变速箱电液比例换向系统
电液换档控制系统

DP-TCN变速箱电液动力换档控制系统传统工程机械的机械动力变速换档在结构上主要由液力变矩器、机械齿轮变速传动机构、手动变速换档机构组成。
今天,动力换档变速器已经发生了重大的变化。
自从1994年起,美国DP-TECNORD公司已开始生产动力换档变速箱的电液比例换档控制系统。
该公司具有电液比例换档控制的多项专利技术,根据各制造厂变速箱的控制原理和结构尺寸,设计、制造其相应的电子液压比例换档控制系统,对原手动换档变速箱进行电液比例控制换档的升级改造。
应用厂家有德国ZF,美国CASE,CLARK,CNH等。
一,电液动力换档系统组成:多动能双轴全方位换档控制手柄--可选,履带式工程车辆。
档位选择逻辑微处理机控制单元--完成如自动换档控制等功能。
离合器接合压力控微处理机制单元 --实现平稳接合过程。
离合器接合压力曲线设定与调整环境软件 --基于WINDOWS操作系统。
动力换档电液比例减压阀(一)JMF多动能双轴全方位换档控制手柄:该控制手柄分左手控制型和右手控制型两种,主要应用于履带车辆的控制。
前推(或后拉)动手柄可以改变行车方向,即向前推接通前进I档,向后拉接通倒车I档,中位为空档。
可根据要求控制的档位数从两种之中选其一。
一种是手柄正面有四个复位按钮的,四个按钮代表档位,可实现前进5档与后退5档,如要求R3时,档位选择逻辑单元可保证按下三档或其它档按钮时,都使系统均按三档执行。
另一种手柄正面有六个复位按钮代表前进6档,后退6档。
如选择R4时,档位选择逻辑单元也可保证按下四、五档或六档按钮时,系统均按倒四档执行。
该档位控制手柄可在手柄的前端装有油门增减控制开关。
需要油门增加时,按下油门增加按钮。
按一次,油门开度增加一个增量,持续按下该按钮则油门持续增加。
需要减少油门时,按下油门减少按钮,按一次,油门开度减少一个增量,持续按下则油门持续减少。
(二) 档位选择与离合器接合压力微处理控制单元对于性能要求较高的车辆控制,在要求实现自动换档、档位与工作装置联合控制以及档位、工作装置与发动机联合控制等情况下,就必须微处理机进行档位逻辑分析控制,这就需要微处理机档位选择逻辑控制单元完成。
电液变速箱的先进性

电液变速箱的先进性电液换档变速箱在发达国家已被广泛应用于推土机、压路机、装载机等工程机械,其变速箱内部的结构原理基本不变,只是在原变速阀前加一电液控制集成块(包括各电液比例阀、电磁换向阀、压力控制阀等和油路阀块)及CPU 控制单元,由操纵手柄来控制电液控制集成块并进一步控制变速阀实现换档的目地。
电液换档变速箱有以下结构及功能:1、离合器接合压力控制单元。
CPU中的离合器接合压力控制单元通过产生的档位信号控制电磁换向阀和比例控制阀,使离合器的压力按照预定的一条快速而又无冲击的档位结合曲线进行结合,从而使换档变的平稳,提高驾驶的舒适性和灵活性。
预定的结合特性曲线实际上是一条特定压力结合特性曲线,根据各档位不同工况特性,可对影响离合器接合时充油时间曲线的六种状态,从软件上进行调整以达到现场调试的最佳工作状态,例如:T1(快速充油时间),T2(快速充油完成初始低压维持时间),T3、T4、T5、T6(各种充油升压斜率时间)。
利用该软件可将初始现场调试的最佳参数存储在离合器接合压力控制单元的EPROM 中作为批量生产之用,是提高效率的有力工具。
2、可编程换档。
编程换档是指根据某一特定的作业对象,事先将档位的模式存储在控制单元中,这样的作业模式可以是:F1-R2,F2-R2,F1-R3和F1-R1等工作模式。
采用这种工作模式换档可以大幅度提高工作效率,减轻工人的作业强度。
3、强制换低档功能。
在负载突然增加的瞬间,操作人员只需按下旋转换档器的强制按钮或踩下换低档踏板,该系统即可自动完成行走减速,增加工作机构功率的程序。
4、档位状态显示装置。
显示器可与所有的档位控制手柄相匹配并显示进行逻辑处理后的当前档位状态,它显示档位、行驶方向、强制换低档是否工作。
显示的灯亮表示相应的档位。
5、操纵手柄为开关式。
前后推(或拉)动手柄可以改变行车方向,即向前推接通前进档,向后拉接通倒车档,中位为空档。
档位则是按纽或旋纽,减轻了操作者的劳动强度。
轮式挖掘机自动挡变速箱的原理及电液控制自动换挡系统介绍
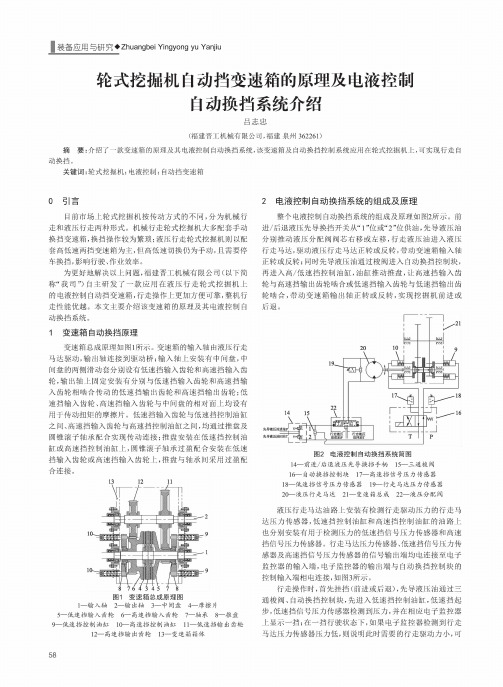
■装备应用与研究Yingyong yu Yanjiu轮式挖掘机自动挡变速箱的原理及电液控制自动换挡系统介绍吕志忠(福建晋工机械有限公司,福建泉州362261)摘要:介绍了一款变速箱的原理及其电液控制自动换挡系统,该变速箱及自动换挡控制系统应用在轮式挖掘机上,可实现行走自 动换挡。
关键词'轮式挖掘机;电液控制;自动挡变速箱〇引言目前市场上轮式挖掘机按传动方式的不同,分为机械行 走和液压行走两种形式。
机械行走轮式挖掘机大多配套手动 换挡变速箱,换挡操作较为繁琐;液压行走轮式挖掘机则以配 套高低速两挡变速箱为主,但高低速切换仍为手动,且需要停 换挡,行作。
为 以上 ,福建晋工机械有限公司(以下简称“我司”)自主研 了一款应用在液压行走轮式挖掘机上的电液控制自动挡变速箱,行走操作上加方可,机行 走 。
主要介绍该变速箱的原理及其电液控制自动换挡系统。
1变速箱自动换挡原理变速箱 原理 1。
变速箱的 液压行走动,动 Z上 有 ,的两 动套分 有低速挡 轮和高速挡轮,上 有分 低速挡 轮和高速挡轮 传动的低速挡 轮和高速挡 轮;低 速挡 轮 高速挡 轮 的上 有用传动扭矩的。
