第4.9脱模机构设计
第四章 推出机构的设计6

•
压缩空气配合推板脱模
• 设置引气装置以后:
4. 推块推出机构 平板状带凸缘的塑件,如 用推板件推出会黏附模具 时,则应使用推块推出机 构推出,如图所示。推块 是型腔的组成部分,因此 应有较高的硬度和较低的 表面粗糙度值,推块与型 腔及型芯应有良好的间隙 配合,既要求滑动灵活, 又不允许溢料。推块所使 用的推杆与模板不必要求 精度很高的配合。
难,同时因增加推件板而使模具质量增加。12
为减少脱模过程中推件板与 型芯之间的摩擦,两者之间 留有0.2~ 0.25mm的间隙, 并采用锥面配合,以防止推 件板 偏斜溢料,锥面的斜 度约取3~5˚左右,
4
推件板推出机构形式-4zzzzz 对于大型深腔的容器,尤其是采用软质塑料时, 如果用推件板脱模,应考虑附设引气装置,以防止在 脱模过程中内腔形成真空,造成脱模困难,甚至使塑 件变形损坏(见下图)。
(4)推管外径应比塑件外壁尺寸小0.5mm左右;推管内 径比塑件内径每边大0.2 ~0.5mm。 (5)推管与型芯的配合长度比推出行程S长3~5 mm,推 管与模板的配合长度一般为(1.5~2)D;其余部分扩 孔,推管扩孔d+l,模板扩孔D十1。推管的厚度一般取 1.5 ~5mm,以保证刚性。
• 3. 推件板推出机 构 • 深腔薄壁的容器、 壳体形塑件以及 不允许有推杆痕 迹的塑件都可采 用推件板推出机 构。推件板推出 机构的结构形式 与原理如图所示。
2、影响塑件脱模力的因素: 1) 脱模力的大小主要与塑件包络型芯侧面积的大小有关 2)脱模力大小与型芯的脱模斜度有关 脱模斜度越大,脱模力越小。 3) 脱模力的大小与型芯的表面粗糙度有关 表面粗糙度值越低,型芯表面越光洁,所需的脱 模力 就越小。 4) 脱模力的大小与塑件的结构有关 塑件厚度越大、形状越复杂,冷却凝固时所引起的包 紧力和收缩应力越大,则所需的脱模力越大。 5)脱模力的大小还与塑件底部是否有孔有关。
塑料模具设计第七周 第一讲(第四章)
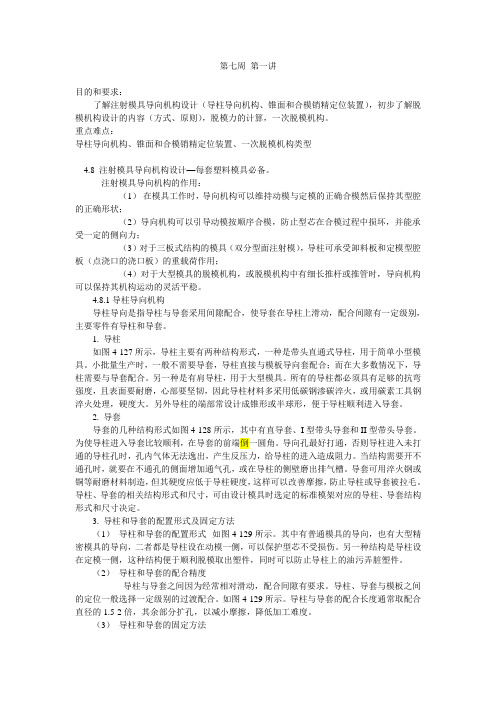
第七周第一讲目的和要求:了解注射模具导向机构设计(导柱导向机构、锥面和合模销精定位装置),初步了解脱模机构设计的内容(方式、原则),脱模力的计算,一次脱模机构。
重点难点:导柱导向机构、锥面和合模销精定位装置、一次脱模机构类型4.8 注射模具导向机构设计—每套塑料模具必备。
注射模具导向机构的作用:(1)在模具工作时,导向机构可以维持动模与定模的正确合模然后保持其型腔的正确形状;(2)导向机构可以引导动模按顺序合模,防止型芯在合模过程中损坏,并能承受一定的侧向力;(3)对于三板式结构的模具(双分型面注射模),导柱可承受卸料板和定模型腔板(点浇口的浇口板)的重载荷作用;(4)对于大型模具的脱模机构,或脱模机构中有细长推杆或推管时,导向机构可以保持其机构运动的灵活平稳。
4.8.1导柱导向机构导柱导向是指导柱与导套采用间隙配合,使导套在导柱上滑动,配合间隙有一定级别,主要零件有导柱和导套。
1. 导柱如图4-127所示,导柱主要有两种结构形式,一种是带头直通式导柱,用于简单小型模具。
小批量生产时,一般不需要导套,导柱直接与模板导向套配合;而在大多数情况下,导柱需要与导套配合。
另一种是有肩导柱,用于大型模具。
所有的导柱都必须具有足够的抗弯强度,且表面要耐磨,心部要坚韧,因此导柱材料多采用低碳钢渗碳淬火,或用碳素工具钢淬火处理,硬度大。
另外导柱的端部常设计成锥形或半球形,便于导柱顺利进入导套。
2. 导套导套的几种结构形式如图4-128所示,其中有直导套、I型带头导套和II型带头导套。
为使导柱进入导套比较顺利,在导套的前端倒一圆角。
导向孔最好打通,否则导柱进入未打通的导柱孔时,孔内气体无法逸出,产生反压力,给导柱的进入造成阻力。
当结构需要开不通孔时,就要在不通孔的侧面增加通气孔,或在导柱的侧壁磨出排气槽。
导套可用淬火钢或铜等耐磨材料制造,但其硬度应低于导柱硬度,这样可以改善摩擦,防止导柱或导套被拉毛。
导柱、导套的相关结构形式和尺寸,可由设计模具时选定的标准模架对应的导柱、导套结构形式和尺寸决定。
4.9 脱模机构设计

(4) 推杆的固定与配合形式
1)推杆的固定形式
a.常用形式 b.采用垫块或垫圈代 替固定板上的沉孔 c.螺钉顶紧推杆 d.推杆固定端无推板 时使用 e.螺钉紧固,用于粗 大推杆 f. 铆钉的形式,用于 直径小的推杆
2)圆形横截面推杆的配合形式
推杆端面应和塑件成型表面在同一平面或高出0.05~0.1mm 推杆与推杆孔有一段配合长度为推杆直径3~5倍的间隙配 合 (H8/f8或H9/f9),其余部分为扩孔。 扩孔直径比推杆大0.5mm。
(1)利用推杆拉断点浇口Байду номын сангаас料 (2)利用拉料杆拉断点浇口凝料
(3)利用侧凹拉断点浇口凝料
(4)利用定模推板拉断点浇口凝料
3.潜伏式浇口凝料的脱出结构
其脱模装置必须分别设置塑件和流道凝料的推出机构, 在推出过程中,浇口被拉断,塑件与浇注系统凝料各自脱 落。 (1)利用脱模板切断浇口凝料
(2)利用差动式推杆切断浇口凝料 (3)
3)摆块拉板式脱模机构 利用活动摆块推动型腔板完成一次脱模,由推杆完成二 次脱模。
4)滑块式
2. 双推板二次脱模机构
这种类型的脱模结构有两组推出装置,利用两组推板的 先后动作完成二次脱模。 1)八字摆杆式脱模机构
① 开模时,当注射机顶杆推动 一次推板时,连接推杆与脱 模板一起以同样速度移动, 使塑件和型腔一起运动而脱 离动模型芯,完成一次推出 动作。
3)定距导柱顺序脱模结构 4)尼龙拉钩式顺序脱模结构
七、浇注系统凝料的脱出机构
1.普通浇注系统凝料的脱出结构
通常采用侧浇口、直接浇口及中心浇口类型的模具,其 浇注系统凝料一般与塑件连在一起。塑件脱出时,先用拉 料杆拉住冷料,使浇注系统凝料留在动模一侧,然后用推 杆或拉料杆推出,靠其自重而脱落。
脱模机构的设计
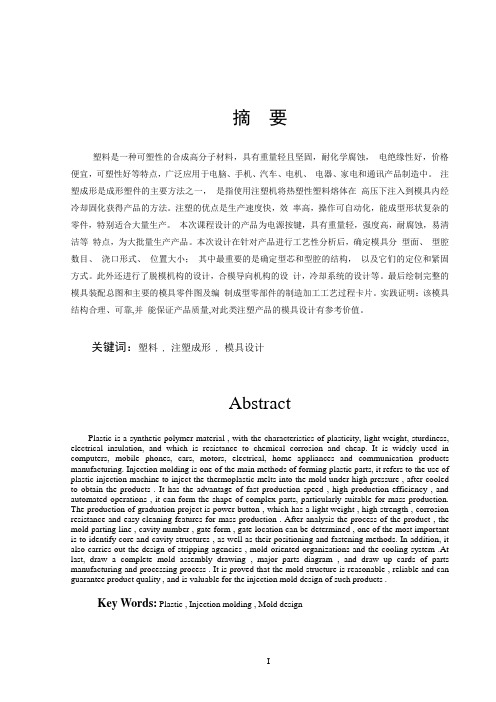
摘要塑料是一种可塑性的合成高分子材料,具有重量轻且坚固,耐化学腐蚀,电绝缘性好,价格便宜,可塑性好等特点,广泛应用于电脑、手机、汽车、电机、电器、家电和通讯产品制造中。
注塑成形是成形塑件的主要方法之一,是指使用注塑机将热塑性塑料熔体在高压下注入到模具内经冷却固化获得产品的方法。
注塑的优点是生产速度快,效率高,操作可自动化,能成型形状复杂的零件,特别适合大量生产。
本次课程设计的产品为电源按键,具有重量轻,强度高,耐腐蚀,易清洁等特点,为大批量生产产品。
本次设计在针对产品进行工艺性分析后,确定模具分型面、型腔数目、浇口形式、位置大小;其中最重要的是确定型芯和型腔的结构,以及它们的定位和紧固方式。
此外还进行了脱模机构的设计,合模导向机构的设计,冷却系统的设计等。
最后绘制完整的模具装配总图和主要的模具零件图及编制成型零部件的制造加工工艺过程卡片。
实践证明:该模具结构合理、可靠,并能保证产品质量,对此类注塑产品的模具设计有参考价值。
关键词:塑料 , 注塑成形 , 模具设计AbstractPlastic is a synthetic polymer material , with the characteristics of plasticity, light weight, sturdiness, electrical insulation, and which is resistance to chemical corrosion and cheap. It is widely used in computers, mobile phones, cars, motors, electrical, home appliances and communication products manufacturing. Injection molding is one of the main methods of forming plastic parts, it refers to the use of plastic injection machine to inject the thermoplastic melts into the mold under high pressure , after cooled to obtain the products . It has the advantage of fast production speed , high production efficiency , and automated operations , it can form the shape of complex parts, particularly suitable for mass production. The production of graduation project is power button , which has a light weight , high strength , corrosion resistance and easy cleaning features for mass production . After analysis the process of the product , the mold parting line , cavity number , gate form , gate location can be determined , one of the most important is to identify core and cavity structures , as well as their positioning and fastening methods. In addition, it also carries out the design of stripping agencies , mold-oriented organizations and the cooling system .At last, draw a complete mold assembly drawing , major parts diagram , and draw up cards of parts manufacturing and processing process . It is proved that the mold structure is reasonable , reliable and can guarantee product quality , and is valuable for the injection mold design of such products .Key Words:Plastic , Injection molding , Mold design1.1 引言随着塑料工业的飞速发展和通用塑料与工程塑料在强度和精度等方面的不断提高,塑料制品的应用范围也在不断地扩大,如:家用电器、仪器仪表、建筑器材、汽车工业、日用五金等众多领域,塑料制品所占的比例正迅速增加,由于在工业产品中,一个设计合理的塑料件往往能代替多个传统金属结构件,加上利用工程塑料特有的性质,可以一次成型非常复杂的形状,并且还能设计成卡装结构,成倍地减少整个产品中的各种紧固件,大大地降低了金属材料消耗量和加工及装配件工时,因此,近年来工业产品塑料化的趋势不断上升。
毕业设计(论文)-一模多腔的注塑模具结构设计及仿真分析

毕业论文(设计)题目:一模多腔的注塑模具结构设计及仿真分析(英文):The Design of Multi-cavity InjectionMould For Multi-way Buttons andSimulation Analysis院别:机电学院专业:机械设计制造与其自动化(CAD/CAM)姓名:学号:指导教师:日期:2011年5月一模多腔的注塑模具结构设计及仿真分析摘要本次设计主要特点是根据MOLDFLOW软件仿真模流分析来指导模具结构的设计。
MOLDFLOW软件模拟塑料熔体在整个注射过程中的充填、冷却及流动情况,确保获得高质量制件。
打破传统模具结构设计的试模、修模等过程,达到降低成本,提高生产率的目的。
在得到仿真分析最佳质量效果的数据、参数之后用来作为模具结构设计的依据。
本次设计主要包括:(1)模流仿真分析注射成型时熔体在型腔中的流动过程非常复杂,与许多因素如聚合物性能、制件结构、温度、压力、时间、模具结构及注射设备等有关。
仿真定量地给出成型过程的成型窗口状态参数(如压力、温度、速度等)。
(2)依据仿真的成型窗口状态参数进行整个注塑模具的结构设计。
如注射机的选择、浇注系统、成型零件、合模机构、脱模机构和冷却系统的设计,绘制模具零件图和装配图等。
关键词:仿真分析;模具设计;一模六腔;PROE建模The Design of Multi-cavity Injection Mould For Multi-way Buttons and Simulation AnalysisABSTRACTThe main features of the design is based on software simulation flow analysis MOLDFLOW to guide the design of die structure. MOLDFLOW software to simulate the injection of plastic melt in the process of filling, cooling and flow, ensuring access tohigh-quality parts. Breaking traditional mold structure design test mode, the process of repair molds, to reduce costs, improve productivity purposes. Obtained the best quality in the simulation results of the data, parameters after the design used as the basis for the mold.The design includes: (1)Moldflow injection molding simulation of melt flow in the cavity is very complex process with many factors. Such as polymer properties, parts structure, temperature, pressure, time, and injection mold structure and other related equipment. Quantitative simulation of the molding window molding process given the state parameters (such as pressure, temperature, speed, etc.). (2) Simulation based on the parameters of the molding window state the structural design of the injection mold. Such as the choice of injection machine, injection system, molded parts, mold bodies, stripping institutions and cooling system design, drawing die part and assembly drawings, etc..Keywords:Simulation Analysis;Mold Design ;Six-cavity Mold;Proe Modeling目录1绪论 (1)1.1 模具工业在国民经济中的地位 (1)1.2我国模具工业的现状 (1)1.3未来模具发展方向 (1)1.4论文的提出及研究意义 (2)2多向按键工艺分析及模具方案的初步确定 (3)2.1塑件的结构和尺寸精度及表面质量分析 (4)2.2塑件的原材料分析 (4)2.3模具方案的初步确定 (6)2.31 模具结构各个部件的分析确定 (6)2.32 总体结构方案的论证和初步确定 (6)3运用MOLDFLOW进行模具结构有限元仿真分析 (7)3.1介绍其功能 (7)3.2 MOLDFLOW分析的流程 (7)3.3应用MOLDFLOW进行分析 (8)3.31 划分产品网格 (8)3.32 选择成型材料 (9)3.33 确定最佳浇口位置 (10)3.34 创建浇注系统及优化 (11)3.35 创建冷却系统及优化 (13)3.36 成型窗口分析 (16)3.37 选择分析类型 (17)3.38 注射工艺参数的优化 (20)4多向按键的注塑模具结构的最终确定 (24)4.1型腔数目及布局的确定 (24)4.2注塑机的选择 (25)4.3分型面的设计 (27)4.4浇注系统的设计 (29)4.41主流道的设计及计算 (29)4.42定位圈 (30)4.43分流道的设计 (30)4.5浇口的设计 (32)4.51浇口形状的分析与确定 (32)4.52浇口位置的确定 (33)4.6排气系统的设计 (34)4.7模架的确定 (34)4.8推出机构的设计 (34)4.81顶杆的设计及计算 (35)4.82复位杆的设计 (36)4.83推板和推杆固定板的设计 (37)4.9合模导向机构的设计 (37)4.10成型零件的设计 (39)4.101计算成型零件的工作尺寸 (40)4.11冷却系统 (42)4.12模具工作原理 (44)5设计总结 (46)参考文献 (47)致谢 (49)附录 (50)1绪论1.1模具工业在国民经济中的地位模具是制造业的一种基本工艺装备,它的作用是控制和限制材料(固态或液态)的流动,使之形成所需要的形体。
第10讲-脱模机构设计-PPT
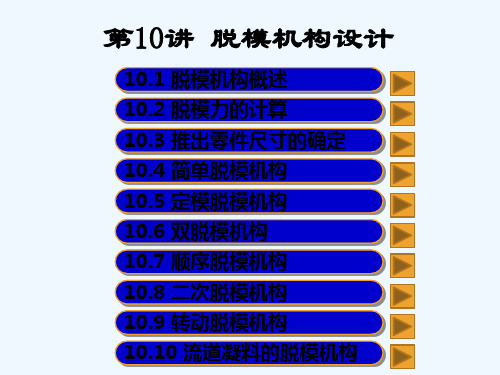
推杆的位置 1-推杆(兼复位杆)2-塑件 3-推杆 4-型芯 5-盘形推杆
10.4.1 常见脱模机构的类型
1.推杆脱模机构
2)应设在塑件强度刚度 较大处。
推杆不宜设在塑件的薄壁
处,应尽可能设在塑件厚壁、
凸缘处及筋与筋或壁与筋的交
点上,以免使塑件变形损坏。
如必须设在薄壁处时,应
增大推杆截面积,以降低单位
大家有疑问的,可以询问和交流
可以互相讨论下,但要小声点
10.2 脱模力的计算
概念
(1)定义:指将塑件从型芯上脱出时所需克服的阻力。 包括:
成型收缩的包紧力; 不带通孔的壳体类塑件的大气压力; 机构运动的摩擦力; 塑件对模具的粘附力;
10.2.1 影响脱模力的因素
(2)影响脱模力的因素
型芯成型部分的表面积及其形状. 收缩率及摩擦系数. 塑件壁厚和包紧型芯的数量. 型芯表面粗糙度. 成型工艺:P注、t冷.
对于生产批量很大的制品,为提高生产率,可 采用结构比较复杂、自动化程度比较高的脱模机构。
10.1.3 推出机构的设计原则
5)推出零件应有足够的强度、刚度和硬度。 6)合模时应正确复位。并保证不与其他模具零 件相干涉。 7)脱模行程应恰当。应保证推出零件运动的初 始位置和终止位置恰当合理,以保证制品可靠脱模。
由上面的式子可以看影响因素脱模力的大小主要有以下几点:
(l)主要与塑件包络型芯侧面积的大小有关。型芯的侧面积越大,所需的脱 模力也越大。 (2)与型芯的脱模斜度有关。脱模斜度越大,所需的脱模力越小。 (3)与型芯的表面粗糙度有关。表面粗糙度值越低,型芯表面越光洁,所需 的脱模力就越小。 (4)与塑件的结构有关。塑件厚度越大、形状越复杂,冷却凝固时所引起的 包紧力和收缩应力越大,则所需的脱模力越大。 (5)与注射工艺有关。 注射压力越大,则包紧型芯的力越大,所需脱模力越大; 脱模时模具温度越高,所需的脱模力越小; 塑件在模内停留时间越长,所需的脱模力越大。 (6)与成型塑件的塑料品种有关。不同的塑料品种,由于分子的结构不一样, 因而它们的脱模力也不一样。
简单脱模机构设计
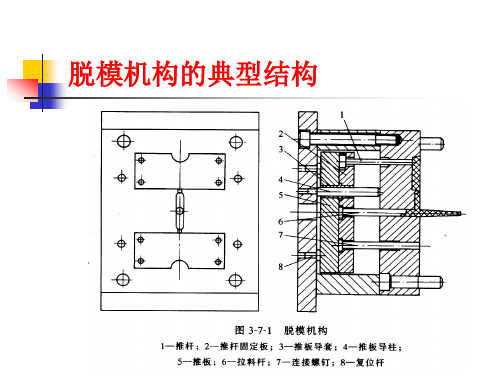
多元脱模方式联合脱模机构
推杆与推件板联合推出机构
多元脱模方式联合脱模机构
推杆与推件板联合推出机构
多元脱模方式联合脱模机构
推杆与推管联合推出机构
多元脱模方式联合脱模机构
推管与推板联合推出机构
脱模机构的典型结构
脱模机构的组成
① 推出元件——推出制件的元件 如推杆、推管、推块、推板及顶针板、面针板等。 ② 复位元件——使推出元件复位 如复位杆(回程杆 )、弹簧等。 ③ 导向元件——对脱模机构起导向作用 如中托司(导柱、导套)。 ④ 传动元件——拖动脱模机构的元件 (指某些螺纹制件的脱模传动) 如齿轮、齿条、链轮、链条等。 ⑤ 限位元件:垃圾钉,限位块。 ⑥ 拉料杆。
推件板脱模机构设计要点
①导向 ②定距 ③摩擦 ④进气
活动镶件脱模机构
气压脱模机构
采用压缩空气推出塑件,塑件受力均匀 且可以简化模具结构,由于不需要在模内设 推板及其运动空间,因此模具总高度可减小。 其推出力为塑件内腔投影面积与气体压强的 乘积,故断面尺寸越大的薄壁壳体越易脱出。
气压脱模机构
气压脱模机构
脱模机构的分类
A)按驱动方式分 1、手动脱模 2、机械脱模 3、液压脱模 4、气压脱模 B)按模具结构分 1)简单脱模机构 2)定模脱模机构 3)双脱模机构 4)顺序脱模机构 5)二级脱模机构
6)浇注系统凝料自动脱出机构
7) 带螺纹制件脱模机构
脱模机构的设计要求
1、脱模机构应动作可靠,结构简单,制造方便。 2、不损坏塑件的外观质量 3、塑件在推出过程中不发生变形和损坏 对模具包紧力和粘附力大小的分析与计算,合理地选择推出的 方式、推出的位置、推出零件的数量和推出面积等。 4、让塑件留于动模 5、合模时应使脱模机构正确复位 在斜导杆和斜导柱侧向抽芯及其他特殊的情况下,还应考虑脱 模机构的先复位问题等
塑料模脱模推出机构的设计

4.14.7 脱模推出机构的设计1.推出方式的确定本塑件圆周采用脱模板,中心采用推杆的综合推出方式。
脱模板推出时为了减小脱模板与型芯的摩擦,设计中在用脱模板与型芯之间留出0.2mm 的间隙,并采用锥面配合,如图4-340所示,可以防止脱模板因偏心而产生溢料,同时避免了脱模板与型芯产生摩擦。
2.脱模力的计算⑴ 圆柱大型芯脱模力 因为1013339>===t r λ,所以,此处视为薄壁圆筒塑件,根据式4-24脱模力为 NNN A K f tESL F 4.34503914.31.0)1cos 1sin 45.01)(3.01()1tan -45.01cos )329(0055.08.1314.321.0)1()tan (cos 22321≈⨯⨯++-⨯⨯-⨯⨯⨯⨯⨯=+--=(μϕϕπ 式中各项的意义,见4.9.2节内容。
⑵ 成型塑件内部圆筒型芯的脱模力计算 因为105.237<===t r λ,所以此处视为厚壁圆筒塑件,同时,由于该塑件的内孔是通孔,所以,脱模力不存在真空压力,参考式(4-24)可得脱模力为NN K K f rESL F 9.4096)1cos 1sin 45.01)(1cos )21(2)1(cos )21(23.01()1tan 45.0(340055.0108.1714.32)1()tan (22223212=+⨯⨯+⨯++-⨯⨯⨯⨯⨯⨯⨯=++-=︒︒︒︒︒μϕπ 对于塑件的四个肋板,由于是径向布置,冷却收缩是径向收缩,所以对型芯的箍紧力不是太大,主要是粘模力,可以按计算脱模力乘以一个不太大的系数,此处考虑为1.2。
3.校核推出机构作用在塑件的单位压应力⑴ 推出面积22222210.1254)4.7888(4)(4mm mm d D A =-=-=ππ2222212121.160)1420(4)(4mm mm d D A =-=-=ππ⑵ 推出应力抗压强度)合格(5305.51.1600.1254)9.40964.3050(2.1)(2.12.12121Mpa Mpa A A F F A F <=++⨯=++==σ4.14.8 冷却系统的设计冷却系统的设计很麻烦,在此只进行简单的计算。
脱模机构的设计与加工教案

【课题编号】5—项目五【课题名称】脱模机构的设计与加工【教学目标与要求】一、知识目标1.了解脱模机构的作用,及脱模机构的设计原则。
2.了解顶出机构、推板脱模机构的结构和设计原则。
3.了解保鲜盒盒体模具脱模的动作原理。
4.了解推杆固定板推杆孔和推板与推杆固定板固定螺纹孔的加工工艺。
5.了解拉杆导柱、拉杆、圆形拉模扣、复位杆、拉料杆的作用及结构。
6.了解脱模机构——侧向抽芯机构及复位机构的作用、结构和设计。
7.熟悉攻制内螺纹的钻孔和攻制工艺。
二、能力目标1.能够分析保鲜盒盒体模具脱模的动作原理。
2.能够分清拉杆导柱、拉杆、复位杆、拉料杆和拉模的区别。
