2017-10-14 磁粉检测工艺修正
《磁粉检测工艺》课件
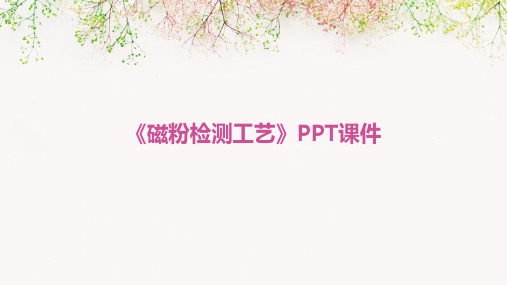
质量等级划分
根据磁粉检测结果,对被检测物体中的缺 陷进行分类和评定,确定其性质、程度和 危害性。
根据缺陷的数量、分布和性质等因素,将 被检测物体的质量等级进行划分,如合格 、不合格、返修等。
质量评估报告
持续改进措施
编制磁粉检测质量评估报告,详细记录检 测过程、结果分析和质量等级划分等内容 ,为后续处理提供依据。
《磁粉检测工艺》PPT课件
目
CONTENCT
录
• 磁粉检测工艺简介 • 磁粉检测工艺流程 • 磁粉检测工艺操作要点 • 磁粉检测工艺质量评估 • 磁粉检测工艺案例分析 • 磁粉检测工艺发展趋势与展望
01
磁粉检测工艺简介
定义与特点
磁粉检测工艺是一种无损检测方法,利用磁性原理 对铁磁性材料进行检测。
磁ቤተ መጻሕፍቲ ባይዱ检测的应用
磁粉检测可以快速、准确地检测出发 动机零件(如曲轴、气缸等)表面和 近表面的裂纹、夹杂物等缺陷,提高 发动机的性能和安全性。
案例三:金属板材检测
金属板材检测的背景
金属板材广泛应用于建筑、制造等领域,其质量和安全性 对整个工程的安全性至关重要。
磁粉检测的应用
磁粉检测可以快速、准确地检测出金属板材表面和近表面 的裂纹、折叠、气孔等缺陷,提高金属板材的质量和安全 性。
当缺陷存在时,磁力线会绕过 缺陷,形成漏磁场,吸附磁粉 形成磁痕,从而显示出缺陷的 存在。
通过观察磁痕的形状、大小和 分布,可以判断缺陷的性质、 位置和尺寸。
应用领域
01
02
03
04
航空航天领域
用于检测飞机、卫星、火箭等 关键部件的表面和近表面缺陷 。
石油化工领域
用于检测管道、压力容器、阀 门等关键设备的表面和近表面 缺陷。
磁粉检测工艺

第6章磁粉检测工艺磁粉检测工序:预处理—磁化—施加磁粉或磁悬液—磁痕的观察与记录—缺陷评级—退磁—后处理6.1 预处理:清除、打磨、分解、封堵、涂敷6.2磁化连续法:适用范围、操作要领、优缺点剩磁法:适用范围、操作要领、优缺点磁化方法:周向磁化:直接通电法、中心导体法、偏置芯棒法、触头(支杆法)、感应电流法、环形件缠绕电缆法纵向磁化:线圈法、磁轭法、永久磁铁法6.3施加磁粉(磁悬液)干法:适用范围、对磁粉的要求、操作要领、优缺点湿法:适用范围、对浓度的要求、操作要领、优缺点6.4磁痕观察与记录磁痕记录方法(6种):照相、贴印、磁粉探伤-橡胶铸型法、录像法、可剥性涂层、临摹法(画草图)6.5 缺陷评级6.6退磁需要退磁的理由:推辞的原理:变向—衰减方法和设备:退磁操作注意事项、固定式退磁机的摆放方向6.7后处理—合格工件的标记—打钢印、刻印(电火花)、电化学腐蚀、挂标签6.8超标缺陷磁痕显示的处理和复验第7章磁痕分析与质量分级7.1 磁痕分析的意义名词解释:磁痕: 磁粉探伤时聚集形成的图象称为磁痕。
不连续性: 材料的均匀状态(致密性)受到破坏称为不连续性。
相关显示:由缺陷产生的漏磁场形成的磁痕显示称为相关显示。
非相关显示:由工件截面突变或材料磁导率差异等产生的漏磁场形成的磁痕显示称为非相关显示。
伪显示:不是漏磁场形成的磁痕显示成为伪显示。
磁痕分析的意义:(1)正确的磁痕分析可以避免误判或漏检,保证产品质量,创造经济效益。
(2)磁痕分析可为产品设计和工艺改进提供较可靠的信息。
(3)对于运行的设备进行定期检验,可监视疲劳裂纹的扩展情况,可避免设备事故和人身事故的发生。
7.2 伪显示:不是漏磁场引起的磁痕伪显示产生的原因:(1)工件表面粗糙滞留磁粉形成磁痕显示。
(2)工件表面有油污或不清洁,粘附磁粉形成磁痕显示。
(3)磁悬液中的纤维、线头粘附磁粉形成磁痕显示。
(4)工件表面的氧化皮、油漆斑点的边缘滞留磁粉形成磁痕显示。
磁粉检测工艺规程
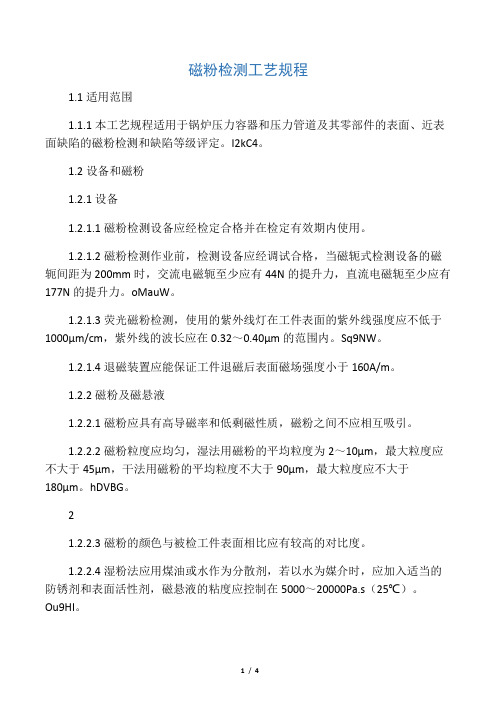
磁粉检测工艺规程1.1适用范围1.1.1本工艺规程适用于锅炉压力容器和压力管道及其零部件的表面、近表面缺陷的磁粉检测和缺陷等级评定。
I2kC4。
1.2设备和磁粉1.2.1设备1.2.1.1磁粉检测设备应经检定合格并在检定有效期内使用。
1.2.1.2磁粉检测作业前,检测设备应经调试合格,当磁轭式检测设备的磁轭间距为200mm时,交流电磁轭至少应有44N的提升力,直流电磁轭至少应有177N的提升力。
oMauW。
1.2.1.3荧光磁粉检测,使用的紫外线灯在工件表面的紫外线强度应不低于1000μm/cm,紫外线的波长应在0.32~0.40μm的范围内。
