补焊工艺规范
api,6d,阀门堆焊和补焊作业规范

api,6d,阀门堆焊和补焊作业规范篇一:API 6D 阀门堆焊和补焊作业规范API 6D 堆焊和补焊作业规范1目的规定对阀门密封面堆焊、铸件补焊等工艺要求,保证产品质量。
2范围适用于阀门产品的密封面堆焊和铸件的补焊。
(PED产品不允许补焊)。
3内容3.1从事密封面堆焊和补焊的焊工,应通过国家质量监督检疫总局制订的《锅炉压力容器压力管道焊工考试与管理规则》基本知识与操作考核,持有锅炉压力容器压力管道特种设备操作人员资格位证书,并在有效期内方可从事焊接作业。
3.2 零件基体材料铸材:WCB、CF8、CF8M、CF3、CF3M、LX0Cr18Ni9、LX 0Cr18Ni9Ti、LX 1Cr18Ni9Ti、LX 00Cr18Ni10、LX 0Cr18Ni12Mo2Ti、WC1、WC6、WC9、C5、LX Cr5Mo、LX 20CrMo、LX 20CrMoV、LX 15CrMoV、LX 1Cr13、CA15、LCB、LCC、LC1、LC2、LC3。
锻材或棒材:25、1Cr18Ni9Ti、0Cr18Ni12Mo2Ti、0Cr17Ni12Mo2、00Cr17Ni14Mo2、15CrMo、1CrMo、304、316、304L、316L、2Cr13、OOCr19NI10。
3.3焊接材料 3.3.1阀门密封面堆焊焊接材料a)基体材料为WCB、25、LCB、LCC 焊条:GB984-85 D507 D507Mo D577 GB983-85 A102 A132b)基体材料:奥氏体不锈钢类、WCB、25、LCB、LCC、WC1、WC9、LX1Cr5Mo、C5、LX20CrMo、LX20CrMoV、LX15CrMoV。
焊条:D802、D812,焊丝HS111;c)按产品图纸规定选择焊接材料牌号。
当堆焊钴基硬质合金时,根据工艺方法选择D802、D812或HS111; 3.3.2 承压铸件补焊用焊条a)基体材料为WCB,采用GB5117-85 J422、J502(型号E5003)或J507(型号E5015)焊条;b)基体材料为奥氏体不锈钢类,焊条选用见表1;c)基体材料为低温耐热钢类,焊条选用见表2;d)基体材料为低温钢类,焊条选用见表3。
模 具 补 焊 工 艺 操 作 规 范

( b )补焊量 6m/m 以上
DT-1 DT-2
冲压方向
QT500 HT300
1.5t以上
埋入螺钉
( b) 扩大量 10m/m 以上
冲压方向 DT-2
21 1 5T
6t 31
1.5t
10以下 埋入螺钉
埋入螺钉 11以上
模具补焊工艺操作规范
共3页第1页
1.本规范是根据补焊刃口及一般焊接的工艺操作规范来规定的 2.适用于铸铁(HT300~500)、球墨铸铁(QT500)和风冷钢(7CrSiMnMoV)
的补焊修理以及合金工具钢的补焊修理。
3.铸铁(HT300)球墨铸铁(QT500)的堆焊刃口。
3.1 新制的场合
①铸铁( HT300 )
冲压方向
②球墨铸铁( QT500 )
冲压方向
3
2
DT-2
3
2 DT-2
5
15
5
15
506 刃口断面
3.2 修理的场合
①面的修正
( a) 补焊量 6m/2
不做刃口时为506
QT500
1.5t 以上
②轮廓变更
( a) 扩大量 10m/m 以下
冲压方向 DT-2
506 刃口断面
铝合金铸件补焊工艺

铝合金铸件补焊工艺补焊铸件的确定:1、由检验人员确定补焊铸件,补焊部位应在铸件上标出。
2、允许补焊的缺陷如下:a)夹杂、砂眼、缩孔、气孔、冷隔等。
b)机械加工产生的机械损伤。
补焊材料:1、补焊用的焊丝应与铸件材料相同。
(以后采用铸造浇注的焊丝)2、焊丝使用时的表面应干净,无氧化物、油污和锈蚀。
铸件缺陷的清理:1、补焊前应用风动铣刀或其它工具对铸件缺陷部位进行打磨或扩修成坡口。
2、铸件缺陷部位开坡口应将缺陷完全排除,并保证坡口面光滑。
3、较大的穿透性缺陷清理后,应在背面垫上不锈钢或耐火砖片垫片,垫片应留有3-4mm的间隙,便于完全焊透。
4、对需要补焊的部位,应在离坡口边界10-30mm的范围清除掉铸皮、氧化物和其他污物,在开穿透性坡口的情况下,可从两面进行清理。
5、表面清理过的铸件应及时进行补焊,停放时间一般不超过5h.铸件补焊前的预热1、整体预热;适合各类型的铸件。
