微电机定转子自动叠片级进模_1_
微型电机定子片和转子片工位级进模设计

湖南农业大学东方科技学院全日制普通本科生毕业设计微型电机定子片和转子片工位级进模设计THE DESIGN OF STATION PROGRESSIVE DIE ON THE MICR OMOTOR STATOR AND ROTOR PLATE学生姓名:学号:年级专业及班级:指导老师及职称:学部:湖南·长沙提交日期:2014 年 5 月湖南农业大学东方科技学院全日制普通本科生毕业设计诚信声明本人郑重声明:所呈交的本科毕业设计是本人在指导老师的指导下,进行研究工作所取得的成果,成果不存在知识产权争议。
除文中已经注明引用的内容外,本设计不含任何其他个人或集体已经发表或撰写过的作品成果。
对本文的研究做出重要贡献的个人和集体在文中均作了明确的说明并表示了谢意。
本人完全意识到本声明的法律结果由本人承担。
毕业设计作者签名:年月日目录摘要 (1)关键词 (1)1 前言 (2)1.1 模具概述 (2)1.2 级进模概述 (3)1.3 Pro/ENGINEER的基础知识 (4)1.3.1 Pro/ENGINEER的诞生 (4)1.3.2 Pro/ENGINEER的功能和特点 (4)1.3.3 Pro/ENGINEER在模具制造中的应用 (5)1.4 课题内容选题意义 (6)1.5本章小结 (7)2微型电动机定子、转子片级进模设计 (7)2.1 设计资料 (7)2.2 设计步距与定距方式 (7)2.3 排样图设计 (8)2.4主要计算 (9)2.4.1 冲压力的计算 (9)2.4.2 压力中心的计算 (10)2.4.3 卸料力与推件力的计算 (12)2.4.4 冲裁间隙 (12)2.4.5 凸、凹模刃口尺寸的计算 (12)2.5压力机的选择 (16)2.6模具总体设计 (18)2.6.1 模架 (18)2.6.2 卸料板 (18)2.6.3 导柱和导套 (19)2.6.4 弹压装置 (19)2.6.5 凹模 (19)2.6.6 定位装置 (21)2.6.7 导料装置 (22)2.7 主要零部件设计 (22)2.7.1 线槽冲模设计 (22)2.7.2 校正模设计 (26)2.7.3 小凸模设计 (27)2.7.4 转子片落料模设计 (28)2.7.5 异行孔冲模设计 (29)2.7.6 切废模设计 (30)2.7.7 切断模设计 (31)2.8 本章小结 (32)3Pro/ENGINEER的模具造型 (33)3.1 总装配图的建立 (33)3.2 零件图的建立 (34)3.3 本章小结 (38)4结论 (38)参考文献 (39)致谢 (39)微型电机定子片和转子片级进模设计摘要:本课题介绍了微型电动机定、转子片多工位级进模的冲压工艺和模具结构设计,并应用Pro/E软件对其进行级进模具设计,解决了模具排样的难点,设计的模具机构应用于工程实践,产生了较好的效益。
电机定转子铁芯三拼式套冲自动叠铆级进模设计
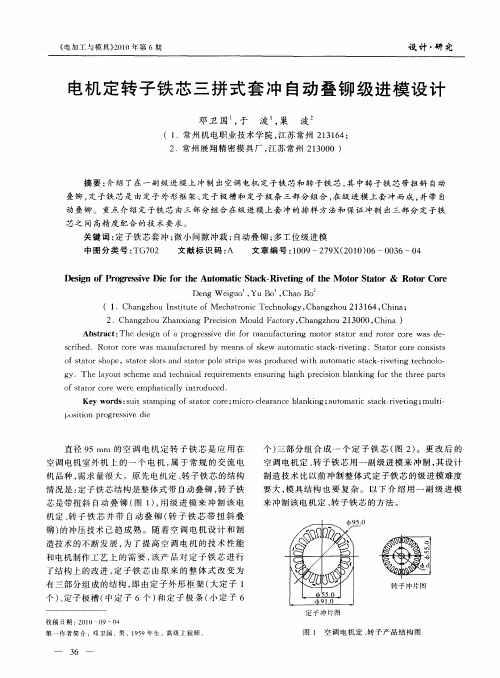
和电机制 作工艺 上 的需 要 , 产 品对 定 子铁 芯 进行 该 了结构 上的改进 , 子铁 芯 由原来 的整 体式 改 变 为 定 有三部分 组成 的结构 , 由定 子外 形框 架 ( 定子 1 即 大
Ab ta t T h sgn o r g e sv i o a f c u g mot r sa o n o orc r s d — sr c : ede i fa p o r si e d e f r m nu a t “n o t t r a d r t o e wa e s rb d. Ro o o e w a nu a t r d b e n fs e a t m a i tc —i e i g.St t o e c n it c ie t rc r s ma fc u e y m a so k w u o tc sa k rv tn aorc r o sss o t t rs a ,sa o lt n tt rp l t isw a r d c d w ih a t m a i t c rv tng t c ol— fsa o h pe t t rso sa d s a o o es rp sp o u e t u o tcs a k—i e i e hn o
g y.Th a o ts h m ea d t c ia e uie n s e s rn i h p e iin b a ki g f r t h e a t e ly u c e n e hn c lrq r me t n u i g h g r cso ln n o het r e p rs
电机定转子铁心自动叠装模设计方案
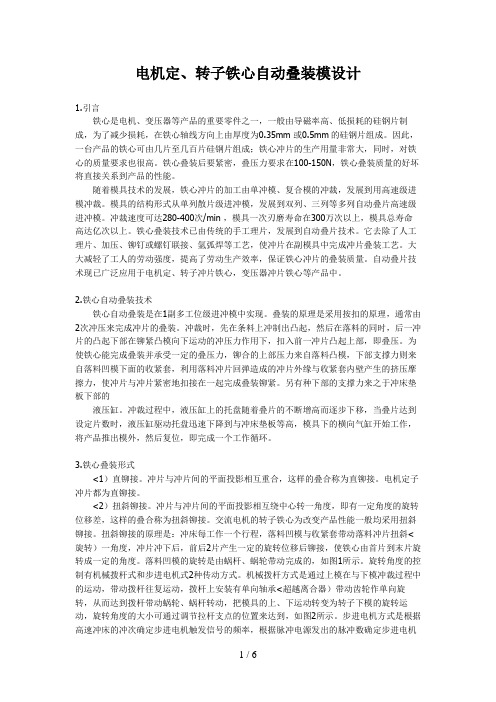
电机定、转子铁心自动叠装模设计1.引言铁心是电机、变压器等产品的重要零件之一,一般由导磁率高、低损耗的硅钢片制成,为了减少损耗,在铁心轴线方向上由厚度为0.35mm 或0.5mm的硅钢片组成。
因此,一台产品的铁心可由几片至几百片硅钢片组成;铁心冲片的生产用量非常大,同时,对铁心的质量要求也很高。
铁心叠装后要紧密,叠压力要求在100-150N,铁心叠装质量的好坏将直接关系到产品的性能。
