注射成型制品常见缺陷及处理方法
注塑缺陷描述及解决方案

注塑缺陷描述及解决方案一、缺陷描述注塑是一种常见的塑料加工方法,广泛应用于各个行业。
然而,在注塑过程中,常常会出现一些缺陷,影响产品的质量和性能。
下面将描述一些常见的注塑缺陷。
1. 气泡缺陷:气泡是注塑过程中常见的缺陷之一。
它们通常出现在塑料制品的表面或内部,给产品的外观和强度带来不利影响。
气泡的形成可能是由于塑料材料中含有挥发性成分,或者注塑过程中存在过高的温度或压力。
2. 热流痕缺陷:热流痕是由于注塑过程中塑料材料的流动受到阻碍而形成的。
它们通常呈线状或条状,并且会降低产品的外观质量。
热流痕的形成可能是由于模具设计不合理、注塑温度过高或注塑速度过快等原因。
3. 毛刺缺陷:毛刺是指产品表面出现的细小突起,给产品的触感和外观带来不良影响。
毛刺的形成可能是由于模具表面粗糙、注塑温度过高或注塑压力过大等原因。
4. 缩孔缺陷:缩孔是指塑料制品内部出现的空洞或凹陷,降低了产品的强度和密封性能。
缩孔的形成可能是由于注塑过程中塑料材料的收缩不均匀或注塑温度不合适。
5. 热胀冷缩缺陷:热胀冷缩是指注塑制品在冷却过程中由于温度变化而引起的尺寸变化。
如果注塑制品的尺寸与设计要求不符,就会影响产品的装配和使用。
热胀冷缩的控制需要合理设计模具和控制注塑工艺参数。
二、解决方案针对上述注塑缺陷,以下是一些常见的解决方案,以帮助改善产品质量和性能。
1. 气泡缺陷解决方案:- 选择低挥发性的塑料材料,减少挥发性成分的含量。
- 调整注塑过程中的温度和压力,避免过高的温度或压力导致气泡的形成。
- 使用真空抽气装置,帮助排除塑料材料中的气泡。
2. 热流痕缺陷解决方案:- 优化模具设计,确保塑料材料的流动畅通无阻。
- 降低注塑温度,避免过高的温度导致热流痕的形成。
- 控制注塑速度,避免过快的注塑速度导致热流痕的产生。
3. 毛刺缺陷解决方案:- 改善模具表面的光洁度,减少毛刺的形成。
- 调整注塑温度和压力,避免过高的温度或压力导致毛刺的产生。
注塑成型常见产品缺陷与处理办法。
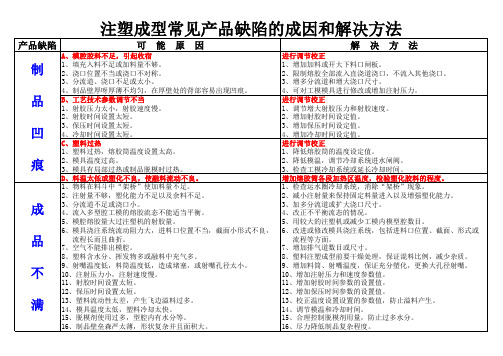
良
6、制品形状不良,壁厚薄不均匀,使融料在薄壁处汇合。
7、模具冷却系统不当或排气不良。
8、塑料内掺有不相熔的的料、油质或脱模剂不当。
12、塑料有及污回染料、混干全燥比不例良大或,有使挥塑发料物收。缩方向性过大或填料分布不均
。
制
3、不适当的脱模设计,制品壁薄,脱模斜度小,有尖角及缺口,容
品
易应力集中。 4、顶针或环定位不当,或成型条件不当,应力过大,顶出不良。
解决方法
所受的背压减少。 11、检查料筒和射嘴,浇注系统太粗糙,应改进和提高。 12、、混原料料时要避干免燥混,入设杂备物干。净,换料时要清除干净,以免留有余料 。 3、保证所用颜料质量,使用搅拌时颜料要均匀附在料粒表面。 4、降低熔胶筒、射嘴温度,清除烧焦的胶料。 5、降低射胶压力和速度参数值,避免添加剂分解。 6、擦干模具表面水分和油污,合理使用脱模剂。 7、合理设置纤维填料的工艺参数,合理使用溶剂,使塑化良好,
5塑料料温太低模温低射嘴孔径小在注射压力速度高时剪应5增加熔胶筒的温度及模具温度减小射胶压力和速度以防止6料温高模温高填充作用过分保压补缩过大射胶压力高时6降低熔胶筒的温度及模具温度减小射胶压力和保压补缩7制品厚薄不均参数调节不当冷却不均或收缩不均
注塑成型常见产品缺陷的成因和解决方法
产品缺陷
可能原因
1、注塑前先干燥处理胶料,也要避免处理过程中受过大的温度变
注塑缺陷描述及解决方案

注塑缺陷描述及解决方案引言概述:注塑技术是一种常用的塑料成型工艺,广泛应用于各个行业。
然而,在注塑过程中,常常会出现一些缺陷,如气泡、热胀冷缩、短射等问题,这些缺陷会影响产品的质量和性能。
本文将从五个大点出发,详细阐述注塑缺陷的描述及解决方案。
正文内容:1.注塑缺陷:气泡1.1 气泡的描述:气泡是注塑过程中常见的缺陷之一。
它们通常出现在产品的内部或表面,给产品的外观和性能带来负面影响。
1.2 气泡的解决方案:1.2.1 调整注塑机的压力和温度,确保塑料完全熔化,减少气体残留。
1.2.2 优化模具结构,增加通气口,促使气泡顺利排出。
1.2.3 使用抗气泡剂或改性剂,减少气泡的生成。
2.注塑缺陷:热胀冷缩2.1 热胀冷缩的描述:热胀冷缩是由于注塑过程中塑料的热胀冷缩性质导致的缺陷。
它会导致产品尺寸不准确,甚至造成产品变形。
2.2 热胀冷缩的解决方案:2.2.1 选择合适的塑料材料,具有较小的热胀冷缩系数。
2.2.2 控制模具温度,使得塑料在注塑过程中均匀冷却,减少热胀冷缩的影响。
2.2.3 使用辅助冷却系统,如冷却水或风扇,加速产品冷却过程,减少热胀冷缩。
