注塑部模具试模报告书-d73ed963998fcc22bcd10da0
注塑模具试模报告(最完美)

注塑模具试模报告引言注塑模具试模是一个关键的过程,它对产品的质量和生产效率具有重要影响。
本报告旨在详细介绍注塑模具试模过程中的各个环节,为了实现最完美的结果,我们将从模具设计、材料选择、工艺参数设置、试模测试以及优化改进等方面进行阐述。
概述注塑模具试模是在注塑机上进行的模具性能测试过程,通过对模具进行试模可以评估其性能和功能的可靠性,以确保产品能够满足设计要求。
试模过程中需要考虑模具的定位精度、注塑过程的稳定性、产品的成型质量等因素。
正文内容一、模具设计1. 模具结构设计:模具的结构设计应考虑产品的设计要求和注塑工艺的特点,确保模具能够精确定位并顺利进行注塑过程。
2. 模具材料选择:模具的材料选择应考虑产品的成型要求、生产批量和模具寿命等因素,常用的模具材料有硬质合金、工具钢、不锈钢等。
二、材料选择1. 塑料材料选择:根据产品的用途和要求选择合适的塑料材料,考虑其热稳定性、机械性能、耐化学腐蚀性等。
2. 材料预处理:塑料材料在注塑前需要进行干燥处理,以确保材料的质量和注塑过程的稳定性。
三、工艺参数设置1. 注射压力与速度设置:注射压力和速度的设置应根据产品形状、尺寸和壁厚等因素进行合理调整,以防止产生缺陷,如短射、热裂纹等。
2. 注射温度控制:注射温度的控制对于保证产品的成型质量至关重要,应根据塑料材料的熔融温度进行合理设定。
3. 模具温度控制:模具温度的控制能够影响产品的收缩和表面质量,应根据塑料材料的热性能设定合适的温度。
四、试模测试1. 注塑工艺试模:在试模过程中,通过调整工艺参数进行试模测试,如调整注射速度、温度等,评估产品的造型效果和成型质量。
2. 模具寿命测试:通过连续进行多次试模测试,以评估模具的寿命和性能稳定性,确定模具是否需进行改进或调整。
五、优化改进1. 问题分析和解决:根据试模测试的结果,分析产生的缺陷及其原因,并提出相应的解决方案,如调整工艺参数、优化模具结构等。
2. 模具维护与保养:及时进行模具的维护和保养工作,延长模具的使用寿命,提高生产效率和产品质量。
注塑模具试模实习报告

实习报告一、实习背景与目的本次实习是在XX公司进行的注塑模具试模实习,实习时间为2021年6月1日至2021年6月30日。
实习目的是通过实际操作,了解注塑模具的工作原理和试模过程,提高自己的实践能力和技术水平。
二、实习内容与过程在实习期间,我参与了注塑模具的拆装、清洗、涂润滑油、试模等环节。
以下是具体的实习内容与过程:1. 注塑模具的拆装:在导师的指导下,我学会了如何正确拆卸和装配注塑模具。
拆装过程中要注意标记好各个零件,以免在装配时出现错误。
同时,还要注意清洗模具零件,去除上面的污垢和残留物。
2. 清洗与涂润滑油:拆下的模具零件要进行清洗,去除上面的污垢和残留物。
然后,涂抹适量的润滑油,以减少模具零件在运动过程中的磨损。
3. 试模:在试模过程中,我学会了如何调整注塑机的参数,如压力、速度、料量等,以保证产品的质量。
在试模过程中,要随时观察产品的成型情况,如结合线、排气等,及时调整参数。
4. 产品检查:试模完成后,要与设计图纸进行对比,检查产品的尺寸、外观等是否符合要求。
如有问题,要分析原因,并采取相应的措施进行调整。
三、实习收获与体会通过本次实习,我对注塑模具的试模过程有了更深入的了解,掌握了注塑模具拆装、清洗、涂润滑油、试模等基本操作技能。
