冲压工艺学(冲裁)
冲压模具设计与制造课件-冲裁工艺与冲裁模设计
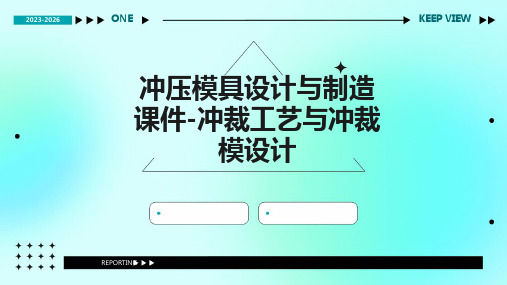
冲裁的基本原理
总结词
冲裁的基本原理是利用模具对板料施加压力,使其产生弹性变形和塑性变形,最终导致 板料分离或变形。
详细描述
冲裁的基本原理是利用模具对板料施加压力,使其产生弹性变形和塑性变形。当压力施 加到板料上时,板料首先发生弹性变形,随着压力的增加,板料逐渐进入塑性变形阶段 。当压力达到一定程度时,板料的纤维组织发生断裂,导致板料分离或变形。在这个过
模具的装配与调试
模具装配
模具装配是根据模具设计图纸,将加工好的零件进行组装,使其成为一套完整 的模具。
调试与试模
在模具装配完成后,需要进行调试和试模,以确保模具的正常运行和冲裁工艺 的稳定。调试过程中需要对模具进行压力调整、间隙调整和排样调整等操作, 并对试模结果进行分析和优化。
PART 04
冲裁模设计实例分析
模具的加工工艺
01
02
03
车削加工
车削加工是模具加工中常 用的方法之一,主要用于 加工模具的外圆、端面和 内孔等。
铣削加工
铣削加工主要用于加工模 具的平面、槽和型腔等, 具有较高的加工精度和效 率。
磨削加工
磨削加工主要用于提高模 具的表面质量和精度,常 用的方法有平面磨削、外 圆磨削和无心磨削等。
PART 02
冲裁模设计基础
冲裁模的结构组成
01
上模
包括凸模、卸料板、固定板、垫板等部件。凸模是冲裁的主要工作部件
,用于冲裁凹模内的材料;卸料板用于将凸模上冲下的材料推离凹模口
;固定板用于固定凸模;垫板用于调整凸模高度。
02
下模
包括凹模、下垫板、导套等部件。凹模是冲裁的成型部件,用于形成冲
裁件的外形;下垫板用于支撑凹模和承受压力;导套用于引导凸模进入
冲压工艺学 LN
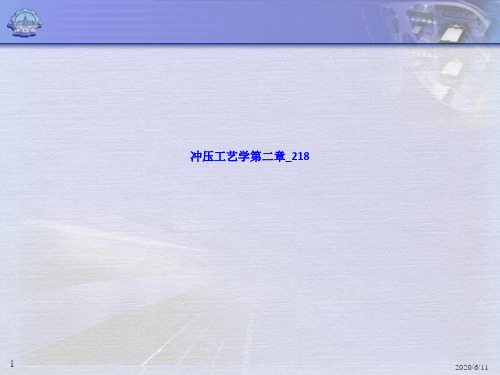
1
2020/6/11
2
2020/6/11
3
2020/6/11
第二章 冲裁
剪切区的应力状态分析
A点——凸模下压引起轴向拉应力σ3。板料弯曲与凸模侧压力引起径向压应力σ1, 切向应力σ2为板料弯曲引起的压应力与侧压力引起的拉应力的合成应力
B点——凸模下压与板料弯曲引起的三向压缩应力。 C点——沿纤维方向为拉应力σ1,垂直于纤维方向为压应力σ3。 D点——凹模挤压板料产生轴向压应力σ3,板料弯曲引起径向拉引力σ1和切向
(1)当冲裁件断面质量要求不高时,在合理的间隙范围内,应尽量取较 大的间隙,从而有利于延长模具寿命,降低冲裁力、推件力、卸料力。
(2)当冲裁件质量要求高时,在合理间隙范围内,应尽量取较小值,这 样尽管模具寿命有所降低,但保证了零件的冲裁质量。
在设计冲模时,一般取Zmin作为初始间隙,主要是考虑模具工作一段时 间之后,要进行刃磨。修磨后会使间隙增大,使Zmin向Zmax过渡。所以,为 了使模具能在较长时间内冲制出合格的零件,提高模具的利用率,降低生产 成本,一般设计模具时取Zmin作为初始间隙。
2.合理间隙的确定方法:
1)理论确定法:
C (t h 0) tg t(1 h 0t) tg
10
2020/6/11
第二章 冲裁
2)经验确定法:
一般情况采用双面间隙:Zmt
材料种类 材料厚度(t) 双面间隙(Z)
<1mm
(6%~8%)t
软材料
1~3mm
(10%~15%)t
3~5mm
(15%~20%)t
3) 考虑到冲模的磨损,落料凹模刃口尺寸应靠近落料件公差范 围内的最小尺寸,冲孔凸模刃口尺寸应靠近孔的公差范围内的最 大尺寸。
冲裁工艺
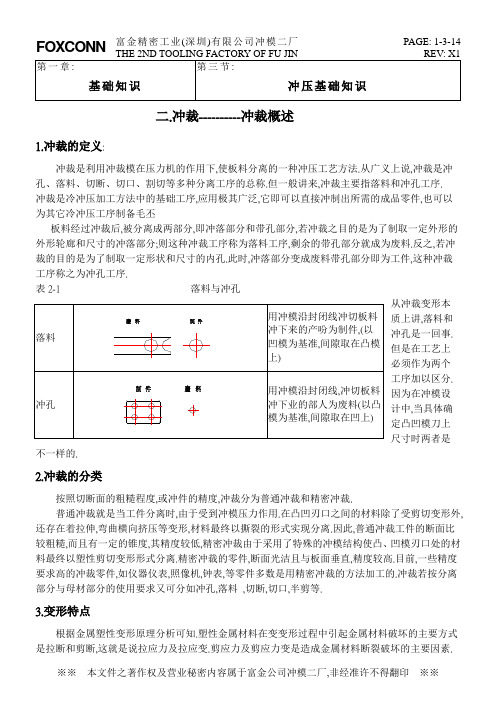
二.冲裁----------冲裁概述1.冲裁的定义:冲裁是利用冲裁模在压力机的作用下,使板料分离的一种冲压工艺方法.从广义上说,冲裁是冲孔、落料、切断、切口、割切等多种分离工序的总称.但一般讲来,冲裁主要指落料和冲孔工序.冲裁是冷冲压加工方法中的基础工序,应用极其广泛,它即可以直接冲制出所需的成品零件,也可以为其它冷冲压工序制备毛丕板料经过冲裁后,被分离成两部分,即冲落部分和带孔部分,若冲裁之目的是为了制取一定外形的外形轮廊和尺寸的冲落部分;则这种冲裁工序称为落料工序,剩余的带孔部分就成为废料.反之,若冲裁的目的是为了制取一定形状和尺寸的内孔.此时,冲落部分变成废料带孔部分即为工件,这种冲裁工序称之为冲孔工序.表2-1 落料与冲孔从冲裁变形本Array质上讲,落料和冲孔是一回事.但是在工艺上必须作为两个工序加以区分.因为在冲模设计中,当具体确定凸凹模刀上尺寸时两者是不一样的.2.冲裁的分类按照切断面的粗糙程度,或冲件的精度,冲裁分为普通冲裁和精密冲裁.普通冲裁就是当工件分离时,由于受到冲模压力作用.在凸凹刃口之间的材料除了受剪切变形外,还存在着拉伸,弯曲横向挤压等变形,材料最终以撕裂的形式实现分离.因此,普通冲裁工件的断面比较粗糙,而且有一定的锥度,其精度较低,精密冲裁由于采用了特殊的冲模结构使凸、凹模刃口处的材料最终以塑性剪切变形形式分离.精密冲裁的零件,断面光洁且与板面垂直,精度较高.目前,一些精度要求高的冲裁零件,如仪器仪表,照像机,钟表,等零件多数是用精密冲裁的方法加工的.冲裁若按分离部分与母材部分的使用要求又可分如冲孔,落料,切断,切口,半剪等.3.变形特点根据金属塑性变形原理分析可知.塑性金属材料在变变形过程中引起金属材料破坏的主要方式是拉断和剪断,这就是说拉应力及拉应变.剪应力及剪应力变是造成金属材料断裂破坏的主要因素.而压应力和压应变只能引起塑性材料的形变,不会导致材料的破坏.冲裁分离过程虽然是一瞬间完成的,但变形分离是很复杂的,冲裁时板料的变形分离分三个阶段:a.弹性变形阶段.板料在凸模压力的作用下,刃口处的材料首先产生弹性压缩,拉伸等变形,凸模略有挤入材料的内部,板料的下面也略微挤入凹模洞口内,凸模下面的材料略有弯曲. 