热塑性塑料注射成型时常见缺陷_产生原因及解决措施
注塑成型常见产品缺陷与处理办法。
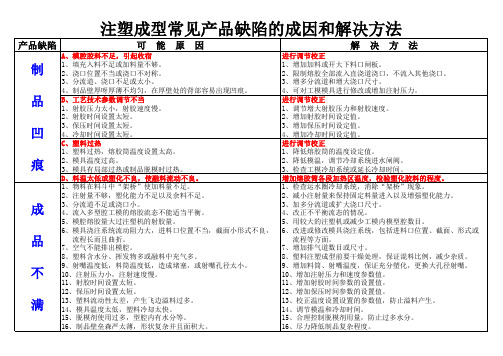
良
6、制品形状不良,壁厚薄不均匀,使融料在薄壁处汇合。
7、模具冷却系统不当或排气不良。
8、塑料内掺有不相熔的的料、油质或脱模剂不当。
12、塑料有及污回染料、混干全燥比不例良大或,有使挥塑发料物收。缩方向性过大或填料分布不均
。
制
3、不适当的脱模设计,制品壁薄,脱模斜度小,有尖角及缺口,容
品
易应力集中。 4、顶针或环定位不当,或成型条件不当,应力过大,顶出不良。
解决方法
所受的背压减少。 11、检查料筒和射嘴,浇注系统太粗糙,应改进和提高。 12、、混原料料时要避干免燥混,入设杂备物干。净,换料时要清除干净,以免留有余料 。 3、保证所用颜料质量,使用搅拌时颜料要均匀附在料粒表面。 4、降低熔胶筒、射嘴温度,清除烧焦的胶料。 5、降低射胶压力和速度参数值,避免添加剂分解。 6、擦干模具表面水分和油污,合理使用脱模剂。 7、合理设置纤维填料的工艺参数,合理使用溶剂,使塑化良好,
5塑料料温太低模温低射嘴孔径小在注射压力速度高时剪应5增加熔胶筒的温度及模具温度减小射胶压力和速度以防止6料温高模温高填充作用过分保压补缩过大射胶压力高时6降低熔胶筒的温度及模具温度减小射胶压力和保压补缩7制品厚薄不均参数调节不当冷却不均或收缩不均
注塑成型常见产品缺陷的成因和解决方法
产品缺陷
可能原因
1、注塑前先干燥处理胶料,也要避免处理过程中受过大的温度变
注射成型常见故障产生的原因及排除方法

一、欠注的故障分析及排除方法1、设备选型不当:塑件的总质量(包括塑件、浇道及飞边)不能超过注射机的最大注射量的85%(同时也不能小于20%)。
2、供料不足:应检查原料粒是否均匀,加料口有无“架桥”现象、加料段是否温度过高,背压是否太低等。
3、原料流动性能太差:这时模具的结构参数是影响欠注的主要原因。
应设法改善浇注系统的滞流缺陷,如合理设置浇道位置、扩大浇口、流道及注料口尺寸和采用较大的喷嘴等。
此外检查原料中的再生料是否过量。
4、冷料杂质阻塞料道:5、浇注系统设计不合理:设计浇注系统时要注意浇口平衡,各型腔内塑件的质量要与浇口的大小成正比,各腔内制件质量与浇口截面的比值基本相等,这样才能使各型腔同时充满,浇口位置应选择在塑件的厚壁部位。
各种成型树脂与浇口、流道的关系如表2-1所示。
6、模具排气不良:对于型腔较深的模具,应在欠注的部位增设排气沟糟或排气孔;在合模面上,可开设深度为此0.02-0.04mm,宽为5-10mm的排气槽,排气槽设置在型腔的终端充模处。
在工艺操作上可提高模温,降低注射速度,减小浇注系统阻力,减小合模力等辅助措施改善排气不良。
表2-1:各种成型树脂与浇口、流道的关系注:表中的符号“0”表示相宜7、模具温度太低:8、熔料温度太低。
9、喷嘴温度太低。
10、注射压力或保压压力不足。
提高注射压力延长注射时间。
11、注射速度太慢。
12、塑件结构设计不合理。
在设计塑件的形体结构时应注意塑件的厚度与塑料熔料充模时的极限流动长度有关。
塑料熔料的极限流动长度与塑件壁厚间的比值(流长比)如表2-2所示。
表2-2 充模过程中,熔料极限流动长度与塑件厚度的比值在注射成型中,塑件厚度采用最多的为1-3mm,大型件为3-6mm,文献推荐的最小厚度为:聚乙烯0.5mm,醋酸纤维素和醋酸丁纤维素塑料0.7mm,乙醋酸纤维素塑料0.9mm,聚甲基丙烯酸甲酯0.7mm,聚酰胺0.7,聚苯乙烯0.75mm,聚氯乙烯2.3mm,通常塑件的厚度超过8mm或小于0.5mm都对注射成型不利。
热塑性塑料注射成型时常见缺陷、产生原因及解决措施
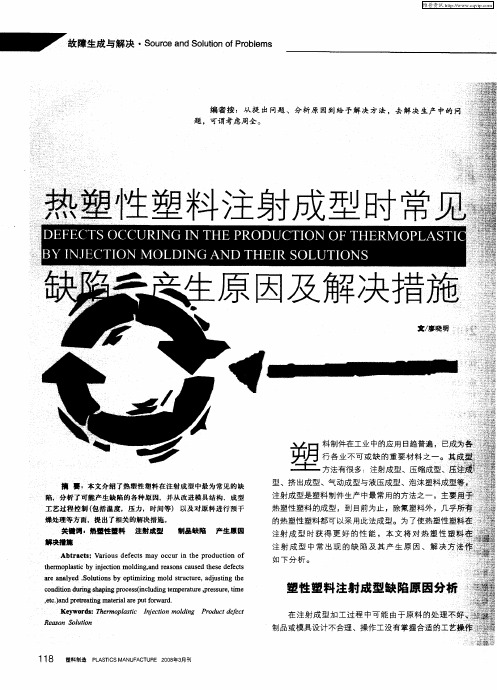
制品或 模具设计不 合理、操作工没有掌握合适的 工艺
1 塑 制 PAT S A UATR 08 3 刊 8 1 料 造 LSI N FCUE 2 年 月 CM 0
