雾化喷水结合流态化喷粉进行烧结烟气脱硫的研究
烧结烟气脱硫新工艺

烧结烟气脱硫新工艺【摘要】本文主要介绍了一种新型的脱硫工艺-SDA(旋转喷雾干燥法),通过与其他主要工艺比较,通过对后得出,旋转喷雾干燥法(SDA)作为一种新型的脱硫工艺,适合作为烧结烟气脱硫的主工艺进行推广。
【关键词】烧结烟气;脱硫;旋转喷雾干燥法我国现有烧结机约1200多台,重点钢铁企业有600多台,现有260多台烧结机拥有脱硫设备,大多数烧结机还没有脱硫装置,钢铁工业“十二五”发展规划提出的吨钢二氧化硫排放量要由2010年的1.63kg/t降低到2015年的1.63kg/t以下,“十二五”期间累计要降低39%。
我国钢铁行业在国民经济中占有举足轻重的地位,在为国民经济发展作出重大贡献的同时,也大量地消耗着国内外资源和能源,向钢铁企业周边环境排放大量的污染物。
为推动钢铁行业实施清洁生产,持续减少能源和资源的消耗,减少污染物排放就成为紧迫的任务。
所以,钢铁企业需加强对烧结烟气的综合治理。
1.烧结烟气特点烧结混合料被点燃后,随台车运行,抽入的空气、固体燃料、含铁料、熔剂等发生了一系列物理化学变化,产生的含尘废气被排出,即形成了烧结烟气。
它与环境含尘气体有着明显区别,主要特点:(1)烟气量大,每生产1吨烧结矿即产生3000~5000m3的烟气。
(2)烟气温度较低,随工艺操作状况的变化温度一般在120~180℃。
(3)烟气携带粉尘多,一般在80~120mg/m3。
(4)含湿量大。
为提高烧结混合料的透气性和导热性,混合料在烧结前必须加适量的水,所以烟气量的含湿量较大,一般在8%~10%,露点在65~80℃。
(5)含有以SO2为主要成分的腐蚀性气体。
在点火及烧结过程中,均产生一定量的SOx、NOx、HCI、HF、H2S等,遇水后形成酸,对环境造成污染。
(6)烟气中氧含量高。
由于烧结机在负压状况下操作,除了燃烧段消耗氧气,机头和冷却段都有大量空气进入,氧气消耗较少,导致烟气中O2浓度高达12%~17%。
(7)SO2浓度较低,一般在1000~3000mg/m3,但由于烟气量大,排放总量大。
循环流态化滤泡法烧结烟气脱硫技术的研究

’
一
o0 东-o J 0 d L 警 0 n
6 + 一・ +一 +
在 我 国的 能 源 消 耗 中 ,燃 煤 是 最 主 要 的 能 源 ,而原 煤 的 直 工 艺 在钙 硫 比 、脱 硫 率 、系 统 阻 力和 运 行 成 本 方 面 ,tq 法 脱 - = g
2 湿法烟 气脱硫 技术 比较及 滤泡吸 收技术 说 明
湿法 烟气 脱 硫其 脱硫 液 的工作 形态 有水 膜 状 、液滴 状 和滤 泡 状 几 种 ,卡 应脱 硫塔 可 分 为旋 流板塔 、喷淋 塔 、滤 泡塔 ,它们 的 H 主要技 术参 数 比较 ,见 下表 2 :
表 2 湿 法烟 气脱硫 主要技 术参数 比较
。
蓑 旋板 蓑 流 塔
塔 体结 构 优点 技术较成熟
喷淋塔
滤 泡塔
表 1 :
技术成 熟
表 1 常用 烟气脱 硫工 艺 比较
结构较简单 系统阻力低
技术不成熟
差蔷
水膜状 境
第2 3卷
第1 期 1
21年1 月 01 1
循环流态化滤泡法烧 结烟气脱硫技术 的研 究
贾树 山
( 苏东 大热能机械 制 造有 限公 司 ,盐城 2 40 ) 江 207
摘 要 :本 文 阐述 了滤泡 烟气 吸收技 术的特 点 ,对现 有烟 气脱硫 技 术 的各项 指标进 行 了较 为详 细的 比较 ,并 论述 了滤泡 吸收技
参考 文献
图 1 滤 泡发 生器结 构 示意 图 [. 1 丁智 华 ,秦 光荣 . 谈 干 法烟 气脱 硫 技 术应 用 及其 进 展 】 浅
烟气脱硫技术的研究与应用
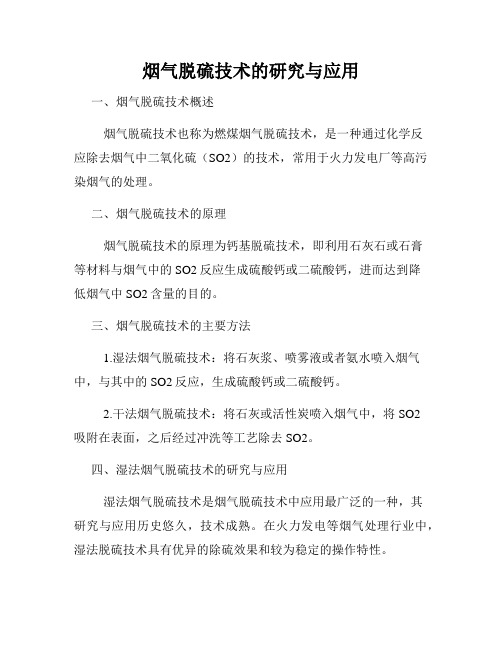
烟气脱硫技术的研究与应用一、烟气脱硫技术概述烟气脱硫技术也称为燃煤烟气脱硫技术,是一种通过化学反应除去烟气中二氧化硫(SO2)的技术,常用于火力发电厂等高污染烟气的处理。
二、烟气脱硫技术的原理烟气脱硫技术的原理为钙基脱硫技术,即利用石灰石或石膏等材料与烟气中的SO2反应生成硫酸钙或二硫酸钙,进而达到降低烟气中SO2含量的目的。
三、烟气脱硫技术的主要方法1.湿法烟气脱硫技术:将石灰浆、喷雾液或者氨水喷入烟气中,与其中的SO2反应,生成硫酸钙或二硫酸钙。
2.干法烟气脱硫技术:将石灰或活性炭喷入烟气中,将SO2吸附在表面,之后经过冲洗等工艺除去SO2。
四、湿法烟气脱硫技术的研究与应用湿法烟气脱硫技术是烟气脱硫技术中应用最广泛的一种,其研究与应用历史悠久,技术成熟。
在火力发电等烟气处理行业中,湿法脱硫技术具有优异的除硫效果和较为稳定的操作特性。
五、干法烟气脱硫技术的研究与应用干法烟气脱硫技术相对于湿法脱硫技术具有的优点包括节能、降低除硫成本等,具有一定的研究价值。
目前,干法脱硫技术的研究尚处于探索阶段,缺少工业化应用经验和成熟的工艺。
六、烟气脱硫技术的发展趋势随着环保意识的不断提高,烟气脱硫技术得到了广泛关注,未来的趋势是技术的进一步完善和创新,降低除硫成本和提高脱硫效果。
同时,综合利用除硫后的废渣、尾气等资源,也成为研究的热点之一。
七、结语烟气脱硫技术的研究和应用为环境保护贡献了重要力量,发展绿色经济事业的大趋势下,其地位和作用日益突显。
今后烟气脱硫技术的研究方向将着重在提高技术创新和成熟度、减少成本和减少废气排放等方面发力。
烧结机循环流化床烟气脱硫技术的分析研究
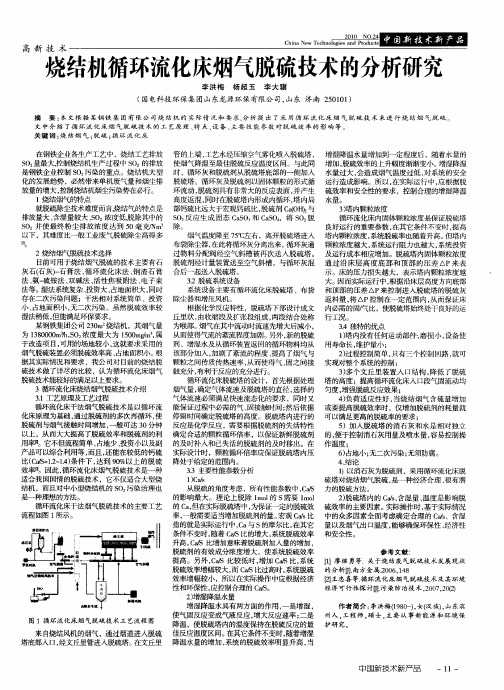
