13-第7.4章 制造过程失效模式及后果分析(PFMEA)管理程序
PFMEA过程失效模式及后果分析
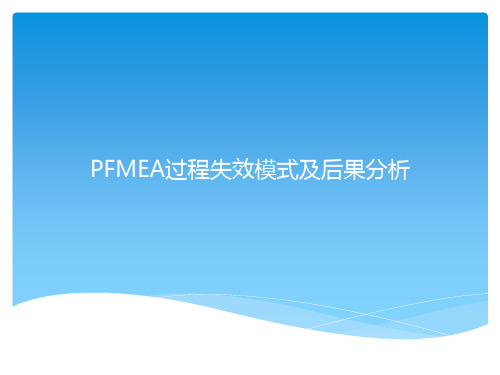
下列可以帮助确定是否将现有的PFMEA纳入最终范围: 新开发的产品和过程; 操作条件的变化; 要求变化(法律/法规,标准规范,客户,最新状态) 制造经验、场内问题,或现场问题/保修; 可能导致危险的过程失效; 人体工程学; 持续改进。
过程FMEA步骤一:规划和准备
PFMEA定义范围的目的---清晰定义过程范围: 识别项目----哪些过程需要分析; 项目计划----培训团队成员、创建项目时间; 定义分析界限---包括什么,不包括什么; 确定能使用的相关经验教训和决策,例如:最佳实践、标准、防错等。
示例:“磨削滑动油封”过程的功能结构
工作坊:步骤三-功能分析(绿色+蓝色笔)
1.过程项目、过程步骤、作业要素具有何种功能和要求? 填入结构树中各项功能和要求: 功能 +要求=绿色字体+蓝色字体 将各项功能填写 在过程项目、过程步骤及作业要素的下面。 备注:“发生什么?”如何从左到右实现产品/过程要求-(过程项目-过程步骤-作业
过程FMEA步骤二:结构分析
结构树按层次排列系统元素,并通过结构连接说明关联关系。这个形象化的结 构考虑了过程项目、过程步骤和过程工作要素之间的关系,在后面,将对他们 分别添加功能模块和失效模块。
对于过程来,查验的最基础层次—变差来源(Sources of Variation),是传统的 “4M(人Man、机Machine、料Material、环Milieu)”,即设备、工装、夹具、 刀/模具的硬件基本参数、动态的控制参数、辅助系统的参数、环境特性、影 响本序的前工序的加工余量、定位点的尺寸及形位公差等。
过程FMEA步骤四:失效分析
PFMEA失效分析的目的是: 1.为过程项目、过程步骤和作业要素的每个功能建立失效(一个或多个失效); 2.识别可能发生的失效/原因,并分配给作业要素和过程步骤; 3.失效关系的可视化(影响-模式-原因,基于功能网的失效网络); 4.通过链接失效链中的失效来创建失效结构; 5.是FMEA表格中记录的失效的基础; 6.失效分析对过程中的每个元素/过程步骤进行了失效描述(结构分析/步骤2和 功能分析/步骤3) 可能的失效从功能/任务推断出来,如设备特定目标状态的不合格、不能充分 完成工作任务、非预期或不必要的活动等; 对失效的描述必须要清晰。不符合、不OK、失效、中断及诸如此类的描述并不 不足以帮助我们去找到失效。 通常,某一功能可以有多种失效。
过程失效模式及后果分析(PFMEA)

XXX汽车技术股份有限公司潜在失效模式及影响分析 PFMEA螺纹孔内无铝屑,机加工面边缘毛刺清理干净;螺纹孔内有铝屑,机加工面边缘未清理干净影响客户装配,客户抱怨61.丝锥损坏2.夹具松动3.切削液未正确喷淋,铝屑未吹掉31.首检记录表2.巡检记录表354None5XΦ0.341±0.01深0.55(英制)尺寸超差 1.毛坯不合格或尺寸变化大4XΦ0.232±0.01深0.5(英制)尺寸超差 2.夹具松动;3.程序错误2XΦ0.232±0.01深0.5(英制)尺寸超差 4.装夹失误2X4.34±0.02(英制)尺寸超差 1.毛坯不合格或尺寸变化大27.19±0.02(英制)尺寸超差 2.夹具松动;3.程序错误2X7.05±0.02(英制)尺寸超差 4.装夹失误2X11.72±0.02(英制)尺寸超差1.毛坯不合格或尺寸变化大1.25±0.02(英制)尺寸超差2.夹具松动;3.程序错误2.38±0.02(英制)尺寸超差 4.装夹失误1.56±0.02(英制)尺寸超差 1.毛坯不合格或尺寸变化大2.44±0.02(英制)尺寸超差 2.夹具松动;3.程序错误8XΦ0.118±0.01(英制)尺寸超差 4.装夹失误尺寸超差1.毛坯不合格或尺寸变化大2X45°±0.5°尺寸超差2.夹具松动;None3影响装配和功能7631.首检记录表2.巡检记录表3★3影响装配和功能7★31.首检记录表2.巡检记录表363NoneNone63影响装配和功能7★31.首检记录表2.巡检记录表3影响装配和功能7★31.首检记录表2.巡检记录表None影响装配和功能7★31.首检记录表2.巡检记录表36363None。
pfmea过程失效模式与后果分析报告

通过深入分析,我们确定了导致这些失效的潜在原因,包 括设备老化、操作规程不完善、员工培训不足、原材料质 量控制不严格以及工艺参数设置不合理等。
对未来工作的建议和展望
改进措施建议
持续改进计划
未来研究方向
基于PFMEA的结果,我们提出了一系 列改进措施,包括更新设备、优化操 作规程、加强员工培训、严格控制原 材料质量以及调整工艺参数等。这些 措施旨在减少失效发生的风险,提高 生产过程的可靠性和稳定性。
为了确保改进措施的有效实施,我们 制定了持续改进计划。该计划包括定 期评估改进效果、监测潜在问题的出 现以及调整改进措施等。通过持续改 进,我们期望能够不断优化生产过程 ,提高产品质量和客户满意度。
在报告的最后,我们提出了一些未来 可能的研究方向。这些方向包括进一 步探索失效模式与潜在原因之间的关 系、研究新的失效分析方法以及开发 更加智能化的失效预测模型等。通过 深入研究,我们期望能够为企业的持 续改进提供更有力的支持。
失效模式
汽车发动机性能下降
后果
影响汽车动力性能,可能导致油耗增加、排放超标
潜在原因
制造过程中材料、工艺、设备等方面的问题
风险评估
高风险,需采取措施进行改进
案例二:电子产品制造过程的PFMEA分析
失效模式
电子元件短路
