Z形件设计
连续Z型檩条的应用设计

图 2 檩托 示意
z型檩 条设 计 成连 续 的情 况 下 , 搭接 部位 的孔 以连 接螺 栓 M1 2为例 : 通 常 打 椭 圆孔 1 4×1 8 , 长 轴方向平行于檩条 的长度方 向。主要解决檩条长 度 方 向 的误 差 , 且 对 截 面 的 削 弱 最 小 。孔 距 与 支 座处作法相 同( 见图3 ) 。
【 K e y w o r d s ] Z e e p u r l i n e , c o n t i n u o u s , n e s t e d l a p - j o i n t
1 前 言
在轻型屋面檩条 中, 斜卷边冷弯z 型薄壁型钢 檩条与传统 的直角卷边 c型檩条 和直角卷边 z 型 钢檩条相 比可叠层 堆放 , 少 占工厂和工地现场 的 空间 , 运输时体积最小 ; 最重要的是 , 斜卷边 z 型钢 檩条可以通过檩条与檩条之间的嵌套搭接达到多 跨 檩 条 连 续 的 目的 , 从 而大 大 减 小 了檩 条 的 下 挠 变形 , 使得檩条可 以跨越更大的跨度 , 承担更大的 荷载, 有 广 阔 的 使 用前 景 。 目前 , 对 连 续 z型檩 条 的性 能研 究仍 是 一项 重要 的课 题 。 2 连续 Z 型檩条的设计计算 檩条 的设计计算 主要包括内力计算 , 强度 、 稳 定性及 刚度计 算 , 对此设计规范及钢结构设计手 册有计算公式及 实例可供参考 。另外 , 值得重视 的是 , 在 实 际工 程 轻 钢 结 构 设 计 中 , 为节 省 钢 材 , 檩条 除用 于承担 梁的功能外 , 往 往兼作支撑体系 中 的 系杆 , 同时 还 通 过 隅撑 对 门 式 刚 架 的 梁 及 柱 提供侧 向支承 , 檩条通常由薄钢板冷 弯成型 , 计算 中还需考虑屈曲后的有效截面等问题 。 在连续檩 条的 内力计算 中 , 荷载分 布情 况对 内力计算影响很大 。 自重恒 载 、 雪 载与风荷 载都 是均匀满布 的。对于活荷载 , 其最不利 的分布 为 任 意隔跨 加载 , 与均匀满布所产生 的内力差别很 大, 前者大于后者。具体计算时 , 可 以按 5 0 %活荷 载均匀满布得到一个效应值 s 。 , 再加 5 0 %活荷载按
折弯治具设计讲解-XX

1.表面刮傷(5min) 2.正位度與平面度控制 (5min)
六﹑交流與考試
(5min) (30min) (30min) (30min) (10min) (15min)
一﹑引言
1﹑連結器制造的几種常見制程介紹
1).產品構成
成型零件(HOUSING、I/M)、金屬零件(CONTACT、SHELL、GROUND PLATE、SPRING 等)、外購件(PCB、電阻、電容、LED、MAGNETIC)
(a)
(b)
二﹑折彎的几種構造分析
1﹑ V形彎曲構造分析 2).沖頭與母模的重合深度與回彈角度有關 (a)重合深度深,回彈角度小 (b)重合深度一般取板厚的5-6倍
二﹑折彎的几種構造分析
2﹑ L形彎曲構造分析 1).成型時必需夾緊材料
成型部位必然是端子局部,要壓緊其餘部分以防止材料移動,位置的準確定位用定位 PIN實現。
側移可能
二﹑折彎的几種構造分析
2﹑ L形彎曲構造分析 2).折彎成型兩段式理論 成型衝子直線段對難易度之影響
此段距離一般取 1~1.5t,
若=0則成型不易.
二﹑折彎的几種構造分析
2﹑ L形彎曲構造分析 3).材料變形兩段式理論 a.衝子導位段下降之過程中即已發生變形(此時若沖子退出,材料亦有塑性 預折) b.衝子R與下模入子R隔材料撞擊,材料變形加大並固化塑性結果..
2).制程簡介
零件供應 二次加工(折彎、裁切) 預裝 檢測 包裝入庫
2﹑折彎的定義及常見折彎類型
壓入、鉚合、焊接、裁切、折彎等
1) 定義
彈性變形 : 施力解除之后可以復原的變形 塑性變形 : 施力解除之后不可以復原的變形
折彎定義 : 上﹑下折彎模仁(沖子P與入子D)施力及壓料 板(脫料板S)的支撐產生胚料的
Z字形弯曲冲孔冲压模具设计

目录第1章前言1第2章冲压件工艺分析22.1材料性能分析22.2工件结构形状分析2第3章工艺参数计算33.1毛坯尺寸的计算33.2弯曲回弹33.3最小弯曲半径43.4弯曲工作尺寸计算53.4.1弯曲凸凹模间隙53.4.2凹模圆角半径53.5冲孔工艺计算63.5.1冲裁间隙的确定63.5.2刃口尺寸的计算及依据与法则6第4章冲压力计算及冲压设备选择84.1冲压力的计算84.1.1弯曲力84.1.2卸料力84.1.3冲孔力84.2冲压设备的选择94.3冲压设备校核9第5章模具总体结构设计115.1模具类型选择115.2定位方式的选用115.3卸料装置的设计115.4模具材料的选择11总结12参考文献13第1章前言冲压是使板料经分离或成形而得到制件的加工方法。
冲压利用冲压模具对板料进行加工。
常温下进行的板料冲压加工称为冷冲压。
模具是大批生产同形产品的工具,是工业生产的主要工艺装备。
模具工业是国民经济的基础工业。
模具可保证冲压产品的尺寸精度,使产品质量稳定,而且在加工中不破坏产品表面。
用模具生产零部件可以采用冶金厂大量生产的廉价的轧钢钢板或钢带为坏料,且在生产中不需加热,具有生产效率高、质量好、重量轻、成本低且节约能源和原材料等一系列优点,是其他加工方法所不能比拟的。
使用模具已成为当代工业生产的重要手段和工艺发展方向。
现代制造业的发展和技术水平的提高,很大程度上取决于模具工业的发展。
目前,工业生产中普遍采用模具成形工业方法,以提高产品的生产率和质量。
一般压力机加工,一台普通的压力机设备每分钟可成形零件几件到几十件,高速压力机的生产率已达到每分钟数百件甚至上千件。
据不完全统计,飞机、汽车、拖拉机、电机、电器、仪表、等产品,有60%左右的零件是用模具加工出来的;而自行车、手表、洗衣机、电冰箱及电风扇等轻工业产品,有90%左右的零件时用模具加工出来的;至于日用五金、餐具等物品的大批量生产基本上完全靠模具来进行。
Z形安装板冲压级进成形工艺与级进模具毕业设计

