汉莎表面处理检验标准
表面处理通用检验标准
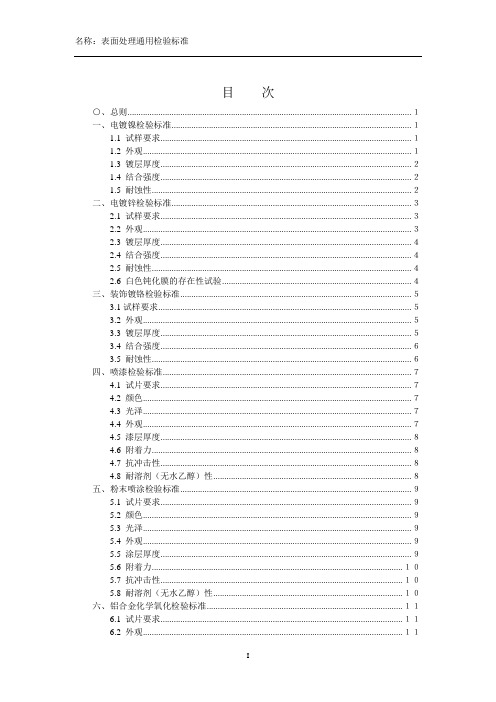
目次○、总则................................................................................................................................. 1一、电镀镍检验标准............................................................................................................. 11.1 试样要求.................................................................................................................. 11.2 外观.......................................................................................................................... 11.3 镀层厚度.................................................................................................................. 21.4 结合强度.................................................................................................................. 21.5 耐蚀性...................................................................................................................... 2二、电镀锌检验标准............................................................................................................. 32.1 试样要求.................................................................................................................. 32.2 外观.......................................................................................................................... 32.3 镀层厚度.................................................................................................................. 42.4 结合强度.................................................................................................................. 42.5 耐蚀性...................................................................................................................... 42.6 白色钝化膜的存在性试验...................................................................................... 4三、装饰镀铬检验标准......................................................................................................... 53.1试样要求................................................................................................................... 53.2 外观.......................................................................................................................... 53.3 镀层厚度.................................................................................................................. 53.4 结合强度.................................................................................................................. 63.5 耐蚀性...................................................................................................................... 6四、喷漆检验标准................................................................................................................. 