埋弧焊钢管焊缝余高的控制
直缝埋弧焊管焊缝余高控制措施

Ab s t r a c t :I n t h i s a r t i c l e ,i t a n ly a z e d a d v e r s e e f f e c t o f h i g h we l d r e i n f o r c e me n t o f S AW L p i p e o n c o n t r o l l i n g we l d q u a l i t y , r e d u c i n g p r o d u c t i o n c o s t ,e l i mi n a t i n g p o t e n t i a l r i s k d u in r g u s a g e .I t a l s o i n t r o d u c e d c o n t r o l t a r g e t a n d ma i n t e c h n i c a l p a r a me t e r s o f S AW L p i p e w e l d r e i n f o r c e me n t . By s t u d y i n g t h e r e l a t i o n s h i p b e t we e n g r o o v e s h a p e, we l d i n g p r o c e s s p a r a me t e r s a n d we l d mo r p h o l o g y,t h e c o n t r o l me a s u r e s f o r w e l d r e i n f o r c e me n t w e r e p r o v i d e d . T h e a p p l i c a t i o n r e s u l t s s h o w e d t h a t t h e s e
埋弧焊管焊接主要缺陷及防控措施
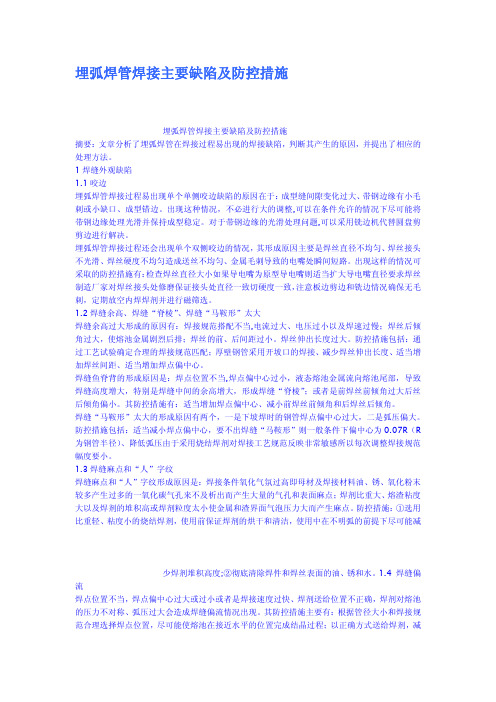
埋弧焊管焊接主要缺陷及防控措施埋弧焊管焊接主要缺陷及防控措施摘要:文章分析了埋弧焊管在焊接过程易出现的焊接缺陷,判断其产生的原因,并提出了相应的处理方法。
1焊缝外观缺陷1.1咬边埋弧焊管焊接过程易出现单个单侧咬边缺陷的原因在于:成型缝间隙变化过大、带钢边缘有小毛刺或小缺口、成型错边。
出现这种情况,不必进行大的调整,可以在条件允许的情况下尽可能将带钢边缘处理光滑并保持成型稳定。
对于带钢边缘的光滑处理问题,可以采用铣边机代替圆盘剪剪边进行解决。
埋弧焊管焊接过程还会出现单个双侧咬边的情况,其形成原因主要是焊丝直径不均匀、焊丝接头不光滑、焊丝硬度不均匀造成送丝不均匀、金属毛刺导致的电嘴处瞬间短路。
出现这样的情况可采取的防控措施有:检查焊丝直径大小如果导电嘴为原型导电嘴则适当扩大导电嘴直径要求焊丝制造厂家对焊丝接头处修磨保证接头处直径一致切硬度一致,注意板边剪边和铣边情况确保无毛刺,定期放空内焊焊剂并进行磁筛选。
1.2焊缝余高、焊缝“脊棱”、焊缝“马鞍形”太大焊缝余高过大形成的原因有:焊接规范搭配不当,电流过大、电压过小以及焊速过慢;焊丝后倾角过大,使熔池金属剧烈后排;焊丝的前、后间距过小。
焊丝伸出长度过大。
