成型不良现象及解决方法
第八讲 成形品常见的不良及解决方法

凹陷
凹陷:制品表面塌陷状况.
分析项目 成型条件 原因对策 1.射出不足:增加射速/压力/保压时间/料温/模温等2.射出过饱: 制品出现脱模不良,降低射出参数.3.冷却不足:肉厚处内部冷却 不充分,溶胶没有完全固化.须增加冷却时间/降低模温来改善.4. 困气:部分空气没有排出占据模空间,造成无法填饱.调整射速/温 度/锁模力来改善. 1.制品脱模受力过大,肋位/柱位/顶出位将产品拉(顶)凹.模具 抛光/斜度/顶出平衡考量;2.增加排气;3.改善进胶. 1.点检射咀(堵塞/利角/溢料);2.点检料温;3.观察残量,点检螺 杆逆止环封胶状况.
COXON GROUP
成型参数
设备
模具 材料
应力痕(光泽)
应力痕:常出现于制品侧壁/肉薄处/顶出部位光泽.
分析项目 原因对策
1.降低保压/保压时间,减轻应力作用. 2.提高料温/模温,改善流动性,以期达到降低压力之目的.
条件
模具
模具排气改良;进胶改良,以期达到降低压力之目的.
COXON GROUP
COXON GROUP
毛边
毛边:熔胶流入模具或模仁间隙而产生之飞边.
原因
材料流动性太强,成型 参数设定不当
对策
1.降低料温/模温,抑制材料流动性. 2.降低注射速度/压力,减缓射出速度. 3.减少计量,加大保压切换位置. 1.加强靠破,避免配合间隙. 2.改良进胶方式(位置/尺寸等),以达到降低 速度/压力之目的,避免高速充填撑模而产生毛边.
成型参数
模具
1.制品脱模受力过大,肋位/柱位/顶出位将产品拉(顶)凹.模具 抛光/斜度/顶出平衡考量.
COXON GROUP
二.寸法不良
一.制品尺寸大小与其充填饱和状态有直接关系,偏大则增加射能; 反之,则降低. 二.制品尺寸大小亦随模温高低发生显著变化,偏大则降低模温; 反之,则升高. 三.除上述因素外,大件产品寸法(长度/圆心距等),要特别考虑制 品制品变形/翘曲影响寸法. 四.寸法不稳定:材料计量/塑化是否正常;参数实际值波动幅度是 否过大;各参数设定是否过急,缓冲不够.螺杆封胶状况等等.
塑胶成形不良现象

塑胶加工成形不良现象与不良对策方法 1.披风不良现象∶模具的分模线、分模面或模具边角之处多胶或有毛刺等。
原因∶塑胶温度过高,射出压力过大,合模压力不足。
对策∶(1)锁模压力增大。
(2)注塑压力减低。
(3)射胶行程减低。
(4)注射速度减低。
(5)模板温度减低。
(6)背压降低。
(7)射胶筒温度降低。
(8)检查模具。
2.结合线不良现象∶胶件之表面有明显的夹线纹。
原因∶两股以上分流射入模腔,细线冷却而生成汇合细纹。
对策∶(1)射胶筒温度提高。
(2)模板温度提高。
(3)射嘴温度提高。
(4)注射压力加大。
(5)注射速度加大。
(6)疏气线加多。
(7)加大入水口。
3.缩水不良现象∶胶件之表面有明显的凹入现象。
t=T/2 以下原因∶肉厚较厚,如右所示∶对策∶(1)射胶行程加大。
(2)螺杆向前时间延长。
(3)保压加大。
(4)注射压力加大。
(5)模板温度降低。
(6)射胶筒温度降低。
(7)注射温度加大。
4.拖花(拖模)不良现象1∶胶件之表面有拖伤条痕。
原因∶金型有伤痕,打光不良,金型有倒扣等现象。
对策∶检查模具是否有伤痕,模具要充分打光,金型倒扣位省平,打光。
不良现象2∶シボ(蝕紋)の場合(表面有拖伤条痕)。
原因∶シボ目大(粗),抜勾配(斜度)小。
(噴沙)对策∶シボ目小(細)に変更,勾配(斜度)大に変更,ビーズ加工5.走水不齐(充填不足)不良现象∶胶件中有部分骨位或较薄部分之胶位有不满胶现象。
原因∶胶件中肉厚太薄,排气不良,浇口截面太小。
对策∶(1)增加料管供料。
(2)增加射出速度。
(3)加大射出行程。
(4)注射压力加大。
(5)保压加大。
(6)射胶筒温度加高。
(7)背压加大。
(8)射嘴温度提高(9)模板温度提高。
(10)入水口加大。
(11)加大浇道截面。
6.流痕不良现象∶浇口或其他窄段成形品表面生成年轮状细条纹。
原因∶溶状聚合物推动固化聚合物前移时,生成细条纹。
对策∶(1)射胶筒温度提高。
(2)射嘴温度提高。
(3)提高模温。
成形品常见的不良及解决方法课件

总结词
01
尺寸偏差是指成形品的实际尺寸与设计尺寸存在偏差的现象。
详细描述
02
尺寸偏差可能是由于模具制造误差、磨损或定位系统不准确等原因引起的。尺寸偏差可能导致装配困难、性能不符合要求或安全问题。
解决方法
03
提高模具制造精度和装配准确性;定期检查和修正模具尺寸;采用高精度的测量设备和质量控制方法;加强生产过程中的质量监控和反馈调整。
详细描述
02
CHAPTER
成形品常见的不良现象
详细描述
变形通常是由于材料内部应力、模具设计不合理或加工工艺不当等原因引起的。变形可能影响成形品的外观和性能,甚至导致产品不合格。
总结词
变形是指成形品形状发生扭曲或不规则变化的现象。
解决方法
优化模具设计,减小内应力;调整加工工艺参数,如温度、压力、时间等;采用适当的后处理工艺,如热处理、矫形等。
VS
模具设计与制造是影响成形品质量的重要因素,合理的模具设计和高质量的制造工艺能够减少产品不良的发生。
详细描述
在模具设计阶段,需要充分考虑产品的形状、尺寸和材料特性,以及成形工艺的要求。合理的模具结构设计能够有效降低产品在成形过程中的缺陷,如缩孔、裂纹等。同时,高质量的模具制造工艺能够保证模具的精度和寿命,从而确保产品的稳定性和一致性。
成形品常见的不良及解决方法课件
目录
成形品不良概述成形品常见的不良现象成形品不良的原因分析解决成形品不良的方法与措施成形品不良的预防与控制成形品不良的案例分析
01
CHAPTER
成形品不良概述
总结词
成形品不良是指在生产过程中出现的各种与预期不符的缺陷或问题,导致产品无法满足设计要求或性能标准。
详细描述
成型不良的原因及改善方法详解
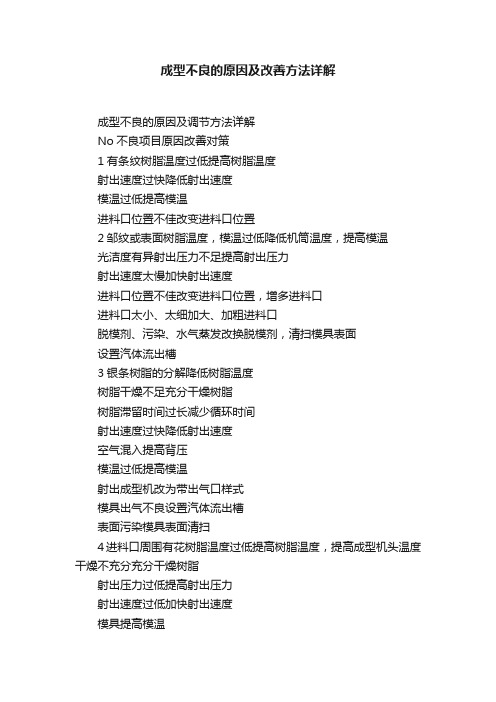
