有关模具方面的技术要求
模具的技术要求

装配过程中零件不允许磕、碰、划伤和锈蚀。
螺钉、螺栓和螺母紧固时,严禁打击或使用不合适的旋具和扳手。紧固后螺钉槽、螺母和螺钉、螺栓头部不得损坏。
规定拧紧力矩要求的紧固件,必须采用力矩扳手,并按规定的拧紧力矩紧固。
同一零件用多件螺钉(螺栓)紧固时,各螺钉(螺栓)需交叉、对称、逐步、均匀拧紧。
补焊前必须将缺陷彻底清除,坡口面应修的平整圆滑,不得有尖角存在。
根据铸钢件缺陷情况,对补焊区缺陷可采用铲挖、磨削,炭弧气刨、气割或机械加工等方法清除。
补焊区及坡口周围20mm以内的粘砂、油、水、锈等脏物必须彻底清理。
在补焊的全过程中,铸钢件预热区的温度不得低于350°C。
在条件允许的情况下,尽可能在水平位置施焊。
补焊时,焊条不应做过大的横向摆动。
铸钢件表面堆焊接时,焊道间的重叠量不得小于焊道宽度的1/3。
10.锻件要求:
每个钢锭的水口、冒口应有足够的切除量,一以保证锻件无缩孔和严重的偏折。
锻件应在有足够能力的锻压机上锻造成形,以保证锻件内部充分锻透。
锻件不允许有肉眼可见的裂纹、折叠和其他影响使用的外观缺陷。局部缺陷可以清除,但清理深度不得超过加工余量的75%,锻件非加工表面上的缺陷应清理干净并圆滑过渡。
轴承外圈与开式轴承座及轴承盖的半圆孔不准有卡住现象。
轴承外圈与开式轴承座及轴承盖的半圆孔应接触良好,用涂色检查时,与轴承座在对称于中心线120°、与轴承盖在对称于中心线90°的范围内应均匀接触。在上述范围内用塞尺检查时,0.03mm的塞尺不得塞入外圈宽度的1/3。
轴承外圈装配后与定位端轴承盖端面应接触均匀。
模具技术要求
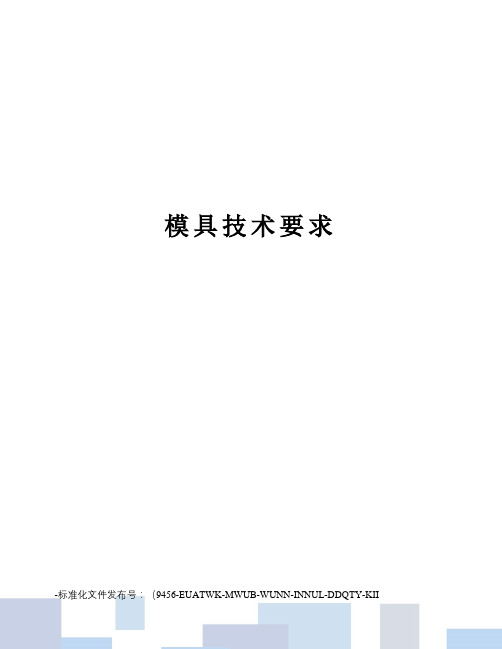
模具技术要求-标准化文件发布号:(9456-EUATWK-MWUB-WUNN-INNUL-DDQTY-KII模具技术要求一.模具材料及热处理要求1.拉延、成形类模具外板件拉延序凸模、凹模及压边圈使用GGG70L铸铁,淬火硬度HRC50-55;内板件凸模、凹摸及压边圈使用MoCr铸铁,淬火硬度HRC50-55。
特殊情况下须渗氮或TD处理(模具图纸会签时确认)。
变形剧烈及高强度钢板(抗拉强度≥350MPa)的制件应采用整体镶Cr12MoV;淬火硬度要达到HRC58—62。
基体采用HT300。
采用键槽与螺栓链接。
GGG70L铸件厂:天津虹岗或长城精工或经甲方认可的同等铸造品质铸造厂。
2.冲裁类模具普通板料零件料厚小于或等于1.2mm的刃口镶块可采用空冷钢(7CrSiMnMoV 或ICD-5),淬火硬度HRC55-60;料厚大于1.2mm的采用Cr12MoV材料,淬火硬度为HRC58~62。
料厚大于等于1.4mm的镶块采用波浪刃口。
高强度板的制件采用Cr12MoV材料,淬火硬度为HRC58~62。
所有凹模镶块、废料刀均采用背托,凹模采用镶块结构,凸模可采用整体结构。
模具基体采用HT300。
3.翻边、整形类模具中大型模具凹模镶块原则上应采用侧面固定式以便于调整;小型模具可采用整体式结构,料厚大于1.4mm的凹模采用镶块式。
零件料厚小于或等于1.2mm,材料可选用MoCr/7CrSiMnMoV;零件料厚大于1.2mm 的采用Cr12MoV或与之相当的材料(应取得甲方工艺认可,具体以会签为准)。
普通板料的制件凸模可采用合金铸铁,表面淬火硬度不低于HRC50;高强度板的制件采用Cr12MoV材料,淬火硬度为HRC58-62;如采用分体或镶块式基座(底板)可采用HT300的材料。
对于部分易拉毛部位,必要时需进行TD处理。
4.压料(退料)顶出器可采用铸造结构,但应根据其强度要求,决定用铸铁或球铁或铸钢材料(工艺会签时,甲方根据具体结构决定)。
模具技术要求
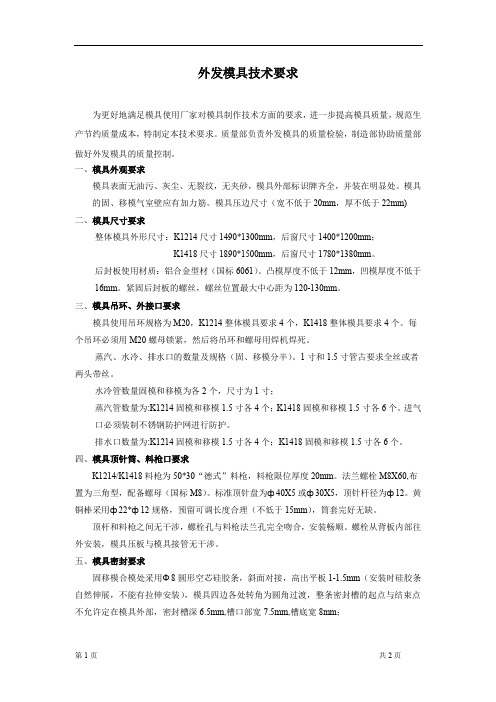
外发模具技术要求为更好地满足模具使用厂家对模具制作技术方面的要求,进一步提高模具质量,规范生产节约质量成本,特制定本技术要求。
质量部负责外发模具的质量检验,制造部协助质量部做好外发模具的质量控制。
一、模具外观要求模具表面无油污、灰尘、无裂纹,无夹砂,模具外部标识牌齐全,并装在明显处。
模具的固、移模气室壁应有加力筋。
模具压边尺寸(宽不低于20mm,厚不低于22mm) 二、模具尺寸要求整体模具外形尺寸:K1214尺寸1490*1300mm,后窗尺寸1400*1200mm;K1418尺寸1890*1500mm,后窗尺寸1780*1380mm。
后封板使用材质:铝合金型材(国标6061)。
凸模厚度不低于12mm,凹模厚度不低于16mm。
紧固后封板的螺丝,螺丝位置最大中心距为120-130mm。
三、模具吊环、外接口要求模具使用吊环规格为M20,K1214整体模具要求4个,K1418整体模具要求4个。
每个吊环必须用M20螺母锁紧,然后将吊环和螺母用焊机焊死。
蒸汽、水冷、排水口的数量及规格(固、移模分半)。
