精益生产模块3-价值流图分析详细版教材PDF
精益生产系列课程——价值流分析

3 shifts
40,000 sec/shift
Push
Before
After
225pcs
150pcs
100S
I275
TURN #2 1
OCT
55 seconds
Auto
45 seconds
C/O
90 min
%UP
90%
FPY or RTY VA Space
95% or 72.9% 2ft^2
VA Time
精益生产系列课程
价值流分析
Just In Time
•Takt Time •One-piece Flow •Downstream Pull
TPS
Operational Excellence •Best Cost, Quality, Delivery •Empowered employees •Customer focused culture
VA Space/ratio 2ft^2/(1/300)
VA Time
5 sec
Product travel
660ft
Information flow Manual Product flow Push
Before 550pcs
After 2,100P pcs 1,285NP pcs
0.3D
200
Sec
Visual
5S
Contro
Kanban
ls
SMED
TPM
3P
Creative Idea Suggestion System
Standard Work
Heijunka
•Averaged daily volume & mix •Smooth production schedule
精益生产体系LMS-价值流图
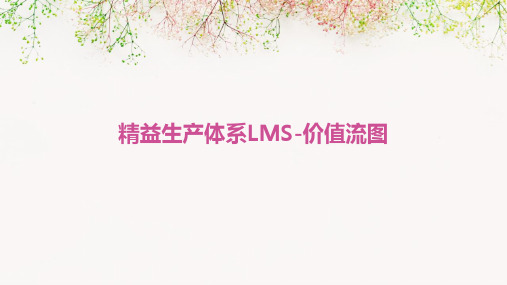
02
价值流现状图
产品流分析
总结词
产品流是价值流的重要组成部分,它描述了产品从原材料到成品 的全过程。
详细描述
产品流分析主要关注产品的生产流程、加工过程、检验过程和包 装过程。通过分析产品流,可以发现生产过程中的瓶颈、浪费和 不必要的环节,为优化生产流程提供依据。
信息流分析
总结词
信息流是价值流中的重要支撑,它确 保了生产过程中的信息传递和协同。
设定关键性能指标(KPIs),对 生产过程进行实时监控,确保生 产稳定、高效地进行。
反馈与调整
反馈机制
01
建立有效的反馈渠道,确保生产过程中的问题能够及时被发现
并传递给相关部门。
调整措施
02
针对发现的问题,制定相应的调整措施,如工艺优化、设备改
造等,以提高生产效率和产品质量。
预防性维护
03
通过对设备进行定期检查和维护,确保设备的稳定运行,减少
故障停机时间。
总结与展望
总结经验教训
对价值流持续改进过程中取得的经验和教训进行总结,为后续的 改进提供参考。
制定改进计划
根据总结的经验和教训,制定下一阶段的改进计划,明确改进目 标、措施和时间表。
展望未来发展
分析行业发展趋势和市场需求变化,预测未来可能面临的挑战和 机遇,制定相应的应对策略。
THANK YOU
缩短交货周期
通过调整生产计划和优化流程 ,预计能缩短交货周期25%。
05
价值流持续改进
持续监控与评估
实时数据采集
通过传感器、RFID等技术,实时 收集生产过程中的数据,确保数 据的准确性和完整性。
数据分析
运用统计分析、数据挖掘等技术, 对收集到的数据进行深入分析, 发现潜在的问题和改进点。
精益生产3VSM(价值流图及价值流分析

针对每个评估指标,制定相应的评估标准,明确达标的具体要求 和标准。
定期调整评估指标
随着企业生产和管理水平的提升,需要定期调整评估指标,以适 应新的发展需求。
绩效评估结果分析
数据收集与整理
收集与评估指标相关的数据,并进行整理、分类 和汇总。
结果分析
运用统计分析方法,对收集的数据进行分析,找 出存在的问题和不足之处。
降低成本
降低生产过程中的成本,包括原材料、 人力、设备等方面的成本。
缩短交货期
通过优化生产流程,缩短产品生产周期 和交货期,提高客户满意度。
流程优化方法
01
价值流分析
通过对生产流程中的价值流进 行分析,识别浪费和非增值活
动,并进行优化。
02
工艺流程再造
对现有的工艺流程进行重新设 计和优化,以提高生产效率和
现场观察
02
