零部件首件检验单
首件检验(FAI)控制程序-E3

首件检验控制程序文件编号:版 次: 生效日期:编 制:审 核:批 准:1 目的为了保证产品批量加工时的质量,在产品量产前对影响产品质量的因素和首件产品实物质量进行验证和确认。
2 范围适用所有新项目,新产品开发设计,供方提供产品等的首件新产品验证,设计、工艺变更后的首件验证以及每日批量生产前首件验证。
2.1 在新开发产品首次上线生产时的首件检验。
2.1.1 新产品的内部首检。
2.1.2 新产品交付顾客前的外部首件检验(顾客有要求现场验证的情况)。
2.1.3 供应商(外包、外协、外购)提供的新产品首件检验。
2.2 因后续设计、工艺更改等变化导致先前首检失效的首件检验。
2.3 在批量生产过程中(每个生产班次开始加工的第一个工件,或加工过程中因换人、换料及换工装、调整机床等改变工序条件后加工的第一个工件)的首件检验。
3 定义3.1 P-FAI(Process First Article Inspection)即工序首检,是对工序的制程因素及其结果的验证。
3.2 FAI (First Article Inspection)即首件检验。
是指按照技术文件的要求,对批量生产前的首个零(部或组)件进行全面的工序和成品检查、考核,以确定零部件是否满足技术要求,是否具备批量的、稳定的生产合格产品的能力。
3.3产品制造过程外包、外协(也叫工序外包、外协):公司提供技术要求(技术协议、图纸等)、必要时提供零部件(或原材料、半成品),要求供应商按技术要求进行相应工序加工的过程。
3.4外购:产品不是由组织(公司)设计的,通过选型向外界直接购买,它是为了与外包相对应而出现的词汇。
4 职责4.1 技术研究院4.1.1负责提供产品的所有图纸、BOM表、技术标准、关键零部件清单等检验准则。
4.1.2参与首检工作。
4.1.3负责组织落实本部门首检开口项关闭。
4.2 工程技术部4.2.1提供生产必须的相关作业指导书和生产设备的配置。
4.2.2负责首检产品的关键、特殊工序工艺验证资料;参与首检工作。
首件鉴定报告(22163FAI)
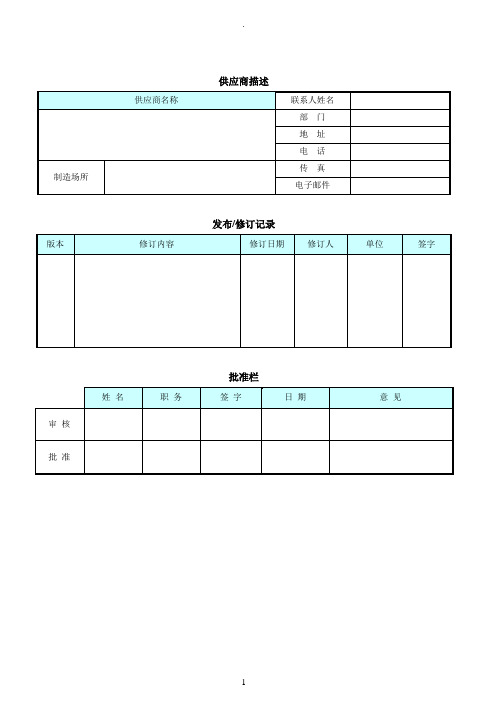
□让步接收□让步申请单编号:
□让步接收申请限定的数量:□让步申请限定的时间范围:
□让步接收申请被批准:□让步接收申请被拒绝:
质量代表签字:日期:
顾客签字(需要时):日期:
⑶、FAI鉴定过程简述:
根据《首件鉴定控制程序》、XX新产品设计开发计划和XX产品项目质量计划中的策划要求,公司于2015年6月16日由质量保证部牵头组织技术部、制造部、车体车间等相关部门/人员,对CRH6A项目T4车体总成进行了车间级首件鉴定工作。
4.2.4
□
□
□
□
□
□
(STBT)焊接结构试验4.2.5*□来自□□□
□
□
(WPQR)焊接工艺评定
4.2.6*
□
□
□
□
□
□
焊工/焊接操作人员证书
4.2.7
□
□
□
□
□
□
焊接工艺规范
4.2.8
□
□
□
□
□
□
焊接计划,点焊计划,焊接顺序计划、焊接检验计划
4.2.9
□
□
□
□
□
□
焊接试件样本,包括文件
4.2.10*
3C认证产品的3C认证报告
4.3.14*
□
□
□
□
□
□
危险品登记表
4.3.15*
□
□
□
□
□
□
依据SN 36350-2(或相关标准)的危险违禁品声明
4.4.1
□
□
□
□
□
□
特殊工艺(油漆、焊接、粘接等)控制计划
关键零部件(产品)首件鉴定资料清单

技术协议中的特别要求
11
设计输入、输出清单
12
产品加工工艺文件、产品组装工艺文件
13
产品质量计划
14
产品检验大纲
15
产品制造号码一览表说明
16
性能试验报告
17
探伤报告、性能报告
18
质量跟踪卡(一件一卡)
19
各类检验记录
20
原材料及配件质量证明
21
工装、检测设备及仪器的台帐及校准记录
22
供应商清单及评价报告(样品及小批记录)(有特殊工序按特殊工序管理办法)
关键零部件(产品)首件鉴定资料清单
检索编号:编号:QR/TZL036-04Rev:A/0
序号
清单内容
责任人
预期完成时间
1
公司管理文件
