洁净钢氧化夹杂分析方法评述
第二篇洁净钢发展及钢中夹杂物控制

Institute of Ferrous Metallurgy
脱氧产物总结
• 单个脱氧产物的直径一般小于10μm,由于尺寸较小,除非最终产品要求极高, 一般不会危害钢材的使用性能; • 若脱氧产物与炉渣、耐材反应形成大颗粒夹杂,则会对钢材性能产生严重影响。
表 不同钢中发现的典型脱氧产物 钢种 Al镇静钢 Si镇静钢 Ca处理镇静钢 Al镇静钢,有残余Mg 钛处理镇静钢 脱氧产物类型 Al2O3 SiO2 、MnO-SiO2 CaO-Al2O3 MgAl2O4 Al2O3、 TiOx、 TiN 备注 脱氧后在钢液中形成,固态 脱氧或凝固过程中形成,固态或液态夹杂物 与氧化铝反应形成,固态或液态 与氧化铝反应形成,固态 TiOx形成于二次氧化过程, TiN形成于凝固 过程,均为固态夹杂物
2.3 钢种对夹杂物特征的要求
钢种 IF钢 汽车深冲钢板 易拉罐钢 压力容器钢 抗HIC钢(油气管) 管线钢 滚珠轴承 帘线钢 重轨钢 最高纯净度,×10-6 [C]≤30, [N] ≤40, T.O ≤40 [C]≤10, [N] ≤50 [C]≤10, [N] ≤30 [C]≤30, [N] ≤30, T.O ≤20 [P] ≤70 [P]≤50, [S] ≤10 [S]≤30, [N] ≤35, T.O ≤30 T.O ≤10 [H]≤30, [N] ≤40, T.O ≤15 [H]≤2, [N] ≤40, T.O ≤20 最小夹杂物尺寸,μm
图 FeO-MnO-SiO2 三元相图
Institute of Ferrous Metallurgy
钢中夹杂物来源Ⅰ---脱氧产物
• Si+Mn+Al脱氧
• 脱氧产物:
MnO·SiO2
℃ 1150
钢中夹杂物的产生与去除途径
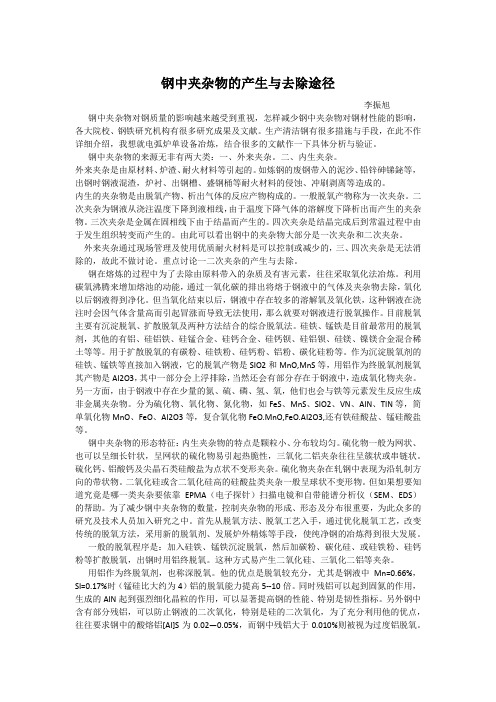
钢中夹杂物的产生与去除途径李振旭钢中夹杂物对钢质量的影响越来越受到重视,怎样减少钢中夹杂物对钢材性能的影响,各大院校、钢铁研究机构有很多研究成果及文献。
生产清洁钢有很多措施与手段,在此不作详细介绍,我想就电弧炉单设备冶炼,结合很多的文献作一下具体分析与验证。
钢中夹杂物的来源无非有两大类:一、外来夹杂。
二、内生夹杂。
外来夹杂是由原材料、炉渣、耐火材料等引起的。
如炼钢的废钢带入的泥沙、铅锌砷锑鉍等,出钢时钢液混渣,炉衬、出钢槽、盛钢桶等耐火材料的侵蚀、冲刷剥离等造成的。
内生的夹杂物是由脱氧产物、析出气体的反应产物构成的。
一般脱氧产物称为一次夹杂。
二次夹杂为钢液从浇注温度下降到液相线,由于温度下降气体的溶解度下降析出而产生的夹杂物。
三次夹杂是金属在固相线下由于结晶而产生的。
四次夹杂是结晶完成后到常温过程中由于发生组织转变而产生的。
由此可以看出钢中的夹杂物大部分是一次夹杂和二次夹杂。
外来夹杂通过现场管理及使用优质耐火材料是可以控制或减少的,三、四次夹杂是无法消除的,故此不做讨论。
重点讨论一二次夹杂的产生与去除。
钢在熔炼的过程中为了去除由原料带入的杂质及有害元素,往往采取氧化法冶炼。
利用碳氧沸腾来增加熔池的动能,通过一氧化碳的排出将熔于钢液中的气体及夹杂物去除,氧化以后钢液得到净化。
但当氧化结束以后,钢液中存在较多的溶解氧及氧化铁,这种钢液在浇注时会因气体含量高而引起冒涨而导致无法使用,那么就要对钢液进行脱氧操作。
目前脱氧主要有沉淀脱氧、扩散脱氧及两种方法结合的综合脱氧法。
硅铁、锰铁是目前最常用的脱氧剂,其他的有铝、硅铝铁、硅锰合金、硅钙合金、硅钙钡、硅铝钡、硅镁、镍镁合金混合稀土等等。
用于扩散脱氧的有碳粉、硅铁粉、硅钙粉、铝粉、碳化硅粉等。
作为沉淀脱氧剂的硅铁、锰铁等直接加入钢液,它的脱氧产物是SIO2和MnO,MnS等,用铝作为终脱氧剂脱氧其产物是AI2O3,其中一部分会上浮排除,当然还会有部分存在于钢液中,造成氧化物夹杂。
钢洁净度的评定和控制二

A C D钢公司 " # $ 7 2 / : &’ $ 0 2 K" # $ 0 2 K : &’ $ 8 2 / 0 / / 7 克利夫兰厂 美国 . / / 7 " # $ 6 1 2 / : &’ $ 6 2 /" # $ @ 2 6 : &’ $ 6 2 8 0 内陆钢公司 # $ ( 2 0 : &’ $ 1 2 6" # $ 6 2 @ : &’ $ 0 2 @ 0 / / 8 美国 . " @号 ; $ " -
? @ & BA> &含量对中间包内钢水总氧含量 # $ % & ’ 的影响 ) ! 1 " 策+ 为了减少 ? 采取了如下对 @ &和 A> &的污染 *
& B( % A> ’ ( A> & B1 % 7 8 ’ C7 8 1 (
钢洁净度的评定和控制 二.