潜在原因
制造过程中元件组装、焊 接等环节出现问题
后果
产品功能失效,可能引发 安全事故
提前发现和预防问
题
PFMEA是一种预防性的质量工具 ,它通过提前发现和预防潜在的 问题,减少后期修改和返工的成 本。
优化设计和过程
PFMEA分析结果可以为设计和过 程的改进提供指导,帮助企业优 化产品和过程的性能、可靠性和 安全性。
过程失效模式与后果分析PFMEA

过程失效模式与后果分析PFMEA一、PFMEA的定义和目标PFMEA是一种系统性的过程分析方法,用于评估潜在的失效模式、错误或缺陷,以及这些失效模式或错误对产品质量和工作过程的潜在影响。
它的主要目标是提前识别和减轻过程中可能导致质量问题的潜在风险,以便采取适当的预防和纠正措施,提高产品质量和客户满意度。
二、PFMEA的基本概念和步骤1.风险识别:通过审核过程文档、历史数据、专家经验等方式,识别可能存在的失效模式。
2.评估失效的严重程度:对每个失效模式进行定量或定性评估,确定其对产品质量和安全性的潜在影响,此项评估需要专业知识和经验的支持。
3.识别可能的失效原因:找出导致失效发生的根本原因,可以通过使用逻辑树、鱼骨图、5W1H等工具进行分析。
4.评估失效的频度:对每个失效模式进行评估,确定其在过程中发生的概率或频次。
5.识别已有的控制措施和预防措施:列举已有的预防和控制措施,以评估其对失效模式的控制效果。
6.评估失效的检测度:确定失效模式是否可以在目前的检测过程中被发现。
7.进行风险评估:通过对失效模式的严重程度、频度和检测度进行组合评估,计算出风险优先级数(RPN)。
8.制定预防和纠正措施:根据风险优先级,确定应采取的预防和纠正措施,并将其确定为优先处理的问题。
9.追踪改进:追踪和记录已实施的预防和纠正措施,并评估其有效性。
三、PFMEA的优势和应用1.优势:PFMEA有助于企业识别和应对过程中的风险,提前预防可能导致质量问题的问题,并减少相关成本。
通过完善的PFMEA过程,可以提高产品质量、可靠性和客户满意度。
2.应用:PFMEA广泛应用于制造业,尤其在汽车、医疗器械和航空航天等高风险行业中。
它通常在新产品开发过程中进行,也可以应用于现有产品或过程的改进。
四、PFMEA存在的挑战和解决方法1.数据收集的困难:获取过程相关数据和知识的困难是PFMEA面临的主要挑战之一、解决方法包括培训和指导工作人员,建立数据收集和共享机制等。
PFMEA过程失效模式及后果分析

PFMEA过程失效模式及后果分析PFMEA(Process Failure Mode and Effects Analysis)过程失效模式及后果分析是一种常用的质量管理工具,用于评估和改进产品制造过程中的潜在问题和风险。
它旨在预测和预防可能导致产品失效的过程步骤。
1.确定过程步骤:首先,识别和定义产品制造过程中的每个关键步骤,包括原材料采购、加工、装配、测试等。
2.确定失效模式:对于每个过程步骤,识别可能导致失效的模式。
失效模式可以是设备故障、人为错误、材料质量问题等。
3.评估失效后果:对于每个失效模式,评估其可能导致的后果和影响。
后果可以涉及到产品质量问题、安全风险、客户满意度等。
4.定义风险优先级:根据失效模式的严重性、发生频率和检测能力,为每个失效模式分配一个风险优先级。
这可以帮助制定合理的风险控制策略。
5.制定改进计划:对于评估出的高优先级失效模式,制定相应的改进计划和控制措施。
这可能包括优化生产工艺、提供培训和教育、改进设备维护等。
6.实施和监控措施:执行改进计划,并监控其有效性。
定期对PFMEA进行更新,以反映过程改进和新的风险评估。
通过实施PFMEA,可以有效地识别和消除潜在的制造过程问题,并降低产品质量问题的风险。
下面以汽车制造业为例,具体分析PFMEA的应用。
在汽车制造过程中,每个制造步骤都可能存在潜在的失效模式。
例如,原材料采购环节可能存在材料质量问题的风险,加工环节可能存在操作错误或设备故障的风险,装配环节可能存在组装错误或安装不良的风险,测试环节可能存在测试不准确或设备故障的风险。
针对这些潜在问题,可以使用PFMEA来识别并评估其风险。
例如,在加工环节,识别可能的失效模式可能包括不正确的参数设置、设备故障、操作错误等。
然后,评估这些失效模式可能导致的后果和影响,如产品偏差、生产延误、设备故障等。
根据评估结果,确定失效模式的风险优先级,以便制定相应的改进计划和控制措施。
例如,对于评估为高风险的加工失效模式,可以采取以下改进措施:加强对操作员的培训和教育,确保他们正确操作设备和设置参数;增加设备维护和保养频率,以减少设备故障的风险;实施过程监控和自动化控制,以确保稳定的生产环境。
过程失效模式及后果分析管理办法

过程失效模式及后果分析管理办法过程失效模式及后果分析(Process Failure Modes and Effects Analysis,简称PFMEA),是一种常用于管理过程风险和改进的工具。
PFMEA通过对过程中可能发生的失效模式及其后果进行分析,提前识别出潜在问题,并采取相应措施降低风险。
下面将介绍PFMEA的管理办法。
一、PFMEA的管理目标PFMEA的管理目标是识别和分析过程中的失效模式及其潜在后果,评估失效发生的概率和影响程度,并制定相应的预防控制措施,降低风险。
二、PFMEA的管理步骤1.选择适当的团队成员:PFMEA的分析需要跨越多个职能领域,因此需要选择适当的团队成员,包括具有相关专业知识和经验的人员。
2.确定过程:明确要分析的过程范围和目标,包括过程流程、输入和输出等。
3.识别失效模式:团队成员通过头脑风暴和过程分析,识别可能导致过程失效的因素。