防控措施包括:通过工艺试验确定合理的焊接规范匹配;厚壁钢管采用开坡口的焊接、减少焊丝伸出长度、适当增加焊丝间距、适当增加焊点偏中心。
焊缝鱼脊背的形成原因是:焊点位置不当,焊点偏中心过小,液态熔池金属流向熔池尾部,导致焊缝高度增大,特别是焊缝中间的余高增大,形成焊缝“脊棱”;或者是前焊丝前倾角过大后丝后倾角偏小。
其防控措施有:适当增加焊点偏中心、减小前焊丝前倾角和后焊丝后倾角。
焊缝“马鞍形”太大的形成原因有两个,一是下坡焊时的钢管焊点偏中心过大,二是弧压偏大。
防控措施包括:适当减小焊点偏中心,要不出焊缝“马鞍形”则一般条件下偏中心为0.07R(R 为钢管半径)、降低弧压由于采用烧结焊剂对焊接工艺规范反映非常敏感所以每次调整焊接规范幅度要小。
焊缝余高处理技巧

焊缝余高处理技巧焊缝余高处理技巧在焊接工艺中,焊缝余高是指焊接过程中产生的高出基材表面的物质,它是焊接过程中不可避免的产物。
焊缝余高的处理对于保证焊接质量和结构强度至关重要。
本文将介绍一些处理焊缝余高的技巧,帮助你更好地理解和应用。
一、焊缝余高的成因焊缝余高的形成原因主要有以下几个方面:1. 关于焊接参数的选择不当:焊接参数包括焊接电流、焊接速度、焊丝直径等。
如果选择不当,容易导致焊接过程中产生过多的熔汁,从而形成焊缝余高。
2. 焊接工艺不合理:焊接工艺中的预热、焊前焊后处理等环节,如果操作不当,也会造成焊缝余高。
3. 极性选择不当:在焊接过程中,焊接电流的极性选择对焊缝余高的形成有一定影响。
错误的极性选择容易导致焊缝余高。
二、焊缝余高处理的技巧下面是一些处理焊缝余高的常用技巧,供参考:1. 合理选择焊接参数:在进行焊接过程中,要根据具体情况合理选择焊接参数,包括电流、速度、焊接方式等。
通过控制参数,可以有效减少焊缝余高。
2. 增加焊缝间距:在焊接时适当增大焊缝之间的间距,可以有效降低焊缝余高的形成。
这是因为增加间距可以使熔汁更好地流向焊缝,减少溢出。
3. 提高焊接质量:焊接质量的提高可以减少焊缝余高的出现。
包括焊接前的清洁处理、焊机的校准等都能够提升焊接质量,减少焊缝余高。
4. 采用合适的焊接工艺:合适的焊接工艺对于焊缝余高的控制至关重要。
在高要求焊接表面质量的场合,可以选择使用惰性气体保护焊(TIG焊)进行焊接,以减少焊缝余高的形成。
5. 进行适当的后处理:焊接完成后,适当的后处理也是减少焊缝余高的重要步骤。
可以利用砂轮等工具对焊接缝进行打磨,使其与基材表面平整。
还可以进行热处理或残余应力消除处理等手段,进一步提升焊接质量。
三、对焊缝余高的观点和理解焊缝余高的存在是焊接不可避免的部分,然而通过合理的处理技巧和控制措施,我们可以降低其产生的概率和影响。
对焊缝余高的处理要在焊接过程中进行全面的考虑,从选择焊接参数到进行后处理,每一步都需要精细的操作和合理的设计。
焊缝余高的要求与处理办法
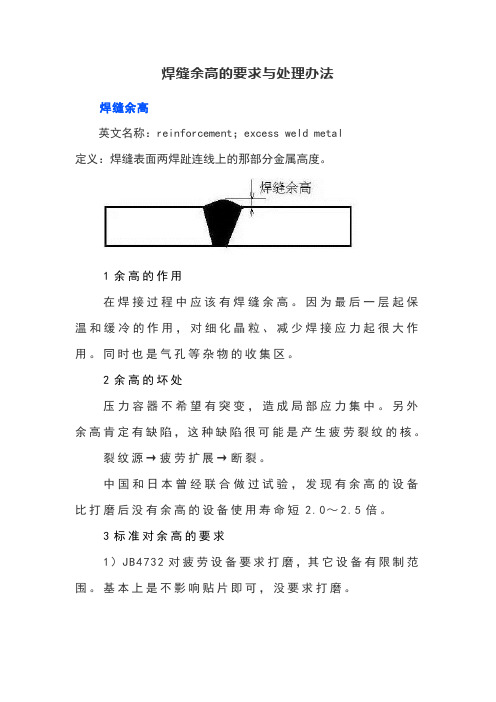
焊缝余高的要求与处理办法焊缝余高英文名称:reinforcement;excess weld metal定义:焊缝表面两焊趾连线上的那部分金属高度。
1余高的作用在焊接过程中应该有焊缝余高。
因为最后一层起保温和缓冷的作用,对细化晶粒、减少焊接应力起很大作用。
同时也是气孔等杂物的收集区。