3.注塑缺陷:短射3.1 短射的描述:短射是指注塑过程中塑料未能充满模具腔体,导致产品缺陷。
短射通常表现为产品的一部分或整个部分未充实。
3.2 短射的解决方案:3.2.1 检查和调整注塑机的注射速度和压力,确保塑料能够充分填充模具腔体。
3.2.2 检查模具的设计和结构,确保流道和出料口的尺寸和位置合理,避免短射现象。
3.2.3 使用模具温度控制系统,确保塑料在注塑过程中保持适当的温度,减少短射的发生。
4.注塑缺陷:毛刺4.1 毛刺的描述:毛刺是指注塑过程中产生的塑料残留物,通常出现在产品的边缘或表面,影响产品的外观和质量。
4.2 毛刺的解决方案:4.2.1 优化模具设计,增加冷却系统,降低模具温度,减少毛刺的生成。
4.2.2 调整注塑机的注射速度和压力,避免过多的塑料残留。
注塑成型缺陷及解决方法

注塑成型缺陷及解决方法注塑成型是一种常用的塑料制品生产工艺,但在实际操作过程中,难免会出现一些缺陷。
下面将介绍几种常见的注塑成型缺陷及其解决方法。
1.短射:短射指的是塑料在模腔中注入不完全,导致制品形状不完整或缺少一部分。
短射可能由于注射速度过快或进气不畅引起。
解决方法是调整注塑机的注射速度和压力,确保塑料充分进入模腔,并检查进气口是否畅通。
2.气泡:气泡是指制品表面或内部出现空洞。
气泡的形成可能由于塑料中含有水分、模具开放不当等原因。
解决方法是在注塑前将塑料干燥处理,确保塑料中不含水分,并检查模具密封性以防止气体进入模腔。
3.缩短:缩短是指制品尺寸比设计要小,可能由于塑料收缩不均匀或模具温度不稳定引起。
解决方法是通过调整模具温度和冷却系统,使塑料在注塑过程中均匀收缩,并确保模具温度稳定。
4.色差:色差是指制品表面颜色不均匀,可能由于塑料熔融不充分、颜料添加不均匀等原因。
解决方法是加长塑料的熔化时间,确保塑料充分熔融,并确保颜料充分混合均匀。
5.枝晶:枝晶是指制品表面出现树枝状的纹理,可能由于注塑温度过高或冷却时间不足引起。
解决方法是降低注塑温度,延长冷却时间,确保塑料在注塑过程中充分凝固。
6.毛刺:毛刺是指制品表面出现刺状的尖突物,可能由于模具间隙过大或模具磨损引起。
解决方法是调整模具间隙,确保模具紧密结合,并定期检查模具磨损情况。
7.烧焦:烧焦是指塑料在注塑过程中受热过度,产生发黑或炭化的现象。
烧焦可能由于注塑温度过高或注射速度过快引起。
解决方法是降低注塑温度,调整注射速度,确保塑料受热均匀。
总结起来,解决注塑成型缺陷的关键是调整注塑机参数、保证模具质量和稳定性,以及进行适当的后处理工艺。
此外,及时发现和修复模具的损坏也是避免缺陷的重要措施。
注塑缺陷描述及解决方案

注塑缺陷描述及解决方案注塑是一种常用的塑料加工方法,通过将熔化的塑料材料注入模具中,经过冷却固化后得到所需的塑料制品。
然而,在注塑过程中,可能会出现一些缺陷,影响产品的质量和性能。
本文将详细描述常见的注塑缺陷,并提供相应的解决方案。
一、缺陷描述1. 短射(Short Shot):指注塑过程中塑料未充满模具腔体,导致制品缺少某些部分或整体不完整。
解决方案:可能的原因包括模具温度过低、注塑速度过快、塑料材料不足等。
解决方法包括增加模具温度、调整注塑速度、增加塑料材料供给量等。
2. 翘曲(Warping):指注塑制品在冷却后产生变形,失去原本的平整形状。
解决方案:可能的原因包括模具温度不均匀、冷却时间不足、注塑压力过大等。
解决方法包括优化模具设计、增加冷却时间、减小注塑压力等。
3. 气泡(Air Traps):指注塑制品中出现气泡或空洞。
解决方案:可能的原因包括塑料材料中含有水分、注塑压力不稳定、模具排气不畅等。
解决方法包括使用干燥的塑料材料、调整注塑压力、改善模具排气系统等。
4. 热缩(Shrinkage):指注塑制品在冷却后出现尺寸缩小的现象。
解决方案:可能的原因包括模具温度过高、冷却时间不足、塑料材料收缩率不合理等。
解决方法包括降低模具温度、增加冷却时间、选择合适的塑料材料等。
5. 热裂纹(Hot Cracks):指注塑制品在冷却过程中出现裂纹。
解决方案:可能的原因包括注塑温度过高、冷却速度过快、塑料材料选择不当等。
解决方法包括降低注塑温度、控制冷却速度、选择合适的塑料材料等。
二、解决方案1. 优化模具设计:合理设计模具结构,确保充模充型均匀,避免短射、翘曲等缺陷的发生。
2. 控制注塑工艺参数:包括模具温度、注塑速度、注塑压力等。
通过调整这些参数,可以解决短射、翘曲、气泡等缺陷。
3. 选择合适的塑料材料:不同的塑料材料具有不同的性能和特点,选择合适的材料可以避免热缩、热裂纹等缺陷的发生。
4. 增加冷却时间:适当延长注塑制品的冷却时间,有助于避免翘曲、热缩等缺陷的产生。
注塑成型各种缺陷的现象及解决方法
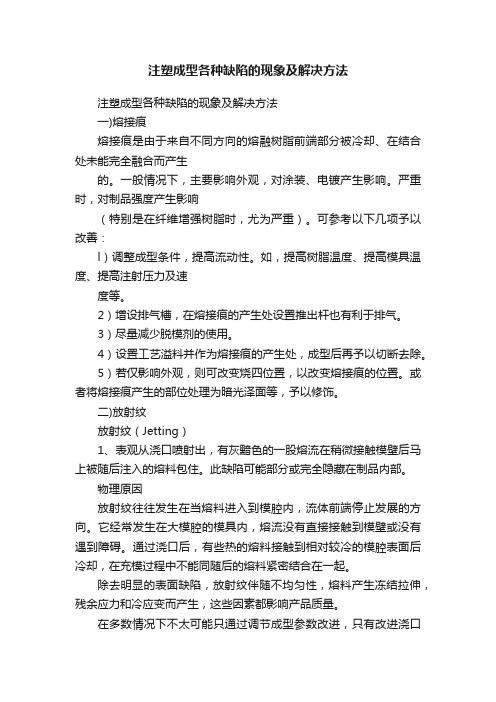