Sq9NW。
1.2.1.4退磁装置应能保证工件退磁后表面磁场强度小于160A/m。
1.2.2磁粉及磁悬液1.2.2.1磁粉应具有高导磁率和低剩磁性质,磁粉之间不应相互吸引。
1.2.2.2磁粉粒度应均匀,湿法用磁粉的平均粒度为2~10μm,最大粒度应不大于45μm,干法用磁粉的平均粒度不大于90μm,最大粒度应不大于180μm。
hDVBG。
21.2.2.3磁粉的颜色与被检工件表面相比应有较高的对比度。
1.2.2.4湿粉法应用煤油或水作为分散剂,若以水为媒介时,应加入适当的防锈剂和表面活性剂,磁悬液的粘度应控制在5000~20000Pa.s(25℃)。
Ou9HI。
1.2.2.5磁悬液的浓度:荧光磁粉浓度为1~3δ/L,非荧光磁粉浓度为10~20δ/L。
1.2.2.6循环使用的磁悬液应定期进行测定,测定前,应对循环系统进行充分的搅拌,搅拌的时间应不少于30min。
一般情况下,每100ml磁悬液中的非荧光磁粉的沉淀体积应不超过1.2~2.4ml,荧光磁粉的沉淀体积应不超过0.1~0.5ml。
测定前应通过循环系统对磁悬液充分的搅拌,搅拌时间不少于30min。
ejpLu。
1.3表面准备1.3.1被检工件的表面粗糙度Ra不大于12.5μm。
1.3.2被检工件表面不得有氧化皮、焊接飞溅和油脂或其它粘附磁粉的物质。
磁粉检测通用工艺规程
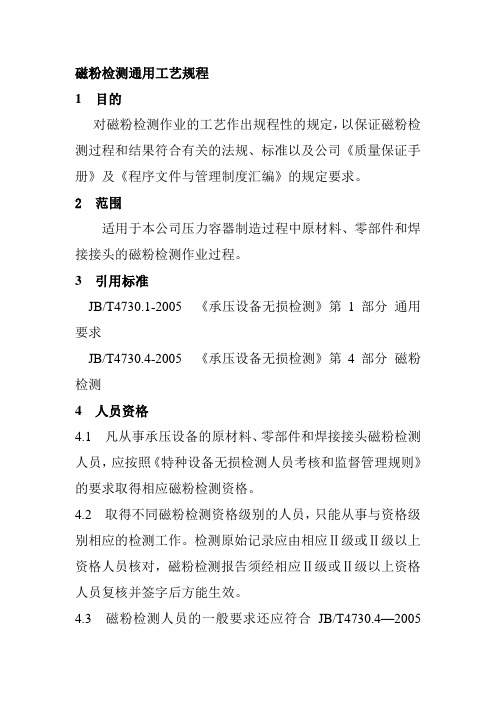
磁粉检测通用工艺规程1 目的对磁粉检测作业的工艺作出规程性的规定,以保证磁粉检测过程和结果符合有关的法规、标准以及公司《质量保证手册》及《程序文件与管理制度汇编》的规定要求。
2 范围适用于本公司压力容器制造过程中原材料、零部件和焊接接头的磁粉检测作业过程。
3 引用标准JB/T4730.1-2005 《承压设备无损检测》第1部分通用要求JB/T4730.4-2005 《承压设备无损检测》第4部分磁粉检测4 人员资格4.1 凡从事承压设备的原材料、零部件和焊接接头磁粉检测人员,应按照《特种设备无损检测人员考核和监督管理规则》的要求取得相应磁粉检测资格。
4.2 取得不同磁粉检测资格级别的人员,只能从事与资格级别相应的检测工作。
检测原始记录应由相应Ⅱ级或Ⅱ级以上资格人员核对,磁粉检测报告须经相应Ⅱ级或Ⅱ级以上资格人员复核并签字后方能生效。
4.3 磁粉检测人员的一般要求还应符合JB/T4730.4—2005中3.1的有关规定。
5检测设备、器材和材料5.1 磁粉、载体和磁悬液5.1.1 磁粉5.1.1.1 磁粉应具有高磁导率、低矫顽力和低剩磁,并应与被检工件表面颜色有较高的对比度。
5.1.1.2 磁粉粒度和性能的其他要求应符合JB/T6063—1992的规定。
5.1.2 湿法应采用水或低粘度的油基载体作为分散介质。
5.1.2.1 若以水为载体时,应加入适当的防锈剂和表面活性剂,必要时添加消泡剂。
5.1.2.2 油基载体的运动粘度在38℃时小于或等于3.0㎜2/S,使用温度下小于或等于5.0㎜2/S,闪点不低于94℃,且无荧光和无异味。
5.1.3 磁悬液—107 —XX压力容器制造规程、作业指导书文件编号TDZZ03007-2014标题磁粉检测通用工艺规程版本号/修改次2014/0页数共 4 页第2 页磁悬液浓度应根据磁粉种类、粒度、施加方法和被检工件表面状态等因素来确定。
5.1.4 对于非荧光磁粉,配制浓度为10~25g/L,其沉淀浓度(含固体量)为1.2~2.4mL/100mL。
磁粉检测的工艺规程
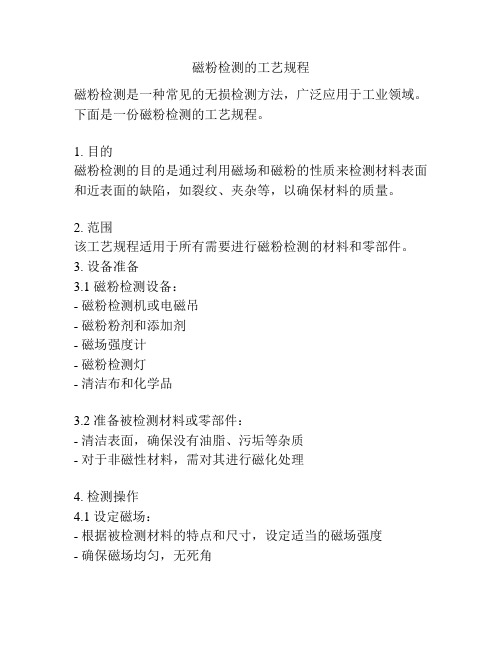
磁粉检测的工艺规程磁粉检测是一种常见的无损检测方法,广泛应用于工业领域。
下面是一份磁粉检测的工艺规程。
1. 目的磁粉检测的目的是通过利用磁场和磁粉的性质来检测材料表面和近表面的缺陷,如裂纹、夹杂等,以确保材料的质量。
2. 范围该工艺规程适用于所有需要进行磁粉检测的材料和零部件。