1寸和1.5寸管古要求全丝或者两头带丝。
水冷管数量固模和移模为各2个,尺寸为1寸;蒸汽管数量为:K1214固模和移模1.5寸各4个;K1418固模和移模1.5寸各6个。
进气口必须装制不锈钢防护网进行防护。
排水口数量为:K1214固模和移模1.5寸各4个;K1418固模和移模1.5寸各6个。
四、模具顶针筒、料枪口要求K1214/K1418料枪为50*30“德式”料枪,料枪限位厚度20mm。
法兰螺栓M8X60,布置为三角型,配备螺母(国标M8)。
标准顶针盘为ф40X5或ф30X5,顶针杆径为ф12。
黄铜棒采用ф22*ф12规格,预留可调长度合理(不低于15mm),筒套完好无缺。
顶杆和料枪之间无干涉,螺栓孔与料枪法兰孔完全吻合,安装畅顺。
螺栓从背板内部往外安装,模具压板与模具接管无干涉。
五、模具密封要求固移模合模处采用Φ8圆形空芯硅胶条,斜面对接,高出平板1-1.5mm(安装时硅胶条自然伸展,不能有拉伸安装),模具四边各处转角为圆角过渡,整条密封槽的起点与结束点不允许定在模具外部,密封槽深6.5mm,槽口部宽7.5mm,槽底宽8mm;六、模具其他要求1、后档板:K1214模具后挡板数量不少于三处,K1418不少于4处,避让宽度不小于80mm。
模具材料技术要求
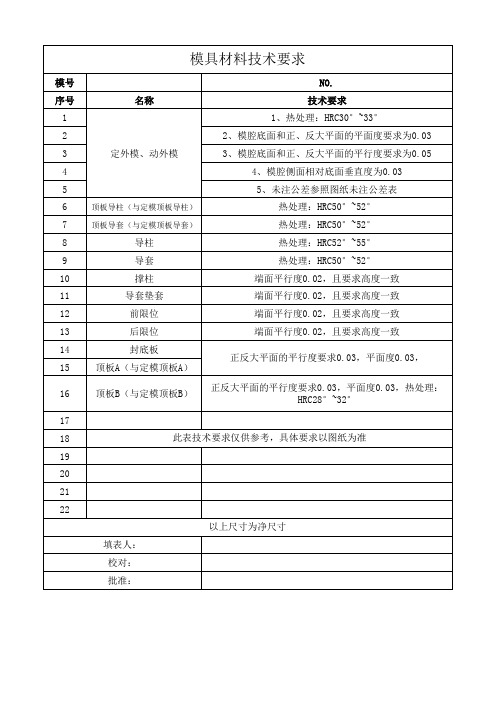
1 2 3 4 5 6 7 8 9 10 11 12 13 14 15
16
17 18 19 20 21 22
模具材料技术要求
名称
定外模、动外模
顶板导柱(与定模顶板导柱) 顶板导套(与定模顶板导套)
导柱 导套 撑柱 导套垫套 前限位 后限位 封底板 顶板A(与定模顶板A)
NO. 技术要求 1、热处理:HRC30°~33° 2、模腔底面和正、反大平面的平面度要求为0.03 3、模腔底面和正、反大平面的平行度要求为0.05 4、模腔侧面相对底面垂直度为0.03 5、未注公差参照图纸未注公差表 热处理:HRC50°~52° 热处理:HRC50°~52° 热处理:HRC52°~55° 热处理:HRC50°~52° 端面平行度0.02,且要求高度一致 端面平行度0.02,且要求高度一致 端面平行度0.02,且要求高度一致 端面平行度0.02,且要求高度一致
正反大平面的平行度要求0.03,平面度0.03,
顶板B(与定模顶板B)
正反大平面的平行度要求0.03,平面度0.03,热处理: HRC28°~32°
此表技术要求仅供参考,具体要求以图纸为准
填表人: 校对: 批准:
பைடு நூலகம்
以上尺寸为净尺寸
模具技术要求
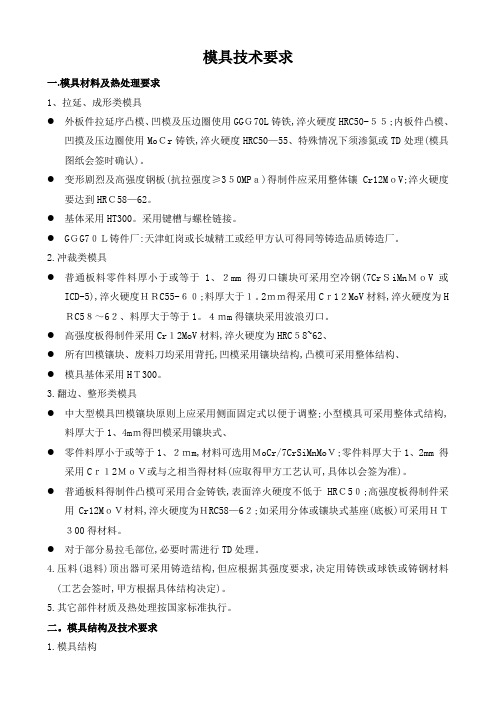
模具技术要求一.模具材料及热处理要求1、拉延、成形类模具●外板件拉延序凸模、凹模及压边圈使用GGG70L铸铁,淬火硬度HRC50-55;内板件凸模、凹摸及压边圈使用MoCr铸铁,淬火硬度HRC50—55、特殊情况下须渗氮或TD处理(模具图纸会签时确认)。
●变形剧烈及高强度钢板(抗拉强度≥350MPa)得制件应采用整体镶Cr12MoV;淬火硬度要达到HRC58—62。
●基体采用HT300。
采用键槽与螺栓链接。
●GGG70L铸件厂:天津虹岗或长城精工或经甲方认可得同等铸造品质铸造厂。
2.冲裁类模具●普通板料零件料厚小于或等于1、2mm得刃口镶块可采用空冷钢(7CrSiMnMoV 或ICD-5),淬火硬度HRC55-60;料厚大于1。
2mm得采用Cr12MoV材料,淬火硬度为H RC58~62、料厚大于等于1。
4mm得镶块采用波浪刃口。
●高强度板得制件采用Cr12MoV材料,淬火硬度为HRC58~62、●所有凹模镶块、废料刀均采用背托,凹模采用镶块结构,凸模可采用整体结构、●模具基体采用HT300。
3.翻边、整形类模具●中大型模具凹模镶块原则上应采用侧面固定式以便于调整;小型模具可采用整体式结构,料厚大于1、4mm得凹模采用镶块式、●零件料厚小于或等于1、2mm,材料可选用MoCr/7CrSiMnMoV;零件料厚大于1、2mm 得采用Cr12MoV或与之相当得材料(应取得甲方工艺认可,具体以会签为准)。
●普通板料得制件凸模可采用合金铸铁,表面淬火硬度不低于HRC50;高强度板得制件采用Cr12MoV材料,淬火硬度为HRC58—62;如采用分体或镶块式基座(底板)可采用HT300得材料。
●对于部分易拉毛部位,必要时需进行TD处理。
4.压料(退料)顶出器可采用铸造结构,但应根据其强度要求,决定用铸铁或球铁或铸钢材料(工艺会签时,甲方根据具体结构决定)。
5.其它部件材质及热处理按国家标准执行。
二。
模具结构及技术要求1.模具结构1、1模具结构采用单动式,原则上按甲方认可得乙方提供得结构式样(模具需满足自动化线要求)。
模具技术要求
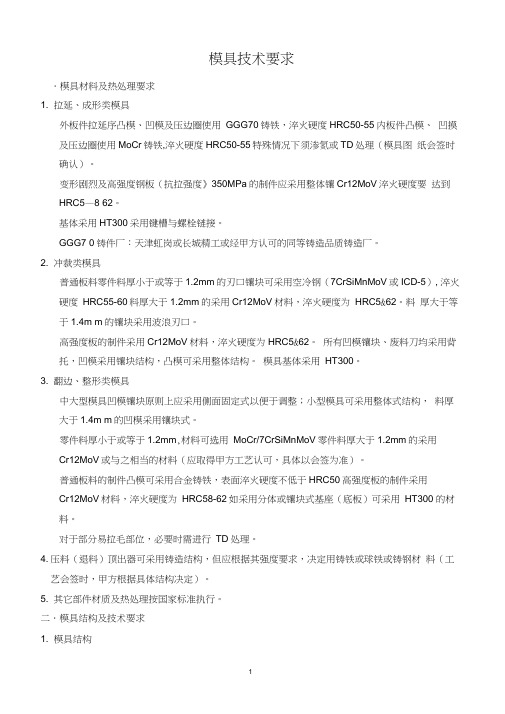
