CAE在汽车NVH设计开发及优化中的应用
cae在汽车nvh方面的应用

人工智能技术为CAE提供了强大的计算能力和 数据分析能力,能够更准确地模拟和预测汽车 NVH性能。
通过深度学习和神经网络等技术,可以自动识 别和优化设计中的问题,提高设计效率和准确 性。
人工智能与CAE的结合将进一步推动汽车设计 的智能化和自动化。
云技术在CAE领域的应用
01
云技术为CAE提供了大规模计算和存储资源,可以处理更复杂、 更高精度的仿真分析。
1 2
起步阶段
20世纪50年代,计算机开始应用于工程领域, CAE技术开始起步。
发展阶段
20世纪70年代,随着计算机性能的提高和数值 计算方法的改进,CAE技术得到快速发展。
3
成熟阶段
20世纪90年代至今,随着计算机技术的不断进 步和数值计算方法的不断完善,CAE技术逐渐成 熟并广泛应用于各个领域。
案例二:汽车发动机振动分析
发动机是汽车的主要噪声源之一,其振动会产生噪音和疲劳损伤。CAE技术可以 对发动机的振动进行分析,优化其结构设计和动态特性。
通过CAE分析,可以预测发动机在不同工况下的振动响应,优化发动机的平衡和 减震设计,降低发动机的振动和噪音,提高汽车的NVH性能。
案例三:汽车车身结构噪声分析
CAE在NVH问题中的优势和挑战
优势
CAE技术可以模拟和分析汽车的NVH 性能,帮助工程师快速定位和解决问 题。通过CAE分析,可以减少试验次 数和成本,缩短产品开发周期。
挑战
CAE分析的精度和可靠性是关键挑战。 对于复杂的NVH问题,需要高精度的模 型和准确的边界条件才能获得可靠的结 果。此外,CAE分析也需要大量的计算 资源和专业技术人员进行操作和解读。
CAE面临的重要挑战。
跨学科交叉也是CAE未来发展 的重要方向,需要加强与其他
汽车优化设计中CAE技术的应用
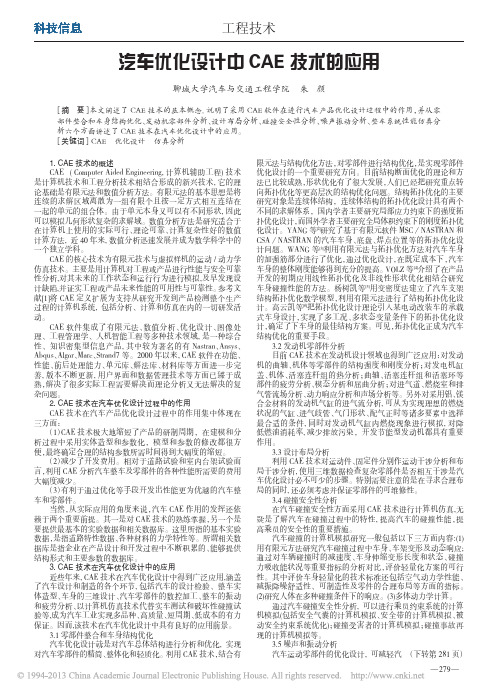
47-CAE在整车开发中NVH方面的应用
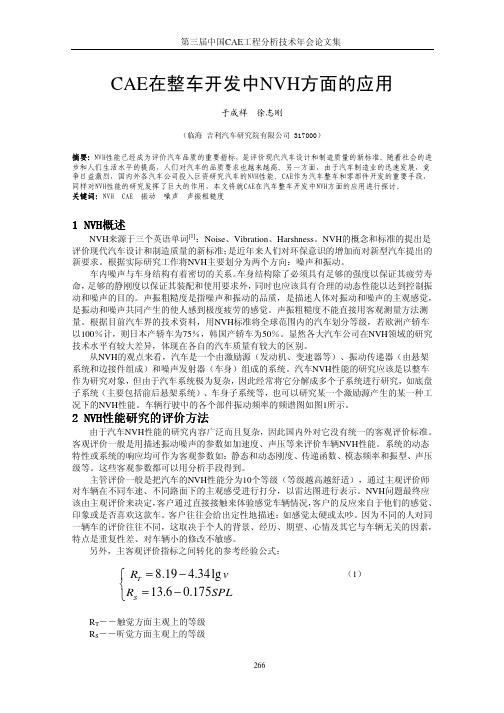
1 NVH概述 NVH概述
NVH来源于三个英语单词[1]:Noise、Vibration、Harshness。NVH的概念和标准的提出是 评价现代汽车设计和制造质量的新标准; 是近年来人们对环保意识的增加而对新型汽车提出的 新要求。根据实际研究工作将NVH主要划分为两个方向:噪声和振动。 车内噪声与车身结构有着密切的关系。 车身结构除了必须具有足够的强度以保证其疲劳寿 命, 足够的静刚度以保证其装配和使用要求外, 同时也应该具有合理的动态性能以达到控制振 动和噪声的目的。声振粗糙度是指噪声和振动的品质,是描述人体对振动和噪声的主观感觉, 是振动和噪声共同产生的使人感到极度疲劳的感觉。声振粗糙度不能直接用客观测量方法测 量。根据目前汽车界的技术资料,用NVH标准将全球范围内的汽车划分等级,若欧洲产轿车 以100%计,则日本产轿车为75%,韩国产轿车为50%。显然各大汽车公司在NVH领域的研究 技术水平有较大差异,体现在各自的汽车质量有较大的区别。 从NVH的观点来看,汽车是一个由激励源(发动机、变速器等)、振动传递器(由悬架 系统和边接件组成)和噪声发射器(车身)组成的系统。汽车NVH性能的研究应该是以整车 作为研究对象,但由于汽车系统极为复杂,因此经常将它分解成多个子系统进行研究,如底盘 子系统(主要包括前后悬架系统)、车身子系统等,也可以研究某一个激励源产生的某一种工 况下的NVH性能。车辆行驶中的各个部件振动频率的频谱图如图1所示。
第三届中国CAE工程分析技术年会论文集
CAE在整车开发中NVH方面的应用
于成祥 徐志刚
(临海 吉利汽车研究院有限公司 317000) 摘要: 摘要:NVH性能已经成为评价汽车品质的重要指标,是评价现代汽车设计和制造质量的新标准。随着社会的进 步和人们生活水平的提高,人们对汽车的品质要求也越来越高。另一方面,由于汽车制造业的迅速发展,竞 争日益激烈,国内外各汽车公司投入巨资研究汽车的NVH性能。CAE作为汽车整车和零部件开发的重要手段, 同样对NVH性能的研究发挥了巨大的作用,本文将就CAE在汽车整车开发中NVH方面的应用进行探讨。 关键词: 关键词:NVH CAE 振动 噪声 声振粗糙度
汽车产品设计制造中CAE技术的运用

汽车产品设计制造中CAE技术的运用随着汽车工业的不断发展,汽车产品的设计和制造也在不断追求更先进的技术和工艺。
在汽车产品设计制造过程中,CAE(Computer Aided Engineering)技术的运用日益广泛,成为汽车设计制造过程中不可或缺的重要技术工具。
本文将从CAE技术的定义、优势、应用和发展趋势等方面进行探讨,以期更加深入了解CAE技术在汽车产品设计制造中的作用和意义。
一、CAE技术的定义CAE(Computer Aided Engineering)是指使用计算机进行工程设计、分析和制造的技术手段。
它是一种工程设计和分析的方法,利用计算机进行模拟和仿真,以辅助工程师进行设计和分析,从而提高产品的质量和性能,减少成本和时间。
CAE技术以其快速、精确、可靠的特点,为工程师提供了强大的工具和支持,成为汽车产品设计制造中不可或缺的技术手段。
1. 减少试验验证次数:CAE技术可以通过仿真和模拟的手段,快速准确地分析产品的性能和行为,减少了试验验证的次数,节省了时间和成本。
2. 优化设计方案:通过CAE技术,工程师可以多方面、多角度地对产品进行分析和评估,优化设计方案,提高产品的质量和性能。
3. 提高产品的可靠性:CAE技术可以对产品进行可靠性分析,预测产品的寿命和损耗,帮助工程师提前发现问题,减少故障率。
4. 辅助制造工艺:CAE技术可以进行成型、焊接、装配等工艺仿真,帮助制造工程师优化工艺流程,提高生产效率和质量。
5. 提高市场竞争力:通过CAE技术的运用,可以加快产品的研发周期,提高产品的质量和性能,从而提升企业在市场竞争中的地位和声誉。
1. 结构分析:CAE技术可以对汽车的车身、底盘、发动机等部件进行结构分析,评估其强度、刚度、稳定性等性能,为产品设计和制造提供重要的参考依据。