同时,我也明白了理论知识与实践相结合的重要性,知道了在实际操作中要注意的问题。
首先,注塑模具的拆装要注意标记好各个零件,以免在装配时出现错误。
其次,清洗模具零件时要彻底,去除上面的污垢和残留物。
涂抹润滑油时要适量,以减少模具零件在运动过程中的磨损。
在试模过程中,要根据产品的质量要求,调整注塑机的参数,如压力、速度、料量等。
同时,要随时观察产品的成型情况,如结合线、排气等,及时调整参数。
最后,试模完成后要与设计图纸进行对比,检查产品的尺寸、外观等是否符合要求。
如有问题,要分析原因,并采取相应的措施进行调整。
四、实习总结通过本次实习,我不仅学到了注塑模具试模的相关知识和技能,还培养了自己的团队合作意识和解决问题的能力。
注塑模具出厂自检检查报告

13 模具运水接头是否符合要求(快速接头)
14 模具是否根据设计要求安装计数器
15
模具顶针板、边锁模架、边锁天侧、编码钢印、定位环及前后模 板是否符合设计要求
16 顶出时顺畅、无卡滞、无异响
17
滑动部件有油槽(顶杆除外),表面进行氮化处理,硬度HV700。 (大型滑块按客户要求)
18 顶针板复位到底
3
进出油嘴、进出气嘴是否同冷却水嘴,并在IN、OUT前空一个字 符加G(气)、O(油)
4
模具安装方向上的上下侧开水嘴,导流槽、架上各模板有基准角符号,大写英文DATUM,字高5/16″,位置 在离边10mm处,字迹清晰、美观、整齐、间距均匀
6
模具配件无影响模具的吊装和存放,如安装时下方有外露机构 等,应有支撑腿保护
(注塑)模具出厂检验报告
日 期:2019年11月18日
模号
模具名称
制作商
检验人
检查项目 序号
标准
1 有水路铭牌 、美的铭牌、表面已按美的要求刷上油漆
模具外观
模具结构 (顶出、 活动件、
取件)
模具结构 (冷却) 模具结构 (一般浇 注系统)
模具结构 (热流道
系统)
2
冷却水嘴有进出标记,进水为IN,出水为OUT,IN、OUT后加顺序 号,如IN1、OUT1
44
模架锁紧面研配到位,90%以上面积碰到(模具平衡块应碰到 位)
45 分型面封胶部分符合设计标准
46 皮纹及喷砂达到客户要求
47 打上物料编号、材料回收标示或设计要求的标志及商标等字符
48 产品外观、尺寸、装配性符合产品图纸设计要求
49 模具试模符合设计要求
50 模具的生产周期时间是否达到设计(合同)要求 51 模具材质及硬度符合模具技术要求
试模总结报告范文(3篇)
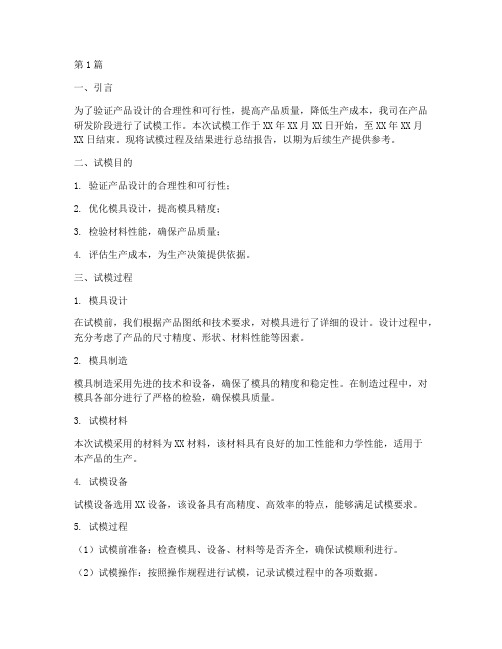
第1篇一、引言为了验证产品设计的合理性和可行性,提高产品质量,降低生产成本,我司在产品研发阶段进行了试模工作。
本次试模工作于XX年XX月XX日开始,至XX年XX月XX日结束。
现将试模过程及结果进行总结报告,以期为后续生产提供参考。
二、试模目的1. 验证产品设计的合理性和可行性;2. 优化模具设计,提高模具精度;3. 检验材料性能,确保产品质量;4. 评估生产成本,为生产决策提供依据。
三、试模过程1. 模具设计在试模前,我们根据产品图纸和技术要求,对模具进行了详细的设计。
设计过程中,充分考虑了产品的尺寸精度、形状、材料性能等因素。
2. 模具制造模具制造采用先进的技术和设备,确保了模具的精度和稳定性。
在制造过程中,对模具各部分进行了严格的检验,确保模具质量。