深入生产现场,仔细观察员工操作、设备运行、物料流动等实
际情况,发现浪费现象。
员工参与
03
鼓励员工积极参与浪费识别,利用他们对生产过程的了解,发
现潜在的浪费问题。
浪费消除策略
精益改善
通过精益工具和方法,对生产过程 进行持续改进,消除浪费,提高效
率。
自动化与智能化
引入自动化设备和智能化技术,减 少人工操作,降低浪费发生的可能
精益生产3VSM(价值流图及 价值流分析
目录
• 精益生产3VSM概述 • 价值流图绘制及分析 • 浪费识别与消除 • 流程优化与改善 • 绩效评估与持续改进 • 案例分析与应用实例
01
精益生产3VSM概述
精益生产3VSM定义
价值流图(Value Stream Mapping,VSM)是一种 可视化的工具,用于描述产品或服务从原材料到最终
精益生产价值流程图分析及设计
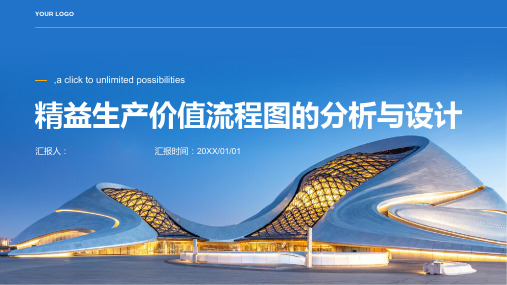
启示:持续改进 与不断创新的重 要性
未来发展趋势预测与展望
精益生产价值流程图在未来的发展趋势 预测未来行业的发展趋势 探讨未来精益生产价值流程图的优化方向 展望未来精益生产价值流程图的应用前景
总结与展望
07
本文总结与亮点回顾
本文主要介绍了精益生产价值流程图的分析与设计方法
分析了精益生产价值流程图在生产过程中的作用和意义
识别价值流程图中的关键活动 确定关键活动的输入和输出 分析关键活动之间的联系和依赖关系 评估关键活动的效率和效益 确定改进的机会和措施
价值流程图的分析工具
价值流程图的基本概念 价值流程图的绘制方法 价值流程图的分析步骤 价值流程图的分析工具:5W1H分析法、流程图分析法、鱼骨图分析法等
价值流程图的分析结果
精益生产价值流程图的持续改进
持续改进的必要性:精益生产价 值流程图需要不断优化和改进, 以适应市场需求和生产环境的变 化。
持续改进的实践:企业需要制定 持续改进计划,并落实到具体实 践中,通过不断尝试和调整,实 现价值流程图的持续改进。
添加标题
添加标题
添加标题
添加标题
持续改进的方法:通过收集数据、 分析流程、调整参数等方式,不 断优化价值流程图,提高生产效 率和降低成本。
精益生产价值流程图有助于企业提高生产效率、降低成本、增强市场竞争力
精益生产价值流程图的作用
识别浪费:通过流程图直观地展示生产过程中的浪费,帮助企业识别并消除不必要的环节 优化流程:通过分析和改进流程图,提高生产效率,降低成本 提升质量:通过流程图的规范化和标准化,减少人为因素对产品质量的影响 促进协作:通过流程图的沟通和协作,提高员工之间的合作和沟通效率
06.
案例分析与 实践经验分 享
精益生产之价值流图ValueStreamMapping
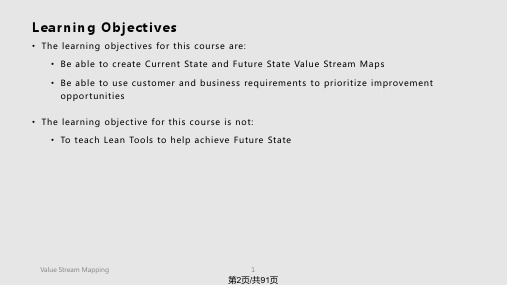
• Identify and Prioritize Improvement Opportunities
Value Stream Mapping
4
第5页/共91页
Value Stream Manager
• Assign Value Stream Manager • One person to manage the mapping of the total flow • Has the capability to make changes across departmental boundaries • Leads the creation and prioritization of the implementation plan for getting from present state to future state • Monitors implementation and updates implementation plan • Driver for results
20,000 pcs/mo Module=100
1/Week 2/Day
Receiving Warehouse
•Raw material •Daily schedule
Forge
•Forge material •Daily schedule
Machine
• Bolts, nuts, washers • Daily schedule
