邯钢热轧线精轧区域速度控制优化与实践
邯钢X70管线钢热轧板卷的生产实践

K e or s: p — wie se l ot— r l d s e oi;pr d to yW d pie r te ;h ole he tc l o uci n;p a tc r c ie
1
前 言
X 0管线 钢生 产 工 艺 流 程 为 : 水 预 处 理 一 转 7 铁 炉一 L F炉一 R H炉一 连铸 一 板坯 清理一 加 热炉一 除 磷、 定宽 一22 0mm 热连 轧机 组一 层 流冷 却一 卷 取 5 一性 能 检验一 入 库 。
线钢 。X 0管 线钢 化学成 分 的设计 思 路是 : 7 ( ) 是 钢 中最 经 济 有 效 的 强 化 元 素 , 显 著 1C 但 恶化 钢 的韧性 和 焊 接 性 能 , 目前 高 级别 管 线 钢 的开
发都 采 用低碳 设计 。
抗腐 蚀 性能 等方 面 的高标 准要 求使 其成 为油 气 长输
nq eCe tr iu ne ,Ha d n I na d S elCo a y,He e rn a d Se lGru ,Ha d n ,He e ,0 6 1 n a r n te mp n o b iIo n te o p na b i 5 0 5)
A b ta t I si tod e he p oc sde i n a o uci n o t—r le h e oi o sr c : ti n r uc d t r es sg nd pr d to fho - ol d s e tc l fX70 pi pe— 。wie se l r te i a e 1 Th r lm fltl o y ed sr ng h i n l z d a m p ov d. n H n Ste . e p ob e o it lw i l te t sa a y e nd i r e e
邯钢2250热轧生产线步进梁加热炉优化
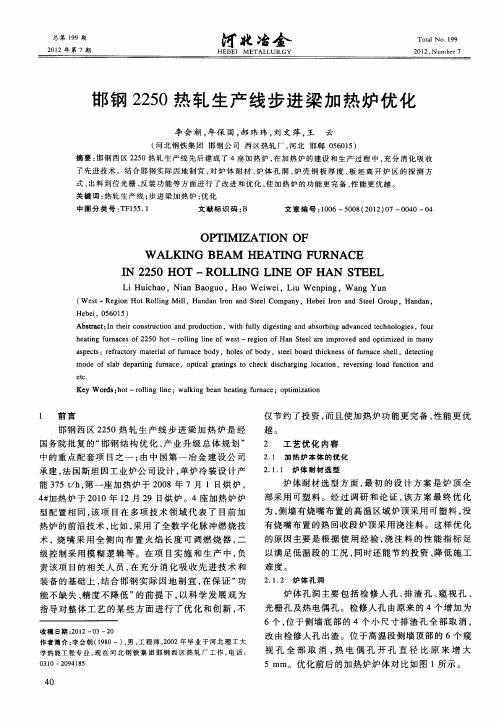
型配 置相 同 , 项 目在 多 项 技术 领 域 代 表 了 目前 加 该 热炉 的前沿 技术 , 比如 , 采用 了全 数字化 脉 冲燃烧 技
术 , 嘴 采 用 全侧 向布 置火 焰 长 度 可调 燃 烧 器 , 烧 二
为, 侧墙 有烧 嘴布置 的高 温 区域 炉顶 采用 可塑 料 , 没
关 键 词 : 轧 生 产线 ; 进 梁 加 热 炉 ; 化 热 步 优
热轧高强带钢板型控制与优化

热轧高强带钢板型控制与优化摘要:随着热轧工艺设备和模型系统的升级,热轧带钢板型问题得到了优化。
下游用户质量意识的不断提高和产能过剩等客观条件,用户对热轧带钢板型的要求越来越严格。
存在两个主要问题:带材沿长度方向平直度的一致性和带材楔形波动性。
这两个问题对用户的焊接工艺和生产效率有很大影响,规格越薄要求越严。
邯钢2250mm热轧生产线2.5mm以下薄带钢比例超过35%,对板型控制的稳定性提出了新要求。
通过长期的生产跟踪和优化,形成了较为完善的CVC联合弯辊加AGC功能的精确控制策略。
通过流程的优化和自动模型控制技术,带钢厚度、楔形和凸度等命中率显著改善,2.5mm以下高强薄规格在张力作用下实现稳定轧制。
关键词:热轧;高强钢板型;控制技术;优化引言中国的粗钢产量居世界第一,在钢铁生产过程中,热轧带钢的生产是一个重要的环节。
大多数钢板只采用热轧工艺生产,因此热轧在冶金工业中占有非常重要的地位,要加快从钢铁大国向钢铁强国转变,必须加快结构调整。
加热、粗轧、精轧和层流冷却工艺控制系统是热轧的重要组成部分。
系统的稳定性和计算精度直接关系到整个机组的各项板型技术指标。
用户对产品质量的要求也在不断提高。
因此,热轧过程控制系统和模型的开发和改进是一个重要的研究课题,具有重要的理论研究和实际应用价值。
1热轧带钢板型的控制技术应用在带钢生产中,当高强带钢内部的残余应力足够大时,带钢开卷后会发生侧弯、单边浪、双边浪和中间浪等翘曲现象。
带钢的翘曲度与宽度和厚度有关。
带材越薄越宽,生产中越容易发生翘曲。
目前市场对热带材的需求既宽又薄,出现以热代冷的趋势,因此良好的板型控制非常重要。
控制热轧高强带钢板型可采取以下技术措施:1.1合理的换辊制度及时更换轧辊是避免过度磨损、改善板型的有效方法。
应根据轧制牌号和规格选择合理的换辊周期,在轧辊表面发生恶化前更换。
注意观察下机辊面粗糙度,测量下机辊面温度。
如果辊面高温且磨损严重不均,应优化计划结构与轧制长度,以免影响带钢的浪形及凸度控制。
邯钢mm热轧生产线轧制节奏的分析及优化

邯钢mm热轧生产线轧制节奏的分析及优化邯钢mm热轧生产线作为中国钢铁厂商之一,一直致力于提高生产效率和产品质量。
