精益管理专业术语-B系列
精益生产知识点

5.加工的Muda。
• Waiting • Manual Touches
6.等待的Muda。
7.搬运的Muda。
消除浪费 持续改善
Tenants of Single Piece Flow
Do Not Make Defects Do Not Pass Along Defects Do Not Accept Defects
Example: 我们正常工作时间为:=5days/week*8h/day*60m/h*60s/m=144000s/w 客户需求:=1000pcs/w 则:takt time=144000/1000=144s/pcs TT是TAKT Time,原本是由音槳上所引用過來的一個概念。 TAKT是德文,它的原意就是節拍的意思,是指在交響樂的演奏過程 中,要將整個樂團導向一個合諧、順暢的結果,變成一個Flow的呈現 。 所以在Lean的想法中,TAKT Time指的就是節拍時間,以客戶的需求 來趨動整個生產線的節奏,達到一個暢流式(Flow)生產的做法。 而最完美的境界是希望能達到One-Piece Flow (單件流)的工作方式。
系数)*(1+宽放),即生产节拍. 2) T.T根据是客户定单而定的节拍时间:T.T=每日的运转时间(定时)/客
户每日需求生产量(由生产计划分解),即客户需求节拍. 2.针对问题:周期时间可分为产品生产周期和单工位作业周期. 1)生产线的节拍时间为8S,周期时间是7+8+7=22S(产品生产周期). 2)生产线的节拍时间为8S,工位作业周期=工位标准工时. 3.了解C.T和T.T的意义在于: 1)当C.T>T.T时,说明生产无法满足客户需求.应进行改善(或加人),降低
精益术语汇编
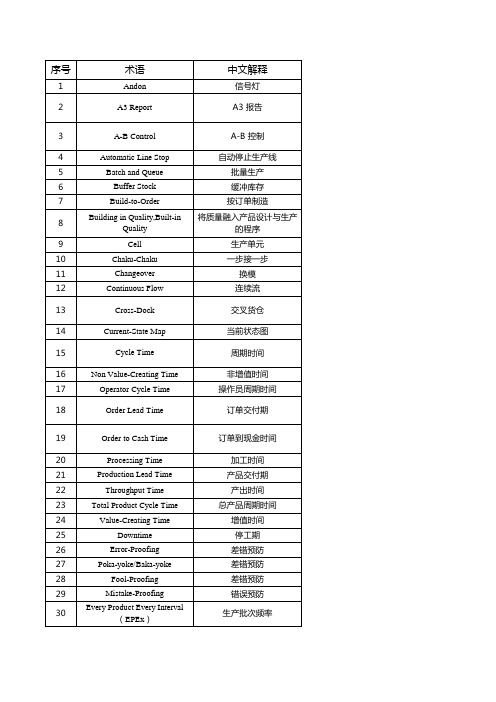
通过更换模具(安装:Set-up),用同样的机器或装配线生产不同的产品 一个用来分类和重新组合众多供应商所提供的不同产品的厂房,继而再将经过分类或 装配的产品发至不同的顾客。 指制造一件产品需要的时间,其时间等于操作时间加上必要的准备、装载及卸载的时 间之和。 不增加产品价值的活动上的时间,如库存、检查、返工等。 产品交付期加上将产品运输到客户的时间,包括处理订单的延误、将订单输入生产系 统的时间,或由于顾客订单超过生产能力而导致的等待时间等。 从收到顾客订单到收到货款所经过的时间。其时间长短取决于生产方式(按单生产、 存货生产等)。 设计或生产一个产品的时间。 生产一件产品,从开始到结束所需要的时间。(“门到门时间”) 在生产过程中可以为顾客增加价值的工序时间。 计划的或是未计划的停工而损失的生产时间。 防止操作员在工作中出现由于选错、遗漏,或是装反零件等操作而导致质量缺陷的方 法。
中文解释
信号灯 A3 报告 A-B 控制 自动停止生产线 批量生产 缓冲库存 按订单制造 将质量融入产品设计与生产 的程序 生产单元 一步接一步 换模 连续流 交叉货仓 当前状态图 周期时间 非增值时间 操作员周期时间 订单交付期 订单到现金时间 加工时间 产品交付期 产出时间 总产品周期时间 增值时间 停工期 差错预防 差错预防 差错预防 错误预防 生产批次频率
库存超市与顺序拉动系统 推动生产 适度装备 减少转换时间 一分钟换模 单件流 标准库存 标准化操作
103 104 105 106 107 108 109 110 111 112 113
标准化操作组合表 标准化操作表 节拍意识 节拍时间 目标成本 全面生产维护 价值图 可视化管理 约束理论 最优生产技术
习惯上常把主要特征值的累计百分数达70%~80%的若干因素称为A类,累计百分数 在10%~20%区间的若干因素称为B类,累计百分数在10%左右的若干因素称C类
精益常用术语

1、安灯(Andon)或称Andon,按灯,日语“灯”的意思。
是目视管理的一种工具,让人一眼看出工作状态,并在有任何异常情况时(如机器停机、质量问题、工装故障、操作员的延误、以及材料短缺等)发出信号。
同样也可以通过计划与实际产量的比值来反映生产状态。
现场出现各种问题致生产线停止时,操作员通过“灯绳”启动信号灯,或自动启动信号灯。
现场管理人员由此快速做出反应。
2、A-B控制(A-B Control)一种控制两台机器或是两个工位之间生产关系的方法,用于避免过量生产,确保资源的平衡使用。
图示中,除非满足下面三个条件,否则任何一台机器或传送带都不能运行:A机器已装满零件;传送带上有标准数量的在制品(本例中为一件);B机器上没有零件。
只有当这三个条件都满足的时候,才可以进行一个生产周期,然后等再次满足这些条件时,再进行下一个周期。
3、A3报告(A3 Report)一种由丰田公司开创的方法,通常用图形把问题、分析、改正措施、以及执行计划囊括在一张A3纸上。
在丰田公司,A3报告已经成为一个标准方法,用来总结解决问题的方案,进行状态报告,以及绘制价值流图。
国际通用的A3纸是指宽297毫米,长420毫米的纸张。
4、标准作业(Standardized Work)或称标准化作业、标准化操作。
为生产工序中每一名操作员都建立准确的工作程序,以人的动作为中心,按没有浪费的操作顺序进行生产的方法。
以下面三个因素作为基础:节拍时间,是指一个生产工序,能够符合顾客需求的制造速度。
准确的工作顺序,操作员在节拍时间里,要按照这个顺序来工作。
标准在制品(包括在机器里的产品),用来保证生产过程能够平顺的运转。
标准作业完成并发布后,就成为Kaizen(改善)的目标。
标准作业的好处包括:能够记录所有班次的工作,减少可变性,更易于培训新员工,减少工伤或疲劳,以及提供改进活动的基础数据。
因此它是管理生产现场的依据,也是寻求改善的基础。
5、标准作业表(Standardized Work Chart)或称标准作业票,标准化操作表。
39个精益管理术语,都在这里了...