随着模具技术的发展,铁心冲片的加工由单冲模、复合模的冲裁,发展到用高速级进模冲裁。
模具的结构形式从单列散片级进冲模,发展到双列、三列等多列自动叠片高速级进冲模。
冲裁速度可达280-400次/min ,模具一次刃磨寿命在300万次以上,模具总寿命高达亿次以上。
铁心叠装技术已由传统的手工理片,发展到自动叠片技术。
它去除了人工理片、加压、铆钉或螺钉联接、氩弧焊等工艺,使冲片在副模具中完成冲片叠装工艺。
大大减轻了工人的劳动强度,提高了劳动生产效率,保证铁心冲片的叠装质量。
自动叠片技术现已广泛应用于电机定、转子冲片铁心,变压器冲片铁心等产品中。
2.铁心自动叠装技术铁心自动叠装是在1副多工位级进冲模中实现。
叠装的原理是采用按扣的原理,通常由2次冲压来完成冲片的叠装。
冲裁时,先在条料上冲制出凸起,然后在落料的同时,后一冲片的凸起下部在铆紧凸模向下运动的冲压力作用下,扣入前一冲片凸起上部,即叠压。
为使铁心能完成叠装并承受一定的叠压力,铆合的上部压力来自落料凸模,下部支撑力则来自落料凹模下面的收紧套,利用落料冲片回弹造成的冲片外缘与收紧套内壁产生的挤压摩擦力,使冲片与冲片紧密地扣接在一起完成叠装铆紧。
另有种下部的支撑力来之于冲床垫板下部的液压缸。
冲裁过程中,液压缸上的托盘随着叠片的不断增高而逐步下移,当叠片达到设定片数时,液压缸驱动托盘迅速下降到与冲床垫板等高,模具下的横向气缸开始工作,将产品推出模外,然后复位,即完成一个工作循环。
3.铁心叠装形式<1)直铆接。
定子片、转子片级进模设计

摘要本次设计生产的是电动机定子片和转子片,精度要求较高,形状比较复杂,生产批量大,通过工艺性分析,工序均为落料和冲孔。
采用级进模制造,能很好的解决这些问题,并且能同时完成两个工件的冲裁,提高材料利用率。
原料选用硅钢片卷料,采用自动送料器和自动送料装置送料。
模架采用四导柱滚珠导向钢板模架和弹性卸料板,并在卸料板和固定板之间设置辅助导向机构——小导柱和小导套,保证卸料板有足够的运动精度。
关键字:定子片、转子片、落料、冲孔、级进模、卸料板1.工件名称:微型电动机定子片、转子片2.生产批量:大批大量3.材料:电工硅钢片4.料厚:0.35mm第一章绪论 31.1 冲压加工与模具设计简介 31.2 冷冲压与模具技术现状 41.3 冲压加工自动化与柔性化 41.4 冲模CAD/CAM 4第二章冲裁工艺设计 52.1冲裁件工艺性分析 52.1.1 分析工件的技术要求 52.1.2 零件材料的选用 62.1.3 零件的结构工艺性分析 82.2 冲裁工艺方案的确定 92.2.1.冲裁工序的组合 92.2.2.冲裁顺序的安排 11第三章排样图设计 133.1 材料利用率初算 133.2 排样方法 143.3 搭边值的选用和条料的选用及步距的确定 16 3.3.1 搭边值的选用 163.3.2 条料宽度的确定 163.3.3 步距的确定 173.4 材料利用率确定 183.5 排样图确定 18第四章主要设计计算 204.1 冲压力的计算 204.1.1 计算冲裁力 204.1.2 卸料力及推件力计算 224.2 压力中心的计算 234.3 压力机选择 244.3.1.冲压设备类型的选择 244.3.2 确定压力机设备的规格 25第五章冲裁模工作部分设计计算 265.1.冲裁间隙 265.1.1 间隙的影响 265.1.2.合理间隙的选用 295.2 模具刃口尺寸的计算 305.2.1 计算原则 305.2.2 计算方法 315.2.3 级进模的各个工位凸、凹模刃口尺寸计算 32 第六章模具总体设计 386.1 确定送料方式 386.2 定位方式选择和定位装置 386.3 卸料方式的选择 386.4 模架选择 386.5 卸料板及其配套设施选择 406.6 导料装置 416.7 模具材料的选用处理 41第七章模具主要零、部件设计 437.1 工作零件设计 437.1.1.线槽冲模设计 447.1.2 校正模设计 457.1.3 小凸模设计 457.1.4 转子片落料凸模设计 457.1.5 异形孔冲模设计 467.1.6 切废料模设计 467.1.7 切断模设计 467.2 垫板、凸模固定板设计 477.3 模具闭合高度的确定 47第八章绘制模具装配图、及零件图及编写设计说明书 48 第九章总结 50参考文献 51致谢 52附录 53文献综述 58。
基于PDW的电机转子定子片级进模设计
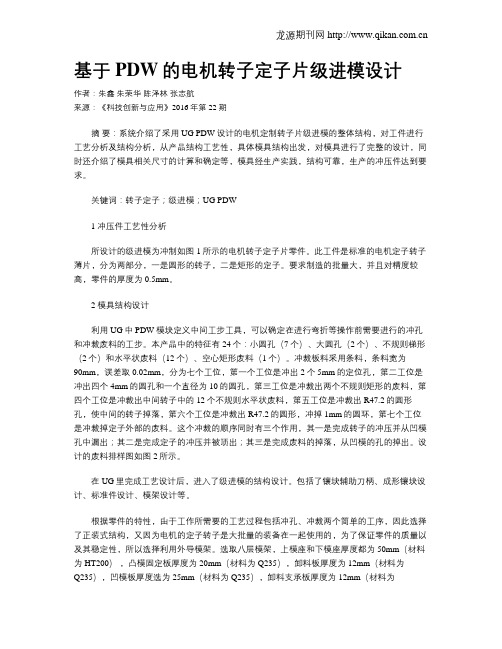
基于PDW的电机转子定子片级进模设计作者:朱鑫朱荣华陈泽林张志航来源:《科技创新与应用》2016年第22期摘要:系统介绍了采用UG PDW设计的电机定制转子片级进模的整体结构,对工件进行工艺分析及结构分析,从产品结构工艺性,具体模具结构出发,对模具进行了完整的设计,同时还介绍了模具相关尺寸的计算和确定等,模具经生产实践,结构可靠,生产的冲压件达到要求。
关键词:转子定子;级进模;UG PDW1 冲压件工艺性分析所设计的级进模为冲制如图1所示的电机转子定子片零件。
此工件是标准的电机定子转子薄片,分为两部分,一是圆形的转子,二是矩形的定子。
要求制造的批量大,并且对精度较高,零件的厚度为0.5mm。
2 模具结构设计利用UG中PDW模块定义中间工步工具,可以确定在进行弯折等操作前需要进行的冲孔和冲裁废料的工步。
