Hazard Identification
Hazard Identification and JSA

识别潜在危险练习
整理场所!!
© 2011 Chevron
39
工作安全分析
工作安全分析用于:
– 确定所要进行的任务的每一步工作步骤; – 识别每一步骤中产生的危害和潜在事故; – 制定方案,采取行动消除或减小事故发生的可能性
© 2011 Chevron
40
工作安全分析 (JSA)
以下情况必须使用工作安全分析:
例如:碰撞噪 声,震动,高 压释放,设备 噪音
© 2011 Chevron 31
声能 –举例
© 2011 Chevron
32
小组练习
工作单位发生的事件中有哪些是涉及以上讨论的能量来源
© 2011 Chevron
33
生物危害
© 2011 Chevron
34
识别能量来源
辐射 化学能
声能
温度
生物能
© 2011 Chevron
16
压力
被压缩的或在真空 条件下的液体或者 气体所产生的能量
例如:加压管、压 缩气筒,控制线, 导管 ,容器,油 罐,软管,风力及 水力设备
© 2011 Chevron
17
压力 – 例子
© 2011 Chevron
18
小组演习
过去发生的事故中哪些涉及我们讨论过的能量来源?
59
工作安全分析
第4步(续) – 识别潜在危险
基本工作步骤
停车
潜在危险
•车辆被过往车辆撞上 •人员被过往车辆撞上 •撞上障碍物
危险排除/降低方法
取下备用胎及千斤顶
•背部劳损 •头撞在车厢上
松螺母
•背部或手臂劳损 •滑倒或跌倒
顶起汽车
hazard warning专业术语

以下是与危险警示有关的一些专业术语:
1. 危险物质(Hazardous substance):指具有潜在危害的化学物质或材料。
2. 危险性(Hazard):指物质或活动可能对人或环境造成伤害的潜在特性。
3. 危险分类(Hazard classification):根据化学品的特性,将其分为不同的危险性类别和等级。
4. 危险标识(Hazard labeling):在容器、包装或产品上使用标签、贴片等方式,提供关于危险物质性质和风险的信息。
5. 危险符号(Hazard symbol):用于标识危险物质性质和风险的图形符号,例如爆炸符号、腐蚀符号等。
6. 危险识别号码(Hazard identification number):在危险品运输中使用的编码,用于标识危险物质的种类和性质。
7. 安全数据表(Safety data sheet, SDS):提供有关化学品成分、危险性、安全操作和应急处理措施等信息的文件。
8. 危险废物(Hazardous waste):指因其危险特性而需要特殊处理和处置的废物。
9. 防护装备(Personal protective equipment, PPE):包括手套、面具、护目镜等个人防护设备,用于保护工作者免受危险物质的威胁。
这些术语在危险物质管理、化学品安全和工业安全等领域中使用广泛。
具体的专业术语可能会因不同的国家、法规和行业而有所差异,因此请参考相关的法规、标准和指南以获得更详细和准确的信息。
SECTION 2 Hazards identification
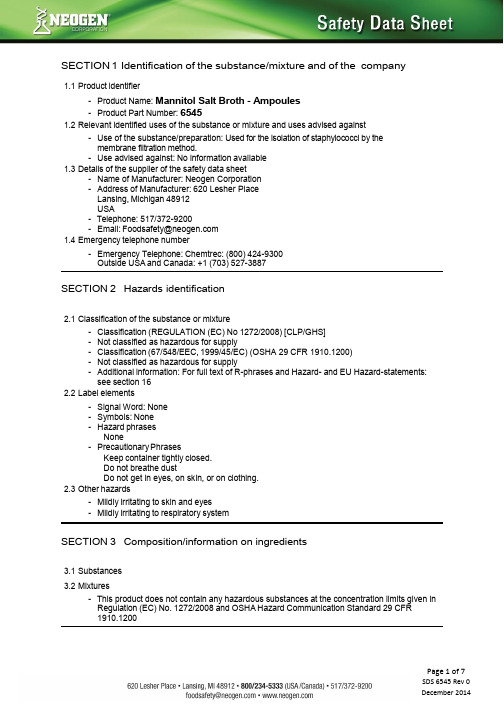
SECTION 1 Identification of the substance/mixture and of the company1.1 Product identifier- Product Name: Mannitol Salt Broth - Ampoules- Product Part Number: 65451.2 Relevant identified uses of the substance or mixture and uses advised against- Use of the substance/preparation: Used for the isolation of staphylococci by themembrane filtration method.- Use advised against: No information available1.3 Details of the supplier of the safety data sheet- Name of Manufacturer: Neogen Corporation- Address of Manufacturer: 620 Lesher PlaceLansing, Michigan 48912USA- Telephone: 517/372-9200- Email: Foodsafety@1.4 Emergency telephone number- Emergency Telephone: Chemtrec: (800) 424-9300Outside USA and Canada: +1 (703) 527-3887SECTION 2 Hazards identification2.1 Classification of the substance or mixture- Classification (REGULATION (EC) No 1272/2008) [CLP/GHS]- Not classified as hazardous for supply- Classification (67/548/EEC, 1999/45/EC) (OSHA 29 CFR 1910.1200)- Not classified as hazardous for supply- Additional information: For full text of R-phrases and Hazard- and EU Hazard-statements:see section 162.2 Label elements- Signal Word: None- Symbols: None- Hazard phrasesNone- Precautionary PhrasesKeep container tightly closed.Do not breathe dustDo not get in eyes, on skin, or on clothing.2.3 Other hazards- Mildly irritating to skin and eyes- Mildly irritating to respiratory systemSECTION 3 Composition/information on ingredients3.1 Substances3.2 Mixtures- This product does not contain any hazardous substances at the concentration limits given in Regulation (EC) No. 1272/2008 and OSHA Hazard Communication Standard 29 CFR1910.1200SECTION 4 First aid measures4.1 Description of first aid measures- Contact with skinRemove contaminated clothingWash affected area with plenty of soap and waterIf skin irritation or rash occurs: Get medical advice/attention.Contaminated clothing should be laundered before reuse- Contact with eyesIf substance has gotten into eyes, immediately wash out with plenty of water for at least 15minutesIrrigate eyes thoroughly while lifting eyelidsSeek medical advice if necessary- IngestionRinse mouth with water (do not swallow)Never make an unconscious person vomit or drink fluidsIf medical advice is needed, have product container or label at hand.- InhalationIf breathing is difficult, remove victim to fresh air and keep at rest in a position comfortablefor breathing.Call a POISON CENTER or doctor/physician if you feel unwell.4.2 Most important symptoms and effects, both acute and delayed- May cause irritation4.3 Indication of any immediate medical attention and special treatment needed- Treat symptomaticallySECTION 5 Fire-fighting measures5.1 Extinguishing media- In case of fire: use foam, carbon dioxide or dry agent for extinction5.2 Special hazards arising from the substance or mixture- Smoke from fires is toxic. Take precautions to protect personnel from exposure- Decomposition products may include carbon oxides- May form explosive dust/air mixtures- See Section 105.3 Advice for firefighters- Keep container(s) exposed to fire cool, by spraying with water- Wear chemical protection suit and positive-pressure breathing apparatus- Wear protective clothing as per section 8SECTION 6 Accidental release measures6.1 Personal precautions, protective equipment and emergency procedures- Shut off all ignition sources- Use non-sparking hand toolsSECTION 6 Accidental release measures (continued)- Avoid raising dust- Remove contaminated clothing- Wear protective clothing as per section 8- Wash thoroughly after dealing with spillage6.2 Environmental Precautions- Do not allow to enter public sewers and watercourses- Avoid scattering in the environment6.3 Methods and material for containment and cleaning up- Absorb spillage in inert material and shovel up- Place in sealable container- Seal containers and label them- Seek expert advice for removal and disposal of all contaminated materials and wastes- Ventilate the area and wash spill site after material pick-up is complete6.4 Reference to other sections- See Section 7SECTION 7 Handling and storage7.1 Precautions for safe handling- Do not breathe dust- Avoid contact with skin and eyes- Do not eat, drink or smoke when using this product.- Ensure adequate ventilation- Eyewash bottles should be available- Wash hands thoroughly after using this substance7.2 Conditions for safe storage, including any incompatibilities- Store at temperatures not exceeding 8°C/46°F. Keep cool.- Store in a well-ventilated place. Keep container tightly closed.- Store in a dry place.- Keep away from oxidizing substances- Keep away from acid7.3 Specific end use(s)- Used for the isolation of staphylococci by the membrane filtration method.SECTION 8 Exposure controls/personal protection8.1 Control parameters- This product contains no substances >1% with occupational exposure values.8.2 Exposure controls- Eyewash bottles should be available- Engineering controls should be provided to prevent the need for ventilation- No respiratory protection is needed if ventilation/extraction is adequate, otherwise wearapproved dust mask, N95 (US) or type FFP1 (EN143) dust masks.- Wear protective gloves. The selected protective gloves have to satisfy the specifications of EU Directive 89/686/EEC and standard EN 374.- Wear safety glasses approved to standard for NIOSH (US) or EN 166.SECTION 8 Exposure controls/personal protection (continued) - Wear suitable protective clothingGloves Safety Lab CoatGlassesSECTION 9 Physical and chemical properties9.1 Information on basic physical and chemical properties- Appearance: Red, clear to slightly hazy- Odor: No information available- pH: 7.4 ± 0.2 @ 25°C- Melting point/Range: No information available- Boiling Point/Range: Not determined- Flashpoint: No information available- Evaporation Rate: No information available- Flammability: No information available- Vapor Pressure: No information available- Vapor Density: No information available- Specific Gravity: No information available- Solubility in water: Completely soluble in water- Partition Coefficient (n-Octanol/Water): No information available- Autoignition Temperature: Product is not self-igniting- Viscosity: No information available- Explosive Properties: Product does not present an explosion hazard- Oxidizing Properties: No information available9.2 Other information- No information availableSECTION 10 Stability and reactivity10.1 Reactivity- No information available10.2 Chemical stability- Considered stable