维普资讯
条件 ,或者 因机 械 方面 的原 因 ,常常
关键调Байду номын сангаас・热丝性丝料 注射 成型
解决措施
制品缺陷 产生原 因
注射 成 型 时 获 得 更 好 的性 能 ,本 文 将 对 热 塑性 塑 料 在 l _ 注 射 成 型 中 常 出现 的缺 陷及 其 产 生 原 因 、解 决 方 法作
如下分 析 。
Abt a t :Va i usde e t a c u n t e p o uci n o rcs ro f c sm y O c r i h r d to f
维普资讯
1g 蔓 t . l j一 l 一 . l
■ _ _ 故障 成 解_ 一_ r dot oes _ _ — 生 与 决・oca loo rl SuenSu nf bm i P _
_ ≮
~
编者按:从提出问 题、分析原因到给予解决方法, 去解决生产中的问 j 0
制 品 有 明 显 的 熔 接 痕
熔接 痕 是 由于 来 自不 同方 向的熔
融 树脂 前 端部 分被 冷 却 、在 结合 处未
能 完全 融 合而 产 生 的。一 般 情况 下 , 主 要 影响 外观 ,对涂 装 、 电镀 产 生影 响 。 严 重 时 ,对 制 品 强 度 产 生 影 响 ( 别是 在纤 维 增强 树脂 时 ,尤 为严 特
temo lsi b jcinmodn , drao scu e eedfcs h r pat yi et liga esn a sdt s eet c n o n h
热塑性塑料注射成型中常见缺陷改善对策

热塑性塑料注射成型中常见缺陷改善对策1.鼓包缺陷:鼓包是指塑料制品表面出现隆起、凹陷等现象。
造成鼓包的原因可能是注塑机压力过高、模具开发板不均匀、塑料熔融不均衡等。
改善对策是合理调节注塑机的压力和速度,仔细调整模具,增加剂量尺寸。
2.短斑缺陷:短斑是指塑料制品表面出现小孔洞或不完整的斑点。
这可能是由于模具中的残留气体造成的,或者是熔融塑料中含有杂质。
改善对策包括使用具有较好流动性的塑料材料、提高塑料熔点来减少气体生成、增加熔融进气口。
3.流痕缺陷:流痕是指塑料制品表面出现沟槽状痕迹的现象,它可能是由于塑料熔融不均匀、模具过热或注射速度过快造成的。
改善对策包括增加塑料的温度,调整模具温度,减少注射速度。
4.尺寸偏差:尺寸偏差是指塑料制品的实际尺寸与设计尺寸之间存在差异。
尺寸偏差可能是由于模具设计不合理、熔融塑料冷却不均匀等原因造成的。
改善对策包括重新设计模具、增加冷却系统、提高塑料的熔融温度。
5.热损失:热损失是指在塑料注射成型过程中,熔融塑料的温度下降过快,导致无法充分填充模具腔体。
改善对策包括增加塑料温度,提高注塑机的注射速度和压力,加热模具等。
6.气泡缺陷:气泡是指塑料制品内部或表面存在充气空洞的现象。
气泡可能是由于塑料材料中含有过多的水分或气体,模具温度不恰当,注射过程中太多的空气进入等原因导致的。
改善对策包括使用低含水量的塑料材料、调整模具和注射过程中的温度、加强模具和注射机的密封性。
7.翘曲缺陷:翘曲是指塑料制品的形状出现变形的现象,通常是由于注射过程中的过度冷凝和收缩造成的。
改善对策包括调整注射温度和注射速度,增加模具的支撑结构,选择具有较小收缩率的塑料材料。
总之,热塑性塑料注射成型中常见的缺陷有很多种,针对不同的缺陷,需要采取相应的改善对策。
通过调整注射机参数、优化模具设计和选择合适材料,可以有效降低注射成型过程中的缺陷发生,提高产品质量。
同时,定期检查和维护设备、监控质量指标的变化也是预防和改善缺陷的必要措施。
塑胶注成型不良缺陷种类及原因分析以及改善对策

塑胶注成型不良缺陷种类及原因分析以及改善对策塑料制品不良及处理方法成型上的缺点有些是发生在机器性能、模具设计或原料特性本身外,大部分问题可靠调整操作条件来解决。
调整操作条件必须注意:每次变动一个因素见到其结果再变动另一个。