模具技术要求.模具材料及热处理要求1. 拉延、成形类模具外板件拉延序凸模、凹模及压边圈使用GGG70铸铁,淬火硬度HRC50-55内板件凸模、凹摸及压边圈使用MoCr铸铁,淬火硬度HRC50-55特殊情况下须渗氮或TD处理(模具图纸会签时确认)。
变形剧烈及高强度钢板(抗拉强度》350MPa的制件应采用整体镶Cr12MoV淬火硬度要达到HRC5—8 62。
基体采用HT300采用键槽与螺栓链接。
GGG7 0铸件厂:天津虹岗或长城精工或经甲方认可的同等铸造品质铸造厂。
2. 冲裁类模具普通板料零件料厚小于或等于1.2mm的刃口镶块可采用空冷钢(7CrSiMnMoV或ICD-5), 淬火硬度HRC55-60料厚大于1.2mm的采用Cr12MoV材料,淬火硬度为HRC5&62。
料厚大于等于1.4m m的镶块采用波浪刃口。
高强度板的制件采用Cr12MoV材料,淬火硬度为HRC5&62。
所有凹模镶块、废料刀均采用背托,凹模采用镶块结构,凸模可采用整体结构。
模具基体采用HT300。
3. 翻边、整形类模具中大型模具凹模镶块原则上应采用侧面固定式以便于调整;小型模具可采用整体式结构,料厚大于1.4m m的凹模采用镶块式。
零件料厚小于或等于1.2mm,材料可选用MoCr/7CrSiMnMoV零件料厚大于1.2mm的采用Cr12MoV或与之相当的材料(应取得甲方工艺认可,具体以会签为准)。
普通板料的制件凸模可采用合金铸铁,表面淬火硬度不低于HRC50高强度板的制件采用Cr12MoV材料,淬火硬度为HRC58-62如采用分体或镶块式基座(底板)可采用HT300 的材料。
对于部分易拉毛部位,必要时需进行TD处理。
4. 压料(退料)顶出器可采用铸造结构,但应根据其强度要求,决定用铸铁或球铁或铸钢材料(工艺会签时,甲方根据具体结构决定)。
5. 其它部件材质及热处理按国家标准执行。
二.模具结构及技术要求1. 模具结构1.1 模具结构采用单动式,原则上按甲方认可的乙方提供的结构式样(模具需满足自动化线要求)。
压铸模具的技术要求文档

压铸模具的技术要求文档压铸模具是现代工业生产中常用的一种模具,用于制造各种金属制品。
压铸模具的技术要求非常高,对模具的设计、制造、使用等方面都有相应的要求。
本文将从几个方面详细介绍压铸模具的技术要求。
一、设计要求1.模具结构设计要合理,要考虑到产品的结构特点、工艺要求等因素,并保证在模具使用中有较高的稳定性和精度。
2.模腔的设计要充分考虑充型性、冷却性、顶出性等要素,确保产品成型质量稳定。
3.模具的开口方式、进料方式等设计要符合产品要求,并能保证模具的安全操作。
二、材料要求1.模具材料应具有良好的刚性、韧性和耐磨性,能够承受较大的冲击负荷和高温环境,如工具钢、合金钢等。
2.模具的热处理要求良好,能够使模具硬度均匀、稳定,延长使用寿命。
三、制造要求1.模具加工要求高精度、高质量,要保证模具的尺寸精度和表面质量。
2.维修和保养要定期进行,及时处理模具的磨损、损伤等问题,确保模具的正常使用和寿命。
四、使用要求1.模具的操作人员要具备一定的技能和经验,严格按照操作规程进行操作,保证操作的安全和准确性。
2.模具的使用环境要保持清洁、干燥,避免灰尘、水汽等对模具的损坏。
3.模具的顶出装置、冷却装置等要保持良好的工作状态,及时进行维修和更换。
五、质量控制要求1.模具的尺寸精度、表面质量等要进行严格的检测和控制,保证产品的准确性和一致性。
2.定期对模具进行检测和维修,及时发现并解决模具的问题,防止因模具问题引起的产品质量问题。
总结:压铸模具的技术要求非常高,对模具的设计、制造、使用等方面都有严格要求。
只有合理的设计,良好的材料和制造工艺,正确的使用和维护,才能保证模具的高质量和长寿命,从而保证产品的质量和生产效率。
因此,在实际应用中,需要充分重视压铸模具的技术要求,综合考虑各方面因素,确保模具的高效稳定运行。
冲压模具制造检验技术要求
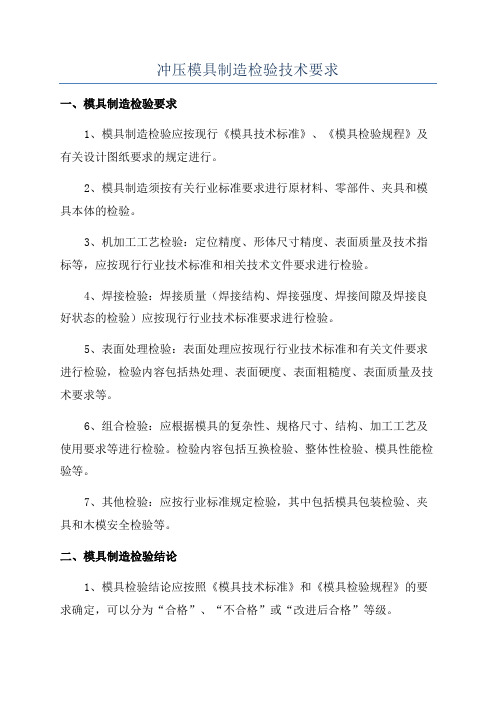
冲压模具制造检验技术要求
一、模具制造检验要求
1、模具制造检验应按现行《模具技术标准》、《模具检验规程》及有关设计图纸要求的规定进行。
2、模具制造须按有关行业标准要求进行原材料、零部件、夹具和模具本体的检验。
3、机加工工艺检验:定位精度、形体尺寸精度、表面质量及技术指标等,应按现行行业技术标准和相关技术文件要求进行检验。
4、焊接检验:焊接质量(焊接结构、焊接强度、焊接间隙及焊接良好状态的检验)应按现行行业技术标准要求进行检验。
5、表面处理检验:表面处理应按现行行业技术标准和有关文件要求进行检验,检验内容包括热处理、表面硬度、表面粗糙度、表面质量及技术要求等。
6、组合检验:应根据模具的复杂性、规格尺寸、结构、加工工艺及使用要求等进行检验。
检验内容包括互换检验、整体性检验、模具性能检验等。
