片剂生产松片、裂片、粘冲与吊冲、片重差异超限的原因及解决方案
片剂产生松片,裂片,粘冲与吊冲,片重差异超限的原因及解决办法
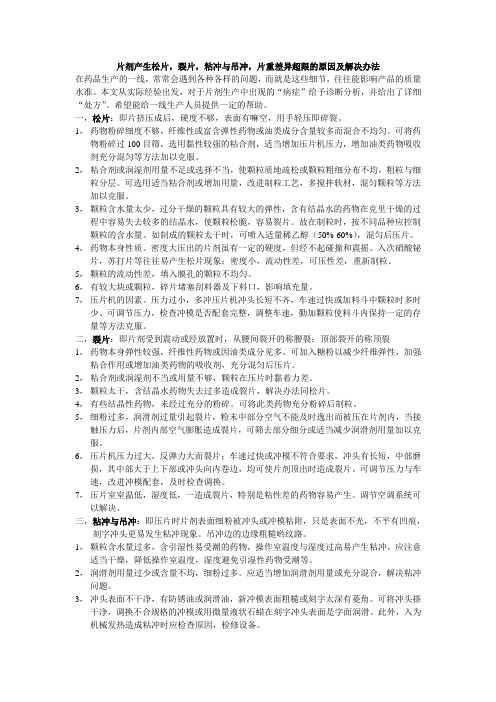
片剂产生松片,裂片,粘冲与吊冲,片重差异超限的原因及解决办法在药品生产的一线,常常会遇到各种各样的问题,而就是这些细节,往往能影响产品的质量水准。
本文从实际经验出发,对于片剂生产中出现的“病症”给予诊断分析,并给出了详细“处方”。
希望能给一线生产人员提供一定的帮助。
一,松片:即片挤压成后,硬度不够,表面有嘛空,用手轻压即碎裂。
1,药物粉碎细度不够,纤维性或富含弹性药物或油类成分含量较多而混合不均匀。
可将药物粉碎过100目筛,选用黏性较强的粘合剂,适当增加压片机压力,增加油类药物吸收剂充分混匀等方法加以克服。
2,粘合剂或润湿剂用量不足或选择不当,使颗粒质地疏松或颗粒粗细分布不均,粗粒与细粒分层。
可选用适当粘合剂或增加用量,改进制粒工艺,多搅拌软材,混匀颗粒等方法加以克服。
3,颗粒含水量太少,过分干燥的颗粒具有较大的弹性,含有结晶水的药物在克里干燥的过程中容易失去较多的结晶水,使颗粒松脆,容易裂片。
故在制粒时,按不同品种应控制颗粒的含水量。
如制成的颗粒太干时,可喷入适量稀乙醇(50%-60%),混匀后压片。
4,药物本身性质。
密度大压出的片剂虽有一定的硬度,但经不起碰撞和震摇。
入次硝酸铋片,苏打片等往往易产生松片现象;密度小,流动性差,可压性差,重新制粒。
5,颗粒的流动性差,填入膜孔的颗粒不均匀。
6,有较大块或颗粒,碎片堵塞刮料器及下料口,影响填充量。
7,压片机的因素。
压力过小,多冲压片机冲头长短不齐,车速过快或加料斗中颗粒时多时少。
可调节压力,检查冲模是否配套完整,调整车速,勤加颗粒使料斗内保持一定的存量等方法克服。
二,裂片:即片剂受到震动或经放置时,从腰间裂开的称腰裂:顶部裂开的称顶裂1,药物本身弹性较强,纤维性药物或因油类成分见多。
可加入糖粉以减少纤维弹性,加强粘合作用或增加油类药物的吸收剂,充分混匀后压片。
2,粘合剂或润湿剂不当或用量不够,颗粒在压片时黏着力差。
3,颗粒太干,含结晶水药物失去过多造成裂片,解决办法同松片。
3-片重超差、粘冲和松片原因及解决方法

片重超差、粘冲和松片原因及解决方法一:片重超差的原因及处理如下:片重超差是指片重差异超过药典规定的限度。
1.颗粒粗细分布不匀,压片时颗粒流速不同,导致填充到中模孔内的颗粒粗细不均匀,如粗颗粒量多则片轻,细颗粒多则片重。
解决方法:应将颗粒混匀或筛去过多细粉,控制粒径分布范围。
2.如有细粉粘附冲头而造成吊冲时可使片重差异幅度较大。
此时下冲转动不灵活,应及时检查,拆下冲模,清理干净下冲与中模孔。
3.颗粒流动性不好,流入中模孔的颗粒量时多时少,引起片重差异过大而超限。
解决方法:应重新制粒或加入适宜的助流剂如微粉硅胶等,改善颗粒流动性。
4.颗粒分层。
解决颗粒分层,减小粒度差。
5.较小的药片选用较大颗粒的物料。
解决方法:选择适当大小的颗粒。
6.加料斗被堵塞,此种现象常发生于粘性或引湿性较强的药物。
应疏通加料斗、保持压片环境干燥,并适当加入助流剂解决。
7.物料内物料存储量差异大,控制在50%以内。
8.加料器不平衡或未安装到位,造成填料不均。
9.刮粉板不平或安装不良。
解决方法:调平。
10.带强迫加料器的,强迫加料器拨轮转速与转台转速不匹配。
解决方法:调一致。
11.冲头与中模孔吻合性不好,例如下冲外周与模孔壁之间漏下较多药粉,致使下冲发生“涩冲”现象,造成物料填充不足,对此应更换冲头、中模。
12.下冲长短不一,超差,造成充填量不均。
解决办法:修差,差±5μm以内。
13.下冲带阻尼的,阻尼螺钉调整的阻尼力不佳。
重新调整。
14.充填轨道磨损或充填机构不稳定。