调整完了后必须观察一段时间,待操作平衡稳定后的结果才算数。
压力的变动在一两模内即知结果,而时间尤其温度的变动需观察十分钟后的结果才算稳定结果。
熟悉各种缺点可能的原因及优先调整因素,以下分项说明各种缺点,其可能发生的原因及对策。
有些缺点及原因仅限于某些原因,有些缺点则是由多种原因引起的。
成品未完整(SHORT SHOT)故障原因处理方法原料温度太低提高料筒温度注射压力太低提高注射压力预塑量不够增多计量行程射出时间太短增长射出时间射出速度太慢加快射出速度模具温度太低提高模具温度模具温度不匀重调模具水管模具排气不良恰当位置加适度之排气孔喷嘴阻塞拆除清理进料不平均重开模具溢口位置浇道或溢口太小加大浇道或溢口原料内润滑剂不够酌加润滑剂螺杆止逆环(过胶圈)磨损拆除检查修理机器注射量不够更换较大机器缩水(SINK MARK)预塑量不够增加预塑计量行程注射压力低提高注射压力保压压力不够提高保压压力注射时间太短增长射出时间注射速度太快减小速度溢口不平衡调整模具入口大小或位置喷嘴阻塞拆除清理料温过高降低料温模温不当调整适当之温度冷却时间不够酌延冷却时间排气不良在缩水处设排气孔成品本身或其肋(RIB)及柱(BOSS)过厚检讨成品料筒过大更换较小规格料筒螺杆止逆环(过胶圈)磨损拆除检查修理成品粘模(PRODUCT STICKING)注射压力太高降低射出压力剂量过多使用脱模剂保压时间太久减少保压时间注射速度太快减小速度料温过高降低料温进料不均匀使部分过饱变更溢口大小或位置冷却时间不足增加冷却时间模具温度过高或过低调整模温及两侧相对温度模具内有脱模倒角(UNDERCUT)修模具去除倒角模具表面不光打光模具浇道(水口)粘模(SPROE STICKING)注射压力太高降低射出压力加热温度过高调节温度浇道过大修改模具浇道冷却不够延长冷却时间或降低料筒温度浇道脱模角不够修改模具重新调整其配合增加角度浇道凹弧(SPRUE BUSHING)与射嘴配合不正重新调整其配合浇道内表面不光或有脱模倒角检修模具浇道外孔有损坏检修模具无浇道抓锁(SNA TCHPIN)加设抓锁填料过饱降低射出剂量、时间及速度毛头、披锋(FLASE)加热温度太高降低加热温度、降低模具温度注射压力太高降低射出压力填料过饱降低射出剂量、时间及速度合模线(PARTING LINE)或密封面(MA TING SURFACE)不良检修模具锁模压力不够增加锁模压力制品投影面积过大更换锁模压力较大之机器开模时或顶出时成品破裂(CRACKING)填料过饱降低射出剂量、时间及速度模温太低升高模温部份脱模角不够检修模具有脱模倒角检修模具成品脱模时不能平衡脱离检修模具顶针不够或位置不当检修模具脱模时模具产生真空现象降低开模或顶出慢速、加进气设备结合线(WELD LINES)塑料熔融不佳提高塑料温度;提高背压;加快螺杆转速模具温度过低提高模具温度注射速度太慢增加注射速度注射压力太低提高注射压力塑料不洁或掺有他料检查原料脱模油太多少用脱模油或尽量不用浇道及溢口过大或过小调整模具入口尺寸或改变位置模内空气排除不及增开排气孔或检查原有排气孔是否堵塞流纹(FLOW LINES)塑料熔融不佳提高塑料温度;提高背压;加快螺杆转速模具温度过低提高模具温度注射速度太快或太慢调整适当注射速度注射压力太高或太低调整适当注射压力塑料不洁或掺有他料检查原料溢口过小产生内射纹加大溢口成品断面厚薄相关太多变更成品设计或溢口位置银纹、气疮(SILVER STREAKS)塑料含有水分塑料彻底烘干;提高背压塑料温度过高或模具过热降低原料温度,射嘴及前段温度塑料中其他添加物如润滑剂染料等之分解减少其使用量或更换耐温较高之代替品塑料中其他添加物混合不匀彻底混合均匀注射速度太快减慢注射速度模具温度太低提高模具温度塑料粒粗细不匀使用粒状均匀之原料料筒内夹有空气降低料筒后段温度;提高背压原料在模内流程不当调整溢口大小及位置使模具温度保持平均成品表面不光泽模具温度太低提高模具温度塑料剂量不够增加注射压力、速度、时间及剂量模内有过多脱模油擦拭干净模内表面有水擦拭并检查是否漏水模内表面不光模具打光成品变形(WARPING)成品顶出时尚未冷却降低模具温度;延长冷却时间;降低塑料温度成品形状及厚薄不对称脱模后以定型架固定;变更成型设计进料过多减少射出压力、速度、时间及剂量几个溢口进料不平均更改溢口顶出系统不平衡改善顶出系统模具温度不均匀调理模具温度近溢口部分原料太松或太紧增加或减少注射时间成品内有气孔(AIR