2. 疲劳分析:汽车在长期使用过程中会受到不同方向的载荷作用,CAE技术可以对汽车的零部件进行疲劳分析,预测零部件的寿命和损耗,提高产品的可靠性和安全性。
汽车产品设计制造中CAE技术的运用
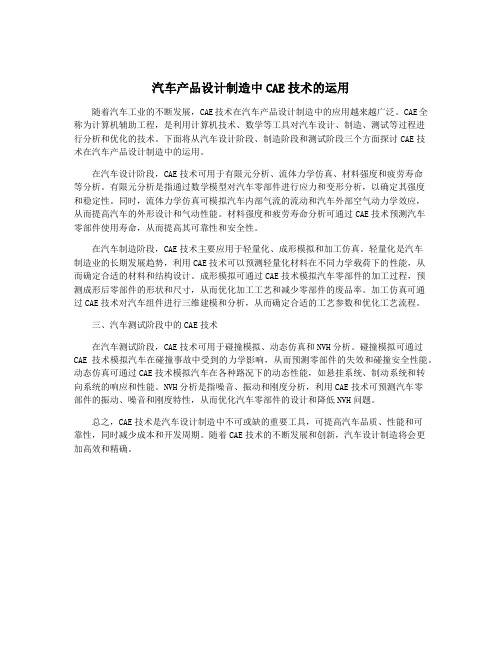
汽车产品设计制造中CAE技术的运用随着汽车工业的不断发展,CAE技术在汽车产品设计制造中的应用越来越广泛。
CAE全称为计算机辅助工程,是利用计算机技术、数学等工具对汽车设计、制造、测试等过程进行分析和优化的技术。
下面将从汽车设计阶段、制造阶段和测试阶段三个方面探讨CAE技术在汽车产品设计制造中的运用。
在汽车设计阶段,CAE技术可用于有限元分析、流体力学仿真、材料强度和疲劳寿命等分析。
有限元分析是指通过数学模型对汽车零部件进行应力和变形分析,以确定其强度和稳定性。
同时,流体力学仿真可模拟汽车内部气流的流动和汽车外部空气动力学效应,从而提高汽车的外形设计和气动性能。
材料强度和疲劳寿命分析可通过CAE技术预测汽车零部件使用寿命,从而提高其可靠性和安全性。
在汽车制造阶段,CAE技术主要应用于轻量化、成形模拟和加工仿真。
轻量化是汽车制造业的长期发展趋势,利用CAE技术可以预测轻量化材料在不同力学载荷下的性能,从而确定合适的材料和结构设计。
成形模拟可通过CAE技术模拟汽车零部件的加工过程,预测成形后零部件的形状和尺寸,从而优化加工工艺和减少零部件的废品率。
加工仿真可通过CAE技术对汽车组件进行三维建模和分析,从而确定合适的工艺参数和优化工艺流程。
三、汽车测试阶段中的CAE技术在汽车测试阶段,CAE技术可用于碰撞模拟、动态仿真和NVH分析。
碰撞模拟可通过CAE技术模拟汽车在碰撞事故中受到的力学影响,从而预测零部件的失效和碰撞安全性能。
动态仿真可通过CAE技术模拟汽车在各种路况下的动态性能,如悬挂系统、制动系统和转向系统的响应和性能。
NVH分析是指噪音、振动和刚度分析,利用CAE技术可预测汽车零部件的振动、噪音和刚度特性,从而优化汽车零部件的设计和降低NVH问题。
总之,CAE技术是汽车设计制造中不可或缺的重要工具,可提高汽车品质、性能和可靠性,同时减少成本和开发周期。
随着CAE技术的不断发展和创新,汽车设计制造将会更加高效和精确。
cae在汽车设计中的应用

cae在汽车设计中的应用CAE(计算机辅助工程)在汽车设计中的应用导语:随着科技的发展和计算机技术的日益成熟,计算机辅助工程(CAE)在汽车设计中的应用越来越广泛。
本文将重点探讨CAE在汽车设计中的应用领域和优势,以及其对汽车设计带来的影响。
一、CAE在汽车设计中的应用领域1. 结构分析:CAE可以通过有限元分析(FEA)来对汽车的结构进行模拟和分析,以评估其强度、刚度和耐久性。
通过对各种载荷情况下的模拟测试,可以帮助设计师优化车身结构,提高整车的安全性和耐久性。
2. 碰撞仿真:通过CAE的碰撞仿真技术,设计师可以在计算机上模拟不同碰撞情况下的车辆行为,以评估车辆的安全性能。
通过对车身和座椅的碰撞仿真,可以优化车辆的结构设计,提高乘员的安全性。
3. 空气动力学分析:CAE可以通过流体力学仿真技术对汽车的空气动力学性能进行模拟和分析。
通过优化车身外形和风道设计,可以降低车辆的风阻系数,提高汽车的燃油经济性和行驶稳定性。
4. 声学分析:通过CAE的声学分析技术,可以对汽车的内部和外部噪声进行模拟和分析。
通过优化车辆的隔音材料和噪声控制装置,可以提高车辆的乘坐舒适性和降低噪声污染。
5. 热流分析:CAE可以通过热流分析技术对汽车的冷却系统和排气系统进行模拟和分析,以评估其热性能。
通过优化散热器和风道设计,可以提高车辆的散热效率,保证发动机的正常运行。
二、CAE在汽车设计中的优势1. 提高设计效率:CAE可以通过模拟和分析技术快速评估各种设计方案的性能,避免了传统试验方法的时间和成本消耗。
设计师可以在计算机上进行多次仿真测试,快速找到最优设计方案,提高设计效率。
2. 降低成本:通过CAE的模拟和分析技术,可以在设计阶段就发现和解决潜在的问题,避免了在实际制造阶段才发现的问题,从而降低了开发成本和生产成本。
3. 提高产品质量:CAE可以通过模拟和分析技术对汽车的性能进行全面评估,从而提高产品的质量和可靠性。
CAE技术及其在车辆设计开发中的应用
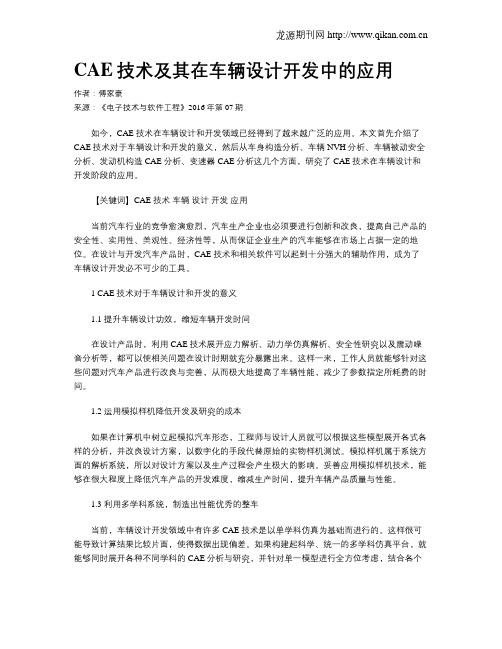
CAE技术及其在车辆设计开发中的应用作者:傅家豪来源:《电子技术与软件工程》2016年第07期如今,CAE技术在车辆设计和开发领域已经得到了越来越广泛的应用。
本文首先介绍了CAE技术对于车辆设计和开发的意义,然后从车身构造分析、车辆NVH分析、车辆被动安全分析、发动机构造CAE分析、变速器CAE分析这几个方面,研究了CAE技术在车辆设计和开发阶段的应用。
【关键词】CAE技术车辆设计开发应用当前汽车行业的竞争愈演愈烈,汽车生产企业也必须要进行创新和改良,提高自己产品的安全性、实用性、美观性、经济性等,从而保证企业生产的汽车能够在市场上占据一定的地位。
在设计与开发汽车产品时,CAE技术和相关软件可以起到十分强大的辅助作用,成为了车辆设计开发必不可少的工具。
1 CAE技术对于车辆设计和开发的意义1.1 提升车辆设计功效,缩短车辆开发时间在设计产品时,利用CAE技术展开应力解析、动力学仿真解析、安全性研究以及震动噪音分析等,都可以使相关问题在设计时期就充分暴露出来。
这样一来,工作人员就能够针对这些问题对汽车产品进行改良与完善,从而极大地提高了车辆性能,减少了参数指定所耗费的时间。
1.2 运用模拟样机降低开发及研究的成本如果在计算机中树立起模拟汽车形态,工程师与设计人员就可以根据这些模型展开各式各样的分析,并改良设计方案,以数字化的手段代替原始的实物样机测试。
模拟样机属于系统方面的解析系统,所以对设计方案以及生产过程会产生极大的影响。
妥善应用模拟样机技术,能够在很大程度上降低汽车产品的开发难度,缩减生产时间,提升车辆产品质量与性能。
1.3 利用多学科系统,制造出性能优秀的整车当前,车辆设计开发领域中有许多CAE技术是以单学科仿真为基础而进行的。
这样很可能导致计算结果比较片面,使得数据出现偏差。