解决方法:更换或稳固。
15.追求产量,转台转速过快,填充量不足。
特别是压大片时,要适当降低转速,以保证充填充足。
16.压片机震动过大,结构松动,装配不合理或重新装配;压片机设置压力过大,减小压力。
二:粘冲的原因及处理如下:粘冲是指压片时片剂表面细粉被冲头和冲模黏附,致使片面不光、不平有凹痕,刻字冲头更容易发生粘冲现象。
1.冲头表面损坏或表面光洁度降低,也可能有防锈油或润滑油、新冲模表面粗糙或刻字太深有棱角。
制剂生产过程中常见问题及处理方法

制剂生产过程中常见问题和处理方法一、质量问题制剂生产过程由于种种原因造成制剂的质量不合格,尤其是在片剂生产中,造成片剂质量问题的因素更多。
现仅对片剂、胶囊剂及注射剂生产中可能产生质量问题的原因及解决方法作介绍。
(一)片剂生产过程中可能发生问题的分析及解决方法1.松片片剂压成后,硬度不够,表面有麻孔,用手指轻轻加压即碎裂,原因分析及解决方法:①药物粉碎细度不够、纤维性或富有弹性药物或油类成分含量较多而混合不均匀。
可将药物粉碎过100目筛、选用黏性较强的黏合剂、适当增加压片机的压力、增加油类药物吸收剂充分混匀等方法加以克服。
②黏合剂或润湿剂用量不足或选择不当,使颗粒质地疏松或颗粒粗细分布不匀,粗粒与细粒分层。
可选用适当黏合剂或增加用量、改进制粒工艺、多搅拌软材、混均颗粒等方法加以克服。
③颗粒含水量太少,过分干燥的颗粒具有较大的弹性、含有结晶水的药物在颗粒干燥过程中失去较多的结晶水,使颗粒松脆,容易松裂片。
故在制粒时,按不同品种应控制颗粒的含水量。
如制成的颗粒太干时,可喷入适量稀乙醇(50%—60%),混匀后压片。
④药物本身的性质。
密度大压出的片剂虽有一定的硬度,但经不起碰撞和震摇。
如次硝酸铋片、苏打片等往往易产生松片现象;密度小,流动性差,可压性差,重新制粒。
⑤颗粒的流动性差,填入模孔的颗粒不均匀。
⑥有较大块或颗粒、碎片堵塞刮粒器及下料口,影响填充量。
⑦压片机械的因素。
压力过小,多冲压片机冲头长短不齐,车速过快或加料斗中颗粒时多时少。
可调节压力、检查冲模是否配套完整、调整车速、勤加颗粒使料斗内保持一定的存量等方法克服。
2.裂片片剂受到震动或经放置时,有从腰间裂开的称为腰裂;从顶部裂开的称为顶裂,腰裂和顶裂总称为裂片,原因分析及解决方法:①药物本身弹性较强、纤维性药物或因含油类成分较多。
可加入糖粉以减少纤维弹性,加强黏合作用或增加油类药物的吸收剂,充分混匀后压片。
②黏合剂或润湿剂不当或用量不够,颗粒在压片时粘着力差。
片剂制备过程产生的问题及解决办法

(一)裂片:片剂发生裂开的现象叫做裂片(常发生顶裂或腰裂)产生原因:片剂的弹性复原率(与物料性质有关)及压力分布不均匀是主要原因。
另外,粘合剂不当或用量不足、细粉过多、颗粒过干、加压过快均会造成裂片。
解决方法:换用塑性大的辅料,适度干燥,选择合适粘合剂与用量,减少细粉等。
(二)松片:指片剂的硬度不够,稍加触动即散碎的现象称为松片。
产生原因:与压力及粘合剂的用量等诸多因素有关。
解决方法:调整压力和适当增加粘合剂。
(三)粘冲:指片剂表面被冲头粘去一薄层或一小部分,造成片面粗糙不平或有凹痕的现象。
产生原因:颗粒不够干燥或物料易于吸潮、润滑剂选择不当或用量不足,以及冲头表面锈蚀或刻字粗糙不光等。
解决方法:应根据实际情况而定。
(四)片重差异超限:片剂的重量超出药典规定的重量差异允许的范围。
产生原因:①颗粒的流动性不好;②细粉过多或颗粒不均匀;③加料斗内物料时多时少;④冲头与模孔吻合不好。
----颗粒向模孔中填充不均匀。
解决方法:改善物料流动性等。
(五)崩解迟缓:指片剂不能在药典规定的时限内完全崩解或溶解1.崩解机理(1)片剂中可溶性成分多,因溶蚀而崩解;(2)“固体桥”溶解,结合力消失;(3)泡腾剂产气作用;(4)吸水膨胀(多数片剂)。
