汽车车身用高强度钢及其加工性能的探讨
浅谈汽车用先进高强钢成形性能研究论文

浅谈汽车用先进高强钢成形性能研究论文浅谈汽车用先进高强钢成形性能研究论文先进高强钢兼具高强度和较好的成形性能,特别是应变硬化指数高,有利于碰撞吸收能的提高,已被广泛用于车身的结构件和安全件。
优化采用先进高强钢板,可减轻车身重量、提高车身被动安全性及提高车型性价比。
先进高强钢中的DP钢和TRIP钢都具有高强度和良好塑性的优点,是汽车轻量化的理想用材。
DP钢主要应用于车底十字构件、防撞杆、纵梁等加强结构件等,而TRIP钢则主要应用于车门防护杆、保险杠和底盘结构件等。
本文通过显微组织分析、拉伸试验、成形极限试验、杯突试验及扩孔试验,对不同强度级别DP钢和TRIP钢的成形性能进行研究,希望对冲压成形及应用提供参考。
1试验材料(1)化学成分试验材料中DP钢采用C-Si-Mn成分体系,TRIP钢采用Si基低合金成分体系。
为获得较细的组织以利于更好地提高塑性和韧性,试验材料中均添加微合金元素Nb。
(2)显微组织以相同强度级别试验材料显微组织为例。
DP590显微组织中灰白色组织为铁素体,灰黑色组织为马氏体,而在TRIP590显微组织中,灰色组织为铁素体,黑色组织为贝氏体,白色组织为残余奥氏体,残余奥氏体分布在多边形铁素体晶粒之间,有少量存在铁素体内部,岛状贝氏体分布在铁素体和残余奥氏体交界处或相邻的铁素体晶粒交界处。
DP钢中铁素体赋予双相钢较低的屈强比、较高的延伸率,具有优良的塑性;而马氏体则赋予其高的强度,同时铁素体在变形过程中会遇到硬相马氏体的阻碍产生大量位错而快速的产生加工硬化,有利于流变应力的均匀分布,使DP钢具有良好的成形性能。
TRIP钢中主要由贝氏体提高材料强度,提供塑性的不仅有铁素体,还有因残余奥氏体向马氏体相变而引入的塑性提高,因此,DP钢与TRIP钢的塑性能力是不同的。
Nb在DP钢中主要通过NbC粒子的析出阻碍再结晶晶粒的长大,使铁素体晶粒较细,马氏体分布弥散,在提高基体强度的同时有利于进一步提高加工硬化速率和延伸率。
汽车高强钢用的选用工艺及常见问题

汽车是现代社会中不可或缺的交通工具,而汽车的安全性能往往决定了行车过程中的安全系数。
在汽车制造中,高强钢被广泛应用于车身结构,以提高车辆的抗压性能和安全性能。
然而,高强钢的选用工艺和常见问题也是汽车制造中需要重点关注的内容。
一、高强钢的选用工艺1. 材料选择在汽车制造中,高强钢的选用首先需要考虑材料的选择。
不同的车型和部位对高强钢的强度和韧性要求不同,因此需要根据具体的设计要求选择合适的材料。
车辆的主体结构可能需要更高强度的高强钢,而车身外板可能需要更好的成形性能。
2. 成型工艺高强钢通常比普通钢更难成型,因此在汽车制造中需要采用更先进的成型工艺,如冷冲压、热冲压等。
这些工艺能够保证高强钢在成型过程中不会出现裂纹和变形,从而保证车身零部件的精度和质量。
3. 焊接工艺汽车的车身结构通常是由多个零部件组装而成的,因此需要采用焊接工艺将它们连接在一起。
在高强钢的焊接过程中,需要考虑热影响区的控制、焊接接头的质量等问题,以确保焊接的强度和密封性。
二、常见问题1. 成型难度大高强钢的硬度和强度较高,因此在成型过程中容易出现裂纹和变形的问题。
为解决这一问题,需要在成型工艺中加入适当的热处理和预成型工艺,以提高高强钢的成形性能。
2. 焊接质量难以保证高强钢在焊接过程中容易出现氢脆等问题,导致焊接接头的质量下降。
因此在汽车制造中需要采用先进的焊接工艺和材料,以提高高强钢的焊接质量。
3. 腐蚀问题高强钢的耐腐蚀性能一般较差,因此在汽车制造中需要采用表面处理等方法来提高高强钢的耐腐蚀性能,以延长汽车的使用寿命。
三、个人观点和理解作为汽车高强钢的文章写手,我认为汽车制造中对高强钢的选用工艺和常见问题需要引起足够的重视。
在材料选择、成型工艺和焊接工艺中,都需要结合高强钢的特性和要求,采用合适的工艺和方法来保证汽车零部件的质量和安全性能。
持续的研发和创新也是保证高强钢在汽车制造中更好应用的关键。
总结通过对汽车高强钢选用工艺和常见问题的全面评估,我们可以看到在汽车制造过程中需要对高强钢的选材、成型和焊接等方面进行精心设计和控制,以保证汽车的安全性能和质量。
高强度薄板在车身上的应用及成形中出现的问题
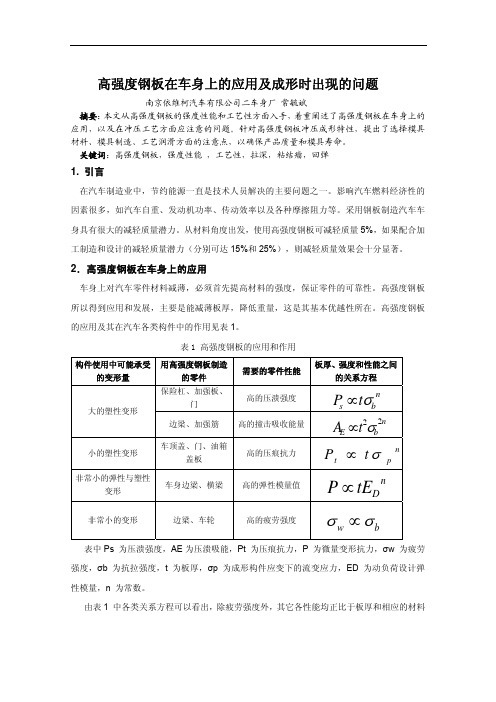
高强度钢板在车身上的应用及成形时出现的问题南京依维柯汽车有限公司二车身厂 常毓斌摘要:本文从高强度钢板的强度性能和工艺性方面入手,着重阐述了高强度钢板在车身上的应用,以及在冲压工艺方面应注意的问题。
针对高强度钢板冲压成形特性,提出了选择模具材料、模具制造、工艺润滑方面的注意点,以确保产品质量和模具寿命。
关键词:高强度钢板,强度性能 ,工艺性,拉深,粘结瘤,回弹1. 引言在汽车制造业中,节约能源一直是技术人员解决的主要问题之一。
影响汽车燃料经济性的因素很多,如汽车自重、发动机功率、传动效率以及各种摩擦阻力等。
采用钢板制造汽车车身具有很大的减轻质量潜力。
从材料角度出发,使用高强度钢板可减轻质量5%,如果配合加工制造和设计的减轻质量潜力(分别可达15%和25%),则减轻质量效果会十分显著。
2.高强度钢板在车身上的应用车身上对汽车零件材料减薄,必须首先提高材料的强度,保证零件的可靠性。
高强度钢板所以得到应用和发展,主要是能减薄板厚,降低重量,这是其基本优越性所在。
高强度钢板的应用及其在汽车各类构件中的作用见表1。
表1 高强度钢板的应用和作用 构件使用中可能承受的变形量 用高强度钢板制造的零件需要的零件性能 板厚、强度和性能之间的关系方程 保险杠、加强板、门高的压溃强度 大的塑性变形 边梁、加强筋高的撞击吸收能量 小的塑性变形车顶盖、门、油箱盖板 高的压痕抗力 非常小的弹性与塑性变形车身边梁、横梁 高的弹性模量值 非常小的变形 边梁、车轮 高的疲劳强度表中Ps 为压溃强度,AE 为压溃吸能,Pt 为压痕抗力,P 为微量变形抗力,σw 为疲劳强度,σb 为抗拉强度,t 为板厚,σp 为成形构件应变下的流变应力,ED 为动负荷设计弹性模量,n 为常数。