如果构建起科学、统一的多学科仿真平台,就能够同时展开各种不同学科的CAE分析与研究,并针对单一模型进行全方位考虑,结合各个学科之间的相互影响及作用,生动而形象地模拟出车辆运作的过程、形态,提高车辆产品的制作精度与可靠性。
CAE结构优化在汽车轻量化开发中的作用

CAE结构优化在汽车轻量化开发中的作用CAE(计算机辅助工程)结构优化在汽车轻量化开发中扮演着至关重要的角色。
为了满足环保要求和节能要求,汽车制造商越来越注重轻量化设计,以降低车辆重量、提高燃油效率和减少尾气排放。
CAE结构优化技术能够帮助汽车制造商实现这些目标,并在新产品开发过程中提供重要的支持。
CAE结构优化是利用计算机模拟技术,通过分析和优化设计,以对汽车车身结构进行减重和优化的过程。
它可以用来评估不同材料和设计选择对车辆性能和结构强度的影响,并找到最佳的设计方案。
CAE结构优化可以帮助汽车制造商优化车身结构。
它可以通过优化设计的方式,减少材料的使用量和重量,从而达到轻量化的目标。
利用CAE技术,汽车制造商可以对车身结构进行仿真分析,通过优化材料分布和几何形状,降低结构的重量,同时满足车辆的安全性能和刚度要求。
CAE结构优化可以提高汽车的燃油效率。
重量是影响燃油效率的重要因素之一,轻量化设计可以显著降低燃料消耗。
CAE结构优化可以通过减少车身重量和降低风阻,降低整车的能耗和燃料消耗。
通过对车辆的流体力学分析和优化,可以设计出更加 aerodynamic 的车身形状,减少空气阻力。
CAE技术还可以通过优化发动机和传动系统的匹配,进一步提高燃油效率。
CAE结构优化可以提高汽车的安全性能。
轻量化设计在不损害车辆强度和刚度的前提下,降低了车身的重量,提高了车辆的安全性能。
CAE技术可以通过仿真分析确定车身的合理材料分布和结构强度,以确保车身在碰撞和冲击时具有足够的刚度和抗变形性能。
利用CAE结构优化,可以减少车辆受损的可能性,提高车辆的安全性能和乘员的保护性。
CAE结构优化还可以加快产品开发的速度和降低开发成本。
传统的车辆设计和测试往往需要大量的物理样机和试验,这不仅费时费力,而且成本较高。
采用CAE结构优化技术后,可以通过计算机模拟来替代物理样机试验,减少试验的次数和成本,缩短产品开发周期。
CAE技术还可以在产品设计的早期阶段进行仿真分析和优化,提前发现问题,减少改动成本。
汽车产品设计制造中CAE技术的运用
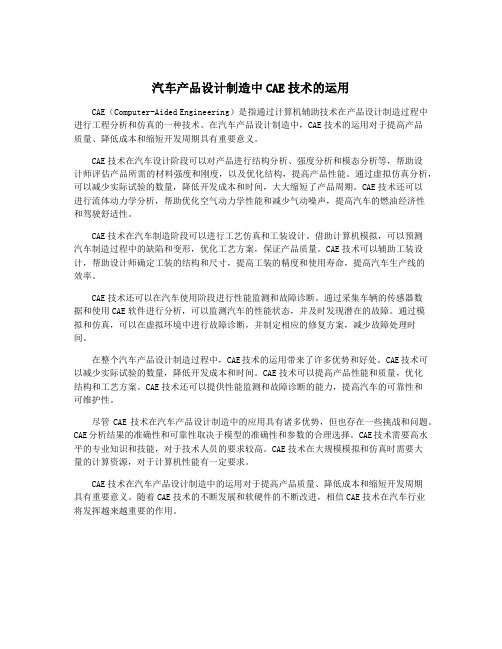
汽车产品设计制造中CAE技术的运用CAE(Computer-Aided Engineering)是指通过计算机辅助技术在产品设计制造过程中进行工程分析和仿真的一种技术。
在汽车产品设计制造中,CAE技术的运用对于提高产品质量、降低成本和缩短开发周期具有重要意义。
CAE技术在汽车设计阶段可以对产品进行结构分析、强度分析和模态分析等,帮助设计师评估产品所需的材料强度和刚度,以及优化结构,提高产品性能。
通过虚拟仿真分析,可以减少实际试验的数量,降低开发成本和时间,大大缩短了产品周期。
CAE技术还可以进行流体动力学分析,帮助优化空气动力学性能和减少气动噪声,提高汽车的燃油经济性和驾驶舒适性。
CAE技术在汽车制造阶段可以进行工艺仿真和工装设计。
借助计算机模拟,可以预测汽车制造过程中的缺陷和变形,优化工艺方案,保证产品质量。
CAE技术可以辅助工装设计,帮助设计师确定工装的结构和尺寸,提高工装的精度和使用寿命,提高汽车生产线的效率。
CAE技术还可以在汽车使用阶段进行性能监测和故障诊断。
通过采集车辆的传感器数据和使用CAE软件进行分析,可以监测汽车的性能状态,并及时发现潜在的故障。
通过模拟和仿真,可以在虚拟环境中进行故障诊断,并制定相应的修复方案,减少故障处理时间。
在整个汽车产品设计制造过程中,CAE技术的运用带来了许多优势和好处。
CAE技术可以减少实际试验的数量,降低开发成本和时间。
CAE技术可以提高产品性能和质量,优化结构和工艺方案。
CAE技术还可以提供性能监测和故障诊断的能力,提高汽车的可靠性和可维护性。
尽管CAE技术在汽车产品设计制造中的应用具有诸多优势,但也存在一些挑战和问题。
CAE分析结果的准确性和可靠性取决于模型的准确性和参数的合理选择。
CAE技术需要高水平的专业知识和技能,对于技术人员的要求较高。
CAE技术在大规模模拟和仿真时需要大量的计算资源,对于计算机性能有一定要求。
CAE技术在汽车产品设计制造中的运用对于提高产品质量、降低成本和缩短开发周期具有重要意义。
汽车产品设计制造中CAE技术的运用
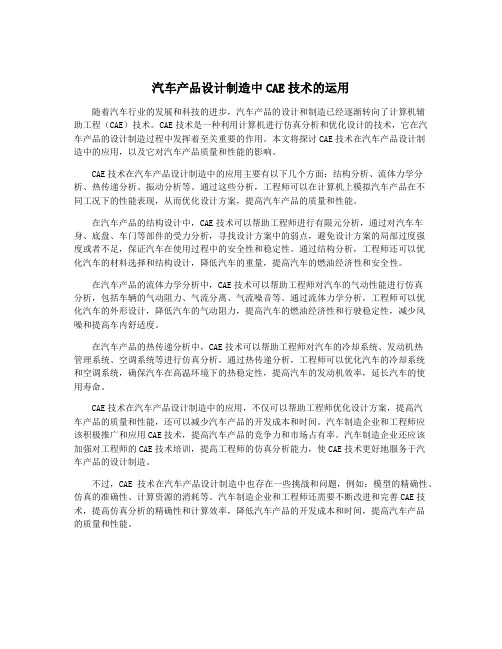
汽车产品设计制造中CAE技术的运用随着汽车行业的发展和科技的进步,汽车产品的设计和制造已经逐渐转向了计算机辅助工程(CAE)技术。
CAE技术是一种利用计算机进行仿真分析和优化设计的技术,它在汽车产品的设计制造过程中发挥着至关重要的作用。
本文将探讨CAE技术在汽车产品设计制造中的应用,以及它对汽车产品质量和性能的影响。
CAE技术在汽车产品设计制造中的应用主要有以下几个方面:结构分析、流体力学分析、热传递分析、振动分析等。
通过这些分析,工程师可以在计算机上模拟汽车产品在不同工况下的性能表现,从而优化设计方案,提高汽车产品的质量和性能。
在汽车产品的结构设计中,CAE技术可以帮助工程师进行有限元分析,通过对汽车车身、底盘、车门等部件的受力分析,寻找设计方案中的弱点,避免设计方案的局部过度强度或者不足,保证汽车在使用过程中的安全性和稳定性。
通过结构分析,工程师还可以优化汽车的材料选择和结构设计,降低汽车的重量,提高汽车的燃油经济性和安全性。
在汽车产品的流体力学分析中,CAE技术可以帮助工程师对汽车的气动性能进行仿真分析,包括车辆的气动阻力、气流分离、气流噪音等。
通过流体力学分析,工程师可以优化汽车的外形设计,降低汽车的气动阻力,提高汽车的燃油经济性和行驶稳定性,减少风噪和提高车内舒适度。
在汽车产品的热传递分析中,CAE技术可以帮助工程师对汽车的冷却系统、发动机热管理系统、空调系统等进行仿真分析。
通过热传递分析,工程师可以优化汽车的冷却系统和空调系统,确保汽车在高温环境下的热稳定性,提高汽车的发动机效率,延长汽车的使用寿命。