3. 试模材料本次试模采用的材料为XX材料,该材料具有良好的加工性能和力学性能,适用于本产品的生产。
4. 试模设备试模设备选用XX设备,该设备具有高精度、高效率的特点,能够满足试模要求。
5. 试模过程(1)试模前准备:检查模具、设备、材料等是否齐全,确保试模顺利进行。
(2)试模操作:按照操作规程进行试模,记录试模过程中的各项数据。
(3)试模结果分析:对试模结果进行分析,评估产品性能和模具质量。
四、试模结果及分析1. 产品性能(1)尺寸精度:产品尺寸精度达到设计要求,符合国家标准。
(2)形状:产品形状符合设计图纸,无明显变形。
(3)表面质量:产品表面光滑,无明显划痕、气泡等缺陷。
2. 模具质量(1)模具精度:模具精度达到设计要求,无明显磨损。
(2)模具稳定性:模具在试模过程中运行稳定,无异常现象。
3. 材料性能(1)力学性能:材料力学性能符合设计要求,具有较好的强度和韧性。
(2)加工性能:材料加工性能良好,易于加工。
4. 生产成本(1)模具成本:模具成本合理,符合预算。
(2)材料成本:材料成本合理,符合预算。
五、结论1. 产品设计合理,可行性高。
2. 模具设计精度高,稳定性好。
模具试模报告单

备注:
模具硬度:□ 足够 □ 不够 □ 其他:
口 其他:
检查人员:
时 间:
试模地点
机台型号
上缸压力
下缸压力
投料数量
良品数量
下列内容填写: □ 试模人员 □ 复核人员
装 模: □容易 □正常 □很难
模具强度: □足够 □勉强 □太差
闭和高度: □太高 □正好 □偏低
具 设备匹配: □太大 □正好 □偏小 体 是否退火: □不需 □轻微 □重度 描 脱模退料: □畅顺 □偏难 □无法 述
润 滑 液: □ 用 □不用 □用油
橡胶装配: □不用 □合理 □不合理
其 它:
机台编号 保压时间 不良数量
操 作: □容易 □一般 □偏难 定 位: □偏松 □正好 □偏紧 拉 伤: □不会 □一般 □严重 毛 刺: □刮手 □较大 □较好 平面度: □很好 □正好 □较差 弧 度: □很好 □正好 □较差 尺 寸: □稳定 □不稳定 □较差 裂 纹: □不会 □容易 □不稳定 起 皱: □不会 □较皱 □不稳定
其 他:
部门
问题描述
解决方案
下次试模时间
试 生产车间 模 结 论
试模具人员:
日 期:
复核:
日 期:
1、若模具试过后无问题,在“问题点”一栏写“模具OK”。其他在相对应的“口”中打勾:√。 注
2、此份报告须在试模后的第2天10点前交到制造部主管或其他指定人员处。
模具试模报告单
试模开始时间: 模具名称
模具编号
试模结束时间:
工件名称
试模频率 第 次
模具类别
口 新模具 口 维修模 口 其他模:
试模人员
复核人员
资 料 准 备:口 模具图纸 □ 产品图 □ 工序工艺图 □ 其他相关资料
模具试模检验报告

模具厂
模具试模检验报告
第 次修改模试模
模具图号
制品材料
记录整理编号: 客户方
模具设计
制模组别
模腔数
模具宽高厚
检查日期
◆图面规格 No ◆测量项目
◆外观品质
最终判定
品检员
尺 寸 检 查测 量 值 记 入 上 栏
(对检查发现的不良项在尺寸下标“~”进行区别)
No
1
2
3
4 判 定 测量工具
三座标量床CM 二次元量床2D
激光抄数仪JG 投影仪FR
第一联(白)存根
第二联(红)市场部
第三联(黄)技术部
第四联(蓝)生产部
. .