失效模式可以是物理性的、功能性的、行为性的等。
4.评估失效影响程度:对每个失效模式,评估其对过程和最终产品或服务的影响程度,包括安全性、质量、交付时间、成本等方面。
5.确定失效发生的概率:评估每个失效模式发生的概率,包括概率的频率、可能性等。
6.评估现有控制措施:评估当前过程中已存在的控制措施,对失效模式的控制程度,包括检验、测试等。
7.制定改进措施:根据评估结果,确定需要改进的控制措施,包括预防措施和检测措施,以降低失效发生的概率和影响程度。
8.实施改进措施:制定实施改进措施的计划,并跟踪监控改进效果。
9.更新PFMEA:根据实施改进措施的结果,修订和更新PFMEA,并确保团队成员了解改进措施的目标和具体要求。
三、PFMEA的管理原则1.整体团队参与:PFMEA需要全员参与,涉及到的问题通常跨越多个职能领域,需要充分调动团队的智慧和经验。
2.系统性分析:PFMEA需要从系统层面进行分析,识别可能的失效模式和其后果,并考虑多种因素对失效的影响。
失效模式与后果分析报告(PFMEA)控制程序

1.程序目的确定与产品生产过程相关的过程失效模式;评价和发现在各个生产过程中可能发生的失效模式的原因/机理,确定减少失效发生或找出失效条件的过程控制变量;为采取预防措施提供对策。
2.适用围适用于公司汽车钣金件产品冲压、焊接、表面处理等汽车零部件中新产品、产品的工程变更时的生产。
3.过程识别产品实现过程过程:产品策划过程过程活动:过程策划、设计与试制4.定义“PFMEA”是指由负责制造的多功能小组采用的一种分析技术,用来保证在可能的围已充分地考虑到并指明潜在失效及其相关的起因/机理。
5.主要职责和权限5.1 PFMEA多功能小组负责过程失效模式及后果分析、制定和跟踪措施。
5.2制造科等部门按策划的结果,实施和完善控制计划、作业指导书。
6.程序容6.1 由APQP多功能小组组长召集有关人员组成PFMEA多功能小组。
这个小组应包括与产品有关的技术、工艺、品质、生产、设备、营业等方面人员。
这个小组的主要执笔人应为负责本产品工艺的技术人员。
6.2 依据APQP策划中确定的过程(工艺)流程图,开展过程失效模式及后果分析(PFMEA),编写《过程失效模式及后果分析(PFMEA)表》。
客户若有特殊批准按客户要求和批准执行。
6.2.1写表头部分1)编号:按过程研究的顺序号编制。
2)项目名称:填写所分析产品/零件的正式名称。
3)过程责任部门:填写生产单位或生产班组名称。
4)编制人:填写主持编制本表人的、及所属部门名称。
5)零件号:填入要分析零件号。
6)关键日期:填写初次PFMEA预定完成的日期,该日期不应超过计划开始生产的日期。
7)PFMEA日期:填写编制PFMEA初稿日期及最新修改的日期。
8)主要参加成员:填写参与分析的多功能小组成员。
6.2.2 过程功能要求简单描述被分析的过程/工序,说明该过程/工序的目的,若某一过程/工序包括多个具有不同失效模式的过程/工序,应把这些过程/工序作为独立过程单列处理。
6.2.3 找出潜在失效模式1)潜在失效模式是指过程/工序中可能发生的不符合过程要求和/或设计意图的形式,是对具体过程/工序不符合要求的描述,它可能是引发下道过程/工序的潜在失效模式,也可能是上一道过程/工序潜在失效的后果。
过程失效模式及后果分析控制程序(中英文版本)
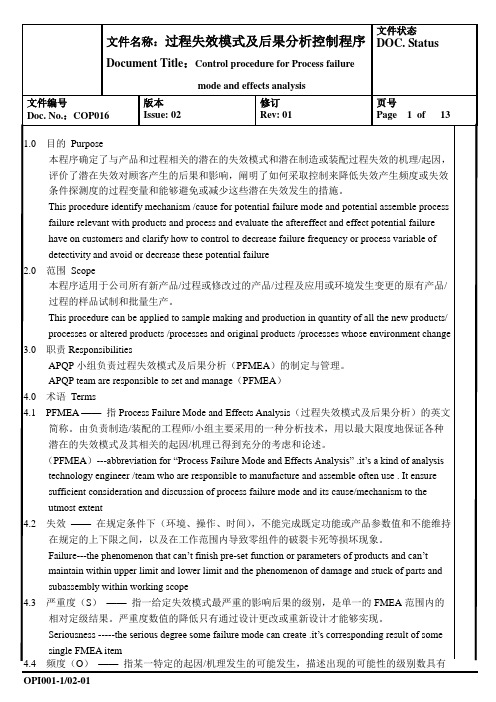
4.0术语Terms
4.1 PFMEA ——指Process Failure Mode and Effects Analysis(过程失效模式及后果分析)的英文
简称。由负责制造/装配的工程师/小组主要采用的一种分析技术,用以最大限度地保证各种
for product quality > before producing ,during or before feasibility phase when customers or
company have requirements and needs .and ask for team leader’s approval . when customers have
可能性。当纠正预防措施实施验证有效后,过程的风险(即RPN值)就会恢复正常(RPN
≤80)。届时,须修改过程失效模式及后果分析(PFMEA)中的风险系数(RPN值)
APQP team can analyze and evaluate risk of process in accordance with flow chart of that products
cause / mechanism , process defect or evaluating target of possibility of appearance of failure mode
in the following procedure . use the third kind of process control method to find out evaluation target
过程失效模式及后果分析控制程序(PMECA)

程序文件QP-XX-XX过程失效模式及后果分析控制程序1 目的:确定与产品在制造或装配过程失效的机理/起因,评价潜在失效对客户满意产生后果和影响,采取控制来降低失效产生频度或失效条件探测度的过程变量和能够避免或减少这些潜在失效发生的措施。
2 范围:适用于公司机械加工零组件的所有新产品/修改过的产品/及应用或环境发生变更的原有产品。