成型不良的原因及改善方法详解成型不良的原因及调节方法详解No不良项目原因改善对策1有条纹树脂温度过低提高树脂温度射出速度过快降低射出速度模温过低提高模温进料口位置不佳改变进料口位置2邹纹或表面树脂温度,模温过低降低机筒温度,提高模温光洁度有异射出压力不足提高射出压力射出速度太慢加快射出速度进料口位置不佳改变进料口位置,增多进料口进料口太小、太细加大、加粗进料口脱模剂、污染、水气蒸发改换脱模剂,清扫模具表面设置汽体流出槽3银条树脂的分解降低树脂温度树脂干燥不足充分干燥树脂树脂滞留时间过长减少循环时间射出速度过快降低射出速度空气混入提高背压模温过低提高模温射出成型机改为带出气口样式模具出气不良设置汽体流出槽表面污染模具表面清扫4进料口周围有花树脂温度过低提高树脂温度,提高成型机头温度干燥不充分充分干燥树脂射出压力过低提高射出压力射出速度过低加快射出速度模具提高模温加大进料口及流道改变进料口位置5黑条主轴、机筒、伤痕清扫主轴机筒、换轴滞留时间过长射出机筒内树脂机筒温度过高降低机筒温度射出速度过快降低射出速度轴转速快烧焦降低转速,降低背压6烧焦空气混入安装出气口装置设置汽体流出槽射出速度过快降低射出速度7云纹、光泽不良树脂过热降低机筒温度成型材料干燥不足充分干燥、改变干燥方式模温过低提高模温机筒温度过高、过低调节机筒温度脱模剂过多减少脱模剂8色差、混色颜料染料分散不良改变树脂,着色剂成型机筒温度过高、过低调节机筒温度可塑化不良降低轴转速,提高背压树脂的分解降低温度,循环时间缩短成型机清扫不良彻底清扫前产品留在机内材料冷却时间过短延长冷却时间进料口位置不佳修正进料口位置分散剂、扩散剂不能加入对该树脂不适合的添加剂等9透明料混浊材料干燥不足,异物混入充分干燥材料、变更材料树脂温度过高、过低调节树脂温度滞留时间过长成型材料滞留时间减短机筒温度过高降低机筒温度添加剂、脱模剂过多确认添加剂的适合性,减少脱模剂10气泡成型材料的分解降低成型温度材料干燥不足充分干燥材料树脂带温过长修正机筒内主轴进料行程射出压力过低提高射出压力保压过低提高保压背压过低提高背压射出速度过慢提高射出速度背压过大背压降低模温过高、过低调节模温料斗下端冷却不足注意改善料斗下端的冷却成型机改为带出气口样式11杂质、异物成型机、料斗、干燥机清扫不良充分清扫成型机、料斗、干燥机材料周围环境有尘埃用塑胶将材料部分隔开材料输送管清扫不良清扫材料输送管模具生锈模具清扫材料不良改换材料12剥离不同材料混入调节材料断裂树脂温度过低提高树脂温度模温过低提高模温材料使用不适、缓冷不足更变材料、改变缓冷条件13裂纹干燥条件不良按树脂种类决定干燥条件树脂温度过低提高树脂温度模温过低提高模温射出压力过高降低射出压力保压压力过高降低保压压力保压时间太长减少保压时间坡度不足增加坡度顶针位置不良调节顶针位置顶针数量少增加顶针数量脱模剂不足增加脱模剂14脆弱成型材料不适改变成型材料强度不够不同材料,粉碎材料混入调节材料质量干燥不适度按材料选择干燥条件树脂温度过高降低树脂温度树脂温度不适当成型温度调节滞留时间过长缩短滞留时间可塑化不良成型温度轴转速、背压调整射出压力不适当射出压力调节保压压力过低提高保压压力射出速度不适当射出速度调节冷却时间过短延长冷却时间模温调节模温模具强度不足修理模具进料口不良、数量不足改变进料口位置,增加进料口数量后处理采用缓冷方式15尺寸不均材料流动性调节成型温度有大有小材料吸湿充分干燥材料射出压力过低调节射出压力保压过低、过短调节保压的压力和时间冷却时间过短延长冷却时间背压过低选择适当背压模温不适调节模温模具关合力过少提高模具关合力模具强度不足修理模具,增加强度进料口位置不适当改变进料口位置进料口数量少增加进料口数量16变形成型材料流动性不足提高树脂温度收缩率过大改提收缩率小的树脂射出压力过高降低射出压力冷却时间短延长冷却时间,使用冷却模具模温使各部位得到冷却,改善模具17凸凹不规则工程塑料较多如PA、PET等注意改善料斗下的冷却料斗侧温度过高降低料斗下机筒温度背压过高调低背压,固定停止时间再生材料不良尽量将再生材料打碎用筛子除去粉末祛除含0.2mm以下厚度胶片的部分玻纤强化颗粒使用2.5mm -3.5mm长度的玻纤材料18毛边、飞刺树脂流动性太快降低成型温度、改变成型材料射出压力过高降低射出压力保压太慢快速保压模具关合力不良提高模具关合力模具强度不足修理模具模具表面不光滑修理模具19多边树脂流动性过剩降低树脂温度改变成型材料射出压力过高降低射出压力快速加入保压模具关合力不足提高模具关合力模具不良模具强度不足分割面密封不良20胡须树脂成型收缩率大改变成型材料树脂温度高降低树脂温度射出压力过低提高射出压力保压压力低提高保压压力射出速度过低加快射出速度模具降低胡须发生侧模温扩大模具进料口、加粗料流道改善进料口位置,壁厚均一模温过高降低模温21缺边树脂流动性不足提高树脂温度改变成型材料射出压力过低提高射出压力保压压力低慢速加入保压提高保压压力射出速度过慢增加射出进入速度计量投量不足增加计量设定值主轴不适合使用带防止逆流功能的主轴模具扩大模具进料口加粗材料流道。
简述棉卷成形不良的原因及维修

棉卷成形不良是纺纱过程中常见的问题,它会直接影响整个生产过程的效率和产品质量。
在生产过程中,棉卷成形不良可能会导致纱线断裂、成纱质量下降以及设备损坏等问题。
对棉卷成形不良的原因进行深入分析,并且开展相应的维修工作,对于提高纺纱生产效率和产品质量有着重要的意义。
本文将就棉卷成形不良的原因及维修进行详细的介绍。
一、棉卷成形不良的原因1.原料质量不良棉纤维的质量直接影响到纺纱的质量,如果原料中含有杂质、过多的短纤维或者受到霉菌的污染等,都会导致棉卷成形不良。
选择优质的棉花原料对于避免棉卷成形不良至关重要。
2.纺纱工艺参数不合理纺纱工艺参数不合理也会导致棉卷成形不良,例如卷曲度、张力、卷绕速度等参数的设定过高或过低都会对成形产生不良影响。
合理设置纺纱工艺参数是预防棉卷成形不良的重要措施。
3.机器设备故障机器设备的故障也是导致棉卷不良的重要原因之一。
卷绕、张力控制、卷曲装置等方面的设备故障都会影响到棉卷的成形质量。
4.操作技术不到位操作人员的技术水平不够也会影响到纺纱的成形质量,不正确的操作方法或者对机器设备的不熟悉都有可能导致棉卷成形不良。
5.环境因素环境因素也会对棉卷成形产生影响,如温湿度、静电等因素都会对棉卷成形质量产生一定的影响。
二、棉卷成形不良的维修1.优化原料质量首先要对原料进行严格的筛选和清洗,保证原料中的杂质、短纤维以及霉菌等都得到有效清除,保证原料的质量。