管 的上端 , 工艺水经压 缩空气雾化喷入脱 硫塔 , 使烟气 降温 至最 佳脱硫反应温度 区间。与此 同 时 ,循环灰 和脱硫 剂从 脱硫塔底部 的一 侧加入 脱硫塔 。循环灰及 脱硫 剂 以固体颗粒 的形式循 环流动 , 脱硫剂具有 非常大的反应表 面 , 生 并产 1 烧结烟气的特点 高度返混 , 同时在脱硫 塔内形成 内循环 , 内局 塔 就脱硫除尘技术难度 而言烧 结气 的特点是 部钙硫 比远大于宏观钙硫 比 , 剂 c f}2 脱硫 a {与 0) 排放量大 、 量较大 、O 浓度低脱 除其 中的 S 含湿 S O 反应 生成 固态 C S CS aO 和 aO,将 S O 脱 S: O 并使 最终 粉尘排 放 浓度 达到 5 0毫克/m 除。 N, 以下 , 难度 比一般工业废气脱硫 除尘高得多 其 烟气温度降至 7℃左右 ,离开脱硫塔进 入 5 布袋除尘器 , 此将循 环灰分离出来 。 环灰通 在 循 2烧结烟气脱硫技术选择 过物料 分配 阀经 空气斜槽 被再 次送人脱 硫塔 。 目 可用于烧结烟气脱硫 的技术 主要有石 脱硫剂经计量装置 送至空气斜槽 ,与循环灰 混 前 灰石 ( 石灰)石膏法 、 环流化 床法 、 渣石 膏 合后一起送 ^ 一 循 钢 脱硫塔。 法 、 硫 铵法 、 氨— 双碱 法 、 活性焦 吸 附法 、 电子 束 3 - 2脱硫 系统设备 法等 。 湿法系统复杂 、 资大 、 投 占地面积大 , 同时 系统设备主要 有循 环流化床脱硫塔 、布袋 存在 二次污染问题 ;干法相对系统简单 、投资 除尘器和增 压风机。 小 、 面积 小 , 次污染。虽然脱硫效 率较 占地 无二 根据化学反应 特性 , 脱硫 塔下部设计成文 湿法稍低 , 但能满足环保要求。 丘里状 , 由收缩段及扩张段组 成 , 结合处称 两段 某钢 铁集团公司 20 3 m 烧结机 ,其 烟气 量 为喉部 。 烟气 在其中流动时流速先增 大后减小 , 为 1800 q, 2 300 m hS 浓度 最大 为 10 m / O 50 g , m 属 从而使 得气 流的紊 流程度 加剧 。 另外 , 的脱硫 新 于改造项 目, 的场地较小 , 可用 这就要求采用 的 剂 、 湿水 及从循环装置返 回的循 环物料均从 增 烟气脱硫装置必须脱硫效率高 、 占地面积小。 根 该 部分加入 , 了紊流 的程度 、 了烟气与 加剧 提高 据其 实际情况 和要求 ,我公司对 目前 的烧结 脱 颗粒之间传质传热速率 , 而使得 气 、 从 固之间接 硫技术做 了详尽的 比较 ,认为循环流化床烟 气 触充分 , 有利于反应的充分进行 。 脱硫技术能较好的满足以上要求 。 循环流化床脱硫塔 的设计 ,首先根据处理 3循环流化床烧结烟气脱硫技术介绍 烟气 量 , 定气体流速及脱硫塔 的直径 , 确 选择 的 3 . 1工艺原理及工艺过程 气体 流速必须满足快速流 态化 的要求 ,同时又 循环流化床干法烟气脱硫 技术是 以循环 流 能保 证过程 中必需 的气 、 固接触 时间 ; 后依据 然 化床原理 为基础 , 通过脱硫 剂的多次再循环 , 使 停 留时间确定脱硫塔 的高度 。脱硫塔 内进行 的 脱硫剂与烟气接触 时间增加 , 一般可达 3 分钟 反应 是化学反应 ,需要根据脱硫剂 的失活特性 0 以上 , 从而大大提 高了脱 硫效率和脱硫剂 的利 确定合 适的颗粒循环倍率 ,以保证 新鲜脱硫剂 用率口 它不但流程简单 、 。 占地少 、 投资小 以及 副 的及 时补入和已失活的脱硫剂 的及 时移 出。在 产 品可 以综合利用 等 , , 能在较 低 的钙硫 实 际设计时 ,颗粒循环倍率应保证脱硫 塔内压 而且 还  ̄(a :. 1 ) LC/ I ~4 条件下 , 到 9%以上 的脱硫 降处 于给定 的范 围内。 S 2 达 0 效率日 。因此 , 循环流 化床烟气脱硫技 术是一种 3 . 3主要性能参数分析 适合我 国国情 的脱 硫技术 ,它不仅适合大型烧 1C / )a s 结机 ,而且对 中小 型烧结 机的 S O 污染治理也 从脱硫 的角度考虑 ,所有 性能参数 中, a C/ S 是一种理想的方法。 的影 响最大 。理论上脱 除 1 o 的 s 要 1 o ml 需 ml 循环流化床干法烟气 脱硫 技术的主要工艺 的 C , a但在实 际脱硫塔 中, 为保证一定的脱硫效 流程如图 1 所示。 率, 一般需要适 当增加脱硫剂的量。 宏观 C/比 a s 指的就是实际运行 中,a s C 与 的摩 尔 比。 在其它 条件不变时 , 随着 C/ a S比的增 大 , 系统脱硫效 率 升高 。 比增加意味着脱硫剂加入量的增加 , c 脱硫剂 的有效 成分浓度增大 ,使系统脱硫效 率 提高 。另外 ,a Ct S比较 低时 , 增加 C t , a S比 系统 脱硫效率增幅较大 , C/比过高时 , 而 a S 系统脱 硫 效率增 幅较小 , 以在实际操作 中应根据经 济 所 性和环保性 , 控制合 理的 c/ 应 a。 S 2增湿 降温水量 ) 增湿 降温水具有两方面的作用 , 一是增 湿 , 使气 固反应变 成气液反应 , 增大反应速率 ; 是 二 图 1循 环 流 化 床 烟 气脱 硫 技 术 工 艺流 程 图 降温 ,使脱硫塔 内的温度保持在脱硫反应 的最 来 自烧结风机 的烟气 , 通过 烟道进入脱硫 佳反应温度 区间。 在其它条件不变时 , 随着增 湿 系统 当 塔底部入 口, 经文 匠里管进 人脱硫塔 。 在文丘里 降温水量 的增 加 , 的脱硫效率 明显升 高 ,
烧结烟气脱硫技术探讨
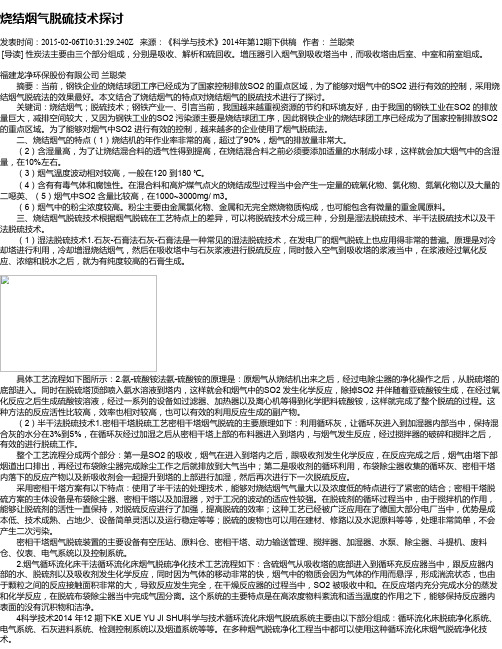
烧结烟气脱硫技术探讨发表时间:2015-02-06T10:31:29.240Z 来源:《科学与技术》2014年第12期下供稿作者:兰聪荣[导读] 性炭法主要由三个部分组成,分别是吸收、解析和硫回收。