3. 设备准备3.1 磁粉检测设备:- 磁粉检测机或电磁吊- 磁粉粉剂和添加剂- 磁场强度计- 磁粉检测灯- 清洁布和化学品3.2 准备被检测材料或零部件:- 清洁表面,确保没有油脂、污垢等杂质- 对于非磁性材料,需对其进行磁化处理4. 检测操作4.1 设定磁场:- 根据被检测材料的特点和尺寸,设定适当的磁场强度- 确保磁场均匀,无死角4.2 准备磁粉混合溶液:- 将磁粉粉剂和添加剂按要求混合,制成磁粉混合溶液4.3 涂敷磁粉混合溶液:- 均匀涂敷磁粉混合溶液于被检测材料表面,确保覆盖整个检测区域4.4 磁化:- 使用磁粉检测机或电磁吊对被检测材料进行磁化- 确保磁场方向和磁场强度符合要求4.5 观察和记录:- 使用磁粉检测灯照射被检测材料- 观察磁粉的聚集情况,标记出缺陷位置- 记录缺陷的位置、大小和形状等信息5. 结果评定5.1 根据检测结果,判断缺陷的类型、大小和严重程度5.2 根据相关标准和要求,判定被检材料的合格与否6. 保存和报告6.1 对于合格材料,及时清除磁粉残留,并进行必要的清洁和防腐处理6.2 对于不合格材料,根据要求进行标记或报废处理6.3 保存检测记录,包括磁化参数、磁粉混合溶液配方、检测结果等6.4 编写磁粉检测报告,详细描述检测过程、结果和评定等,并保存备查。
以上是一份磁粉检测的工艺规程,该规程应根据实际情况进行具体调整和执行。
续写:7. 安全措施7.1 操作人员应穿戴适当的个人防护装备,包括手套、防护眼镜和呼吸器等,以保护自身安全。
7.2 磁粉粉剂和添加剂应存放在干燥、通风的地方,远离火源和易燃物。
磁粉检测技术:磁粉检测工艺

三、磁粉检测时机的选择
(2)焊接接头应安排在焊接工序完成之后进行,对于有 延迟裂纹倾向的材料,应至少在焊接完成24h后进行。有再 热裂纹倾向的应在热处理后磁粉检测。对紧固件和锻件应在 最终热处理之后进行。
(3)对滚动轴承等装配件,如在检测后无法完全去掉磁 粉而影响产品质量,应在装配前对工件进行检测。
二、基本操作步骤
预处理(1) 磁化工件和施加磁悬液(2、3)
观察和评定磁痕显示(4、5) 后处理(7去除工件表面煤油及磁粉)
三、磁粉检测时机的选择
(1)在容易产生缺陷的工序之后(如焊接、热处理、机 加工、磨削、锻造、铸造、矫正和加载),在喷漆、喷丸、 发蓝、磷化、氧化、阳极化、电镀或其他表面处理工序之前。 表面处理之后进行机加工,则再次检测。
磁粉检测工艺
与操作
磁粉检测工艺
一、磁粉检测工艺
工艺(Craft) 是劳动者利用生产工具对各种原材料、半成品进行增值 加工或处理,最终使之成为制成品的方法与过程。 制 定工艺的原则是:技术上的先进和经济上的合理。
磁粉检测工艺 是指磁粉检测预处理、磁化工件(选择磁化方法和磁化 规范)、施加磁粉或磁悬液、磁痕观察和记录、缺陷评 级、退磁和后处理七个程序的全过程。
三、磁粉检测时机的选择
操作 operation 焊接、热处理、机加、加载 welding, hest treatment, machining, loading 延迟裂纹材料 Delaying-crack material 喷涂、电镀 painting or coating 腐蚀 Surface temper etch 喷丸 Shot peening 发黑 Black oxidizing 压力实验 Pressure testing 打磨 light finish grinding
磁粉检测工艺规程
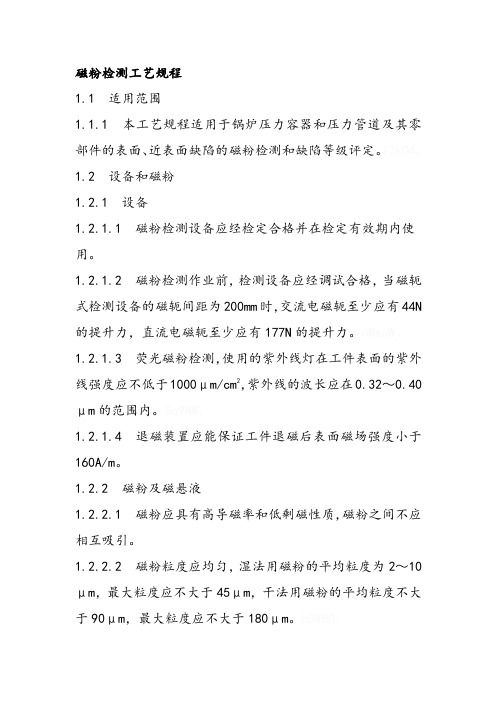
磁粉检测工艺规程1.1 适用范围1.1.1 本工艺规程适用于锅炉压力容器和压力管道及其零部件的表面、近表面缺陷的磁粉检测和缺陷等级评定。
1.2 设备和磁粉1.2.1 设备1.2.1.1 磁粉检测设备应经检定合格并在检定有效期内使用。
1.2.1.2 磁粉检测作业前,检测设备应经调试合格,当磁轭式检测设备的磁轭间距为200mm时,交流电磁轭至少应有44N 的提升力,直流电磁轭至少应有177N的提升力。
1.2.1.3 荧光磁粉检测,使用的紫外线灯在工件表面的紫外线强度应不低于1000μm/cm2,紫外线的波长应在0.32~0.40μm的范围内。
1.2.1.4 退磁装置应能保证工件退磁后表面磁场强度小于160A/m。
1.2.2 磁粉及磁悬液1.2.2.1 磁粉应具有高导磁率和低剩磁性质,磁粉之间不应相互吸引。
1.2.2.2 磁粉粒度应均匀,湿法用磁粉的平均粒度为2~10μm,最大粒度应不大于45μm,干法用磁粉的平均粒度不大于90μm,最大粒度应不大于180μm。
1.2.2.3 磁粉的颜色与被检工件表面相比应有较高的对比度。
1.2.2.4 湿粉法应用煤油或水作为分散剂,若以水为媒介时,应加入适当的防锈剂和表面活性剂,磁悬液的粘度应控制在5000~20000Pa.s(25℃)。
1.2.2.5 磁悬液的浓度:荧光磁粉浓度为1~3δ/L,非荧光磁粉浓度为10~20δ/L。