3 引用文件:QP-31 《新产品引入流程》QP-02 《质量记录》4 术语和定义:4.1 FMEA:指Process Failure Mode and Effects Analysis(过程失效模式及后果分析)的英文简称。
由负责制造/装配及检测的工程师(工艺员)/小组主要采用的一种分析技术,用以最大限度地保证各种潜在的失效模式及其相关的起因/机理已得到充分的考虑和论述。
4.2失效:在规定条件下(环境、操作、时间),不能完成既定功能或产品参数值和不能维持在规定的上下限之间。
4.3严重度(S):指一给定失效模式最严重的影响后果的级别,是单一的FMEA范围内的相对定级结果。
4.4频度(O):指某一特定的起因/机理发生的可能发生,描述出现的可能性的级别数具有相对意义,但不是绝对的。
4.5探测度(D):指在零部件离开制造工序或装配之前,利用第二种现行过程控制方法找出失效起因/机理过程缺陷或后序发生的失效模式的可能性的评价指标;或者用第三种过程控制方法找出后序发生的失效模式的可能性的评价指标。
4.6风险优先数(RPN):指严重度数(S)和频度数(O)及不易探测度数(D)三项数字之乘积。
5 职责:项目小组负责过程失效模式及后果分析(PFMEA)的制定与管理。
6 工作流程和内容:6.1、当客户或公司有需求和要求时,项组组依《新产品引入流程》在生产加工之前,在可行性阶段或之前进行过程失效模式及后果分析(PFMEA),经项目组长核准。
如客户有要求时,过程失效模式及后果分析(PFMEA)必须提交客户评审和批准。
过程失效模式及后果分析PFMEA
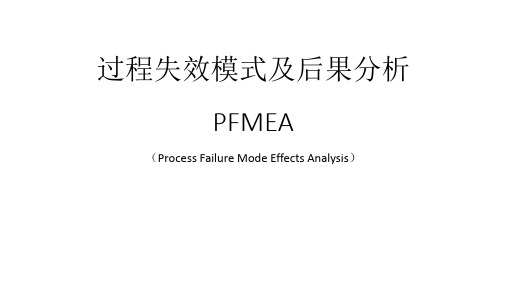
100~500 10~100
1~10
≥1.20
3
≥1.30
2
≥1.67
1
FMEA开发要点
8)当前控制方式
• 当前控制措施包括预防控制(error/mistake proofing or Statistical Process Control)和探测控制(post-process evaluation),“当前措施”应是在本过程或类似过程的中已落实的措施或已证明有效的措施。
Very High: 非常高 Persistent failures 持续失效
High:高 Frequent failures 频繁失效
Suggested PFMEA Occurrence Evaluation Criteria
Likely Failure Rates
以一百万块板里的缺陷计数
Ppk
Ranking
四、FMEA开发要点
下图展示了PFMEA模板。我们今天把理解最容易跑偏的板 块跟大家做一个梳理。
FMEA开发要点
1)功能要求 A 功能要求既包括过程特性和产品特性两大类。 • 过程特性: 过程参数及过程要求,即加工条件和加工参数 • 产品特性:产品规范,如尺寸\性能 B 对于同一个Operation上有多个操作动作的(an operation for a multistation machine or sequential process in one piece of equipment), 不管是人工操作还是极其操作,需要细化到每一个操作,比如:
Criteria: Severity of Effect 标准:后果严重性
This ranking results when a potential failure mode results in a final customer and/or a manufacturing/assembly plant defect. The final customer should always be considered first. If both occur, use the higher of the two severities.
生产件批准(PPAP)之过程失效模式及后果分析(PFMEA)

同一份设计或过程FMEA可适用于相似零件或材料的生产过程
3
进行PFMEA的开发,必须围绕顾客的特殊要求进行
4
PFMEA给出的严重度、频度和探测度的定级标准,用来对风险因素进行适当的区别
生产件批准(PPAP)之过程失效模式及后果分析(PFMEA)
定义/说明/要求/目的:
过程失效模式是指:由负责制造的工程师/小组为确保最大可能考虑并记录潜在的失效模式和相关的原因/机理而使用的分后果分析。
检查表:
编号
检查内容
1
组织必须依据手册的要求进行过程失效模式及后果分析开发
过程失效模式及后果分析(PFMEA)
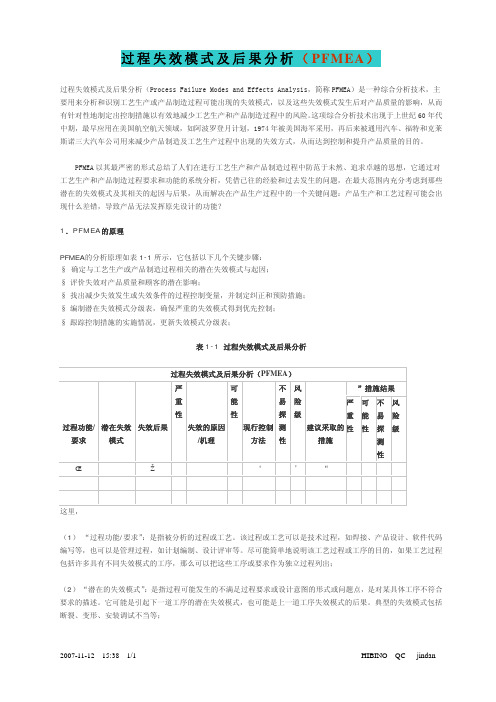
过程失效模式及后果分析(PFMEA)过程失效模式及后果分析(Process Failure Modes and Effects Analysis,简称PFMEA)是一种综合分析技术,主要用来分析和识别工艺生产或产品制造过程可能出现的失效模式,以及这些失效模式发生后对产品质量的影响,从而有针对性地制定出控制措施以有效地减少工艺生产和产品制造过程中的风险。
这项综合分析技术出现于上世纪60年代中期,最早应用在美国航空航天领域,如阿波罗登月计划,1974年被美国海军采用,再后来被通用汽车、福特和克莱斯诺三大汽车公司用来减少产品制造及工艺生产过程中出现的失效方式,从而达到控制和提升产品质量的目的。
