起成型,且制件残余应力大,易翘曲变形,表面有缩痕。
新发展的气辅技术通过把厚壁的内部掏空,成功地生产出厚壁不均制品,而且制品外观表面性质优异,内应力低,轻质高强。
该工艺已用于成型汽车的前后挡板、门把手、保险杠等。
(2)水辅注射成型。
同气辅注射成型类似,水辅助注射成型先将一段熔体注入模腔,随后将水注入,通过挤破使工件成型,填充过程结束后,水可以继续提供保压压力,预防翘曲,水辅助注射成型可以直接冷却制品的内部,更适合较厚和较长的制品成型,能生产出均匀的薄壁制品,零件内表面平滑。
可以在更短的成型周期下,减少制品壁厚及减少残留的壁厚,对于大件且较薄的制品可使用较均匀而且较低的压力即可成型,从而节省了材料,拓展了应用范围循环使用水而可降低生产成本,适合成型管状的零件、汽车油管和其他流体系统、把手、行李架、汽车上的仪表板、缓冲器、门把手、离合器以及驾驶杆支持架等。
气体辅助注塑工艺简介

气体辅助注塑工艺简介1.气体辅助注塑目前所指的气体辅助注塑:是指将氮气注射入产品内,使产品内部形成中空。
模具打开前,控制器会将塑胶工件内的氮气释放回大气中。
2.气辅注塑成形工艺的优势1)低射胶、低锁模力;2)压力分布均匀、收缩均匀、残余应力低、不易翘曲,尺寸稳定;3)消除凹陷,型面再现性高;4)省塑料,可用强度及价格更低的塑料;5)可用强度和价格更低的模具金属;6)厚薄件一体成型,减少模具及装配线数目;7)可用较厚的筋,角板等补强件,提高制品刚性,使得制件公称厚度得以变薄。
8)增强设计自由度。
3.气辅射胶控制工艺1)短射工艺,即胶料未完全充满型腔时,继之以氮气注射;2)满射工艺,塑胶熔体充满型腔之后,停止注射,继之以氮气注射。
短射工艺的特点:在气辅注塑中,塑胶注射取决于胶件形状及胶料性能,在以下条件才可进行短射。
1)胶件必须有独立完整的气体通道,即气流在穿透胶件时,无分支气道可走。
2)气体通道中多余胶料有足够的溢流空间。
3)胶料流动性优良,粘度不可太低,尽量避免使用含破坏高分子键的填充物的胶料。
4)胶料导热度较低,有可较长时间保持熔融状态的能力。
满射工艺特点:胶件射胶完成,通过气体代替啤机,防止胶件收缩。
其优点在于,啤机保压是以射胶量及压力来防止胶件收缩,气辅保压,则以气体穿透塑胶收缩后的空间,防止胶件表层埸陷。
4.气辅压力分析:现我们看以下气辅压力与啤机压力的对比:1)气辅压力a)低气压800psi=56.34kg/cm2b)中气压1500psi=105.63 kg/cm2c)高气压2500psi=176.06kg/cm22)啤机压力a)100 TON注塑最大压力188Mpa=1917 kg/cm2b)280 TON注塑最大压力150Mpa=1530 kg/cm2c)650TON注塑最大压力153Mpa=1560 kg/cm2从以上压力对比可知,氮气压力只相当于普通啤机注塑压力的十分之一,甚至更少。
气辅注塑

1)封闭式气体注射(SEALED INJECTION GAS)方法: * 是把气体直接注入模腔内,使塑料成品中空的方法。无需采用活阀,只是 通过简单模具加工,把气辅气嘴装在模具中。 * 在同一模具上,可有单一或多个注入气体的地方,这视乎同产品的需要, 慕求令产品有良好效果和提供产品设计有较大的灵活性。
太小会使气体流动失去控制 7.冷却要尽量均匀,内外壁温差要尽量小
8.在流道上放置合理流道半径的截流块,辅助注塑设备按工艺需求大致应有以下几类: 1、氮气机:主要用于氮气的制造 2、氮气增压器:主要是将氮气的气压加大,以便于氮气的注入 3、气辅控制器:主要用于控制氮气注入量、气压、时间及排气的控制,是
• 降低生产成本
– 由于减少了壁厚,因此降低了零件成品的总重量. – 由于壁厚较小,因此缩短了冷却时间和循环时间. – 由于降低了锁模力和注塑保压压力,能源消耗成本降低. – 由于零件的集成化,从而降低了装配成本.
• 降低投资成本
– 由于注射压力较低,因此可以降低注塑机的锁模压力,可使用吨位较小的注塑 机.
整个气辅设备的控制中心 4、气辅配件:主要有气针、气管及各种接头等,用于气辅设备与模具的连
接
因各种设备加在一起,占用的空间较大,现有很大一部分已采用一体化的气 辅系统。
END
同传统注射成型工艺相比.应用气体辅助注塑技术,有以下优点:
• 自由设计
– 综合功能较为复杂的塑胶零件可以整装为单一的组件. – 可以在同一零件上结合厚壁和薄壁部分. – 使用空心的"加强筋"部分可以提高其强度.