2余高的坏处压力容器不希望有突变,造成局部应力集中。
另外余高肯定有缺陷,这种缺陷很可能是产生疲劳裂纹的核。
裂纹源→疲劳扩展→断裂。
中国和日本曾经联合做过试验,发现有余高的设备比打磨后没有余高的设备使用寿命短 2.0~2.5倍。
3标准对余高的要求1)JB4732对疲劳设备要求打磨,其它设备有限制范围。
基本上是不影响贴片即可,没要求打磨。
2)中国国家标准GB150是这样规定的,见图表格与图:4欧美国家对余高的要求打磨。
外观质量好是国外产品畅销的原因之一,另外打磨之后能防环境腐蚀、避免产生过大的应力集中、延长了焊缝的使用寿命。
5余高的处理建议提倡打磨,确实好。
标准是最低要求,所以建议对重要设备或投资较大的设备进行打磨,对投资小的设备就没有必要进行打磨了。
6焊缝余高过大的危害焊趾处易形成应力腐蚀裂纹对接接头的应力集中主要是焊缝余高引起的,对接接头的焊缝,其焊趾处的应力最大。
焊缝的余高愈大,应力集中程度愈严重,焊接接头的强度反而会降低。
焊后削平余高,只要不低于母材,减少应力集中,有时反而可以提高焊接接头的强度。
7外焊缝余高大,不利于防腐作业时如采用环氧树脂玻璃布进行防腐,外焊缝余高大,将使焊趾处不易压牢。
同时,焊缝越高则防腐层就越应加厚,因标准规定防腐层的厚度是以外焊缝的顶点为基准测算的,这就加大了防腐成本。
8内焊缝余高大,增加输送介质的能源损失输送用焊管内表面若未做涂层防腐处理时,其内焊缝的余高大,则对输送介质的摩擦阻力也大,由此将使输送管线的能耗增加。
9焊缝余高的控制措施调整好焊接线能量检查焊接线能量是否合适,一般用焊接接头的酸蚀样来检查。
锅炉和压力容器埋弧自动焊焊缝余高超标原因及对策

锅炉和压 力容器埋弧 自动焊焊缝余 高超标原 因及对 策
郭佳琦 ( 朝阳 市 特 种设 备 监 督 检 验所 ’
摘要 : 焊接过程的机械化和 自动化 , 是近代焊接技术 的一项 重要 成 型使 这 些参 数 的关 系息 息相 关 , 只 有把 这 些参数 进 行合
发展 。 它不仅标志着更高的焊接生产效率和 更好 的焊接质量 , 而且还 理 匹配才 能保证焊 缝 的质 量。 大大改善了生产 劳动条件。 而 自动 焊又 分为明弧和埋弧两种 。 本 文则 2焊缝余高超标的原因 是 重点介绍 了埋 弧在焊接锅炉、压 力容器等的过程 中可能出现 的焊
一
标, 一种 是 断续超 标 。 造 成这种 现 象 的原 因有很 多种 , 影 响 因索 也 是 多种 多 样 , 比如 焊 接 电流 、 电弧 电压 、 焊 接 速 度 等, 具体 的影 响是 : 保 证 除焊 接 电流之 外其 他 条件 不 变 , 随
随着 电弧 电压 的 降低 焊 缝 宽度 会 变得 高而 个 环节 , 这个 环节 质量 的好坏 直 接地 影 响着锅 炉和 压 力 其他 条 件 不 变 , 保证除焊接速度之外的其他条件不变, 随着焊接速度 容器 的质 量好 坏。近年 来 , 随着科 技水 平 的发展 , 出现 了越 窄 ; 的减 少焊 缝 余高 会增加 。 来 越 多 的焊 接 方法 ,但是 受 到普 遍欢 迎 的还 是 埋 弧 自动 焊 丝 伸 出 长度 、 焊剂堆散高度、 焊 件 倾斜 度 等 这 些 次 焊, 有调查资料显示 , 在所有的焊接 方法中埋弧焊所 占的 要 参数 也会 影 响到焊 缝余 高。