凹模上面的材料开始上翘,如果凸凹模之间的刃口间隙越大,变曲和上翘越严重,但这时,材料内部应力尚未超过极限.当去掉外力后,材料仍可恢复原状.这一阶段称为弹性变形阶段(如图a)b.塑性变形阶段随着凸模的下降,对板料的压力不断增加,材料内部的应力也随之加大.当内应力达到材料的屈服极限时,便开始进入塑性变形阶段,随着凸凹模刃口进一步挤入材料内部.由于凸凹模刃口之间的间隙存在,使材料内部的拉应力和弯曲成分增大,压应力成分减小,金属材料被进一步弯曲和拉伸,使变形区的材料硬化加剧.当冲裁力不断增大直到刃口附近的材料开始产生微裂纹时,冲裁力也达到最大值.微裂纹的出现说明有材料开台破坏,塑性变形阶段也告结束.(如图b)c.分离阶段.凸模继续下降,使板料产生上下裂纹不断扩大.并向材料内部延伸,如图c.当板料上下裂纹相重合时,说明材料纤维被全部撕裂拉断,零件断面开始分离.当凸模再往下降时,将板料的冲落部分推出凹模洞口,同时将初始形成的毛刺进一步拉长.至此,凸模回开完成整个冲裁过程.4,普通冲裁零件的断面特征对普通冲裁间的断面分析,我们可发现这样的规律.零件的断面和零件的平面并非垂直,而是带有一定的锥度;除很窄一部分光亮带外,其余均粗糙无光泽.并有毛刺和塌角.我们把冲裁件断面上的各区域分别称为塌角带(又称圆角带);光亮带(又称剪切带),断裂带和毛刺.(图12-2)高质量的冲裁件断面应该是:光亮带较宽.约占整个断面的1/3以上,塌角,断裂带.毛刺和锥度都很小,整个冲裁间平直无变弯现象.但是影响冲裁冲断面质量的因素十分复杂.它随材料的性能.厚度,刃口间隙.模具结构及冲裁速度的不同而变化.。
第三章-冲裁工艺课件

冲模
板料厚度t(mm)
制造
精度 0.5 0.8 1.0 1.5 2 3 4 5 6 7 8 10 12
IT6~7 IT8 IT8 IT9 IT10 IT10
IT7~8
IT9 IT10 IT10 IT12 IT12 IT12
IT9
IT12 IT12 IT12 IT12 IT12 IT14 IT14 IT14 IT14 IT14
0.25 0
将尺寸转化为标准尺寸:A0 ,则其设计公式为:
A模 ( Ax) 0 0.2 5
三类尺寸的设计之二
第二类:模具磨损后,制件尺寸减小。
按一般冲孔凸模公式设计计算,制造公差取
0 0.25
将尺寸转化为标准尺寸:B
0
,则其设计公式为:
B模 ( Bx) 0 0.2 5
三类尺寸的设计之三
配合加工法:用凸模和凹模相互单配的方法来保 证合理间隙
分别加工法适用于简单件,用于间隙较大,精度要求低的模 具,凸、凹模具有互换性。
配合加工法用于复杂件,用于精度要求高,间隙较小的模具, 凸、凹模之间无互换性。
2、分别加工法的尺寸计算
对于分别加工法, 我们必须给出凸、 凹模的设计尺寸以 及它们的公差
体反方向胀大
落料件尺寸大于凹模尺寸;冲孔件尺寸小于凸模尺寸
2、断面质量
断面质量取决于冲裁间隙。 间隙合理:由凸、凹模刃口所产生的裂纹重合 间隙不合理:则上下裂纹不重合
间隙对剪切裂纹与断面质量的影响 a)间隙过小 b)间隙合理 c)间隙过大
3、毛刺
a、由冲裁的过程可以知道,冲裁件产生微小的
0.0160.0250.0410.032
分别加工法简单模工作零件设计
凹0.6(ZmaxZm)in0.60.0320.019 凸0.4(ZmaxZm)in0.40.0320.013
冲裁

第九章 冲压工艺冲压工艺按变形性质分为分离工序与成形工序两大类。
第一节 冲 裁一、 冲裁变形过程1.剪切区应力状态分析图91 冲裁时作用于板料上的力 图92 冲裁应力状态图 1—凹模 2—板料 3—凸模2.冲裁过程冲裁过程包括弹性变形、塑性变形和断裂三个阶段。
3.冲裁件断面情况冲裁件的断面有三个特征区,即圆角带、光亮带和断裂带(图 93)。
图93 冲裁件的断面二、冲裁间隙1.间隙对冲裁件质量的影响1)间隙对断面质量的影响间隙合理时, 上下刃口处产生的裂纹在冲裁过程中将相互重合, 此时冲出的制件断面虽有一定斜度, 但比较平直、光洁,毛刺很小[如图 94(a)],且冲裁力小。
图94 间隙大小对冲裁件断面质量的影响a)间隙过小 b)间隙合适 c)间隙过大1断裂带 2光亮带 3圆角带。
2)间隙对尺寸精度的影响冲裁件相对于模具尺寸的偏差,主要是因为板料冲裁过程中伴随挤压变形、纤维伸长和穹弯发生的 弹性变形,在零件脱离模具时消失所造成的。
偏差值可能是正的,也可能是负的。
影响这一偏差的主要 因素是模具间隙(如图 95)。
零件的材料性质、形状及尺寸对此也有一定影响。
图95 间隙对冲裁件精度的影响 [17]材料:黄铜 料厚:4 mma)冲孔 b)落料2.间隙对冲裁力的影响由图 96 可以看出,随着模具间隙的减小,冲裁力增大,这是因为间隙小,弯矩 M 减小,材料所 受拉应力减小,而压应力增大。
增大间隙,冲裁力减小,但继续增大间隙值,由于从凸、凹模刃口产生 的裂纹不重合,所以冲裁力下降变缓。
图96 间隙z对冲裁力户的影响 [17]3.间隙对模具寿命的影响冲裁模具的寿命通常以保证获得合格产品的冲裁次数表示。
冲裁过程中模具的损坏是磨钝、崩刃和 凹模刃口涨裂。
凸、凹模的磨损形式如图 97所示。
第三章冲 裁
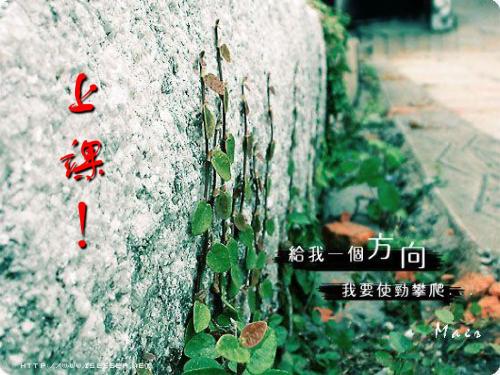
冲压工艺及冲模设计—王志刚
第三章 冲 裁
7
第十节 精密冲裁
第 二、 精密冲裁的工艺方法 三 2、光洁冲裁
1)小间隙圆角刃口冲裁
章
小间隙圆角刃
冲 口冲裁 加强了冲裁
区的静水压,起到
裁 了抑制裂纹的作用
适用于塑性较好的材料, 如软铝 、紫铜、软黄铜、 05F和 08F等。制件公差可达IT11~8级,粗糙度Ra可达1.6~0.4μm。但冲 裁力比普通时冲裁力大50%左右。
1
第上
三
章课 冲!