XXX工程学院毕业设计(论文)题目:Z形安装板冲压级进成形工艺与级进模具设计专业:班级:学号:学生姓名:指导老师:起迄日期:20XX 年 X 月 XX毕业设计说明书(论文)中文摘要Z形安装板级进成形工艺与级进模具设计论文本文首先分析了Z形安装板冲压的结构,尺寸,精度和原材料性能,并制定出有效的成形方案:多工位级进模。
分析了Z形安装板冲压的成形工艺特点,包括工件的三维造型、工件的工艺分析、工序排样、工艺计算,确定了该模具包括冲孔,弯曲,切边,落料在内的7个工位。
完成了级进模的总体概要设计、级进模零件详细设计、冲压设备的选择等工作。
详细介绍了模具凸模、凹模、固定板、卸料装置、出件装置等零部件的设计方法。
同时阐述了模具的工作过程以及凸模和凹模、凸模与卸料板间的装配间隙。
关键词多工位级进模;成形工艺;工艺分析;模具设计;零件设计;毕业设计说明书(论文)外文摘要Title Z Rotaing Bearing Frame Progressive FormingProcess and Progressive-Die DesignAbstractThis article first analyzes YL05 rotating bearing frame structure, size, accuracy and material properties, and to develop effective shaping program: multi-position progressive die.Analysis of YL05 rotating bearing frame forming process features, including parts of three-dimensional shape, parts of the process analysis, process layout, process calculation. Identify the mold' s 16 station, including punching, bending, trimming, pleted a general summary of progressive die design, detailed design of progressive die parts, stamping equipment selection, etc.Details of the mold punch and die, fixed plate, discharge device, the pieces of equipment and other parts of the design method.Also explained the working process of the die and assembly gap between Punch and die, punch and stripper plate.Keywords Multi-Position Progressive Die ; Forming process ;Process analysis ; Mold Design ; Part Design ;目录前言 (1)第一章零件工艺性分析 (2)1.1Z形安装板冲压工艺性分析 (2)1.5Z形安装板冲压的工艺方案确定 (3)第二章排样设计 (4)2.1 毛坯排样设计 (5)2.1.1 毛坯尺寸计算 (5)2.1.5 条料搭变值确定 (6)2.1.3 毛坯排样 (6)2.2 冲切刃口外形设计 (7)2.3 工艺排样设计 (7)2.3.1 确定步距 (8)2.3.2 工序排样图 (8)第三章工艺计算 (9)3.1冲压工艺力的计算 (9)3.1.1 冲裁力计算 (9)3.1.5 弯曲力计算 (12)3.1.3 卸料力的计算 (13)3.1.4 总压力的计算 (13)3.2 压力中心计算 (13)第四章模具总体概要设计 (14)4.1 模具结构概要设计 (14)4.1.1 模具基本结构形式 (15)4.1.5 模具基本尺寸 (15)4.1.3 模架结构确定 (17)4.1.4 模具闭合高度 (17)4.2 模具结构详细设计 (17)4.2.1 工作单元结构 (17)4.2.2 卸料机构结构 (17)4.2.3 导正销结构 (18)4.2.4 各模板结构 (18)4.3 模具结构图 (18)4.4 模具工作过程 (20)第五章模具零件详细设计 (21)5.1工作零件 (21)5.1.1 冲裁凸模设计 (21)5.1.5 凹模设计 (25)5.2 定位零件 (27)5.2.1 导料板 (27)5.2.2 导正销 (27)5.3 出件零件 (29)5.3.1 卸料板 (29)5.4 导向零件 (30)5.5 其他零件 (30)第六章设备选择 (31)6.1 设备选择 (31)6.2 设备校合 (31)第七章结论 (32)致谢 (33)参考文献 (34)前言随着电子、电器、轻工、汽车等行业的不断发展,多工位级进模的应用也越来越广泛。
第三章弯曲工艺与弯曲模设计

形状复杂或精度要求高的弯曲件,需反复试 验弯曲,才能确定弯曲件毛坯尺寸。
测验题
填空 1、弯曲件展开长度的计算依据是 。
判断 1、弯曲件的中性层一定位于工件1 / 2料厚位置。( ) 计算 1、计算如图所示弯曲件的坯料长度。
参考答案
课后思考
1、如何计算弯曲件的展开尺寸?
3.5
弯曲时回弹补偿量的确定
3.7
弯曲凸、凹模成形尺寸计算
学习目标: 能够确定弯曲模凸、凹模的结构参数,理解 凸、凹模的各部分尺寸大小对弯曲模工作或弯曲 件质量的影响。 教学要求: 根据弯曲相对半径,设计凸模的圆角半径和 圆弧中心角;根据弯曲件的尺寸及厚度确定凸、 凹模的各部分尺寸。
3.7.1
凸模
凸模设计主要是圆角半径和圆弧中心角。 圆角半径应始终大于材料最小相对弯曲半径。 凸模圆角半径的确定方法:
lmax,lmin—工件的最大,最小极限尺寸; Z—凸、凹模单边间隙; —工件公差; d,p—凹、凸模制造公差,一般按IT9级选用, 也可按d=p=/4选取。
测验题
计算 1、计算如图所示弯曲制件的模具工作部分尺寸。
参考答案
课后思考
1、如何确定弯曲模凸、凹模的尺寸?
