热处理质量控制环节中的问题研究
热处理危险有害因素辨识及控制措施
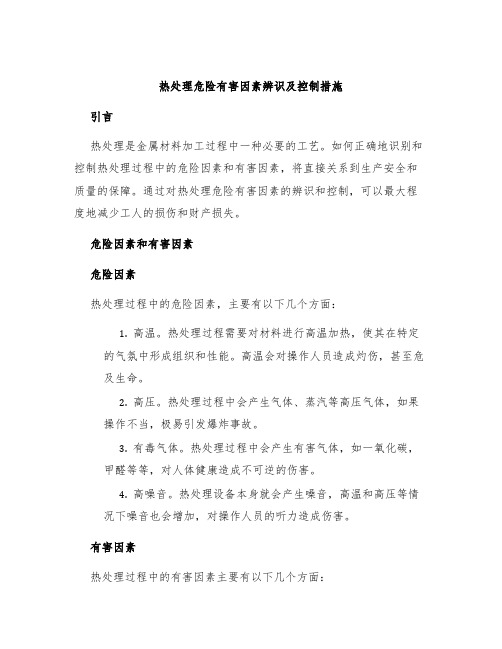
热处理危险有害因素辨识及控制措施引言热处理是金属材料加工过程中一种必要的工艺。
如何正确地识别和控制热处理过程中的危险因素和有害因素,将直接关系到生产安全和质量的保障。
通过对热处理危险有害因素的辨识和控制,可以最大程度地减少工人的损伤和财产损失。
危险因素和有害因素危险因素热处理过程中的危险因素,主要有以下几个方面:1.高温。
热处理过程需要对材料进行高温加热,使其在特定的气氛中形成组织和性能。
高温会对操作人员造成灼伤,甚至危及生命。
2.高压。
热处理过程中会产生气体、蒸汽等高压气体,如果操作不当,极易引发爆炸事故。
3.有毒气体。
热处理过程中会产生有害气体,如一氧化碳,甲醛等等,对人体健康造成不可逆的伤害。
4.高噪音。
热处理设备本身就会产生噪音,高温和高压等情况下噪音也会增加,对操作人员的听力造成伤害。
有害因素热处理过程中的有害因素主要有以下几个方面:1.氧化物。
高温情况下,热处理材料会与空气中的氧气反应,产生一些氧化物,如氧化碳、氮氧化物等。
这些氧化物是一些有害物质,对环境和人体有害。
2.气溶胶。
热处理过程中会产生大量的气溶胶,主要来源于涂层材料和氧化物的挥发。
这些气溶胶会通过呼吸进入人体,对身体造成伤害。
3.感光性物质。
高温下感光性物质易发生光化学反应,产生有害物质,如PM2.5等对人体呼吸系统和心血管系统造成极大的危害。
控制措施为了有效地控制热处理过程中的危险因素和有害因素,需要采取以下措施:1.减少或消除热处理过程中产生的危险因素和有害因素,比如在热处理前要对材料进行预处理,在热处理过程中采取严格的操作流程和规范,控制温度和气氛,减少或消除产生有害气体的可能性。
2.加强个人防护,比如必须穿戴防护服、手套、护目镜等个人防护装置,人员必须接受严格的培训,掌握正确的操作方法和紧急处置措施,加强个人和团队的安全意识。
3.加强对热处理设备的维护,确保设备处于最佳的工作状态,减少设备出现故障和事故的可能性。
钢的热处理实验中存在的问题

钢的热处理实验中存在的问题
钢的热处理是一种常见的工业处理方法,通过改变钢材的组织结构和化学元素的状态来改变其性能,进而满足不同的工业需求。
然而,在进行钢的热处理实验时,可能会遇到以下问题:
一、温度控制不准确
钢的热处理需要在严格的温度控制下进行,以保证其组织结构的改变和化学元素的状态转化达到预期。
但是,由于仪器设备的精度限制、操作人员的技术水平等原因,实验中可能存在温度控制不准确的问题。
这将导致钢材的热处理效果不理想,甚至无法达到预期的目的。
二、时间控制不准确
钢的热处理还需要在一定的时间范围内进行,以保证组织结构的改变和化学元素的状态转化得以完成。
但是,在实验中,可能会存在时间控制不准确的情况,这将影响钢材的热处理效果,使其性能无法满足工业需求。
三、冷却方式不合理
钢的热处理需要在一定的温度下进行冷却,以使钢材的组织结构和化学元素的状态得以稳定。
但是,在实验中,可能会存在冷却方式不合理的情况,如过快或过慢的冷却速度、不同部位采用不同的冷却方式等。
这将使钢材的组织结构和化学元素的状态无法达到理想的稳定状态,从而影响钢材的性能和质量。
四、样品处理不规范
在进行钢的热处理实验时,样品的处理过程需要规范,以保证实验结果的准确性和可重复性。
但是,在实验中,可能会存在样品处理不规范的情况,如样品的制备不均匀、样品的保存不当等。
这将导致实验结果的不可靠性和不确定性,影响钢材的性能和质量评估。
总之,钢的热处理实验中存在的问题主要包括温度控制不准确、时间控制不准确、冷却方式不合理、样品处理不规范等。
为了确保实验结果的准确性和可靠性,需要采取科学、规范、严谨的实验操作和管理措施。
热处理过程质量控制
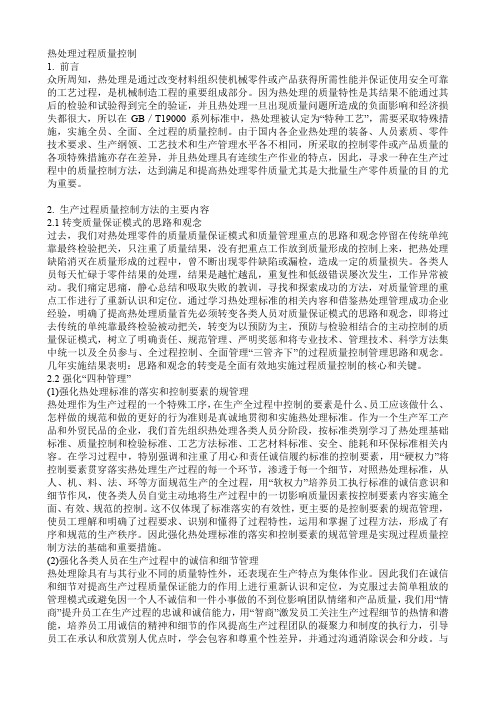
热处理过程质量控制1. 前言众所周知,热处理是通过改变材料组织使机械零件或产品获得所需性能并保证使用安全可靠的工艺过程,是机械制造工程的重要组成部分。
因为热处理的质量特性是其结果不能通过其后的检验和试验得到完全的验证,并且热处理一旦出现质量问题所造成的负面影响和经济损失都很大,所以在GB/T19000系列标准中,热处理被认定为“特种工艺”,需要采取特殊措施,实施全员、全面、全过程的质量控制。
由于国内各企业热处理的装备、人员素质、零件技术要求、生产纲领、工艺技术和生产管理水平各不相同,所采取的控制零件或产品质量的各项特殊措施亦存在差异,并且热处理具有连续生产作业的特点,因此,寻求一种在生产过程中的质量控制方法,达到满足和提高热处理零件质量尤其是大批量生产零件质量的目的尤为重要。
2. 生产过程质量控制方法的主要内容2.1转变质量保证模式的思路和观念过去,我们对热处理零件的质量质量保证模式和质量管理重点的思路和观念停留在传统单纯靠最终检验把关,只注重了质量结果,没有把重点工作放到质量形成的控制上来,把热处理缺陷消灭在质量形成的过程中,曾不断出现零件缺陷或漏检,造成一定的质量损失。
各类人员每天忙碌于零件结果的处理,结果是越忙越乱,重复性和低级错误屡次发生,工作异常被动。
我们痛定思痛,静心总结和吸取失败的教训,寻找和探索成功的方法,对质量管理的重点工作进行了重新认识和定位。
通过学习热处理标准的相关内容和借鉴热处理管理成功企业经验,明确了提高热处理质量首先必须转变各类人员对质量保证模式的思路和观念,即将过去传统的单纯靠最终检验被动把关,转变为以预防为主,预防与检验相结合的主动控制的质量保证模式,树立了明确责任、规范管理、严明奖惩和将专业技术、管理技术、科学方法集中统一以及全员参与、全过程控制、全面管理“三管齐下”的过程质量控制管理思路和观念。
几年实施结果表明:思路和观念的转变是全面有效地实施过程质量控制的核心和关键。