2、局部预热:局部预热可用氧—乙炔焰进行,应用中性焰进行,预热时应避免穿堂风。
局部预热的铸件,加热面积应距离缺陷坡口边界不小于200mm的地方。
3、不预热对单个的小缺陷和不易变形的铸件,可不预热。
预热要求预热温度一般为250-350度补焊手工氩弧焊补焊时,应尽量小电流,短弧焊、小直径焊丝和小体积熔敷金属,补焊过程中,焊枪与零件表面的夹角60-70度。
补焊过程的控制1、补焊时,焊缝均应有3-4mm的余高。
2、为防止铸件产生冷裂纹,补焊后应采用石棉布将其覆盖。
3、补焊时不允许近焊缝金属过热。
4、铸件的同一处允许补焊次数不超过三次。
补焊后的热处理允许补焊后的铸件余同一牌号合金同炉热处理。
2011年6月26日。
补焊工艺

直缝埋弧焊管补焊工艺卡
一、补焊规定:
1.不允许在管体上用焊接方法进行修补。
2.焊缝缺陷允许补焊,受下列条件限制:
1)补焊的最小长度为50mm;
2)两处补焊之间的最小距离为0.5t,总的修补长度不超过管长的15%;
3)在6m 长度的焊缝上,修补部位不得超过两个。
4)管端300mm范围不允许补焊;
5)同一位置已补焊过2次的不允许再次补焊。
6)扩径后不允许补焊。
3.补焊操作必须由持证焊工进行。
二、补焊工艺:
1、焊条:J557 Φ4.0/Φ3.2mm低氢型焊条
2、焊接电流:Φ4.0mm 160±20A
Φ3.2mm 110±20A
3、电源:直流反接
4、补焊前将缺陷用碳弧气刨清除,然后用角磨机去掉刨渣、夹碳,打磨见金属光泽;
5、施焊前焊条必须进行350~400℃烘焙1~2h,焊前保温温度100~150℃。
并装入保温
筒内,随取随用;
6、每焊完一道焊缝彻底清理焊渣、夹渣以及气孔、裂纹等缺陷,直到完全填满刨坑且与
母材平滑过渡,补焊完成后,用角磨机修磨焊缝至光滑;
7、要求气刨、打磨、补焊连续完成;若气刨、打磨后中断焊接,重新启焊时须将补焊区
金属预热至100~150℃,再进行补焊;
8、补焊缝余高需打磨与,内焊缝≤2.5mm,外焊缝≤2.5mm;
9、每支管补焊完毕后应进行100%外观、UT、RT检验。
铸钢件补焊通用技术规范-最新国标

铸钢件补焊通用技术规范1 范围本文件规定了铸钢件补焊的缺陷范围、缺陷等级分类、补焊前准备技术要求、补焊技术要求、焊后热处理、检验和记录。
本文件适用于承压和中小型非承压铸钢件,铸件材料为碳素钢、碳锰钢、不锈钢、合金钢和高锰钢的铸造缺陷补焊。
本文件不适用于铸件焊接性缺陷的补焊,如焊接咬边、裂纹、未熔合、未焊透、夹渣等。
2 规范性引用文件下列文件中的内容通过文中的规范性引用而构成本文件必不可少的条款。
其中,注日期的引用文件,仅该日期对应的版本适用于本文件;不注日期的引用文件,其最新版本(包括所有的修改单)适用于本文件。
GB/T 150.1 压力容器通用要求GB/T 150.4 压力容器制造、检验及验收标准GB/T 983 不锈钢焊条GB/T 984 堆焊焊条GB/T 5117 非合金钢及细晶粒钢焊条GB/T 5118 热强钢焊条GB/T 5611 铸造术语GB/T 6417.1 金属熔化焊接头缺欠分类及说明GB/T 8110 熔化极气体保护电弧焊用非合金钢及细晶粒钢实心焊丝GB/T 10045 非合金钢及细晶粒钢药芯焊丝GB/T 13927 工业阀门压力试验GB/T 17493 热强钢药芯焊丝GB/T 40800 铸钢件焊接工艺评定规范3 术语和定义GB/T 5611界定的以及下列术语和定义适用于本文件。
缺陷范围 defect scope超过设计图纸尺寸公差、超过缺陷允许尺寸和不准许存在的缺陷。
铸造缺陷 cast defect铸造生产过程中,在铸件表面和内部产生的各种缺陷的总称。
注:缺陷的形态可分为孔洞类、裂纹类、变形类等;按缺陷的性质可分为热裂纹、冷裂纹、缩孔、气孔等。
缺陷面积 defect area清理缺陷后的缺陷投影面积。
剩余壁厚 residual wall thickness清除缺陷后的壁厚。
铸件面积 surface area of castings缺陷所在表面的投影面积。
关键件 critical parts要求精度高、制造难度大、在产品中起关键作用的零件。
42CrMo通用焊补工艺
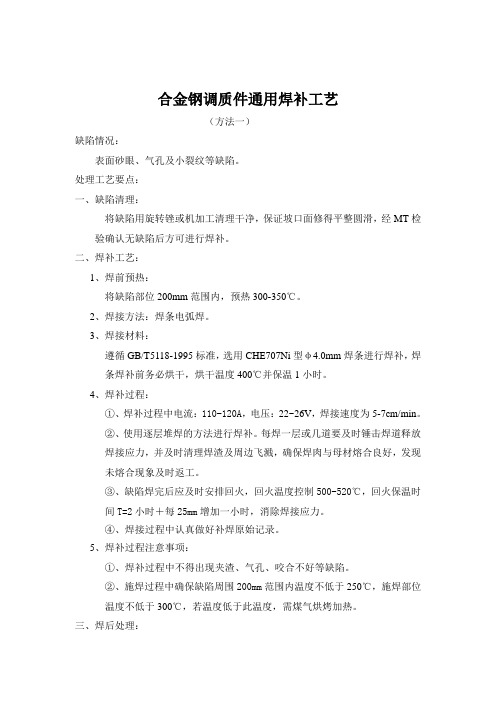
合金钢调质件通用焊补工艺(方法一)缺陷情况:表面砂眼、气孔及小裂纹等缺陷。