under normal conditions10.3 Possibility of hazardous reactions- No hazardous reactions known if used for its intended purpose10.4 Conditions to avoid- Avoid contact with moisture- Keep away from heat and sources of ignition10.5 Incompatible materials- Incompatible with oxidizing substances10.6 Hazardous Decomposition Products- Decomposition products may include carbon oxidesSECTION 11 Toxicological information11.1 Information on toxicological effects- No experimental data available- Contact with skinMay cause redness and irritation- Contact with eyesMay cause redness and irritation- IngestionMay cause irritation of the throat- InhalationMay cause coughing- CarcinogenicityNo evidence of carcinogenic effects- MutagenicityNo evidence of mutagenic effects- TeratogenicityNo information availableSECTION 12 Ecological information12.1 Toxicity- No information available12.2 Persistence and degradability- No information available12.3 Bioaccumulation Potential- No information available12.4 Mobility in soil- No information available12.5 Results of PBT and vPvB assessment- Not a PBT according to REACH Annex XIII- PBT/vPvB assessment not available12.6 Other Adverse Effects- To the best of our knowledge, the properties of this material have not been fully evaluated - On available data, substance is not harmful to the environmentSECTION 13 Disposal considerations13.1 Waste treatment methods- Disposal should be in accordance with local, state or national legislation- Do not discharge into drains or the environment, dispose to an authorized waste collectionpoint- Do not reuse empty containers without commercial cleaning or reconditioning- Refer to manufacturer/supplier for information on recovery/recycling13.2 Classification (REACH)- Waste Codes in accordance with the European Waste catalogue (EWC) are origin-defined.Since this product is used in several industries, no Waste Code can be provided by thesupplier. The Waste Code should be determined in arrangement with your waste disposalpartner or the responsible authority.SECTION 14 Transport information14.1 UN NumberNot classified as hazardous for transport14.2 UN Proper Shipping Name- Not applicable14.3 Transport hazard class(es)- Not applicable14.4 Packing group- Not applicable14.5 Environmental hazards- Not Classified14.6 Special precautions for user- Not Classified14.7 Transport in bulk according to Annex II of MARPOL 73/78 and the IBC code- Not Classified14.8 DOT- Proper Shipping Name: Not applicable- DOT UN No.: Not applicable- DOT Hazard Class: Not applicable- DOT Packing Group: Not applicable14.9 Road/Rail (ADR/RID)- Proper Shipping Name: Not applicable- ADR UN No.: Not applicable- ADR Hazard Class: Not applicable- ADR Packing Group: Not applicable- Tunnel Code: Not applicable14.10 Sea (IMDG)- Proper Shipping Name: Not applicable- IMDG UN No.: Not applicable- IMDG Hazard Class: Not applicable- IMDG Pack Group.: Not applicable14.11 Air (ICAO/IATA)- Proper Shipping Name: Not applicable- ICAO Un No.: Not applicable- ICAO Hazard Class: Not applicable- ICAO Packing Group: Not applicableSECTION 15 Regulatory information15.1 Safety, health and environmental regulations/legislation specific for the substance or mixture- This Safety Data Sheet is provided in compliance with the EC Directive 1907/2006-453/2010 and OSHA Hazard Communication Standard 29 CFR 1910.1200.- Regulation (EC) No. 1272/2008 on the classification, labelling and packaging of substances and mixtures (CLP Regulation) applies in Europe15.2 Chemical Safety Assessment- No information available15.3 United States Regulatory InformationSECTION 15 Regulatory information (continued)SARA 302 ComponentsSARA 302: No chemicals in this material are subject to the reporting requirements of SARA Title III, Section 302.SARA 313 ComponentsSARA 313: The material does not contain any chemical components with known CAS numbers that exceed the threshold (De Minimis) reporting levels established by SARA Title III, Section313.SARA 311/312No SARA HazardsSECTION 16 Other informationThis document is believed to be correct, but does not purport to be all inclusive and shall be used only as a guide. Neogen Corporation shall not be held liable for any damage resulting from handling or from contact with the above product. These suggestions should not be confused with state, municipal or insurance requirements, and constitute NO WARRANTY.。
隐患排查各模块介绍

隐患排查各模块介绍### English Answer:1. Hazard Identification.Hazard identification is the process of identifying and evaluating potential hazards that could cause harm to people, property, or the environment. This process involves identifying and assessing the risks associated with a particular operation, process, or activity. Hazard identification can be performed using a variety of methods, including:Job safety analysis (JSA): A JSA is a systematic review of a job or task to identify potential hazards and develop controls to mitigate those hazards.Hazard and operability study (HAZOP): A HAZOP is a structured brainstorming session that is used to identify and evaluate potential hazards in a process or system.What-if analysis: A what-if analysis is a brainstorming session that is used to identify potential hazards by asking "what if" questions about a particular operation or activity.2. Hazard Assessment.Hazard assessment is the process of evaluating the likelihood and severity of potential hazards. This process involves considering the following factors:The probability of the hazard occurring.The severity of the consequences of the hazard.The number of people who could be affected by the hazard.3. Hazard Control.Hazard control is the process of implementing measuresto mitigate or eliminate potential hazards. This process involves the following steps:Identifying the most appropriate hazard control measures.Implementing the hazard control measures.Evaluating the effectiveness of the hazard control measures.4. Hazard Monitoring.Hazard monitoring is the process of monitoring the effectiveness of hazard control measures and identifying any new hazards that may arise. This process involves the following steps:Regularly inspecting hazard control measures.Reviewing incident reports and other data.Conducting hazard audits.### 中文回答:1. 隐患排查。
危险评估hazard identification and risk assessment form
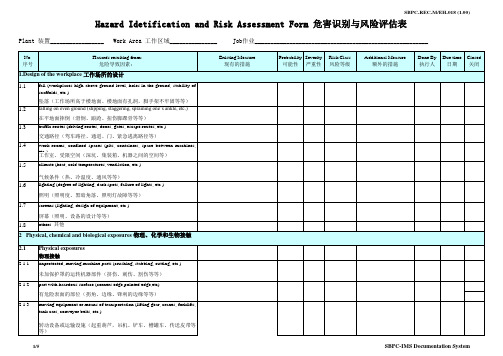
No. 3.1.1 序号
Work Area 工作区域_______________
Job作业_______________________________________________________
Existing Measure 现有的措施 Probability Severity 可能性 严重性 Risk Class 风险等级 Additional Measure 额外的措施 Done By 执行人 Due time 日期 Closed 关闭
hot or cold media and/or surfaces (hot liquids, vapors, gases, Dry Ice, etc.) 接触热或冷媒介和/或表面(热的液体、汽化物、气体、干冰等)
3.2.2
Noise 噪声
3.2.3
Ultrasound 超频率音响
3.2.4
vibrations of the body (pneumatic hammers, drills, etc.) 身体的振动(气锤、气钻等)
SBPC-REC-M/EH-018 (1.00)
Hazard Idetification and Risk Assessment Form 危害识别与风险评估表
Plant 装置_________________
No. 序号
Work Area 工作区域_______________
Job作业_______________________________________________________
Hazards resulting from: 危险导致因素: 由于气体、液体和固体(粉尘)引起的爆炸危险
危险源识别评价控制程序(中英文)

文件制修订记录危险源识别和评价控制程序Hazard identification and evaluation control procedures1、目的Purpose对公司范围内存在的危险源进行辨识与评价,制定风险控制措施,并对其实施控制,以减少或避免不期望的事件发生,保证安全生产。
Identify and evaluate existed hazards in the company, prepare risk control measures and control them to reduce or avoid undesirable incidents,to ensure safety in production.2、适用范围Scope本程序适用于公司范围内的生产活动、服务过程中的安全评价与控制。
This procedure applies to the safety evaluation and control of company's production activities and service process.3、职责Responsibilities3.1各部门:负责制定《危险源识别及风险评价表》及《危险岗位清册》3.1 All Departments: responsible for preparing "hazard identification and risk assessment form"and "dangerous job list".3.2 行政部:3.2 Administration Department:3.2.1组织危险源辨别,将各部门《危险辨别及风险评价表》汇总。
3.2.1Identify hazard, summarize each department’s"hazard identification and riskassessment form".3.2.2进行环境因素评价,制订公司《危险辨别及风险评价表》。