• 提高零件质量
– 由于减小了微收缩,因此扭曲和变形就减少了. – 消除缩痕. – 由于注射点的数量减少,所以波纹和熔接线也相应减少.
浅谈嵌件注塑技术及其自动化生产在汽车内饰零件中的发展趋势

不同材质各有的特性可以在同一个产品 上充分结合并展现;
不同材质的物理性能优势能够满足一些 新产品设计的特殊性能需求;
缩短产品制造生产工序,避免大量的且 复杂的装配作业;
相对于几道直接装配生产模式,嵌件注 塑使得复合产品的可靠性更加高;
2 嵌件注塑工艺的嵌入方式
纯人工放置:人工放置模式局限性较大, 不适合大型吨位注塑机(一般超过 350 吨以 上),仅限一些简单且结构较小的嵌件产品 生产,生产效率相对较低,且安全性不足,
AUTO TIME 123
Copyright©博看网 . All Rights Reserved.
AUTO PARTS | 汽车零部件
图2
开始 start
顶杆 / 抽芯返回 ejector&core back
放置嵌件在模具内 put insert in the mould
合模 clamp close
注射 injection
保压 hold
取件 take out
顶出 / 抽芯 ejector&core out
开模 clamp open
冷却 cooling
朔化 / 计量 charge
复循环。 为了实现上述术细节问题需特 别关注 ;
(1)机械抓手设计复杂性:由于嵌件注 塑工艺相对传统注塑工艺增加了一步嵌件放 置环节,对于机械抓手的设计需要兼备嵌件 以及注塑成品取件的两个部分,注塑成品的 取件部分,设计与应用已非常成熟,没什么 特殊,一般都是吸盘吸取,夹具夹取或两者 结合形式为主;其复杂性在于嵌件部分,由于 嵌物有些是单一材料简单构造(见图 3),也 有些是多种材质复合型的复杂构造(见图 4)。
为了确保嵌物放入模具型腔时就能精确 放置,在抓取时就需要精确抓取定位,故导 向,限位与感应判断是该部分必不可少的三 大设计要素,之前做过的一个实例项目,其 嵌件抓取要求特别高,主要分成了两块细节, 一是应用插片机构来定位气囊门总成中网布 折叠槽,保证该产品结构功能性(气囊爆破 时网布该折叠部分拉住气囊门总成),二是 应用了三个直径 10mm 的吸盘来真空吸附金 属螺钉,在此项目开发初期,最不稳定的就 是插片机构,由于插片机构是由齿牙排布而 成,开发初期经常性的出现部分齿牙未插入, 或者齿牙插入后又松开,或者齿牙偏移角度 过大将网布冲破等等异常情况,也是通过不 断的调整,优化设计构造,固化设计数据, 将所有齿牙的宽度,长度,间隔及偏移角度 等等要素都完全与网布折叠槽匹配好,最终 确定了最优方案,实现了稳定且精确的连续 抓取要求。
注塑气辅技术指南

气体辅助注塑成型是从传统的注射成型发展而来的。它的工作原理是将高压氮气通过注塑喷嘴或气针射至模腔内。射入的气体会产生气泡,这个气泡将推动熔体塑料进入模具的末端从而产生中空截面。
气辅成型有很多工艺和设计特点,这些工艺和设计特点有助于满足应用要求。一些潜在的特性和优点如下:
Extend Design Guidelines
Troubleshooting
过程控制
厚壁形成
厚壁的控制
速度对厚壁的影响
零件的连贯性
厚壁和气体渗入的相互作用
发现并修理故障
About Gas Assist Injection Molding
Gas assist injection molding is a variation of conventional injection molding that can be easily retrofitted to an existing injection press by the addition of an auxiliary gas unit. The usual injection of molten plastic is assisted by the introduction of pressurized gas (usually nitrogen) into the mold. The gas produces a bubble which pushes the plasticinto the extremities of the mold creating hollow sections as the bubble propagates.