3.能根据图样要求攻制内螺纹。
三、素质目标1.了解脱模机构在模具生产中的作用,能够根据设计选用原则分析保鲜盒脱模方式的动作过程。
2.了解各种不同杆在脱模机构中的作用,侧向抽芯机构与各种复位机构的作用和结构特点。
3.熟悉螺纹孔的钻孔和攻螺纹的过程。
四、教学要求1.了解推杆固定板推杆孔与推板和推杆固定板固定螺纹孔的加工工艺。
2.了解脱模机构的作用、结构及设计原则。
3. 能够分析保鲜盒盒体模具脱模方式的动作过程及其优点。
4.了解圆形拉模和安装孔的加工工艺。
5.了解各种杆件在脱模中的作用和结构。
6.了解侧向抽芯机构和复位机构的组成、动作原理及设计方法。
7.掌握攻内螺纹的工艺过程。
【教学重点】1.保鲜盒盒体模具脱模过程分析。
2.推杆固定板推杆孔、推板和推杆固定板固定螺纹孔、圆形拉模扣安装孔的加工工艺。
【难点分析】1.脱模机构中的各种机构、构件的设计。
2.侧向抽芯机构和复位机构的作用与设计。
3.攻内螺纹前底孔直径的确定。
【分析学生】要了解脱模机构的结构与设计要求,首先要熟悉塑料制作的生产过程,了解脱模机构的作用及动作过程,才能理解脱模机构的结构,设计出合理实用的脱模机构。
侧向抽芯机构的结构比较特殊,如果对模具的制作和制件的生产过程不熟悉,是比较不容易理解的。
学生需要具备一定的基础知识和实践知识后,才能比较容易理解侧向机构的结构特点。
基于DOE法的注塑成型工艺仿真优化本科毕业论文

摘要注塑成型制品质量控制方面存在的困难主要来源于力学的复杂性和在温度、压力波动下材料行为的不可预测性,研究工艺参数对注塑制品质量的影响关系,建立工艺参数与制品质量之间的关系模型,并用DOE法对工艺进行仿真优化是注塑制品工艺优化的前提。
本文选用半结晶型和无定型ABS两种材料,针对一维流动平板两个方向上的收缩、强度,熔接线强度、制品重量及沉降斑等质量指标进行了实验研究。
研究了工艺参数对质量指标的影响及因素之间的交互作用。
本文主要工作包括以下几方面: 1 工艺参数对制品质量的交互影响分析;2 应用DOE法结合析因分析结果;3.CAE技术结合DOE法进行设计,并用MOLDFLOW进行仿真分析,为质量控制技术提供了工艺模型。
关键词: 注塑成型,正交实验,Moldflow,三维建模,工艺仿真优化,实验设计AbstractQuality control of injection molding products, mainly difficulties from that exist in the complexity of process dynamics and in the temperature and pressure fluctuations unpredictable behavior of materials, of process parameters on product quality of injection molding between the relationship,DOE method with simulation and optimization technology of injection molding products, process optimization is a prerequisite.Semi-crystalline and amorphous ABS we usd in this paper,For a flat that two-dimensional flow direction shrinkage, strength, weld line strength, weight and sink marks and other products, the quality indicators studied. In this paper, include the following:1. Process parameters on product quality of interaction analysis;2. Application of DOE method with the results of factorial analysis;3. CAE design method combined with DOE,Simulation and analysis with MOLDFLOW,quality control technology provides for the process model.Key words:Injection Molding,Orthogonal,Moldflow,Three-dimensional modeling,Process simulation and optimization,design of experiment.目录1.1 引言 (1)1.2 注塑成型工艺过程简介 (1)1.3注塑成型工艺的发展趋势 (3)1.4 注塑成型工艺优化国内外研究概况 (6)1.5本文主要工作内容及其意义 (10)2. 注塑成型工艺参数影响性分析 (13)2.1 压力参数分析 (13)2.1.1注塑压力 (13)2.1.2保压压力 (13)2.1.3 塑化压力(背压) (14)2.2 温度参数分析 (14)2.2.1模具温度 (14)2.2.2熔体温度 (15)2.3时间参数分析 (15)2.3.1注射时间 (16)2.3.2保压时间 (16)2.4注射速度分析 (16)3. 基于DOE法的注塑成型仿真优化 (18)3.1软件Moldflow以及正交实验助手的介绍 (19)3.1.1 moldflow软件简介 (19)3.1.2 正交实验助手介绍 (20)3.2材料的选取及模型的导入 (23)3.3本次实验设计法的分析理论依据 (27)3.3.1.实验基本参数取值范围的确定及输入 (28)3.3.2.正交表的设置及数据生成 (29)3.3.3实验分析类型以及结果的选取 (31)3.4实验设计法的仿真优化过程 (34)3.4.1 Moldflow与正交表的数据结合分析 (34)3.4.2实验数据的反馈与整合 (43)4.模具设计 (47)4.1塑件用途及其性能要求 (47)4.2注射量的计算 (48)4.3锁模力的计算 (48)4.4注塑机的选择及参数 (49)4.5 分型面的确定 (50)4.6 浇注系统的设计 (51)4.7 成型零部件的设计与计算 (57)4.8 推出机构设计 (59)4.9标准模架的选取 (59)4.10 开模行程的校核 (61)4.11 推出脱模机构设计 (62)4.12合模导向机构的设计 (64)4.13 排气系统与冷却系统的设计 (67)5. 结论 (68)5.1设计的总结与创新点: (68)5.2论文所存在的问题及其解决方案: (69)谢辞 (70)参考文献: (72)1.绪论1.1 引言随着科学技术水平的不断提高以及加工方法的改进,塑料这一20世纪才发展起来的新材料已经在我们的日常生活中占据了重要的地位,成为国民经济中不可缺少的一部分。
脱模机构设计
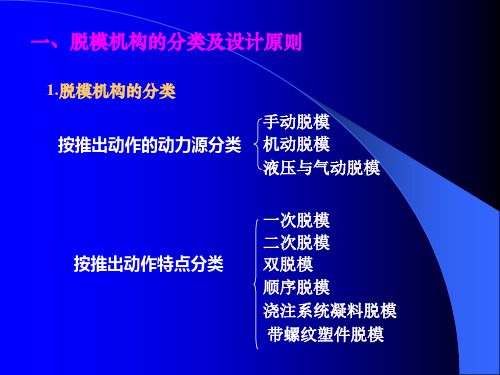
0.1A
2. 厚壁塑件(λ<10) 1)塑件为圆形断面时
2rESL f tan F 0.1A 1 K1 K 2
2)塑件为矩形断面时
2a b ESL f tan F 0.1A 1 K1 K 2
F:脱模力; E:塑料的弹性模量;S:塑料成型的平均收缩率;t:塑件壁厚; L:被包型芯长度;μ:塑料泊松比;ψ:脱模斜度;f:塑料与钢材的摩擦因数 A:塑件在与开模方向垂直的平面上的投影面积,若塑件底部有通孔, A=0 r:型芯的平均半径。a, b:矩形型芯短边和长边长度。
(1)普通推管
采用型芯穿过推板固定在动模座板上的形式,型芯较长,可 作为脱模机构运动的导柱,运动比较可靠,但装配和制造比较困 难,适用于推出行程不大的场合。
(2)底部有台阶结构推管
型芯固定在动模与型芯固定板之间,推管在型腔板内滑动,使推管和 型芯长度大为缩小,但是使型腔板厚度增加。
(3)中心开槽的推管
K1 2 2 cos 2 2 cos
K 2 1 f sin cos
三、一次推出脱模机构
1. 推杆(顶杆)脱模机构 推杆脱模机构的组成 由推杆1,推杆固定板2,推板5 和挡销8等组成. 推杆推出塑件,推板传递压 力,挡销起调节推杆位置和便 于消除杂物的作用.