热处理过程中的质量控制
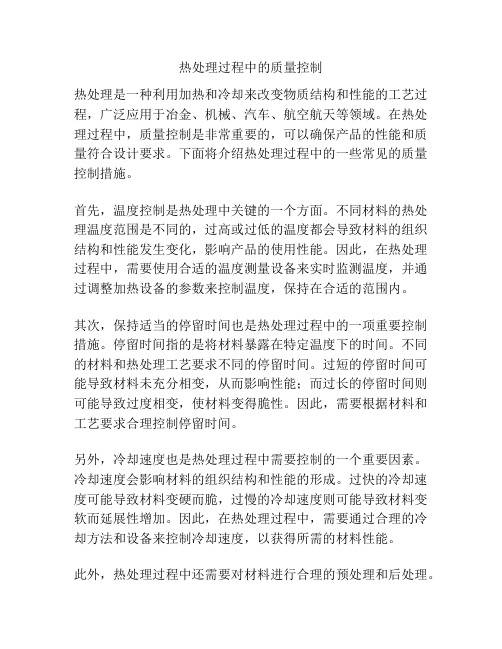
热处理过程中的质量控制热处理是一种利用加热和冷却来改变物质结构和性能的工艺过程,广泛应用于冶金、机械、汽车、航空航天等领域。
在热处理过程中,质量控制是非常重要的,可以确保产品的性能和质量符合设计要求。
下面将介绍热处理过程中的一些常见的质量控制措施。
首先,温度控制是热处理中关键的一个方面。
不同材料的热处理温度范围是不同的,过高或过低的温度都会导致材料的组织结构和性能发生变化,影响产品的使用性能。
因此,在热处理过程中,需要使用合适的温度测量设备来实时监测温度,并通过调整加热设备的参数来控制温度,保持在合适的范围内。
其次,保持适当的停留时间也是热处理过程中的一项重要控制措施。
停留时间指的是将材料暴露在特定温度下的时间。
不同的材料和热处理工艺要求不同的停留时间。
过短的停留时间可能导致材料未充分相变,从而影响性能;而过长的停留时间则可能导致过度相变,使材料变得脆性。
因此,需要根据材料和工艺要求合理控制停留时间。
另外,冷却速度也是热处理过程中需要控制的一个重要因素。
冷却速度会影响材料的组织结构和性能的形成。
过快的冷却速度可能导致材料变硬而脆,过慢的冷却速度则可能导致材料变软而延展性增加。
因此,在热处理过程中,需要通过合理的冷却方法和设备来控制冷却速度,以获得所需的材料性能。
此外,热处理过程中还需要对材料进行合理的预处理和后处理。
预处理包括材料表面的清洁和去除氧化物等处理,以提高热处理的效果。
后处理主要是对热处理后的材料进行调质、淬火、固溶等处理,以进一步改善材料的性能。
对于这些预处理和后处理工艺,需要严格控制各个工艺环节的参数,确保处理效果的稳定性和一致性。
综上所述,热处理过程中的质量控制是确保产品性能和质量的关键。
通过合理控制加热温度、停留时间、冷却速度,以及进行适当的预处理和后处理,可以获得符合设计要求的材料性能和质量。
同时,需要建立完善的质量控制体系,对热处理过程中的各个环节进行监控和记录,以便进行质量追溯和问题分析,不断提升热处理过程的稳定性和一致性。
热处理质量控制和检验
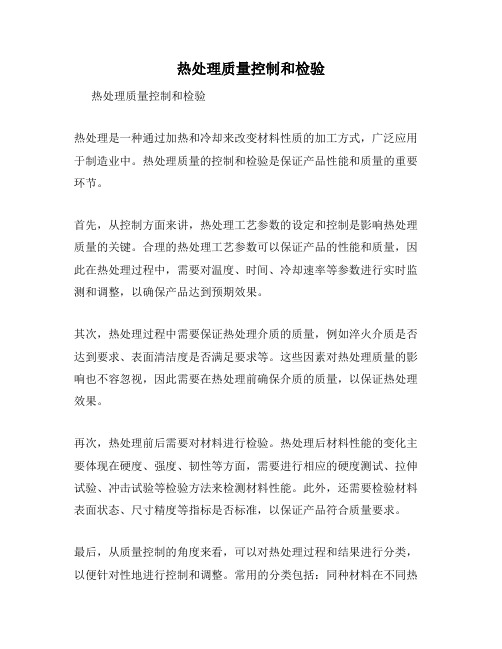
热处理质量控制和检验
热处理质量控制和检验
热处理是一种通过加热和冷却来改变材料性质的加工方式,广泛应用于制造业中。
热处理质量的控制和检验是保证产品性能和质量的重要环节。
首先,从控制方面来讲,热处理工艺参数的设定和控制是影响热处理质量的关键。
合理的热处理工艺参数可以保证产品的性能和质量,因此在热处理过程中,需要对温度、时间、冷却速率等参数进行实时监测和调整,以确保产品达到预期效果。
其次,热处理过程中需要保证热处理介质的质量,例如淬火介质是否达到要求、表面清洁度是否满足要求等。
这些因素对热处理质量的影响也不容忽视,因此需要在热处理前确保介质的质量,以保证热处理效果。
再次,热处理前后需要对材料进行检验。
热处理后材料性能的变化主要体现在硬度、强度、韧性等方面,需要进行相应的硬度测试、拉伸试验、冲击试验等检验方法来检测材料性能。
此外,还需要检验材料表面状态、尺寸精度等指标是否标准,以保证产品符合质量要求。
最后,从质量控制的角度来看,可以对热处理过程和结果进行分类,以便针对性地进行控制和调整。
常用的分类包括:同种材料在不同热
处理工艺下的性能对比、同种材料在相同热处理工艺下的批次性能对比、不同材料在相同热处理工艺下的性能对比等。
总之,热处理质量的控制和检验是制造业中不可或缺的重要环节。
通过对热处理工艺参数的合理控制和材料检验的科学、精细化,保证了产品性能和质量的稳定性和可靠性,为制造业的发展创造了条件。
航空产品热处理的质量检验1张守辉
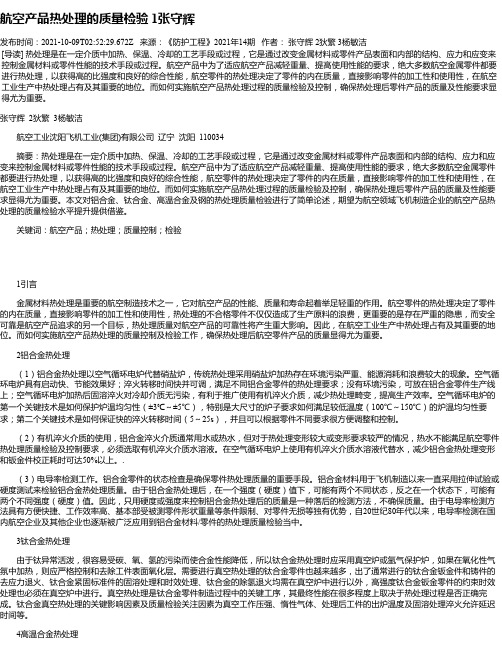
航空产品热处理的质量检验 1张守辉发布时间:2021-10-09T02:52:29.672Z 来源:《防护工程》2021年14期作者:张守辉 2狄繁 3杨敏洁[导读] 热处理是在一定介质中加热、保温、冷却的工艺手段或过程,它是通过改变金属材料或零件产品表面和内部的结构、应力和应变来控制金属材料或零件性能的技术手段或过程。
航空产品中为了适应航空产品减轻重量、提高使用性能的要求,绝大多数航空金属零件都要进行热处理,以获得高的比强度和良好的综合性能,航空零件的热处理决定了零件的内在质量,直接影响零件的加工性和使用性,在航空工业生产中热处理占有及其重要的地位。
而如何实施航空产品热处理过程的质量检验及控制,确保热处理后零件产品的质量及性能要求显得尤为重要。
张守辉 2狄繁 3杨敏洁航空工业沈阳飞机工业(集团)有限公司辽宁沈阳 110034摘要:热处理是在一定介质中加热、保温、冷却的工艺手段或过程,它是通过改变金属材料或零件产品表面和内部的结构、应力和应变来控制金属材料或零件性能的技术手段或过程。
航空产品中为了适应航空产品减轻重量、提高使用性能的要求,绝大多数航空金属零件都要进行热处理,以获得高的比强度和良好的综合性能,航空零件的热处理决定了零件的内在质量,直接影响零件的加工性和使用性,在航空工业生产中热处理占有及其重要的地位。
而如何实施航空产品热处理过程的质量检验及控制,确保热处理后零件产品的质量及性能要求显得尤为重要。
本文对铝合金、钛合金、高温合金及钢的热处理质量检验进行了简单论述,期望为航空领域飞机制造企业的航空产品热处理的质量检验水平提升提供借鉴。
关键词:航空产品;热处理;质量控制;检验1引言金属材料热处理是重要的航空制造技术之一,它对航空产品的性能、质量和寿命起着举足轻重的作用。
航空零件的热处理决定了零件的内在质量,直接影响零件的加工性和使用性,热处理的不合格零件不仅仅造成了生产原料的浪费,更重要的是存在严重的隐患,而安全可靠是航空产品追求的另一个目标,热处理质量对航空产品的可靠性将产生重大影响。