-增加结构件的强度/坚固度对质量的比值,
- Molding large cross-sections (parts consolidation)
汽车内饰件注塑工艺

汽车内饰件注塑工艺汽车内饰件注塑工艺是指通过注塑机将熔融的塑料注入到模具中,经过冷却凝固后得到汽车内饰件的生产过程。
注塑工艺在汽车内饰件的生产中具有重要的作用,它能够高效、快速地生产出具有一定强度和表面质量要求的内饰件,满足汽车外观和内部舒适性的需求。
汽车内饰件注塑工艺的主要流程包括原料选型、配料、塑料熔融、注射成型和冷却凝固等环节。
首先,根据汽车内饰件的要求选择合适的塑料材料,如聚丙烯(PP)、聚氯乙烯(PVC)等。
然后,通过精确的计量和搅拌,将原料进行配料,以保证塑料材料的质量和稳定性。
接下来,将配好的塑料颗粒放入注塑机的料斗中,经过加热和熔化,使塑料变为可流动的熔融状态。
熔化好的塑料通过注射机的射嘴和喷嘴系统,经过高压注射进入模具的腔内。
模具是根据内饰件的形状和要求设计制造的,它有一个或多个腔,可以同时生产多个内饰件。
注塑过程中,塑料在模具腔中经过冷却凝固,形成所需的饰件形状。
注塑机通过温度控制和冷却系统,可以控制塑料的冷却速度,从而控制内饰件的周期时间和质量。
冷却凝固完成后,模具打开,取出成品内饰件,并进行后续的修整和加工,如去除余料、修边、打磨、安装等。
在汽车内饰件注塑工艺中,有一些关键的技术要点需要注意。
首先,注塑机的选择和调试非常重要,需要考虑到内饰件的尺寸、形状和材料特性等因素。
其次,模具的设计和制造也是关键,需要考虑到内饰件的复杂程度、模具的开合力和冷却系统等因素。
此外,注塑过程中的温控系统、压力控制和速度控制等也需要精确调整,以保证内饰件的质量和稳定性。
总体来说,汽车内饰件注塑工艺是一种高效、精确、稳定的生产工艺,它能够满足汽车内饰件在强度、表面质量和装配性等方面的要求。
随着汽车工业的发展和消费者对内饰品质的要求不断提高,注塑工艺将在汽车内饰件生产中发挥越来越重要的作用。
气辅注塑 气道设计
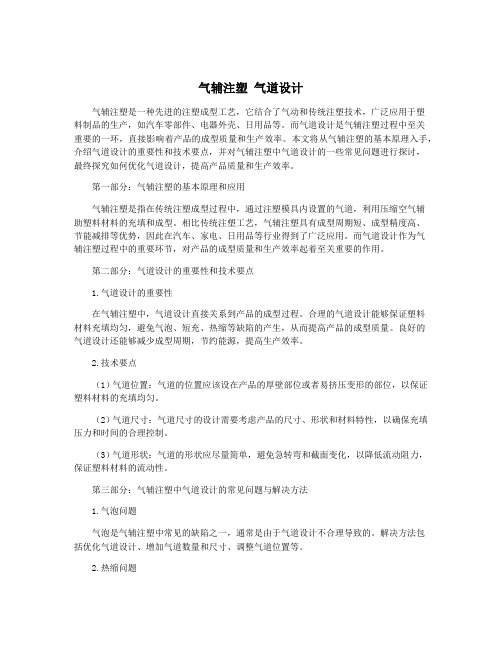
气辅注塑气道设计气辅注塑是一种先进的注塑成型工艺,它结合了气动和传统注塑技术,广泛应用于塑料制品的生产,如汽车零部件、电器外壳、日用品等。
而气道设计是气辅注塑过程中至关重要的一环,直接影响着产品的成型质量和生产效率。
本文将从气辅注塑的基本原理入手,介绍气道设计的重要性和技术要点,并对气辅注塑中气道设计的一些常见问题进行探讨,最终探究如何优化气道设计,提高产品质量和生产效率。
第一部分:气辅注塑的基本原理和应用气辅注塑是指在传统注塑成型过程中,通过注塑模具内设置的气道,利用压缩空气辅助塑料材料的充填和成型。
相比传统注塑工艺,气辅注塑具有成型周期短、成型精度高、节能减排等优势,因此在汽车、家电、日用品等行业得到了广泛应用。
而气道设计作为气辅注塑过程中的重要环节,对产品的成型质量和生产效率起着至关重要的作用。
第二部分:气道设计的重要性和技术要点1.气道设计的重要性在气辅注塑中,气道设计直接关系到产品的成型过程。
合理的气道设计能够保证塑料材料充填均匀,避免气泡、短充、热缩等缺陷的产生,从而提高产品的成型质量。
良好的气道设计还能够减少成型周期,节约能源,提高生产效率。
2.技术要点(1)气道位置:气道的位置应该设在产品的厚壁部位或者易挤压变形的部位,以保证塑料材料的充填均匀。
(2)气道尺寸:气道尺寸的设计需要考虑产品的尺寸、形状和材料特性,以确保充填压力和时间的合理控制。
(3)气道形状:气道的形状应尽量简单,避免急转弯和截面变化,以降低流动阻力,保证塑料材料的流动性。
第三部分:气辅注塑中气道设计的常见问题与解决方法1.气泡问题气泡是气辅注塑中常见的缺陷之一,通常是由于气道设计不合理导致的。