(1) 推杆的横截面形状 圆形、矩形、三角形、椭圆形、半圆形等
一、脱模机构的分类及设计原则
1.脱模机构的分类 按推出动作的动力源分类 手动脱模 机动脱模 液压与气动脱模 一次脱模 二次脱模 双脱模 顺序脱模 浇注系统凝料脱模 带螺纹塑件脱模
按推出动作特点分类
2. 脱模机构的设计原则 ① 塑件滞留于动模。 ② 保证塑件不因推出而变形损坏:设计时应仔细分析塑件对
第五节--推出机构的设计
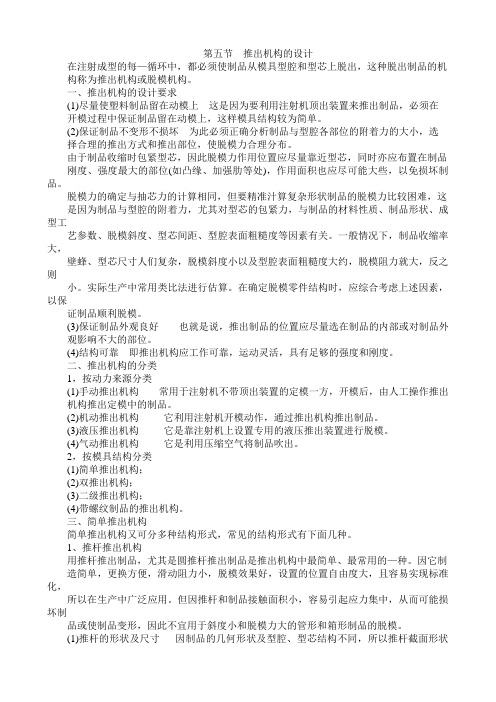
第五节推出机构的设计在注射成型的每—循环中,都必须使制品从模具型腔和型芯上脱出,这种脱出制品的机构称为推出机构或脱模机构。
一、推出机构的设计要求(1)尽量使塑料制品留在动模上这是因为要利用注射机顶出装置来推出制品,必须在开模过程中保证制品留在动模上,这样模具结构较为简单。
(2)保证制品不变形不损坏为此必须正确分析制品与型腔各部位的附着力的大小,选择合理的推出方式和推出部位,使脱模力合理分布。
由于制品收缩时包紧型芯,因此脱模力作用位置应尽量靠近型芯,同时亦应布置在制品刚度、强度最大的部位(如凸缘、加强肋等处),作用面积也应尽可能大些,以免损坏制品。
脱模力的确定与抽芯力的计算相同,但要精准汁算复杂形状制品的脱模力比较困难,这是因为制品与型腔的附着力,尤其对型芯的包紧力,与制品的材料性质、制品形状、成型工艺参数、脱模斜度、型芯间距、型腔表面粗糙度等因素有关。
一般情况下,制品收缩率大,壁蜂、型芯尺寸人们复杂,脱模斜度小以及型腔表面粗糙度大约,脱模阻力就大,反之则小。
实际生产中常用类比法进行估算。
在确定脱模零件结构时,应综合考虑上述因素,以保证制品顺利脱模。
(3)保证制品外观良好也就是说,推出制品的位置应尽量选在制品的内部或对制品外观影响不大的部位。
(4)结构可靠即推出机构应工作可靠,运动灵活,具有足够的强度和刚度。
二、推出机构的分类1,按动力来源分类(1)手动推出机构常用于注射机不带顶出装置的定模一方,开模后,由人工操作推出机构推出定模中的制品。
(2)机动推出机构它利用注射机开模动作,通过推出机构推出制品。
(3)液压推出机构它是靠注射机上设置专用的液压推出装置进行脱模。
(4)气动推出机构它是利用压缩空气将制品吹出。
2,按模具结构分类(1)简单推出机构;(2)双推出机构;(3)二级推出机构;(4)带螺纹制品的推出机构。
三、简单推出机构简单推出机构又可分多种结构形式,常见的结构形式有下面几种。
1、推杆推出机构用推杆推出制品,尤其是圆推杆推出制品是推出机构中最简单、最常用的—种。
脱模机构

脱模(推出) 第九章 脱模(推出)机构设计推出机构——把塑件及浇注系统从从型腔中或型芯上脱出来的 推出机构——把塑件及浇注系统从从型腔中或型芯上脱出来的 —— 机构。
机构。
第一节推出机构的组成及分类一、推出机构的组成推出机构组成:推出部件(推杆、拉料杆、推杆固定板、 推出机构组成:推出部件(推杆、拉料杆、推杆固定板、推杆 垫板、限位钉)、导向部件(推杆导柱、推杆导套)、 )、导向部件 )、复位部 垫板、限位钉)、导向部件(推杆导柱、推杆导套)、复位部 复位杆)。
件(复位杆)。
二、推出机构分类按驱动方式分: 机动推出机构 液压推出机构 手动推出机构 按推出元件的类别分: 推杆推出机构 推管推出机构 推件板推出机构按模具结构分: 简单推出机构 二次推出机构 带螺纹的推出机构 浇注系统自动切断推出机构 多元联合脱模机构复杂推出机构三、推出机构设计原则1.尽量使塑件留于动模一侧塑件留于动模推出机构简单,否则要设计定模推出机构。
塑件留于动模推出机构简单,否则要设计定模推出机构。
设计定模推出机构2.保证塑件推出时不变形不损坏脱模力应作用于塑件刚度及强度最大的部位 作用力面积尽可能大3.推出位置尽量选在塑件内侧,保证塑件外观良好 4.合模时应使推出机构正确复位 5 .推出机构应动作可靠 推出和复位过程中,结构应简单,动作可靠、灵活, 推出和复位过程中,结构应简单,动作可靠、灵活, 无卡死与干涉现象。
机构本身应有足够的刚度、 无卡死与干涉现象。
机构本身应有足够的刚度、强度 和耐磨性。
和耐磨性。
第二节1.定义脱模力的计算脱模力——指将塑件从型芯上脱出时所需克服的阻力。
成型收缩的包紧力 大气压力 机构运动的摩擦力 塑件对模具的粘附力2.影响脱模力的因素型芯成型部分的表面积及其形状 收缩率及摩擦系数 塑件壁厚和包紧型芯的数量 型芯表面粗糙度 成型工艺:P注、t冷3.脱模力计算 受力分析: ∑Fx=0 F摩cosα-F脱-F正sinα=0 F脱= F摩cosα-F正sinα F摩=f·F正 F正=pA f—摩擦系数(0.15~1.0) p—因塑件收缩对型芯产生的单位正压力(12~20MPa) A—塑件包紧型芯的侧面积(mm2) F脱= pA(f·cosα-sinα) 总脱模力等于 总 脱 大气 大气压力影响:引气、不引气) 大气(大气压力影响 总脱模力等于F总=F脱+F大气 大气压力影响:引气、不引气) 等于 以上对脱模力的计算是一种比较粗略的方法。
4.7脱模机构

推件板和型芯的配合
留有0.2~025mm的间隙 配合长度
配合锥度20°
二次脱模机构
作用:由于塑件的特殊形状或生产自动化的需要;为避 免一次脱模塑件受力过大。
摆杆拉钩二级脱模机构
三角滑块式双推板二次脱模机构
螺纹的脱模
强制脱出:弹性较好或较柔软的塑件,用于精 度不高和小批量生产的塑件 模外脱出:活动螺纹镶块
3)直径和数量
保证足够的刚度。可设计成阶梯形
数量应保证顺利脱模且不损伤塑件表观
4)推杆固定形式
推杆
推杆
推杆
推杆
推杆
推杆
(a)
(b)
(c)
(d)
(e)
(f)