比如 焊丝伸 出长度 可 以改 变 比例大约是 1 0 % ,并且这项数据一直维持了相 当长的一 进 而 改 变焊 丝 的熔 化速 度 , 达 到 改 变焊 段 时 间。在很 多重 要钢 结构 制作 中主 要 的焊接 方法 是埋 弧 通 过 自身 的 电阻 , 当工 件倾 斜 为上 坡 焊 时 , 焊件 倾 斜 度 和 焊 自动 焊 , 埋 弧 自动 焊 是 一种 工 艺 方 法 , 它是 通 过 利 用 焊 剂 缝 余 高 的 目的 :
直缝埋弧焊钢管技术标准
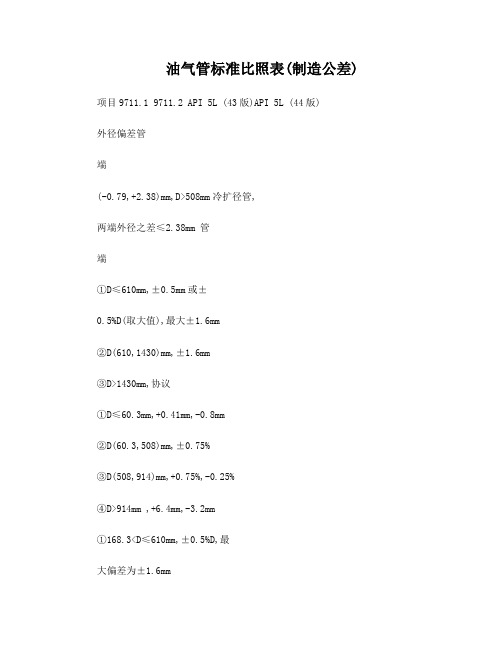
油气管标准比照表(制造公差) 项目9711.1 9711.2 API 5L (43版)API 5L (44版)外径偏差管端(-0.79,+2.38)mm,D>508mm冷扩径管,两端外径之差≤2.38mm 管端①D≤610mm,±0.5mm或±0.5%D(取大值),最大±1.6mm②D(610,1430)mm,±1.6mm③D>1430mm,协议①D≤60.3mm,+0.41mm,-0.8mm②D(60.3,508)mm,±0.75%③D(508,914)mm,+0.75%,-0.25%④D>914mm ,+6.4mm,-3.2mm①168.3<D≤610mm,±0.5%D,最大偏差为±1.6mm②610<D≤1219mm,±1.6mm管体管体①D≤610mm,±0.75%D最大±3mm②D(610,1430】mm,±0.5%D, 最大±4mm③D>1430mm,协议①D≤273mm,+ 1.6mm,-0.4mm②D(273,508)mm,+2.4mm,-0.8mm③D(508,1066)mm,+2.4mm,-0.8mm④D>1066mm ,+2.4mm,-0.8mm ①168.3<D≤610mm,±0.75%D,最大偏差为±3 mm②610<D≤1219mm,±0.5%D,最大偏差为±4 mm椭圆度管端:2%D ①D≤610mm,1.5%(管端)、2%(管体)②D>610mm管端:D/T≤75时,1.0%,D/T>75时,1%(D>1430mm时协议)管体:D/T≤75时,1.5%但最大15mm,D/T>75时,2% 管端,一般至少每十根测量一次;管体,每班测量两次,开始中间各测量一根。
JCO埋弧焊外防腐涂装钢管焊缝余高的控制
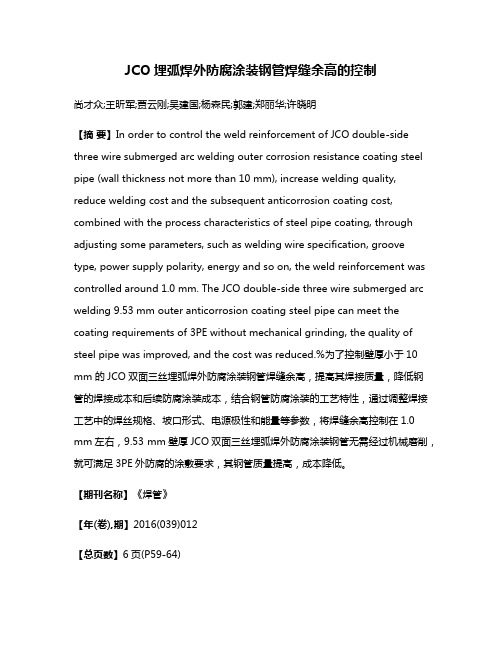
JCO埋弧焊外防腐涂装钢管焊缝余高的控制尚才众;王昕军;贾云刚;吴建国;杨森民;郭建;郑丽华;许晓明【摘要】In order to control the weld reinforcement of JCO double-side three wire submerged arc welding outer corrosion resistance coating steel pipe (wall thickness not more than 10 mm), increase welding quality, reduce welding cost and the subsequent anticorrosion coating cost, combined with the process