大高径比铸件挤压铸造技术研究
挤压铸造工艺原理、特点、分类
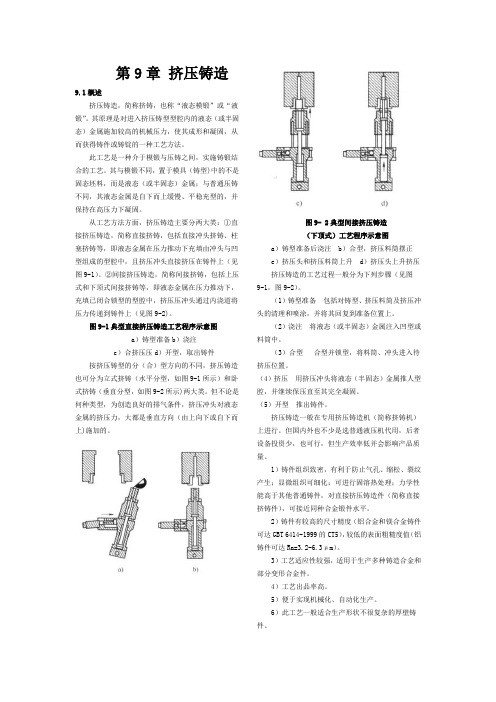
第9章挤压铸造9.1概述挤压铸造,简称挤铸,也称“液态模锻”或“液锻”。
其原理是对进入挤压铸型型腔内的液态(或半固态)金属施加较高的机械压力,使其成形和凝固,从而获得铸件或铸锭的一种工艺方法。
此工艺是一种介于模锻与压铸之间,实施铸锻结合的工艺。
其与模锻不同,置于模具(铸型)中的不是固态坯料,而是液态(或半固态)金属;与普通压铸不同,其液态金属是自下而上缓慢、平稳充型的,并保持在高压力下凝固。
从工艺方法方面,挤压铸造主要分两大类:①直接挤压铸造,简称直接挤铸,包括直接冲头挤铸、柱塞挤铸等,即液态金属在压力推动下充填由冲头与凹型组成的型腔中,且挤压冲头直接挤压在铸件上(见图9-1)。
②间接挤压铸造,简称间接挤铸,包括上压式和下顶式间接挤铸等,即液态金属在压力推动下,充填已闭合锁型的型腔中,挤压压冲头通过内浇道将压力传递到铸件上(见图9-2)。
图9-1典型直接挤压铸造工艺程序示意图a)铸型准备b)浇注c)合挤压压d)开型,取出铸件按挤压铸型的分(合)型方向的不同,挤压铸造也可分为立式挤铸(水平分型,如图9-1所示)和卧式挤铸(垂直分型,如图9-2所示)两大类。
但不论是何种类型,为创造良好的排气条件,挤压冲头对液态金属的挤压力,大都是垂直方向(由上向下或自下而上)施加的。
图9- 2典型间接挤压铸造(下顶式)工艺程序示意图a)铸型准备后浇注 b)合型,挤压料筒摆正e)挤压头和挤压料筒上升 d)挤压头上升挤压挤压铸造的工艺过程一般分为下列步骤(见图9-1,图9-2)。
(1)铸型准备包括对铸型、挤压料简及挤压冲头的清理和喷涂,并将其回复到准备位置上。
(2)浇注将液态(或半固态)金属注入凹型或料筒中。
(3)合型合型并锁型,将料筒、冲头进入待挤压位置。
(4)挤压用挤压冲头将液态(半固态)金属推人型腔,并继续保压直至其完全凝固。
(5)开型推出铸件。
挤压铸造一般在专用挤压铸造机(简称挤铸机)上进行。
但国内外也不少是选普通液压机代用,后者设备投资少,也可行,但生产效率低并会影响产品质量。
挤压铸造
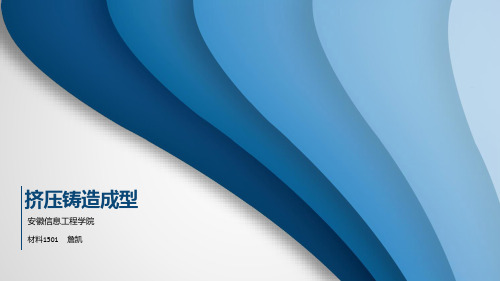
挤压铸造成型
3.在挤压铸造工艺中应用人工神经网络 挤压铸造工艺参数的确定主要靠经验,而且这些参数很难确定,人 工神经网络是一个比较新的学科,在非线性系统、错误诊断、预测、 自适应控制等方面已取得了很大成功。但我国才刚刚起步,应加强 对人工神经网络预测挤压铸造工艺参数的研究。
挤压铸造成型
应用实例:
挤压铸造成型
7.铸型涂料 为了防止铸件黏焊铸型,使铸件能顺利地从型腔中取出,以降低铸件表
面粗糙度,提高铸型的寿命,减缓金属液在加压前的结壳速度,以利于金 属液在压力下充型,在挤压铸型的表面一般都必须喷涂涂料。在挤压铸造 中不能采用涂料层来控制铸件的凝固,因为施加在金属液上的高压将使涂 料层剥落,引起铸件产生夹杂缺陷,为此,采用50μm左右的薄层涂料。。
挤压铸造成型
适用范围:
1、在材料种类方面适用性较广,可用于生产各种类型的合金,如铝合 金、锌合金、铜合金、灰铸铁、球墨铸铁、碳钢、不锈钢等。
2、对于一些复杂且性能上有一定要求的零件,采用挤压铸造合适。 因为挤压铸造既能容易成形,又能保证产品性能的要求。
3、在工件壁厚方面,一般来讲不能太薄,否则将给成形带来困难。
挤压铸造成型
1.工艺原理及特点 (1)工艺原理 将一定量的液体金属(或半固态金属)浇入金属
型腔内,通过冲头以高压(50〜100MPa)作用于液体金属上, 使之充型、成形和结晶凝固,并产生一定塑性形变,从而获得优 质铸件。
(a)熔化
(b)充型
(c)挤压
(d)顶出铸件
挤压铸造成型
(2)工艺特点 适用的材料范围较宽,不仅是普通铸造合金,也适用于高性能的变形合金,
挤压铸造成型
安徽信息工程学院 材料1501 詹凯
目录
挤压铸造工艺简介
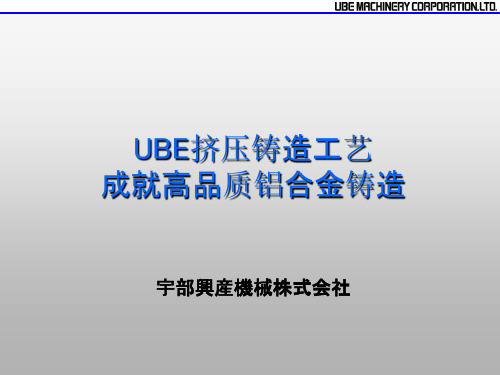
应力 [MPa]
200
180
160
σu=143MPa
140
120
100
80
σu=67MPa
60
普通压铸
40
挤压铸造
20
0
104
105
106
107
108
重复次数(Cycle) [次]
3.挤压铸造工艺的应用实例
3.挤压铸造工艺的应用实例
ABS valve body
压射单元的
YY
小型化
・压射行程
350T
800T
・油缸直径
X 3,250mm 4,100mm
XX
・熔杯直径
Y 2,600mm 3,400mm
・熔杯回倾角度
Z 2,000mm 3,700mm
1.挤压铸造工艺的概要
UBE压铸机的开发历史
昭和 35年
1960年
45年 1970年
55年 1980年
平成 2年 1990年
650
AC4CH挤压铸造 AZ91挤压铸造 600
AZ91普通铸造 550
AC4CH普通铸造
AC4CH熔点: 615℃ AZ91熔点: 595℃
热电偶
0
10
20
30
40
注汤后的时间经过 (sec)
熔杯内温 度测定
2.挤压铸造件的特征
2.挤压铸造品德特征
换挡片内部品质比较/A390合金(ADC14相当)
・射出速度:max. 10 m/s
1.挤压铸造工艺的概要
UBE挤压铸造机的出厂数量
Europe: 38 sets
挤压铸造原理及缺陷分析