BUBBLES)成品断面、肋或柱过厚变更成品设计或溢口位置注射压力太低提高注射压力注射时间不足增加注射时间浇道溢口太小加大浇道及入口注射速度太快调慢注射速度塑料含水分塑料彻底干燥塑料温度过高以致分解降低塑料温度模具温度不平均调整模具温度冷却时间太长减少模内冷却时间,使用水浴冷却水浴冷却过急减短水浴时间或提高水浴温度背压不够提高背压料筒温度不当降低喷嘴及前段温度,提高后段温度黑点(BLACK SPOTS)原料过热部分附着料筒管壁彻底空射;拆除料筒清理;降低塑料温度;减短加热时间塑料混有异物、纸屑等检查塑料;彻底空射射入模内时产生焦斑(BURNING MARK)降低注射压力及速度;降低塑料温度;加强模具排气孔;酌降合模压力;更改入口位置料筒内有使原料过热的死角检查喷嘴与料筒间接触面有无间隙或腐蚀现象必须考虑回收材料的材质硬度必须要和新料相同,最理想的回收是连续性粉碎、干燥、加工不使回收材料贮放太久,粉碎粒子尽量和新粒子接近,树脂经一再的回收,将降低成品的特性,制品有特殊性要求时,最好勿使用回收料。
注塑成型各种缺陷的现象及解决方法
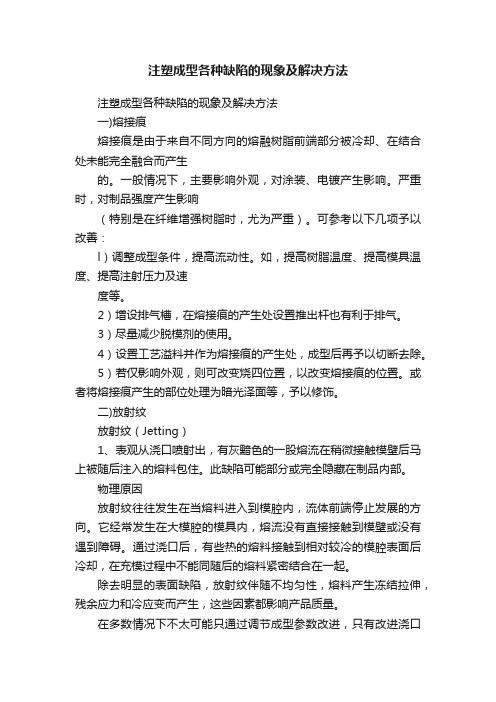
注塑成型各种缺陷的现象及解决方法注塑成型各种缺陷的现象及解决方法一)熔接痕熔接痕是由于来自不同方向的熔融树脂前端部分被冷却、在结合处未能完全融合而产生的。
一般情况下,主要影响外观,对涂装、电镀产生影响。
严重时,对制品强度产生影响(特别是在纤维增强树脂时,尤为严重)。
可参考以下几项予以改善:l)调整成型条件,提高流动性。
如,提高树脂温度、提高模具温度、提高注射压力及速度等。
2)增设排气槽,在熔接痕的产生处设置推出杆也有利于排气。
3)尽量减少脱模剂的使用。
4)设置工艺溢料并作为熔接痕的产生处,成型后再予以切断去除。
5)若仅影响外观,则可改变烧四位置,以改变熔接痕的位置。
或者将熔接痕产生的部位处理为暗光泽面等,予以修饰。
二)放射纹放射纹(Jetting)1、表观从浇口喷射出,有灰黯色的一股熔流在稍微接触模壁后马上被随后注入的熔料包住。
此缺陷可能部分或完全隐藏在制品内部。
物理原因放射纹往往发生在当熔料进入到模腔内,流体前端停止发展的方向。
它经常发生在大模腔的模具内,熔流没有直接接触到模壁或没有遇到障碍。
通过浇口后,有些热的熔料接触到相对较冷的模腔表面后冷却,在充模过程中不能同随后的熔料紧密结合在一起。
除去明显的表面缺陷,放射纹伴随不均匀性,熔料产生冻结拉伸,残余应力和冷应变而产生,这些因素都影响产品质量。
在多数情况下不太可能只通过调节成型参数改进,只有改进浇口位置和几何形状尺寸才可以避免。
与加工参数有关的原因与改良措施见下表:1、注射速度太快降低注射速度2、注射速度单级采用多级注射速度:慢-快3、熔料温度太低提高料筒温度(对热敏性材料只在计量区)。
增加低螺杆背压与设计有关的原因与改良措施见下表:1、浇口和模壁之间过渡不好提供圆弧过渡2、浇口太小增加浇口3、浇口位于截面厚度的中心浇口重定位,采用障碍注射、工艺溢料是指用手工在模具上開一條深一些的排气槽,在生產時此槽產生出來的(批峰),又叫工藝批峰,主要是用來改善燒膠或熔接痕,可將燒膠或熔接痕調整到此批峰上,生產后將其切除。
注塑缺陷描述及解决方案

注塑缺陷描述及解决方案引言概述注塑是一种常见的塑料加工方法,但在生产过程中常常会出现一些缺陷,影响产品质量和生产效率。
本文将介绍注塑缺陷的常见描述和解决方案。