characteristics of steel pipe coating, through adjusting some parameters, such as welding wire specification, groove type, power supply polarity, energy and so on, the weld reinforcement was controlled around 1.0 mm. The JCO double-side three wire submerged arc welding 9.53 mm outer anticorrosion coating steel pipe can meet the coating requirements of 3PE without mechanical grinding, the quality of steel pipe was improved, and the cost was reduced.%为了控制壁厚小于10 mm 的JCO双面三丝埋弧焊外防腐涂装钢管焊缝余高,提高其焊接质量,降低钢管的焊接成本和后续防腐涂装成本,结合钢管防腐涂装的工艺特性,通过调整焊接工艺中的焊丝规格、坡口形式、电源极性和能量等参数,将焊缝余高控制在1.0 mm左右,9.53 mm壁厚JCO双面三丝埋弧焊外防腐涂装钢管无需经过机械磨削,就可满足3PE外防腐的涂敷要求,其钢管质量提高,成本降低。
螺旋埋弧焊管焊缝形貌控制
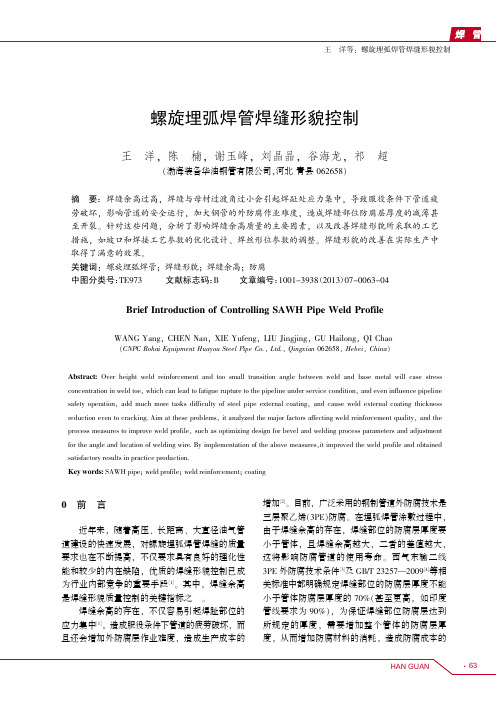
摘要:焊缝余高过高,焊缝与母材过渡角过小会引起焊趾处应力集中,导致服役条件下管道疲劳破坏,影响管道的安全运行,加大钢管的外防腐作业难度,造成焊缝部位防腐层厚度的减薄甚至开裂。
针对这些问题,分析了影响焊缝余高质量的主要因素,以及改善焊缝形貌所采取的工艺措施,如坡口和焊接工艺参数的优化设计、焊丝形位参数的调整。
焊缝形貌的改善在实际生产中取得了满意的效果。
关键词院螺旋埋弧焊管;焊缝形貌;焊缝余高;防腐中图分类号:TE973文献标志码:B文章编号:1001-3938(2013)07-0063-04螺旋埋弧焊管焊缝形貌控制王洋,陈楠,谢玉峰,刘晶晶,谷海龙,祁超(渤海装备华油钢管有限公司,河北青县062658)Abstract:Over height weld reinforcement and too small transition angle between weld and base metal will case stress concentration in weld toe,which can lead to fatigue rupture to the pipeline under service condition,and even influence pipeline safety operation,add much more tasks difficulty of steel pipe external coating,and cause weld external coating thickness reduction even to cracking.Aim at these problems,it