PFMEA以其最严密的形式总结了人们在进行工艺生产和产品制造过程中防范于未然、追求卓越的思想,它通过对工艺生产和产品制造过程要求和功能的系统分析,凭借已往的经验和过去发生的问题,在最大范围内充分考虑到那些潜在的失效模式及其相关的起因与后果,从而解决在产品生产过程中的一个关键问题:产品生产和工艺过程可能会出现什么差错,导致产品无法发挥原先设计的功能?1.PFMEA的原理PFMEA的分析原理如表1-1所示,它包括以下几个关键步骤:§确定与工艺生产或产品制造过程相关的潜在失效模式与起因;§评价失效对产品质量和顾客的潜在影响;§找出减少失效发生或失效条件的过程控制变量,并制定纠正和预防措施;§编制潜在失效模式分级表,确保严重的失效模式得到优先控制;§跟踪控制措施的实施情况,更新失效模式分级表;表1-1 过程失效模式及后果分析过程失效模式及后果分析(PFMEA)”措施结果过程功能/要求潜在失效模式失效后果严重性失效的原因/机理可能性现行控制方法不易探测性风险级建议采取的措施严重性可能性不易探测性风险级ŒŽ‘ ’“这里,(1)“过程功能/要求”:是指被分析的过程或工艺。
该过程或工艺可以是技术过程,如焊接、产品设计、软件代码编写等,也可以是管理过程,如计划编制、设计评审等。
过程失效模式和后果分析教材

过程失效模式和后果分析教材引言过程失效模式和后果分析(Process Flure Mode and Effects Analysis,简称PFMEA)是一种系统的方法,用于识别过程中可能出现的失效模式,评估其后果,并采取相应的纠正和预防措施。
该方法可以帮助组织识别潜在的风险,减少失效对生产质量和成本的影响,提高过程的可靠性和稳定性。
本教材将介绍PFMEA的基本概念、步骤和工具,帮助读者理解和应用这一方法来改进和优化过程。
1. PFMEA概述1.1 定义PFMEA是一种通过具体的方法和步骤,对过程中可能出现的失效模式进行分析和评估的工具。
它可以帮助组织识别潜在的风险,评估失效对产品质量的影响,并采取相应的纠正和预防措施。
1.2 作用PFMEA的主要作用是:•识别和评估过程中可能发生的失效模式;•评估失效对产品质量和成本的影响;•提供改进和纠正措施的建议;•改善过程的可靠性和稳定性。
2. PFMEA步骤2.1 选择标准过程在进行PFMEA之前,需要选择一个标准过程作为分析的对象。
标准过程应该具有代表性,包括所有的关键步骤和环节。
2.2 列出过程步骤将选定的标准过程的所有步骤和环节逐一列出,并对其进行编号。
针对每个过程步骤,识别可能出现的失效模式。
失效模式可以是过程中的错误、缺陷或不符合要求的情况。
2.4 评估失效后果对每个失效模式,评估其对产品质量和成本的影响。
可以使用一定的评估指标,如风险优先数(Risk Priority Number)来对失效后果进行量化评估。
针对每个失效模式,识别可能导致该失效模式发生的潜在原因。
潜在原因可以是设计、材料、设备、操作等方面的问题。
2.6 制定纠正和预防措施基于潜在原因的分析,制定相应的纠正和预防措施,以防止失效模式的发生或减少其影响。
2.7 实施措施并跟踪有效性将制定的纠正和预防措施实施到实际过程中,并跟踪其有效性。
如果措施未能达到预期效果,需要重新评估并调整相应措施。
过程潜在失效模式及后果分析(PFMEA)管理规定CN

过程潜在失效模式及后果分析(PFMEA)管理规定CN质量管理体系?管理办法过程潜在失效模式及后果分析(PFMEA)管理规定编号:第A0版编制:标审:审核:批准:2008年06月13日发布 2008年06月16日实施有限公司发布中国文件更改记录1、目的1.1根据过程失效模式,分析出潜在失效原因,研究该项失效模式对下工序和最终用户会产生什么影响。
1.2失效分析用于找出零件、组件或系统的潜在弱点,以便技术、制造、质量等部门采取可行对策,降低产品的失效风险,最大限度地保证产品能满足客户的要求和期望。
2、适用范围本程序适用于xxxxx有限公司新产品进入批量生产前阶段,以及工艺改进阶段。
3、职责3.1供应链管理部门工艺人员、研发工程师/系统工程师、质量部工程师、售后工程师及供应链管理部门经理共同组成过程潜在失效模式及后果分析小组;3.2研发工程师和系统中心工程师给供应链管理部门工艺人员提供工艺过程潜在失效模式分析的技术支持;3.3销售与市场部售后人员应及时将现场故障情况及客户反馈反映给质量部门及供应链管理部门,协助其进行产品工艺过程潜在失效模式分析;3.4供应链管理部门车间应协助工艺人员和质量工程师完成改进措施。
4、过程控制及流程4.1过程失效模式的定义过程失效模式是一种按小组进行工作的严格的预防性分析技术,在失效分析中,首先要明确产品的失效是什么,否则产品的数据分析和可靠度评估结果将不一样。
一般而言,失效是指:4.1.1在规定条件下(环境、操作、时间),被分析对象不能完成既定功能。
4.1.2在规定条件下,产品参数值不能维持在规定的上下限之间。
4.1.3产品在工作范围内,导致零组件的破裂、断裂、卡死、损坏等现象。
4.2过程失效模式分析的内容4.2.1过程功能:根据附件表格,依次填入要被分析的过程或工序。
尽可能简单地说明该工艺过程或工序的目的,当过程包含不同失效模式工序(如:组装、布线),可将这些工序作为独立的过程分析其失效模式。
过程失效模式与后果分析(PFMEA)管制程序
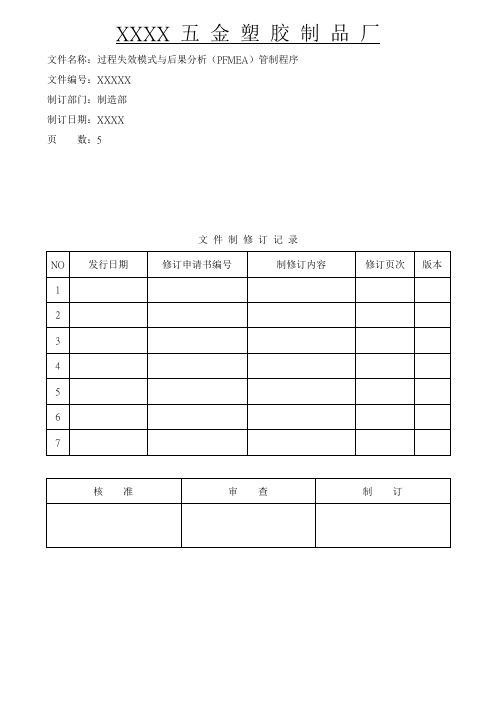
XXXX 五金塑胶制品厂文件名称:过程失效模式与后果分析(PFMEA)管制程序文件编号:XXXXX制订部门:制造部制订日期:XXXX页数:5文件制修订记录1目的确定与汽车零件産品生産过程相关的过程失效模式,评价和发现在各个生産工序中失效的原因,确定减少失效发生或找出失效条件的程序控制变量,编制失效模式分级表,爲采取矫正和预防措施提供对策。
2适用范围适用于本公司所生産的汽车零件産品。
3权责3.1制造部汽车零件生産车间:负责过程失效模式和后果分析的制定及实施。