增压器引入烟气到吸收塔当中,而吸收塔由后室、中室和前室组成。
福建龙净环保股份有限公司兰聪荣摘要:当前,钢铁企业的烧结球团工序已经成为了国家控制排放SO2 的重点区域,为了能够对烟气中的SO2 进行有效的控制,采用烧结烟气脱硫法的效果最好。
本文结合了烧结烟气的特点对烧结烟气的脱硫技术进行了探讨。
关键词:烧结烟气;脱硫技术;钢铁产业一、引言当前,我国越来越重视资源的节约和环境友好,由于我国的钢铁工业在SO2 的排放量巨大,减排空间较大,又因为钢铁工业的SO2 污染源主要是烧结球团工序,因此钢铁企业的烧结球团工序已经成为了国家控制排放SO2的重点区域。
为了能够对烟气中SO2 进行有效的控制,越来越多的企业使用了烟气脱硫法。
二、烧结烟气的特点(1)烧结机的年作业率非常的高,超过了90%,烟气的排放量非常大。
(2)含湿量高,为了让烧结混合料的透气性得到提高,在烧结混合料之前必须要添加适量的水制成小球,这样就会加大烟气中的含湿量,在10%左右。
(3)烟气温度波动相对较高,一般在120 到180 ℃。
(4)含有有毒气体和腐蚀性。
在混合料和高炉煤气点火的烧结成型过程当中会产生一定量的硫氧化物、氯化物、氮氧化物以及大量的二噁英、(5)烟气中SO2 含量比较高,在1000~3000mg/ m3。
(6)烟气中的粉尘浓度较高。
粉尘主要由金属氯化物、金属和无完全燃烧物质构成,也可能包含有微量的重金属原料。
三、烧结烟气脱硫技术根据烟气脱硫在工艺特点上的差异,可以将脱硫技术分成三种,分别是湿法脱硫技术、半干法脱硫技术以及干法脱硫技术。
(1)湿法脱硫技术1.石灰-石膏法石灰-石膏法是一种常见的湿法脱硫技术,在发电厂的烟气脱硫上也应用得非常的普遍。
钙基循环流化床烧结烟气同时脱硫脱硝技术
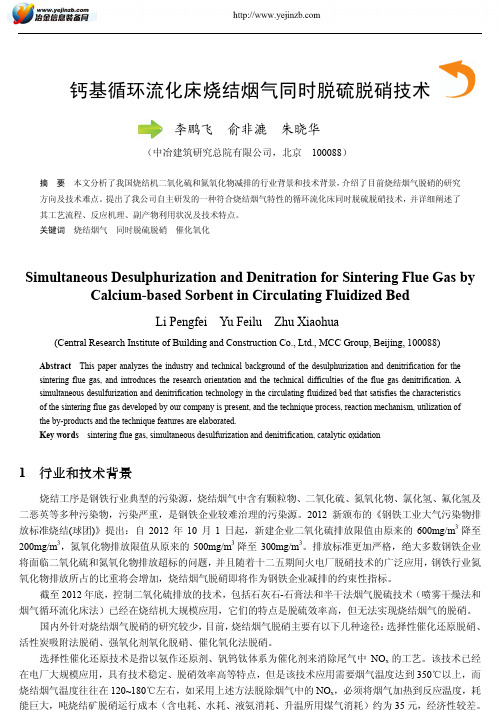
钙基循环流化床烧结烟气同时脱硫脱硝技术李鹏飞俞非漉朱晓华(中冶建筑研究总院有限公司,北京 100088)摘 要 本文分析了我国烧结机二氧化硫和氮氧化物减排的行业背景和技术背景,介绍了目前烧结烟气脱硝的研究方向及技术难点。
提出了我公司自主研发的一种符合烧结烟气特性的循环流化床同时脱硫脱硝技术,并详细阐述了其工艺流程、反应机理、副产物利用状况及技术特点。
关键词 烧结烟气 同时脱硫脱硝 催化氧化Simultaneous Desulphurization and Denitration for Sintering Flue Gas by Calcium-based Sorbent in Circulating Fluidized BedLi Pengfei Yu Feilu Zhu Xiaohua(Central Research Institute of Building and Construction Co., Ltd., MCC Group, Beijing, 100088)Abstract This paper analyzes the industry and technical background of the desulphurization and denitrification for the sintering flue gas, and introduces the research orientation and the technical difficulties of the flue gas denitrification. A simultaneous desulfurization and denitrification technology in the circulating fluidized bed that satisfies the characteristics of the sintering flue gas developed by our company is present, and the technique process, reaction mechanism, utilization of the by-products and the technique features are elaborated.Key words sintering flue gas, simultaneous desulfurization and denitrification, catalytic oxidation1 行业和技术背景烧结工序是钢铁行业典型的污染源,烧结烟气中含有颗粒物、二氧化硫、氮氧化物、氯化氢、氟化氢及二恶英等多种污染物,污染严重,是钢铁企业较难治理的污染源。
烧结烟气有机胺法脱硫工艺_李玲密
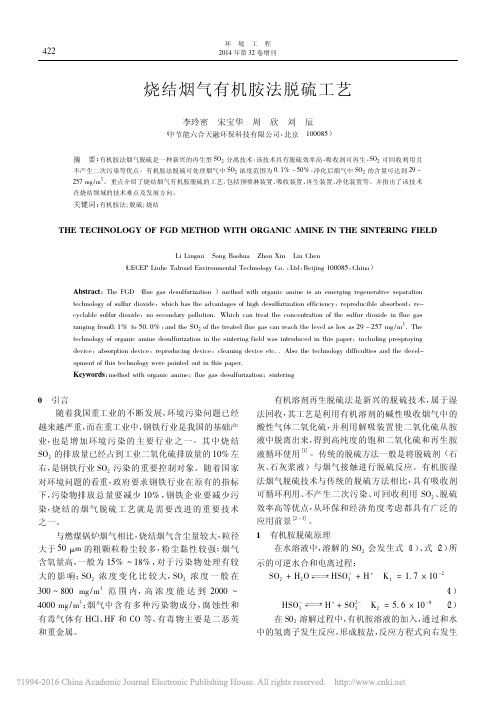
环境工程
2014 年第 32 卷增刊
423
反应,增大了 S02 的溶解量如反应式(3) 。 R3 N + SO2 + H2 O 幈幇 R3 NH + + HSO3- (3)
该 反 应 是 质 子 传 递 过 程,反 应 速 率 常 数[4] K
> 109m3 / kmol·s,反应瞬间完成,主要受气膜控制。随
有机溶剂再生脱硫法是新兴的脱硫技术,属于湿 法回收,其工艺是利用有机溶剂的碱性吸收烟气中的 酸性气体二氧化硫,并利用解吸装置使二氧化硫从胺 液中脱离出来,得到高纯度的饱和二氧化硫和再生胺 液循环使用[1]。传统的脱硫方法一般是将脱硫剂( 石 灰、石灰浆液) 与烟气接触进行脱硫反应。有机胺湿 法烟气脱硫技术与传统的脱硫方法相比,具有吸收剂 可循环利用、不产生二次污染、可回收利用 SO2 、脱硫 效率高等优点,从环保和经济角度考虑都具有广泛的 应用前景[2 - 3]。 1 有机胺脱硫原理