C/O = 60 Min
C/O = 5 Min
C/O = 10 Min
Uptime 75%
Uptime 95%
Uptime 95%
Uptime 95%
Batch Size 100
价值流程图绘制方法(精益生产)

对工作流程进行优化,消除浪费,提高生产效率。
引入新技术
引入新技术和设备,提高生产过程的自动化和智能化水平。
培养员工的价值流意识与能力
培训员工
对员工进行价值流相关培训,提高其对价值流 的认识和理解。
鼓励员工参与
鼓励员工参与到价值流改进过程中,发挥其主 动性和创造性。
建立激励机制
建立激励机制,对在价值流改进中做出贡献的员工给予奖励和表彰。
05
价值流程图的持续改进
定期审查与更新价值流程图
定期审查
价值流程图绘制完成后,应定期进行审 查,以确保其与实际生产过程保持一致 。
VS
更新价值流程图
随着生产过程的改进和变化,价值流程图 也应随之更新,以反映最新的生产状况。
持续改进的策略与方法
识别瓶颈
通过价值流程图,识别生产过程中的瓶颈,并制定相应的改进措 施。
非价值流
描述生产过程的原材料、组件、 信息和能源的来源。
描述生产过程中的浪费环节,如 等待、库存、搬运、重复作业等。
价值流程图的作用
识别生产过程中的浪费
提高生产效率
通过绘制价值流程图,企业可以清晰地看 到生产过程中的浪费环节,从而有针对性 地采取措施消除浪费。
价值流程图可以帮助企业优化生产流程, 减少不必要的环节和等待时间,提高生产 效率。
增强了企业的竞争力。
THANK YOU
服务流程梳理
利用价值流程图对服务流程进行全面梳理,包括客户需求、服务 提供、售后支持等环节。
服务效率提升
基于价值流程图的分析结果,优化服务提供方式,提高服务效率和 质量。
服务创新
通过价值流程图发现服务中的瓶颈和浪费,实施服务创新,如开发 新的服务项目、优化服务流程等。
精益生产3.VSM价值流图及价值流分析课件
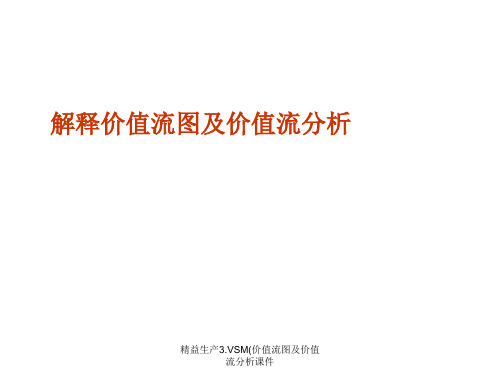
4天
统计数据
50秒 5分钟
LB=34天 T总=170秒
27600秒
99% 4天
50秒
二、什么是价值流分析
1、价值流分析的概念
价值流分析是建立在价值流图基础之上的有效分析 工具,它起源于丰田公司的材料及信息流图“,任何的 生产过程中均存在着材料流和信息流,价值流分析是从 为客户创造价值的视角,将我们的注意力倾注于建立流 动,消除非增值活动,快速增加价值的改进上去,并建 立起材料流和信息流的联系。借助价值流图的价值流分 析,是有效的”学会发现“的手段。
精益生产3.VSM(价值流图及价值 流分析课件
3、价值流图的目标
价值流图是一种强力的可视化工具,它的主要目 标是帮助我们确认运营流程中存在的潜在的,对客户 不增值的浪费活动,价值流图是任何企业展开流程分 析的有效工具,既可作为企业内部沟通的工具,也可 作为企业的战略规划工具,将企业流程所有相关的物 流,信息流和现金流以图示的方式加以表达,有利于 企业了解目标的经营现况和未来的经营现况。绘制一 副现有系统的
附
加
价 值
发布草案
产品X 产品A
月末结算 现金需求
销售报价
定单目录
返回材料需求
概念
原材料
产成品
现金
第0周
第52周
注:图中的APQP代表的含义是“质量先期计划”。
精益生产3.VSM(价值流图及价值 流分析课件
5、价值流图形的信息沟通
由于价值流图形直观地反映了某一产品系 列(价值流)的物资和信息的流动,因此,它 是对过程革新进行目视管理的一种必不可少的 工具。绘制一个过程的图形能够使你清楚地看 到阻碍流动的浪费现象。消除浪费现象能够使 生产的订货提前期缩短,这还会有助于你持续 不断地满足客户的需求。
价值流程图全面教材(现状、改善、未来)精益生产
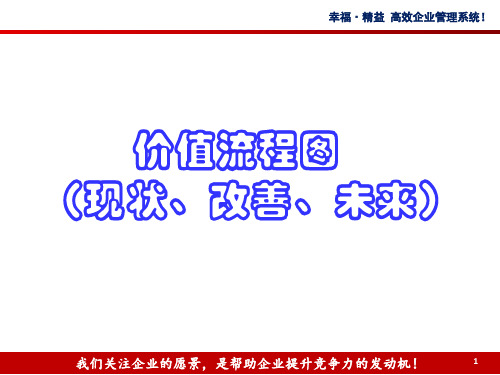
我们关注企业的愿景,是帮助企业提升竞争力的发动机!
26
幸福·精益 高效企业管理系统!
3、到处都有的浪费(MUDA)现象
我们关注企业的愿景,是帮助企业提升竞争力的发动机!
27
幸福·精益 高效企业管理系统!
4、传统VS精益改善解决思路
我们关注企业的愿景,是帮助企业提升竞争力的发动机!
28
幸福·精益 高效企业管理系统!