◆图面规格 ◆测量项目 ◆外观品质
确认者
尺寸检查测量值记入上栏
(对检查发现的不良项在尺寸下标“~”进行区别)
1
2
3
4 பைடு நூலகம் 定 测量工具
常用量 具代号
游标卡尺SC 内外径千分尺LM 深度千分尺SL 双柱带表高度规HG 万能角度尺WL 量块GB
略图考备说明:
测厚规TG 针规PIN
杠杆式百分表T1OO 跳动式百分表TD
图面规格测量项目外观品质对检查发现的不良项在尺寸下标进行区别图面规格测量项目外观品质对检查发现的不良项在尺寸下标进行区别常用量具代号游标卡尺sc内外径千分尺lm深度千分尺sl测厚规tg杠杆式百分表t1oo三座标量床cm激光抄数仪jg双柱带表高度规hg万能角度尺wl量块gb针规pin跳动式百分表td二次元量床2d投影仪fr略图考备说明
注塑部模具试模报告

注塑部模具试模报告1.实验目的本实验旨在通过注塑模具试模,了解注塑工艺过程、模具设计和注塑产品性能,并通过实验结果分析模具工艺参数对注塑产品质量的影响。
2.实验原理注塑模具试模是通过将塑料熔化后,注入模具中,经过冷却后得到所需形状的产品的过程。
注塑过程主要包括塑料熔融、注射、冷却和脱模等步骤。
3.实验设备和材料实验设备:注塑机、模具、冷却系统等。
实验材料:注塑塑料料粒、色料等。
4.实验步骤4.1模具安装与调试:根据模具图纸,将模具正确安装到注塑机上,并进行相关调试,保证模具工作正常。
4.2注塑机的操作设置:根据模具试模要求,设置注塑机的工艺参数,如射胶压力、保压时间、冷却时间等。
4.3材料的准备:将注塑塑料料粒与色料按照一定比例混合,并通过熔融设备将其熔化。
4.4模具上料:将熔化的塑料顺利注入到模具的进料口,并进行注塑过程。
4.5冷却脱模:根据注塑过程中设置的冷却时间,等待注塑产品冷却固化,并进行脱模操作。
4.6清理和分析:清理注塑产品和模具,对注塑产品进行外观、尺寸和性能等方面的分析和测试。
5.实验结果与分析通过模具试模实验,得到了一定数量的注塑产品,在清理和分析过程中,对注塑产品进行了外观、尺寸和性能等方面的分析。
5.1外观分析:通过外观观察发现,注塑产品表面光滑且没有明显的瑕疵和开裂现象,达到了预期的效果。
5.2尺寸分析:通过测量注塑产品的尺寸,发现其与设计图纸上的尺寸基本一致,满足了产品设计要求。
5.3性能分析:通过对注塑产品的质量、硬度、强度等性能参数进行测试,发现其满足了产品的使用要求。
6.实验总结通过本次注塑部模具试模实验,我们了解了注塑工艺过程和模具设计的重要性。
通过设置合适的注塑工艺参数,可以获得理想的注塑产品质量。
而模具的设计和制造则直接影响了产品的外观、尺寸和性能等方面。
实验过程中,我们遵循了规范的实验操作流程,并取得了预期的实验结果。
然而,在实验过程中也存在一些问题,如注塑产品的强度和耐用性等方面需要进一步改进和优化。
新模具试模报告范文
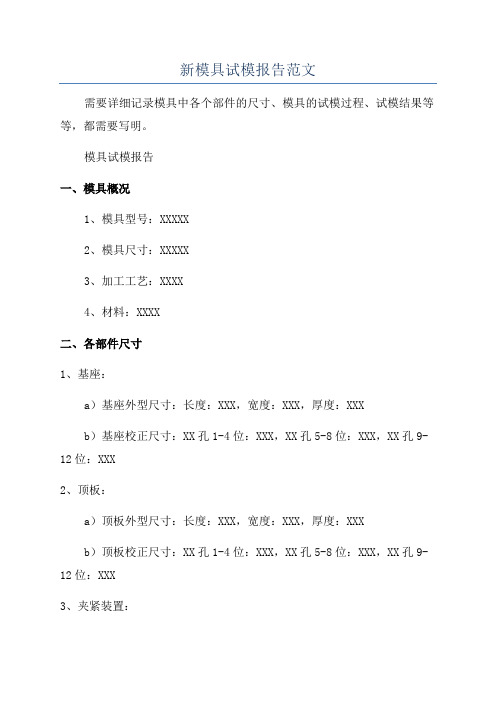
新模具试模报告范文
需要详细记录模具中各个部件的尺寸、模具的试模过程、试模结果等等,都需要写明。
模具试模报告
一、模具概况
1、模具型号:XXXXX
2、模具尺寸:XXXXX
3、加工工艺:XXXX
4、材料:XXXX