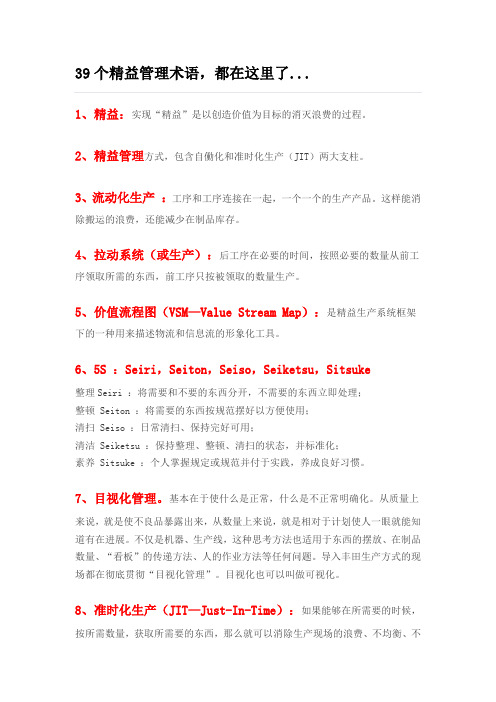
39个精益管理术语,都在这里了...1、精益:实现“精益”是以创造价值为目标的消灭浪费的过程。
2、精益管理方式,包含自働化和准时化生产(JIT)两大支柱。
3、流动化生产:工序和工序连接在一起,一个一个的生产产品。
这样能消除搬运的浪费,还能减少在制品库存。
4、拉动系统(或生产):后工序在必要的时间,按照必要的数量从前工序领取所需的东西,前工序只按被领取的数量生产。
5、价值流程图(VSM—Value Stream Map):是精益生产系统框架下的一种用来描述物流和信息流的形象化工具。
6、5S :Seiri,Seiton,Seiso,Seiketsu,Sitsuke整理Seiri :将需要和不要的东西分开,不需要的东西立即处理;整顿 Seiton :将需要的东西按规范摆好以方便使用;清扫 Seiso :日常清扫、保持完好可用;清洁 Seiketsu :保持整理、整顿、清扫的状态,并标准化;素养 Sitsuke :个人掌握规定或规范并付于实践,养成良好习惯。
7、目视化管理。
基本在于使什么是正常,什么是不正常明确化。
从质量上来说,就是使不良品暴露出来,从数量上来说,就是相对于计划使人一眼就能知道有在进展。
不仅是机器、生产线,这种思考方法也适用于东西的摆放、在制品数量、“看板”的传递方法、人的作业方法等任何问题。
导入丰田生产方式的现场都在彻底贯彻“目视化管理”。
目视化也可以叫做可视化。
8、准时化生产(JIT—Just-In-Time):如果能够在所需要的时候,按所需数量,获取所需要的东西,那么就可以消除生产现场的浪费、不均衡、不合理,提高生产效率。
该思想的开山鼻祖是丰田汽车的创始人-丰田喜一郎,其后继者将此思想展开,概括成为了一个生产体系。
不单是in time, 而是just in time,这是一个重要的关键。
“Just-In-Time”和“自働化”共同形成丰田生产方式的两大支柱。
9、自働化(Jidoka):在丰田的生产方式当中,必须完全是带人字旁的“自働化”。
精益术语

精益术语
三定三要素:定点、定容、定量,场所、方法、标识
三全:全员、全方位、全过程
致胜法宝:
改善,持续改善!