公司第三层次文件
3
FAI实施日程安排表
4
FAI鉴定申请表
5
产品设计任务书
6
产品设计策划书
7
产品项目进程表(项目管理计划)
8
产品图纸
9
产品试验大纲(型式试验、例行试验)
23
产品防护(包装)
编制/日期:批准/日期:
ISO9001-2015首件自检专检质量控制程序

首件自检专检质量控制程序(ISO9001:2015)1 范围本程序规定了产品首件自检专检的控制要求。
本程序适用于产品生产过程中首件。
2 职责2.1 生产单位负责识别需自检专检的首件,并负责首件自检。
2.2 检验部门负责首件专检。
3 工作程序3.1 对由模具保证的冲压、锻造及机械加工、焊接工序,根据产品特性及加工要求,由生产单位确定本单位需进行首件自检专检工序,并列出首件自检专检工序目录,关键件、重要件必须执行首件自检专检。
3.2 首件自检专检工序目录检验部门一份,生产单位自存一份。
3.3 首件自检专检的工序,符合以下情况之一,必须对首件实行自检、专检。
a)每个工作班开始;b)更换操作者;c)更换或调整设备、工艺装备;d)更换技术文件、工艺方法、工艺参数;e)采用新标准;f)采用新材料或材料代用;g)更换或重新化验槽液、渗透液等;h)操作者加工前应检查工序过程受控状态,确保符合下列条件;i)产品图、技术文件、工艺规程、检验规程等应是现行有效版本;j)材料符合工艺规程、技术条件的要求;k)工、夹、量、模具、测试设备和机床符合工艺规程要求。
3.4 首件产品应检验以下内容:a)首件的技术文件是否正确、完整、有效;b)首件是否符合图样和技术文件的要求;c)加工首件的工艺装备和检验用的计量器具是否符合规定要求;d)首件生产环境是否符合要求;e)生产首件的操作者是否持证上岗。
3.5 每个班次开始生产的第一个工件首先由操作者自检,合格后在首件自检专检卡片上填写检验记录,而后提请专检人员检验确认是否合格并填写检验记录。
3.6 首件自检专检是鉴定过程能力,确定是否能批量生产。
首件自检、专检合格后,方可连续生产,如首件经检验不合格,应从人、机、料、法、环、测等方面查找原因,采取纠正措施后,再生产第二件产品,继续实施首件自检、专检,直至合格,方可连续生产。
3.7 对经过检验合格的首件应标记“首件合格”,单独存放,待所在批次产品加工完毕后,方可随所在批产品放行。
班组零部件加工首、末件检验管理规定

1目的为了强化班组的质量管理,规范首件、末件检验,降低质量风险。
2适用范围本管理规定适用于生产线的首件检验和末件检验。
3职责3.1 技术质量室负责本规定的归口管理,对执行情况进行检查并按《班组产品质量评审考核办法》实施考核。
3.2 各相关部门应严格执行本规定。
4机加工工序首件检验要求4.1 首件检验指令的分类首件检验指令包括:首件自检、首件边做边检和首件停机送检等。
首件自检:即首件生产后仅要求操作工进行自检,合格后开始生产。
首件边做边检:即首件生产后送精测间或平台边生产边等待检测结果。
首件停机送检:即首件生产后送精测间或平台停机检测,检测合格后生产。
4.2 自检检测要求4.2.1普通加工工序:要求所有加工项目都要检测。
4.2.1.1同一把刀具钻、攻、粗镗具有相同检测内容的孔允许使用规定的检测手段检测该刀具加工的最后一个孔,其它孔目测。
4.2.1.2其它同一把刀具加工的具有相同检测内容的加工部位,首、尾加工部位必须检测,中间加工部位目测。
4.2.1.3具有不相同检测内容的加工部位,必须按4.3.1.1和4.3.1.2规定进行检测。
4.2.2精加工工序:同一把刀具钻、攻具有相同检测内容的孔允许按4.3.1.1和4.3.1.3要求检测,其它同一把刀具加工的所有内容都必须检测。
4.2.3有专用量具检测的项目必须使用相应的专用量具检测。
无专用量具检测的项目,通用量具可以检测的项目必须使用通用量具检测(高精度通用量具可以代用低精度通用量具,量程在测量范围内的游标卡尺、深度卡尺允许代用)。
无专用量具检测的项目,通用量具不可以检测的项目必须目测。
4.2.4首检工件在填写自检记录表时在“追溯号”旁标注“首”记号(自检记录表中有特殊规定的按自检记录表中的要求填写)。
末检件工件在填写自检记录表时在“追溯号”旁标注“末”记号。