(5)
2 有机胺法脱硫技术发展概况
早在 20 世纪 80 年代,甲基二乙醇胺( MDEA) 就 广泛用于气体净化[5],其特点是能选择性地脱除硫而 将碳保留在净化气中,得到很高纯度的含硫气体可供 回收利用。而乙醇胺( MEA) 和 2 - 甲基 - 2 - 氨基 - 1 - 丙醇( AMP) 也被广泛应用在天然 气 选 择 性 脱 除 H2 S 气体[6 - 7]。BASF 公司开发出了 aMDEA1 - 6 系列 溶剂[8],通过 加 入 不 同 的 活 化 剂 和 添 加 剂 改 善 了 原 MDEA 吸 收 剂 的 性 能。 Winsto Ho[9] 等 人 研 究 了 在 MDEA 中添加位阻胺盐或位阻氨基酸的溶液吸收酸性 气体,对 H2 S 具有相当高的选择性。
烟气脱硫技术及脱硫脱硝除尘与环保策略分析

烟气脱硫技术及脱硫脱硝除尘与环保策略分析烟气脱硫技术是指将燃煤、燃油等化石燃料燃烧产生的烟气中的二氧化硫(SO2)去除的技术。
传统的烟气脱硫技术包括石灰石湿法脱硫、碱液湿法脱硫、海水湿法脱硫等方法。
这些方法主要通过将烟气与反应剂(如石灰石、氨水、碱液等)接触,使SO2发生化学反应生成硫酸钙、硫化氢等物质,从而达到脱硫的目的。
除了传统的湿法脱硫技术,近年来外界还出现了一些新的烟气脱硫技术。
其中较为常见的包括喷射干法脱硫技术、喷射喷雾干法脱硫技术等。
喷射干法脱硫技术是将喷射干法脱硫剂直接喷入炉膛,通过与烟气中的SO2进行反应达到脱硫目的。
喷射喷雾干法脱硫技术则是将脱硫剂与喷雾液混合成烟气雾滴,在炉膛内与 SO2反应,然后与排气一同进入除尘器进行脱硫脱硝。
除了烟气脱硫技术,脱硝也是烟气治理的关键环节之一。
脱硝技术是指将燃煤、燃油等化石燃料燃烧产生的氮氧化物(NOx)去除的技术。
脱硝技术主要有选择性催化还原脱硝技术(SCR)、非选择性催化还原脱硝技术(SNCR)、湿法脱硝技术等。
SCR技术是应用最广泛的一种脱硝技术,该技术通过将氨水或尿素溶液喷射到烟气中,利用催化剂将NOx还原为无害的氮气和水。
除了烟气脱硫和脱硝,除尘也是烟气治理中的重要环节。
除尘技术是将燃煤、燃油等化石燃料燃烧产生的颗粒物去除的技术。
目前常用的除尘技术包括静电除尘、袋式除尘器、湿式除尘器等。
静电除尘主要通过电荷作用将颗粒物带电,然后利用电场力将带电颗粒物从烟气中除去;袋式除尘器主要通过滤袋的作用将颗粒物截留下来;湿式除尘器则是通过喷雾水与颗粒物接触,将颗粒物冲洗下来。
在环保策略方面,可以从以下几个方面进行分析和应对:1. 加强监管和执法:加大对工业企业排污行为的监管力度,对违规排放的行为进行严厉的处罚,推动企业充分履行环境保护的责任;2. 推动技术进步:鼓励企业引进和采用先进的烟气治理技术,提高燃煤电厂、化工厂等排放标准,促进燃煤、燃油等化石燃料的清洁燃烧;3. 提高环保意识:加强对公众和企业的环保教育与宣传,提高公众的环境保护意识,培养企业的环保责任意识;4. 发展清洁能源:加快清洁能源发展,推动可再生能源的利用,减少对化石能源的依赖,降低燃煤、燃油等化石燃料的使用量;5. 加强国际合作:开展国际合作,借鉴先进国家的烟气治理经验和技术,共同应对气候变化和大气污染问题。
适合燃烧结烟气脱硫的SDA技术
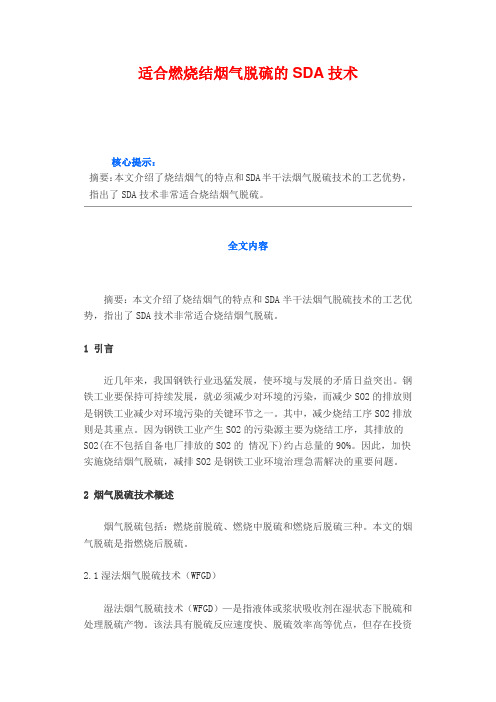
适合燃烧结烟气脱硫的SDA技术核心提示:摘要:本文介绍了烧结烟气的特点和SDA半干法烟气脱硫技术的工艺优势,指出了SDA技术非常适合烧结烟气脱硫。
全文内容摘要:本文介绍了烧结烟气的特点和SDA半干法烟气脱硫技术的工艺优势,指出了SDA技术非常适合烧结烟气脱硫。
1 引言近几年来,我国钢铁行业迅猛发展,使环境与发展的矛盾日益突出。
钢铁工业要保持可持续发展,就必须减少对环境的污染,而减少SO2的排放则是钢铁工业减少对环境污染的关键环节之一。
其中,减少烧结工序SO2排放则是其重点。
因为钢铁工业产生SO2的污染源主要为烧结工序,其排放的SO2(在不包括自备电厂排放的SO2的情况下)约占总量的90%。
因此,加快实施烧结烟气脱硫,减排SO2是钢铁工业环境治理急需解决的重要问题。
2 烟气脱硫技术概述烟气脱硫包括:燃烧前脱硫、燃烧中脱硫和燃烧后脱硫三种。
本文的烟气脱硫是指燃烧后脱硫。
2.1湿法烟气脱硫技术(WFGD)湿法烟气脱硫技术(WFGD)—是指液体或浆状吸收剂在湿状态下脱硫和处理脱硫产物。
该法具有脱硫反应速度快、脱硫效率高等优点,但存在投资和运行维护费用都很高、脱硫后产物处理较难、易造成二次污染、系统复杂、启停不便等问题。
2.2干法烟气脱硫技术(DFGD)干法烟气脱硫技术(DFGD)—干法吸收和产物处理均在干状态下进行。
该法具有无污水和废酸排出、设备腐蚀小、烟气在净化过程中无明显温降、净化低、反应速度较慢、设备庞大。
干法燃气脱硫技术次污染等问题,近年来得到了迅速的发展和应用,但对脱硫率要求较高的情况来说,它的低效率无法满足要求。
2.3半干法烟气脱硫技术(SDFGD)半干法烟气脱硫技术(SDFGD)—半干法兼有干法与湿法的一些特点,使脱硫剂在干燥状态下在湿状态下再生(如水洗活性炭再生流程)或者在湿状态下脱硫在干状态下处理脱硫产物(如喷雾干燥法)的烟气脱硫技术。
特别是在湿状态下脱硫在干状态处理脱硫产物的半干法,以其既具有湿法脱硫反应速度快、脱硫效率高的优点,又具有干法无污水和废酸排出、脱硫后产物易于处理的优点而受到人们广泛的关注。
大连理工大学科技成果——喷雾干燥-干粉活化大倍率循环烟气脱硫技术

大连理工大学科技成果——喷雾干燥-干粉活化大倍率循环