低速挡 轮与低速挡控制高速挡 轮 高速挡控制 ,及配实现传动Z在低速挡控制油高速挡控制 上,配 在低速挡 轮高速挡轮上,用配合连接。
图1变速箱总成原理图1一输入轴 2%输出轴 3%中间盘4一摩擦片5—低速挡输入齿轮6—高速挡输入齿轮7—轴承 8—推盘9一低速挡控制油缸 10 —高速挡控制油缸 11一低速挡输出齿轮12—高速挡输出齿轮13—变速箱箱体2电液控制自动换挡系统的组成及原理电液控制自动换挡系统的 及原理 2 。
前!液压 换挡 ”1””2”,液压油分 动液压分配 ,行走液压 液压行走 ,动液压行走 ,动变速箱z同液压 自动换挡控制,高/低速挡控制 ,动推盘,高速挡.齿轮高速挡轮 低速挡 轮与低速挡轮 ,动变速箱 ,实现挖掘机前进或。
051210电液比例换向阀

电液比例换向阀由前置级( 电液比例换向阀由前置级(电液比 例双向减压阀)和放大级( 例双向减压阀)和放大级(液动比 例双向节流阀)两部分组成。 例双向节流阀)两部分组成。 前置级由比例电磁铁控制双向减压 阀阀芯位移。 阀阀芯位移。当比例电磁铁输入电 流时,减压阀芯移动, 流时,减压阀芯移动,减压开口一 定,经阀口减压后得到稳定的控制 压力。 压力。 放大级由阀体、主阀芯、左右端盖、 放大级由阀体、主阀芯、左右端盖、 阻尼螺钉和弹簧等零件组成。 阻尼螺钉和弹簧等零件组成。控制 压力油经阻尼孔作用在主阀芯的端 面时, 面时,液压力将克服弹簧力使阀芯 移动,开启阀口,沟通油道。 移动,开启阀口,沟通油道。主阀 开口大小取决于输入电流的大小。 开口大小取决于输入电流的大小。 改变比例电磁铁的输入电流, 改变比例电磁铁的输入电流,不仅 可以改变阀的工作液流方向, 可以改变阀的工作液流方向,而且 可以控制阀口大小实现流量调节, 可以控制阀口大小实现流量调节, 即具有换向、节流复合功能。 即具有换向、节流复
电液转向器工作原理

电液转向器工作原理
电液转向器是一种采用电子控制单元(ECU)控制的转向助力系统,其工作原理如下:- 组成结构:由油箱、动力转向调节单元、电动泵、转向器、动力转向传感器等部件组成。
- 助力原理:与传统机械动力转向系统相同,但增加了电动转向泵。
- 控制方式:转向助力的大小由电子调节单元根据车辆行驶速度和转向角度计算得出,并通过控制电动液压泵的转速来实现。
在不转向时,电动转向泵关闭,以减少油耗。
正常情况下,电动转向泵的转速与车速成反比,以提供停车时的轻转向和高速行驶时的重而稳的手感。
与传统的机械液压转向动力系统相比,电液转向器能够降低约0.1-0.2L/100km的油耗。
电液比例控制后桥主动转向系统 标准

电液比例控制后桥主动转向系统标准1. 引言1.1 研究背景随着汽车工业的不断发展,人们对汽车性能和安全性能的要求也越来越高。
而且,随着城市交通流量的增加和道路拥堵的加剧,车辆操控性和转向灵活性也成为了人们关注的焦点。
传统的汽车转向系统主要依靠驾驶员的操纵来实现,但在某些特定的情况下,驾驶员的反应速度和操作技能可能无法满足对车辆操控性的要求。
开发一种能够提高车辆操控性和安全性能的转向系统成为了一个迫切的需求。
电液比例控制技术和桥主动转向系统的结合,可以有效地提高车辆的转向响应速度和稳定性,进一步提升车辆的操控性和安全性能。
探索电液比例控制后桥主动转向系统的设计和应用具有重要的实用价值和研究意义。
通过对这一领域的深入研究和探索,可以为汽车工业的发展和车辆安全性能的提升提供有力的支持。
1.2 研究意义通过研究电液比例控制后桥主动转向系统,可以实现车辆在转弯过程中后桥的主动转向,从而降低车辆的侧倾倾角,提高车辆的稳定性和安全性。
该系统还能够提高车辆的操控性能,使驾驶者更加轻松自如地驾驶车辆,提升驾驶体验。
研究电液比例控制后桥主动转向系统具有重要的意义,可以为汽车制造行业带来新的技术突破,推动汽车操控性能的提升,满足用户对驾驶体验需求的不断增长。
2. 正文2.1 电液比例控制技术电液比例控制技术是一种通过电子和液压联合控制的先进技术,广泛应用于汽车、机械设备等领域。
它基于电子控制单元(ECU)和液压执行单元(HCU)的协同工作,通过精确控制液压阀的开启和关闭来实现对液压系统的精准控制。
电液比例控制技术的优势在于其快速响应、精准控制和高效能力。
通过调节电子控制单元发送的电压信号,可以实现流量、压力等参数的精确控制,从而提高液压系统的工作效率和性能。
在汽车行业中,电液比例控制技术被广泛应用于制动系统、转向系统等关键部件中。
通过电液比例控制技术,汽车可以实现更加灵活、稳定的转向控制,提高行驶安全性和舒适性。
电液比例控制技术的发展为各个领域带来了更高效、更精准的控制方式,是现代控制领域的重要突破之一。
工程车辆变速器电液换挡控制系统研究
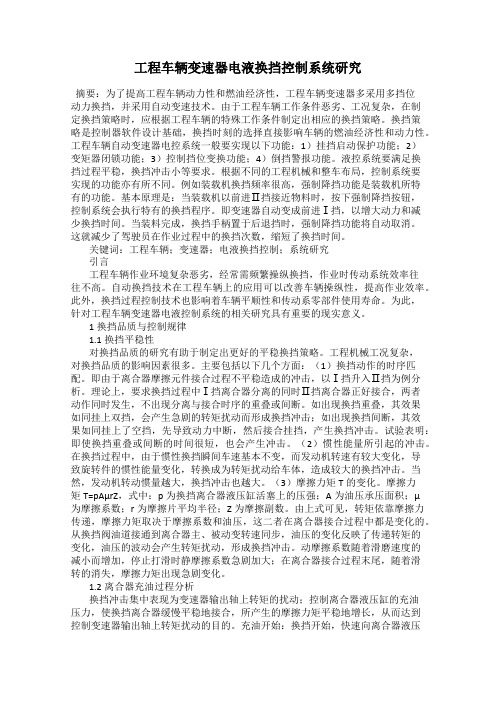
工程车辆变速器电液换挡控制系统研究摘要:为了提高工程车辆动力性和燃油经济性,工程车辆变速器多采用多挡位动力换挡,并采用自动变速技术。
由于工程车辆工作条件恶劣、工况复杂,在制定换挡策略时,应根据工程车辆的特殊工作条件制定出相应的换挡策略。
换挡策略是控制器软件设计基础,换挡时刻的选择直接影响车辆的燃油经济性和动力性。
工程车辆自动变速器电控系统一般要实现以下功能:1)挂挡启动保护功能;2)变矩器闭锁功能;3)控制挡位变换功能;4)倒挡警报功能。
液控系统要满足换挡过程平稳,换挡冲击小等要求。