3.8
弯曲模结构设计
(2)当工件r/t≤[rmin/t]时:
p
实例分析
3.7.2
凹模
凹模圆角半径各方向应一致,通常根据材料 的厚度t选取。 当 t≤2mm时
t=24mm时
t>4mm时
R d= (3 6 )t R d= (2 3 ) t Rd=2t
凹模圆角半径不得小于3mm
3.7.3
凸、凹模间隙
V形件弯曲:间隙由调整冲床的闭合高度获得。 U形件弯曲:
弯曲工艺和弯曲模具设计
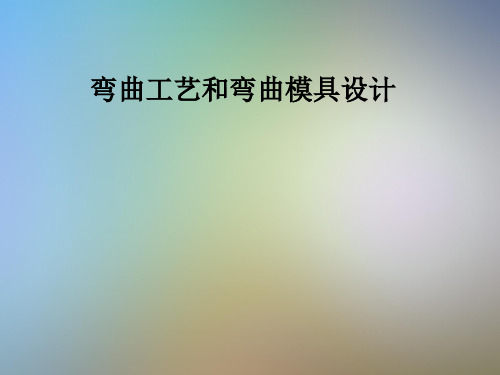
3.2.2影响回弹的因素
1.材料的力学性能 材料的屈服点 越高,弹性模量E越小,弯曲弹性回跳
越大。
2.相对弯曲半径 相对弯曲变径
越大,则回弹也越大。
3.弯曲中心角 弯曲中心角 越大,表明变形区的长度越长,故回弹的
积累值越大,其回弹角越大。但对弯曲半径的回弹影响不大。
4.弯曲方式及弯曲模具结构 采用校正弯曲时,工件的回弹小。
时弯曲半径r继续减小,而直边部分反而向凹模方向变形, 直至板料与凸、凹模完全贴合。
3.1.2板料弯曲变形特点
通过网格试验观察弯曲变形特点(如图3.1.3)。
图3.1.3 弯曲前后坐标网络的变化
1.弯曲圆角部分是弯曲变形的主要变形区 变形区的材料外侧伸长,内侧缩短,中性层长度不变。
2.弯曲变形区的应变中性层
•
• 1、弹性弯曲条件
若材料的屈服应力为 σs ,
则• 弹性弯曲的条件为:
•
2、塑性弯曲的应力与应变条件
• (a)弹性弯曲; (b)弹-塑性弯曲; (c)塑性弯 曲
• 图3.1.5弯曲毛坯变形区的切向应力分布
• 3.1.3弯曲时变形区的应力和应变
•
• 板料在塑性弯曲时,变形区
内的应力应变状态取决于弯曲
铰链弯曲和一般弯曲件有所不同,铰链弯曲常用推卷的方法成形
。在弯曲卷圆的过程中,材料除了弯曲以外还受到挤压作用,板料不是 变薄而是增厚了,中性层将向外侧移动,因此其中性层位移系数K≥0.5。 图3.3.13所示为铰链中性层位置示意图。
•图3.3.12 铰链中性层位置
•图3.3.13 铰链弯曲件
3.3.5弯曲件弯曲工序的安排
3.弯曲件直边高度对弯曲的影响(如图3.3.5) 在进行弯曲时,若弯曲的直边高度过短,弯曲过程中
轻钢结构中Z型连续檩条设计问题的探讨

17
© 1995-2005 Tsinghua Tongfang Optical Disc Co., Ltd. All rights reserved.
M3 控制截面设计 。具体设计时 ,可令第一跨檩条加 厚 ,其余跨由 M10控制计算 。对于满布均匀荷载 、跨度 相等且跨数无限的等截面连续梁 ,支座处的弯矩与跨 中的弯矩之比为 2[10] ,考虑支座处弯矩释放 10 % ,则 为 019/ (015 + 011) = 115 。国内通常不考虑支座处双 檩条强度 ,仍按单檩条计算 ,这样支座处的弯矩必然控 制截面强度设计 ,其结果将不经济 。
一 、前言 在应用广泛的门式刚架轻型房屋钢结构设计中 ,
最为困难的是对檩条的设计计算 。困难来自于两方 面 :首先 ,在设计规范或规程中无简单实用的计算公式 供设计人员采用 ;其次 ,为节省钢材 ,轻钢结构中的檩 条除用于 承 担 梁 的 功 能 外 往 往 兼 作 支 撑 体 系 中 的 压 杆 ,同时还通过隅撑对门式刚架的梁和柱提供侧向支 承 。如果考虑门式刚架轻钢房屋中的蒙皮效应 ,则檩 条的构造和受力计算更为复杂 。檩条通常由薄钢板冷 弯成型 ,计算中还需考虑屈曲后的有效截面等问题 ,因 此 ,精确计算檩条的承载能力非常困难 。
© 1995-2005 Tsinghua Tongfang Optical Disc Co., Ltd. All rights reserved.
Z形冷弯薄壁型钢墙梁计算分析
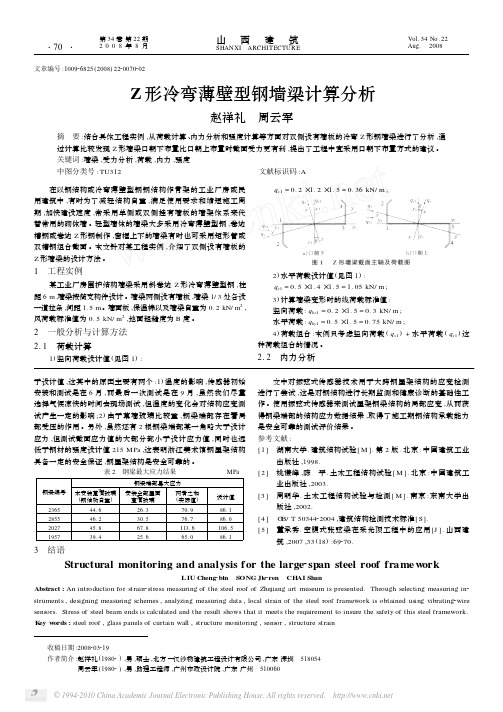
某工业厂房围护结构墙梁采用斜卷边 Z 形冷弯薄壁型钢 ,柱 距 6 m ,墙梁按简支构件设计。墙梁两侧设有墙板 ,墙梁 1/ 3 处各设 一道拉条 ,间距 1. 5 m。墙面板 ,保温棉以及墙梁自重为 0. 2 kN/ m2 , 风荷载标准值为 0. 5 kN/ m2 ,地面粗糙度为 B 度 。
Key words : steel roof , glass panels of curtain wall , structure monitoring , sensor , structure strain
收稿日期 :2008203219 作者简介 :赵祥礼 (19802 ) ,男 ,硕士 ,北方 —汉沙杨建筑工程设计有限公司 ,广东 深圳 518054
周云军 (19802 ) ,男 ,助理工程师 ,广州市政设计院 ,广东 广州 510060
© 1994-2010 China Academic Journal Electronic Publishing House. All rights reserved.