4.2.5首件自检必须完成所有频次检内容。
4.3 送精测间检测要求4.3.1送检前工件必须进行自检并清理,送检时按照精测间要求进行登记,并注明“首件”、“专检”等能清楚表明检测目的的字样(允许简写)。
首件及首件检验的定义
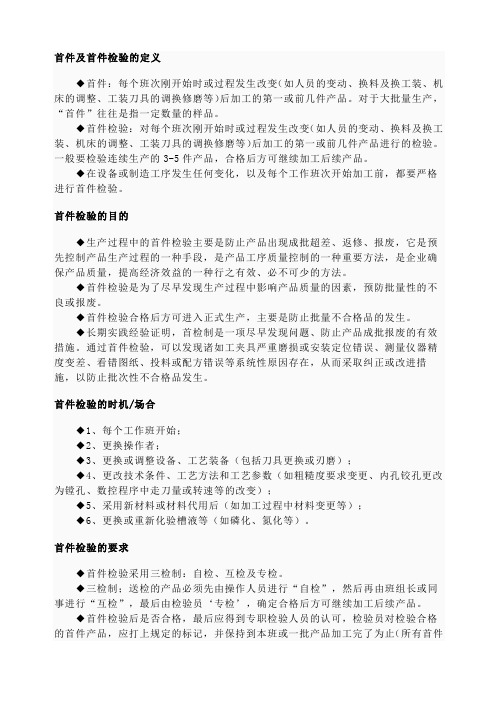
首件及首件检验的定义◆首件:每个班次刚开始时或过程发生改变(如人员的变动、换料及换工装、机床的调整、工装刀具的调换修磨等)后加工的第一或前几件产品。
对于大批量生产,“首件”往往是指一定数量的样品。
◆首件检验:对每个班次刚开始时或过程发生改变(如人员的变动、换料及换工装、机床的调整、工装刀具的调换修磨等)后加工的第一或前几件产品进行的检验。
一般要检验连续生产的3-5件产品,合格后方可继续加工后续产品。
◆在设备或制造工序发生任何变化,以及每个工作班次开始加工前,都要严格进行首件检验。
首件检验的目的◆生产过程中的首件检验主要是防止产品出现成批超差、返修、报废,它是预先控制产品生产过程的一种手段,是产品工序质量控制的一种重要方法,是企业确保产品质量,提高经济效益的一种行之有效、必不可少的方法。
◆首件检验是为了尽早发现生产过程中影响产品质量的因素,预防批量性的不良或报废。
◆首件检验合格后方可进入正式生产,主要是防止批量不合格品的发生。
◆长期实践经验证明,首检制是一项尽早发现问题、防止产品成批报废的有效措施。
通过首件检验,可以发现诸如工夹具严重磨损或安装定位错误、测量仪器精度变差、看错图纸、投料或配方错误等系统性原因存在,从而采取纠正或改进措施,以防止批次性不合格品发生。
首件检验的时机/场合◆1、每个工作班开始;◆2、更换操作者;◆3、更换或调整设备、工艺装备(包括刀具更换或刃磨);◆4、更改技术条件、工艺方法和工艺参数(如粗糙度要求变更、内孔铰孔更改为镗孔、数控程序中走刀量或转速等的改变);◆5、采用新材料或材料代用后(如加工过程中材料变更等);◆6、更换或重新化验槽液等(如磷化、氮化等)。
首件检验的要求◆首件检验采用三检制:自检、互检及专检。
◆三检制;送检的产品必须先由操作人员进行“自检”,然后再由班组长或同事进行“互检”,最后由检验员‘专检’,确定合格后方可继续加工后续产品。
◆首件检验后是否合格,最后应得到专职检验人员的认可,检验员对检验合格的首件产品,应打上规定的标记,并保持到本班或一批产品加工完了为止(所有首件产品必需留样,留作后续产品对比之用,来看过程是否发生变化,并用记号笔标记“√”以示通过首件检验)。
首尾件制度宣传资料

首尾件制度宣讲资料
一、首检(首件检验):
首件检验是指当班生产开始时或工艺要素变化时,对第一件(批量生产或特殊因素变化时首件检查2-3件)产品进行检验判定。
二、首件检验作用:
首件检验由生产部门和品管员共同按工艺生产图纸或BOM(物料清单表)标准要求,对批量生产的第一件产品进行检查核对,防止了批量性不良的产生起到预防作用,帮忙产线减少批量性产品不良,减少产品报废与浪费。
从而提高生产操作人员的生产效率。
三、自检(自主检验):
自主检验是指操作工按工艺、图纸、标准(含实物样件)对自已加工,使用的零部件进行自主检查。
四、自主检验作用:
操作工自已按生产加工规定数量或规定时段对自已生产的产品与首件进行比对检查,以检查规定某段加工产品的数量或某时间段内加工的产品是否与首件一致,是否合格,及时发现生产过程中的不良,减少过程生产不良品的数量,减少产品报废与浪费。
从而提高生产操作人员的生产效率。
五、尾检(尾件检验):
尾件检验:每批(数量较大,一天加工不能完成时则为每天生产最后一个产品)加工完毕,由车间操作者进行完工自主检验。
六、尾件检验作用:
操作工本批加工完成后,对最后一个产品进行自主检验,确认批生产产品是否合格,以防止不良品流出本岗位,影响下工序生产。
首尾件、自检制度实施,可以减少批量不良产生,减少制程作业不良,防止不良品流入下工序,影响下工序正常生产,将制程质量控制转变为制程预防质量为主,从而减少产品报废与减少浪费,从而提升车间产品良率,提升车间产品质量。
车辆维修前诊断检验车辆维修前诊断检验单(小型车)单