烟气脱硫技术
一、项目简介:
烟气脱硫是节能减排的重要内容,受到广泛重视。
本技术是在已有喷雾干燥脱硫技术的基础上,针对该脱硫技术目前存在的问题,提出的一种综合半干法优点的集成创新脱硫技术。
其基本原理是:以钢厂的钢渣微粉(也可用石灰粉)作脱硫剂,加入到工业废水中,打浆制成吸收剂浆液,浆液由泵打入位于吸收塔内的雾化器中雾化,被雾化成细小液滴的吸收剂与烟气在吸收塔内混合接触,与烟气中的二氧化硫发生化学反应生成CaSO3和CaSO4,烟气中的二氧化硫被脱除。
同时,在塔顶雾化区,引入干粉活化技术,进一步增加脱硫效率。
在喷雾吸收干燥法脱硫技术的基础上,加入干粉活化大倍率循环技术,不仅保持了原技术的脱硫效率高的优势,同时克服了脱硫剂利用率低的缺点,实现了脱硫工艺的高效经济运行.以钢渣微粉作为脱硫剂,脱硫后的灰渣可以作为钢渣水泥的原料使用,既减少了脱硫成本,又解决了灰渣的再利用问题。
本技术适用于钢厂的烧结机烟气脱硫,以及燃煤电厂的烟气脱硫。
对于已有的工业装置或新建的装置,均可采用该技术,不影响装置的正常运行。
对于钢厂烧结机烟气脱硫而言,可处理烟气量50万m3/h~200万m3/h,投资费用在2000万元~6000万元左右。
图工艺原理
图工业实验装置。
喷淋散射法烟气脱硫机理及其优化

喷淋散射法烟气脱硫的应用现状
应用领域
喷淋散射法烟气脱硫技术广泛应 用于火力发电厂、钢铁厂、化工 厂等领域,是工业烟气治理的重
要手段之一。
技术发展
随着环保要求的提高,喷淋散射 法烟气脱硫技术也在不断优化和 完善,如采用新型吸收剂、改进 反应器结构等,以提高脱硫效率
和降低成本。
未来展望
未来,随着环保政策的进一步严 格和技术的不断创新,喷淋散射 法烟气脱硫技术将继续发挥重要 作用,为工业烟气治理做出更大
强化吸收剂的循环利用
通过循环利用吸收剂,减少吸收剂的消耗和损失,提高吸收剂的利用率。
降低能耗与减少水耗
01
02
03
优化烟气入口设计
合理设计烟气入口,降低 烟气进入吸收塔的阻力, 减少能耗。
回收利用余热
将吸收塔内的余热进行回 收利用,减少能源消耗。
减少水耗
通过优化工艺参数和操作 条件,减少用水量和废水 排放量。
氧化还原反应
喷淋液中的氧化剂将SO2氧化为硫酸 盐,同时自身被还原为还原态物质。
反应产物的处理与利用
回收利用
反应产物经过处理后可以回收利用,如亚硫酸盐可以进一步氧化为硫酸盐,用于 制备硫酸等化学品。
无害化处理
对于不能回收利用的反应产物,应进行无害化处理,避免对环境造成二次污染。
03
喷淋散射法烟气脱硫的工艺流 程
喷淋散射法烟气脱硫技术概述
喷淋散射法的定义与特点
定义
喷淋散射法是一种烟气脱硫技术,通过向烟气中喷入吸收剂,使烟气中的SO2 与吸收剂发生化学反应,生成硫酸盐或亚硫酸盐,从而达到脱硫的目的。
特点
喷淋散射法具有较高的脱硫效率,同时能够适应高浓度SO2烟气的处理,且投 资和运行成本相对较低。
喷硫干燥脱硫的基本原理(一)

喷硫干燥脱硫的基本原理(一)喷硫干燥脱硫的基本原理什么是喷硫干燥脱硫?喷硫干燥脱硫是一种常用的燃煤电厂排放脱硫的方法。
该方法通过将二氧化硫与喷雾剂反应,将其转化为固态颗粒物,并通过设备的脱除,以减少对大气环境的污染。
喷硫干燥脱硫的原理和步骤喷硫干燥脱硫主要分为以下几个步骤:1.喷雾剂制备:将一定比例的喷雾剂与水进行混合,以生成一种能与二氧化硫进行反应的溶液。
2.喷雾混合:将喷雾剂溶液通过喷嘴雾化成细小液滴,并与煤燃烧产生的烟气进行混合。
3.溶液反应:在喷嘴雾化后的液滴表面,二氧化硫与喷雾剂中的反应物发生化学反应,产生固态颗粒物。
4.固态颗粒物脱除:通过设备(如除尘器)的作用,将固态颗粒物从烟气中脱除。
喷硫干燥脱硫的原理解析喷雾剂与二氧化硫的反应当喷雾剂与二氧化硫接触时,发生着一系列复杂的化学反应。
喷雾剂中的反应物与二氧化硫发生氧化反应,产生固态颗粒物,并将硫化物等有害物质固化其中。
这些固态颗粒物可以通过后续处理设备进行去除。
液滴表面化学反应速率的影响因素在液滴表面发生的化学反应速率主要受以下因素影响:•反应物浓度:增加反应物的浓度可以提高反应速率。
•温度:提高反应温度有助于加快化学反应。
•液滴尺寸:较小的液滴表面积更大,反应速率更快。
•喷雾剂性质:喷雾剂的物理化学性质对反应速率有直接影响。
固态颗粒物脱除通过合适的设备,如除尘器,可以有效脱除固态颗粒物。
这些设备利用一系列物理和化学的方法,将固态颗粒物从烟气中分离出来。
常见的脱除方法包括静电除尘、湿式除尘和滤袋除尘等。
喷硫干燥脱硫的优势与局限性优势•高效脱硫:喷硫干燥脱硫法对二氧化硫的去除效率高,可以达到90%以上。
•对烟气温度要求低:相比其他脱硫方法,喷硫干燥脱硫对烟气温度要求较低,适用范围广。
•处理能力强:喷硫干燥脱硫设备可以适应处理不同规模和产量的燃煤电厂。
局限性•投资和运营成本较高:喷硫干燥脱硫设备的购置和运营成本较高,对电厂的投资需求较大。
浅析喷雾干燥烟气脱硫技术
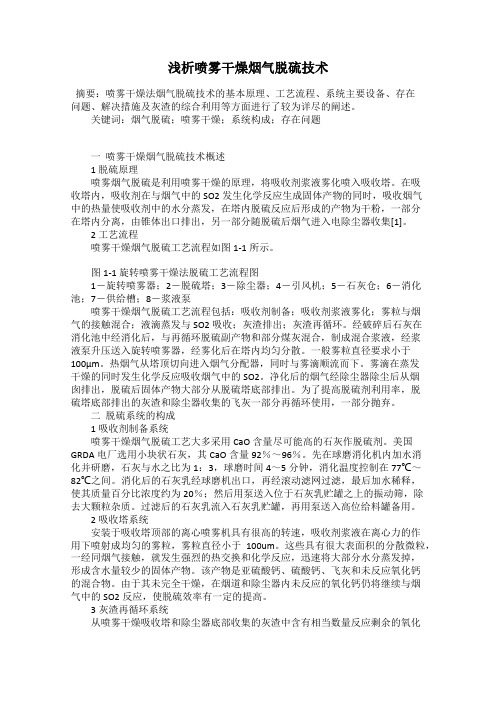
浅析喷雾干燥烟气脱硫技术摘要:喷雾干燥法烟气脱硫技术的基本原理、工艺流程、系统主要设备、存在问题、解决措施及灰渣的综合利用等方面进行了较为详尽的阐述。
关键词:烟气脱硫;喷雾干燥;系统构成;存在问题一喷雾干燥烟气脱硫技术概述1 脱硫原理喷雾烟气脱硫是利用喷雾干燥的原理,将吸收剂浆液雾化喷入吸收塔。
在吸收塔内,吸收剂在与烟气中的SO2发生化学反应生成固体产物的同时,吸收烟气中的热量使吸收剂中的水分蒸发,在塔内脱硫反应后形成的产物为干粉,一部分在塔内分离,由锥体出口排出,另一部分随脱硫后烟气进入电除尘器收集[1]。