(4)
其中 ,θ为主轴 x 与平行于墙面轴 x1 的夹角 。
试选墙梁截面为斜卷边 Z 形冷弯薄壁型钢 Z160 ×60 ×20 ×
2. 0 ,墙梁口朝下布置 ,截面特性 :
W x1 = 40. 271 cm3 , W x2 = 29. 603 cm3 , W y1 = 8. 018 cm3 , W y2 = 9. 554 cm3 , Ix1 = 246. 830 cm4 ,θ= 22. 104°。
结合具体工程实例从荷载计算内力分析和强度计算等方面对双侧设有墙板的冷弯z形钢墙梁进行了分析通过计算比较发现z形墙梁口朝下布置比口朝上布置时截面受力更有利提出了工程中宜采用口朝下布置方式的建议
模具毕业设计11Z形件弯曲模设计说明书

学校冲压模具课程设计说明书——Z形件弯曲模设计院系机械系班级模具班学生姓名同组成员指导教师完成日期年7 月7 日零件简图:如右图所示生产批量:大批量材料:Q235材料厚度:1.5mm1.冲压件工艺分析该工件只有切断和弯曲两个工序,材料Q235钢为软材料,在弯曲时应有一定的凸凹模间隙.工件的尺寸全部为自由公差,可看作IT14级,尺寸精度较低,普通弯曲就能满足要求.2.冲压方案的确定该工件包括切断和弯曲两个工序,可以有以下几种方案:方案一:先切断,后弯曲.采用单工序模生产;方案二:切断___弯曲复合冲压.采用复合模生产;方案一模具结构简单,但需要两道工序两副模具,生产效率低,难以满足该工件大批量生产要求;方案二需一副模具,生产效率高,尽管模具结构较方案一复杂,但由于零件几何形状简单,模具制造并不困难.通过对上述方案的分析比较,该工件的冲压生产采用方案二为佳.3.主要设计计算(1)毛坯尺寸计算工件弯曲半径r>0.5t,故坯料展开尺寸公式为:L Z=L直1+ L直2 +L直3 +L弯1+ L弯2查表3.4.1,当r/t=2.5,x=0.39.L直1=14-r-t=14-4-1.5=8.5mm,L直2=40-2t-2r=29mm,L弯1=∏α/180(r+xt)=3.14×90(4+0.39×1.5)/180=7.1984mm, 故L Z=8.5+29+8.5+7.1984+7.1984=60.3968mm(2)排样及相关计算采用直排,且无废料。
坯料尺寸为60.40mm×16mm.查板材标准,选用冲压力的计算落料力:F落=KLtτb=10920 N τb=350MPa弯曲力:F自=6.6KBt2σb/r+t=2042.182 N σb=400MPaF校=AP=19600 N顶件力或压料力: FD =0.5 F自=1021.91 N压力机公称压力: F压=1.2 F校=23520 N(3)冲压工序力计算根据冲压工艺总力计算结果,并结合工件高度,初选开式固定台压力机JH21-25.(4)工作部分尺寸计算①凸模圆角半径: rT=4mm工作相对弯曲半径r/t较小,故凸模圆角半径rT等于工件的弯曲半径。
跨桥式端子Z形折弯多工位级进模设计
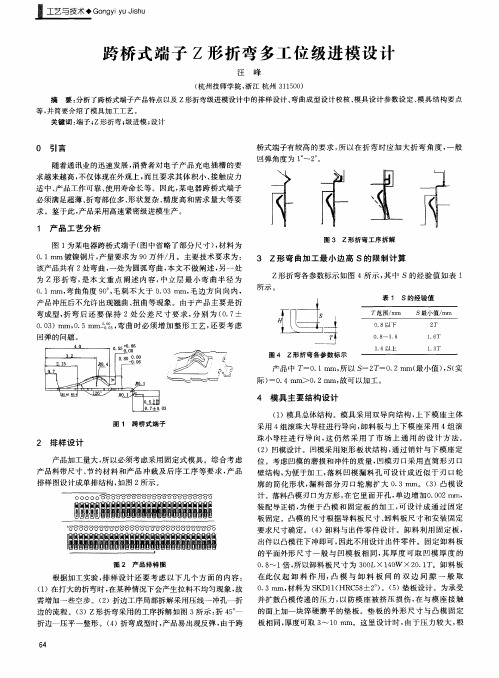
边的流程 。( 3 )z形折弯采用的工序拆解如 图
所示 : 折 4 5 。 一
折边一压平一整形 。( 4 )折弯成型时 , 产品易出现反弹 , 由于跨
6 4
G。 n g Y i y u J i s h u
,
* 5 2 Z -  ̄ t Y l J .
据 GB 2 8 6 5 . 2 —8 1选 取 规 格 为 3 0 0 L× 1 4 0 WX 1 5 . 0 T。 ( 6 ) 凸
( 1 )在打大 的折弯时 , 在某种情况下会产生拉料不均匀现象 , 故
需增加一些空步。( 2 )折边 工序 局 部 拆 解 采 用 压线 一 冲孔 一 折
士2 。 ) 。( 5 ) 垫 板 设 计 。为 承 受
并扩散凸模传 递的压力 , 以防模座被 挤压损 伤 , 在 与模 座接 触
的面 上 加 一 块 淬 硬 磨 平 的 垫 板 。垫 板 的 外 形 尺 寸 与 凸模 固 定 板相 同, 厚度可取 ~ 。这 里 设 计 时 , 由于压 力较大 , 根
壁结构 , 为便于加工 , 落料 凹模 漏料孔 可设计 成近似 于 刃 口轮 廓的简化 形状 , 漏料 部分刃 口轮廓扩 大 . 。( 3 )凸模设 , 计。落料凸模刃 口为方形 , 在它里 面开孔 , 单边 增加O .