4 Identification of Hazards 危害识别 v3
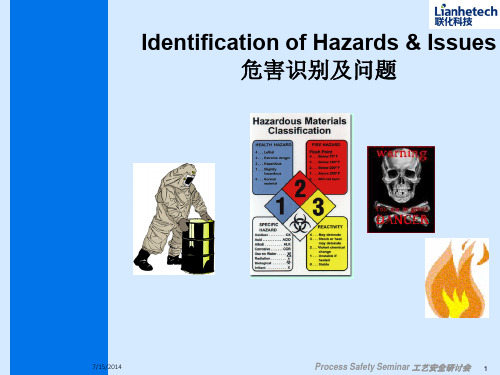
The use of a list of topics and key words does not automatically ensure the finding of all hazards 主题和关键词清单的使用不会自动确保找到所有危害。
Equally important are experience, creativity and thorough understanding of the process 同样重要的还有经验,创造性,工艺的透彻理解
主题一
Sufficient knowledge of material properties 足够的物料性质知识 Sufficient knowledge of chemical reactions足够的化学反应知识
Process concept and design features 工艺概念和设计特点
9
Topics tools hazard Topicsas and key for words as identification 危害识别工具 tools for hazard identification
Topics II主题二 Power failure / utilities failure 停电、公用工程缺失 Explosion protection 防爆 Fire protection 防火 Building concept 建筑概念 Impact on environment 环境影响 Location of the plant 车间的位置
2014/7/21
Process Safety Seminar 工艺安全研讨会
11
Example: Key words belonging to the topic Example: Key words belonging to the topic “Sufficient knowledge of chemical reactions” “Sufficient knowledge of chemical reactions” 例子: 主题的关键词“足够的化学反应知识”
危害因素辨识 Hazard Identify

1. 技能:操作人员应具备的操作资质。如:特种作业操作证(电工、焊接、易燃易爆 等),高风险作业培训(登高、安全锁定、受限空间等),其他培训; 2. 控制:当前所采取的对应预防措施。可采取“工程控制,SOS/JIS,培训,警示, PPE,作业许可 ,PM/TPM”等措施; 3. 应急:对已发生的事件的处置措施,以降低事件造成的伤害程度。如:应急预案、 现场急救、消防器材、医药箱、应急疏散、应急物资等措施。
料: 生产过程中使用的材料、工件
后: 操作过程后方区域
侧: 合作配合作业、交叉作业等
环: 工作区域的环境
法: WES及PM/TPM等
危害因素辨识
可能导致的事故后果:
危险性评价 危险性再评价
是否 工位/ 可能导致 是 风 风 备 序 作业项目/ 潜在的危 现有控 为重 补充的控 是 班组 作业 的事故后 非 险 要危 制措施 险 注 号 步骤 险因素 制措施 非L E C D 区域 果 法L E C D 等 等 险源 法 级 级 1
E -- 暴露于潜在危害环境的频繁程度
分值 暴露频繁程度
10
6 3 2 1 0.5
连续暴露
每天几次暴露 每周几次暴露 每月几次暴露 每年几次暴露 非常罕见地暴露
危害因素辨识
LECD评价法
危险性评价 可能 工位/ 导致 是 风 序 作业项目/ 潜在的危 班组 作业 的事 现有控制措施 非 险 号 步骤 险因素 区域 故后 法L E C D 等 果 级 1 危险性再评价 是否 风 备 为重 补充的控 是 要危 制措施 非 L E C D 险 注 等 险源 法 级
危害因素辨识
LECD评价法
危险性评价 可能 工位/ 导致 是 风 序 作业项目/ 潜在的危 班组 作业 的事 现有控制措施 非 险 号 步骤 险因素 区域 故后 法L E C D 等 果 级 危险性再评价
健康风险评估的简介

健康風險評估的簡介壹、風險的簡介一、何謂風險?韋氏字典(Webster’s unabridged dictionary, 1970)對風險(risk)所下的定義為:1.傷害、損害或損失的機會;危險的機會;危害(hazard)2.在保險方面,即(a)損失的機會;(b)損失之機率的大小程度;(c)保險公司可能損失的數量;(d)關於保障個人或事件本身的風險;(e)保險單可以理賠的損失,例如:壽險及火險等等;冒險;暴露於傷害或損失的機會;危害自己。
健康風險是因為暴露到環境物質而導致傷害、疾病或死亡的可能性。
風險評估(Risk assessment)是估計關於一組特定狀況的風險,由此定義,風險包括兩個主要成分,即(1)危害(hazard)的存在,以及(2)暴露到危害的可能性(likelihood)。
二、歷史的觀點健康風險的概念是隨年代有所變遷。
過去可接受的風險,因為預防與控制技術的進步、法律演進、需求提昇、對健康危害的資訊增加,以及有其他替代方案等等因素,人們對風險的接受度會有改變。
例如過去必須對抗因衛生不良、食物腐敗及水質不良而發生傳染病的健康風險,因流行病學、微生物學科技的進步,衛生的改善,水質淨化,疫苗的發展,已使傳染病的風險降低。
在較未發展的國家中人們可能比已開發國家願意忍受較大的風險以獲得基本的需求。
三、為何擔心風險?有兩個原因:除了暴露到物質會產生不良健康效應的可能性,還要考慮大眾對於潛在危害暴露所引起風險的感受。
風險感受(Risk perception)是相對的概念,受許多社會及心理因素的影響。
一般社會大眾願意接受的風險程度,是取決於在較可能造成有利的情況之下,對可能發生之不良後果的忍受程度。
舉例而言,當一個人選擇股票認股權時就必須考慮到可能一無所得的財務損失及風險,通常在決定是否從事這項投資時就會涉及風險評估,進而決定成功或失敗之結果的可能性。
社會活動不是完全沒有風險的,許多可接受或甚至期望去作的活動(如開車、工作、抽煙及喝酒等等)會縮短預期壽命,並且比環境因孛風險更嚴重,然而因為這些活動提供了人們「較想要的生活方式」,使人們願意接受某種程度的風險。
Hazard Identification and Risk Assessment
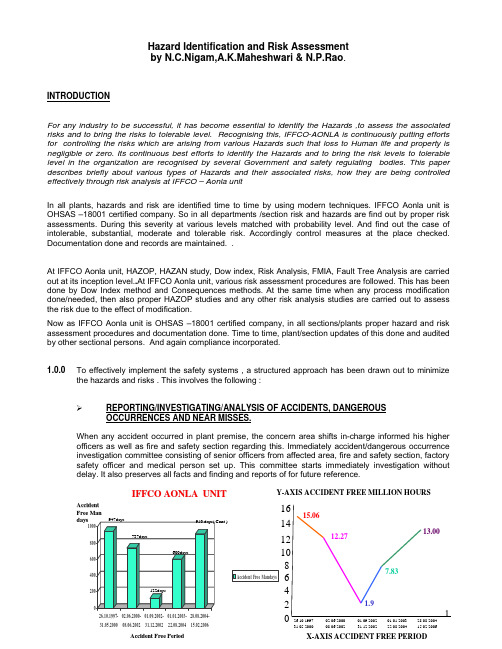
Hazard Identification and Risk Assessment by N.C.Nigam,A.K.Maheshwari & N.P.Rao .INTRODUCTIONFor any industry to be successful, it has become essential to identify the Hazards ,to assess the associated risks and to bring the risks to tolerable level. Recognising this, IFFCO-AONLA is continuously putting efforts for controlling the risks which are arising from various Hazards such that loss to Human life and property is negligible or zero. Its continuous best efforts to identify the Hazards and to bring the risk levels to tolerable level in the organization are recognised by several Government and safety regulating bodies. This paper describes briefly about various types of Hazards and their associated risks, how they are being controlled effectively through risk analysis at IFFCO – Aonla unitIn all plants, hazards and risk are identified time to time by using modern techniques. IFFCO Aonla unit is OHSAS –18001 certified company. So in all departments /section risk and hazards are find out by proper risk assessments. During this severity at various levels matched with probability level. And find out the case of intolerable, substantial, moderate and tolerable risk. Accordingly control measures at the place checked. Documentation done and records are maintained. .At IFFCO Aonla unit, HAZOP, HAZAN study, Dow index, Risk Analysis, FMIA, Fault Tree Analysis are carried out at its inception level..At IFFCO Aonla unit, various risk assessment procedures are followed. This has been done by Dow Index method and Consequences methods. At the same time when any process modification done/needed, then also proper HAZOP studies and any other risk analysis studies are carried out to assess the risk due to the effect of modification.Now as IFFCO Aonla unit is OHSAS –18001 certified company, in all sections/plants proper hazard and risk assessment procedures and documentation done. Time to time, plant/section updates of this done and audited by other sectional persons. And again compliance incorporated.1.0.0 To effectively implement the safety systems , a structured approach has been drawn out to minimizethe hazards and risks . This involves the following :¾ REPORTING/INVESTIGATING/ANALYSIS OF ACCIDENTS, DANGEROUSOCCURRENCES AND NEAR MISSES.When any accident occurred in plant premise, the concern area shifts in-charge informed his higher officers as well as fire and safety section regarding this. Immediately accident/dangerous occurrence investigation committee consisting of senior officers from affected area, fire and safety section, factory safety officer and medical person set up. This committee starts immediately investigation without delay. It also preserves all facts and finding and reports of for future reference.IFFCO AONLA UNIT131.05.200008.06.200231.12.200222.08.200415.02.2006Accident Free Man days Accident Free Period026.10.1997-31.05.200002.06.2000-08.06.200201.09.2002-31.12.200201.01.2003-22.08.200428.08.2004-15.02.200624681012141615.0612.271.97.8313.00Y-AXIS ACCIDENT FREE MILLION HOURS X-AXIS ACCIDENT FREE PERIOD31.05.200008.06.200231.12.200222.08.200415.02.2006Accident Free Million Man hours Accident Free Period IFFCO AONLA UNITNow we see what type of risks and how they are being handled through some models of risk analysis in IFFCO –AONLA unit.¾PROCESS & SAFETY–RELATED DATA FOR INDIVIDUAL PROCESS STAGES :Physical and Health Occupational Hazards in any large scale Chemical /Hydrocarbon Processing Industry (CPI/HPI) like our can be broadly classified into the following categories:i. Mechanical Risks ii. Electrical Risks iii. Fire/Explosion Risks iv. High /low Temperature Exposure Risks v. Toxic/Carcinogenic Chemicals Exposure Risks vi. Corrosive/Reactive/Radioactive Chemicals Exposure RisksThe first two types of risks are of universal nature associated with any industrial activity and not specific to a particular plant or process. Mechanical risks which are generally encountered are injuries to the head, Limbs, eyes, etc usually as a results of negligence on the part of operating/maintenance personnel in the use of improper tools, bypassing prescribed safety procedures neglect of personal protective wear and risks associated with rotating machinery as well as risks associated with high-energy release from compressed gases. Electrical risks which result in shock and/or burns are most often a consequence of poor maintenance, ingress of dust or moisture, handling by unauthorized personnel and use of improper/substandard hardware.Other categories of risks associated with specific plants are detailed here under.Ammonia Plant :The manufacture of anhydrous liquid ammonia involves processing of hydrocarbons under high temperature, high pressure conditions in the presence of various catalysts, chemicals etc. Typical risks are as follows:Fire /Explosion¾ Glands/seal leaks in valves, pumps, compressors handling hydrogen, natural gas, naphtha, synthesis gas etc.¾ Hose/pipe failure, leakage from flanged joints carrying combustiblegases, vapours, liquids.