根据不同的工程机械和整车布局,控制系统要实现的功能亦有所不同。
例如装载机换挡频率很高,强制降挡功能是装载机所特有的功能。
基本原理是:当装载机以前进Ⅱ挡接近物料时,按下强制降挡按钮,控制系统会执行特有的换挡程序。
即变速器自动变成前进Ⅰ挡,以增大动力和减少换挡时间。
当装料完成,换挡手柄置于后退挡时,强制降挡功能将自动取消。
这就减少了驾驶员在作业过程中的换挡次数,缩短了换挡时间。
关键词:工程车辆;变速器;电液换挡控制;系统研究引言工程车辆作业环境复杂恶劣,经常需频繁操纵换挡,作业时传动系统效率往往不高。
自动换挡技术在工程车辆上的应用可以改善车辆操纵性,提高作业效率。
此外,换挡过程控制技术也影响着车辆平顺性和传动系零部件使用寿命。
为此,针对工程车辆变速器电液控制系统的相关研究具有重要的现实意义。
1换挡品质与控制规律1.1换挡平稳性对换挡品质的研究有助于制定出更好的平稳换挡策略。
工程机械工况复杂,对换挡品质的影响因素很多。
主要包括以下几个方面:(1)换挡动作的时序匹配。
即由于离合器摩擦元件接合过程不平稳造成的冲击,以Ⅰ挡升入Ⅱ挡为例分析。
理论上,要求换挡过程中Ⅰ挡离合器分离的同时Ⅱ挡离合器正好接合,两者动作同时发生,不出现分离与接合时序的重叠或间断。
如出现换挡重叠,其效果如同挂上双挡,会产生急剧的转矩扰动而形成换挡冲击;如出现换挡间断,其效果如同挂上了空挡,先导致动力中断,然后接合挂挡,产生换挡冲击。
液力自动变速箱原理

液力自动变速箱原理液力自动变速箱是一种常见的汽车变速器类型,它通过液力传递动力和变速器来实现车辆的换挡。
液力自动变速箱的工作原理基于液力变矩器以及油压系统的控制。
液力变矩器是液力自动变速箱的核心组件之一。
它由一个外壳和三个主要的元件组成:泵轮、涡轮和涡轮蜗壳。
泵轮与发动机曲轴相连,涡轮与变速器输入轴相连,而涡轮蜗壳则连接泵轮和涡轮。
当发动机工作时,泵轮带动液体流动,产生液力。
液体通过涡轮蜗壳的引导,使涡轮转动。
这个过程中,发动机的动力被传递到涡轮上,实现了动力的传递。
液力变矩器的另一个重要功能是提供变速器的多个挡位。
液力变矩器内部还有一个液力离合器,它通过控制油压来实现换挡操作。
当车辆需要换挡时,液压系统会调整液压力,使液力离合器开合,从而实现不同挡位的换挡。
这种液力传递的方式,相比于手动变速器,更加平稳、顺畅。
液力自动变速箱的工作原理可以分为三个阶段:起步阶段、行驶阶段和换挡阶段。
在起步阶段,当车辆踩下油门时,发动机的动力通过液力变矩器传递到涡轮上,使车辆开始行驶。
由于液力传递的特性,车辆起步时的顿挫感较小,驾驶更加平稳。
在行驶阶段,液力变矩器会根据车速和负载的变化来调整液力的传递比例。
这样可以使发动机保持在高效工作区域,提高燃油利用率,并且根据驾驶需求提供合适的动力输出。
在换挡阶段,当车辆需要换挡时,液压系统会根据驾驶模式和车速来判断合适的挡位,并调整液力离合器的开合。
液力离合器的开合过程中,会产生一定的能量损失,但由于液力传递的特性,换挡过程仍然相对平稳。
液力自动变速箱的优点是换挡平稳、驾驶舒适,适用于城市驾驶和长途旅行。
然而,由于液力传递的特性,液力自动变速箱的燃油经济性相对较低。
因此,一些新型的变速器技术如双离合器变速箱和无级变速器逐渐得到应用。
液力自动变速箱通过液力传递和油压系统的控制来实现车辆的换挡操作。
它具有换挡平稳、驾驶舒适的优点,但相对燃油经济性较低。
随着汽车技术的不断发展,液力自动变速箱正在逐渐被新型变速器技术所取代。
比例换向阀工作原理
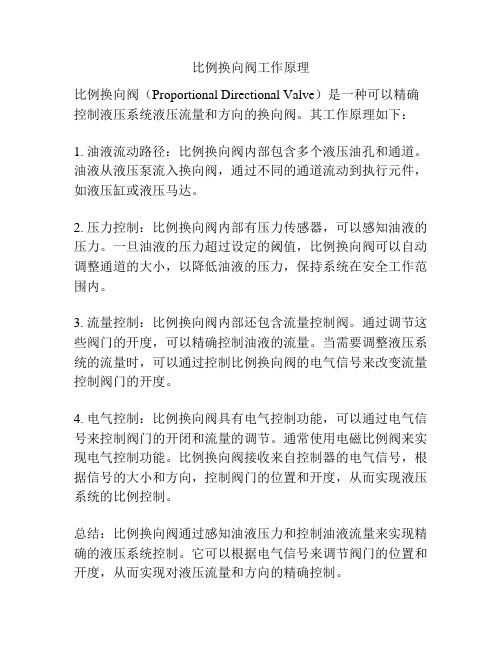
比例换向阀工作原理
比例换向阀(Proportional Directional Valve)是一种可以精确控制液压系统液压流量和方向的换向阀。
其工作原理如下:
1. 油液流动路径:比例换向阀内部包含多个液压油孔和通道。
油液从液压泵流入换向阀,通过不同的通道流动到执行元件,如液压缸或液压马达。
2. 压力控制:比例换向阀内部有压力传感器,可以感知油液的压力。
一旦油液的压力超过设定的阈值,比例换向阀可以自动调整通道的大小,以降低油液的压力,保持系统在安全工作范围内。
3. 流量控制:比例换向阀内部还包含流量控制阀。
通过调节这些阀门的开度,可以精确控制油液的流量。
当需要调整液压系统的流量时,可以通过控制比例换向阀的电气信号来改变流量控制阀门的开度。
4. 电气控制:比例换向阀具有电气控制功能,可以通过电气信号来控制阀门的开闭和流量的调节。
通常使用电磁比例阀来实现电气控制功能。
比例换向阀接收来自控制器的电气信号,根据信号的大小和方向,控制阀门的位置和开度,从而实现液压系统的比例控制。
总结:比例换向阀通过感知油液压力和控制油液流量来实现精确的液压系统控制。
它可以根据电气信号来调节阀门的位置和开度,从而实现对液压流量和方向的精确控制。
矿用车电液自动换挡电液系统样本