本产品中的特征有24个:小圆孔(7个)、大圆孔(2个)、不规则梯形(2个)和水平状废料(12个)、空心矩形废料(1个)。
冲裁板料采用条料,条料宽为90mm,误差取 0.02mm,分为七个工位,第一个工位是冲出2个5mm的定位孔,第二工位是冲出四个4mm的圆孔和一个直径为10的圆孔,第三工位是冲裁出两个不规则矩形的废料,第四个工位是冲裁出中间转子中的12个不规则水平状废料,第五工位是冲裁出R47.2的圆形孔,使中间的转子掉落,第六个工位是冲裁出R47.2的圆形,冲掉1mm的圆环,第七个工位是冲裁掉定子外部的废料。
这个冲裁的顺序同时有三个作用,其一是完成转子的冲压并从凹模孔中漏出;其二是完成定子的冲压并被顶出;其三是完成废料的掉落,从凹模的孔的掉出。
设计的废料排样图如图2所示。
在UG里完成工艺设计后,进入了级进模的结构设计。
包括了镶块辅助刀柄、成形镶块设计、标准件设计、模架设计等。
根据零件的特性,由于工作所需要的工艺过程包括冲孔、冲裁两个简单的工序,因此选择了正装式结构,又因为电机的定子转子是大批量的装备在一起使用的,为了保证零件的质量以及其稳定性,所以选择利用外导模架。
电机定转子铁心自动叠装模设计方案
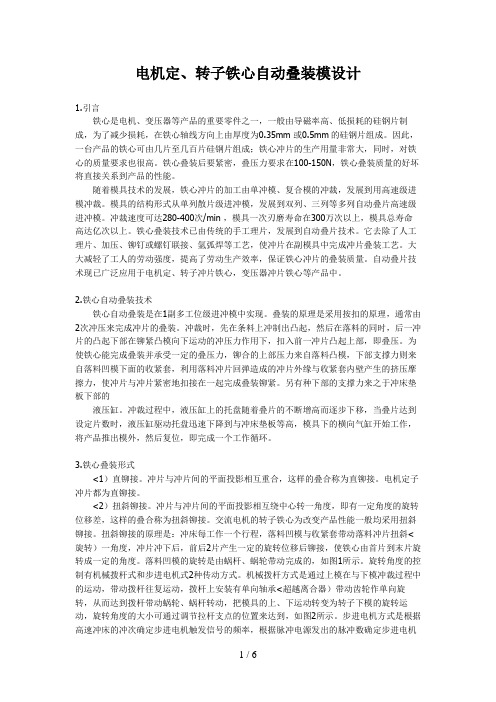
电机定、转子铁心自动叠装模设计1.引言铁心是电机、变压器等产品的重要零件之一,一般由导磁率高、低损耗的硅钢片制成,为了减少损耗,在铁心轴线方向上由厚度为0.35mm 或0.5mm的硅钢片组成。
因此,一台产品的铁心可由几片至几百片硅钢片组成;铁心冲片的生产用量非常大,同时,对铁心的质量要求也很高。
铁心叠装后要紧密,叠压力要求在100-150N,铁心叠装质量的好坏将直接关系到产品的性能。
随着模具技术的发展,铁心冲片的加工由单冲模、复合模的冲裁,发展到用高速级进模冲裁。
模具的结构形式从单列散片级进冲模,发展到双列、三列等多列自动叠片高速级进冲模。
冲裁速度可达280-400次/min ,模具一次刃磨寿命在300万次以上,模具总寿命高达亿次以上。
铁心叠装技术已由传统的手工理片,发展到自动叠片技术。
它去除了人工理片、加压、铆钉或螺钉联接、氩弧焊等工艺,使冲片在副模具中完成冲片叠装工艺。
大大减轻了工人的劳动强度,提高了劳动生产效率,保证铁心冲片的叠装质量。
自动叠片技术现已广泛应用于电机定、转子冲片铁心,变压器冲片铁心等产品中。
2.铁心自动叠装技术铁心自动叠装是在1副多工位级进冲模中实现。
叠装的原理是采用按扣的原理,通常由2次冲压来完成冲片的叠装。
冲裁时,先在条料上冲制出凸起,然后在落料的同时,后一冲片的凸起下部在铆紧凸模向下运动的冲压力作用下,扣入前一冲片凸起上部,即叠压。
为使铁心能完成叠装并承受一定的叠压力,铆合的上部压力来自落料凸模,下部支撑力则来自落料凹模下面的收紧套,利用落料冲片回弹造成的冲片外缘与收紧套内壁产生的挤压摩擦力,使冲片与冲片紧密地扣接在一起完成叠装铆紧。
另有种下部的支撑力来之于冲床垫板下部的液压缸。
冲裁过程中,液压缸上的托盘随着叠片的不断增高而逐步下移,当叠片达到设定片数时,液压缸驱动托盘迅速下降到与冲床垫板等高,模具下的横向气缸开始工作,将产品推出模外,然后复位,即完成一个工作循环。
3.铁心叠装形式<1)直铆接。
电机定转子片冲压工艺及模具设计

电机定转子片冲压工艺及模具设计电机定子和转子片的冲压工艺及模具设计是电机制造过程中非常重要的环节。
下面将对这两个环节进行分别介绍。
电机定子是电机的重要部件之一,它负责传递电能到转子,并通过相互作用转化为动力。
电机定子的冲压工艺设计主要包括:冲压工艺流程设计、工件材料选择、模具设计等。
1.冲压工艺流程设计:冲压工艺流程设计是指根据电机定子的结构和要求,确定冲压过程中的各个步骤和工序。
其中包括切割、冲孔、冲凹、成形等工序。
在设计过程中,要考虑到定子的材料的特性和加工工艺的可行性,使得冲压效果更加稳定和高效。
2.工件材料选择:电机定子的材料一般选择导电性好、磁性强、机械强度高的硅钢板。
在确定材料时,要综合考虑材料的特性和成本因素,确保产品的性能和经济性。
3.模具设计:模具是冲压过程中的重要设备,它的设计直接影响到冲压的准确度和效果。
在模具设计过程中,要考虑到定子的结构和尺寸,确定冲孔、冲凹的位置和尺寸。
同时,还要考虑到材料的屈服强度和导热性能,确定模具的材料和结构,以确保模具在冲压过程中的稳定性和耐用性。
电机转子片是电机的核心部件之一,它通过旋转产生动力。
电机转子片的冲压工艺设计主要包括:冲压工艺流程设计、工件材料选择、模具设计等。
1.冲压工艺流程设计:冲压工艺流程设计是指根据转子片的结构和要求,确定冲压过程中的各个步骤和工序。
其中包括切割、冲孔、冲凸、成形等工序。
在设计过程中,要考虑到转子片的材料特性和形状复杂性,同时还要考虑到冲压过程中的变形和残余应力等因素,确保冲压效果和转子片的性能。
2.工件材料选择:电机转子片的材料一般选择具有稳定性和导电性的钢材。
在确定材料时,要综合考虑材料的特性和成本因素,确保产品的性能和经济性。
3.模具设计:模具是冲压过程中的核心设备,它的设计直接影响到冲压的准确度和效果。
在模具设计过程中,要考虑到转子片的结构和尺寸,确定冲孔、冲凸的位置和尺寸。
同时,还要考虑到材料的屈服强度和导热性能,确定模具的材料和结构,以确保模具在冲压过程中的稳定性和耐用性。