2 工艺流程喷雾干燥烟气脱硫工艺流程如图1-1所示。
图1-1 旋转喷雾干燥法脱硫工艺流程图1-旋转喷雾器;2-脱硫塔;3-除尘器;4-引风机;5-石灰仓;6-消化池;7-供给槽;8-浆液泵喷雾干燥烟气脱硫工艺流程包括:吸收剂制备;吸收剂浆液雾化;雾粒与烟气的接触混合;液滴蒸发与SO2吸收;灰渣排出;灰渣再循环。
经破碎后石灰在消化池中经消化后,与再循环脱硫副产物和部分煤灰混合,制成混合浆液,经浆液泵升压送入旋转喷雾器,经雾化后在塔内均匀分散。
一般雾粒直径要求小于100μm。
热烟气从塔顶切向进入烟气分配器,同时与雾滴顺流而下。
雾滴在蒸发干燥的同时发生化学反应吸收烟气中的SO2。
净化后的烟气经除尘器除尘后从烟囱排出,脱硫后固体产物大部分从脱硫塔底部排出。
为了提高脱硫剂利用率,脱硫塔底部排出的灰渣和除尘器收集的飞灰一部分再循环使用,一部分抛弃。
二脱硫系统的构成1吸收剂制备系统喷雾干燥烟气脱硫工艺大多采用CaO含量尽可能高的石灰作脱硫剂。
美国GRDA电厂选用小块状石灰,其CaO含量92%~96%。
先在球磨消化机内加水消化并研磨,石灰与水之比为1:3,球磨时间4~5分钟,消化温度控制在77℃~82℃之间。
消化后的石灰乳经球磨机出口,再经滚动滤网过滤,最后加水稀释,使其质量百分比浓度约为20%;然后用泵送入位于石灰乳贮罐之上的振动筛,除去大颗粒杂质。
烟气脱硫旋流喷嘴雾化特性实验研究

烟气脱硫旋流喷嘴雾化特性实验研究胡鹏睿;惠龙;王永琴【摘要】石灰浆液雾化喷嘴是烟气脱硫系统的关键设备.对一种简式旋流石灰浆液雾化喷嘴的雾化特性进行了实验研究,分析了雾化压力、浆液浓度对雾化角、雾滴粒径分布的影响规律.实验表明:浓度增加,雾化角减小;而雾化压力对雾化角影响较小,雾化角在60°~70°之间;随着雾化压力的增大,雾化流量也增大;当雾化压力大于0.09 Mpa临界雾化压力,雾化粒径集中在1150~1350μm之间.实验结果表明该结构喷嘴的雾化性能满足细烟气脱硫系统的性能要求【期刊名称】《过滤与分离》【年(卷),期】2011(021)001【总页数】4页(P20-23)【关键词】喷嘴;简式旋流喷嘴;雾化特性【作者】胡鹏睿;惠龙;王永琴【作者单位】陕西科技大学机电学院,陕西,西安,710021;国电环境保护研究院,江苏,南京,210031;陕西科技大学机电学院,陕西,西安,710021【正文语种】中文【中图分类】X701.3烟气脱硫是减少SO2排放的一种经济有效的手段,石灰石/石灰-石膏湿法脱硫工艺是技术成熟、应用广泛的一种脱硫方法。
其主要设备是脱硫喷淋塔,SO2的脱除是在喷淋塔内进行的。
SO2的吸收反应主要在吸收液雾化液滴表面进行,雾化液滴的颗粒大小、雾化液滴的均匀性等对吸收反应都有重要的影响。
因此,产生雾滴的喷嘴是喷淋塔内的关键部件,直接影响到脱硫效率和脱硫剂的利用率[1、2]。
本文针对某电厂300 MW机组拟采用的一种旋流喷嘴进行了实验研究,分析了这种喷嘴的雾化性能,为脱硫工艺设计中喷嘴造型选择提供了依据。
选择吸收塔中喷雾喷嘴是控制FGD系统运行和维护费用的重要因素。
在吸收塔中对喷嘴的选择是最严苛的。
选择雾化器时,在给定的操作条件下雾化器应获得最佳的喷雾特性。
本文根据通过量纲分析[3],建立包含喷嘴的几何参数、流动参数和流体特性参数的一些量纲平衡的关系式进行喷嘴的结构设计。
旋转喷雾净化烧结SO2烟气分析
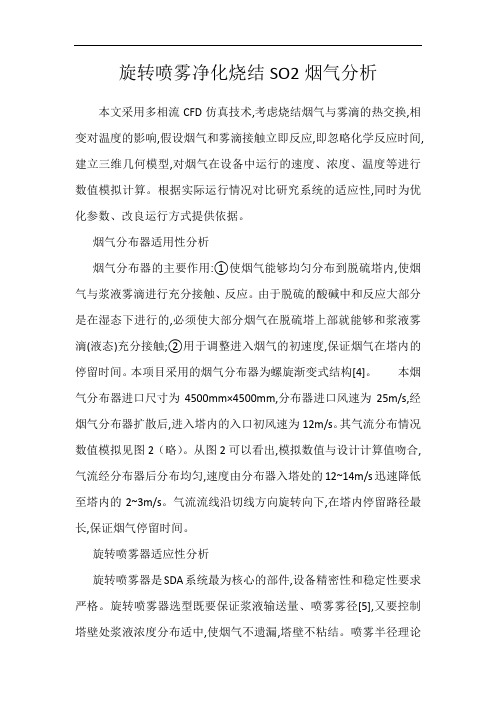
旋转喷雾净化烧结SO2烟气分析本文采用多相流CFD仿真技术,考虑烧结烟气与雾滴的热交换,相变对温度的影响,假设烟气和雾滴接触立即反应,即忽略化学反应时间,建立三维几何模型,对烟气在设备中运行的速度、浓度、温度等进行数值模拟计算。
根据实际运行情况对比研究系统的适应性,同时为优化参数、改良运行方式提供依据。
烟气分布器适用性分析烟气分布器的主要作用:①使烟气能够均匀分布到脱硫塔内,使烟气与浆液雾滴进行充分接触、反应。
由于脱硫的酸碱中和反应大部分是在湿态下进行的,必须使大部分烟气在脱硫塔上部就能够和浆液雾滴(液态)充分接触;②用于调整进入烟气的初速度,保证烟气在塔内的停留时间。
本项目采用的烟气分布器为螺旋渐变式结构[4]。
本烟气分布器进口尺寸为4500mm×4500mm,分布器进口风速为25m/s,经烟气分布器扩散后,进入塔内的入口初风速为12m/s。
其气流分布情况数值模拟见图2(略)。
从图2可以看出,模拟数值与设计计算值吻合,气流经分布器后分布均匀,速度由分布器入塔处的12~14m/s迅速降低至塔内的2~3m/s。
气流流线沿切线方向旋转向下,在塔内停留路径最长,保证烟气停留时间。
旋转喷雾器适应性分析旋转喷雾器是SDA系统最为核心的部件,设备精密性和稳定性要求严格。
旋转喷雾器选型既要保证浆液输送量、喷雾雾径[5],又要控制塔壁处浆液浓度分布适中,使烟气不遗漏,塔壁不粘结。
喷雾半径理论计算公式为(略),式中,d为雾化器转轮直径,m;ML为进料速率,kg/h;N 为转速,r/min;(R99)0.9为雾化器下0.9m处雾滴占全喷雾量99%时的雾滴飞行距离,m。
本项目旋转喷雾器转轮直径为350mm,运行进料速率为35~45t/h,最大量可以达到90t/h,转速为9000~12000r/min。
带入式(1)可以得出喷雾半径范围为8.0~8.6m。
相对于塔半径9.4m来说显得略小,本项目增加了中心烟气通道,使形成的伞雾向上托起,达到增大雾径的效果。
- 1、下载文档前请自行甄别文档内容的完整性,平台不提供额外的编辑、内容补充、找答案等附加服务。
- 2、"仅部分预览"的文档,不可在线预览部分如存在完整性等问题,可反馈申请退款(可完整预览的文档不适用该条件!)。