装配导正销 , 为便于 凸模 和 固定 板 的加 工 , 可 设计成 通过 固定
桥式端子有较 高的要求 , 所 以在折弯 时应加 大折弯 角度 , 一般
回弹 角 度 为 1 。 ~2 。 。
1 产 品 工 艺 分 析
图1 为某电器跨桥式端子 ( 图 中省略 了部分 尺寸) , 材料为
图 Z形 折 弯 工 序 拆解
弯曲件设计的参考数据和设计

弯曲模具的结构设计是在弯曲工序确定后的基础上进行的,设计时应考虑弯曲件的形状、精度要求、材料性能以及生产批量等因素,下面分析常见各类型弯曲模的结构和特点。
一. V 形件弯曲模V 形件即为单角弯曲件,形状简单,能够一次弯曲成形。
这类形状的弯曲件可以用两种方法弯曲:一种是沿着工件弯曲角的角平分线方向弯曲,称为 V 形弯曲;另一种是垂直于工件一条边的方向弯曲,称为 L 形弯曲。
1-顶杆;2定位钉;3-模柄; 4-凸模;5-凹模;6-下模座;3.4.1 有压料装置的V形件弯曲模V 形件弯曲模的基本结构如图 3.4.1 所示,图中弹簧顶杆 1 是为了防止压弯时板料偏移而采用的压料装置。
除了压料作用以外,它还起到了弯曲后顶出工件的作用。
这种模具结构简单,对材料厚度公差的要求不高,在压力机上安装调试也较方便。
而且工件在弯曲冲程终端得到校正,因此回弹较小,工件的平面度较好。
如果弯曲件精度要求不高,为简化模具结构,压料装置也可以省略不用。
图 3.4.2 所示为无压料装置的 V 形件弯曲模。
1-模柄;2-上模座;3-导柱、导套;4、7-定位板;5-下模座;6-凹模;7-凸模3.4.2 无压料装置的V形件弯曲模当弯曲相对宽度很大的细长 V 形件时,会产生明显的翘曲现象,这种情况下可以采用带侧板结构的弯曲模,以阻碍材料沿弯曲线方向的流动(见图 3.4.3a );也可以改变弯曲凸、凹模形状,将翘曲量设计在与翘曲方向相反的方向上(见图 3.4.3b )。
图3.4.3 减少弯曲件翘曲的模具结构L 形弯曲模常用于两直边相差较大的单角弯曲件,如图 3.4.4a 所示。
弯曲件的长边被夹紧在压料板和凸模之间,弯曲件过程中另一边竖立向上弯曲。
由于采用了定位销定位和压料装置,压弯过程中工件不易偏移。
但是,由于弯曲件竖边无法受到校正,因此工件存在回弹现象。
a〕1-凸模;2-凹模;3-定位销;4-压料板;5-挡块 b〕1-凸模;2-压料板 3-凹模;4-定位板;5-挡块图3.4.4 L形弯曲模图 3.4.4b 为带有校正作用的 L 形弯曲模,由于压弯时工件倾斜了一定的角度,下压的校正力可以作用于原先的竖边,从而减少了回弹。
机械自动化本科毕业设计题目大全

8、五层电梯的PLC自动控制
9、PLC在多工步机床控制中的应用
10、移动罩滤池PLC控制系统的设计
11、PLC控制直列式加工自动线设计
12、PLC在火力发电厂气力除灰中的应用
13、切片机的电气控制
14、PLC在立式车床控制系统中的应用
15、双面钻孔组合机床的控制电路设计
6、金属垫片的冲孔落料模具设计
7、胶水瓶盖塑料模具设计
8、物料输送装备系统设计
9、工频淬火机床的优化与设计
10、漱口杯塑料模具设计
11、米杯塑料模具设计
12、粒状物分选设备输送定位机构设计
13、工业电器盒注射模具设计
14、洗衣桶塑料模具设计
15、对辊式破碎机及提升装置设计
16、手机电池后盖塑料模具设计
14、扬声器锥形盘架冲拉复合模设计及虚拟加工
15、花生湿式去皮机的设计
16、便携式探伤仪壳体注塑模设计及仿真
17、曲轴多体动力学仿真加工及优化
5
黄崇林
(15人)
1、齿轮单面啮合综合检查仪的设计
2、垃圾粉碎机的设计
3、物料灌装自动生产线的设计
4、CA6136普通车床数控化改造
5、电子计价称的设计
6、乳粉包装称重控制系统的设计
17、相关注塑模具的机械设计;
2
邓昌奇
(15人)
1、原料系统的控制
2、一种高可靠性生产线控制器的设计
3、CK6140车床电气化改造设计
4、行李输送机构的控制
5、机械手电气控制设计
6、模糊电冰箱控制系统
7、基于PLC组合机床电气化控制的设计
8、节水灌溉工程的应用
9、五层电梯的单片机、PLC控制
z形冲压折弯方法
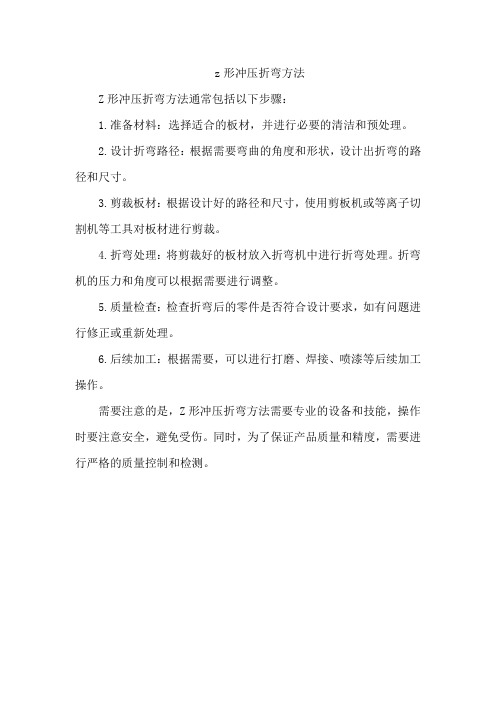
z形冲压折弯方法
Z形冲压折弯方法通常包括以下步骤:
1.准备材料:选择适合的板材,并进行必要的清洁和预处理。
2.设计折弯路径:根据需要弯曲的角度和形状,设计出折弯的路径和尺寸。
3.剪裁板材:根据设计好的路径和尺寸,使用剪板机或等离子切割机等工具对板材进行剪裁。
4.折弯处理:将剪裁好的板材放入折弯机中进行折弯处理。
折弯机的压力和角度可以根据需要进行调整。
5.质量检查:检查折弯后的零件是否符合设计要求,如有问题进行修正或重新处理。
6.后续加工:根据需要,可以进行打磨、焊接、喷漆等后续加工操作。
需要注意的是,Z形冲压折弯方法需要专业的设备和技能,操作时要注意安全,避免受伤。
同时,为了保证产品质量和精度,需要进行严格的质量控制和检测。
z型钣金折弯计算公式

z型钣金折弯计算公式Z型钣金折弯计算公式。
钣金折弯是一种常见的加工工艺,用于将平板钣金通过折弯成各种形状的零件。
在钣金折弯过程中,我们需要根据材料的性质和要求的尺寸来计算折弯的参数,以确保折弯后的零件符合设计要求。