74.1 试片要求.................................................................................................................. 74.2 颜色.......................................................................................................................... 74.3 光泽.......................................................................................................................... 74.4 外观.......................................................................................................................... 74.5 漆层厚度.................................................................................................................. 84.6 附着力...................................................................................................................... 84.7 抗冲击性.................................................................................................................. 84.8 耐溶剂(无水乙醇)性.......................................................................................... 8五、粉末喷涂检验标准......................................................................................................... 95.1 试片要求.................................................................................................................. 95.2 颜色.......................................................................................................................... 95.3 光泽.......................................................................................................................... 95.4 外观.......................................................................................................................... 95.5 涂层厚度.................................................................................................................. 95.6 附着力.................................................................................................................. 105.7 抗冲击性.............................................................................................................. 105.8 耐溶剂(无水乙醇)性...................................................................................... 10六、铝合金化学氧化检验标准......................................................................................... 116.1 试片要求.............................................................................................................. 116.2 外观...................................................................................................................... 116.3 耐蚀性.................................................................................................................. 11七、铝合金喷砂光亮阳极化检验标准............................................................................. 127.1 试片要求.............................................................................................................. 127.2 外观...................................................................................................................... 127.3 氧化膜厚度.......................................................................................................... 127.4 耐蚀性.................................................................................................................. 127.5 封闭质量.............................................................................................................. 12八、喷砂及拉丝检验标准................................................................................................. 138.1 拉丝件.................................................................................................................. 138.2 喷砂件.................................................................................................................. 13表面处理通用检验标准○、总则0.1 零部件表面处理前应去除毛刺、飞边、划痕、氧化层等缺陷,锐边棱角倒钝。
表面处理检验标准
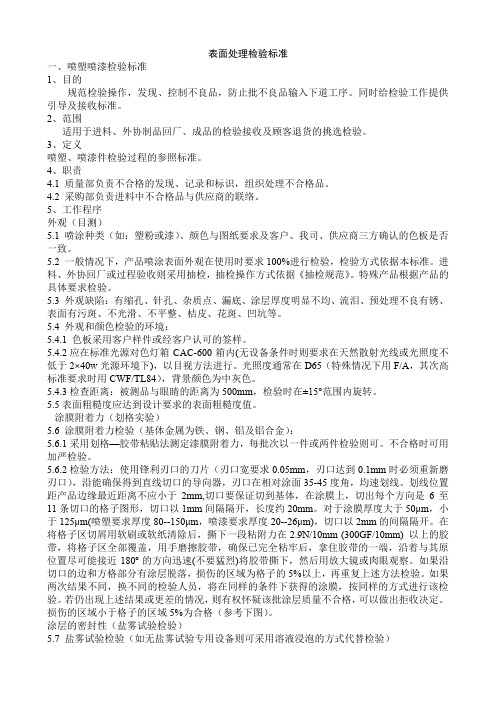
表面处理检验标准一、喷塑喷漆检验标准1、目的规范检验操作,发现、控制不良品,防止批不良品输入下道工序。
同时给检验工作提供引导及接收标准。
2、范围适用于进料、外协制品回厂、成品的检验接收及顾客退货的挑选检验。
3、定义喷塑、喷漆件检验过程的参照标准。
4、职责4.1 质量部负责不合格的发现、记录和标识,组织处理不合格品。
4.2 采购部负责进料中不合格品与供应商的联络。
5、工作程序外观(目测)5.1 喷涂种类(如:塑粉或漆)、颜色与图纸要求及客户、我司、供应商三方确认的色板是否一致。
5.2 一般情况下,产品喷涂表面外观在使用时要求100%进行检验,检验方式依据本标准。
进料、外协回厂或过程验收则采用抽检,抽检操作方式依据《抽检规范》。
特殊产品根据产品的具体要求检验。
5.3 外观缺陷:有缩孔、针孔、杂质点、漏底、涂层厚度明显不均、流泪、预处理不良有锈、表面有污斑、不光滑、不平整、桔皮、花斑、凹坑等。
5.4 外观和颜色检验的环境:5.4.1 色板采用客户样件或经客户认可的签样。
5.4.2应在标准光源对色灯箱CAC-600箱内(无设备条件时则要求在天然散射光线或光照度不低于2×40w光源环境下),以目视方法进行。
光照度通常在D65(特殊情况下用F/A,其次高标准要求时用CWF/TL84),背景颜色为中灰色。
5.4.3检查距离:被测品与眼睛的距离为500mm,检验时在±15°范围内旋转。
5.5表面粗糙度应达到设计要求的表面粗糙度值。
涂膜附着力(划格实验)5.6 涂膜附着力检验(基体金属为铁、钢、铝及铝合金):5.6.1采用划格—胶带粘贴法测定漆膜附着力,每批次以一件或两件检验则可。
不合格时可用加严检验。
5.6.2检验方法:使用锋利刃口的刀片(刃口宽要求0.05mm,刃口达到0.1mm时必须重新磨刃口),沿能确保得到直线切口的导向器,刃口在相对涂面35-45度角,均速划线。
划线位置距产品边缘最近距离不应小于2mm,切口要保证切到基体,在涂膜上,切出每个方向是6至11条切口的格子图形,切口以1mm间隔隔开,长度约20mm。
表面处理检验规范
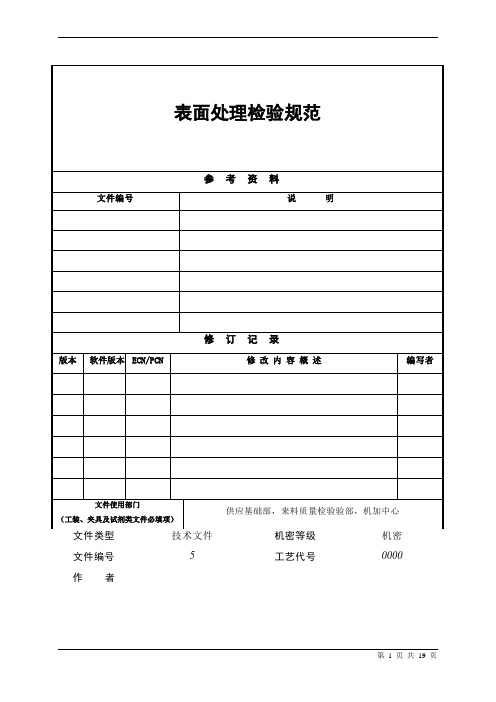
文件编号5工艺代号0000作者第 1 页共19 页表面处理检验规范1适用范围本规范适用于电镀、氧化、化学处理、喷塑、喷漆、喷砂、拉丝等金属表面处理的检验。
2术语和定义2.1 A级表面:在使用过程中总能被客户看见的部分(如:面壳的正面和顶面,后壳的顶面,手柄,透镜,按键及键盘正面,探头整个表面等)。
2.2 B级表面:在使用过程中常常被客户看见的部分(如:面壳的左右侧面,底壳或后壳的左右侧面及背面等)。
这些表面允许有轻微不良,但是不致引起挑剔客户不购买产品。
2.3 C级表面:在使用过程中很少被客户注意到的表面部分(如:面壳的底面,底壳或后壳的底面,内部零件表面)。
此表面的外观缺陷应合理而且不至于给客户觉得该产品质量不佳。
2.4 金属表面:包括电镀、氧化、钝化等表现为金属质感的表面,非喷涂表面。
2.5 基材花斑:电抛光、电镀或氧化前因基体材料腐蚀、或者材料中的杂质、材料微孔等原因所造成的、与周围材质表面不同光泽或粗糙度的斑块状花纹外观。
2.6 抛光区:对基材上的腐蚀、划伤、焊接区、铆接区等部位进行机械打磨抛光后表现出的局部高光泽、光亮区域。
2.7 浅划痕:镀(膜/塑/漆)层表面划伤,但未伤及底层(即底层未暴露);对其它无镀(膜/塑/漆)层表面则为:目测不明显、手指甲触摸无凹凸感、未伤及材料本体的伤痕。
数控冲床加工中机床台面对板材的摩擦产生的轻微痕迹属于此类划痕。
2.8 深划痕:镀(膜/塑/漆)层表面划伤,且已伤至底层(即底层已暴露出来);对其它无镀(膜/塑/漆)层表面则为:目测明显、手指甲触摸有凹凸感、伤及材料本体的伤痕。
2.9 凹坑:由于基体材料缺陷,或在加工过程中操作不当等原因而在材料表面留下的小坑状痕迹。
2.10 凹凸痕:因基材受撞击或校形不良等而呈现出的明显变形、凹凸不平的现象,手摸时有不平感觉。
2.11 烧伤:拉丝、电抛光、电镀处理时因操作不当、造成零件表面过热而留下的烧蚀痕迹。
2.12 水印:电镀、氧化或电抛光后因清洗水未及时干燥或干燥不彻底所形成的斑纹、印迹。
表面处理工艺及检验标准