OQ P O
从根本上降低补吹频率 4 ; $ "采用副枪 : 采用高效的机械挡渣设备 : 如挡渣球 浮在钢 水和炉渣界面之间 . 有助于减少出钢带入钢包的 : 渣 量约7 钢. 也 可 采 用 一 些 传 感 器9 出 钢 < = > ? : 后: 钢包厚渣层引起了大量渣携带问题 9 例如 : 美 国内陆钢公司第 @ ; $ "车间标准钢种通过机械扒 渣 使钢包炉 渣层厚度低于 @ A &" . 8 B B90 / / 7年 A C D钢 公 司 克 力 夫 兰 厂 最 后 钢 包 渣 平 均 厚 度 为 厂低碳铝镇 ! 1 B B: A C D钢 公 司 印 第 安 那 E F G H I G 静钢钢包渣层厚 / 高强度低合金钢钢包渣 ! B B: 层厚 0 要求增碳条件的钢种渣层厚 7 1 B B:
洁净钢与夹杂物

洁净钢与夹杂物刘志明 2016年11月8日一 二洁净钢的简介 钢中非金属夹杂物的类型、来源 冶炼精炼连铸过程非金属夹杂物行为演变 洁净钢生产关键技术三 四洁净钢的简介洁净钢的定义1、洁净钢没有固定的定义,因为各个钢种所达到的洁净度是和钢种的用途 相关的,因此钢种不同对洁净度的要求也不同。
2、国外流行的看法是指钢中夹杂物总量或钢中夹杂物含量水平。
Holpapa 把洁净钢狭义地定义为钢中非金属夹杂物的含量,即氧化物、硫化 物的含量。
而纯净钢是指钢中S、P、H、N、O的含量,有时甚至包括钢中碳含量。
Kiessling扩充了洁净钢的概念,把有害的微量元素Pb、As、Bi、Cu、Sn等也包括 在内。
洁净钢也是相对的,而绝对纯净钢是不存在的,洁净钢和纯净钢侧重点不 同。
洁净钢应该根据产品的用途来决定钢的品质,产品的使用性能主要决定于钢的 洁净度水平,主要包括两个方面的内容: 一是钢中杂质元素和有害元素含量要非常低; 二是要严格控制钢中夹杂物的数量和形态、组织、尺寸分布等以满足不同的 使用条件。
要得到更高洁净度的钢产品,需要采用相应先进的工艺设备和工艺技术,进 一步减少钢中有害元素的含量,控制钢中夹杂物。
洁净钢的简介洁净钢的简介 浸入式水口端部堵塞洁净钢的简介 浸入式水口端部堵塞洁净钢的简介中间包水口堵塞洁净钢的简介洁净钢的简介夹杂物引起的缺陷洁净钢的简介夹杂物引起的缺陷洁净钢的简介夹杂物引起的缺陷洁净钢的简介夹杂物引起的缺陷洁净钢的简介夹杂物引起的缺陷洁净钢的简介一 二洁净钢的简介 钢中非金属夹杂物的类型、来源 冶炼精炼连铸过程非金属夹杂物行为演变 洁净钢生产关键技术环节三 四钢中非金属夹杂物的类型、来源为什么要给夹杂物分类?因为夹杂物分类能够帮助我们了解夹杂物形成的 机理,判断其形成原因并使我们能够找到对策以减 少炼钢和连铸中水口堵塞和夹杂物引起的缺陷 。
钢中非金属夹杂物的类型、来源钢中非金属夹杂的来源 钢中非金属夹杂物的来源主要来源有内生夹杂和外来夹杂两部分 组成。
控制钢中夹杂物改善铸坯洁净度
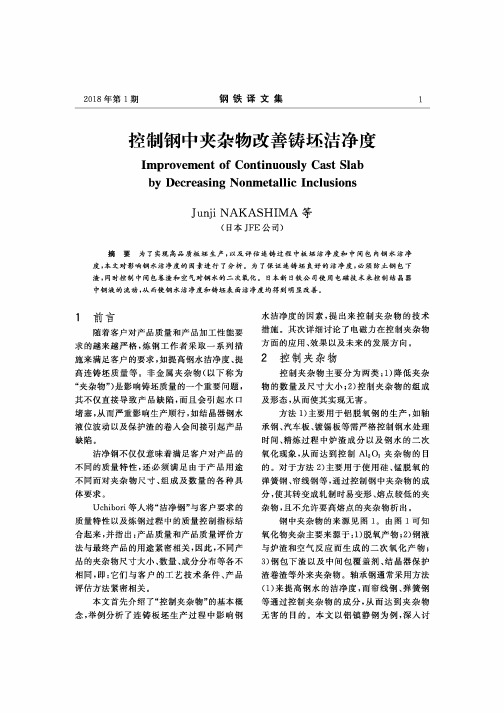
2018年第1期钢铁译文集1控制钢中夹杂物改善铸坯洁净度Improvement of Continuously Cast Slabby Decreasing Nonmetallic InclusionsJunji NAKASHIMA等(日本JF E公司)摘要为了实现高品质板坯生产,以及评估连铸过程中板坯洁净度和中间包内钢水洁净度,本文对影响钢水洁净度的因素进行了分析。
为了保证连铸坯良好的洁净度,必须防止钢包下渣,同时控制中间包卷渣和空气对钢水的二次氧化。
日本新日铁公司使用电磁技术来控制结晶器中钢液的流动,从而使钢水洁净度和铸坯表面洁净度均得到明显改善。
1前言随着客户对产品质量和产品加工性能要 求的越来越严格,炼钢工作者采取一系列措 施来满足客户的要求,如提高钢水洁净度、提 高连铸坯质量等。
非金属夹杂物(以下称为 “夹杂物”)是影响铸坯质量的一个重要问题, 其不仅直接导致产品缺陷,而且会引起水口 堵塞,从而严重影响生产顺行,如结晶器钢水 液位波动以及保护渣的卷入会间接引起产品 缺陷。
洁净钢不仅仅意味着满足客户对产品的 不同的质量特性,还必须满足由于产品用途 不同而对夹杂物尺寸、组成及数量的各种具 体要求。
U ch ib o ri等人将“洁净钢,,与客户要求的 质量特性以及炼钢过程中的质量控制指标结 合起来,并指出:产品质量和产品质量评价方 法与最终产品的用途紧密相关,因此,不同产 品的夹杂物尺寸大小、数量、成分分布等各不 相同,SU:它们与客户的工艺技术条件、产品 评估方法紧密相关。
本文首先介绍了“控制夹杂物”的基本概 念,举例分析了连铸板坯生产过程中影响钢水洁净度的因素,提出来控制夹杂物的技术 措施。
其次详细讨论了电磁力在控制夹杂物 方面的应用、效果以及未来的发展方向。
2控制夹杂物控制夹杂物主要分为两类:i)降低夹杂 物的数量及尺寸大小;2)控制夹杂物的组成 及形态,从而使其实现无害。
方法1)主要用于铝脱氧钢的生产,如轴 承钢、汽车板、镀锡板等需严格控制钢水处理 时间、精炼过程中炉渣成分以及钢水的二次 氧化现象,从而达到控制A1203夹杂物的目 的。
钢中夹杂物的类型及控制技术发展

钢中夹杂物的类型及控制技术发展XX(河北联合大学冶金与能源学院,唐山,063009)摘要:综合论述了钢中非金属夹杂物的按化学成分、形态、粒度、来源的分类以及控制夹杂物含量时所采用的气体搅拌-钢包吹氩、中间包气幕挡墙、电磁净化-钢包电磁搅拌、中间包离心分离和结晶器电磁制动、过滤器技术、超声处理技术和渣洗技术,并针对钢中夹杂物的控制技术的优、缺点进行了简要的归纳。
随着氧化物冶金工艺纯净钢产品的开发,夹杂物去除技术的不断进步,非金属夹杂物的控制技术仍面临着新任务。
