温度对加氢反应器配管设计的影响
对反应器部分管道配管设计的探讨

对反应器部分管道配管设计的探讨加氢反应器是石油化工加氢装置的核心设备。
加氢装置主要工艺特点是高温、高压、临氢,火灾危险性分类属甲类。
加氢反应器的配管设计不但要满足化工工艺要求,还要达到节省投资,方便操作、检修,满足消防和长周期安全运行的目的。
标签:加氢装置;管道配管;设计探讨加氢装置火灾危险性分类属甲类,主要工艺特点是高温、高压、临氢,加氢反应器是装置的核心部分,其配管设计的好坏是装置设计成功与否的关键。
1 反应器平面布置①反应器的布置应满足工艺设计的要求。
为控制反应系统的温降,压降,避免发生副反应,一般将反应器,换热器和反应进料加热炉等靠近布置,同时在反应器管嘴和其相关管道的应力不超过许用应力的前提下,反应器布置应使管道长度尽量短;②反应器布置应满足建设地区的自然条件和地理位置的要求。
反应器和反应进料加热炉是装置中潜伏火灾危险性比较大的设备,一般布置在装置区的边缘并靠近消防通道,且位于可燃气体、液化烃、甲B类液体介质设备的全年最小频率风向的下风侧,同时考虑将反应器布置于地质条件好的地段,确保其基础牢固可靠;③反应器布置应满足安全的要求。
反应器与其进料加热炉之间或取走反应热的换热器,可视为一个系统,没有防火间距的要求,一般联合集中布置在装置的一端或一侧。
反应器与其无关设备和加热炉一般分开布置,其间距应满足防火和防爆规范的要求;④反應器布置应满足操作和检修要求。
反应器一般按一条直线成组布置在构架内,构架顶部设置吊运机具,装催化剂和检修用的平台,构架下部有卸催化剂的空间,构架一侧有堆放和运输催化剂所需要的场地和道路;⑤反应器布置应满足施工安装要求。
为方便可施工,应提供必要的反应器吊装、运输或在现场进行组装所需要的场地和通道。
2 反应器框架及平台的设置因加氢反应操作温度高,在设置反应框架的时候应充分考虑反应器的热膨胀:①应仔细计算反应器顶部框架平台的高度及开洞大小,要特别注意避免因反应器受热向上膨胀时其封头(包括设备保温)与框架平台梁相碰;②反应器框架其他各层平台的设置,在满足操作和检修要求的同时,应保证在反应器的热膨胀的时候,反应器各个嘴子包括进料口,出料口,冷氢注入口,催化剂卸料口,热电偶口)均不会与框架平台梁相碰;③冷氢嘴子的检修和安装时需要抽出和插入,在冷氢嘴子方位设计时要考虑抽出空间,与冷氢嘴子相邻热电偶要与其成90度角布置。
加氢反应器的管道设计要点
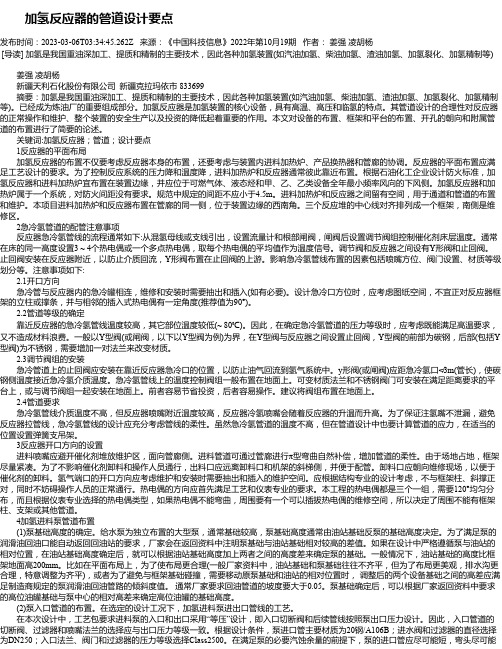
加氢反应器的管道设计要点发布时间:2023-03-06T03:34:45.262Z 来源:《中国科技信息》2022年第10月19期作者:姜强凌胡杨[导读] 加氢是我国重油深加工、提质和精制的主要技术,因此各种加氢装置(如汽油加氢、柴油加氢、渣油加氢、加氢裂化、加氢精制等)姜强凌胡杨新疆天利石化股份有限公司新疆克拉玛依市 833699摘要:加氢是我国重油深加工、提质和精制的主要技术,因此各种加氢装置(如汽油加氢、柴油加氢、渣油加氢、加氢裂化、加氢精制等)。
已经成为炼油厂的重要组成部分。
加氢反应器是加氢装置的核心设备,具有高温、高压和临氢的特点。
其管道设计的合理性对反应器的正常操作和维护、整个装置的安全生产以及投资的降低起着重要的作用。
本文对设备的布置、框架和平台的布置、开孔的朝向和附属管道的布置进行了简要的论述。
关键词:加氢反应器;管道;设计要点1反应器的平面布局加氢反应器的布置不仅要考虑反应器本身的布置,还要考虑与装置内进料加热炉、产品换热器和管廊的协调。
反应器的平面布置应满足工艺设计的要求。
为了控制反应系统的压力降和温度降,进料加热炉和反应器通常彼此靠近布置。
根据石油化工企业设计防火标准,加氢反应器和进料加热炉宜布置在装置边缘,并应位于可燃气体、液态烃和甲、乙、乙类设备全年最小频率风向的下风侧。
加氢反应器和加热炉属于一个系统,对防火间距没有要求。
规范中规定的间距不应小于4.5m。
进料加热炉和反应器之间留有空间,用于通道和管道的布置和维护。
本项目进料加热炉和反应器布置在管廊的同一侧,位于装置边缘的西南角。
三个反应堆的中心线对齐排列成一个框架,南侧是维修区。
2急冷氢管道的配管注意事项反应器急冷氢管线的流程通常如下:从混氢母线或支线引出,设置流量计和根部闸阀,闸阀后设置调节阀组控制催化剂床层温度。
通常在床的同一高度设置3 ~ 4个热电偶或一个多点热电偶,取每个热电偶的平均值作为温度信号。
调节阀和反应器之间设有Y形阀和止回阀。
浅析加氢反应器急冷氢管系设计
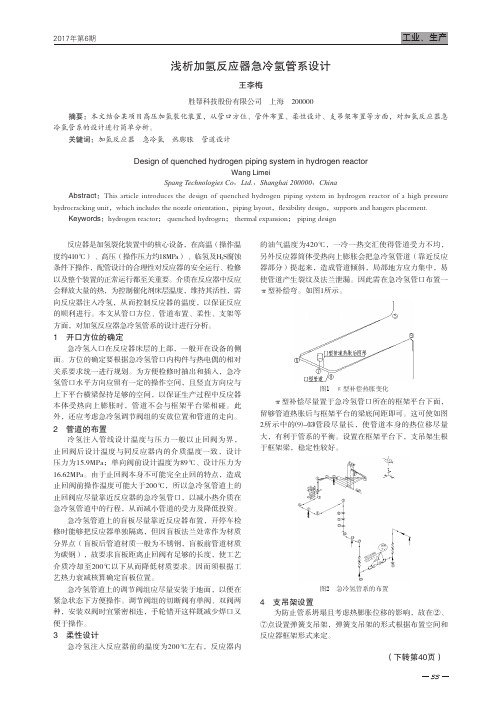
33反应器是加氢裂化装置中的核心设备,在高温(操作温度约410℃) 、高压(操作压力约18MPa) 、临氢及H 2S腐蚀条件下操作,配管设计的合理性对反应器的安全运行、检修以及整个装置的正常运行都至关重要。