电机转子叠片组 -回复

电机转子叠片组-回复电机转子叠片组是电机中的一个重要部件,它负责将电能转化为机械能,驱动机械设备的运转。
本文将从电机转子的构成、工作原理、制造工艺以及未来发展趋势等方面对电机转子叠片组进行详细解析。
一、电机转子的构成电机转子是由多个叠片组成的,这些叠片通常由导电材料制成,如铁心片、铝合金板等。
每个叠片都有自己的形状和尺寸,它们按一定的顺序和方式叠加在一起,并通过固定的轴承与电机主轴相连接。
整个转子可分为两部分:定子和转子。
定子是电机中固定不动的一部分,它由若干个绕组和铁心片组成。
绕组通常由绕制在铁心片上的导线组成,而铁心片则是由铁磁材料制成。
当电流通过绕组时,铁心片产生的磁场与转子的磁场相互作用,产生电磁力,从而驱动转子转动。
转子是电机中旋转的部分,它由多个相互连接的叠片组成。
每个叠片都有自己的形状和尺寸,并通过轴承与电机主轴相连接。
叠片之间通过一定的间隙分隔开,以减少互相之间的摩擦和磨损。
电流通过转子中的导线时,会在导线周围产生磁场,这个磁场与定子的磁场相互作用,从而产生旋转力矩,驱动转子旋转。
二、电机转子的工作原理电机转子的工作原理可以用电磁感应定律和洛伦兹力定律来解释。
当通电线圈中的电流变化时,就会在电流线圈周围产生磁场。
根据电磁感应定律,若将一个导体放在磁场中,导体两端将会产生电动势,从而产生电流。
在电机转子中,当电流通过叠片中的导线时,导线所处的磁场方向会发生变化,从而产生电动势并驱动转子旋转。
根据洛伦兹力定律,当导体中的电流与磁场相互作用时,会受到某一方向的力的作用。
在电机转子中,由于导线周围产生的磁场与定子的磁场相互作用,导致导线受到的洛伦兹力方向与定子的磁场方向相反。
这个力会驱动转子旋转,从而实现电能到机械能的转换。
三、电机转子的制造工艺电机转子的制造工艺包括原料准备、叠片制备、叠片装配以及电流试验等环节。
原料准备:根据设计要求选择合适的导线材料和铁磁材料,确保其导电性和磁导率满足要求。
转子铁芯自动叠铆级进模设计

转子铁芯自动叠铆级进模设计随着电动机的广泛应用,转子铁芯的制造技术也在不断提高。
其中,铆接技术是一种常用的连接方式,其优点在于连接坚固、稳定性好。
本文通过研究转子铁芯的自动叠铆级进模设计,提出了一种新的叠铆技术,该技术不仅提高了生产效率,而且可以保证叠铆的质量。
关键词:转子铁芯;铆接技术;自动叠铆;级进模设计;生产效率一、引言随着全球经济的快速发展,电动机已经在各个领域得到了广泛的应用。
而电动机中的转子铁芯作为核心部件,其制造技术也在不断提高。
其中,铆接技术是一种常用的连接方式,其优点在于连接坚固、稳定性好。
但是,传统的叠铆方式存在一些问题,例如生产效率低、叠铆质量不稳定等。
因此,本文通过研究转子铁芯的自动叠铆级进模设计,提出了一种新的叠铆技术,该技术不仅提高了生产效率,而且可以保证叠铆的质量。
二、转子铁芯的铆接技术转子铁芯是电动机中的核心部件,其质量直接影响电动机的性能。
在转子铁芯的制造过程中,铆接技术是一种常用的连接方式,其优点在于连接坚固、稳定性好。
同时,铆接技术也有一些缺点,例如需要专门的设备和工艺、生产效率低、叠铆质量不稳定等。
传统的叠铆方式是采用手工操作,即工人将铆钉从铆枪中取出,然后放入转子铁芯的孔中,最后用铆钳将铆钉压入。
这种方式的缺点在于生产效率低、叠铆质量不稳定。
因此,需要寻找一种更加高效、稳定的叠铆方式。
三、自动叠铆级进模设计为了提高叠铆的生产效率和稳定性,本文提出了一种自动叠铆级进模设计。
该设计通过采用自动化设备和模具,实现了叠铆的自动化操作。
其具体操作流程如下:1.确定叠铆的位置和数量。
2.将转子铁芯放入模具中。
3.将铆钉放入模具中的铆钉槽内。
4.启动自动化设备,按照预定的程序进行叠铆操作。
该设计的优点在于可以实现叠铆的自动化操作,减少了人工操作的干扰和误差。
同时,由于采用了模具,可以保证铆钉的位置和数量的精度,从而保证了叠铆的质量。
四、实验结果分析为了验证自动叠铆级进模设计的效果,本文进行了实验。
电机转子采用叠片的原因

电机转子采用叠片的原因电机转子是电机的核心部件之一,它负责转动并传递动力。
为了提高电机的效率和性能,转子的设计和制造过程需要考虑多个因素。
叠片结构正是其中一种常见的设计方式,它具有以下优点。
叠片结构能够提高转子的强度和刚度。
通过将多个薄片堆叠在一起,可以增加转子的整体强度,使得它能够承受更大的负载和扭矩。
叠片结构还可以增加转子的刚度,减少在运转过程中的变形和振动,从而提高电机的稳定性和可靠性。
叠片结构能够提高转子的散热性能。
电机在工作过程中会产生大量的热量,如果不能及时散热,就会导致电机温度过高,进而影响电机的性能和寿命。
叠片结构中的薄片之间会形成许多散热通道,能够提供更大的表面积用于散热,从而有效地降低电机的温度。
叠片结构还可以提高转子的动态平衡性能。
电机在高速运转时,转子的不平衡会导致振动和噪音的产生,影响电机的正常工作。
叠片结构中的每个薄片都可以独立进行动平衡处理,从而减小不平衡量,提高电机的平衡性能。
叠片结构还具有制造成本低、重量轻等优点。
相比于传统的整体结构转子,叠片结构可以使用更薄的材料,减少材料的使用量和制造成本。
同时,叠片结构的重量也相对较轻,可以降低电机的整体重量,提高电机的功率密度。