(5)润湿热2.影响崩解的因素毛细管理论公式:L2 = Rγcosθ/2η.t式中L:液体渗入毛细管的距离;R:毛细管半径;γ:液体的表面张力;θ:液体与毛细管的接触角;η:液体的黏度,t:时间。
由公式可知,影响介质渗入的主要参数有:毛细管数量(孔隙率)、毛细管半径、液体表面张力与接触角。
对四参数产生影响的主要因素是以下几方面(1)原辅料的可压性:原辅料的可压性好,片剂的崩解性能差,适量加入淀粉可增大片剂的空隙率,增加吸水性,有利于片剂的崩解;(2)颗粒的硬度:颗粒的硬度小影响片剂的孔隙率,近而影响片剂的崩解;(3)压片力:压力大,片剂的孔隙率及孔隙径小,片剂崩解速度慢;(4)表面活性剂:加入表面活性剂,改变物料的疏水性,增加润湿性,有利于片剂的崩解;(5)润滑剂:使用疏水性强的润滑剂,水分不易进入片剂,不利于片剂的崩解,硬脂酸镁;(6)粘合剂与崩解剂:粘合力越大,崩解时间越长,黏合剂粘合力大小顺序:明胶>阿拉伯胶>糖浆>淀粉浆。
片剂生产松片、裂片、粘冲与吊冲、片重差异超限的原因及解决方案

片剂生产松片、裂片、粘冲与吊冲、片重差异超限的原因及解决方案在药品生产的一线,常常会遇到各种各样的小问题,而就是这些细节,往往能影响产品的质量水准。
本文从实际经验出发,对于片剂生产中出现的“病症”给与诊断分析,并给出了详实“处方”。
希望能给一线生产人员提供一定的帮助。
1:病症:松片,即片剂压成后,硬度不够,表面有麻孔,用手指轻轻加压即碎裂。
处方:①药物粉碎细度不够、纤维性或富有弹性药物或油类成分含量较多而混合不均匀。
可将药物粉碎过100目筛、选用黏性较强的黏合剂、适当增加压片机的压力、增加油类药物吸收剂充分混匀等方法加以克服。
②黏合剂或润湿剂用量不足或选择不当,使颗粒质地疏松或颗粒粗细分布不匀,粗粒与细粒分层。
可选用适当黏合剂或增加用量、改进制粒工艺、多搅拌软材、混均颗粒等方法加以克服。
③颗粒含水量太少,过分干燥的颗粒具有较大的弹性、含有结晶水的药物在颗粒干燥过程中失去较多的结晶水,使颗粒松脆,容易松裂片。
故在制粒时,按不同品种应控制颗粒的含水量。
如制成的颗粒太干时,可喷入适量稀乙醇(50%- 60%),混匀后压片。
④药物本身的性质。
密度大压出的片剂虽有一定的硬度,但经不起碰撞和震摇。
如次硝酸铋片、苏打片等往往易产生松片现象;密度小,流动性差,可压性差,重新制粒。
⑤颗粒的流动性差,填入模孔的颗粒不均匀。
⑥有较大块或颗粒、碎片堵塞刮粒器及下料口,影响填充量。
⑦压片机械的因素。
压力过小,多冲压片机冲头长短不齐,车速过快或加料斗中颗粒时多时少。
可调节压力、检查冲模是否配套完整、调整车速、勤加颗粒使料斗内保持一定的存量等方法克服。
2:病症:裂片,即片剂受到震动或经放置时,从腰间裂开的称为腰裂;顶部裂开的称为顶裂,腰裂和顶裂总称为裂片。
处方:①药物本身弹性较强、纤维性药物或因含油类成分较多。
可加入糖粉以减少纤维弹性,加强黏合作用或增加油类药物的吸收剂,充分混匀后压片。
②黏合剂或润湿剂不当或用量不够,颗粒在压片时黏着力差。
片剂裂片的原因及解决方法
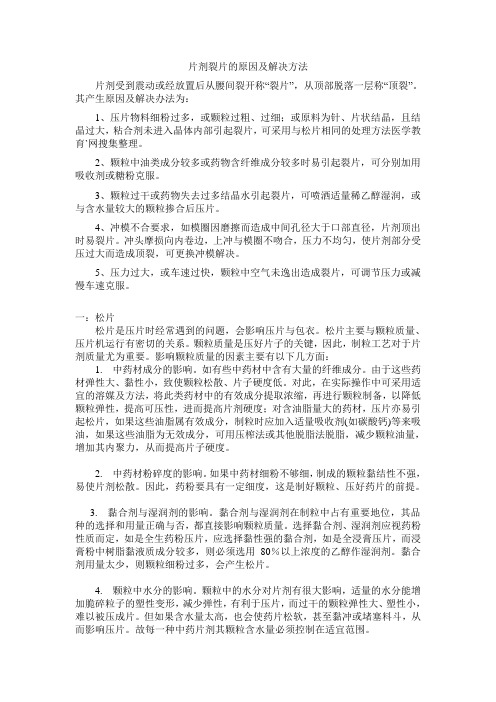
片剂裂片的原因及解决方法片剂受到震动或经放置后从腰间裂开称“裂片”,从顶部脱落一层称“顶裂”。
其产生原因及解决办法为:1、压片物料细粉过多,或颗粒过粗、过细;或原料为针、片状结晶,且结晶过大,粘合剂未进入晶体内部引起裂片,可采用与松片相同的处理方法医学教育`网搜集整理。
2、颗粒中油类成分较多或药物含纤维成分较多时易引起裂片,可分别加用吸收剂或糖粉克服。
3、颗粒过干或药物失去过多结晶水引起裂片,可喷洒适量稀乙醇湿润,或与含水量较大的颗粒掺合后压片。
4、冲模不合要求,如模圈因磨擦而造成中间孔径大于口部直径,片剂顶出时易裂片。