其中,Z型钣金是一种常见的折弯形式,下面我们来介绍一下Z型钣金折弯的计算公式。
Z型钣金折弯是指将一块平板钣金通过一系列的折弯工序,将其折弯成Z字形的零件。
在进行Z型钣金折弯计算时,我们需要考虑到材料的弹性模量、厚度、折弯角度等因素。
下面是Z型钣金折弯计算的公式:1. 弯曲力矩的计算公式。
在进行Z型钣金折弯计算时,首先需要计算弯曲力矩。
弯曲力矩是指在折弯过程中,材料所受到的力矩。
其计算公式为:M = W L。
其中,M为弯曲力矩,单位为牛顿·米(N·m);W为折弯力,单位为牛顿(N);L为折弯长度,单位为米(m)。
2. 折弯力的计算公式。
折弯力是指在进行Z型钣金折弯时,所需的力量。
其计算公式为:W = σ S L。
其中,W为折弯力,单位为牛顿(N);σ为材料的应力,单位为帕斯卡(Pa);S为材料的截面积,单位为平方米(m²);L为折弯长度,单位为米(m)。
3. 应力的计算公式。
在进行Z型钣金折弯计算时,需要计算材料在折弯过程中所受到的应力。
其计算公式为:σ = (M h) / (W t)。
其中,σ为材料的应力,单位为帕斯卡(Pa);M为弯曲力矩,单位为牛顿·米(N·m);h为材料的高度,单位为米(m);W为折弯力,单位为牛顿(N);t为材料的厚度,单位为米(m)。
4. 折弯角度的计算公式。
在进行Z型钣金折弯时,需要根据设计要求计算折弯的角度。
其计算公式为:θ = (180 α) / 2。
其中,θ为折弯角度,单位为度(°);α为V型模具的夹角,单位为度(°)。
以上就是Z型钣金折弯计算的公式,通过这些公式我们可以计算出在进行Z型钣金折弯时所需的各种参数,以确保折弯后的零件符合设计要求。
z型檩条自重

z型檩条自重一、概述Z型檩条是一种广泛应用于钢结构建筑中的构件,其主要作用是支撑和固定屋面板材。
其轻质高强的特性使得它在许多场合下成为了优秀的选择。
本文将重点讨论Z型檩条的自重及其对结构的影响。
二、基本原理与公式Z型檩条的自重主要取决于其材料密度和截面积。
根据基本的力学原理,我们可以计算出不同型号和长度的Z型檩条在不同环境下的自重。
具体的计算公式如下:G = ρV其中,G为重量(kg),ρ为材料密度(如钢材通常在7.8-7.9g/cm ³),V为体积(对于Z型檩条,可以近似视为截面积乘以长度)。
需要注意的是,这里计算的只是裸檩条的重量,实际应用中还需要考虑各种安装配件和垫片的重量。
三、影响及应对策略1. 自重对建筑设计的影响:Z型檩条的自重会对整个结构的负荷产生影响,需要合理分配到其他构件上以保持整体稳定。
在设计过程中,应充分考虑到这一点,确保结构设计能够承受檩条自重的压力。
2. 如何减轻自重:为了降低建筑的总重量并提高建筑的抗震性能,可以采用更轻质的材料来制造Z型檩条。
此外,优化设计也是减轻自重的重要手段,例如通过改变形状或使用更合理的布局方式等。
3. Z型檩条与其他构件的配合:在实际施工中,需要考虑Z型檩条和其他构件(如梁、板)之间的配合问题。
为了保证整体的稳定性,需要对这些构件进行精确的计算和布置。
四、实践应用与案例分析在具体的工程实践中,我们可以通过优化Z型檩条的形状和材料,以及合理的安装方式,来降低其自重。
例如,采用高强度钢材或者新型轻质材料制造Z型檩条,可以显著降低其重量。
同时,通过精确的计算和设计,可以将檩条与其他构件的负荷进行合理分配,避免因局部负荷过大而影响整体结构的安全性。
以下是一个实际案例:某钢结构厂房的设计中,原设计方案采用的是较重的传统檩条类型。
为了降低建筑的自重,并提高抗震性能,我们建议改用更轻质的Z型檩条。
经过精确计算和设计,新的方案不仅满足了结构安全性的要求,而且显著降低了檩条的自重。
Z 形件弯曲模(切断弯曲复合模)
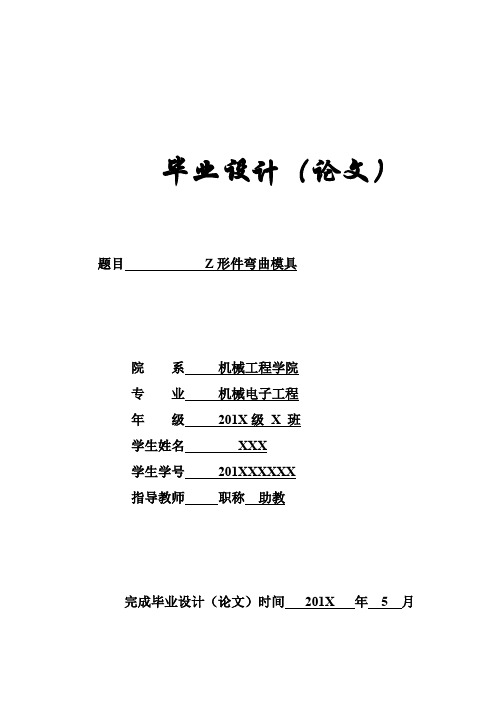
毕业设计(论文)题目Z形件弯曲模具院系机械工程学院专业机械电子工程年级201X级X班学生姓名XXX学生学号201XXXXXX指导教师职称助教完成毕业设计(论文)时间201X年 5 月XXX:Z形件弯曲模目录摘要 (I)Abstract ....................................................................................................................................................... I I 第一章绪论 (1)1.1 我国目前的模具发展水平 (1)1.2 国外模具行业发展水平 (1)1.3 我国模具的发展方向 (1)第二章冲压分析及方案的确定 (3)2.1 冲压工艺分析 (3)2.1.1 弯曲制件 (3)2.1.2 制件材料 (3)2.1.3 模具分析 (3)2.2 确定冲压方案 (4)第三章排样设计及相关计算 (5)3.1毛坯尺寸计算 (5)3.2 排样及定距设计 (5)第四章计算冲裁力确定压力中心 (7)4.1冲裁力的计算 (7)4.2确定压力中心 (8)第五章冲裁工艺计算 (9)5.1 选择双面间隙 (9)5.2 冲裁模刃口尺寸计算原则 (9)5.3落料刃口尺寸及相关计算 (10)第六章各零件结构尺寸设计 (12)6.1 凹模设计及材料工艺选择 (12)6.2 凸模设计及材料工艺选择 (12)6.3 固定垫板设计 (13)6.4卸料部分设计 (14)6.4.1卸料装置 (14)6.4.2 推件和顶件设计 (14)6.4.3 橡胶的选择 (14)6.5 定位部分的设计 (15)6.6 模架、模具和导柱导套 (15)6.6.1 模架 (15)6.6.2 模座 (16)6.6.3 导柱与导套的选用 (17)结论 (19)致谢 (20)参考文献 (21)2017届机械电子工程专业毕业设计(论文)Z形件弯曲模摘要:此次毕业设计参照模具使用手册上的设计方案进行的Z形件弯曲模设计。