¾ Fire box explosions in furnaces.High/Low Temp.Exposure RisksToxic ChemicalsExposure Risks¾ Burns due to contact with hot surfaces of pipelines, equipments, etc. or leaking steam lines, process fluids at high temperature. ¾ Frost bite due to contact with anhydrous liquid ammonia at -33 deg. C ¾ Burns due to contact with pyrophoric catalyst. ¾ Asphyxia due to inhalation of simple asphyxiants like CO2 , N2, H2, CH4, naphtha etc. and chemical asphyxiants like CO, NH3, Nickel carbonyl, V2O5, Hydrazine, NOx, SOx, H2S etc. ¾ Acute toxicity due to inhalation of catalyst dusts containing heavy metals like Ni, Cr, CO, Mo, Fe, Zn, Alumina etc. and silica gel molecular sieves, insulation fibers/dusts.1000020060080026.10.1997-31.05.200002.06.2000-08.06.200201.09.2002-31.12.200201.01.2003-22.08.200428.08.2004-15.02.2006947400737122700Y-AXIS –ACCIDENT FREE MAN DAYSX-AXIS ACCDIENT FREE PERIOD 910Urea PlantThe manufacture of urea involves reaction of Ammonia and Carbon dioxide under high temperature & pressure and subsequent recovery and concentration of the solution at various pressure stages. Typical risks are as follows :Fire / Explosion Risks¾ Ammonia leaks from glands / seals Risks involves, pumps orflanged joints piping resulting in formation explosive mixtures in air.Accumulation of H2 may take place in HP Section in case CO2 purity from Ammonia Plant is not within allowable limits. Ignition of this accumulated H2 can occur due to dissipation of static charge.High / Low Temperature Exposure Risks¾ Refer to risks in Ammonia Plant Toxic Chemicals Exposure Risks ¾ Asphyxia due to inhalation of simple Exposure Risks asphyxiants like CO2 and N2 and chemical asphyxiant, NH3. Solution of Urea, Ammonium carbamate and ammonium carbonatecontaining high NH3 content.¾ Irritation due to inhalation of urea dust.Corrosive / Radioactive Chemicals Exposure Risks¾ Severe burns, damage to eyes, skin and body tissues due to contact with anhydrous ammonia, conc. Urea and Ammonium carbamate solutions.Power PlantThe captive Power Plant involves generation of steam in N.G./Naphtha-fired boilers and utilizing the steam in Urea and Ammonia plants. Typical risks are as follows :Fire / Explosion Risks ¾ Explosion and fire risks associated with storage and handling of B Class (Naphtha) and Natural gas handling pipelines (Referoff site Facilities).¾ Fire Box explosion in BoilerFlammable Material Lower Upper Temp. °C High / Low Temp. Exposure Risks ¾ Burns due to contact with hot surfaces of pipelines, equipments, etc. or leaking steam lines. Toxic Chemical Exposure Risk¾ Asphyxia due to inhalation of SOX and Nox.¾ Irritation due to inflammation caused by inhalation of Natural gas and the Naphtha vapors.The permissible exposure limits for cyclohexylamine coal dust / fly-ash are given below :Offsite FacilitiesThe offsite facilities, as already described at the very outset, consist of integrated units for water and effluent treatment, inert gas generation, cooling towers, storage of petroleum products and ammonia, supply / distribution of utilities like compressed air, water, etc. Potential risks in the above offsite facilities are essentially on account of handling of corrosive, toxic and reactive chemicals as well as inflammable petroleum products.Fire / Explosion Risks ¾ Gland / Seal leaks in valves, pumps, compressor, handling naphtha,N.G., ammonia hydrogen, syngas etc.¾ Hose / pipe failure, leakage from flanged joints in pipes conveying petroleum products, ammonia, hydrogen, syngas, etc.¾ Leakage of petroleum products during tanker unloading operations. ¾ Overflow from storage tanks.¾ Overheating / pressurization of storage tanks.¾ Improper earthing / lightning protection of storage tanks and pipelines.¾ Improper sealing of floating roof tanks.¾ In adequate / improper breather valves leading to tank failures. ¾ Fire Box Explosion in cracker Furnace.Critical data for flammable materials stored / handled in off sites has already been furnished under Ammonia Plant and Power Plant.High / Low Temp. Exposure Risks ¾ Burns due to contact with hot surfaces of pipe lines, equipments, etc or leaking steam lines.¾ Heat radiation burns from high intensity flames from the flare stack. ¾ Frost bite due to contact with anhydrous liquid ammonia at – 33 °CToxic Chemicals Exposure Risks ¾ Asphyxia due to inhalation of simple asphyxiants like N2, H2, Naphtha, etc. and Chemical asphyxiants like Cl2, NH3, NOx, Sox,etc.¾ Toxicity due to inhalation of catalyst dust containing heavy metals like Ni, Pd, Alumina etc. and perlite / insulation fibers, silica gel dust.Data on Threshold Limit Values Limits for most of the above toxic Chemicals and dusts encountered in off sites has already been furnished under Ammonia Plant. Data for Cl2 are as follows :Corrosive Chemicals Exposure Risks ¾ Severe burners, damage to eyes, skin & body tissues due to contact with corrosive chemicals like anhydrous liquidAmmonia, Sulphuric acid, Hydrochloric acid, etc.Bagging PlantThe bagging plant encompasses storage, packing, loading and dispatch activities for product urea via road or rail. Typical risks in this plant are as follows :Fire Risks¾ Fire hazards due to storage of bulk quantity of polyethylene – lined jute bags or HDPE bags which are easily combustible. Chemicals Exposure Risks ¾ Irritation due to inhalation of urea dust and jute fibers.S.No Name of Chemical Form under normal condition Expected form ofChemical under abnormal condition1. 2. 3. 4. 5. 6.AmmoniaChlorineNaphthaHydrochloric AcidSulphuric AcidNatural GasLiquid state at – 33 °C temp. & atmospheric pressure.Liquid at ambient temp. & 17.0 Kg/cm² pressure.Liquid at ambient temp. & pressure.Liquid at ambient temp. & pressure.Liquid at ambient temp. & pressure.Gaseous at ambient temp &PressureVapour / Gaseous form.Vapour / Gaseous form.Vapour Acid fumes Acid fumes Gaseous Form¾INFORMATION ON THE PRELIMINARY HAZARD ANALYSISTypes of AccidentIt is clear that during the course of Urea manufacture, furnaces, reactors, moving machineries, material handling, cranes, chain, pulley blocks, wire ropes, chemicals, Rail wagons, etc. are involved. Past reportable accidents are related to these agencies.Type of personnel injuries indicates burn, cut, bone fracture burn injury etc. A brief resume of types of accidents may happen are as follows ;-1. Burn injury due to handling cleaning of burners in furnaces.2. Fire accidents in furnaces leading to property damage.3. Burn injury accident due to attending electrical faults.4. Burn injury accidents due to handling of acids / alkalies.5.Hit / cut type accidents due to various maintenance jobs. For reference purposes and internal report titled “Safety Performance at a glance” is enclosed as Annexure 5.System Elements or Events that can lead to a major AccidentAll the section / plants of IFFCO Aonla unit are constructed and designed taking care of all relevant safety measures possible. However the system elements such as Ammonia storage, Naphtha storage, Chlorine tonners, Ammonia Plant area, Urea Plant HP section are some of them which can lead to a major accident.Although, Fire, explosion and release / leakage of toxic chemicals may lead to major accident, all necessary safety measures have been duly incorporated in the plant design and regular up gradation of safety appliances is carries out.Hazards Urea manufacturing process involves many chemicals such as NG, as feed stock, Ammonia as anintermediate product and chlorine, hydrochloric / sulfuric acids, as water treatment chemicals.Furnaces, High pressure vessels, Reactors, pipe lines, storage tanks are also involved in thecourse of Urea and Ammonia manufacturing. Handling and storage of these Hazardous chemicals and their use in the process may leak to a hazardous situation.Failure Mode AnalysisThere are various modes in which flammable and toxic chemicals can leak into atmosphere causing adverse affects. It may be small leaks from gaskets of the flanged joints, or guillotine failure of a pipeline of even catastrophic failure of the storage tank. Some typical modes of failures and their possible causes are discussed below :S.No. Failure Mode Probable Cause Remarks1. Flange / Gasket failure Incorrect gasket Incorrect installation. Attention to be paid during selectionand installation of gaskets. 