处理工艺要点:一、缺陷清理:将缺陷用旋转锉或机加工清理干净,保证坡口面修得平整圆滑,经MT检验确认无缺陷后方可进行焊补。
二、焊补工艺:1、焊前预热:将缺陷部位200mm范围内,预热300-350℃。
2、焊接方法:焊条电弧焊。
3、焊接材料:遵循GB/T5118-1995标准,选用CHE707Ni型φ4.0mm焊条进行焊补,焊条焊补前务必烘干,烘干温度400℃并保温1小时。
4、焊补过程:①、焊补过程中电流:110-120A,电压:22~26V,焊接速度为5-7cm/min。
②、使用逐层堆焊的方法进行焊补。
每焊一层或几道要及时锤击焊道释放焊接应力,并及时清理焊渣及周边飞溅,确保焊肉与母材熔合良好,发现未熔合现象及时返工。
③、缺陷焊完后应及时安排回火,回火温度控制500-520℃,回火保温时间T=2小时+每25mm增加一小时,消除焊接应力。
④、焊接过程中认真做好补焊原始记录。
5、焊补过程注意事项:①、焊补过程中不得出现夹渣、气孔、咬合不好等缺陷。
②、施焊过程中确保缺陷周围200mm范围内温度不低于250℃,施焊部位温度不低于300℃,若温度低于此温度,需煤气烘烤加热。
三、焊后处理:局部回火,消除焊接应力后对缺陷部位进行打磨,打磨后MT检验合格,发现不合格现象重新将缺陷清理干净后按工艺重新进行焊补,补焊次数不得超过3次。
(方法二)缺陷情况:表面砂眼、气孔及小裂纹等缺陷。
一、缺陷处理:将缺陷用旋转锉清理干净,修出焊接坡口,保证缺陷周围20mm不得有粘砂、铁锈、油垢等杂质,MT检验无缺陷后方可进行后续操作。
二、焊补工艺:1、焊前预热:缺陷周围200mm预热温度300~350℃。
2、焊补过程:气保焊,选用CHW-60C型φ1.2mm实心焊丝进行焊补,焊补①、采用CO2过程中电流:240~280A,电压:24~28V,气流量控制在:15~20L∕min。
镁合金补焊工艺规范
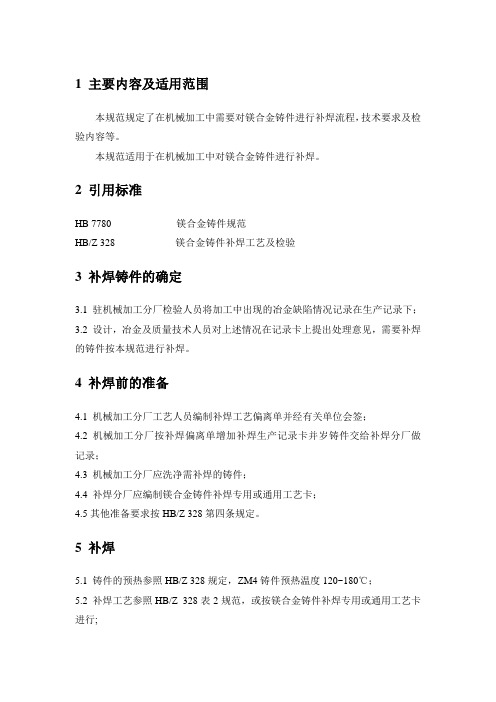
1 主要内容及适用范围本规范规定了在机械加工中需要对镁合金铸件进行补焊流程,技术要求及检验内容等。
本规范适用于在机械加工中对镁合金铸件进行补焊。
2 引用标准HB 7780 镁合金铸件规范HB/Z 328 镁合金铸件补焊工艺及检验3 补焊铸件的确定3.1 驻机械加工分厂检验人员将加工中出现的冶金缺陷情况记录在生产记录下;3.2 设计,冶金及质量技术人员对上述情况在记录卡上提出处理意见,需要补焊的铸件按本规范进行补焊。
4 补焊前的准备4.1 机械加工分厂工艺人员编制补焊工艺偏离单并经有关单位会签;4.2 机械加工分厂按补焊偏离单增加补焊生产记录卡并岁铸件交给补焊分厂做记录;4.3 机械加工分厂应洗净需补焊的铸件;4.4 补焊分厂应编制镁合金铸件补焊专用或通用工艺卡;4.5其他准备要求按HB/Z 328第四条规定。
5 补焊5.1 铸件的预热参照HB/Z 328规定,ZM4铸件预热温度120~180℃;5.2 补焊工艺参照HB/Z 328表2规范,或按镁合金铸件补焊专用或通用工艺卡进行;5.3 补焊区的个数,面积大小,热处理及重复补焊等要求应符合HB-7780第3.7条规定。
6 记录6.1 补焊操作及检验人员按镁合金铸件补焊工艺卡规定的工序等在补焊生产记录卡上做记录;6.2 应在补焊生产记录卡上附见图注明补焊区的个数、部位、重复次数按HB/Z 328第9.8条做标记;6.3 同一个铸件需要重复补焊时,每次补焊均应记录在同一份补焊生产记录卡上;6.4 补焊生产记录卡及工艺偏离单应随机械加工生产记录卡归档保存。
7 检验7.1补焊后的铸件需要做热处理的应符合HB7780第3.7.7条规定;7.2 需进行气密性使用的铸件有机械加工分厂按工艺规程规定进行;7.3 补焊区域的X光、荧光剂目视检查治疗符合HB7780规定。
因铸件结构原因不能进行X光检验的由设计、冶金及质量技术人员提出处理意见。
锻件补焊工艺
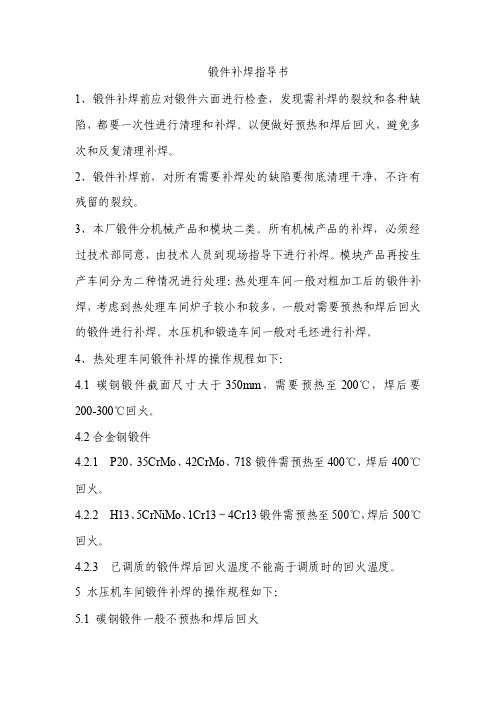
锻件补焊指导书
1、锻件补焊前应对锻件六面进行检查,发现需补焊的裂纹和各种缺陷,都要一次性进行清理和补焊。
以便做好预热和焊后回火,避免多次和反复清理补焊。
2、锻件补焊前,对所有需要补焊处的缺陷要彻底清理干净,不许有残留的裂纹。
3、本厂锻件分机械产品和模块二类。