F5+R1动力换挡变速箱自动换档电气液压控制系统PBSS按键式自动换档系统技术条件一,设计参数:1.变速器各挡位传动比(变速箱厂家填写)挡位前进Ⅰ挡前进Ⅱ挡前进Ⅲ挡前进Ⅳ挡前进Ⅴ挡倒退挡主减速比传动比2,变速器各挡位离合器行程及容积(变速箱厂家填写):挡位 离合器行程mm 离合器容积mm^2前进档五档四档三档二档一档闭锁离合器4,相关参数(变速箱厂家填写):#1齿轮泵(主泵)流量:- /min,#2齿轮泵(润滑泵)流量:--L/min变矩器输出轴每转齿数:齿轮箱输出轴每转齿数:二,系统部件组成:(一)信号传感器(采集各种信号的传感器)(二)档位控制器-按键式档位控制器含OLED显示器(行驶变速档位,控制模式,发动机工况),(三)变速换档可编程微机控制器ECU(四)SERVO-ACTR发动机油门伺服驱动器(可选-配置电子油门电喷发动机无需此项)(五)悬挂式电子油门踏板(六) 变速换档阀块和压力调节阀块三,技术条件(一)信号传感器(采集各种信号的传感器)1)发动机油门位置传感器SERVO-ACTR(检测0-100%油门踏板的位移位置),2)涡轮转速传感器(监测变速箱涡轮端的转速),3)变速箱输出转速传感器(监测变速箱输出轴的转速)4)变速箱油温传感器 (100度报警,120度停机)5) 变速箱油位传感器(高位报警、低位报警)6)发动机转速传感器(二)档位控制器-按键式档位控制器1.1档位控制器-按键式档位控制器(CAN 总线,OLED状态信息显示板),换挡范围:R, N, D,4, 3, 2, 1按键式挡位控制器可以方便安装。
按下相关按键选择实现行车方向控制和停止,即:D自动挡,N为中位空档,R为倒车档。
按上、下箭头键可以选择换挡模式。
在停车状态下,按下MODE键可进入诊断菜单,档位范围如下:D(前进挡1//2-5档)4(4:自动挡1-4)3(3:自动挡1-3档)2(2:自动挡1-2档)1(1/M1:前进1档)R (倒档)N(空档)1.2 OLED状态信息显示板,显示器用来显示所选档位和当前接合档位,左侧SELECT栏显示选择档位模式:R, N, D,4, 3, 2, 1,右侧MONITOR栏显示当前离合器接合档位:1,2,3,4,5底部栏显示栏(12码)系统故障诊断模式、状态报警,故障代码表,详见见附件。
电液比例减压阀控换档系统控制策略研究

引 言 采用 电液 比例减压 阀的电液换 档系 统可 以灵 活 改变离合缸的升压规律 , 实现不同的换档过程 , 国 在 外的重型车辆上 已获得广泛的应用。我国也开始进 行 了有关 研究 _ 目前 主要 的控 制 方式 是 将一 个 离 1 1 。
忽 略诸如 过滤 器阻力 、 配合 间隙泄 露等 因素 , 建 立 该 阀的数学模 型 。
图 1控 制 换 档 系 统 原 理 图
1流 量方 程 )
先导 固定节 流 口 、 先导 球 阀 口 、 馈 节 流管 、 反 主
阀口、 减压阀出口、 传输管道流量方程( 1 R) 和缓冲器 节流口流量方程分别如式( )( ) 1一7 所示。其 中反馈 节流管和传输管路既考虑了其沿程阻力 ,也考虑了 其局 部阻力 。
.
1 电液 比例 减 压 阀控 离 合 缸
电液 比例减 压 阀控 离 合缸 原 理如 图 1 示 , 所 减 压 阀用 以控 制离合 缸 内压力 ,渐近关 闭缓 冲器 用 以
( 2 )
p ^ f f 一 {£ f _ I ’ f
( 3 )
吸收离合缸充油终点的压力冲击。
收稿 日期 :0 9 1— 0 20 — 0 1
— —
— —
式 中 , + —各 流量 , ; 口— m P —— 工作 油液 密度 ,gm ; k/ C —— 流量 系数 ;
2 阀控 换 档 系统 控 制策 略研 究
根据上述数学模型 , 利用 M t bS u n 建立 aa i l k l m i 系统仿真模型 , 对系统控制策略进行仿真研究。 设离 合缸处于缸起点处 由回程弹簧预压缩力决定 的起点 压力为 p , q 离合缸处于额宅行 程终点 由回 处, 程弹簧压 缩力决定的终点压力为 P。本文仿真系统起点压力 : 01MP , 点压力 02MP , . a终 . a液压缸 额定行 程 5 m。 m 1无 缓 冲 、 ) 两段 式控制 仿真 中摘去缓冲器部分。充油段 比例 阀指令 1 P, - M a 当缸 内压力达到 P 时立即开始升压段 , 3 即 比例阀指令立即下降到升压段起始值 ,然后沿斜坡 上升 , 图 2曲线 C所示。离合缸充油及建压过程 如
电液比例控制技术简介
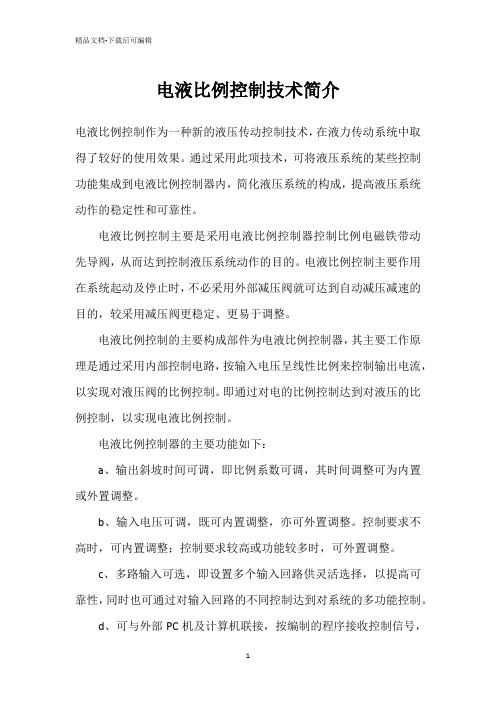
电液比例控制技术简介
电液比例控制作为一种新的液压传动控制技术,在液力传动系统中取得了较好的使用效果。
通过采用此项技术,可将液压系统的某些控制功能集成到电液比例控制器内,简化液压系统的构成,提高液压系统动作的稳定性和可靠性。
电液比例控制主要是采用电液比例控制器控制比例电磁铁带动先导阀,从而达到控制液压系统动作的目的。
电液比例控制主要作用在系统起动及停止时,不必采用外部减压阀就可达到自动减压减速的目的,较采用减压阀更稳定、更易于调整。
电液比例控制的主要构成部件为电液比例控制器,其主要工作原理是通过采用内部控制电路,按输入电压呈线性比例来控制输出电流,以实现对液压阀的比例控制。
即通过对电的比例控制达到对液压的比例控制,以实现电液比例控制。
电液比例控制器的主要功能如下:
a、输出斜坡时间可调,即比例系数可调,其时间调整可为内置或外置调整。
b、输入电压可调,既可内置调整,亦可外置调整。
控制要求不高时,可内置调整;控制要求较高或功能较多时,可外置调整。
c、多路输入可选,即设置多个输入回路供灵活选择,以提高可靠性,同时也可通过对输入回路的不同控制达到对系统的多功能控制。
d、可与外部PC机及计算机联接,按编制的程序接收控制信号,
执行程序功能。
e、采用标准插板,便于安装及与其它控制设备连接。