然而,叠片结构也存在一些局限性。
首先,叠片结构的制造过程相对复杂,需要采用专门的加工设备和工艺。
其次,叠片结构在高速运转时容易产生共振现象,需要通过合理的设计和优化来避免。
最后,叠片结构的可靠性和耐久性需要进一步提高,以满足电机在长时间运行中的需求。
电机转子采用叠片结构的原因主要有增加强度和刚度、提高散热性能、改善动态平衡性能、降低制造成本和减轻重量等。
虽然叠片结构存在一些局限性,但通过合理的设计和优化,可以充分发挥叠片结构的优点,提高电机的性能和可靠性。
微型转子片级进模设计

微型转子片级进模设计陈炎嗣【摘要】微型转子片产量一般较大,对内外形同轴度精度要求较高,常用复合模或级进模生产.本文对两种加工方法作了分析比较,针对具体制件选择了用级进模的理由,并在模具结构方面大胆采用薄板凹模,获得了成功;固定方法与常规模具也不同,都作了相应介绍,供参考和借鉴.【期刊名称】《模具制造》【年(卷),期】2013(013)009【总页数】3页(P14-16)【关键词】微型转子片;级进模;薄板凹模【作者】陈炎嗣【作者单位】北京东方电子集团模具厂,北京100102【正文语种】中文【中图分类】TG385.21 制件冲压工艺分析及冲压工艺方案的确定如图1所示为微型电动机转子片,材料为厚0.35mm的硅钢。
该件内外形尺寸较小,同轴度要求小于φ0.02mm,精度要求较高,未注公差按GB/T15055极限偏差m级控制(较高)。
产量较大,可采用的冲压生产方案有多种,各自特点分析比较见表1所示。
图1 转子片表1 几种冲压方案的比较序号 1 2 3冲压工艺方案单工序模(用2副模具冲裁)复合模(用一副模具冲裁)特点级进模(用一副模具冲成)冲压过程①落料(落下的坯件作为冲孔用);②冲孔(用落料坯件外形定位,冲孔后得制件)。
冲孔落料在一副模具的同一工位上一次冲压而成。
冲孔、落料在一副模具上不同工位进行,能实现连续自动冲压。
模具结构简单,制造容易,但生产率低,生产成本高,制件存在定位误差,同轴度差。
模具结构较复杂,模具成本高些,制件内外形同轴度质量好,生产效率高。
能采用自动送料和采用多排排样,生产效率很高,适合大批量生产。
内外形同轴度精度虽不如复合模高,但有送料器初定位,导正销精定位,制件质量能保证。
模具结构比复合模简单,维修方便。
由表1分析可知,当制件产量较大的情况下,在保证制件质量的前提下,为实现自动送料和提高生产率,考虑采用三排冲压级进模生产比较理想。
如果制件产量特大,级进模生产5排或更多排冲压也是可以考虑的,但须注意模具的制造成本随着排数的增加而增加,模具的维修亦因排数的增加带来更多问题,因此,排数的确定要仔细思考,不全是越多越好。
[机械类类论文]浅谈电机定转子自动叠铆级进模
![[机械类类论文]浅谈电机定转子自动叠铆级进模](https://img.taocdn.com/s3/m/7e9ccb1af61fb7360a4c654e.png)
学生毕业论文系别:机电工程系专业:模具设计与制造班级:模具053学生姓名:学生学号:论文题目:浅谈电机定转子自动叠铆级进模指导教师:设计地点:起迄日期:~2007.8.25毕业论文任务书专业模具设计与制造班级模具053班姓名一、课题名称:浅谈电机定转子自动叠铆级进模二、主要技术指标:电机定转子铁芯自动叠铆级进模,是当代国际先进水平的高速冲模。
该冲模在一副模具内自动完成冲压成形、扭槽、回转、叠铆、分组等高难度的技术功能,冲制出来的不是单片零件,而是经自动叠铆后的铁芯组件,它突破了铁芯传统的生产方式,给大批量自动化生产高精度铁芯开辟了新路。
定转子铁芯自动叠铆级进模的结构复杂,精度要求高,制造难度大等因素,能设计制造该类模具的厂家较少。
因此,本文通过介绍一些自动叠铆技术、铁心叠铆的装配方法、扭转和回转运动实现过程、回转平安机构、并举例说明该类模具的主要结构、有关设计工艺要求和制造技术,最后探讨了该类模具的开展前景,以便使更多的厂家了解生产该类模具,以此为代表,从而提高我国多工位级进模在世界上的整体水平。
三、工作内容和要求:1. 通过查阅一些最根底的关于定子、转子设计的课件,了解定子、转子分别设计的大致过程。
2. 通过研究三本有关单排微电机定转子〔包括零部件〕设计过程的书籍,了解单排微电机定转子的设计过程。
3. 通过查阅一些书籍,了解自动叠铆技术、铁心叠铆的装配方法、扭转和回转运动实现过程、回转平安机构。
4. 网上搜索相关资料,进一步了解自动叠铆技术、铁心叠铆的装配方法、扭转和回转运动实现过程、回转平安机构以及双排电机定转子自动叠铆的简单设计过程。
5. 综观了多个电机定转子自动叠铆级进模的设计过程,比拟分析此类模具的最正确方案。