1.2.2.6 循环使用的磁悬液应定期进行测定,测定前,应对循环系统进行充分的搅拌,搅拌的时间应不少于30min。
一般情况下,每100ml磁悬液中的非荧光磁粉的沉淀体积应不超过 1.2~2.4ml,荧光磁粉的沉淀体积应不超过0.1~0.5ml。
测定前应通过循环系统对磁悬液充分的搅拌,搅拌时间不少于30min。
1.3 表面准备1.3.1 被检工件的表面粗糙度Ra不大于12.5μm。
1.3.2 被检工件表面不得有氧化皮、焊接飞溅和油脂或其它粘附磁粉的物质。
磁粉检测通用工艺作业指导书

Technics Regulation for Magnetic particle Examination作业指导书Operation Guidebook编制Prepared By : 审核Checked By : 批准Approved By :科恩马特殊过程装备(常熟)有限公司KNM SPECIAL PROCESS EQUIPMENT (CHANGSHU) CO.,LTD.磁粉检测通用工艺规程Technics Regulation for Magnetic particle Test1主要内容和适用范围1 Scope1.1 本规程规定了磁粉检测人员资格、所用设备、器材、检测技术和质量分级等。
1.1 This regulation define the qualification of Magnetic particle test person, facility , equipment, examining method and quality grade.1.2本规程按JB/T 4730.4-2005的要求编写。
适用于铁磁性材料的机加工件、焊缝、板材坡口面等表面和近表面缺陷的检测,不适用于非磁性材料及磁性材料与非磁性材料结合部位的检测。
满足GB 150、《压力容器安全技术监察规程》和相关标准的要求。
1.2 This regulation is compile based on JB/T 4730.4-2005. It is suitable for ferro-magnetic material, such as machining workpiece, weld seam, groove face of plate and near surface flaw. The regulation is not suitable for non-magnetic substance and bonded block made with ferro-magnetic material and non-magnetic substance. The regulation satisfied with GB-150, 《Supervision, Regulation on Safety Technology for Pressure vessel》and correlative standard.1.3 本规程适用于非荧光湿磁粉的连续磁化技术。
磁粉检测工艺规程

磁粉检测工艺规程1 主题内容和适用范围1.1 本规程规定了磁粉检测人员资格、所用设备、器材、检测技术和质量分级等。
1.2 本规程依据JB/T4730-2005.4 《承压设备无损检测》编制。
适用于铁磁性材料(磁导率≥1)的机加工件、焊缝、板材坡口面等表面和近表面缺陷的检测。
1.3 本规程适用于荧光湿磁粉的剩磁磁化技术。
1.4 检测工艺卡是本规程的补充。
由II级人员按合同要求及本规程编制,其参数规定的更具体。
2 检测人员2.1 检测人员必须经过培训,取得与其工作相应的资格证书,并负相应的技术责任。
2.2 检测人员每年应检查一次身体,其未经矫正或经矫正的近(距)视力和远(距)视力应不低于5.0(小数记录值为1.0),不得有色盲。
3 检测设备和材料I、II级人员按下列条件和工艺卡要求选用设备、工具和材料。
3.1 磁化设备及校验3.1.1 本工艺规程选定的设备为:CJW-4000Z3.1.2 磁化设备的校验磁粉检测设备的电流表,至少半年校验一次。
当设备进行重要电气修理或大修后,应进行校验。
3.2 磁场指示器磁场指示器的作用与标准试片相同,但它仅是一种粗略的校验。
3.3 磁粉、载体及磁悬液3.3.1 磁粉磁粉应具有高磁导率、低矫顽力和低剩磁,并应与被检工件表面颜色有较高的对比度。
磁粉粒度和性能的其他要求应符合JB/T 6063的规定。
3.3.2 载体湿法应采用水或低粘度油基载体作为分散媒介。