双辽发电厂翻车机系统ZDC型重车调车机牵车臂的液压控制回路经改造后采用VT3006BS30型比例控制器,避免了大臂在起落过程及中途停止时的冲击,取消了原装外部减压阀及减压阀控制曲线板,简化了系统,提高了稳定性和可靠性。
运行实践证明,此项技术先进、可靠,具有推广使用价值。
比例换向阀的工作原理

比例换向阀的工作原理
比例换向阀是一种用于控制液压系统中液压执行元件运动方向的设备。
它通过改变阀芯的位置来实现液体流向的转换。
比例换向阀的主要部件包括活塞、弹簧、阀芯和阀体等。
当液压油进入活塞的一侧时,活塞会开始移动。
弹簧通过对活塞施加力来保持阀芯的初始位置。
当阀芯的位置发生变化时,液压油的流向也会随之改变。
在初始状态下,阀芯处于中性位置,液压油可以流向两个方向。
通过改变阀芯的位置,比例换向阀可以将液压油引导到所需的方向。
例如,当活塞移动到阀芯的一侧时,液压油会被引导到一个输出通道,从而推动液压执行元件向一个方向运动。
当活塞移动到阀芯的另一侧时,液压油会被引导到另一个输出通道,从而改变液压执行元件的运动方向。
比例换向阀通过在液压系统中控制液压油的流向和流量来实现对液压执行元件运动的精确控制。
它广泛应用于各种液压系统中,如机械设备、工程机械和汽车等。
电液式自动变速器的组成与基本工作原理

电液式自动变速器的组成与基本工作原理
电液式自动变速器是一种高级的汽车变速器,其组成部分相对于
手动变速器更加复杂。
但是,其基本原理相对简单。
电液式自动变速器由液压系统、电控系统和机械系统三部分组成。
液压系统主要由油泵、离合器、制动器、减速器和行星齿轮等部
分组成,其作用是针对不同车速和转速进行液压传递,从而实现车辆
的换挡操作。
电控系统则由控制芯片、传感器、阀门等电子部分组成,对自动
变速器进行控制和监测,并对车辆进行软件调节。
机械系统则是液压系统和电控系统的执行系统,主要由齿轮和联
轴器等部分组成,使变速器异步运行,实现汽车的加速和刹车等系统
操作。
电液式自动变速器的基本工作原理是通过液体传递信号,由电控
系统实时监测车辆的运行状态,从而相应地调整液压传递系统,使得
车辆顺畅地进行换挡操作。
当车辆加速时,液压泵通过齿轮将动力转化为流体动力能,并将
其传递到离合器。
此时,电控芯片通过传感器即时检测车辆的转速和
行驶状态,并根据需要调整液压传递系统,使得离合器自动切换到相
应的增速档位。
最终实现变速器的换挡操作。
总的来说,电液式自动变速器在实现变速操作方面具有许多优势,可以帮助驾驶员改善驾驶体验,同时也更加安全可靠。
当然,对于电
液式自动变速器的优点与问题,我们还需要加以深入的了解和评估。
电液比例换向阀工作原理

可以构成直动式比列换向阀。由于使用比例电磁铁,阀
芯不仅可以换位,而且换位的行程可以连续或按比例地 变化。
因此,联通油口间的通流面积也可以连续或按比例
地变化,所以比列换向阀不仅能控制执行元件的运动方
向,还可以控制它运动的速度。
比例电磁铁前端附有位移传感器,因此这种比例电 磁铁称为行程控制比例电磁铁,位移传感器能准确测定
电磁铁的行程,并向放大器发出电反馈信号。电放大器
将输入信号与反馈信号加以比较后,再向电磁铁发出纠 正信号来补偿误差。
简述变速器换向的原理

简述变速器换向的原理变速器是汽车传动系统中的重要部件,它的主要功能是将发动机提供的动力通过不同的齿轮组合转化为合适的扭矩和速度输出到车轮上。
而在行驶过程中,车辆需要改变行进方向,这就需要变速器进行换向操作。
换向是指在行驶过程中改变车辆行进方向的操作。
在传统的手动变速器中,换向主要是通过操作离合器和换挡杆来完成的。
当驾驶员需要换向时,他首先会踩下离合器,将发动机与变速器分离。
接下来,他会将换挡杆从当前的齿轮位置移到目标齿轮位置,然后松开离合器,使得发动机的动力能够传递到目标齿轮上,从而实现车辆的换向操作。
在自动变速器中,换向的操作相对更为复杂,但原理基本相同。
自动变速器采用了液力传动和离合器系统来实现换向。
液力传动是指通过液压作用将发动机的动力传递到齿轮上,而离合器系统则是用来控制液力传动的连接和分离。
在自动变速器中,液力传动的核心是液力变矩器。
液力变矩器由涡轮、泵和涡轮叶轮构成,通过液压的作用将动力从发动机传递到变速器。
当驾驶员需要换向时,自动变速器会根据当前的行驶状态和驾驶员的操作信号,控制液力变矩器的液压系统,从而实现齿轮的换向。
具体来说,当驾驶员将换挡杆从D挡移到R挡时,自动变速器会控制液力变矩器的液压系统,使得液力变矩器的涡轮与泵之间的连接断开,涡轮与涡轮叶轮之间的液压传动停止。
这样一来,涡轮不再受到液压的驱动,车辆的行进方向也就发生了改变。
除了离合器和液力变矩器,自动变速器中还有其他一些重要的部件,如换挡阀和控制单元。
换挡阀负责控制液力传动的连接和分离,根据驾驶员的操作信号和车辆的行驶状态来判断何时进行换挡操作;控制单元则是变速器的大脑,负责接收并处理来自传感器的信号,并向换挡阀发送相应的指令,从而实现换挡的精准控制。
变速器换向的原理是通过控制离合器、液力变矩器、换挡阀和控制单元等部件,将发动机的动力传递到目标齿轮上,从而改变车辆的行进方向。
无论是手动变速器还是自动变速器,都是通过这些部件的协同工作,实现车辆换向操作的。
基于AVR的电液比例换档控制器设计

图2控制器硬件结构图图1电液比例换档系统结构收稿日期:2009-10-16作者简介:杨庆俊,博士,副教授。