四、主要参考文献:[1] 邓卫国. 微电机定转子自动叠片级进模[J].微电机,1998年,第31卷;[2] 陈炎嗣. 多工位级进模设计与制造[M].北京:机械工业出版社,2006.学生〔签名〕年月日指导教师〔签名〕年月日教研室主任〔签名〕年月日系主任〔签名〕年月日毕业论文开题报告目录摘要 (7)关键词 (7)0. 引言 (7)1. 自动叠铆技术 (8)1.1 铁心叠铆形成 (8)1.2 铁心叠铆结构形式 (9)1.3 铁心叠铆点的设置及数量确实定 (9)1.4 叠铆点的几何形状 (10)1.5 叠铆点的过盈量 (11)1.6 自动叠铆的计数别离装置和控制箱 (12)2.铁心叠铆的装配方法 (13)2.1 直接叠铆 (13)2.2 带扭转叠铆 (13)2.3 带回转叠铆 (15)3.扭转和回转运动实现过程 (17)3.1 扭转运动实现过程 (17)3.2 回转运动实现过程 (18)4.回转平安机构 (19)4.1 机械平安机构 (19)4.2 电器平安机构 (19)5.一般自动叠铆级进模结构特点 (20)5.1 模具根本组成局部 (20)5.2 模具主体结构设计 (20)5.3 凸模、凹模设计 (21)5.4 平安保护装置 (21)6.举例说明定转子铁芯叠铆模设计中的有关情况 (22)6.1 定、转子铁芯冲片零件图及排样图 (22)6.2 模具主要设计结构及技术要求 (22)6.3 定转子铁芯叠铆模的工艺制造技术 (24)6.4 双排定转子铁芯自动叠铆级进模的效果 (27)7. 电机铁芯自动叠铆级进模的开展趋势 (27)8. 结束语 (30)答谢辞 (30)参考文献 (32)毕业论文成绩评定表 (33)浅谈电机定转子自动叠铆级进模摘要:本文主要介绍一些自动叠铆技术、铁心叠铆的装配方法、扭转和回转运动实现过程、回转平安机构、该类模具的主要结构、有关设计工艺要求和制造技术,最后探讨了该类模具的开展前景。
电机转子冲片双排叠片级进模设计
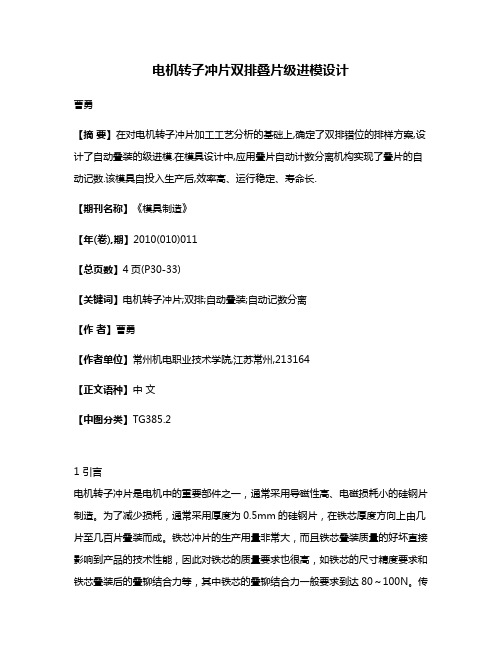
电机转子冲片双排叠片级进模设计曹勇【摘要】在对电机转子冲片加工工艺分析的基础上,确定了双排错位的排样方案,设计了自动叠装的级进模.在模具设计中,应用叠片自动计数分离机构实现了叠片的自动记数.该模具自投入生产后,效率高、运行稳定、寿命长.【期刊名称】《模具制造》【年(卷),期】2010(010)011【总页数】4页(P30-33)【关键词】电机转子冲片;双排;自动叠装;自动记数分离【作者】曹勇【作者单位】常州机电职业技术学院,江苏常州,213164【正文语种】中文【中图分类】TG385.21 引言电机转子冲片是电机中的重要部件之一,通常采用导磁性高、电磁损耗小的硅钢片制造。
为了减少损耗,通常采用厚度为0.5mm的硅钢片,在铁芯厚度方向上由几片至几百片叠装而成。
铁芯冲片的生产用量非常大,而且铁芯叠装质量的好坏直接影响到产品的技术性能,因此对铁芯的质量要求也很高,如铁芯的尺寸精度要求和铁芯叠装后的叠铆结合力等,其中铁芯的叠铆结合力一般要求到达80~100N。
传统的加工工艺是先经过多道工序得到转子铁芯单冲片,再采用手工或机械理片,最后在专用装备上进行压装,这种工艺效率低、定位误差大、毛刺方向一致性也很难控制。
采用自动叠铆级进模代替单冲模、复合模进行冲裁加工,它去除了理片、加压、铆接、氩弧焊等工艺,使冲片在一副模具中完成冲片叠装工艺,大大减轻了工人的劳动强度,提高了劳动生产效率。
同时,提高了铁芯叠铆后的整齐度和叠铆结合力,保证了铁芯的技术要求和精度要求,满足了大批量生产的要求。
2 工艺分析及排样设计图1所示为某电机转子,材料为厚0.5mm的50DW470硅钢片,要求叠装后外观整齐,毛刺小于0.05mm,形位公差要求铁芯内外圆的同心度为0.05mm,上、下平面的平行度为0.15mm、外圆与端面的垂直度为0.1mm,转子铁芯的叠铆力为80N,由此可见该转子铁芯的尺寸精度要求较高。
为保证转子铁芯叠铆力,在转子冲片结构上设计5个圆形(φ3.6mm)的叠铆点。
YDL09电机定转子无搭边硬质合金级进模设计

YDL09电机定转子无搭边硬质合金级进模设计王桂英;汪鹏虎;荆维柱【摘要】分析了电机定转子产品的冲压成形工艺,从优化排样入手,对单排自动叠压硬质合金级进模的相关结构及加工工艺的改进.【期刊名称】《模具制造》【年(卷),期】2010(010)010【总页数】5页(P13-17)【关键词】电机定转子;硬质合金;级进模设计;成形工艺【作者】王桂英;汪鹏虎;荆维柱【作者单位】安徽机电职业技术学院,安徽芜湖,241000;安徽机电职业技术学院,安徽芜湖,241000;安徽机电职业技术学院,安徽芜湖,241000【正文语种】中文【中图分类】TG385.21 零件工艺分析(1)YDL09电动机定、转子如图1所示,其材料为硅钢片50W800,厚度0.5mm,产品叠压厚度8~40mm,转子要求扭斜,年产量80万台,每台需要16~80片(可调节)。
由于该产品的年需求量大,为了给客户节省成本,便于提高材料利用率,采用无搭边排样设计,经与客户协商后在不影响产品使用性能的情况下对制件做如下修改:将直径ϕ120mm与ϕ112mm尺寸相交处增加8×R1mm,如图2所示。
图1 定、转子产品图a——定子 b——转子(2)排样方案。
排样是级进模具设计的最重要的部分,原来排样图如图3所示,上有工艺搭边;经多种方案对比,改进后排样图如图4所示,采用无搭边,材料的总利用率提高5.6%,每台节约材料费约1元,该模具冲压产品总量可达150万台,节省材料费可达150万。
为厂家节省了成本,赢得利益,经济效益可观。
图2 修改后的制件图图3 原排样图①冲导正孔、转子叠压工艺孔②冲转子槽孔、中间轴孔③定转子叠压孔冲通④转子叠压预弯⑤转子落料、叠压、扭转⑥空工位⑦冲定子槽形⑧定子叠压、预弯⑨定子落料图4 改进后排样图①冲导正孔、转子叠压工艺孔②冲转子槽孔、中间轴孔③定转子叠压孔冲通④转子叠压预弯⑤转子落料、叠压、扭转⑥空工位⑦冲定子槽形⑧定子叠压、预弯⑨定子切边⑩空步切断落料叠压2 模具结构设计对于高速自动送料冲压、叠压、扭转级进模而言,模具的导向精度要求很高,该模具采用典型的“可拆卸三板式”结构,这样才能满足精度的要求。