热轧生产线是邯钢mm主要的生产部门之一,也是钢材生产的核心流程之一。
但是,由于生产条件和工艺的限制,热轧生产线轧制节奏的分析和优化变得尤为重要。
本文将对邯钢mm热轧生产线的轧制节奏进行分析,并提出一些优化建议。
一、热轧生产线轧制节奏分析1.生产线概述邯钢mm热轧生产线主要生产各种规格的铸坯和钢材,主要设备包括鼻架、四辊轧机、热剪机、冷卷机等。
该生产线按照生产流程将铸坯加工成钢材。
2.节奏分析邯钢mm热轧生产线轧制节奏的优化主要是基于四辊轧机的节奏进行分析和改进。
四辊轧机是热轧生产线的核心设备,负责对钢坯进行轧制、整形和调整。
其轧制节奏对整个生产线的生产率和质量起着至关重要的作用。
在实际生产中,四辊轧机的轧制节奏与钢坯的温度、尺寸、宽度、厚度、材质和轧制工艺等因素密切相关。
在轧制过程中,四辊轧机的辊筒在高速旋转的同时,将钢坯进行成型和调整,使其得以达到设计要求。
由于钢坯的物理特性复杂,加工过程中易受外界因素的影响,四辊轧机的轧制节奏需要按照具体情况进行调整,以保证生产线的生产效率和产品质量。
在实际生产中,邯钢mm热轧生产线的轧制节奏主要表现在以下几个方面:(1)辊轴转速和逆向转速调整:辊轴转速和逆向转速决定了钢材的厚度和宽度。
在实际生产中,辊轴转速和逆向转速需要根据钢坯的尺寸、宽度和厚度等因素进行调整,以达到所需的钢材尺寸和厚度。
(2)调整轧制间隙:轧制间隙直接影响轧制效果和钢材的表面质量。
在实际生产中,轧制间隙需要根据钢坯的尺寸、宽度和厚度等因素进行调整,以保证钢材表面的质量和细节。
(3)调整辊轴位置:辊轴位置决定了钢坯的轧制路径和轧制力量。
在实际生产中,辊轴位置需要根据钢坯的物理属性和轧制工艺进行调整,以保证整个轧制过程的稳定性和效率。
(4)调整辊筒表面温度:辊筒表面温度对轧制效果和钢材表面的质量有着重要的影响。
热轧精轧机组速度控制研究

关键词 : 精 轧机 ; 速度 控 制 ; 主 速度 调 节 器 中图 分类 号 : T G3 3 3 . 1 7 文 献标 识 码 : A 文章 编 号 : 1 1 — 5 0 0 4 ( 2 0 1 7) 0 5 — 0 0 4 7 — 2
在热轧 生产 线中精 轧机 组一般 由 6架 轧机或 7架 轧机组 成 。并 且精 轧机组 由 AC主 电机作 为驱动 。精轧机组 通过 AC 主 电机 、减 速 机 、减 速 机 接 轴 带 动 轧 辊 进行 转 动 轧 制 。其 中 6 架轧 机或 是 7架 轧机根 据过 程计算 机控制 下设 定 ,通 过一级 P L C、变 频器 控制 进行 速度 控制 。其 中精 轧机 主驱 动速 度有
算 。详 见 图 1 。
两个 MR H ( 主速度调 节器 )共同用于精轧机速度参考值 的设定 ,一个 M R H 用来对当前带钢升速轧制 ,另 一个 MR H 设定下一块带钢的穿带速度 。
2 _ 2 级 联 控 制 和 各 架 轧机 的修 正 对于全 连续j f  ̄ r J 式 布 置 的 轧 机 ,级 联 控 制 功 能 用 于 确 保
来 搞 日 期 :2 0 1 7年 4月 作者简 介 : 陈 光 ,男 ,生 于 1 9 8 2年 , 汉 族 ,辽 宁 沈 阳 人 , 硕士, 现 在 首 钢 京
度参考 值达到最 大速度 的 9 5 %,通过控制 秒流量 MR H 的所 有轧机速度参考值将会降低 5 %。减速度是一个确定值 ( 0 . 5 m/ s 2 ) 。在 升速过程 中如果速度极 限控制运行 ,则停 止升速并执
轧机需 要减 速见图 4 。减速时序取决于轧制速度 。减速开 始时 序 ( 轧 机号 ,或与 F1 距离 )、减速度和 带尾抛钢速度都 由二 级 自动化设定 。
邯钢2250mm热轧厂提高成材率的研究与应用
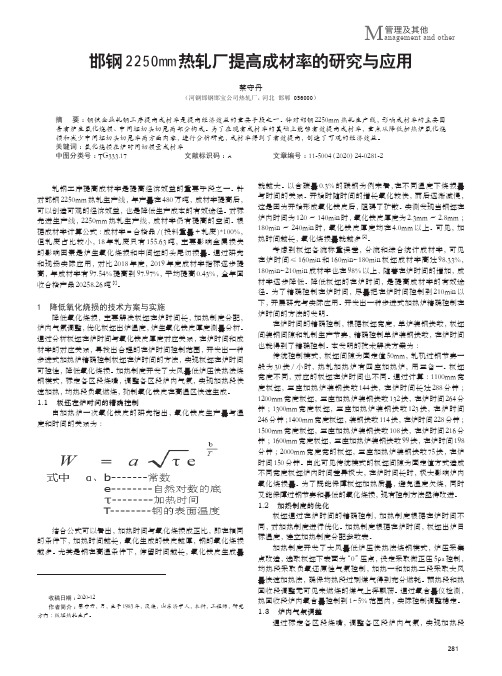
281管理及其他M anagement and other邯钢2250mm 热轧厂提高成材率的研究与应用蔡守丹(河钢邯钢邯宝公司热轧厂,河北 邯郸 056000)摘 要:钢铁企业轧钢工序提高成材率是提高经济效益的重要手段之一。
针对邯钢2250mm 热轧生产线,影响成材率的主要因素有炉生氧化烧损、中间坯切头切尾两部分构成。
为了在现有成材率的基础上能够有效提高成材率,重点从降低加热炉氧化烧损和减少中间坯切头切尾率两方面内容,进行分析研究,成材率得到了有效提高,创造了可观的经济效益。
关键词:氧化烧损在炉时间切损量成材率中图分类号:TG333.17 文献标识码:A 文章编号:11-5004(2020)24-0281-2 收稿日期:2020-12作者简介:蔡守丹,男,生于1983年,汉族,山东济宁人,本科,工程师,研究方向:板坯热轧生产。
轧钢工序提高成材率是提高经济效益的重要手段之一。