若以水为载体时,应加入适当的防锈剂和表面活性剂,必要时添加消泡剂。
油基载体的运动粘度在38℃时小于或等于3.0 mm2/s,使用温度下小于或等于5.0mm2/s,闪点不低于94℃,且无荧光和无异味。
3.3.3 磁悬液磁悬液浓度应根据磁粉种类、粒度、施加方法和被检工件表面状态等因素来确定。
一般情况下,磁悬液浓度范围应符合表1的规定。
测定前应对磁悬液进行充分的搅拌。
表1 磁悬液浓度磁粉类型配制浓度(g/L)沉淀浓度(含固体量:mL/100mL)非荧光磁粉10~25 1.2~2.4荧光磁粉0.5~3.0 0.1~0.44 被检表面的制备4.1 被检工件表面不得有油脂、铁锈、氧化皮或其它粘附磁粉的物质。
磁粉探伤方法和工艺简介

磁粉探伤方法和工艺简介射阳县德阳电子有限公司一. 剩磁法和连续法1. 剩磁法指先将工件磁化,再将磁粉或磁悬液施加到工件表面以检查工件缺陷的方法 。
适用于经淬火,调质处理等增强强度或硬度的热处理后的高碳钢和合金钢 ,不适用于低碳钢和经退火处理或热变形钢材 ,马氏体不锈钢用剩磁法效果不如连续法 。
剩磁法特别适用于批量小件的探伤,此时生产效率高。
2. 连续法又称外加法,系指在外加磁场的作用下,将磁粉或磁悬液施加到工件上去进行探伤的,先喷洒磁悬液,接着磁化(通电1-3秒),此时仍继续浇 ,每次0.5-1秒,中断磁化后观察缺陷,最后退磁。
连续法适用于所有铁磁性材料 。
二. 直流磁化和交流磁化1 .直流磁化目前已很少采用纯直流电,而采用单相半波或全波,三相半波或全波整流电。
2. 交流磁化般采用工频交流电。
交流磁化时,起作用的是电流的峰值,但一般标示的电流值是有效值。
方法。
目前该法比较流行的工艺是 注磁悬液,停止浇注后再通电数次教科书中推荐优先使用剩磁法 ,实际中多采用连续法。
交流磁化和直流磁化都能检测表面和近表面缺陷,交流磁化对表面缺陷的检测灵敏度高,直流磁化检测表面下的缺陷的能力强一些。
一般说来,电流中包含的脉动成份越大,探测内部缺陷的能力越弱。
直流磁化用于剩磁法时剩磁稳定,交流磁化则剩磁不够稳定加断电相位控制器可解决此问题(采用过零点断电的方法叫断电相位控制,以防止对工件形成退磁作用)。
直流磁化退磁困难,交流磁化退磁容易。
目前一般推荐使用交流磁化,且多采用连续法,此时一般也加断电相位控制。
使用交流连续磁化,设备结构简单,成本低,磁化效果一般都能满足要求。
也有使用交直流混合磁化的,此时,交流磁化在前,直流磁化在后,以利于退磁。
三.磁化方法1.周向磁化。
指给工件直接通电,或者使电流流过贯穿工件中心孔的导体,旨在工件中建立一个环绕工件的并与工件轴垂直的闭合磁场。
周向磁化主要用于发现与工件轴线平行的缺陷。
2 . 纵向磁化。
磁粉检测通用工艺规程
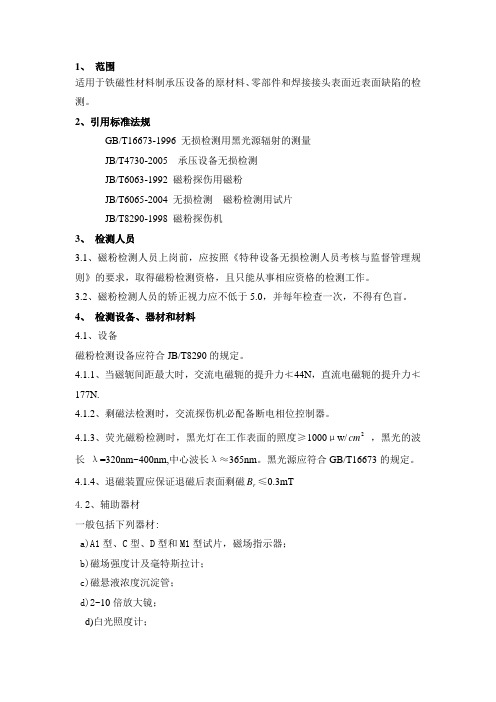
1、范围适用于铁磁性材料制承压设备的原材料、零部件和焊接接头表面近表面缺陷的检测。
2、引用标准法规GB/T16673-1996 无损检测用黑光源辐射的测量JB/T4730-2005 承压设备无损检测JB/T6063-1992 磁粉探伤用磁粉JB/T6065-2004 无损检测磁粉检测用试片JB/T8290-1998 磁粉探伤机3、检测人员3.1、磁粉检测人员上岗前,应按照《特种设备无损检测人员考核与监督管理规则》的要求,取得磁粉检测资格,且只能从事相应资格的检测工作。
3.2、磁粉检测人员的矫正视力应不低于5.0,并每年检查一次,不得有色盲。
4、检测设备、器材和材料4.1、设备磁粉检测设备应符合JB/T8290的规定。
4.1.1、当磁轭间距最大时,交流电磁轭的提升力≮44N,直流电磁轭的提升力≮177N.4.1.2、剩磁法检测时,交流探伤机必配备断电相位控制器。
4.1.3、荧光磁粉检测时,黑光灯在工作表面的照度≥1000μw/2cm,黑光的波长λ=320nm~400nm,中心波长λ≈365nm。
黑光源应符合GB/T16673的规定。
B≤0.3mT4.1.4、退磁装置应保证退磁后表面剩磁r4.2、辅助器材一般包括下列器材:a)A1型、C型、D型和M1型试片,磁场指示器;b)磁场强度计及毫特斯拉计;c)磁悬液浓度沉淀管;d)2~10倍放大镜;d)白光照度计;f)黑光灯;g)黑光辐照计。
4.3、磁粉、载液、磁悬液4.3.1、磁粉应具有高磁导率、低矫顽力和低剩磁,并与工件表面的颜色对比度要较高。
其他要求应符合GB/T6063的规定。
4.3.2、载液为水时,应加入防锈剂、表面活性剂及清洗剂。