CAE技术在汽车产品设计制造中的应用,不仅可以帮助工程师优化设计方案,提高汽车产品的质量和性能,还可以减少汽车产品的开发成本和时间。
汽车制造企业和工程师应该积极推广和应用CAE技术,提高汽车产品的竞争力和市场占有率。
汽车制造企业还应该加强对工程师的CAE技术培训,提高工程师的仿真分析能力,使CAE技术更好地服务于汽车产品的设计制造。
整车NVH性能开发中的CAE技术综述

整车NVH性能开发中的CAE技术综述一、本文概述随着汽车工业的飞速发展,消费者对汽车品质的要求日益提高,整车的NVH(Noise, Vibration, and Harshness,即噪声、振动与声振粗糙度)性能已成为评价汽车品质的重要指标。
为了满足市场的需求和提升产品竞争力,整车NVH性能开发显得尤为关键。
在这个过程中,计算机辅助工程(CAE)技术以其高效、精准的特点,成为了NVH性能开发中不可或缺的工具。
本文旨在对整车NVH性能开发中的CAE技术进行全面综述。
我们将对NVH性能的重要性和影响因素进行简要介绍,以便更好地理解CAE技术在NVH性能开发中的应用背景。
接着,我们将重点分析CAE 技术在整车NVH性能开发中的应用现状,包括其在噪声控制、振动分析和声振粗糙度优化等方面的具体应用。
我们还将探讨CAE技术在NVH性能开发中的优势和局限性,以及未来可能的发展方向。
通过本文的综述,我们期望能够为从事整车NVH性能开发的工程师和研究人员提供有益的参考和启示,推动CAE技术在整车NVH性能开发中的进一步应用和发展。
二、NVH性能开发概述NVH(Noise, Vibration, and Harshness)性能是评价汽车乘坐舒适性的重要指标,涵盖了车内噪音、振动以及冲击等感觉。
随着消费者对汽车舒适性要求的日益提高,NVH性能的开发和优化在整车开发中占据了越来越重要的地位。
NVH性能开发不仅涉及到车辆设计、制造、试验等多个环节,还涵盖了声学、振动理论、材料科学等多个学科领域。
在整车NVH性能开发中,CAE(Computer-Aided Engineering)技术以其高效、精确的特点,成为了不可或缺的工具。
CAE技术可以对车辆的NVH性能进行仿真分析和预测,帮助工程师在车辆设计阶段就发现并解决潜在的NVH问题,避免了后期物理样车试验的繁琐和高昂成本。
同时,CAE技术还可以对不同的设计方案进行快速比较和优化,提高了整车的NVH性能开发效率。
汽车产品设计制造中CAE技术的运用
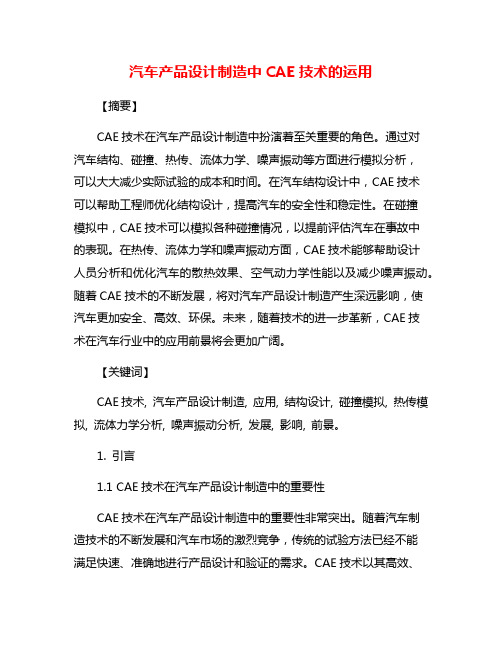
汽车产品设计制造中CAE技术的运用【摘要】CAE技术在汽车产品设计制造中扮演着至关重要的角色。
通过对汽车结构、碰撞、热传、流体力学、噪声振动等方面进行模拟分析,可以大大减少实际试验的成本和时间。
在汽车结构设计中,CAE技术可以帮助工程师优化结构设计,提高汽车的安全性和稳定性。
在碰撞模拟中,CAE技术可以模拟各种碰撞情况,以提前评估汽车在事故中的表现。
在热传、流体力学和噪声振动方面,CAE技术能够帮助设计人员分析和优化汽车的散热效果、空气动力学性能以及减少噪声振动。
随着CAE技术的不断发展,将对汽车产品设计制造产生深远影响,使汽车更加安全、高效、环保。
未来,随着技术的进一步革新,CAE技术在汽车行业中的应用前景将会更加广阔。
【关键词】CAE技术, 汽车产品设计制造, 应用, 结构设计, 碰撞模拟, 热传模拟, 流体力学分析, 噪声振动分析, 发展, 影响, 前景。
1. 引言1.1 CAE技术在汽车产品设计制造中的重要性CAE技术在汽车产品设计制造中的重要性非常突出。
随着汽车制造技术的不断发展和汽车市场的激烈竞争,传统的试验方法已经不能满足快速、准确地进行产品设计和验证的需求。
CAE技术以其高效、低成本、可重复性等优势,成为汽车产品设计制造过程中不可或缺的重要工具。
CAE技术可以在设计初期就进行虚拟仿真,通过对汽车结构、碰撞、热传、流体力学等方面进行分析和验证,为设计师提供科学依据和方向,避免了传统试验中可能出现的时间、成本、资源等方面的浪费。
CAE技术可以帮助设计团队快速地进行优化设计,减少试验和修改次数,缩短产品开发周期,提高产品质量和市场竞争力。
CAE技术还可以有效降低产品的研发成本,提高研发效率,提升企业的技术创新能力和核心竞争力。
1.2 CAE技术的定义和作用CAE技术(Computer-Aided Engineering)是指利用计算机技术和软件工具进行工程设计和分析的一种方法。
它包括了结构分析、碰撞模拟、热传模拟、流体力学分析、噪声振动分析等多个方面,能够帮助工程师在产品设计制造过程中进行更加准确、高效和经济的工作。
07-CAE在乘用轿车NVH设计开发及优化中的应用[1]
![07-CAE在乘用轿车NVH设计开发及优化中的应用[1]](https://img.taocdn.com/s3/m/904509ec4afe04a1b071de0f.png)
第四届中国 CAE 工程分析技术年会论文集CAE 在汽车 NVH 设计开发及优化中的应用刘显臣 刘亚彬 周鹂麟 姚俊贤(北京希艾益科技有限公司 北京市大兴区亦庄东工业区科创三街 7 号 100076) 摘要:本文阐述了在乘用轿车开发过程中,如何应用 CAE 分析技术提高整车的 NVH 性能,并运用 CAE 技术对 某乘用轿车进行了结构分析与优化设计。
首先,用 CDH/AMLS 软件结合 NASTRAN 软件计算了车体及车室内流体 固有模态,运用流固耦合技术获得激励下的车体振动及车室内声学特性结果,用 CDH/VAO 软件对车身结构不 合理之处进行了优化,实现了满足轻量化要求的最佳 NVH 性能。
关键词:CAE NVH CDH 优化 有限元法 汽车1 综述相对于 CAE 在车身强度、刚度领域内的应用,NVH 的 CAE 技术起步比较晚,NVH 的建模方 法以及计算方法还处于摸索阶段。
但随着计算机的能力及容量的越来越强大,计算结果的精 度越来越准确,计算方法越来越科学性,CAE 在汽车的 NVH 开发设计当中所发挥的作用也越来 越大。