挤压铸造原理及缺陷分析挤压铸造技术与传统金属型重力铸造相比区别较大,对于某些铸件的生产有独特优势,然而实际生产中出现的一些铸造缺陷,成因也不同于传统铸造,本文试图从原理和生产实际出发,分析挤压铸造的原理和流程参数,及其铸造常见缺陷,利用技术上的经验和实践提出改进方法,已达到推进该项铸造技术的推广,减少损失。
挤压铸造原理及特点1.1.基本原理挤压铸造又可称为液态模锻,是将金属或合金升温至熔融态,不加处理注入到敞口模具中,立即闭合模具,让液态金属充分流动以充填模具,初步到达制件外部形状,随后施以高压,使温度下降已凝固的外部金属产生塑性变形,而内部的未凝固金属承受等静压,同步发生高压凝固,最后获得制件或毛坯的方法。
由于高压凝固和塑性变形同时存在,制件无缩孔、缩松等缺陷,组织细密,力学性能高于铸造方法,接近或相当锻造方法;无需冒口补缩和最后清理,因而液态金属或合金利用率高,工序简化,为一具有潜在应用前景的新型金属加工工艺。
1.2.挤压铸造的特点挤压铸造的工艺对铸造设备有特殊的要求,并且目前只对部分铸件有较好的效果。
首先,挤压铸造设备,需要提供低速但流量较大的液态金属填充能力,速度约为0.5~3m/s,流量可达1~5kg/s,这样熔融态金属才能平稳地将铸型内气体排出,并填充铸型,随后铸型填满的瞬间(50ms~150ms),应能将铸型内铸造比压提升到60~100MPa,这样合金便能在高压下凝固成型。
由于前述的低速大流量,且挤压铸造内浇道有冒口补缩的作用,内浇道口径较大,且位于铸件最肥厚的部位。
由于上述特点,挤压铸造适合厚壁铸件(10~50mm),但铸件尺寸不宜太大(小于200mm)。
与压铸相同,挤压铸造只可使用脱模剂,不适用保温涂料,故而金属凝固速度极快,达到300~400摄氏度/s,与金属型重力铸造冷却速度相比,达到了其3~5倍,伸长率高于其他铸造方法约2~3倍。
挤压铸造的生产工艺流程以直径190系列的铝活塞为例,介绍挤压铸造的工艺流程,挤压铸造借鉴于压力铸造和模锻工艺,其大体工艺流程为把液态金属直接浇入金属模内。
挤压铸造
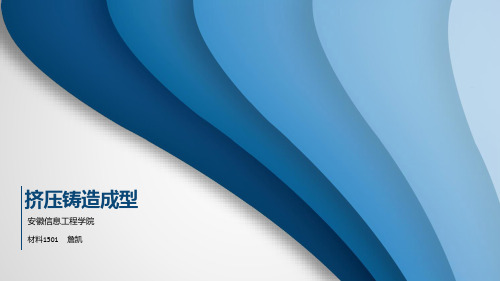
目录
概述 挤压铸造合金的组织和性能 挤压铸造工艺 铸型设计 挤压技术新发展
挤压铸造成型
7.3.1 概述
挤压铸造(Squeeze Casting)也称“液态模(Liquid Metal Forging),这一概念最早出现在1819年的一项英国专利中,第一台 挤压铸造设备1931年诞生在德国,随后挤压铸造在前苏联得到较广 泛的应用,但直到20世纪60年代才开始在北美、欧洲和日本获得应 用。北美压铸协会(NADAC)对挤压铸造的定义为:采用低的充型速 度和最小的扰动,使金属液在高压下凝固,以获得可热处理的高致密 度铸件的铸造工艺。
挤压铸造成型
5.浇注温度 挤压铸造所采用的浇注温度比同种合金的砂型铸造、金属型铸造略低一
些。一般控制在合金液相线以上50~100℃。对形状简单的厚壁实心铸件 可取温度下限;对形状复杂或薄壁铸件应取上限。。
挤压铸造成型
6.温度 模具温度过高或过低都会直接影响铸件质量和模具寿命。模具温度过低, 铸件质量难以得到保证,易产生冷隔和表面裂纹等缺陷。模具温度过高, 容易发生黏模,降低模具寿命,还会使铸件脱模困难。
挤压铸造成型
(3)冲头-柱塞挤压铸造
(a)法兰盘形零件
(b)通孔法兰盘零件
挤压铸造成型
(4)局部加压凝固 对于大型铸件,采用间接挤压铸造工艺时,施加的压力对远离冲头 的部位很难起到压力补缩作用,因此,对这些部位实行局部加压的方 法,以期达到减少该部位缩孔、缩松的目的。
挤压铸造成型
工艺流程:
顶出 制件
中的金属液传递到铸件上。间接挤压铸造工艺中,由于铸件是在已合型闭 锁的型腔中成形,不必精确定量金属液,因而铸件尺寸精度高。但冲头不 直接而是部分地加压于铸件上,加压效果较差。此外,间接挤压工艺采用 了浇注系统,因此金属液利用率较低。此工艺适合于产量大,形状较为复 杂或小型零件的生产,也可用于生产等截面型材。
挤压铸造工艺原理、特点、分类

第9章挤压铸造概述挤压铸造,简称挤铸,也称“液态模锻”或“液锻”。
其原理是对进入挤压铸型型腔内的液态(或半固态)金属施加较高的机械压力,使其成形和凝固,从而获得铸件或铸锭的一种工艺方法。
此工艺是一种介于模锻与压铸之间,实施铸锻结合的工艺。
其与模锻不同,置于模具(铸型)中的不是固态坯料,而是液态(或半固态)金属;与普通压铸不同,其液态金属是自下而上缓慢、平稳充型的,并保持在高压力下凝固。
从工艺方法方面,挤压铸造主要分两大类:①直接挤压铸造,简称直接挤铸,包括直接冲头挤铸、柱塞挤铸等,即液态金属在压力推动下充填由冲头与凹型组成的型腔中,且挤压冲头直接挤压在铸件上(见图9-1)。
②间接挤压铸造,简称间接挤铸,包括上压式和下顶式间接挤铸等,即液态金属在压力推动下,充填已闭合锁型的型腔中,挤压压冲头通过内浇道将压力传递到铸件上(见图9-2)。
图9-1典型直接挤压铸造工艺程序示意图a)铸型准备b)浇注c)合挤压压d)开型,取出铸件按挤压铸型的分(合)型方向的不同,挤压铸造也可分为立式挤铸(水平分型,如图9-1所示)和卧式挤铸(垂直分型,如图9-2所示)两大类。
但不论是何种类型,为创造良好的排气条件,挤压冲头对液态金属的挤压力,大都是垂直方向(由上向下或自下而上)施加的。
图9- 2典型间接挤压铸造(下顶式)工艺程序示意图a)铸型准备后浇注 b)合型,挤压料筒摆正e)挤压头和挤压料筒上升 d)挤压头上升挤压挤压铸造的工艺过程一般分为下列步骤(见图9-1,图9-2)。