2.合理设置纺纱工艺参数要根据原料的特性、设备的性能以及生产的需要,科学合理地设置纺纱工艺参数,避免参数的过高或过低对成形的不良影响。
3.定期维护设备定期对机器设备进行检查和维护,发现故障及时地处理,保证设备的正常运转,避免设备故障对成形的不良影响。
4.加强人员培训加强对操作人员的技术培训和理论知识学习,提高操作人员的技术水平,保证操作人员能够正确地操作机器设备。
5.控制环境因素在生产和工作环境中控制温湿度、减少静电等环境因素的影响,保证环境对纺纱生产的影响降到最低。
成形发生不良的处理对策及方法

成形机
计量值变化 不能高压合模
毛边
树脂温度高 滞留时间不长 异物嵌入 金型 浇道出现渣滓 模芯磨损
单品/中间检查人员检查不够 仔细,在判定方面还不够明 确,导致流出
模具处有异物夹杂吗 金型PL面上有渣滓残留吗 模芯缝隙处有渣滓堵塞吗
单品检查
是否按照作业标准书进行检查
《单品外观检查基准书》 两个制品一起检查,对产品的每个部位进行确认
MI值变化
MI值在规定以内吗 确认材料批号MI值 干燥机的温度正常吗 设定干燥机温度 进行4小时以上的干燥 打开SW 输入正确值 确认配合比率履历 去掉树脂渣滓 清扫浇道口 对缺肉发生部位的气路进行清扫 《单品外观检查基准书》 两个制品一起检查,对产品的每个部位进行确认 观察中 在制板槽上贴上微软的塑料片,3/5开始试行
成形机 时没有清扫干净
7B58-4415(B-2)
异材混入
材料
在作业完了后是否有其它材料附在上面 材料工程在粉碎、混料、加 (如:粉尘等)
料时没有清扫干净 单品/中间检查人员检查不够
对清扫后的部位及易发部位进行确认
单品检查 仔细,在判定方面还不够明
确,导致流出 1.成形场所的环境因素 2.制品盒没有很好的管理 3.成形员工在“5S”时把异 物吹入 1.料筒底部、粉碎机的本体 没有清扫干净,在粉碎时流枝 带入 2.粉碎材的利用也是导致异 物的因素
确认射出速度设定值 保压P2的确认 确认S4,S5的位置 确认SM的位置 确认高压合模P的设定值 设定树脂温度确认 清机后再开始生产 金型PL面的确认 金型PL面的确认 拿到模具维修处更换模芯
7B83-5523-70(B-2) 7B83-5527-70(HA-1) 7B83-5522-70(B-2) 7B58-4021(B-2) 7B58-4410(A-1、B-2) 7B58-4413(B-3) 7B58-4414(B-4) 7B58-4415(B-2) 7B58-4632(A-1、A-2) 7B82-5524-70(HB-1) 7B58-7110-70(B-1、A-2、A-3)
成型不良现象及解决办法
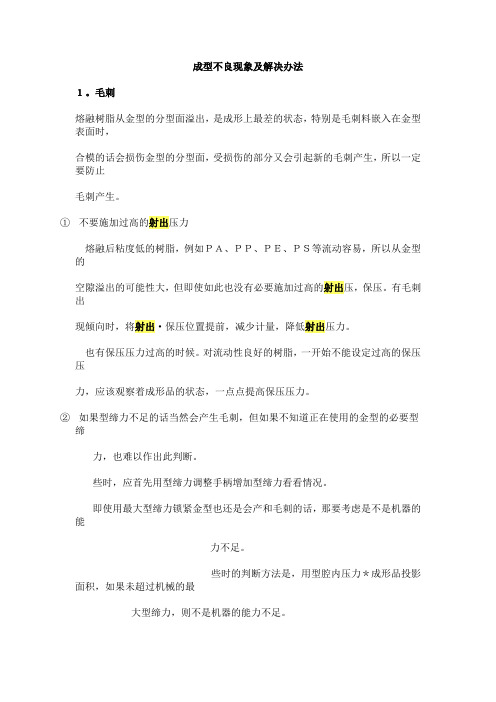
成型不良现象及解决办法1。
毛刺熔融树脂从金型的分型面溢出,是成形上最差的状态,特别是毛刺料嵌入在金型表面时,合模的话会损伤金型的分型面,受损伤的部分又会引起新的毛刺产生,所以一定要防止毛刺产生。
①不要施加过高的射出压力熔融后粘度低的树脂,例如PA、PP、PE、PS等流动容易,所以从金型的空隙溢出的可能性大,但即使如此也没有必要施加过高的射出压,保压。
有毛刺出现倾向时,将射出·保压位置提前,减少计量,降低射出压力。
也有保压压力过高的时候。
对流动性良好的树脂,一开始不能设定过高的保压压力,应该观察着成形品的状态,一点点提高保压压力。
②如果型缔力不足的话当然会产生毛刺,但如果不知道正在使用的金型的必要型缔力,也难以作出此判断。
些时,应首先用型缔力调整手柄增加型缔力看看情况。
即使用最大型缔力锁紧金型也还是会产和毛刺的话,那要考虑是不是机器的能力不足。
些时的判断方法是,用型腔内压力*成形品投影面积,如果未超过机械的最大型缔力,则不是机器的能力不足。
但是,型腔内压力的推定必须正确无误,不能将商品目录上标出的射出压力认为是型腔内压力。
射出压力是理论上的机筒内压力,树脂流入金型后冷却,压力急剧下降,平均压力从低粘度杂货的250kg/cm到高粘度工业部品的800kg/cm不等.推定这个压力很难,虽有一定基准,但若要推定得很精确,需有丰富的经验。
③金型的分型面上有伤,或夹入异物,或金型平行度不好的话,当然要产生毛刺,如金型保管不善,安装面上有打痕或生锈的话会产生毛刺,所以必须养成妥善保管金型的习惯,绝对不允许将金型直接置于地上。
④成形机的金型安装面也要仔细保养,安装金型前要用抹布擦拭干净。
⑤计量过多,或机筒温度设定过高都会产生毛刺,最好的方法是将计量值一点点增大,而机筒所需温度是随材料变化的,最好记住标准温度位。
毛刺多易产生在如图所示的分型面上,另外也易产生在顶针周围,镶块周围。
这一般都称为“竖毛刺”,产生原因多是金型精度不良,象尼龙这样熔融粘度低的树脂特别容易产生这种毛刺,PC这样粘度高的材料不易产生毛刺。
射出成形不良原因及对策

1. 流痕在成品表面或透視成品時,可以看到流動的痕跡。
例如:冰線、橘皮及結合線。
註:其它成品表面的缺失請參考:銀線、凹陷、噴痕及光澤。
原因解決方法/檢查要點1. 調整料管溫度曲線。
2. 提高噴嘴溫度設定。
3. 提高熱澆道溫度設定。
4. 提高背壓。
5. 提高螺桿轉速。
6. 如果冷卻時間比塑化時間長的話,降低螺桿轉速。
7. 檢查螺桿與料管之間的間隙。
註:如果必要的話,更換料管和螺桿。
A.融膠溫度太低或不均勻。
8. 在射出單元中增加混料裝置。
1. 提高保壓壓力。
2. 延長保壓時間。
B.保壓壓力太低或無效。
3. 檢查澆口是否阻塞(污染)。
註:如果必要的話,加大澆口。
1. 調整射出速度。
2. 調整射出速度曲線。
3. 調整射出壓力。
4. 調整射出壓力曲線。
C.射出速度/壓力不正確。
5. 檢查澆口是否阻塞(污染)。
註:如果必要的話,加大澆口。
D.塑料流動不足。
檢查澆口位置。
註:如果必要的話,增加或重新安排澆口位置(平衡)1. 提高模具溫度。
E.模具太冷或冷卻不均勻而造成塑料流動不良或不規則。
2. 檢查模具冷卻是否均勻或阻塞。
1. 檢查模具的合模面是否污染。
註:如果必要,清潔並拋光。
F.模具污染,如:過度潤滑。
2. 減少使用或不使用潤滑劑,不管是內部(在塑膠中)或外部(離型劑)的潤滑劑。