在汽车开发设计的初期,就已经开始了 NVH 的各项规划,甚至在样车完成之前或设计 图纸完成之前,通过对现有车型的对比,就可以预先得到新开发车型的 NVH 性能指标,并在 此基础上,对设计及制造的各个环节加以优化及完善。
无论是从设计成本上,还是从开发周 期上考虑,都为车厂更快、更好地开发出新一代车型来提供了强有力的保障。
可以预测,NVH 的 CAE 技术,在汽车设计开发及改进领域内的应用会越来越广泛,而其本身也会越来越成熟, [1,2] 成为人们进行汽车设计开发所不可或缺的工具 。
2 模态分析对白车身进行模态分析,求得结构的固有频率和振型,从而了解结构的动态特性。
获得 车身的模态有试验和有限元计算两种方法。
而在样车制造出来这前,有限元法是最常用的一 种方法,对于一名经验丰富的 CAE 工程师来说,利用有限元法计算得到的车身模态值,与试 [1] 验测试结果相比,可以控制 5%的误差范围内 。
汽车产品设计制造中CAE技术的运用

汽车产品设计制造中CAE技术的运用随着汽车行业的快速发展,汽车产品设计制造技术也在不断创新和改进。
计算机辅助工程(CAE)技术的应用已经成为汽车产品设计与制造的重要工具。
CAE技术通过模拟和分析汽车产品的性能,不仅可以提高设计质量和效率,还可以降低成本和周期。
本文将对汽车产品设计制造中CAE技术的运用进行详细分析。
汽车产品设计中的CAE技术应用。
在汽车产品设计阶段,CAE技术可以用于结构分析、疲劳分析、碰撞模拟、声学分析等方面。
通过CAE技术可以对汽车车身、底盘、发动机、零部件等进行详细的强度分析和优化设计,确保产品的安全性和稳定性。
还可以进行碰撞模拟,预测汽车在碰撞事故中的受力情况,为汽车的 pass 故性能提供重要参考。
声学分析可以有效地降低汽车的噪音和振动,提高乘坐舒适性。
CAE技术在汽车产品设计阶段的应用,可以辅助工程师快速高效地完成设计和验证工作,提高设计质量和效率。
CAE技术还可以在汽车产品的性能优化和新产品开发中发挥重要作用。
通过CAE技术可以对汽车产品的整体性能进行综合分析和优化设计,确保产品在安全性、燃油经济性、乘坐舒适性等方面达到最佳状态。
还可以对新产品的技术方案进行仿真验证,加速产品的研发和上市进程。
CAE技术的应用不仅可以提高汽车产品的市场竞争力,还可以降低产品的开发成本和风险。
CAE技术在汽车产品设计制造中的运用不断拓展和深化。
通过CAE技术可以对汽车产品的设计、制造和性能进行全面分析和优化,提高产品的质量和效率,降低成本和周期。
随着计算机技术和仿真技术的不断发展,相信CAE技术在汽车行业的应用前景将更加广阔。
汽车企业应积极引进和应用CAE技术,不断提升自身的设计制造能力和市场竞争力。
政府部门和科研机构也应加大对CAE技术的研发和推广力度,为汽车行业的发展提供更多的支持与保障。
相信在CAE技术的推动下,汽车产品的设计制造水平将迎来新的飞跃。
汽车产品设计制造中CAE技术的运用

汽车产品设计制造中CAE技术的运用随着现代科技的不断发展,汽车产业也在不断进行创新和改革。
在汽车产品设计和制造过程中,计算机辅助工程(CAE)技术的应用已经成为了不可或缺的一部分。
CAE技术是指将计算机技术应用于工程领域,通过数值模拟、分析和优化来辅助产品的设计和制造。
本文将对汽车产品设计制造中CAE技术的运用进行探讨。
CAE技术在汽车产品设计中的应用是非常广泛的。
在汽车产品设计的初期阶段,工程师可以利用CAE软件进行各种仿真分析,提前预测产品性能和行为,从而提前发现潜在的问题并进行改进。
在汽车车身结构设计中,CAE技术可以帮助工程师进行强度、刚度、疲劳寿命等方面的分析,从而确保车身结构的安全性和稳定性。
CAE技术还可以应用于汽车动力系统设计、悬挂系统设计、乘坐舒适性分析等方面,为汽车设计提供全面的技术支持。
CAE技术在汽车产品制造中的应用也是十分重要的。
在汽车产品的制造过程中,工程师可以利用CAE技术进行制造工艺的仿真模拟,帮助优化制造过程并提高生产效率。
在汽车车身冲压工艺中,CAE技术可以模拟车身冲压过程,分析变形情况并优化冲压模具设计,以降低成本并提高冲压质量。
CAE技术还可以用于汽车焊接工艺、涂装工艺、装配工艺等方面的仿真分析,为汽车制造提供科学的技术支持。
CAE技术还可以在汽车产品的性能优化和节能环保方面发挥重要作用。
通过CAE技术的辅助,工程师可以对汽车产品进行全面的性能分析和优化设计,以提高产品的性能和可靠性。
在汽车发动机设计中,CAE技术可以进行燃烧过程模拟、流场分析等,帮助工程师优化燃烧室结构和气缸排列方式,从而提高发动机的燃烧效率和动力性能。
CAE技术还可以应用于汽车空气动力学优化、轮胎滚动阻力优化、混合动力系统优化等方面,帮助汽车产品实现节能环保的目标。
CAE结构优化在汽车轻量化开发中的作用
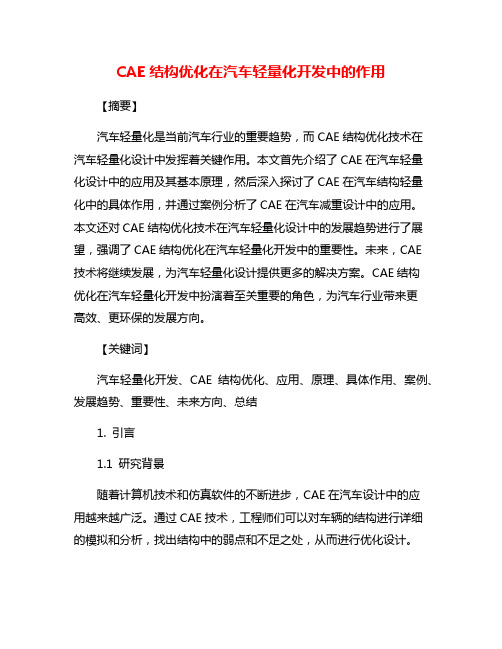
CAE结构优化在汽车轻量化开发中的作用【摘要】汽车轻量化是当前汽车行业的重要趋势,而CAE结构优化技术在汽车轻量化设计中发挥着关键作用。
本文首先介绍了CAE在汽车轻量化设计中的应用及其基本原理,然后深入探讨了CAE在汽车结构轻量化中的具体作用,并通过案例分析了CAE在汽车减重设计中的应用。
本文还对CAE结构优化技术在汽车轻量化设计中的发展趋势进行了展望,强调了CAE结构优化在汽车轻量化开发中的重要性。
未来,CAE技术将继续发展,为汽车轻量化设计提供更多的解决方案。
CAE结构优化在汽车轻量化开发中扮演着至关重要的角色,为汽车行业带来更高效、更环保的发展方向。
【关键词】汽车轻量化开发、CAE结构优化、应用、原理、具体作用、案例、发展趋势、重要性、未来方向、总结1. 引言1.1 研究背景随着计算机技术和仿真软件的不断进步,CAE在汽车设计中的应用越来越广泛。
通过CAE技术,工程师们可以对车辆的结构进行详细的模拟和分析,找出结构中的弱点和不足之处,从而进行优化设计。
CAE结构优化的基本原理是通过数学建模和计算分析,找出结构中的瓶颈部位,并通过优化算法对结构进行调整,达到最优设计方案。
在汽车结构轻量化中,CAE可以帮助工程师们优化车身和底盘结构,减少不必要的材料使用,提高车辆的整体强度和刚性。
CAE还可以对车辆的各个部位进行局部优化,如减少零部件的重量和材料厚度,提高零部件的性能和可靠性。