图4-79 推杆的固定形式
2、复位机构 复位杆:2~4根 弹簧复位:先复位
3、导向机构 导柱、垫块、复位杆
二)推管脱模机构
又称为空心推杆,主要用于圆筒形塑件的脱模
对于盖、壳类塑件,因侧面脱模阻力较大,应在底面和侧面周边同时布 置脱模机构。
图4-77 盖类塑件的顶出位置
图4-78 加强筋部增设推杆结构
2)配合和装配
推杆和推杆孔配合取H8/f8间隙配合,配合段长度取推杆直径的2~3倍, 不小于10mm。非工作段与孔有0.5 ~1mm的间隙,以减少磨擦。 推杆端面应和型腔在同一平面或比型腔的平面高出0.05~0.1mm。一般 不允许推杆端面低于塑件表面。
顶出位置应设在塑件内部
4)结构可靠
工作可靠、运动灵活、制造方便、配换容易。
二、简单脱模机构
通过一次推出动作将塑件脱卸出模具的机构称为一次推出脱模机构, 或称为简单脱模机构。最常见的结构形式,包括推杆机构、推板机构、 推管机构等
脱模机构设计讲解
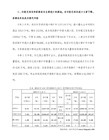
1、教学目的与要求
目的: 学习塑料注射模具脱模机构及设计要求。 要求: (1)掌握脱模机构的结构分类; (2)掌握脱模机构结构中的简单脱模机构设计; (3)熟悉脱模机构结构中的二次脱模机构及其 它结构的设计; (4)掌握相关的英文词汇。
制品包裹型芯的情况
顶杆(ejector pin )
(7)顶杆的强度计算 a 圆形顶杆 2 2 64 u L Q d 4 由欧拉公式: min 3 n E
设计时为保证可靠程度,d = 1.5 dmin。 u—考虑支撑条件的长度系数,u≈0.7; L—顶杆长度,cm; E—顶杆的抗拉弹性模量,N/ cm; n—顶杆件数; Q—脱模力,N;
Q一般情况下也可按下式计算: 对通孔型芯: Q = LHq(f· cos—sin) 对盲孔型芯: Q = LHq(f· cos—sin) + B 以上两式中: L—活动型芯中被塑件包紧的断面周长,cm; H—活动型芯成型部分的高度,cm; B—垂直于顶出方向的型芯投影面积,cm; q—包紧型芯的单位压力,一般取800~3400N/ cm; —塑料与钢的摩擦系数,一般取0.15~0.2。
2
二、脱模力的计算
如塑件孔为盲孔,上述计算式中还须加上塑件所 受的大气压力。
F = 10A
式中:F—克服真空增加的脱模阻力,N;
A—塑件盲孔的底面积, cm。
三、简单脱模机构 1、顶杆脱模机构
设计要点: (1)顶杆应设在塑件能承力较大或脱模阻力较大的 地方,尽量使顶出的塑件受力均匀,但不宜与型芯或 的镶件的距离过近,以免影响成型零件的强度; (2)顶杆直径必须有足够的强度,能承受顶出时 的冲击力。顶杆直径一般取2.5~12mm,对3 毫米以下的顶杆建议采用阶梯式结构,即顶杆下部 加粗以增加强度;
脱模机构解析PPT课件
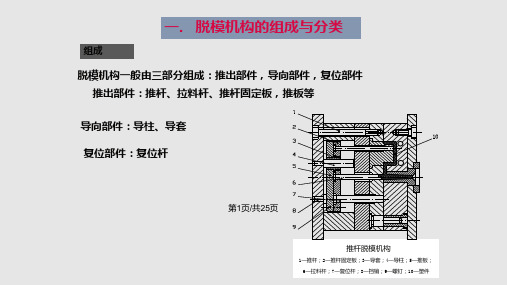
4)考虑合模时推出机构的复位。 第3页/共25页
二. 脱模力的计算
当塑件从包紧的型芯上脱出所需要克服的阻 力称为脱模力,主要是塑件收缩引起的塑件 与型芯的摩擦阻力。 塑件刚开始脱模时,所需的脱模力最大, 称为初始脱模力;其后,脱模力的作用仅 仅为了克服脱模机构移动的摩擦力,称为 相继脱模力。 脱模力一般指初始脱模力。
双推板
三角滑块式双推板二次脱模机构
第15页/共25页
螺纹的脱模
强制脱出:弹性较好或较柔软的塑件,用于精度不高和小批 量生产的塑件
模外脱出:活动螺纹镶块
第16页/共25页
对合螺纹型环成型时的脱出 齿轮齿条机动脱螺纹机构
第17页/共25页
第18页/共25页
第19页/共25页
第20页/共25页
3)直径和数量
保证足够的刚度。可设计成阶梯形 数量应保证顺利脱模且不损伤塑件表观
第6页/共25页
4)推杆材料及热处理要求
材料常用T8A,T10A或65Mn,碳素工具钢热处理要求硬度HRC50~54, 弹簧钢热处理硬度要求HRC50~54。
5)推杆固定形式
推杆
推杆
推杆
推杆
推杆
推杆
(a)
(b)
第7页/共25页
脱模机构的分类
1、按动力来源分:
1)机动脱模:注射机上设置机械或者液压顶出装置,通过该顶 出装置推动模具脱模机构顶出塑件。
2)手动脱模:开模后人工操纵脱模机构,多用于定模(定模部分 注射机未设脱模装置)
3)气动脱模: 利用压缩空气将塑件吹出。
2、按模具结构分
第2页/共25页
一次推出脱模(简单脱模)、二次推出脱模、动定模双向推出脱模、 顺序脱模、带螺纹塑件脱模等不同类型
简单脱模机构
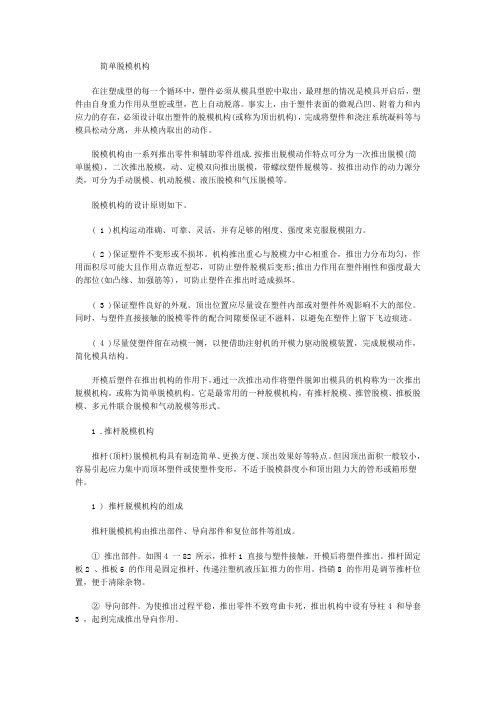
简单脱模机构在注塑成型的每一个循环中,塑件必须从模具型腔中取出,最理想的情况是模具开启后,塑件由自身重力作用从型腔或型,芭上自动脱落。
事实上,由于塑件表面的微观凸凹、附着力和内应力的存在,必须设计取出塑件的脱模机构(或称为顶出机构),完成将塑件和浇注系统凝料等与模具松动分离,并从模内取出的动作。
脱模机构由一系列推出零件和辅助零件组成.按推出脱模动作特点可分为一次推出脱模(简单脱模),二次推出脱模,动、定模双向推出脱模,带螺纹塑件脱模等。
按推出动作的动力源分类,可分为手动脱模、机动脱模、液压脱模和气压脱模等。
脱模机构的设计原则如下。
( 1 )机构运动准确、可靠、灵活,并有足够的刚度、强度来克服脱模阻力。
( 2 )保证塑件不变形或不损坏。
机构推出重心与脱模力中心相重合,推出力分布均匀,作用面积尽可能大且作用点靠近型芯,可防止塑件脱模后变形;推出力作用在塑件刚性和强度最大的部位(如凸缘、加强筋等),可防止塑件在推出时造成损坏。
( 3 )保证塑件良好的外观。