目录表面处理工艺规程 (1)表面磷化工艺规程 (1)表面电镀工艺规程 (3)表面发黑处理工艺规程 (12)表面淬火处理工艺规程 (17)金属表面处理检验规程 (19)表面磷化处理检验规程 (19)表面电镀检验规程 (20)表面发黑处理检验规程 (23)高频淬火检验规程 (24)一、表面处理工艺规程1、表面磷化工艺规程122.表面镀铬工艺规程2.1镀铬浴的分类2. 1.1 铬酸—硫酸浴(Sargent浴)2. 1.2 氟化物含有浴氟化物含有浴硅氟化物含有浴硼氟化物含有浴2.1.3 铬酸钠浴2.1.4 硫酸铬浴2.1.5 黑色铬浴2.2 Sargent浴(1)浴成分与组成Sargent浴的成分为铬酸及触媒的硫酸,单独的铬酸溶液无法镀铬,但加1种或2种以上的酸根为触媒在阴极帮助的还原析出时,即可电镀.触媒根可用硫酸盐和氟化物,硫酸盐有硫酸、硫酸铬等,指化物有氟酸、氟化铵、氟化钠、氟化钾、硅氟化钠、硅氟酸、硼氟酸之类的错氟化物.铬酸与硫酸的配合比在镀铬的析出条件中很重要,CrO3:SO4在50:1~200:1之间,大致要保持100:1的比例,触媒根用1种以上时,要计算全量,此时,相当于以触媒效果与硫酸根相等的当量计算的值之总计.因而,Sargent浴的标准浴组成为铬酸250g/ι、硫酸2.5g/ι,现在使用铬酸100g/ι的低浓度到400~500g/ι的高浓度浴.镀铬浴在建浴时,溶解铬酸(CrO3,无水铬酸)250g/ι,加100:1的2.5g/ι硫酸即可,但铬酸常混有少量硫酸,故须相对减少硫酸的添加量.无水铬酸为红褐色的片状结晶,很易溶解水中,入水后搅拌速溶.铬酸与硫酸量是以分析决定,铬酸量可由比重得知概略,标准液大致是玻美21度.如此建浴的铬酸一硫酸溶液为深红色透明液,由此溶液电镀也得不到满足的镀铬,但电解后变成稍不透明的暗红色液,比重也成玻美22~23度.理由是CrO3因电解而还原,液中局部生成3价铬,此3价铬的存在对镀铬有极重要的影响,含有3价铬的溶液才能得满足的镀铬.镀铬液须含有3价铬,除了电解而还原生成以外,也可直接添加草酸(10g/ι成2.75g/ιCr³)柠檬酸、碳酸铬、氢氧化铬等还原剂还原,但以电解生成法最好,下为药品还原法的式子一例.2CrO3+3(HCOO)2→Cr2O3+6CO2+3H2O 电解生成法的两极用铅板,在开始析出铬的电流密度电解.浴温越高或硫酸根越多越快,例如浴温60℃、以10A/dm²的阳极电流密度电解100小时生在约3g/ι的3价铬宜为2~3g/ι,设为5g/ι以下,此量不宜过多或过少,液中须保持约3g/ι,这关连硫酸量与阳极.(2)浴成分的作用Sargent浴的浴成分为铬酸、硫酸(触媒根)、3价铬,无水铬酸溶于水,CrO3+H2O«H2CrO4,成为铬酸液,再如H2CrO4«2H+SO4电离,此SO4²¯使铬酸的一部份成为硫酸铬(Cr(SO4)3),Cr(SO4)3«2Cr³⁺+3SO4²¯.也可为硫酸以外的酸或硫酸盐,但不宜用有氧化作用的酸、溶解阳极铅的酸—硝酸、盐酸、醋酸、磷酸或其盐.最好用有还原性的酸,诸如硼酸、氟酸或其盐、错盐等.有机酸虽有还原性,但会与铬酸作用而分解,所以只用于3价铬的生成.金属盐除了铬盐之外,会增加其它金属成分,所以不大使用.在以上的浴成分,液中有H⁺、4²¯、Cr⁺、SO4²¯存在,3价铬量多时,因此组成而暗色较强,成不透明,比重增高,适当的组成为250 CrO3‧3Cr2O3.镀铬的析出机构有各种假说,假说经下示过程.1. Cr⁶⁺→Cr³⁺→Cr⁺2. Cr⁶⁺→Cr³⁺→Cr²⁺→Cr⁺3. Cr⁶⁺→Cr⁺有Sargent等研究,尚无定说,下面概述一例.将铬酸水溶液电解的话,在阴极还原铬酸,如下产生3价铬和游离碱.HCrO4¯+3H2O+3⊖→Cr³⁺+7OH2H2CrO4-3⊕→Cr(OH)CrO4+3OH¯3价铬成为盐基性铬酸铬的不导性薄膜,包覆阴极,其后不还原铬酸,此皮膜为微孔性,通过此微孔,只离子半径小的H放电.在阳极是氧放,电只引起水的分解.但是,液中若有硫酸或氟酸之类的阴离子,此离子很小,藉静电引力被拉入铬酸铬此膜的微孔中,接触盐基成分,溶解皮膜分子,同时生成Cr³,皮膜有孔的话, HCrO4¯径此孔到达极,引起上式的反应,皮膜再生,但在此皮膜反复溶解再生的同时,往Cr³还原,并发生氢,此3价铬直接或径2价铬的阶段析出金属铬.3价铬的存在不直接关连铬的电着机构,但影响光泽电流密度范围、液电阻、包覆力等.(3)电镀条件(a)铬酸浓度的影响铬酸浓度的标准为250g/ι实际有100g/ι的低浓度浴到400~500g/ι的高浓度浴,高浓度浴与低浓度浴的差异不大明显,分别有下示特色:高浓度浴低浓度浴光泽稍劣良包覆力稍劣良硬度低高电流效率劣良液电阻小稍高镀层的外观关连浴温与电流密度变方,可得良好镀金的浴温和电流密度的范围大致一定,铁、镍素地上镀铬的浴温与电流密度的关系,浴温一定时,电流密度低处为乳白色,增大电流密度时,即成光泽电镀范围.增大电流密度时,成为灰色.光泽范围因素地种类而稍有不同,在镀镍上较小,在铜、黄铜上较大,由此图可知,光泽电镀范围在低温移到低电流密度,在高温移到高电流密度范围,但低温时,光泽范围减小,周边部容易发生灰色部,高温时,需要大电流的光泽差,故用45~55℃的范围.欲得无裂纹的镀铬时要在55~60℃之间.铁、镍素地上的电流密度为浴温(℃) 标准电流密度(A/dm²)50 20~3555 30~50浴温的1/2~2/3值为电流密度范围.镀铬发生的列纹在电镀初期为针孔状,不发生裂纹,随着镀层厚度的增大,裂纹会生长,大致在0.25~0. 5μ以内尚无裂纹.裂纹数受浴温与电流密度影响,在CrO3 250g/ι、H2SO4 2.5g/ι的浴中,随浴温的上升及电流密度的增加而减少裂纹数.内部应力因浴温的影响而大变,在20 A/dm²的电流密度,在40℃最小,密着性良好.电镀速度取决于浴温、电流密度,电流效率值在一般用条件下约为5~20%,此范围为光泽电镀范围.电镀速度在普通浴的浴温50℃、电流密度30时,析出1μ所需时间约2分半,1小时约成25μ的厚度,在同一浴温,电镀速度并非正比于电流密度,电流效率随电流密度的增加而激增.铬酸浓度增大时,比较两图,可知电镀速度、电流效率都下降.这些电镀速度、电流效率值是在电流均匀分布于被镀阴极全体的条件下决定,在实际的电镀作业条件中,铬的均匀电着性不良,电流很少均匀分布于复杂物品全体.损失于吊架等的电流也占某种比率,所以电镀速度或电流效率在实际作业中未必完全一致,但使电镀条件接近试验条件的话,但使电镀条件接近试验条件的话,平均值适用此值.(4)镀浴的管理铬酸因掏出、铬的析出、飞散、铬酸铅的生面而消耗,但因阴极用不溶性极,可由阴极溶解而补充,而且摇出量极多,在装饰镀铬作业中约达7成,飞散所致的消耗约占2成,因而,铬酸的洗净回收及飞沬防止剂可防止消耗.铬酸的被给量是将浴中的铬量定量而决定,现场是每日测定比重,推定消费量,因液中含有3价铬或铁分等而增高比重,所以实际为玻美23~24,配合比重测定,每月化学分析1~2次,可维持铬量.硫酸因掏出、飞散而消耗,但不因铬酸的析出或铬酸铅的生成而消费,所以消费率小于铬酸.硫酸分是藉分析决定,将钡所致的沉淀离心沈淀的迅速3、表面发黑处理工艺规程常温发黑处理工艺,主要由以下工艺步骤完成:1)清洗;2)脱脂:工件必须完全浸入脱脂液中;脱脂液浓度ph值12-14,处理时间10-30min,每过3-5分钟上下抖动几次,药液浓度低于ph12时补充脱脂粉;3)水洗;4)酸洗:酸洗液浓度ph值2-4,处理时间5-10min;5)水洗;6)发黑:池液浓度ph值2.5-3.5,处理时间10-12min;7)水洗;8)吹干;9)上油。