介质在反应器中反应会释放大量的热,为控制催化剂床层温度,维持其活性,需向反应器注入冷氢,从而控制反应器的温度,以保证反应的顺利进行。
本文从管口方位、管道布置、柔性、支架等方面,对加氢反应器急冷氢管系的设计进行分析。
1 开口方位的确定急冷氢入口在反应器床层的上部,一般开在设备的侧面。
方位的确定要根据急冷氢管口内构件与热电偶的相对关系要求统一进行规划。
为方便检修时抽出和插入,急冷氢管口水平方向应留有一定的操作空间,且竖直方向应与上下平台横梁保持足够的空间,以保证生产过程中反应器本体受热向上膨胀时,管道不会与框架平台梁相碰。
此外,还应考虑急冷氢调节阀组的安放位置和管道的走向。
2 管道的布置冷氢注入管线设计温度与压力一般以止回阀为界,止回阀后设计温度与同反应器内的介质温度一致,设计压力为15.9MPa;单向阀前设计温度为89℃、设计压力为16.62MPa。
由于止回阀本身不可能完全止回的特点,造成止回阀前操作温度可能大于200℃,所以急冷氢管道上的止回阀应尽量靠近反应器的急冷氢管口,以减小热介质在急冷氢管道中的行程,从而减小管道的受力及降低投资。
急冷氢管道上的盲板尽量靠近反应器布置,开停车检修时能够把反应器单独隔离,但因盲板法兰处常作为材质分界点(盲板后管道材质一般为不锈钢,盲板前管道材质为碳钢),故要求盲板距离止回阀有足够的长度,使工艺介质冷却至200℃以下从而降低材质要求。
因而须根据工艺热力衰减核算确定盲板位置。
急冷氢管道上的调节阀组应尽量安装于地面,以便在紧急状态下方便操作。
调节阀组的切断阀有单阀、双阀两种,安装双阀时宜紧密相连,手轮错开这样既减少焊口又便于操作。
3 柔性设计急冷氢注入反应器前的温度为200℃左右,反应器内的油气温度为420℃,一冷一热交汇使得管道受力不均,另外反应器筒体受热向上膨胀会把急冷氢管道(靠近反应器部分)提起来,造成管道倾斜,局部地方应力集中,易使管道产生裂纹及法兰泄漏。
浅谈加氢反应器急冷氢管道的配管设计及应力分析
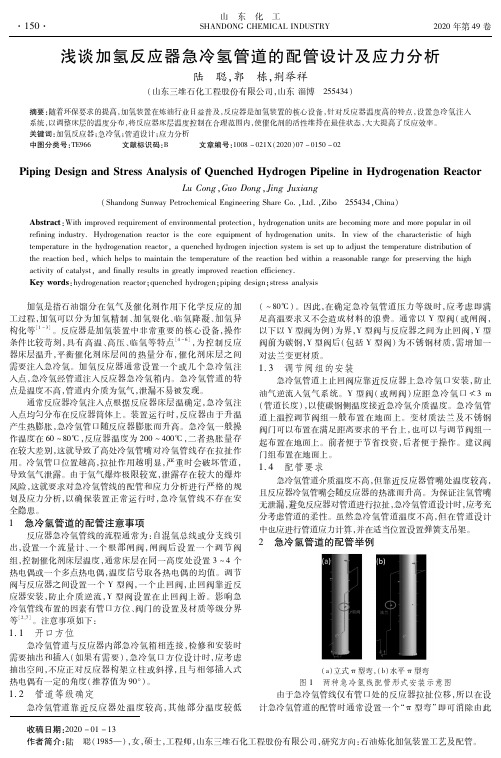
急冷氢管道介质温度不高,但靠近反应器管嘴处温度较高, 且反应器冷氢管嘴会随反应器的热涨而升高。为保证注氢管嘴 无泄漏,避免反应器对管道进行拉扯,急冷氢管道设计时,应考充 分考虑管道的柔性。虽然急冷氢管道温度不高,但在管道设计 中也应进行管道应力计算,并在适当位置设置弹簧支吊架。
(~80℃)。因此,在 确 定 急 冷 氢 管 道 压 力 等 级 时,应 考 虑 即 满 足高温要求又不会造成材料的浪费。通常以 Y型阀(或闸阀, 以下以 Y型阀为例)为界,Y型阀与反应器之间为止回阀,Y型 阀前为碳钢,Y型阀后(包括 Y型阀)为不锈钢材质,需增加一 对法兰变更材质。
1.3 调节阀组的安装
1.1 开口方位
急冷氢管道与反应器内部急冷氢箱相连接,检修和安装时 需要抽出和插入(如果有需要),急冷氢口方位设计时,应考虑 抽出空间,不应正 对 反 应 器 构 架 立 柱 或 斜 撑,且 与 相 邻 插 入 式 热电偶有一定的角度(推荐值为 90°)。
1.2 管道等级确定
急冷氢管道 靠 近 反 应 器 处 温 度 较 高,其 他 部 分 温 度 较 低
·150·
山 东 化 工 SHANDONGCHEMICALINDUSTRY 2020年第 49卷
浅谈加氢反应器急冷氢管道的配管设计及应力分析
陆 聪,郭 栋,荆举祥
(山东三维石化工程股份有限公司,山东 淄博 255434)
摘要:随着环保要求的提高,加氢装置在炼油行业日益普及,反应器是加氢装置的核心设备,针对反应器温度高的特点,设置急冷氢注入 系统,以调整床层的温度分布,将反应器床层温度控制在合理范围内,使催化剂的活性维持在最佳状态,大大提高了反应效率。 关键词:加氢反应器;急冷氢;管道设计;应力分析 中图分类号:TE966 文献标识码:B 文章编号:1008-021X(2020)07-0150-02
浅析渣油加氢装置加氢反应器的配管设计
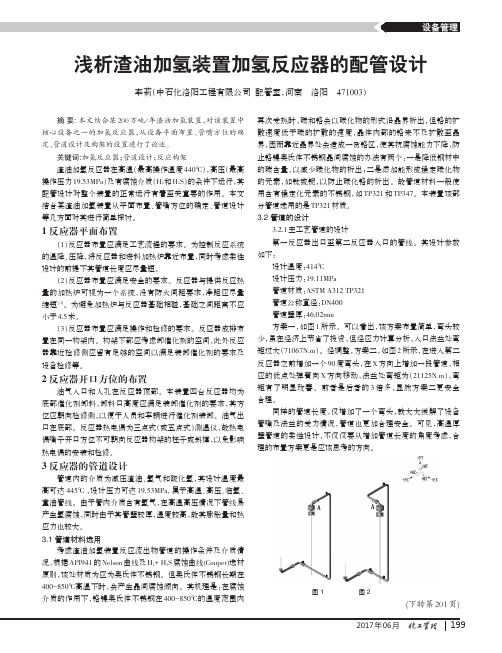
摘要:本文结合某200万吨/年渣油加氢装置,对该装置中核心设备之一的加氢反应器,从设备平面布置、管嘴方位的确定、管道设计及构架的设置进行了论述。
关键词:加氢反应器;管道设计;反应构架渣油加氢反应器在高温(最高操作温度440℃),高压(最高操作压力19.53MPa)及有腐蚀介质(H2和H2S)的条件下运行,其配管设计对整个装置的正常运行有着至关重要的作用。
本文结合某渣油加氢装置从平面布置、管嘴方位的确定、管道设计等几方面对其进行简单探讨。
1反应器平面布置(1)反应器布置应满足工艺流程的要求。
为控制反应系统的温降、压降,将反应器和进料加热炉靠近布置,同时考虑柔性设计的前提下其管道长度应尽量短。