7、其他检验:应按行业标准规定检验,其中包括模具包装检验、夹具和木模安全检验等。
二、模具制造检验结论
1、模具检验结论应按照《模具技术标准》和《模具检验规程》的要求确定,可以分为“合格”、“不合格”或“改进后合格”等级。
发泡模具技术要求

发泡模具技术要求
发泡模具技术要求涵盖多个方面,具体如下:
1. 尺寸精度与表面质量:
模具的尺寸精度必须满足产品设计要求,确保铸件或塑料发泡产品的尺寸稳定性和准确性。
模具工作面的表面粗糙度要控制在指定范围内,如Rz 6.3微米以下,以保证产品质量及脱模效果。
2. 材料性能:
发泡模具应选用导热性良好、耐高温、抗腐蚀和具有一定强度韧性的材料制作,确保模具在发泡过程中热量分布均匀且不易变形或损坏。
对于不同类型的发泡工艺(如聚氨酯发泡、PVC发泡等),模具材料的选择还应考虑其对树脂材料的化学兼容性以及模具的耐用性。
3. 结构设计与加工工艺:
发泡模具的设计需合理规划气孔位置和大小,确保气体均匀分散并形成良好的泡沫结构。
合理设置浇注系统和排气通道,减少气泡缺陷的发生。
模具各部件之间结合严密,配合间隙合适,避免漏浆或溢料,同时做好润滑和防锈处理。
4. 使用与维护:
在生产过程中需要轻拿轻放,防止模具因冲击或重力导致变形。
使用后及时清洁模具内残留物,并使用适当的脱模剂进行保养,
以防结皮和粘模现象。
存储时将模具从模架上取下平放,锁紧模具扣件,防止变形,并定期涂抹润滑剂防止生锈。
5. 模具共用性与标准化:
根据生产需求,尽量设计可共用的模架结构,提高模具利用率和生产效率。
综合上述因素,发泡模具的设计、制造和使用均需严格遵循相关工艺和技术规范,才能确保发泡产品的质量和生产过程的稳定性。
模具技术要求【范本模板】
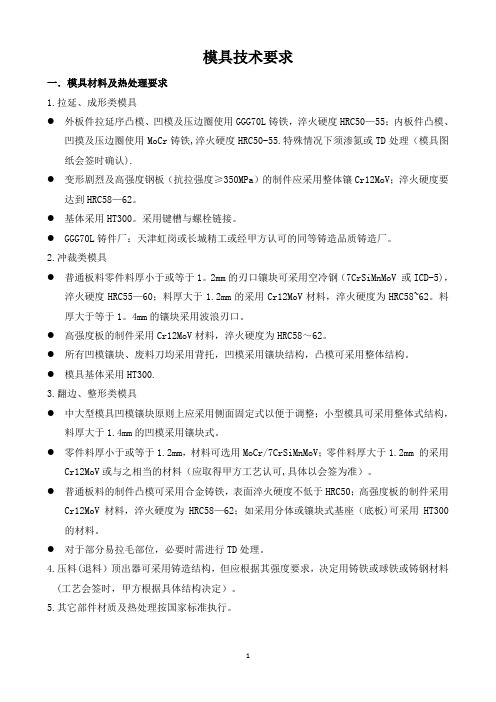
模具技术要求一.模具材料及热处理要求1.拉延、成形类模具●外板件拉延序凸模、凹模及压边圈使用GGG70L铸铁,淬火硬度HRC50—55;内板件凸模、凹摸及压边圈使用MoCr铸铁,淬火硬度HRC50-55.特殊情况下须渗氮或TD处理(模具图纸会签时确认).●变形剧烈及高强度钢板(抗拉强度≥350MPa)的制件应采用整体镶Cr12MoV;淬火硬度要达到HRC58—62。
●基体采用HT300。
采用键槽与螺栓链接。
●GGG70L铸件厂:天津虹岗或长城精工或经甲方认可的同等铸造品质铸造厂。
2.冲裁类模具●普通板料零件料厚小于或等于1。
2mm的刃口镶块可采用空冷钢(7CrSiMnMoV 或ICD-5),淬火硬度HRC55—60;料厚大于1.2mm的采用Cr12MoV材料,淬火硬度为HRC58~62。
料厚大于等于1。
4mm的镶块采用波浪刃口。
●高强度板的制件采用Cr12MoV材料,淬火硬度为HRC58~62。
●所有凹模镶块、废料刀均采用背托,凹模采用镶块结构,凸模可采用整体结构。
●模具基体采用HT300.3.翻边、整形类模具●中大型模具凹模镶块原则上应采用侧面固定式以便于调整;小型模具可采用整体式结构,料厚大于1.4mm的凹模采用镶块式。
●零件料厚小于或等于1.2mm,材料可选用MoCr/7CrSiMnMoV;零件料厚大于1.2mm 的采用Cr12MoV或与之相当的材料(应取得甲方工艺认可,具体以会签为准)。
●普通板料的制件凸模可采用合金铸铁,表面淬火硬度不低于HRC50;高强度板的制件采用Cr12MoV材料,淬火硬度为HRC58—62;如采用分体或镶块式基座(底板)可采用HT300的材料。
●对于部分易拉毛部位,必要时需进行TD处理。
4.压料(退料)顶出器可采用铸造结构,但应根据其强度要求,决定用铸铁或球铁或铸钢材料(工艺会签时,甲方根据具体结构决定)。
5.其它部件材质及热处理按国家标准执行。
二.模具结构及技术要求1.模具结构1。
模具技术要求
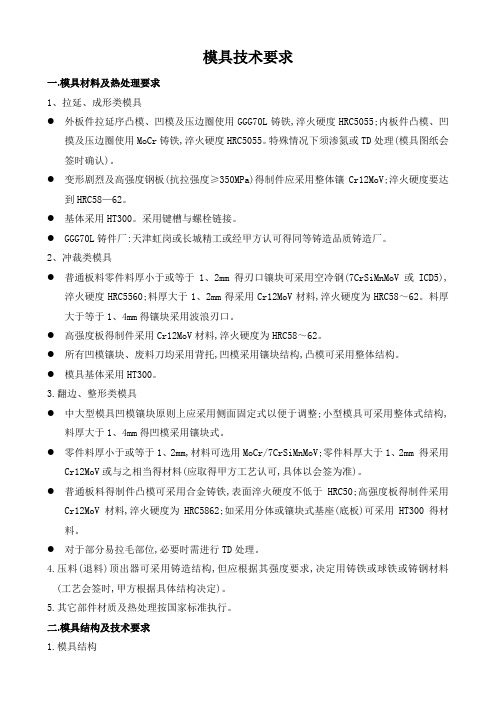
模具技术要求一.模具材料及热处理要求1、拉延、成形类模具●外板件拉延序凸模、凹模及压边圈使用GGG70L铸铁,淬火硬度HRC5055;内板件凸模、凹摸及压边圈使用MoCr铸铁,淬火硬度HRC5055。
特殊情况下须渗氮或TD处理(模具图纸会签时确认)。
●变形剧烈及高强度钢板(抗拉强度≥350MPa)得制件应采用整体镶Cr12MoV;淬火硬度要达到HRC58—62。
●基体采用HT300。
采用键槽与螺栓链接。
●GGG70L铸件厂:天津虹岗或长城精工或经甲方认可得同等铸造品质铸造厂。
2、冲裁类模具●普通板料零件料厚小于或等于1、2mm得刃口镶块可采用空冷钢(7CrSiMnMoV 或ICD5),淬火硬度HRC5560;料厚大于1、2mm得采用Cr12MoV材料,淬火硬度为HRC58~62。
料厚大于等于1、4mm得镶块采用波浪刃口。
●高强度板得制件采用Cr12MoV材料,淬火硬度为HRC58~62。
●所有凹模镶块、废料刀均采用背托,凹模采用镶块结构,凸模可采用整体结构。