关键词:非金属夹杂物;夹杂物类型;控制技术Types and Progress on Technique for Removel of inclusions in steelXX(College of Metallurgy and Energy Hebei United University, Tangshan 063009) Abstract:The behavior of inclusions in molten steel includes physical processes such as nucleation, growth, polymerization and transmission. The removal of inclusions can be seen as the result of transmission, which involves inclusion growth, floating and separating. The key progress on technique for removal of inclusions in steel is gas stirring-ladle argon blowing, gas shielding weir and dam in tundish, electromagnetic cleaning-ladle electromagnetic stirring, tundish centrifugal separating and mold electromagnetic braking, slag washing, ultrasonic technique ,and filter technique.Key words:non-metallic inclusions Typesof inclusions, Technique for Removel of inclusions1引言钢中非金属夹杂物是指钢中不具有金属性质的氧化物、硫化物、硅酸盐或氮化物。
钢中夹杂物的无损检测分析方法

钢中夹杂物的无损检测分析方法目前,大批量、快节奏地生产洁净钢是当今世界钢铁流程发展的重要趋势。
如何要提高钢水的洁净度,就要全面获取夹杂物的特征信息,无损检测就是检查和测试夹杂物的手段之一。
无损检测包含:1、超声波检测超声波检测在钢铁企业中已被广泛应用,常规应用于检测200μm以上的缺陷。
超声波检测夹杂物是基于钢基体与缺陷之间的声学性能差异。
一般超声波检测系统所使用的探头频率一般小于10MHz,很难检测到更小的缺陷。
但随着高频探头的发展,如30-100MHz探头的使用,已可以检测到直径小于100μm的缺陷或夹杂物。
但要求试样检测面要光洁和组织要均匀,且晶粒大小需小于所检测的缺陷或夹杂物大小。
超声波检测的主要优点是可以在线无损检测,并且可以对试样中的缺陷进行定位,此外检测的试样体积很大,因此可以减少遗漏大的有害夹杂的可能性;缺点是不能检测小尺寸夹杂物,并且不能很好区分缺陷类型,比如气孔和夹杂物。
2、电磁法电磁法也被用来检测金属内部质量。
一个常用的方法是磁漏通量检测法。
当一个缺陷或者夹杂物出现在铁磁材料的近表面时会产生一个漏通量,与其他位置相比在夹杂物位置的磁阻会显著增大。
如果磁性材料的磁化近饱和,磁通量会被夹杂物扰乱,从而进入缺陷位置的上部空间形成一个漏通量,这个漏通量就被磁传感器检测到。
这种方法对长条状夹杂物比较敏感,夹杂物太短的话不容易从背景噪声中区分。
同时,如果夹杂物过于长,超过了最佳值,也会检测不到。
3、微型CT微型CT又称为X射线计算机微断层扫描技术,它可以通过从不同角度拍摄的一系列X射线投射图片来重现试样的内部结构,获得夹杂物的三维形貌。
微断层扫描技术与医用CT的不同之处在于其拥有更高的空间分辨率,此外在微断层扫描中试样时旋转的,而射线发射器和接收器是固定的。
伴随X射线管技术的进步,微型CT的空间分辨率已经达到微米级。
用标准仪器时图片几乎不放大,而使用带微距的X射线管时可以获得放大5-10倍的图片。
钢中的氧化物系夹杂物的微细分散及组成控制技术

氧化 物 系非 金属 夹杂 物 的控制 技 术 。
2 氧 化 物 系非 金 属 夹 杂 物在 氧 化 物 冶金 学 中 的作
用
事 实说 明 , 由于钢 液脱 氧方 法不 同 ,钢 中 Mn S的析 出分布 状态 有 大 的差 异 。
为 了改 善焊 接熔 合线 附 近接 合 面的韧 性 ,进行 了很 多关 于采用 TN 进行 晶粒 细化 的研究 ;并 且 ,为了 i 进一 步改善 H Z ( A 焊接 热影 响区 )的韧性 ,开发 了
E MA ( l t npo em co a a sr P ee r rd i — n l e 简称 电子探针 ) co r y 解 析所 得 Mn S分 布变 化示 于 图 1 在 钢 中氧浓度 ( 。 即
至 今 为止 ,钢 中 的非 金属 夹 杂物 对 产 品特 性 是 有 害 的 ,为 了将 之 除 去 已尽 了极 大努 力 。这些 有 害
的 析 出在很 大程 度 上取 决 于氧 化物 的种 类 。研究 了 在 氧 化 物Mn — i 的Mn 溶 解 度 和 Mn 向 氧化 物 O SO 系 S S
的析 出率 ,两者 的倾 向 良好 一致 ,当M O 至 5 % n增 3
以上 时 ,M S n 的析 出率 变成最 大 的 6 %。 5 31 Mn .. 2 S向氧化 物 的析 出机 理
夹 杂物 尺寸 一般 多在 5 m以上 。 上世 纪 9 年代 , 0 在 0
业 界有 很 多研 究报 告 提 出对数 m 尺 寸 的钢 中氧 化
氧含 量 )极低 ( 9 p ) < p m ,基本 上不 存 在 氧化物 的真
空 熔炼 材 ( 上 ,表示 Mn a) S的 白点 偏析 的在 灰色 的 网络 ( e w r ) nt ok 区域 即 M n的偏析部 。 在 Mn S— r 而 — iZ
不锈钢中夹杂物控制综述