我们关注企业的愿景,是帮助企业提升竞争力的发动机!
2
幸福·精益 高效企业管理系统!
第一章 精益精髓
• 精益生产概述 • 丰田生产方式核心思想 • 增值与浪费 • 精益模式核心理念 • 丰田生产方式(丰田屋) • 精益十四项原则 • 如何降低库存 • 精益七大终极目标
我们关注企业的愿景,是帮助企业提升竞争力的发动机!
31
幸福·精益 高效企业管理系统!
3、价值流图的基本结构
我们关注企业的愿景,是帮助企业提升竞争力的发动机!
23
幸福·精益 高效企业管理系统!
2、价值流的内容
Requirements
Design
Raw Materials Parts Manufacturing
Assembly Plants
Distribution
Customer
息
流
信
销售& 市场
研发
订单录入 采购/制造/交付 财务 &计划
我们关注企业的愿景,是帮助企业提升竞争力的发动机!
30
幸福·精益 高效企业管理系统!
2、价值流图是一个基本工具
显示信息流、工艺 流、材料流的联系
可借助衡量指 数来了解制造 过程绩效及改 善目标
精益生产之价值流图

未来
第2节 什么是价值流图?
价值流图的定义
价值流图是一种对产品价值流的描述工具;
价值流是指从原材料转变为成品,并赋予价值的全部活动。 包括从供应商处购买的原材料到达企业,企业对其进行加工 后转变为成品再交付客户的全过程,企业内以及企业与供应 商、客户之间的信息沟通形成的信息流也是价值流的一部分。
以客户的眼光审视当前运营效率; 以客户的要求确立未来运营模式; 对比当前与未来,找到更好满足
客户要求的道路方向;
引导
价值流图的作用
解析 当前
从客户服务角度出发,以 增值的角度审视当前运营 模式;
剔除非必要无增值细节, 发现瓶颈,为精益改进 确定方向;
瞄准
浪费
价值 角度
基于客户服务角度,对未 来运营模式进行畅想,追 求最高效率,最低成本;
未来价值流图的原则
头脑风暴法,集合团队的专业智慧; 充分贯彻精益生产理念; 从客户需求条件为出发; 引用前沿先进理念; 考虑均衡性与技术瓶颈的问题;
未来价值流图范本1
未来价值流图范本2
未来价值流图范本3
未来价值流图范本4
未来价值流图范本5
第4节 如何使用价值流图?
价值流图的使用
第1步
• 收集客 户需求 信息
• 绘制客 户需求 模块
第2步
• 跟踪产 品加工 过程
• 收集加 工工序 信息
第3步
• 收集供 应商信 息
• 绘制供 应商模 块
第4步
• 收集信 息系统 数据
• 绘制信 息系统 模块
第5步
• 统计各 工序时 间
• 绘制工 序时间 线
价值流图的绘制原则
从实际出发,以现场实测数据为准; 数据样本数量要多,平均值更可靠; 数据收集过程中,注意异常情况区分; 数据收集过程中发现可改善点需标识; 尽量手动模式,多尝试联系绘制; 多学习,多参考,才能多积累; 集体的智慧结晶,提高队员的参与度;
精益管理之价值流图

精益管理之价值流图一、价值流图的定义价值流图(Value Stream Mapping,简称VSM)是一种用于精益生产的工具,它通过可视化的方式,展现了产品从原材料到成品交付给客户的整个生产流程中,所有的物流、信息流以及价值流的情况。
二、价值流图的组成部分1、物流部分原材料和在制品库存:表示在生产过程中各个环节所存储的原材料和尚未完工的产品。
生产工序:包括加工、装配、检验等各个生产步骤。
每个工序都有相应的操作时间、换模时间、设备利用率等信息。
运输环节:展示原材料、在制品和成品在不同工序之间的运输方式和运输时间。
2、信息流部分生产计划:描述生产计划是如何制定和下达的,包括计划的周期、频率和准确性。
例如,有些企业采用月度生产计划,每周进行调整;而有些企业则根据客户订单实时生成生产计划。
订单信息传递:显示客户订单从接收、处理到转化为生产指令的过程。