针对邯钢2250mm 热轧生产线,年产量在480万吨,成材率提高后,可以创造可观的经济效益,也是降低生产成本的有效途径。
对标先进生产线,2250mm 热轧生产线,成材率仍有提高的空间。
根据成材率计算公式:成材率=合格品/(投料重量+轧废)*100%,但轧废占比较小,18年轧废只有155.63吨,主要影响金属损失的影响因素是炉生氧化烧损和中间坯的头尾切损量。
通过研究和现场实际应用,对比2018年度,2019年度成材率指标逐步提高,年成材率有97.54%提高到97.97%,平均提高0.43%,全年回收合格产品20258.26吨[1]。
1 降低氧化烧损的技术方案与实施降低氧化烧损,主要解决板坯在炉时间长,加热制度分配,炉内气氛调整,优化板坯出炉温度,炉生氧化铁皮厚度测量分析。
通过分析板坯在炉时间与氧化铁皮厚度对应关系,在炉时间和成材率的对应关系,寻找出合理的在炉时间控制范围,开发出一种步进式加热炉精确控制板坯在炉时间的方法,实现板坯在炉时间可控性,降低氧化烧损。
邯钢冷轧热镀锌线光整机控制系统简析

邯钢冷轧热镀锌线光整机控制系统简析张红霞(邯郸钢铁公司冷轧厂,邯郸 056015 )0 引言随着市场经济的不断深化,近年来对于家电,建材、汽车板、容器、包装等实用冷轧镀锌板的需求越来越多。
为了适应新的形式,邯郸钢铁公司冷轧厂新建一条连续热镀锌线。
在生产线的关键设备光整机上采用的是Innovation系列中的Stand控制器。
这种控制器在光整机上的应用有一些特点和优势。
下1 Stand控制器Stand控制器是一个特定I/O的基于微处理器的控制器系统,是为中、大型复杂系统设计的控制器。
系统要求控制器具有先进的控制能力、高速的响应能力、强大的诊断功能和多种类型的I/O接口。
这些特点已超出传统PLC的范畴。
Stand控制器能够将特殊控制功能块和多任务连接在一起,并且将多任务连接到连续的操作流程中。
每个任务可快速分别定制,以优化控制回路的响应性能。
此外,它还允许用户定义多个任务的应用时间。
高速任务能0.5ms运行一次,低速任务根据要求可定在10~100ms。
Stand控制器包括以太网口和ISA总线,控制器包含闪存和多任务QNX操作系统。
它还有连接多种I/O的能力:包括Genius总线、GE ISBUS和GE传动局域网(DLAN+),它支持多种通信协议,如EGD、以太网Modbus、AB DH+等。
Stand控制器的编程工具运行环境为Windows 2000或Windows XP,核心编程工具软件为Toolbox可完成:控制器、I/O和传动的组态;控制逻辑的组态及监视和归档;历史趋势的组态和监视。
编程人员可为控制器定制几种不同编程语言,较为简单的顺序控制和许可功能可配置在继电器逻辑中,较为复杂的控制功能可通过执行预先定义在Toolbox中的控制模块来完成。
控制模块包括:联锁、RLD(继电器梯形逻辑)块;计数器和计时器块;布尔和逻辑块;许可和诊断块;运算(代数和统计)块;控制调节块。
Stand控制器允许建立公用代码模块和宏。
邯钢2250mm热轧生产线轧制节奏的分析及优化
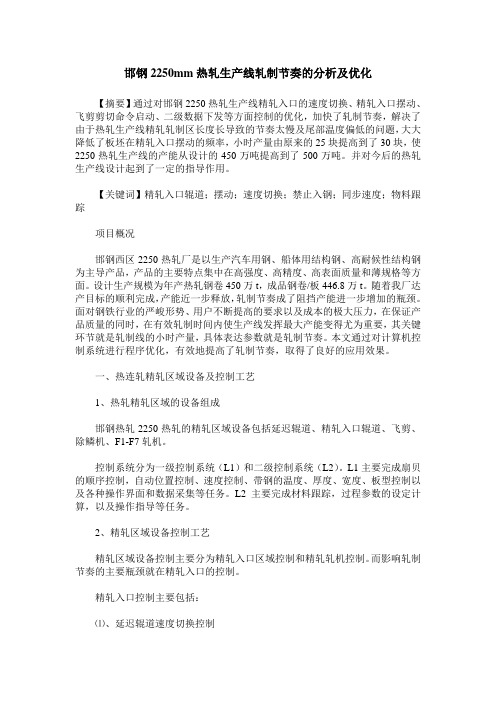
邯钢2250mm热轧生产线轧制节奏的分析及优化【摘要】通过对邯钢2250热轧生产线精轧入口的速度切换、精轧入口摆动、飞剪剪切命令启动、二级数据下发等方面控制的优化,加快了轧制节奏,解决了由于热轧生产线精轧轧制区长度长导致的节奏太慢及尾部温度偏低的问题,大大降低了板坯在精轧入口摆动的频率,小时产量由原来的25块提高到了30块,使2250热轧生产线的产能从设计的450万吨提高到了500万吨。
并对今后的热轧生产线设计起到了一定的指导作用。
【关键词】精轧入口辊道;摆动;速度切换;禁止入钢;同步速度;物料跟踪项目概况邯钢西区2250热轧厂是以生产汽车用钢、船体用结构钢、高耐候性结构钢为主导产品,产品的主要特点集中在高强度、高精度、高表面质量和薄规格等方面。
设计生产规模为年产热轧钢卷450万t,成品钢卷/板446.8万t。
随着我厂达产目标的顺利完成,产能近一步释放,轧制节奏成了阻挡产能进一步增加的瓶颈。
面对钢铁行业的严峻形势、用户不断提高的要求以及成本的极大压力,在保证产品质量的同时,在有效轧制时间内使生产线发挥最大产能变得尤为重要,其关键环节就是轧制线的小时产量,具体表达参数就是轧制节奏。
本文通过对计算机控制系统进行程序优化,有效地提高了轧制节奏,取得了良好的应用效果。
一、热连轧精轧区域设备及控制工艺1、热轧精轧区域的设备组成邯钢热轧2250热轧的精轧区域设备包括延迟辊道、精轧入口辊道、飞剪、除鳞机、F1-F7轧机。
控制系统分为一级控制系统(L1)和二级控制系统(L2)。
L1主要完成扇贝的顺序控制,自动位置控制、速度控制、带钢的温度、厚度、宽度、板型控制以及各种操作界面和数据采集等任务。