三讲:
讲热情、讲方向、讲方法
三化:
省力化、少人化、自働化
企业文化:
思考、勤奋、忠诚
企业价值观:
1110
企业经营理念:
低成本制造优质产品
四不伤害:
不伤害自己、不伤害他人、不被他人伤害、保护他人不被伤害
四不放过:
事故原因没查清不放过、事故责任者未受到处理不放过、事故责任者和周围群众未受到教育不放过,事故制定切实可行的防范措施未落实不放过
我们的追求:
深入人心的改善哲学,
无处不在的改善文化!。
精益专业名词缩写
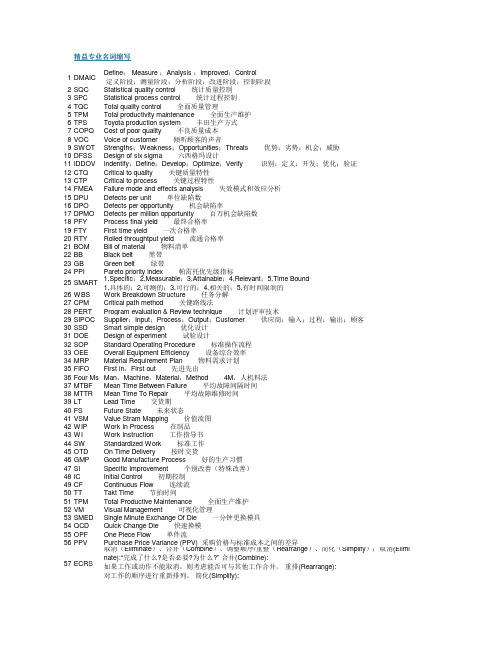
精益专业名词缩写1DMAIC Define ; Measure ;Analysis ;Improved ;Control定义阶段;测量阶段;分析阶段;改进阶段;控制阶段2SQC Statistical quality control 统计质量控制3SPC Statistical process control 统计过程控制4TQC Total quality control 全面质量管理5TPM Total productivity maintenance 全面生产维护6TPS Toyota production system 丰田生产方式7COPQ Cost of poor quality 不良质量成本8VOC Voice of customer 倾听顾客的声音9SWOT Strengths ;Weakness ;Opportunities ;Threats 优势;劣势;机会;威胁10DFSS Design of six sigma 六西格玛设计11IDDOV Indentify ;Define ;Develop ;Optimize ;Verify 识别;定义;开发;优化;验证12CTQ Critical to quality 关键质量特性13CTP Critical to process 关键过程特性14FMEA Failure mode and effects analysis 失效模式和效应分析15DPU Defects per unit 单位缺陷数16DPO Defects per opportunity 机会缺陷率17DPMO Defects per million opportunity 百万机会缺陷数18PFY Process final yield 最终合格率19FTY First time yield 一次合格率20RTY Rolled throughtput yield 流通合格率21BOM Bill of material 物料清单22BB Black belt 黑带23GB Green belt 绿带24PPI Pareto priority index 帕雷托优先级指标25SMART 1,Specific ;2,Measurable ;3,Attainable ;4,Relevant ;5,Time Bound 1,具体的;2,可测的;3,可行的;4,相关的;5,有时间限制的26WBS Work Breakdown Structure 任务分解27CPM Critical path method 关键路线法28PERT Program evaluation & Review technique 计划评审技术29SIPOC Supplier ;Input ;Process ;Output ;Customer 供应商;输入;过程;输出;顾客30SSD Smart simple design 优化设计31DOE Design of experiment 试验设计32SOP Standard Operating Procedure 标准操作流程33OEE Overall Equipment Efficiency 设备综合效率34MRP Material Requirement Plan 物料需求计划35FIFO First in ,First out 先进先出36Four Ms Man ,Machine ,Material ,Method 4M ,人机料法37MTBF Mean Time Between Failure 平均故障间隔时间38MTTR Mean Time To Repair 平均故障维修时间39LT Lead Time 交货期40FS Future State 未来状态41VSM Value Stram Mapping 价值流图42WIP Work In Process 在制品43WI Work Instruction 工作指导书44SW Standardized Work 标准工作45OTD On Time Delivery 按时交货46GMP Good Manufacture Process 好的生产习惯47SI Specific Improvement 个别改善(特殊改善)48IC Initial Control 初期控制49CF Continuous Flow 连续流50TT Takt Time 节拍时间51TPM Total Productive Maintenance 全面生产维护52VM Visual Management 可视化管理53SMED Single Minute Exchange Of Die 一分钟更换模具54QCD Quick Change Die 快速换模55OPF One Piece Flow 单件流56PPV Purchase Price Variance (PPV) 采购价格与标准成本之间的差异57ECRS 取消(Eliminate )、合并(Combine )、调整顺序/重整(Rearrange )、简化(Simplify );取消(Eliminate):“完成了什么?是否必要?为什么?” 合并(Combine): 如果工作或动作不能取消,则考虑能否可与其他工作合并。