解决方法包括优化气道设计、增加气道数量和尺寸、调整气道位置等。
2.热缩问题热缩是指产品在冷却后出现收缩不均匀的现象,通常是由于气道位置不当或尺寸设计不合理引起的。
解决方法包括优化气道位置、增加气道数量、调整气道尺寸等。
3.短充问题短充是指产品某一部位塑料材料未充填完全的现象,常常与气道设计不当有关。
汽车内饰件气辅注塑工艺模拟分析

汽车内饰件气辅注塑工艺模拟分析摘要:在分析制件结构及其工艺的基础上,简述了模型前的处理,从确定浇口及进气口位置和气辅注射工艺模拟分析两个方面进行了注塑模拟分析,在实验验证中获得了与模拟分析一致的结果。
关键词:moldflow;气辅注射成型;模拟分析;工艺参数;汽车内饰件作为一种新型的塑料加工技术,气体辅助注射成型( gas-assisted injection molding,简称gaim)可以有效的提高产品的精度和解决产品的变形问题,从而达到减少塑料材料的使用和模具设计周期缩短的目的。
气辅成型技术的使用范围非常的广泛,从汽车内饰件到大型家具、家电外壳和手柄等都可见该种技术的应用。
本文以汽车内饰件为例,在moldflow的mpi/gaim的帮助下模拟分析了气体辅助注射。
一、制件结构和工艺分析图1为零件结构的三维模型图,采用基本壁厚为25毫米的改性pp作为零件的材料,在截面的设计上,选择了壁厚可达20毫米的三角形形状。
由于普通注射工艺的缺陷造成必须采用可以适应该零件的壁厚和形状结构的复杂的气辅注射成型工艺成型。
二、模型前处理就目前而言,moldflow的mpi/gaim分析模块支持的是3d网格和midplane网络。
另者,基于零件复杂的结构和提取困难的中性面考虑,在本文中使用了3d网格来对零件进行划分。
3d网格有着非常明显的优势,其设计出的模型质量高。
自动设置气道、分析精度高。
但是3d网格操作繁琐,处理复杂麻烦,且对计算机的性能要求特别高。
图2为局部3d网格划分图。
三、注塑模拟分析1.确定浇口及进气口位置基于对最佳浇口位置、零件结构、气辅注射工艺等考虑,选定了图3中所示的a、b两个为,选定c点作为气体注射点。
2.气辅注射工艺模拟分析选定50℃作为模具温度,选定230℃作为熔体温度,采取欠料注射方式,零件末端开设溢料槽以确保厚壁气体的溢出。
(1)对方案1模拟结果的分析将a选定为浇口的位置,在浇口的60毫米左右的地方设定为进气口,在气体最大气压为6mpa的情况下将欠料注射进去,溢料槽选定的尺寸为边长等于40毫米的正方体。
气体辅助注塑成型技术简介.
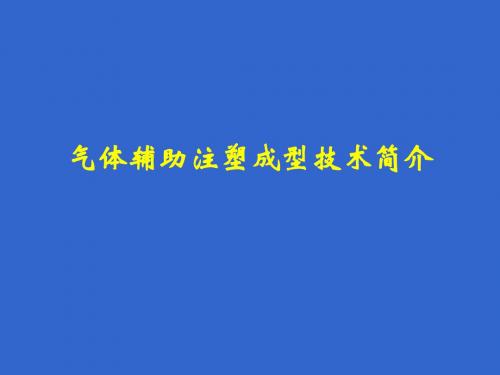
四、气体辅助注塑整系统的原理图:
A、整套系统
氮气 发生 器
低压 贮气缸
电动 高压 增压机
高压 贮气缸
气辅 主控 制器
单相电源 压缩空气 三相电源
模具的工作寿命; 7、降低注塑机的锁模压力,可高达50%; 8、提高注塑机的工作寿命和降低耗电量。
三、气体辅助注塑技术的应用:
基本上所有用于注塑的热塑性塑料及一般的工程材料 (如PS、HIPS、PP、ABS…)都适用于气辅技术。
目前气辅技术广泛应用于各类塑胶产品上,例如:电视 机、电冰箱、空调或音响外壳、汽车塑料产品、家电、日用 品、玩具等。
B、简易系统
氮气 缸瓶
气动 高压 增压机
压缩空气
单相电源
高压 贮气缸
气辅 主控 制器
单相电源
模具 模具
五、气体辅助注塑周期简介:
1、注塑期——以定量塑化塑料充填入模腔内。所需塑料 份量要通过试验找出来,以保证在充氮期间,气体不 会把成品表面冲破及能有一理想的充氮体积。
2、充气期——注塑期中或后,不同时间注入气体,气体 注入的压力必需大于注塑压力,以达至产品成中空状 态。
气体辅助注塑成型技术简介
一、气体辅助注塑原理:
气体辅助注塑原理是把高压氮气经气辅 主控制器(分段压力控制系统)直接注射入 模腔内塑化塑料里,使塑件内部膨胀而造成 真空,但仍然保持产品表面的外形完整无缺, 减小产品表面的收缩、产品变形和翘曲,从 而达到提高产品的质量,降低成本的目的。
二、采用气体辅助注塑技术的优点:
汽车机械制造中的零部件注塑技术

汽车机械制造中的零部件注塑技术在汽车机械制造领域中,零部件的注塑技术扮演着重要的角色。
注塑技术广泛应用于汽车行业中的各个环节,从内饰件到外饰件,从发动机零部件到车灯,都离不开注塑技术的支撑。
本文将对汽车机械制造中的零部件注塑技术进行探讨。
1. 汽车行业对注塑技术的需求随着汽车产业的迅速发展,对于零部件的要求也越来越高。
注塑技术作为一种高效、精确、经济的生产技术,能够满足汽车行业对于零部件质量、外观和成本的要求。
注塑技术的应用不仅可以提高零部件的生产效率,还能够保证零部件的一致性和可靠性。
2. 注塑技术在汽车零部件制造中的应用案例2.1 内饰件汽车的内饰件通常由塑料制成,注塑技术能够灵活地塑造各种形状和纹理,从而满足汽车制造商对于内饰件设计的需求。
通过注塑技术,可以生产出具有高强度、轻质、耐磨损等特点的内饰件,提升汽车的舒适性和安全性。
2.2 外饰件汽车的外饰件需要具备一定的刚度和耐候性,在注塑技术的帮助下,可以生产出具有复杂形状和精细纹理的外饰件。
注塑技术还能够实现多色注塑,使得汽车外饰件更加丰富多样,提升整车的吸引力和市场竞争力。
2.3 发动机零部件发动机零部件对于汽车的性能和可靠性至关重要。
注塑技术可以生产出具有高温耐受性和化学稳定性的塑料零部件,用于发动机的密封、冷却和隔热等功能。
同时,注塑技术也能够满足发动机零部件在形状、尺寸和精度上的要求。
2.4 车灯车灯是汽车的重要安全设备之一,而注塑技术为车灯的制造提供了便利。
注塑技术可以生产出具有高透明度和耐磨抗刮性的塑料材料,用于车灯的灯罩和透镜。
此外,注塑技术还可以实现车灯的复杂结构和多种颜色的注塑,提升车灯的照明效果和辨识度。
3. 注塑技术在汽车机械制造中的挑战与发展趋势随着汽车制造技术的不断进步,注塑技术也面临着挑战和发展的机遇。
其中,注塑材料的研发与应用、注塑模具的设计与制造、注塑工艺的优化与控制等方面是当前亟需解决的问题。
同时,注塑技术也面临着节能减排和环境友好的要求,例如研发可降解塑料材料和优化注塑工艺,以减少废料产生和资源浪费。
气体辅助注塑成型简介
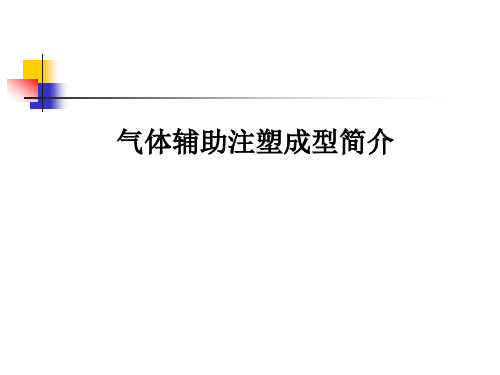
1.什么是气体辅助注射成型?
气体辅助注塑成型其原理是利用高压气体在塑件内部产生中空截面,利用 气体保压代替塑料注射保压,消除制品缩痕,完成注射成型过程。 气体辅助注塑成型的工艺过程主要包括塑料熔体注射、气体注射、气体保 压三个阶段。气体辅助注射成型过程首先是向模腔内进行树脂的欠料注射,然后 把经过高压压缩的氮气导入熔融物料当中,气体沿着阻力最小方向流向制品的低 压和高温区域。当气体在制品中流动时,它通过置换熔融物料而掏空厚壁截面。 这些置换出来的物料充填制品的其余部分。当填充过程完成以后,由气体继续提 供保压压相比,气体辅助注塑成型有更多的工艺参数需要确 定和控制,因而对于制品设计、模具设计和成型过程的控制都有特殊的要求。
5. 气辅成型常见问题及对策
⑹气道与薄壁连接处缩凹 气道由于气体穿透,导致气道与薄壁接触部分壁厚较大,解决方法: 1.在气道与薄壁接触位置增设防缩槽 2.气道与薄壁连接处尽量不采用圆角过渡 3.尽量增大气道表面积,以利于迅速冷却 ⑺气体穿透不均 原因: 1.熔体流动不平衡 2.气道布局不合理 3.模具精度差,导致塑件壁厚不均 解决方法: 1.修改浇口布局 2.修改气道布局 3.提高模具制造精度
2.气体辅助注射成型有什么优点?