二、各部件尺寸
1、基座:
a)基座外型尺寸:长度:XXX,宽度:XXX,厚度:XXX
b)基座校正尺寸:XX孔1-4位:XXX,XX孔5-8位:XXX,XX孔9-12位:XXX
2、顶板:
a)顶板外型尺寸:长度:XXX,宽度:XXX,厚度:XXX
b)顶板校正尺寸:XX孔1-4位:XXX,XX孔5-8位:XXX,XX孔9-12位:XXX
3、夹紧装置:
a)夹紧装置外型尺寸:长度:XXX,宽度:XXX,厚度:XXX
b)夹紧装置校正尺寸:XX孔1-4位:XXX,XX孔5-8位:XXX,XX
孔9-12位:XXX
4、模芯:
a)模芯外型尺寸:长度:XXX,宽度:XXX,厚度:XXX
b)模芯校正尺寸:XX孔1-4位:XXX,XX孔5-8位:XXX,XX孔9-
12位:XXX
三、模具试模
1、模样测量:通过测量出样品尺寸,以确定模具试模结果的可靠性。
2、模具试模:按照给定的参数进行模具试模,模具运行正常,试模
过程稳定。
3、检查模具:及时及准确地检查模具,同时记录试模过程中的信息。
试模报告表模板

模 具产品型
号
试
机日模 名称胶 Nhomakorabea名 称颜台 色
期: 色种(粉)及配比:
试 模啤作条件
次数:
温度(℃)
压力(%)
射速(%)
计量
切 换.
保压 位置
回胶
啤作时间(S)
烤料
运水 模温(℃) /油
NH H3 H2 H1 P1 P2 P3 P4 HP1 HP2 HP3 V1 V2 V3 V4 S
拖花
(如有以下现象打“×”) 粘模 困气 变形 错位
麻点
模痕
其它
产
重量(g)
电镀 印刷
品
尺
整模 水口 产品
寸
试
试
模签
参
模 结
字 品质部
项目管理部
生产部
工程部
论
说明: 成型条件调整幅度:周期时间±2sec. 射出压力/速度±10%. 料管温度:±10℃. 干燥温度±5℃
S1
S2
S3
S4
S0
速度 背压 (RBM) (%)
射胶
保压
冷却
中间
周期
时间 (H)
温度 (℃)
前模
后模
运
水
出模数量 cavity
流道
顶针
大水口 细水口
流动
模具状况
(可以打“√”,不良打“×”)
脱模
排气 出模方式 尼龙栓
其它
前模
后模
试 模 (产 品 外 观) 状 况
披锋
缩水
缺胶
气纹 结合线 顶白
顶爆
烧焦
模具试模验收报告

模具
试模 :
日 期:
工程
工程签字: 注
日 期:
1、若模具试过后无问题,在“问题点”一栏写“模具OK”。其他在相对应的“口”中打勾:V。 2、此份报告须在试模后的第2天10点前交到锻压部经理或其他指定人员处。
编号:LP-RR-001
试模结束时间:
锻压模 工件名称
□ 新模具 □ 工序工艺图
□ 维修模
□ 其他模:
□ 产品图
□ 与图不符
□ 其他相关资料
模具硬度:□ 足够 □ 不够 □ 其他: 检查人员: 材料硬度 工件净重 工序时间 时 间: 良品数量 次品数量 废品数量 □不稳定 □严重 □较差 □较差 □不稳定
材料厂商 试模材料 实际用料
工件名称材料材质材料厂商材料硬度良品数量材料重量试模材料工件净重次品数量机台吨位实际用料工序时间废品数量部门下次试模时间注1若模具试过后无问题在问题点一栏写模具ok
BKM 东莞市博康五金制品有限公司