通过CAE技术,汽车制造商可以在设计阶段就对车辆进行减重设计,实现轻量化目标。
一些知名的汽车品牌已经成功利用CAE技术进行轻量化设计,并取得了显著的节能和性能提升效果。
随着CAE技术的不断发展,未来在汽车轻量化设计中的应用前景将更加广阔。
通过不断改进优化算法和仿真模型,提高预测精度和优化效率,CAE结构优化技术将在汽车轻量化开发中发挥越来越重要的作用。
1.2 研究目的研究目的是为了探讨CAE结构优化在汽车轻量化开发中的作用,通过分析其基本原理和具体作用,揭示CAE在汽车结构轻量化设计中的重要性和优势。
CAE在乘用轿车NVH设计开发与优化中的应用
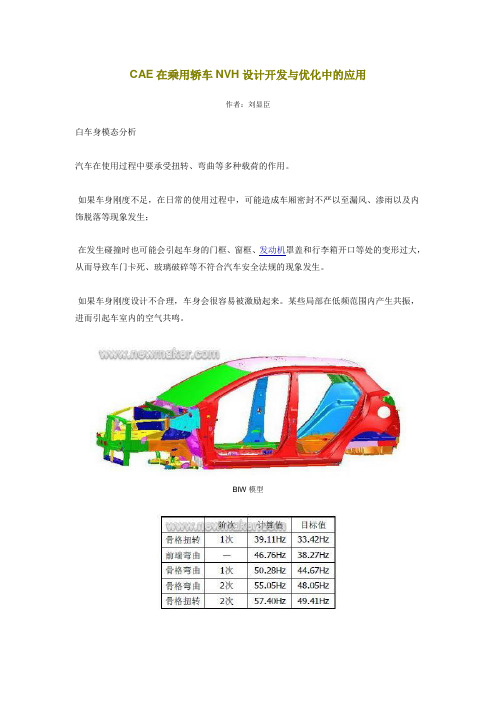
CAE在乘用轿车NVH设计开发与优化中的应用作者:刘显臣白车身模态分析汽车在使用过程中要承受扭转、弯曲等多种载荷的作用。
·如果车身刚度不足,在日常的使用过程中,可能造成车厢密封不严以至漏风、渗雨以及内饰脱落等现象发生;·在发生碰撞时也可能会引起车身的门框、窗框、发动机罩盖和行李箱开口等处的变形过大,从而导致车门卡死、玻璃破碎等不符合汽车安全法规的现象发生。
·如果车身刚度设计不合理,车身会很容易被激励起来。
某些局部在低频范围内产生共振,进而引起车室内的空气共鸣。
BIW模型白车身各阶模态振型车身振动灵敏度分析车身结构振动灵敏度的评价车身是噪声与振动的传递通道,各种噪声与振动都会通过车身传入到车室内。
汽车上大多数部件都是直接与车身相连接,如排气系统、传动轴、悬架系统、发动机等。
这些系统的振动与噪声会传递到车身。
车身的结构模态频率一定要与之相连的系统的模态频率分开,否则两个系统之间会发生共振,比如排气系统的模态频率就不能与车身模态频率一样。
在车身设计时,结构振动的灵敏度非常重要。
与车身相连接的系统要尽可能地安装在车身灵敏度低的地方。
车身设计优劣的评价车身的设计对结构传播噪声十分重要。
车外各种激厉引起的结构振动和结构噪声的特性直接表明车身设计的优劣。
好的车身设计对各支撑点的激励灵敏度低,即激振力引起的振动和噪声的响应值低。
计算结果(前悬架中心激励)计算结果(发动机悬置中心激励)计算结果(变速器悬置中心激励)计算结果(后悬置中心激励)车室内音响灵敏度分析NASTRAN流体·结构耦合分析车室内音响模型固有模态分析车室内音响模型固有模态分析音响灵敏度分析结果(前悬架中心激励)音响灵敏度分析结果(发动机悬置安装点激励)音响灵敏度分析结果(变速器悬置安装点激励)音响灵敏度分析结果(后悬置安装点激励)音响灵敏度结果评价车室内噪声优化流-固耦合分析:声学有限元法可以根据车室内空间声学模型和车身结构模型求得车室内声学模态频率及其声模态,以及车身结构的模态频率及其振动模态。
CAE分析在汽车白车身NVH性能开发中的应用
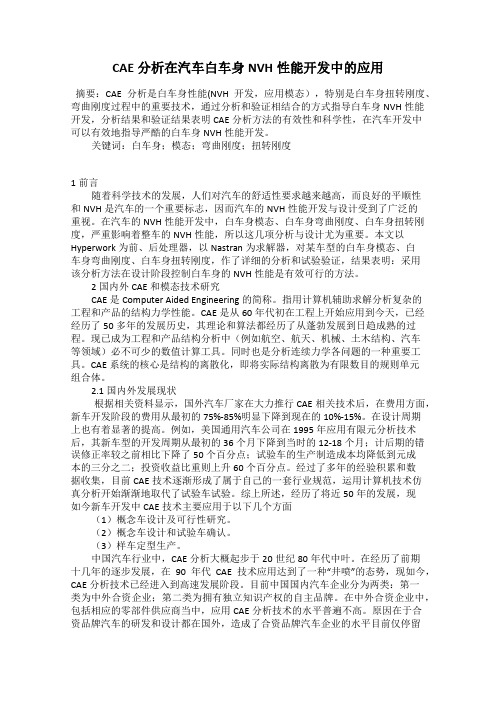
CAE分析在汽车白车身NVH性能开发中的应用摘要:CAE分析是白车身性能(NVH开发,应用模态),特别是白车身扭转刚度、弯曲刚度过程中的重要技术,通过分析和验证相结合的方式指导白车身NVH性能开发,分析结果和验证结果表明CAE分析方法的有效性和科学性,在汽车开发中可以有效地指导严酷的白车身NVH性能开发。
关键词:白车身;模态;弯曲刚度;扭转刚度1前言随着科学技术的发展,人们对汽车的舒适性要求越来越高,而良好的平顺性和NVH是汽车的一个重要标志,因而汽车的NVH性能开发与设计受到了广泛的重视。
在汽车的NVH性能开发中,白车身模态、白车身弯曲刚度、白车身扭转刚度,严重影响着整车的NVH性能,所以这几项分析与设计尤为重要。
本文以Hyperwork为前、后处理器,以Nastran为求解器,对某车型的白车身模态、白车身弯曲刚度、白车身扭转刚度,作了详细的分析和试验验证,结果表明:采用该分析方法在设计阶段控制白车身的NVH性能是有效可行的方法。
2国内外CAE和模态技术研究CAE是Computer Aided Engineering的简称。
指用计算机辅助求解分析复杂的工程和产品的结构力学性能。
CAE是从60年代初在工程上开始应用到今天,已经经历了50多年的发展历史,其理论和算法都经历了从蓬勃发展到日趋成熟的过程。
现已成为工程和产品结构分析中(例如航空、航天、机械、土木结构、汽车等领域)必不可少的数值计算工具。
同时也是分析连续力学各问题的一种重要工具。
CAE系统的核心是结构的离散化,即将实际结构离散为有限数目的规则单元组合体。
2.1国内外发展现状根据相关资料显示,国外汽车厂家在大力推行CAE相关技术后,在费用方面,新车开发阶段的费用从最初的75%-85%明显下降到现在的10%-15%。
在设计周期上也有着显著的提高。
例如,美国通用汽车公司在1995年应用有限元分析技术后,其新车型的开发周期从最初的36个月下降到当时的12-18个月;计后期的错误修正率较之前相比下降了50个百分点;试验车的生产制造成本均降低到元成本的三分之二;投资收益比重则上升60个百分点。
CAE优化技术在汽车概念设计中的应用
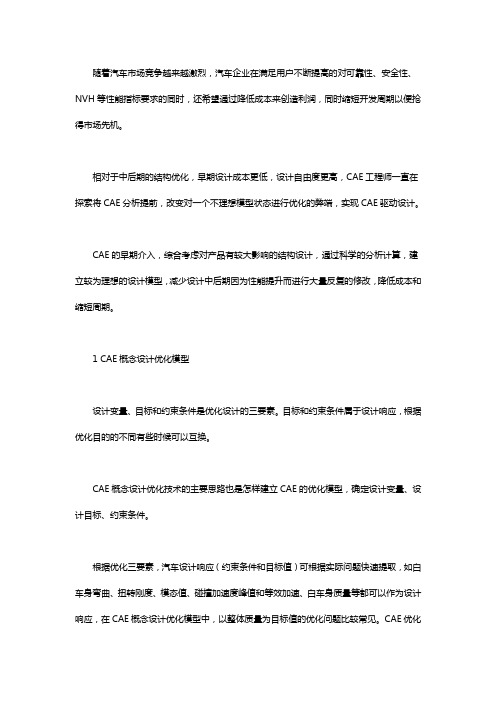
随着汽车市场竞争越来越激烈,汽车企业在满足用户不断提高的对可靠性、安全性、NVH等性能指标要求的同时,还希望通过降低成本来创造利润,同时缩短开发周期以便抢得市场先机。
相对于中后期的结构优化,早期设计成本更低,设计自由度更高,CAE工程师一直在探索将CAE分析提前,改变对一个不理想模型状态进行优化的弊端,实现CAE驱动设计。
CAE的早期介入,综合考虑对产品有较大影响的结构设计,通过科学的分析计算,建立较为理想的设计模型,减少设计中后期因为性能提升而进行大量反复的修改,降低成本和缩短周期。
1 CAE概念设计优化模型设计变量、目标和约束条件是优化设计的三要素。
目标和约束条件属于设计响应,根据优化目的的不同有些时候可以互换。
CAE概念设计优化技术的主要思路也是怎样建立CAE的优化模型,确定设计变量、设计目标、约束条件。