不锈钢中夹杂物的成分、形态、尺寸以及分布 直接影响着产品的工艺性能,甚至直接导致各种类 型的缺陷,不锈钢中大多数夹杂物产生于脱氧过 程[1]。大尺 寸 的 Al2 O3 夹 杂 物 容 易 引 起 水 口 堵 塞[2],影响连铸生产顺行。细小 Al2 O3 夹杂物可引 起的抛光后“点状”缺陷[3],产品质量不能满足用 户加工使用的需求。高熔点和高硬度镁铝尖晶石 ( MgAl2 O4 ) 夹杂物会引起裂纹,导致产品失效[4]。 钙处理时间不充分时,较大尺寸的钙铝酸盐夹杂物 轧制后仍有不变形的镁铝尖晶石夹杂物的核心,导 致冷轧产品表面线鳞状缺陷[5]。硅酸盐夹杂物难 以从钢液中去除,需要更长的精炼时间。含钛铁素 体不锈钢中网状 TiN 夹杂物[6]、TiO2 夹杂物[7]和 CaTiO3 夹杂物[8]引起水口结瘤或结晶器“结鱼”
2. 1 铝基脱氧不锈钢中夹杂物的改性
铝基脱氧不锈钢中夹杂物改性的思路是: 通 过铝极强的脱氧能力,很容易将不锈钢中的溶解 氧降低到很低的水平,同时生成大量危害较大的 Al2 O3 夹杂物,然后再通过钙处理尽可能将其改 性为液态钙铝酸盐夹杂物,促进其长大上浮去除, 同时,防止堵塞水口,减小其对不锈钢材的危害。 即铝脱氧生产的不锈钢虽然可能存在一些危害较 大的未完全改性氧化铝夹杂物,但结块、结壳或冷皮) 导致不锈钢中板、薄板表面 易产生大量缺陷。同时,不锈钢中夹杂物的合理控 制和利用也可以细化铸坯凝固组织,提升产品质 量。因此,夹杂物的合理控制是高品质不锈钢生产 的重中之重。本文对前人在不锈钢中夹杂物的控 制方面所做的工作包括不锈钢中夹杂物的生成、变 性和利用等方面进行了综合阐述。
2014 年 2 月 第 30 卷 第 1 期
炼钢 Steelmaking
Feb. 2014 Vol. 30 No. 1 ·71·
洁净炼钢的夹杂物特征和质量控制

清 洁炼 钢 工具 和 质量 控 制 同等 重 要 , 因为在 工 艺过 程 中 , 通过 钢水 洁净度 的测 量设定 它 们 的标 准 。
过去 经 常采用 多重过 程 中和离 线工具 确定 钢种 的 洁 净度 。先 前 出 版 的 文 献 列 出 了 在 安 塞 乐 米 塔 尔 R & D 以及 北美 钢 厂 平 时采 用 的 一 些 技 术 。这 些 技 术包 括采 用 自动扫 描 电子 显 微镜 ( S E M) 、 阴极 电子 激发 光显 微镜 ( C L M) 、 脉 冲鉴 别分 析 ( P D A) 对钢 水 和炉 渣化 学成 分测量 、 夹 杂物分 析 , 并 且测 量产 品特
或者 对产 品性 能 的不 利影 响降 至最小 。
采 用 发 射光 谱 仪分 析 棒 状钢 样 化学 组 成 , 采用 力 可燃 烧分 析仪 分 析 中 间包 或 结 晶器 试 样 中的硫 。 试 样首 先经 发射 光谱 仪 P D A分析 夹 杂物 , 然后 采 用 相 同的光谱 仪分 析 钢水 化 学 组 成 , 仅 有钙 处 理 钢 种
2 0 1 6年第 4期
现
代
冶
金
2 1
洁净 炼 钢 的夹 杂物 特 征 和质 量 控 制
( 美国) P . K a u s h i k等
摘
要: 为 了适应内外部顾客的需求 , 提高炼钢 和浇铸过程 , 包括监测和评价现有和新 开发的钢水精炼 工艺。半成
品的内部质量控制需要一种工具 , 其与工艺过程反常导致 产 品缺 陷相关 。本 文重点关 注 了采 用的技术 , 像成 品钢
生 产 过 程 控制 条 件 的必 要 性 所 带 来 的优 点 , 同时可提高钢材质量。
炼钢脱氧工艺及夹杂物控制措施分析
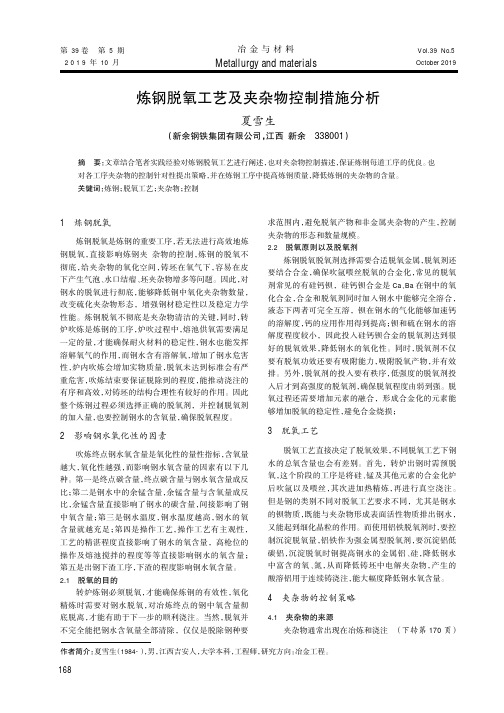
(下转第170页)炼钢脱氧工艺及夹杂物控制措施分析夏雪生(新余钢铁集团有限公司,江西新余338001)摘要:文章结合笔者实践经验对炼钢脱氧工艺进行阐述,也对夹杂物控制描述,保证炼钢每道工序的优良。
也对各工序夹杂物的控制针对性提出策略,并在炼钢工序中提高炼钢质量,降低炼钢的夹杂物的含量。
关键词:炼钢;脱氧工艺;夹杂物;控制Metallurgy and materials作者简介:夏雪生(1984-),男,江西吉安人,大学本科,工程师,研究方向:冶金工程。
1炼钢脱氧炼钢脱氧是炼钢的重要工序,若无法进行高效地炼钢脱氧,直接影响炼钢夹杂物的控制,炼钢的脱氧不彻底,给夹杂物的氧化空间,铸坯在氧气下,容易在皮下产生气泡、水口结瘤、坯夹杂物增多等问题。
因此,对钢水的脱氧进行彻底,能够降低钢中氧化夹杂物数量,改变硫化夹杂物形态,增强钢材稳定性以及稳定力学性能。
炼钢脱氧不彻底是夹杂物清洁的关键,同时,转炉吹炼是炼钢的工序,炉吹过程中,熔池供氧需要满足一定的量,才能确保耐火材料的稳定性,钢水也能发挥溶解氧气的作用,而钢水含有溶解氧,增加了钢水危害性,炉内吹炼会增加实物质量,脱氧未达到标准会有严重危害,吹炼结束要保证脱除到的程度,能推动浇注的有序和高效,对铸坯的结构合理性有较好的作用。
因此整个炼钢过程必须选择正确的脱氧剂,并控制脱氧剂的加入量,也要控制钢水的含氧量,确保脱氧程度。
2影响钢水氧化性的因素吹炼终点钢水氧含量是氧化性的量性指标,含氧量越大,氧化性越强,而影响钢水氧含量的因素有以下几种。
第一是终点碳含量,终点碳含量与钢水氧含量成反比;第二是钢水中的余锰含量,余锰含量与含氧量成反比,余锰含量直接影响了钢水的碳含量,间接影响了钢中氧含量;第三是钢水温度,钢水温度越高,钢水的氧含量就越充足;第四是操作工艺,操作工艺有主观性,工艺的精湛程度直接影响了钢水的氧含量,高枪位的操作及熔池搅拌的程度等等直接影响钢水的氧含量;第五是出钢下渣工序,下渣的程度影响钢水氧含量。
钢洁净度的评定和控制

钢洁净度的评定和控制1前言市场对洁净钢的需求逐年增加,除了要求降低钢中非金属氧化物夹杂含量和控制其形态、化学成分及尺寸分布外,还要求降低钢中杂质元素(如:S、P、H、N、甚至C)和痕量元素(如:As、Sn、Sb、Se、Cu、Pb及Bi)含量。