热处理工业炉存在的问题

热处理工业炉存在的问题
热处理工业炉在运行过程中可能存在以下问题。
1.温度控制不准确:热处理工业炉需要对温度进行精确控制,以保证工件的热处理效果。
然而,在实际操作过程中,温度控制可能受到许多因素的影响,如炉内气氛、加热速度、设备老化等,导致温度控制不准确。
2.炉内气氛不良:热处理工业炉在进行热处理过程中,需要保持炉内气氛的稳定性。
然而,炉内气氛可能受到各种因素的影响,如燃料燃烧不完全、炉内氧气含量过高、炉内气氛调节不当等,导致炉内气氛不良,从而影响工件的热处理质量。
3.设备老化:热处理工业炉经过长时间的使用,设备可能出现老化现象,如炉膛磨损、加热元件损坏、温度传感器失灵等。
这些老化现象可能导致炉子性能下降,影响热处理的质量和效率。
4.能源利用率低:热处理工业炉的能源利用率直接影响到生产成本和环境保护。
然而,部分热处理炉在设计和操作过程中可能存在能源利用率低的问题,如燃料燃烧不充分、热量损失较大等。
5.自动化程度不高:随着工业生产自动化程度的提高,对热处理工业炉的自动化要求也越来越高。
然而,部分热处
理炉在自动化方面可能存在不足,如控制系统不完善、自动化设备故障频发等,导致生产效率低下。
6.安全隐患:热处理工业炉在高温、高压、有毒等环境下运行,存在一定的安全隐患。
如设备老化、安全防护措施不到位、操作不规范等,可能导致事故发生。
为了解决上述问题,需要对热处理工业炉进行定期维护和检查,提高设备的自动化程度,加强操作人员的安全培训,改进炉内气氛调节技术,提高能源利用率,以确保热处理工业炉的正常运行和热处理质量。
热处理中的热处理质量控制技术

热处理中的热处理质量控制技术热处理是一种重要的工业过程,它可以对金属材料进行加工和改变其性能。
在进行热处理时,确保热处理质量的一致性和稳定性是至关重要的。
这就需要运用热处理质量控制技术来确保产品质量。
热处理的质量控制技术可以从多个方面来考虑。
其中最重要的是,要把控热处理温度、时间和处理环境。
这些因素直接影响热处理后材料的性质和质量。
首先,热处理温度是影响热处理效果的最重要因素。
温度不合适会导致材料内部结构与性能发生剧烈变化,从而造成热处理质量不稳定。
温度的过高或过低都会对热处理质量产生影响。
技术人员需要根据不同的材料特性和所需热处理效果,确定合适的温度范围,来确保热处理的稳定性和一致性。
其次,热处理时间也是影响热处理质量的关键因素之一。
热处理时间短,则材料的性能可能无法完全改变;热处理时间长则会导致材料过度脆化或淬火不完全等情况。
因此,需要技术人员进行热处理时间的调整和控制,以确保热处理量的一致性和稳定性。
最后,处理环境也是影响热处理质量的重要因素之一。
在热处理过程中,处理环境会直接影响材料硬度、韧性等性能。
例如在淬火工艺中,冷却介质的选择直接决定了淬火后的结构和性能。
因此,技术人员需要掌握不同材料对处理环境的要求,并进行相应的调整和控制,以确保热处理产品质量的稳定性。
总之,热处理中的热处理质量控制技术是确保产品质量和稳定性的关键。
需要技术人员具备精湛的技术和丰富的经验,通过合理的温度、时间、处理环境等热处理参数的控制,来确保热处理的一致性和稳定性。
同时,还要注重设备的维护和保养,不断提高热处理质量控制技术的水平和精度。
只有如此才能保证热处理产品的质量和竞争力。
热处理变形产生的原因及控制方法
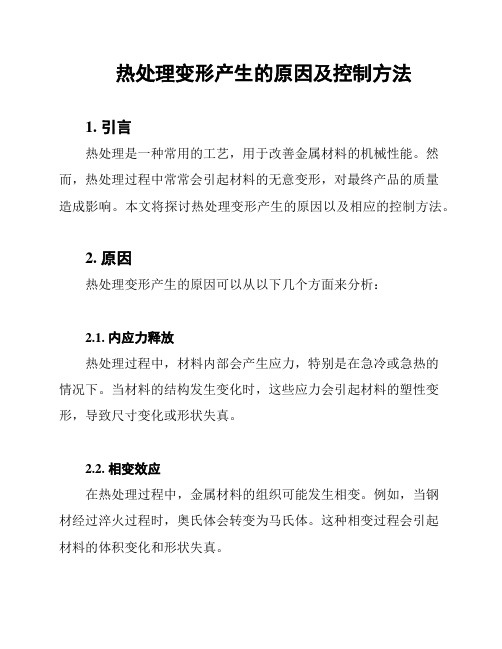
热处理变形产生的原因及控制方法1. 引言热处理是一种常用的工艺,用于改善金属材料的机械性能。
然而,热处理过程中常常会引起材料的无意变形,对最终产品的质量造成影响。
本文将探讨热处理变形产生的原因以及相应的控制方法。
2. 原因热处理变形产生的原因可以从以下几个方面来分析:2.1. 内应力释放热处理过程中,材料内部会产生应力,特别是在急冷或急热的情况下。
当材料的结构发生变化时,这些应力会引起材料的塑性变形,导致尺寸变化或形状失真。
2.2. 相变效应在热处理过程中,金属材料的组织可能发生相变。
例如,当钢材经过淬火过程时,奥氏体会转变为马氏体。
这种相变过程会引起材料的体积变化和形状失真。
2.3. 不均匀加热或冷却如果热处理过程中加热或冷却不均匀,材料的局部温度会存在差异。
这种温度差异会导致材料的非均匀膨胀或收缩,从而引起变形。
3. 控制方法为了减少热处理产生的变形,可以采取以下控制方法:3.1. 控制加热和冷却速率合理控制加热和冷却速率,避免过快或过慢,可以减少材料的变形。
在进行急冷或急热处理时,可以采取预先控制的温度梯度,以缓解内应力的释放。
3.2. 优化工艺参数通过调整热处理过程中的工艺参数,如温度、时间和冷却介质等,可以最大限度地减少材料的变形。
合理选择工艺参数,可以提高材料的均匀性和稳定性。
3.3. 采用合适的支撑结构对于形状复杂的工件,可以采用合适的支撑结构来减少变形。
支撑结构可以提供一定的约束,防止材料发生不受控制的变形。
4. 结论热处理变形是热处理过程中常见的问题,但通过合理的控制方法可以有效减少其影响。
合理控制加热和冷却速率、优化工艺参数以及采用合适的支撑结构都是减少热处理变形的有效途径。
这些控制方法可以提高最终产品的质量和性能。
---以上是关于热处理变形产生的原因及控制方法的内容。
请基于以上内容,进一步完善和添加具体细节,使文档达到800字以上的要求。
热处理过程质量控制
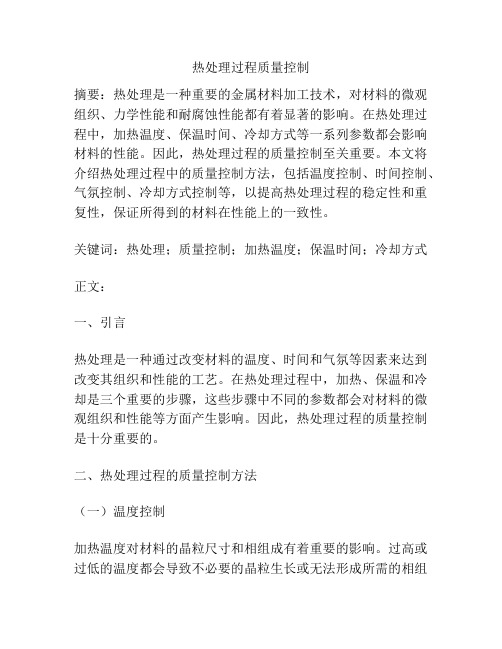
热处理过程质量控制摘要:热处理是一种重要的金属材料加工技术,对材料的微观组织、力学性能和耐腐蚀性能都有着显著的影响。
在热处理过程中,加热温度、保温时间、冷却方式等一系列参数都会影响材料的性能。
因此,热处理过程的质量控制至关重要。
本文将介绍热处理过程中的质量控制方法,包括温度控制、时间控制、气氛控制、冷却方式控制等,以提高热处理过程的稳定性和重复性,保证所得到的材料在性能上的一致性。