analyzed the major factors affecting weld reinforcement quality,and the process measures to improve weld profile,such as optimizing design for bevel and welding process parameters and adjustment for the angle and location of welding wire.By implementation of the above measures,it improved the weld profile and obtained satisfactory results in practice production.Key words:SAWH pipe;weld profile;weld reinforcement;coatingBrief Introduction of Controlling SAWH Pipe Weld ProfileWANG Yang,CHEN Nan,XIE Yufeng,LIU Jingjing,GU Hailong,QI Chao(CNPC Bohai Equipment Huayou Steel Pipe Co.,Ltd.,Qingxian 062658,Hebei ,China )0前言近年来,随着高压、长距离、大直径油气管道建设的快速发展,对螺旋埋弧焊管焊缝的质量要求也在不断提高,不仅要求具有良好的理化性能和较少的内在缺陷,优质的焊缝形貌控制已成为行业内部竞争的重要手段[1]。
- 1、下载文档前请自行甄别文档内容的完整性,平台不提供额外的编辑、内容补充、找答案等附加服务。
- 2、"仅部分预览"的文档,不可在线预览部分如存在完整性等问题,可反馈申请退款(可完整预览的文档不适用该条件!)。
- 3、如文档侵犯您的权益,请联系客服反馈,我们会尽快为您处理(人工客服工作时间:9:00-18:30)。
埋弧焊钢管焊缝余高的控制
摘要:主要阐述了控制输送用钢管埋弧焊内、外焊缝余高的重要性。
焊缝的余高大,则焊缝的应力集中系数大,容易形成应力腐蚀裂纹。
外焊缝余高大,不利于防腐;内焊缝余高大,将会增加输送介质的能源损失等。
重点介绍了螺旋埋弧焊管内焊缝易出现的“马鞍形”问题。
“马鞍形”内焊缝在焊趾处的应力相当大,这对用于输送腐蚀性介质的钢管是最有害的。
为了延长钢管的服役年限,必须对焊缝余高进行有效的控制。
结合生产实际,提出了输送用钢管埋弧焊焊缝余高的控制措施。
0 前言无论是直缝埋弧焊管(LSAW)还是螺旋缝埋弧焊管(SSAW),对其焊接质量的评价,首先是看内、外焊缝的余高及其形状控制得好不好,焊缝流线是否规整等。
焊缝余高大且不是圆滑过渡(即转角半径小),则焊缝焊趾部位的应力集中系数大,对抗SCC不利。
此外,外焊缝的余高大,会给管子的防腐作业增加难度,成本增高;内焊的余高大,则对管道输送介质的摩擦阻力大,管输耗能也就大。
因此,在生产埋弧焊管时,必须控制内、外焊缝的余高。
API 5L标准中规定的焊缝余高只是最低标准,而油气输送管线和海洋用管均将焊缝余高控制在2.5 mm以下。
输送用埋弧焊管的焊缝最大余高,在多个标准中都作了规定,见表1。