(2)反应器布置应满足安全的要求。
反应器与提供反应热量的加热炉可视为一个系统,没有防火间距要求,净距应尽量缩短[2]。
为避免加热炉与反应器基础相碰,基础之间距离不应小于4.5米。
(3)反应器布置应满足操作和检修的要求。
反应器成排布置在同一构架内。
构架下部应考虑卸催化剂的空间,此外反应器靠近检修侧应留有足够的空间以满足装卸催化剂的要求及设备检修等。
2反应器开口方位的布置油气入口和人孔在反应器顶部。
本装置四台反应器均为底部催化剂卸料,卸料口高度应满足装卸催化剂的要求,其方位应朝向检修侧,以便于人员和车辆进行催化剂装卸。
油气出口在底部。
反应器热电偶为三点式(或五点式)测温仪,故热电偶嘴子开口方位不可朝向反应器构架的柱子或斜撑,以免影响热电偶的安装和检修。
3反应器的管道设计管道内的介质为减压渣油、氢气和硫化氢,其设计温度最高可达445℃,设计压力可达19.53MPa,属于高温、高压、临氢、重油管线。
由于管内介质含有氢气,在高温高压情况下管线易产生氢腐蚀,同时由于其管壁较厚,温度较高,故其膨胀量和热应力也较大。
3.1管道材料选用考虑渣油加氢装置反应流出物管道的操作条件及介质情况,根据API941的Nelson曲线及H2+H2S腐蚀曲线(Couper)选材原则,该处材质为应为奥氏体不锈钢。
煤焦油加氢装置反应区配管设计浅谈

煤焦油加氢装置反应区配管设计浅谈作者简介:陈梦莹,(1986-),隶属于新佑能源配管室,任项目经理职位,化工工程师摘要:讨论了煤焦油加氢装置反应区管道材料的选择;反应器与加热炉,串联反应器之间,反应器与高压换热器之间配管的设计,以及此部分管道支架的设置特点;通过对反应器与相关连设备特点的分析,阐述了反应区配管设计的原则及难点。
关键词:煤焦油加氢装置;反应区;配管;材料Discussion ofthe Coal Tar Hydrogenation Reaction Zone Piping System DesignChen MengyingAbstract: This article discusses theselection of coal tar hydrogenation reaction zone means piping material; Thereactor andthe furnace, disposed in series between the characteristics of thereactor, the design of the piping between the reactor and thehigh pressureheat exchanger, and this part of the stand pipe; Through the reactor andassociated equipment features analysis, elaborated the principles anddifficulties reaction zone piping design.Keywords: coal tar hydrogenationunit;reaction zone; pipeline design;material煤焦油加氢技术是采用固定床加氢处理技术将煤焦油所含的金属杂质、S、N、O等杂原子脱除,并将其中的烯烃和芳烃类化合物进行饱和或裂化来生产质量优良的石脑油馏分和柴油馏分。
加氢裂化反应影响因素
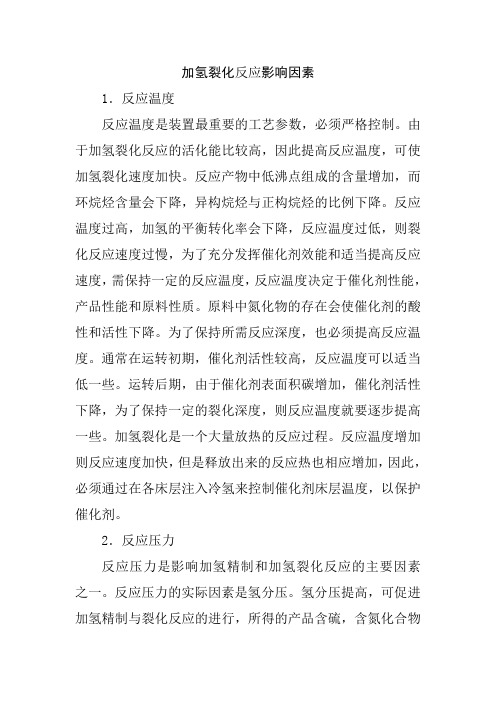
加氢裂化反应影响因素1.反应温度反应温度是装置最重要的工艺参数,必须严格控制。
由于加氢裂化反应的活化能比较高,因此提高反应温度,可使加氢裂化速度加快。
反应产物中低沸点组成的含量增加,而环烷烃含量会下降,异构烷烃与正构烷烃的比例下降。
反应温度过高,加氢的平衡转化率会下降,反应温度过低,则裂化反应速度过慢,为了充分发挥催化剂效能和适当提高反应速度,需保持一定的反应温度,反应温度决定于催化剂性能,产品性能和原料性质。
原料中氮化物的存在会使催化剂的酸性和活性下降。
为了保持所需反应深度,也必须提高反应温度。
通常在运转初期,催化剂活性较高,反应温度可以适当低一些。
运转后期,由于催化剂表面积碳增加,催化剂活性下降,为了保持一定的裂化深度,则反应温度就要逐步提高一些。
加氢裂化是一个大量放热的反应过程。
反应温度增加则反应速度加快,但是释放出来的反应热也相应增加,因此,必须通过在各床层注入冷氢来控制催化剂床层温度,以保护催化剂。
2.反应压力反应压力是影响加氢精制和加氢裂化反应的主要因素之一。
反应压力的实际因素是氢分压。
氢分压提高,可促进加氢精制与裂化反应的进行,所得的产品含硫,含氮化合物减少,更重要的是可减少结焦,保持催化剂活化,提高催化剂的稳定性。
反应器中的氢分压等于油汽加上循环氢的总压与氢气占全部气体分子数的乘积。