2Weld failureIt is normally due to poor quality of welds Welding to be done by certifiedwelders with right quality of weldingrods. Inspection and radiography must also be done.3 Pipe corrosion erosion or failure due to stress Some times fabrication or installation leaves stress in the pipes. Erosion or corrosion also are sometimes the cause. Pipes material of constructionshould be selected correctly. Design should take care of erosioneffects. And installation of pipes should not leave any stress.4 Over pressurization of pipeline Over pressurization can occur due to failure of SRV or incorrect operation.Necessary procedures should bethere to prevent.5 Deficient installation of pipes Pipes design and installation is sometimes not as per appropriate standard.It must be ensured that installationis as per correct standardscompletely. 6 Leaks from valve Leaks from glands, bonnets or failures valves spindle is sometimes the cause.Right selection of valves and theirmaintenance should be ensured. 7 Instruments failure Multifarious instruments are used for control of process parameters. Any such instrument failure can cause mishap.Reliability of instruments workingmust be ensured through proper selection and maintenance. 8 Failures of protective system Protective system like SRV, bursting discs, vent header, drain lines etc. are provided to take care of abnormal conditions.Reliability of protective system mustbe ensured highest throughinspection and proper maintenance. 9 Operational effort Plant operational parameters should not be exceeded beyond the permissible limits.Operating procedures must becomplete and strictly followed. 10 Other failures There are external other reasons causing the failures.Design and operating philosophymust consider all possible reasons. ¾ INFORMATION ON THE HAZARD ASSESSMENTIdentification Of HazardsThe following main hazards may exist in the factory under the situations given below-• High temperature and pressure.• Fire & explosions (due to inflammable / combustible materials). • Toxic and corrosive chemicals.• Toxic and poisonous gases and dust.• Electricity (Receiving / Clue ration / Distribution). • Disposal of wastes. • Work at heights.• Work in confined spaces / vessels / tank etc.• Specific jobs carried under highly hazards atmosphere (CO2, NH3, Naphtha vapours etc.). • Non working of safety devices, inter locks, failure of high RPM machineries. • Failure of boilers etc.• Any other consequences due to leak of Ammonia, Chlorine gases. • Hazards during heavy equipment handling (Crane, etc.) • Road accidentsHowever, the threats posed to the aforesaid hazards may be on account of (i) Fire or (ii) explosion or (iii) Release of toxic or corrosive liquid / gas from their confinement. Causes Of Major AccidentsFollowing Major causes may lead to major accidents :-1. Release of Ammonia in huge quantity from storage tank.2. Release of chlorine due to leakage / rupture in chlorine toner or its valve failure of injection pipe failure feeding to cooling tower.3. Fire / explosion in Naphtha tanks due to leakage, unconfirmed clouds, or boil over, etc.4.Explosion in High pressure equipments, reactors in Ammonia / Urea Plants.5. Fire / explosion in furnaces of Ammonia Plant and boilers in Power Plant.Assessment Of Hazards According To Their Occurrence FrequencyConcurrency frequency (probability failure / year) for each selected failure case is given in table 9.c.1. For most of the cases the probability of failure occurrence is very less. Fire / explosion, sling failure, safety rule failure, and injuries etc. are some cases which are considered as associated hazards.Assessment Of Accident ConsequencesA major accident may cause severe danger to life and properties. The assessment will be based on :• Onsitelosses.losses.• OffsiteThe first one will be loss of life, property damage and injuries to the scene of occurrence where the people are working or combating with the accident control.The offsite losses will include the loss of lives, injuries and properties damages of neighbor hood bases on the affected area of accident or major event, if any.Assessment Of The Possible Release Of Hazardous Chemicals Or Of Energy.Technological Risks posed by this Fertiliser factory constitute threat to :i) Its workersii) To a third party who may be present either in the factory or in its vicinity at the time of accident. iii) Inhabitants living in the immediate neighborhood of the factory and their property.iv) Environmental Conditions around the factory site.The threats posed to the aforesaid entities may be on account of -i) Fire,ii) Explosion,iii) Release of Toxic or corrosive liquids / gas from their confinement. The primary reason why such a disaster may occur, in spite of all precautionary measures is that major type of chemicals handled, are highly hazardous in nature and in substantial quantities, oriv) A combination of more than one of such accidental phenomenon.These risks may manifest due to accidental failures, break down or rupture of processing vessels, equipments, storage tanks or pipelines. They may also arise due to undetected loss of containment because of which liquid or gas contents gradually leak out in sufficient quantities to create a hazardous situation. The loss of containment and associated hazards may be realized in one of the following ways :-Large scale fire in naphtha storage area due to damage to the storage tank.-Naphtha leak from pipeline resulting into fire.-Flash fire due to leakage of flammable gas.-Equipment failure, pipeline failure, flange gasket failure, pump seal failure, safety relief valve failure etc. resulting in leakage of flammable, explosive and toxic material.-Accidents due to human errors.-Acts of nature like earthquake, enemy air attack during war, sabotage, act of terrorism etc.When the scale of such accident is as to cause either –a) Severe destruction of property.b) Multiple fatalities and other casualties and cannot be contained within the premises, a DisasterSituation is said to prevail.However the release of components listed below may cause hazards:-a) Natural Gas, the feed stock for ammonia plant andb) Hydrogen gas produced by reformation process for synthesizing Ammonia andc) Ammonia itself, generated as an intermediate product, constitute the gravest risks both fromtheir nature of properties and the quantities involved.Natural Gas is a highly flammable Gas equivalent to gasoline from fire and explosion hazard angle, having a auto ignition temp. of 482 °C and a flammable range of 3.8 – 17 %.Naphtha is also highly flammable liquid having flash point of -40o C and flammable range between 1 and 6%.Ammonia is highly toxic gas its TLV being 25 ppm. It is also a combustible gas which can explode under certain circumstances, although its lower explosive limit is rather high being of the order of 16%. It is true that two other highly flammable gases viz Carbon Monoxide and Methane are also evolved in of the Ammonia plant. However, as these gases are immediately converted into non-hazardous substances, they at best constitute transient risks. Besides the materials directly involved in the manufacturing process, another extremely toxic gas viz Chlorine.Chlorine (which has a TLV of 1 ppm) is used for treatment of water in the Cooling Towers. In-spite of the fact, that quantity of chlorine held in the plant is almost insignificant, because of its extremely high toxicity a leakage even in a ‘tonner’ holding only 900 Kg of gas can endanger the persons present inside the plant.Assessment of risks posed by industrial accidents has two aspects viz.