注塑成型各种缺陷的现象及解决方法注塑成型各种缺陷的现象及解决方法一)熔接痕熔接痕是由于来自不同方向的熔融树脂前端部分被冷却、在结合处未能完全融合而产生的。
一般情况下,主要影响外观,对涂装、电镀产生影响。
严重时,对制品强度产生影响(特别是在纤维增强树脂时,尤为严重)。
可参考以下几项予以改善:l)调整成型条件,提高流动性。
如,提高树脂温度、提高模具温度、提高注射压力及速度等。
2)增设排气槽,在熔接痕的产生处设置推出杆也有利于排气。
3)尽量减少脱模剂的使用。
4)设置工艺溢料并作为熔接痕的产生处,成型后再予以切断去除。
5)若仅影响外观,则可改变烧四位置,以改变熔接痕的位置。
或者将熔接痕产生的部位处理为暗光泽面等,予以修饰。
二)放射纹放射纹(Jetting)1、表观从浇口喷射出,有灰黯色的一股熔流在稍微接触模壁后马上被随后注入的熔料包住。
此缺陷可能部分或完全隐藏在制品内部。
物理原因放射纹往往发生在当熔料进入到模腔内,流体前端停止发展的方向。
它经常发生在大模腔的模具内,熔流没有直接接触到模壁或没有遇到障碍。
通过浇口后,有些热的熔料接触到相对较冷的模腔表面后冷却,在充模过程中不能同随后的熔料紧密结合在一起。
除去明显的表面缺陷,放射纹伴随不均匀性,熔料产生冻结拉伸,残余应力和冷应变而产生,这些因素都影响产品质量。
在多数情况下不太可能只通过调节成型参数改进,只有改进浇口位置和几何形状尺寸才可以避免。
与加工参数有关的原因与改良措施见下表:1、注射速度太快降低注射速度2、注射速度单级采用多级注射速度:慢-快3、熔料温度太低提高料筒温度(对热敏性材料只在计量区)。
增加低螺杆背压与设计有关的原因与改良措施见下表:1、浇口和模壁之间过渡不好提供圆弧过渡2、浇口太小增加浇口3、浇口位于截面厚度的中心浇口重定位,采用障碍注射、工艺溢料是指用手工在模具上開一條深一些的排气槽,在生產時此槽產生出來的(批峰),又叫工藝批峰,主要是用來改善燒膠或熔接痕,可將燒膠或熔接痕調整到此批峰上,生產后將其切除。
注塑成型常见不良现象及处理措施

注塑成型常见不良现象及处理措施注塑成型常见的不良现象有以下几种:
1. 短射:指注塑料进模型中未充满模腔,导致产品缺陷。
处理措施:增加注射
压力、延长注射时间、增加料缸温度、增加模具温度、增加模具出料口直径等。
2. 气泡:指产品表面或内部出现气泡,影响产品质量。
处理措施:增加注射压力、延长注射时间、增加模具温度、增加料缸温度、增加模具出料口直径、增加模具排气孔等。
3. 热熔线:指产品表面出现细小的线状缺陷,通常是由于注射速度过快导致的。
处理措施:减小注射速度、增加模具温度、增加模具出料口直径等。
4. 毛刺:指产品表面出现细小的凸起,通常是由于模具设计不合理或模具磨损
导致的。
处理措施:修复模具、修改模具设计、增加模具温度、增加模具出料口直径等。
5. 缩水:指产品尺寸缩小,通常是由于注射压力不足或冷却时间不足导致的。
处理措施:增加注射压力、延长冷却时间、增加模具温度等。
6. 毛洞:指产品表面或内部出现凹陷,通常是由于注射速度过快或模具设计不
合理导致的。
处理措施:减小注射速度、修改模具设计、增加模具温度等。
处理不良现象的关键是找到问题的根源,然后针对性地采取相应的处理措施。
同时,注塑成型过程中的参数控制和模具维护也是关键的因素,需要进行定期检查和调整。
注塑缺陷描述及解决方案

注塑缺陷描述及解决方案引言概述注塑是一种常见的塑料加工方法,但在生产过程中常常会出现一些缺陷,影响产品质量和生产效率。
本文将介绍注塑缺陷的常见描述和解决方案。
一、短射1.1 描述:短射是指注塑成型时,塑料材料未充满模具腔体,导致产品表面或内部出现缺陷。
1.2 原因:可能是注射压力不足、模具温度不稳定、料斗内塑料不足等。
1.3 解决方案:增加注射压力、调整模具温度、确保料斗内塑料充足等。
二、气泡2.1 描述:气泡是指产品表面或内部出现的气体孔洞,影响产品的外观和性能。
2.2 原因:可能是注塑过程中塑料材料中含有水分、注射速度过快、模具排气不畅等。
2.3 解决方案:使用干燥塑料材料、减慢注射速度、改进模具结构以提高排气效果等。
三、热缩3.1 描述:热缩是指产品在冷却后尺寸缩小,导致尺寸不稳定或变形。
3.2 原因:可能是模具温度不均匀、冷却时间不足、塑料材料热胀冷缩系数不匹配等。
3.3 解决方案:调整模具温度均匀性、延长冷却时间、选择合适的塑料材料等。
四、毛刺4.1 描述:毛刺是指产品表面出现的细小突起,影响产品的外观和手感。
4.2 原因:可能是模具间隙过大、注射速度过快、模具表面粗糙等。
4.3 解决方案:调整模具间隙、减慢注射速度、提高模具表面光洁度等。
五、色差5.1 描述:色差是指同一批次产品颜色不一致,影响产品的整体美观度。