- 3、如文档侵犯您的权益,请联系客服反馈,我们会尽快为您处理(人工客服工作时间:9:00-18:30)。
第二届大学生工艺流程比赛参赛作品说明书作品名称:雾化喷水结合流态化喷粉进行烧结烟气脱硫的研究设计者:单美龙、刘中秋、张晓博、刘鹏、宋杨、穆丹指导老师:李宝宽、周建安东北大学材料与冶金学院东北大学2010年3月第二届大学生工艺流程比赛申报作品情况说明:1.必须由申报者本人填写;雾化喷水结合流态化喷粉进行烧结烟气脱硫的研究设计者:刘中秋(硕士)、单美龙(硕士)郭颖、刘文军、李自红、李雨言指导老师:李宝宽、周建安东北大学材料与冶金学院作品内容简介目前,烧结烟气脱硫工艺基本可以分为三类:湿法、干法和半干法。
一般来说,湿法脱硫工艺的脱硫剂采用浆液形式,脱硫副产物含水量较高,需要浓缩脱水后才能得到含水量较低的副产物;干法脱硫采用干态脱硫剂,脱硫副产物也是干态的固体;半干法脱硫介于湿法和干法之间,脱硫剂以雾化或加湿的小颗粒形式存在于脱硫过程中,副产物是干态的固体。
针对目前烟气脱硫技术特别是湿法、半干法烟气脱硫技术存在的不足之处,本研究团队在结合了多种烟气脱硫工艺的优点,在循环流化床脱硫方法基础上,开发了一种干法脱硫新工艺——雾化喷水结合流态化喷粉进行烧结烟气脱硫。
该工艺主要是将现代制粉技术与现代脱硫技术有机地结合,取消了利用消化器进行塔外消化的传统做法,集预除尘、消化、脱硫为一体,确保了脱硫剂生石灰的活性及粒度可控性,生产适应能力强,在钢铁烧结烟气脱硫方面优势更为明显。
物理实验研究表明其脱硫效果明显,尤为重要的是克服了传统的湿法、半干法烟气脱硫技术存在的耗费大量资源和能源的问题,且对环境负荷小。
该工艺的深入研究和推广对于革新我国烧结烟气脱硫工艺、实现新形势下的钢铁工业节能减排具有十分重要的意义。
关键词:烧结烟气;脱硫;干法1 研制背景及意义我国是一个能源消耗大国,但在工业生产过程中能源利用率却不是很高,这不仅浪费了大量的能源,而且污染了环境。
因此现在大力倡导建设资源节约型、环境友好型社会。
这不仅要求企业生产高质量、高性能的产品,而且为了实现可持续发展,产品的生产工艺也必须高效率、低成本、节省资源和能源[1,2]。
20 世纪90 年代以来,中国钢铁业快速发展,粗钢产量已连续12 年居世界首位。
2008 年,中国粗钢产量达到510048 亿吨,约占世界粗钢产量的37.16 %,是世界上最大的钢材生产国和消费国。
随着钢铁工业的跨越式发展,环境污染问题也越来越严重。
《国民经济和社会发展第十一个五年规划纲要》要求[3]。
“十一五”期间,我国钢铁企业GDP 能耗降低20 % ,主要污染物排放总量减少10 %。
按中国钢铁工业协会公布的数据,2007年钢铁工业SO2的排放量(应)为95. 36万吨。
2008年SO2 排放量为91. 74 万吨,,较上年同期降低了3. 82%。
预计2010年我国粗钢产量将达到6. 2亿吨、烧结矿7. 6亿吨、球团矿1. 5亿吨,SO2 的排放也将达到127万吨。
目前,“十一五”已经过去了三年多,但钢铁企业已配套建成投运的脱硫设施系统相比于脱硫减排压力仍远远不够,因此,“十一五”后期钢铁企业烟气脱硫的任务仍非常艰巨。
据统计,我国钢铁行业烧结工序的SO2排放量占钢铁行业SO2 总排放量的40% ~60%,因此控制烧结机生产过程中SO2的排放,是钢铁企业SO2 污染控制的重点[4]。
烧结烟气的脱硫,对于实现“十一五”钢铁行业SO2 减排目标具有重要的意义。
2 烧结的工艺流程烧结是指将各种粉状含铁原料,配入适量的燃料和熔剂,加入适量的水,经混合和造球后在烧结设备上使物料发生一系列物理化学变化,将矿粉颗粒黏结成块的过程[5]。
目前生产上广泛采用带式抽风烧结机生产烧结矿。
烧结生产的工艺流程主要包括烧结料的准备,配料与混合,烧结和产品处理等工序。
流程图如下:将筛选合格的铁精矿,高炉炉尘,轧钢皮,钢渣等按比例称量,经物理处理后,进行一次混合,已达到润湿与混匀的目的,并且当加热返矿时还可使物料预热。
使用细磨精矿粉烧结时,因粒度过细,料层透气性差,为改善透气性,必须在混合过程中造球,所以采用二次混合,混合时间一般不少于2.5~3min。
在布混合料之前,先铺一层粒度为10~25mm,厚度为20~25mm 的小块烧结矿作为铺底料,铺完底料后,随之进行布料。
布料时要求混合料的粒度和化学成分等沿台车纵横方向均匀分布,并且有一定的松散性,表面平整。
准备完成后,对台车上的料层表面进行点燃,同时通入煤气和空气并使之燃烧,温度控制在1250±50℃。
这样,一边烧结后的烧结料经过破碎、筛分且冷却后可加入高炉中,成为原料;另一边,烧结烟气中含有大量的污染物,必须经过处理才可以排向大气中,烟气将进入复杂的烟气处理系统,这其中包括重要的烟气脱硫过程。
烧结的一般工艺流程如图1所示:图1 烧结的一般工艺流程3 本设计的工艺流程本工艺的流程如图2所示,烧结排除的烟气首先经过通过引风机进入重力除尘器除尘(在反应塔最下部),经过预除尘的烟气通过一系列的导流板后,烟气的速度分布会变的相对均匀,然后烟气经过拉法尔喷管加速后进入循环流化床多功能反应塔下部,此时烟气的速度相对较大,在拉法尔喷管上方,由喷粉装置喷入生石灰颗粒(颗粒直径<50μm),与此同时在反应塔的另一侧喷入雾化水。
喷入的雾化水一是增湿颗粒表面,二是使烟气温度降低至高于烟气露点20℃左右,创造了良好的脱硫反应温度。
在反应塔上方,生石灰颗粒与雾化水进行消化反应生成熟石灰,熟石灰与烟气中的SO2和水发生化学反应,实现脱硫过程。
消化后的熟石灰与烟气接触后即反应,反应时间一般为3秒。
为了防止烟气速度过快,使脱硫反应更加完全,在反应塔上部又加入了一套喷水装置,如果气体速度过快,打开喷水装置可以增加了烟气在反应塔内的反应时间,增大的脱硫效率。