由表1 中各类关系方程可以看出,除疲劳强度外,其它各性能均正比于板厚和相应的材料n b s t P σ∝n b E t A 22σ∝n D tE P ∝b w σσ∝n p t t P σ∝性能(抗拉强度、流变应力、动负荷设计弹性模量)n 次方的乘积。
干货汽车轻量化用高强度钢板应用技术研发

干货汽车轻量化用高强度钢板应用技术研发来源:钢铁共性技术为了提高汽车的燃料效率,满足减排CO2及保护环境的需要,要求汽车车体轻量化。
另一方面,为应对逐年严格的抗冲撞要求以及车载部件的增多,车体重量有不断增加的趋势。
扩大高强度钢板在车体结构上的应用,使车体轻量化是解决车体重量增加问题的必要方法。
近年来,抗拉强度达980、1180MPa级的高强度钢板用于车体结构部件的事例不断增加。
随着抗拉强度的升高,钢板的冲压成形性和焊接性下降。
为了解决这些问题,日本JFE钢铁公司对高强度钢板的冲压成形技术、提高高强度钢板车体刚性和抗冲撞性技术以及焊接技术进行了深入研发。
为了进一步扩大高强度钢板的应用,JFE公司构建了从最佳材料选择到高强度钢板应用技术的解决方案体制。
1高强度钢板的成形技术高强度钢板成形时存在的主要问题是,成形产生裂纹和皱折以及成形品发生回弹,使成形品尺寸精度下降。
此外,随着钢板的高强度化,钢板剪切刀具损坏和冲压卡模问题也日益突显。
为解决这些问题,JFE公司开发出利用CAE和试验方法的预测技术以及相应的解决对策。
1.1关于冲压裂纹的技术1.1.1冲压裂纹预测技术随着强度的升高,高强度钢板的延性和拉伸凸缘性下降。
目前,普遍使用成形极限曲线(FLD)对钢板冲压成形时产生的胀出裂纹和拉延裂纹进行评价。
但是由于扩孔加工和翻边加工时,在钢板端部产生拉伸凸缘裂纹和弯曲加工时钢板外表面产生弯曲裂纹到断裂的机制与上述冲压成形裂纹不同,所以不能用FLD进行评价。
为此,JFE公司开发出拉伸凸缘裂纹的预测方法。
该方法对包括钢板扩孔性、钢板端部应变梯度、剪切加工条件等因素在内的变形极限进行定义,用成形模拟法对拉伸凸缘裂纹进行预测(如图1)。
弯曲加工时钢板外表面产生的弯曲裂纹是无缩颈发生的、从拉伸弯曲的外表面产生的裂纹。
JFE开发出弯曲裂纹的预测方法。
该方法将拉伸弯曲外表面的成形极限作为V型弯曲试验得到的极限表面应变,可对弯曲裂纹进行高精度预测。
汽车车身用高强度钢及其加工性能的探讨

汽车车身用高强度钢及其加工性能的探讨1 高强度钢板的应用现状和发展动向迄今为止,根据用途的不同,采用不同的强化机制获得了多种汽车车身用高强度钢板。
图1显示了不同的强化机制下获得的几种高强度钢的强度和伸长率。
传统的汽车车身用钢主要是靠添加合金成分获得固溶强化(solid-solution hardened)或析出强化(precipitation hardened)型钢。
由图1可知,析出强化型钢虽然具有较高的强度,可是伸长率低的特性使其冲压成形性较差;而固溶强化型钢虽具有较好的延展性,但其强度却较低。
图1 各种高强度钢的强度和伸长率对于用来制造汽车部件的钢板,既要确保其冲压成形性,又需对其碳当量加以控制以不妨害其焊接性。
在这种情况下,要获得高强度钢,通常钢的组织需保证有马氏体相。
但单纯马氏体相钢,如图1所示的回火马氏体(Tempered martensite)钢虽具有980~1480MPa超高强度,因其延展性很低而难以保证加工性,在汽车车身中的应用则受到限制,仅用于加强件。
于是,对提高延展性的组织控制型高强度钢进行了研制,并于20世纪末进入了实用化阶段。
最先实用化的组织控制型钢是抗拉强度为590MPa级的双相钢(Dual Phase Steel,以下称DP钢)。
DP钢室温组织主要由铁素体和马氏体构成,铁素体为基体相,岛状的马氏体分布于其上。
软的铁素体赋予DP钢较低的屈强比、较大的伸长率,具有优良的塑性;而硬的马氏体则赋予其高的强度。
鉴于此,综合性能较好的58 0MPa级DP钢取代了原来的440MPa级钢作为汽车车身结构件的主要材料。
随之研制的780MPa级DP钢,现在广泛应用于汽车结构件。
最近,通过控制马氏体的体积分数、分散状态和两相的硬度差,从而改善DP钢的伸长翻边性不足,研制出延展性和伸长翻边性兼备的980MPa级DP钢。
众所周知,汽车车身零件绝大部分是冲压成形件。
因此,为保证较复杂零件的冲制,需进一步提高汽车车身用高强度钢的延展性。
汽车高强度钢热成型关键技术研究

汽车高强度钢热成型关键技术研究摘要:迅猛发展的汽车工业更加突显出环保、能源等方面的难题。
汽车用高强度钢对汽车工业的发展起着举足轻重的作用,是汽车轻量化的关键材料之一。
在未来的数年内,我国汽车工业将会取得更大的发展,对汽车用高强度钢的要求也会越来越多,汽车开发公司需进一步加强与钢铁研究者的合作,这对发展汽车用高强度钢板,促进我国汽车行业发展以及提高我国汽车竞争能力大有裨益。
关键词:汽车高强度钢;成型技术1高强度板料的特性高强度板料具有很高的抗拉强度、耐冲击性,其抗拉强度是普通材料的3倍甚至更多,因此对汽车的碰撞安全性能非常重要。
高强度板料的这种特性对汽车的安全、减重和节能是非常重要的,其效果也是非常明显的。
研究结果表明,使用高强度板料,汽车冲压件抗拉强度从220MPa提高到700MPa,材料厚度从1.8mm减小到1.4mm,而材料可吸收冲击能指数则基本保持不变。
汽车减重也与材料强度密切相关。
研究表明,材料抗拉强度从300MPa左右提高到900MPa左右,汽车减重率则从25%左右提升到40%左右。
由此可以看出使用高强度板料已是汽车行业以后发展的趋势。
但板料的强度和塑性一般是矛盾的,板料强度的提高必然导致塑性下降。
而板料塑性的下降就为冲压件的成型带来了很多问题和难题,回弹就是其中冲压件成型过程中很难避免的缺陷之一。
如何预防、减少高强度板料的回弹就成了摆在高强度板料冲压件面前最大的问题。
2高强度钢热成型技术2.1成型原理高强度钢热成型技术的原理是将高强度钢在加热过程中实现相变,使珠光体和铁素体均匀奥氏体化,然后在模具内冲压成型,同时利用模具内的冷却水道,将冲压成型的零件快速均匀的冷却,从而将奥氏体转化为马氏体。
进而使汽车用高强度钢获得更高的屈服强度和抗拉强度,有效的提升车身的整体性能,获得更高的安全性。
2.2特点对于汽车用高强度钢热成型技术,由于其相对于一般的冷冲压零件具有更高的强度,可以减少车身加强板的使用,在汽车制造过程中带来更高安全性的同时也实现了整车质量的轻量化。