冲头摩损向内卷边,上冲与模圈不吻合,压力不均匀,使片剂部分受压过大而造成顶裂,可更换冲模解决。
5、压力过大,或车速过快,颗粒中空气未逸出造成裂片,可调节压力或减慢车速克服。
一:松片松片是压片时经常遇到的问题,会影响压片与包衣。
松片主要与颗粒质量、压片机运行有密切的关系。
颗粒质量是压好片子的关键,因此,制粒工艺对于片剂质量尤为重要。
影响颗粒质量的因素主要有以下几方面:1. 中药材成分的影响。
如有些中药材中含有大量的纤维成分。
由于这些药材弹性大、黏性小,致使颗粒松散、片子硬度低。
对此,在实际操作中可采用适宜的溶媒及方法,将此类药材中的有效成分提取浓缩,再进行颗粒制备,以降低颗粒弹性,提高可压性,进而提高片剂硬度;对含油脂量大的药材,压片亦易引起松片,如果这些油脂属有效成分,制粒时应加入适量吸收剂(如碳酸钙)等来吸油,如果这些油脂为无效成分,可用压榨法或其他脱脂法脱脂,减少颗粒油量,增加其内聚力,从而提高片子硬度。
2. 中药材粉碎度的影响。
如果中药材细粉不够细,制成的颗粒黏结性不强,易使片剂松散。
因此,药粉要具有一定细度,这是制好颗粒、压好药片的前提。
3. 黏合剂与湿润剂的影响。
黏合剂与湿润剂在制粒中占有重要地位,其品种的选择和用量正确与否,都直接影响颗粒质量。
选择黏合剂、湿润剂应视药粉性质而定,如是全生药粉压片,应选择黏性强的黏合剂,如是全浸膏压片,而浸膏粉中树脂黏液质成分较多,则必须选用80%以上浓度的乙醇作湿润剂。
片剂生产过程中常见问题和处理方法

片剂生产过程中常见问题和处理方法片剂压成后,硬度不够,表面有麻孔,用手指轻轻加压即碎裂,原因分析及解决方法:①药物粉碎细度不够、纤维性或富有弹性药物或油类成分含量较多而混合不均匀。
可将药物粉碎过100目筛、选用黏性较强的黏合剂、适当增加压片机的压力、增加油类药物吸收剂充分混匀等方法加以克服。
②黏合剂或润湿剂用量不足或选择不当,使颗粒质地疏松或颗粒粗细分布不匀,粗粒与细粒分层。
可选用适当黏合剂或增加用量、改进制粒工艺、多搅拌软材、混均颗粒等方法加以克服。
③颗粒含水量太少,过分干燥的颗粒具有较大的弹性、含有结晶水的药物在颗粒干燥过程中失去较多的结晶水,使颗粒松脆,容易松裂片。
故在制粒时,按不同品种应控制颗粒的含水量。
如制成的颗粒太干时,可喷入适量稀乙醇(50%—60%),混匀后压片。
④药物本身的性质。
密度大压出的片剂虽有一定的硬度,但经不起碰撞和震摇。
如次硝酸铋片、苏打片等往往易产生松片现象;密度小,流动性差,可压性差,重新制粒。
⑤颗粒的流动性差,填入模孔的颗粒不均匀。
⑥有较大块或颗粒、碎片堵塞刮粒器及下料口,影响填充量。
⑦压片机械的因素。
压力过小,多冲压片机冲头长短不齐,车速过快或加料斗中颗粒时多时少。
可调节压力、检查冲模是否配套完整、调整车速、勤加颗粒使料斗内保持一定的存量等方法克服。
2.裂片片剂受到震动或经放置时,有从腰间裂开的称为腰裂;从顶部裂开的称为顶裂,腰裂和顶裂总称为裂片,原因分析及解决方法:①药物本身弹性较强、纤维性药物或因含油类成分较多。
可加入糖粉以减少纤维弹性,加强黏合作用或增加油类药物的吸收剂,充分混匀后压片。
②黏合剂或润湿剂不当或用量不够,颗粒在压片时粘着力差。
③颗粒太干、含结晶水药物失去过多造成裂片,解决方法与松片相同。
④有些结晶型药物,未经过充分的粉碎。
可将此类药物充分粉碎后制粒。
⑤细粉过多、润滑剂过量引起的裂片,粉末中部分空气不能及时逸出而被压在片剂内,当解除压力后,片剂内部空气膨胀造成裂片,可筛去部分细粉与适当减少润滑剂用量加以克服。
制剂生产过程中常见问题及处理方法

制剂生产过程中常见问题和处理方法一、质量问题制剂生产过程由于种种缘故造成制剂的质量不合格,尤其是在片剂生产中,造成片剂质量问题的因素更多。