5.2 原因:可能是塑料材料颜色不均匀、注射温度不稳定、色母添加不均匀等。
5.3 解决方案:使用均匀颜色的塑料材料、稳定注射温度、充分混合色母等。
结论通过对注塑缺陷的描述和解决方案的介绍,可以有效提高注塑产品的质量和生产效率。
在实际生产中,需要根据具体情况采取相应的措施,及时解决问题,确保产品质量和客户满意度。
注射成型工艺—注射成型缺陷处理方法(塑料成型加工课件)

2.制品冷却
设计塑件结构时,各部位的断面厚度应尽量一致, 塑件在模具内必须保持足够 的冷却定型时间。对于模 具冷却系统的设计,必须注意将冷却管道设置在温度易 升高热量比较集中的部位,对于那些容易冷却的部位应 尽量进行缓冷,使得塑件各部分的冷却均衡。
2.锁模参数
注塑机锁模力太低,不足以维持模具的锁紧时, 就会发生披锋。应当调整塑件面积与成型压力是否超 出了设备的额定合模力,提高锁模力,如已超极限, 可以换顿位大的机台,也可以从调机工艺上调整注塑 压力,模温、射出速度、时间、位置。
3.注射参数
塑料温度太高,造成熔体粘度太低而在模板之间 溢料,可以手动射胶来观察原料的流动性,应当适当 的降低料温。
检查有无冷料腔,或位置是否正确,对于型腔较深的 模具,应在欠注的部位增设排气沟槽和排气孔。
2.供料不足
(1)无法进料 检查料斗是否物料,或加料口出现“桥架”现象。
(2)储料不足。 可适当增加螺杆注射行程,增加供料量
3.流动性差
(1)温度太低 适当增加料筒温度和模具温度,使物料在充模过程中
具有足够流动性。 (2)注射压力低
2.流动性差
提高塑料流动性有助于减小缝合线,所以在塑件 功能许可范围内,可以考虑改用流动指数为(MI)值 较高的塑料。
低温熔料的分流汇合性能较差,可适当提高料温, 廷长注射周期,促使料温上升。对模具进行加温调整 成型工艺,提高注塑压力和射出速度。
1.工艺参数
四、变形
由于产品内部收缩不一致导致内应力不同引起变形。
1.模具缺陷
在熔融塑料填充型腔时,如果两股或更多的熔料在相 遇时,前沿部分已经冷却, 使它们不能完全融合,便在 汇合处产生线性凹糟,形成熔拦痕。
注塑缺陷描述及解决方案

注塑缺陷描述及解决方案一、缺陷描述在注塑过程中,可能会浮现各种缺陷,这些缺陷会影响产品的质量和外观。
以下是常见的注塑缺陷描述:1. 气泡缺陷:在注塑制品表面或者内部浮现气泡,影响产品的美观度和强度。
2. 热胀冷缩缺陷:注塑制品在冷却过程中,由于热胀冷缩不均匀,导致产品尺寸不许确或者变形。
3. 短射缺陷:注塑模具中的塑料未能充满模腔,导致产品浮现不完整或者部份缺失。
4. 毛刺缺陷:注塑制品表面浮现细小的毛刺,影响产品的外观质量。
5. 沉痕缺陷:注塑制品表面浮现凹陷或者凸起的痕迹,影响产品的美观度。
6. 热裂缺陷:注塑制品在冷却过程中,由于塑料内部应力过大,导致浮现裂纹。
7. 毛躁缺陷:注塑制品表面浮现粗糙的纹理或者颗粒,影响产品的触感和外观。
二、解决方案针对以上注塑缺陷,可以采取以下解决方案:1. 控制注塑工艺参数:合理调整注塑机的注射速度、压力、温度等参数,确保塑料充满模腔,避免短射温和泡缺陷的发生。
2. 优化模具设计:对于容易浮现热胀冷缩缺陷的产品,可以通过优化模具结构和冷却系统设计,平衡热胀冷缩过程,减少尺寸偏差和变形。
3. 选择合适的塑料材料:根据产品的要求和使用环境,选择适合的塑料材料,以提高产品的强度和耐用性,减少热裂和毛刺缺陷的发生。
4. 加工后处理:对于浮现毛刺、沉痕和毛躁等缺陷的产品,可以采用打磨、抛光、喷涂等后处理方法,改善产品的外观质量。
5. 增加注塑模具的维护保养:定期清洁和保养注塑模具,确保模具表面光滑,减少缺陷的发生。
6. 引入质量控制措施:建立完善的质量控制体系,通过检测和测试,及时发现和解决注塑缺陷问题,确保产品质量符合要求。
总结:注塑缺陷的描述及解决方案是为了匡助生产企业更好地理解和解决注塑过程中可能浮现的问题。
通过合理调整工艺参数、优化模具设计、选择合适的材料、加工后处理和加强质量控制,可以有效地解决注塑缺陷问题,提高产品质量和客户满意度。
注塑缺陷描述及解决方案

注塑缺陷描述及解决方案一、注塑缺陷描述注塑是一种常见的塑料加工方法,用于创造各种塑料制品。
然而,在注塑过程中,可能会浮现一些缺陷,影响产品的质量和性能。
下面将描述几种常见的注塑缺陷。
1. 气泡缺陷:气泡是注塑过程中最常见的缺陷之一。
它们通常浮现在产品表面或者内部。
气泡的形成可能是由于塑料材料中的挥发性成份或者水分引起的。
此外,过高的注塑温度、注塑速度过快或者模具设计不合理也可能导致气泡缺陷的浮现。
2. 热裂缺陷:热裂是指注塑制品在冷却过程中浮现的裂纹。
这种缺陷通常发生在产品的薄壁部份或者结构复杂的零件上。
热裂的原因主要是由于注塑温度过高、冷却不均匀或者注塑材料的选择不当。