z型檩条标准件

z型檩条标准件
Z型檩条是一种广泛使用的结构构件,主要用于连续檩条的搭接和支撑。
以下是Z型檩条标准件的一些主要特点:
1.尺寸和形状:Z型檩条的截面形状为Z型,具有两个弯曲的翼缘和一个直腹板。
其标准尺寸通常由行业规范或标准确定,例如国家标准或地方标准。
2.材料:Z型檩条的标准件通常采用钢材(如Q235、Q345等)或铝合金等材料制作。
不同的材料具有不同的物理和化学特性,适用于不同的应用场景。
3.表面处理:为了提高耐腐蚀性和美观性,Z型檩条标准件通常需要进行表面处理,如镀锌、喷塑、涂装等。
4.连接方式:Z型檩条可以通过自攻螺钉、螺栓、焊接等方式与其他结构件连接。
连接位置需要按照标准要求进行设计和施工,以确保结构的安全性和稳定性。
5.承载能力:Z型檩条标准件的承载能力通常由其材料、截面尺寸、连接方式等因素决定。
在设计时,需要考虑其承载要求,并选择合适的规格和型号。
总之,Z型檩条标准件是一种具有广泛应用的建筑结构构件,其尺寸、材料、表面处理、连接方式和承载能力等方面都有标准化的要求。
在设计、制造和施工时,需要遵循相关规范和标准,以确保结构的安全性和稳定性。
弯曲模具设计实例

2. 凹模圆角半径rd: a. 当t<=2mm时,rd=(3~6)t; b. 当t=2~4mm时,rd=(2~3)t; c . 当t>4mm时,rd=2t。
对于V形弯曲件,凹模底部圆角半径rdˊ: rdˊ=()(rp+t)
第三十页,共45页。
3. 弯曲凹模深度:过小,弯曲件自由部分太长,工 件回弹大且不平直;过深,耗费模具材料。
第二页,共45页。
2.1.1 弯曲变形过程分析 弯曲变形过程:弯曲变形的含义、变形过程三阶段
、弯曲回弹、自由弯曲、矫正弯曲。 弯曲变性特点:网格法、中性层 2.1.2 弯曲件质量(zhìliàng)分析 弯裂、回弹、偏移等
第三页,共45页。
2.1.3 弯曲件的工艺性:指弯曲件的结构形状、尺寸 、精度、材料及技术要求是否符合弯曲加工的工艺要
弯曲前后应变中性层长度不变;(r>t/2)
因此,弯曲件坯料长度应等于弯曲件中性层的展 开长度。
第十五页,共45页。
弯曲中性层位置(wèi zhi)的确定
ρ。= r + xt
L = ρп α/180
ρ。— 中性层曲率半径,r—弯曲内侧半径,
t—料厚,L—弯曲部分展开长度。
a=90 时̊ ,L总=L1+L2+ 1.57(r+xt)
第五页,共45页。
第六页,共45页。
2. 弯曲件直边高度:弯曲件直边高度不宜过小,否 则影响工件的弯曲质量,不能保证零件的形状 (xíngzhuàn)精度。根据经验:
直边高度(经验值)
不满足要求时,可预先开槽,或增加直边高度 (gāodù)成 形后再切除多余部分。
第七页,共45页。
第八页,共45页。
- 1、下载文档前请自行甄别文档内容的完整性,平台不提供额外的编辑、内容补充、找答案等附加服务。
- 2、"仅部分预览"的文档,不可在线预览部分如存在完整性等问题,可反馈申请退款(可完整预览的文档不适用该条件!)。
- 3、如文档侵犯您的权益,请联系客服反馈,我们会尽快为您处理(人工客服工作时间:9:00-18:30)。
Z形件弯曲模设计——冲压模具课程设计说明书
目录
一、冲压工艺分析; (1)
二、冲压方案的确定;.......................1--2
三、主要设计计算;.......................2--4
A、毛胚尺寸的计算;
B、排样及相关计算;
C、冲压力的计算;
D、冲压工序力计算;
E、工作不分尺寸计算;
四、回弹的计算;.......................4--10
五、模具的总体设计; (10)
1、模具类型的选择;
2、工作零件的结构设计;
3、模具总装配图;
4、冲压设备的选定;
5、模具的装配;
一、冲压件工艺分析
零件简图:如下图所示;
生产批量:大批量;
材料:Q235;
材料厚度:1.5mm;
该工件只有切断和弯曲两个工序,材料Q235钢为软材料,在弯曲时应有一定的凸凹模间隙。
工件的尺寸全部为自由公差,可看作IT14级,尺寸精度较低,普通弯曲就能满足要求。
二、冲压方案的确定
该工件包括切断和弯曲两个工序,可以有以下几种方案:
方案一:先切断,后弯曲.采用单工序模生产;
方案二:切断___弯曲复合冲压.采用复合模生产;
方案一模具结构简单,但需要两道工序两副模具,生产效率低,难以满足该工件大批量生产要求;方案二需一副模具,生产效率高,尽管模具结构较方案一复杂,但由于零件几何形状简单,模具制造并不困难.通过对上述方案的分析比较,该工件的冲压生产采用方案二为佳.