关键词:热处理;质量控制;加热温度;保温时间;冷却方式正文:一、引言热处理是一种通过改变材料的温度、时间和气氛等因素来达到改变其组织和性能的工艺。
在热处理过程中,加热、保温和冷却是三个重要的步骤,这些步骤中不同的参数都会对材料的微观组织和性能等方面产生影响。
因此,热处理过程的质量控制是十分重要的。
二、热处理过程的质量控制方法(一)温度控制加热温度对材料的晶粒尺寸和相组成有着重要的影响。
过高或过低的温度都会导致不必要的晶粒生长或无法形成所需的相组织。
因此,温度控制是热处理工艺的重要措施。
在热处理过程中,需要使用一定的温度计来测量加热炉中的温度,并通过调节加热功率、炉膛气氛等因素来控制温度。
同时,由于温度计的精度和可靠性也会对热处理过程的控制产生影响,因此,在进行质量控制时还需要对温度计的准确性进行验证。
(二)时间控制保温时间对材料的组织和性能都有着显著的影响。
过短的保温时间会导致晶粒尺寸过大、相组成不稳定等现象,而过长的保温时间则可能使晶粒长大甚至出现烧结现象。
因此,在热处理的保温过程中,需要精确控制保温时间,同时需要考虑不同材料的特性以及不同的热处理工艺对保温时间的影响。
(三)气氛控制气氛控制是热处理过程中不可忽视的一个环节。
不同的气氛组成会影响材料的表面形貌和结构组成,进而影响材料的性能。
例如,在氧化性气氛中进行热处理可能会造成表面氧化,影响热处理的效果。
因此,在进行热处理时需要选择合适的气氛,并对气氛进行精确控制,以保证热处理后所得到的材料具有理想的表面形貌和组织结构。
热处理质量控制
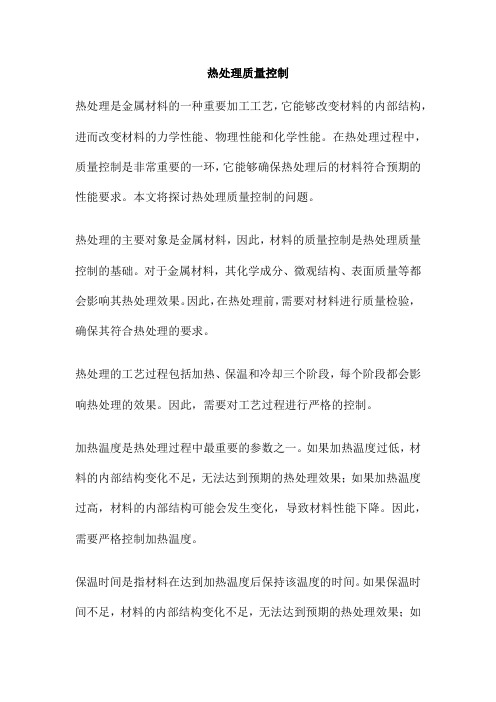
热处理质量控制热处理是金属材料的一种重要加工工艺,它能够改变材料的内部结构,进而改变材料的力学性能、物理性能和化学性能。
在热处理过程中,质量控制是非常重要的一环,它能够确保热处理后的材料符合预期的性能要求。
本文将探讨热处理质量控制的问题。
热处理的主要对象是金属材料,因此,材料的质量控制是热处理质量控制的基础。
对于金属材料,其化学成分、微观结构、表面质量等都会影响其热处理效果。
因此,在热处理前,需要对材料进行质量检验,确保其符合热处理的要求。
热处理的工艺过程包括加热、保温和冷却三个阶段,每个阶段都会影响热处理的效果。
因此,需要对工艺过程进行严格的控制。
加热温度是热处理过程中最重要的参数之一。
如果加热温度过低,材料的内部结构变化不足,无法达到预期的热处理效果;如果加热温度过高,材料的内部结构可能会发生变化,导致材料性能下降。
因此,需要严格控制加热温度。
保温时间是指材料在达到加热温度后保持该温度的时间。
如果保温时间不足,材料的内部结构变化不足,无法达到预期的热处理效果;如果保温时间过长,材料的内部结构可能会发生变化,导致材料性能下降。
因此,需要严格控制保温时间。
冷却速度是指材料从加热温度冷却到室温的速度。
如果冷却速度过快,可能会导致材料内部产生应力,影响其力学性能;如果冷却速度过慢,可能会导致材料内部结构发生变化,影响其性能。
因此,需要严格控制冷却速度。
热处理设备是实现热处理工艺的重要工具,设备的性能和状态直接影响到热处理的效果。
因此,需要对设备进行定期的维护和保养,确保设备的正常运行。
环境因素也会影响热处理的效果,例如温度、湿度和空气流动速度等。
因此,需要对环境进行控制,以避免其对热处理效果的影响。
为了保证热处理质量,需要对热处理后的材料进行检测和记录。
检测内容包括材料的化学成分、微观结构、力学性能等。
记录内容包括热处理的工艺参数、设备运行状态和环境因素等。
通过对检测结果和记录的分析,可以找出热处理过程中存在的问题和不足之处,为改进热处理工艺提供依据。
热处理过程中的质量控制
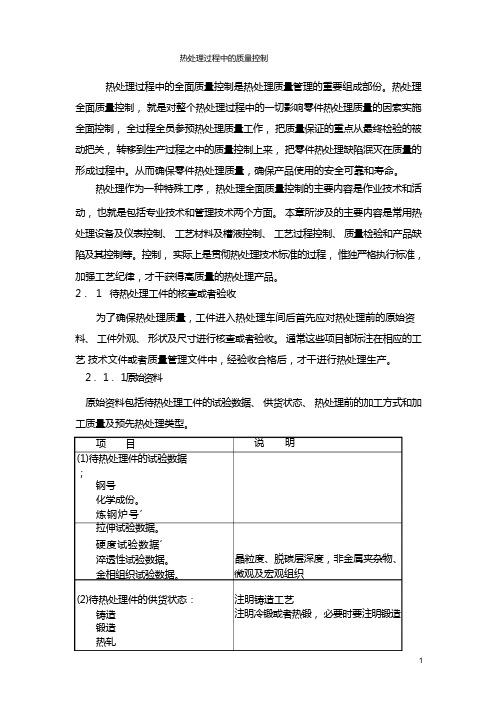
热处理过程中的质量控制热处理过程中的全面质量控制是热处理质量管理的重要组成部份。
热处理全面质量控制, 就是对整个热处理过程中的一切影响零件热处理质量的因索实施 全面控制, 全过程全员参预热处理质量工作, 把质量保证的重点从最终检验的被 动把关, 转移到生产过程之中的质量控制上来, 把零件热处理缺陷泯灭在质量的 形成过程中。
从而确保零件热处理质量,确保产品使用的安全可靠和寿命。
热处理作为一种特殊工序, 热处理全面质量控制的主要内容是作业技术和活 动, 也就是包括专业技术和管理技术两个方面。
本章所涉及的主要内容是常用热 处理设备及仪表控制、 工艺材料及槽液控制、 工艺过程控制、 质量检验和产品缺 陷及其控制等。
控制, 实际上是贯彻热处理技术标准的过程, 惟独严格执行标准, 加强工艺纪律,才干获得高质量的热处理产品。
2. 1 待热处理工件的核查或者验收为了确保热处理质量,工件进入热处理车间后首先应对热处理前的原始资 料、 工件外观、 形状及尺寸进行核查或者验收。
通常这些项目都标注在相应的工艺 技术文件或者质量管理文件中,经验收合格后,才干进行热处理生产。
2. 1. 1原始资料原始资料包括待热处理工件的试验数据、 供货状态、 热处理前的加工方式和加 工质量及预先热处理类型。
说 明晶粒度、脱碳层深度,非金属夹杂物、 微观及宏观组织注明铸造工艺注明冷锻或者热锻, 必要时要注明锻造比项 目 (1)待热处理件的试验数据;钢号化学成份。
炼钢炉号’ 拉伸试验数据。
硬度试验数据’ 淬透性试验数据。
金相组织试验数据。
(2)待热处理件的供货状态:铸造 锻造 热轧冷拔项 目 说 明(3)待热处理件热处理前的加土方式:切削方法及切削量。
冲压或者拉制 冷轧或者冷挤压 焊接热校正或者冷校正。
(4)待热处理件的预先热处理类型: 正火(或者正火回火)彻底退火 球化退火去应力退火 . 调质注:对普通工件,有*号的项目可以省略。
2024年石油化工建设施工现场焊接及热理质量控制(三篇)