(1)解决制件表面缩痕问题,能够大大提高制件的表面质量。 (2)局部加气道增厚可增加制件的强度和尺寸稳定性,并降低制品内应力,减 少翘曲变形。 (3)节约原材料,最大可达40%~50%。
(4)简化制品和模具设计,降低模具加工难度。
(5)降低模腔压力,减小锁模力,延长模具寿命。 (6)冷却加快,生产周期缩短。
5. 气辅成型常见问题及对策
⑴制件表面银纹(streak) 浇口处料流速度过快,剪切速率过大 修改浇口类型,或者增大浇口尺寸,减小料流速度
气体辅助注塑工艺简析
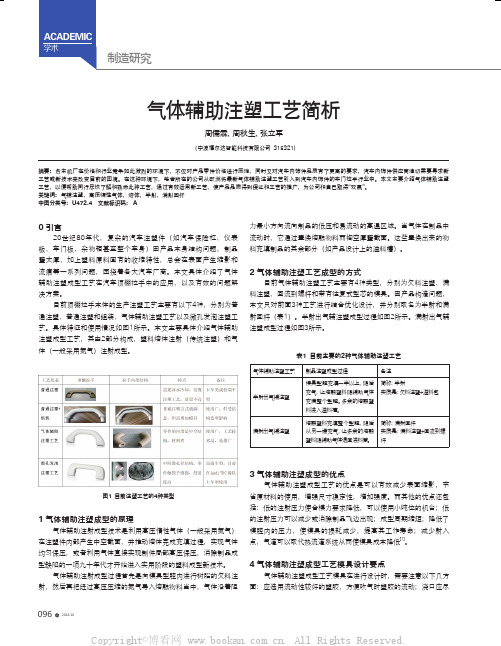
图3 满射出气辅注塑成型过程
6 结束语
国外从上世纪90年代起,将气辅技术陆续应用于汽车、彩 电、飞机及日用品等诸多领域。目前,美国和日本的汽车注塑件, 已有80%采用气辅注塑成型,日本电视机行业64 cm以上的大屏幕 彩电机壳,90%以上采用气辅注塑成型。然而此技术在我国起步较 晚,基础较差,但放眼未来,该技术在注塑行业中的应用必将越来 越广泛,有急迫的市场需求与重要的技术经济意义。
(3)通过对原材料本身的光泽控制。 5.3 其他方面的运用
在汽车配件方面使用气辅注塑方式,除了在顶棚拉手结构运用广 泛,同时在部分零件上也可以通过气辅结构方式,来改善或解决部分 零件本身设计问题引起的臂厚缩影问题。在零件臂厚位置增加气辅工 艺的气针,利用在注塑过程中增加吹气来解决臂厚造成的缩影,有效 降低零件成型要求工艺,比如门内拉手等。与普通的注塑成型相比, 气体辅助注塑技术还有很多无可比拟的优点,它不仅仅可以降低塑料 制品的制造成本,还可以提高零件本身的强度等性能。
5 部分案例的问题探讨 5.1 熔接线/痕
熔接线/痕是注塑成型(原理)工艺形成的溶接痕。其形成的原因 是,由于进料端的温度可以保持不变,但是另一端以及早期进入的 塑料,因温差问题出现冷却,导致不能充分与新进入的塑料进行有 效混合,从而引起熔接线/痕。目前对于熔接线/痕,只能尽量缩少 而不能完全消去(图4)。
4 气体辅助注塑成型工艺模具设计要点
气体辅助注塑成型工艺模具在进行设计时,需要注意以下几方 面:应选用流动性较好的塑胶,方便吹气时塑胶的流动;浇口应尽
096 2018.10
Copyright©博看网 . All Rights Reserved.
量选在产品的端部;半射出注塑成型方式吹气口,应选在靠近浇口 的地方;如是一模多件,必须保证一件一条进气孔设计;吹气口必 须在模具的下方,以防止因重力作用胶料堆积于模具下方,而造成 胶厚不均匀;气辅模要求模温较高,一般都采用热流道,以及在动 定模镶件时用热油加热,如果产品太长,还需要在动定模镶件时添 加发热棒进行加热;气辅模流道和溢料槽的形状一般做成梯形。
- 1、下载文档前请自行甄别文档内容的完整性,平台不提供额外的编辑、内容补充、找答案等附加服务。
- 2、"仅部分预览"的文档,不可在线预览部分如存在完整性等问题,可反馈申请退款(可完整预览的文档不适用该条件!)。
- 3、如文档侵犯您的权益,请联系客服反馈,我们会尽快为您处理(人工客服工作时间:9:00-18:30)。
图8产品滥料井
5结束语 采用气辅成型技术的关键在于气道设计、进气
位置设定、氮气开始注入时刻以及氮气注射压力的
万方数据
模具工业2009年第35卷第12期
局部薄壁透光塑件随形热冷注射模
伍晓宇1,程 蓉1。梁 雄‘.李积彬1。孙成红2.黄 山2’杨文海3 (1.深圳大学机电与控制工程学院。广东深圳51∞60:
收稿日期:2ID∞一∞一100 作者简介:欧荔苹(19∞一),男,湖南永州人,工程师,从事模具 设计工作.地址:广东省增城市中新镇中福北路3号广州市中新 塑料有限公司研发中心.(电话)0∞一82黼63眩转872l,(电子信
箱)ld@出∞o凼IpIa菇c.锄.口lo
作用。另1种为有溢料井的成型方式。采用溢流井来 吸收被气体代替的熔体。
中图分类号:贼.669 关键词:气体辅助注射;汽车尾门饰件;优化设计 文献标识码:B 文章编号:1001—2168(加09)12—0042一05
量。
品翘曲量略有减小。
昌 E \
嘲 鲁 霸 K 皤
图6延迟时间对制品最大翘曲量的影响
4结束语 (1)按照1硇】chi试验设计方法设计了L,g(37)
试验矩阵.通过信噪比来衡量制品在各因素取值水
采用气辅成型技术生产的产品气道结构如图5 和图6所示,产品流道如图7所示。产品溢料井之一 如图8所示。
图5气道横向结构
图6气遭纵向结构
图7产品流道
往射 延迟 洼 ’(
气体保压 捧气,取件
j,
/\
0
了.I
丁2丁'
丁4
Hale Waihona Puke 丁,时问/r图4压力一时间曲线
图4中,丁。时刻为注射终止时间点,丁广n为 气体注射延迟时间。T2 ̄T,为注气时间,T3 ̄T。为
腔的随形介质通道.而且需要在其背面近距离位置增加隔热层.从而实现沿模具型腔表面均匀传热.减
少模具传热体积。并在动模一侧增加局部调温槽以加速塑件薄壁以下内部结构的冷却.以克服凹陷的
RDce爨i唱Tecb∞k舒,2005,169:314-319.