中图分类号:TH137文献标识码:A 文章编号:1672-8904(2009)06-0028-003基于AVR 的电液比例换档控制器设计杨庆俊1,2顾宏韬2向东1吕庆军2(1.哈尔滨工业大学机电学院哈尔滨150080;2中国北方车辆研究所车辆传动国家重点实验室北京100072)引言目前国内使用的动力换档控制系统通常采用液压平稳结合阀进行换档控制,操纵件结合特性不易调节、控制精度低、控制特性单一,以及在切换时流量突变会引起液压冲击,对系统的平稳性和可靠性很大。
因此部分研究者在电液换档系统中使用了电液比例减压阀。
为了降低液压冲击,通常采用的方法是在离合缸未达到行程终点时,提前将充油阶段的指令大幅降低[1,2]。
而提前量则由实验确定或在线根据实际冲击大小迭代调节。
由于系统工作条件的变化,如油温变化、系统供油压力变化等,使得这个提前量很难确定,因此难以精确控制。
为此,本文研制开发了基于AVR 的电液比例换档控制器,可直接装载在车辆上,通过压力和转速的反馈信号来决定各控制段的切换和比例阀的调节。
1电液比例换档系统总体方案基于AVR 的电液比例换档系统结构图如图1所示。
系统由控制器、信号传感器、电液比例减压阀及电磁阀组成。
测量信号包括12个压力信号、3个转速信号及温度信号;系统控制算法存储在ECU 中,通过反馈信号来切换电磁阀的开合以及调节电液比例阀的输出量;人机交换通过LCD 和键盘实现;上下位机的通信通过RS232通信接口完成。
2控制器硬件设计系统以AVR 系列单片机ATMEGA64为核心创建了AD 采样电路、PWM 输出电路、扩展存储电路、键盘输入电路、LCD 显示电路、DO 输出电路以及RS232通信电路。
其结构如图2所示。
由于单片机I/O 口资源有限,因此对很多I/O 口进行了复用,使用573芯片对复用的I/O 口进行了索存隔离。
叉车用电液自动换挡变速器
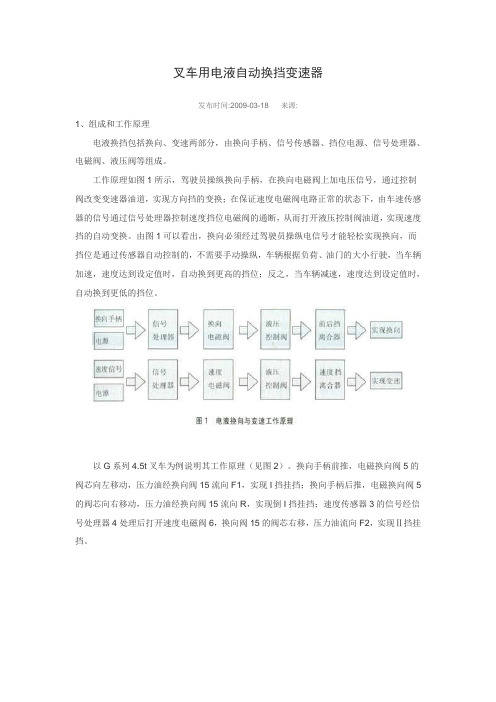
叉车用电液自动换挡变速器发布时间:2009-03-18 来源:1、组成和工作原理电液换挡包括换向、变速两部分,由换向手柄、信号传感器、挡位电源、信号处理器、电磁阀、液压阀等组成。
工作原理如图1所示,驾驶员操纵换向手柄,在换向电磁阀上加电压信号,通过控制阀改变变速器油道,实现方向挡的变换;在保证速度电磁阀电路正常的状态下,由车速传感器的信号通过信号处理器控制速度挡位电磁阀的通断,从而打开液压控制阀油道,实现速度挡的自动变换。
由图1可以看出,换向必须经过驾驶员操纵电信号才能轻松实现换向,而挡位是通过传感器自动控制的,不需要手动操纵,车辆根据负荷、油门的大小行驶,当车辆加速,速度达到设定值时,自动换到更高的挡位;反之,当车辆减速,速度达到设定值时,自动换到更低的挡位。
以G系列4.5t叉车为例说明其工作原理(见图2)。
换向手柄前推,电磁换向阀5的阀芯向左移动,压力油经换向阀15流向F1,实现I挡挂挡;换向手柄后推,电磁换向阀5的阀芯向右移动,压力油经换向阀15流向R,实现倒I挡挂挡;速度传感器3的信号经信号处理器4处理后打开速度电磁阀6,换向阀15的阀芯右移,压力油流向F2,实现Ⅱ挡挂挡。
2、特点分析叉车作为短距离搬运机械,挡位较少,变速控制精度不高,在某些特定的工况下不能满足使用要求。
例如,下坡时,叉车可能会自动变速到高速挡,爬坡时,会频繁变速。
此外,挡位手柄应具备空挡保护、换向、变速、高速挡锁定的功能;电液阀应当耐高温、运动灵活无卡阻、体积小。
油液的污染度要求高,须经10μm滤网过滤;换挡要平稳,低换高挡或高换低挡要有合适的速度差,否则会造成频繁换挡,不仅舒适性差,而且影响离合器、电磁阀等元件的使用寿命。
使用电液自动换挡变速器可自动控制速度升降。
例如G系列4.5t叉车I挡速度达到9km/h时自动升挡,Ⅱ挡速度降到6km/h时自动降挡。
操纵机构布置在转向盘旁,操作方便,控制电信号容易。
使用中需注意电磁阀无电时可能是保险丝损坏、线接头松动,可通过更换保险丝或重接线头解决;信号传递不畅时可能是传感器松动、间隙过大,可通过调整间隙解决;电磁阀被杂物卡阻引起无挡位时,简单清洗即可解决;信号处理器出现故障时,需要专业人员才能维修,但也是有一个最简单临时处理办法,即把电压信号修理器直接与最低挡电磁阀连接,让该电磁阀常闭,以保证车辆以最低挡开回维修站。
电控液力自动变速器的组成
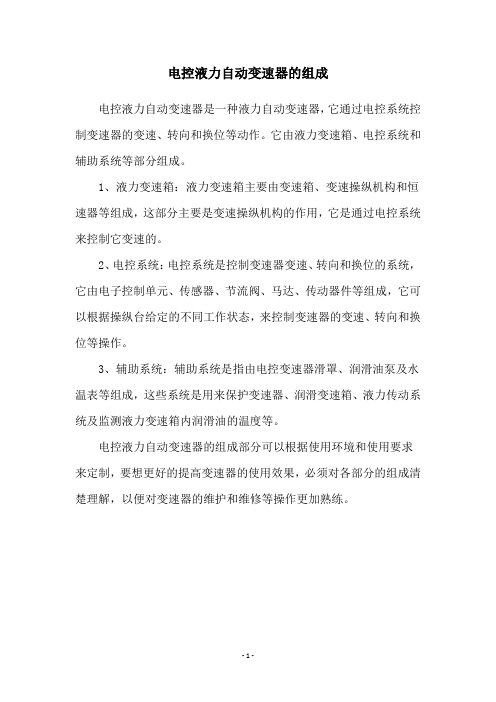
电控液力自动变速器的组成
电控液力自动变速器是一种液力自动变速器,它通过电控系统控制变速器的变速、转向和换位等动作。
它由液力变速箱、电控系统和辅助系统等部分组成。
1、液力变速箱:液力变速箱主要由变速箱、变速操纵机构和恒速器等组成,这部分主要是变速操纵机构的作用,它是通过电控系统来控制它变速的。
2、电控系统:电控系统是控制变速器变速、转向和换位的系统,它由电子控制单元、传感器、节流阀、马达、传动器件等组成,它可以根据操纵台给定的不同工作状态,来控制变速器的变速、转向和换位等操作。
3、辅助系统:辅助系统是指由电控变速器滑罩、润滑油泵及水温表等组成,这些系统是用来保护变速器、润滑变速箱、液力传动系统及监测液力变速箱内润滑油的温度等。
电控液力自动变速器的组成部分可以根据使用环境和使用要求来定制,要想更好的提高变速器的使用效果,必须对各部分的组成清楚理解,以便对变速器的维护和维修等操作更加熟练。
- 1 -。
工程机械变速箱电液控制系统分析
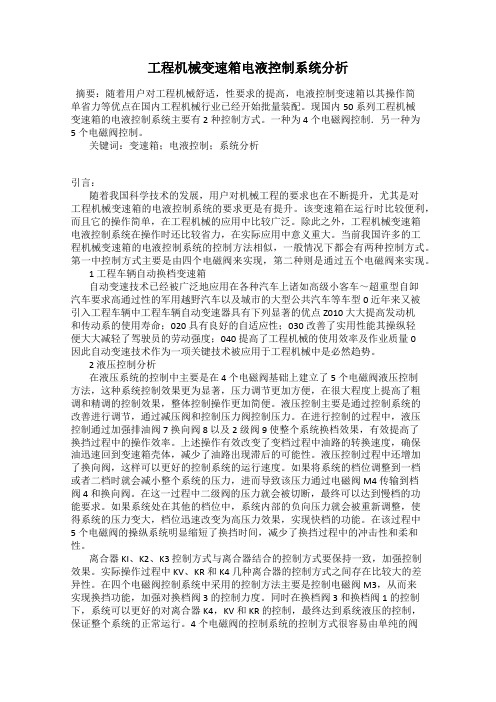