L2主要完成材料跟踪,过程参数的设定计算,以及操作指导等任务。
2、精轧区域设备控制工艺精轧区域设备控制主要分为精轧入口区域控制和精轧轧机控制。
而影响轧制节奏的主要瓶颈就在精轧入口的控制。
精轧入口控制主要包括:⑴、延迟辊道速度切换控制⑵、精轧入口速度控制⑶、精轧入口摆动控制⑷、精轧入口前后两块板坯距离控制⑸、精轧区域二级数据下发控制⑹、飞剪的剪切控制当板坯从R2轧制完最后一道次,进入精轧区域,首先延迟辊道以6米/秒的速度将板坯传送到飞剪入口,到达EE23HMD 时速度切换为1.1米/秒的切头部速度,切头完成后,速度切换为精轧机速度进入精轧机轧制。
热连轧精轧速度控制系统及其完善
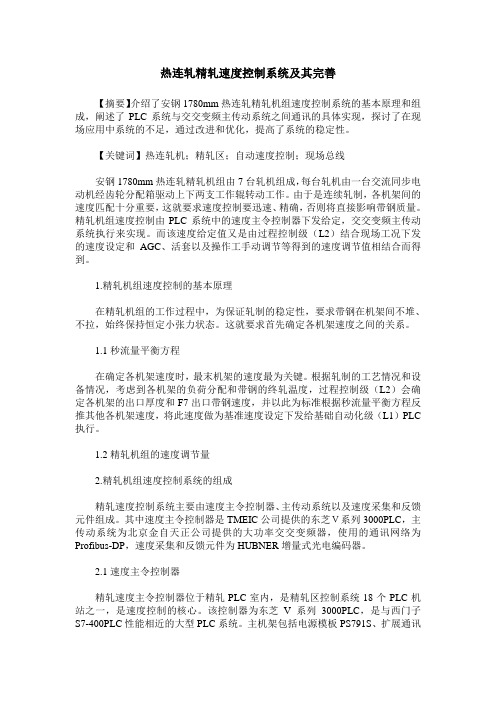
热连轧精轧速度控制系统及其完善【摘要】介绍了安钢1780mm热连轧精轧机组速度控制系统的基本原理和组成,阐述了PLC系统与交交变频主传动系统之间通讯的具体实现,探讨了在现场应用中系统的不足,通过改进和优化,提高了系统的稳定性。
【关键词】热连轧机;精轧区;自动速度控制;现场总线安钢1780mm热连轧精轧机组由7台轧机组成,每台轧机由一台交流同步电动机经齿轮分配箱驱动上下两支工作辊转动工作。
由于是连续轧制,各机架间的速度匹配十分重要,这就要求速度控制要迅速、精确,否则将直接影响带钢质量。
精轧机组速度控制由PLC系统中的速度主令控制器下发给定,交交变频主传动系统执行来实现。
而该速度给定值又是由过程控制级(L2)结合现场工况下发的速度设定和AGC、活套以及操作工手动调节等得到的速度调节值相结合而得到。
1.精轧机组速度控制的基本原理在精轧机组的工作过程中,为保证轧制的稳定性,要求带钢在机架间不堆、不拉,始终保持恒定小张力状态。
这就要求首先确定各机架速度之间的关系。
1.1秒流量平衡方程在确定各机架速度时,最末机架的速度最为关键。
根据轧制的工艺情况和设备情况,考虑到各机架的负荷分配和带钢的终轧温度,过程控制级(L2)会确定各机架的出口厚度和F7出口带钢速度,并以此为标准根据秒流量平衡方程反推其他各机架速度,将此速度做为基准速度设定下发给基础自动化级(L1)PLC 执行。
1.2精轧机组的速度调节量2.精轧机组速度控制系统的组成精轧速度控制系统主要由速度主令控制器、主传动系统以及速度采集和反馈元件组成。
其中速度主令控制器是TMEIC公司提供的东芝V系列3000PLC,主传动系统为北京金自天正公司提供的大功率交交变频器,使用的通讯网络为Profibus-DP,速度采集和反馈元件为HUBNER增量式光电编码器。
2.1速度主令控制器精轧速度主令控制器位于精轧PLC室内,是精轧区控制系统18个PLC机站之一,是速度控制的核心。
邯钢2250mm热轧线飞剪常见故障分析及控制优化
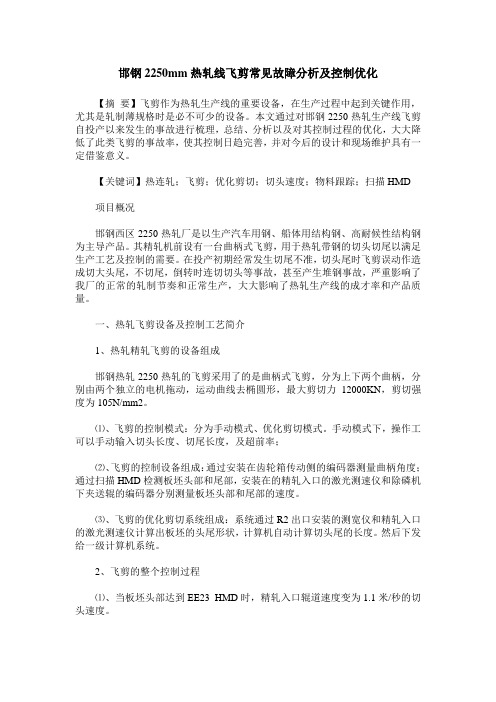
邯钢2250mm热轧线飞剪常见故障分析及控制优化【摘要】飞剪作为热轧生产线的重要设备,在生产过程中起到关键作用,尤其是轧制薄规格时是必不可少的设备。
本文通过对邯钢2250热轧生产线飞剪自投产以来发生的事故进行梳理,总结、分析以及对其控制过程的优化,大大降低了此类飞剪的事故率,使其控制日趋完善,并对今后的设计和现场维护具有一定借鉴意义。
【关键词】热连轧;飞剪;优化剪切;切头速度;物料跟踪;扫描HMD 项目概况邯钢西区2250热轧厂是以生产汽车用钢、船体用结构钢、高耐候性结构钢为主导产品。
其精轧机前设有一台曲柄式飞剪,用于热轧带钢的切头切尾以满足生产工艺及控制的需要。
在投产初期经常发生切尾不准,切头尾时飞剪误动作造成切大头尾,不切尾,倒转时连切切头等事故,甚至产生堆钢事故,严重影响了我厂的正常的轧制节奏和正常生产,大大影响了热轧生产线的成才率和产品质量。
一、热轧飞剪设备及控制工艺简介1、热轧精轧飞剪的设备组成邯钢热轧2250热轧的飞剪采用了的是曲柄式飞剪,分为上下两个曲柄,分别由两个独立的电机拖动,运动曲线去椭圆形,最大剪切力12000KN,剪切强度为105N/mm2。
⑴、飞剪的控制模式:分为手动模式、优化剪切模式。
手动模式下,操作工可以手动输入切头长度、切尾长度,及超前率;⑵、飞剪的控制设备组成:通过安装在齿轮箱传动侧的编码器测量曲柄角度;通过扫描HMD检测板坯头部和尾部,安装在的精轧入口的激光测速仪和除磷机下夹送辊的编码器分别测量板坯头部和尾部的速度。
⑶、飞剪的优化剪切系统组成:系统通过R2出口安装的测宽仪和精轧入口的激光测速仪计算出板坯的头尾形状,计算机自动计算切头尾的长度。
然后下发给一级计算机系统。
2、飞剪的整个控制过程⑴、当板坯头部达到EE23 HMD时,精轧入口辊道速度变为1.1米/秒的切头速度。
⑵、当板坯头部到达KZ21HMD时,飞剪曲柄动作到310度的等待剪切位。