•How frequently such accidents can occur and•What could be their impact on people, property and environment.Making a technically sound assessment of accident frequency for any individual plant is like walking on treacherous grounds. It is true that there are various structured methods like HAZOP, HAZAN, fault tree, Analysis Event tree Analysis etc. through which an estimate of such frequencies can be attempted. However, no such methods can ensure that all potential accidents or top – events would be identified, that all potential fault paths would be found and all common cause failures covered. More-over, the adoption of such methods need use of Reliability Indices of equipment and components of the system under study. These Reliability Indices are expected to be furnished by the manufacturers, which is seldom the case in actual practice. No doubt generic data could be used as a less preferable alternative. However, besides such data not being available for every component, their use may give an entirely erroneous picture, as the real values of such indices are greatly dependent on conditions of use, standards of maintenance etc. Even if correct Reliability data were available, the results may not be quite accurate as accidents are known to have taken place due to Human errors in operation and maintenance for which no satisfactory models are yet available.A statistical estimate of the risk could have been made if enough operating experience of the facts was available. However, in the present case, the experience is not long enough to predict with any degree of certainly of probability of accidents of different magnitudes, especially of that which may cause Maximum credible loss, as such accidents are incidents of extremely low frequency. All that can be stated with confidence is that since.a) The process carried out in the plant is well tested.b) The design and installation of the plant comply with recognized standards and codes ofpractice andc) All reasonable precautions are followed in respect of operation and maintenance, chancesof a major accident is of low order.HAZARDOUS AREAS OF THE PLANTThe following areas of the IFFCO Aonla Unit are hazardous with respect to nature of materials handled and operating parameters.• Ammonia Plant• Urea Plant• Ammonia storage•Naphtha Storage and Handling• Chlorine storagePLANT WISE HAZARDSThe plant wise hazards due to nature of materials handled there at are given below :Plant Hazardous Material Nature of Hazard Ammonia Plant Urea Plant Ammonia storage Naphtha Storage and handlingD.M. Water plant Cooling TowerNatural Gas Naphtha Process gas containing H2, CO, CH4 Ammonia (liquid or gas) Ammonia Carbon dioxide Ammonia Naphtha Hydrochloric acid caustic lye Chlorine Fire Fire Fire Explosion Toxic Toxic Asphyxiant ToxicFire Corrosive Toxic ASSESSMENT OF THE POSSIBLE DISPERSION OF RELEASED CHEMICALS STORAGE CAPACITY OF HAZARDOUS MATERIALSThe hazardous materials stored in the plant in substantial quantities. The detail of storage capacity for each material is given below:Equipment Nos. Material CapacityNaphtha storage tank (old) 2 Naphtha 6000 KL Naphtha storage tank (new) 1 Naphtha 10000 KL Ammonia storage Tank 2 Liquid Ammonia 10,000 Te * Chlorine Tonners 16 Chlorine 900KG* Though the capacities of Ammonia storage tanks are 10000 Te each , we normally store minimal quantity of liquid Ammonia in our Ammonia storage Tanks. The storage quantity at no times goes beyond 40% in the storage tanks. This conscious decision reduces the hazard potential.FAILURE CASE LISTINGKeeping in view, the inventories of different hazardous material, plant process parameters etc. following are the selected failure case which way be considered for consequence analysis. This includes the worst case scenario i.e. catastrophic failure of Ammonia storage tanks and Naphtha storage tanks, also leakage of ammonia from ammonia storage tank or from the system handling ammonia, chlorine from tonners and fire in the naphtha tanks or from handling systems is identified as the major accident hazards. This can occur as given below:Incident ConsequenceCatastrophic rupture of Ammonia storage tank or major leakage from the ammonia handling system.Refrigerated liquid ammonia or liquid ammonia spill and dispersion. Chlorine leakages from the tonners due to valve getting sheared.Chlorine leakage and dispersion Catastrophic failure of Naphtha/ FO storage tanks and the leakage catching fire. Major fire. Pipeline fracture / Nozzle failure Liquid ammonia spills at hydraulic head or pump deliverypressure and dispersion.Chlorine leakage at tonners pressure and dispersionIf the leakage due to pipeline fracture or nozzle failure in naphtha and catches fire- fire incident.Gasket failure Liquid ammonia spill and dispersion.Chlorine leakage and dispersion.Fire if the naphtha or FO leakage due to gasket failure and theleakage catch fire.System elements or events that can lead to major accident.a. Catastrophic rupture of Ammonia storage tank or major leakage from the ammonia handlingsystem.b. Chlorine leakage from the tonners due to valve getting sheared.c. Catastrophic failure of Naphtha/FO / Diesel storage tanks or major leakage from the handlingsystems of these materials catching fire.d. Pipeline fracture / Nozzle failure.e. Gasket failure leading to flange leakagesHazardsIncident QuantityReleasedConsequences1 Catastrophic rupture ofAmmonia storage tanks. 4000 MT Ammonia Concentration upto 500 ppm indown-wind direction upto 11000 m2 Liquid ammonia line totank failure (20%) 40MT Ammonia concentration upto 500 ppm indown wind direction upto 4700ft downwind& 8000ft cross wind.3 Chlorine leakage fromthe tonners 900 kg Chlorine Concentration upto 30 PPM indown-wind direction upto 1247 m4 Catastrophic failure ofNaphtha storage Tank 10000 KL 12.5 KW/m2 heat radiation level at a distance of 56.35mBurnpool radius : 150ft, Flame height:210ft, Fatality radius upto distance 300ft, First degree/Injury Zone radius upto400ft(approx.)5 10000KL Naphtha tankoutlet line failure (100%) First degree burn upto 300 ft. Fatality radius upto 210ft Burnpool radius: 100ft6 Catastrophic failure ofNaphtha storage Tanks 7000KL 12.5KW/m2 heat radiation level at adistance of 46.53m7 Catastrophic failure ofFuel Oil Storage tank. 1000 KL 12.5 KW/m2 heat radiation level at adistance of 43.5m8 Leakage of synthesisgas from loop 12.5KW/m2 heat radiation due to flash fireextends up to 224.3 m12.5 KW/m2 radiation level due to jet flameoccur till 92.87 mThe over pressure of 0.2068 bar g is up to adistance of 265.6m This over pressure mayresult in extensive damage.Note: 1. The IDLH of ammonia has been taken as 500ppm (NIOSH)2.The IDLH of chlorine has been taken as 30 ppm. (NIOSH)3. The weather is taken as 5 m/s D pasquillHydrogenSynthesis gas (which is hydrogen rich) is produced in the plant for conversion to Ammonia. There is no hydrogen gas holder for storage. Due to high pressure sufficient quantity is present in theprocess vessels and pipings to pose fire / explosion hazard. No off-site effect is envisaged for any synthesis gas fire explosion accidents.。
Hazard risk的区别

1、accident,incident,event,occurrence,happening的区别这些名词均有“事故、事件”之意。
1)accident :强调偶然或意外发生的不幸事情。
eg:An awful accident has happened.(发生了一起可怕的意外事故。
)2)incident :既可指小事件或附带事件,又可指政治上具有影响的事件或事变。
eg:The demonstration proceeded without incident.(游行示威进行时没有出事。
)3)event :可指任何大小事件,但尤指历史上的重大事件。
eg:The new book was the cultural event of the year.(这本新书的出版是今年文化界的大事。
)4)occurrence 和happening 这两个词多指日常生活中发生的一般事件,有时也指偶然发生的事。
eg:Newspapers record the chief occurrences of the day.(纸报道了当天发生的大事。
)I know nothing at all about the recent happenings there.(对那里近来发生的事我一点儿也不知道。
)2、delegate, deputy, representative, agent, substitute有什么区别?这些名词有“代表、代理人”之意。
delegate : 指一般被派参加某一会议的代表。
He is one of the delegates to the conference.(他是与会代表之一。
)deputy : 指上级授权代理行事的代表,特指被选择为执行全部或部分公务的人。