一、短射1.1 描述:短射是指注塑成型时,塑料材料未充满模具腔体,导致产品表面或内部出现缺陷。
1.2 原因:可能是注射压力不足、模具温度不稳定、料斗内塑料不足等。
1.3 解决方案:增加注射压力、调整模具温度、确保料斗内塑料充足等。
二、气泡2.1 描述:气泡是指产品表面或内部出现的气体孔洞,影响产品的外观和性能。
2.2 原因:可能是注塑过程中塑料材料中含有水分、注射速度过快、模具排气不畅等。
2.3 解决方案:使用干燥塑料材料、减慢注射速度、改进模具结构以提高排气效果等。
三、热缩3.1 描述:热缩是指产品在冷却后尺寸缩小,导致尺寸不稳定或变形。
3.2 原因:可能是模具温度不均匀、冷却时间不足、塑料材料热胀冷缩系数不匹配等。
3.3 解决方案:调整模具温度均匀性、延长冷却时间、选择合适的塑料材料等。
四、毛刺4.1 描述:毛刺是指产品表面出现的细小突起,影响产品的外观和手感。
4.2 原因:可能是模具间隙过大、注射速度过快、模具表面粗糙等。
4.3 解决方案:调整模具间隙、减慢注射速度、提高模具表面光洁度等。
五、色差5.1 描述:色差是指同一批次产品颜色不一致,影响产品的整体美观度。
5.2 原因:可能是塑料材料颜色不均匀、注射温度不稳定、色母添加不均匀等。
5.3 解决方案:使用均匀颜色的塑料材料、稳定注射温度、充分混合色母等。
结论通过对注塑缺陷的描述和解决方案的介绍,可以有效提高注塑产品的质量和生产效率。
在实际生产中,需要根据具体情况采取相应的措施,及时解决问题,确保产品质量和客户满意度。
注塑制品产生缺陷的原因及其处理方法
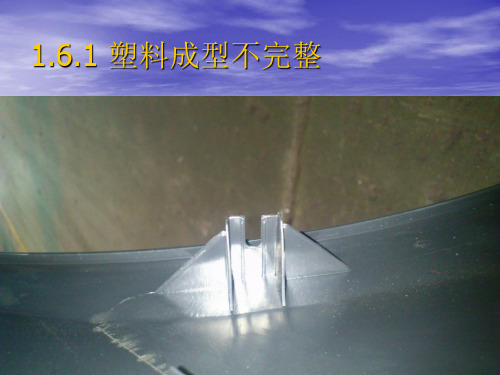
(3)模具的关键部位应有效地设置冷却水道。
(4)整个模具应不带毛刺且具有可靠的合模密 封性 。
三 工艺方面【凹痕】
(1)增加注射压力,保压压力,延长注射时间。
(2)提高注射速度可以较方便地使制件充满并 消除大部分的收缩。
(3)薄壁制件应提高模具温度,保证料流顺畅; 厚壁制件应减低模温以加速表皮的固化定型。
道入口配合不良,塑料炭化沉积物等堵塞; 喷嘴或主流道入口球面损伤、变形,影响 与对方的良好配合;
(4)塑料熔块堵塞加料通道这种情况只 有在凿通通道,排除料块后才能得到根本 解决。
(5)喷嘴冷料入模,应降低机筒前端和喷嘴的 温度以及减少机筒的储料量,减低背压压力避 免机筒前端熔料密度过大。
(6)注塑周期过短。由于周期短,料温来不及跟上 也会造成缺料。延长料粒在机筒内的预热时间。
总结处理方法
流道和螺杆料温太高,射出和储料速度太快, 背压太小,烘干不足,有混料,模温低,未打 保备方面【熔接痕】 塑化不良,熔体温度不均,可延长模塑周期。
二 模具方面【熔接痕】
(1)模具温度过低。 (2)流道细小、过狭或过浅,冷料井小。 (3)扩大或缩小浇口截面,改变浇口位置。 (4)排气不良或没有排气孔
三 工艺方面【飞边】
(1)注射压力过高或注射速度过快。由于高压 高速,对模具的张开力增大导致溢料。 (2)加料量过大造成飞边。值得注意的是不要 为了防止凹陷而注入过多的熔料,这样凹陷未 必能“填平”,而飞边却会出现。这种情况应 用延长注射时间或保压时间来解决。
(3)机筒、喷嘴温度太高或模具温度太高都会 使塑料黏度下降,流动性增大,在流畅进模的 情况下造成飞边。
(2)对流动性差或热敏性高的塑料适当添加润 滑剂及稳定剂,必要时改用流动性好的或耐热性 高的塑料。
注塑常见缺陷及解决方法

注塑常见缺陷及解决方法1. 引言在注塑过程中,由于材料、设备、工艺等多种因素的影响,常常会出现一些缺陷。
这些缺陷不仅会影响产品的质量,还可能导致产品性能下降甚至无法使用。
因此,了解注塑常见缺陷及其解决方法对于提高产品质量至关重要。
2. 注塑常见缺陷2.1 短射短射是指注塑过程中,塑料无法充满模具腔体的情况。
造成短射的原因可能是模具设计不合理、注塑机参数设置不当等。
解决方法包括优化模具结构、增加注射压力等。