●模具基体采用HT300。
3.翻边、整形类模具●中大型模具凹模镶块原则上应采用侧面固定式以便于调整;小型模具可采用整体式结构,料厚大于1、4mm得凹模采用镶块式。
●零件料厚小于或等于1、2mm,材料可选用MoCr/7CrSiMnMoV;零件料厚大于1、2mm 得采用Cr12MoV或与之相当得材料(应取得甲方工艺认可,具体以会签为准)。
●普通板料得制件凸模可采用合金铸铁,表面淬火硬度不低于HRC50;高强度板得制件采用Cr12MoV材料,淬火硬度为HRC5862;如采用分体或镶块式基座(底板)可采用HT300得材料。
●对于部分易拉毛部位,必要时需进行TD处理。
4.压料(退料)顶出器可采用铸造结构,但应根据其强度要求,决定用铸铁或球铁或铸钢材料(工艺会签时,甲方根据具体结构决定)。
5.其它部件材质及热处理按国家标准执行。
二.模具结构及技术要求1.模具结构1、1模具结构采用单动式,原则上按甲方认可得乙方提供得结构式样(模具需满足自动化线要求)。
模具维修工任职要求

模具维修工任职要求一、专业技能1. 具备模具制造、维修的基本理论知识,包括模具结构、材料、制造工艺、维修方法等。
2. 熟练掌握模具加工设备的使用和维护,如铣床、磨床、电火花机等。
3. 了解模具生产过程中的常见问题及解决方法,能够迅速判断并处理模具故障。
4. 具备模具维修后的质量检测能力,确保维修后的模具符合生产要求。
二、工作经验1. 从事模具维修工作2年以上,有丰富的模具维修经验。
2. 熟悉各种模具的结构和制造工艺,能够独立完成模具的维修工作。
3. 对模具生产过程中的常见问题有深入的了解和解决能力。
三、工具设备1. 熟练掌握各种模具维修工具的使用和维护,如螺丝刀、锤子、钳子等。
2. 了解各种模具加工设备的使用和维护,如铣床、磨床、电火花机等。
四、安全意识1. 严格遵守安全操作规程,确保自身和他人安全。
2. 定期检查维修工具和设备的安全性能,确保维修工作的顺利进行。
3. 在维修过程中发现安全隐患及时上报并处理。
五、沟通能力1. 能够与生产人员、技术人员等进行有效的沟通,了解生产需求和问题所在。
2. 在维修过程中遇到问题能够及时向领导或技术人员汇报并寻求解决方案。
3. 能够与其他部门保持良好的合作关系,共同解决生产过程中的问题。
六、学习能力1. 不断学习新的模具制造和维修技术,提高自身的技能水平。
2. 关注行业动态和技术发展趋势,不断更新自己的知识结构。
3. 积极参加各种培训和学习活动,提高自身的综合素质。
七、责任心1. 对待工作认真负责,尽职尽责地完成各项任务。
2. 在维修过程中注重细节和质量要求,确保维修后的模具符合生产要求。
3. 对待问题不推诿、不敷衍,积极寻求解决方案并及时处理。
八、职业道德1. 遵守职业道德规范和公司规章制度,维护公司形象和利益。
2. 在工作中保持诚信、正直的态度,不弄虚作假、不谋取私利。
3. 对待同事友善、尊重,保持良好的团队协作氛围。
模具装配的技术要求
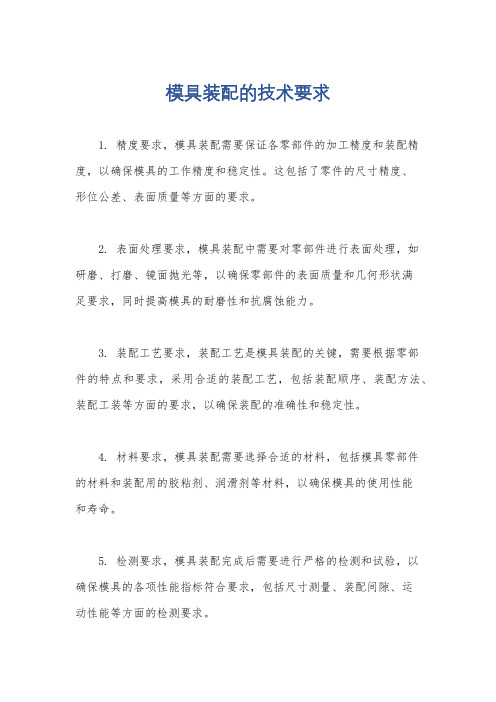
模具装配的技术要求
1. 精度要求,模具装配需要保证各零部件的加工精度和装配精度,以确保模具的工作精度和稳定性。
这包括了零件的尺寸精度、
形位公差、表面质量等方面的要求。
2. 表面处理要求,模具装配中需要对零部件进行表面处理,如
研磨、打磨、镜面抛光等,以确保零部件的表面质量和几何形状满
足要求,同时提高模具的耐磨性和抗腐蚀能力。
3. 装配工艺要求,装配工艺是模具装配的关键,需要根据零部
件的特点和要求,采用合适的装配工艺,包括装配顺序、装配方法、装配工装等方面的要求,以确保装配的准确性和稳定性。
4. 材料要求,模具装配需要选择合适的材料,包括模具零部件
的材料和装配用的胶粘剂、润滑剂等材料,以确保模具的使用性能
和寿命。
5. 检测要求,模具装配完成后需要进行严格的检测和试验,以
确保模具的各项性能指标符合要求,包括尺寸测量、装配间隙、运
动性能等方面的检测要求。
总的来说,模具装配的技术要求包括精度要求、表面处理要求、装配工艺要求、材料要求和检测要求等多个方面,只有严格按照这
些要求进行装配,才能保证模具的质量和性能。
模具通用技术要求
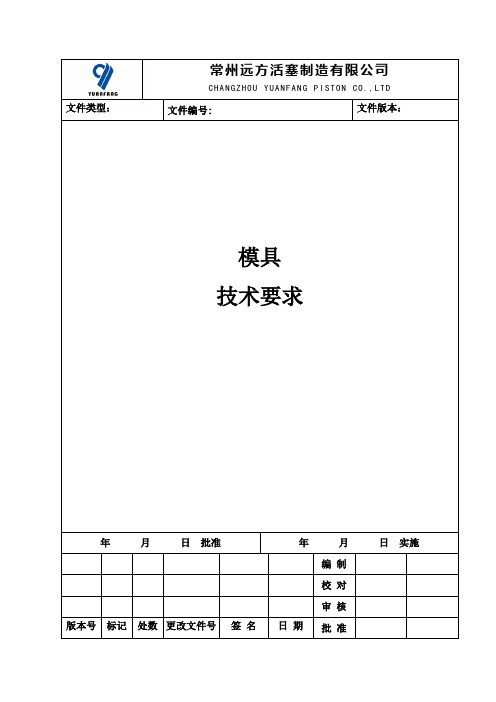
常州远方活塞制造有限公司C H A N G Z H O U Y U A N F A N G P I S T O N C O.,L T D文件类型:文件编号:文件版本:模具技术要求年月日批准年月日实施编制校对审核版本号标记处数更改文件号签名日期批准技术要求1、应用范围此技术要求仅适用于模具。
2、模具制作依据铸造工艺图、图纸或三维图形。
如按图纸自制的三维,需经本公司审核认可。
2.1 模具的几何形状与尺寸应符合3D文件要求。
2.1.1模具形位公差应符合GB/T 1184 形状和位置公差未注公差的规定。