高强度钢在汽车行业的应用研究
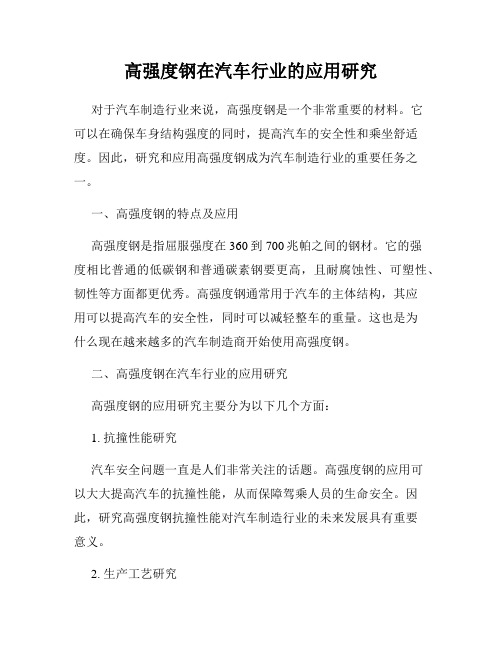
高强度钢在汽车行业的应用研究对于汽车制造行业来说,高强度钢是一个非常重要的材料。
它可以在确保车身结构强度的同时,提高汽车的安全性和乘坐舒适度。
因此,研究和应用高强度钢成为汽车制造行业的重要任务之一。
一、高强度钢的特点及应用高强度钢是指屈服强度在360到700兆帕之间的钢材。
它的强度相比普通的低碳钢和普通碳素钢要更高,且耐腐蚀性、可塑性、韧性等方面都更优秀。
高强度钢通常用于汽车的主体结构,其应用可以提高汽车的安全性,同时可以减轻整车的重量。
这也是为什么现在越来越多的汽车制造商开始使用高强度钢。
二、高强度钢在汽车行业的应用研究高强度钢的应用研究主要分为以下几个方面:1. 抗撞性能研究汽车安全问题一直是人们非常关注的话题。
高强度钢的应用可以大大提高汽车的抗撞性能,从而保障驾乘人员的生命安全。
因此,研究高强度钢抗撞性能对汽车制造行业的未来发展具有重要意义。
2. 生产工艺研究汽车制造行业中的工艺问题一直是影响汽车制造水平和质量的主要因素之一。
高强度钢的生产工艺较为复杂,需要钢铁厂家进行特殊的处理,以保证钢材的质量和性能。
因此,研究高强度钢的生产工艺对提高汽车制造的效率和质量是十分重要的。
3. 焊接技术研究高强度钢的应用也为汽车制造行业带来了一定的技术挑战,其中最大的挑战之一就是高强度钢的焊接技术问题。
高强度钢与普通钢的焊接比较困难,需要采用特殊的焊接技术。
因此,研究高强度钢的焊接技术对推动汽车制造行业的技术创新和发展也具有很大的意义。
三、高强度钢在未来的应用前景随着汽车制造行业的不断发展壮大,高强度钢也将继续得到广泛的应用。
为了提高汽车的性能、安全及耐用性,汽车制造商还需要加大对高强度钢研究的力度。
同时,这也激发了高强度钢制造商持续推进研发进程,以更好地满足汽车制造行业的需求。
高强度钢的应用可以满足未来汽车制造行业对材料性能和品质的不断追求,并对汽车安全和环保提供全面保障。
总之,高强度钢在汽车制造行业的应用研究具有巨大的潜力。
超高强度钢在汽车车身上的应用
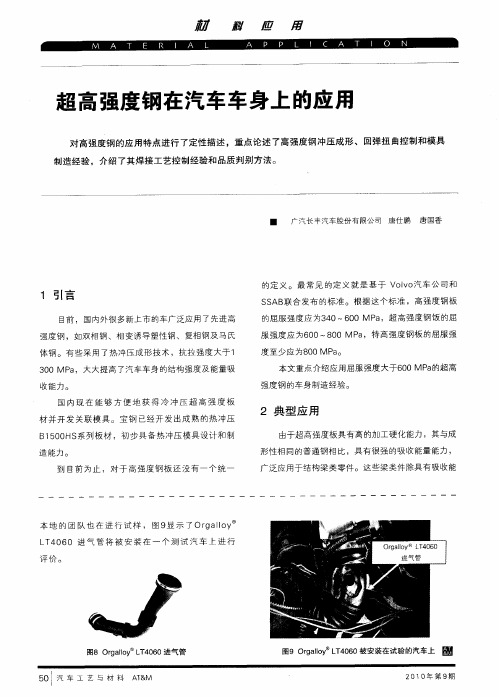
1 引言
目前 ,国内外很 多新 上市 的车广 泛应 用 了先进高 强 度钢 ,如双 相钢 、相 变诱 导塑性 钢 、复相 钢及 马 氏 体 钢 。有 些采 用 了热 冲压 成 形技 术 ,抗 拉 强度 大于 1 3 0 MP ,大 大提高 了汽 车车身 的结构 强度 及能量 吸 0 a
一
样 的优 点 。 典 型 的 应 用 零 件 有 前 、 后 门左 / 防 撞 右 杆 ( ),前 、 后 保 险 杠 ,A 加 强 板 ,B 加 强 梁 柱 柱 板 ,C 加 强 板 ,下 边 板 ,地 板 中 通 道 , 车 顶 加 强 柱
梁等。
种 将含 硼 元 素 坯 料 加 热 并 转 移 到成 形 工具 中 的 工 艺 ,成 形和 硬 化 一 步 完 成 , 回火 可 以通 过在 压 力机 中零 件 冲压 过 程 中 自身 的热 量 完 成 ,零 件 可 以 获 得
B 0 H 系列 板 材 ,初步 具 备 热冲 压 模具 设 计和 制 5 0 S 1
造 能 力。
到 目前 为 止 ,对于 高 强度 钢 板 还 没 有 一 个统 一
广泛 应用 于结 构梁 类零 件。 这些梁 类件 除具 有 吸收能
本地 的 团 队 也 在 进 行 试 样 , 图9显 示 了 0r a l y I 。 g o
的材 质 、硬 度和 表 面 处理 上 。材 质 使 用DC5 、 D 、 3 2
在 最 小 。 热 冲 压 一 般 有 6 工 序 :剪 板 落 料 、 热 冲 道 压 、激 光剪 切 和 冲 孔 、 喷 丸 除 锈 和 涂 防 锈 油 ,其 中 只 有 第 二道 工 序 热 冲 压 使 用 模 具 。热 冲 模 与普 通 模 具 的 区 别也 较 大 , 内部 要 钻 空 以布 置 复 杂 的冷 却 水
高强度钢材在汽车制造中有何应用
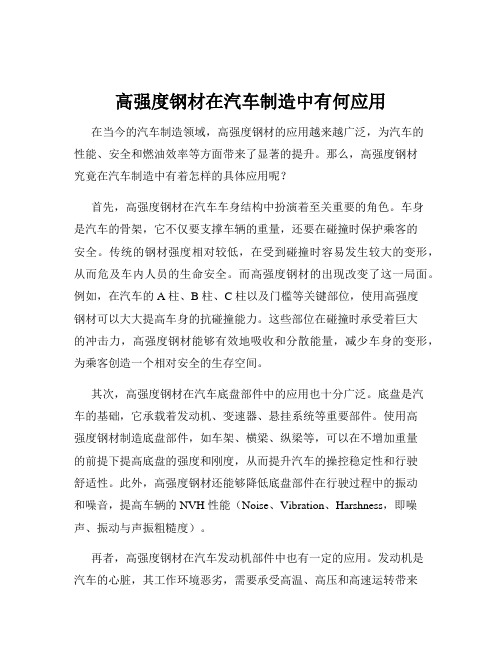
高强度钢材在汽车制造中有何应用在当今的汽车制造领域,高强度钢材的应用越来越广泛,为汽车的性能、安全和燃油效率等方面带来了显著的提升。
那么,高强度钢材究竟在汽车制造中有着怎样的具体应用呢?首先,高强度钢材在汽车车身结构中扮演着至关重要的角色。
车身是汽车的骨架,它不仅要支撑车辆的重量,还要在碰撞时保护乘客的安全。
传统的钢材强度相对较低,在受到碰撞时容易发生较大的变形,从而危及车内人员的生命安全。
而高强度钢材的出现改变了这一局面。
例如,在汽车的 A 柱、B 柱、C 柱以及门槛等关键部位,使用高强度钢材可以大大提高车身的抗碰撞能力。
这些部位在碰撞时承受着巨大的冲击力,高强度钢材能够有效地吸收和分散能量,减少车身的变形,为乘客创造一个相对安全的生存空间。
其次,高强度钢材在汽车底盘部件中的应用也十分广泛。
底盘是汽车的基础,它承载着发动机、变速器、悬挂系统等重要部件。
使用高强度钢材制造底盘部件,如车架、横梁、纵梁等,可以在不增加重量的前提下提高底盘的强度和刚度,从而提升汽车的操控稳定性和行驶舒适性。
此外,高强度钢材还能够降低底盘部件在行驶过程中的振动和噪音,提高车辆的 NVH 性能(Noise、Vibration、Harshness,即噪声、振动与声振粗糙度)。
再者,高强度钢材在汽车发动机部件中也有一定的应用。
发动机是汽车的心脏,其工作环境恶劣,需要承受高温、高压和高速运转带来的巨大负荷。
例如,发动机的缸体、缸盖、曲轴等部件可以采用高强度钢材制造,以提高其强度和耐磨性,延长发动机的使用寿命。
同时,高强度钢材的使用还有助于减轻发动机的重量,提高发动机的功率输出和燃油经济性。
除了上述主要部件,高强度钢材在汽车的悬挂系统、转向系统、制动系统等部件中也有不同程度的应用。
在悬挂系统中,高强度钢材可以制造弹簧、减震器等部件,提高悬挂系统的承载能力和响应速度;在转向系统中,高强度钢材可以制造转向拉杆、转向节等部件,确保转向的精准性和可靠性;在制动系统中,高强度钢材可以制造制动盘、制动卡钳等部件,提高制动系统的性能和耐久性。