(1)铸型准备包括对铸型、挤压料简及挤压冲头的清理和喷涂,并将其回复到准备位置上。
(2)浇注将液态(或半固态)金属注入凹型或料筒中。
(3)合型合型并锁型,将料筒、冲头进入待挤压位置。
(4)挤压用挤压冲头将液态(半固态)金属推人型腔,并继续保压直至其完全凝固。
(5)开型推出铸件。
挤压铸造一般在专用挤压铸造机(简称挤铸机)上进行。
但国内外也不少是选普通液压机代用,后者设备投资少,也可行,但生产效率低并会影响产品质量。
挤压铸造工艺优势与应用简介
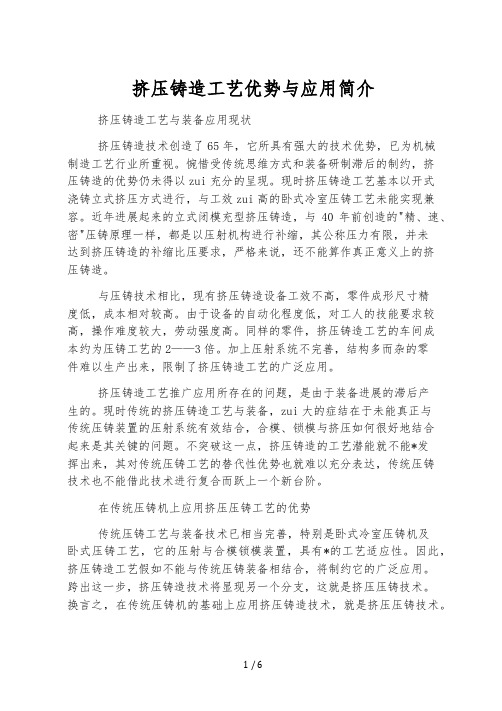
挤压铸造工艺优势与应用简介挤压铸造工艺与装备应用现状挤压铸造技术创造了65年,它所具有强大的技术优势,已为机械制造工艺行业所重视。
惋惜受传统思维方式和装备研制滞后的制约,挤压铸造的优势仍未得以zui充分的呈现。
现时挤压铸造工艺基本以开式浇铸立式挤压方式进行,与工效zui高的卧式冷室压铸工艺未能实现兼容。
近年进展起来的立式闭模充型挤压铸造,与40年前创造的"精、速、密"压铸原理一样,都是以压射机构进行补缩,其公称压力有限,并未达到挤压铸造的补缩比压要求,严格来说,还不能算作真正意义上的挤压铸造。
与压铸技术相比,现有挤压铸造设备工效不高,零件成形尺寸精度低,成本相对较高。
由于设备的自动化程度低,对工人的技能要求较高,操作难度较大,劳动强度高。
同样的零件,挤压铸造工艺的车间成本约为压铸工艺的2——3倍。
加上压射系统不完善,结构多而杂的零件难以生产出来,限制了挤压铸造工艺的广泛应用。
挤压铸造工艺推广应用所存在的问题,是由于装备进展的滞后产生的。
现时传统的挤压铸造工艺与装备,zui大的症结在于未能真正与传统压铸装置的压射系统有效结合,合模、锁模与挤压如何很好地结合起来是其关键的问题。
不突破这一点,挤压铸造的工艺潜能就不能*发挥出来,其对传统压铸工艺的替代性优势也就难以充分表达,传统压铸技术也不能借此技术进行复合而跃上一个新台阶。
在传统压铸机上应用挤压压铸工艺的优势传统压铸工艺与装备技术已相当完善,特别是卧式冷室压铸机及卧式压铸工艺,它的压射与合模锁模装置,具有*的工艺适应性。
因此,挤压铸造工艺假如不能与传统压铸装备相结合,将制约它的广泛应用。
跨出这一步,挤压铸造技术将显现另一个分支,这就是挤压压铸技术。
换言之,在传统压铸机的基础上应用挤压铸造技术,就是挤压压铸技术。
依据挤压压铸自身工艺的特点,对传统压铸机进行相应的完善改造,这套设备就是一台全新的挤压压铸机了。
正确而全面认得压铸工艺与传统压铸机的功能把握挤压铸造工艺的原理,在传统压铸机上地简单应用挤压压铸工艺并不是件难事,关键的是突破传统观念。
我国挤压铸造技术的研究现状及展望
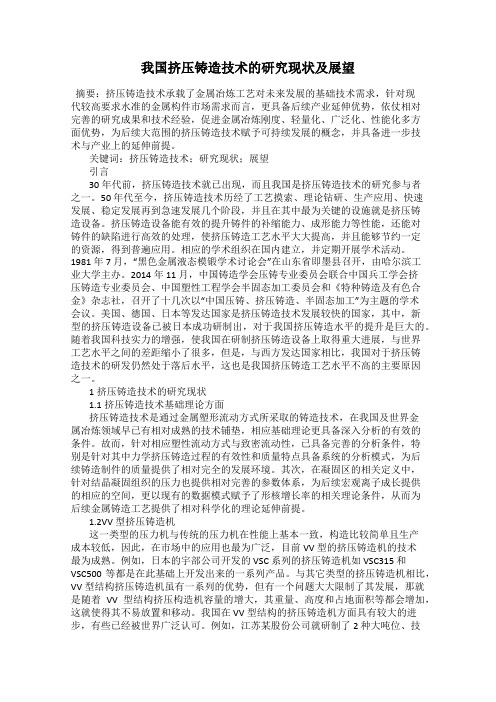
我国挤压铸造技术的研究现状及展望摘要:挤压铸造技术承载了金属冶炼工艺对未来发展的基础技术需求,针对现代较高要求水准的金属构件市场需求而言,更具备后续产业延伸优势,依仗相对完善的研究成果和技术经验,促进金属冶炼刚度、轻量化、广泛化、性能化多方面优势,为后续大范围的挤压铸造技术赋予可持续发展的概念,并具备进一步技术与产业上的延伸前提。
关键词:挤压铸造技术;研究现状;展望引言30 年代前,挤压铸造技术就已出现,而且我国是挤压铸造技术的研究参与者之一。
50 年代至今,挤压铸造技术历经了工艺摸索、理论钻研、生产应用、快速发展、稳定发展再到急速发展几个阶段,并且在其中最为关键的设施就是挤压铸造设备。
挤压铸造设备能有效的提升铸件的补缩能力、成形能力等性能,还能对铸件的缺陷进行高效的处理,使挤压铸造工艺水平大大提高,并且能够节约一定的资源,得到普遍应用。
相应的学术组织在国内建立,并定期开展学术活动。
1981 年 7 月,“黑色金属液态模锻学术讨论会”在山东省即墨县召开,由哈尔滨工业大学主办。
2014年 11 月,中国铸造学会压铸专业委员会联合中国兵工学会挤压铸造专业委员会、中国塑性工程学会半固态加工委员会和《特种铸造及有色合金》杂志社,召开了十几次以“中国压铸、挤压铸造、半固态加工”为主题的学术会议。
美国、德国、日本等发达国家是挤压铸造技术发展较快的国家,其中,新型的挤压铸造设备已被日本成功研制出,对于我国挤压铸造水平的提升是巨大的。
随着我国科技实力的增强,使我国在研制挤压铸造设备上取得重大进展,与世界工艺水平之间的差距缩小了很多,但是,与西方发达国家相比,我国对于挤压铸造技术的研发仍然处于落后水平,这也是我国挤压铸造工艺水平不高的主要原因之一。
1挤压铸造技术的研究现状1.1挤压铸造技术基础理论方面挤压铸造技术是通过金属塑形流动方式所采取的铸造技术,在我国及世界金属冶炼领域早已有相对成熟的技术铺垫,相应基础理论更具备深入分析的有效的条件。
挤压铸造成形技术在金属材料上的应用研究
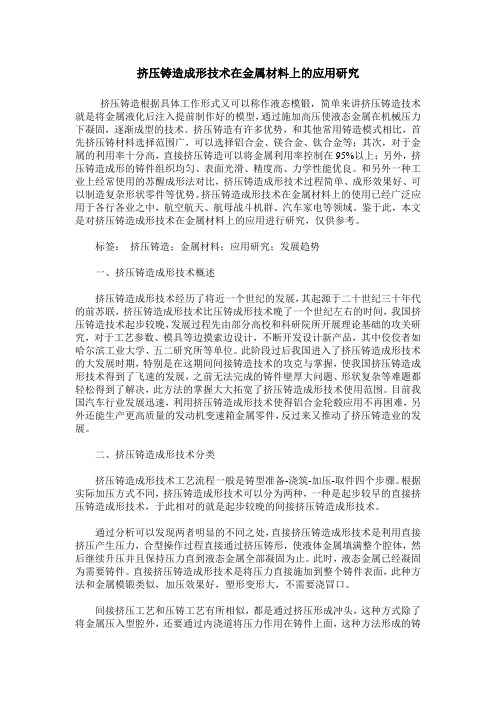
挤压铸造成形技术在金属材料上的应用研究挤压铸造根据具体工作形式又可以称作液态模锻,简单来讲挤压铸造技术就是将金属液化后注入提前制作好的模型,通过施加高压使液态金属在机械压力下凝固,逐渐成型的技术。
挤压铸造有许多优势,和其他常用铸造模式相比,首先挤压铸材料选择范围广,可以选择铝合金、镁合金、钛合金等;其次,对于金属的利用率十分高,直接挤压铸造可以将金属利用率控制在95%以上;另外,挤压铸造成形的铸件组织均匀、表面光滑、精度高、力学性能优良。