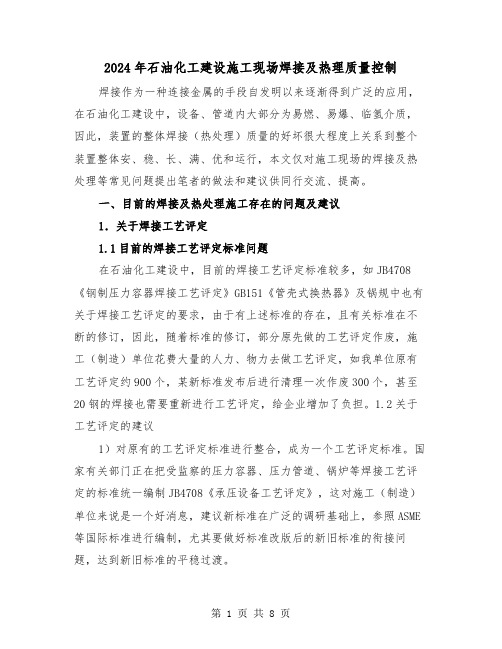
2024年石油化工建设施工现场焊接及热理质量控制焊接作为一种连接金属的手段自发明以来逐渐得到广泛的应用,在石油化工建设中,设备、管道内大部分为易燃、易爆、临氢介质,因此,装置的整体焊接(热处理)质量的好坏很大程度上关系到整个装置整体安、稳、长、满、优和运行,本文仅对施工现场的焊接及热处理等常见问题提出笔者的做法和建议供同行交流、提高。
一、目前的焊接及热处理施工存在的问题及建议1.关于焊接工艺评定1.1目前的焊接工艺评定标准问题在石油化工建设中,目前的焊接工艺评定标准较多,如JB4708《钢制压力容器焊接工艺评定》GB151《管壳式换热器》及锅规中也有关于焊接工艺评定的要求,由于有上述标准的存在,且有关标准在不断的修订,因此,随着标准的修订,部分原先做的工艺评定作废,施工(制造)单位花费大量的人力、物力去做工艺评定,如我单位原有工艺评定约900个,某新标准发布后进行清理一次作废300个,甚至20钢的焊接也需要重新进行工艺评定,给企业增加了负担。
1.2关于工艺评定的建议1)对原有的工艺评定标准进行整合,成为一个工艺评定标准。
国家有关部门正在把受监察的压力容器、压力管道、锅炉等焊接工艺评定的标准统一编制JB4708《承压设备工艺评定》,这对施工(制造)单位来说是一个好消息,建议新标准在广泛的调研基础上,参照ASME 等国际标准进行编制,尤其要做好标准改版后的新旧标准的衔接问题,达到新旧标准的平稳过渡。
2)像工艺评定这样的标准要具有相对稳定性,而且要尽量和ASME这样的国际标准接轨,以适应国内企业承包国际工程的需要。
3)目前对于工艺评定的规定过死,各家均单独进行工艺评定,这样浪费了大量的人力、物力,对于国内的大型企业(如同为石化工程承包一级企业)可考虑对工艺不太特殊的工艺评定进行资源共享。
2.关于焊工2.1焊工对于保证工程的焊接质量起着至关重要的作用,因此,焊工的技术水平高低可以反映一个企业的焊接水平的高低,但目前普遍存在的问题是焊工执行工艺卡不严格,甚至有些焊工见不到焊接工艺卡,焊工只凭自己的经验施焊,尤其是对一些要求严格控制焊接能量的钢种,焊接质量得不到保证。
热处理过程中的质量控制范文

热处理过程中的质量控制范文热处理是一种改变金属材料组织结构和性质的方法。
在实际的生产过程中,热处理起到了至关重要的作用。
对于热处理过程,除了掌握热处理的基本原理和技术方法,还需要对热处理过程中的质量控制有深刻的认识,并采用科学的方法进行操作。
本文将介绍热处理过程中的质量控制范文。
热处理中的质量控制1.原材料的入库检验:在进行热处理过程之前,需要对原材料进行入库检验。
入库检验的主要目的是对原材料的质量状况进行了解、评估和记录,确保原材料的质量符合相关的要求,从而为后续的生产过程提供可靠的保障。
2.加热温度的控制:在进行热处理过程时,需要控制金属的加热温度。
加热温度的高低直接影响金属组织的性质和质量,因此加热温度的控制至关重要。
为了保证加热温度的准确性,通常采用温度控制器进行控制。
对于一些高要求的产品,还需要进行多点测温,确保加热过程中的温度均匀性。
3.保温时间的控制:在进行热处理过程时,需要设定保温时间。
保温时间的长短对产品的性质和质量也有很大的影响。
通常采用定时器进行控制。
为了确保产品的稳定性和均匀性,需要进行多点测温,并根据测量结果进行适当的调整。
4.冷却速率的控制:在进行热处理过程之后,需要对金属材料进行冷却。
冷却速率的快慢直接影响金属的组织结构和性质,并会对产品的质量产生直接的影响。
对于不同的金属材料,需要采用不同的冷却方式和速率。
常见的冷却方式有自然冷却、水冷却、油冷却等。
在进行冷却过程时,需要控制冷却速率,确保冷却过程的稳定性和均匀性。
5.存储和运输控制:在进行热处理过程之后,需要对产品进行存储和运输。
存储和运输控制是产品实际应用中的最后一道质量控制环节,也是非常重要的一环。
在进行存储和运输控制时,需要对产品的尺寸、重量、形状等进行严格的检验,并采用合适的包装材料,确保产品不会在运输过程中发生意外情况。
总结热处理是一种重要的加工和处理方法,质量控制是热处理过程中不可或缺的一部分。
通过对原材料的入库检验、加热温度的控制、保温时间的控制、冷却速率的控制和存储和运输控制等方面的质量控制,可以最大程度地保证产品的质量,从而为用户提供更好的产品体验。
热处理质量报告

热处理质量报告
1. 背景
本报告旨在详细记录热处理过程中的质量控制情况,以确保产品质量符合要求。
2. 热处理流程
2.1 加热
- 使用加热设备将待处理材料加热至指定温度。
- 控制加热速率,确保温度均匀升高。
2.2 保持时间
- 在指定温度保持一段时间,使得材料结构发生所需的变化。
- 保持时间根据不同材料和处理要求而定。
2.3 冷却
- 快速冷却材料以固定结构并提高硬度。
- 控制冷却速率,以确保性能的稳定性。
3. 质量控制
3.1 温度监控
- 在整个加热和保持过程中,使用温度计对温度进行实时监控。
- 记录温度变化曲线,以评估加热和保持的稳定性。
3.2 保持时间控制
- 使用定时器或计时器精确记录保持时间。
- 确保保持时间达到规定要求。
3.3 冷却控制
- 使用冷却剂进行快速冷却,确保结构固定。
- 控制冷却速率,避免快速冷却导致材料脆性增加。
3.4 样品测试
- 从处理过的材料中提取样品进行一系列测试。
- 测试项目包括硬度、韧性、拉伸强度等,以验证热处理效果。
4. 结论
通过详细记录热处理过程,并进行质量控制措施,确保热处理质量符合要求。
各项质量控制步骤的监控和记录有助于追溯和评估热处理效果,提高产品安全性和可靠性。
以上是热处理质量报告的内容,希望对您有所帮助。
如有任何问题或需要进一步信息,请随时与我们联系。
谢谢!。
热处理设备维修与管理现存问题及改进建议分析