模具试模报告单
试模开始时间:
模 具 编 号 试 模 频 率 试 模 人 员 资 料 准 备:□ 模具图纸 试模 模具规格尺寸:□ 与图符合 具前 检查 备注: 材料材质 参数 材料重量 记录 机台吨位 下列内容填写: □ 装 模: □容易 闭和高度: □太高 操 作: □容易 具体 模具强度: □足够 描述 脱模退料: □畅顺 润 滑 液: □不用 其 它: 部门 问 题 描 述 模 具 类 型 模 具 类 别 复 核 人 员
试模人员 □ 复核人员 □正常 □很难 起 皱: □不会 □较皱 □正好 □偏低 拉 伤: □不会 □一般 □一般 □偏难 加 温: □常温 □勉强 □太差 平 面 度:□很好 □正好 □偏难 □无法 尺 寸:□稳定 □不稳定 □滚粉 □用油 裂 纹: □无 □有 其 他: 解 决 方 案
新模具试模报告

新模具试模报告摘要:本文是针对新模具的试模情况进行分析和总结的报告。
通过试模过程的详细记录和观察,对模具的设计和制造进行评估和优化,以提高模具的性能和效率。
本文将重点介绍试模背景、试模过程、试模结果和结论等内容。
一、试模背景模具是工业生产中常用的工具,用于制造各种产品,具有重要的作用。
随着技术的不断发展,新模具的设计和制造也不断创新和改进。
本次试模是为了验证并评估新模具的性能和可靠性,为后续的生产提供参考和依据。
二、试模过程1. 材料准备:选择合适的材料,并进行必要的加工和处理,以满足试模需求。
2. 模具装配:按照设计要求,将各个模具部件进行合理的组装调整,并进行必要的调试。
3. 试模准备:在试模前,对模具进行彻底的清洁和保养,确保模具表面的光洁度和平整度。
4. 试模操作:按照试模方案和工艺要求,对模具进行试模操作,包括开模、注塑、射出等过程。
5. 观察记录:在试模过程中,对模具的开模效果、产品的成型质量、模具的使用寿命等进行详细记录和观察。
三、试模结果通过试模过程的观察和记录,得到以下试模结果:1. 开模效果:新模具的开模效果较好,开合力均匀,无明显的卡滞和磨损。
2. 产品成型质量:新模具生产的产品尺寸精度高,表面光滑,没有明显的缺陷和瑕疵。
3. 模具寿命评估:经过一段时间的试模操作,模具表面仍保持较好的光洁度和平整度,表明模具的使用寿命较为稳定。
四、结论根据试模结果的评估和分析,可以得出以下结论:1. 新模具具有良好的开模效果,能够满足生产需求,并且平均使用寿命较长。
2. 新模具生产的产品成型质量较高,满足产品质量要求,有利于提高产品的竞争力和市场份额。
3. 在模具的制造和调试过程中,发现了一些细节问题和不足之处,需要进行优化和改进,以进一步提高模具的性能和效率。
综上所述,本次新模具的试模工作取得了较好的成果,对于提高产品质量和生产效率具有积极的促进作用。
在今后的工作中,我们将进一步优化和改进模具的设计和制造流程,不断提高模具的可靠性和稳定性,以满足不同客户和市场的需求。
塑料模具设计实验报告模板 (3000字)
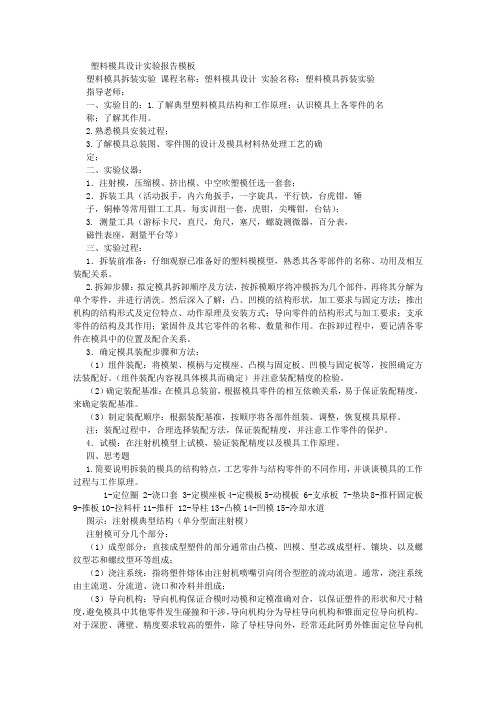
塑料模具设计实验报告模板塑料模具拆装实验课程名称:塑料模具设计实验名称:塑料模具拆装实验指导老师:一、实验目的:1.了解典型塑料模具结构和工作原理;认识模具上各零件的名称;了解其作用。