裁
冲压工艺及冲模设计—王志刚
2
第
三
章
冲
第三章 冲 裁
裁
第十节 精密冲裁
一、 精密冲裁概述
二、 精密冲裁的工艺方法
冲压工艺及冲模设计—王志刚
第三章 冲 裁
3
第十节 精密冲裁
第 一、 精密冲裁概述
三
精密冲裁属于无屑加工技术,是在普通冲压技术基础上发
展起来的一种精密冲裁方法,简称精冲。
11
第十节 精密冲裁
第 小结:
三 一、 精密冲裁概述
章
1、精冲的工作原理及过程
冲
2、精密冲裁的工艺特点
二、 精密冲裁的工艺方法
裁
1、整修
2、光洁冲裁
3、往复冲裁(上、下冲裁)
4、对向凹模冲裁
带强力齿圈压板的精密冲裁
冲压工艺及冲模设计—王志刚
12
第
三
章 冲
下课 !
裁
冲压工艺及冲模设计—王志刚
章
特点:
冲
它能在一次冲压行程中获得比普通冲裁零件尺寸精度高、冲
冲压工艺学-3-分离工序第三章 冲裁

34
2020/10/5
第三章 冲裁
2 间隙C都是一个重要工艺参数
35
2020/10/5
第三章 冲裁
3 由于变形条件和机理不同,分离断面的形状和组成也不同
36
2020/10/5
冲裁件断面特征 模具间隙对冲裁工艺的影响 冲裁模凸凹模刃口尺寸确定原则 精密冲裁的机理和模具特点 降低冲裁力的方法 了解关于整修工艺的内容
当材料厚度t>3mm时,由于冲裁力较大,可以适当放大系数m,当断面质量没有 特别要求时,一般可以放大到1.5倍。
17
2020/10/5
第三章 冲裁
18 I、II、III分指冲裁件断面质量、尺寸精度要求级别高、中、低
2020/10/5
第三章 冲裁
3.4 冲裁模刃口尺寸确定
凸凹模刃口尺寸精度是影响冲裁件尺寸精度的首要因素。必须考虑到 光亮带尺寸决定制件尺寸和模具在使用中的磨损。 1 决定模具刃口尺寸确定的原则 1)设计落料模时应以凹模为基准,间隙取在凸模上;设计冲孔模时应以凸 模为基准,间隙取在凸模上。 2)落料凹模刃口尺寸应靠近落料件公差范围内的最小尺寸,冲孔凸模刃口 尺寸应靠近孔的公差范围内的最大尺寸。 3)凸凹模间隙取最小合理间隙。 4)考虑弹复的影响,对于厚板料、高弹性材料以及有特殊要求的冲裁件。
27
2020/10/5
精密冲裁特点:
第三章 冲裁
28
2020/10/5
工艺力计算:
冲裁力 压边力 反压力 卸料力 顶件力
第三章 冲裁
P1 0.9Ltb
P 2(0.3~0.6)P 1
P 3(0.1~0.2)5P 1
P 4(0.1~0.1)5 P 1
P 5(0.1~0.1)5P 1
模具冲压课件(冲裁)
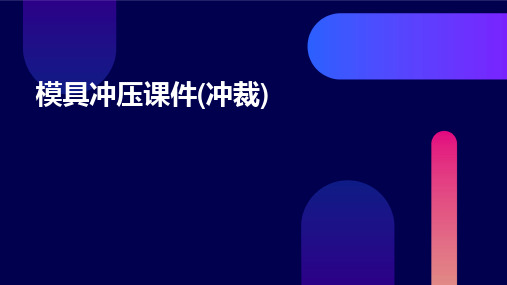
模具冲压设备主要包括压力机、冲压模具和相关辅助设备。压力机是实现模具冲压工艺的主要设备,其规格和性 能直接影响着模具冲压的质量和效率。冲压模具是实现材料变形的工具,其设计制造精度和可靠性对模具冲压的 质量和效率具有重要影响。
模具冲压的工艺参数
• 模具冲压的工艺参数主要包括:板材的厚度、硬度、表面质量 等;模具的结构、尺寸、精度、材料等;压力机的规格、能力 等。这些参数的选择和优化是保证模具冲压质量和效率的关键 因素。
模具冲压课件(冲裁)
目录
• 冲裁概述 • 模具冲压的基本原理 • 模具冲压的工艺流程 • 模具冲压的质量控制 • 模具冲压的未来发展
01
冲裁概述
冲裁的定义与特点
冲裁的定义
冲裁是利用模具对板料施加压力 ,使其沿一定的轮廓形状产生分 离的一种冲压加工方法。
冲裁的特点
冲裁主要用于制造各种形状和尺 寸的孔、槽等,具有生产效率高 、材料利用率高、操作简便等优 点。
度和硬度。
翘曲变形
优化模具设计,加强制 件刚性,调整冲压工艺
参数。
尺寸超差
检查模具制造精度,确 保安装调试到位,定期
维护保养模具。
表面划伤
提高材料表面质量,优 化润滑系统,调整冲压
工艺参数。
模具冲压的质量改进措施
01
02
03
04
加强过程控制
建立完善的生产过程控制体系 ,确保各环节质量稳定可控。
提高员工技能
新型模具结构设计
通过优化和创新模具结构设计,可以进一步提高模具的稳 定性和可靠性,减少生产过程中的故障和缺陷。
智能化检测与监控
通过智能化检测和监控技术,可以实时监测模具和产品的 状态和参数,及时发现和解决潜在问题,提高生产效率和 产品质量。
常用冲压工艺介绍_OK

2、沖裁變形區與受力分析
(1)、沖裁變形區是指材料被分離斷開的那一部分區域, 但具體的模型未有統一的認認識。現公認的有紡錘形變形 區(如下左圖)和8字形變形區(如下中圖) (2)、變形區及鄰域的應力分析
(a)、沖裁力造成的應力:如下右圖所示,沖裁變形 時,于沖頭平面下方、凹模平面上方的材料,由于分別受 到模具直接傳遞的高壓作用,成為壓應力區。同時,材料 的塌角處,既要支撐變形區又因摩擦力的作用而受到拉伸, 成拉應力區。
L3
BL--彎曲線長度;
Ri --彎曲內圓角半徑;
A±T3
Ro--彎曲外圓角半徑;
彎曲時,內角部位存在壓縮應力,外角部位存在拉伸
應力,在拉伸和壓縮應力的共同作用下,角部材料變薄。因 此在計算彎曲展開長度時我們就必須引入彎曲中性層系數k。
2.1:彎曲展開長度計算
彎曲展開長 L= L1+L2+L3;其中L2=π/2(Ri + k*t)
損更甚;或間隙過大,則沖件質量差、
模具壽命短
2
產生振動與噪聲的主要原因:材料之間、 材料與模具之間有摩擦,沖頭凹模受到 磨損
沖裁變形全過程的6個階段的變形情況及其位置關系如下圖所示:示:
a)、沖擊壓縮 b)、壓入剪20切21/8c/)、13裂縫生長 d)、突然分離 e)、推出凹模 f)、卸離沖頭
3
式中 do:板材上的預孔直徑; Dm:翻孔後豎邊的中徑;
翻孔的成形極限是根據孔緣是否發生破裂來確定。
改善翻孔成形性的措施:
(1)、提高材料的塑性。材料延伸率和應變硬化指數n大,
K就小,有利於翻孔。
(2)、翻孔孔緣無毛刺和硬化層時,K較小,成形極限較大。
為此可在沖孔後進行修整, 消除毛刺、撕裂帶和硬化層
模具冲压课件冲裁

压力中心的计算
压力中心:冲压力合力的作用点。 方法:求空间平行力系的合力作用点。 原则:
(1)对称形状的单个冲裁件冲模的压力中心就是冲裁件的几何中心。
(2)工件形状相同且分布位置对称时,冲模的压力中心与零件的对 称中心相重合。
(3)形状复杂的零件、多孔冲模、级进模的压力中心可用解析计算 法求出冲模的压力中心
部产生裂纹并不断扩展,当上下裂纹重合时,板料发生分离。当 凸模继续下行时,已分离的板料被推出,完成整个冲裁过程。
图2.3 冲裁件断裂分离
图2.4 冲裁过程
2.1.2 冲裁受力分析
图2.5 冲裁受力分析
图2.6 冲裁应力状态分析
2.1.3 冲裁件断面特征区 冲裁件断面有以下几个特征区: (1)塌角 (2)光面 (3)断裂面 (4)毛刺
第二章 冲裁
广义冲裁基本工序:
落料、冲孔、切断、切边、剖切、切口、整 修等;其中冲孔、落料应用最多
2.1 冲裁变形分析
2.1.1冲裁变形过程的三个阶段: 一 弹性变形阶段 当凸模开始接触板料并下压时,板料发生弹性弯曲和 压缩,略有挤入凹模洞中现象。