⑶、当板坯头部到达MA01扫描HMD时,激光测速仪开始测量板坯通过HMD的距离。
邯钢2250mm生产线减少麻点麻面实现高速钢轧辊使用

邯钢2250mm生产线减少麻点麻面实现高速钢轧辊使用作者:陈福兰来源:《商品与质量·学术观察》2013年第08期摘要:自2008年建厂以来麻点麻面缺陷一直是困绕表面质量提高的难题,为了降低麻点麻面一级品改判率、提高带钢表面质量、降低质量损失,因此研究解决了这一难题,同时实现了高速钢轧辊的正常使用。
关键词:麻点麻面化学成分高速钢轧辊简介邯钢集团邯宝公司热轧厂拥有一条具有当代国际先进水平的2250mm常规热连轧带钢生产线,年设计产能450万吨。
热炉由法国斯坦因公司设计,主轧线由德国西马克公司设计配以日本TMEIC公司电气控制系统。
整条生产线采用了加热炉数字化燃烧、定宽机大侧压、中间坯边部加热、精轧机组多手段板型控制和大功率交直变频传动等先进技术,具有轧机轧制能力大、生产工艺先进、设备配置合理、轧机能力大和控制手段齐全等特点。
产品可涵盖厚度范围从1.2毫米至25.4毫米,宽度最大可达2130 mm的汽车用钢、船体用结构钢、高耐候性结构钢以及高强度管线钢等,产品的主要特点集中在宽断面、高精度、品种多、强度高等方面。
1、前言自2250mm投产以来特别是随着冷轧备料量的增加麻点麻面和氧化铁皮缺陷一直是困扰一级品率提高的难题;下道工序也多次提出我厂备料存在麻点麻面质量问题,在冷轧过程中不能纠正因而产生降级改判;2012年外部用户提出麻点麻面异议共9起,通过二项过程能力分析2012年麻点麻面缺陷一级品改判率0.68%,给公司造成损失。
目前面对严峻的市场形势,公司生产经营转型力度、坚持“品种、质量、效益型”道路,大力压减非计划产品,全面提高过程控制能力和产品实物质量。
解决麻点麻面缺陷势在必行。
2、麻点麻面缺陷的特性:根据对去年所有麻点缺陷钢卷信息进行统计分析,发现其分布存在以下明显特征:2.1基本都是在SS400薄规格轧制计划中产生,大部分为冷轧备料,规格偏薄,厚度多分布在2.0-3.5mm;2.2麻点麻面缺陷75%以上发生在下表面;下线后轧辊表面均有明显氧化膜剥落,表面粗糙,下辊尤为明显。
邯钢热基镀锌自动控制系统的优化与创新-最新文档资料
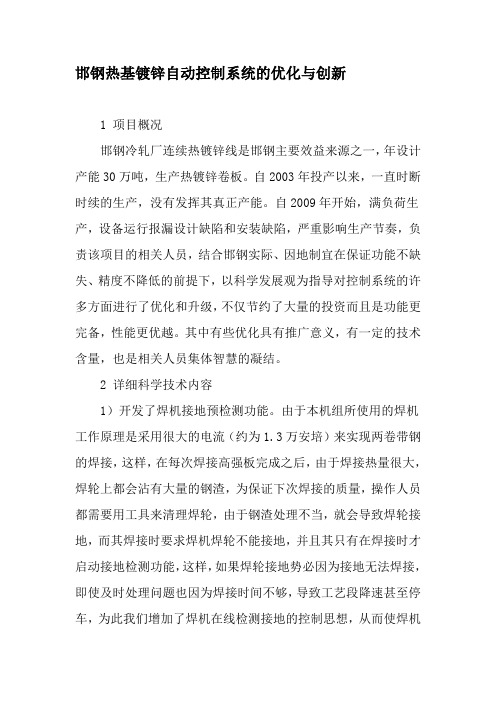
邯钢热基镀锌自动控制系统的优化与创新1 项目概况邯钢冷轧厂连续热镀锌线是邯钢主要效益来源之一,年设计产能30万吨,生产热镀锌卷板。
自2003年投产以来,一直时断时续的生产,没有发挥其真正产能。
自2009年开始,满负荷生产,设备运行报漏设计缺陷和安装缺陷,严重影响生产节奏,负责该项目的相关人员,结合邯钢实际、因地制宜在保证功能不缺失、精度不降低的前提下,以科学发展观为指导对控制系统的许多方面进行了优化和升级,不仅节约了大量的投资而且是功能更完备,性能更优越。
其中有些优化具有推广意义,有一定的技术含量,也是相关人员集体智慧的凝结。
2 详细科学技术内容1)开发了焊机接地预检测功能。
由于本机组所使用的焊机工作原理是采用很大的电流(约为1.3万安培)来实现两卷带钢的焊接,这样,在每次焊接高强板完成之后,由于焊接热量很大,焊轮上都会沾有大量的钢渣,为保证下次焊接的质量,操作人员都需要用工具来清理焊轮,由于钢渣处理不当,就会导致焊轮接地,而其焊接时要求焊机焊轮不能接地,并且其只有在焊接时才启动接地检测功能,这样,如果焊轮接地势必因为接地无法焊接,即使及时处理问题也因为焊接时间不够,导致工艺段降速甚至停车,为此我们增加了焊机在线检测接地的控制思想,从而使焊机在不焊接时也能进行接地检测,当进行在线接地检测时,如果有接地现象,接地指示灯亮,且触摸屏显示接地报警,提醒操作人员焊机接地,不能完成焊接程序,请操作人员及时清理焊轮铁屑和杂质,保证焊轮清洁,从而为下次焊接时提供充足的焊接时间。
2)优化了焊机焊接电流控制系统。
因焊接回路电阻很低,焊接瞬间所产生的电流接近短路电流。
经过与厂家沟通,改变原来的梅达760电流控制系统焊接电流控制方式,改为通过改变交流调压装置的门极触发角,进行焊接电压值的调节,采用焊接电压控制焊接电流,而电流采用开环控制,从而保证所产生的焊接电流更加平稳。
同时修改了电流触发控制参数,使电流控制系统能够缓慢响应电流增大命令,避免焊接开始时因电流瞬间增大造成对焊轮及带钢的损坏(已获取专利)。
热轧2250mm生产线优化活套控制避免F7划伤
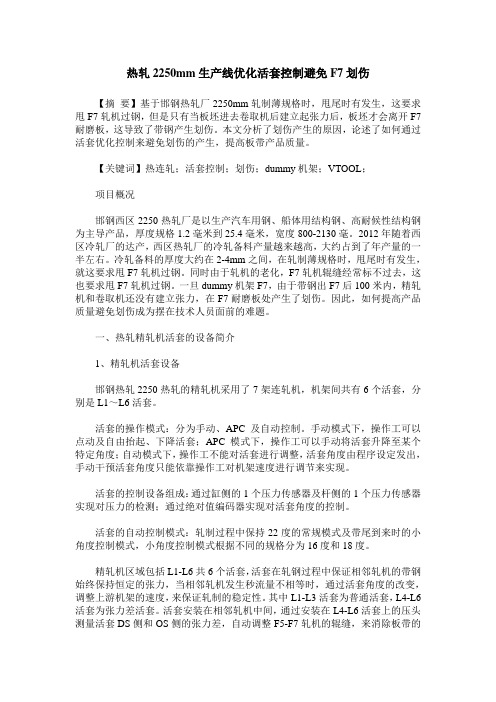
热轧2250mm生产线优化活套控制避免F7划伤【摘要】基于邯钢热轧厂2250mm轧制薄规格时,甩尾时有发生,这要求甩F7轧机过钢,但是只有当板坯进去卷取机后建立起张力后,板坯才会离开F7耐磨板,这导致了带钢产生划伤。