顶出位置应尽量设在塑件内部或对塑件外观影响不大的部位。
同时,与塑件直接接触的脱模零件的配合间隙要保证不滋料,以避免在塑件上留下飞边痕迹。
( 4 )尽量使塑件留在动模一侧,以便借助注射机的开模力驱动脱模装置,完成脱模动作,简化模具结构。
开模后塑件在推出机构的作用下,通过一次推出动作将塑件脱卸出模具的机构称为一次推出脱模机构,或称为简单脱模机构。
它是最常用的一种脱模机构,有推杆脱模、推管脱模、推板脱模、多元件联合脱模和气动脱模等形式。
1 .推杆脱模机构推杆(顶杆)脱模机构具有制造简单、更换方便、顶出效果好等特点。
但因顶出面积一般较小,容易引起应力集中而顶坏塑件或使塑件变形,不适于脱模斜度小和顶出阻力大的管形或箱形塑件。
1 ) 推杆脱模机构的组成推杆脱模机构由推出部件、导向部件和复位部件等组成。
① 推出部件。
如图4 一82 所示,推杆1 直接与塑件接触,开模后将塑件推出。
塑件脱模机构设计

人工取出针点浇口凝料
塑料成型模具
利用斜孔(面)拉断针点浇口
此种结构最好用倒锥头或球头拉料杆,且分流道最好开 在定模板上,如开在动模板上则要用较长的中心顶杆。
Flash 动画
塑料成型模具
利用拉料杆拉断针点浇口
模具先从A面分型,距离由限位杆6确定;再从B面分型,距离 由(限位杆7减去限位杆6的限位距离)决定.最后完成主分型, 再顶出制品.
Flash 动画
二级脱模-气动式
塑料成型模具
塑料成型模具
二级脱模-弹簧式
Flash 动画
二级脱模-凸轮推杆式
塑料成型模具
用于第一级脱模距离较短的情况。注意凸轮的旋转角度 不能太大,以免合模发生自锁,使凸轮不能压回。
塑料成型模具
二级脱模-拉勾推杆式
Flash 动画
二级脱模-滑块式
塑料成型模具
带螺纹制品的脱模
利用硅橡胶螺纹型芯强制脱螺纹
塑料成型模具
开模时,在弹簧的作用下,先让出硅橡胶中的型芯以便于 桂橡胶螺纹型芯的向内收缩。为顺利地强制脱螺纹作好准 备。 硅橡胶螺纹型芯寿命低,用于小批量生产。
带螺纹制品的脱模 利用分瓣式可涨缩型芯脱螺纹
缺点是螺纹的内表面有拼合线痕迹。 也可成型其它的塑料件侧凹。
脱螺纹机构的设计计算
塑料成型模具
故要正确设计定模的分型距离l1,如果l1过 长,则型芯已旋出,而制品还未从型腔中退出。 如果l1太短,则会使制品完全从型腔中脱出时, 而还有几扣螺纹未旋出。 设还有n扣螺纹未旋出时,定模停止分型,此时 制品仍在型腔内。则有:n=H/(2iT-t) 其中H为 制品的高度。l1= N-n)(2iT-t)=2iNT-h-H 其中 =(N-n)(2iT-t)=2iNT-h-H h为制品的螺纹部分高度。总开模距L=l1+h+H =2iNT+5~10mm. 方轴与丝杆的相对运动距离为开模行程的一半, 故方轴长度L1=L/2+a 。a为配合部分长度(一 般取25mm)。
- 1、下载文档前请自行甄别文档内容的完整性,平台不提供额外的编辑、内容补充、找答案等附加服务。
- 2、"仅部分预览"的文档,不可在线预览部分如存在完整性等问题,可反馈申请退款(可完整预览的文档不适用该条件!)。
- 3、如文档侵犯您的权益,请联系客服反馈,我们会尽快为您处理(人工客服工作时间:9:00-18:30)。
4.9 脱模机构设计
(3)利用拉料杆拉断点浇口凝料
4.9 脱模机构设计
(4)利用定模推板拉断点浇口凝料
4.9 脱模机构设计
(4)利用定模推板拉断点浇口凝料
4.9 脱模机构设计
(4)利用定模推板拉断点浇口凝料(续)
4.9 脱模机构设计
(4)利用定模推板拉断点浇口凝料(续)
4.9 脱模机构设计
(2)楔块摆钩式二次脱模机构 (一)
4.9 脱模机构设计
(2)楔块摆钩式二次脱模机构
4.9 脱模机构设计
(2)楔块摆钩式二次脱模机构 (二)
4.9 脱模机构设计
(2)楔块摆钩式二次脱模机构
4.9 脱模机构设计
3.气动或液压二次脱模机构
4.9 脱模机构设计
3.气动或液压二次脱模机构
4.9 脱模机构设计
4.9 脱模机构设计
(2)旋转脱螺纹的驱动方式
1)人工驱动
①模外手工脱螺纹
4.9 脱模机构设计
②模内手工脱螺纹
4.9 脱模机构设计
2)利用开模运动脱螺纹
①使用齿条机构使螺纹型芯旋转
4.9 脱模机构设计
②使用大升角的丝杠螺母使螺纹型芯旋转
4.9 脱模机构设计
②使用大升角的丝杠螺母使螺纹型芯旋转
H 0.54 L(
BE
F脱
)
1 3
4.9 脱模机构设计
4 .推块脱模
4.9 脱模机构设计
4 .推块脱模
4.9 脱模机构设计
4 .推块脱模
4.9 脱模机构设计
5.利用成型零件的脱模机构
4.9 脱模机构设计
5.利用成型零件的脱模机构
4.9 脱模机构设计
5.利用成型零件的脱模机构
脱模杆的使用实例
4.9 脱模机构设计
脱模杆的使用实例
4.9 脱模机构设计
(2)脱模板的厚度计算
1)对圆筒形塑件
按刚度计算: H (
k1 F脱 R 2 E
)
1 3
按强度计算:
H (
k 2 F脱
)
1 2
4.9 脱模机构设计
2)对矩形或异环形横截面塑件,其脱模板所用推杆分布如 图4-156b所示,若按刚度计算,则:
22 K1 cos 2 2 cos
4.9 脱模机构设计
4.9.3一次脱模机构
1 推杆脱模机构
4.9 脱模机构设计
4.9.3一次脱模机构
1 推杆脱模机构
4.9 脱模机构设计
1)推杆的固定形式
4.9 脱模机构设计
4.9.3一次脱模机构
1 推杆脱模机构
4.9 脱模机构设计
4.9 脱模机构设计
4.9.1 脱模机构和设计原则
1)塑件滞留于动模,模具开启后应以使塑件及浇口凝 料滞留于带有脱模装置的动模上。
2)保证塑件不变形损坏。
3)力求良好的塑件外观。
4.9 脱模机构设计