2. 縮水造成的空洞空洞的地方產生在壁厚最大的地方,如果將成品切開,就可以看到許多空洞地方。
原因解決方法/檢查要點A.由於壁厚太厚造成成品內空洞。
增加料量,並且經常秤成品重量(檢查重量)1. 增加射出速度。
B.射出速度/壓力不對。
2. 調整射出速度曲線。
3. 加大射出壓力。
4. 調整射出壓力曲線。
1. 提高保壓壓力。
2. 增長保壓時間。
C.保壓壓力太低或不足以補償塑膠3. 檢查澆口是否阻塞(污染)。
的收縮。
4. 檢查澆口尺寸。
註:如果必要的話,加大或重新安排澆口位置(以求平衡)。
D.由於料溫度太高,造成過度收縮。
降低料管溫度。
成型产品的不良现象原因分析及解决对策

成型产品的不良现象原因分析及解决对策主要针对目前成型品产生不良有原因加以分析判断,在成型机,模具及原料方面提供参考因素从而有效的控制不良的产生,降低生产成本。
内容:1 起疮:(银色条纹)成品表面,以CATE为中心,有很多银白色的条痕,基本上是顺着原料的流动方向产生。
这种现象是许多不良条件累积后发生的,有时要抓住真正的原因很困难。
1.1 原料中如果有水分或其他挥发成分,未充分烘干,则表面上就会产生很多银条。
1.2 原料中偶然混入其它原料时,也会形成起疮,其形状呈云母状或针点状,容易与其它原因造成的起疮分别。
1.3 原料或料管不清洁时,也容易发生这种情况。
1.4 射出时间长,初期射入到模的原料温度低,固化的结果,使挥发成分不会排除,尤其对温度敏感的原料,发常会出现这种状况。
1.5 如果模温低,则原料固化快也容易发生(1。
4)之状况,使挥发成分不会排出除。
1.6 模具排气不良时,原料进入时气体不易排除,会产生起疮,像这种状况,成品顶部往往会烧黑。
1.7 模具上如果附着水分,则充填原料带来的热将其蒸发,与熔融的原料融合,形成起疮,呈蛋白色雾状。
1.8 胶道冷料窝有冷料或者小,射出时,冷却的原料带入模,一部分会迅速固化形成薄层,刚开始生产时模温低也会开成起疮。
1.9 原料在充填过程中,因模穴面接触部分急冷形成薄层,又被后面的原料融化分解,形成白色或污痕状,多见於薄壳产品。
1.10 充填时,原料成乱流状能,使原料流径路线延长,并受模结构的影响产生磨擦加之充填速度比原料冷却速度快,GATE位置处于筋骨处或者小容易产生起疮,成品肉厚急剧化的地方也容易产生起疮。
1.11 GATE以及流道小或变形,充填速度快,瞬间产生磨擦使温度急升造成原料分解。
1.12 原料中含有再生料,未充分烘干,射出时分解,则产生起疮。
1.13 原料在料管中停留时间久,造成部分过热分解。
1.14 背压不足,卷入空气(压缩比不足)。
起疮:表一2 会胶线会胶线是原料在合流处产生细小的线,由于没完全融合而产生,成品正、反面都在同一部位上出现细线,如果模具的一方温度高,则与其接触的会胶线比另一方浅。
成形不良的原因与对策
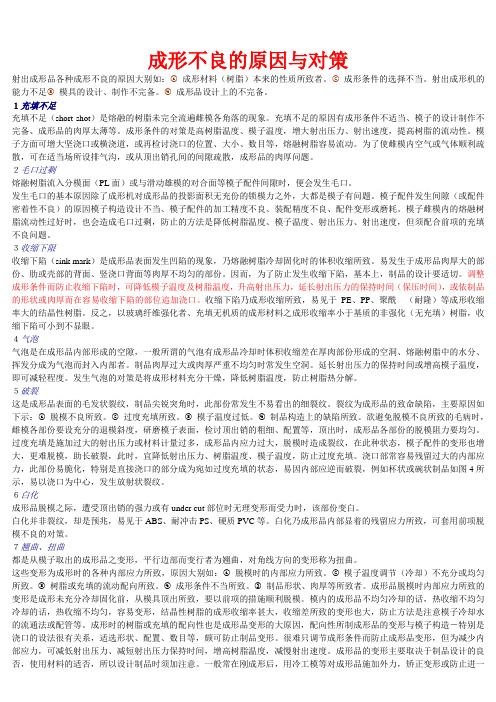
成形不良的原因与对策射出成形品各种成形不良的原因大别如: 成形材料(树脂)本来的性质所致者。
成形条件的选择不当。
射出成形机的能力不足●模具的设计、制作不完备。
❍成形品设计上的不完备。
1充填不足充填不足(short shot)是熔融的树脂未完全流遍雌模各角落的现象。
充填不足的原因有成形条件不适当、模子的设计制作不完备、成形品的肉厚太薄等。
成形条件的对策是高树脂温度、模子温度,增大射出压力、射出速度,提高树脂的流动性。
模子方面可增大坚浇口或横浇道,或再检讨浇口的位置、大小、数目等,熔融树脂容易流动。
为了使雌模内空气或气体顺利疏散,可在适当场所设排气沟,或从顶出销孔间的间隙疏散,成形品的肉厚问题。
2毛口过剩熔融树脂流入分模面(PL面)或与滑动雄模的对合面等模子配件间隙时,便会发生毛口。
发生毛口的基本原因除了成形机对成形品的投影面积无充份的锁模力之外,大都是模子有问题。
模子配件发生间隙(或配件密着性不良)的原因模子构造设计不当、模子配件的加工精度不良、装配精度不良、配件变形或磨耗。
模子雌模内的熔融树脂流动性过好时,也会造成毛口过剩,防止的方法是降低树脂温度、模子温度、射出压力、射出速度,但须配合前项的充填不良问题。
3收缩下限收缩下陷(sink mark)是成形品表面发生凹陷的现象,乃熔融树脂冷却固化时的体积收缩所致。
易发生于成形品肉厚大的部份、肋或壳部的背面、竖浇口背面等肉厚不均匀的部份。
因而,为了防止发生收缩下陷,基本上,制品的设计要适切。
调整成形条件而防止收缩下陷时,可降低模子温度及树脂温度,升高射出压力,延长射出压力的保持时间(保压时间),或依制品的形状或肉厚而在容易收缩下陷的部位追加浇口。
收缩下陷乃成形收缩所致,易见于PE、PP、聚酰(耐隆)等成形收缩率大的结晶性树脂。
反之,以玻璃纤维强化者、充填无机质的成形材料之成形收缩率小于基质的非强化(无充填)树脂,收缩下陷可小到不显眼。
4气泡气泡是在成形品内部形成的空隙,一般所谓的气泡有成形品冷却时体积收缩差在厚肉部份形成的空洞、熔融树脂中的水分、挥发分成为气泡而封入内部者。
成形不良现象及解决办法

(3)、模具排气不良时受压的空气会使模的分型面胀开而出现飞边,应开设良好的排气系统,或在分型面上挖排气沟。
3.塑料的流动性过大,或加太多的润滑剂,应适当降低压力、速度、温度等,减小润滑剂的使用量,必要时要选用流动性低的塑料。
4.加工、调整方面:
(1)排气不良。
(2)模具中流道、浇口、型腔的磨擦阻力大,造成局部过热而出现分解。
(3)浇口、型腔分布不平衡,冷却系统不合理都会造成受热不平衡而出现局部过热或阻塞空气的通道。(4)冷却通路漏水进入型腔。
3.塑料方面:
(1)塑料湿度大,添加再生料比例过多或含有有害性屑料(屑料极易分解),应充分干燥塑料及消除屑料。
大体有三种表现,即深色底暗色线,暗色底深色线及在浇口周围暗色线密而发白。这类缺陷大多在注制聚苯乙烯与改性聚苯乙烯混合料时出现,与下列因素有关:
两种料在流变性、着色性等方面有差异,浇注系统平流层与紊流层流速和受热状况有差异;塑料因热分解而生成烧焦丝;塑料进模时气态物质的干扰。
解决措施:
(1)、采用混合塑料时,要混合好塑料,塑料的颗粒大小要相同与均匀。