现仅对片剂、胶囊剂及注射剂生产中可能产生质量问题的缘故及解决方法作介绍。
(一)片剂生产过程中可能发生问题的分析及解决方法1.松片片剂压成后,硬度不够,表面有麻孔,用手指轻轻加压即碎裂,缘故分析及解决方法:①药物粉碎细度不够、纤维性或富有弹性药物或油类成分含量较多而混合不均匀。
可将药物粉碎过100目筛、选用黏性较强的黏合剂、适当增加压片机的压力、增加油类药物汲取剂充分混匀等方法加以克服。
②黏合剂或润湿剂用量不足或选择不当,使颗粒质地疏松或颗粒粗细分布不匀,粗粒与细粒分层。
可选用适当黏合剂或增加用量、改进制粒工艺、多搅拌软材、混均颗粒等方法加以克服。
③颗粒含水量太少,过分干燥的颗粒具有较大的弹性、含有结晶水的药物在颗粒干燥过程中失去较多的结晶水,使颗粒松脆,容易松裂片。
故在制粒时,按不同品种应操纵颗粒的含水量。
如制成的颗粒太干时,可喷入适量稀乙醇(50%—60%),混匀后压片。
④药物本身的性质。
密度大压出的片剂虽有一定的硬度,但经不起碰撞和震摇。
如次硝酸铋片、苏打片等往往易产生松片现象;密度小,流淌性差,可压性差,重新制粒。
⑤颗粒的流淌性差,填入模孔的颗粒不均匀。
⑥有较大块或颗粒、碎片堵塞刮粒器及下料口,阻碍填充量。
⑦压片机械的因素。
压力过小,多冲压片机冲头长短不齐,车速过快或加料斗中颗粒时多时少。
可调节压力、检查冲模是否配套完整、调整车速、勤加颗粒使料斗内保持一定的存量等方法克服。
2.裂片片剂受到震动或经放置时,有从腰间裂开的称为腰裂;从顶部裂开的称为顶裂,腰裂和顶裂总称为裂片,缘故分析及解决方法:①药物本身弹性较强、纤维性药物或因含油类成分较多。
可加入糖粉以减少纤维弹性,加强黏合作用或增加油类药物的汲取剂,充分混匀后压片。
②黏合剂或润湿剂不当或用量不够,颗粒在压片时粘着力差。
片剂生产中遇到常见问题解决方法
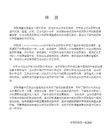
片剂生产过程中可能发生问题的分析及解决方法1.松片:片剂压成后,硬度不够,表面有麻孔,用手指轻轻加压即碎裂,原因分析和解决方法:1.1.药物粉碎细度不够、纤维性或富有弹性药物或油类成分含量较多而混合不均匀。
可将药物粉碎过100目筛,选用黏性较强的黏合剂,适当增加压片机压力,增加油类药物吸收剂充分混匀等方法加以克服。
1.2.黏合剂或润滑剂用量不足或选择不当,使颗粒质地疏松或颗粒粗细分布不匀,粗粒与细粒分层,可选用适当黏合剂或增加用量,改进制粒工艺,多搅拌软材,混均颗等方法加以克服。
1.3.颗粒含水量太少,过分干燥的颗粒具有较大的弹性,含有结晶水的药物在颗粒干燥过程中失去较多的结晶水,使颗粒松脆,容易松裂片,故在制粒时,按不同品种应控制颗粒的含水量,如制万的颗粒太干时,可喷入适量稀乙醇(50~60%)混匀后压片。
1.4.药物本身的性质,密度大,压出的片剂虽有一定的硬度,但经不起碰撞和震摇。
如次硝酸铋片,苏打片等往往易产生松片现象,密度小,流动性差,可压性差,重新制粒。
颗粒的流动性差,填入模孔的颗粒不均匀。
1.5.有较大块或颗粒,碎片堵塞刮粒器及下料品,影响填充量。
1.6.压片机械的因素。
压力过小,多冲压片机冲头长短不一,车速过快,加料斗中颗粒时多时少,可调节压力,检查冲模是否配套,调整车速,勤加颗粒使料斗内保持一定的存量。
2、裂片:片剂爱到震动或经放置时,有从腰间裂天的称为腰裂,从顶部裂开的称为顶裂,二者总称为裂片,原因分析及解决方法:2.1.药物本身弹性较强,纤维性药物或因含油类成分较多,可加入糖粉以减少纤维弹性,加强黏合作用或增加油类药物的吸收剂,充分混匀后压片。
2.2.黏合剂蓝天润湿剂不发或用量不够,颗粒在压片时粘着力差。
2.3.颗粒太干,含结晶水药物失去过多造成裂片,解决方法与松片相同。
2.4.有些结晶型药物,未经过充分的粉碎。