关于高强度钢作为汽车轻质材料的应用分析

10AUTO TIMEFRONTIER DISCUSSION | 前沿探讨关于高强度钢作为汽车轻质材料的应用分析1 汽车用高强度钢研究进展在世界范围内的汽车行业中,高强度钢本身已经实现了较好的普及,而超高强度钢板材料才是当下世界范围内汽车行业所关注的焦点。
对于高强度钢来说,马氏体钢与热冲压成形用钢在汽车行业中的应用较为广泛,马氏体钢的抗拉强度高达1500MPa ,而热冲压成形用钢的最高强度能够达到1800MPa ,这就使得两种高强度钢材都能够较好的满足汽车的轻量化需求,但对于这两种高强度钢来说,其本身很容易在加热状态下出现表面脱碳和氧化起皮问题,这类问题的出现就会直接影响其本身强度。
除了马氏体钢与热冲压成形用钢外,Q &P 钢、TG 钢、TWIP 钢等高强度钢还处于研究阶段,但笔者希望这些新型高强度钢材能够早日在我国汽车行业中实现广泛应用。
2 高强度钢材料的性能下面主要详细介绍了屈服强度700MPa 级热轧微合金高强度钢典型材料的成分、强化机理、力学性能,并以载货车车架纵梁和客车车身骨架等为例,说明了该钢种对商用车轻量化的作用。
2.1 材料成分及强化机理表1为DOMEX700MC 钢板和QStE700TM 钢板的化学成分实测值。
根据上面的测试表中我们能够清楚的看到,这两种材料的自身特点主要是碳含量较低,并且钢李伟良江苏建康汽车有限公司 江苏省南京市 211500摘 要: 随着我国的经济不断发展,如果将汽车轻量化那么可以降低汽车自重,提高燃油经济性,因此这是当今汽车技术主要发展方向之一。
并且随着国家节能减排的逐步实施以及对于治超限载力度的不断加大,汽车的轻量化势在必行。
虽然铝与塑料在汽车制造中所占的比重不断提高,但钢铁仍旧是汽车制造的主要材料,这就使得钢铁的轻质材料化能够较好的满足汽车的轻量化需求,下面本文对于高强度钢作为汽车轻质材料进行研究。
关键词:高强度;钢汽车;轻质材料;应用板中都含有大量的微量元素。
车身高强度钢材参数

车身高强度钢材参数
车身高强度钢材是指用于汽车制造的高强度钢材,它具有优异
的强度、韧性和耐腐蚀性能,能够提高汽车的安全性能和减轻车身
重量。
一般来说,车身高强度钢材的参数包括以下几个方面:
1. 强度参数,车身高强度钢材通常具有较高的屈服强度和抗拉
强度。
这些参数可以通过屈服强度(yield strength)和抗拉强度(tensile strength)来表示。
屈服强度是材料开始变形的强度,
而抗拉强度是材料抵抗拉伸力的能力。
2. 成分参数,车身高强度钢材的成分参数包括碳含量、合金元
素含量等。
这些成分可以影响钢材的强度、硬度、韧性和耐腐蚀性能。
3. 加工参数,车身高强度钢材的加工参数包括冷加工硬化指数、成形性能等。
这些参数可以影响钢材的加工性能,包括冲压、弯曲、拉伸等加工过程中的表现。
4. 耐腐蚀参数,车身高强度钢材通常需要具有良好的耐腐蚀性能,这可以通过相关的参数来评价,比如盐雾试验、腐蚀试验等。
5. 其他参数,除了上述参数外,车身高强度钢材还可能涉及到其他参数,比如热处理参数、热膨胀系数等。
总的来说,车身高强度钢材的参数涉及材料的力学性能、化学成分、加工性能、耐腐蚀性能等多个方面。
这些参数对于汽车制造具有重要意义,能够直接影响汽车的安全性能、节能性能和环保性能。
高强钢在汽车制造中的应用研究

高强钢在汽车制造中的应用研究随着汽车工业的快速发展,高强钢已经成为了汽车制造中不可或缺的一部分。
高强钢可用于汽车的车身、底盘等各个部位,不仅提高了汽车的安全性能,还有助于降低汽车的油耗和碳排放。
一、高强钢的定义和特点高强钢是指屈服强度在390-430MPa以上的钢材,其主要特点是强度高、延展性好、蠕变强度高、强度与塑性的比值高。
相比传统的钢材,高强钢的使用可以大幅度降低车身的重量,并提高车身的刚度和强度,从而使得汽车的安全性能得到提高。
二、高强钢在汽车制造中的应用1.车身用高强钢高强钢在汽车车身制造中的应用越来越广泛。
高强度钢板可以帮助汽车在碰撞时吸收更多的能量,从而降低车内人员受到的冲击力,提高汽车的碰撞安全性。
同时,高强钢的使用还能够缩小车身结构的间隙,减少水、沙、尘等入侵车内的现象。
车身用高强钢的类型包括双相钢、韧性增强高强度钢以及淬火加回火高强度钢等。
2.底盘用高强钢汽车底盘部位的零部件同样可以使用高强度钢材制造。
比如,使用高强度钢材制造车辆悬挂系统中的各个零部件,可以增加底盘的刚度和强度,提高车辆的行驶稳定性和操控性。
同时,高强度钢材的应用还可以缩小零部件的厚度,进一步减小车辆的重量。
三、高强钢在汽车制造中的优势1.提高汽车安全性能高强钢具有优异的强度和韧性,能够提供更好的碰撞保护,保护驾驶员和乘客的生命安全。
同时,高强度钢的优秀性能也可以帮助汽车在极端条件下进行更好的应对,如在崎岖不平的路面或高速行驶中的负载变化,都能保持车身的稳定性和强度。
2.提高汽车的经济性能由于高强度钢具有更优异的强度和延展性,所以同样的载荷情况下,高强度钢零件的重量会比普通钢材更轻,这也就意味着汽车在同等质量的情况下,可以搭载更多的部件和功能,减少汽车的油耗和碳排放。
3.提高汽车的可维修性高强度钢所需的很少的车密度,使汽车更容易进行维修和维护。
高强度钢的较小的形变和碰撞会更容易进行恢复,从而增加了汽车的可靠性和可用性。
trip钢研究的现状与发展的概述

trip钢研究的现状与发展的概述trip钢研究的现状与发展的概述引言:近年来,新材料的研究与应用取得了长足的进展,在其中,trip钢作为一种重要的新型高强度钢材备受瞩目。
trip钢以其优异的力学性能和耐腐蚀性能,广泛应用于汽车、建筑和航空航天等领域。
本文将就trip钢研究的现状与发展进行深入探讨,并分享我的观点和理解。
一、trip钢的基本特性1. 高强度:trip钢以其出色的强度特性而闻名,常用于制造高强度结构件,如车身、发动机支撑件等。
其抗拉强度和屈服强度明显高于传统钢材。
2. 良好的塑性:trip钢具有良好的塑性,不易发生断裂,能够在挤压、拉伸等工艺过程中保持较好的可塑性,有利于工程加工和成形。
3. 优异的耐腐蚀性:trip钢通过合金化和微观组织调控,能够有效抵御外界环境对钢材的侵蚀,具有很好的耐腐蚀性能,延长了使用寿命。