工程机械变速箱电液控制系统分析摘要:随着用户对工程机械舒适,性要求的提高,电液控制变速箱以其操作简单省力等优点在国内工程机械行业已经开始批量装配。
现国内 50 系列工程机械变速箱的电液控制系统主要有 2种控制方式。
一种为 4 个电磁阀控制.另一种为5 个电磁阀控制。
关键词:变速箱;电液控制;系统分析引言:随着我国科学技术的发展,用户对机械工程的要求也在不断提升,尤其是对工程机械变速箱的电液控制系统的要求更是有提升。
该变速箱在运行时比较便利,而且它的操作简单,在工程机械的应用中比较广泛。
除此之外,工程机械变速箱电液控制系统在操作时还比较省力,在实际应用中意义重大。
当前我国许多的工程机械变速箱的电液控制系统的控制方法相似,一般情况下都会有两种控制方式。
第一中控制方式主要是由四个电磁阀来实现,第二种则是通过五个电磁阀来实现。
1 工程车辆自动换档变速箱自动变速技术已经被广泛地应用在各种汽车上诸如高级小客车~超重型自卸汽车要求高通过性的军用越野汽车以及城市的大型公共汽车等车型 0 近年来又被引入工程车辆中工程车辆自动变速器具有下列显著的优点 Z010 大大提高发动机和传动系的使用寿命;020 具有良好的自适应性;030 改善了实用性能其操纵轻便大大减轻了驾驶员的劳动强度;040 提高了工程机械的使用效率及作业质量 0因此自动变速技术作为一项关键技术被应用于工程机械中是必然趋势。
2 液压控制分析在液压系统的控制中主要是在 4 个电磁阀基础上建立了 5 个电磁阀液压控制方法,这种系统控制效果更为显著,压力调节更加方便,在很大程度上提高了粗调和精调的控制效果,整体控制操作更加简便。
液压控制主要是通过控制系统的改善进行调节,通过减压阀和控制压力阀控制压力。
在进行控制的过程中,液压控制通过加强排油阀 7 换向阀 8 以及 2 级阀 9 使整个系统换档效果,有效提高了换挡过程中的操作效率。
上述操作有效改变了变档过程中油路的转换速度,确保油迅速回到变速箱壳体,减少了油路出现滞后的可能性。
- 1、下载文档前请自行甄别文档内容的完整性,平台不提供额外的编辑、内容补充、找答案等附加服务。
- 2、"仅部分预览"的文档,不可在线预览部分如存在完整性等问题,可反馈申请退款(可完整预览的文档不适用该条件!)。
- 3、如文档侵犯您的权益,请联系客服反馈,我们会尽快为您处理(人工客服工作时间:9:00-18:30)。
传统工程机械的动力变速换档系统是由液力变矩器、机械齿轮变速传动机构、手动变速换档机构组成。
今天,原机械动力换档变速系统逐步由电液一体化动力换挡系统取而代之。
美国
DP-TCN公司是生产变速箱电液比例自动换档控制系统的专业厂家,具有电液动力换档的多项专利技术。
DP-TCN的电液换档控制系统使重型动力机械的换档变得简单、轻巧,提高了整车工作效率,降低了操作人员的劳动强度。
该系统能使满足驾驶员的快速反应,适应外界环境的变化,是对传统变速箱进行升级改造的低成本、高技术方案。
电液动力换挡系统可以调整离合器接合压力曲线对离合器实现快速的软接合控制换档功能。
采用该电液自动换档控制系统可使重型工程机械的操作像"自动波"变速系统一样舒适、灵活。
DP-TCN公司可生产各种各种低压先导开关换挡阀(2位2通,2位3通,2位4通)和先导驱动比例减压阀IP-PRZ整体插装阀,EG-PRZ, EV-PRZ螺纹插装阀,可根据各制造厂商变速箱的控制原理和结构尺寸,来设计和制造其各种电液一体化动力换档控制系统,对原机械换挡变速箱进行电液一体化的换挡技术升级更新。
国内外应用厂家有ZF,CASE,CLARK,CNH,山推,一拖等。
电液换挡系统主要参数:
最大比例流量:0-4/28/30/35/50升,最大比例压力:0-25/30 Bar,
最大换挡流量:0-6.5/9/18/23/50 升,最大工作压力:50/70 Bar,
电气参数:
电源:12/24VDC,
PWM脉宽放大电流:250-900/1800 mA,
离合减压响应时间:30-80ms,
变速箱换挡范围:F3/F3,F4/R4等。
变速箱电液动力换档系统(POWER SHIFT)部件组成:
B, 多动能双轴全方位换档控制手柄--可选,履带式工程车辆。
MFLD, 动力换档电液比例减压阀,电液动力换挡阀块(TE-RVP高响应低压溢流阀,
RPP-T059先导电液比例减压阀,HT-S3A 2位3通先导电磁换挡阀)
A, MPC4-PS-H电子换挡控制器--完成换档控制、实现离合器平稳接合。
D, MPC4-PS电子控制器输入/输出接口插头及信号电缆。
C, MPC4-PS电子控制器压力曲线设定与调整软件 -- 基于WINDOWS操作系统。
(一)JMF-DB 多动能双轴全方位换档控制手柄:
型号:JMF-DB-F4R4, JMF-DB-F6R4,
该控制手柄分左/右手控制型,主要应用于履带车辆的控制。
前推(或后拉)
动手柄可以改变行车方向,即向前推接通前进I档,向后拉接通倒车I档,中
位为空档。
可根据要求控制的档位数从两种之中选其一。
一种是手柄正面有
四个复位按钮的,四个按钮代表档位,可实现前进5档与后退5档,如要求
R3时,档位选择逻辑单元可保证按下三档或其它档按钮时,都使系统均按三
档执行。
另一种手柄正面有六个复位按钮代表前进6档,后退6档。
如选择
R4时,档位选择逻辑单元也可保证按下四、五档或六档按钮时,系统均按倒
四档执行。
可选项:
1,电子油门控制:该档位控制手柄可在手柄的前端装有油门增减控制开关。