表面处理检验规范

镀种
膜厚
判定标准
检验依据
缺点 区分
1锌
蓝白锌 白锌 彩锌
1.附着力:将铁块用2公斤以上的力砸 到产品上检查产品镀层面不可有起皮 脱皮现象(破坏性测试)
目视
5~10um
2.盐雾测试:用浓度为5%氯化钠盐
水,水温度为35±1℃连续喷雾,喷12 供应商提供盐 小时保温12小时,被腐蚀面不可有红锈 雾测试报告
进料检验规范
表面处理 检验规范
文件编号 文Leabharlann 版本 制定日期文件页次1. 目 的:为确保本公司表面处理产品在进料检验过程中有依据可循;
2.适用范围:适用于本公司烤漆,喷漆,电著,镀(锌、镍)产品膜厚检验;
3.权 责:品管单位负责制定、执行和修订。
4.作业内容:(抽样水数:每批产品抽样3~5PCS)
序 号
MA
生成
黑镍 2 镍 一般镍
化学镍
3~8um 3~5um
3.电镀膜厚:用电解式膜厚测试仪,测 试要求符合膜厚标准即可
供应商提供电 镀膜厚测试报
告
烤 3喷
漆
粉体漆 液体漆
40~150um
10~60um
4.附着力 7.光泽度
4 电 著 5~12um
5.耐腐蚀性 8.耐磨性
6.膜厚
喷漆件SIP MA
备注:以上检验相关测试报告由供货商提供,如有特殊要求除外.
核准
审核
制定
表面处理检验标准

表面处理检验标准 Prepared on 22 November 2020
表面处理检验标准一.目的:统一检验标准,明确目标,降低不良批次,及时供应生产出货。
二.相关部门:弘南科品质部,采购部,各表面处理协力厂商。
三.适用产品:公司所有外发表面处理加工零配件,半成品。
四.检查标准:
(1)等级定义:A面:产品的主要面或直观面。
B面:产品的次要面。
(2)外观要求:喷油加工:A面不能有积油,流纹,透底,磨花,划伤,颜色不匀,发白等现象,尘点,杂点A面≤1个,直径≤;B面不能有明显积油,流纹,透底,磨花,划伤,颜色不匀,发白等现象,尘点,杂点≤2个,直径≤。
丝印加工:字迹要清晰,不能有字体变形,飞边,模糊,线条粗细字体大小不一,丝印不完整等现象。
(3)附着力测试:喷油件以百格刀在表面划6*6个1mm*1mm小网格,电镀件表面划6*6个2mm*2mm小网格,丝印件不用划,以3M600或3M610胶带平整压在测试面上并压紧,使其100%牢牢附于测试面上,然后呈90度角迅速拉起,如此三次,测试面脱落总面积小于5%为合格。
(4)颜色检验:以我司签样为标准,颜色偏差不能太明显,同一批料不能有色差,同一批次相配合件不能有色差。
丝印颜色要与签样颜色一致或相近。
(5)功能检测:外发加工产品结构不能损坏,喷油不能过厚以致影响装配,有热熔脚位的地方要注意,熔脚位要尽量避免喷到油,以防影响热熔。
(6)所有来料抽检不良超过3%为不合格。
五.未尽事项,在产品加工时另做要求。
核准:品质:采购:厂商确认:。
表面处理检测规范

产品表面处理检测规范一耐盐雾试验能力1 试验标准:耐盐雾试验能力,盐雾试验的条件,遵循国家标准GB/T10125-1997 ;①氯化钠溶液浓度:50/- 1℅G/L (按照质量百分比计算);②PH值:6.5-7.2 ③试验温度:35/-20C2 条件描述:④喷雾量:1.0-2.0 ML/80cm2/h ⑤试验温度≥85RH ⑥测试压强:1.0kgf/cm2 ⑦驻留时间:48小时,试样后流动温水清洗,清洗水温度<400C ①表面镀蓝白锌钝化,镀层8um,DIN 50961-Fe/Zn 8 B gl-Cr Vi Free passivated耐盐雾试验48小时(镀锌,没有特殊说明一律为镀蓝白锌)②表面镀铬,DIN EN12540-GD Zn/Cu 8 Ni 10 b Crr 耐盐雾试验48小时(没3 结果要求:有特殊说明一律为镀亮铬)③表面镀镍,DIN EN 12540-Fe/Cu5/Ni 10 s耐盐雾试验12小时④表面电泳漆,E-Coating耐盐雾试验48小时(没有特殊说明一律为亚光)⑤表面喷粉,Black Coated耐盐雾试验48小时二耐磨耗试验①负重:530G ②工作行程:5-40mm1 试验条件:③工作速率:10-60 往返/分④2H铅笔⑤橡皮或者带有酒精的摩擦头A:耐磨耗试验最少20000次2 结果要求:B:硬度2H三附着力测试①白格刀1 试验条件:②Scotch胶带2 结果:表面处理100℅不能脱离四外观检测1 表面镀层符合规定要求光滑、平整、均匀光亮,同批产品无色差(注:色差包括颜色和光泽度)(1)起泡:镀层与基体因局部剥离致表面呈气泡现象;(2)脱皮:镀层与基体有剥离现象;镀层成片状脱离基体材料的现象(3)烧焦:在过高电流下形成的颜色黑暗、粗糙、松散等质量不佳的沉积物,其中常含有氧化物或其他杂质。
(4)麻点:在电镀或腐蚀中,与金属表面上形成的小坑或小孔(5)粗糙:在电镀过程中,由于种种原因造成的镀层粗糙不光滑的现象。
表面处理检验标准

用戒刀在批次样板上划10*10MM的方格,9*9=81个,
然后用进口封口胶贴平压紧,然后再用力撕下,掉粉面积不超过20%。
弯曲强度
批次样件,弯曲超过90°,粉层不开裂。
环保测试
要求喷粉厂提供粉末的SGS报告。
尺寸
卡尺
按图纸检验
c=0/n=5
珠海市椿田机械有限公司
表面处理检验作业规范
文件编号
CTT-MS-PG-008
制定日期
2021.11.05
制定
版次
A/1
生效日期
2021.11.05
审核
页 数
3of 3
抽样标准
GB/T2828.1-2012
批准
丝印
外观
目视/比对样品
重影:不可有重影,字体粗细正确
C=0
目视/图纸/比对样品
缺字:不可缺字错字
目视/比对样品毛边:不可有毛边目视断线:不可有断线
目视/色板/样品
污染、颜色:不可油墨(碳黑)涂层不均匀,颜色正确无杂色
表面处理检验作业规范
文件编号
CTT-MS-PG-008
制定日期
2021.11.05
制定
版次
A/1
生效日期
2021.11.05
审核
页 数
1of 3
抽样标准
GB/T2828.1-2012
批准
1.目的
1.1 明确产品要求,统一检验标准。
2.适用范围