可将此类药物充分粉碎后制粒。
2.5.细粉过多,润滑剂过量引起的裂片,粉末中部分空气不能及时逸出而被压在片剂内,当解除压力后,片剂内部空气膨胀造成裂片,可筛去部分细粉与造当减少润滑剂用量加以克服。
中药片剂粘冲的原因及解决方法

中药片剂粘冲是指中药制剂在生产或使用过程中出现的粘附在包装袋或药瓶内壁上的现象。
这种现象不仅影响了中药品的外观质量,还可能影响药效和药品的服用体验。
中药片剂粘冲的原因各种各样,但主要包括以下几个方面:1. 材料选择:中药片剂制备过程中所使用的原料药材料品质不良、含水量过高、混杂杂质等都会导致制剂粘附。
保证原料品质的稳定性和纯度对避免中药片剂粘冲至关重要。
2. 工艺技术:制剂的生产工艺中,如果烘干温度不够、时间过长或者压片工艺不完善,都可能导致制剂含水量不均匀或者含水过多,从而引起粘附的现象。
3. 包装材料:包装材料的选择和加工质量也是影响中药片剂粘冲的重要因素。
如果包装材料表面不光滑或者容易吸附水分,就容易造成中药片剂的粘附。
针对中药片剂粘冲的问题,可以从以下几个方面着手解决:1. 优化原料选用:对原料的选择要求更加严格,要求供应商提供高纯度、低含水量、无杂质的原料,从源头上杜绝制剂粘冲问题的发生。
2. 改良生产工艺:优化制剂的生产工艺,通过调整烘干温度、时间等参数,确保制剂的含水量均匀且在合适的范围内。
加强粉碎、筛分等步骤的控制,也能有效降低制剂粘冲的发生率。
3. 选用合适的包装材料:选择表面光滑、不易吸附水分的包装材料,并且在加工过程中要控制好包装材料的质量,以确保包装不会成为制剂粘附的隐患。
中药片剂粘冲是一个综合性问题,需要从原料选用、生产工艺到包装材料等多个环节进行全面的控制和管理。
只有全面优化制剂的生产全过程,才能有效避免中药片剂粘冲的问题。
作为写手,我个人认为只有深刻理解和全面掌握中药片剂粘冲的原因和解决方法,才能够更好地指导生产实践。
也需要更加注重原料和生产过程的质量管理,以确保中药片剂的品质和药效。
中药片剂粘冲是一个影响中药品质量的重要问题,对于中药行业来说,如何有效地解决这一问题是至关重要的。
随着中药产业的不断发展,各种新技术、新工艺不断涌现,中药品质管理也面临着新的挑战和机遇。
生产过程中得压片问题及解决办法
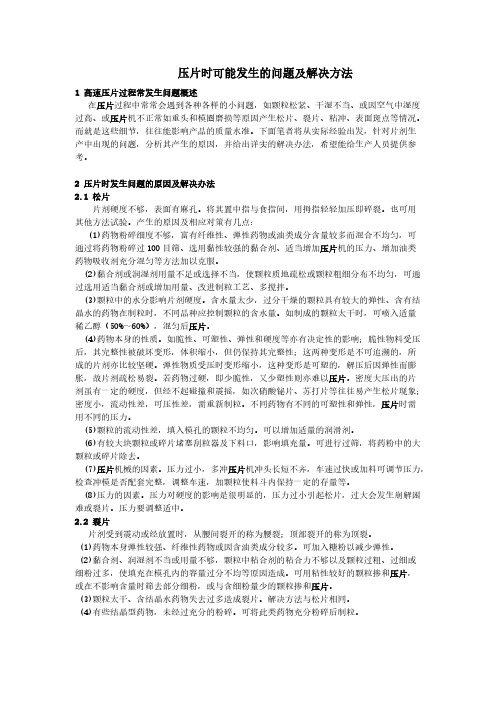
压片时可能发生的问题及解决方法1 高速压片过程常发生问题概述在压片过程中常常会遇到各种各样的小问题,如颗粒松紧、干湿不当、或因空气中湿度过高、或压片机不正常如重头和模圈磨损等原因产生松片、裂片、粘冲、表面斑点等情况。
而就是这些细节,往往能影响产品的质量水准。
下面笔者将从实际经验出发,针对片剂生产中出现的问题,分析其产生的原因,并给出详实的解决办法,希望能给生产人员提供参考。
2 压片时发生问题的原因及解决办法2.1 松片片剂硬度不够,表面有麻孔。
将其置中指与食指间,用拇指轻轻加压即碎裂。
也可用其他方法试验。
产生的原因及相应对策有几点:(1)药物粉碎细度不够,富有纤维性、弹性药物或油类成分含量较多而混合不均匀,可通过将药物粉碎过100目筛、选用黏性较强的黏合剂、适当增加压片机的压力、增加油类药物吸收剂充分混匀等方法加以克服。
(2)黏合剂或润湿剂用量不足或选择不当,使颗粒质地疏松或颗粒粗细分布不均匀,可通过选用适当黏合剂或增加用量、改进制粒工艺、多搅拌。
(3)颗粒中的水分影响片剂硬度。
含水量太少,过分干燥的颗粒具有较大的弹性、含有结晶水的药物在制粒时,不同品种应控制颗粒的含水量。
如制成的颗粒太干时,可喷入适量稀乙醇(50%~60%),混匀后压片。
(4)药物本身的性质。
如脆性、可塑性、弹性和硬度等亦有决定性的影响;脆性物料受压后,其完整性被破坏变形,体积缩小,但仍保持其完整性;这两种变形是不可追溯的,所成的片剂亦比较坚硬。