4. 良好的焊接性能:trip钢在焊接过程中表现出较低的热裂倾向和良好的焊缝塑性,使其成为工程结构中的理想材料。
二、trip钢研究的现状1. 合金化研究:通过添加特定的合金元素,如锰、硅等,可以有效提高trip钢的强度和塑性,改善其综合性能。
目前,研究人员正在探索不同合金化方式对trip钢性能的影响,并努力寻找合适的合金化配方。
2. 微观组织调控:trip钢的微观组织对其力学性能具有重要影响。
通过控制相变温度和相变形貌等因素,研究人员正在寻求最佳的微观组织设计,以提高trip钢的强度和韧性。
3. 加工工艺研究:trip钢的加工过程对其综合性能具有重要影响。
目前,研究人员正致力于开发适用于trip钢的新型加工工艺,以提高生产效率和降低成本。
三、trip钢研究的未来发展趋势1. 多功能性:人们对trip钢的要求越来越高,希望其不仅具有高强度和良好的塑性,还能够具备其他功能,如自修复、防腐蚀等。
未来,研究人员将进一步探索多功能trip钢的合成方法和性能优化策略。
2. 精细化制备:目前,trip钢制备过程中存在着杂质的掺入和组织非均匀的问题。
汽车车身结构的强度与刚度分析

汽车车身结构的强度与刚度分析汽车的车身结构是保证安全和性能的基础之一。
车身的强度和刚度对汽车在碰撞、行驶和悬挂系统上承受的力量和压力至关重要。
本文将分析汽车车身结构的强度和刚度,并探讨对车辆性能和安全的影响。
一、强度分析汽车车身的强度是指其在受到外部力量作用下不发生破坏的能力。
强度分析需要考虑车身所承受的各种载荷,如碰撞、颠簸、悬挂系统的负载等。
其中,碰撞是最重要的考虑因素之一。
1. 碰撞强度分析碰撞是指车辆在发生事故时所受到的撞击力。
车身的碰撞强度取决于车身所采用的材料、结构设计和制造工艺等。
高强度钢材料的运用可以提高车身的碰撞强度,并减少碰撞事故对乘车人员的伤害。
2. 抗压强度分析抗压强度是指车身在受到压力作用下不发生破坏的能力。
汽车行驶中会受到来自地面的压力,而高强度材料和合理的结构设计可以提高车身的抗压强度,确保车辆在不同路面条件下的稳定性和安全性。
二、刚度分析汽车车身的刚度是指其抵抗形变的能力。
刚度分析需要考虑车身在行驶过程中受到的扭转、弯曲和弯矩等力的影响。
1. 扭转刚度分析扭转刚度是指车身在受到扭转力作用下不发生过大形变的能力。
合适的车身刚度可以提高汽车的操控性能和行驶稳定性。
2. 弯曲刚度分析弯曲刚度是指车身在受到弯曲力作用下不发生过大形变的能力。
合理的材料选择和结构设计可以提高车身的弯曲刚度,从而提升汽车的稳定性和乘坐舒适性。
3. 弯矩刚度分析弯矩刚度是指车身在受到弯矩力作用下不发生过大形变的能力。
弯矩力通常来自于车辆行驶过程中的颠簸和不平路面,因此,合适的刚度设计可以提高车身的抗颠簸性能和悬挂系统的工作效果。
三、强度与刚度的影响汽车车身的强度和刚度不仅影响车辆的性能,还直接关系到乘员的安全。
1. 性能影响强度和刚度的增加可以提高汽车的操控性能、加速性能和制动性能。
车身的扭转刚度和弯曲刚度决定了车辆在转弯和行驶过程中的稳定性和响应灵敏度。
2. 安全影响强度和刚度的提高可以增加车辆在碰撞事故中乘员的保护能力。
汽车高强度钢板材料解析
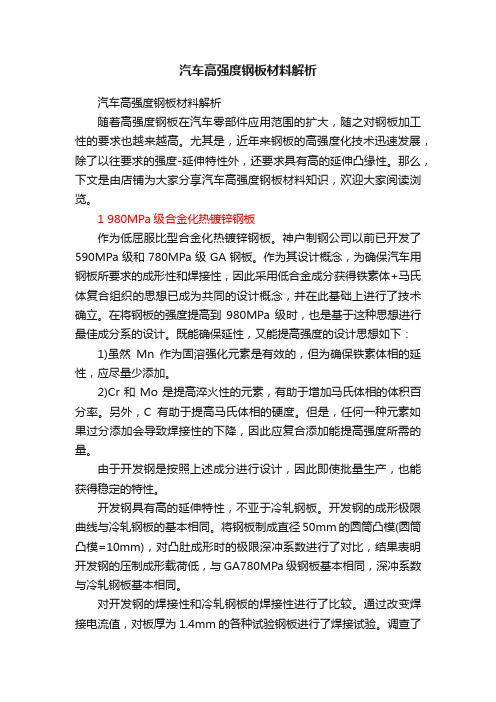
汽车高强度钢板材料解析汽车高强度钢板材料解析随着高强度钢板在汽车零部件应用范围的扩大,随之对钢板加工性的要求也越来越高。
尤其是,近年来钢板的高强度化技术迅速发展,除了以往要求的强度-延伸特性外,还要求具有高的延伸凸缘性。
那么,下文是由店铺为大家分享汽车高强度钢板材料知识,欢迎大家阅读浏览。
1 980MPa级合金化热镀锌钢板作为低屈服比型合金化热镀锌钢板。
神户制钢公司以前已开发了590MPa级和780MPa级GA钢板。
作为其设计概念,为确保汽车用钢板所要求的成形性和焊接性,因此采用低合金成分获得铁素体+马氏体复合组织的思想已成为共同的设计概念,并在此基础上进行了技术确立。
在将钢板的强度提高到980MPa级时,也是基于这种思想进行最佳成分系的设计。
既能确保延性,又能提高强度的设计思想如下:1)虽然Mn作为固溶强化元素是有效的,但为确保铁素体相的延性,应尽量少添加。
2)Cr和Mo是提高淬火性的元素,有助于增加马氏体相的体积百分率。
另外,C有助于提高马氏体相的硬度。
但是,任何一种元素如果过分添加会导致焊接性的下降,因此应复合添加能提高强度所需的量。
由于开发钢是按照上述成分进行设计,因此即使批量生产,也能获得稳定的特性。
开发钢具有高的延伸特性,不亚于冷轧钢板。
开发钢的成形极限曲线与冷轧钢板的基本相同。
将钢板制成直径50mm的圆筒凸模(圆筒凸模=10mm),对凸肚成形时的极限深冲系数进行了对比,结果表明开发钢的压制成形载荷低,与GA780MPa级钢板基本相同,深冲系数与冷轧钢板基本相同。
对开发钢的焊接性和冷轧钢板的焊接性进行了比较。
通过改变焊接电流值,对板厚为1.4mm的各种试验钢板进行了焊接试验。
调查了焊接接头的剪切抗拉强度和断裂后测定的熔核直径的关系,结果可知开发钢的熔核断裂临界直径比冷轧钢板的大。
另外,在发生熔核断裂时,接头强度大大超过了JIS标准。
十字形拉力强度的断裂形式受化学成分的影响大,即使母材强度增加,在发生熔核内部断裂和剥落断裂的情况下,有时强度也没有发生变化。
高强度钢在汽车制造中的应用研究

高强度钢在汽车制造中的应用研究高强度钢是指抗拉强度大于等于440MPa的钢材。
它具有高强度、高延展性、高韧性等优异性能,同时具有较高的强度重量比和抗腐蚀性能。
因此,高强度钢在汽车制造中被广泛应用,可以提高汽车的安全性、节约材料和降低能耗。
一、高强度钢在汽车安全性中的应用高强度钢的应用可以提高汽车的整体刚性,更好地抵御碰撞和挤压。
高强度钢还可以用来制造汽车的防护结构,如前保险杠,以减少碰撞造成的伤害。
此外,高强度钢在汽车底盘和车门等部位的应用,也可以增强其防护性能,保护车内人员的安全。
二、高强度钢在节约材料方面的应用高强度钢具有密度小、强度高的特点,可以在保证刚度和强度的情况下,达到减轻汽车自身重量的目的。
这样不仅可以节约材料,同时还可以降低汽车对环境的污染,提高燃油效率。