随后烟气进入布袋除尘器除尘,最后由烟囱排除,此时烟囱出口处的烟气含硫量已大幅降低,脱硫效率在90%以上。
由于固体生成物CaSO4只沉积在颗粒表面,这样部分未反应完全的颗粒表面就会留下一层惰性产物,反应速度会受到影响。
由于流化床中颗粒物存在不断磨损,所以反应产物会不断剥落,为了使生石灰充分的到反应,部分的反应产物会从新进入多功能反应塔进行循环反应。
图2 工艺流程图图3 反应器概念图图4是多功能反应塔的模型图,它形象的给出了反应塔的外部结构,主要包括喷粉系统、灰循环系统及喷雾状水系统。
具体反应塔里面的结构在图3中有显示,主要有导流板和用于气体加速的拉法尔喷管。
图4 多功能反应塔的模型图具体的装置系统安装图如图5所示,其中的煤炉是模拟实际烧结烟气的反应塔,在模拟实验中,在此将煤进行燃烧并加入高含量的硫,通过测量煤炉出口和布袋除尘器后部的硫含量来预测脱硫效率。
图5 本实验装置系统的安装图4 本工艺的化学过程循环流化床多功能脱硫塔内进行的化学反应非常复杂[6],本工艺从不同角度进行了多方面的探索,一般认为石灰粉、工艺水、烟气同时加入流化床中,会有以下主要反应:生石灰粉与雾化液滴结合产生消化反应:CaO + H2O Ca(OH)2 (1)SO2被液滴吸收:SO2 + H2O H2SO3 (2)Ca(OH)2与H2SO3发生反应:Ca(OH)2 + H2SO3 CaSO3·H2O (3)部分Ca(OH)2·H2O被烟气中的O2氧化:Ca SO3·H2O +O2CaSO4·H2O (4)烟气中的HCl和HF等酸性气体同时也被Ca(OH)2脱除:Ca(OH)2 + 2HCl CaCl2 + 2H2O (5)Ca(OH)2 + 2HF CaF2 + 2H2O (6)5 物理实验研究本实验采用的主要测量仪器是雷博3030系列烟尘烟气(油烟)测试仪,它可以完成烟道、管道排气参数(动压、静压、温度、流速、标干流量等)的测定;烟气含氧量、空气过剩系数的测定(可选);管道、烟道气含湿量(干、湿球温度)的测定(可选);各种锅炉、工业炉窑的SO2、NO、NO2、CO排放浓度、折算浓度和排放总量的测定及各类脱硫设备效率的测定(可选)等;一、含湿量测量原理:微处理器控制采气流量,使之通过快速冷凝器,将冷凝水收集到带刻度的玻璃容器内、根据冷凝水的量及后面湿度传感器测量的绝对湿度,准确计算烟气的含湿量。
二、含氧量测量原理:将采样管放入烟道中,抽取含有O2 的烟气,使之通过O2电化学传感器,检测出O2的瞬时浓度,同时根据检测到的O2浓度,换算出空气过剩系数α。
三、SO2、NO、NO2、CO、H2S瞬时浓度及排放量测量:将采样管放入烟道中,抽取含有SO2、NO、NO2、CO的烟气,进行除尘、脱水处理后再通过SO2、NO电化学传感器,分别发生如下反应:SO2+2H2O —> SO42- + 4H++2e-NO +2H2O —> NO3- + 4H++3e-NO2+ H2O —> NO3- + 2H++e-CO +2H2O —> CO32- + 4H++2e-传感器输出的电流的大小在一定条件下与SO2、NO 、NO2、CO 的浓度成正比,所以测量传感器输出的电流即可计算出SO2、NO 、NO2、CO 的瞬时浓度;同时仪器根据检测到的烟气排放量等参数计算出SO2、NO 、NO2、CO 的排放量。
当整个实验系统正常工作后,准备好生石灰粉,把烟气测试仪安装调试好,接下来分以下工况进行测试:工况一:低硫煤燃烧,无喷水的情况, 测定进口和出口处SO 2的浓度(mg/m 3)烟温(℃) 湿度(%) 流速(m/s ) 流量(m 3/h ) SO 2浓度(mg/m 3)O 2浓度(mg/m 3) NO 浓度(mg/m 3)进口-1 220.7 3.3 26 3553 10 17.5 0 进口-2 225.9 1.6 24.2 3340 9 17.4 0 出口-1 56.7 1.2 38.6 4132 9 20.5 0 出口-2 58.61.136.54036820.4工况二:高硫煤燃烧,无喷水的情况, 测定进口和出口处SO 2的浓度(mg/m 3)烟温(℃) 湿度(%) 流速(m/s ) 流量(m 3/h ) SO 2浓度(mg/m 3)O 2浓度(mg/m 3) NO 浓度(mg/m 3)进口-1 202.4 3.4 27.7 7481 255 17.5 0 进口-2 210.5 3.5 28.5 7574 261 17.4 0 出口-1 44.3 1.0 34.9 8313 183 20.4 0 出口-2 46.51.135.1841619520.5工况三:高硫煤燃烧,并外加SO2气体,测定进口和出口处SO2的浓度(mg/m3)烟温(℃) 湿度(%) 流速(m/s ) 流量(m 3/h ) SO 2浓度(mg/m 3)O 2浓度(mg/m 3) NO 浓度(mg/m 3)进口-1 212.4 3.3 28.6 7574 582 17.5 0 进口-2 210.5 3.5 27.8 7517 829 17.4 0 出口-2 39.5 1.9 35.1 8416 51 20.7 0 出口-1 38.62.034.983537020.6脱硫效率对比表工况 工况一 工况二 工况三 情况 低硫,无喷水 高硫,无喷水 高硫,喷水 数据1 10.00% 16.33% 90.26% 数据2 11.11% 16.98% 90.61% 平均10.56%16.66%90.44%公式(7)给出了脱硫效率的计算公式:(7)其中,η—效率,1Q —进口烟气流量m 3/h ,1C —进口烟气硫浓度mg/m 3,2Q —出口烟气流量m 3/h ,2C —出口烟气硫浓度mg/m 3。