表1为普通用钢内杂质元素对其机械性能的影响。
钢材中的夹杂物可引起许多缺陷,例如,美国国家钢公司Midwest厂低碳铝镇静钢发生边部裂纹,经鉴定,该裂纹是由脱氧和二次氧化产物Al2O3夹杂、来自中间包覆盖剂的铝酸钙和夹带的结晶器保护渣而引起。
纵向裂纹发生在带钢表面平行于轧制方向,裂纹可导致低碳铝镇静钢汽车板表面缺陷和可成型性问题,正如美国内陆钢公司4号BOF车间和国家钢公司大湖厂多项研究论文所述,钢中的铝酸盐夹杂物来自裹入结晶器的脱氧产物和复合非金属夹杂物。
钢的洁净度取决于钢中非金属夹杂物的数量、形态和尺寸分布,因钢种及其用途不同而定义不同,如表2所示。
由于大型宏观夹杂对钢的机械性能危害最大,其尺寸分布非常重要。
据报道,1kg典型的低碳铝镇静钢含107~109个夹杂物(其中,仅含80~130Lm夹杂物400个,130~200Lm夹杂物10个,200~270Lm 夹杂物少于1个)。
显然,检测少量大型夹杂物是非常困难的。
尽管大型夹杂物在数量上比小型夹杂物少得多,但其总体积分数可能较大,有时一个大型夹杂物能引起整个一炉钢的灾难性缺陷。
因此,洁净钢不仅要控制钢中夹杂物平均含量,而且还要避免夹杂物尺寸超过对产品有害的临界尺寸。
由此,表2中列出了许多钢材对夹杂物最大尺寸的限定值。
夹杂物尺寸分布的重要性在图1中得到了进一步解释。
测试结果表明,大于30Lm的夹杂物由钢包内的1.61×10-4%降到中间包的0.58×10-4%。
因此,尽管钢包内钢水总氧含量稍高且夹杂物总量较多,中间包内的钢水还是较洁净的。
图1钢包和中间包内Al2O3夹杂物尺寸分布非金属夹杂物来源很多,包括:(1)脱氧产物。
洁净钢中微观夹杂物表征技术及应用
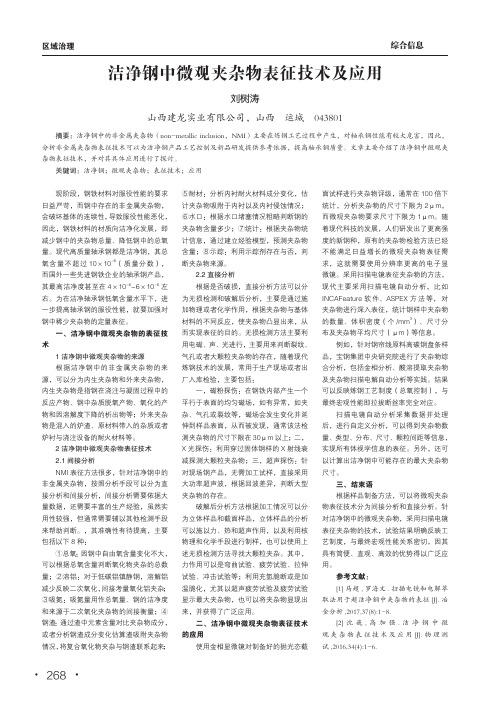
区域治理综合信息洁净钢中微观夹杂物表征技术及应用刘树涛山西建龙实业有限公司,山西 运城 043801摘要:洁净钢中的非金属夹杂物(non-metallic inclusion,NMI)主要在炼钢工艺过程中产生,对轴承钢性能有较大危害,因此,分析非金属夹杂物表征技术可以为洁净钢产品工艺控制及新品研发提供参考依据,提高轴承钢质量。
文章主要介绍了洁净钢中微观夹杂物表征技术,并对其具体应用进行了探讨。
关键词:洁净钢;微观夹杂物;表征技术;应用现阶段,钢铁材料对服役性能的要求日益严苛,而钢中存在的非金属夹杂物,会破坏基体的连续性,导致服役性能恶化,因此,钢铁材料的材质向洁净化发展,即减少钢中的夹杂物总量、降低钢中的总氧量。
现代高质量轴承钢都是洁净钢,其总氧含量不超过10×10-6(质量分数),而国外一些先进钢铁企业的轴承钢产品,其最高洁净度甚至在4×10-6-6×10-6左右。
为在洁净轴承钢低氧含量水平下,进一步提高轴承钢的服役性能,就要加强对钢中稀少夹杂物的定量表征。
一、洁净钢中微观夹杂物的表征技术1洁净钢中微观夹杂物的来源根据洁净钢中的非金属夹杂物的来源,可以分为内生夹杂物和外来夹杂物,内生夹杂物是指钢在浇注与凝固过程中的反应产物、钢中杂质脱氧产物、氧化的产物和因溶解度下降的析出物等;外来夹杂物是混入的炉渣、原材料带入的杂质或者炉衬与浇注设备的耐火材料等。
2洁净钢中微观夹杂物表征技术2.1间接分析NMl表征方法很多,针对洁净钢中的非金属夹杂物,按照分析手段可以分为直接分析和间接分析,间接分析需要依据大量数据,还需要丰富的生产经验,虽然实用性较强,但通常需要辅以其他检测手段来帮助判断。
,其准确性有待提高,主要包括以下8种:①总氧:因钢中自由氧含量变化不大,可以根据总氧含量判断氧化物夹杂的总数量;②溶铝:对于低碳铝镇静钢,溶解铝减少反映二次氧化,间接考量氧化铝夹杂;③吸氮:吸氮量用作总氧量、钢的洁净度和来源于二次氧化夹杂物的间接衡量;④钢渣:通过渣中元素含量对比夹杂物成分,或者分析钢渣成分变化估算渣吸附夹杂物情况,将复合氧化物夹杂与钢渣联系起来;⑤耐材:分析内衬耐火材料成分变化,估计夹杂物吸附于内衬以及内衬侵蚀情况;⑥水口:根据水口堵塞情况粗略判断钢的夹杂物含量多少;⑦统计:根据夹杂物统计信息,通过建立经验模型,预测夹杂物含量;⑧示踪:利用示踪剂存在与否,判断夹杂物来源。
钢中夹杂物的鉴定

钢中夹杂物的鉴定一、实验目的在正常条件下,钢的温度冷却到固相线以下时就会发生硫化物、碳化物和氮化物的析出。
绝大多数氧化物和一些硫化物夹杂在钢液中形成。
在钢凝固之前,如果不去除这些夹杂物,将引起连铸产品的缺陷,对连铸生产顺利进行带来问题和困难,如,降低生产率、降低产品性能、降低金属收得率等。
本实验的主要目的是为了让同学了解钢中夹杂物对钢性能的影响,并掌握对钢中夹杂物的评级。
二、实验设备与试样1.蔡司金相显微镜2.非金属夹杂物的标准试样三、实验原理----钢中夹杂物的分类A类、(硫化物类)具有高延展性,有较宽范围形态比(长度/宽度>3)的单个呈灰色夹杂物。
B类、(氧化铝类)大多数没有变形,带角,形态比小(一般<3)呈黑色或者蓝色颗粒,沿轧制方向排成一行,至少三个。
C类、(硅酸盐类)具有高延展性,有较宽范围形态比(>3)的单个呈黑色或深灰色夹杂物,一般端部呈锐角。
D类、(球状氧化物类)不变形,带角或者圆形的,形态比小(<3)。
黑色或者带蓝色的,无规则分布的颗粒。
DS类、(单颗粒球状类)圆形,或近似圆形,直径不小于13um的单颗粒夹杂物。
四、实验内容及步骤2、国标《钢中非金属夹杂物的测定》(GB/T10561-2005)3、金相显微镜的操作4、非金属夹杂物的标样观察,并评级五、作业1、对下列三幅图中任选一副图,评级,并在实验报告中画出大概的图样。
2、去图书馆查阅非金属夹杂的书籍或者文献,书籍写出名称、作者名称、出版社,并摘抄前言或者概述中有关本书内容的简介,字数多于300。
文献写出名字,作者,期刊名,页数范围,以及摘要。
钢中稳定氧化物夹杂激光粒度分析方法

2 3 仪器及设备 . 2 3 1 电解设备 ..