3. 热失真缺陷:热失真是指注塑制品在使用过程中由于温度变化而发生形状变化的现象。
这种缺陷通常浮现在高温环境下,例如汽车内饰件。
热失真的原因可能是注塑温度过高、材料选择不当或者产品设计不合理。
4. 缩水缺陷:缩水是指注塑制品在冷却过程中收缩产生的缺陷。
这种缺陷通常表现为产品尺寸偏小或者形状不规则。
缩水的原因可以是注塑温度过低、冷却时间不足或者注塑材料的收缩率不合适。
5. 短射缺陷:短射是指注塑过程中未能将模具腔室彻底填充的现象。
这种缺陷通常表现为产品的一部份或者多个部份未能形成完整。
短射的原因可能是注塑压力不足、注塑温度过低或者模具设计不合理。
二、注塑缺陷的解决方案针对上述描述的注塑缺陷,可以采取以下解决方案来改善产品质量和性能。
1. 控制注塑温度:合理控制注塑温度可以减少气泡、热裂和热失真等缺陷的发生。
通过调整注塑机的温度控制参数,确保塑料材料在注塑过程中达到适宜的熔融状态,从而减少缺陷的产生。
2. 优化注塑工艺:合理的注塑工艺参数设置对于减少缺陷非常重要。
通过调整注塑速度、注塑压力和冷却时间等参数,确保模具腔室能够彻底填充,并且产品能够充分冷却,从而减少短射和缩水等缺陷的发生。
3. 选择合适的注塑材料:不同的注塑材料具有不同的熔融性能和收缩率。
注塑成型缺陷及解决方法

注塑成型缺陷及解决方法注塑成型是一种常用的塑料加工方法,可以制造各种塑料制品。
然而,在注塑成型过程中会出现一些缺陷,如熔接线、气泡、缩孔、短射和翘曲等。
这些缺陷不仅会影响产品的外观和品质,还会降低产品的使用寿命。
因此,及时发现并解决这些缺陷是非常重要的。
下面将介绍一些常见的注塑成型缺陷及相应的解决方法。
1.熔接线熔接线是指注塑成型制品表面上的一条细线状痕迹,一般与注塑模具的组合线、移动线或流动前沿线相关。
解决方法有:-调整注塑模具的温度和压力,使其匹配,并避免出现组合线、移动线或流动前沿线。
-增加注塑机的射胶速度和压力,以提高塑料的充填速度。
-使用熔接线消除剂,改善塑料的熔合性能。
2.气泡气泡是指在注塑成型制品内部或表面形成的气体腔体。
解决方法有:-提高塑料的熔融温度,以便更好地排除气体。
-采用真空辅助注塑技术,在充模过程中抽取模具腔体内的空气。
-添加消泡剂,降低塑料的表面张力,以减少气泡的形成。
3.缩孔缩孔是指注塑成型制品内部或表面形成的缺陷,常常呈现圆形或椭圆形。
解决方法有:-提高熔融温度和注射速度,增加塑料的充填压力和充填时间,以促进塑料的充填和流动。
-优化注塑模具的冷却系统,以提高冷却效果,避免局部过热或过冷。
-增加塑料的流道和浇口,以减少塑料在流动过程中的紊乱。
4.短射短射是指注塑成型制品中存在充填不完全的现象,一般呈现空洞或缺料的情况。
解决方法有:-调整注塑机的射胶速度和压力,以提高塑料的充填效果。
-优化注塑模具的充填系统,提高塑料的流动性和温度分布均匀性。
-缩小制品的厚度或重新设计制品的形状,以减少塑料在充填过程中的阻力。
5.翘曲翘曲是指注塑成型制品在冷却后出现弯曲或变形的现象。
解决方法有:-优化注塑模具的冷却系统,提高冷却效果,避免制品过早脱模或过长时间停留在模具中。
-调整注塑机的注射速度和压力,使塑料充填和流动更加均匀,减少内部应力的产生。
-改变制品的结构设计,增加支撑或增加应力分散部位。
注塑缺陷描述及解决方案
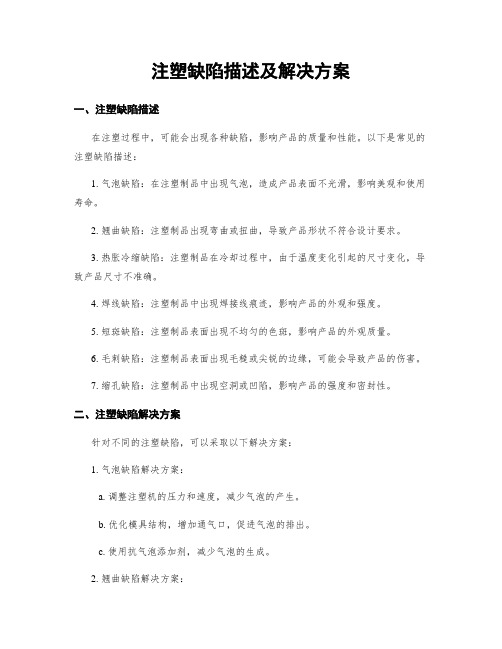
注塑缺陷描述及解决方案一、注塑缺陷描述在注塑过程中,可能会出现各种缺陷,影响产品的质量和性能。
以下是常见的注塑缺陷描述:1. 气泡缺陷:在注塑制品中出现气泡,造成产品表面不光滑,影响美观和使用寿命。
2. 翘曲缺陷:注塑制品出现弯曲或扭曲,导致产品形状不符合设计要求。
3. 热胀冷缩缺陷:注塑制品在冷却过程中,由于温度变化引起的尺寸变化,导致产品尺寸不准确。
4. 焊线缺陷:注塑制品中出现焊接线痕迹,影响产品的外观和强度。
5. 短斑缺陷:注塑制品表面出现不均匀的色斑,影响产品的外观质量。
6. 毛刺缺陷:注塑制品表面出现毛糙或尖锐的边缘,可能会导致产品的伤害。
7. 缩孔缺陷:注塑制品中出现空洞或凹陷,影响产品的强度和密封性。
二、注塑缺陷解决方案针对不同的注塑缺陷,可以采取以下解决方案:1. 气泡缺陷解决方案:a. 调整注塑机的压力和速度,减少气泡的产生。
b. 优化模具结构,增加通气口,促进气泡的排出。
c. 使用抗气泡添加剂,减少气泡的生成。
2. 翘曲缺陷解决方案:a. 调整注塑机的温度和压力,控制翘曲的发生。
b. 优化模具结构,增加支撑结构,增强产品的稳定性。
c. 选择合适的注塑材料,减少翘曲的可能性。
3. 热胀冷缩缺陷解决方案:a. 控制注塑机的冷却时间和温度,减少尺寸变化。