John will act as a deputy for me during my absence.(我离开期间, 约翰将代理我的职务。
)He is one of the delegates to the conference.(他是与会代表之一。
危险源辨识参考(Hazard Identification)
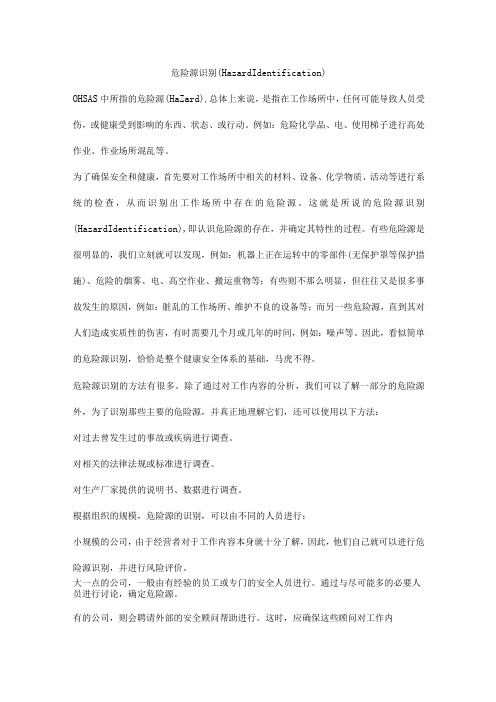
危险源识别(HazardIdentification)OHSAS中所指的危险源(HaZard),总体上来说,是指在工作场所中,任何可能导致人员受伤,或健康受到影响的东西、状态、或行动。
例如:危险化学品、电、使用梯子进行高处作业、作业场所混乱等。
为了确保安全和健康,首先要对工作场所中相关的材料、设备、化学物质、活动等进行系统的检查,从而识别出工作场所中存在的危险源。
这就是所说的危险源识别(HazardIdentification),即认识危险源的存在,并确定其特性的过程。
有些危险源是很明显的,我们立刻就可以发现,例如:机器上正在运转中的零部件(无保护罩等保护措施)、危险的烟雾、电、高空作业、搬运重物等;有些则不那么明显,但往往又是很多事故发生的原因,例如:脏乱的工作场所、维护不良的设备等;而另一些危险源,直到其对人们造成实质性的伤害,有时需要几个月或几年的时间,例如:噪声等。
因此,看似简单的危险源识别,恰恰是整个健康安全体系的基础,马虎不得。
危险源识别的方法有很多。
除了通过对工作内容的分析,我们可以了解一部分的危险源外,为了识别那些主要的危险源,并真正地理解它们,还可以使用以下方法:对过去曾发生过的事故或疾病进行调查。
对相关的法律法规或标准进行调查。
对生产厂家提供的说明书、数据进行调查。
根据组织的规模,危险源的识别,可以由不同的人员进行:小规模的公司,由于经营者对于工作内容本身就十分了解,因此,他们自己就可以进行危险源识别,并进行风险评价。
大一点的公司,一般由有经验的员工或专门的安全人员进行。
通过与尽可能多的必要人员进行讨论,确定危险源。
有的公司,则会聘请外部的安全顾问帮助进行。
这时,应确保这些顾问对工作内容有足够的了解和适当的经验。
但,无论是由谁来进行危险源识别,以下原则,希望能够被充分地考虑:组织的最高责任者(经营者),永远是对工作场所的安全负有责任的。
一定要听取真正在现场工作的员工或员工代表的意见。
2 HAZARDS IDENTIFICATION
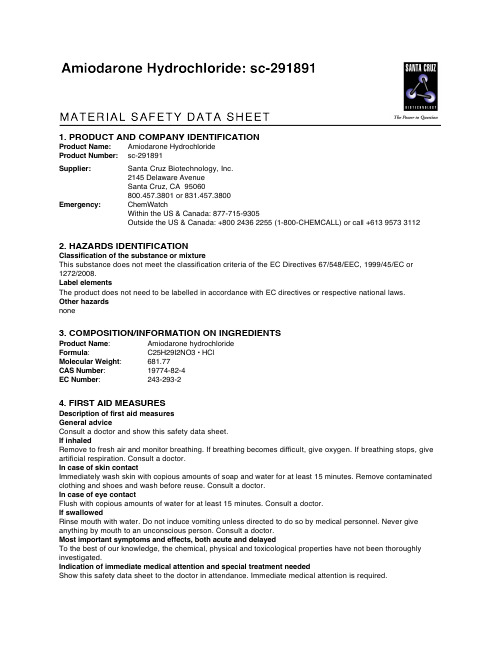
1. PRODUCT AND COMPANY IDENTIFICATIONProduct Name: Amiodarone HydrochlorideProduct Number:sc-291891Supplier:Santa Cruz Biotechnology, Inc.2145 Delaware AvenueSanta Cruz, CA 95060800.457.3801 or 831.457.3800Emergency:ChemWatchWithin the US & Canada: 877-715-9305Outside the US & Canada: +800 2436 2255 (1-800-CHEMCALL) or call +613 9573 3112 2. HAZARDS IDENTIFICATIONClassification of the substance or mixtureThis substance does not meet the classification criteria of the EC Directives 67/548/EEC, 1999/45/EC or 1272/2008.Label elementsThe product does not need to be labelled in accordance with EC directives or respective national laws.Other hazardsnone3. COMPOSITION/INFORMATION ON INGREDIENTSProduct Name: Amiodarone hydrochlorideFormula: C25H29I2NO3 • HClMolecular Weight: 681.77CAS Number:19774-82-4EC Number: 243-293-24. FIRST AID MEASURESDescription of first aid measuresGeneral adviceConsult a doctor and show this safety data sheet.If inhaledRemove to fresh air and monitor breathing. If breathing becomes difficult, give oxygen. If breathing stops, give artificial respiration. Consult a doctor.In case of skin contactImmediately wash skin with copious amounts of soap and water for at least 15 minutes. Remove contaminated clothing and shoes and wash before reuse. Consult a doctor.In case of eye contactFlush with copious amounts of water for at least 15 minutes. Consult a doctor.If swallowedRinse mouth with water. Do not induce vomiting unless directed to do so by medical personnel. Never give anything by mouth to an unconscious person. Consult a doctor.Most important symptoms and effects, both acute and delayedTo the best of our knowledge, the chemical, physical and toxicological properties have not been thoroughly investigated.Indication of immediate medical attention and special treatment neededShow this safety data sheet to the doctor in attendance. Immediate medical attention is required.5. FIRE-FIGHTING MEASURESExtinguishing mediaSuitable extinguishing mediaUse water spray, alcohol-resistant foam, dry chemical or carbon dioxide.Special hazards arising from the substance or mixtureIn combustion, may emit toxic fumes.Precautions for fire-fightersWear suitable protective clothing to prevent contact with skin and eyes and self-contained breathing apparatus. 6. ACCIDENTAL RELEASE MEASURESPersonal precautions, protective equipment and emergency proceduresDo not take action without suitable protective clothing - see section 8 of SDS. Evacuate personnel to safe areas. Ensure adequate ventilation. Avoid breathing vapors, mist, dust or gas.Environmental precautionsDo not let product enter drains.Methods and materials for containment and cleaning upCover spillage with suitable absorbent material. Using non-spark tools, sweep up material and place in an appropriate container. Decontaminate spill site with 10% caustic solution and ventilate area until after disposal is complete. Hold all material for appropriate disposal as described under section 13 of SDS.Reference to other sectionsFor required PPE see section 8. For disposal see section 13.7. HANDLING AND STORAGEPrecautions for safe handlingUse in a chemical fume hood, with air supplied by an independent system. Avoid inhalation, contact with eyes, skin and clothing. Avoid the formation of dust and aerosols. Use in a well-ventilated area. Keep away from sources of ignition. Avoid prolonged or repeated exposure.Conditions for safe storage, including any incompatibilities.Store in cool, well-ventilated area. Keep away from direct sunlight. Keep container tightly sealed until ready for use. Store at room temperature.Specific end usesUse in a laboratory fume hood where possible. Refer to employer's COSHH risk assessment.8. EXPOSURE CONTROLS/PERSONAL PROTECTIONControl parametersComponents with workplace control parametersContains no substances with occupational exposure limit values.Exposure controlsAppropriate engineering controlsUse in a fume hood where applicable. Ensure all engineering measures described under section 7 of SDS are in place. Ensure laboratory is equipped with a safety shower and eye wash station.Personal protective equipmentEye/face protectionUse appropriate safety glasses.Skin protectionUse appropriate chemical resistant gloves (minimum requirement use standard BS EN 374:2003). Gloves should be inspected before use. Wash and dry hands thoroughly after handling.Body protectionWear appropriate protective clothing.Respiratory protectionIf risk assessment indicates necessary, use a suitable respirator.9. PHYSICAL AND CHEMICAL PROPERTIESForm solid Vapor pressure No data available Odor No data available Vapor density No data available Odor threshold No data available Relative density No data available Solubility(ies) To 50 mM in DMSO pH No data available Melting / freezing point No data available Partition coefficient No data available Boiling point / range No data available Auto-ignition temperature No data available Flash point No data available Decomposition temperature No data available Evaporation rate No data available Viscosity No data available Flammability (solid, gas) No data available Explosive properties No data available Upper / lower flammability limits No data available Oxidizing properties No data available Other safety information No data available10. STABILITY AND REACTIVITYReactivityStable under recommended transport or storage conditions.Chemical stabilityStable under recommended storage conditions.Possibility of hazardous reactionsHazardous reactions will not occur under normal transport or storage conditions. Decomposition may occur on exposure to conditions or materials listed below.Conditions to avoidHeat, moistureIncompatible materialsStrong acids/alkalis, strong oxidizing/reducing agents.Hazardous decomposition productsIn combustion may emit toxic fumes. No known decomposition information.11. TOXICOLOGICAL INFORMATIONInformation on toxicological effectsAcute ToxicityORL-RAT LD50: >3gm/kg; IPR-RAT LD50: 610mg/kg; IVN-RAT LD50: 170mg/kgSkin corrosion/irritationClassification criteria are not met based on available dataSerious eye damage/irritationClassification criteria are not met based on available dataRespiratory or skin sensitizationClassification criteria are not met based on available dataGerm cell mutagenicityClassification criteria are not met based on available dataCarcinogenicityClassification criteria are not met based on available dataReproductive toxicityClassification criteria are not met based on available dataSpecific target organ toxicity - single exposureClassification criteria are not met based on available dataSpecific target organ toxicity - repeated exposureClassification criteria are not met based on available dataAspiration hazardClassification criteria are not met based on available