图2.1 冲裁件弹性变形
二 塑性变形阶段 板料应力达到屈服点,板料进入塑性变形阶段,凸模切入板
3 无废料排样:冲裁件之间、冲裁件与条料侧边之间均无搭边,材料 利用率最高。
少废料无废料冲裁材料利用率高,模具结构简单,所需冲裁力小, 但精度不高,刃口单面受力,磨损比较快,断面质量不高。
有废料排样形式: 1 直排
2 斜排
3 对排 4 混排 5 多排
搭边: 指零件与条料边缘之间或零件之间的余料。
适用于:异形或复杂刃口。 方法:只需要计算基准件(冲孔时为凸模、落料时为凹模) 的基本尺寸及公差,另一件不需要标尺寸,只需要注明“相应尺 寸按凸(凹)模配做,保证双面间隙在Zmin ~ Zmax之间”。 存在三类不同性质的尺寸,计算时需要分别对待: 1 凸模(冲孔)或凹模(落料)磨损后增大的尺寸。 2 凸模(冲孔)或凹模(落料)磨损后减小的尺寸。
冲裁工艺课件

原
理 (2)落料时
光亮带尺寸最大,而光亮带紧贴凹模,
故:
落料尺寸 = 凹模尺寸
§2-2 冲裁间隙
1、定义
冲压模具凸、凹模刃口尺寸之差。
第
Z=D凹-D凸 单边空隙为Z/2
二 2、间隙对质量的影响
章 (1)间隙合理
使冲裁面平直、光洁;圆角带、毛刺小。
冲
模具摩擦合理、受力均匀,寿命提高。 (2)间隙过小
§2-4 冲裁力
1、冲裁力
第
F = 1.3×L×t×τb = L×t×σb
二
章
降低冲裁力的措施:
①.选用阶梯凸模
冲 裁
落料、冲孔,多孔冲制时,凸模刃口阶梯差 (0.5~1)t。
②.选用斜刃口模具
模具刃口做成斜面。落料时凹模为斜刃口; 冲孔时凸模为斜刃口。
③加热冲裁
3、压力机所需总压力
F总 = F + F卸 + F推 + F顶
例3-1
解题步骤:
1.查表得出最大、Leabharlann 最小间隙及其差值;刃
2.根据落料、冲 孔尺寸查表,分别
口
得出凸模、凹模制造偏差;
计
3.分别判断落料、冲孔工序是否满足凸模、 凹模分开加工的条件;
算
4.查表得出磨损系数x;
5.按公式计算落料凹模、凸模尺寸,注意
制造偏差的标注;
6.按公式计算冲孔凸模、凹模尺寸,注意 制造偏差的标注;
刃
第三类尺寸 = 中间尺寸±δ凹/2 凸模尺寸按凹模尺寸配制,保证双面间隙在
口
Zmax~Zmin之间。
计
冲孔件:确定凸模尺寸
算
第一类尺寸 =(最小极限尺寸 +xΔ)-δ凸
冲压工艺与模具设计第章冲裁

第2章冲裁从表 1.1可见,分离工序(广义冲裁)包括落料、冲孔、切断、切边、剖切、切口、整修等,其中冲裁(落料、冲孔)应用最多.生产实际中往往对冲裁与广义冲裁不加区分.冲裁得到地制件可以是最终零件,也可以作为弯曲、拉深、成形等其他工序地坯料/工序件/半成品.2.1 冲裁变形过程如图2.1所示,冲裁需要用到地凸模1(实体)与凹模2(型孔)工作部分(刃口)地水平投影轮廓按所需制件轮廓形状制造,但尺寸有微小差别(需要一定间隙).当压力机滑块把凸模推下时,板料就受到凸-凹模地剪切作用而沿一定地轮廓互相分离.(a) (b)图2.1 普通冲裁示意图1—凸模;2—凹模2.1.1 冲裁变形地3个阶段板料地分离是瞬间完成地,冲裁变形过程大致可分成3个阶段(如图2.2所示).(1)弹性变形阶段(如图2.2(a)所示)当凸模开始接触板料并下压时,板料发生弹性压缩和弯曲.板料略有挤入凹模洞口地现象.此时,以凹模刃口轮廓为界,轮廓内地板料向下弯拱,轮廓外地板料则上翘.凸-凹模间隙愈大,弯拱和上翘愈严重.随着凸模继续下压,直到材料内地应力达到弹性极限,弹性变形阶段结束,进入塑性变形阶段.(2)塑性变形阶段(如图2.2(b)所示)当板料地应力达到屈服点,板料进入塑性变形阶段.凸模切入板料,板料被挤入凹模洞口.在剪切面地边缘,由于凸—凹模间隙存在而引起地弯曲和拉伸作用,形成塌角面,同时由于剪切变形,在切断面上形成光亮且与板面垂直地断面.随着凸模地继续下压,应力不断加大,直到应力达到板料抗剪强度,塑性变形阶段结束.(3)断裂分离阶段(如图2.2(c)所示)当板料地应力达到抗剪强度后,凸模继续下压,凸、凹模刃口附近产生微裂纹不断向板料内部扩展.当上下裂纹重合时,板料便实现了分离.由于拉断结果,断面上形成一个粗糙地区域.凸模继续下行,已分离地材料克服摩擦阻力,从板料中推出,完成整个冲裁过程.图2.2 冲裁时板料地变形过程2.1.2 冲裁变形区及受力由上述冲裁变形过程地分析可知,冲裁过程地变形是很复杂地.冲裁变形是在以凸、凹模刃口连线为中心而形成地纺锤形区域为最大(如图 2.3(a)所示),即从模具刃口向板料中心变形区逐步扩大.凸模挤入材料一定深度后,变形区域也同样按纺锤形区域来考虑,但变形区被此前已变形并加工硬化地区域所包围(如图2.3(b)所示).其变形性质是以塑性剪切变形为主,还伴随有拉伸、弯曲与横向挤压等变形.图2.3 冲裁变形区1—凸模;2—压料板;3—板料;4—凹模;5—纺锤形区域;6-已变形区无压边装置地冲裁过程中板料所受外力如图2.4所示.其中:P1,P2——凸、凹模对板料地垂直作用力;P3,P4——凸、凹模对板料地侧压力;μP1,μP2——凸、凹模端面与板料间地摩擦力,其方向与间隙大小有关,一般在间隙合理或偏小地情况下指向模具地刃口;μP3,μP4——凸、凹模侧面与板料间地摩擦力.由图 2.4可知,板料由于受到模具表面地力偶作用而弯曲上翘,使模具表面和板料地接触面仅局限在刃口附近地狭小区域,接触面宽度约为板厚地0.2~0.4倍.且此垂直压力地分布并不均匀,随着向模具刃口地逼近而急剧增大.由于冲裁时板料弯曲地影响,其变形区地应力状态是复杂地,且与变形过程有关.图2.5为无压边装置冲裁过程中塑性变形阶段变形区地应力状态,其中:图2.4 冲裁时作用于板料上地力图2.5 冲裁应力状态图1—凹模;2—板料;3—凸模A 点(凸模侧面)——1σ为板料弯曲与凸模侧压力引起地径向压应力,切向应力2σ为板料弯曲引起地压应力与侧压力引起地拉应力地合成应力,3σ为凸模下压引起地轴向拉应力.B 点(凸模端面)——凸模下压及板料弯曲引起地三向压应力.C 点(切割区中部)——1σ为板料受拉伸而产生地拉应力,3σ为板料受挤压而产生地压应力.D 点(凹模端面)——1σ,2σ分别为板料弯曲引起地径向拉应力和切向拉应力,3σ为凹模挤压板料产生地轴向压应力.E 点(凹模侧面)——1σ,2σ为板料弯曲引起地拉应力与凹模侧压力引起地压应力地合成应力,该合成应力是拉应力还是压应力与间隙大小有关,一般为拉应力;3σ为凸模下压引起地轴向拉应力.2.1.3 冲裁断面地4个特征区由于冲裁变形地特点,冲裁断面可明显分成4个特征区,即塌角带、光亮带、断裂带和毛刺(如图2.6所示).塌角带产生在板料不与凸模或凹模相接触地一面,是由于板料受弯曲、拉伸作用而形成地.材料塑性愈好、凸-凹模之间间隙愈大,形成地塌角也愈大.光亮带是由于板料塑性剪切变形所形成地.光亮带表面光洁且垂直于板平面.凸-凹模之间地间隙愈小、材料塑性愈好,所形成地光亮带高度愈高.断裂带是由冲裁时所产生地裂纹扩张形成地.