【 关键词 】 热 处理 设备 维修 i 管理 i 问题 改进 【 中图分类号 】 F 4 0 6 【 文献标识码 】 A 【 文章编号 】 2 0 9 5 — 2 0 6 6 ( 2 0 1 5 ) 2 0 — 0 3 2 2 — 0 2
不 可控 制 , 致 使 生 产任 务 不 能 热 处理 设 备 的 维修 和 管 理 .从 某 种 程 度 上 来 说 可 以 划分 队伍 进 行 维 修 。 修 理 周 期 较 长 . 到 一 类 工 作 中 ,但 由 于 目前 讲 究 精 细 化 和 专 业 化 的 工作 。 因 按 计 划 节点 完成 。 其次 . 生 产调 度 以 生产 任 务 为 首 位 , 不 关心 、
1 热处理设备维修 与管理现存 问题
热 处 理 设 备 是 众 多机 械 设 备 中 比较 高 端 的 一 项 .在 很 多
工业 中都 具 有 较 强 的 应 用。 现 阶 段 常 用 的 热 处 理设 备 包 括 箱
式电阻炉、 井式回火炉( 渗碳 炉) 、 真空淬火炉、 真 空退 火 炉 等 。 从 客 观 的 角度 来分 析 . 由 于 热 处 理 设 备 的 应 用频 率 较 高 , 所以
前 的热 处理 设备 在 应 用 过 程 中 , 维 修 比较 单 一 , 无 法将 问题 从 根 源 上 解 决 ; 管理 方面, 对热 处 理 设 备 的 管 理 流 于 表 面 , 主 观 上和 客 观 上 的 问题 , 都 不 能较 好 的 处理 , 直 接 影 响到 了最 终 的工 作 效 率 。 热 处理 设 备 是 很 多 工 业 生 产 、 加 工中的重点设备 , 应 通 过 积 极 的维 修 手段 、 健 全 的管 理 手
皮带机主轴热处理质量控制的若干思考

皮带机主轴热处理质量控制的若干思考皮带机一直以来都是我厂主打产品之一,近年来,我厂承接了一大批大型皮带机生产任务。
在这些大型皮带机上其主要传动轴直径普遍超过300mm,长度超过3000mm,在对此类主轴质量的控制中,我厂通过多次的探索总结了一些实用的方法。
皮带机主轴属于传动件,在工作过程中要承受复杂载荷(如扭转、弯曲、拉压、冲击等)的作用,并经受强烈摩擦,是皮带机中性能要求较高的零件。
因此,必须对该轴的机械性能进行强化处理,即调质热处理。
调质能使零件获得良好的综合力学性能,能够提高零件的强度、塑性和韧性。
由于皮带机主轴的直径较大,长度较长,在调质淬火时表面与心部冷却速度冷却顺序和冷却速度的差异,使表面和心部存在温度和组织差异,产生了热应力和组织压力。
如果主轴内部存有少许组织缺陷,很容易造成淬火断裂和弯曲变形,一旦造成断裂或严重弯曲变形,带来的后果一方面是工件报废,给生产带来重大损失,另一方面如果出现隐性内裂现象,可能会存在巨大安全隐患,甚至造成机毁人亡的事故。
因此必须对大型皮带机主轴热处理的质量控制。
1 产生质量问题的原因分析从材料学的观点看,工件之所以产生裂纹、断裂和弯曲变形现象除了工件材质存在杂质、气孔、组织不均匀等缺陷外,主要由于材料所承受的应力超过了材料本身的破断抗力。
因此,我们从热处理淬火加热时的应力及材料回火的应力两方面分析:1.1 淬火应力大型工件热处理淬火过程中的应力主要由热应力、组织应力及由于截面上转变组织比容不同引起的应力。
(1)热应力是在热处理过程中,工件表面和中心由于加热或冷却速度不一,导致体积膨胀不均匀而产生的内应力。
对于大型轴类工件,从高温快速冷却时表面冷却得快,心部冷却得慢,内外存在较大的温差。
由于表面先冷必然收缩,而心部有较高温度比热阻止其收缩,即心部使表面受拉,表面对心部产生压力。
但是,钢在高温塑性阶段屈服强度低,塑性变形后应力将得到松弛,当外部先进入弹性阶段形成冷硬外壳后,将对心部收缩产生阻碍作用。
23mnb履带板热处理质量控制的研究
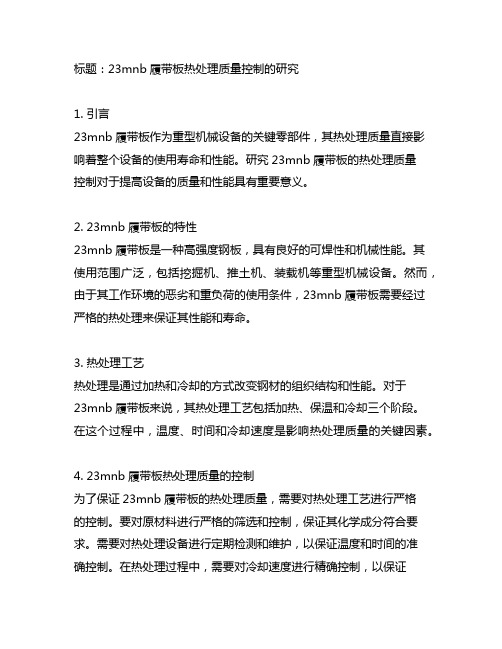
标题:23mnb履带板热处理质量控制的研究1. 引言23mnb履带板作为重型机械设备的关键零部件,其热处理质量直接影响着整个设备的使用寿命和性能。
研究23mnb履带板的热处理质量控制对于提高设备的质量和性能具有重要意义。
2. 23mnb履带板的特性23mnb履带板是一种高强度钢板,具有良好的可焊性和机械性能。
其使用范围广泛,包括挖掘机、推土机、装载机等重型机械设备。
然而,由于其工作环境的恶劣和重负荷的使用条件,23mnb履带板需要经过严格的热处理来保证其性能和寿命。
3. 热处理工艺热处理是通过加热和冷却的方式改变钢材的组织结构和性能。
对于23mnb履带板来说,其热处理工艺包括加热、保温和冷却三个阶段。
在这个过程中,温度、时间和冷却速度是影响热处理质量的关键因素。
4. 23mnb履带板热处理质量的控制为了保证23mnb履带板的热处理质量,需要对热处理工艺进行严格的控制。
要对原材料进行严格的筛选和控制,保证其化学成分符合要求。
需要对热处理设备进行定期检测和维护,以保证温度和时间的准确控制。
在热处理过程中,需要对冷却速度进行精确控制,以保证23mnb履带板的组织结构和性能达到设计要求。
5. 个人观点和理解对于23mnb履带板的热处理质量控制,我认为需要从原材料到热处理工艺再到质量检测环节,都需要严格控制。
只有这样,才能保证产品的质量和性能达到设计要求。
还需要不断的进行研究和改进,以适应不断变化的市场需求和技术发展。
6. 总结通过对23mnb履带板热处理质量控制的研究,可以得出结论:热处理工艺是影响23mnb履带板质量和性能的关键因素,需要进行严格控制。
只有通过不断的研究和改进,才能保证产品的质量和性能达到最佳状态。
以上是对23mnb履带板热处理质量控制的研究的一些润色内容。
希望对你有所帮助。
热处理质量控制是23mnb履带板生产过程中至关重要的一环。
在23mnb履带板的生产过程中,热处理工艺是其制造过程中不可或缺的一部分。
P91管道热处理过程控制及常见问题控制