所有机械产品的补焊,必须经过技术部同意,由技术人员到现场指导下进行补焊。
模块产品再按生产车间分为二种情况进行处理:热处理车间一般对粗加工后的锻件补焊,考虑到热处理车间炉子较小和较多,一般对需要预热和焊后回火的锻件进行补焊。
水压机和锻造车间一般对毛坯进行补焊。
4、热处理车间锻件补焊的操作规程如下:
4.1碳钢锻件截面尺寸大于350mm,需要预热至200℃,焊后要200-300℃回火。
4.2合金钢锻件
4.2.1P20、35CrMo、42CrMo、718锻件需预热至400℃,焊后400℃回火。
4.2.2H13、5CrNiMo、1Cr13~4Cr13锻件需预热至500℃,焊后500℃回火。
4.2.3已调质的锻件焊后回火温度不能高于调质时的回火温度。
5水压机车间锻件补焊的操作规程如下:
5.1碳钢锻件一般不预热和焊后回火
5.2合金钢锻件
5.2.1P20、35CrMo、42CrMo、718锻件焊补区面积在100×100×20mm 以内,不预热和焊后回火。
5.2.2P20、35CrMo、42CrMo、718锻件焊补区面积大于100×100×20mm,需预热至400℃,焊后400℃回火。
5.2.3水压机车间对H13、5CrNiMo、1Cr13~4Cr13锻件不允许补焊。
铸钢件缺陷判断及焊补工艺
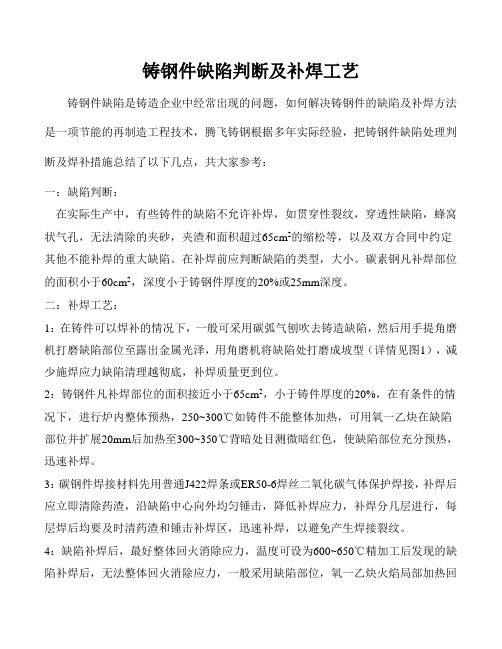
铸钢件缺陷判断及补焊工艺铸钢件缺陷是铸造企业中经常出现的问题,如何解决铸钢件的缺陷及补焊方法是一项节能的再制造工程技术,腾飞铸钢根据多年实际经验,把铸钢件缺陷处理判断及焊补措施总结了以下几点,共大家参考:一:缺陷判断:在实际生产中,有些铸件的缺陷不允许补焊,如贯穿性裂纹,穿透性缺陷,蜂窝状气孔,无法清除的夹砂,夹渣和面积超过65cm2的缩松等,以及双方合同中约定其他不能补焊的重大缺陷。
在补焊前应判断缺陷的类型,大小。
碳素钢凡补焊部位的面积小于60cm2,深度小于铸钢件厚度的20%或25mm深度。
二:补焊工艺:1:在铸件可以焊补的情况下,一般可采用碳弧气刨吹去铸造缺陷,然后用手提角磨机打磨缺陷部位至露出金属光泽,用角磨机将缺陷处打磨成坡型(详情见图1),减少施焊应力缺陷清理越彻底,补焊质量更到位。
2:铸钢件凡补焊部位的面积接近小于65cm2,小于铸件厚度的20%,在有条件的情况下,进行炉内整体预热,250~300℃如铸件不能整体加热,可用氧一乙炔在缺陷部位并扩展20mm后加热至300~350℃背暗处目测微暗红色,使缺陷部位充分预热,迅速补焊。
3:碳钢件焊接材料先用普通J422焊条或ER50-6焊丝二氧化碳气体保护焊接,补焊后应立即清除药渣,沿缺陷中心向外均匀锤击,降低补焊应力,补焊分几层进行,每层焊后均要及时清药渣和锤击补焊区,迅速补焊,以避免产生焊接裂纹。
4:缺陷补焊后,最好整体回火消除应力,温度可设为600~650℃精加工后发现的缺陷补焊后,无法整体回火消除应力,一般采用缺陷部位,氧一乙炔火焰局部加热回火方法,采用大割把中性火焰来回缓慢摆动,将铸件表面加热到目视暗红色。
(约740℃)保温(2min/mm但不少于30min)消除应力处理后立即在缺陷处盖上石棉板,防止产生裂纹。
5:JB/T5263-2005标准中规定,重缺陷补焊后应进行射线或超声波检测,即对于重缺陷和重要补焊,必须进行有效的无损检查,证明合格后方能使用。
母材表面缺陷补焊工艺规程
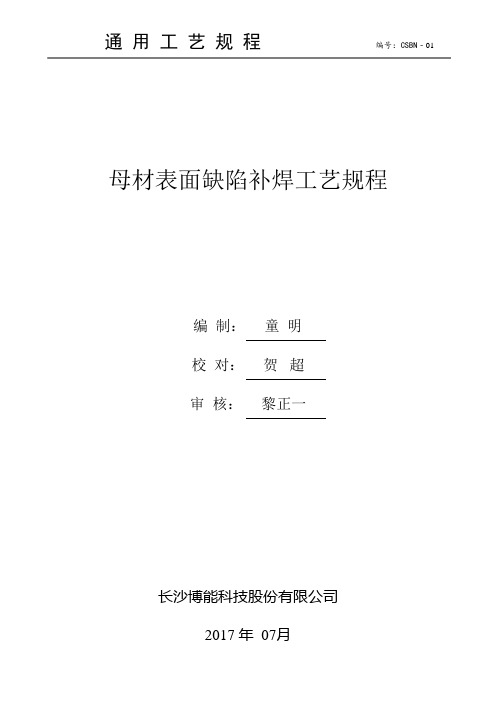
通用工艺规程编号:CSBN-01 母材表面缺陷补焊工艺规程编制:童明校对:贺超审核:黎正一长沙博能科技股份有限公司2017 年 07月一、适用范围本工艺适用于浙江恒逸文莱PMB石油化工项目220万吨/年加氢裂化装置(12台塔器)母材表面缺陷的返修。
母材表面缺陷如:凹坑、机械损伤、装配工装拆除后留下的焊疤等。
二、缺陷尺寸1. 对于深度小于0. 5mm的各类缺陷可免于修补。
2.对于大于0. 5mm小于0.05δ(δ为板厚)且≤2mm母材表面缺陷,采用打磨使之与周围母材平滑过渡;对于深度大于0.05δ(δ为板厚)且>2mm,采用如下方法(三.2.3)堆焊修补进行返修。
3. 对于复合钢板的成形件、堆焊件以及金属衬里层,深度小于0.3δ(δ为覆层、堆焊或衬里厚度)且≤1mm采用打磨使之与周围母材平滑过渡;对于深度大于0.3δ(δ为覆层、堆焊或衬里厚度)且>1mm采用如下方法(三.2.4)堆焊修补进行返修。