三、高强度钢在减少车辆能耗方面的应用高强度钢可以降低汽车的整体重量,并提高汽车的动态性能,从而降低车辆的能耗。
这样的应用,可以在减少车辆使用过程中的能量消耗的同时,降低车辆的运行成本,还可以起到促进汽车行业可持续发展的作用。
四、高强度钢在汽车制造中的制造工艺研究高强度钢的制造工艺与常规钢材不同,因此在汽车制造中的应用,需要针对不同的应用场景,制定不同的生产工艺。
目前,汽车制造企业对高强度钢的加工性能和连接性能等进行了深入研究,并逐步实现高强度钢及其复合材料的快速、精准、高效加工。
五、高强度钢的市场前景高强度钢在汽车制造中的应用趋势非常明显,目前国内外大部分汽车主机厂和零部件厂都在积极推广高强度钢的应用。
根据市场统计数据,随着汽车安全和环保的重要性不断提升,高强度钢的市场需求将会不断扩大,预计未来国内高强度钢的市场需求将逐年增长。
总之,高强度钢在汽车制造中具有广泛的应用前景和良好的市场前景,未来将会成为汽车制造中不可或缺的重要材料之一。
同时,随着汽车安全和环保要求的不断提高,高强度钢在汽车制造中将会得到更加广泛的应用。
汽车车身用高强度钢及其加工性能的探讨
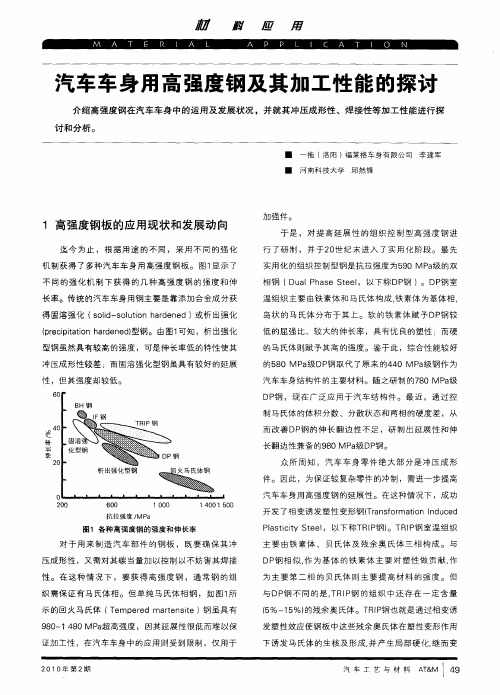
镇 静 钢 之后 第 三代 冲 压 用钢 , 的 生产 已成 为一个 国 它
家 汽车用 钢板 生产 水平 的标 志。 为 了弥 补 I钢 强度 的不 足 ,提 高车 身外 表零件 抗 F
C mso k等人提 出在 钢中加 T 消 除 C、N o tc I 闻隙 原 子 , 降低 C N含 嚣 ,可提 高 钢 的 、
(%~ 5 的 残余 奥 氏体 。T f钢 也就 是通 过相 变诱 5 1 %) RP 发 塑 性效应 使 钢板 中这 些残 余奥 氏体 在 塑性 变形 作用
下 诱 发 马 氏体 的生 核 及 形成 , 并产 生 局 部硬 化 而 变 继
9 0 1 8 a 高强度 ,因其延 展 性很 低而 难 以保 8 ~ 0MP 超 4 证加 工 性 ,在汽 车车 身 中的应 用则 受到 限制 ,仅 用 于 2 1 年第2 0 o 期
汽 车 工 艺 与 材 料 A& 4 TM I 9 1
I
赫
融 匝 用
形 不再 集 中在 局 部, 相 变均 匀 扩散 到 整 个材 料ቤተ መጻሕፍቲ ባይዱ以提 使
生 产 出C≤00 2 的现 代I 钢。 图3 .0 % F 显示 了I钢研 制 F
高钢板 的强度和塑性 ,实现 了强度和塑性较好的统
众所 周 知 ,汽 车 车 身 零件 绝 大部 分 是 冲压 成 形 件 。 因此 ,为保证 较 复杂 零件 的冲 制 ,需进 一步 提 高 汽车 车身 用高 强度 钢 的延 展性 。在 这种 情 况下 ,成功
抗 拉 强震 / P M a
开 发 了相 变诱 发塑 性 变形 钢(rn f r t n Id c d T a so ma i n u e o
得 固溶 强化 ( oi s l i ad n d) s l — ou o h e e 或析 出强 化 d tn r
车身材料了解高强度钢在汽车制造中的应用

车身材料了解高强度钢在汽车制造中的应用近年来,随着汽车工业的不断发展,对于车身材料的要求也越来越高。
高强度钢作为一种优秀的材料,逐渐在汽车制造中得到广泛应用。
本文将带您了解高强度钢在汽车制造中的应用。
一、高强度钢的特点高强度钢具有优异的强度、韧性和耐腐蚀性能,相较于传统的普通钢材,具有更高的强度和更轻的重量。
高强度钢通过合理的合金设计和热处理工艺,使得钢材获得了更好的力学性能,并且在成本上也具备了一定的优势。
因此,高强度钢成为了汽车制造领域的热门材料。
二、高强度钢在汽车制造中的应用1. 结构件高强度钢在汽车的结构件中得到了广泛应用。
例如,车辆底盘和骨架是车辆的重要组成部分,需要具备较高的强度和刚性。
高强度钢具有优异的承载能力和疲劳寿命,因此成为了制造车身结构件的理想材料。
高强度钢可以有效地提高车辆的安全性和稳定性。
2. 安全件高强度钢在汽车的安全件中也有重要的应用。
例如,车辆的安全架构和各种安全装备(如安全气囊和安全带等)需要具备足够的强度和刚性以保护车辆乘员的安全。
高强度钢能够有效地吸收和分散碰撞能量,提供更好的保护性能。
3. 节能环保高强度钢的应用还有助于汽车的节能环保。
相较于传统的普通钢材,高强度钢具有更轻的重量,并且可以使用较薄的板材,从而减轻了车辆的整体重量。
减轻车辆重量可以降低燃油消耗,减少尾气排放,减轻对环境的污染。
因此,高强度钢的应用是推动汽车行业可持续发展的重要因素之一。
三、高强度钢的挑战与前景虽然高强度钢在汽车制造中具有广泛的应用前景,但也存在一些挑战。
首先,高强度钢的生产工艺相较于普通钢材更为复杂,需要更加精细的控制。
其次,高强度钢的成本相对较高,这也是其在大规模应用中的一个限制因素。
然而,随着技术的不断进步和制造工艺的改善,高强度钢在汽车制造中的应用前景依然十分广阔。
随着对车辆安全性和节能环保的要求越来越高,高强度钢将成为一种必不可少的材料。
同时,应用高强度钢材料也有助于汽车行业的技术创新和发展。
车身材料的强度与刚度分析

车身材料的强度与刚度分析1. 介绍随着汽车工业的快速发展,车身材料的选择变得越来越重要。
车身材料的强度和刚度对汽车的性能、安全性和经济性都有着重要影响。
在本篇文章中,我们将对车身材料的强度和刚度进行深入分析,探讨其对汽车性能的影响。
2. 车身材料的强度车身材料的强度是指材料抵抗外部应力的能力。
一种材料的强度取决于其原子结构和化学组成。
常见的车身材料包括钢铁、铝合金和纤维增强复合材料等。
2.1 钢铁钢铁是目前最常用的车身材料之一,具有优异的强度和刚性。
由于其高抗拉强度和抗压强度,钢铁能够保护车内乘员免受碰撞时的严重伤害。
钢铁的使用还可以增加车身的稳定性,提高操控性能。
2.2 铝合金铝合金相比于钢铁,在重量上更轻且具有较好的强度。
这使得使用铝合金可以减少汽车的整体重量,从而提高燃油效率和减少环境污染。
然而,与钢铁相比,铝合金的强度稍差,容易发生塑性变形和断裂。
2.3 纤维增强复合材料纤维增强复合材料是一种由纤维和树脂组成的复合材料。
这种材料具有优异的强度和刚度,同时重量轻、耐腐蚀性好。
由于其高比强度和比刚度,纤维增强复合材料在高端汽车制造业中被广泛应用。