精益生产词汇

精益生产专业词汇解释A3 Report ||A3报告A-B Control ||A-B控制Act||行动Andon ||信号灯Apparent Efficiency||表面效率Automatic Line Stop ||自动停止生产线Batch and Queue ||批量生产Batch and Queue||批量与队列breakthrough kaizen||突破性改善Buffer Stock ||缓冲库存Capital Linearity ||线性化的设备投资Capital Linearity||投资线性化Cell ||生产单元Chaku-Chaku ||一步接一步Change Agent ||实施改变的领导者Changeover ||换模Check||检查Chief Engineer ||总工程师Continuous Flow||连续流Cross-dock||交叉货仓Cycle Time ||周期时间Demand Amplification||需求扩大Design-In ||共同设计Do||实施Downtime ||停工期Effective Machine Cycle Time||有效机器周期时间Efficiency ||效率EPEx||生产批次频率Error-Proofing||预防差错Every Product Every Interval ||EPEx ||生产批次频率Fill-Up System ||填补系统Finished Goods||成品First In, First Out ||FIFO ||先进先出Five Whys ||五个“为什么”Fixed-Position Stop System ||固定工位来停止生产Fixed-Position Stop System||固定位置停止系统Flow Production ||流水线生产Four Ms ||四MGemba||现场Greenfield ||新建工厂Heijunka ||均衡化Heijunka Box||生产均衡柜Heijunka||均衡化Inspection||检查Inventory ||库存Inventory Turns ||库存周转率Jidoka ||自动化Jishuken||自主研修JIT||及时生产job breakdown||任务细分书job element||工作要点书Just-In-Time||及时生产Kaikaku ||突破性改善Kaizen ||改善Kaizen Workshop ||改善研习会Kaizen||改善Kanban ||看板Labor Linearity||人力线性化Lean Enterprise ||精益企业Lean Logistics ||精益物流Lean Production ||精益生产Local Efficiency||局部效率Machine Cycle Time||机器周期时间Mass Production||大规模制造Material Flow||材料流Material Flow||物料流Mixed Supermarket and Sequential Pull System||库存超市与顺序拉动混合系统Monuments||大型装备Muda||浪费Multi-Process Handling||多工序操作Non Value-Creating ||非增值Non Value-Creating Time||非增值时间One-Piece Flow||单件流。
精益生产管理中的常见术语(一)
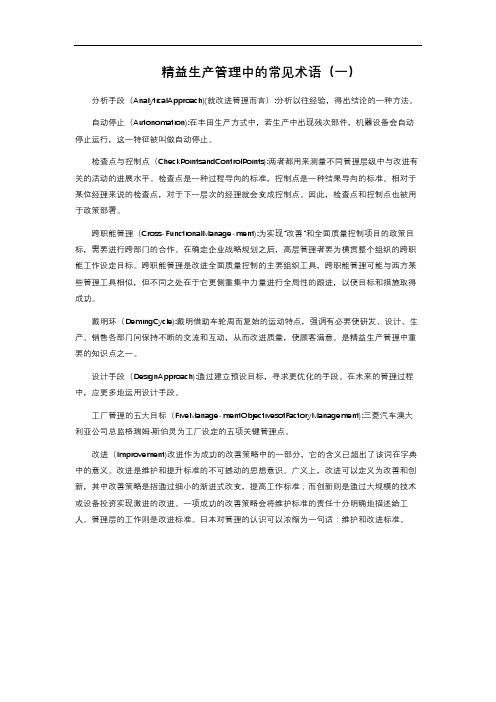
精益生产管理中的常见术语(一)分析手段(AnalyticalApproach)(就改进管理而言):分析以往经验,得出结论的一种方法。
自动停止(Autonomation):在丰田生产方式中,若生产中出现残次部件,机器设备会自动停止运行,这一特征被叫做自动停止。
检查点与控制点(CheckPointsandControlPoints):两者都用来测量不同管理层级中与改进有关的活动的进展水平。
检查点是一种过程导向的标准,控制点是一种结果导向的标准。
相对于某位经理来说的检查点,对于下一层次的经理就会变成控制点。
因此,检查点和控制点也被用于政策部署。
跨职能管理(Cross-FunctionalManage-ment):为实现“改善”和全面质量控制项目的政策目标,需要进行跨部门的合作。
在确定企业战略规划之后,高层管理者要为横贯整个组织的跨职能工作设定目标。
跨职能管理是改进全面质量控制的主要组织工具,跨职能管理可能与西方某些管理工具相似,但不同之处在于它更侧重集中力量进行全局性的跟进,以使目标和措施取得成功。
戴明环(DemingCycle):戴明借助车轮周而复始的运动特点,强调有必要使研发、设计、生产、销售各部门间保持不断的交流和互动,从而改进质量,使顾客满意。
是精益生产管理中重要的知识点之一。
设计手段(DesignApproach):通过建立预设目标,寻求更优化的手段。
在未来的管理过程中,应更多地运用设计手段。