本文分析了划伤产生的原因,论述了如何通过活套优化控制来避免划伤的产生,提高板带产品质量。
【关键词】热连轧;活套控制;划伤;dummy机架;VTOOL;项目概况邯钢西区2250热轧厂是以生产汽车用钢、船体用结构钢、高耐候性结构钢为主导产品,厚度规格1.2毫米到25.4毫米,宽度800-2130毫。
2012年随着西区冷轧厂的达产,西区热轧厂的冷轧备料产量越来越高,大约占到了年产量的一半左右。
冷轧备料的厚度大约在2-4mm之间,在轧制薄规格时,甩尾时有发生,就这要求甩F7轧机过钢。
同时由于轧机的老化,F7轧机辊缝经常标不过去,这也要求甩F7轧机过钢。
一旦dummy机架F7,由于带钢出F7后100米内,精轧机和卷取机还没有建立张力,在F7耐磨板处产生了划伤。
因此,如何提高产品质量避免划伤成为摆在技术人员面前的难题。
一、热轧精轧机活套的设备简介1、精轧机活套设备邯钢热轧2250热轧的精轧机采用了7架连轧机,机架间共有6个活套,分别是L1~L6活套。
活套的操作模式:分为手动、APC及自动控制。
手动模式下,操作工可以点动及自由抬起、下降活套;APC模式下,操作工可以手动将活套升降至某个特定角度;自动模式下,操作工不能对活套进行调整,活套角度由程序设定发出,手动干预活套角度只能依靠操作工对机架速度进行调节来实现。
活套的控制设备组成:通过缸侧的1个压力传感器及杆侧的1个压力传感器实现对压力的检测;通过绝对值编码器实现对活套角度的控制。
活套的自动控制模式:轧制过程中保持22度的常规模式及带尾到来时的小角度控制模式,小角度控制模式根据不同的规格分为16度和18度。
精轧机区域包括L1-L6共6个活套,活套在轧钢过程中保证相邻轧机的带钢始终保持恒定的张力,当相邻轧机发生秒流量不相等时,通过活套角度的改变,调整上游机架的速度,来保证轧制的稳定性。
邯钢热轧表面检测仪速度输入信号的选取修正实例
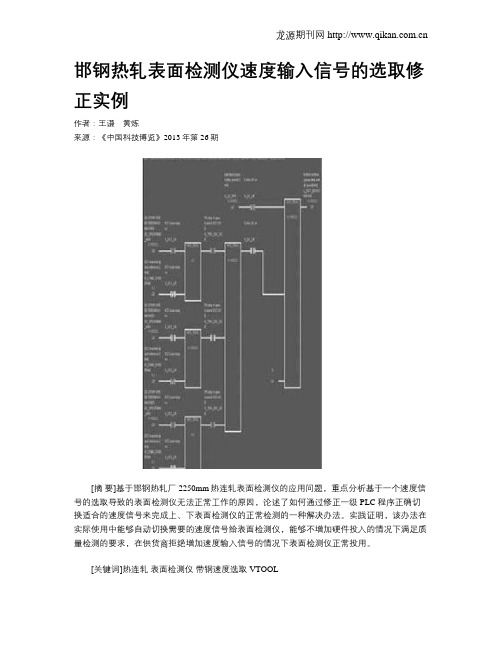
邯钢热轧表面检测仪速度输入信号的选取修正实例作者:王谦黄炼来源:《中国科技博览》2013年第26期[摘要]基于邯钢热轧厂2250mm热连轧表面检测仪的应用问题,重点分析基于一个速度信号的选取导致的表面检测仪无法正常工作的原因,论述了如何通过修正一级PLC程序正确切换适合的速度信号来完成上、下表面检测仪的正常检测的一种解决办法。
实践证明,该办法在实际使用中能够自动切换需要的速度信号给表面检测仪,能够不增加硬件投入的情况下满足质量检测的要求,在供货商拒绝增加速度输入信号的情况下表面检测仪正常投用。
[关键词]热连轧表面检测仪带钢速度选取 VTOOL中图分类号:TG335.11 文献标识码:A 文章编号:1009-914X(2013)26-310-02项目概况邯钢2250热轧是邯钢新区产业升级中的一个重要工序,该热轧生产线自动控制及传动系统引自日本TMEIC公司,其控制水平具有世界先进水平,并于2008年8月建成投产。
随着热连轧自动化程度的提高,轧制节奏的逐渐加快的同时对板带的质量提出了更高的要求。
板带质量的提高要求对板带质量出现问题要及时发现,2012年表面检测仪进行安装调试,但是在调试过程中发现基于使用环境及处理堆钢事故的考虑将上、下表面检测仪安装于不同位置,但是由于供货商答复只能接收一个速度信号输入点,造成了造成在上下表面检测仪分别出现不同速度的带头带尾,因此无论用精轧机速度或是卷取机速度都不能保证表面检测仪能够准确的测量带钢表面质量并记录及报警。
进而造成表面检测仪始终无法投用。
随着轧制速度的提高很多缺陷卷不能及时发现,给热轧厂造成重大损失。
如何在只有一个速度信号输入点的情况下,PLC 选取正确的速度信号输出给表面检测仪,使其能正常使用就成为热连轧生产线工程技术人员面临的重要难点和课题。
一、表面检测仪系统的设备简介1、一级控制系统设备该热轧厂精轧机换辊自动化控制系统采用了东芝的V3000系列控制器,使用的控制器主要有S3、R3、STC及C3 。
热轧带钢轧制节奏的优化分析

热轧带钢轧制节奏的优化分析[摘要]随着我国钢铁行业的形势不断严峻,用户的要求不断提高,为成本的投入增加了巨大的压力如何在确保产品质量的同时,能够在相对的时间内使生产线发挥出更大的优势,是现阶段最为重要的问题。
本文针对热连扎窄带钢生产中出现的精轧区轧区长度长和传统控制方式导致轧制节奏慢等问题进行分析,并通过对两级自动化的控制系统进行相映的改善,完善轧制规程,发送时序和速度算法,解决了两块刚同时炸制的问题,为相关生产单位提供参考。
[关键词]窄带钢热连轧;轧制节奏;控制系统;优化分析受我国社会经济的影响,钢铁行业的形势逐渐严峻。
人们不断提高对钢铁行业的要求,增加投入的成本。