b. 优化模具结构,增加冷却系统,加快冷却速度。
c. 使用具有低热胀冷缩性能的注塑材料。
4. 焊线缺陷解决方案:a. 调整注塑机的注射速度和压力,减少焊线的产生。
b. 优化模具结构,减少焊线的形成位置。
c. 使用具有良好流动性的注塑材料,减少焊线的可能性。
5. 短斑缺陷解决方案:a. 调整注塑机的温度和压力,减少短斑的产生。
b. 优化模具结构,增加注塑流道的宽度,提高注塑材料的流动性。
c. 使用具有良好熔融性的注塑材料,减少短斑的可能性。
6. 毛刺缺陷解决方案:a. 优化模具结构,减少毛刺的形成位置。
b. 调整注塑机的注射速度和压力,减少毛刺的产生。
注塑缺陷描述及解决方案
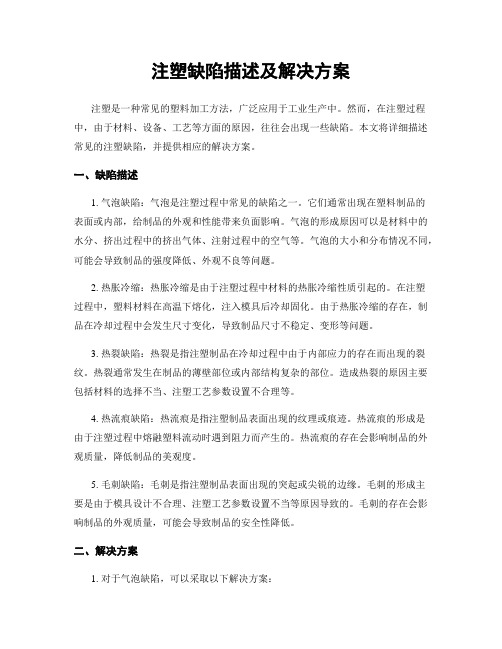
注塑缺陷描述及解决方案注塑是一种常见的塑料加工方法,广泛应用于工业生产中。
然而,在注塑过程中,由于材料、设备、工艺等方面的原因,往往会出现一些缺陷。
本文将详细描述常见的注塑缺陷,并提供相应的解决方案。
一、缺陷描述1. 气泡缺陷:气泡是注塑过程中常见的缺陷之一。
它们通常出现在塑料制品的表面或内部,给制品的外观和性能带来负面影响。
气泡的形成原因可以是材料中的水分、挤出过程中的挤出气体、注射过程中的空气等。
气泡的大小和分布情况不同,可能会导致制品的强度降低、外观不良等问题。
2. 热胀冷缩:热胀冷缩是由于注塑过程中材料的热胀冷缩性质引起的。
在注塑过程中,塑料材料在高温下熔化,注入模具后冷却固化。
由于热胀冷缩的存在,制品在冷却过程中会发生尺寸变化,导致制品尺寸不稳定、变形等问题。
3. 热裂缺陷:热裂是指注塑制品在冷却过程中由于内部应力的存在而出现的裂纹。
热裂通常发生在制品的薄壁部位或内部结构复杂的部位。
造成热裂的原因主要包括材料的选择不当、注塑工艺参数设置不合理等。
4. 热流痕缺陷:热流痕是指注塑制品表面出现的纹理或痕迹。
热流痕的形成是由于注塑过程中熔融塑料流动时遇到阻力而产生的。
热流痕的存在会影响制品的外观质量,降低制品的美观度。
5. 毛刺缺陷:毛刺是指注塑制品表面出现的突起或尖锐的边缘。
毛刺的形成主要是由于模具设计不合理、注塑工艺参数设置不当等原因导致的。
毛刺的存在会影响制品的外观质量,可能会导致制品的安全性降低。
二、解决方案1. 对于气泡缺陷,可以采取以下解决方案:a. 在材料加工前,对原料进行干燥处理,以减少材料中的水分含量。
b. 在注塑过程中,控制好挤出和注射过程中的温度和压力,避免产生气泡。
c. 优化模具设计,合理设置通气孔,以便将气泡排出。
2. 对于热胀冷缩问题,可以采取以下解决方案:a. 在模具设计中考虑材料的热胀冷缩性质,合理设置模具尺寸和结构,以减少尺寸变化。
b. 控制注塑过程中的温度和冷却时间,避免过快的冷却导致热胀冷缩问题。
常见注塑缺陷及解决措施

1.充填不足2.溢料3.气孔4.波纹5.银条纹6.表面晕喑7.融合线8.气泡9.黑条纹及烧痕10.龟裂11.离模溢料12.弯曲13.脱模不良14.直浇口的脱模不良15.材料的叠边不良不良现象及其原因处理办法1、充填不足[1] 成形品的体积过大i)要使用成形能力大的成形机。
ii)使用成形多数个成品的模具时,要关闭内腔。
[2] 流道、浇口过小i)扩展流道或浇口。
ii)放快射出速度。
iii)增强射出压力。
[3] 喷头温度低i)喷射空气,以排出冷却的材料。
ii)升高材料的温度。
iii)改用大型喷头。
[4] 材料的温度或者射出压力低i)升高材料的温度。
ii)增强射出压力。
iii)添加外部润滑。
[5] 内腔里的流体流动距离过长i)设置冷余料洼坑。
ii)升高材料的温度。
[6] 模具温度低了i)升高模具温度。
ii)放快射出速度。
iii)增强射出压力。
i)升高材料的温度[7] 射出速度慢了i)加快射出速度。
ii)升高材料的温度[8] 材料的供给量过少如属螺桨式装置,增加增塑量;而采用柱塞方式时,则增加从料斗落下的数量。
ii)减少外部润滑,改进螺桨的加工条件[9] 排气不良i)放慢射出速度。
ii)将填充不良的位置改为镶件结构或在模具上加设排气槽。
iii)改变胶口的位置iiii)改变成形品的厚度2.2、溢料[1]锁模力不足i)加强锁模力。
ii)降低射出压力。
iii)改用大型成形机。
i)确实调整好连杆。
[2]模具不好i)补修导推杆或导钉梢的部位ii)修正模具安装板。
增加支撑柱。
iii)使用轨距联杆的强度足够的成机i)确实做好模具面的贴合。
[3]模具面的杂质i)除去杂物[4]成形品的投影面积过大i)使用大型成形机。
[5]材料的温度过高i)降低材料的温度。
ii)放慢射出速度。
[6]材料供给量过剩i)调整好供给量。
[7]射出压力高i)降低射出压力。