(3)机台的动作慢。可从油路与电路调节使之适当加快。(4)模具的设计要方便脱模,尽量设计成全自动操作。(5)制作壁厚过大,造成冷却时间过长。
(6)喷嘴流涎,妨碍正常生产。应采用自锁式射嘴,或降低射嘴温度。
(7)料筒供热量不足。应换用塑化容量大的机台或加强对料的预热。
开裂
开裂:包括制件表面丝状裂纹、微裂、顶白、开裂及因制件粘模、流道粘模而造成或创伤危机,按开裂时间分脱模开裂和应用开裂。
4.加工方面:
(1)料筒温度过高,容积变化大,特别是前炉温度,对流动性差的塑料应适当提高温度、保证畅顺。
铁件成形及常见不良介绍
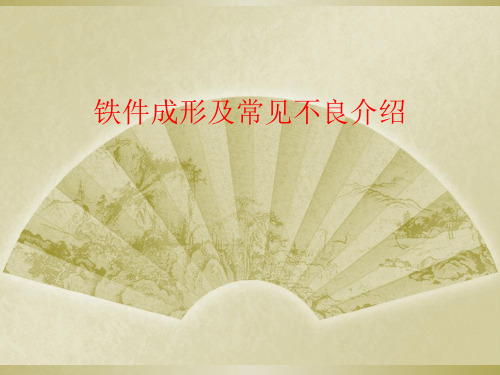
1.1 间隙
冲裁间隙过大、过小或不均匀均可产生毛刺。影响间隙过大、过小或不均匀的有如下因素: a 模具制造误差-冲模零件加工不符合图纸、底板平行度不好等;
b 模具装配误差-导向部分间隙大、凸凹模装配不同心等; c 压力机精度差—如压力机导轨间隙过大,滑块底面与工作台表面的平行度不好 ,或是滑块行程与压力
过小的一边,进料过多,易起皱,皱后进料困难,引起破裂。 2.1.7不按工艺规定涂润滑剂,后阻力增大,造成进料困难而开裂。 2.1.8冲模安装不当或压力机精度差,引起间隙偏斜,造成进料阻力不均。
2.2皱纹和折纹 皱纹产生的原因主要因为局部毛坯受压引起失稳和材料流向不均引起局部材料堆积而产生皱纹。具体 有下面几个方面:
3、表面擦(拉)伤 表面擦伤的主要原因是模具工作部分选材不当,热处理硬度低,凹模圆角磨损、光洁度差,弯曲毛
坯表面质量差(有锈、结疤等),材料厚度超差,工艺方案选择不合理,缺少润滑等。 4、挠度和扭曲
三、大型曲面拉深件的常见缺陷及原因分析
1、大型曲面制件的拉深特点 1.1 变形特点
大型曲面制件的变形特点是:周边为拉深,内部则有胀形成分。表面形状是靠压料面外部材料来 补充,而内部则靠材料延伸来满足胀形的要求。同时由于拉深深度不一,形状复杂,变形部分周边分 布不均。因此,控制材料的流向及流速极为重要。大型曲面制件的局部既易起皱,又易开裂。 1.2要有足够稳定的压边力
2、常见缺陷及原因分析
大型曲面拉深件常见的缺陷有:裂纹和破裂、皱纹和折纹、棱线不清、刚度差、表面划痕、表面粗 糙和滑移线等。
2.1裂纹和破裂
裂纹和破裂产生的原因主要是由于局部毛坯受到的拉应力超过了强度极限所致。具体影响的原因有 :
成型尺寸不良的原因大汇总

成型尺寸不良的原因大汇总尺寸不良是指超出本来的图纸上所表示的规格尺寸,有些不符而成形的成形品,如果把它们进行分类的话,对于规格尺寸来说有尺寸偏小和尺寸偏大的两种现象,这些再具体细分的话有以下的情况,下面让我们考虑这些现象发生的原因和应采取的对策:1、尺寸偏小的不良2、尺寸偏大的不良3、芯摆动不良4、平面摆动不良5、圆柱形的产品芯振动不良一、尺寸偏小的不良成形品偏小于规格尺寸原因:地球上的东西大多数物质都有热胀冷缩的特性,树脂也一样,所以成形品被成形后开始收缩,一直冷却到与常温相等的时候,可是存在的问题是如果最后的收缩量过大的话,成形品尺寸变得过小,结果就造成了尺寸偏小不良,其原因之一是因为确定最初模具尺寸的时候,考虑到各种各样树脂的基本收缩率并将其数值计算出来作为参考,不过即使考虑了收缩率在实际进行当中也发生收缩的成形品的尺寸比规格尺寸小的,因此,遇到上述情况有必要将模具重新修正一下。
其次是跟被成形时的环境有关,这些当中有材料的干燥状态,再利用材料的混合率、成形条件等问题,不过最重要的是成形条件,因为其中模具温度,射注压力能使收缩量增大,所以有必要引起注意。
一般情况下,如果升高注射压力成形品就会尺寸变大,如果升高模具温度就有尺寸变小的倾向,这些如果用简单易懂的说法就是:成形品的尺寸与注射压力、注射时间成正比;与模具温度成反比第三是在长期批量生产常发生的现象中,注射时从材料中产生的废气积存在模具中,因此材料的填充性变的不好而发生尺寸偏小的不良,关于与废气有关的内容中,关键的问题是在注塑成形的精密塑料上,是无法做到没有欠缺的,因为缺欠是比较重要的问题,所以我们今后要详细的考虑下去。
成形时的对策:a.升高注射压力b.降低模具温度c.延长注射和冷却时间d.确认成形机的种类和模具是否相适合。
模具的对策:a.新模具的情况下重新加工不好的地方b.在批量生产当中,发生这类情况是由于模具的磨损或废气阻塞的缘故,首先把模具全部进行清洗将废气清洗掉后再次进行成形,并必须好好确认一下。
注塑成形常见缺陷及分析处理
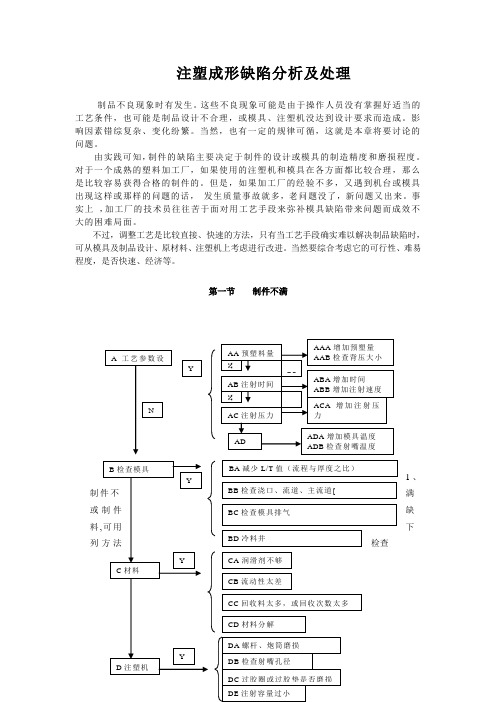
注塑成形缺陷分析及处理制品不良现象时有发生。
这些不良现象可能是由于操作人员没有掌握好适当的工艺条件,也可能是制品设计不合理,或模具、注塑机没达到设计要求而造成。
影响因素错综复杂、变化纷繁。
当然,也有一定的规律可循,这就是本章将要讨论的问题。
由实践可知,制件的缺陷主要决定于制件的设计或模具的制造精度和磨损程度。
对于一个成熟的塑料加工厂,如果使用的注塑机和模具在各方面都比较合理,那么是比较容易获得合格的制件的。
但是,如果加工厂的经验不多,又遇到机台或模具出现这样或那样的问题的话, 发生质量事故就多,老问题没了,新问题又出来。
事实上 ,加工厂的技术员往往苦于面对用工艺手段来弥补模具缺陷带来问题而成效不大的困难局面。
不过,调整工艺是比较直接、快速的方法,只有当工艺手段确实难以解决制品缺陷时,可从模具及制品设计、原材料、注塑机上考虑进行改进。
当然要综合考虑它的可行性、难易程度,是否快速、经济等。
第一节制件不满1、制满或缺料下列2、原因分析2.1在注塑成型工艺参数设定方面Aas预塑料量的设定V预塑=(1.4~1.1)*V制件一般应有10~40%的缓冲量,以便补缩。
粘度较高的塑料如ABS、PC等应调较高料量,结晶性比容变化大的塑料如PE、PP、PA等应调较高料量。
颗粒大、空隙多、背压小时应调较高料量。
当V预塑比V制件大得多的情况下,即当料筒端部存料过多,缓冲垫过大时,注射螺杆要消耗额外多的注射压力来压紧、推动料筒内的超额料量,这就大大地降低了进入模腔的塑料的有效压力,反而使制件难以充满,或需要额外大的注塑压力来充填。