载液为油时,其运动粘度在38℃时应小于或等于3.02mm/s,闪点不mm/s, 使用温度小于或等于5.02低于94℃,且无荧光和异味。
4.3.3、磁悬液浓度范围应符合表1的规定。
测定前应充分搅匀。
表1 磁悬液浓度4.4、标准试块4.4.1、一般应选用A1-30/100,检测狭小部位可选用C-15/50。
磁粉检测的工艺规程(doc 10页)

磁粉检测的工艺规程(doc 10页)磁粉检测工艺规程本工艺规程适用于铁磁性材料的承压设备原材料、焊接接头及压力管道焊接接头的表面、近表面缺陷的磁粉检测和评定。
与承压设备有关的支承件和结构件也可参照本部分进行磁粉检测。
2.编制依据JB/T4730-2005 ;《承压设备无损检测》GB150-1998钢制压力容器、GB151-1999 钢制换热器TSG R0004-2009固定式压力容器安全技术规程TSG D0001-2009 压力管道安全技术检测规程-工业管道GB50235-1997 工业金属管道工程施工及验收规范GB50148-1993 工业金属管道工程质量检验3.0一般规定3.1检测人员3.1.1从事磁粉检测的人员必须持有承压设备无损检测人员资格证书,操作人员应具有I级或I级以上检测资格,磁粉检测报告应由具有II级II级以上检测资格者签发。
3.1.2色盲、色弱及矫正视力低于1.0者不得从事磁分检测工作。
3.2检测设备和材料3.2.1检测设备3.2.1.1磁粉检测设备应经检定合格并在检定有效期内使用。
3.2.1.2磁粉检测作业前,检测设备应经调试合格。
当磁轭式检测设备磁轭间距为最大时,交流电磁轭至少应有45N的提升力;直流电磁轭至少应有177N的提升力;交叉磁轭至少应有118N的提升力(磁极与试件表面间隙为0.5mm)3.2.1.3采用剩磁法检测时,交流探伤机应配备断电相位控制器。
3.2.1.4黑光辐照度及波长当采用荧光磁粉检测时,使用黑光灯在工件表面的黑光辐照度应大于或等于1000μW/cm2,黑光的波长约为320nm~400nm,中心波长约365nm 。
黑光源应符合GB/T16673的规定。
3.2.1.5退磁装置应能保证工件退磁后表面剩磁小于或等于0.3mT(240A/m) 。
3.2.1.6磁场强度计、标准试片、磁场指示器、黑光灯等辅助器材应满足磁粉检测的需要。
3.2.2检测材料3.2.2.1磁粉检测材料应有产品合格证或质量证明书,并应符合以下要求:3.2.2.2磁粉应具有高导磁率、低矫顽力和低剩磁,磁粉之间不应相互吸引;3.2.2.3磁粉粒度均匀,颜色与检测工件应有较高的对比度。
(完整版)磁粉探伤工艺规程-2017

磁粉探伤工艺规程编制:年月日审核:年月日批准:年月日1 目的和范围1.1 目的:使产品磁粉探伤作业质量符合质量要求,并处于受控状态。
1.2 范围:本规程适用于检验钢质模锻件及其加工件表面及近表面的裂纹和其它缺陷。
2 岗位任职条件2.1 必须具有高中、技校、中专及以上学历,视力(包括矫正视力)达到1.0以上,无色盲;熟练掌握磁粉探伤基本知识,热爱本职工作。
2.2 必须经过铁道部门无损检测鉴定考核委员会组织的磁粉探伤专门培训,并取得铁道部门无损检测人员考核委员会颁发的Ⅱ级及以上级别的磁粉探伤技术资格证书。
3 工具、量具、工装设备及材料4 环境条件4.1 探伤作业场地应远离翻砂、锻打、电焊、潮湿、粉尘场所,地面须经硬化;室内温度达到10—30℃。
4.2 探伤作业场地应整洁明亮,采用荧光磁粉探伤时,观察磁痕显示处紫外灯的辐照度不得低于1500μW/cm2。
4.3磁粉探伤机所用电源必须与大型机械、动力电源分开。
4.4 探伤作业场地应设有工件存放架或箱,待探、待处理、合格的零件应隔离放置,并设有明显的标识。
5 检验规则5.1新造工件的磁粉探伤应在最终热处理工序或机加工工序之后进行。
最终热处理工序之前的磁粉探伤结果不能作为产品交验的依据。
检修工件的磁粉探伤应在分解抛丸除锈工序之后进行。
5.2工件探伤部位表面经过处理应达到规定清洁度,探伤部位应光滑平整,不得存在油污、尘垢、锈蚀、氧化皮等影响磁化及磁痕识别的物质。
5.3 探伤部位经过修磨或机械加工后,必须进行复探。
5.4探伤后,探伤部位再次经过热处理的工件,热处理后探伤部位必须进行全面复探。
5.5探伤后,探伤部位再次经过机加工的工件加工后探伤部位必须进行全面复探。
6 探伤方法6.1 工件磁粉探伤采用湿法连续法。
悬液应比磁化提前结束,或在施加磁悬液结束后,再进行一至两次磁化。