本装置补充氢纯度确定为99.9%。
从经济角度出发,不采用提高补充氢纯度的办法来提高氢分压。
3.氢油比氢油体积比有两种,其一是反应器入口的氢油比,其二是总冷氢油比。
反应器入口氢油比是每小时通过反应器内氢气(循环氢气+新氢)体积与每小时通过的原料油体积之比。
(单位为Nm3 /m3)。
总冷氢油体积比是每小时通入反应器的总冷氢气体积总和与每小时通过的原料油体积之比。
在加氢反应器中只有一部分氢气起反应。
大部分氢气仍以自由状态存在。
采用高氢油比,可提高氢分压,有利于传质和加氢反应的进行,在一定范围内防止油料在催化剂表面结焦。
温度管理对化学反应速率的影响探究

温度管理对化学反应速率的影响探究化学反应是物质变化的过程,而温度是影响化学反应速率的重要因素之一。
在实际应用中,探究温度管理对化学反应速率的影响具有重要意义,可以帮助我们更好地理解和控制化学反应过程,从而提高生产效率和优化产品质量。
一、温度对化学反应速率的影响温度是分子运动的直接体现,高温下分子运动更加剧烈,碰撞频率和碰撞能量增加,从而促进了反应速率的提高。
根据阿伦尼乌斯方程,当温度升高10摄氏度时,反应速率将增加大约2倍。
这是因为高温下分子的平均动能增加,分子能够更容易克服反应物之间的能垒,从而更容易发生有效碰撞。
二、温度管理对化学反应速率的影响1. 温度控制在合适范围内尽管温度升高可以加快反应速率,但过高的温度也可能导致副反应的发生,甚至破坏反应体系。
因此,在实际应用中,需要根据反应的特性和需求,合理选择和控制温度。
例如,一些化学反应对温度的要求较高,需要在高温下进行,而另一些反应则需要在低温下进行,以避免副反应的发生。
2. 温度梯度的控制在一些复杂的反应体系中,温度梯度的控制对于反应速率的均匀性和产物的选择性具有重要影响。
通过合理设计反应器的结构和控制系统,可以实现温度梯度的控制,从而优化反应条件,提高产物的纯度和收率。
三、温度管理对实际化学反应的应用1. 化学合成反应在化学合成反应中,温度的选择对反应速率和产物选择性具有重要影响。
合理的温度管理可以提高反应速率,减少副反应的发生,并且有助于选择性合成目标产物。
例如,许多有机合成反应需要在特定的温度下进行,以避免副反应的发生和产物的降解。
2. 工业生产过程在工业生产过程中,温度管理对于反应速率和产品质量的控制至关重要。
通过合理控制反应温度,可以提高反应速率,减少副反应的发生,并且有助于优化产品的物理和化学性质。
例如,一些化学反应需要在特定的温度下进行,以保证产品的纯度和收率。
3. 药物研发在药物研发过程中,温度管理对于反应速率和产物选择性的控制非常重要。
锻焊结构加氢反应器的温度控制与调节研究
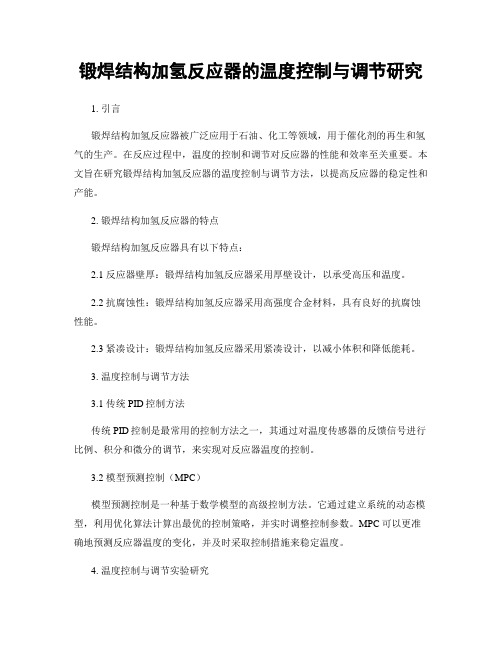
锻焊结构加氢反应器的温度控制与调节研究1. 引言锻焊结构加氢反应器被广泛应用于石油、化工等领域,用于催化剂的再生和氢气的生产。
在反应过程中,温度的控制和调节对反应器的性能和效率至关重要。
本文旨在研究锻焊结构加氢反应器的温度控制与调节方法,以提高反应器的稳定性和产能。
2. 锻焊结构加氢反应器的特点锻焊结构加氢反应器具有以下特点:2.1 反应器壁厚:锻焊结构加氢反应器采用厚壁设计,以承受高压和温度。
2.2 抗腐蚀性:锻焊结构加氢反应器采用高强度合金材料,具有良好的抗腐蚀性能。
2.3 紧凑设计:锻焊结构加氢反应器采用紧凑设计,以减小体积和降低能耗。
3. 温度控制与调节方法3.1 传统PID控制方法传统PID控制是最常用的控制方法之一,其通过对温度传感器的反馈信号进行比例、积分和微分的调节,来实现对反应器温度的控制。
3.2 模型预测控制(MPC)模型预测控制是一种基于数学模型的高级控制方法。
它通过建立系统的动态模型,利用优化算法计算出最优的控制策略,并实时调整控制参数。
MPC可以更准确地预测反应器温度的变化,并及时采取控制措施来稳定温度。
4. 温度控制与调节实验研究为验证上述控制方法的有效性,我们进行了一系列的实验研究。
4.1 实验装置设计我们设计了一个小型的锻焊结构加氢反应器实验装置,包括反应器、加热系统、传感器和控制系统。
4.2 温度控制实验我们首先使用传统PID控制方法对反应器温度进行控制,并记录温度的变化。
实验结果表明,PID控制方法在短时间内可以较好地控制温度,但在长时间运行时会产生温度波动。
4.3 MPC控制实验接着,我们采用MPC控制方法进行实验控制。
通过建立反应器的数学模型,并通过离线优化计算出最优的控制策略,将该策略导入实验装置的控制系统中。
实验结果显示,MPC控制方法能够更加精确地控制反应器温度,不仅可以稳定温度,还可以减小温度波动。
5. 结果分析与讨论实验结果表明,锻焊结构加氢反应器的温度控制与调节对反应器的性能和效率具有重要影响。