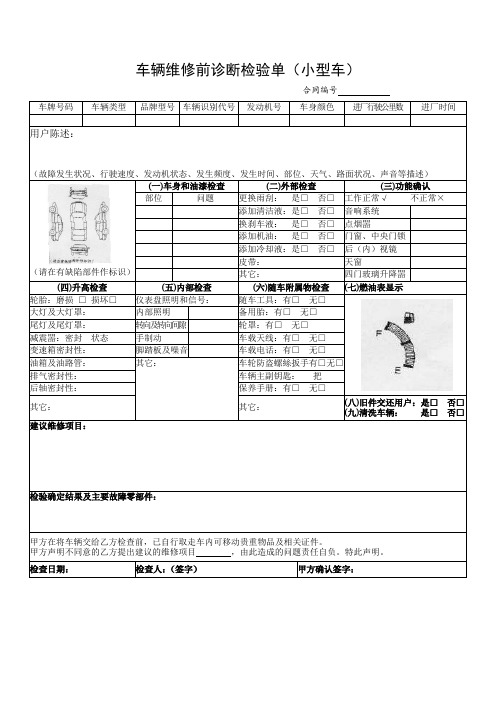
车辆维修前诊断检验单(小型车)
合同编号
车牌号码车辆类型品牌型号车辆识别代号发动机号车身颜色进厂行驶公里数进厂时间用户陈述:
(故障发生状况、行驶速度、发动机状态、发生频度、发生时间、部位、天气、路面状况、声音等描述)
(请在有缺陷部件作标识)
(一)车身和油漆检查(二)外部检查(三)功能确认
部位问题更换雨刮:是□否□工作正常√不正常×
添加清洁液:是□否□音响系统
换刹车液:是□否□点烟噐
添加机油:是□否□门窗、中央门锁
添加冷却液:是□否□后(内)视镜
皮带:天窗
其它:四门玻璃升降噐
(四)升高检查(五)内部检查(六)随车附属物检查(七)燃油表显示轮胎:磨损□损坏□仪表盘照明和信号:随车工具:有□无□
大灯及大灯罩:内部照明备用胎:有□无□
尾灯及尾灯罩:转向及转向间隙轮罩:有□无□
减震噐:密封状态手制动车载天线:有□无□
变速箱密封性:脚踏板及噪音车载电话:有□无□
油箱及油路管:其它:车轮防盗螺絲扳手有□无□
排气密封性:车辆主副钥匙:把
后轴密封性:保养手册:有□无□
其它:其它:(八)旧件交还用户:是□否□
(九)清洗车辆:是□否□
建议维修项目:
检验确定结果及主要故障零部件:
甲方在将车辆交给乙方检查前,已自行取走车内可移动贵重物品及相关证件。
甲方声明不同意的乙方提出建议的维修项目,由此造成的问题责任自负。
特此声明。
检查日期:检查人:(签字)甲方确认签字:。
FAI首检表

焊 接 操 作 人 员
4.8
Q/E
4.9
Q/E
4.10
Q/E
焊 接 工 装
是否配备了适合的工装、卡具?工装卡具是否能做 4.11 到黑白金属隔离。
5.质量文件及证明确认
5.1
焊 接 记 录
是否进行原材料的可追溯性并进行了记录。
确认供应商在原材料可追溯性是否满足EN15085的要求。 记录追溯性的情况。
Q
1.2
产品是否符合合同供货范围?
Q
供 方 资 质
1.3
是否为SATCO合格焊接供应商?(K.O)
Q
1.4
供货是否符合资质范围?(K.O)
Q
F 供 A 方 I
1.5
是否提交供应商内部FAI报告或检验报告?
Q
2.供应商证书确认
2.1
供应商是否通过了EN15085-2焊接体系,证书是否 在有效期内?(K.O) 供应商提供的EN15085-2焊接体系证书是否覆盖首 检产品的焊接结构? 供应商提供的EN15085-2焊接体系证书是否覆盖首 检产品所使用的焊接工艺? 供应商提供的EN15085-2焊接体系证书中所涉及的 焊接责任人员是否还在企业就职?
版本/Rev:A
Welding Products First Article Inspection焊接 产品首件检验(外检)
No. 编号
Mark 签字
Items to be checked 检验项目
满足
不满足 不适用
Inspection Record 检查记录
1.首件检验前提条件确认
合 同 定 单 1.1
Q
5.3
无损探伤的识别以及检验方式的选择。
Q
首件检验(16949)
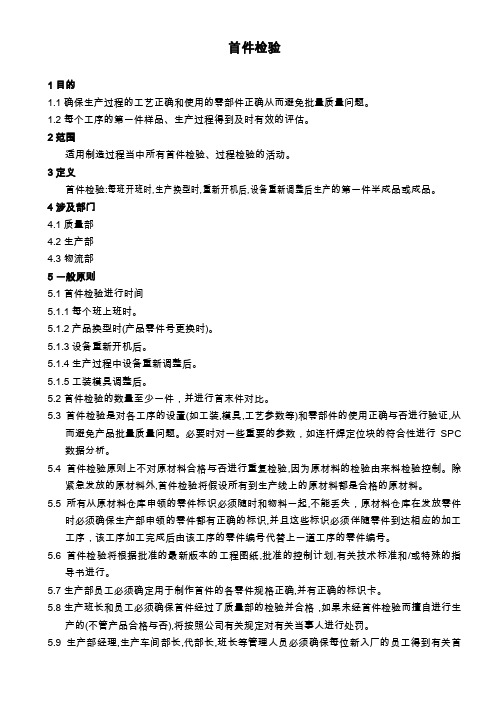
首件检验1目的1.1确保生产过程的工艺正确和使用的零部件正确从而避免批量质量问题。
1.2每个工序的第一件样品、生产过程得到及时有效的评估。
2范围适用制造过程当中所有首件检验、过程检验的活动。
3定义首件检验:每班开班时,生产换型时,重新开机后,设备重新调整后生产的第一件半成品或成品。
4涉及部门4.1质量部4.2生产部4.3物流部5一般原则5.1首件检验进行时间5.1.1每个班上班时。
5.1.2产品换型时(产品零件号更换时)。
5.1.3设备重新开机后。
5.1.4生产过程中设备重新调整后。
5.1.5工装模具调整后。
5.2首件检验的数量至少一件,并进行首末件对比。
5.3首件检验是对各工序的设置(如工装,模具,工艺参数等)和零部件的使用正确与否进行验证,从而避免产品批量质量问题。
必要时对一些重要的参数,如连杆焊定位块的符合性进行SPC 数据分析。
5.4首件检验原则上不对原材料合格与否进行重复检验,因为原材料的检验由来料检验控制。