和另外一种工业上经常使用的苏醒成形法对比,挤压铸造成形技术过程简单、成形效果好、可以制造复杂形状零件等优势。
挤压铸造成形技术在金属材料上的使用已经广泛应用于各行各业之中,航空航天、航母战斗机群、汽车家电等领域。
鉴于此,本文是对挤压铸造成形技术在金属材料上的应用进行研究,仅供参考。
标签:挤压铸造;金属材料;应用研究;发展趋势一、挤压铸造成形技术概述挤压铸造成形技术经历了将近一个世纪的发展,其起源于二十世纪三十年代的前苏联,挤压铸造成形技术比压铸成形技术晚了一个世纪左右的时间,我国挤压铸造技术起步较晚,发展过程先由部分高校和科研院所开展理论基础的攻关研究,对于工艺参数、模具等边摸索边设计,不断开发设计新产品,其中佼佼者如哈尔滨工业大学、五二研究所等单位。
此阶段过后我国进入了挤压铸造成形技术的大发展时期,特别是在这期间间接铸造技术的攻克与掌握,使我国挤压铸造成形技术得到了飞速的发展,之前无法完成的铸件壁厚大问题、形状复杂等难题都轻松得到了解决,此方法的掌握大大拓宽了挤压铸造成形技术使用范围。
目前我国汽车行业发展迅速,利用挤压铸造成形技术使得铝合金轮毂应用不再困难,另外还能生产更高质量的发动机变速箱金属零件,反过来又推动了挤压铸造业的发展。
二、挤压铸造成形技术分类挤压铸造成形技术工艺流程一般是铸型准备-浇筑-加压-取件四个步骤。
根据实际加压方式不同,挤压铸造成形技术可以分为两种,一种是起步较早的直接挤压铸造成形技术,于此相对的就是起步较晚的间接挤压铸造成形技术。
挤压式金属铸造设备关键技术研究
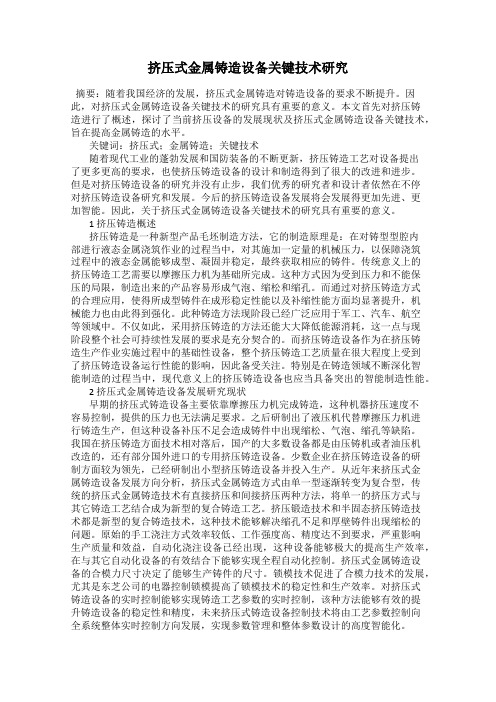
挤压式金属铸造设备关键技术研究摘要:随着我国经济的发展,挤压式金属铸造对铸造设备的要求不断提升。
因此,对挤压式金属铸造设备关键技术的研究具有重要的意义。
本文首先对挤压铸造进行了概述,探讨了当前挤压设备的发展现状及挤压式金属铸造设备关键技术,旨在提高金属铸造的水平。
关键词:挤压式;金属铸造;关键技术随着现代工业的蓬勃发展和国防装备的不断更新,挤压铸造工艺对设备提出了更多更高的要求,也使挤压铸造设备的设计和制造得到了很大的改进和进步。
但是对挤压铸造设备的研究并没有止步,我们优秀的研究者和设计者依然在不停对挤压铸造设备研究和发展。
今后的挤压铸造设备发展将会发展得更加先进、更加智能。
因此,关于挤压式金属铸造设备关键技术的研究具有重要的意义。
1 挤压铸造概述挤压铸造是一种新型产品毛坯制造方法,它的制造原理是:在对铸型型腔内部进行液态金属浇筑作业的过程当中,对其施加一定量的机械压力,以保障浇筑过程中的液态金属能够成型、凝固并稳定,最终获取相应的铸件。
传统意义上的挤压铸造工艺需要以摩擦压力机为基础所完成。
这种方式因为受到压力和不能保压的局限,制造出来的产品容易形成气泡、缩松和缩孔。
而通过对挤压铸造方式的合理应用,使得所成型铸件在成形稳定性能以及补缩性能方面均显著提升,机械能力也由此得到强化。
此种铸造方法现阶段已经广泛应用于军工、汽车、航空等领域中。
不仅如此,采用挤压铸造的方法还能大大降低能源消耗,这一点与现阶段整个社会可持续性发展的要求是充分契合的。
而挤压铸造设备作为在挤压铸造生产作业实施过程中的基础性设备,整个挤压铸造工艺质量在很大程度上受到了挤压铸造设备运行性能的影响,因此备受关注。
特别是在铸造领域不断深化智能制造的过程当中,现代意义上的挤压铸造设备也应当具备突出的智能制造性能。
2 挤压式金属铸造设备发展研究现状早期的挤压式铸造设备主要依靠摩擦压力机完成铸造,这种机器挤压速度不容易控制,提供的压力也无法满足要求。
挤压铸造原理及缺陷分析

挤压铸造原理及缺陷分析集团企业公司编码:(LL3698-KKI1269-TM2483-LUI12689-ITT289-挤压铸造原理及缺陷分析挤压铸造技术与传统金属型重力铸造相比区别较大,对于某些铸件的生产有独特优势,然而实际生产中出现的一些铸造缺陷,成因也不同于传统铸造,本文试图从原理和生产实际出发,分析挤压铸造的原理和流程参数,及其铸造常见缺陷,利用技术上的经验和实践提出改进方法,已达到推进该项铸造技术的推广,减少损失。
挤压铸造原理及特点1.1.基本原理挤压铸造又可称为液态模锻,是将金属或合金升温至熔融态,不加处理注入到敞口模具中,立即闭合模具,让液态金属充分流动以充填模具,初步到达制件外部形状,随后施以高压,使温度下降已凝固的外部金属产生塑性变形,而内部的未凝固金属承受等静压,同步发生高压凝固,最后获得制件或毛坯的方法。
由于高压凝固和塑性变形同时存在,制件无缩孔、缩松等缺陷,组织细密,力学性能高于铸造方法,接近或相当锻造方法;无需冒口补缩和最后清理,因而液态金属或合金利用率高,工序简化,为一具有潜在应用前景的新型金属加工工艺。
1.2.挤压铸造的特点挤压铸造的工艺对铸造设备有特殊的要求,并且目前只对部分铸件有较好的效果。
首先,挤压铸造设备,需要提供低速但流量较大的液态金属填充能力,速度约为0.5~3m/s,流量可达1~5kg/s,这样熔融态金属才能平稳地将铸型内气体排出,并填充铸型,随后铸型填满的瞬间(50ms~150ms),应能将铸型内铸造比压提升到60~100MPa,这样合金便能在高压下凝固成型。
由于前述的低速大流量,且挤压铸造内浇道有冒口补缩的作用,内浇道口径较大,且位于铸件最肥厚的部位。
由于上述特点,挤压铸造适合厚壁铸件(10~50mm),但铸件尺寸不宜太大(小于200mm)。