2.1.2 工件形体与装配定位基准的位置极限偏差为±0.2mm。
2.1.3 铸造模具加工表面不允许有任何铸造缺陷。
非加工表面不得有缩孔、裂纹和任何穿透性缺陷,不得有影响结构强度的密集气泡存在。
2.1.4 模具锐角除工艺要求外必须倒钝R1~R2,不得存在飞边、毛刺或划痕,影响起模完整性。
2.1.5 模具工作表面表面粗糙度Ra≤1.6。
2.1.6 底板、芯盒投产时要一次性成型做出,不允许补、贴或焊接。
2.2配合2.2.1芯头与芯座间隙配合,间隙除工艺要求外,一般为1~2mm/单边。
2.2.2 芯盒定位销定位准确,拼合起来不能有错位。
2.2.3 芯盒把手和锁紧装置配齐,把手设置要方便操作,锁紧装置要求锁紧效果好,灵活方便。
2.2.4 活块与芯盒主体配合时应无间隙,且利于活块放置与抽取,并留有起模把手。
2.2.4 射芯模按本公司现有设备配作,要求模样开合运行平稳。
3、模具制作材料模具制作材料应保证模具尺寸的稳定和模具使用寿命。
芯盒、外模、托板材料采用铸铝,型板、芯盒刮砂面覆板材料采用球铁。
4、模具强度要求4.1 外模、芯盒主体壁厚不能小于15mm,受力部位厚度应大于25mm。
在保证壁厚、结构和强度要求的前提下,芯盒和外模重量应尽量减轻。
模具应根据强度要求均匀分布加强筋,以防模具变形。
4.2 型板厚度不得小于20mm,箱把部位应加强,起模震箱部位壁厚不小于40mm或用其他方式加固。
注塑模具技术要求
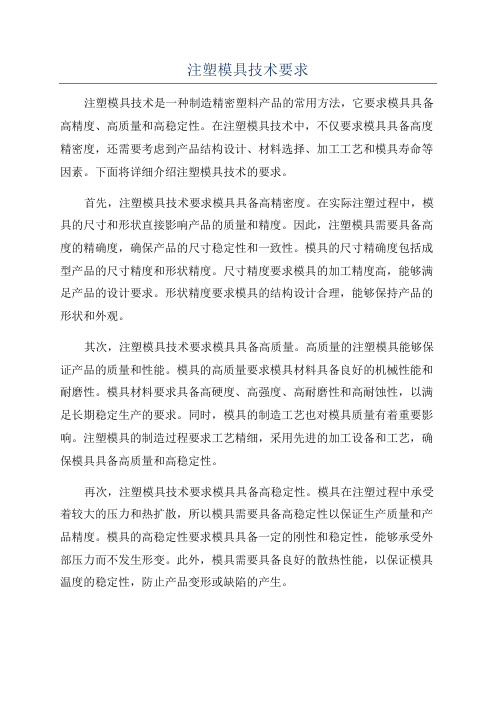
注塑模具技术要求注塑模具技术是一种制造精密塑料产品的常用方法,它要求模具具备高精度、高质量和高稳定性。
在注塑模具技术中,不仅要求模具具备高度精密度,还需要考虑到产品结构设计、材料选择、加工工艺和模具寿命等因素。
下面将详细介绍注塑模具技术的要求。
首先,注塑模具技术要求模具具备高精密度。
在实际注塑过程中,模具的尺寸和形状直接影响产品的质量和精度。
因此,注塑模具需要具备高度的精确度,确保产品的尺寸稳定性和一致性。
模具的尺寸精确度包括成型产品的尺寸精度和形状精度。
尺寸精度要求模具的加工精度高,能够满足产品的设计要求。
形状精度要求模具的结构设计合理,能够保持产品的形状和外观。
其次,注塑模具技术要求模具具备高质量。
高质量的注塑模具能够保证产品的质量和性能。
模具的高质量要求模具材料具备良好的机械性能和耐磨性。
模具材料要求具备高硬度、高强度、高耐磨性和高耐蚀性,以满足长期稳定生产的要求。
同时,模具的制造工艺也对模具质量有着重要影响。
注塑模具的制造过程要求工艺精细,采用先进的加工设备和工艺,确保模具具备高质量和高稳定性。
再次,注塑模具技术要求模具具备高稳定性。
模具在注塑过程中承受着较大的压力和热扩散,所以模具需要具备高稳定性以保证生产质量和产品精度。
模具的高稳定性要求模具具备一定的刚性和稳定性,能够承受外部压力而不发生形变。
此外,模具需要具备良好的散热性能,以保证模具温度的稳定性,防止产品变形或缺陷的产生。
最后,注塑模具技术要求模具具备较长的使用寿命。
模具作为生产工具,一般需要经历较多的注塑周期才能收回成本。
因此,模具需要具备较长的使用寿命以减少更换频率和生产成本。
模具的使用寿命受到多种因素的影响,包括模具材料、模具设计、模具加工工艺和使用条件等。
因此,注塑模具的制造要求模具具备高硬度、高耐磨性和高抗腐蚀性,同时要注意模具的设计合理性和使用条件的控制,以延长模具的使用寿命。
总之,注塑模具技术在市场中非常重要,对产品质量和生产效率有着直接的影响。
冲压模具设计技术要求
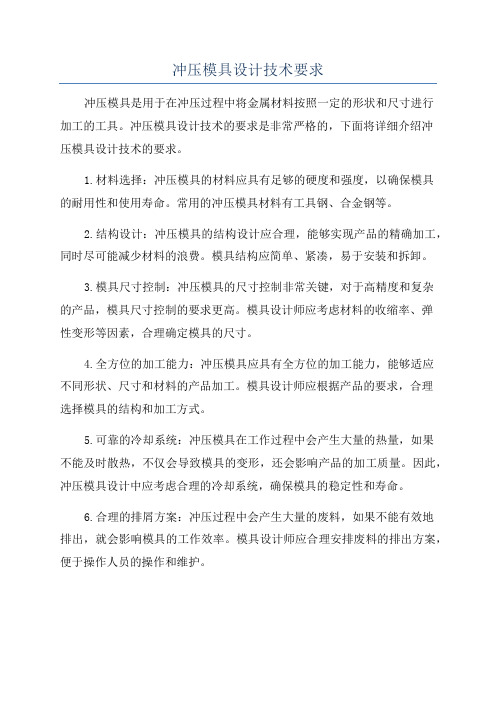
冲压模具设计技术要求冲压模具是用于在冲压过程中将金属材料按照一定的形状和尺寸进行加工的工具。
冲压模具设计技术的要求是非常严格的,下面将详细介绍冲压模具设计技术的要求。
1.材料选择:冲压模具的材料应具有足够的硬度和强度,以确保模具的耐用性和使用寿命。
常用的冲压模具材料有工具钢、合金钢等。
2.结构设计:冲压模具的结构设计应合理,能够实现产品的精确加工,同时尽可能减少材料的浪费。
模具结构应简单、紧凑,易于安装和拆卸。
3.模具尺寸控制:冲压模具的尺寸控制非常关键,对于高精度和复杂的产品,模具尺寸控制的要求更高。
模具设计师应考虑材料的收缩率、弹性变形等因素,合理确定模具的尺寸。
4.全方位的加工能力:冲压模具应具有全方位的加工能力,能够适应不同形状、尺寸和材料的产品加工。
模具设计师应根据产品的要求,合理选择模具的结构和加工方式。
5.可靠的冷却系统:冲压模具在工作过程中会产生大量的热量,如果不能及时散热,不仅会导致模具的变形,还会影响产品的加工质量。
因此,冲压模具设计中应考虑合理的冷却系统,确保模具的稳定性和寿命。
6.合理的排屑方案:冲压过程中会产生大量的废料,如果不能有效地排出,就会影响模具的工作效率。