9
维普资讯
卢翠芬.等 :钢 中稳定氧化物夹杂激光粒度分析方法
第6 ( 期 总第 16 ) 2期
2 3 11 硅整 流器 :交 流 电转 变成 直 流电 , 纸 ,趁热进行抽滤 ,用 1g L热碳酸钠溶液洗涤滤 ... O/ 输出电位 0 5 V — 0 ,输 出电流 0—1A 0 ,直流 电表 I 纸 和残渣 3 ,再用热水洗 4~ 次 。 次 5
”
…
22 试样的制备 . 将 上 述 成 份 的 钢 制 成 O O m ×lO m 或 lm Om
O 5 m×8 r 圆柱 形 试祥 ,共 1 1m 0m a 0—1 2支 ,约
10 10 00— 20克 ,在距顶端部位 2 m处车一个 2 m r n a r 深的槽 ,便 于栓铜丝用 ,将试 样先用 1 % 一 0 5 2% ( / )H I 5 ( / vV C + % V V)甘油无水 乙醇溶液 电解
一
杂混入 了大 量 的沉渣 ( 括渗碳 体 、碱 式铁 盐 、 包 金属粒子 、游离碳 和一些不稳定 的夹杂物 ) 。为 了 使稳定的氧化物夹杂和多量的其它沉渣分离开 ,需 进行水簸 ,磁选 ,氢还原 ,超声波筛分 ,进行大小 颗粒分级等操作步骤 ,非常麻烦 ,而且许多小颗粒 的夹杂物随阳极泥在进行水簸 ,磁选等过程 中被损
( nl d nt me t o p ya d L US pi il w r rsne . tble xd n ls n s e o lc o E g )Is u na C m a n r cpe eepee td Sa izdo ieic i i fe t - n a r l n n i uo z e r
钢中夹杂物的系统分析技术_张立峰

超声波检测的主要优点是可以在线无损检测, 并且可以对试样中 的 缺 陷 进 行 定 位,此 外 检 测 的 试 样体积很大,因此可 以 减 少 遗 漏 大 的 有 害 夹 杂 的 可 能 性 ;缺 点 是 不 能 检 测 小 尺 寸 夹 杂 物 ,并 且 不 能 很 好 区 分 缺 陷 类 别 ,比 如 气 孔 和 夹 杂 物 。
Systematic Analysis of Non-Metallic Inclusions in Steel
ZHANG Li-feng, YANG Wen, ZHANG Xue-wei, LUO Yan, LIU Yang
(School of Metallurgical and Ecological Engineering,University of Science and Technology Beijing,Beijing 100083,China)
10MHz,因此很难检测到更小的缺陷。而 随 着 高 频 探头的发展,如 30~100MHz探 头 的 使 用,已 可 以 检测到直径小于100μm 的缺陷(包括气孔或者夹杂 物)[6-7]。然而随着 探 头 频 率 的 增 加,超 声 波 信 号 的 穿透深度变浅,所 能 检 测 的 材 料 厚 度 也 越 薄。 此 外 超声波检测的精度受试样表面质量和组织均匀性影 响 很 大 ,要 求 光 洁 的 试 样 检 测 面 和 均 匀 的 组 织 ,且 晶 粒大小需小于所检测的缺陷大小。图2为超声波检 测得到 的 粒 径 为 0.191mm 的 夹 杂 物 粒 子,夹 杂 物 位置位于图中蓝线十字交叉处,其中通过 B 扫描 可 以看到夹杂物在 Z 方向的位置,通过 C 扫描可 以 得 到夹杂物在 X-Y 面的位置。
钢中夹杂物分析方法探讨
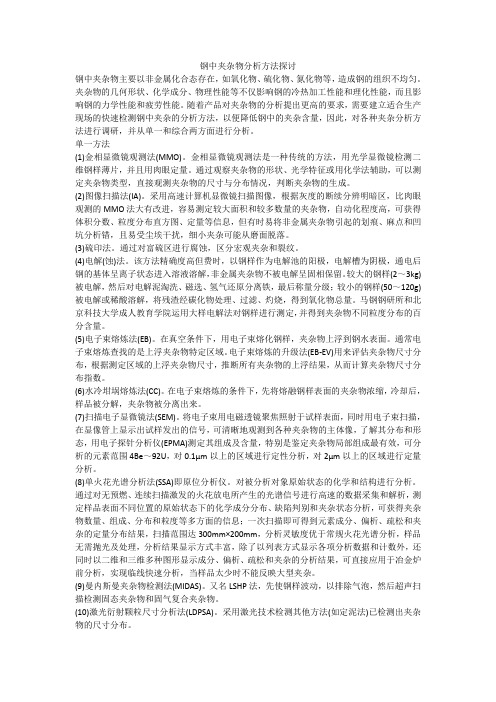
钢中夹杂物分析方法探讨钢中夹杂物主要以非金属化合态存在,如氧化物、硫化物、氮化物等,造成钢的组织不均匀。
夹杂物的几何形状、化学成分、物理性能等不仅影响钢的冷热加工性能和理化性能,而且影响钢的力学性能和疲劳性能。
随着产品对夹杂物的分析提出更高的要求,需要建立适合生产现场的快速检测钢中夹杂的分析方法,以便降低钢中的夹杂含量,因此,对各种夹杂分析方法进行调研,并从单一和综合两方面进行分析。
单一方法(1)金相显微镜观测法(MMO)。
金相显微镜观测法是一种传统的方法,用光学显微镜检测二维钢样薄片,并且用肉眼定量。
通过观察夹杂物的形状、光学特征或用化学法辅助,可以测定夹杂物类型,直接观测夹杂物的尺寸与分布情况,判断夹杂物的生成。
(2)图像扫描法(IA)。
采用高速计算机显微镜扫描图像,根据灰度的断续分辨明暗区,比肉眼观测的MMO法大有改进,容易测定较大面积和较多数量的夹杂物,自动化程度高,可获得体积分数、粒度分布直方图、定量等信息,但有时易将非金属夹杂物引起的划痕、麻点和凹坑分析错,且易受尘埃干扰,细小夹杂可能从磨面脱落。
(3)硫印法。
通过对富硫区进行腐蚀,区分宏观夹杂和裂纹。
(4)电解(蚀)法。
该方法精确度高但费时,以钢样作为电解池的阳极,电解槽为阴极,通电后钢的基体呈离子状态进入溶液溶解,非金属夹杂物不被电解呈固相保留。
较大的钢样(2~3kg)被电解,然后对电解泥淘洗、磁选、氢气还原分离铁,最后称量分级;较小的钢样(50~120g)被电解或稀酸溶解,将残渣经碳化物处理、过滤、灼烧,得到氧化物总量。
马钢钢研所和北京科技大学成人教育学院运用大样电解法对钢样进行测定,并得到夹杂物不同粒度分布的百分含量。
(5)电子束熔炼法(EB)。
在真空条件下,用电子束熔化钢样,夹杂物上浮到钢水表面。
通常电子束熔炼查找的是上浮夹杂物特定区域。
电子束熔炼的升级法(EB-EV)用来评估夹杂物尺寸分布,根据测定区域的上浮夹杂物尺寸,推断所有夹杂物的上浮结果,从而计算夹杂物尺寸分布指数。
钢水炉外精炼及夹杂物分析方法
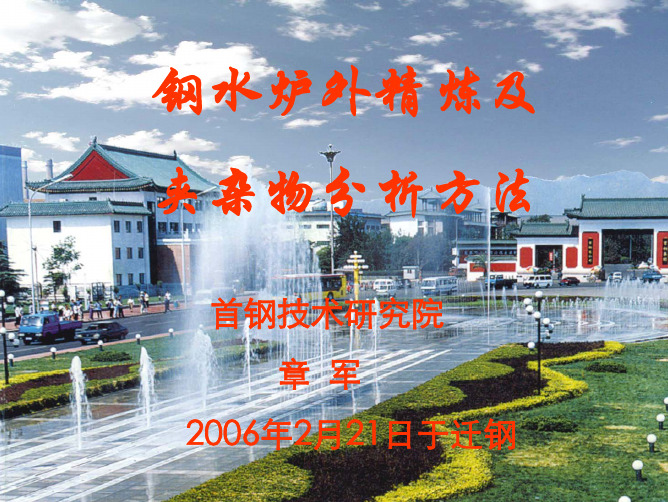
19
精炼渣的成分及作用
CaO SiO2 Al2O3 调节炉渣碱度,脱硫剂 调节炉渣碱度和粘度 调整CaO-SiO2- Al2O3三元渣系处于低 熔点位置
Ca(Mg)CO3 脱硫剂,发泡剂 Na(K)2CO3 Al Si-Fe CaC2, SiC Si-Ca CaF2 脱氧,促进脱硫 脱氧 脱氧,促进发泡 脱氧,改变夹杂物形态 助熔,调整炉渣粘度