3. 车身材料的刚度车身材料的刚度是指材料对外部应力的响应能力。
刚度越高,材料在受力时变形越小。
车身材料的刚度对车辆的操控性、平稳性和乘坐舒适性具有重要影响。
3.1 材料的弹性模量材料的弹性模量是描述材料刚度的一个物理量。
弹性模量越高,材料的刚度也就越高。
由于刚度的要求,汽车制造商通常选择具有较高弹性模量的材料,以提高车辆的操控性和稳定性。
4. 强度与刚度对汽车性能的影响强度和刚度是车身材料最重要的性能之一。
它们对汽车的性能、安全性和经济性都有着重要影响。
4.1 性能车身材料的强度和刚度直接影响车辆的加速性能、行驶稳定性和制动效果。
强度和刚度高的车身材料可以提供更好的操控性能和车辆稳定性,提高驾驶体验。
4.2 安全性车身材料的强度对汽车的碰撞安全性具有重要影响。
[高强,汽车,技术]试论高强钢成形技术及其在汽车轻量化中的应用
![[高强,汽车,技术]试论高强钢成形技术及其在汽车轻量化中的应用](https://img.taocdn.com/s3/m/8292691baef8941ea66e0573.png)
试论髙强钢成形技术及其在汽车轻量化中的应用汽车轻疑化是指在保证汽车的强度和安全性能的前提下,尽可能地减轻汽车的整车质量, 从而提高汽车的动力性,减少燃料消耗,降低排气污染。
汽车的快速发展方便了人们的生活,但同时带来了金属、石油等资源、能源的过量消耗,大气严重污染,通过汽车轻量化实现降低排放和油耗成为汽车工业最具挑战的目标。
有研究表明,当钢板厚度分别减小0. 05mm. 0.1mm和0. 15mm 时,车身减重分别为6%、12%和18%,可见增加钢板强度的同时减小板厚是减轻车重的主要途径。
高强钢具有较高的强度,且成本较轻金属低,汽车采用先进高强钢的主要效果有:高强钢的使用降低了板厚使得汽车结构轻量化、汽车的抗凹陷性、耐久强度和大变形冲击强度安全性均得到提高。
髙强钢的优点使得英在汽车行业中得到快速发展及广泛应用,如1980年日本和欧洲的汽车公司,白车身中高强钢用量分別为12%和5%,目前均上升到50%以上。
高强钢的应用不仅为轻量化创造了更多的机遇,更有助于使汽车达到轻量化和提髙安全性的统一。
一、髙强钢的种类高强度钢板的分类主要有按冶金特点、强化机理和生产工艺等几种划分方法。
1.按冶金特点分类根据国际钢铁协会U S L - A B项目的左义,屈服强度为210〜550MPa及抗拉强度为270〜700M P a的为高强度钢(简称H S S)。
普通高强度钢为单一铁素体组织,由于采用了以相变为主的复合强化方法,基体的强度和综合性能得到提髙。
普通髙强度钢包括有微合金钢、碳镭钢、烘烤硬化钢、各向同性钢、髙强度I F钢和低合金高强度钢等几种。
屈服强度大于550M P a及抗拉强度大于700M P a的则称为先进高强度钢(简称A H S S)。
A H S S 的研究基于H S S朝2个方向发展,一个方向是强度基体不变,提髙其塑性;期一个方向是塑性基体不变提高幷强度。
强度提髙的钢种包括复向钢(CP)、马氏体钢(MS)等,塑性提髙的钢种包括有双相钢(C P)、相变诱发塑性钢(T R I P)等。
- 1、下载文档前请自行甄别文档内容的完整性,平台不提供额外的编辑、内容补充、找答案等附加服务。
- 2、"仅部分预览"的文档,不可在线预览部分如存在完整性等问题,可反馈申请退款(可完整预览的文档不适用该条件!)。
- 3、如文档侵犯您的权益,请联系客服反馈,我们会尽快为您处理(人工客服工作时间:9:00-18:30)。
汽车车身用高强度钢及其加工性能的探讨
1 高强度钢板的应用现状和发展动向
迄今为止,根据用途的不同,采用不同的强化机制获得了多种汽车车身用高强度钢板。
图1显示了不同的强化机制下获得的几种高强度钢的强度和伸长率。
传统的汽车车身用钢主要是靠添加合金成分获得固溶强化(solid-solution hardened)或析出强化(precipitation hardened)型钢。
由图1可知,析出强化型钢虽然具有较高的强度,可是伸长率低的特性使其冲压成形性较差;而固溶强化型钢虽具有较好的延展性,但其强度却较低。
图1 各种高强度钢的强度和伸长率
对于用来制造汽车部件的钢板,既要确保其冲压成形性,又需对其碳当量加以控制以不妨害其焊接性。
在这种情况下,要获得高强度钢,通常钢的组织需保证有马氏体相。
但单纯马氏体相钢,如图1所示的回火马氏体(Tempered martensite)钢虽具有980~1480MPa超高强度,因其延展性很低而难以保证加工性,在汽车车身中的应用则受到限制,仅用于加强件。
于是,对提高延展性的组织控制型高强度钢进行了研制,并于20世纪末进入了实用化阶段。
最先实用化的组织控制型钢是抗拉强度为590MPa级的双相钢(Dual Phase Steel,以下称DP钢)。
DP钢室温组织主要由铁素体和马氏体构成,铁素体为基体相,岛状的马氏体分布于其上。
软的铁素体赋予DP钢较低的屈强比、较大的伸长率,具有优良的塑性;而硬的马氏体则赋予其高的强度。
鉴于此,综合性能较好的58 0MPa级DP钢取代了原来的440MPa级钢作为汽车车身结构件的主要材料。
随之研制的780MPa级DP钢,现在广泛应用于汽车结构件。
最近,通过控制马氏体的体积分数、分散状态和两相的硬度差,从而改善DP钢的伸长翻边性不足,研制出延展性和伸长翻边性兼备的980MPa级DP钢。
众所周知,汽车车身零件绝大部分是冲压成形件。
因此,为保证较复杂零件的冲制,需进一步提高汽车车身用高强度钢的延展性。
在这种情况下,成功开发了相变诱发塑性变形钢(Transformation Induce d Plasticity Steel,以下称TRIP钢)。
TRIP钢室温组织主要由铁素体、贝氏体及残余奥氏体三相构成。
与DP钢相似,作为基体的铁素体主要对塑性做贡献,作为主要第二相的贝氏体则主要提高材料的强度。
但与DP钢不同的是,TRIP钢的组织中还存在一定含量(5%~15%)的残余奥氏体。
TRIP钢也就是通过相变诱发塑性效应使钢板中这些残余奥氏体在塑性变形作用下诱发马氏体的生核及形成,并产生局部硬化,继而变形不再集中在局部,使相变均匀扩散到整个材料以提高钢板的强度和塑性,实现了强度和塑性较好的统一,解决了强度和塑性的矛盾。