弹性物质受压时变形缩小,这种变形是可塑的,解压后因弹性而膨胀,故片剂疏松易裂。
若药物过硬,即少脆性,又少塑性则亦难以压片。
密度大压出的片剂虽有一定的硬度,但经不起碰撞和震摇,如次硝酸铋片、苏打片等往往易产生松片现象;密度小,流动性差,可压性差,需重新制粒。
不同药物有不同的可塑性和弹性,压片时需用不同的压力。
(5)颗粒的流动性差,填入模孔的颗粒不均匀。
可以增加适量的润滑剂。
(6)有较大块颗粒或碎片堵塞刮粒器及下料口,影响填充量。
片剂
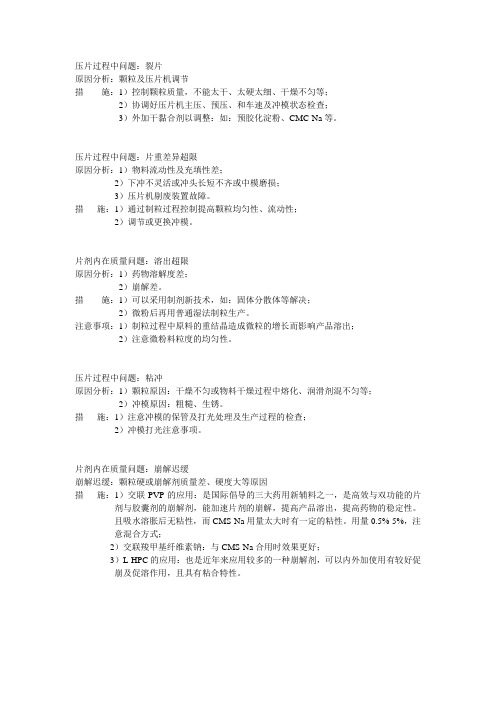
压片过程中问题:裂片原因分析:颗粒及压片机调节措施:1)控制颗粒质量,不能太干、太硬太细、干燥不匀等;2)协调好压片机主压、预压、和车速及冲模状态检查;3)外加干黏合剂以调整:如:预胶化淀粉、CMC-Na等。
压片过程中问题:片重差异超限原因分析:1)物料流动性及充填性差;2)下冲不灵活或冲头长短不齐或中模磨损;3)压片机剔废装置故障。
措施:1)通过制粒过程控制提高颗粒均匀性、流动性;2)调节或更换冲模。
片剂内在质量问题:溶出超限原因分析:1)药物溶解度差;2)崩解差。
措施:1)可以采用制剂新技术,如:固体分散体等解决;2)微粉后再用普通湿法制粒生产。
注意事项:1)制粒过程中原料的重结晶造成微粒的增长而影响产品溶出;2)注意微粉料粒度的均匀性。
压片过程中问题:粘冲原因分析:1)颗粒原因:干燥不匀或物料干燥过程中熔化、润滑剂混不匀等;2)冲模原因:粗糙、生锈。
措施:1)注意冲模的保管及打光处理及生产过程的检查;2)冲模打光注意事项。
片剂内在质量问题:崩解迟缓崩解迟缓:颗粒硬或崩解剂质量差、硬度大等原因措施:1)交联PVP的应用:是国际倡导的三大药用新辅料之一,是高效与双功能的片剂与胶囊剂的崩解剂,能加速片剂的崩解,提高产品溶出,提高药物的稳定性。
且吸水溶胀后无粘性,而CMS-Na用量太大时有一定的粘性。
用量0.5%-5%,注意混合方式;2)交联羧甲基纤维素钠:与CMS-Na合用时效果更好;3)L-HPC的应用:也是近年来应用较多的一种崩解剂,可以内外加使用有较好促崩及促溶作用,且具有粘合特性。
片剂内在质量问题:含量均匀度不合格含量均匀度不合格:原因分析:1)片重差异原因;2)可溶性成分的迁移;3)混合方式不合理;4)片重太大/太小或含量太高/太低。
措施:1)控制片重差异;2)选择合理的干燥方式;3)严格按等量递加法混合;4)注意投料量准确和片重控制。
糖包衣过程中常见问题:掉皮、磨黑掉皮:多在粉衣过程中出现原因:片芯潮或没掌握好加粉料的时间措施:1)片子放置一定时间后包衣;2)糖浆进入片芯适当时机加粉料;3)粉料中增加糊精比例;4)不能赶快补救,仍需等片子充分干透。
- 1、下载文档前请自行甄别文档内容的完整性,平台不提供额外的编辑、内容补充、找答案等附加服务。
- 2、"仅部分预览"的文档,不可在线预览部分如存在完整性等问题,可反馈申请退款(可完整预览的文档不适用该条件!)。
- 3、如文档侵犯您的权益,请联系客服反馈,我们会尽快为您处理(人工客服工作时间:9:00-18:30)。
片剂生产松片、裂片、粘冲与吊冲、片重差异超限的原因及解决方案
在药品生产的一线,常常会遇到各种各样的小问题,而就是这些细节,往往能影响产品的质量水准。
本文从实际经验出发,对于片剂生产中出现的“病症”
给与诊断分析,并给出了详实“处方”。
希望能给一线生产人员提供一定的帮助。
1:病症:松片,即片剂压成后,硬度不够,表面有麻孔,用手指轻轻加压即
碎裂。
处方:
①药物粉碎细度不够、纤维性或富有弹性药物或油类成分含量较多而混合不
均匀。
可将药物粉碎过100目筛、选用黏性较强的黏合剂、适当增加压片机的压
力、增加油类药物吸收剂充分混匀等方法加以克服。