除紧急发放的原材料外,首件检验将假设所有到生产线上的原材料都是合格的原材料。
5.5所有从原材料仓库申领的零件标识必须随时和物料一起,不能丢失,原材料仓库在发放零件时必须确保生产部申领的零件都有正确的标识,并且这些标识必须伴随零件到达相应的加工工序,该工序加工完成后由该工序的零件编号代替上一道工序的零件编号。
5.6首件检验将根据批准的最新版本的工程图纸,批准的控制计划,有关技术标准和/或特殊的指导书进行。
5.7生产部员工必须确定用于制作首件的各零件规格正确,并有正确的标识卡。
5.8生产班长和员工必须确保首件经过了质量部的检验并合格,如果未经首件检验而擅自进行生产的(不管产品合格与否),将按照公司有关规定对有关当事人进行处罚。
5.9生产部经理,生产车间部长,代部长,班长等管理人员必须确保每位新入厂的员工得到有关首件检验、过程检验的培训。
5.10首件检验的合格与否由质量部检验员确定,检验员不能确定的,必须会同生产班长,车间部长,质量经理等熟知该产品和工艺的人员共同判定。
首件检验记录表填写说明

首件检验记录表填写说明
制造部:填写一部或二部或三部
车间:(即所属车间)
首件类型:一般在新产品或换班中打钩。
如第二天生产的产品与第一天的相同也要首检并在换班框中打钩。
特殊情况下选择相应的类型。
序号:即1、2、3、4、5、6、7、8、9
订单号:为营管部下发的订单制程确认表中的订单号。
客户名称:为客户的公司名称(例如STACK-ON,AMSEC,JVN等等)
产品型号:即技术要求中的型号(例如SC1717E-935-01)
零部件名称:即在加工单填写的名称(例如防撬挡板,锁安装板,外壳,门板等等)
检验内容:()内填写工序名称。
(例如冲孔折弯磷化喷塑焊接等)钣金车间一般填写数据和外观(例如孔距23±0.5,折弯尺寸57.6
±0.4,冲孔尺寸45±1.0。
板面弯曲情况,材质)
焊接车间一般填写焊接零部件齐全,牢固;摇杆焊接尺寸(例如摇杆
焊接尺寸59±0.5),清理杂质
涂装车间一般填写磷化情况,刮灰情况,打磨情况,塑粉型号,喷塑
表面质量等。
检验结果:根据检验内容记录检验的结果,有数据的必须填写数据。
判定:以下情况在判定时为X,即不合格
1首件1件至3件发现有严重的A类不合格
2首件5件时有相同的B类或C类不合格(批量)
备注:填写出现不合格的处理措施或质量状况
首检人/日期:填写检验人和制作当天的日期
审核/日期:由车间主管或车间主任和制作当天的日期
会签/日期:所在品质部检验员和签署的日期
A类不合格、B类不合格、C类不合格的定义请参照2012年IPQC检验报表。
首件及首件检验的定义
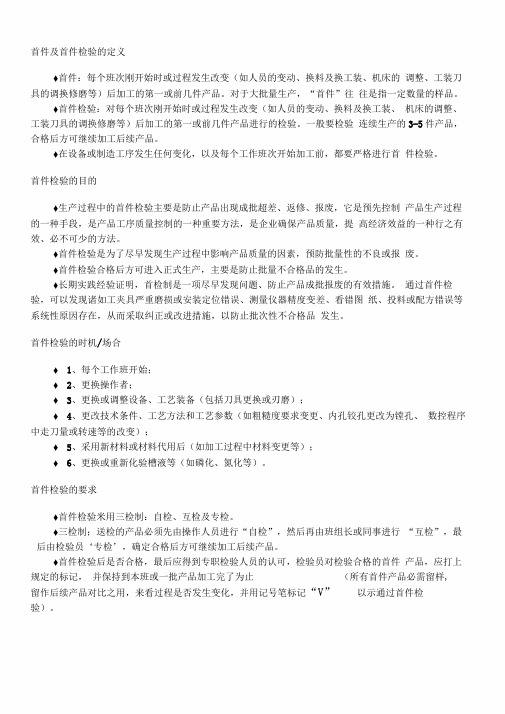
首件及首件检验的定义♦首件:每个班次刚开始时或过程发生改变(如人员的变动、换料及换工装、机床的调整、工装刀具的调换修磨等)后加工的第一或前几件产品。
对于大批量生产,“首件”往往是指一定数量的样品。
♦首件检验:对每个班次刚开始时或过程发生改变(如人员的变动、换料及换工装、机床的调整、工装刀具的调换修磨等)后加工的第一或前几件产品进行的检验。
一般要检验连续生产的3-5件产品,合格后方可继续加工后续产品。
♦在设备或制造工序发生任何变化,以及每个工作班次开始加工前,都要严格进行首件检验。
首件检验的目的♦生产过程中的首件检验主要是防止产品出现成批超差、返修、报废,它是预先控制产品生产过程的一种手段,是产品工序质量控制的一种重要方法,是企业确保产品质量,提高经济效益的一种行之有效、必不可少的方法。
♦首件检验是为了尽早发现生产过程中影响产品质量的因素,预防批量性的不良或报废。
♦首件检验合格后方可进入正式生产,主要是防止批量不合格品的发生。
♦长期实践经验证明,首检制是一项尽早发现问题、防止产品成批报废的有效措施。
通过首件检验,可以发现诸如工夹具严重磨损或安装定位错误、测量仪器精度变差、看错图纸、投料或配方错误等系统性原因存在,从而采取纠正或改进措施,以防止批次性不合格品发生。