适用于本公司外协回厂的所有喷涂/丝印/电镀产品的检验。
3.权责
C=0
目视/色板
颜色、色差:不可有颜色不对
C=0
目视/手感/比对样品
起皮起泡:A面不可有起泡起皮,B和C面小于0.2X0.2mm
表面处理检验规程

底座及绞车表面处理检验规程总则1、本规程中叙述的关于检验的的内容是以《钻井井架底座及绞车表面处理工艺规程》为基础。
如采用的是其它表面处理工艺方法,另行制定相应的检验规程。
2、本规程适用于定点生产厂家的产品(涂料)的质量检验。
预处理检验1、清洁度:除锈后钢材表面的清洁度应达到国家标准GB/T 8923.1-2011《涂覆涂料前钢材表面处理表面清洁度的目视评定第1部分:未涂覆过的钢材表面和全面清除原有涂层后的钢材表面的锈蚀等级和处理等级》规定的St2级以上的要求:1.1锈蚀等级分为A、B、C、D四级。
A级全面地覆盖着氧化皮而几乎没有铁锈的钢材表面;B级为已发生锈蚀,并且部分氧化皮已经剥落的钢材表面;C级为氧化皮已因锈蚀而剥落,或者可以刮除,并且有少量点蚀的钢材表面;D级为氧化皮已因锈蚀而全面剥落,并且已普遍发生点蚀的钢材表面。
1.2钢材表面会无可见的油脂、污垢,氧化皮、铁锈和油漆涂层等附着物,任何残留的痕迹应仅是点状或条纹状的轻微色斑。
1.3手工或动力工具除锈以字母“St”表示。
St分为St2、St3两级。
St2为彻底的手工和动力工具除锈:钢材表面应无可见的油脂、污垢,并且没有附着不牢的氧化皮、铁锈和油漆涂层等附着物。
我公司涂装的产品应达到St2要求。
涂料的检验1、涂料全面的质量检验由定点生产厂家完成。
定点生产厂家供货时应提供包括产品合格证、产品检验内容及数据、使用的测试标准等技术资料。
2、涂料购回后和使用前,进行检验,主要内容为外观检验:观察无色涂料是否浑浊,有色涂料是否有颜料沉淀。
目的是防止变质的、或有水分、结皮等杂物混入的无色涂料投入使用,防止有色涂料在涂装后超过色差范围,使金属结构件外观色泽不一致。
涂层的检验1、涂层检验涂膜外观、厚度、附着力和硬度光泽等项目。
2、涂膜外观检验:主要观察涂膜是否有如流挂、起气泡、针孔、起皱、桔皮、收缩、干喷、缩孔、咬底等缺陷,以及涂膜的光泽是否达到要求;3、涂膜厚度的检测:3.1为了较好地控制涂膜的喷涂厚度,必要时可采用湿膜厚度计进行测量,测定的结果用以校正涂装的条件,使涂装达到规定的厚度。
表面处理标准.pptx

• SP6 常规喷砂处理 • 至少喷砂处理到面积的2/3的部分没有可见的残迹。
• SP7 扫砂除锈处理第2页/共15页
• SP8 浸酸除锈法 • 通过酸液或电解质的浸洗除去所有的锈迹和氧化皮
• • SP10 喷砂近白处理
• 喷砂处理至接近SP5标准表面至少95%没有可见的残渣。 •
第3页/共15页
Sa 2.5(SSPC SP10)标准--非常彻底的喷射清理
• Sa 2.5级标准的内容;
• 在不放大的情况下进行观察时,表面应无可见的油 脂和污垢,并且没有氧化皮、铁锈、油漆涂层和异 物。任何残留的痕迹应仅是点状或条纹状的轻微色 斑。可参见标准照片。
• 为了达到Sa 2.5级的第打4页/砂共15标页 准,通常采用的磨料是
第5页/共15页
第6页/共15页
第7页/共15页
第8页/页/共15页
第11页/共15页
打砂粗糙度标准,粗糙度多大合适 底材打砂后的表面粗糙度要控制在一定的范围之内。粗糙度过大时浪费油漆的用量,而 且车间底漆容易露底;粗糙度过小时影响油漆与底材的附着力。粗糙度范围控制大约在 30~80μm,最好在40~60μm之间。 粗糙度的测量工具主要有指针式测量仪和压膜式测量仪。指针式测量仪对于现场检测非 常方便,使用也很简单。压膜式测量仪检测的速度 较慢,不适合打砂现场的随时测量, 但是测得的结果可以保留存档。除此之外,还可以直接对照标准样板进行目视检测。当 用测量仪器对打砂粗糙度进行测量时,应在板面上均匀地选取测量位置,对各不同部位 的粗糙度进行检测,并针对不同的结果对打砂设备作出适当的调整。
第13页/共15页
一、 打砂的密度 打砂密度是指钢板表面被磨料切削的面积占总面积 的比例。 要达到Sa 2.5级打砂标准,打砂密度一般要达到95% 以上。打砂密度的一般检测方法为目视法,可通过 带有刻度的放大镜进行观察。
零件表面处理检验规范

零件表面处理检验规范一、适用范围本规范适用于电镀、氧化、化学处理、喷塑、喷漆、喷砂、拉丝等金属表面处理的检验。
二、术语和定义2.1 A级表面:在使用过程中总能被客户看见的部分(如:面壳的正面和顶面,后壳的顶面,手柄,透镜,按键及键盘正面,探头整个表面等)。
2.2 B级表面:在使用过程中常常被客户看见的部分(如:面壳的左右侧面,底壳或后壳的左右侧面及背面等)。
这些表面允许有轻微不良,但是不致引起挑剔客户不购买产品。
2.3 C级表面:在使用过程中很少被客户注意到的表面部分(如:面壳的底面,底壳或后壳的底面,内部零件表面)。
此表面的外观缺陷应合理而且不至于给客户觉得该产品质量不佳。
2.4 金属表面:包括电镀、氧化、钝化等表现为金属质感的表面,非喷涂表面。
2.5 基材花斑:电抛光、电镀或氧化前因基体材料腐蚀、或者材料中的杂质、材料微孔等原因所造成的、与周围材质表面不同光泽或粗糙度的斑块状花纹外观。
2.6 抛光区:对基材上的腐蚀、划伤、焊接区、铆接区等部位进行机械打磨抛光后表现出的局部高光泽、光亮区域。
2.7 浅划痕:镀(膜/塑/漆)层表面划伤,但未伤及底层(即底层未暴露);对其它无镀(膜/塑/漆)层表面则为:目测不明显、手指甲触摸无凹凸感、未伤及材料本体的伤痕。
数控冲床加工中机床台面对板材的摩擦产生的轻微痕迹属于此类划痕。
2.8 深划痕:镀(膜/塑/漆)层表面划伤,且已伤至底层(即底层已暴露出来);对其它无镀(膜/塑/漆) 层表面则为:目测明显、手指甲触摸有凹凸感、伤及材料本体的伤痕。
2.9 凹坑:由于基体材料缺陷,或在加工过程中操作不当等原因而在材料表面留下的小坑状痕迹。
2.10 凹凸痕:因基材受撞击或校形不良等而呈现出的明显变形、凹凸不平的现象,手摸时有不平感觉。
2.11 烧伤:拉丝、电抛光、电镀处理时因操作不当、造成零件表面过热而留下的烧蚀痕迹。
2.12 水印:电镀、氧化或电抛光后因清洗水未及时干燥或干燥不彻底所形成的斑纹、印迹。
表面处理检验

镀硬铬通畅只在硬基体(钢、铸铁)上才有效
铬层表面有网状沟纹或点状孔隙,能够保存足 够的润滑油
用于内燃机的汽缸、汽缸套、活 塞环、活塞销以及上述零件磨损 后的修复
汽车、车厢、摩托车和各类仪表
以及医疗器具,日常用品等装饰
用。根据零件使用条件分为三类:
1)零 件 不 受 摩 擦 也 不 经 常 用 手 在制品表面上镀上许多层金属(如铜、镍、铬), 接触,形状不复杂,加工表面
表面处理检验——表面处理层的特性和用途
零件表面处理层的选择取决于零件的使用条件和覆盖层的特性,常用表面
处理层的特性和用途见下表:
表面处理层 种类
黑色金属阳 极化
磷化
阳极化
硬阳极化
着色阳极化 无色阳极化 草酸阳极化 铬酸阳极化
表 1 表面处理层的特性和用途
表面处理层特性
用途
氧化膜很薄,防护性能较差。在干燥的空气中 氧化膜具有良好的安定性;在潮湿的大气中防 护性差
在碱中镉层完全不溶解
3)镉的价格高而稀少,只有在不
鍍镉层柔软并有高的弹性,便于焊接
宜镀锌时才进行鍍镉
为提高鍍镉层的保护性能,进行钝化处理生成
稍带浅绿-虹色色调的浅黄色铬酸盐保护膜 对于钢,镀镍属于阴极性镀层;只有镀层达一
定的厚度,孔隙度很小时其防护性才可靠 1)要求有光泽的外表或有良好
为了增强镍层保护性能,采用带底层的镀镍
其中每一层照例都要加以抛光。形状比较简单 的修饰等级和表面光洁度要
的零件,其必要的抛光余量均为镀层规定厚度 求高的零件
的 15~20%;形状复杂的零件,其抛光余量(考 2)形状复杂且有深孔和凸缘的
虑到金属的损失)个别情况下单独确定
零件(此类零件不容许在硫酸
表面处理检验标准2016_01
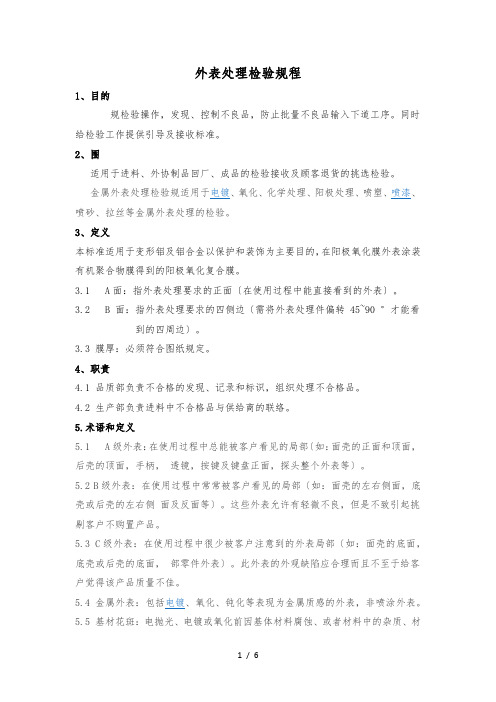
外表处理检验规程1、目的规检验操作,发现、控制不良品,防止批量不良品输入下道工序。
同时给检验工作提供引导及接收标准。
2、围适用于进料、外协制品回厂、成品的检验接收及顾客退货的挑选检验。
喷砂、拉丝等金属外表处理的检验。
3、定义本标准适用于变形铝及铝合金以保护和装饰为主要目的,在阳极氧化膜外表涂装有机聚合物膜得到的阳极氧化复合膜。
3.1 A面:指外表处理要求的正面〔在使用过程中能直接看到的外表〕。
3.2 B 面:指外表处理要求的四侧边〔需将外表处理件偏转45~90 °才能看到的四周边〕。
3.3 膜厚:必须符合图纸规定。
4、职责4.1 品质部负责不合格的发现、记录和标识,组织处理不合格品。
4.2 生产部负责进料中不合格品与供给商的联络。
5.术语和定义5.1 A级外表:在使用过程中总能被客户看见的局部〔如:面壳的正面和顶面,后壳的顶面,手柄,透镜,按键及键盘正面,探头整个外表等〕。
5.2 B级外表:在使用过程中常常被客户看见的局部〔如:面壳的左右侧面,底壳或后壳的左右侧面及反面等〕。
这些外表允许有轻微不良,但是不致引起挑剔客户不购置产品。
5.3 C级外表:在使用过程中很少被客户注意到的外表局部〔如:面壳的底面,底壳或后壳的底面,部零件外表〕。
此外表的外观缺陷应合理而且不至于给客户觉得该产品质量不佳。
5.4 金属外表:包括电镀、氧化、钝化等表现为金属质感的外表,非喷涂外表。
5.5 基材花斑:电抛光、电镀或氧化前因基体材料腐蚀、或者材料中的杂质、材料微孔等原因所造成的、与周围材质外表不同光泽或粗糙度的斑块状花纹外观。
5.6 抛光区:对基材上的腐蚀、划伤、焊接区、铆接区等部位进展机械打磨抛光后表现出的局部高光泽、光亮区域。
5.7 浅划痕:镀(膜/塑/漆)层外表划伤,但未伤及底层〔即底层未暴露〕;对其它无镀(膜/塑/漆)层表面那么为:目测不明显、手指甲触摸无凹凸感、未伤及材料本体的伤痕。
数控冲床加工中机床台面对板材的摩擦产生的轻微痕迹属于此类划痕。
表面处理检验规范(含表格)
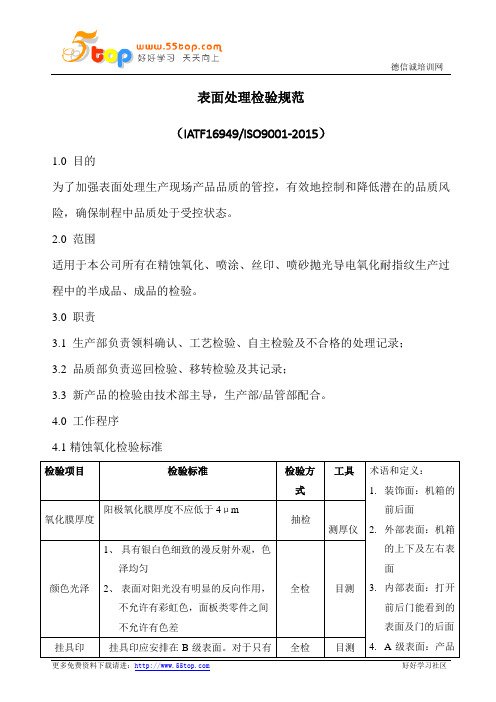
表面处理检验规范(IATF16949/ISO9001-2015)1.0 目的为了加强表面处理生产现场产品品质的管控,有效地控制和降低潜在的品质风险,确保制程中品质处于受控状态。
2.0 范围适用于本公司所有在精蚀氧化、喷涂、丝印、喷砂抛光导电氧化耐指纹生产过程中的半成品、成品的检验。
3.0 职责3.1 生产部负责领料确认、工艺检验、自主检验及不合格的处理记录;3.2 品质部负责巡回检验、移转检验及其记录;3.3 新产品的检验由技术部主导,生产部/品管部配合。
4.0 工作程序4.1精蚀氧化检验标准检验项目检验标准检验方式工具术语和定义:1.装饰面:机箱的前后面2.外部表面:机箱的上下及左右表面3.内部表面:打开前后门能看到的表面及门的后面4.A级表面:产品氧化膜厚度阳极氧化膜厚度不应低于4μm抽检测厚仪颜色光泽1、具有银白色细致的漫反射外观,色泽均匀2、表面对阳光没有明显的反向作用,不允许有彩虹色,面板类零件之间不允许有色差全检目测挂具印挂具印应安排在B级表面。
对于只有全检目测A级表面的零件,其挂具印应位于边角位置,并要求其大小控制在S≤1.0 且P≤2在公司的客户处进行安装、操作及日常维护时能被看到的表面。
装饰面、外部表面,内部表面均属A级表面5.B级表面:除A级表面以外的表面6.外观检验条件:在自然光或光照度在300-600LX的近似自然光下(如40W日光灯,距离500mm处),相距为600-650mm,观测时间为10秒,且检查者位于被检查表面的正面,视线、光线分别与被检查面呈45-90°,要求检查者的校正视力不低于1.2。
7.标准中W表示宽度、S表示面积、L表示长度、水印1、安装板、面板类零件装饰面不允许2、其它结构件外部表面S≤1.0 且P≤23、其它结构件内部表面S≤3.0 且P≤2全检目测划痕1、安装板、面板类零件装饰面不允许2、其它结构件外表面W≤0.3、L≤20、H≤0.1且P≤3 或W≤0.3、L≤40 、H≤0.1且P≤13、其它结构件内部表面W≤0.3、L≤20 且P≤3 或W≤0.3、L≤40且P≤2或L≤80 且P≤1全检目测小凹坑1.外部表面每100*100范围内1处缺陷面积S﹤1.0;内部表面每处缺陷面积S﹤2.5全检目测凸起颗粒1.安装板,面板类零件装饰面每100*100范围内S≤0.3且 P≤12.其它结构件外表面每100*100范围内S≤0.3且 P≤3 或S≤0.5且P≤2 或S≤0.7且P≤1全检目测异物脏污不允许全检目测拉丝1、原则上,不提倡拉丝。
表面处理工艺及检验规程

1.磷化1.1.范围:适用于需要磷化处理的产品及部件。
1.2.工艺流程:脱脂(碱性)→水洗→除锈→水洗→中和→表调→磷化→水洗→磷化后处理(喷涂)1.3.作业内容及管控重点:1.3.1 工件装框:轻拿轻放,防止工件变形。
高度不能超过溶液侵泡范围(产品杂乱放置放入框子中比规则放除油、磷化效果更好,但要确保排水充分)1.3.2 除油:(常温)碱性除油:主要是清除工件表面油污,效果很好。
PH值9-11(广泛试纸),滴定总碱度为45-60点,侵泡时间15-20分钟,根据工件所附着的油污,可适当延长侵泡时间。