②黏合剂或润湿剂用量不足或选择不当,使颗粒质地疏松或颗粒粗细分布不
匀,粗粒与细粒分层。
可选用适当黏合剂或增加用量、改进制粒工艺、多搅拌软
材、混均颗粒等方法加以克服。
③颗粒含水量太少,过分干燥的颗粒具有较大的弹性、含有结晶水的药物在
颗粒干燥过程中失去较多的结晶水,使颗粒松脆,容易松裂片。
故在制粒时,按
不同品种应控制颗粒的含水量。
如制成的颗粒太干时,可喷入适量稀乙醇(50%-
60%),混匀后压片。
④药物本身的性质。
密度大压出的片剂虽有一定的硬度,但经不起碰撞和震
摇。
如次硝酸铋片、苏打片等往往易产生松片现象;密度小,流动性差,可压性
差,重新制粒。
⑤颗粒的流动性差,填入模孔的颗粒不均匀。
⑥有较大块或颗粒、碎片堵塞刮粒器及下料口,影响填充量。
⑦压片机械的因素。
压力过小,多冲压片机冲头长短不齐,车速过快或加料
斗中颗粒时多时少。
可调节压力、检查冲模是否配套完整、调整车速、勤加颗粒
使料斗内保持一定的存量等方法克服。
2:病症:裂片,即片剂受到震动或经放置时,从腰间裂开的称为腰裂;顶部
裂开的称为顶裂,腰裂和顶裂总称为裂片。
处方:
①药物本身弹性较强、纤维性药物或因含油类成分较多。
可加入糖粉以减少
纤维弹性,加强黏合作用或增加油类药物的吸收剂,充分混匀后压片。
②黏合剂或润湿剂不当或用量不够,颗粒在压片时黏着力差。
③颗粒太干、含结晶水药物失去过多造成裂片,解决方法与松片相同。
④有些结晶型药物,未经过充分的粉碎。
可将此类药物充分粉碎后制粒。
⑤细粉过多、润滑剂过量引起的裂片,粉末中部分空气不能及时逸出而被压
在片剂内,当解除压力后,片剂内部空气膨胀造成裂片,可筛去部分细粉与适当
减少润滑剂用量加以克服。
⑥压片机压力过大,反弹力大而裂片;车速过快或冲模不符合要求,冲头有
长短,中部磨损,其中部大于上下部或冲头向内卷边,均可使片剂顶出时造成裂
片。
可调节压力与车速,改进冲模配套,及时检查调换。
⑦压片室室温低、湿度低,易造成裂片,特别是黏性差的药物容易产生。
调
节空调系统可以解决。
3:病症:粘冲与吊冲,即压片时片剂表面细粉被冲头和冲模黏附,致使片面
不光、不平有凹痕,刻字冲头更容易发生粘冲现象。
吊冲边的边缘粗糙有纹路。
处方:
①颗粒含水量过多、含有引湿性易受潮的药物、操作室温度与湿度过高易产生粘冲。
应注意适当干燥、降低操作室温度、湿度,避免引湿性药物受潮等。
②润滑剂用量过少或混合不匀、细粉过多。
应适当增加润滑剂用量或充分混合,解决粘冲问题。
③冲头表面不干净,有防锈油或润滑油、新冲模表面粗糙或刻字太深有棱角。
可将冲头擦净、调换不合规格的冲模或用微量液状石蜡擦在刻字冲头表面使字面润滑。
此外,如为机械发热而造成粘冲时应检查原因,检修设备。
④冲头与冲模配合过紧造成吊冲。
应加强冲模配套检查,防止吊冲。
4:病症:片重差异超限,指片重差异超过药典规定的限度,
处方:
①颗粒粗细分布不匀,压片时颗粒流速不同,致使填入模孔内的颗粒粗细不均匀,如粗颗粒量多则片轻,细颗粒多则片重。
应将颗粒混匀或筛去过多细粉。
如不能解决时,则应重新制粒。
②如有细粉黏附冲头而造成吊冲时,可使片重差异幅度较大,此时下冲转动不灵活,应及时检查,拆下冲模,擦净下冲与模孔即可解决。
③颗粒流动性不好,流入模孔的颗粒量时多时少,引起片重差异过大而超限,应重新制粒或加入适宜的助流剂,如微粉硅胶,改善颗粒流动性。
④加料斗被堵塞,此种现象常发生于黏性或引湿性较强的药物。
应疏通加料斗、保持压片环境干燥,并适当加入助流剂解决。
⑤冲头与模孔吻合性不好,例如下冲外周与模孔壁之间漏下较多药粉,致使下冲发生“涩冲”现象,造成物料填充不足,对此应更换冲头、模圈。
⑥车速过快,填充量不足。
⑦先下冲长短不一,造成填料不一。
⑧分配器未安装到位,造成填料不一。