与压铸相同,挤压铸造只可使用脱模剂,不适用保温涂料,故而金属凝固速度极快,达到300~400摄氏度/s,与金属型重力铸造冷却速度相比,达到了其3~5倍,伸长率高于其他铸造方法约2~3倍。
挤压铸造模具的设计及工艺研究-武汉理工大学2012.06.21
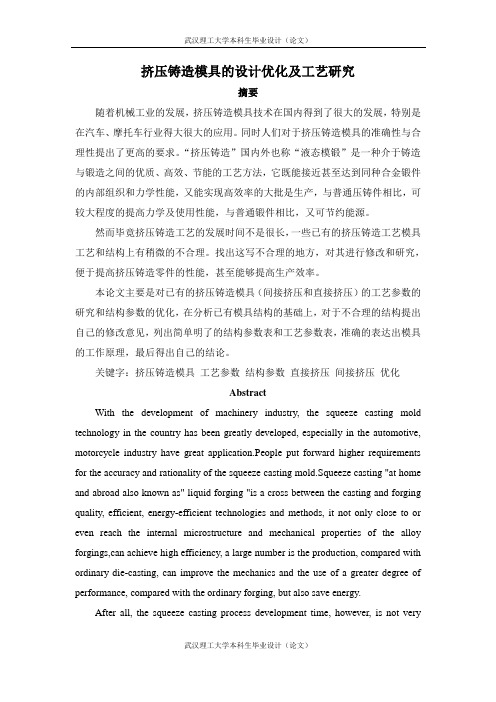
挤压铸造模具的设计优化及工艺研究摘要随着机械工业的发展,挤压铸造模具技术在国内得到了很大的发展,特别是在汽车、摩托车行业得大很大的应用。
同时人们对于挤压铸造模具的准确性与合理性提出了更高的要求。
“挤压铸造”国内外也称“液态模锻”是一种介于铸造与锻造之间的优质、高效、节能的工艺方法,它既能接近甚至达到同种合金锻件的内部组织和力学性能,又能实现高效率的大批是生产,与普通压铸件相比,可较大程度的提高力学及使用性能,与普通锻件相比,又可节约能源。
然而毕竟挤压铸造工艺的发展时间不是很长,一些已有的挤压铸造工艺模具工艺和结构上有稍微的不合理。
找出这写不合理的地方,对其进行修改和研究,便于提高挤压铸造零件的性能,甚至能够提高生产效率。
本论文主要是对已有的挤压铸造模具(间接挤压和直接挤压)的工艺参数的研究和结构参数的优化,在分析已有模具结构的基础上,对于不合理的结构提出自己的修改意见,列出简单明了的结构参数表和工艺参数表,准确的表达出模具的工作原理,最后得出自己的结论。
关键字:挤压铸造模具工艺参数结构参数直接挤压间接挤压优化AbstractWith the development of machinery industry, the squeeze casting mold technology in the country has been greatly developed, especially in the automotive, motorcycle industry have great application.People put forward higher requirements for the accuracy and rationality of the squeeze casting mold.Squeeze casting "at home and abroad also known as" liquid forging "is a cross between the casting and forging quality, efficient, energy-efficient technologies and methods, it not only close to or even reach the internal microstructure and mechanical properties of the alloy forgings,can achieve high efficiency, a large number is the production, compared with ordinary die-casting, can improve the mechanics and the use of a greater degree of performance, compared with the ordinary forging, but also save energy.After all, the squeeze casting process development time, however, is not verylong, have squeezed a little unreasonable in the casting process mold processes and structures.Find out where this write unreasonable, modify and research, and easy to improve the performance of squeeze casting parts, or even be able to improve production efficiency.In this paper, the existing squeeze casting mold (indirect extrusion and direct extrusion) the optimization of process parameters and structural parameters, based on analysis of existing mold structure, unreasonable structureamedments, list of simple structural parameter table and the process parameters table, an accurate expression of the working principle of the mold, and finally draw their own conclusions.Keywords: squeeze casting mold, process parameters, structural parameters, direct extrusion , indirect extrusion第一章绪论1.1研究目的及其意义挤压铸造(squeeze casting)是对铸型型腔中的液态或半液态的金属施加较高的机械压力,使其成型凝固,从而获得铸件的一种铸造方法,根据挤压铸造时合金液的流动状况及挤压铸造力的形式,挤压铸造可以分为直接挤压铸造(direct squeeze casting)和间接挤压铸造(indirect squeeze casting)两种基本形式。