2.2 气泡气泡是注塑过程中常见的缺陷之一。
气泡的出现可能是由于塑料中含有气体、注塑过程中存在气体进入等原因。
解决方法包括在塑料中加入消泡剂、提高注射速度等。
2.3 热胀冷缩热胀冷缩是指注塑过程中,塑料在冷却过程中由于体积收缩而导致产生应力。
这种缺陷会导致产品变形、尺寸不稳定等问题。
解决方法包括优化模具结构、增加冷却时间等。
2.4 毛刺毛刺是指注塑制品表面出现的突起或凹陷。
毛刺的产生可能是由于模具表面不光滑、注塑过程中存在杂质等原因。
解决方法包括优化模具表面处理、提高注射速度等。
3. 注塑常见缺陷的解决方法3.1 优化模具结构优化模具结构是解决注塑常见缺陷的重要方法之一。
通过对模具的设计进行改进,可以减少短射、热胀冷缩等缺陷的发生。
3.2 控制注射参数注塑过程中的注射参数设置对于产品质量至关重要。
合理的注射压力、注射速度等参数可以有效地解决短射、气泡等缺陷。
3.3 加入添加剂在注塑过程中,可以加入一些添加剂来改善产品的性能。
例如,在塑料中加入消泡剂可以有效地解决气泡缺陷。
3.4 提高冷却时间热胀冷缩是注塑过程中常见的缺陷之一。
通过增加冷却时间,可以使塑料充分冷却,减少热胀冷缩导致的尺寸变化。
4. 结论注塑过程中常见的缺陷包括短射、气泡、热胀冷缩、毛刺等。
通过优化模具结构、控制注射参数、加入添加剂、提高冷却时间等方法,可以有效地解决这些缺陷,提高产品质量。
在实际生产中,需要根据具体情况选择合适的解决方法,并进行不断的改进和优化,以提高注塑产品的质量和竞争力。
注射成型塑件常见缺陷问题及改善措施

摘要:本文主要阐述了在注射成型塑料制品时,主要会存在哪些常见的缺陷,同时说明了可以采取怎样的方法处理这些问题。
关键词:缺陷解决方法注射塑件塑料是以树脂为主要成分的高分子化合物,它是我们在生活中常用的三大合成材料之一。
具体来说,它是以合成树脂为主要成分加入各种一定比例的添加剂,在一定的压力和温度作用下,制成各种形状和性能的产品,并且在常温下保持形状不变的材料。
相较于其他材料的制品,塑料制品具有重量轻、比强度高等优点,在人民生活中得到广泛应用,现在各大商场超市随处可见用塑料制成的产品,平且在一些对于产品性能要求较高的场合也可以选用一些改性的塑料制品,并且现在大有“以塑代钢”的趋势。
塑料工业在当今世界上占有极为重要的地位。
从《2013-2017年中国塑料制品行业产销需求与投资预测分析报告》数据统计,我国塑料制品产量在世界排名中始终位于前列,其中多种塑料制品产量已经位于全球首位,我国已经成为世界塑料制品生产大国。
2001-2010年我国塑料制品产量年均增幅维持在15%以上,2010年我国塑料制品总产量达到5830万吨。
而在成型这些塑料制品时,根据每种产品的不同性能要求和使用环境,就要求我们要严格其成型工艺,对于在日常生活中常用的一些制品,我们必须严格控制制品的表面质量,因此在这里我们就几种常见的塑件表面质量做一下分析。
1充填不足(缺料)充填不足主要是指熔融塑料不能充满整个型腔所产生的缺料现象。
可能产生的原因及解决方法:①要成型塑件的体积过大。
解决方案:更换注塑机,选择成型能力大的成型设备。
②流道或者浇口的尺寸太小。
解决方案:将流道、浇口的尺寸扩大;加快注射速度、增大注射压力。
③熔融塑料在型腔中的流程太长。
解决方案:在此我们就要想办法提高材料的流动性,使其尽快的充满型腔。
如:升高模具温度,加快注射速度、增大注射压力。
④排气效果不佳。
解决方案:不能只是依靠分型面或者一些配合间隙排气,需要专门设置排气装置;改变浇口位置,增强原来排气系统的排气效果;在产品质量允许的情况下,调整产品的厚度。
注射成型塑料制品常见缺陷及其解决方案

注射成型塑料制品常见缺陷及其解决方案摘要:对塑料制品在注射成型过程中常见缺陷的产生进行了分析,阐述了影响塑件注射成型质量的几种主要因素。