1 焊缝余高大的负面影响
1.1焊趾处易形成应力腐蚀裂纹(SCC)
对接接头的应力集中主要是焊缝余高引起的。
埋弧焊管对接接头中的工作应力分布如图1所示[1]。
从图1看出,对接接头的焊缝,其焊趾处的应力最大。
应力集中系数的大小取决于焊缝余高h、焊趾处夹角θ和转角半径r。
焊缝余高h增加,则θ角增加,r值减小,会使应力集
中系数增大。
从图1还可得出埋弧焊管对接接头几何尺寸与应力集中系数KT的关系式
为:
KT=σmax/σ0焊缝的余高愈大,应力集中程度愈严重,焊接接头的强度反而会降低。
焊后削平余高,只要不低于母材,减少应力集中,有时反而可以提高焊接接头的强度。
焊缝的转角半径愈小,应力集中的程度则愈大;反之,应力集中的程度则愈小。
因此,对埋弧焊缝的要求:一是余高要小;二是焊缝要圆滑过渡,使转角半径r值增大。
埋弧焊管的焊缝均为对接接头的焊缝,如果不控制好焊缝余高和转角半径,则焊趾处的应力就大,以致焊管在服役过程尤其是在腐蚀介质中,如H2S水溶液、海水、海洋大气等,易在焊趾处产生应力腐蚀裂纹。
焊管在成型和焊接过程中不可避免地会产生残余应力,因此管坯在成型、焊接后要消除残余应力。
扩径可消除残余应力,但是残余应力很难完全消除,焊趾处的残余应力也就不可能消除。
为了预防在焊趾处产生应力腐蚀裂纹,这就需要控制好成型、焊接时的残余应力,尤其是焊趾处的残余应力。
国外油气输送钢管生产厂家对焊管残余应力都有内控标准。
例如,日本NKK公司规定,UOE焊管内表面的残余压应力σr∧100 MPa;日本住友金属公司规定,UOE焊管内表
面不允许存在残余拉应力,即σr∧0;加拿大Welland公司规定每班检查环切试样的张开位移量ΔL,要求ΔL∧20 mm[2]。
在螺旋焊管的生产中,内焊缝往往出现“马鞍形”,即焊缝中间低,两边高,焊缝和母材基本上成直角,更谈不上圆滑过渡了,这种焊缝在焊趾处的应力集中度相当大。
笔者在工作期间发现,已服役多年的螺旋焊管内焊缝的两边焊趾处腐蚀出很深的沟槽。
因此,必须避免出现这种“马鞍形”焊缝,否则就会严重影响输送管道的服役年限。
“马鞍形”焊缝的产生,主要是由于内焊缝焊头的位置处于下坡焊位置,焊速越大越严重。
据文献[3]介绍,国外螺旋焊管的内焊焊头处在上坡焊的位置,如图2所示。
焊缝的形状随着前丝的偏中心位置L和前丝与后丝之间的间隙I的变化而改变,当L的取值范围为0~20 mm,I 的取值范围为14~18 mm时可获得良好的焊缝形状[3],可减少或预防“马鞍形”焊缝的产生。
L的调整还应随焊速的变化而改变。
除焊头位置外,焊剂也是影响焊缝形状的一个重要因素。
国内螺旋焊管的内焊焊头大都处在下坡焊的位置。
当螺旋埋弧焊管处在边成型边焊接的过程中,必然会造成内焊焊缝呈“马鞍形”,且焊速愈大愈严重。
要改变这种状态,就要使焊头基本处在图2所示的上坡焊位置。
1.2外焊缝余高大不利于防腐在防腐
作业时如采用环氧树脂玻璃布进行防腐,外焊缝余高大,将使焊趾处不易压牢。
同时,焊缝越高则防腐层就越应加厚,因标准规定防腐层的厚度是以外焊缝的顶点为基准测算的,这就加大了防腐成本。
螺旋埋弧焊时往往容易出现“鱼脊背形”的外焊缝,这就更难保证防腐的质量。
因此,调整好焊头的空间位置和焊接规范,减少或消除“鱼脊背形”的外焊缝也是很重要的。