首件检验的时机/场合♦1、每个工作班开始;♦2、更换操作者;♦3、更换或调整设备、工艺装备(包括刀具更换或刃磨);♦4、更改技术条件、工艺方法和工艺参数(如粗糙度要求变更、内孔铰孔更改为镗孔、数控程序中走刀量或转速等的改变);♦5、采用新材料或材料代用后(如加工过程中材料变更等);♦6、更换或重新化验槽液等(如磷化、氮化等)。
首件检验的要求♦首件检验米用三检制:自检、互检及专检。
♦三检制;送检的产品必须先由操作人员进行“自检”,然后再由班组长或同事进行“互检”,最后由检验员‘专检’,确定合格后方可继续加工后续产品。
♦首件检验后是否合格,最后应得到专职检验人员的认可,检验员对检验合格的首件产品,应打上规定的标记,并保持到本班或一批产品加工完了为止(所有首件产品必需留样, 留作后续产品对比之用,来看过程是否发生变化,并用记号笔标记“V”以示通过首件检验)。
产品首件鉴定检验程序(含表格)

产品首件鉴定检验程序(ISO9001-2015)1.目的为确保新产品制造工艺的正确性,保证产品质量,避免出现批量不合格品。
2.适用范围本程序适用于公司对产品首件鉴定和检验工作。
3.术语3.1首件:每个班次刚开始时或过程发生改变(如人员的变动、换料及换工装、设备的调整、工装的调换修磨等)后加工的第一或前几件产品。
对于大批量生产,“首件”往往是指一定数量的样品。
3.2首件鉴定是对试生产的第一件零部件按设计图样和工艺规程的要求全面的过程和成品检查,以确定生产工艺和设备能否保证生产出符合设计要求的产品,以验证和鉴定过程的生产能力,并为零部件生产(工艺)定型做准备。
3.3首件检验:对每个班次刚开始时或过程发生改变(如人员的变动、换料及换工装、机床的调整、工装刀具的调换修磨等)后加工的第一或前几件产品进行的检验。
一般要检验连续生产的3-5件产品,合格后方可继续加工后续产品。
在设备或制造工序发生任何变化,以及每个工作班次开始加工前,都要严格进行首件检验。
4.职责4.1 技术部负责组织产品首件鉴定和检验工作,并对正确性、及时性负责。
4.2 生产部只有在首件产品鉴定合格后,才能组织批量生产;4.3各车间有责任配合技术部做好产品首件鉴定和检验工作,只有首件鉴定和检验合格才能批量生产。
4.4 质保部应配合技术部做好产品首件鉴定和检验工作,并对其结果进行确认;5.首件产品鉴定工作程序5.1首件鉴定范围a)新产品在工艺定型前的首件;b)不连续的批生产,间隔一年后又恢复生产的首件;c)设计图纸发生重大更改后生产的首件;d)工艺规程发生重大更改后生产的首件;e)合同要求指定的首件。
5.2首件鉴定的内容a)首件生产所依据的技术、工艺文件是否正确、完整、协调、有效,并能指导生产;b)产品加工的工艺安排是否合理可行,适合批量生产;c)所用采购产品是否符合规定要求;d)选用的所有设备能否满足生产要求,生产环境是否满足生产要求;e)生产操作人员是否具备相应的能力;f)首件质量与其质量记录是否相符,质量问题是否按规定得到处理;g)有顾客要求的工序是否经顾客签署认可。
产品首件鉴定和检验控制程序

产品首件鉴定和检验控制程序1.目的为确保新产品制造工艺的正确性,保证产品质量,避免出现批量不合格品。
2.适用范围本程序适用于公司对产品首件鉴定和检验工作。
3.术语3.1首件:每个班次刚开始时或过程发生改变(如人员的变动、换料及换工装、设备调整、设备异常维修等)后加工的第一或前几件产品。
对于大批量生产,“首件”往往是指一定数量的样品。
3.2首件鉴定是对试生产的第一件零部件按设计图样和工艺规程的要求全面的过程和成品检查,以确定生产工艺和设备能否保证生产出符合设计要求的产品,以验证和鉴定过程的生产能力,并为零部件生产(工艺)定型做准备。
3.3首件检验:对每个班次刚开始时或过程发生改变(如人员的变动、换料及换工装、设备调整、设备异常维修等)后加工的第一或前几件产品进行的检验。
一般要检验连续生产的3-5件产品,合格后方可继续加工后续产品。
在设备或制造工序发生任何变化,以及每个工作班次开始加工前,都要严格进行首件检验。
4.职责4.1 技术部负责组织产品首件鉴定和检验工作,并对正确性、及时性负责。
4.2 生产部只有在首件产品鉴定合格后,才能组织批量生产;4.3各车间有责任配合技术部做好产品首件鉴定和检验工作,只有首件鉴定和检验合格才能批量生产。