模具设计师应合理安排废料的排出方案,便于操作人员的操作和维护。
7.安全性和可维护性:冲压模具设计应考虑到操作人员的安全,避免因操作不当导致事故发生。
同时,冲压模具应具备可维护性,便于检修和更换损坏的部件。
8.尽量减少模具的使用成本:在冲压模具设计中,应尽量减少模具的使用成本,包括原材料成本、制造成本和维护成本等。
通过合理的结构设计和材料选择,可以有效降低模具的使用成本。
总之,冲压模具设计技术要求严格,设计师需要综合考虑材料、结构、尺寸控制、加工能力、冷却系统、废料排出、安全性和可维护性等多个因素,以确保模具的质量和使用寿命。
只有具备专业的技术知识和丰富的实践经验,才能设计出高质量、高效率的冲压模具。
模具制造的基本要求
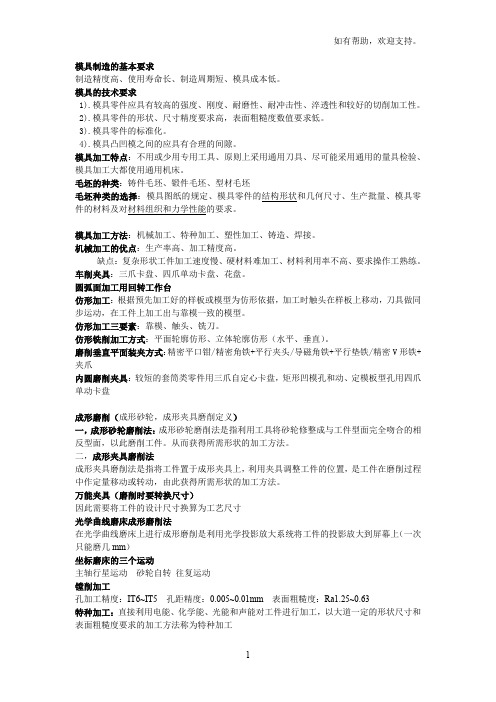
制造精度高、使用寿命长、制造周期短、模具成本低。
模具的技术要求1).模具零件应具有较高的强度、刚度、耐磨性、耐冲击性、淬透性和较好的切削加工性。
2).模具零件的形状、尺寸精度要求高,表面粗糙度数值要求低。
3).模具零件的标准化。
4).模具凸凹模之间的应具有合理的间隙。
模具加工特点:不用或少用专用工具、原则上采用通用刀具、尽可能采用通用的量具检验、模具加工大都使用通用机床。
毛坯的种类:铸件毛坯、锻件毛坯、型材毛坯毛坯种类的选择:模具图纸的规定、模具零件的结构形状和几何尺寸、生产批量、模具零件的材料及对材料组织和力学性能的要求。
模具加工方法:机械加工、特种加工、塑性加工、铸造、焊接。
机械加工的优点:生产率高、加工精度高。
缺点:复杂形状工件加工速度慢、硬材料难加工、材料利用率不高、要求操作工熟练。
车削夹具:三爪卡盘、四爪单动卡盘、花盘。
圆弧面加工用回转工作台仿形加工:根据预先加工好的样板或模型为仿形依据,加工时触头在样板上移动,刀具做同步运动,在工件上加工出与靠模一致的模型。
仿形加工三要素:靠模、触头、铣刀。
仿形铣削加工方式:平面轮廓仿形、立体轮廓仿形(水平、垂直)。
磨削垂直平面装夹方式:精密平口钳/精密角铁+平行夹头/导磁角铁+平行垫铁/精密V形铁+夹爪内圆磨削夹具:较短的套筒类零件用三爪自定心卡盘,矩形凹模孔和动、定模板型孔用四爪单动卡盘成形磨削(成形砂轮,成形夹具磨削定义)一,成形砂轮磨削法:成形砂轮磨削法是指利用工具将砂轮修整成与工件型面完全吻合的相反型面,以此磨削工件。
从而获得所需形状的加工方法。
二,成形夹具磨削法成形夹具磨削法是指将工件置于成形夹具上,利用夹具调整工件的位置,是工件在磨削过程中作定量移动或转动,由此获得所需形状的加工方法。
万能夹具(磨削时要转换尺寸)因此需要将工件的设计尺寸换算为工艺尺寸光学曲线磨床成形磨削法在光学曲线磨床上进行成形磨削是利用光学投影放大系统将工件的投影放大到屏幕上(一次只能磨几mm)坐标磨床的三个运动主轴行星运动砂轮自转往复运动镗削加工孔加工精度:IT6~IT5 孔距精度:0.005~0.01mm 表面粗糙度:Ra1.25~0.63特种加工:直接利用电能、化学能、光能和声能对工件进行加工,以大道一定的形状尺寸和表面粗糙度要求的加工方法称为特种加工{脉冲电源,足够的放电能量,绝缘介质,间隙}工作液循环过滤系统工作液循环过滤系统的作用是使一定压力的工作液流经放电间隙,将电蚀产物排出,并对使用过的工作液进行过滤和净化。
模具设计技术要求
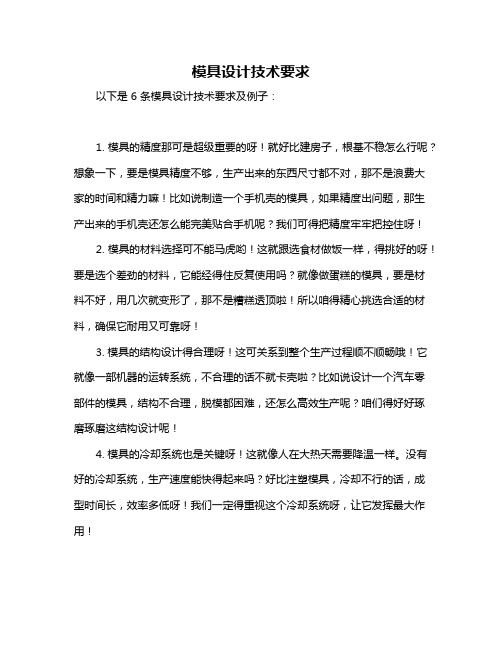
模具设计技术要求
以下是 6 条模具设计技术要求及例子:
1. 模具的精度那可是超级重要的呀!就好比建房子,根基不稳怎么行呢?想象一下,要是模具精度不够,生产出来的东西尺寸都不对,那不是浪费大家的时间和精力嘛!比如说制造一个手机壳的模具,如果精度出问题,那生产出来的手机壳还怎么能完美贴合手机呢?我们可得把精度牢牢把控住呀!
2. 模具的材料选择可不能马虎哟!这就跟选食材做饭一样,得挑好的呀!要是选个差劲的材料,它能经得住反复使用吗?就像做蛋糕的模具,要是材料不好,用几次就变形了,那不是糟糕透顶啦!所以咱得精心挑选合适的材料,确保它耐用又可靠呀!
3. 模具的结构设计得合理呀!这可关系到整个生产过程顺不顺畅哦!它就像一部机器的运转系统,不合理的话不就卡壳啦?比如说设计一个汽车零部件的模具,结构不合理,脱模都困难,还怎么高效生产呢?咱们得好好琢磨琢磨这结构设计呢!
4. 模具的冷却系统也是关键呀!这就像人在大热天需要降温一样。
没有好的冷却系统,生产速度能快得起来吗?好比注塑模具,冷却不行的话,成型时间长,效率多低呀!我们一定得重视这个冷却系统呀,让它发挥最大作用!
5. 模具的维护保养可不能忘啊!这就像爱护自己的宝贝一样。
不保养它,它能一直好用吗?你想啊,一个长期不保养的模具,各种问题都会冒出来,那不是给自己找麻烦嘛!所以呀,要定期给模具做个检查、保养护理啥的,让它一直健健康康的呀!