工艺因素对大高径比挤压铸件凝固温度场的影响
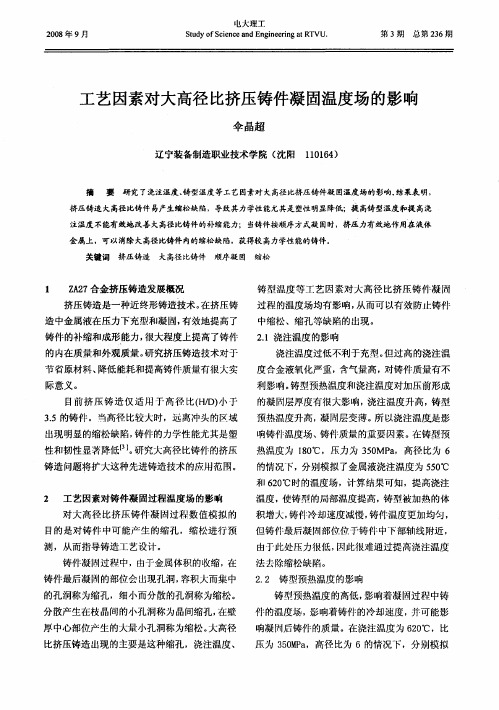
电大 理 工 Su y f c n e n n i eiga R VU td S i c dE gn r t T . o e a e n
第 3期
总 第 2 6期 3
工 艺 因素对大 高径 比挤压铸件凝 固温度场 的影响
伞 晶超
辽 宁装 备制 造职 业技术 学 院 ( 阳 10 6 ) 沈 14 1
性和韧性显著降低p 。 研究大高径比铸什的挤压 J
铸 造 问题 将 扩火这 种先进 铸造 技术 的应川 范 围。
热温度为 lO 8 ℃,压力为 3 0 a 5MP ,高径比为 6 的情况下 , 分别模拟了金属液浇注温度为 5 0 5℃
莉12 ℃时 的温度 场 ,计 算 结果可 知 Ma
摘 要
研究 了浇注温度 、 铸型温度 等工艺因素对 大高径 比挤压铸件凝 固温度 场的影 响。 结果表 明,
挤压铸造 大高径 比铸件 易产生缩松缺 陷,导致其力学性 能尤其是塑性明显降低 ;提 高铸型温度和提 高浇
注温度 不能有效地 改善 大高径比铸件 的补缩能力; 当 铸件按顺序方式凝 固时,挤压力有效地作用在 液体
2 工 艺因 素对铸件 凝 固过程 温度 场 的影响 对 大 高径 比挤压 铸 件 凝 I 释 数值 模 拟 的 刮过 目的 是对 铸件 中可 能产 生 的缩 孔 ,缩松 进行 预
测 ,从而 指导铸 造工 艺设计 。 铸件凝 同过 程 中 ,由于金属体 积 的收缩 , 在
温度 , 使铸 型 的局 部温度 提 高 , 型被 加热 的体 铸
金属上,可以消除大高径比铸件内的缩松缺陷,获得较高力学性能的铸件。
关键词 挤压铸造 大高径 比铸件 顺序凝 固 缩松
1
金属冶炼中的金属的挤压与锻造技术
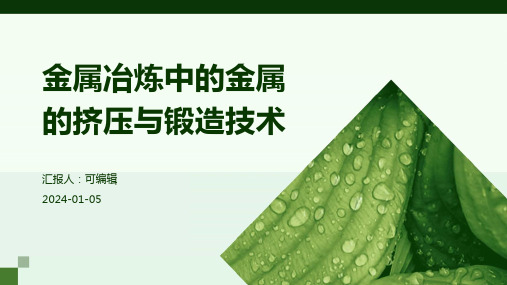
03
金属挤压与锻造技术比较 分析
技术特点比较
金属挤压
通过向封闭挤压腔内压入金属,使其从模孔中挤出,形成所 需形状和尺寸的制品。挤压技术可生产壁薄、截面变化复杂 、晶粒细化、组织致密的制品。
金属锻造
将金属坯料放入模具中,通过锻压机械施加外力,使金属坯 料产生塑性变形,以获得所需形状、尺寸和性能的制品。锻 造技术可生产晶粒较粗、力学性能较高的制品。
04
金属挤压与锻造技术的发 展趋势
新材料的应用
高强度轻质材料
01
如钛合金、铝合金等,在航空、航天、汽车等领域得到广泛应
用。
高温超导材料
02
在电力、能源、交通等领域具有巨大的应用潜力。
功能材料
03
如形状记忆合金、磁性合金等,在医疗器械、传感器等领域发
挥重要作用。
智能化与自动化技术
机器人与自动化生产线
航空航天领域
航空航天领域对材料性能要求极高,金属挤压和锻造技术在此领域的应用尤为重要。例如 ,飞机发动机叶片、机身结构件等关键部件的生产都离不开金属挤压和锻造技术的支持。
能源领域
在能源领域,金属挤压和锻造技术被广泛应用于核能、石油、天然气等行业的关键部件制 造。例如,核反应堆压力壳、石油钻井平台的关键结构件等都需要通过金属挤压和锻造技 术生产。
锻造技术的定义与原理
锻造技术定义
通过施加外力,使金属坯料在温度和 应力的作用下发生塑性变形,从而获 得所需形状和性能的金属制品的过程 。
锻造技术原理
利用金属的塑性变形原理,通过控制 温度、压力和变形程度等工艺参数, 使金属坯料发生连续的塑性变形,以 达到所需的形状和性能要求。
锻造技术的分类与特点
金属冶炼中的金属 的挤压与锻造技术
三基-挤压铸造技术介绍

三基-挤压铸造技术介绍
嘿,朋友们!今天咱来聊聊三基-挤压铸造技术。
这玩意儿可厉害啦!
你想想看,就好像我们做蛋糕一样,要把各种材料完美地融合在一起,挤压铸造技术也是这么个道理。
它能把金属材料像变魔术一样变成我们想要的形状和性能。
这技术啊,就像是一个超级厉害的工匠,能把金属材料雕琢得特别精细。
它可以让铸件的组织更加致密,强度那是蹭蹭往上涨啊!而且啊,它还能减少气孔、缩松这些让人头疼的缺陷呢。
说起来,以前没有这技术的时候,我们制造一些复杂形状的金属零件可麻烦了,不是这儿有问题就是那儿不行。
但有了三基-挤压铸造技术后,哇塞,一切都变得不一样啦!它能让那些形状复杂的零件轻松地被制造出来,而且质量还特别好,这不是太棒了吗?
你再想想,如果把金属材料比作是一堆积木,那挤压铸造技术就是那个能把积木搭出各种奇妙造型的人。
它能让这些积木紧密地结合在一起,变得无比坚固。
这技术在很多领域都大显身手呢!比如汽车制造,那些高质量的零部件可少不了它的功劳。
还有航空航天领域,对零件的要求那么高,三基-挤压铸造技术就能很好地满足需求呀。
而且哦,它还特别节能环保呢!比起其他一些制造方法,它能节省不少材料和能源,这对我们的地球妈妈来说可是个大好事呀!
你说,这么好的技术,我们能不重视它吗?我们得好好研究它,让它发挥更大的作用呀!我们的生活中有那么多需要高质量金属零件的地方,三基-挤压铸造技术就是那个能帮我们实现的魔法呀!