例如,通过电子数据交换(EDI)系统、电子邮件或纸质订单等方式传递订单信息,以及信息传递过程中可能出现的延迟、错误或丢失等问题。
库存水平信号:表明各个环节库存水平的监控和反馈机制,如使用库存管理系统、可视化看板或定期盘点等方式来掌握库存状况。
三、价值流图的作用1、识别浪费和瓶颈通过价值流图可以清晰地看到生产过程中存在的各种浪费,如等待时间、过度生产、运输浪费、库存积压、不必要的动作和不良品等。
例如,在一个机械加工车间,发现大量的半成品堆积在某个工序旁等待下一道工序加工,这就是明显的等待浪费。
同时,还能找出制约生产效率提升的瓶颈工序,这些瓶颈工序通常是整个价值流中生产能力最低或最不稳定的环节,对它们进行改善可以极大地提高整个生产系统的效率。
2、优化生产流程基于价值流图分析的结果,可以对生产流程进行有针对性的优化。
例如,通过重新布局生产车间,减少工序之间的运输距离和时间;调整生产节拍,使各工序之间的生产速度更加均衡;采用连续流生产方式,减少在制品库存等。
3、设定改进目标价值流图可以帮助企业设定明确的改进目标。
精益生产-价值流管理

描绘与分析现状图
开
始
新
一
绘制未来图
轮 图
析
制定改善计划
实施改善计划
7
2.描绘现状图
价值流图的管理
价值流现状图绘制的五大步骤: (1)表示顾客的需求,画出基本的生产过程 (2)绘制所有过程的数据框及库存 (3)绘制物料流 (4)绘制信息流 (5)绘制生产时间线条和计算增值比
8
价值流图的管理
价值环
定义
改进方向
改善工具
客户环
顾客和定拍过程之间的材 料和信息流。这是你的公 司中最下游的环,你如何 管理这个环将影响你的价
值流中所有上游过程
发展连续流,降低生产制 造周期(L/T),快速切换、
设备的TPM改善等
安全库存、线平衡、 TPM、快速切换等
生产环
制造过程中的材料和信息 流
进行均衡化生产,降低在 制品缩短生产制造周期, 提升产品质量,提升设备
难易度 影响度
易
中
难
高
1
3
6
中
2
5
8
低
4
7
9
利用难易度、影响度矩阵图确定各改善机会优先
次序选定重点改善项目
42
价值流图的管理
3).制定改善机会实施计划
价值流计划内容:
按步骤表达你的计划是什么,什么时候开始实施 定可量度的指标目标 责任人员、团队、审核人员 有截止日期和审核人员的清晰的核查点
43
价值流图的管理
将计划只发给门到门价值流中的一个点,这一个点叫做定拍过程,定拍过 程是一个由外部顾客订单 控制的过程
27
价值流图的管理
分析五大准则
准则五:在定拍过程按时间均匀分配多品种多产品的生产
精益生产3-价值流篇
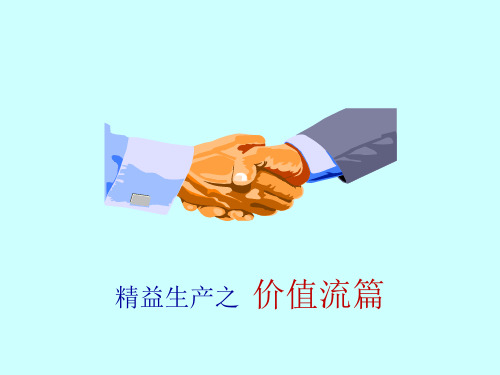
上洗手间/喝水 ..: 60分钟
每天实际工作时间:1094 分钟 (1094x60=65640秒)
每天调机 :40分钟
每天其它原 因损失:126
分钟
T/T=75600秒/2200ea=34.3秒 T/T=34 秒
不良损失 操作不熟练 质量判定等候 …非计划性
实际生产工序节拍时间=65640秒/2200ea=29.8秒 Pc/T=29 秒
减少更换设备进行生产, 以在问题出 现时, 更容易发现和避免
ABC 分析
按手上订单量/库存按其总价值 ($) 而分级别
价值占 5%. 产品数占约50-60% C类
价值占 15-25%. 产品数占约30% B类
价值占 70-80%. 产品数占约15% A类
对A类产品优先作精益生产研究
ABC 分析实例
2. 连续流无法向前 工序扩展时, 采用 超市控制
绘制未来流程图
考虑信息流
1. 将订单下到一个 工序
2. 用超市系统时,拉 动,以控制生产节 拍
3. 用连续流时, 上 游工序推动
超市系统
工序A
工序B
工序C
工序D
工序A Max. 工序B Max. 工序C Max. 工序D
20 pcs
20 pcs
20 pcs
CNC C/O time is long
L/T=1690 min