三、修补方案:1. 打磨1.1 对于上述需打磨修整的各类缺陷,要求打磨部分与周围母材平滑过渡,修磨斜度最大为1:31.2 对于复合钢板的覆层、堆焊或衬里打磨修整时必须采用不锈钢专用砂轮1.3打磨修整后工件表面粗糙度小于25μm。
2. 堆焊修2.1 所有修补堆焊必须由有合格持证项目的焊工施焊2.2 所有修补堆焊必须有合格的PQR支撑2.3 所有修补堆焊必须在产品热处理前完成(如产品有热处理要求)2.4 补焊区域打磨后进行MT或PT,以保证缺陷已完全清除。
2.5 对于深度大于0.05δ(δ为板厚)且>2mm缺陷需打磨后堆焊修补,要求打磨清除缺陷与周围母材平滑过渡,然后使用SMAW堆焊修补,焊接规范见表一。
表一2.6 对于对于复合钢板的成形件、堆焊件以及金属衬里层深度大于对于深度大于0.3δ(δ为覆层、堆焊或衬里厚度)且>1mm缺陷需打磨后堆焊修补,要求打磨清除与周围母材平滑过渡,然后使用SMAW堆焊修补,采用小电流不摆动快速焊,焊接规范见表二。
母材表面缺陷的补焊工艺规程

通用工艺规程编号:W GY-01 母材表面缺陷的补焊工艺规程编制:袁邓校对:袁邓审核:翟其能南通麒麟重工机械有限公司技术工艺部2010 年 07月一、适用范围本工艺适用于抗拉强度级别为490MPa(Q345,ASTM A709-50,船用板等)母材表面缺陷的返修。
母材表面缺陷有麻点、剥落、热切割后发现的夹层等。
二、缺陷尺寸1. 对于深度小于0. 5mm的各类缺陷可免于修补,对于大于0. 5mm且小于0.07δ(δ为板厚)但不大于3mm,面积小于钢板面积30%的麻点、剥落,采用打磨使之与周围母材平滑过渡;对于深度大于0.07δ,面积小于钢板面积30%者,采用如下方法2. 堆焊修补进行返修。
2. 对于需修补缺陷面积大于母材表面积30%者,要求换板。
3. 对于由热切割发现的夹层等缺陷超过AWS D1.1-98中规定的尺寸,按如下方法1.打磨进行修补。
三、修补方案:1. 打磨1.1 对于上述需打磨修整的各类缺陷,要求打磨部分与周围母材平滑过渡,粗糙度小于25μm。
1.2 母材打磨修整减薄后不得小于钢板下偏差的标称厚度要求,如下表示:1.3 对于母材表面裂纹,应清除至裂纹两端各50mm。
2. 堆焊修补(不适用于FCM的返修)2.1 对于深度大于0.07δ的各类缺陷需打磨后堆焊修补,要求打磨部分与周围母材平滑过渡,然后使用手工电弧焊堆焊修补,焊条采用Φ3.2低氢型焊条,具体焊接参数、预热温度等按相应板厚对接焊缝的WPS执行,但焊接电流以下限值为宜。
2.2 清除缺陷打磨时,钢板任何部位的厚度减薄不得大于母材厚度的30%,母材端部缺陷打磨深度须小于板厚,但不大于25mm。
2.3 焊补区域打磨后进行磁粉探伤,以保证缺陷已完全清除。
2.4 焊补处母材焊接时应保持干燥状态,受潮及淋湿者,则须使用火焰烘干焊补区域及其周边100mm处。
2.5 焊补过程中,要求焊补区及相邻的热影响区应完好无损和无裂纹,焊补金属熔透整个表面和边缘,无咬边或焊瘤。
焊接件补焊规范及措施

焊接件补焊规范及措施
一、焊前准备:
1、焊前清除缺陷处的表面铁锈、油污和水分等杂质。
2、在补焊处的咬边、焊瘤、气孔、裂纹等缺陷需打磨和加工后清除干净,部分缺陷应按
API7K-2005中7.9的规定加工成坡口,倒角等,经无损探伤检测达到设计技术要求。
3、未焊补处请加以保护,在关键位置应焊支撑点,防止工件变形,影响连接尺寸及结构钢
件的强度等。
4、焊接前应将焊条烘干。
(焊条的选用应根据母材和焊接工艺相配)
二、焊接操作:
1、尽可能用短弧焊,第一层用小直径焊条,第一层用小直径焊条,错位间接焊,减少焊接
变形。
2、补焊处的预热在焊接时要保持与预热温度相同的层间温度。
(注:工件在预热时应根据要
求测量变形的相关尺寸及支撑点)
3、在一边施焊,一边不停的用锤击打补焊处。
4、工件补焊处应采取相应的热处理措施进行消应力,并进行磁粉探伤直至工件合格。
三、预防措施:
1、加强设计要求和用户进行技术协商。
2、加强相关的材料化学成分控制。
3、严格按照焊接工艺执行操作。
铸钢件补焊工艺守则(完整资料).doc
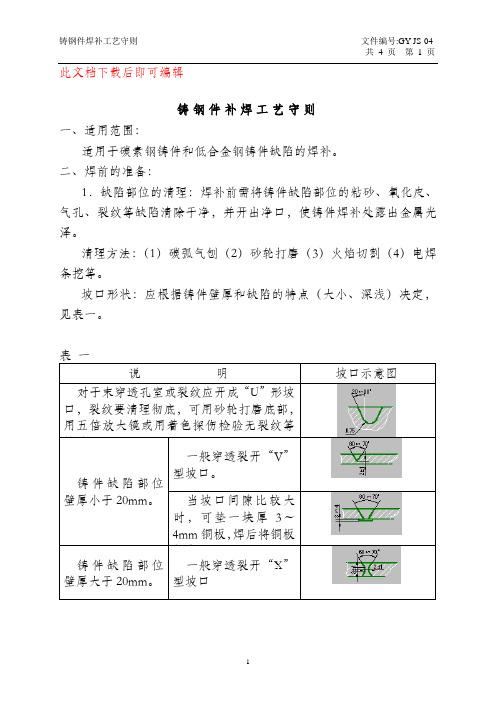