从成型工艺控制、模具及塑件结构设计等角度,探讨了各方面条件对成型缺陷的影响程度,提出了防止质量缺陷产生,获得优良注塑件的措施。
关键词:注射成型;缺陷;解决方法1引言塑料制品广泛用于家用电器、玩具和汽车等各个领域,其生产以注射成型为主。
但在成型过程中,由于受材料、模具、成型设备等多种因素的影响,制品的质量经常会出现各种各样的缺陷。
理解质量缺陷形成的过程和原因,掌握消除制品缺陷的方法对实际生产具有非常重要的作用。
现列举几种常见的缺陷作以扼要分析论述。
2常见塑件缺陷及预防措施2.1飞边现象:当塑料熔料被迫从分型面挤压出模具型腔而产生薄片时便形成了飞边,又称溢边、披锋、毛刺等,如图1所示。
(1)模具缺陷。
这是产生溢料飞边的主要原因。
必须认真检查模具分型面是否贴合,是否有缝隙或损伤。
特别是在大型成型品的情况下,模具一般都会发生变形,此时,有无支柱对飞边也有影响。
如果没有支柱,变形缝隙就会增大,飞边也会增多。
(2)合模力不足。
应检查合模力设定值,加大合模力,或考虑减少型腔数及改用合模吨位大的注塑机。
(3)熔料过热。
应适当降低料筒温度、喷嘴及模具温度,加快树脂固化,这样飞边就不容易出现。
同时,应选用流动性稍低的原料,否则树脂流动性越好,树脂就越容易进入缝隙,因此飞边也就越大。
(4)工艺条件控制不当。
必须做到①延缓注射速度;②降低注射压力。
2.2熔接痕现象:由于来自不同方向的熔融树脂前端部分被冷却、在结合处未能完全融合,如图2所示。
一般情况下主要影响制品的外观,严重时对制品强度产生影响。
主要原因及解决方法:(1)注射压力太小或注射速度慢。
必须提高注射速率,增加注射压力,使熔料在高压下快速充模,以达到良好的自然熔合。
(2)料温或模温太低。
低温熔料的分流汇合性能较差,容易形成熔接痕。
热塑性塑料注射成型制品缺陷及产生的原因

12.制品翘曲变形
1.模具温度太高,冷却时间不够 2.制品厚薄悬殊 3.浇口位置不当,数量不够 4.顶出位置不当,受力不均 5.塑料大分子定向作用太大
13.制件分层脱皮
1.不同塑料混杂 2.同一种塑料不同级别相混 3.塑化不均匀 4.原料污染或混入异物
14.制品褪色 15.制品强度下降
1.塑料污染或干燥不够 2.螺杆转速太快,背压太高 3.注射压力太大 4.注射速度太快 5.注射保压时间太长 6.料筒温度过高,致使塑料、着色剂或添加剂分解 7.流道、浇口尺寸不合适 8.模具排气不良
4.管壁厚度不均 5.管材口径不圆
1.芯棒和模套定位不正 2.口模各点温度不均 3.牵引位置偏离挤出机的轴线
1.定型套口径不圆 2.牵引前部的冷却不足
1.校正其相对位置 2.校正温度 3.校正牵引的位置
1.掉换或改正定型套 2.校正冷却系统或放慢挤出速度
6.管材口径大小不同 7.制品带有杂质
1.挤出温度有波动 2.牵引速度不均
1.塑料干燥不良、含有水分、单体、溶剂和 挥发性气体 2.塑料有分解物 3.注射速度太快 4.注射压力太小 5.模温太低、充模不完全 6.模具排气不良 7.从加料端带入空气
1.加料量不足 2.料温太高 3.制品壁厚或壁薄相差大 4.注射及保压时间太短 5.注射压力不够 6.注射速度太快 7.浇口位置不当
1.滤网破损或滤网不够细 2.塑料发生降解 3.用料中加入的再生料太多
1.控制温度恒定 2.检查牵引装置,使达到平衡
1.掉换滤网 2.校正各段温度 3.降低再生料的比例
解决措施
1.干燥塑料 2.适当提高温度 3.清理机头与口模 4.降低螺杆转速
2.制品带有焦粒或变色
1.挤压温度过高 2.机头与口模内部不洁净或有死角
注塑制品产生缺陷的原因及其处理方法(已整理)

注塑制品产生缺陷的原因及其处理方法在注塑成型加工过程中可能由于原料处理不好、制品或模具设计不合理、技术人员没有掌握合适的工艺操作条件,或者因机械方面的原因,常常使制品产生注不满、凹陷、飞边、气泡、裂纹、翘曲变形、尺寸变化等缺陷。
对塑料制品的评价主要有三个方面,第一是外观质量,包括完整性、颜色、光泽等;第二是尺寸和相对位置间的准确性;第三是与用途相应的机械性能、化学性能、电性能等。