Paint C/T is long
L/T=6.1 Days
绘制未来流程图
平衡生产流程
1. 确定定拍工序 2. 选定节拍时间 3. 重新考虑工序平
衡
定拍工序, 生产工序的关键位置 其对前后工序均有明显的影响
绘制未来流程图
考虑物流
精益生产中的价值流图分析法
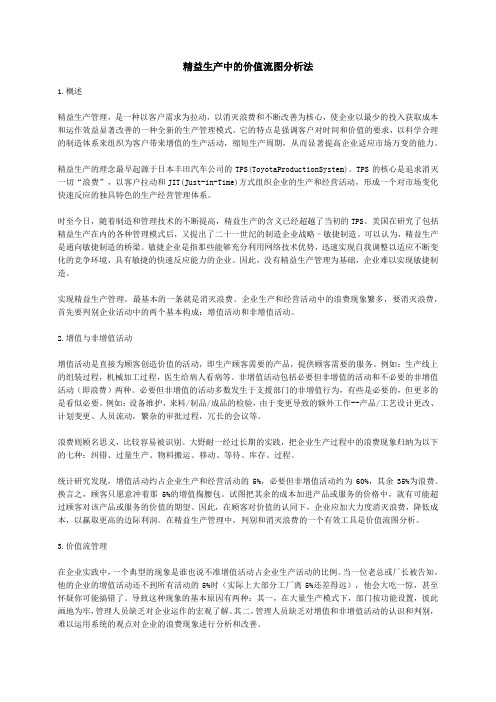
精益生产中的价值流图分析法1.概述精益生产管理,是一种以客户需求为拉动,以消灭浪费和不断改善为核心,使企业以最少的投入获取成本和运作效益显著改善的一种全新的生产管理模式。
它的特点是强调客户对时间和价值的要求,以科学合理的制造体系来组织为客户带来增值的生产活动,缩短生产周期,从而显著提高企业适应市场万变的能力。
精益生产的理念最早起源于日本丰田汽车公司的TPS(ToyotaProductionSystem)。
TPS的核心是追求消灭一切“浪费”,以客户拉动和JIT(Just-in-Time)方式组织企业的生产和经营活动,形成一个对市场变化快速反应的独具特色的生产经营管理体系。
时至今日,随着制造和管理技术的不断提高,精益生产的含义已经超越了当初的TPS。
美国在研究了包括精益生产在内的各种管理模式后,又提出了二十一世纪的制造企业战略–敏捷制造。
可以认为,精益生产是通向敏捷制造的桥梁。
敏捷企业是指那些能够充分利用网络技术优势,迅速实现自我调整以适应不断变化的竞争环境,具有敏捷的快速反应能力的企业。
因此,没有精益生产管理为基础,企业难以实现敏捷制造。
实现精益生产管理,最基本的一条就是消灭浪费。
企业生产和经营活动中的浪费现象繁多,要消灭浪费,首先要判别企业活动中的两个基本构成:增值活动和非增值活动。
2.增值与非增值活动增值活动是直接为顾客创造价值的活动,即生产顾客需要的产品,提供顾客需要的服务。
例如:生产线上的组装过程,机械加工过程,医生给病人看病等。
非增值活动包括必要但非增值的活动和不必要的非增值活动(即浪费)两种。
必要但非增值的活动多数发生于支援部门的非增值行为,有些是必要的,但更多的是看似必要。
例如:设备维护,来料/制品/成品的检验,由于变更导致的额外工作--产品/工艺设计更改、计划变更、人员流动,繁杂的审批过程,冗长的会议等。
浪费则顾名思义,比较容易被识别。
大野耐一经过长期的实践,把企业生产过程中的浪费现象归纳为以下的七种:纠错、过量生产、物料搬运、移动、等待、库存、过程。
精益生产衡量指标价值流分析

*依计划执行(从控制缓行最小于最大水准)
未来价值流图析步骤
future state value stream mapping
*使用工具如流程分析以协助分析及鉴别浪费降低的机 会
Use tools, such as process flow analysis,to help analyze and identify waste reduction opportunities. Identify one single point in the production chain (the pacemaker process “)where you will schedule production
– 僅是裁減員額數
课程目标 Objectives
在完成此一课程你将能
At the end of this section, you will be able to :
*定义期间价值流及价值流图分析
Define the terms Value stream and value stream Mapping
*确认在生产鍊单一点(制程速率点)可排生产计划
*张贴价值流图在作业区给全部工作人员清楚目视為持 续改进的基础
Post the map in area that is clearly visible to all work group members on a continuous basis.