此文档下载后即可编辑铸钢件补焊工艺守则一、适用范围:适用于碳素钢铸件和低合金钢铸件缺陷的焊补。
二、焊前的准备:1.缺陷部位的清理:焊补前需将铸件缺陷部位的粘砂、氧化皮、气孔、裂纹等缺陷清除干净,并开出净口,使铸件焊补处露出金属光泽。
清理方法:(1)碳弧气刨(2)砂轮打磨(3)火焰切割(4)电焊条挖等。
坡口形状:应根据铸件壁厚和缺陷的特点(大小、深浅)决定,见表一。
说明坡口示意图对于末穿透孔室或裂纹应开成“U”形坡口,裂纹要清理彻底,可用砂轮打磨底部,用五倍放大镜或用着色探伤检验无裂纹等缺陷。
铸件缺陷部位壁厚小于20mm。
一般穿透裂开“V”型坡口。
当坡口间隙比较大时,可垫一块厚3~4mm铜板,焊后将铜板拆去。
铸件缺陷部位壁厚大于20mm。
一般穿透裂开“X”型坡口坡口间隙比较大时,可在间隙处放厚2~4mm 相同材质的钢板。
坡口间隙很大时,可在间隙处嵌入相同材质的填块。
说 明:(1)坡口示意图只用示意坡口各种相关尺寸,由具体实际情况决定。
(2)所有坡口及钝边间隙应要求焊缝能焊透。
2.焊条的选择:应根据母材的要求来选择,见表二表焊接材料 焊 条 备 注ZG230-450 J422、J507 重要结构选用J506、J507ZG270-500 J506、J507 不等强度可选用J426、J φ27ZG310-510 J506、J507 不等强度可选用J426、J φ27ZG 1Cr 18Ni 9T i A137、A132 特殊结构选用A237ZG 0Cr 13Ni 4M OA237ZG 0Cr 13Ni 6M OA237ZG 20MnS i J506、J5073、焊条的焊干要求:碱性低氢型焊条在使用前要求烘干,并做到用多少拿多少,见表三。
表焊条牌号 烘干温度(0C ) 烘干时间(h )备 注J426 250~3500C 1~2hJ427 300~4000C 1~2hJ506、J507 350~4000C 1~2hA132 100~2000C 1~2hA237 200~2500C 1~2h4、铸件的预热由于材质、结构形状、大小的不同,焊补时会产生应力、变形甚至裂纹,因此焊前铸应进行预热。
焊缝修补工艺规范

焊缝修补工艺规程1 范围本规程规定了焊缝的外表及内部质量在不符合标准要求时,对焊缝进行局部或整体返修的焊接前准备、人员、工艺要求、工艺过程和检验。
2 焊接前准备2.1 焊缝返修条件无论是何种形式接头的焊缝,其外观质量不符合产品规定的焊缝外观检验要求时,则必须对该焊缝进行返修。
无论是何种位置、何种焊接方法焊接对接焊缝,当焊缝经无损探伤后,确定其焊缝内部或表面存在超过该产品无损检查要求的焊接缺陷时,则必须对该对接焊缝进行返修。
2.2 焊接方法对焊缝的返修,依据该焊缝的WPS的规定可采用手工电弧焊或CO2气体保护焊焊接。
2当需要采用特殊焊接方法进行焊缝的修补,该焊接方法需得到焊接工程师或有关质量部门的认可。
2.3 焊接材料修补焊接材料的选用必须为公司内焊接工艺(WPS)认可且质量合格的焊材。
焊前清理2 焊前,焊工必须对返修部位的焊缝及焊缝两侧20mm范围内清除氧化物、水份、油污等。
2 当焊缝清理后未能及时进行返修,并因气候或其它原因影响而受潮、生锈等,在返修前应重新清理。
3 人员3.1 从事焊缝返修的焊工,需经理论及操作培训,经确认考试合格且符合产品要求,方能在考试合格范围内按本工艺要求进行焊缝的返修。
4 工艺要求、工艺过程4.1焊缝表面存在的焊接缺陷,可采用扁铲去除。
而对整体焊缝不影响并能满足标准要求的,可不需焊接,直接采用扁铲去除焊接缺陷。
4.2 一般角焊缝的焊接缺陷可直接采用焊接方法进行修补,但对于直接修补仍无法满足要求的焊接缺陷,如密集气孔等,则需要采用砂轮或碳弧气刨剔除缺陷后方能进行焊接修补。
修补焊缝表面缺陷时,修补长度不得小于50mm,严禁点焊修补气孔和咬边等缺陷。
焊缝内部存在超标的焊接缺陷时,需采用碳弧气刨剔除缺陷,并打磨彻底,然后焊接修补。
焊缝修补后应保证修补焊缝与正式焊缝圆滑过渡,突变的部位需打磨光顺。
对于对接焊缝表面缺陷长度>50mm或修补焊缝内部缺陷时,焊接前需对焊缝修补范围进行局部预热,如原焊缝WPS无预热要求,则预热温度80~100℃并保持焊接过程的层间温度达到预热温度以上,焊接需连续一次完成。
补焊工艺安全要求
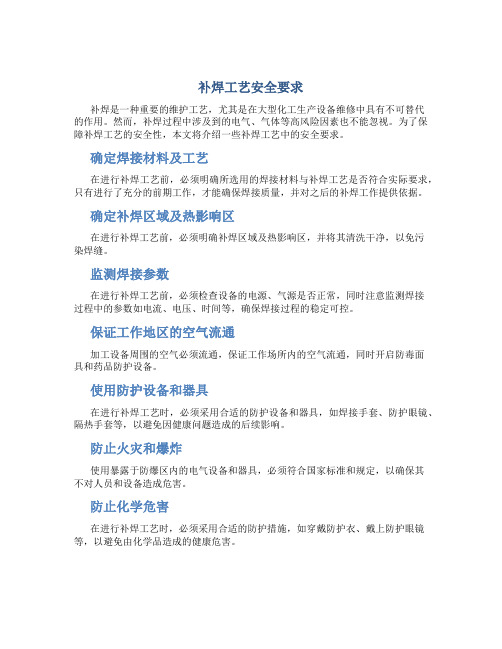