需要油门增加时,按下油门增加按钮。
按一次,油门开度增加一个增量,持续按下该按钮则油门持续增加。
需要减少油门时,按下油门减少按钮,按一次,油门开度减少一个增量,持续按下则油门持续减少。
2,KD强制降低档功能:在负载突然增加的瞬间,操作人员只需按下换挡器的强制按钮或踩下换低档踏板,该系统即可自动完成从高
档到低档的行走减速,防止发动机突然
熄火。
(二) MPC4-PS-H动力换挡电子控制器
型号:MPC4-PS-H
当接到挡位控制手柄的挡位电子信号时,电子控制器通过程序控制,选择最佳的接合曲线,根据控制器设定的程序,控制减压阀和相应挡位电磁阀,实现换挡离合器的柔性接合、离合过程。
主要特点:
1、柔性换挡功能:电子控制器根据换挡手柄产生的某一档位信号输出指令,启动相应的挡位电磁换向阀和比例减压阀,使相应离合器按照预定的压力曲线实现软结合。
该压力曲线存储在电子控制器的EPROM中,控制器可根据各档位指令,调用相应挡位曲线,实现快速而有无冲击的档位切换。
2、空挡连锁保护:发动机在空挡时才能启动。
3、直接换向功能:对前进I挡和II挡可直接挂入相应的挡位。
4、误操作容错功能:若同时按下2个或多个挡位按键时,只有最低档位信号可被触发。
5、刹车电子脱挡功能:通常在刹车踏板下安装一限位开关。
踩刹车时触发的限位信号启动空挡控制元件。
6、任选匀速升挡功能:当车辆处于低速(1挡)状态时,容许直接按下高速档键,例如3挡或4挡,电子控制器自动按照2-3挡或2-3-4挡的顺序实现匀速升挡,反之也是一样。
当车辆处于高速挡(3/4挡)状态时,容许直接按下低速档键,例如1挡或2挡,电子控制器自动按照4-3-2挡、或4-3-2-1挡的顺序实现匀速降挡。
7、失效保护功能:当发生线路断开,反向短路,负荷过载情况,控制器断开所有输出信号,转入空挡状态。
(三)动力换挡接合曲线设定与调整软件
DP-TECNORD公司为方便各厂家对于不同规格离合器的压力曲线的设定调整,开发了如下图所示的换挡离合器接合压力设定软件,该软件可以对离合器接合各时刻的压力进行设定与调整。
此软件在计算机上通过WINDOWS环境运行,并可将若干离合器的验证曲线传送到MPC4-PS 编程控制器的EPROM中保存。
使用该软件可对影响离合器接合时间至充油时间曲线的多种状态进行调整以达到工况要求的最佳工作状态,根据不同的挡位设置不同的曲线。
一般存储有6-12条曲线(F3/R3为6条,F6/R6为12条)。
各曲线的调整点可根据各种设备的容积参数及精度为6-12点,例如:T1(快速充油时间),T2(快速充油完成初始低压维持时间),
T3、T4、T5、T6-T12(各时间段充油升压斜率时间)。
利用该软件可将初始现场调试的最佳参数存储作为批量生产之用,是提高生产效率的有力工具。
(四)DP TCN比例减压阀和电
液换挡控制阀组
IP-PRZ-59带零位偏置的先导比
例控制减压阀工作原理:
比例减压阀有三个油口,P进油
口,RP控制口,T回油口:
1、比例阀线圈不通电时,控制
口的油通过主阀芯上的反馈节
流孔进入弹簧腔,与弹簧共同作
用,将阀芯推到最上端。
主阀芯
处于封死状态,P口和RP控制
口不相通。
2、P口少量的先导供油通过主
阀芯中央油孔,经过滤器,从主
阀芯上方的先导油节流孔流出,
通过常开的先导球阀直接回油。
3、当比例阀线圈通入PWM电流信号时,衔铁柱塞产生一个与电流成正比的向下的推力,作用在推杆和定位球阀上,通过限制先导回油逐渐建立起球阀和主阀芯间先导腔的压力。
限压:先导油须克服球阀的压力,将球阀顶开,才能流回油箱。
建压:随着线圈电流增加,作用在球阀上的力增加,主阀芯上端的油压相应升高。
该油压克服弹簧力将主阀芯向下推,进油口和控制口相通,先导油经P口和RP控制口流入离合器摩擦片的活塞腔。
4、同时,控制口离合器摩擦片的活塞腔的先导油经主阀芯上的反馈节流孔进入弹簧腔,作用于主阀芯下端,将主阀芯向上推,最终上下压力一致,阀芯处于平衡状态。
当阀线圈中的电流变化时,主阀芯上腔的油压变化,阀芯下腔的压力自动做相应的调整,最终使阀芯处于平衡状态。
阀,适用于ZF, CASE, CNH等变速箱电液
动力换挡阀组。
MPC4-PS编程控制器输出的PWM放大信
号来驱动比例电磁线圈,从而带动减压阀
内部阀芯的运动。
阀的输出压力与阀线圈
的PWM电流信号大小成正比,响应时间
50-80ms, 可用控制器对其压力曲线进
行调整。
当阀的控制线圈断电时,阀的入
口P关闭,工作油口RP通过回油口回油
箱。
当线圈得电,比例电流的增加,工作
油口输出油压也成比例的增加,从而实现
离合器摩擦片的软结合。
该阀采取输出油
压反馈方式稳定工作油口压力,使之不受
输入压力影响。
右图为DP-TCN比例减压阀比例减压阀特
性曲线:
A, MPC4-PS控制器控制电流曲线(%)
B, 离合器充油、柔性接合流量曲线(L/min)
C, 离合器充油、柔性接合压力曲线(bar)
动力换档变速箱中的液压集成块中的液压阀采用DP公司动力换挡专用的的螺纹插装阀或整体插装阀,其液压回路根据各不同生产商离合器的个数和流量略有差异,对于"前进5/后退3"的变速箱其液压原理如下图,包括RPP-T059电液比例减压阀、HT-S3A 2位3通电磁换向阀和TE-RVP机械式溢流阀。
HT-S3A是先导驱动电磁换向阀(50bar),其低压大流量的特点专用于电液动力换挡系统。
TE-RVP是动力换挡系统专用的机械式低压高响应溢流阀(50 bar)。