AB注射时间当注射时间调得较长时,有T注射时间=T充填+T压缩+T保压当注射时间调得较短时,可能T注射时间=T充填或充填不足螺杆就开始预塑了。
无压缩和保压阶段,也就注不满。
T充填=L螺杆行程/V注射速度=L1/V1+L2/V2+L3/V3+……(多级注射情况)当注射速度加快时,T充填可减少,从而使压缩和保压时间相对增加。
成形不良现象及解决办法

(4)制件的造型和浇口形式,位置对塑料充填情况有影响,使制件的某些局部产生色差,必要时要进行修改。
白霜
有些聚苯乙烯类制件,在脱模时,会在靠近分型面的局部表面发现附着一层薄薄的白霜样物质,大多经抛光后能除去。这些白霜样物质同样会附在型腔表面,这是由于塑料原料中的易挥发物或可溶性低分子量的添加剂受热后形成气态,从塑料熔体释出,进入型腔后被挤迫到靠近有排气作用的分型面附近,沉淀或结晶出来。这些白霜状的粉末和晶粒粘附在模面上,不单会刮伤下一个脱模制件,次数多了还将影响模面的光洁度。不溶性填料和着色剂大多与白霜的出现无关。白霜的解决方法:加强原料的干燥,降低成型温度,加强模具排气,减少再生料的掺加比例等,在出现白霜时,特别要注意经常清洁模面。
4.加工、调整方面:
(1)设置的温度、压力、速度过高,应采用分段注射。注射时间、保压时间、加料量过多都会造成飞边。(2)调节时,锁模机铰未伸直,或开、锁模时调模螺母经常会动而造成锁模力不足出现飞边。(3)调节头与二极的平行度不够或调节的系统压力过大。
5.飞边和制件不满反复出现的原因:
(1)塑料原料粒度大小悬殊不均时会使加料份量不定。
4.加工方面:
(1)料筒温度过高,容积变化大,特别是前炉温度,对流动性差的塑料应适当提高温度、保证畅顺。
(2)注射压力、速度、背压过低、注射时间过短,使料量或密度不足而收缩压力、速度、背压过大、时间过长造成飞边而出现收缩。
(3)加料量即缓冲垫过大时消耗注射压力,过小时,料量不足。
(4)对于不要求精度的制件,在注射保压完毕,外层基本冷凝硬化而夹心部份尚柔软又能顶出的制件,及早出模,让其在空气或热水中缓慢冷却,可以使收缩凹陷平缓而不那么显眼又不影响使用。
成形不良的原因与对策
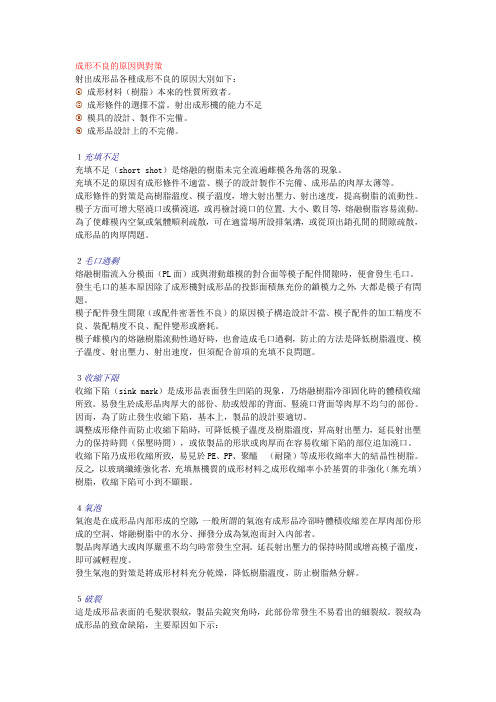
成形不良的原因與對策射出成形品各種成形不良的原因大別如下:成形材料(樹脂)本來的性質所致者。
成形條件的選擇不當。
射出成形機的能力不足●模具的設計、製作不完備。
❍成形品設計上的不完備。
1充填不足充填不足(short shot)是熔融的樹脂未完全流遍雌模各角落的現象。
充填不足的原因有成形條件不適當、模子的設計製作不完備、成形品的肉厚太薄等。
成形條件的對策是高樹脂溫度、模子溫度,增大射出壓力、射出速度,提高樹脂的流動性。
模子方面可增大堅澆口或橫澆道,或再檢討澆口的位置、大小、數目等,熔融樹脂容易流動。
為了使雌模內空氣或氣體順利疏散,可在適當場所設排氣溝,或從頂出銷孔間的間隙疏散,成形品的肉厚問題。
2毛口過剩熔融樹脂流入分模面(PL面)或與滑動雄模的對合面等模子配件間隙時,便會發生毛口。
發生毛口的基本原因除了成形機對成形品的投影面積無充份的鎖模力之外,大都是模子有問題。
模子配件發生間隙(或配件密著性不良)的原因模子構造設計不當、模子配件的加工精度不良、裝配精度不良、配件變形或磨耗。
模子雌模內的熔融樹脂流動性過好時,也會造成毛口過剩,防止的方法是降低樹脂溫度、模子溫度、射出壓力、射出速度,但須配合前項的充填不良問題。
3收縮下限收縮下陷(sink mark)是成形品表面發生凹陷的現象,乃熔融樹脂冷卻固化時的體積收縮所致。
易發生於成形品肉厚大的部份、肋或殼部的背面、豎澆口背面等肉厚不均勻的部份。
因而,為了防止發生收縮下陷,基本上,製品的設計要適切。
調整成形條件而防止收縮下陷時,可降低模子溫度及樹脂溫度,昇高射出壓力,延長射出壓力的保持時間(保壓時間),或依製品的形狀或肉厚而在容易收縮下陷的部位追加澆口。
收縮下陷乃成形收縮所致,易見於PE、PP、聚醯(耐隆)等成形收縮率大的結晶性樹脂。
反之,以玻璃纖維強化者、充填無機質的成形材料之成形收縮率小於基質的非強化(無充填)樹脂,收縮下陷可小到不顯眼。
4氣泡氣泡是在成形品內部形成的空隙,一般所謂的氣泡有成形品冷卻時體積收縮差在厚肉部份形成的空洞、熔融樹脂中的水分、揮發分成為氣泡而封入內部者。
成形不良的原因与对策

成形不良的原因舆封策射出成形品各槿成形不良的原因大别如下:①成形材料(榭脂)本来的性^所致者。
②成形修件的逗撵不常。
射出成形檄的能力不足③模具的言殳三九裂作不完借。
④成形品卷殳三十上的不完借。
1充填不足充填不足(short shot)是熔融的榭脂未完全流遍雌模各角落的垣象。
充填不足的原因有成形修件不遹常、模子的言殳三十裂作不完借、成形品的肉厚太薄等。
成形修件的封策是高榭脂温度、模子温度,增大射出屋力、射出速度,提高榭脂的流勤性。
模子方面可增大笺洗口或横洗道,或再横制洗口的位置、大小、数目等,熔融榭脂容易流勤。
悬了使雌模内空氧或氟骨胤嗔利疏散,可在遹常埸所^排氧潢,或彳能项出金肖孔^的^隙疏散,成形品的肉厚冏魅。
2毛口谩剩熔融榭脂流入分模面重1面)或舆滑重力雄模的封合面等模子配件^隙畤,便曾彝生毛口。
彝生毛口的基本原因除了成形檄封成形品的投影面稹辗充份的金胤莫力之处大都是模子有冏题。
模子配件赞生^隙(或配件密著性不良)的原因模子情造言殳三十不常、模子配件的加工精度不良、装配精度不良、配件燮形或磨耗。
模子雌模内的熔融榭脂流勤性遇好畤,也曾造成毛口遇剩,防止的方法是降低榭脂温度、模子温度、射出屋力、射出速度,但须配合前项的充填不良冏题。
3收缩下限收缩下陷(sink 0@心)是成形品表面彝生凹陷的垣象,乃熔融榭脂冷郤固化畤的艘稹收缩所致。
易彝生於成形品肉厚大的部份、肋或段部的背面、鳖洗口背面等肉厚不均匀的部份。
因而,悬了防止樊生收缩下陷,基本上,裂品的尚殳^要遹切。
言周整成形修件而防止收缩下陷日寺,可降低模子温度及榭脂温度,昇高射出屋力,延晨射出屋力的保持畤^ (保屋畤^),或依裂品的形状或肉厚而在容易收缩下陷的部位追加洗口。
收缩下陷乃成形收缩所致,易见於PE、PP、聚醯(耐隆)等成形收缩率大的结晶性榭脂。