3.2品管部:负责对PFMEA活动进行跟踪监察。
4定义PFMEA—过程失效模式和后果分析5作业内容5.1 由制造部、品管部有关人员组成PFMEA分析小组,由总经理批准任命。
5.2 PFMEA分析小组依据工艺流程图,确定哪些过程是高风险过程,针对高风险过程做PFMEA 分析,记录于〈过程潜在失效模式及后果分析(PFMEA)表〉。
在一年中对每种産品至少做一次PFMEA。
5.3按下列要求填写PFMEA表格:5.3.1PFMEA编号:按过程号编号。
5.3.2项目名称:填入所分析的项目名称。
5.3.3过程责任:填入生産部门或生産班组名称。
5.3.4 编制人:填入负责编制的人员姓名及所在部门。
5.3.5 车型号/部件类型/零件号:填入要分析的车型/ 部件类别号/零件号。
5.3.6 关键日期:填写初次FMEA预定完成的日期,该日期不应超过计划开始生産的日期。
5.3.7 FMEA日期:填写编制PFMEA初稿日期及最新修订的日期。
5.3.8 主要参加人:填写执行此项工作的责任部门和负责人(参与人)。
5.3.9 过程功能/要求:简单描述被分析的过程或工序,说明该过程或工艺的目的,这些过程应该是独立的过程。
5.3.10潜在失效模式:指过程中可能发生的不符合过程要求和/或设计意图的形式,是对具体工序不符合要求的描述,客观存在可能是引发下道工序的潜在失效模式,也可能是上道工序潜在失效的后果。
PFMEA过程潜在失效模式和后果分析管理程序

版本修改条款1.目的通过分析、预测设计、过程中潜在的失效,研究失效的原因及其后果,并采取必要的预防措施,避免或减少这些潜在的失效,从而提高产品、过程的可靠性。
2.适用范围适用于公司过程设计PFMEA活动的控制。
3.职责3.1研发中心(PE)负责组织成立PFMEA(过程FMEA)小组,负责PFMEA活动的管理。
3.2研发中心、工艺、品质、生产部、业务部等部门指定人员参加DFMEA小组与PFMEA小组。
必要时,由品质邀请供应商、客户参加。
3.3PFMEA小组负责制定《PFMEA潜在失效后果严重程度(S)评价标准》、《PFMEA潜在失效模式发生频度(O)评价标准》、《PFMEA潜在失效模式发现难度(D)评价标准》。
并负责准备《DFMEA和PFMEA的措施优先级(AP)》。
4.工作程序4.1过程FMEA的开发实施4.1.1PFMEA实施的时机4.1.1.1按APQP的计划进行PFMEA。
4.1.1.2在出现下列情况时,PFMEA小组应在工装准备之前,在工艺文件(作业指导书)最终定稿之前,针对从单个零件到总成的所有制造工序,开展PFMEA活动:①开发新产品/产品更改;②生产过程更改;③生产环境/加工条件发生变化;④材料或零部件变化。
4.1.2PFMEA实施前的准备工作4.1.2.1研发中心工艺(PE)牵头成立PFMEA(过程FMEA)小组,研发中心工艺(PE)、品质、生产部、物料部采购等部门指定人员参加PFMEA小组,必要时,由品质邀请供应商、客户参加。
4.1.2.2在PFMEA活动实施前,PFMEA小组应制定出《PFMEA潜在失效后果严重度(S)评价标准》、《PFMEA潜在失效模式频度(O)评价标准》、《PFMEA潜在失效模式探测度(D)评价标准》。
a)PFMEA小组根据FMEA手册参考标准,确定出本公司的实际示例。
b)在工艺水平或生产环境发生变化时,应根据需要适时修订以上标准。
4.1.2.3PFMEA小给负责准备《DFMEA和PFMEA的措施优先级(AP)》。
PFMEA过程失效模式及后果分析

PFMEA过程失效模式及后果分析PFMEA(Process Failure Mode and Effects Analysis)是一种通过系统地识别和评估潜在的失效模式及其后果来预防产品和过程问题的方法。
它有助于组织在设计和开发阶段就发现并解决潜在的问题,从而提高产品质量和生产效率。
在这篇文章中,我们将重点讨论PFMEA过程中的失效模式及其后果分析。
失效模式是指导致产品或过程失效的特定原因或机制。
它可以是由于设计缺陷、材料问题、加工误差、操作失误等引起的。
失效模式常常以不同的方式出现,在不同的环境下可能会有不同的后果。
在进行PFMEA过程中,首先需要识别潜在的失效模式。
这可能涉及到对产品、过程和相关文档的仔细研究,以了解可能存在的问题。
接下来,需要对每个失效模式的影响进行评估,这也就是后果分析。
后果分析可以帮助确定失效对产品质量、生产效率和安全性等方面造成的影响,从而决定需要采取的预防措施。
在进行PFMEA过程失效模式及后果分析时,以下是一些常见的失效模式和其可能的后果:1.设计缺陷:-可能的后果:产品性能不达标、产品寿命缩短、安全隐患、产品被召回等-预防措施:加强设计评审、使用可靠的设计工具、进行模拟测试等2.材料问题:-可能的后果:产品强度不足、耐腐蚀性差、产品寿命缩短等-预防措施:严格选择、测试和审查材料供应商、加强入库检查等3.加工误差:-可能的后果:产品尺寸偏差、表面质量不良、装配困难等-预防措施:加强生产工艺控制、使用先进的制造设备、严格执行质量标准等4.操作失误:-可能的后果:生产过程中出现错误、设备损坏、人员伤亡等-预防措施:提供员工培训、实施作业规程、设立安全警示标志等除了上述提到的失效模式和后果,还有许多其他可能的情况需要被考虑和分析。
在进行PFMEA过程中,团队成员需要全面了解产品和过程,积极参与讨论和决策,以确保有效识别和评估潜在的问题。
此外,通过对失效模式及后果进行分析,团队还可以确定应对措施的优先级和实施计划。
- 1、下载文档前请自行甄别文档内容的完整性,平台不提供额外的编辑、内容补充、找答案等附加服务。