【7】左敏.刘浩。杨伟.等.气体控制参数对气体辅助
成型产品翘曲的影响【J】.中国塑料,2002,16(2):5㈣.
万方数据
在装卸搬运时有其特点及方法: 物流装卸搬运的概念:物流装卸搬运 是指在一定的区域内(通常指某一个物流 结点,如车站、码头、仓库等,以改变物 品的存放状态和位置为主要内容的活动。 它是伴随输送和保管而产生的物流活动, 是对运输、保管、包装、流通加工、配送 等物流活动进行衔接的中间环节。 在整个物流活动中,如果强调存放状 态的改变时,一般用“装卸”一词表示;如 果强调空间位置改变时,常用“搬运”一词 表示。物流的各环节和同一环节不同活动 之间,都必须进行装卸搬运作业。所以杭 州搬家公司就是来完成其作业的。正是装 卸搬运活动把物流运动的各个阶段联结起 来,成为连续的流动过程。
d面t晒∞al R崛耵蚓be陪∞warp略e d dl岫sheU plastic
s呶如挺日ated 阳rt
RsIb瞪宅鼠也ceⅡ蟹d10d缸d孽netic
蛔dIIl【J】.1懈m汹I(bm衄Ⅱli∞6口B.m Heat ard
Mbs ma璐f矗,20Q5,32:10吕孓1094.
【o6】pcⅪ蛐贼dR削H,卿(B.职刁聪MUT.帆 a bus∞il魄咖base嘲删呶 础m池l and髓mtic a喀触n【J】..『a哪l d M拍五aIs
moldiflg;au咖吐v℃陀ar朗te 窃3电豁isted illjec石on mo^dir喀tecllI的lo秽reduoed me wa印a的and iITI邮ved the s眦白∞q∞U锣.
1河wor凼:髓s电鸽妇ted iIl;ec的n
iIlterio疆;optimi翻bon
l引言 气体辅助注射成型技术(Ga争A鼙豳ed hljec岫1
1 ,_。-、广_
——
{酾涵
I
删: 蚴趔 皿
11
9
.
IQ
I
II
(d)动模结构
4I
蚴 蚴 ’_r—I’ 一1 r11一
\
、
,
一
F
幂 藉 ≮ 罗 T TrT 1
咖 卅j
£ 姒 一-
]fffI|
F 叫
l Ⅲ
◎
◎
图3模具结构 1.氮气进气管2.气针3.牛角型浇口4.尾门左饰件5.定模板6.主流道7.尾门右饰件8.气 针9.氮气进气管 10.动模板 11.主流道封气液压缸12.溢料井封气液压缸13.冷却水管 14.尾 门右饰件溢料并15.尾门右饰件溢料井16.尾门左饰件溢料井17.尾门左饰件溢料井
M)Id魄.G姐讧以下简称气辅成型技术)从20世纪 90年代开始在美、日、欧等发达国家和地区得到了 广泛应用。目前该技术主要被应用在家电、汽车零 部件、日常用品、办公用品等领域nlo
气辅成型技术的工艺过程如图l所示.先向模
具型腔中注入塑料熔体.再向塑料熔体中注入压缩 氮气,塑料借助氮气的推动作用充填到模具型腔的 各个部分,使塑件最后形成中空断面而保持完整外 形。待制品冷却后先排出氮气,然后打开模具取出制 品。与普通注射成型相比,气辅成型技术整个过程 多—个气体注射阶段,且制品在模具中通过气体保 压。而不是注射压力保压。
万方数据
模具工业2009年第35卷第12期
45
4产品成型工艺过程 气辅成型工艺过程有:塑料注射过程;气体注
射过程。具体过程如下: 塑料开始注射前,液压缸12(共4个)关闭溢料
井流道,而液压缸1l处于初始位置,分流道处于打 开状态。熔融塑料通过主流道6和牛角型浇口3注 满模具型腔。延迟一定时间后,液压缸11前进。连接 在液压缸11上的销关闭分流道,同时液压缸12(共 4个)后退。打开溢料井流道,接着通过氮气进气管 1、氮气进气管9通入压缩氮气,气针2和气针8在 氮气压力作用下打开,这时气体进入分流道,氮气 入口位置在产品分流道上,如图3(a)所示。由于产 品较厚部位的中心区域冷却速度较慢,塑料温度较 高,流动性较好,压缩氮气推动分流道和牛角型浇 口中心区域的高温塑料进入左、右饰件,进而推动 左、右饰件气道中心区域的塑料流入尾门左饰件溢 料井17、尾门左饰件溢料井16、尾门右饰件溢料井 14、尾门右饰件溢料井15中,从而在分流道、牛角型 浇口和左、右尾门饰件内部形成中空截面。继续通 入压缩氮气保压,直到制品冷却定型。打开模具前 关闭通入氮气进气管1、氮气进气管9的氮气,此时 气针后退。产品内部气体排出,然后再打开模具取 出产品。