三、主要设计计算
A、毛坯尺寸计算
工件弯曲半径r>0.5t,故坯料展开尺寸公式为:
LZ=L直1+ L直2 +L直3 +L弯1+ L弯2
查表3.4.1,当r/t=2.5,k =0.458.
L直1=14-r-t=14-4-1.5=8.5mm,
L直2=40-2t-2r=29mm,
L弯1= α/180(r+kt)=3.14×90(4+0.39×1.5)/180=7.1984mm,
故LZ=8.5+29+8.5+7.1984+7.1984=60.3968mm
B、排样及相关计算
采用直排,且无废料。
坯料尺寸为60.40mm×16mm.查板材标准,选用
C、冲压力的计算
落料力:F落=KLtτ=10920 N tτ=350MPa
弯曲力:F自=0.7KBt2σb/(r+t)=2042.182 N σb=400MPa
F校=Aq=19600 N
顶件力或压料力:FD=0.5 F自=1021.91 N
压力机公称压力:F压压=1.2 F校=23520 N
D、冲压工序力计算
根据冲压工艺总力计算结果,并结合工件高度,初选开式固定台压力机JH21-25.
E、工作部分尺寸计算
=4mm
凸模圆角半径:r
凸
工作相对弯曲半径r/t较小,故凸模圆角半径rT等于工件的弯曲半径。
=6mm
②凹模圆角半径:r
凹
=(3--6)t=6mm.
∵t≤2mm,∴r
凹
凸,凹模间隙:
弯曲模:Z/2=tmax+kt=1.5+0.075+0.05×1.5=1.7mm 切断:Z=0.18mm 凹模深度:
t=1.5mm,凹模L0值: L0=20mm.
横向尺寸及公差:
凹模:(60.40-0.5Δ)
d
δ
+
0=51.90030.00+mm
活动凸模:L
凹=(Lmax-0.75Δ)
d
δ
+
0=39.55030.00+
L 凸=(L
凹
-2z)
p
δ
-=39.55-3.4=36.15
020
.0
-mm
则活动凸模尺寸为36.15+1.5=37.650
020
.0
-mm
凸模尺寸:51.90-37.25-1.7-0.18=11.970
020
.0
-mm
四、回弹的计算
在弯曲的圆弧中,因其相对弯曲半径较大,将产生弯曲角度的回弹和弯曲半径的变化,但是后道工序将会使这些误差消除,所以不需要进行弯曲回弹补偿。
五、模具的总体设计
1、模具类型的选择
由冲压工艺分析可知,采用复合冲压,所以模具类型为切断——弯曲复合模。
定位方式的选择:
导料采用导料销,并采用挡料销定位,以及采用压料装置。
卸料方式的选择:
采用顶件装置。
导向方式的选择:
为了提高模具寿命和工件质量,方便安装调整,该复合模采用后侧导柱的导向方式。
2、工作零件的结构设计
活动凸模:
结合工件并考虑加工,将弯曲凸模设计成活动的。
用M8螺钉固定在凸模托板上,与凸模托板配合按H6/M5,其长度为60mm。
如下图所示:
凸模
由于要先切断在弯曲,故在凸模上嵌入镶块,并采用黏结剂固定。
这样可以节约材料,以免全部采用较好材料。
镶块尺寸为2 5mm。
凸模与上模座采用螺钉固定。
选用M6螺钉。
,与上模按H6/M5配合。
其总长
L=150mm.如下图所示。
凹模
凹模与模座用螺钉固定固定。
安装凹模在模架上的位置时,要依据计算压力中心的数据,将压力中心和模柄中心重合。
其轮廓尺寸如下图所示:
顶件块
由于要先弯曲左侧部分,其采用顶件装置。
故在凹模内装配顶板。
具体尺寸如下图所示:
模架及其他零部件的选用
模具选用后侧导柱标准模架,可承受较大的冲压力。
为了提高模具
寿命和工件质量,方便安装调整,该复合模采用后侧导柱的导向方式。
导柱为32mm×160mm,导套为32mm×105mm×43mm
上模座厚度取45mm,即H上模=45mm;
压块厚度取50mm,即H压块=50mm;
凸模托板厚度取25mm,即H托板=25mm;
下模座厚度取50mm,即H下模=50mm;
模具闭合高度H闭=H上模+H压块+H托板+H下模+H凸-H入=207mm 可见该模具闭合高度小于所选压力机JH21-25的最大装模高度,可以使用。
3、模具总装图
模具工作过程:在冲压前活动凸模在橡皮的作用下与凸模端面齐平。
冲压时,右侧弹簧将坯料压紧。
凸模和活动凸模一起往下,凸模将坯料切断。
继续往下,由于橡皮产生的的弹压力大于顶板下方缓冲器产生的弹顶力,推动顶板下移,使坯料左端弯曲,当顶板接触下模座后,橡皮压缩,则凸模相对于活动凸模下移,将坯料右端弯曲成形,当压块与上模座相碰时,整个工件得以校正。
当上模回程时,顶件块将工件顶出,并手工将工件取走,然后将条料送进,进行下一个工件的生产。
模具装配图如下图所示:
4、冲压设备的选定
通过校核,选择开式固定台压力机JH21-25能满足要求。
其主要参数如下:标称压力:250KN
标称行程:2.8mm
滑块行程:80mm
行程次数:100次/min
最大闭合高度:250mm
封闭高度调节:50mm
滑块中心到机身距离:210mm
工作台尺寸(前后×左右):440mm×700mm
工作台孔尺寸:150mm
模柄孔尺寸:40mm×65mm
电动机功率:2.2kw
5、模具的装配
本模具的装配先凸,凹模为基准件,先装上模,再装下模。
装配应保证间隙均匀。
然后装机试冲,并根据试冲结果做相应的调整。