7 作业程序及标准7.1 开工前的准备7.1.1上岗前要充分休息,上岗应按规定穿戴好劳保防护用品,准备好工具。
磁粉检测工艺与操作

磁粉检测的工艺与操作磁粉检测工艺过程磁粉检测工艺过程主要包括磁粉检测的预处理、工件的磁化、施加磁粉或磁悬液、磁痕的观察与记录、缺陷评定、退磁与后处理的全过程。
工序安排与预处理一、工序安排的一般原则是:(1)磁粉检测一般应在各道加工工序完成以后进行,特别是在容易发生缺陷的加工工序(如冷作变形、焊接、磨削、矫正和加载试验等)后进行,必要时也可安排在工序间进行检测。
(2)由于电镀层、涂漆层、表面发蓝、喷丸等表面处理工艺会给检测缺陷显示带来困难,一般应在这些工序之前进行磁粉检测。
如果镀层可能产生缺陷,则应在电镀工艺前后都进行检测,以便明确缺陷产生的时机与环境。
(3)对于产生延迟裂纹倾向的材料,磁粉检测应安排在焊接完成24小时后进行。
(4)对于装配件,如在检测后无法完全去掉磁粉而影响检测的质量时,应在装配前进行磁粉检测。
(5)紧固件和锻件在最终热处理后进行。
金属表面发黑(发蓝)的目的是为了防止钢铁工件的腐蚀生锈、增加零件表面的美观。
二、被检工件的预处理(1)工件表面的清理清除工件表面的油污、铁锈、氧化皮、毛刺、焊接飞溅物等杂质。
(2)打磨通电部位的非导电层和毛刺通电部位存在非导电层(如漆层及磷化层等)及毛刺会隔断磁化电流,还容易在通电时产生电弧烧伤工件。
(3)分解组合装配件由于装配件一般形状和结构复杂,磁化和退磁都困难,分解后探伤操作容易进行。
(4)若工件有盲孔和内腔,磁悬液流进后难以清洗者,探伤前应将孔洞用非研磨性材料封堵上。
应注意,检验使用过的工件时,小心封堵物掩盖住疲劳裂纹。
(5)如果磁痕与工件表面颜色对比度小,或工件表面粗糙影响磁痕显示时,可在探伤前先给工件表面涂敷一层反差增强剂。
在役压力容器由于长期使用,表面受到氧化、腐蚀,降低了表面光洁度、平整度,工件表面上油污、损伤及不平整等都对检测灵敏度产生影响。
由于表面不平整使磁探检测时,磁极与工件的实际接触面减小,穿过的磁力线数量降低,影响了磁场的正常分布。
压力容器磁粉检测通用工艺规程

压力容器磁粉检测通用工艺规程1、总则1.1、本规程规定了铁磁性材料制承压设备的原材料、零部件和焊接接头表面、近表面缺陷的磁粉检测方法。
1.2、本规程适用于本企业铁磁性材料制压力容器的磁粉检测工作。
2、.引用标准GB 11533 标准对数视力表GB12604.5 无损检测术语磁粉检测GB/T5097 无损检测渗透检测和磁粉检测观察条件GB/T16673 无损检测用黑光源(UV-A)辐射的测量JB/T6063 无损检测磁粉检测用材料技术条件JB/T6065 无损检测磁粉检测用试片JB/T6066 无损检测磁粉检测用环形试块JB/T8290 磁粉探伤机NB/T47013.1 承压设备无损检测第1部分:通用要求《容规》3、一般要求3.1、磁粉检测人员3.1.1、从事磁粉检测的人员应满足NB/T47013.1的有关规定。
3.1.2 磁粉检测人员的未经矫正或经矫正的近(小数)视力和远(距)视力应不低于5.0,测试方法应符合GB 11533的规定;并一年检查一次,不得有色盲。
3.1.3 磁粉检测程序磁粉检测程序如下:a)预处理;b)磁化;c)施加磁粉或磁悬液;d)磁痕的观察与记录;e)缺陷评级;f)退磁;g)后处理。
3.2、设备要求3.2.1、磁粉检测设备应符合JB/T8290标准的要求。
3.2.2、当使用磁轭最大间距时,交流电磁轭至少应有45N的提升力,交叉磁轭至少应有118N的提升力。
3.3、磁粉、载体及磁悬液3.3.1、磁粉应具有高磁导率、低矫顽力和低剩磁,并应与被检工件表面颜色有较高的对比度。
磁粉粒度和性能的其他要求应符合JB/T6063的规定。
3.3.2、湿法采用水或低粘度油基载体作为分散媒介。
若以水为载体时,应加入适当的防锈剂和表面活性剂,必要时添加消泡剂。
油基载体的运动粘度在38℃时小于或等于3.0mm2/s,使用温度下小于或等于5.0mm2/s,闪点不低于94℃,且无荧光和无异味。
3.3.3、磁悬液浓度应根据磁粉种类、粒度、施加方法和被检工件表面状态等因素来确定。
特种设备磁粉检测工艺卡修改1

淮北特种设备监督检验中心
磁粉检测工艺卡
工件名称储气罐检验材料牌号规格尺寸
热处理状态检测部位焊缝及热影响区被检表面要求清除并打磨焊缝及
热影响区
检测时机检测设备磁粉探伤机标准试片A1-30/100
检测方法非荧光、湿式连续法光线及检测环境被检表面光照度