氢气输送管道温度控制规范研究

氢气输送管道温度控制规范研究氢气是一种清洁、高效的能源,被广泛应用于工业生产和交通运输领域。
随着氢能技术的不断发展,氢气输送管道作为氢气的主要输送方式,其安全性和可靠性备受关注。
在氢气输送管道运输过程中,温度控制是至关重要的一环。
氢气输送管道在运输过程中受到多种外界因素的影响,如温度波动、气候条件变化等,会对管道内氢气的温度产生影响。
过高或过低的温度会导致氢气在管道内产生压力变化,从而增加管道的安全风险。
因此,在氢气输送管道的设计和运行中,必须对管道内氢气的温度进行严格控制。
目前,国内外对于氢气输送管道温度控制的规范较为模糊,缺乏统一的标准和指导。
因此,有必要对氢气输送管道温度控制规范进行深入研究,制定出科学、合理的控制措施,提高氢气输送管道的安全性和可靠性。
在这一背景下,本文旨在对氢气输送管道温度控制规范进行系统性的探讨和研究。
首先,本文将对氢气输送管道的基本原理和温度控制的重要性进行介绍。
随后,将对国内外相关标准和规范进行梳理和比较分析,探讨不同标准对氢气输送管道温度控制的要求和做法。
在此基础上,将进一步研究不同环境条件下氢气输送管道的温度控制策略,包括采用保温材料、控制加热、调节氢气流量等方法。
同时,本文还将结合实际案例,对氢气输送管道在不同温度条件下的运行情况进行模拟和分析,验证温度控制方案的有效性。
通过对比实验结果,得出最佳的氢气输送管道温度控制方案,为今后氢气输送管道的设计和运行提供参考。
最后,将总结研究结果,探讨氢气输送管道温度控制规范的完善方向和发展趋势。
让我们总结一下本文的重点,我们可以发现,具有重要的理论和实践意义。
通过对其进行深入研究,可以提高氢气输送管道的安全性和可靠性,促进氢能技术的发展和应用。
希望本文的研究成果能够为相关领域的学者和工程师提供参考,推动氢气输送管道温度控制规范的进一步完善和发展。
浆态床加氢反应器的反应温度
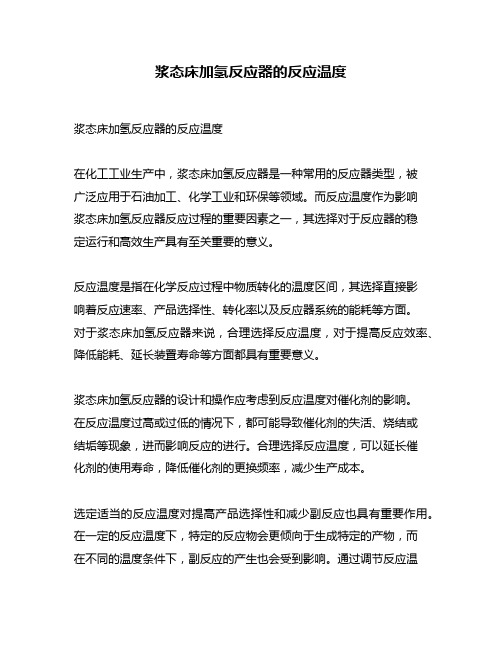
浆态床加氢反应器的反应温度浆态床加氢反应器的反应温度在化工工业生产中,浆态床加氢反应器是一种常用的反应器类型,被广泛应用于石油加工、化学工业和环保等领域。
而反应温度作为影响浆态床加氢反应器反应过程的重要因素之一,其选择对于反应器的稳定运行和高效生产具有至关重要的意义。
反应温度是指在化学反应过程中物质转化的温度区间,其选择直接影响着反应速率、产品选择性、转化率以及反应器系统的能耗等方面。
对于浆态床加氢反应器来说,合理选择反应温度,对于提高反应效率、降低能耗、延长装置寿命等方面都具有重要意义。
浆态床加氢反应器的设计和操作应考虑到反应温度对催化剂的影响。
在反应温度过高或过低的情况下,都可能导致催化剂的失活、烧结或结垢等现象,进而影响反应的进行。
合理选择反应温度,可以延长催化剂的使用寿命,降低催化剂的更换频率,减少生产成本。
选定适当的反应温度对提高产品选择性和减少副反应也具有重要作用。
在一定的反应温度下,特定的反应物会更倾向于生成特定的产物,而在不同的温度条件下,副反应的产生也会受到影响。
通过调节反应温度,可以获得更高的产品选择性,减少废品的产生,提高反应的经济效益。
另外,反应温度对于提高反应速率同样具有重要意义。
在合适的温度范围内,反应物子在催化剂表面的吸附速率、反应物分解速率等都会达到平衡,使得反应速率能够达到最优。
通过选择适当的反应温度,可以提高反应速率,减少反应时间,提高生产效率。
反应温度还可以影响反应系统的能耗。
在一定的温度条件下,反应物的分解能量、转化热、热损失等都会受到影响,因此选择合适的反应温度,可以降低能耗、减少生产成本。
总结来说,浆态床加氢反应器的反应温度选择对于反应过程的稳定、产品选择性、反应速率、能耗等方面都有着重要的影响。
在实际生产中,应根据具体反应物性质、催化剂特性、产品要求等多方面因素,权衡利弊,选择合适的反应温度,以达到最优的反应效果。
个人观点在选择浆态床加氢反应器的反应温度时,应当综合考虑多方面因素,不能片面追求提高反应速率或产品选择性,而忽视了对催化剂、能耗等方面的影响。
氢气管道设计温度

氢气管道设计温度English:The design temperature for a hydrogen pipeline primarily depends on the intended operational conditions and the surrounding environment. It is crucial to consider the maximum and minimum temperatures the pipeline will encounter during its operational lifespan. The design temperature should be set