- 2、"仅部分预览"的文档,不可在线预览部分如存在完整性等问题,可反馈申请退款(可完整预览的文档不适用该条件!)。
- 3、如文档侵犯您的权益,请联系客服反馈,我们会尽快为您处理(人工客服工作时间:9:00-18:30)。
第7.4章制造过程失效模式及影响分析(PFMEA)管理程序1目的确定与产品制造相关的过程失效模式;评价和发现在各个制造工序中失效的原因,确定减少失效发生或找出失效条件的过程控制变量;编制失效模式分级表,为采取纠正和预防措施提供对策。
2范围本标准适用于各公司新产品、改型产品及因环境发生变更时的样件试制和批量生产过程的失效模式及影响分析(PFMEA)。
3职责3.1各公司技术部负责制订制造过程失效模式及影响分析(PFMEA)。
3.2各公司APQP小组负责对PFMEA的评审。
3.3各公司品质部负责对PFMEA实施的跟踪监督。
3.4各公司办公室负责PFMEA的发放、保管。
3.5各公司相关车间负责PFMEA的实施。
3.6各公司负责技术的副总经理负责PFMEA的批准。
4程序4.1成立PFMEA小组各公司在APQP过程中,APQP小组组长应从小组成员中选择具有PFMEA知识的人员组成PFMEA小组,并报本公司负责技术的副总经理批准。
4.2制定PFMEA的依据和范围各公司PFMEA小组应依据在制造过程设计和开发中编制的产品制造过程流程图(即产品工序路线图、工序流程图)、产品及过程的特性,特别是特殊特性、相关的法律法规,针对其每一过程(工序)进行PFMEA的开发设计。
4.3PFMEA表的格式及内容见表1。
4.4PFMEA表的表头(A-H)的填写4.4.1FMEA编号(A)填写一个识别FMEA文件的一组数字和/或字母。
公司采用以公司部门代号、PFMEA、两位年代号、三位顺序号或各公司代号、部门代号、PFMEA、两位年代号、三位顺序号的顺序组合进行FMEA编号。
各公司、部门代号见《文件发放范围审批表》。
例1:公司技术部2009年编制第10号PFMEA,FMEA编号表示为:JS PFMEA09010。
例2:南京川页机械有限公司技质部2009年编制第16号PFMEA,FMEA编号表示为: NJJZ PFMEA09016。
4.4.2项目(B)填写受分析过程的系统,子系统或零部件名称和编号。
如CM10燃油箱总成、SC1016FA 货箱总成等。
4.4.3过程职责 (C)填写过程设计的OEM(整车厂),部门或班组;适用时,还需填写供应商的名称(如定州市顺达机械有限公司)。
4.4.4车型年/项目(D)在知道的情况下,填入会使用到或者会受分析的过程(如果知道)影响的预期车型年和项目。
4.4.5关键日期(E)填入初次FMEA应完成的日期,不能超过计划的生产日期。
如果是供应商,则此日期不能超过顾客要求的生产件批准程序(PPAP)的提交日期。
FMEA日期(原始)(F) 填入原始FMEA的完成日期,以及最近的修订日期。
4.4.6核心小组(G)填入负责开发PFMEA的小组成员。
成员的联系方式【如姓名、组织(公司)、电话、E-mail】可以记录在另一份补充文件内。
4.4.7编制人(H)填入准备PFMEA的设计人员的姓名,联系方式及设计人员的所属组织(公司)。
5 PFMEA表格的内容(a-n)解释及填写5.1过程步骤(a1):根据编号的过程和术语,填入受分析的过程步骤或操作标识。
例如:填入编号和识别符(比如:工序的顺序号或名称)。
过程编号方案、排列顺序和术语应当和过程流程图内的一致,确保其可追溯性,以及与其它文件(如控制计划,作业指导书等)的联系。
返工和返修操作也应当包括在内。
5.2过程功能(a1)填入与每个受分析的过程步骤/操作相应的过程功能。
过程功能描述的是操作的目的。
建议使用风险分析来限制步骤数量,使其仅包括那些增值看起来对产品有负面影响的步骤。
如果有多个与规定操作有关的受分析的过程功能(如燃油箱装配过程,包括装单向阀、装加油软管、装通气软管、装双钢丝环箍、装卡箍、油泵口封胶带等多个过程功能),每个过程功能应当和各自的“要求”相符合,来帮助相关失效模式的开发。
5.3要求(a2)列出每个受分析的过程步骤/操作的过程功能的要求。
要求是对规定过程的输入,以期达到设计目的和其他顾客要求。
如果有关于规定功能有多个要求,每个要求应当和关联的失效模式相符合,从而帮助分析。
5.4 潜在失效模式(b)潜在失效模式是指过程可能潜在地无法满足过程要求(包括设计目的)的状态。
在准备FMEA时,假定即将接收的零件/材料是正确的。
当有历史数据显示进货零件质量有差异时,FMEA小组可以给出例外。
小组还应假定产品的基础设计是正确的;但是,如果设计问题可能导致对过程的担忧,应当将这些问题交给设计小组进行沟通解决。
根据过程要求(比如:在过程流程图里的记录),列出特定操作的潜在失效模式。
假定失效模式可能会发生,但不是必然会发生。
潜在失效模式应当用专业技术术语来描述,不必描述成顾客注意得到的现象。
请参见表2示例:PFMEA设计人员在“要求”已经得到妥善定义后,就能通过确定规定要求是否被满足的状态来识别潜在失效模式。
每个要求都可能有多个失效模式。
单个要求内若有大量的失效模式,这意味着要求没有被妥善定义。
各公司在验证潜在失效模式的完整性时,可以通过小组头脑风暴来评审以往的运行不良、关注点、拒收或报废,或对相似过程的比较,或与相似零部件的相关顾客的索赔等方式进行。