大于或等于
1000lx
缺陷记录方式临摹草图
磁化方法磁轭法电流种类
磁化规范
AC提升力
大于等于45N
磁粉、载夜及磁
悬液配制浓度
黑磁膏
水悬液
10~25g/l
磁悬液
施加方法
磁化时喷洒磁悬液检测方法标准JB/T4730.4-2005 质量验收等级级
磁粉检测质量评级要求1、不允许存在任何裂纹
2、不允许存在任何线性缺陷磁痕
3、圆形缺陷磁痕(评定尺寸为35mm×100mm), 长径d≤1.5 mm,且在评定框内不大于1个
附加说明1、焊缝用可变角度交流磁轭法,在垂直和平行焊缝的两个方向磁化。
磁极间距L≥75mm,保证有
效磁化区重叠,在磁化时施加磁悬液
2、磁化规范最终以A1-30/100标准试片上磁痕显示确定
编制审核审批
年月日年月日年月日
淮北特种设备监督检验中心磁粉检测工艺卡附图。
磁粉检测工艺规程
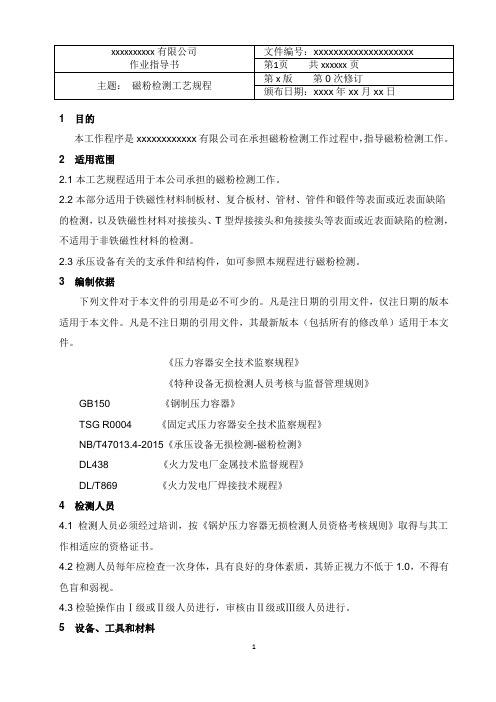
1 目的本工作程序是xxxxxxxxxxxx有限公司在承担磁粉检测工作过程中,指导磁粉检测工作。
2 适用范围2.1本工艺规程适用于本公司承担的磁粉检测工作。
2.2本部分适用于铁磁性材料制板材、复合板材、管材、管件和锻件等表面或近表面缺陷的检测,以及铁磁性材料对接接头、T型焊接接头和角接接头等表面或近表面缺陷的检测,不适用于非铁磁性材料的检测。
2.3承压设备有关的支承件和结构件,如可参照本规程进行磁粉检测。
3 编制依据下列文件对于本文件的引用是必不可少的。
凡是注日期的引用文件,仅注日期的版本适用于本文件。
凡是不注日期的引用文件,其最新版本(包括所有的修改单)适用于本文件。
《压力容器安全技术监察规程》《特种设备无损检测人员考核与监督管理规则》GB150 《钢制压力容器》TSG R0004 《固定式压力容器安全技术监察规程》NB/T47013.4-2015《承压设备无损检测-磁粉检测》DL438 《火力发电厂金属技术监督规程》DL/T869 《火力发电厂焊接技术规程》4 检测人员4.1 检测人员必须经过培训,按《锅炉压力容器无损检测人员资格考核规则》取得与其工作相适应的资格证书。
4.2检测人员每年应检查一次身体,具有良好的身体素质,其矫正视力不低于1.0,不得有色盲和弱视。
4.3检验操作由Ⅰ级或Ⅱ级人员进行,审核由Ⅱ级或Ⅲ级人员进行。
5 设备、工具和材料5.1 磁化设备5.1.1磁化设备见表5.1表5.15.1.2 提升力当使用磁轭最大间距时,交流电磁轭至少应有45N的提升力;直流电(包括整流电)磁轭或永磁轭至少应有177N的提升力;交叉磁轭至少应有118N的提升力(磁极与试件表面间隙为小于等于0.5mm)。
5.1.3磁化设备的选择5.1.3.1对于表面开口型缺陷宜选用能提供交流电的磁化设备。
5.1.3.2对于近表面缺陷及埋藏缺陷,宜选用能提供直流电的磁化设备。
5.2辅助器材5.2.1辅助器材a)A型、C型、标准试块和磁场指示器;b)磁悬液浓度沉淀管;c)2倍~10倍放大镜;d)光照度计:光照度计用于测量被检工件表面的可见光照度。
- 1、下载文档前请自行甄别文档内容的完整性,平台不提供额外的编辑、内容补充、找答案等附加服务。
- 2、"仅部分预览"的文档,不可在线预览部分如存在完整性等问题,可反馈申请退款(可完整预览的文档不适用该条件!)。
- 3、如文档侵犯您的权益,请联系客服反馈,我们会尽快为您处理(人工客服工作时间:9:00-18:30)。
一、检测对象
如图1所示,现有长为2000米的在用压力管道,规格φ57×5mm,材质20g,表面有较厚的油漆防腐层(0.2mm),定期检验中,要求对外表面对接环焊缝进行100%磁粉检测,检测标准为NB/T47013.4-2015,质量要求为I级合格。
二、检测技术要求
采用直接通电和绕电缆法磁化,非荧光磁粉水载液,连续法,交流电,检测该焊缝。
三、现有如下检测设备与器材
1、CYE-3交叉磁轭磁粉探伤仪
2、CDD-1000交流磁粉探伤仪(配Φ20长约3m软电缆、触头1付、夹钳1付)。
3、Φ20×1000mm铜棒
4、白光照度计
5、磁粉、磁悬液(水载液)
6、A1-30/100、A1-15/100、C-8/50、C-15/50型试片
7、磁粉检测其它辅助器材
四、工艺修正要求
请审核实际操作步骤及过程,对于错误的地方用下划线方式划出,在其右边“修改”栏中填写正确内容;如认为原填写内容正确,则不作任何修改,只需在其右边“修改”栏中“√”。
图1 在用压力管道
检测工艺及修正。