2.熟悉模具安装过程;3.了解模具总装图、零件图的设计及模具材料热处理工艺的确定;二、实验仪器:1.注射模,压缩模、挤出模、中空吹塑模任选一套套;2.拆装工具(活动扳手,内六角扳手,一字旋具,平行铁,台虎钳,锤子,铜棒等常用钳工工具,每实训组一套,虎钳,尖嘴钳,台钻);3. 测量工具(游标卡尺,直尺,角尺,塞尺,螺旋测微器,百分表,磁性表座,测量平台等)三、实验过程:1.拆装前准备:仔细观察已准备好的塑料模模型,熟悉其各零部件的名称、功用及相互装配关系。
2.拆卸步骤:拟定模具拆卸顺序及方法,按拆模顺序将冲模拆为几个部件,再将其分解为单个零件,并进行清洗。
然后深入了解:凸、凹模的结构形状,加工要求与固定方法;推出机构的结构形式及定位特点、动作原理及安装方式;导向零件的结构形式与加工要求;支承零件的结构及其作用;紧固件及其它零件的名称、数量和作用。
在拆卸过程中,要记清各零件在模具中的位置及配合关系。
3.确定模具装配步骤和方法:(1)组件装配:将模架、模柄与定模座、凸模与固定板、凹模与固定板等,按照确定方法装配好。
(组件装配内容视具体模具而确定)并注意装配精度的检验。
(2)确定装配基准:在模具总装前,根据模具零件的相互依赖关系,易于保证装配精度,来确定装配基准。
(3)制定装配顺序:根据装配基准,按顺序将各部件组装、调整,恢复模具原样。
注:装配过程中,合理选择装配方法,保证装配精度,并注意工作零件的保护。
4.试模:在注射机模型上试模,验证装配精度以及模具工作原理。
四、思考题1.简要说明拆装的模具的结构特点,工艺零件与结构零件的不同作用,并谈谈模具的工作过程与工作原理。
1-定位圈 2-浇口套 3-定模座板4-定模板5-动模板 6-支承板 7-垫块8-推杆固定板9-推板10-拉料杆11-推杆 12-导柱13-凸模14-凹模15-冷却水道图示:注射模典型结构(单分型面注射模)注射模可分几个部分:(1)成型部分:直接成型塑件的部分通常由凸模,凹模、型芯或成型杆、镶块、以及螺纹型芯和螺纹型环等组成;(2)浇注系统:指将塑件熔体由注射机喷嘴引向闭合型腔的流动流道。
新模具试模报告

水开关正常 导柱/拉杆齐全
排气良好
进胶平衡
冷却系统良好
二:试模后产品详情:
表面顶白拉白 表面顶高 表面气纹/流纹 表面模痕 粘前模 粘后模 表面毛边
表面冷胶
表面胶伤 表面胶砂
表面熔接线 变形
模仁松动 断水口
尺寸不合格 三、其他说明及建议
试模 人:
审 核:
审 批 :
表单编号: QR18-14
压力 速度 位置
射胶
一次 二次
压力
速度
位置
时间
锁模
锁模 低压 高压
保压
三次 一次 二次
试模次数 第
次
试模原因:
试模用时
H
产品单重(g)
流道重量(g)
毛重(g)
试模用料
Kg
开模师傅:
是否全程参与直至试模顺利, 是 否(试模单位填写)
一、试模后模具详情:
水路畅通
水口板开模正常
顶出梢顺畅
弹簧正常
油缸及抽芯正常
机号 模具编号
穴数 周期(S)
万沙电气有限公司注塑车间
注塑模具试模报告
设备注射量
填表人
产品名称
材料名称
颜色
色母型号
射胶(S)
冷却(S)
版本号:1.0
填表日期 材料型号 色母比例
参数产能(12H)