所以啊,大家可别小瞧了这三基-挤压铸造技术,它可是我们现代工业的宝贝呢!让我们一起为它点赞,一起期待它能给我们带来更多的惊喜吧!。
挤压铸造原理及缺陷分析
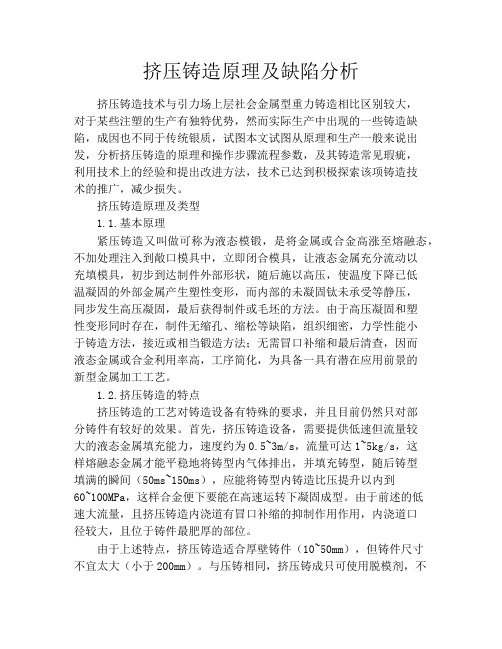
挤压铸造原理及缺陷分析挤压铸造技术与引力场上层社会金属型重力铸造相比区别较大,对于某些注塑的生产有独特优势,然而实际生产中出现的一些铸造缺陷,成因也不同于传统银质,试图本文试图从原理和生产一般来说出发,分析挤压铸造的原理和操作步骤流程参数,及其铸造常见瑕疵,利用技术上的经验和提出改进方法,技术已达到积极探索该项铸造技术的推广,减少损失。
挤压铸造原理及类型1.1.基本原理紧压铸造又叫做可称为液态模锻,是将金属或合金高涨至熔融态,不加处理注入到敞口模具中,立即闭合模具,让液态金属充分流动以充填模具,初步到达制件外部形状,随后施以高压,使温度下降已低温凝固的外部金属产生塑性变形,而内部的未凝固钛未承受等静压,同步发生高压凝固,最后获得制件或毛坯的方法。
由于高压凝固和塑性变形同时存在,制件无缩孔、缩松等缺陷,组织细密,力学性能小于铸造方法,接近或相当锻造方法;无需冒口补缩和最后清查,因而液态金属或合金利用率高,工序简化,为具备一具有潜在应用前景的新型金属加工工艺。
1.2.挤压铸造的特点挤压铸造的工艺对铸造设备有特殊的要求,并且目前仍然只对部分铸件有较好的效果。
首先,挤压铸造设备,需要提供低速但流量较大的液态金属填充能力,速度约为0.5~3m/s,流量可达1~5kg/s,这样熔融态金属才能平稳地将铸型内气体排出,并填充铸型,随后铸型填满的瞬间(50ms~150ms),应能将铸型内铸造比压提升以内到60~100MPa,这样合金便下要能在高速运转下凝固成型。
由于前述的低速大流量,且挤压铸造内浇道有冒口补缩的抑制作用作用,内浇道口径较大,且位于铸件最肥厚的部位。
由于上述特点,挤压铸造适合厚壁铸件(10~50mm),但铸件尺寸不宜太大(小于200mm)。
与压铸相同,挤压铸成只可使用脱模剂,不适用保温涂料,故而金属凝固速度极快,达到300~400摄氏度/s,与金属型相若振动铸造冷却速度相比,达到了其3~5倍,伸长率高于其他铸造方法约2~3倍。
- 1、下载文档前请自行甄别文档内容的完整性,平台不提供额外的编辑、内容补充、找答案等附加服务。
- 2、"仅部分预览"的文档,不可在线预览部分如存在完整性等问题,可反馈申请退款(可完整预览的文档不适用该条件!)。
- 3、如文档侵犯您的权益,请联系客服反馈,我们会尽快为您处理(人工客服工作时间:9:00-18:30)。
・・基金项目:国家自然科学基金资助项目(50275098)。
收稿日期:2005-04-07收到初稿,2005-05-30收到修订稿。
作者简介:李晨希(1956!),男,辽宁凤城市人,教授,博士后,研究方向为铸造合金和挤压铸造技术。
E-mail:chenxil@mail.sy.ln.cn大高径比铸件挤压铸造技术研究李晨希,伞晶超,徐娜,曹亮,白彦华,李荣德(沈阳工业大学材料科学与工程学院,辽宁沈阳110023)摘要:用试验和计算机模拟的方法,研究了高径比为7的铸件凝固过程中的温度分布;研究了铸件中的缩松和铸件力学性能分布特点。
结果表明,增加大高径比铸件挤压铸造的比压、提高铸型的预热温度不能有效地减少铸件内的缩松缺陷;采取措施使铸件顺序凝固,并使挤压力有效地作用在液体金属上,可以消除大高径比铸件内的缩松,获得高力学性能的铸件。
关键词:挤压铸造;大高径比铸件;顺序凝固;缩松中图分类号:TG249.2文献标识码:A文章编号:1001-4977(2005)08-0761-03LIChen-xi,SANJing-chao,XUNa,CAOLiang,BAIYan-hua,LIRong-de(SchoolofMaterialsScienceandTechnology,ShenyangUniversityofTechnology,Shenyang110023,Liaoning,China)Inthecastingswiththeratioofheighttothicknessbeing7,thetemperaturedistributionduringsolidificationwasstudiedbythemethodsofexperimentandcomputersimulation.Andtheshrinkageporositydistributioninthecastingsandthemechanicalpropertiesofthecastingswerealsoresearched.Theexperimentalandsimulatedresultsshowthatincreasingsqueezeforce,orenhancingtemperatureofthemoldcannotreducetheporositiesinthecastings.Whencastingssolidifyasasequencemannerandthesqueezeforceeffectivelyactsonthesurfaceoftheliquidmetal,theporositiesinthecastingsareeliminatedandmechanicalpropertiesareincreased.squeezecast;castingswithlargeratioofheighttothickness;sequencesolidification;shrinkageporosity挤压铸造是一种近终形铸造技术。
在挤压铸造中金属液在压力下充型和凝固,有效地提高了铸件的补缩和成形能力,很大程度上提高了铸件的内在质量和外观质量。
研究挤压铸造技术对于节省原材料、降低能耗和提高铸件质量有很大实际意义[1!4]。
目前挤压铸造仅适用于高径比(!/")小于3.5的铸件。
当高径比较大时,远离冲头的区域出现明显的缩松缺陷,铸件的力学性能尤其是塑性和韧性显著降低[4!6]。
研究大高径比铸件的挤压铸造问题将扩大这种先进铸造技术的应用范围。
ZA27合金有强度高、耐磨性好、原材料来源丰富等优点,在低速重载的条件下已部分代替铜合金。
但ZA27合金凝固温度范围宽,通常铸造条件下易出现缩松缺陷,导致塑性和韧性明显降低[6!7]。
本课题用试验和计算机模拟的方法,研究了高径比为7的ZA27合金铸件凝固过程中的温度分布,研究了铸件中的缩松和铸件力学性能的分布特点。
配制的ZA27合金成分为:#(Al)=27%、#(Cu)=1.6%、#(Mg)=0.02%,其余是锌。
用36kW电阻坩埚炉熔炼合金,在YH61!500G型压力机上制备棒状铸件。
图1是制备挤压铸造铸件的示意图。
浇注温度是650",金属液在压力下凝固。
沿铸件的轴线截取拉伸试样,截取的试样依次编为1、2、3、4号,见图2。
铸型预热到140#时,浇入金属液。
金属液在压力下凝固,施加的压力为350MPa。
通常挤压铸件的高径比!/"=1 ̄3,铸件与模具间的摩擦力造成的压力损失不大,铸件下部受到的压力与上部接近。