4.4 质保部应配合技术部做好产品首件鉴定和检验工作,并对其结果进行确认;5.首件产品鉴定工作程序5.1首件鉴定范围a)新产品在工艺定型前的首件;b)不连续的批生产,间隔一年后又恢复生产的首件;c)设计图纸发生重大更改后生产的首件;d)工艺规程发生重大更改后生产的首件;e)合同要求指定的首件。
5.2首件鉴定的内容a)首件生产所依据的技术、工艺文件是否正确、完整、协调、有效,并能指导生产;b)产品加工的工艺安排是否合理可行,适合批量生产;c)所用采购产品是否符合规定要求;d)选用的所有设备能否满足生产要求,生产环境是否满足生产要求;e)生产操作人员是否具备相应的能力;f)首件质量与其质量记录是否相符,质量问题是否按规定得到处理;g)有顾客要求的工序是否经顾客签署认可。
零部件首件检验审核项点审查表解读
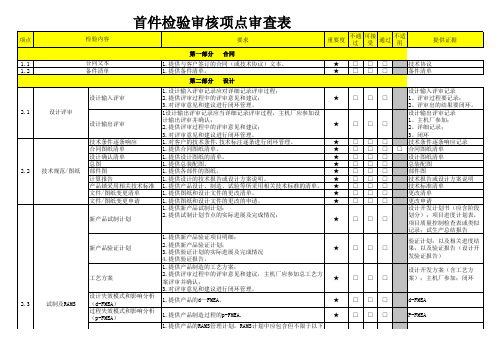
★
□
□
□
★
□
□
□
2.3
试制及RAMS
★ ★Biblioteka □ □□ □□ □
d-FMEA P-FMEA
2.3 项点
试制及RAMS 检验内容 要求 重要度 1.提供产品的RAMS管理计划,RAMS计划中应包含但不限于以下 内容: (1)确定必须得RAMS资源和人员的责任 (2)可靠性预计 (3)可靠性分配(需要时) ★ (4)有效性,安全性分析 (5)预防性维修分析 (6)全寿命周期成本分析 (7)故障树分析(需要时) 1.提供产品试制总结; ★ 2.提供产品试制后整改的情况。 第三部分 同类产品历史记录 ★ □ □ □ □ 故障统计表; 整改报告。 试验大纲 型式试验计划(应在设计开 发计划里面) 型式试验报告 □ □ □ □ □ □ □ □ □ □ □ □ □ □ □ □ □ □ □ □ □ □ □ □ □ □ □ □ □ □ □ □ □ □ □ 型式试验报告 试验大纲 例行试验报告 首件尺寸记录 成品出厂检查记录 成品出厂检查记录 工艺要求及实物测试 工艺要求及实物测试 工艺要求及实物测试 成品出厂检查记录 1.提供同类产品的运行故障记录; 2.提供同类产品运行故障的改进措施。 第四部分 型式试验大纲 型式试验计划 型式试验 ★★ ★★ ★★ ★★ ★★ ★★ ★★ ★★ ★★ ★★ ★★ ★★ ★★ ★★ ★★ ★★ ★★ ★★ ★★ □ □ □ □ 1.提供按相关规定确认的型式试验大纲 1.提供型式试验计划; 2.提供型式试验计划完成情况。 1.提供具有相关资质部门的型式试验报告,报告内容包含但不 限于以下内容: (1)机械性能试验程序与报告 (2)电气性能试验程序与报告 (3)环境试验程序与报告 (4)耐久性试验程序与报告 1.型式试验结果必须符合试验大纲和技术条件要求。 第五部分 例行试验 1.提供按相关规定确认的例行试验大纲。 1.提供产品的例行试验报告。 1.进行产品实物质量的外观检查。 1.对产品的相关尺寸进行检测 1.对产品的功能是试验进行测试。 1.对产品的紧固件紧固情况及防松标识进行检查。 1.对电气的布线情况进行检查。 1.检查电气连接是否正确、牢固。 1.对产品的电性能情况进行测试。 第六部分 产品安全性证明 □ 材质报告 □ 工艺方案/特殊过程和关键 工序 1.检查产品的烟火试验报告 1.提供“八防”的措施或方案。 不通 可接 不适 通过 过 受 用 提供证据
9-首件检验报告单
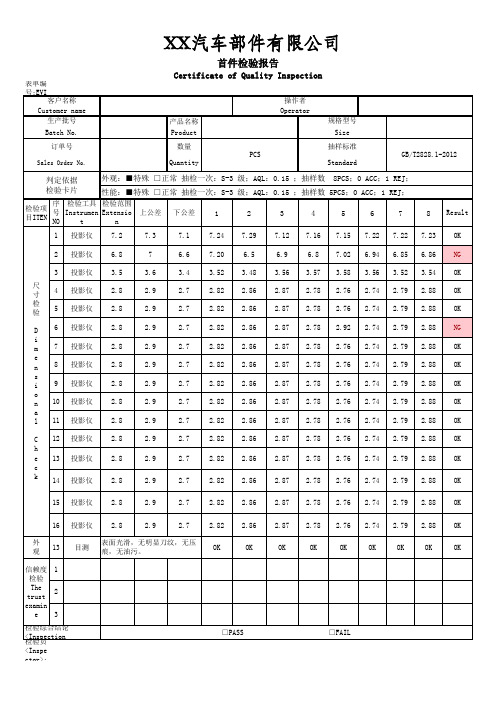
序 号 NO
检验工具 Instrumen
t
检验范围 Extensio
n
上公差
下公差
1
2
3
4
5
6
7
8
Result
1 投影仪 7.2
7.3
7.1
7.24 7.29 7.12 7.16 7.15 7.22 7.22 7.23 OK
2 投影仪 6.8
7
6.6
7.20
6.5
6.9
6.8 7.02 6.94 6.85 6.86 NG
XX汽车部件有限公司
表单编 号:EVI
客户名称 Customer name
生产批号
Batch No.
首件检验报告
Certificate of Quality Inspection
产品名称 Product
操作者 Ope Sales Order No.