ii)降低材料的温度3.气孔在材料为充分干燥时,是挥发物或空气所致;大多时候发生在产品胶厚的位置,实际是材料的收缩引起的真空气泡[1] 流道或浇口过小i)将流道或浇口扩展。
5.7 注射成型常见缺陷及对策
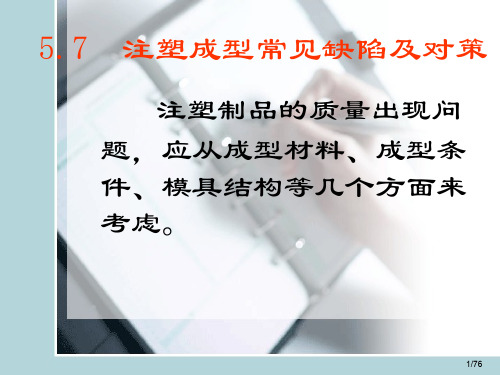
图5-67 双色(清色)注射装置 1一注射装置(1) 2一注射装置(2) 3一定模板 4一回转盘 5一回转盘驱动装置 6一动模板 7-合模机构
47/76
如图双色(清色)注塑机的 注射装置,它具有两个独立的 塑化部件,一个公用的合模系 统,两副模具,其中两副模具 的型芯相同,型腔不同(B的 型腔大于A),型芯固定在与 动模板相连的回转板上,回转 板有单独的驱动机构,可绕中 心轴线旋转1800。
39/76
电 加 热 器
图5-64 恒温控制水加热系统 1一出水阀 2一回水阀 3一电磁阀 4一放水阀 5一安全阀 6一充水阀 7一热水泵
40/76
热固性塑料注射机与热塑性塑料注射机的比较
热固性塑料注射机
料筒一般用水或油加热,温度较低 螺杆压缩比小,一般为1.05~1.2 螺杆长径比小,一般为12~18 螺杆与料筒间隙小 螺杆头部为锥形(约600) 喷嘴为敞开式,易装卸,无需加热
19/76
5.7.5 翘曲
缺陷特征:注塑制品的形状偏离 了模具型腔的形状。
20/76
产生原因
收缩率各向异性;制品 壁厚或温度引起的收缩率差; 制品内部存在残余应力。
21/76
对策
• 成型材料的改进:选用流动性好的材 料;选择收缩率各向异性小的材料。 • 成型条件的改进:提高注射温度;降 低注射压力;选用适当的模具温度; 延长冷却时间;逐渐降低保压压力; 冷却取出制品的机械手装置等。 • 模具结构的改进:改变浇口的位置; 采用合适的冷却系统;改善模具表面 光洁度;改善顶出方式。
精密注射成型机
特点: • 采用直压式锁模系统,锁模力高; • 计量装置精密,重复性好; • 注射速度高,注射相应快; • 塑化能力强,均匀程度高。
注塑缺陷描述及解决方案

注塑缺陷描述及解决方案一、注塑缺陷描述注塑是一种常用的塑料加工方法,但在注塑过程中常会浮现一些缺陷。
以下是常见的注塑缺陷描述:1. 气泡:注塑制品表面浮现小气泡,影响外观质量。
2. 热缩:制品在注塑后浮现尺寸变化,导致尺寸不许确。
3. 热分解:注塑过程中,塑料材料发生热分解,导致制品表面浮现黑斑或者发黄。
4. 热裂纹:注塑制品在冷却过程中浮现裂纹。
5. 短射:注塑模具中未彻底填充塑料材料,导致制品缺少部份或者彻底缺失。
6. 缩痕:注塑制品表面浮现凹陷或者凸起的痕迹。
7. 毛边:注塑制品边缘浮现毛糙或者不平整。
8. 色差:注塑制品颜色不均匀或者与预期颜色不符。
二、解决方案针对以上注塑缺陷,可以采取以下解决方案:1. 气泡:增加注塑过程中的压力和温度,使用抗气泡添加剂,调整注塑工艺参数。
2. 热缩:优化注塑模具设计,增加冷却系统,控制注塑过程中的温度。
3. 热分解:选择合适的塑料材料,避免过高的注塑温度,加强模具通风。
4. 热裂纹:优化注塑模具设计,增加冷却时间,降低注塑温度。
5. 短射:调整注塑工艺参数,增加注塑压力和速度,优化模具结构。
6. 缩痕:增加注塑压力和温度,调整模具结构,增加冷却时间。
7. 毛边:优化模具设计,增加模具表面光洁度,调整注塑工艺参数。
8. 色差:选择合适的塑料材料,控制注塑温度和时间,使用色母粒。
除了以上解决方案,还可以通过对注塑设备进行维护保养,提高操作人员的技术水平,加强质量检验等措施来预防和解决注塑缺陷问题。
总结:注塑缺陷是在注塑加工过程中常见的问题,但通过合理的解决方案可以有效降低缺陷率,提高注塑制品的质量。
在实际生产中,需要根据具体情况选择合适的解决方案,并进行持续改进和优化,以确保注塑制品的质量和生产效率。
注射成型中常见缺陷及解决方法

注射成型中常见缺陷及解决方法注塑成型过程中,很容易发生一些异常现象,比如说:裂纹、制品表面有波纹、制品脆性强度下降、脱模难、制品尺寸不稳定、制品尺寸不稳定、制件脱皮分层、熔接痕、注射不满等,这些现象都会影响到成型模具的具体使用效果,因此我们需要找出相关因素以及解决方法。
裂纹1.模具太冷,调整模具温度。
2.冷却时间太长,降低冷却时间。
3.塑料和金属嵌件收缩不一样,对金属嵌件预热。
4.顶出装置倾斜不平衡,顶出截面积小或分布不当,调整顶出装置或合理安排顶杆数量及其位置。
5.制作斜度不够,脱模难,正确设计脱模斜度。
制品表面有波纹1.物料温度低,拈度大提高料温。
2.注射压力,料温高,可减少注射压力,反之则加大注射压力。
3.模具温度低,提高模具温度或增大注射压力。
4.注射速度太慢提高注射速度。
5.浇口太小,适当扩展浇口。
制品脆性强度下降1.料温太高,塑料分解,降低料温,控制物料在料筒内滞留时间。