P91管道热处理过程控制及常见问题控制摘要:本文针对乙烷制乙烯项目裂解炉超压蒸汽管线P91钢管进行了热处理工艺实践,制定合格的P91焊接工艺评定,过程中通过对预热和层间温度的严格监控,焊后马氏体转变、合格的后热处理以及焊后热处理的控制,得到优质合格性能的P91焊接接头。
关键词:P91钢管;热处理工艺;预热;马氏体转变;焊后热处理引言:P91 我国于1995年将该钢列入GB5310标准中,牌号为10Cr9Mo1VNb。
该钢的特点是在9Cr1Mo钢中加入少量V、Nb,控制N和Al含量,降低C含量。
该钢具有高温强度高、抗氧化性能和抗蠕变性能好等特点,在我国石化行业和电力行业得到广泛的应用。
该钢进行焊后热处理的目的是降低焊接接头的残余应力,改善焊缝及热影响区组织,使淬硬组织得到回火处理,从而提高焊缝及热影响区的性能。
焊后热处理温度过高会促使碳化物积聚和长大,降低焊接接头的强度,热处理温度过低达不到回火的效果,因而严格的热处理工艺控制是确保P91焊接接头性能的保障。
1、P91钢焊接热处理原理P91钢作为新型马氏体耐热钢,具有良好的高温持久强度、热稳定性和高温抗蠕变能力,经过焊接后的P91钢焊接接头,要达到和保留P91钢优良的综合性能非常困难,由于火电焊接作业大部分在施工现场进行,焊缝熔池金属的加热熔化和冷却结晶属于“焊接小冶金”,没有该钢材在制造过程中的“提纯冶炼、控轧控冷加工”等条件。
为了保障P91钢的焊接后性能达到优质合格的焊接接头,必须严格执行经过焊接工艺评定确定的施工程序和工艺参数,加强过程监控措施。
焊前预热是防止P91钢产生焊接冷裂纹的最有效措施之一。
预热可降低焊接应力,减缓焊后冷却速度,有利于焊缝金属中扩散氢的逸出,避免产生氢导致裂纹。
同时,也可减少焊缝及热处理影响区的淬硬程度,提高焊接接头的抗裂性。
层间温度控制从防止冷裂纹产生、细化晶粒、提高韧性等诸方面考虑。
为避免过热组织出现,有效保障P91钢焊接接头综合力学性能。
热处理产品质量的主要影响因素及其控制
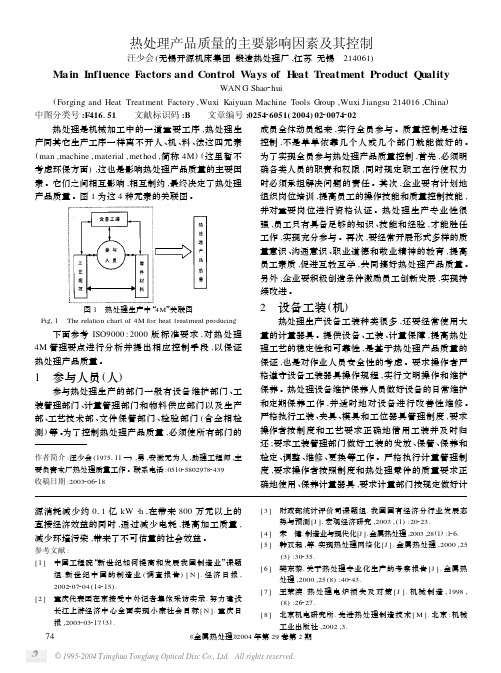
热处理产品质量的主要影响因素及其控制汪少会(无锡开源机床集团锻造热处理厂,江苏无锡 214061)Main Influence F actors and Control W ays of H eat T reatment Product Q ualityWAN G Shao 2hui(Forging and Heat Treatment Factory ,Wuxi Kaiyuan Machine Tools Group ,Wuxi Jiangsu 214016,China )中图分类号:F416151 文献标识码:B 文章编号:025426051(2004)022******* 热处理是机械加工中的一道重要工序,热处理生产同其它生产工序一样离不开人、机、料、法这四元素(man ,machine ,material ,method ,简称4M )(这里暂不考虑环保方面),这也是影响热处理产品质量的主要因素。
它们之间相互影响,相互制约,最终决定了热处理产品质量。
图1为这4种元素的关联图。
图1 热处理生产中“4M ”关联图Fig 11 The relation chart of 4M for heat treatment producing下面参考ISO9000:2000版标准要求,对热处理4M 管理要点进行分析并提出相应控制手段,以保证热处理产品质量。
1 参与人员(人)参与热处理生产的部门一般有设备维护部门、工装管理部门、计量管理部门和物料供应部门以及生产部、工艺技术部、文件保管部门、检验部门(含金相检测)等。
为了控制热处理产品质量,必须使所有部门的作者简介:汪少会(1975111—),男,安徽无为人,助理工程师,主要负责本厂热处理质量工作。
联系电话:0510258029782439收稿日期:2003206218成员全体动员起来,实行全员参与。
质量控制是过程控制,不是单单依靠几个人或几个部门就能做好的。
- 1、下载文档前请自行甄别文档内容的完整性,平台不提供额外的编辑、内容补充、找答案等附加服务。
- 2、"仅部分预览"的文档,不可在线预览部分如存在完整性等问题,可反馈申请退款(可完整预览的文档不适用该条件!)。
- 3、如文档侵犯您的权益,请联系客服反馈,我们会尽快为您处理(人工客服工作时间:9:00-18:30)。
热处理质量控制环节中的问题研究
作者:关春辉
来源:《中国新技术新产品》2018年第04期
摘要:热处理质量控制环节是制造厂生产活动中质量保证体系中的最基本环节之一,热处理工艺质量的好坏会直接影响到出厂产品的质量和性能。
所以对于一个制造厂商来说,必须要重视热处理质量控制的相关环节。
一般热处理质量控制环节主要包括对热处理过程控制、热处理工艺的控制和热处理进行分包时对分包方质量的控制。
笔者在这里结合自己的实践经验对热处理质量控制环节中存在的一些问题进行剖析,希望以后在生产中可以更好地规避这些问题。
关键词:热处理;质量控制环节;问题研究
中图分类号:TG158 文献标志码:A
热处理质量控制环节作为压力容器制造质量控制中所不可或缺的一环,是TSGZ0004—2007《特种设备制造、安装、改造、维修质量保证体系基本要求》中规定的18个基本要素之一。
但是在压力容器制造厂的实际的生产活动中,各个制造厂在关于压力容器的热处理质量控制环节中仍然存在诸多的问题,总的来说出现的这些问题大致可以归结为4个方面。
在这里,我们就针对这四方面来具体地谈一谈在热处理质量控制环节中存在的问题。
1 热处理的具体操作手段没有达到相关法规的规定标准
对于压力容器的制造来说,在其生产的具体的过程中,需要用到的热处理种类一共有3个,分别是成形受压元件的焊后热处理、恢复性能热处理和改善材料力学性能热处理。