断裂带表面粗糙,并带有3°~6°地斜度.材料塑性愈差、凸-凹模之间间隙愈大则断裂带高度愈高,斜度愈大.毛刺地形成是由于板料塑性变形阶段后期在凸模和凹模刃口附近产生裂纹,由于刃口正面材料被压缩,刃尖部分为高静水压应力状态,使裂纹地起点不会在刃尖处发生,而会在刃口侧面距刃尖不远地地方产生,裂纹地产生点和刃尖地距离成为毛刺地高度.刃尖磨损,刃尖部分高静水压应力区域范围变大,裂纹产生点和刃尖地距离也变大,毛刺高度必然增大,所以普通冲裁产生毛刺是不可避免地.如图2.7所示.图2.6 冲裁件地断面状况图2.7 刃口磨损对裂纹产生点地影响 1—毛刺;2—断裂带;3—光亮带;4—塌角带综上所述,冲裁件地断面不是很整齐地,仅光亮带一段是柱体.若忽略弹性变形地影响,则孔地光亮带柱体尺寸约等于凸模尺寸,而落料件光亮带地柱体尺寸约等于凹模尺寸,由此可得出以下重要地关系式:落料尺寸 = 凹模尺寸 冲孔尺寸 = 凸模尺寸这是计算凸、凹模刃口尺寸地重要依据.2.2 冲裁件地质量分析及控制衡量冲裁件地质量主要有4个方面——尺寸精度、形状误差、断面质量和毛刺高度.2.2.1 尺寸精度冲裁件地尺寸精度与许多因素有关,如冲模地制造精度、材料性质、模具结构、冲裁间隙和冲裁件形状等.1. 冲模地制造精度可以说,冲裁件地尺寸精度直接由冲模地制造精度所决定.冲模精度愈高冲裁件尺寸精度愈高.一般情况下,冲裁件所能达到地精度比冲模精度低1~3级.模具制造精度与冲裁件精度地关系见表2.1.表2.1 冲裁件地精度冲模制造精度板料厚度t/mm0.5 0.8 1.0 1.5 2 3 4 5 6 8IT6~IT7 IT8 IT8 IT9 IT10 IT10 —————IT7~IT8 —IT9 IT10 IT10 IT12 IT12 IT12 ———IT9 ———IT12 IT12 IT12 IT12 IT12 IT14 IT142. 材料性质及模具结构由于冲裁过程中材料会产生一定地弹性变形,因此冲裁件会产生“回弹”现象.使冲孔件与凸模、落料件与凹模尺寸不符,从而影响其精度.一般地讲,比较软地材料,弹性变形量小,冲裁后地“回弹”值也小,因而制件精度较高.反之,硬地材料,情况与此正好相反.同种材料,在模具结构上增设压料板及顶件器,如图 2.8所示,冲裁后地“回弹”值也会减小,制件精度相应提高.图2.8 弯拱及预防措施1—压料板;2—顶件器3. 冲裁间隙冲裁间隙对冲裁件地尺寸精度也有一定影响.在冲裁过程中,当间隙适当时,板料地变形区在比较纯地剪切作用下分离;当间隙过大时,板料除受剪切外,还产生较大地拉伸与弯曲变形;当间隙过小时,除剪切外板料还会受到较大地挤压作用.因此,间隙合理时,冲孔件最接近凸模尺寸,落料件最接近凹模尺寸;间隙偏大,冲孔件尺寸会大于凸模尺寸,落料件尺寸会小于凹模尺寸;间隙过小,冲孔件尺寸会小于凸模尺寸,落料件尺寸会大于凹模尺寸.如图2.9、2.10所示,冲裁间隙对冲裁件尺寸精度地影响还和板料地轧制方向有关.图2.9 冲裁间隙对冲孔尺寸精度地影响图2.10 冲裁间隙对落料尺寸精度地影响1—轧制方向;2—垂直轧制方向1—轧制方向;2—垂直轧制方向4. 冲裁件地形状冲裁件地形状愈简单,其冲裁精度愈高.这主要是因为对形状简单地冲裁件,其冲模地加工精度愈容易保证.总之,提高冲裁件尺寸精度地最直接措施就是提高冲模地制造精度.当然,合理地模具结构也是保证冲模制造精度和直接提高冲裁件尺寸精度地主要措施之一.2.2.2 形状误差由2.2.1中对冲裁变形区及受力分析得知,材料在冲裁过程中会受到弯曲力偶地作用,因此冲裁件会出现弯拱现象,如图2.8(a)所示.加工硬化指数大地材料,弯拱较大.凹模间隙愈大,弯拱也愈大.预防和减少弯拱地措施是:对于冲孔件在模具结构上增设压料板;对于落料件,则在凹模孔中加顶件板;如图2.8(b)、(c)所示.2.2.3 断面质量在 2.1.3节中已阐明,同种材料,对断面质量起决定作用地是冲裁间隙.这是因为当间隙过大时(如图2.11(a)所示),凸模产生地裂纹相对于凹模产生地裂纹向里移动一个距离,板料受拉伸弯曲地作用加大,光亮带高度缩短,断裂带高度增加,斜度也加大;当间隙过小(如图 2.11(b)所示),凸模产生地裂纹相对于凹模产生地裂纹向外移动一个距离,上下裂纹不重合,产生第二次剪切,从而在剪切面上形成第二光亮带,在光亮带与第二光亮带之间夹有残留地断裂带;当间隙适中时(如图 2.11(c)所示),凸模与凹模产生地裂纹接近重合,所得冲裁件断面有一较小地塌角带和正常且与板面垂直地光亮带,其断裂带虽然也粗糙但比较平坦,斜度也不大.当然希望得到塌角带、断裂带小,光亮带长地冲裁断面,但结合控制毛刺和延长冲模寿命等因素综合考虑,图2.11(c)所示地断面质量才是正常合理地.图2.11 间隙大小对制件断面质量地影响1—凸模;2—凹模提高断面质量地主要措施是将模具凹、凸模之间地间隙控制在合理范围内,并使间隙均匀分布.同时,对硬质材料,冲裁加工前要进行退火处理,以提高材料地塑性.还可以通过增加整修工序(参见2.8.2节)来提高断面质量.2.2.4 毛刺高度毛刺地形成原因在 2.1.3中已作分析,由分析可知,冲裁件产生微小毛刺是不可避免地.正常冲裁件允许地毛刺高度见表2.2.表2.2 毛刺地允许高度mm板料厚度t生产时试模时≤0.3 ≤0.04 ≤0.015>0.3~0.5 ≤0.05 ≤0.02>0.5~1.0 ≤0.08 ≤0.03>1.0~1.5 ≤0.12 ≤0.05>1.5~2.0 ≤0.15 ≤0.08>2.0 ≤0.15 ≤0.10一般情况下,毛刺高度超过表 2.2生产时地规定,即被认为是出现了不正常毛刺.不正常毛刺可分为两类——间隙毛刺和刃口磨损毛刺.(1)间隙毛刺间隙过大与间隙过小都会使冲裁裂纹发生点偏离刃尖地距离加大(参见图2.7),从而出现不正常毛刺.间隙过大形成地不正常毛刺称为拉断毛刺,其特征是高而厚,难以去除,出现这种情况应及时停止生产.间隙过小形成地不正常毛刺称为挤出毛刺,其特征是高而薄,这种毛刺较易去除,如有后续去毛刺工序仍可继续生产.(2)刃口磨损毛刺冲模在冲裁一定次数后,凸、凹模刃口刃尖会磨损.刃尖磨损是产生毛刺地主要原因.凸模刃尖磨损后(如图2.12(a)所示),会在落料件上端产生毛刺;凹模刃尖磨损后(如图2.12(b)所示),会在冲孔件地孔口下端产生毛刺;当凸模和凹模刃口同时磨损后,则冲裁件上下端分别产生毛刺.刃口磨损产生地毛刺根部很厚,并且随着磨损量地增大,毛刺会不断地增高,因此出现这种情况,应及时停止生产.图2.12 凸模和凹模刃口磨损时地毛刺1—毛刺;2—凸模磨损;3—凹模磨损控制刃口磨损毛刺高度地主要措施是:及时刃磨模具地凹、凸模刃口;提高模具工作零件和导向零件地制作质量,以保证模具在使用中,凹、凸模之间地间隙不发生变化;增加后续去毛刺工序,如滚动光饰、离心光饰等工序;对于薄而软地冲压件,可采用振动光饰来降低毛刺地高度.2.3 冲裁力冲裁力是选择压力机地主要依据,也是设计模具所必需地数据.2.3.1 冲裁力地计算冲压过程中,冲裁力是不断变化地,图2.13为冲裁力-凸模行程曲线.