工厂管理的五大目标(FiveManage-mentObjectivesofFactoryManagement):三菱汽车澳大利亚公司总监格瑞姆·斯伯灵为工厂设定的五项关键管理点。
改进(Improvement)改进作为成功的改善策略中的一部分,它的含义已超出了该词在字典中的意义。
改进是维护和提升标准的不可撼动的思想意识。
广义上,改进可以定义为改善和创新,其中改善策略是指通过细小的渐进式改变,提高工作标准;而创新则是通过大规模的技术或设备投资实现激进的改进。
精益管理术语
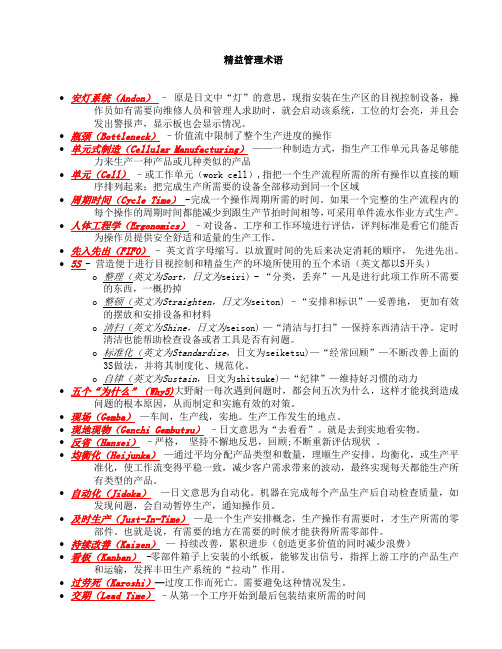
精益管理术语∙安灯系统(Andon)–原是日文中“灯”的意思,现指安装在生产区的目视控制设备,操作员如有需要向维修人员和管理人求助时,就会启动该系统,工位的灯会亮,并且会发出警报声,显示板也会显示情况。
∙瓶颈(Bottleneck)–价值流中限制了整个生产进度的操作∙单元式制造(Cellular Manufacturing)——一种制造方式,指生产工作单元具备足够能力来生产一种产品或几种类似的产品∙单元(Cell)–或工作单元(work cell),指把一个生产流程所需的所有操作以直接的顺序排列起来;把完成生产所需要的设备全部移动到同一个区域∙周期时间(Cycle Time)-完成一个操作周期所需的时间。
如果一个完整的生产流程内的每个操作的周期时间都能减少到跟生产节拍时间相等,可采用单件流水作业方式生产。
∙人体工程学(Ergonomics)–对设备、工序和工作环境进行评估,评判标准是看它们能否为操作员提供安全舒适和适量的生产工作。
∙先入先出(FIFO)–英文首字母缩写。
以放置时间的先后来决定消耗的顺序,先进先出。
∙5S - 营造便于进行目视控制和精益生产的环境所使用的五个术语(英文都以S开头)o整理(英文为Sort,日文为seiri) - “分类,丢弃”—凡是进行此项工作所不需要的东西,一概扔掉o整顿(英文为Straighten,日文为seiton) –“安排和标识”—妥善地,更加有效的摆放和安排设备和材料o清扫(英文为Shine,日文为seison) —“清洁与打扫”—保持东西清洁干净。
定时清洁也能帮助检查设备或者工具是否有问题。
o标准化(英文为Standardize,日文为seiketsu)—“经常回顾”—不断改善上面的3S做法,并将其制度化、规范化。
o自律(英文为Sustain,日文为shitsuke)—“纪律”—维持好习惯的动力∙五个“为什么”(Why5)大野耐一每次遇到问题时,都会问五次为什么,这样才能找到造成问题的根本原因,从而制定和实施有效的对策。
实验室管理学精益管理名词解释
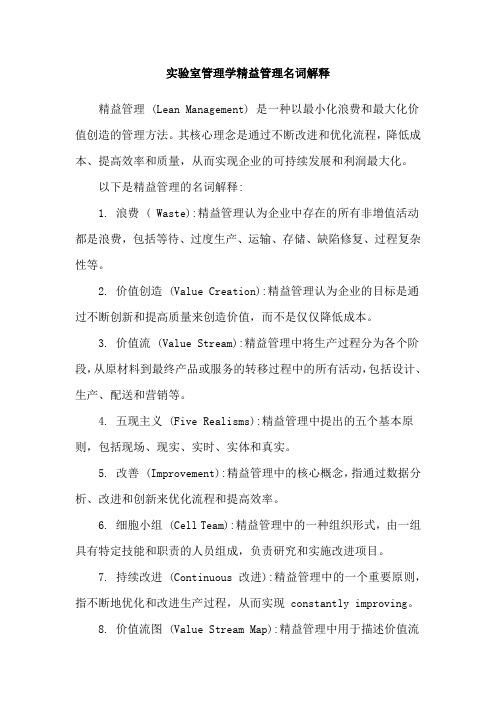
实验室管理学精益管理名词解释精益管理 (Lean Management) 是一种以最小化浪费和最大化价值创造的管理方法。
其核心理念是通过不断改进和优化流程,降低成本、提高效率和质量,从而实现企业的可持续发展和利润最大化。
以下是精益管理的名词解释:1. 浪费 ( Waste):精益管理认为企业中存在的所有非增值活动都是浪费,包括等待、过度生产、运输、存储、缺陷修复、过程复杂性等。
2. 价值创造 (Value Creation):精益管理认为企业的目标是通过不断创新和提高质量来创造价值,而不是仅仅降低成本。
3. 价值流 (Value Stream):精益管理中将生产过程分为各个阶段,从原材料到最终产品或服务的转移过程中的所有活动,包括设计、生产、配送和营销等。
4. 五现主义 (Five Realisms):精益管理中提出的五个基本原则,包括现场、现实、实时、实体和真实。
5. 改善 (Improvement):精益管理中的核心概念,指通过数据分析、改进和创新来优化流程和提高效率。
6. 细胞小组 (Cell Team):精益管理中的一种组织形式,由一组具有特定技能和职责的人员组成,负责研究和实施改进项目。
7. 持续改进 (Continuous 改进):精益管理中的一个重要原则,指不断地优化和改进生产过程,从而实现 constantly improving。
8. 价值流图 (Value Stream Map):精益管理中用于描述价值流的图形化工具,可以帮助企业分析和优化生产过程。
9. 浪费可视化 ( Waste Visualization):精益管理中的一种方法,通过可视化浪费,帮助企业更好地识别和消除浪费。
10. 拉动系统 (Pull System):精益管理中的一种生产组织形式,强调由客户需求来拉动生产,而不是通过堆积和过量生产来响应客户需求。
21个精益生产专业术语!一定要记住哦!
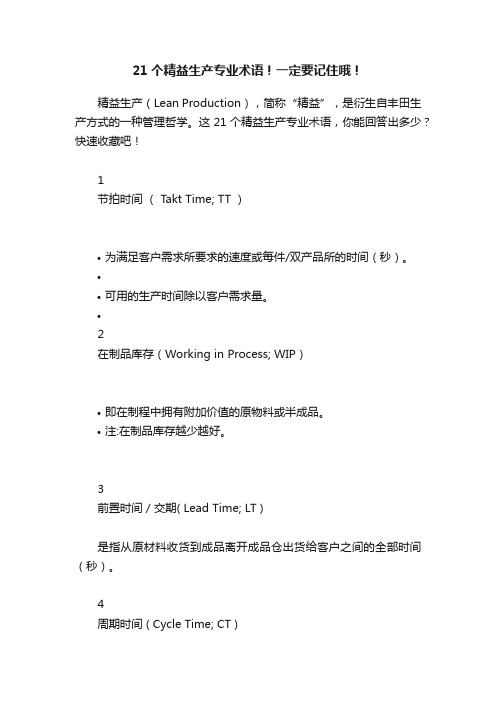
21个精益生产专业术语!一定要记住哦!精益生产(Lean Production),简称“精益”,是衍生自丰田生产方式的一种管理哲学。
这21个精益生产专业术语,你能回答出多少?快速收藏吧!1节拍时间( Takt Time; TT )•为满足客户需求所要求的速度或每件/双产品所的时间(秒)。
••可用的生产时间除以客户需求量。
•2在制品库存(Working in Process; WIP)•即在制程中拥有附加价值的原物料或半成品。
•注:在制品库存越少越好。
3前置时间 / 交期( Lead Time; LT )是指从原材料收货到成品离开成品仓出货给客户之间的全部时间(秒)。