dataSymptoms / Routes of exposureInhalation: There may be irritation of the throat with a feeling of tightness in the chest.Ingestion: There may be irritation of the throat.Skin: There may be mild irritation at the site of contact.Eyes: There may be irritation and redness.Delayed / Immediate Effects:No known symptoms.Additional InformationRTECS No: OB1361000Exposure may cause irritation to eyes, mucous membranes, upper respiratory tract and skinTo the best of our knowledge, the chemical, physical and toxicological properties have not been fully investigated.12. ECOLOGICAL INFORMATIONToxicityNo data availablePersistence and degradabilityNo data availableBioaccumlative potentialNo data availableMobility in soilNo data availableResults of PBT and vPvB assessmentNo data availableOther adverse effectsMay be harmful to the aquatic environment.13. DISPOSAL CONSIDERATIONSWaste treatment methodsProductTransfer to a suitable container and arrange for collection by specialized disposal company in accordance with National legislation.Contaminated packagingDispose of in a regulated landfill site or other method for hazardous or toxic wastes in accordance with National legislation.14. TRANSPORT INFORMATIONClassified according to the criteria of the UN Model Regulations as reflected in the IMDG Code, ADR, RID and IATA.UN-NumberDoes not meet the criteria for classification as hazardous for transport.UN proper shipping nameDoes not meet the criteria for classification as hazardous for transport.Transport hazard class(es)Does not meet the criteria for classification as hazardous for transport.Packaging groupDoes not meet the criteria for classification as hazardous for transport.Environmental hazardsThis product is not classified as environmentally hazardous according to the UN Model Regulations, nor a marine pollutant according to the IMDG Code.Special precautions for usersNo data available15. REGULATORY INFORMATIONThis safety datasheet complies with the requirements of Regulation (EC) No. 453/2010.Safety, health and environmental regulations/legislation specific for the substance or mixtureNo data availableChemical safety assessmentA Chemical Safety Assessment has not been made for this product.16. OTHER INFORMATIONThe above information is believed to be correct but does not purport to be complete and should be used only as a guide. The burden of safe use of this material rests entirely with the user.05/23/2014。
02_Hazard Identification
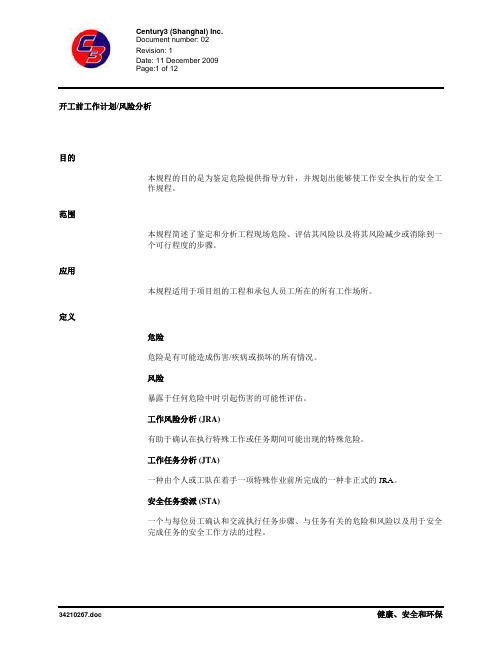
Page:1 of 12开工前工作计划/风险分析目的本规程的目的是为鉴定危险提供指导方针,并规划出能够使工作安全执行的安全工作规程。
范围本规程简述了鉴定和分析工程现场危险、评估其风险以及将其风险减少或消除到一个可行程度的步骤。
应用本规程适用于项目组的工程和承包人员工所在的所有工作场所。
定义危险危险是有可能造成伤害/疾病或损坏的所有情况。
风险暴露于任何危险中时引起伤害的可能性评估。
工作风险分析 (JRA)有助于确认在执行特殊工作或任务期间可能出现的特殊危险。
工作任务分析 (JTA)一种由个人或工队在着手一项特殊作业前所完成的一种非正式的JRA。
安全任务委派 (STA)一个与每位员工确认和交流执行任务步骤、与任务有关的危险和风险以及用于安全完成任务的安全工作方法的过程。
Page:2 of 12开工前工作计划/风险分析目的 (1)范围 (1)应用 (1)定义 (1)1.0概要 (3)2.0危险鉴定 (3)3.0风险评估、风险管理和危险管理 (3)3.1工程方法 (3)3.2工程危险研究过程 (3)3.3风险管理和评估 (5)3.4规划解决方案/控制 (5)4.0控制危险的系统方法 (6)4.1危险鉴定方法 (6)4.2评估 (7)4.3控制 (7)4.4评估 (7)4.5监控 (7)5.0检查 (8)6.0工作风险分析 (8)6.1JRA小组 (8)6.2要分析的工作选择 (8)A.潜在的危险 (9)B.失败后果 (9)C.事故历史纪录 (9)D.带电机械/设备 (9)6.3限制范围 (9)6.4完成JRA的基本过程 (9)7.0工作任务分析 (10)8.0安全任务委派 (11)8.1责任 (11)8.2规程 (11)8.3后-STA (11)9.0参考 (12)10.0附件 (12)Page:3 of 12开工前工作计划/风险分析1.0概要所有的工程都要实施和记录危险鉴定。
所有的工程都要执行危险管理规程。
- 1、下载文档前请自行甄别文档内容的完整性,平台不提供额外的编辑、内容补充、找答案等附加服务。
- 2、"仅部分预览"的文档,不可在线预览部分如存在完整性等问题,可反馈申请退款(可完整预览的文档不适用该条件!)。
- 3、如文档侵犯您的权益,请联系客服反馈,我们会尽快为您处理(人工客服工作时间:9:00-18:30)。
PPT-072-01
6
Hazard Identification
• HAZID process must be ongoing to ensure existing hazards are known, and • New hazards recognized before they are introduced: - Prior to modification of facility - Prior to change in workforce - Before and during abnormal operations, troubleshooting - Facility early warning signals - Employee feedback - After an incident
PPT-072-01 15
Safety Inspection Checklist
PPTPPT-072-01
17 16
Brainstorming
Advantages • Useful starting point for many HAZID techniques to focus a group’s ideas, especially at the concept phase • Facilitates active participation and input • Allows employees experience to surface • Enables “thinking outside the box” • Very useful at early stages hazard identification Disadvantages • Less rigorous and systematic than other techniques • High risk of missing hazards unless combined with other tools • Relies on experience and competency of facilitator
Disadvantages • Tends to limit creative thinking • Used alone introduces the potential of limiting to already known hazards - no new hazard types are identified • On their own will rarely be able to satisfy regulatory requirements
PPT-072-01
4
Identifying Hazards
It takes a hazard and someone exposed to the hazard to produce an incident. Hazard + Exposure = Incident
Is this an incident waiting to happen?
PPT-072-01
13
HAZID Techniques
• Checklists - questions to assist in hazard identification • Brainstorming - whatever anyone can think of
• “What If” analysis - possible outcomes of change
PPT-072-01 9
Hazard Identification
Conducting the HAZID – Consider the Past, Present and Future
Historical conditions
What has gone wrong in the past? Root cause Historical records Process experience Near misses
•Hazards should not be disregarded simply because: - They appear to be very unlikely - They have not happened previously - They are considered to be adequately controlled by existing measures
• “Non-credible” scenarios have happened to others • Worst cases are important to emergency planning
PPT-072-01
11
Hazard Identification
Issues for consideration
PPT-072-01
Existing conditions
Identified hazards
Future conditions
Unforeseeable
10
Hazard Identification
It is tempting to disregard “non-credible” scenarios BUT:
PPT-072-01 12
Hazard Detection & Identification
• The following list shows the main ways to
identify hazards:
→ Walkthrough surveys
→ → → → → Inspection checklists Past records Accident investigations Consultation Documentation
PPT-072-01 7
Hazard Identification
• A systematic, transparent and comprehensive HAZID process should be used based on a comprehensive and accurate description of the facility
Hazard Identification
Bureau of Workers’ Comp PA Training for Health & Safety (PATHS)
PPT-072-01
1
Hazard Detection & Inspection
• What is a hazard? • What should I look for? • How do I perform the inspection? • How do I document the inspection? • How do I evaluate the hazards? • What type of control measure(s)
PPT-072-01 17
What If Analysis
Advantages • Useful for an early method of identifying hazards • It can be used for almost every type of analysis situation Disadvantages • Checklists are used extensively which can provide tunnel vision, running the risk of overlooking possible causal factors
• HAZOP - identifies “process plant” type incidents
ห้องสมุดไป่ตู้
• Job safety analysis – procedures
• Fault tree analysis - combinations of failures
PPT-072-01 14
Checklists
PPT-072-01 3
Risk vs. Hazard
Risk: The measure of the probability and severity of an adverse effect caused by a hazard
Hazard: What causes the risk; administrative or physical (causes or has the potential to cause a loss)
• • • • • • • •
Equipment can be off-line Safety devices can be disabled or fail to operate Several tasks may be concurrent Procedures are not always followed People are not always available How we act is not always how we plan to act Things can take twice as long as planned Abnormal conditions - Power failure
•
should I use? What standards do I reference?
PPT-072-01
2
Hazard vs. Near Miss
Hazard - An act or a condition in the workplace that has the potential to cause injury, illness, or death to a person and/or damage to company property, equipment and materials Near Miss - is an unplanned event that did not result in injury, illness, or damage – but had the potential to do so. Only a fortunate break in the chain of events prevented an injury, fatality or damage