1.3 外焊缝余高过大对水压扩径后的管形有影响
直缝埋弧焊管在水压扩径时,是通过内腔与钢管扩径尺寸一致的左、右2部分外模将钢管包住的,因此,焊缝的余高过大,在扩径时焊缝承受的剪应力就大,焊缝2侧就易出现“小直边”现象。
但经验证明,当外焊缝的余高控制在2 mm左右时,水压扩径时不会出现“小直边”现象,管形不会受到影响。
这是因为外焊缝的余高小,焊接接头所承受的剪应力也小。
只要这种剪应力在弹性变形范围内,卸载后产生回弹,管子就会恢复原状。
1.4 内焊缝余高大增加输送介质的能源损失
输送用埋弧焊管内表面若未做涂层防腐处理时,其内焊缝的余高大,则对输送介质的摩擦阻力也大,由此将使输送管线的能耗增加。
2 控制焊缝余高的措施
2.1 壁厚较大的钢管应开坡口
对于壁厚大于14.3 mm的钢管,应开X形坡口并预焊。
如预焊条件不成熟,则应在内焊后用气刨清根,或砂轮自动磨削清根,或铣削清根等方法,将外焊缝在未焊之前加工成U形槽再进行焊接。
2.2 调整好焊接线能量
检查焊接线能量是否合适,一般用焊接接头的酸蚀样来检查。
一是检查内外焊缝的重合量的程度,二是检查焊道腰部的宽窄。
对重合量的规定一般是大于1.5 mm,但笔者认为内外焊缝的重合量以1.3~3.0 mm较合适,若超过3.0 mm就说明线能量大了。
线能量大,不仅仅是熔深大,而且焊缝余高也大,如不开坡口或U形槽,焊缝余高就更大。
这是因为焊接线能量越大,单位时间内熔化的焊丝必然增加。
对于高强钢,焊接的线能量更应严格控制。
焊接高强度钢板时,为了降低每层的线能量,一般采用多道焊(2道以上),且应使焊缝的形状系数在1.3~2.0 mm内。
2.3 多丝焊时宜采用较细的前丝
采取多丝焊时,如原外焊三丝直径的匹配是4mm+3.2 mm+3.2 mm(DC-AC-AC),则前丝改为Ф3.2 mm较好。
因为在采用相同电流的情况下,使用Ф3.2 mm的焊丝比使用Ф4 mm的焊丝熔深大。
也就是说,前丝采用Ф3.2 mm的焊丝,即便降低一些线能量,也可以达到采用Ф4 mm时同样的熔深效果,这是因细丝比粗丝的电流密度大所致。
经验证明,在其他条件不变的情况下,采用Ф3.2 mm的前丝要比Ф4 mm的前丝熔深大20%左右。
这在外焊不开坡口或不刨凹槽时所减少的外焊缝余高效果更明显。
但是,当焊接壁厚大于14.3 mm的钢管而需要前丝电流在1 000 A左右时,应采用Ф4 mm的前丝,否则就可能影响到电弧的稳定燃烧。
2.4 螺旋焊必须调整好内外焊头的位置
螺旋埋弧焊管在内焊时应调整好内焊头的位置,尽量减少或消除“马鞍形”内焊缝(图2);在外焊时,也应调整焊头的空间位置,尽量减少或消除“鱼脊背形”的外焊缝,这主要是靠对外焊焊点的偏中心值调整来实现。
不同口径的螺旋焊管,其外焊焊点的偏中心值是不同的。
根据试验结果,采用双丝焊的外焊,其焊点偏中心值可按表2设定。
3 结语
(1)对于埋弧焊管的对接焊缝,一是余高要小,二是要使焊缝圆滑过渡以及焊缝的转角半径要大,否则在焊缝应力集中部位的焊趾处就会产生应力腐蚀裂纹。
埋弧焊缝的余高控制在2.5 mm以下较为合适。
(2)螺旋埋弧焊管在内焊时,要精心调整好内外焊缝的空间位置,使其内焊缝尽量减少和避免出现“马鞍形”,外焊缝不出现“鱼脊背形”。
建议在制定输送用螺旋焊管标准时,对内焊缝的“马鞍形”应有相应的规定。