to ensure the pipeline materials maintain their structural integrity and mechanical properties within this temperature range. Factors such as ambient temperature variations, solar radiation, and potential heat sources nearby also need to be taken into account. Additionally, safety regulations and codes specific to hydrogen pipeline design must be adhered to when determining the appropriate design temperature.中文:氢气管道的设计温度主要取决于预定的操作条件以及周围环境。
在设计过程中,必须考虑管道在其使用寿命期间可能遇到的最高和最低温度。
设计温度应设定在确保管道材料在此温度范围内保持其结构完整性和机械性能。
加氢装置进热高分器的温度

加氢装置进热高分器的温度
在加氢技术中,加氢装置是至关重要的设备之一。
随着近年来加氢技术不断发展,加氢装置也在不断升级和改进。
在加氢装置中,热高分器作为关键的装置之一,其温度控制也变得尤为重要。
热高分器是加氢装置的重要组成部分,通常由多级换热器、冷却器、加热器、再生器等组成。
在加氢过程中,热高分器承担着将氢气中的杂质去除以及将氢气提高至一定压力的重要作用。
关键的是,热高分器的温度对氢气的质量和加氢速度有着很大的影响。
在氢气加氢过程中,加氢装置所产生的热量需要通过换热器向外释放,以保持热高分器的温度处于恰当的范围内。
具体来说,当热高分器的温度太高时,不仅会影响氢气的质量,还可能导致加氢过程不稳定,从而影响氢气加氢速度;当热高分器的温度太低时,不仅会降低加氢效率,还会增加氢气中杂质的含量,从而不利于氢气纯度的提高。
因此,在加氢装置中,往往需要对热高分器进氢气的温度进行精确的控制和调节,以保证氢气的质量和加氢速度。
为了实现对热高分器温度的控制和调节,通常需要采取一系列措施。
首先,需要利用温度传感器等设备监测热高分器的温度变化,并将其传递给控制中心。
其次,需要根据热高分器的温度变化调节芯片来控制加氢装置的加热或冷却操作。
此外,为了更好地保持热高分器的温度处于恰当的范围内,加氢装置还可以采用多级换热器等装置进行高效换热,使产生的大量热量及时释放,保持热高分器的温度稳定。
总之,加氢装置的进热高分器温度控制对于氢能产业的发展至关重要。
只有在温度控制和调节等方面做好充分的准备工作,才能实现高效、稳定、可靠的氢气加氢过程,为氢能产业的发展注入新的动力。
影响加氢反应的主要因素
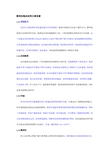
影响加氢反应的主要因素1.3.1反应压力反应压力的影响常常是通过氢分压来体现的,系统中的氢分压决定于操作压力、循环氢纯度以及原料的汽化率。
选择适宜的加氢精制压力时,主要考虑催化剂寿命及产品质量。
由于加氢反应是体积缩小的反应,提高压力反应平衡向着产物方向移动,使加氢精制深度增加。
尤其是脱氮作用能显著提高,也对减少催化剂积碳、保持催化剂活性,提高催化剂稳定性有积极作用。
但同时也增加了设备投资,因此选择加氢精制压力要综合考虑。
1.3.2反应温度反应温度对反应速度、产品质量和收率起着较大的作用。
加氢精制是个放热反应,提高温度不利于加氢化学平衡往产物方向移动,但加氢反应速度又主要取决于反应温度,因此提温会促进加氢反应,提高加氢深度,但反应温度又受热力学平衡条件的限制,过高会使加氢裂化反应加剧,放出更多热量,导致催化剂床层超温,表面积碳速度加快,原料部分裂解,产品收率下降。
在工业生产中,温度条件的选择一般受原料的性质和产品质量的影响,同时还要考虑催化剂活性。
1.3.3空速单位时间内单位数量催化剂上所通过的原料油量叫空速。
空速反应了装置的处理能力,但空速的提高受到反应速度的制约。
降低空速意味着增加原料油同催化剂的接触时间,增加了加氢深度,有利于脱除杂质,提高产品质量,但空速过低,不仅降低了装置的处理量,而且还会增加裂化反应,从而降低液收,使催化剂表面积碳量相应增加。
因此选择适宜的空速可以使反应朝所希望的方向进行,空速一般控制在1.0~2.0时-1。
1.3.4氢油比进入反应器之纯氢气量与原料量之体积比称为氢油比。
提高氢油比也就是提高氢分压,有利于加氢反应、抑制催化剂上积碳形成和反应热的导出,但氢油比过大要引起原料油气相分压降低,缩短反应时间,同时增大动力消耗,使操作费用增大。
因此应根据具体条件选择最适宜的氢油比。
我装置的氢油比设计值为485:1。