双排定转子铁芯自动叠铆级进模
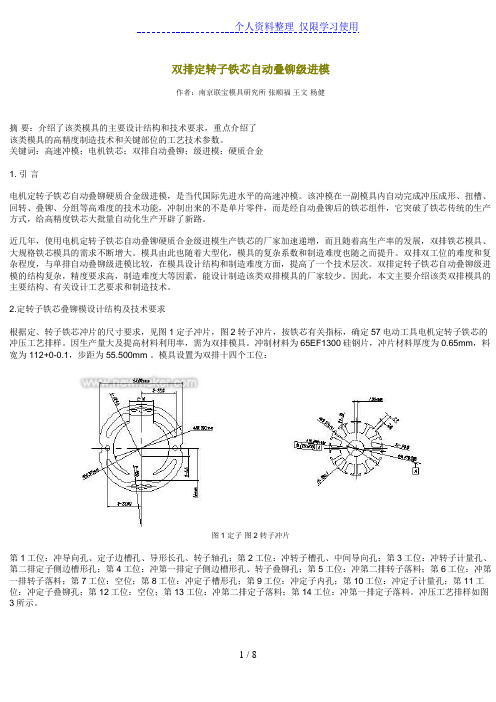
双排定转子铁芯自动叠铆级进模作者:南京联宝模具研究所张顺福王文杨健摘要:介绍了该类模具的主要设计结构和技术要求,重点介绍了该类模具的高精度制造技术和关键部位的工艺技术参数。
关键词:高速冲模;电机铁芯;双排自动叠铆;级进模;硬质合金1. 引言电机定转子铁芯自动叠铆硬质合金级进模,是当代国际先进水平的高速冲模。
该冲模在一副模具内自动完成冲压成形、扭槽、回转、叠铆、分组等高难度的技术功能,冲制出来的不是单片零件,而是经自动叠铆后的铁芯组件,它突破了铁芯传统的生产方式,给高精度铁芯大批量自动化生产开辟了新路。
近几年,使用电机定转子铁芯自动叠铆硬质合金级进模生产铁芯的厂家加速递增,而且随着高生产率的发展,双排铁芯模具、大规格铁芯模具的需求不断增大。
模具由此也随着大型化,模具的复杂系数和制造难度也随之而提升。
双排双工位的难度和复杂程度,与单排自动叠铆级进模比较,在模具设计结构和制造难度方面,提高了一个技术层次。
双排定转子铁芯自动叠铆级进模的结构复杂,精度要求高,制造难度大等因素,能设计制造该类双排模具的厂家较少。
因此,本文主要介绍该类双排模具的主要结构、有关设计工艺要求和制造技术。
2.定转子铁芯叠铆模设计结构及技术要求根据定、转子铁芯冲片的尺寸要求,见图1定子冲片,图2转子冲片,按铁芯有关指标,确定57电动工具电机定转子铁芯的冲压工艺排样。
因生产量大及提高材料利用率,需为双排模具。
冲制材料为65EF1300硅钢片,冲片材料厚度为0.65mm,料宽为112+0-0.1,步距为55.500mm 。
模具设置为双排十四个工位:图1 定子图2 转子冲片第1工位:冲导向孔、定子边槽孔、导形长孔、转子轴孔;第2工位:冲转子槽孔、中间导向孔;第3工位:冲转子计量孔、第二排定子侧边槽形孔;第4工位:冲第一排定子侧边槽形孔、转子叠铆孔;第5工位:冲第二排转子落料;第6工位:冲第一排转子落料;第7工位:空位;第8工位:冲定子槽形孔;第9工位:冲定子内孔;第10工位:冲定子计量孔;第11工位:冲定子叠铆孔;第12工位:空位;第13工位:冲第二排定子落料;第14工位:冲第一排定子落料。
电机定转子铁芯三拼式套冲自动叠铆级进模设计

电机定转子铁芯三拼式套冲自动叠铆级进模设计邓卫国于波巢波摘要:介绍在一副级进模上冲制出空调电机定子铁芯和转子铁芯,其中转子铁芯带扭斜自动叠铆,定子铁芯是由定子外形框架、定子极槽和定子极条三部分组合,在级进模上套冲而成,并带自动叠铆。
重点介绍定子铁芯由三部分组合在级进模上套冲的排样方法和保证冲制出三部分定子铁芯之间高精度配合的技术要求。
关键词:定子铁芯套冲;微小间隙冲裁;自动叠铆;多工位级进模1 前言Φ95空调电机定转子铁芯是应用在空调电机室外机上的一个电机,属于常规的交流电机品种,需求量很大。
原来电机定、转子铁芯的结构情况是:定子铁芯结构是整体式带自动叠铆,转子铁芯是带扭斜自动叠铆,见附图1,用级进模来冲制该电机的定、转子铁芯并带自动叠铆(转子铁芯带扭斜叠铆)的冲压技术已趋成熟。
随着空调电机设计和制造技术的不断发展,为了提高空调电机的技术性能和电机的制作工艺上的需要,该产品对定子铁芯进行了结构上的改进,定子铁芯由原来的整体式改变为有三部分组成的结构,即由定子外形框架(大定子1 个)、定子极槽(中定子6个)和定子极条(小定子6个)三部分组合成一个定子铁芯,见附图2。
更改后的空调电机定、转子铁芯用一副级进模来冲制,其设计制造技术比以前冲制整体式定、转子铁芯的级进模难度要大,模具结构也要复杂。
以下介绍用一副级进模来冲制该电机定、转子铁芯的方法。
2 冲压工艺分析图3所示为空调电机定转子铁芯结构更改后的产品图,铁芯冲片的材料厚度为0.5mm,冲制材料为冷轧硅钢片DW470,该电机定、转子铁芯的技术要求为:叠铆点应保证铁芯结合强度大于50N,定子铁芯三部分之间的配合间隙为一个微小间隙,六个配合处可相互换,定子铁芯结合面及内孔应平直、光洁,定子铁芯装配后的内外圆同心度在0.04mm之内,转子铁芯扭槽线应平直,无明显横折形。
对该电机定、转子铁芯进行综合冲压工艺分析,冲制该电机的定、转子铁芯重点技术难点在三件套冲定子铁芯上。
微型步进电机原理
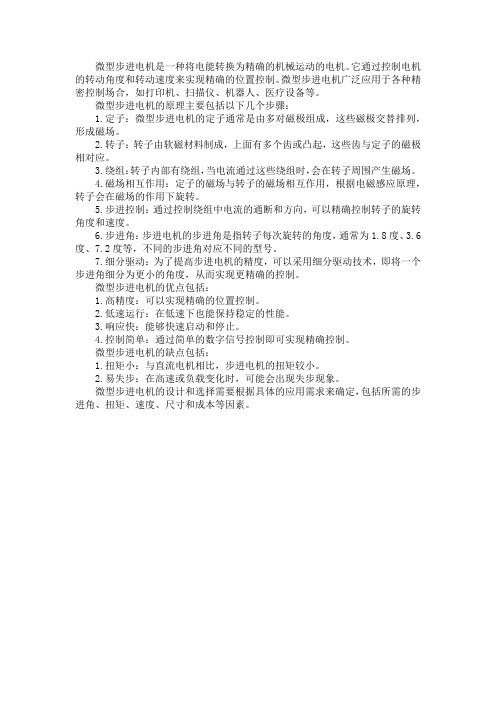
微型步进电机是一种将电能转换为精确的机械运动的电机。
它通过控制电机的转动角度和转动速度来实现精确的位置控制。
微型步进电机广泛应用于各种精密控制场合,如打印机、扫描仪、机器人、医疗设备等。
微型步进电机的原理主要包括以下几个步骤:
1.定子:微型步进电机的定子通常是由多对磁极组成,这些磁极交替排列,形成磁场。
2.转子:转子由软磁材料制成,上面有多个齿或凸起,这些齿与定子的磁极相对应。
3.绕组:转子内部有绕组,当电流通过这些绕组时,会在转子周围产生磁场。
4.磁场相互作用:定子的磁场与转子的磁场相互作用,根据电磁感应原理,转子会在磁场的作用下旋转。
5.步进控制:通过控制绕组中电流的通断和方向,可以精确控制转子的旋转角度和速度。