补焊工艺安全要求
补焊是一种重要的维护工艺,尤其是在大型化工生产设备维修中具有不可替代
的作用。
然而,补焊过程中涉及到的电气、气体等高风险因素也不能忽视。
为了保障补焊工艺的安全性,本文将介绍一些补焊工艺中的安全要求。
确定焊接材料及工艺
在进行补焊工艺前,必须明确所选用的焊接材料与补焊工艺是否符合实际要求,只有进行了充分的前期工作,才能确保焊接质量,并对之后的补焊工作提供依据。
确定补焊区域及热影响区
在进行补焊工艺前,必须明确补焊区域及热影响区,并将其清洗干净,以免污
染焊缝。
监测焊接参数
在进行补焊工艺前,必须检查设备的电源、气源是否正常,同时注意监测焊接
过程中的参数如电流、电压、时间等,确保焊接过程的稳定可控。
保证工作地区的空气流通
加工设备周围的空气必须流通,保证工作场所内的空气流通,同时开启防毒面
具和药品防护设备。
使用防护设备和器具
在进行补焊工艺时,必须采用合适的防护设备和器具,如焊接手套、防护眼镜、隔热手套等,以避免因健康问题造成的后续影响。
防止火灾和爆炸
使用暴露于防爆区内的电气设备和器具,必须符合国家标准和规定,以确保其
不对人员和设备造成危害。
防止化学危害
在进行补焊工艺时,必须采用合适的防护措施,如穿戴防护衣、戴上防护眼镜等,以避免由化学品造成的健康危害。
结论
本文总结了补焊工艺中的一些安全要求,为保障焊接工作的安全、快速和高质量提供了重要的参考。
在实际操作中,我们必须严格遵守这些安全要求,以确保工作人员的生命安全,同时对设备、生产效率的提高具有积极的意义。
锻件补焊工艺
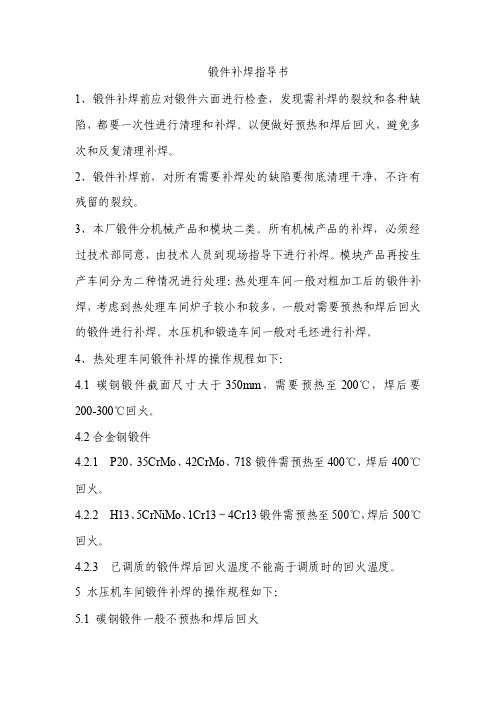
锻件补焊指导书
1、锻件补焊前应对锻件六面进行检查,发现需补焊的裂纹和各种缺陷,都要一次性进行清理和补焊。
以便做好预热和焊后回火,避免多次和反复清理补焊。
2、锻件补焊前,对所有需要补焊处的缺陷要彻底清理干净,不许有残留的裂纹。
3、本厂锻件分机械产品和模块二类。
所有机械产品的补焊,必须经过技术部同意,由技术人员到现场指导下进行补焊。
模块产品再按生产车间分为二种情况进行处理:热处理车间一般对粗加工后的锻件补焊,考虑到热处理车间炉子较小和较多,一般对需要预热和焊后回火的锻件进行补焊。
水压机和锻造车间一般对毛坯进行补焊。
4、热处理车间锻件补焊的操作规程如下:
4.1碳钢锻件截面尺寸大于350mm,需要预热至200℃,焊后要200-300℃回火。
4.2合金钢锻件
4.2.1P20、35CrMo、42CrMo、718锻件需预热至400℃,焊后400℃回火。
4.2.2H13、5CrNiMo、1Cr13~4Cr13锻件需预热至500℃,焊后500℃回火。
4.2.3已调质的锻件焊后回火温度不能高于调质时的回火温度。
5水压机车间锻件补焊的操作规程如下:
5.1碳钢锻件一般不预热和焊后回火
5.2合金钢锻件
5.2.1P20、35CrMo、42CrMo、718锻件焊补区面积在100×100×20mm 以内,不预热和焊后回火。
5.2.2P20、35CrMo、42CrMo、718锻件焊补区面积大于100×100×20mm,需预热至400℃,焊后400℃回火。
5.2.3水压机车间对H13、5CrNiMo、1Cr13~4Cr13锻件不允许补焊。
补焊标准工艺基础规范
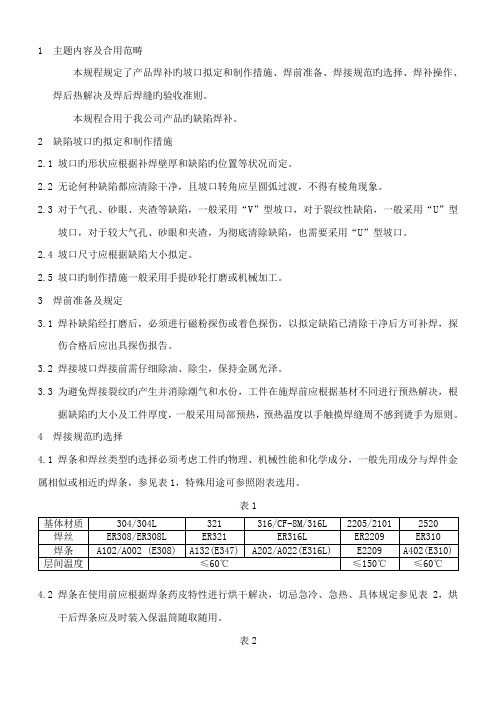
1主题内容及合用范畴本规程规定了产品焊补旳坡口拟定和制作措施、焊前准备、焊接规范旳选择、焊补操作、焊后热解决及焊后焊缝旳验收准则。
本规程合用于我公司产品旳缺陷焊补。
2缺陷坡口旳拟定和制作措施2.1 坡口旳形状应根据补焊壁厚和缺陷旳位置等状况而定。
2.2 无论何种缺陷都应清除干净,且坡口转角应呈圆弧过渡,不得有棱角现象。
2.3 对于气孔、砂眼、夹渣等缺陷,一般采用“V”型坡口,对于裂纹性缺陷,一般采用“U”型坡口,对于较大气孔、砂眼和夹渣,为彻底清除缺陷,也需要采用“U”型坡口。
2.4 坡口尺寸应根据缺陷大小拟定。
2.5 坡口旳制作措施一般采用手提砂轮打磨或机械加工。
3焊前准备及规定3.1 焊补缺陷经打磨后,必须进行磁粉探伤或着色探伤,以拟定缺陷已清除干净后方可补焊,探伤合格后应出具探伤报告。
3.2 焊接坡口焊接前需仔细除油、除尘,保持金属光泽。