数量 PCS
Quantity
OK
OK
OK
OK
OK
信赖度 1
检验
The trust
2
examin
e3
检验综合结论 检 <I验ns员pection <Inspe ctor>:
□PASS
□FAIL
C 12 投影仪
2.8
2.9
2.7
2.82 2.86 2.87 2.78 2.76 2.74 2.79 2.88 OK
h
e 13 投影仪
2.8
2.9
2.7
2.82 2.86 2.87 2.78 2.76 2.74 2.79 2.88 OK
c
k 14 投影仪
2.8
首件检验
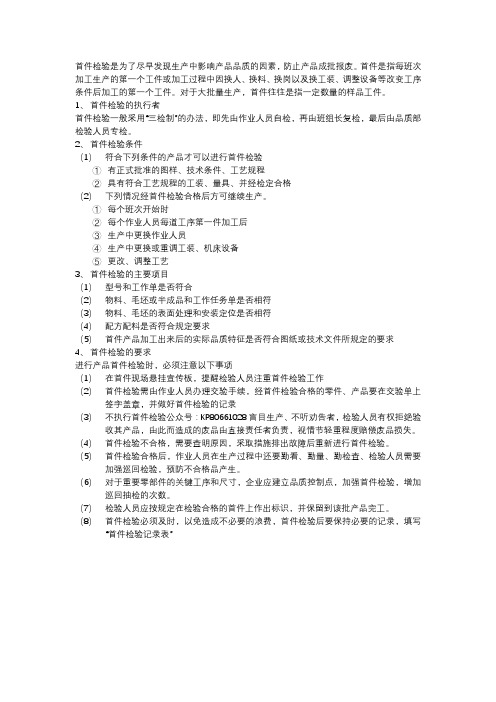
首件检验是为了尽早发现生产中影响产品品质的因素,防止产品成批报废。
首件是指每班次加工生产的第一个工件或加工过程中因换人、换料、换岗以及换工装、调整设备等改变工序条件后加工的第一个工件。
对于大批量生产,首件往往是指一定数量的样品工件。
1、首件检验的执行者首件检验一般采用“三检制”的办法,即先由作业人员自检,再由班组长复检,最后由品质部检验人员专检。
2、首件检验条件(1)符合下列条件的产品才可以进行首件检验①有正式批准的图样、技术条件、工艺规程②具有符合工艺规程的工装、量具、并经检定合格(2)下列情况经首件检验合格后方可继续生产。
①每个班次开始时②每个作业人员每道工序第一件加工后③生产中更换作业人员④生产中更换或重调工装、机床设备⑤更改、调整工艺3、首件检验的主要项目(1)型号和工作单是否符合(2)物料、毛坯或半成品和工作任务单是否相符(3)物料、毛坯的表面处理和安装定位是否相符(4)配方配料是否符合规定要求(5)首件产品加工出来后的实际品质特征是否符合图纸或技术文件所规定的要求4、首件检验的要求进行产品首件检验时,必须注意以下事项(1)在首件现场悬挂宣传板,提醒检验人员注重首件检验工作(2)首件检验需由作业人员办理交验手续,经首件检验合格的零件、产品要在交验单上签字盖章,并做好首件检验的记录(3)不执行首件检验公众号:KP80661028盲目生产、不听劝告者,检验人员有权拒绝验收其产品,由此而造成的废品由直接责任者负责,视情节轻重程度赔偿废品损失。
(4)首件检验不合格,需要查明原因,采取措施排出故障后重新进行首件检验。
(5)首件检验合格后,作业人员在生产过程中还要勤看、勤量、勤检查、检验人员需要加强巡回检验,预防不合格品产生。
(6)对于重要零部件的关键工序和尺寸,企业应建立品质控制点,加强首件检验,增加巡回抽检的次数。
(7)检验人员应按规定在检验合格的首件上作出标识,并保留到该批产品完工。
(8)首件检验必须及时,以免造成不必要的浪费,首件检验后要保持必要的记录,填写“首件检验记录表”。
浅谈对首件检验、首件鉴定、首件批准的认识

浅谈对首件检验、首件鉴定、首件批准的认识摘要:在装备产品研制过程中,应按照要求对全过程进行全面有效的过程控制,以保障装备产品质量可靠。
通过首件检验、首件鉴定、首件批准等措施方法,可以有效落实对过程的控制。
关键词:首件检验,首件鉴定,首件批准在装备产品研制中,对于过程的控制和管理,应严格落实国家军用标准要求,包括GJB 9001C-2017《质量管理体系要求》、GJB/Z 16-1991《军工产品质量管理要求与评定导则》、GJB 1405A-2006《装备质量管理术语》等,1.首件检验根据《装备质量管理术语》,首件检验是对批量加工的第一件产品所进行的自检和检验员专检的活动,主要在批量加工阶段执行。
首件检验主要是为了尽早发现生产过程中影响产品质量的因素,防止产品出现成批超差、返修、报废。
当首件检验合格后方可进入正式生产。
检验包括文件检查和实物检查,重点关注首件产品实际质量是否满足图纸或技术文件要求。
通常在以下情况应进行首件检验:(1)首次投产的首件产品(2)每个工作班、连续生产交接班后的首件产品;(2)更换操作者后的首件产品;(3)更换或调整设备、工艺装备后生产的首件产品;(4)更改技术条件、工艺方法和参数后生产的首件产品;(5)原材料或毛坯更改后生产的首件产品。
首件检验一般采用“三检制”,即自检、互检、专检,检验是否合格应由最后的专职检验认可给出结论;若首件检验不合格,应查明原因、落实措施后加工并通过“三检”合格后,再启动批量加工。
目前《质量管理体系要求》中对军工产品首件检验规定了自检和专检,不再强制要求互检。
2.首件鉴定首件鉴定是对试生产的第一件(批)零部(组)件进行全面的过程和成品检查,以确定规定的过程、设备及人员等要求能否保证持续地生产出符合设计要求的产品。
首件鉴定产品的制造方法应能代表后续批量生产产品的制造方法,首件鉴定关注的重点是制造过程能力。
一般新产品试制、批生产中产品或者生产过程发生重大变更后首次加工零组件、停产两年以上恢复生产或顾客提出要求时,均应该进行首件鉴定。