如何能够在确保产品质量的同时,还能够在有效的时间内发挥最大的优势是最为重要的内容,最关键的环节就是扎制线的小时产量,具体的表达参数就是扎制节奏。
现阶段计算机技术已经在窄带钢生产线中得到了普遍的使用。
下面通过对计算机技术系统进行优化,提升轧制节奏并取得优秀的应用成果。
一、轧制节奏概念概念一:轧钢工作过程中钢到开始连续轧制第一根筋在钢到最后开始连续轧制第二根筋在钢的中间延续一段时间节奏称为开始轧制时间节奏。
概念二:钢机轧制时间指相邻两根类型轧件同时进入(或混合轧出)同一类型轧机的轧制时间节奏间隔。
在同样工艺条件下,轧制机的节奏时间越短,轧机小时生生产童越高;反之,轧机小时生的产量越低。
所以影响不同轧制机的节奏时间长短的主要因素一般是分为多方面的,不仅与现场工艺生产因素(即诸如轧制坯体材料剪切长短、断面切割尺寸面积大小、道次多少、操作设备条件等)之间有直接相互联系,也与现场设备生产条件(即诸如压制轧机整体布置操作形式、机架多少、速度效率高低以及轧制电机操作能力消耗大小等)密切直接相关。
合理地正确分配不同轧制机的道次可以使各轧制机组操作负荷均匀、提高轧机操作效率水平、减少轧机操作过程间隙占用时间、改变轧机操作运动方式、实行轧机文叉混合乳制、在现场设备条件允许操作条件下同时加大轧制变形机数量、强化钢机轧制操作过程等都足以可直接收到有效缩短钢机轧制时间节奏的良好效果。
轧钢厂的精轧工序轧制批量调度的优化模型74

轧钢厂的精轧工序轧制批量调度的优化模型摘要:对于钢铁轧制的基本工艺流程来讲,精轧工序构成了其中很关键的工序。
轧钢厂具体在拟定精轧钢铁的规划时,关键应当着眼于批量的轧制钢铁调度。
因此轧钢厂在实现批量调度以及调整精轧工序的过程中,应当运用优化模型的措施对其加以适当改进,确保精轧工序的良好效果。
关键词:轧钢厂;精轧工序;轧制批量调度;优化模型在全过程的钢铁生产中,精轧工序构成了其中关键性的轧钢操作环节。
从目前现状来看,信息化手段正在全面适用于轧钢操作中,而与之相应的建模措施也实现了优化与改进。
具体而言,轧钢厂通过运用优化模型的方式,应当能够灵活调度钢材生产,从而运用建模方式来全面监管整个的轧钢操作流程。
轧钢厂只有通过运用批量调度的方式,才能够在根源上优化精轧工序的有关环节,同时也保障了精轧工序能够获得的优良效果。
截至目前,对于精轧工序构建模型的措施已经可以用来完成针对型钢生产、带钢生产以及钢管生产的批量轧制操作,在此前提下显著优化了轧钢操作工艺的实效性。
一、对于精轧工序全面构建批量调度模型的必要性从现状来看,各地轧钢厂都在着眼于引进信息化手段来辅助开展日常生产。
在轧钢厂现有的各个生产流程中,核心工序就在于精轧操作。
这是由于,通过运用精轧操作的方式,应当能够生产出优质的钢材产品,其中包含型钢、带钢、钢管与其他典型的钢材产品。
由此可见,轧钢厂在批量完成精轧钢材的具体操作中,应当能够因地制宜给出相应的调度规划,以此来保障顺利完成全过程的精轧钢材操作。
在此前提下,针对精轧钢材的核心工序应当构建与之相适应的批量调度模型。
具体而言,轧钢厂在全面开展钢材精轧的有关操作时,应当确保结合现有的钢材轧制规划,依照合同拟定的生产规划予以全面完成。
在此基础上,轧钢厂针对原有的钢材轧制规划还需予以适当转型,从而给出与之有关的各项信息与数据。
在目前看来,轧钢厂已经可以凭借信息化的措施来构建相应的调度模型,上述模型相比而言具备独特的技术优势。
- 1、下载文档前请自行甄别文档内容的完整性,平台不提供额外的编辑、内容补充、找答案等附加服务。
- 2、"仅部分预览"的文档,不可在线预览部分如存在完整性等问题,可反馈申请退款(可完整预览的文档不适用该条件!)。
- 3、如文档侵犯您的权益,请联系客服反馈,我们会尽快为您处理(人工客服工作时间:9:00-18:30)。
邯钢热轧线精轧区域速度控制优化与实践
作者:夏焕梅任连波
来源:《中国科技博览》2013年第26期
中图分类号:TG333.17 文献标识码:A 文章编号:1009-914X(2013)26-320-01
1 前言
邯钢西区热轧厂2250轧机自2008年8月投产以来,年产量已经由100万吨提高到500万吨,产品规格多,并且能够轧制X80、X100等高级别管线钢。
自动控制系统引进TEMIC公司的VTOOL控制软件及INTOUCH人机操作界面,处于世界领先水平。
热轧生产节奏较快且连续生产,现场工艺复杂,全自动生产,因此自动化控制在生产中起着至关重要的作用,而精轧区域的自动化控制又是最复杂、精度要求最高的。
这也造成由于精轧自动控制不完善,出现生产事故的几率很大。
2010年,由于精轧入口速度控制原因飞剪出现了20次以上的切大头或切大尾事故,辊道速度控制不同步造成跳电8次等问题,同时由于精轧控制复杂、轧机多,是制约提高产量和轧制X80/100等特殊钢种的瓶颈。