表1 潜在过程失效模式及影响分析表(过程FMEA表)Q/SDJX-JS-▲▲☆☆□□□-□□□□ FMEA编号:A页码:第页,共页项目: B 过程职责: C 编制人:H车型年/项目: D 关键日期: E FMEA日期(原始): F编制/日期:审核/日期:批准/日期:表2 13D燃油箱油箱上体拉伸成型的过程步骤/功能、要求和潜在失效模式示例弯曲;毛刺;起皱;裂纹;裂缝;破裂;断裂;变形;棱线模糊;脏污(油污);锈蚀;拉延深度不够;尺寸不符;孔位偏差;孔径偏差;孔未加工;成型不到位;焊接不牢;焊穿;焊接位置不符;焊接角度不符;焊接砂眼;焊接气孔;清洁度超标;表面处理油污未净;涂层厚度不符;涂层硬度低;涂层附着力差;漏喷;流挂;颗粒;漏装;错装;装配不到位;产品未粘贴合格证;合格证粘贴不牢;燃油箱未粘贴3C标识;3C标识粘贴不牢;3C标识粘贴位置不符等。
5.5失效潜在影响(c)失效潜在影响是指由顾客察觉出的失效模式的影响。
PFMEA设计人员应根据顾客可能发现或经历到的情况来描述失效的影响。
这里所指的顾客可以是下一步操作(即下一道工序),后续操作(即后续工序)或场所,总装厂,经销商和车辆使用者。
因此,在评估失效潜在影响时,应当将每一种顾客都考虑进去。
如果失效模式可能对安全造成影响,或引起法律的不符合,PFMEA设计人员应在PFMEA里清楚的标明。
针对最终顾客,应当根据产品或系统性能来说明影响。
如果顾客是下一步操作、后续操作/场所,应当就过程(工序)/操作性能来说明影响。
请参见表3示例:为了确定潜在影响,PFMEA设计人员应考虑下列问题:a)潜在失效模式是否物理性阻碍了下道工序和/或后续过程操作,或者对设备,或者对操作人员构成潜在危险?它包括在任何后续顾客的设施处,或匹配零部件之间的无法装配,或对接合的影响。
遇到此类情况,则需评估对制造的影响,而且不需要进一步分析;若不是,则转到b)。
当潜在失效模式发生在外部顾客(如总装厂)设施处时,PFMEA设计人员应予说明。
本公司属于a)类的问题包括但不限于:无法紧固;无法安装;无法配合;无法焊接;无法连接;影响加工;影响装配;增加模具/工装磨损;损坏设备;增加额外工序;降低后续效率;危害操作人员安全等。
b)对最终顾客(使用者)的潜在影响是什么?PFMEA设计人员应考虑最终顾客会察觉或经历到什么。
本公司对最终顾客的潜在影响包括,但不限于:非正常功效(如燃油箱漏油、加不进油等);使用费力;异响;外观不良;阻力过大;表3 13D燃油箱油箱上体拉伸成型要求、潜在失效模式及影响示例加发动机磨损和进油);影响使用;顾客不满意;违反法规(如燃油箱未贴3C标识)等。
c)如果影响还未波及到最终顾客,就被发现,会产生什么影响?PFMEA设计人员应考虑到对当前场所和接收场所(公司生产现场或总装现场)的潜在影响。
如:生产线中断;停止产品发运;库房堆积占用;返工/返修;产品报废;降低生产线速度;为了维持要求的生产线速率,增加人力资源;在考虑问题b)和问题c)时,如果有不止一个的潜在影响,均应将其全部列出;但是,出于分析的目的,在记录严重度等级时,只需考虑最坏的情况。
5.6严重度(S)(d)严重度是对一个已假定的失效模式的最严重影响的评价等级。
严重度在单个PFMEA范围内是一个相对等级。
各公司的PFMEA设计小组在评估严重度时,即使由于单个过程分析而受到调整,也应一致性地使用《潜在失效模式与影响分析FMEA》(第四版)推荐的PFMEA严重度评估标准,请详见表4。
《潜在失效模式与影响分析FMEA》(第四版)不建议调整等级为9和10的评级标准。
等级为1的失效模式,不应当再进一步分析。
表4 严重度评估标准这一栏可以用来强调失效模式的优先级,或者需要额外的工程评估的原因。
还可用来分类需要附加过程控制的零部件、系统、子系统一些特殊产品或过程特性(如:关键、重要、严重、显著)。
特殊产品或过程特殊特性符号及其使用,可根据顾客的特殊要求予以确定。
在PFMEA内识别到严重度等级为9或10的特殊特性时,由于会影响到工程文件,所以,各公司的PFMEA设计人员应将此特殊特性书面通知相关负责设计的人员(如工艺设计人员、检验文件编制人员等),以便在制定相应的工程文件及控制项目时进行分类的标识。
5.8潜在失效原因(f)潜在失效原因是对失效是如何发生的过程的说明,应被描述为可以纠正、控制的问题。
潜在失效原因可能是一个设计或过程不足的显示,其结果是失效模式。
各公司的PFMEA设计人员应尽可能将每个失效模式的每个潜在原因予以识别并记录。
原因应当记录得尽量详细、简明和完整。
将原因分别独立列出,就可以对每个原因进行重点分析,从而可以产生不同的衡量、控制和措施计划。
一个失效模式可能会有一个或多个原因,所以,在表格内有多行可以填写原因。
各公司在设计PFMEA时,PFMEA设计小组应当假定即将接受的零件/材料是正确的。
在有历史数据表明零件质量有差异时,小组可作例外处理。
应具体地列出错误或误操作情况(如油压机顶出缸压力不足,喷枪堵塞,堵头未安装等)。
不应使用模棱两可的用词(如设备原因;操作人员失误;喷枪影响等)。
原因与控制示例,请参见表6。
各公司比较典型的潜在失效原因包括但不限于:定位不准;定位器松动;油压机压边压力过大或过小;顶出缸压力过大或过小;模具间隙过大或过小;模具形状不符;冲床闭模高度过高或过低;喷涂压力不足;喷枪喷头堵塞;喷涂量不足;喷涂表面不清洁;喷涂材料质量不符合要求;烘烤温度过高或过低,烘烤时间过长或过短;防护不良;标识不明;外购(外协)件不符合要求;监视测量装置失准;焊接表面不清洁或有异质镀层(涂层);点焊参数(电流、电压、气压、加压周期、焊接周数、维持周数、电极直径)不正确;CO2保护焊参数(电流、电压、气体流量、调节档位、焊丝直径)不正确;滚焊参数(电流、电压、气压、加压周数、焊接周数、维持周数、电极直径、电极间隙、圆度)不正确;盛具摁伤;运输撞伤;拖拉划伤等。