1.3.5原料油性质原料油的组成决定加氢反应的方向和放出热量的大小,也是确定氢油比和反应温度的主要依据。
影响加氢精制效果的主要因素

影响加氢精制效果的主要因素有:反应压力、反应温度、空速、氢油比、原料性质和催化剂。
1、反应压力反应压力的影响是通过氢分压来体现的。
加氢装置系统中的氢分压决定于操作压力、氢油比、循环氢纯度以及原料的汽化率。
对于硫化物的加氢脱硫和烯烃的加氢饱和反应,在压力不太高时就有较高的转化深度。
汽油在氢分压高于2.5~3.0MPa压力下加氢精制时,深度不受热力学平衡控制,而取决于反应速度和反应时间。
汽油在加氢精制条件下一般处于气相,提高压力使汽油的停留时间延长,从而提高了汽油的精制深度。
氢分压高于3.0MPa时,催化剂表面上氢的浓度已达到饱和状态,如果操作压力不变,通过提高氢油比来提高氢分压则精制深度下降,因为这时会使原料油的分压降低。
柴油馏分(180~360℃)加氢精制的反应压力一般在4.0~8.0MPa(氢分压3.0~7.0MPa)。
压力对柴油加氢精制的影响要复杂一些。
柴油馏分在加氢精制条件下可能是汽相,也可能是汽液混相。
在处于汽相时,提高压力使反应时间延长,从而提高了反应深度。
提高反应压力使精制深度增大,特别是脱氮率显着提高,这是因为脱氮反应速度较低;而对脱硫率影响不大,这是因为脱硫速度较高,在较低的压力时已有足够的反应时间。
在精制氮含量较高的原料时,为了保证达到一定的脱氮率而不得不提高压力或降低空速。
如果其它条件不变,将反应压力提高到某个值时,反应系统会出现液相,在开始出现液相后,继续提高压力将会使精制效果变差。
有液相存在时,氢通过液膜向催化剂表面扩散的速度往往是影响反应速度的控制因素,这个扩散速度与氢分压成正比而随着催化剂表面上液层厚度的增加而降低。
因此,在出现液相之后,提高反应压力会使催化剂表面上的液层加厚,从而降低了反应速度。
如果压力不变,通过提高氢油比来提高氢分压,则精制深度会出现一个最大值。
出现这种现象的原因是:在原料完全汽化以前,提高氢分压有利于原料汽化,而使催化剂表面上的液膜减小,同时也有利于氢在催化剂表面的液膜减小,也有利于氢向催化剂表面的扩散,因此在原料油完全汽化以前,提高氢分压(总压不变)有利于提高反应速度。
氢气生产过程中温度对氢燃料电池性能的影响研究
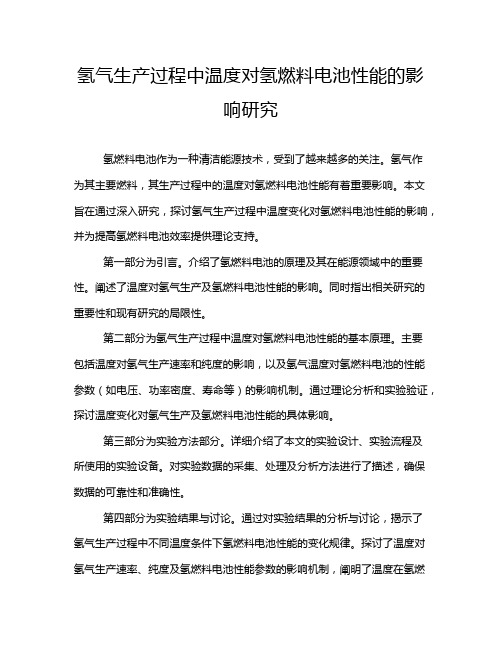
氢气生产过程中温度对氢燃料电池性能的影响研究氢燃料电池作为一种清洁能源技术,受到了越来越多的关注。
氢气作为其主要燃料,其生产过程中的温度对氢燃料电池性能有着重要影响。
本文旨在通过深入研究,探讨氢气生产过程中温度变化对氢燃料电池性能的影响,并为提高氢燃料电池效率提供理论支持。
第一部分为引言。
介绍了氢燃料电池的原理及其在能源领域中的重要性。
阐述了温度对氢气生产及氢燃料电池性能的影响。
同时指出相关研究的重要性和现有研究的局限性。
第二部分为氢气生产过程中温度对氢燃料电池性能的基本原理。
主要包括温度对氢气生产速率和纯度的影响,以及氢气温度对氢燃料电池的性能参数(如电压、功率密度、寿命等)的影响机制。
通过理论分析和实验验证,探讨温度变化对氢气生产及氢燃料电池性能的具体影响。
第三部分为实验方法部分。
详细介绍了本文的实验设计、实验流程及所使用的实验设备。
对实验数据的采集、处理及分析方法进行了描述,确保数据的可靠性和准确性。
第四部分为实验结果与讨论。
通过对实验结果的分析与讨论,揭示了氢气生产过程中不同温度条件下氢燃料电池性能的变化规律。
探讨了温度对氢气生产速率、纯度及氢燃料电池性能参数的影响机制,阐明了温度在氢燃料电池领域中的重要作用。
第五部分为结论与展望。
总结了本文的研究成果,阐明了温度对氢气生产过程及氢燃料电池性能的重要影响。
同时,对未来进一步深入研究的方向和重点进行了展望,为氢燃料电池技术的发展提供了参考和建议。
总结一下本文的重点,我们可以发现,本文通过对氢气生产过程中温度对氢燃料电池性能的影响进行了深入研究,为提高氢燃料电池效率和性能提供了理论基础和实验依据。
通过本研究可以更好地理解氢燃料电池在不同温度条件下的工作性能,为其在可再生能源领域的应用和推广提供技术支持。
希望本研究能为相关领域的研究和实践提供一定的参考价值,促进氢燃料电池技术的进一步发展与完善。
- 1、下载文档前请自行甄别文档内容的完整性,平台不提供额外的编辑、内容补充、找答案等附加服务。
- 2、"仅部分预览"的文档,不可在线预览部分如存在完整性等问题,可反馈申请退款(可完整预览的文档不适用该条件!)。
- 3、如文档侵犯您的权益,请联系客服反馈,我们会尽快为您处理(人工客服工作时间:9:00-18:30)。
2016年12月
温度对加氢反应器配管设计的影响
刘复生(中国石油工程建设有限公司大连设计分公司,辽宁
大连116000)