future state value stream map Measurements :衡量指标
*應用价值流图分析实施步骤以模拟精实
Apply the steps for Mapping a Value Stream to the Lean Simulation
精益生产价值流分析与价值流图的介绍

精益生产价值流分析与价值流图的介绍实施精益生产,就是逐步构筑拥有完美增值流程的生产系统。
改善的着眼点,则是从顾客的角度考察生产系统,从中发现问题。
所以,精益生产分析问题的方法,一般是观察客户的产品,看这个产品在生产流程中有什么样的遭遇,从中分析价值,发现浪费。
这种根据产品本身的生产流程分析问题的思路与方法,贯穿精益生产的始终,是与以往按照部门分析问题截然不同的方式。
一、什么是价值流、识别价值流、价值流图所谓流程,就是在完成一个目标的过程中产生的一组连续活动。
精益思想把纷繁芜杂的生产活动归纳成三组为顾客创造价值的流程:①设计流程:从概念设想到细节设计,再到正式投产。
②生产流程:从接受订单到送货。
③售后服务流程:从货物销售到产品生命周期结束。
图1 产品的生产流程如图1所示,在工厂里,在把原材料变成成品的过程中,产生了冲压、焊接、组装三组活动,这二组活动共同组成了产品的生产流程。
所谓价值流,是把流程中的活动细分成了增值活动和非增值活动,从价值和浪费的角度来记录流程。
识别价值流,即是在这组特定活动中识别浪费和寻找改善机会。
识别价值流的工具,就是价值流图(ValueStream Mapping)。
绘制价值流图,运用的是流程分析法:我们关注向顾客提供的产品或者服务,从流程的开始一直到流程结束,然后把产品或者服务所涉及的所有物流与信息流相关内容用目视图表的方法绘制出来,形成一张价值流图,作为今后实施精益生产的依据。
二、价值流图的作用1、分析系统整体存在的问题。
常规企业的改善活动,往往是各个部门各自为战,每个车间在组织生产时都尽量把自己的车间按照最优的方法进行管理。
但是,一个车间最优并不代表整体最优。
因此,就需要从整体角度来对工厂进行分析,提出整体最优的解决方案。
2、分析生产与计划之间的联系。
精益生产的重要指标之一是减少库存,库存不是自己变出来的,一般都是按照计划生产出来的,因此,要想减少库存,就必须要从生产计划入手。
- 1、下载文档前请自行甄别文档内容的完整性,平台不提供额外的编辑、内容补充、找答案等附加服务。
- 2、"仅部分预览"的文档,不可在线预览部分如存在完整性等问题,可反馈申请退款(可完整预览的文档不适用该条件!)。
- 3、如文档侵犯您的权益,请联系客服反馈,我们会尽快为您处理(人工客服工作时间:9:00-18:30)。
标明工序间的 库存
锻造
机加工
抛光
电镀
包装
装运
I
6000 切割棒材
I
=6
Dor = 12” C/O = 1 Hr
开动率100% 质量 95%
18000 12k英制 6k公制
I
= 15
Dor = 12”
C/O = 20 分 开动率98% 质量 98%
25000 18k英制 7k公制
I
= 11
Dor = 10” C/O = n/a
25000 18k英制 7k公制
I
= 11
Dor = 10” C/O = n/a
开动率99% 质量 94%
55000 35k英制 20k公制
I
=5
Dor = 16” C/O = n/a
开动率99% 质量 98%
6000 6k英制 0k公制
I
= 12
Dor = 200” C/O = n/a
开动率n/a 质量 99.5%
画出当前价值流图
• 1) 画出客户
– 使用“巴特.辛普森” 图标 – 标明他们业务运作的一些参数 – 标明他们业务运作的需求
• 2) 画出装运过程
– 不要考虑的太多 – 使用过程方块图图标 表示装运过程 – 仅画出内部的装运过程
画出客户:
巨人工具
3200 套/月 2200 套英制 1000 套公制 1班 1套 = 25件
I
= 15
Dor = 12”
C/O = 20 分 开动率98% 质量 98%
25000 18k英制 7k公制
I
= 11
Dor = 10” C/O = n/a
开动率99% 质量 94%
55000 35k英制 20k公制
I
=5
Dor = 16” C/O = n/a
开动率99% 质量 98%
6000 6k英制 0k公制
记录过程(工序)的 测量指标:
锻造 =6
Dor = 12” C/O = 1 Hr
开动率100% 质量 95%
机加工 = 15
Dor = 12”
C/O = 20 分 开动率98% 质量 98%
抛光 = 11
Dor = 10” C/O = n/a
开动率99% 质量 94%
电镀 =5
Dor = 16” C/O = n/a
价值流图的组成和作用
当前状态图 未来状态图 实施计划及追踪
• • • • •
可视化 掌握当前状态; 确定系统中浪费及根源; 确定产品_____中的关键问题点; 使我们把注意力集中到能够缩短________和削减 产品______的关键因素上; • 建立精益的愿景。
价值流的层次
加工工序层次
从这里开始
画出基本的 生产过程:
巨人工具
3200 套/月 2200 套英制 1000 套公制 1班 1套 = 25件
锻造
机加工
抛光
电镀
包装
装运
画出重要的 分支过程 (若必要):
巨人工具
3200 套/月 2200 套英制 1000 套公制 1班 1套 = 25件
?
?
?