4.9.2脱模力的计算
1.薄壁塑件脱模力的计算 当圆形塑件的内孔半径与壁厚 ab r 10 ) 之比: ;(矩形塑件 : 10 t t (1)当塑件横断面形状为圆形时
4.9 脱模机构设计
7 .气动脱模机构
4.9 脱模机构设计
7 .气动脱模机构
4.9 脱模机构设计
4.9.4 二次脱模机构
1 单推板二次脱模机构
(1)弹簧式
4.9 脱模机构设计
4.9.4 二次脱模机构
1 单推板二次脱模机构
(1)弹簧式
4.9 脱模机构设计
4.9.4 二次脱模机构
(2)U形限制架式
3.旋转式脱螺纹
(1)螺纹部分的止转、回转方式与推出
4.9 脱模机构设计
1)塑件外部有止转的情况
4.9 脱模机构设计
1)塑件外部有止转的情况
4.9 脱模机构设计
2)塑件内部有止动的情况
4.9 脱模机构设计
3)塑件的端面有止动的情况
4.9 脱模机构设计
(2)旋转脱螺纹的驱动方式
1)人工驱动
①模外手工脱螺纹
港、台模具推杆名称
4.9 脱模机构设计
港、台模具推杆名称
4.9 脱模机构设计
4.9.3一次脱模机构
1 推杆脱模机构
4.9 脱模机构设计
4.9.3一次脱模机构
推杆推出机构型式
4.9 脱模机构设计
4.9.3一次脱模机构
1 推杆脱模机构
4.9 脱模机构设计
4.9.3一次脱模机构
1 推杆脱模机构
4.9 脱模机构设计
4.9.4 二次脱模机构
(2)U形限制架式
4.9 脱模机构设计
4.9.4 二次脱模机构
(3)摆块拉板式
4.9 脱模机构设计
4.9.4 二次脱模机构
(3)摆块拉板式
4.9 脱模机构设计
4.9.4 二次脱模机构
(4)滑块式:图4-171通过斜导柱和滑块实现二次脱模
4.9 脱模机构设计
r 10 t
;矩形塑件:
ab 10 t
(1)当塑件横截面形状为圆形时
2rESL( f tan ) F 0.1A (1 K1 ) K 2
(2)当塑件端面形状为矩形时
2(a b) ESL( f tan ) F 0.1A (1 K1 ) K 2 r ①当塑件为圆形时: t ab ②当塑件为矩形时: t
4.9 脱模机构设计
4.9.3一次脱模机构
1 推杆脱模机构
4.9 脱模机构设计
4.9.3一次脱模机构
1 推杆脱模机构
4.9 脱模机构设计
4.9.3一次脱模机构
1 推杆脱模机构
4.9 脱模机构设计
(4)推杆的固定与配合形式
1)推杆的固定形式
4.9 脱模机构设计
1)推杆的固定形式
4.9 脱模机构设计
4.9 脱模机构设计
(2)利用硅橡胶螺纹型芯强制脱螺纹
4.9 脱模机构设计
(2)利用硅橡胶螺纹型芯强制脱螺纹
4.9 脱模机构设计
2.拼合式螺纹型芯和型环
4.9 脱模机构设计
2.拼合式螺纹型芯和型环
4.9 脱模机构设计
2.拼合式螺纹型芯和型环
4.9 脱模机构设计
2.拼合式螺纹型芯和型环
4.9 脱模机构设计
2tESL cos ( f tan ) F 0.1A (1 ) K 2
(2)当塑件横截面形状为矩形时
8tESL cos ( f tan ) F 0.1A (1 ) K 2
4.9 脱模机构设计
2.厚壁塑件脱模力的计算 当塑件的当塑件的内孔半径
与壁厚之比
1)推杆的固定形式
4.9 脱模机构设计
2)圆形横截面推杆的配合形式
4.9 脱模机构设计
(5)推出机构的导向
4.9 脱模机构设计
(5)推出机构的导向
4.9 脱模机构设计
(5)推出机构的导向
4.9 脱模机构设计
(5)推出机构的导向
4.9 脱模机构设计
(5)推出机构的导向
4.9 脱模机构设计
4.9 脱模机构设计
3)使用气缸和油缸驱动脱螺纹机构
4.9 脱模机构设计
4)使用电机驱动脱螺纹
4.9 脱模机构设计
5)使用液压马达驱动脱螺纹
拉料杆拉住冷料井,使浇注系统留在动模一侧,然后用推
杆或拉料杆推出,靠其自重而脱落。
4.9 脱模机构设计
2 点浇口式浇注系统凝料的脱出机构
(1)利用推杆拉断点浇口凝料
4.9 脱模机构设计
(2)利用侧凹拉断点浇点浇口凝料
4.9 脱模机构设计
(3)利用拉料杆拉断点浇口凝料
4.9 脱模机构设计
(3)定距导柱顺序脱模机构
4.9 脱模机构设计
(4)尼龙拉钩式顺序脱模机构注射模
4.9 脱模机构设计
其他定距装置动作模拟
4.9 脱模机构设计
其他定距装置动作模拟
4.9 脱模机构设计
其他定距装置动作模拟
4.9 脱模机构设计
其他定距装置动作模拟
4.9 脱模机构设计
其他定距装置动作模拟
3)气缸和油缸复位
4.9 脱模机构设计
(2)底部有台阶结构推管
4.9 脱模机构设计
(2)底部有台阶结构推管
4.9 脱模机构设计
(3)中心开槽的推管
4.9 脱模机构设计
推管推出动作模拟
4.9 脱模机构设计
3 脱模板脱模机构
4.9 脱模机构设计
3 脱模板脱模机构
(1)脱模板的结构形式
4.9 脱模机构设计
3. 潜伏式浇口凝料的脱出机构
(1)利用脱模板切断浇口凝料
4.9 脱模机构设计
3. 潜伏式浇口凝料的脱出机构
(1)利用脱模板切断浇口凝料
4.9 脱模机构设计
(2)利用差动式推杆切断浇口凝料
4.9 脱模机构设计
(2)利用差动式推杆切断浇口凝料
4.9 脱模机构设计
(2)利用差动式推杆切断浇口凝料
4.9 脱模机构设计
5.利用成型零件的脱模机构
4.9 脱模机构设计
6.二及多元联合脱模机构
4.9 脱模机构设计
6.二及多元联合脱模机构
4.9 脱模机构设计
6.二及多元联合脱模机构
4.9 脱模机构设计
6.多元联合脱模机构
4.9 脱模机构设计
6.多元联合脱模机构
4.9 脱模机构设计
7 .气动脱模机构
4.9 脱模机构设计
4.9.6 顺序脱模机构
(1)弹簧顺序脱模机构
2)定距拉杆式顺序脱模机构注射模