钢水炉外精炼及 夹杂物分析方法
首钢技术研究院 章 军 2006年2月21日于迁钢
1
主要内容
• • • • • 钢中非金属夹杂物的来源 炉外精炼的种类与功能 夹杂物的检测和判定方法 夹杂物研究的边沿技术 超低碳钢的精炼及夹杂物问题
2
什么是非金属夹杂物?
氧化物,硫化物,氮化物
如何形成的?
3
非金属夹杂物的形成
12
夹杂物数量和体积
12 10 8
个数(%)
6 4 2 0 0 5 10
夹杂物尺寸(μm)
夹杂物直径 体积 /μm /μm3 5
15 20
倍数
392 314159 8014
100
1kg的超低碳钢含有107-109个夹杂物 其中包括 400个80-130 μm 10个130-200 μm 1个左右200-270 μm 剩余的都为小于80 μm的夹杂
26
钢水静压力对夹杂成分的影响
0.1m 0.4m 2m
CaS
2CaO·SiO2
CaO-Al2O3-SiO2-Fe2O3-MnO-MnS
27
工艺路线选择的一般原则
• • • • 普通热轧板和深冲用低碳铝镇静钢可采用CAS-OB 超低碳深冲钢以RH为主 管线钢以LF+RH为主 中/高碳钢(重轨,帘线,弹簧钢等)棒线材配 LF+VD为主, 与方坯连铸机配套
- 1、下载文档前请自行甄别文档内容的完整性,平台不提供额外的编辑、内容补充、找答案等附加服务。
- 2、"仅部分预览"的文档,不可在线预览部分如存在完整性等问题,可反馈申请退款(可完整预览的文档不适用该条件!)。
- 3、如文档侵犯您的权益,请联系客服反馈,我们会尽快为您处理(人工客服工作时间:9:00-18:30)。
第35卷 第4期2000年4月钢 铁I RON AND ST EELV o l.35,N o.4A p ril2000洁净钢氧化夹杂分析方法评述陈名浩 沈汝美(钢铁研究总院)摘 要 概述了钢中氧化夹杂来源和可测信息,当前各种夹杂分析方法的要点和适用场合,探讨了新测试技术在洁净钢质量表征及配合精炼工艺开展临线快速分析的应用前景。
关键词 洁净钢 氧化物夹杂 在线分析 临线分析αD ISCUSSI ON ON ANALY SISM ETHOD SOF OX I D E INCL USI ONS IN CL EAN STEEL SCH EN M inghao SH EN R um ei(Cen tral Iron and Steel R esearch In stitu te)ABSTRACT Som e asp ects of ox ide inclu si on s in steel including the ox ide sou rces and detectab le info r m ati on,and the po in ts and app licab ility of vari ou s m ethods fo r inclu si on analysis are discu ssed.Several new ly developed techn iques are in troduced to show the cap ab ilities fo r on2line o r on2site rap id analysis and quality characterizati on of clean steels. KEY WOR D S clean steel,ox ide inclu si on,on2line analysis,on2site analysis 随着炼钢技术进步,原材料纯度改善,优质耐火材料的应用以及生产管理的加强,钢的洁净度已大幅度提高,O+N+S+P+C+H非金属元素的合量可控制在100×10-6以下,研制和生产高洁净的超级钢已成可能,并将是我国钢铁工业的重要任备。
随着洁净度提高,对夹杂分析的灵敏度和可靠性提出了更高的要求,特别需要建立适合生产现场的快速检测方法,以配合工艺研究。
由于夹杂物的生成、变形、分布以及对材料性能的影响是很复杂的,取样和选用分析方法要针对检测重点,才能省事而奏效。
本文就氧化夹杂的来源、可测信息、分析代价和应用等方面来评价当前国内外采用的多种方法,着重探讨为发展超级钢需要开发的新方法。
1 氧化夹杂的来源和检测信息钢中氧化夹杂来自四个方面:①炼钢及浇注过程的氧化产物;②脱氧精炼过程的生成物;③冷凝过程过饱和氧的析出物;④夹渣、炉衬及挡坝等被浸蚀而引入的外来夹杂。
目前,脱氧和防二次氧化技术已相当完善,外来夹杂也可减至极少,因此有人提出冶炼零夹杂物钢[1],实际上凝固过程的再析出是难以完全避免的,而细小弥散且含量愈来愈低,将是新建分析方法应重视的特征。
夹杂分析的可测信息与相关方法有下列方面:(1)氧化夹杂总量及主要元素组成,以电解抽取和化学分离分析为主要手段,辅以X衍射作相鉴定,可称为化学类型及含量信息;(2)形状、体积分数、颗粒尺寸分布,以定量金相为主(扫描电镜,图象分析仪,激光散射仪)辅以电解抽取、电子束重熔等富集手段,可称为粒度分布及形态信息;(3)综合化学成分、形态、体积分数、粒度分布的统计分析,以能谱仪配合定量金相来完成,常需辅以富集手段,可称为化学类型及其形态等的综合信息;(4)将各种缺陷(夹杂、气孔等)强度与面积的乘积相叠加,表示为清洁度指数,由高频超声波探测,称为清洁度信息。
2 各种分析方法的比较和应用夹杂分析既是为检验和评定钢材质量,也是为探讨其来源和危害,以采取使其减少或改变性状的α联系人:陈名浩,高级工程师(教授级),北京(100081)钢铁研究总院测试所措施,有关组成、数量、形态、分布等各种信息都是需要的,但作全面检测相当繁琐,分析周期长且成本高,因此,须根据探讨目的作重点测定,对比了解不同方法的功能和优缺点,将有助于正确选用方法和解析结果。
有关钢中夹杂分析方法,近年来英、法钢铁企业相继有较详细的报道[2,3],日本多家钢厂实验室通过共同试验,评价了用不同方法对几种高洁净钢夹杂含量和粒度等分析结果的可比性[4],表1概括列出当前实用方法的一些要点。