6.步进角:步进电机的步进角是指转子每次旋转的角度,通常为1.8度、3.6度、
7.2度等,不同的步进角对应不同的型号。
7.细分驱动:为了提高步进电机的精度,可以采用细分驱动技术,即将一个步进角细分为更小的角度,从而实现更精确的控制。
微型步进电机的优点包括:
1.高精度:可以实现精确的位置控制。
2.低速运行:在低速下也能保持稳定的性能。
3.响应快:能够快速启动和停止。
4.控制简单:通过简单的数字信号控制即可实现精确控制。
微型步进电机的缺点包括:
1.扭矩小:与直流电机相比,步进电机的扭矩较小。
2.易失步:在高速或负载变化时,可能会出现失步现象。
微型步进电机的设计和选择需要根据具体的应用需求来确定,包括所需的步进角、扭矩、速度、尺寸和成本等因素。
- 1、下载文档前请自行甄别文档内容的完整性,平台不提供额外的编辑、内容补充、找答案等附加服务。
- 2、"仅部分预览"的文档,不可在线预览部分如存在完整性等问题,可反馈申请退款(可完整预览的文档不适用该条件!)。
- 3、如文档侵犯您的权益,请联系客服反馈,我们会尽快为您处理(人工客服工作时间:9:00-18:30)。
工艺与装备 TECHNOLOGY &EQUIPMENT
微电机定转子自动叠片级进模(1)
邓卫国(江苏常州宝马集团公司 213011)
1 引 言
在微电机行业中,定、转子铁心是电机的
重要部件,它的质量好坏,直接影响到电机的技术性能。
传统电机定、转子铁心制造工艺是用一般冲模冲制出定、转子冲片(散片),经过齐片,再用铆钉铆结、扣片、氩弧焊等方法制成铁心,对于交流电机转子铁心还需用手工进行扭转出斜槽,步进电机要求定、转子铁心磁性能和厚度方向均匀,定子铁心和转子铁心冲片之间分别要求旋转一定的角度,如用传统方法制作,效率低,精度很难达到技术要求。
随着工业生产技术的不断发展,在电机、电器等技术领域,已广泛采用高速冲压多工位级进模制造自动叠片式结构铁心,如各种微电机的定、转子铁心,山字形、U 字形、小型变压器铁心等,其中定、转子铁心还可带扭
转叠斜槽、冲片之间带大角度回转叠铆结构
等,与普通冲模相比,多工位级进模具有冲制精度高、生产效率高、使用寿命长、所冲制铁心尺寸精度一致性好、容易实现自动化、适合大批量生产等优点,是微电机行业精密模具发展的方向。
定、转子铁心自动叠铆级进模的冲制过程是,从冲制条料(卷料)通过校平机、自动送料器、自动加油润滑装置进入多工位级进模,通过各工位的冲制,到转子铁心和定子铁心从模具中通过输送带输送出,所留条料搭边由高速冲床上专用废料刀切断(或有专用切废料机切断,或在级进模上专用废料凸模进行切断),整个过程自动进行,如图1所示。
其中自动叠铆、转子带扭叠铆、大角度回转叠铆冲制工步都是放在定、转子冲片落料工位上完成的。
定、转子自动叠铆级进模具有制造精度高、结构先进、带有技术性要求高的回转机构、计数分离机构及安全机构等,
级
图1 高速冲床冲制过程
—
43—微电机定转子自动叠片级进模(1)
进模的主要零件凸模、凹模采用硬质合金,每磨一次刃口可冲100万次以上,模具总寿命在1亿次以上。
2 自动叠铆技术
级进模上带自动叠铆技术就是要把原来传统制作铁心的工序过程(冲出散片—→齐片—→铆合)放在一副模具内完成,即在级进模的基础上增加了新的冲压工艺技术,除了冲定、转子上轴孔、槽孔等冲片形状要求外,增设了定、转子铁心叠铆需要的叠铆点及起叠铆点分离作用的计数孔的冲压工位,并将原来定、转子的落料工位改变成先起落料作用,然后使各种冲片再引成叠铆过程和叠片计数分离过程(以确保铁心厚度)的叠铆工位,如定、转子铁心需要带扭转、旋转叠铆功能的,即在模具上要带有扭转机构或旋转机构,由叠铆点在冲片上不断改变或转动位置而形成,从而满足在一副模具内自动完成这些功能的需要。
2.1 铁心叠铆形成
在定、转子冲片适当部位上冲出一定几何形状的叠铆点,这些叠铆点沿落料方向的上部是凹形孔,沿落料方向的下部是凸起的,如图2所示,如将同一名义尺寸的凸起部分嵌入到凹形孔时,将自然形成“过盈”而达到紧固连接的目的。
定、转子铁心自动叠铆过程就是按照这一冲压机理进行的。
在模具内铁心形成的过程是,在冲片落料工位上使上面一片叠铆点的凸起部位准确地与下面一片的叠铆点凹形孔部位重合在一起,当上面一片受到落料凸模压力作用时,下面一片借助其外形与凹模壁摩擦所产生的反作用力使两片产生叠铆。
这样,通过自动冲床连续不断的冲制,就可得到一片挨一片排列、毛刺同一方向
且具有一定叠厚的整齐铁心。
图2 铁心叠铆结构
2.2 铁心叠铆结构形式
a.密叠式:叠铆成组的铁心不需要在模
具外再加压,出模即可达到铁心叠铆结合力的要求。
b .半密叠式:出模时已叠合的铁心冲片之间有间隙,还需要再加压才能保证结合力。
2.3 铁心叠铆点的设置及数量的确定 铁心叠铆点位置选择应根据冲片的几何形状确定,同时考虑电机的电磁性能及使用要求。
叠铆点在铁心上分布应对称和均匀,叠铆点数量及大小应根据铁心冲片之间结合牢度大小确定,同时必须考虑模具制造工艺性,如铁心冲片之间带有大角度回转叠铆的,还要考虑叠铆点的等分要求等。
图3表示定、转子铁心的叠铆点分布。
(待续
)
图3 铁心叠铆点分布图
(收稿日期:1997-08-05)
邓卫国:男,1959年11月出生,工程师,主要从事多工位级进模等的设计与制造。
—
44—微电机 1998年 第31卷 第1期(总第100期)。