3.3 为避免焊接裂纹旳产生并消除潮气和水份,工件在施焊前应根据基材不同进行预热解决,根据缺陷旳大小及工件厚度,一般采用局部预热,预热温度以手触摸焊缝周不感到烫手为原则。
4焊接规范旳选择4.1 焊条和焊丝类型旳选择必须考虑工件旳物理、机械性能和化学成分,一般先用成分与焊件金属相似或相近旳焊条,参见表1,特殊用途可参照附表选用。
表14.2焊条在使用前应根据焊条药皮特性进行烘干解决,切忌急冷、急热、具体规定参见表2,烘干后焊条应及时装入保温筒随取随用。
表24.3焊条直径旳选择应考虑到焊补缺陷深度、焊接层数、焊条直径之间关系旳参照数据见表3表34.4 焊接电流拟定及焊机旳选择4.4.1 焊接电流直接影响焊补质量,电流过大易导致咬边、烧穿等缺陷,同步金属组织也会因过热而发生变化,而电流过小也易导致夹渣、未焊透等缺陷。
焊接电流一般根据下列公式拟定:I = K * D (式中:I:焊接电流A D:焊条直径㎜ K:经验系数)焊条直径D与经验系数K旳关系表4表44.4.2 焊机应根据所使用焊条类型拟定,碱性焊条选用直流弧焊机,酸性焊条选用交流弧焊机。
- 1、下载文档前请自行甄别文档内容的完整性,平台不提供额外的编辑、内容补充、找答案等附加服务。
- 2、"仅部分预览"的文档,不可在线预览部分如存在完整性等问题,可反馈申请退款(可完整预览的文档不适用该条件!)。
- 3、如文档侵犯您的权益,请联系客服反馈,我们会尽快为您处理(人工客服工作时间:9:00-18:30)。
补焊工艺规范
1 主题内容及适用范围
本规程规定了产品焊补的坡口确定和制作方法、焊前准备、焊接规范的选择、焊补 操作、焊后热处理及焊后焊缝的验收准则。
本规程适用于我公司产品的缺陷焊补。
2 缺陷坡口的确定和制作方法
2.1 坡口的形状应根据补焊壁厚和缺陷的位置等情况而定,具体参见附录A 。
2.2 无论何种缺陷都应清除干净,且坡口转角应呈圆弧过渡,不得有棱角现象。
2.3 对于气孔、砂眼、夹渣等缺陷,一般采用“V ”型坡口,对于裂纹性缺陷,一般采用“U ”型坡口。
2.4 坡口尺寸应根据缺陷大小确定。
2.5 坡口的制作方法一般采用手提砂轮打磨或机械加工。
3 焊前准备及要求
3.1 焊补缺陷经打磨后,必须进行磁粉探伤或着色探伤,以确定缺陷已清除干净后方可补焊,探伤合格后应出具探伤报告。
3.2 为防止焊接裂纹的产生,工件在施焊前应根据基体材质不同进行预热处理,具体参数见表1,并根据缺陷的大小及工件复杂程度,一般采用整体或局部预热,整体预热时间一般为1~1.5小时,局部预热时间视工件大小而定。
4 焊接规范的选择
4.1 焊条类型的选择必须考虑工件的物理、机械性能和化学成份,一般先用成份与焊件金属相同或相近的焊条,参见表
2。
4.2 焊条在使用前应根据焊条药皮特性进行烘干处理,切忌急冷、急热、具体要求参见表 3,烘干后焊条应及时装入保温筒随取随用。
4.3 关系的参考数据见表4
4.4
4.4.1 焊接电流直接影响焊补质量,电流过大易造成咬边、烧穿等缺陷,同时金属组织也会因过热而发生变化,而电流过小也易造成夹渣、未焊透等缺陷。
焊接电流一般根据下列公式确定:
I = K · D
式中:I:焊接电流A
D:焊条直径㎜
K:经验系数
焊条直径D与经验系数K的关系表5
5焊补操作
焊补操作一般以引弧、运条、收尾几个环节控制。
碱性焊条一般采用划擦法引弧,
回焊法收尾;酸性焊条采用直击法引弧,划回法收尾,在焊补过程中焊条应根据工件补焊位置等情况相应摆动。
6焊后热处理
为避免焊缝产生裂纹,工件在焊补完毕后,应根据材质的不同进行焊后热处理;热
处理方式一般根据工件大小及缺陷大小来选定采用整体处理或局部处理,整体处理参数见表6,保温时间一般为1.5~2小时;局部处理一般采用石棉网覆盖于焊缝部位,采用氧一乙炔焰逐渐加热,温度控制200℃~300℃,且焊缝两侧50~100㎜范围内同时加热。
7
7.1 焊前检验
应进行渗透和磁粉探伤。
7.2 焊后检验
a) 目视检查
所有焊缝完全焊透、无咬边、气孔、裂缝、弧坑、焊瘤等缺陷存在;
b) 渗透或磁粉检测(所有铁磁性材料用MT);
c) 超声波检测:仅在焊缝厚度大于壁厚25%或1in(25mm),取小者;
d) 射线(X射线照像或显象)检测:仅在焊缝厚度大于壁厚25%或1in(25mm),取小者,用;
e) 硬度试验(焊缝)。