摘要:本文通过阐述温度对加氢装置中加氢反应器构架平
台的设置,管道布置的影响,总结了加氢反应器在温度影响下的配管设计要点。
关键词:温度;加氢反应器;构架平台设置;管道布置;应力分析
加氢工艺具有生产灵活性大,加工原料范围较大、液体产品收率高、产品质量稳定性好等特点,是重油深加工的主要工艺技术手段之一。
因此近年来汽油加氢技术在国内得到了长足的发展。
加氢反应器是加氢装置中非常重要的核心设备,操作条件比较苛刻,具有高温、高压、临氢等特点。
与反应器关联的管道多采用不锈钢,合金钢管线,因此反应器配管的合理性关系到整个加氢装置的安全生产及节约工程投资。
而温度是影响加氢反应器配管的主要因素,本文通过某加氢装置加氢反应器的配管过程总结了在温度影响下的配管设计要点。
1温度对反应器构架平台设置的影响
1.1反应器构架中间平台的设置
反应器构架中间各层平台的设置应根据反应器冷油注入口、热点偶口、催化剂中间卸料口及压力表口等管嘴及其连接管道的操作和检修的要求进行确定,但在确定平台标高时应充分考虑到因反应器的热膨胀而引起设备管嘴上移的现象,防止各管嘴与构架平台梁相碰。
以反应器上的热电偶口为例,通常反应器外壁热电偶口较多,且热电偶口垂直间距通常为1100mm 左右,而构架平台间距通常为4000mm 左右,因此通常容易造成热电偶口距离上层平台梁较近的情况,在此情况下我们不但应满足反应器冷态安装情况下其设备本体上的热电偶口法兰不与平台梁相碰撞,而且应该满足在最苛刻条件下反应器向上膨胀后,其热电偶法兰上边缘与上层平台梁不碰撞,且至少有50mm 的间隙。
1.2反应器构架顶平台的设置
反应器构架顶平台的设置根据以下几点确定:
①反应器及其顶部入口管道在操作工况下会发生向上的位移,因此通常需要在入口管底设置弹簧,且通常为恒力弹簧,因此入口管道管底与顶平台的间距应能满足弹簧的安装要求,通常为800mm 左右;②反应器顶入口管道距离顶平台的高度应便于管线上的仪表和阀门的检修操作;③反应器顶人孔法兰盖应露出顶平台,顶人孔螺栓的安装与拆卸应比较方便,通常顶平台的高度应设置在距反应器顶人孔法兰螺栓最下端100mm 处;④由于反应器内介质温度较高,引起反应器向上的热位移也较大,因此在考虑顶平台开洞时不但要考虑其安装工况下洞口的尺寸,还要考虑到其最苛刻工况即温度最高的工况下反应器的向上热位移,开洞的大小应能避免在最苛刻的操作条件下反应器与顶平台梁相碰。
一般顶平台的开洞大小可按反应器热胀后平台高度处反应器外壁+保温厚度+50mm 设计。
计算方法如下:
计算反应器向上的热位移是可将反应器看做一端固定的
直管,由常温(20℃)受热后将沿着轴向膨胀,其向上热位移可根据以下公式进行计算:
Δt =L•αt ΔT=L•e t
Δt ——管系的热胀量,cm ;ΔT ——管系的温升,℃;αt ——线膨胀系数,由20℃至t℃的每m 温升1℃的平均膨胀量,
cm/m•℃,见《工艺管道安装设计手册》第一册表17-1-12;L ——管系的长度,m ;e t ——单位线膨胀量,由20℃至t℃的每m 热膨胀量,cm/m 。
2温度对反应器的管道布置的影响
2.1反应器进出口管道
①反应器出入口管道通常口径较大,温度较高,管系应做详尽的应力分析,使进出口管嘴受力合理,过大将可能增加反应器壁厚,过小将可能使管线增长,弯头增多,因此管道设计专业应与设备专业协商反应器进出口管嘴受力大小,使其在合理的范围内;②在管道设计布置时要充分考虑其热位移,避免操作工况时管道和构架梁及斜撑相碰。
③为避免管道的轴向位移受到限制,导向支架不宜选用管卡的,应选用框式导向支架,且框式导向支架应避免管道因热位移过大而使管托脱离导向框。
2.2冷氢管道
①冷氢管道的介质操作温度不高,自身的热胀量不大,但反应器冷氢口的管嘴会随反应器的热胀而升高,为保证冷油管嘴法兰安全无泄漏,冷氢管道设计时应有足够的柔性并进行应力分析,在操作工况下容易脱空的位置设置弹簧支架。
②由于靠近冷氢注入口设备管嘴处温度比较高,冷氢管道等级一般以止回阀为界,氢气总管到止回阀前管道为碳钢,从止回阀到冷氢管嘴见管道为不锈钢。
为防止高温对止回阀前管道的影响,从止回阀到冷氢管嘴间管道一般不小于2m ,为节约材料也不宜过长。
3温度对应力分析的影响
不同工况的分析,由于加氢反应器设备本身及其管道具有高温、高压的特点,因此在正常工况下设备和管道会自身进行热膨胀,若不进行一定的热补偿,管道部分支撑可能会脱空,造成设备管嘴受力超限或管道局部应力增大,不利于管系及装置的安全运行,因此我们要对温度高的管道进行详尽的应力分析。
4结语
本文在构架平台设置,管道布置及应力分析等方面阐述了温度对反应器配管设计中的影响,熟练掌握这些内容能够避免出现设计错误,加快设计进度,并能够确保加氢装置的安全运行。
参考文献:
[1]张德江,王怀义.工艺管道安装设计手册第一篇中国石化出版社.
81。