的长度范围设计为20哪宽度6处的尺寸设计为
10m珥厚度7处的尺寸设计为1.2硼1。区域1,宽度 6处的尺寸设计为10 rrm'厚度7处的尺寸设计为 1.6mTlo区域3,宽度6处的尺寸设计为10Iml’厚度
7处的尺寸设计为1.6舢。
3模具设计 根据产品结构和成型工艺的要求。尾门左右饰
件模具结构‘2如图3所示。
液压缸1l上的销的作用是在塑料注射完成后 关闭分流道,防止压缩氮气进入料筒。液压缸12上 的销的作用是:注射塑料时关闭溢料井流道,防止 塑料进入溢料井中.塑料注射完成后且氮气注射前 打开溢料井流道。以便压缩氮气将多余熔融塑料通 过溢料井流道挤入到溢料井中。整个成型过程的压 力一时间曲线如图4所示。
气体保压时间,T4~丁,为排气、打开模具以及取出 制品所用时间。
舒。2001.110(1):1.9.
iIliem∞ⅡDldj唱岬i呕阳疆膳嘲∞li翻}吐鼬池山地 【4】JIANG B Y,WU w Q,只小jG H J。d a1.E旺ect d
widl删∞咖妯聪蚰y【J】.0嘶∞ald跏ciS两Ergi
【5】删(B.R刁珏疆MI 难商唱.200r7,15(11):173&1744. y T.De嘧面∞妇d印.ecti呕
Ab臼翻醴:Tl℃硼nciple and a阱啦∞don of翻s—assis6酣iIliec廿on moIding钯dl∞foJ盯w目e pre靶nted.
The g咖ctIlre of an automoti、7e re盯韵te m翻or啪s anaIyz酣a耐optin血酣.1k appli∞廿on of
现主要介绍汽车尾门左右饰件气道设计要点和 气辅成型技术在该产品上的生产工艺过程。该产品 采用的气辅成型技术为有溢料井的成型方式。
2产品结构设计 产品结构设计对气道具有重要影响,若气道周
围壁厚较大.在注气过程中.气体可能会渗透到产品 内部。造成非气道区域形成中空面,从而影响产品外 观以及强度。因此要对气道周围的壁厚进行优化设 计。防止气体渗透。
42
模具工业2009年第35卷第12期
气体辅助注射成型技术
在汽车内饰件上的应用
欧荔苹,杨军,邓云 (广州市中新塑料有限公司,广东广州 511365)
摘要:介绍了气体辅助注射成型技术的原理和应用.分析了汽车尾门饰件结构。并对其进行优化设计。 对尾门饰件进行了气体辅助注射成型模设计。生产实际表明,采用气辅成型技术。在结构上解决了采用 传统设计方法难以解决的结构难题.减轻了产品重量。降低了产品成型后的翘曲变形。提高了产品表面 质量。
图2为尾门右饰件结构图和设计的气道。产品 所用材料为聚丙烯(PP),基本壁厚为2.3 rn【Il’左饰 件与右饰件结构对称。若厚度7处为2.3Ⅱm在注
万方数据
气过程中,气体会穿透气道渗透到产品内部。因此 需要对产品局部结构进行更改。根据需要对产品的 区域1、区域2、区域3、壁厚7处和宽度6处的尺寸 进行优化,区域2处,以进气口为中心位置,区域2
(a)塑料填充阶段
(b)气体注射阶段
(c)气体保压阶段
(d)捧气阶段
图1气辅成型技术的工艺过程
气辅成型技术的优势主要体现在以下方面: (1)缩短产品成型周期。 (2)节省材料。 (3)降低填充压力和锁模力。 (4)降低产品内应力。 (5)减小产品表面缩痕。 (6)降低产品翘曲变形。 气辅成型技术主要有2种.1种是欠料注射方 式,即在制品体积的70%~85%注射完成后。注入 气体来推动熔体完成全部填充.同时气体也起保压