TRIP钢与其他同级别的高强度钢相比,最大特点是兼具高强度和高延展性,可冲制较复杂的零件;T RIP钢还具有高的抗冲撞吸收功的特点,一旦遭遇碰撞,将通过自身形变来吸收能量,常用于汽车的保险杠、汽车底盘等防撞部位。
此外,这种钢还因其优良的高速力学性能和疲劳性能,受到现代汽车制造商的青睐,与DP钢一样主要用于汽车结构件。
见图2。
图2 590MPa级以上钢板应用部位
TRIP钢在加工时由于变态诱发塑性的效果可得到高延展性,但却和DP钢板同样具有伸长翻边性差的缺点。
随着其用途的扩大亦要求加工性进一步提高。
于是在TRIP钢基础上,又开发出延展性和伸长翻边性两者同时提高的980MPa级贝氏铁素体(BF: Banitic Ferrite)基相变诱发塑性变形钢(Transformation Induced Plasticity Aided Banitic Ferrite Steel,以下称TBF钢)。
TBF钢是以微细板条状BF为母相,微细残留奥氏体散布在板条BF间。
这种钢板因其综合性能良好被认为是继DP钢、TRIP钢之后又一种汽车车身结构主要用钢,具有极大的应用前景。
对于形状复杂、强度要求不高的汽车车身外板,主要采用具有极优异的深冲性能的无间隙原子钢(I nterstitial Free Steel;以下称IF钢)。
IF钢的特点是C、N含量很低,并在钢中加入Ti和Nb,形成Ti和Nb的C、N化合物,使钢中的C、N间隙原子得以消除,从而具有优越的深冲性能。
其实,IF钢早在1949年已研制成功,由于受到冶炼等技术的限制,直至20世纪80年代,冶炼技术进一步发展,采用底吹转炉和改进的RH(Ruhrstahl & Heraeus)真空处理后经济地生产出C≤0.002%的现代IF钢。
图3显示了I F钢研制的变迁。
目前,伸长率和塑性应变比(r : Plastic strainratio)可达45%和2.0以上的IF钢已成为继沸腾钢、铝镇静钢之后第三代冲压用钢,它的生产已成为一个国家汽车用钢板生产水平的标志。
为了弥补IF钢强度的不足,提高车身外表零件抗凹陷性能,在IF钢的基础上又研发出具有极优异的深冲性能的烘烤硬化钢(Bake Hardening Steel,以下称BH钢)。
这种钢本身强度并不高,甚至略低于IF钢,通过加工过程中的加工硬化和烤漆过程中的时效现象来获得最终零件的强度。
其主要机理就是这种
钢中Nb和Ti含量比IF钢低,这使得BH钢中含有一定数量的间隙原子。
由于BH钢主要应用在汽车外壳上,在烤漆过程中,间隙原子会在烤漆温度下进行时效反应,使得钢在最后的过程中有一个固溶强化的过程,而最终提高零件的强度。
用BH钢冲压成的零件经油漆烘干后其强度提高显著,可达BH钢本身强度的120%左右,它代表了当今冲压用钢板发展的最高水平,是今后冲压用钢的发展方向。
图3 IF钢研制的变迁
2 高强度钢的加工性
汽车车身用高强度钢及其他材料主要是通过冲压成形、焊接组装成车身。
因此,高强度钢的冲压成形性、焊接性等加工性能也是评价汽车车身用高强度钢的主要依据。
在此,通过与普通低碳钢(Mild Ste el)对比,对强度较高、碳当量较高的两种具有代表性的汽车车身用高强度钢板(780MPa级DP钢和980M Pa级TRIP钢)的冲压成形性、焊接性进行分析与探讨。
(1)高强度钢板的冲压成形性
成形极限被认为是材料的成形性能指标。
图4显示了普通低碳钢、780MPa级DP钢、980MPa级TRIP 钢的成形极限曲线。
由图4可见,与普通低碳钢相比,两种高强度钢的成形极限相对较低,可其绝对值仍然较高。
由于在实际运用中,大部分成形复杂的拉伸件、胀形件一般采用IF钢或BH钢。
所以,这样的成形极限足可保证其具有良好的成形性。
图4 高强度钢板成形极限曲线
因为超高强度钢(590MPa级以上)的强度很高,导致出现冲压成形后回弹较大、零件精度较低的问题。
对此,日本等国家已经开发了新的工艺。
例如,在高强度钢弯曲成形时采用反回弹技术,即在设计、制造冲模时考虑材料的回弹量,使冲制的零件经回弹后达到所需尺寸。
最近,针对超高强度钢的复杂成形提出了温间冲制工艺,即含碳量约0.25%的超高强度钢板冲压成形时,进行900℃加热,等材料完全奥氏体化后再冲压成形,然后在冲模中冷却、淬火使其产生马氏体。
利用温间冲制工艺可获得1500MPa以上强度的尺寸合格的零件。
当然,随着1000t以上超大型压力机的使用,超高强度钢的冲压加工将会更加容易。
(2)高强度钢板的焊接性
电阻点焊是汽车车身焊装的主要焊接方法,所以汽车车身用高强度钢板的点焊性是其重要性能之一。
图5显示了1.0mm厚的普通低碳钢、780MPa级DP钢、980MPa级TRIP钢的可焊范围(Acceptable welding range)。
由图5可见,两种高强度钢与普通低碳钢一样,其可焊范围随焊接时间的变化较小,但是当焊接电流变化时其可焊范围却显示出不一致性;两种高强度钢几乎与普通低碳钢一样,当焊接电流大于14.5 k A时,因电极的主要成分铜与钢板发生冶金反应而造成电极头出现蚀坑、电极粘着(Pick-up)现象。
根据焊接标准,可焊参数范围的上限是点焊时发生飞溅(Expulsion)所使用的参数,下限则是获得5t1/2 mm(t 为钢板厚度)的最小可接受溶核直径(Nugget diameter)时的焊接参数。
由图5可知,虽然780MPa级DP钢板和980 MPa级TRIP钢板的可焊范围上限(约8.6kA)与普通低碳钢的可焊范围上限(约11kA)相比较低;可是由于受材料的比热、电阻率、热传导系数等物理性质的影响,两种高强度钢在较低的焊接电流(约5. 7kA)下能获得直径5mm的最小可接受溶核,使其可焊范围下限比普通低碳钢的低。
所以,就可焊范围宽度而言,两种高强度钢(5.7-8.6 kA)和普通低碳钢(8-11 kA)有着几乎相同宽度的可焊范围,显示出与普通低碳钢相同的焊接性。
图5 高强度钢的电阻点焊性(板厚1mm)
3 结束语
高强度钢板的使用,既可以保证汽车车身整体强度、安全性,又可以减轻汽车自身质量,节约能耗、降低排放并改善环境。
目前,为了充分发挥材料的性能,根据零部件使用性能的要求,已研制出多种汽车车身用高强度钢,并由此推动新技术、新材料、新工艺和新产品的研发。