有些钢厂尚无铁水预处理和炉外精炼设施,也表1 各种夹杂分析方法的要点T able1 Key po ints of vari ous m ethods fo r inclusi on analysis序号方法信息类型试样量 g分析时间优点缺点1电解抽取+化学分析(EE+CA)(1) 40~80 5~6天取样量大,对大小颗粒都有代表性;含量和组成分析精度较好费时;要求试剂及环境纯度高;不稳定夹杂物被溶解而测不到2定量金相(QM)(2)①5c m×20c m,>50Λm②20c m2;4000个 015mm2,10~50Λm③320mm2:4000个 0108mm2,>2Λm 1~10h自动化程度高,可获得体积分数、粒度分布直方图等定量信息易受尘埃干扰,细小夹杂可能从磨面脱落3抽取+激光衍射和散射(PS M)(2) 50~1002~3天(抽取),3~5m in(测定)粒度范围宽:011~1000Λm抽取(电解或酸溶)及除去碳化物均费时且可能损失目的物4电解抽取+电镜 能谱(EE+SE MED S)(3) 50~250 8~10天取样量及信息量大,适合考察聚合的或外来的大型夹杂费时;不稳定夹杂被破坏5电子束重熔+电镜 能谱(EBR+SE M ED S)(3) 10~200 30m in+5天快速富集夹杂部分夹杂可能因聚合而改变其原来形状和化学组成6高频超声探测(H E2U S)(4)5(由探测面与深度估计的量) 3~4h不分解试样,联合SE M ED S可作原位分析仅能探测到30Λm以上的颗粒7差热抽取(D T E)(1)015~1(5mm×5mm×5mm) 3~5m in快速给出几类氧化夹杂含量,适合探讨工艺过程对某类夹杂的影响无形态粒度信息;加热过程可能导致某些夹杂物发生变化8单火花光谱分析(SSA)(1)(1~10)×10-3(20mm2×5Λm) 2~3m in快速给出各氧化物化学组成类型、粒度分布和相对含量样品量太少,不能确切反映大型夹杂,标样困难目前尚处定性阶段未采取全封闭浇铸,夹杂物含量高且大型夹杂(> 50Λm)比例大,须较大量采样才能反映各类夹杂存在状况,宜用EE+CA测定总量,用EE+SE M ED S(过滤收集在银膜上)分析组成和形态。
由于电解抽取和化学分离(除去渗碳体)会损伤部分对酸性试剂不稳定的夹杂物,必要时须直接对钢样磨面作能谱分析,补充组成分析结果。
当专门考察大型夹杂,常需电解2~3kg钢样,并用淘洗法除去碳化物和小夹杂,EBR重熔可使夹杂上浮富集于钢样表层供分析综合信息。
有些钢种明确限定夹杂物容许尺寸或体积分数,宜采用QM来检测,直接给出(2)类信息,为节省分析时间,可按待测物粒度决定试样被测面积(表1)。
图象分析已有国际标准方法,如A STM E45和SEP1570 71等,但随着夹杂含量愈来愈少而细小,定量分析就很困难了,对这种场合的粒度分布分析,宜采用PS M法,即将抽取物分散在介质中,用激光衍射和散射进行测定,例如应用于RH脱气处理对10Λm以下A l2O3夹杂去除机构的研究[5]。
H F2U S通常是用于器件可靠性检验和失效分析,取样要求有代表性的指定部位。
国外钢厂有的利用高频超声探测所得清洁度指数来考察工艺制度去除大夹杂的效果。
精炼过程的许多环节需要夹杂分析,期待快速分析方法的建立。
从转炉出钢经钢包炉脱氧吹氩、VD或RH脱气并翻动钢水、中间包内用挡坝和过滤器起导流和粘附作用、连铸结晶器附加电磁制动以控制钢水流动、以及喂丝或用合成渣与夹杂起复合反应等措施,都为使夹杂物能够充分上浮排除且改变性状;另一方面,过程中钢水可能接触空气或与卷渣反应而再度氧化,视其发生的阶段和脱氧剂残留及补加情况,会形成不同组分和数量的氧化物,显然,需要跟踪分析,及时反映工艺过程的各种变・7・钢 铁 第35卷化。
D T E 法可望在生产现场快速地进行氧的状态分析,弄清关键步骤脱氧和再氧化的后果。
SSA 法则可快速获得夹杂物组成、数量、粒度等多种信息,用以考察工艺制度对夹杂物改性、形态控制和去除的效果。
D T E 和SSA 都是最近提出的新方法,其应用价值及所需软硬件均在研究开发之中。
图1 电压脉冲探头的结构F ig 11 T he constructi on of E .M .Z .p robe3 新技术的应用前景在线分析对于及时调整工艺参数,把握钢水质量是有意义的。
加拿大M CG I LL 大学开发了电脉冲传感器的在线测定技术,并与日本钢厂合作完成实试,将带有对电极的探头插入中间包,钢水自下而上通过探头,如图1所示,其中非导体夹杂物引起电极间电压变化,产生的电脉冲个数与夹杂物个数相当,脉冲的幅度则与夹杂物颗粒大小成正比,通过换算直接给出单位体积钢水中夹杂物数量和粒度分布图[4]。
由于探头造价昂贵而寿命短,目前尚不实用。
另外,因脉冲电压微弱,只能检测10Λm 以上的颗粒,局限了其用途,如轴承钢中夹杂物,绝大部分小于10Λm ,正在开发的夹杂物在线分析技术还有超声散射探测法,因探头材质等诸多问题,迄今只有定性检测中间包钢水混渣的实例。
比较起来,下述能发展成临线快速分析的方法则更有实用前景。
差热抽取(D T E )是利用不同氧化物热分解温度的差异,在程序升温条件下使获得对应于不同氧化物的氧释放峰,由各峰所辖面积和对应温度(或加热电流)可得到各氧化夹杂数量和类别信息。
文献[6]表明:由微机控制的跟踪升温,可使钢中铁系、硅系和铝系氧化物的释氧峰分开,对同炉钢水从L F —中间包—结晶器三处取样分析可见,硅系和铝系夹杂都随工艺进程而下降,由于上浮和碱性渣的作用,到结晶器中铝系夹杂已降至零;另外,当水口防氧不严,注流氧化,引起铁系氧化物再生,都可由峰形图和定量数据得知,如图2所示,直观且快速。
对氧化夹杂的炉前分析靠测定总氧,而总氧量并不能确切反映脱氧情况。
将通常的定氧仪(红外检测)配备程序升温和分峰解析软件,就可开展差热抽取,容易推广。
目前,D T E 法在宝钢、包钢已开始采用,并在判断CA S 处理去除铝系夹杂等方面取得初步成效。
热抽取过程中,钢样熔体中氧化物之间可能发生复合反应,必需使释氧反应完成在前,为进一步开展各种氧化物的分析,对有关反应动力学的研究是必要的。