锻造
机加工
抛光
电镀
包装
装运
巨人工具
3200 套/月 2200 套英制 1000 套公制 1班 1套 = 25件
生产整体的未来目标状态
1)客户的订单信息________下达到生产线,生产线可以及时地 进行生产、发货,几乎没有产品库存 2)__________非常短(基本与生产一个产品的增值加工时间相 等),对于产品量的变化、品种的变化可以迅速响应。 3)在制品的库存极少,生产为多品种小批量生产,但生产效率 如同单一品种的大批量生产 4)生产流程为整流、顺畅。
PQ Analysis
产品族选定案例:
产品系列 工序1 注塑 注塑 工序2 抛光 工序3 打孔 打孔 工序4 装配 装配 装配 注塑 注塑 打孔 装配 工序5 包装 包装 包装 包装 包装
A B C D E
Product Group
21% 2% 5% 13% 13%
15%
31%
Type 1 Type 2 Type 3 Type 4 Type 5 Type 6 Other
精益钢铁
切割棒材仓库
巨人工具
3200 套/月 2200 套英制 1000 套公制 1班 1套 = 25件
添加原材料 及成品 的移动:
周一及 周四
1X 每日
锻造
机加工
抛光
电镀
包装
装运
I
6000 切割棒材
I
=6
Dor = 12” C/O = 1 Hr
开动率100% 质量 95%
18000 12k英制 6k公制
Dor = 10” C/O = n/a
开动率99% 质量 94%
55000 35k英制 20k公制
I
=5
Dor = 16” C/O = n/a
开动率99% 质量 98%
6000 6k英制 0k公制
I
= 12
Dor = 200” C/O = n/a
开动率n/a 质量 99.5%
75000 50k英制 25k公制
I
= 12
Dor = 200” C/O = n/a
开动率n/a 质量 99.5%
75000 50k英制 25k公制
8 周的 预测
生产控制
90/60/30 预测 每日 订单
精益钢铁
切割棒材仓库
每周 传真
MRP
巨人工具
3200 套/月 2200 套英制 1000 套公制 1班
建周计划
每日装运 计划
1套 = 25件
I
= 11
Dor = 10”
55000 35k英制 20k公制
I
=5
Dor = 16” C/O = n/a
开动率99% 质量 98%
6000 6k英制 0k公制
I
= 12
Dor = 200” C/O = n/a
开动率n/a 质量 99.5%
75000 50k英制 25k公制
添加时间线:
开动率99% 质量 94%
3200 套/月 2200 套英制 1000 套公制 1班 1套 = 25件
添加供应商:
锻造
机加工
抛光
电镀
包装
装运
I
6000 切割棒材
I
=6
Dor = 12” C/O = 1 Hr
开动率100% 质量 95%
18000 12k英制 6k公制
I
= 15
Dor = 12”
C/O = 20 分 开动率98% 质量 98%
建周计划
日装运 计划
1套 = 25件
周一及 周四
1X 每日
锻造
机加工
抛光
电镀
包装
装运
I
6000 切割棒材
I
=6
Dor = 12” C/O = 1 Hr
开动率100% 质量 95%
18000 12k英制 6k公制
I
= 15
Dor = 12”
C/O = 20 分 开动率98% 质量 98%
25000 18k英制 7k公制
开动率99% 质量 94%
55000 35k英制 20k公制
I
=5
Dor = 16” C/O = n/a
开动率99% 质量 98%
6000 6k英制 0k公制
I
= 12
Dor = 200” C/O = n/a
开动率n/a 质量 99.5%
75000 50k英制 25k公制
精益钢铁切割棒材仓库Fra bibliotek巨人工具
• 9) 画中间库存移动线
– 按流程画出半成品移动方向 – 选择最主要的流程(频率最高的或最长的流程)
• 10) 添加时间线
– – – – 在每个流程和库存图标下画出时间线 标明时间长短 增值部分在上面,不增值部分在下面(较多画法) 累计增值和总长时间,算出增值%。
8 周的 预测
生产控制
90/60/30 预测 每日 订单
周一及 周四
添加信息流:
1X 每日
锻造
机加工
抛光
电镀
包装
装运
I
6000 切割棒材
I
=6
Dor = 12” C/O = 1 Hr
开动率100% 质量 95%
18000 12k英制 6k公制
I
= 15
Dor = 12”
C/O = 20 分 开动率98% 质量 98%
25000 18k英制 7k公制
I
= 11
单个工厂
(门至门)
多个工厂 跨公司
当前状态图 - 示例
建立价值流图的4个步骤
1 选定产品族 2 画当前状态
现状调查! - 我们的基础数据。
3 画未来状态
设计出一个精益的流程. 我们的愿景!
4 制定并实施 工作计划
画图的目的!
Product-Anual Output
9000 8000 7000 Anual Output 6000 5000 4000 3000 2000 1000 0 1 10 19 28 37 46 55 64 73 82 91 100 109 118 127 136 145 154 163 172 181 190 199 208 217 No of P/N
结论
• 我们需要一个___________,可以________; • 我们需要一个__________来讨论问题; • 我们需要一个_____显示 • 我们需要一个把公司或某个局部的现状、发展 计划、发展信息及结果内容全部综合在一起的 东西