根据优化三要素,汽车设计响应(约束条件和目标值)可根据实际问题快速提取,如白车身弯曲、扭转刚度、模态值、碰撞加速度峰值和等效加速、白车身质量等都可以作为设计响应,在CAE概念设计优化模型中,以整体质量为目标值的优化问题比较常见。
CAE优化技术关键点是设置及选取设计变量,本文将介绍两种提取设计变量的方法,参数化建模法和网格变形过程录制法。
2 概念设计阶段优化流程传统研发流程存在以下问题:(1)概念设计方案主要依靠工程师的经验来确定。
(2)设计早期阶段缺少对产品性能有较大影响的结构设计方面的考虑。
(3)设计中后期进行大量反复的修改,带来成本和周期的问题。
随着研发的推进,零部件逐步开始进行开模、招标,设计自由度越来越小,优化更改方案的成本也越来越高,受到周期、成本、空间等限制,很多优化方案不能实施。
研发成本模型如图1所示。
图1 研发成本模型由图1可知,相对于中后期的结构优化,早期设计成本更低,设计自由度更高,概念设计阶段引入CAE性能评估优化,将CAE软件分析提前,改变对一个不理想模型状态进行优化的弊端,实现CAE驱动设计。
CAE在汽车NVH方面的应用

一、CAE与FEM 二、CAE在汽车NVH方面的应用 三、我研究生阶段的工作
一、 CAE与FEM
1、CAE概念
Computer Aided Engineering, 即计算机辅助工程。用计算机对 工程和产品的功能、性能、安全可靠性等进行计算、分析、优化设计, 对其未来的工作状态和运行行为进行模拟仿真,以及早发现设计缺陷, 改进和优化设计方案,证实未来工程/产品的各项性能是否达到设计指 标。
Excellent for high order quads, good for near parallelogram linear quads, poor for non-parallelogram linear quads Mesh generation method(s) Unstructured (“free”) mesh of quads is possible for any area, but may contain a few triangles Structured mesh of quads is possible in 3 or 4-sided areas only
实体单元
流体单元
…
…
一、 CAE与FEM
单元选择准则
准则
:
• 在结构分析中,结构的应力状态决定单元类型的选择。 • 选择维数最低的单元去获得预期的结果 (尽量做到能选择点而 不选择线,能选择线而不选择平面,能选择平面而不选择壳, 能选择壳而不选择三维实体). • 对于复杂结构,应当考虑建立两个或者更多的不同复杂程度的 模型。你可以建立简单模型,对结构承载状态或采用不同分析 选项作实验性探讨。 • 在许多情况下,相同的网格划分,采用更高阶类型的单元可以 得到更好的计算结果,但计算时间会增加。
- 1、下载文档前请自行甄别文档内容的完整性,平台不提供额外的编辑、内容补充、找答案等附加服务。
- 2、"仅部分预览"的文档,不可在线预览部分如存在完整性等问题,可反馈申请退款(可完整预览的文档不适用该条件!)。
- 3、如文档侵犯您的权益,请联系客服反馈,我们会尽快为您处理(人工客服工作时间:9:00-18:30)。
车身振动灵敏度分析
计算结果(发动机悬置中心激励)
后席SR右
X向加振_响应
STG 12时方向
X向加振_响应
Inertance (m/s 2 /N)
Y向加振_响应 Z向加振_响应
Inertance (m/s /N)
Y向加振_响应 Z向加振_响应
驾驶席脚下
Inertance (m/s /N)
X向加振_响应 Inertance (m/s 2 /N) Y向加振_响应 Z向加振_响应
X向加振 Y向加振 Z向加振 Target Frequence (Hz)
前席中央音响感度-TM Mtt加振
后席中央音响感度-TM Mt加振
音响感度 (dB-A)
音响感度 (dB-A)
X向加振 Y向加振 Z向加振 Target Frequence (Hz)
X向加振 Y向加振 Z向加振 Target Frequence (Hz)
前席中央音响感度-Roll Mt加振
后席中央音响感度-Roll Mt加振
音响感度 (dB-A)
音响感度 (dB-A)
X向加振 Y向加振 Z向加振 Target Frequence (Hz)
X向加振 Y向加振 Z向加振 Target Frequence (Hz)
车室内音响灵敏度分析
音响灵敏度结果评价
车身振动灵敏度分析
ISO 2631 和 ISO 2631-1标准中,列出了人体舒适 程度对振动大小的主观统计数据,如下表所示:
振动加速度大小(m/s2) <0.315 0.315~0.63 0.5~1 0.8~1.6 1.25~2.5 >2
人体舒适程度 感觉不到不舒服 有一点不舒服 比较不舒服 不舒服 非常不舒服 极度不舒服
车身结构振动灵敏度的评价
评价位置 STG FLOOR 评价标准 0.35以下 0.15以下 评价结果 ○ ○
车室内音响灵敏度分析
NASTRAN流体·结构耦合分析
音响固有模态值
频率值 1阶模态 2阶模态 3阶模态 4阶模态 5阶模态 6阶模态 7阶模态 8阶模态 9阶模态 10阶模态 62.9 104.7 116.2 138.3 149.2 151.4 178.5 182.5 193.3 196.9
响应点:后席窗边 加振点:Front sus tower
车室内噪声优化
板件对车室内声压的贡献量分析:
响应点:前席窗边 加振点:ROLL Mt加振
车室内噪声优化
板件对车室内声压的贡献量分析:
响应点:后席窗边 加振点: ROLL Mt加振
车室内噪声优化
板件对车室内声压的贡献量分析:
响应点:前席窗边 加振点:前炮塔
BIW模型
骨格扭转 前端弯曲 骨格弯曲 骨格弯曲 骨格扭转
1次 — 1次 2次 2次
车身振动灵敏度分析
车身是噪声与振动的传递通道,各种噪声与振动都会通过 车身传入到车室内。衡量车身结构振动和噪声特性的常用 指标是车身振动和声学灵敏度。在车身设计时,结构振动 的灵敏度非常重要。与车身相连接的系统要尽可能地安装 在车身灵敏度低的地方。 车身设计优劣的评价 车身的设计对结构传播噪声十分重要。车外各种激厉引起 的结构振动和结构噪声的特性直接表明车身设计的优劣。 好的车身设计对各支撑点的激励灵敏度低,即激振力引起 的振动和噪声的响应值低。 车内噪声是车身声学灵敏度与激励力的乘积。为降低车内 噪声,需要从降低车身声学灵敏度和激励力及激励力的传 递等几个方面入手。