反之,以玻璃^雉强化者、充填瓢檄^的成形材料之成形收缩率小於基^的非强化(辗充填)榭脂,收缩下陷可小到不^眼。
成形品常见的不良及解决方法课件

• 解决方法:在模具上增加排气口,确保气体能够
03
及时排出。
实例三
2. 冷隔 • 原因:金属液温度过低,导致在填充模具时出现冷隔现象。 • 解决方法:控制金属液温度,使其保持在适宜的范围内。
实例三
01
3. 缩松
02
• 原因:金属液在冷却过程中 收缩过大,导致压铸件内部 出现间隙。
03
• 解决方法:优化模具设计, 使金属液在冷却过程中充分 填充模具内部。
实例二
01
3. 尺寸偏差
02
• 原因:冲压速度过快或过慢,导致材料受力不均。
03
• 解决方法:控制冲压速度,确保材料受力均匀。
实例二
4. 破裂 • 原因:冲压材料厚度过薄,无法承受冲压压力。 • 解决方法:增加材料厚度,确保其能够承受冲压压力。
实例三
01 1. 气孔
02
• 原因:模具排气不良,导致气体留在压铸件内形 成气孔。
调整注射速度
注射速度过快可能导致充填不足或气穴,过慢可能导致材料降解或 色泽不均,因此需要根据实际情况调整注射速度。
更换材料或改进材料
更换牌号
对于因材料流动性、收缩率等问题引起 的成形品不良,可以尝试更换牌号,选 择更合适的材料。
VS
改进材料
通过添加助剂、改变配方等方法,改良材 料的加工性能和力学性能,提高成形品的 合格率。
• 解决方法:降低注射压力,确保塑料在模具内 完全融会。
实例二
1. 变形
• 原因:冲压温度过高或过低,导致材料变形。
• 解决方法:控制冲压温度,确保材料在最佳状态下 进行冲压。
实例二
2. 毛刺
• 原因:模具磨损或间隙过大,导致材料在冲压时产生毛 刺。
- 1、下载文档前请自行甄别文档内容的完整性,平台不提供额外的编辑、内容补充、找答案等附加服务。
- 2、"仅部分预览"的文档,不可在线预览部分如存在完整性等问题,可反馈申请退款(可完整预览的文档不适用该条件!)。
- 3、如文档侵犯您的权益,请联系客服反馈,我们会尽快为您处理(人工客服工作时间:9:00-18:30)。
成型不良现象及解决方法成型缺陷及所采取的改正措施1、1影响成型的因素影响成型的因素有很多方面:模具的结构及加工精度、设备状况、注射成型环境、原料特性及质量等,但是,最主要因素还在于前三者。
1、工艺条件注塑时的工艺条件有三大要素:温度、压力、时间,彼此相关的情况如下:1)与时间相关的是注射速率、压力的作用时间、模具的闭合时间、材料的塑化时间和螺杆转速。
2)与温度相关的是模具温度、机筒温度、喷嘴温度、背压引起的温度、螺杆转速引起的温度、进入模腔的熔体在整个模具表面产生的温度、摩擦温度和引起气体产生的温度。
3)与压力有关的是注射高压压力、注塑保压压力、背压,由小浇口、长浇口、小流道无圆角弯道、流道的粗糙表面光洁度、排气和附加料量不均匀性造成的模腔外的压降。
2、设备状况注塑机的锁模方式及精度可以直接影响制品的分型面质量;分段注射及调整工艺条件的好坏可以直接影响制品能否顺利填充成功;注射速率的调整可以影响制品的表观质量。
因此,设备的精度状况直接影响制品的质量。
3、模具结构模具结构包括:成型浇注方式、浇口尺寸大小、浇口位置、镶块镶拼方式的合理性、脱模方式的合理性、排气道是否流畅、整体加工精度等。
1、2、常见制品缺陷及对策1、注射填充不足所谓填充不足是指在足够大的压力、足够多的料量条件下注射不满型腔而得不到完整的制件1)注塑机的成形能力不足注塑机的实际塑化能力达不到实际工作的需要,只有更换大一些注射量的设备。
2)流动阻力过大a)喷嘴阻力过大:加大喷嘴直径、提高喷嘴温度、使用流动阻力较低的喷嘴b)主、分流道阻力过大:加大主、分流道直径,改变分流道截面形状,尽量采用整圆形、梯形等相似的形状、避免采用半圆浇道,尽可能缩短流程c)制品壁厚过薄:尽可能加大壁厚,尤其是在熔料阻力过大部位,相对加厚;d)模温过低:提高模具温度。
3)型腔排气不良型腔排气不良时造成充模困难,而且易产生烧焦现象。
增加排气部位的方式有:a)增设顶杆,利用间隙排气;b)在分型面上加工排气槽;c)在较深的下陷部件使整体变为镶块。
4)塑料流动性太差可以采用加快注射速度、提高料筒温度、提高注射压力、提高模具温度等方法。
如仍不能达到理想效果,只有更换流动性更好的原料。
2、毛刺过大不仅充满型腔,而且出现毛刺,尤其分型面处的毛刺更大,甚至在型腔镶块缝隙处也有毛刺存在,其原因在于:1)锁模力不足:模腔涨力大于合模力,在注射压力作用下,动、定模之间产生缝隙因而毛刺产生。
降低注射压力,加大锁模力可消除这种现象。
2)模具局部配合不佳:由于模具结构所决定的模具平平行度不佳或锁模装置不良,产生左右不平衡现象,毛刺由此产生。
3)模板翘曲变形:由于模板刚度不足,受力时产生弹性变形甚至塑性变形,使分型间隙增大。
应加大模板厚度或补加紧固螺钉等方法。
4)流动性好:塑料流动性过好或模具温度过高。
此时应降低模具温度,降低料温或降低注射压力。
5)注射过量3、缩孔在成形表面因收缩产生的下陷叫缩孔。
其主要原因有:4)压缩不足:当注射压力偏低时,不能将物料压缩至适当的密度,也不能将气体和空气充分从物料中排除,形成缩孔。
这时要提高注射压力,但是主、分流道、浇口的尺寸、直径等过小,压力无法传递到熔料的因素也应当考虑。
5)树脂的温度偏高:高温下分子间距较大,占据空间较大,在固化时产生较大的收缩。
6)注射量调整不当:当注射终了时,必须在螺杆头与喷嘴之间留有适当的熔融塑料,用它来缓冲,一般是注射结束时螺杆仍能够前进数毫米至十几毫米,保压时仍有熔料补进。
7)模具冷却不均匀4、熔接痕这种情况发生在带孔的成形制品或多个浇口成形的制品,熔接痕处的温度低于其它部位。
其改进方法有:1)提高注射压力2)提高模具温度3)加快注射速度4)合理设置排气槽,在熔接处达到排气通畅5)少用或不用脱模剂:当接合处的熔料前锋沾有脱模剂时,会因二者相互不熔合而形成更大的熔接缝。
5、翘曲、弯曲、扭曲引起制品翘曲、弯曲、扭曲等不规律变形的具体原因及其防止方法有:1)由成形应变引起:因为成形收缩在方向上有差异以及壁厚的变化产生了成形应变,因此,提高模具温度、提高熔料温度、降低注射压力、改善浇注系统的流动条件等均可以减少收缩率在方向上的差异。