4周期时间 ( Cycle Time; CT )观察测量得出完成一个作业的时间。
更正确的说,是工人完成该工位的工作步骤,并周而复始,到下一个产品开始的时间(秒)。
5总周期时间 ( Total Cycle Time; TCT )某一特定产品的生产速度,等于该产品各工序CT之和。
6每人每时的生产力 (Pairs per People per hour; PPH )是一种衡量生产力和直接劳动力成本的可靠方法,双/人/时。
7及时生产(Just in Time; JIT)下一道工序需要的时候,生产需要的产品和数量。
8首次通过率 ( First Time Through; FTT )计算工件在每一工序成功完成的百分比(不含报废或返工),此为测量首次就能生产无瑕疵的、无须返修的产品的能力。
9转换时间 ( Change Over; CO)介于上一批次A最后一件产品完成的时间与下一批次B第一件产品产出的间隔时间。
说明:B的第1双需为良品,且后续产出的B亦需为连续产出的良品。
10快速切换 ( Quickly Change Over; QCO )在output 之A→B鞋型转换时,仍维持原TT标准之产出即为快速切换之目标。
11先入先出(First in First Out; FIFO)置时间的先后来决定消耗的顺序,先进先出。
精益专业术语解释
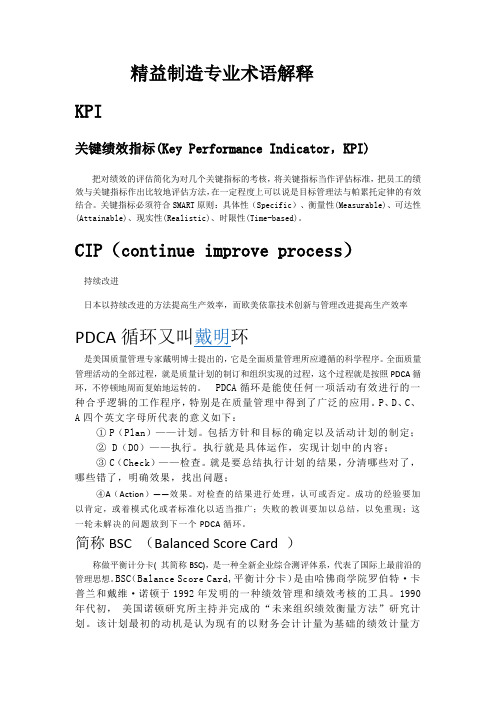
精益制造专业术语解释KPI关键绩效指标(Key Performance Indicator,KPI)把对绩效的评估简化为对几个关键指标的考核,将关键指标当作评估标准,把员工的绩效与关键指标作出比较地评估方法,在一定程度上可以说是目标管理法与帕累托定律的有效结合。
关键指标必须符合SMART原则:具体性(Specific)、衡量性(Measurable)、可达性(Attainable)、现实性(Realistic)、时限性(Time-based)。
CIP(continue improve process)持续改进日本以持续改进的方法提高生产效率,而欧美依靠技术创新与管理改进提高生产效率PDCA循环又叫戴明环是美国质量管理专家戴明博士提出的,它是全面质量管理所应遵循的科学程序。
全面质量管理活动的全部过程,就是质量计划的制订和组织实现的过程,这个过程就是按照PDCA循环,不停顿地周而复始地运转的。
PDCA循环是能使任何一项活动有效进行的一种合乎逻辑的工作程序,特别是在质量管理中得到了广泛的应用。
P、D、C、A四个英文字母所代表的意义如下:① P(Plan)——计划。
包括方针和目标的确定以及活动计划的制定;② D(DO)——执行。
执行就是具体运作,实现计划中的内容;③ C(Check)——检查。
就是要总结执行计划的结果,分清哪些对了,哪些错了,明确效果,找出问题;④A(Action)——效果。
对检查的结果进行处理,认可或否定。
成功的经验要加以肯定,或着模式化或者标准化以适当推广;失败的教训要加以总结,以免重现;这一轮未解决的问题放到下一个PDCA循环。
简称BSC (Balanced Score Card )称做平衡计分卡( 其简称BSC),是一种全新企业综合测评体系,代表了国际上最前沿的管理思想。
BSC(Balance Score Card,平衡计分卡)是由哈佛商学院罗伯特·卡普兰和戴维·诺顿于1992年发明的一种绩效管理和绩效考核的工具。
精益生产专业名词解释

TPS(Toyota Production System)------丰田生产系统Lean Production System ------精益制造体系、精益生产IE (Industrial Engineering)工业工程WIP(WORK IN PROCESS)------在制品库存7S(Seiri、Seiton、Seiso、Standardize、Sustain、Satety、Save) ------整理、整顿、清扫、清洁、素养、安全、微笑SOP(Standard Operation Procedure)-------标准作业指导书QST-------品质允收标准OTT-------所有主、副料到位的时间T/T(Takt Time)-------(节拍时间)作业人员一天或一月的有效工作时数除以市场一天或一月的确定订单数C/T -------(周期时间)在制品加工时间,不含休息时间;L/T-------(前置时间)在制品加工总时间,含休息时间及其它所有等待浪费时间SOP-------作业标准(含时间量度)PPP(Production Preparation Process)-------产前准备过程GSD(GENERAL SEWING DATA)--------通用車縫數據KPI(Key Performance Indication)------重要绩效指标TOTAL------总数Layout------ 布置图JIT (Just In Time) -----即时化管理PDCA(Plan、Do、Check、Action )------计划、行动、检查、实施Bottleneck------瓶颈Line Balance ------生产线平衡PM--------生产排期(估算工厂及生产线的产能并根据客人订单数量及交期进行计划安排生产)QCO------(quick change over)快速转款E------: Elimination剔除C------ Combination合并R------: Re-arrangement重排S------ Simplification简化ISO ( International Organization for Standardization) ------国际标准组织WF (Work factor system) -----工作因素法FMS (Flexible Manufacture System) ------弹性制造系统TPM(Total Production Management)------全面生产管理TQM(Total Quality Management)------全面品质管理QE (quality engineering)------ 品质工程人员QIT(Quality Improvement Team)------ 品质改善小组CAM(Computer-aided-manufacturing)------计算机辅助制造CAD(Computer-aided-design)------计算机辅助设计CAE(Computer-aided-engineering)------计算机辅助工程CAPP(Computer-aided-process planning)------计算机辅助工艺编制BMS(Basic motion study)------基本动作世界研究法ABC分类法------ ABC Classing MethodPC(Production control) ------生管QCC(Quality Control Circle)------品管圈QE(Quality Engineering) ------品质工程。
精益管理专业术语

精益管理六西格玛——常用专业术语:(筛选)什么是六西格玛西格玛(大写Σ,小写σ)是希腊文的字母,其小写“σ”在统计学中称为标准差。
在六西格玛方法中,用来表示过程的质量水平,其中4σ=6210 /百万,5σ=230/百万,6σ=3.4/百万。
一般企业的产品瑕疵率大约是3~4σ,以4σ而言,相当于每一百万个机会里有6210次误差。
如果企业不断改进流程,达到6σ的程度,即在一百万个机会里只找得出3.4个瑕疪,这样的绩效已经近于完美。
六西格玛作为流程改进方法论,最早是由摩托罗拉公司的比尔·史密斯于1986年提出,于20世纪90年代通过通用电气公司的实践得以发展和完善。
它通过精确的数理统计和分析,找出影响质量的因素并解决问题,力求使产品和服务的质量接近6σ水平。
随着实践的经验积累,六西格玛现在已不仅仅是一个衡量业务流程能力的标准和业务流程优化方法,而是已经衍生成一套成体系的管理哲学,为企业提高绩效提供了一套行之有效的方法,因此为世界各地越来越多的现代企业所采用,并逐渐从制造业、服务业拓展到医院和政府部门。
实施六西格玛管理的好处主要表现在以下几个方面:——提升企业管理能力——提升企业产能——增加财务收益——节约企业运营成本——提高顾客满意度——改进服务水平——形成积极向上的企业文化Five Whys (五个“为什么”)当遇到问题的时候,不断重复问“为什么”,目的要发现隐藏在表面下的问题根源。
例如,一个关于机器故障停机的例子:1.为什么机器停止工作?机器超负荷运转导致保险丝烧断了。
2.为什么机器会超负荷运转?没有能够对轴承进行充分的润滑3.为什么没有给轴承充分的润滑?润滑油泵泵送不足4.为什么泵送不足?润滑泵的转轴过于陈旧,甚至受损发出了“卡嗒卡嗒”的响声。
5.为什么转轴会破旧受损?由于没有安装附加滤网,导致金属碎屑进入了油泵。
如果没有反复的追问“为什么”,操作员可能只会简单的更换保险丝或者油泵,而机器失效的情况仍会再次发生。
精益术语汇编
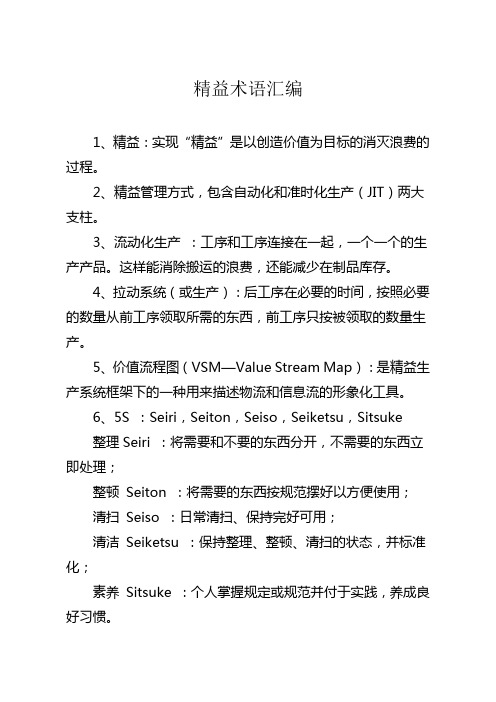
精益术语汇编1、精益:实现“精益”是以创造价值为目标的消灭浪费的过程。
2、精益管理方式,包含自动化和准时化生产(JIT)两大支柱。
3、流动化生产:工序和工序连接在一起,一个一个的生产产品。
这样能消除搬运的浪费,还能减少在制品库存。
4、拉动系统(或生产):后工序在必要的时间,按照必要的数量从前工序领取所需的东西,前工序只按被领取的数量生产。
5、价值流程图(VSM—Value Stream Map):是精益生产系统框架下的一种用来描述物流和信息流的形象化工具。
6、5S :Seiri,Seiton,Seiso,Seiketsu,Sitsuke整理Seiri :将需要和不要的东西分开,不需要的东西立即处理;整顿Seiton :将需要的东西按规范摆好以方便使用;清扫Seiso :日常清扫、保持完好可用;清洁Seiketsu :保持整理、整顿、清扫的状态,并标准化;素养Sitsuke :个人掌握规定或规范并付于实践,养成良好习惯。
7、目视化管理。
基本在于使什么是正常,什么是不正常明确化。
从质量上来说,就是使不良品暴露出来,从数量上来说,就是相对于计划使人一眼就能知道有在进展。
不仅是机器、生产线,这种思考方法也适用于东西的摆放、在制品数量、“看板”的传递方法、人的作业方法等任何问题。
导入丰田生产方式的现场都在彻底贯彻“目视化管理”。
目视化也可以叫做可视化。
8、准时化生产(JIT—Just-In-Time):如果能够在所需要的时候,按所需数量,获取所需要的东西,那么就可以消除生产现场的浪费、不均衡、不合理,提高生产效率。
该思想的开山鼻祖是丰田汽车的创始人-丰田喜一郎,其后继者将此思想展开,概括成为了一个生产体系。