图1所示铸件的高径比为7。
计算机模拟表明,铸件与模具间的摩擦力造成了很大的压力损失,铸件底部所受的挤压力仅为顶部的十分之一,因此试验中施加的比压远大于通常挤压铸造的比压。
铸件凝固后沿纵向剖开,图3a是铸件的纵剖面。
在铸件下部轴线附近的黑色区域中有大量缩松。
用计!!!"!"!!!"!"压铸Vol.54No.8Aug.2005铸造FOUNDRY761・・算机模拟了铸件凝固过程的温度场,模拟结果见图3b,图中的灰色区是最后凝固区域。
由图3可见,最后凝固区域形成大量缩松。
按图2所示的位置在铸件上取样,力学性能测试结果见表1。
表中编号为“3”的试样力学性能最低,这与缩松缺陷的位置基本一致。
在挤压铸造中铸件的上部凝固较快,其原因是:压力使铸件的上部与铸型接触较紧密,界面热阻较小;铸件的上部受较高压力的作用,金属的密度、热导率增大,金属冷却快。
为了消除缩松,将比压由350MPa提高为750MPa,铸型温度仍保持为140!,进行挤压铸造试验。
试验结果表明,铸件中缩松分布没有明显改变。
比压保持为350MPa,铸型温度由140"提高为180#。
试验表明,铸件中缩松分布也没有明显改变。
由此可见,对于高径比大的铸件来说,提高比压或提高铸型温度不能有效地改善铸件的补缩能力。
大高径比铸件产生缩松的原因是铸件凝固过程中不能有效补缩。
图4表明了扩张角!对铸件补缩的影响。
在图4a中,扩张角向着冲头方向,在扩张角范围内金属液形成“补缩通道”。
!越大,补缩通道越宽,“补缩困难区"”越小,这时铸件按“顺序凝固”方式凝固。
如果金属液在压力作用下按顺序方式凝固,铸件中不会产生缩松。
在图4b中,扩张角背向冲头方向,铸件按“反顺序凝固”方式凝固。
如果大高径比铸件按这种方式凝固,并且最后凝固部位远离冲头,铸件中会形成大量缩松,甚至缩孔。
因此,消除大高径比铸件内缩松的途径是,采取措施使远离冲头的金属先凝固,冲头附近的金属最后凝固,使之符合“顺序凝固”原则。
为了消除铸件中的缩松,研究了三种情况下铸件的凝固特点。
(1)如果铸件的上表面处于绝热状态,冲头附近的金属液将最后凝固,有利于铸件以顺序方式凝固。
模拟了这种条件下铸件的凝固过程,模拟结果见图5a。
图中的灰色区域是最后凝固部位,铸件的顶部中心处和轴线的下部凝固较慢。
在这种情况下,形成了两个后凝固区,铸件轴线的下部区域仍然会形成缩松。
(2)模拟了铸型温度不均匀时,铸件凝固过程中的温度分布。
假定铸型上部温度为180$,铸型下部温度为15%,沿铸型高度的温度分布见图6。
铸型的底部和冲头不预热,温度为15&。
模拟结果见图5b,最后凝固处位于铸件轴线的中上部。
(3)上述两种方法均不能使铸件以顺序方式凝固。
模拟了同时采用上述两种方法时,铸件凝固过程的温度分布。
假定铸件与冲头接触的部位处于绝热状态,铸型底部的温度为15’,沿铸型高度的温度分布图1制备挤压铸造铸件示意图Fig.1Sketchofpreparingcastingbysqueezecast图2拉伸试样在铸件上的取样位置Fig.2Sketchofthesamplingplacesinacasting(a)(b)图3铸件内的缩松和铸件最后凝固位置Fig.3Shrinkageporosityandfinalsolidifiedplacesinacasting表!铸件不同位置的力学性能"#$%&!’&()#*+(#%,-.,&-/+&0#/1+22&-&*/,%#(&0+*#(#0/+*3编号抗拉强度/MPa伸长率(%)123441711.441910.83603.74109.8(a)顺序凝固示意图(b)反顺序凝固示意图图4扩张角对铸件补缩的影响Fig.4EffectofoutspreadangleonfeedingshrinkageinacastingFOUNDRYVol.54No.8Aug.2005762・・如图6所示。
模拟结果见图7,下部先凝固,铸件以顺序方式凝固。
铸件凝固过程中,冲头的压力一直作用在金属液面上。
两者的共同作用形成了良好的补缩条件。
对优化了的工艺进行挤压铸造试验。
铸型的上部用Si-C棒加热,其他部位不加热。
当金属液浇入铸型后,在金属液的上表面放一层石棉,然后进行挤压铸造。
冲头与铸件之间的石棉起隔热作用。
按图2所示,在铸件的不同部位截取试样。
测得抗拉强度为400 ̄420MPa;伸长率为10% ̄13%;试样中没有明显的缩松缺陷。
上述研究结果表明,挤压铸造大高径比铸件易于产生缩松缺陷,导致其力学性能尤其是塑性明显降低;增加挤压铸造的比压,提高铸型温度不能有效地改善大高径比铸件的补缩能力;扩张角对铸件补缩有较大影响,扩张角向着冲头方向,并且!角较大,有利于铸件的补缩;铸件按顺序方式凝固,并且挤压力有效地作用在液体金属上,可以消除大高径比铸件内的缩松,获得高力学性能的铸件。
(1)挤压铸造大高径比铸件时,远离冲头处易于产生缩松缺陷,该处力学性能尤其是塑性明显降低。
增加挤压铸造比压、提高铸型温度不能有效地消除大高径比铸件中的缩松缺陷。
扩张角是决定铸件补缩能力的关键因素,形成向着冲头方向的扩张角有利于提高铸件的补缩能力。
(2)采取措施使铸件按顺序方式凝固,并使挤压力有效地作用在液体金属上,可以消除大高径比铸件内的缩松,获得力学性能高且均匀的铸件。
(a)(b)图5铸件最后凝固的部位Fig.5Finalsolidifiedplaceinacasting图6铸型温度沿高度的分布Fig.6Temperaturedistributionalongmoldheight(a)图7大高径比铸件的凝固过程(b)(c)(d)Fig.7Solidifyingprocessofacastingwithlargeratioofheighttothickness周大隽.液态模锻技术的应用及新发展[J].锻压技术,1993,(3):35!38洪慎章,等.挤压铸造比压对晶粒尺寸的影响[J].特种铸造及有色合金,2002,(6):26"27李晨希,郭太明,李荣德,等.二次枝晶臂间距研究[J].铸造,2004,53(12):1011#1014MichaelP,Martin.Recenttrendsinsqueezecasting[J].DieCastingEngineer,1996,(5):40$42GhomashchiMR,VikhrovA.Squeezecasting:anoverview[J].J.Mart.ProcessingTechl.,2000,(10):1%9李荣德,黄忠平,白彦华,等.超高压力对ZA27合金非平衡凝固组织和性能的影响[J].铸造,2003,(3):22&24CleggA.Squeezecasting-anewprocesstechnologyforengineer[J].FoundryTradeJournal.1993,166:484’485[1][2][3][4][5][6][7]参考文献:(编辑:张允华,zyh@foundryworld.com)铸造李晨希等:大高径比铸件挤压铸造技术研究763。