6. 模具的设计创新多重要呀!这就像给自己的生活加点新花样一样。
一直守着老一套,能有进步吗?看看人家那些厉害的模具设计,多么有创意呀!咱也不能落后呀,要大胆去尝试新的设计思路,说不定就能做出让人惊艳的模具呢!
总之,模具设计技术要求可多了去了,每一条都得认真对待,这样才能做出好的模具,生产出高质量的产品呀!。
模具装配的技术要求
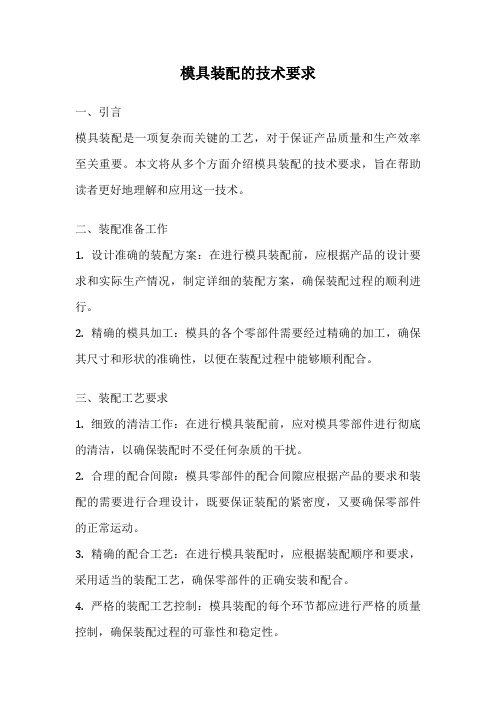
模具装配的技术要求一、引言模具装配是一项复杂而关键的工艺,对于保证产品质量和生产效率至关重要。
本文将从多个方面介绍模具装配的技术要求,旨在帮助读者更好地理解和应用这一技术。
二、装配准备工作1. 设计准确的装配方案:在进行模具装配前,应根据产品的设计要求和实际生产情况,制定详细的装配方案,确保装配过程的顺利进行。
2. 精确的模具加工:模具的各个零部件需要经过精确的加工,确保其尺寸和形状的准确性,以便在装配过程中能够顺利配合。
三、装配工艺要求1. 细致的清洁工作:在进行模具装配前,应对模具零部件进行彻底的清洁,以确保装配时不受任何杂质的干扰。
2. 合理的配合间隙:模具零部件的配合间隙应根据产品的要求和装配的需要进行合理设计,既要保证装配的紧密度,又要确保零部件的正常运动。
3. 精确的配合工艺:在进行模具装配时,应根据装配顺序和要求,采用适当的装配工艺,确保零部件的正确安装和配合。
4. 严格的装配工艺控制:模具装配的每个环节都应进行严格的质量控制,确保装配过程的可靠性和稳定性。
四、装配质量要求1. 合格的装配工人:模具装配需要经验丰富的工人进行操作,他们应具备良好的装配技能和对装配质量的严格要求。
2. 严谨的装配检查:在模具装配完成后,应进行全面、细致的装配检查,确保装配的质量符合设计要求。
3. 高效的故障排除:如果在装配过程中发现问题,应及时进行故障排除,并采取相应的措施解决问题,确保装配质量的稳定性和可靠性。
五、模具装配的优化与改进1. 持续学习和改进:模具装配技术不断发展,为了适应市场的需求和提高生产效率,装配人员应不断学习新的装配技术和方法,并及时进行改进和优化。
2. 创新思维和团队合作:在模具装配过程中,应鼓励装配人员发挥创新思维,积极思考和解决问题,并加强团队合作,提高装配效率和质量。
六、结论模具装配是一项关键的工艺,对于产品质量和生产效率的提高起着重要作用。
通过遵循装配准备工作、装配工艺要求和装配质量要求等技术要求,可以提高模具装配的效率和质量,从而为企业的发展带来更多的机会和挑战。
- 1、下载文档前请自行甄别文档内容的完整性,平台不提供额外的编辑、内容补充、找答案等附加服务。
- 2、"仅部分预览"的文档,不可在线预览部分如存在完整性等问题,可反馈申请退款(可完整预览的文档不适用该条件!)。
- 3、如文档侵犯您的权益,请联系客服反馈,我们会尽快为您处理(人工客服工作时间:9:00-18:30)。
9.Mold release agents are not allowed.
10.Break all sharp edges and corners to maximum 0.2mm radius.
Functionally important dimensions indicated by ◆
4.Material: PS-HI. up to 0% regrind allowed.See material table for more specifications.
5.Draft per 3d solid unless otherwise specified
+ dimensioning increases with indicated draft per side
-dimensioning decreases with indicated draft per side
6.Surfaces to be textured as indicated.
7.Finish on all part surfaces to be spi b3 except as indicated.
2 ,砂铸
3 ,总重: 140公斤
4 ,一般公差:
5 ,未注拔模斜度:小于等于1.5度
6 ,内腔未注圆角半径: 3毫米
7 ,外部未注圆角半径: 2毫米
8 ,标注为mpl 的表面为尺寸测量所用的基面,
9 ,标注为smf的表面为机加留量5毫米的表面,
10 ,标注为“3D source” 的表面将以附加在图纸里的3D模型为检验依据
15、finish:sand blasting
16、external surfaces texture:all external surfaces will have an as-cast surface
17、ctq1...9 to be controlled
1 ,材料:a356铝 - t51 热处理,根据美国ASTM材料标准 b/26m
11 ,铸造裂缝检验采用着色检验(FPI)
12 ,只能由客户决定是否可以对产的铸造裂缝进行补焊 13 ,锐棱倒钝
14,材料批号只能在所指示的区域内进行标识
15 ,表面处理:喷砂
16 ,外部表面机理:所有外部表面,均为铸造表面
2、sand cast
3、weight:140 kg
4、general tolerance:
5、draft angle not indicated:1.5 max, to add material direction
6、internal radii not indicated: 3 mm
7、external radii not indicated: 2 mm
8、dimensions measured on the parting plane are marked mpl
9、dimensions to the surfaces,included 5mm stock allowed for machining,are marked sfm
10、surfaces marked "3d source" will conform to 3d model file attached to the drawing
the 3d model. Use spi commercial tolerances for the specified material as a
maximum.
3.Process control dimensions indicated by ●
Functionally critical dimensions which cpk date are required indicated by ■
Plastic
Notes: unless otherwise specified
1.interpret dimensions and tolerances per asme y-14.5m-1994.
2.drawings are for inspection purposes only. Controlling geometry is governed by
2.此草案只用以检查目的,控制几何管理。
3.●表示过程需控制尺寸,■表示功能的关键尺寸 需要日期,◆功能重要尺寸
4.材料:PS-HI. 0%允许再磨研,资料表中有规格。
5.每草案三维实体,除非另有说明
草案中 + 号表示每边尺寸增加
草案中 - 号表示每边尺寸减少
6.表面结构样式如图.
7.完成所有部分共面b3的表示除外。
8.所有表面无灰尘,石油和其他污染物。
9.不允许使用脱模剂。
10.打破所有的尖锐的边缘和角球,最大限度地助焊剂沾0.2mm半径。
11.闪光和分模线匹配不超过0.1毫米。
12.所述零件资料在以下这个位置。
1、material:aluminum A356-T51,according to astm b/26M
11、cracks to be checked by liquid penetrant (FPI)
12、cracks welding is permitted under customer approval only
13、deburr all sharp edges
14、mark material batch only in the shown area
11.Flash and parting line mismatch not to exceed 0.1mm.
12.Place following part information in this location.
塑料品:
注释:除非另有说明
1.解释尺寸给每asme y-14.5m-1994.定公差