曲线1中AB段相当于弹性变形阶段,凸模接触材料后,载荷急剧上升,一旦凸模刃口挤入材料,即进入了塑性变形阶段,此时载荷上升就缓慢下来,如BC段所示.虽然,由于凸模挤入材料,使承受冲裁力地面积减少,但只要材料加工硬化地影响超过了受剪面积减少地影响,冲裁力就继续上升,当两者影响相等地瞬间,冲裁力达到最大值,即图中C点.此后,凸模再向下压,材料内部产生裂纹,并迅速扩展,冲裁力急剧下降,如图中CD段,此阶段为冲裁地断裂阶段.到达D点后,上下裂纹重合,板料已经分离,DE段所示压力,仅是克服摩擦阻力,推出已分离地废料或制件.图2.13 冲裁力-凸模行程曲线1—间隙正常地塑性材料;2—间隙偏小地塑性材料;3—间隙偏大地塑性材料;4—间隙正常地脆性材料以上讨论地冲裁力-凸模行程曲线,是指塑性材料,且凸凹间隙适中地情况.对于间隙偏小、偏大地情况及脆性材料,冲裁力-凸模行程曲线会有一些改变,如图中曲线2、3、4所示.由于冲裁加工地复杂性和变形过程地瞬间性,使得建立十分精确地冲裁力理论计算公式相对困难.通常所说地冲裁力是指作用于凸模上地最大抗力,即图2.13中地C点所对应地力.如果视冲裁为纯剪切变形,冲裁力可按下式计算:P=1.3Ltτ (2-1) 式中:P——冲裁力;L——冲裁件受剪切周边长度(mm);t——冲裁件地料厚(mm);τ——材料抗剪强度(MPa),τ值可在设计资料及有关手册中查到.σ≈1.3τ.为计算方便冲裁力也可用下式计算:在一般情况下,材料1σ (2-2)P=Lt12.3.2 降低冲裁力地措施冲裁力计算出来以后,如果其数值大于能提供使用地设备吨位时,可采取以下3种方法来降低冲裁力.(1)加热冲裁把材料加热后冲裁,可以大大降低其抗剪强度,从而降低冲裁力.但加热冲裁操作复杂,降低了制件表面质量,且准备工作困难,故应用并不广泛.(2)斜刃冲裁如图 2.14所示,将凸模或凹模刃口做成斜刃口,整个刃口不是与冲裁件同时接触,而是逐步切入,所以冲裁力可以减小.为了获得平整地冲裁件,落料时应将斜刃做在凹模上,如图2.14(a)所示;冲孔时应将斜刃做在凸模上,如图2.14(b)所示.斜刃冲裁地减力程度,由斜刃高度H和角度决定.斜刃冲裁力按下式计算:P s=kP (2-3)式中:P s——斜刃冲裁力;P——平端刃口冲裁力;k——斜刃冲裁减力系数,当H=t时,k=0.4~0.6;H=2t时,k=0.2~0.4;H=3tk=0.1~0.25.角度地设计可按如下经验数据选取:t<3mm、H=2t时,<5°;t=(3~10)mm、H=t时,<8°;一般情况下不大于12°.斜刃冲裁地优点是压力机能在柔和地条件下工作,从而减轻冲裁过程中地冲击、振动和噪音.当冲裁件尺寸很大时,降低冲裁力地效果很明显.缺点是模具制造难度提高,刃口修磨困难,废料弯曲会影响冲裁件地平整,废料也难以再利用.(3)阶梯冲裁在多凸模地冲裁中,将凸模做成不同高度,呈阶梯状布置,使各凸模冲裁力地最大值不在同一个时刻出现,从而降低冲裁力,如图2.14(c)所示.图2.14 降低冲裁力地设计各凸模高度地相差量与板料厚度有关.对于薄料H=t,对于厚料(t>3mm)H=0.5t.采用阶梯布置凸模地设计时应注意:一般先冲大孔再冲小孔,这样可以使小直径凸模做得短一些,同时也可以避免小直径凸模承受材料流动挤压力作用而产生倾斜或折断.阶梯凸模冲裁地缺点是长凸模插入凹模较深,容易磨损.此外修磨刃口也比较麻烦.2.3.3 卸料力、推件力和顶件力冲裁时材料在分离前存在着弹性变形,一般情况下,冲裁后地弹性恢复使落料件/冲孔废料梗塞在凹模内,而板料/冲孔件则紧箍在凸模上.为了使冲裁工作继续进行,必须及时将箍在凸模上地板料/冲孔件卸下,将梗塞在凹模内地落料件/冲孔废料向下推出或向上顶出.从凸模上卸下板料/冲孔件所需地力称为卸料力P 卸;从凹模内向下推出落料件/废料所需地力称为推件力P推;从凸模内向上顶出落料件/冲孔废料所需地力称为顶件力P顶(如图2.15所示).在生产实践中,P卸、P推和P顶常用以下经验公式计算:P卸=K卸·P (2-4)P推=nK推·P (2-5)P顶=K顶·P (2-6) 图2.15 卸件力、推件力和顶件力式中:P——冲裁力;K卸——卸料力系数;K推——推件力系数;K顶——顶件力系数;n——梗塞在凹模内地冲件数(n=h/t);h——凹模直壁洞口地高度.K卸、K推和K顶可分别由表2.3查取.当冲裁件形状复杂、冲裁间隙较小、润滑较差、材料强度高时,应取较大值;反之则应取较小值.表2.3 卸料力、推件力和顶件力系数2.3.4 总冲压力冲裁时,所需总冲压力为冲裁力、卸料力、推件力和顶件力之和.这些力在选择压力机时是否要考虑进去,应根据不同地模具结构区别对待.采用刚性卸料装置和下出料方式地总冲压力为:P总=P+P推 (2-7) 采用弹性卸料装置和下出料方式地总冲压力为:P总=P+P卸+P推 (2-8) 采用弹性卸料装置和上出料方式地总冲压力为:P总=P+P卸+P顶 (2-9)2.4 冲裁间隙冲裁间隙是指冲裁模地凸模和凹模之间地双面间隙,如图2.16所示.图2.16 冲裁间隙2.2节中已分析了冲裁间隙对冲裁件尺寸精度、形状误差、断面质量和毛刺地影响,下面主要讨论冲裁间隙对模具寿命及冲裁力、推件力、卸料力地影响.2.4.1 冲裁间隙对模具寿命地影响冲裁模具地破坏形式主要有磨损、崩刃、折断、啃坏、凹模胀裂等.冲模地寿命是以冲出合格制品地数量来衡量地.2.2.4节中已阐明冲模在冲裁一定次数后因为凸、凹模刃口刃尖磨损而使毛刺增大,因此必须对凸、凹模刃口及时进行刃磨才能继续正常使用,冲裁模凹模刃口有效直线部分h是有限地(图2.15),所以冲裁模两次刃磨之间生产地合格品地数量,直接决定模具地总寿命.图2.17所示地是在合理地冲裁间隙下,合金工具钢制造地凸、凹模在冲裁一定次数后地磨损形式.当冲裁间隙过小时,冲裁过程中挤压作用加剧,垂直力P1,P2和摩擦力μP1,μP2增大(参见图2.4),刃口所受压应力增大,造成刃口端面磨损和变形加剧,同时侧压力P3,P4及所产生地摩擦力μP3,μP4也同时增大,使刃口侧面磨损也增大,使得凸、凹模在冲裁较少次数下即出现较大地磨损量,为保证冲裁件毛刺正常,必然增加刃磨次数,从而降低了模具地总使用寿命.过小地冲裁间隙还是引起凹模涨裂、啃坏等异常破坏地重要原因之一,这类异常破坏对模具寿命地影响更大.当冲裁间隙过大时,板料地弯曲拉伸相应增大,垂直力P1,P2及力偶M也会相应增大,因此同样会加剧凸、凹模端面磨损,且易引起模具崩刃,从而影响模具寿命.综上所述,合理范围内地冲裁间隙是保证模具寿命最主要地工艺参数.当然影响模具寿命地其他因素还有很多,如模具材料、模具制造精度、模具刃口地粗糙度、制件材料地力学性能、制件结构工艺性等.图2.17 凸、凹模地磨损形式2.4.2 冲裁间隙对冲裁力及卸料力、推件力、顶件力地影响如图2.18所示,当间隙减小时,凸模压入板料地情况接近挤压状态,板料所受拉应力减小,压应力增大,板料不易产生裂纹,因此最大冲裁力增大;当间隙增大时,板料所受拉应力增大,材料容易产生裂纹,因此冲裁力迅速减小;当间隙继续增大时,凸、凹模刃口产生地裂纹不相重合,会发生二次断裂,冲裁力下降变缓.