1.3.3.水洗:PH值6-7(广泛试纸),针对除油后的水洗,当工件完全倾入水中,要上下左右不停地晃动2-3分钟,目的彻底清除上工序带来工件表面残留的非离子表面活性剂等。
在清洗过程需用保持清水溢流。
1.3.4.除锈:盐酸除锈的目的除锈完全,要求表面白净,无麻点。
本工序对氧化皮也有很好的去除功能。
弊病是盐酸易挥发,造成酸雾严重对人体有害,环境污染严重,因此要求不使用时需用PVC塑料板密盖。
PH值1-2(广泛试纸)滴定总酸度为300-500点,侵泡时间为25-30分钟。
1.3.5.水洗:PH值6-7(广泛试纸),针对除油后的水洗,当工件完全侵入水中,要上下左右不停地晃动2-3分钟,目的是彻底清除上道工序带来残留在工件表面的氯离子以防止带到下一道工序损坏槽液等。
在清洗过程中需保持清水溢流。
1.3.6.中和:PH值7-10(广泛试纸),针对除锈后的水洗,当工件完全侵泡水中,要上下左右不停地晃动2-3分钟,目的是彻底清除上道工序带来残留在工件表面的氯离子完全中和,防止因工件暴露在空气中造成返锈等。
当槽液PH值低于7或者严重发黄时,应及时更换槽液。
1.3.7.表调处理:PH值7-9(广泛试纸)目的是为了促使磷化形成晶体细致密实的磷化膜,以及加快磷化速度。
再配置表调剂是需用50-80摄氏度的温水将表调剂搅拌溶解后放入槽液钟,配置比例为0.3%。
表面处理检验规范

5.4.2.2用以上方法测量厚度时,当出现对镀层厚度有争议时,可采用GB/T 4955-1997中规定的方法
测量,但表面积小于100mm2的工件需用GB/T 9799-97中(见10.1.2.1和10.1.2.2)方法。
品不及时浸油封闭,已活化的元素和空气继续反应,有时会出现变色现象。
5.3环保性要求:产品发黑后要求:无毒,无异味,环保。
(发黑剂不得含有硒化物,亚销酸盐,铬等有毒化合物)
5.4性能测试:
5.4.1附着力和耐蚀性:
硫酸铜点滴法:每升溶液(去离子水)含硫酸铜30g、20℃、浸32秒,如有发红(触铜斑点,锈
苏州********有限公司
文件编号:
制订单位:质量部
版 本: A/0 总页数:4 页
制订日期:2014年 2 月 27 日
发行日期:2014年 2 月 27 日
核准
审 核
制订
制订部门
制订日期
发黑处理
检验规范
文件编号
版本
页次
质量部
1、目的
为了进一步加强表面发黑处理产品的质量控制,确保产品质量,满足客户要求。
5.2.7白斑:材料电镀前表面锈蚀深及底材时,电镀后因光线折射,产生白色斑纹。
5.2.8水纹:烘干作业不完全或水质不干净造成。
5.2.9过度酸洗:浸于酸液中的时间过长,造成金属表面过度腐蚀。
5.2.10脱层(翘皮):镀层附着力不佳,有剥落的现象。
5.3外观检验允收标准
现象
检验标准
缺陷度
污渍
不允许
轻
异色
5.2.4氧化膜不牢,判定为不良:
由于发黑前产品除油清洗不彻底、发黑处理时间过长,发黑层过厚,形成了发黑浮层,附着力差,
- 1、下载文档前请自行甄别文档内容的完整性,平台不提供额外的编辑、内容补充、找答案等附加服务。
- 2、"仅部分预览"的文档,不可在线预览部分如存在完整性等问题,可反馈申请退款(可完整预览的文档不适用该条件!)。
- 3、如文档侵犯您的权益,请联系客服反馈,我们会尽快为您处理(人工客服工作时间:9:00-18:30)。
HANSA CHINA中国汉莎
表面处理检验标准
1.目的
为使公司表面处理产品之检验有据可依。
2.适用范围
适用于公司所有表面处理产品。
3.管理责任者
品貭部主管
4.制订、修改、废止
4.1 本标准之制订、修改、废止均由品保部主管核决后生效。
4.2 本标准之表面处理是指电镀、PVD镀和有机涂层产品,并规定了其外观判定标准和相关的测试标准,如客户无特别要求将依此标准执行。
4.3 本标准自核准发布之日起执行
5.名词定义
A面:在安装后,对观察者来说不转动,直接看到的表面。
B面:对观察者来说不太重要,并且产品安装后需要转动,才能观察到的表面。
C面:在正常使用的条件下,对观察者来说不可见的表面。
起泡:镀层与基材之间附着性不良,而造成的镀层隆起现象。
剥离:镀层从底层或基材之间,剥落起皮之现象。
烧焦:镀层表面发白目视粗糙。
发黄:镀层表面露出黄色镍层。
发白:镀件表面有白色雾团状痕迹,手感粗糙.
碰伤:工件表面因碰伤产生凹状痕迹。
5.10划伤:产品表面被尖锐物体划出线状痕迹。
5.11擦伤:产品表面因包装运输,安装操作等工作过程中擦出细微线状痕迹。
5.12砂眼:机加、铸造、焊接、压铸件抛光后,表面留有较大凹洞。
电镀品表现为较明现的孔眼.
5.13针孔:机加、抛光或电镀后看到的部件表面上的小孔,它是由材质不良或焊接不良而引起的缺
陷。
5.14麻点:产品表面细微小点常有群体现象。
5.15杂质:产品表面较明显凸状附着物,手感粗糙,有刮手的感觉.
5.16露底材:镀件表面,未镀上铬、镍及PVD处理层之现象。
5.17弧伤:镀后产品表面呈雪花状痕迹。
5.18色差:同一产品不同表面,同一批产品不同表面,不同批产品表面,与标准色样板有较明显差
异。
5.19脱落:产品镀后表面镀层脱落,露出原电镀表面。
5.20变形:产品连接边、直角边、圆弧面明显变形及螺纹变形。
5.21砂印:产品表面留下抛光前打砂工序痕迹。
5.22毛边:产品加工时表面留下的薄金属片或金属毛刺。
5.23过度抛光:工作表面、平面、圆弧面抛光后波浪状痕迹。
5.24砂孔:工件内部小孔,抛光后露出细微小孔。
主要为材质不良造成.
6实施程序
6.1 表面处理产品依客户对外观目视需求不同划分为一、二、三类(见附件一),表面处理产品目视检验标准(见附件二至四)。
6.2 外观目视检验具体要求:
6.2.1 使用环境,光源为日光灯,并依据不同等级分面检验
6.2.2 检验者与产品之间间距300-400㎜,矫正视力为1.2以上,并无色盲
6.2.3 检验使用三秒钟法则:即在以上检验条件下,对同一面同一地方目视3秒钟进行评估(指针对某一个缺陷,而不是指用来检查整个产品所用的时间)
6.3 电镀膜厚测试依《膜厚测试标准》执行,如客户有特别要求时,以客户要求为准。
6.4 表面处理产品测试项目标准(见附件五)
6.5 表面处理之膜厚、盐雾测试要求(见附件六)
6.6 客户有特别要求的,依客户要求为准,必要时需制作外观限度标准样品(HANSA)作对比用。
附件二
附件三
附件四
附件五
表面处理产品测试项目标准
附件六
膜厚,盐雾测试标准
核决: 编制:
版次: 01 编号: HANSA CHINA-QD-SF-001。