不单是in time, 而是just in time,这是一个重要的关键。
“Just-In-Time”和“自动化”共同形成丰田生产方式的两大支柱。
9、自动化(Jidoka):在丰田的生产方式当中,必须完全是带人字旁的“自动化”。
精益术语(下)

精益术语(下)Inspection (检查)在大批量生产中,专业检验员在制造产品的工序外,检查产品质量的行动。
精益制造商在生产工序中,使用防止错误的设施,并且把质量保证的任务分配给操作员。
如果发现有质量问题,经由质保小组找出问题的源头所在。
这个工序不仅要防止缺陷进入到后续工序,而且要停下来确定原因,并采取纠正措施。
Heijunka Box (生产均衡柜)在固定的时间间隔里,利用看板来平衡产品的型号和数量的工具,称为生产均衡柜。
由于看板槽代表了对材料和信息流的定时,因此看板槽内的每块看板,就代表了生产一种型号产品的一个批量时间(批量时间Pitch =节拍时间×每批次的产品数量)。
例如产品A的批量时间为20分钟,那么每个时间间隔的看板槽里就放一张看板;产品B的批量时间为10分钟,那么每个看板槽里就各放两张看板;产品C的批量时间为40分钟,因此每隔一个看板槽放置一张看板。
产品D和E共用一个生产工序,并且D产品与E产品的需求比例为2:1,因此把D 产品的两张看板分别放在前两个间隔里,而在第三个间隔里放入E产品的一张看板,以此循环下去。
由上文阐述的方法可以看出,生产均衡柜是一个工具,能够在一定时间内,用看板平衡多种产品的混合生产与数量,例如,确保在半小时内,以一个稳定的产品比例,来制造小批量的D和E。
参见:EPEx(每个产品每次间隔),Heijunka(均衡化),Kanban (看板),Material Handling(材料搬运),Paced Withdrawal(有节奏的提取),Pitch(批量时间)。
Heijunka (均衡化)在固定的生产周期内,平衡产品的类型与数量。
这样可以在避免大量生产的同时,有效的满足顾客的需求,最终带来整条价值流中的最优化的库存、投资成本、人力资源以及产品交付期。
举例说明“按照客户需求的产品数量来均衡生产”:假设一个制造商每周都收到500个产品的订单,但是每天收到的订单的产品数量却有着显著的差别:周一要运送200个,周二100个,周三50个,周四100个,周五再运送50个。
- 1、下载文档前请自行甄别文档内容的完整性,平台不提供额外的编辑、内容补充、找答案等附加服务。
- 2、"仅部分预览"的文档,不可在线预览部分如存在完整性等问题,可反馈申请退款(可完整预览的文档不适用该条件!)。
- 3、如文档侵犯您的权益,请联系客服反馈,我们会尽快为您处理(人工客服工作时间:9:00-18:30)。
精益管理专业术语-B系列
1.BatchandQueue(批量生产)
一种生产方法,指不考虑实际的需求,而大批量的生产,导致半产品堆积在下一个生产工序,造成大量库存(包括在制品与成品)。
2.BackFlushing(拉动)
指只有当产品出货时才根据BOM来倒冲人力与物料的消耗,而不是通过物料领用或卡片就直接消耗。
反冲系统的目的是减少非增值的事务性流程。
3.BalancedPlant(均衡化工厂)
一个所有资源与市场需要完全平衡的工厂。
4.Balancedproduction(均衡化生产)
所有动作或生产线以同样节拍来生产。
在均衡化系统中,CT应小于TT。
5.BatchManufacturing(批量制造)
以一个批量的方式在工序与工序之间来生产半制品。
6.Batch-and-Queue(批量序列)
以批量方式生产然后转移到下一工序。
7.Benchmarking(标杆比较)
与其他类似与相关企业来比较关键绩效指标。
8.BillofActivities(活动清单)
生产一个产品或提供一项服务所有的活动清单。
9.BillofMaterials(BoM)(物料清单)
生产一个产品或提供一项服务所有的物料清单
10.BlackBelt(黑带)
在组织内部实施过程改善的六西格玛团队领导。
11.Blitz(闪电)
一种快速和聚集的流程用于改进业务单元,一条生产线、一台机器或者一个流程。
利用跨功能团队和快速解决问题方法,集中制定解决方案来达成较好的目标!
12.Bottleneck(瓶颈)
瓶颈一般是指在整体中的关键限制因素。
瓶颈在不同的领域有不同的含义。
生产中的瓶颈是指那些限制工作流整体水平(包括工作流完成时间,工作流的质量等)的单个因素或少数几个因素。
通常把一个流程中生产节拍最慢的环节叫做“瓶颈”(Bottleneck)。
更广义地讲,所谓瓶颈是指整个流程中制约产出的各种因素。
13.BreakthroughObjectives(突破目标)
组织的“伸展性目标”,代表卓越的改变。
14.BufferStock(缓冲库存)
存放在价值流下游工序的产品。
当顾客需求在短期内突然增加,超过了生产能力时,通常用缓冲库存来避免出现断货的问题。
由于术语“缓冲”与“安全库存”通常交互使用,因此这也常常引起混淆。
这两者之间最重要的差别可以概括为:顾客需求突然出现变化时,缓冲库存能够有效的保护顾客的利益;安全库存则是用来防止上游工序,或是供应商出现生产能力不足的情况。
15.Build-to-Order(按订单制造)
生产者完全按照订单的数量,而不是根据市场需要预测生产,使产品交付期尽可能的满足客户的要求。
这是精益思想家们所力求实现的目标,因为它避免了根据预测生产所必然导致的浪费。