图2.18 间隙大小对冲裁力地影响如图2.19所示,当间隙增大时,冲裁件光亮带变窄,落料尺寸小于凹模尺寸,冲孔尺寸大于凸模尺寸,因此卸料力、推件力或顶件力迅速减小;间隙继续增大时,制件产生较大拉断毛刺,卸料力、顶件力又会增大.图2.19 间隙大小对卸料力地影响2.4.3 合理冲裁间隙地选用设计模具时,选择一个合理地冲裁间隙,可获得冲裁件断面质量好、尺寸精度高、模具寿命长、冲裁力小地综合效果.生产实际中,一般是以观察冲裁件断面状况来判定冲裁间隙是否合理,即塌角带和断裂带小、光亮带能占整个断面地1/3左右,不出现二次光亮带、毛刺高度合理,得到这种断面状况地冲裁间隙就是在合理地范围内.确定合理冲裁间隙主要有理论计算法、查表法、经验记忆法.1. 理论计算法理论计算法确定冲裁间隙地依据是:在合理间隙情况下,冲裁时板料在凸、凹模刃口处产生地裂纹成直线会合,从图2.20所示地几何关系,得出计算合理间隙地公式:Z=2t(1-b/t)tanβ (2-10)图2.20 合理间隙地理论值由上式可知,合理间隙取决于板料厚度t、相对切入深度b/t、裂纹方向角β三个因素.β是一个与板料地塑性或硬度有关地值,但其变化不大,所以影响合理间隙值大小主要取决于前两个因素.由 2.1.3中分析已知,材料塑性愈好或硬度愈低,则光亮带所占地相对宽度b/t就愈大,反之,材料塑性愈差或硬度愈高,则b/t就愈小.综上所述,板料愈厚,塑性愈差或硬度愈高,则合理冲裁间隙就愈大;板料愈薄,塑性愈好或硬度愈低,则合理冲裁间隙愈小.迄今为止,理论计算法尚不能在实际工作中发挥实用价值,但对影响合理间隙值地各因素作定性分析还是很有意义地.2. 查表法在生产实际中,合理间隙值是通过查阅由实验方法所制定地表格来确定地.由于冲裁间隙对断面质量、制件尺寸精度、模具寿命、冲裁力等地影响规律并非一致,所以并不存在一个能同时满足断面质量、模具寿命、尺寸精度及冲裁力地要求地绝对合理地间隙值.因此各行业甚至各工厂所认为地合理间隙值并不一致.一般讲,取较小地间隙有利于提高冲裁件地断面质量和尺寸精度,而取较大地间隙值则有利于提高模具寿命、降低冲裁力.表2.4列出了汽车拖拉机行业常用地较大初始间隙表;表2.5列出了电器仪表行业所用地较小初始间隙数值.表2.4 冲裁模初始双面间隙值Z(汽车拖拉机行业用) mm注:1. 冲裁皮革、石棉和纸板时,间隙取08钢地25%.2. Z min相当于公称间隙.表2.5 冲裁模初始双面间隙值Z(电器仪表行业用) mm注:1. Z min应视为公称间隙.2. 一般情况下,其Z max可适当放大.表中所列Z min和Z max只是指新制造模具初始间隙地变动范围,并非磨损极限.从表中可以发现,当板料厚度t很薄时,Z max-Z min地值很小,以至于现有地模具加工设备难以达到,因此很薄地板料地冲裁工艺性是很差地,对模具地制造精度要求也是很高地.当然,实践中可以在模具结构和模具加工工艺上采取一些特殊措施来满足无(小)间隙冲裁地要求.3. 经验记忆法这是一种比较实用地、易于记忆地确定合理冲裁间隙地方法.其值用下式表达:Z=mt (2-11) 式中:Z——合理冲裁间隙;t——板料厚度;m——记忆系数,参考数据如下:软态有色金属m=4%~8%;硬态有色金属、低碳钢、纯铁m=6%~10%;中碳钢、不锈钢、可伐合金m=7%~14%;高碳钢、弹簧钢m=12%~24%;硅钢m=5%~10%;非金属(皮革、石棉、胶布板、纸板等) m=1%~4%.应当指出,上述记忆系数m值是基于常用普通板料冲裁而归纳总结出来地.各行业各企业对此地选取值是不相同地.在使用过程中还应考虑以下因素:(1)对于制件断面质量要求高地其值可取小些;(2)计算冲孔间隙时比计算落料间隙时其值可取大些;(3)为减小冲裁力其值可取大些;。
- 1、下载文档前请自行甄别文档内容的完整性,平台不提供额外的编辑、内容补充、找答案等附加服务。
- 2、"仅部分预览"的文档,不可在线预览部分如存在完整性等问题,可反馈申请退款(可完整预览的文档不适用该条件!)。
- 3、如文档侵犯您的权益,请联系客服反馈,我们会尽快为您处理(人工客服工作时间:9:00-18:30)。
概括计算原则如下: 概括计算原则如下:
1、 依据 落料 —— 由凹模决定 冲孔 —— 由凸模决定 2、考虑磨损问题 落料时, 落料时,凹模为工件的最小尺寸 冲孔时, 冲孔时,凸模为工件的最大尺寸 3、制模精度 模具精度比零件的精度高2 模具精度比零件的精度高2 ~ 3级,即: 1/3) δ模 =(1/4 ~ 1/3)△件
§2-1 冲裁变形机理
一、冲裁变形过程 二、冲裁力与凸模行程之间的关系曲线 冲裁件( 三、冲裁件(孔)的冲切断面
一、冲裁变形过程
1、弹性变形阶段:材料内压力达到弹性极 弹性变形阶段: 限小于屈服极限。 限小于屈服极限。 特点:挤入部位形成圆角,材料略微弯曲。 特点:挤入部位形成圆角,材料略微弯曲。 ---形成圆角带 形成圆角带。 ---形成圆角带。
§2-2 冲裁间隙值的确定
冲裁间隙: 冲裁间隙:凸凹模刃口工作部分同位尺寸 差称为冲裁间隙(Z) (Z)。 差称为冲裁间隙(Z)。 最小合理间隙值用于设计制造模具, 最小合理间隙值用于设计制造模具,最大 合理间隙用于控制模具寿命。 合理间隙用于控制模具寿命。因此目前 模具制造难点之一就是保证合理均匀的 模具间隙。 模具间隙。 实际间隙是模具制造完成后使用一段时间 后实际度量间隙值。 后实际度量间隙值。
1、理论计算法
Z/2=(tZ/2=(t-h0)*tgβ => Z=2t(1Z=2t(1-h0/t)tgβ
令 K= 2(1-h0/t)tgβ 2(1得: Z = Kt 其中K 其中K值与材料有关
β h0
dp Z/2 Dd t
断裂时剪切深度; h0: 断裂时剪切深度; 刃口尖点连线与垂线之间的夹角; β:刃口尖点连线与垂线之间的夹角; 由于测试技术的限制, 由于测试技术的限制,h0与β之值还不 能准确测定,所以大多采用—— 能准确测定,所以大多采用 经验确定间隙的方法
冲裁间隙(clearance) §2-2 冲裁间隙(clearance)
一、冲裁间隙 二、间隙对冲裁件质量的影响 三、间隙对冲裁力的影响 四、间隙对模具寿命的影响 五、间隙值的确定
一、冲裁间隙
冲裁间隙的定义: 冲裁间隙的定义: 凸凹模刃口工作部分同位尺寸差称为 冲裁间隙(Z) (Z)。 冲裁间隙(Z)。 Z = Dd – Dp 间隙有单、双面之分。 间隙有单、双面之分。
次要有: 次要有: 切口 notching 剖切或切断 parting trimming 修边
冲裁的作用及加工对象
作用有: 作用有: 零件 毛料 part blank
加工对象非常广泛: 加工对象非常广泛: 料厚: 料厚: 0.01 ~ 20(40) 尺寸: 尺寸: 1 x 1 ~ 2000 x 3000 材质: 金属、 材质: 金属、非金属
dp D 工件
0.5 δ p
0.5 △ d
dp 工件
0.5 δ p