但是,大面积板状制品可采用侧面扇状浇口,在非工作面添加加强肋等方式防止向上翘曲。
2)冷却不充分或不均匀:在制品未完全冷却的情况下脱出型腔会因为形状不对称而翘曲,延长在模具内的冷却时间,或待硬化后再顶出,降低模具温度,相对延长冷却时间,也可以收到良好的效果。
6、开裂、裂纹、微裂和发白PS原料的制品在数小时后可能会自然开裂,AS原料的制品在顶出的瞬间易产生微裂,而ABS和PP料却会以顶杆部位发白(可以用热风加温的方式来消除),主要原因有:1)脱模不畅2)过填充3)冷却不充分7、银丝在制品表面熔融料流动方向上产生银白色纹理称为银丝,主要是原料干燥不彻底,原料中有水分或挥发成分造成的,如彻底干燥后仍不能排除,可从下列原因检查:1)塑料或添加剂分解引起的:降低熔料温度或尽量缩短熔料在机筒内的停留时间,2)模具表面的水分挥发或挥发成分引起的3)由粉料造成的:当注塑机采用粉料直接成形时很容易卷入空气,此时要将料筒下部充分冷却或者使料筒后部温度偏低,降低螺杆转数,提高背压等方法4)熔料温度偏低:此时一般表现为波纹,熔料温度不均匀,注入模腔时就产生波纹8、粘模1)粘模腔、粘模芯a)注射压力过高或保压压力过高b)注射保压、注射高压时间过长c)固化时间过短d)模腔温度太高,不利于在设定时间内固化e)机筒、喷嘴温度过高2)粘主流道a)注射压力过高或保压压力过高b)注射保压、注射高压时间过长c)闭模时间太短,使主流道物料来不用充分收缩d)检查主流道拉料杆是否正常工作纠正注塑的缺点:注射模塑缺点和反常现象最终集中在注塑制品的质量上反映出来。
注塑制品缺点可分成下列几点:(1)产品注射不足;(2)产品溢边;(3)产品凹痕和气泡;(4)产品有接痕;(5)产品发脆;(6)塑料变色;(7)产品有银丝、斑纹和流痕;(8)产品浇口处混浊;(9)产品翘曲和收缩;(10)产品尺寸不准;(11)产品粘贴模内;(12)物料粘贴流道;(13)喷嘴流涎。
下面一一叙述其产生的原因及克服的办法。
⒈怎样克服产品注射不足产品注料不足往往由于物料在未充满型腔之前即已固化,当然还有其他多种的原因。
⑴设备原因:① 料斗中断料;② 料斗缩颈部分或全部堵塞;③ 加料量不够;④ 加料控制系统操作不正常;⑤ 注压机塑化容量太小;⑥ 设备造成的注射周期反常。
⑵注塑条件原因:① 注射压力太低;② 在注射周期中注射压力损失太大;③ 注射时间太短;④ 注射全压时间太短;⑤ 注射速率太慢;⑥ 模腔内料流中断;⑦ 充模速率不等;⑧ 操作条件造成的注射周期反常。
⑶温度原因:① 提高料筒温度;② 提高喷嘴温度;③ 检查毫伏计、热电偶、电阻电热圈(或远红外加热装置)和加热系统;④ 提高模温;⑤ 检查模温控制装置。
⑷模具原因① 流道太小;② 浇口太小;③ 喷嘴孔太小;④ 浇口位置不合理;⑤ 浇口数不足;⑥ 冷料穴太小;⑦ 排气不足;⑧ 模具造成的注射周期反常;⑸物料原因:物料流动性太差。
⒉怎样克服产品飞边溢料:产品溢边往往由于模子的缺陷造成,其他原因有:注射力大于锁模力、物料温度太高、排气不足、加料过量、模子上沾有异物等。
⑴模具问题:① 型腔和型芯未闭紧;② 型腔和型芯偏移;③ 模板不平行;④ 模板变形;⑤ 模子平面落入异物;⑥ 排气不足;⑦ 排气孔太大;⑧ 模具造成的注射周期反常。
⑵设备问题:① 制品的投影面积超过了注压机的最大注射面积;② 注压机模板安装调节不正确;③ 模具安装不正确;④ 锁模力不能保持恒定;⑤ 注压机模板不平行;⑥ 拉杆变形不均;⑦设备造成的注射周期反常⑶注塑条件问题:① 锁模力太低;② 注射压力太大;③ 注射时间太长;④ 注射全压力时间太长;⑤ 注射速率太快;⑥ 充模速率不等;⑦ 模腔内料流中断;⑧ 加料量控制太大;⑨ 操作条件造成的注射周期反常。
⑷温度问题:① 料筒温度太高;② 喷嘴温度太高;③ 模温太高。
⑸设备问题:①增大注压机的塑化容量;②使注射周期正常;⑹冷却条件问题:①部件在模内冷却过长,避免由外往里收缩,缩短模子冷却时间;②将制件在热水中冷却。
⒋怎样防止产品接痕(拼缝线)产品接痕通常是由于在拼缝处温度低、压力小造成。
⑴温度问题:①料筒温度太低;②喷嘴温度太低;③模温太低;④ 拼缝处模温太低;⑤ 塑料熔体温度不均。
⑵注塑问题:① 注射压力太低:② 注射速度太慢。
(3)模具问题:<1>拼缝处排气不良;<2>部件排气不良;<3>分流道太小; <4>浇口太小;<5>三流道进口直径太小;<6>喷嘴孔太小;<7>浇口离拼缝处太远,可增加辅助浇口;<8>制品壁厚太薄,造成过早固化;<9>型芯偏移,造成单边薄;<10>模子偏移,造成单边薄<11>制件在拼缝处太薄,加厚;<12>充模速率不等;<13>充模料流中断。
(4)设备问题:①塑化容量太小;②料筒中压力损失太大(柱塞式注压机)。
(5)物料问题:①物料污染;②物料流动性太差,加润滑剂改善流动性。
5、怎样防止产品发脆产品发脆往往由于物料在注塑过程中降解或其他原因。
⑴注塑问题:<1>料筒温度低,提高料筒温度;<2>喷嘴温度低,提高它;<3>如果物料容易热降解,则降低料筒喷嘴温度;<4>提高注射速度;<5>提高注射压力;<6>增加注射时间;<7>增加全压时间;<8>模温太低,提高它;<9>制件内应力大,减少内应力;<10>制件有拼缝线,设法减少或消除;<11>螺杆转速太高因而降解物料。
⑵模具问题:①制品设计太薄;②浇口太小;③分流道太小;④制品增加加强筋、圆内角。
⑶物料问题:①物料污染;②物料未干燥好;③物料中有挥发物;④物料中回料太多或回料次数太多;⑤物料强度低。
⑷设备问题:①塑化容量太小;②料筒中有障碍物促使物料降解。
12、怎样克服塑料粘贴流道塑料粘贴流道是由于注口与喷嘴圆弧接触面不良,浇口料未同制品一起脱模以及不正常的填料。
通常,主流道直径要足够大,使制件脱模时浇口料仍未全部固化。
(1)流道与模具问题:①流道注口与喷嘴必须配偶好;②确保喷嘴喷孔不大于流道注口直径;③抛光主流道;④增加主流道锥度;⑤调正主流道直径;⑥控制流道温度;⑦增加浇口料拉出力;⑧降低模具温度。
(2)注塑条件问题:①采用流道切断;②减少注射供料;③降低注射压力;④缩短注射时间;⑤减少全压时间;⑥降低物料温度;⑦降低料筒温度;⑧降低喷嘴温度;(3)物料问题:①清理物料污染;②干燥物料。