这严重影响着热轧的正常生产和新品种的开发,因此对精轧入口区域辊道速度的自动控制系统优化升级尤为重要。
2 精轧前入口辊道速度控制的实践与优化
2.1 精轧前入口辊道控制过程
精轧入口辊道连接粗轧机及精轧机,在轧制过程中入口辊道速度要与对应设备匹配,速度控制比较复杂。
精轧入口区域速度控制,包括R2同步速度控制、板坯运送速度控制,EH抛钢速度控制,CS区域摆动速度控制,FSB区域摆动速度控制,精轧机同步速度控制。
如下图:
板坯在出R2轧机时,辊道速度与R2轧机速度匹配,当板坯到达精轧入口时,如果此时精轧机F4没有抛钢,板坯在入口辊道摆动;如果此时精轧机已经抛钢,PLC控制系统发出
1.1m/s的飞剪剪切速度,此时辊道速度与飞剪速度进行同步;剪切完成后到精轧机F1发出咬钢信号,辊道与F1轧机速度进行同步。
2.2 轧制过程中存在的问题及优化方案
由于板坯轧制过程中,速度控制比较复杂,在实际生产中多次出现入口辊道与相应设备速度不匹配,PLC发出速度值变化过大导致辊道电机逆变跳电及辊道速度过快造成飞剪切头过长等问题,严重影响了正常生产及造成成材率过低。
2.2.1 轧机禁止入钢时,延时辊道板坯摆动速度控制优化
2.2.1.1 轧机禁止入钢时,入口辊道速度控制存在问题
在轧钢过程中,当精轧机正在轧制板坯,而下一块板坯到达精轧入口时,系统发出精轧机禁止入钢信号。
原功能控制没有考虑辊道在禁止入钢信号消失后的速度参考值的切换。
所以当辊道向粗轧方向转动时,如果此时禁止入钢信号消失,辊道速度参考值会瞬间切换成向精轧方向转动,这种瞬间切换给延时辊道传动系统带来了很大的负载冲击,造成传动系统频繁故障报警,同时逆变跳。
如果逆变没跳,会导致更严重的后果:辊道速度设定值向前(精轧方向),实际辊道速度反馈向后(粗轧方向),出现了模型计算板坯位置和实际板坯位置脱节的情况,从而使该块板坯作废。
2.2.1.2 轧机禁止入钢时辊道速度控制优化
鉴于上述问题,在充分研究了速度控制程序后,决定采用延长禁止入钢信号的方法来解决问题。
即如果板坯正在向粗轧方向摆动,速度参考值为负,那么即使此时禁止入钢信号消失,此时强制继续禁止入钢,直到辊道停下来。
程序中禁止入钢条件是一系列的连锁条件,当条件都满足时,可以过钢;当有条件不满足时,发出禁止入钢信号。
在三种情况下系统检查禁止入钢条件是否满足:EE23得电时发出检查脉冲;延时辊道和飞剪前辊道操作模式切换回自动时发出检查脉冲;另外就是禁止入钢条件从不满足到满足时,将会发出自检脉冲。
取延时辊道的速度反馈值,然后作了一个比较功能模块,即当辊道速度反馈值不是负值时发出1(V>=0),然后将此点和到禁止入钢信号自锁复位点并联,也就是即使禁止入钢条件满足,由于辊道速度为负,禁止入钢信号自锁不能解除,将继续保持禁止入钢,直到辊道速度不为负。
2.2.2 除鳞机辊道速度控制优化
2.2.2.1 除鳞机辊道速度存在问题
板坯在精轧机轧制过程中,精轧入口辊道速度同步精轧机速度。
当板坯通过后,辊道停止或同步飞剪剪切速度。
但当此时R2轧机中也有钢在轧制时,就会出现精轧入口辊道速度同步
R2轧机速度,造成除鳞机辊道跳电,此时如果正好赶上下一块板坯的头部到达飞剪处,就会导致飞剪切出2米的大头或者大尾,造成堆钢。
并且精轧区域会禁止入钢,如果辊道得不到及时恢复,就会造成推中间坯。
在对热轧厂半年数据统计中发现共发生三次类似事故,推出中间坯5块。
因此迫切需要解决精轧除鳞机辊道跳电及飞剪切头尾过长难题。
2.2.2.2 除鳞机辊道速度控制优化
通过观察,倒转都发生在坯子尾部,并且倒转后除鳞机辊道就会跳电,造成禁止入钢,一个是解决辊道速度设定值的给定,另一个是飞剪切尾的速度给定。
通过优化程序,在精轧入口辊道速度设定值给出R2同步速度501信号后,并且精轧机处于咬钢状态,精轧入口辊道速度会自动切换到和精轧机速度,当入口辊道的速度设定值给出正确的511或者611后,精轧入口辊道速度值自动切换回来。
当然这种情况只发生在精轧入口辊道的速度模式是自动模式下,并且精轧入口区域没有摆动命令发出。
在这种情况在精轧入口辊道就会跟随精轧机运行,避免除鳞机辊道跳电引起禁止入钢,同时也给飞剪剪切提供了板坯的速度值,不会因为倒转或者加速造成飞剪切大头。
2.3 速度控制系统优化后效果
(1)对精轧入口辊道速度控制优化后,取得了显著效果。
轧机故障率明显下降,见下表:
(2)产品成材率显著提高
飞剪剪切的精度得到大大提高,杜绝了板坯切大头、大尾现象,切头的平均误差由原来的≤80mm降低到≤20mm,切尾误差由≤100mm降低到≤30mm,切损率逐月降低(见下图),目前我厂剪切精度在国内同类型生产线中处于领先水平。
3 结语
热轧厂自动控制系统在轧制过程中进行了大量的控制优化后,故障率明显下降,成材率取得了显著提高,对原程序设计存在的缺陷进行优化使控制过程更加满足了生产需要。