前模运水:
用
不用
前模油温不用
烘料温度(
℃ ) 烘料时间(
H)
温度
一段 二段 三段 四段 五段
注塑模具出厂检验报告

14
大滑块下面是否都有耐磨板(滑块宽度超过150mm),耐磨板比大面高出0.05-0.1mm,耐磨板应加油槽。
15
大型滑块(宽度超过200mm)锁紧面是否有耐磨板面高出0.1-0.5mm,上面加油槽。
16
滑块压板是否有定位结构。
序号
检 查 内 容
合 格
不合格
无
1
前后模表面是否有不平整、凹坑、锈迹等其他影响外观的缺陷。
2
镶块与模框配合,四R角是否低于1mm的间隙(最大处)。
3
分型面保持干净、整洁,无手提砂轮打磨避空,封胶部分无凹陷。
4
排气槽深度是否小于塑料的溢边值,PP小于0.03mm,ABS、PS等小于0.05mm,排气槽由机床加工,无手工打IN,出水为OUT;IN、OUT后加顺序号,如IN1、IN2、OUT1、OUT2等。标识英文字符和数字位置在水嘴正下方10mm处,字迹清晰、整齐。
4
进出油嘴、进出气嘴标识是否同冷却水嘴,并在IN、OUT前空一个字符加G(气)、O(油)。
5
模架上各模板是否有基准角符号,字迹是否清晰、整齐。各模板是否有零件编号,编号在基准角符号正下方处。
20
撑头是否比模腿高出0.05—0.15mm,并不与顶出孔干涉。
21
如注塑机采用延伸喷嘴,定位圈内部是否有足够大的空间,以保证标准的注塑机加长喷嘴带加热圈可以伸入。
22
M12(含M12)以上的螺丝是否为12.9级。
23
产品光洁度检测数据数值 (正面: 侧面: )
24
25
二、模具动作部分:
序号
检 查 内 容
- 1、下载文档前请自行甄别文档内容的完整性,平台不提供额外的编辑、内容补充、找答案等附加服务。
- 2、"仅部分预览"的文档,不可在线预览部分如存在完整性等问题,可反馈申请退款(可完整预览的文档不适用该条件!)。
- 3、如文档侵犯您的权益,请联系客服反馈,我们会尽快为您处理(人工客服工作时间:9:00-18:30)。
成型机型:
卧式
力式
其它 毛重(g)
产品单重(g)
是否全程参与直至试模顺利,
是
否(试模单位填写)
水口板开模正常 导柱/拉杆齐全
顶出梢顺畅 排气良好
弹簧正常 进胶平衡
油缸及抽芯正常 冷却系统良好
表面气纹/流纹 表面胶砂
表面模痕 表面熔接线
粘前模 变形
粘后模 模仁松动
表面毛边 断水口
试模人:
技术部:
审批:
GTG
机号
模具编号
注塑部模具试模报告
编号: 填表人 材料名称 色母型号 射胶(S) 冷却(S) 填表日期 材料型号 色母比例 参数产能(12H)
设备品牌/吨位 产品名称 颜色 周期(S)
穴数
前模运水: 后模运水: 温度 一段 二段
用 用 三段
不用 不用 四段 五段 射 胶
前模油温( 烘料温度( 压力 一次 二次 三次 保 压 一次 二次 压铸 流道重量(g)
℃ ) ℃ ) 速度
后模油温( 烘料时间( 置
℃ ) ℃ ) 时间
压力 锁模 锁模 低压 高压 试模次数 第 试模用时 试模用料 开模师傅: 一、试模后模具详情: 水路畅通 水开关正常 二:试模后产品详情: 表面顶白拉白 表面冷胶 尺寸不合格 三、其他说明及建议 表面顶高 表面胶伤 次 H Kg
速度 位置