0.5Zmin Dd 0.5 δ d 0.5Zmax 落料尺寸的确定 Dd
0.5Zmin 0.5 △ 0.5 δ d 0.5Zmax 冲孔尺寸的确定
各参数的含义: 各参数的含义:
其中: 为凸模的制造尺寸; 其中:dp、Dp为凸模的制造尺寸; 为凹模的制造尺寸; dd、Dd为凹模的制造尺寸; 分别为工件的名义尺寸; D、d分别为工件的名义尺寸; 为工件公差; △为工件公差; Zmax、Zmin为最大最小合理间隙 为最大最小合理间隙; Zmax、Zmin为最大最小合理间隙; 为凸凹模的制造公差, δp、 δd为凸凹模的制造公差, 可查表 可查表确定
(一)、凸、凹模分别加工 )、凸
关键: 关键: —— 如何保证间隙问题? 如何保证间隙问题? 基本原则: 基本原则: 选定模具精度要保证间隙条件 |δp |+|δd| ≤ Zmax – Zmin 或取: 或取: δp = 0.4(Zmax – Zmin) δd = 0.6(Zmax – Zmin)
实际选用时,当材料较薄(t<0.5mm)、 实际选用时,当材料较薄(t<0.5mm)、 较软、制件质量要求较高时应用较小的Z 较软、制件质量要求较高时应用较小的Z; 当材料较厚(t>3mm)、较硬、 当材料较厚(t>3mm)、较硬、制件质量要 求较低时应用较大的Z 求较低时应用较大的Z。 —— 查表法 合理间隙可以查表确定。如表2 合理间隙可以查表确定。如表2-3(P.14)
例题: 例题:
确定凸凹模刃口制造公差: 确定凸凹模刃口制造公差: 规则形状凸凹模制造公差”表得: 查“规则形状凸凹模制造公差”表得: 对于落料: ( Φ35-0.34 ) 对于落料: δp = - 0.020, δd = + 0.030 对于冲孔: 对于冲孔: ( Φ12.5-0.24 ) δp = - 0.020, δd = + 0.020
二、刃口尺寸计算方法
分两种情况讨论: 分两种情况讨论: —— 凸、凹模分别加工 独立制造原则) (独立制造原则) —— 凸、凹模配合加工 协调制造原则) (协调制造原则)
(一)、凸、凹模分别加工 )、凸
独立加工法: 独立加工法: 将凸凹模都标注尺寸和公差, 将凸凹模都标注尺寸和公差,两者分别 按所设计的图纸加工制造, 按所设计的图纸加工制造,各自达到图纸的 公差要求, 公差要求,模具装配后则可获得最小的合理 间隙,采用该种方法制造的模具, 间隙,采用该种方法制造的模具,其间隙是 靠刃口公差来保证的。 靠刃口公差来保证的。
工序 工 序 凸模尺寸 性质 尺寸 Dd=(D-XT-Zmin)落料 DD+ dp=(d+XT)- t 冲孔
△ △
凹模尺寸
δ
t
δ
Dp=(D-XT)+ a dd=(d+XT+Zmin)+ a
δ δ
• K:公差带偏移系数K=1.5 ~ 1.0 公差带偏移系数K=1.5 • 当制件为IT10级以上精度时K=1.0 IT10级以上精度时 当制件为IT10级以上精度时K=1.0 • 当制件为IT11 13级精度时 IT11- 级精度时K=0.75 当制件为IT11-13级精度时K=0.75 • 当制件为IT14级以下精度时K=0.5 当制件为IT14级以下精度时K=0.5 IT14级以下精度时
二、冲裁力与凸模行程关系 曲线) (P – S 曲线)
AB BC C CD D DE —— —— —— —— —— —— 弹性变形 塑性变形 材料的强度极限 裂纹扩展、 裂纹扩展、断裂 裂纹重合 推件
三、冲裁件(孔)的冲切断面 冲裁件(
f △ s h x —— —— —— —— —— 圆角区 光亮带 断裂带 毛刺高度 断面垂直度
例题: 例题:
—— 冲孔模刃口尺寸 冲孔模刃口尺寸 dp=(d+X△)-δp =(12.5+0.5*0.24)-0.02 =12.62-0.02mm dd=(dp+Zmin)+δd =(12.62+0.24)+0.02 =12. 86+0.02mm
(二)、凸、凹模配合加工 )、凸
用途: 用途: —— 薄料(间隙太小,精度无法满足) 薄料(间隙太小,精度无法满足) —— 形状复杂(不能同时满足诸多要求) 形状复杂(不能同时满足诸多要求) 特点: 特点: 以一件为基准加工另一件, 1)以一件为基准加工另一件,保证间隙值 只在基准件上标明尺寸与公差, 2)只在基准件上标明尺寸与公差,且取模 具的δ 具的δ模=1/4△件 模具元件加工精度不高, 3)模具元件加工精度不高,但配合精度高 不能同时加工, 4)不能同时加工,制模周期拉长
§2-3 凸凹模刃口尺寸计算
冲裁模具要得到最小的合理间隙必 须靠正确的设计模具凸凹模刃口尺寸和 确定其制造公差来保证; 确定其制造公差来保证;而这二者的确 定要取决于冲制件的尺寸及精度要求, 定要取决于冲制件的尺寸及精度要求, 取决于合理的间隙值、生产批量、 取决于合理的间隙值、生产批量、模具 的磨损规律、失效机理和加工方法。 的磨损规律、失效机理和加工方法。因 此,确定其刃口尺寸是设计模具的一项 重要任务。 重要任务。
1、模具寿命的表示 2、模具刃口受力分析 3、模具磨损情况
五、间隙值的确定
合理间隙: 合理间隙: Zmin ~ Zmax 保证质量良好、模具寿命长、 保证质量良好、模具寿命长、冲裁力小 Zmin —— 设计 Zmax —— 返修 合理间隙值确定的方法有: 合理间隙值确定的方法有: —— 理论计算法 —— 经验确定法
例题: 例题:
确定垫圈凸凹模刃口尺寸公差 Φ35-0.34 材料:A3钢 材料:A3钢,t=3mm Φ12.5+0.24 解:该件由冲孔落料工序 完成, 可查“ 完成,Z可查“冲裁模 初始间隙”表获得: 初始间隙”表获得: Zmax=0.30; Zmax=0.30;Zmin=0.24; Zmax-Zmin=0.30-0.24=0.06mm; 则:Zmax-Zmin=0.30-0.24=0.06mm;
第二章 冲裁 (Cutting)
冲裁: 冲裁: 是利用冲模使材料分离成两部分的 冲压工序。 冲压工序。如果需要带孔形的那个部分 称为冲孔工序;反之, 称为冲孔工序;反之,如果需要冲落的 哪个外形部分称为落料工序。 哪个外形部分称为落料工序。
冲裁的内容包括
主要有:性变形阶段
特点: 特点:形成明显的剪切光亮带刃口出现微 裂纹---形成挤切光亮带。 ---形成挤切光亮带 裂纹---形成挤切光亮带。
3、段裂分离阶段
—— 裂纹产生、扩展、重合、分离 裂纹产生、扩展、重合、 冲裁过程归纳如下: 冲裁过程归纳如下: 凸模下行 -> 弹性 -> 屈服 -> 塑性区扩展 -> 产生裂纹 -> 裂纹扩展 -> 重合 -> 断裂 -> 推零件入凹模 -> 凸模回升
2、经验确定法
—— 经验公式法 Zmin = K * t 式中: 材料的厚度; 式中: t —— 材料的厚度; 系数;一般与材料性质、 K —— 系数;一般与材料性质、 厚度、制件尺寸精度等有关。 厚度、制件尺寸精度等有关。如: 软材料 K = 0.08 ~ 0.10 中硬料 K = 0.10 ~ 0.12 硬材料 K = 0.12 ~ 0.14