2.塑料和嵌件处内应力过大,对嵌件预热,保证嵌件周围有一定厚度的塑料。
3.塑料回用次数多控制回料配比。
4.塑料含水,原料预热干燥。
脱模难1.模具顶出装置结构不良,改进顶出设计。
2.模腔脱模斜度不够,正确设计模具。
3.模腔温度不合适,适当控制模温。
4.模腔有接缝或存料,清理模具。
5.成型周期太短或太长,适当控制注塑周期6.模芯无进气孔,修改模具。
制品尺寸不稳定1.机器电路或油路系统不稳,修正电器或油压系统。
2.成型周期不一样,控制成型周期,使一致。
3.温度。
时间。
压力变化,调节,控制基本一致。
4.塑料颗粒大小不一,使用均一塑料。
5.回收下脚料与新料混合比例不均,控制混合比例,使均匀。
6.加料不均控制或调节加料均匀。
制件脱皮分层1.不同塑料混杂,采用单一品种的塑料。
2.同一塑料不同牌号混杂,采用同牌号的塑料。
3.塑化不良,提高成型温度。
4.混入异物,清理原材料,出去杂质。
熔接痕1.塑料温度太低提高机筒。
喷嘴及模具温度。
2.浇口太多减少浇口或改变浇口位置。
- 1、下载文档前请自行甄别文档内容的完整性,平台不提供额外的编辑、内容补充、找答案等附加服务。
- 2、"仅部分预览"的文档,不可在线预览部分如存在完整性等问题,可反馈申请退款(可完整预览的文档不适用该条件!)。
- 3、如文档侵犯您的权益,请联系客服反馈,我们会尽快为您处理(人工客服工作时间:9:00-18:30)。
注射成型制品常见缺陷及处理方法
注射成型制品是指采用注射成型方法制造的许多小零件或大型组件,它们可在产品设计中发挥重要作用。
但是,由于过程中精度要求较高,过程中许多参数影响都会导致注射成型制品存在缺陷。
本文将简要介绍注射成型制品的常见缺陷,并针对每种缺陷提出适当的处理方法。
一、变形
变形是注射成型制品最常见的缺陷之一,它会引起零件的精度降低,从而影响到产品的性能。
变形的可能原因有:1、机械过程中,制品本身的塑性变形;2、因使用的树脂处于过热、过冷或非预期温度而引起的变形,造成注射成型制品不能正常复原;3、未正确设置成型模具,或者成型模具受到外界力的作用而变形;4、有时在模具安装时失误导致成型制品变形,以及使用不符合凭证技术要求的树脂也会导致制品变形。
处理变形的方法:
1、正确选择注射参数,通过调整模具温度,填充时间和填充压力,确保注射制品有良好的外观和尺寸的精度。
2、在实际操作中,要控制成型模具的加热温度,确保模具表面均匀加热,防止模具变形造成注射件变形。
3、如果成型模具受到外界气流或外力的影响,应及时修复或更
换模具,以避免变形。
4、当成型失败或发现变形时,仔细检查模具,确认模具是否损坏,是否受到外界力的影响,以确保模具的正常使用。
二、夹杂缺陷
夹杂缺陷是指在注射成型过程中,由于树脂的杂质和模具的不良,使得成型制品中的缺陷看起来像是被夹带在其中的物体。
例如:有气泡、缺口、裂痕和氧化物等。
夹杂缺陷的处理方法:
1、在注射成型之前做好质量检查,确保注射树脂无杂质,成型
模具也是新的,没有夹杂物。
2、调整注射压力,确保注射树脂能均匀流动,有效防止出现夹
杂缺陷。
3、注射完成后,应及时进行上料清理,以避免残留的杂质,造
成进一步的夹杂缺陷开发。
三、热变形
热变形是指在热加工前后发生的变形,这是由于注射成型制品的结晶受到热能的影响而导致的。
热变形的可能原因有:1、模具温度
的不均匀,使得制品的一部分处于低温状态,另一部分处于高温状态;
2、制品本身含有杂质,在热加工过程中,杂质会留在制品中,使得
制品变形;3、热处理过程中,热能会转移到制品内部,从而导致制
品变形。
处理热变形的方法:
1、调节成型模具的温度,使成型模具上下料面保持均匀温度,以确保注射成型制品可以正常成型;
2、在实际操作中,应控制树脂的温度,确保树脂处于适宜的温度,避免使用过热、过冷的树脂;
3、可以采用添加剂的方法,增加树脂的热稳定性,以防止注射成型制品受到热能影响而变形;
4、在热处理完成后,应及时进行冷却处理,以确保注射件能够正常复原。
四、表面缺陷
表面缺陷是指注射成型制品表面存在的缺陷,主要有气孔、毛刺、针孔、裂痕等。
表面缺陷的可能原因有:1、树脂过于疏松,树脂过稀会使注射成型制品表面出现气孔;2、模具的加热不均匀或模具受外力作用,也会使注射件表面出现毛刺或裂痕;3、模具尺寸不精确或模具表面存在疏洞或缺口,也会使注射件表面出现针孔。
处理表面缺陷的方法:
1、在注射成型过程中,要正确选择注射压力和模具参数,使树脂填充均匀,防止表面缺陷的产生。
2、模具要定期清洗,以免模具表面的污物,或模具表面有缺口和毛刺,影响注射件的质量。
3、在热处理过程中,要保持恒温,确保模具温度均匀,以防止成型制品表面出现针孔和裂痕。
4、定期检查树脂是否有杂质,以确保树脂中无杂质,防止注射
件表面出现气孔。