而在具体的生产实践中,制造厂商对产品的焊后热处理一般都能够按照事先的规定进行规范化的操作,但是对成形受压元件的恢复性能热处理和改善材料力学性能热处理却不够重视,其操作过程也往往不能够达到规定的标准。
例如:现有一台按照GB150.3—2011的标准进行设计的压力容器,其筒节的材质是
Q345R,其规格是φ450×24mm。
另外其筒节的冷成形变形率(%)=50×δ[1-(Rf/Ro)]/Rf,算式中:Rf=237mm,δ=24mm,Ro为∞,将数值带入可以计算出该压力容器的筒节冷成形变形率(%)为5.06%。
这一数值超出了GB150表4中的数值范围,所以对于该压力容器的筒节来说,应该在成型受压处理之后,再经过相应的恢复性能热处理过程来恢复材料的力学性能。
但是在实际的操作中,笔者发现许多的制造厂在筒节冷卷成形之后,并没有再进行必要的相关的恢复性能热处理过程。
而是选择在焊接步骤之后再进行筒节的恢复性能热处理。
制造商的这种选择在焊接处理之后再进行恢复性能热处理是不合理的。
对于金属材料来说,一旦经过冷加工变形处理之后,其自身的性能都会发生比较大的变化,对于碳素钢来说更是如此。
在进行冷加工变形处理的过程中,伴随着塑性变形量的不断增大,其自身的等轴晶组织会顺着金属整体的变形而发生伸长变化。
随着金属整体上变形量较大的时候,其等轴晶组织则会逐渐变成纤维状。
如此一来金属硬度和内应力相应的就会变大,但是金属的可塑性也会随之降低,这就是所谓的金属加工过程中的“加工硬化”现象。
而恢复性能的热处理工艺则可以很好地恢复金属材料的力学性能,很好地规避因“加工硬化” 而带来的不良后果。
但是若是在不进行恢复性能的热处理的情况下,而选择提前进行焊接处理,这样一来极容易因焊接过程中出现金属因受热不均匀而出现塑性应变现象。
这样一来可能会使得等轴晶体之间产生一些不可逆的拉伸变化而对母材的性能造成伤害。
所以建议恢复性能热处理还是要在焊接处理之前进行比较妥当。
2 对热处理工艺的编制存在的缺陷
关于热处理过程的最短保温时间的设定是所有存在于热处理工艺中的问题中最为突出的一个。
在NB/T47015《压力容器焊接规程》中推荐了一些热处理工艺中的最短保温时间的设定。
具体的热处理的时间的长短是由焊后热处理厚度来决定的。
而焊后热处理的厚度有时取决于焊缝的厚度,也有时取决于母材的厚度。
而在具体的热处理时间的相关选择中有规定,当存在两块相邻的受压元件时,其母材厚度的数值参照其中相对较薄的一块的母材的厚度值。
而在接管与法兰相互焊接的时候,其焊接厚度值取接管颈在接头处的焊缝厚度。
但是在进行具体的焊接工作的时候,相关的工作人员往往都不太注意这些方面的细节,从而设置的热处理时间并不符合科学规定的标准。
3 热处理过程中的控制问题
(1)对热处理炉的有效加热区的测定工作中存在的问题
在实际的生产过程中,许多的生产商在进行热处理的时候,根本就没有对热处理炉的有效加热区进行有效的测定,即使有些厂家测定了,但是其测定的方法也并不合理。
一般情况下,生产商对热处理炉的有效加热区测定时所采用的方法参照的是GB/T9452—2003《热处理炉有效加热区测定方法》。
但是GB/T9452—2003的方法针对的是周期式箱式热处理炉,这种热处理炉的最大长度为5m,最大宽度为1.5m。
但是所使用的热处理炉的长度和宽度都已经远远的超出了这个范围,在这种情况下,相关的生产单位还在按照过去的那套旧的标准在执行,自然达不到很好的效果。
因而相关的生产方应该根据新时代的具体的生产实际需要(如:API Spec 8C 标准中附录B 热处理设备的鉴定指南,就有对热处炉的鉴定的具体要求),制定出科学的热处理炉的有效加热区的测定方法。
(2)在热电偶的校验和敷设过程中所出现的问题
在实际的热处理炉测温工作中,经常会出现没有按照相关的规定对热电偶进行科学合理的计量检定。
同时热处理过程中,热敷设电偶的时候,由于并没有严格地按照NB/T47015《压力容器焊接规程》中的相关规定执行,而致使热电偶的脱落,进一步影响到了热处理炉测温工作的最终测量结果。
(3)在进行工件装炉的时候,工作态度不够严谨
通常在进行工件装炉的时候,需要工作人员拥有一个严谨认真的态度,确保将工件都放在有效加热区的范围之内,这也是进行有效加热区测定工作的意义所在。
但是在实际的操作中,许多的工作人员根本就没有有效加热区的概念,只是按照工作的需要,随意地将工件放在加热炉之中。
其实许多的工件却并没有放在有效的加热区之内,并没有起到对工件进行有效的热处理的目的。
4 在热处理分包环节中存在的质量控制问题
(1)没有对分包方的工作能力进行科学的评估
许多生产单位由于工作的需要,往往在没有对分包方的具体的工作能力进行一个严格测评的情况下,武断地将工件的热处理工作外包。
双方之间只是简单地签订一份协议,并没有实地的去考察分包方的加热炉设备是否符合实际生产的需要。
(2)没有对分包单位热处理过程进行必要的监督和检查
通常在当事人双方签订协议的时候,协议中有规定可以定期对分包单位的具体工作进行监督和检查,但是实际上,相关的工作人员在思想上并没有意识到热处理工作的重要性。
通常情况下都不会去认真地对分包单位的工作进行监督,有时即使监督了,也仅仅是浮于形式,并没有深入到具体的工作细节当中去。
结语
热处理质量控制是热容器制造过程中极为重要的一个环节,需要相关的制造单位给予充分的重视。
但是在实际的工作中,笔者发现热处理工作并没有达到尽善尽美,其具体的工作流程当中存在着诸多的纰漏,需要进一步改进。
总体来说,导致这些问题的原因大致来自两方面,一是相关的工作人员的工作态度不认真,二是一些具体的工艺手段落后。
所以今后相关的生产单位应该从这两方面来努力改进,进而更好地规避以上提到的这些问题。
参考文献
[1]马容忠,周国华.热处理质量控制环节存在的问题[J].中国特种设备安全,2012(12):36-38.
[2]马容忠,周国华.浅谈热处理质量控制环节存在的问题[J].中国化工装备, 2013(1):45-48.。