Y向加振_响应 Z向加振_响应
I n e r t a n c e ( m / s 2/ N )
Y向加振_响应 Z向加振_响应
驾驶席脚下
Inertance (m/s2/N)
I ner tan ce (m/ s 2 / N)
X向加振_响应 Y向加振_响应 Z向加振_响应
驾驶席SR左
X向加振_响应 Y向加振_响应 Z向加振_响应
车室内噪声优化
使用软件:CDH/VAO
CDH/VAO是一款用于解决大型结构动力学分析的交互式工程软件。用户可以借助此软件快速 地评估目标设计值变化引起的结构声学响应的变化,也可以自动地预测出设计参数的范围,以便 进行结构声学优化。此软件利用模态修改方法进行结构优化,相比传统的模态方法更为有效和省 时。
2
X向加振_响应 Y向加振_响应 Z向加振_响应
Inertance (m/s /N)
Y向加振_响应 Z向加振_响应
2
驾驶席脚下 Inertance (m/s /N)
/N)
2 X向加振_响应 Y向加振_响应 Z向加振_响应
驾驶席SR左
X向加振_响应 Y向加振_响应 Z向加振_响应
2
Inertance (m/s
车室内噪声优化
振型分析:156Hz
车室内噪声优化
振型分析:180Hz
车室内噪声优化
设计更改方案 更改内容之二 更改内容之一
更改内容之三
车室内噪声优化
改良后的效果
前席窗边音响感度-Fr_Tower加振
后席窗边音响感度-Fr_Tower加振
音响感度 (dB-A)
音响感度 (dB-A)
X向加振 Y向加振 Z向加振 Target Frequence (Hz)
X向加振 Y向加振 Z向加振 Target Frequence (Hz)
X向加振 Y向加振 Z向加振 Target Frequence (Hz)
车室内音响灵敏度分析
音响灵敏度分析结果(发动机悬置安装点激励)
前席窗边音响感度-Eng Mt加振 后席窗边音响感度-Eng Mt加振
音响感度 (dB-A)
①划分模型:约10000个子 结构树 ②使用子结构模态代替全 局模态
计算流程
AMLS执行步骤如下: ①NASTRAN生成矩阵 ②将模型划分子结构 ③子结构模态求解 ④求解得到全局特征值数据 ⑤扩展到全局特征值,写入文件
车身振动灵敏度分析过程
求解器:NX/NASTRAN+CDH/AMLS
计算用模型 要素数 节点数 刚体要素数 结构模态 流体模态 加振频率 484419 482356 56604 0~150Hz 0~200Hz 5~105Hz SGI Origin 2000 CPU数:32个 内存:2Gbyte/1CPU
X向加振 Y向加振 Z向加振 Target Frequence (Hz)
车室内音响灵敏度分析
音响灵敏度分析结果(变速器悬置安装点激励)
前席窗边音响感度-TM Mt加振
后席窗边音响感度-TM Mt加振
音响感度 (dB-A)
音响感度 (dB-A)
X向加振 Y向加振 Z向加振 Target Frequence (Hz)
VAO可以提供以下分析: ① ② 使用模态修正方法进行快速的频率响应分析 能量分析 复杂的应变能和动能分析 等效辐射能量分析 ③ 声学分析 板件贡献量分析 ④ 瞬态分析 直接的FFT分析 对非线性单元的支持 支持NASTRAN的TLOAD(时域)数据输入
车室内噪声优化
板件对车室内声压的贡献量分析:
X向加振_响应 Y向加振_响应 Z向加振_响应
2
驾驶席SR左
2
车身振动灵敏度分析
计算结果(变速器悬置中心激励)
后席SR右 /N)
X向加振_响应 Y向加振_响应 Z向加振_响应
STG 12时方向 I n e r t a n c e ( m / s 2/ N ) X向加振_响应 Y向加振_响应 Z向加振 Target Frequence (Hz)
X向加振 Y向加振 Z向加振 Target Frequence (Hz)
前席中央音响感度-Eng Mt加振
后席中央音响感度-Eng Mt加振
音响感度 (dB-A)
音响感度 (dB-A)
X向加振 Y向加振 Z向加振 Target Frequence (Hz)
前炮塔中心(右) 激振力 发动机悬置 变速器悬置 后悬置
1N
X、Y、Z三方向
后席SR、左 后席SR、中 后席SR、右
AMLS软件介绍
AMLS是Automated Multi Level Sub_structure 的简称。它是一款极具工程意义的软件,它能够在保 证精度的前提下,大幅地降低特征值和频率响应计算时间和磁盘空间。 百万个自由度以上的有限元模型,被分解为大约一万个子结构。原模型就按照子结构的特征向量被 转化为一个非常准确有效并便于计算的结构树。
车身结构模型
耦合 (Coupling)
位 置 大 小 前炮塔中心(右)
车室内音响模型
方 向
激振点
发动机悬置安装点 变速器悬置安装点 后悬置安装点 位 置
X、Y、Z三方向
方
向
前席中央 响应点 前席窗边 后席中央 后席窗边 X、Y、Z三方向
车室内音响灵敏度分析
音响灵敏度分析结果(前悬架中心激励)
前席窗边音响感度-Fr_Tower加振 后席窗边音响感度-Fr_Tower加振
CAE在汽车NVH设计开发及优化中的应用
刘显臣
北京CAE
白车身模态分析
白车身模态分析
汽车在使用过程中要承受扭转、弯曲等多种载荷的作用。 如果车身刚度不足,在日常的使用过程中,可能造成车厢密封不严以至漏风、渗雨 以及内饰脱落等现象发生; 在发生碰撞时也可能会引起车身的门框、窗框、发动机罩盖和行李箱开口等处的变 形过大,从而导致车门卡死、玻璃破碎等不符合汽车安全法规的现象发生。 如果车身刚度设计不合理,车身会很容易被激励起来。某些局部在低频范围内产生 共振,进而引起车室内的空气共鸣。 阶次 计算值 39.11Hz 46.76Hz 50.28Hz 55.05Hz 57.40Hz 目标值 33.42Hz 38.27Hz 44.67Hz 48.05Hz 49.41Hz