这些质量要求又根据制品使用场合的不同,要求的尺度也不同。
生产实践证明,制品的缺陷主要在于模具的设计、制造精度和磨损程度,工艺调整和操作不当,设备的机械故障,材料的选用和处理不当等多方面引起的,所以在生产中应客观的分析缺陷的真正原因。
生产过程中工艺的调整是提高制品质量和产量的必要途径。
在调整工艺时最好一次只改变一个条件,多观察几回,如果压力、温度、时间统统一起调的话,很易造成混乱和误解,出了问题也不知道是何道理。
调整工艺的措施、手段是多方面的。
例如:解决制品注不满的问题就有十多个可能的解决途径,要选择出解决问题症结的一、二个主要方案,找到问题的真正原因,才能有效的解决问题。
此外,还应注意解决方案中的辨证关系。
比如:制品出现了凹陷,有时要提高料温,有时要降低料温;有时要增加料量,有时要减少料量。
要承认逆向措施的解决问题的可行性。
注塑制品的翘曲变形分析翘曲变形是指注塑制品的形状偏离了模具型腔的形状,它是塑料制品常见的缺陷之一。
随着塑料工业的发展,人们对塑料制品的外观和使用性能要求越来越高,翘曲变形程度作为评定产品质量的重要指标之一也越来越多地受到模具设计者的关注与重视。
模具设计者希望在设计阶段预测出塑料件可能产生翘曲的原因,以便加以优化设计,从而提高注塑生产的效率和质量,缩短模具设计周期,降低成本。
一、模具的结构对注塑制品翘曲变形的影响在模具设计方面,影响塑件变形的因素主要有浇注系统、冷却系统与顶出系统等。
(1)浇注系统的设计注塑模具浇口的位置、形式和浇口的数量将影响塑料在模具型腔内的填充状态,从而导致塑件产生变形。
注塑工艺 注塑成型缺陷分析及不良解决对策
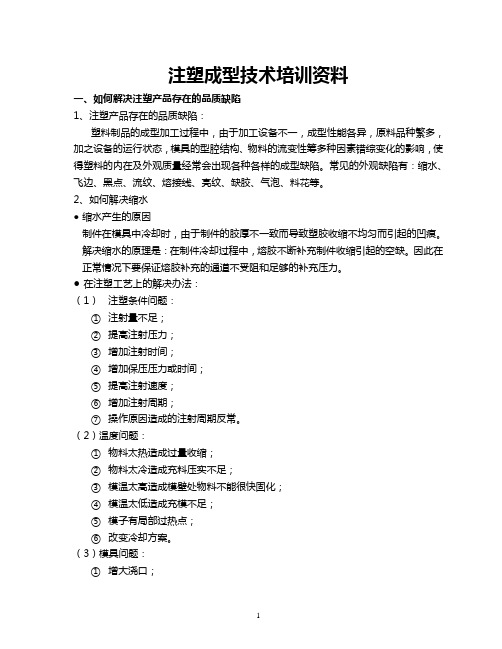
注塑成型技术培训资料一、如何解决注塑产品存在的品质缺陷1、注塑产品存在的品质缺陷:塑料制品的成型加工过程中,由于加工设备不一,成型性能各异,原料品种繁多,加之设备的运行状态,模具的型腔结构、物料的流变性筹多种因素错综变化的影响,使得塑料的内在及外观质量经常会出现各种各样的成型缺陷。
常见的外观缺陷有:缩水、飞边、黑点、流纹、熔接线、亮纹、缺胶、气泡、料花等。
2、如何解决缩水●缩水产生的原因制件在模具中冷却时,由于制件的胶厚不一致而导致塑胶收缩不均匀而引起的凹痕。
解决缩水的原理是:在制件冷却过程中,熔胶不断补充制件收缩引起的空缺。
因此在正常情况下要保证熔胶补充的通道不受阻和足够的补充压力。
●在注塑工艺上的解决办法:(1)注塑条件问题:①注射量不足;②提高注射压力;③增加注射时间;④增加保压压力或时间;⑤提高注射速度;⑥增加注射周期;⑦操作原因造成的注射周期反常。
(2)温度问题:①物料太热造成过量收缩;②物料太冷造成充料压实不足;③模温太高造成模壁处物料不能很快固化;④模温太低造成充模不足;⑤模子有局部过热点;⑥改变冷却方案。
(3)模具问题:①增大浇口;②增大分流道;③增大主流道;④增大喷嘴孔;⑤改进模子排气;⑥平衡充模速率;⑦避免充模料流中断;⑧浇口进料安排在制品厚壁部位;⑨如果有可能,减少制品壁厚差异;⑩模子造成的注射周期反常。
(4)设备问题:①增大注压机的塑化容量;②使注射周期正常;(5)冷却条件问题:①部件在模内冷却过长,避免由外往里收缩,缩短模子冷却时间;②将制件在热水中冷却。
3、如何解决飞边●产生飞边的原因:产品溢边往往由于模子的缺陷造成,其他原因有:注射力大于锁模力、物料温度太高、排气不足、加料过量、模子上沾有异物等。
●如何判断产生飞边的原因:在一般情况下,采用短射的办法。
即在注塑压力速度较低、不用保压的情况下注塑出制件90%的样板,检查样板是否出现飞边,如果出现,则是模具没有配好或注塑机的锁模压力不足,如果没有出现,则是由于注塑条件变化而引起的飞边,比如:保压太大、注射速度太快等。
热塑性塑料注塑成型制品的常见缺陷及可能产生的原因
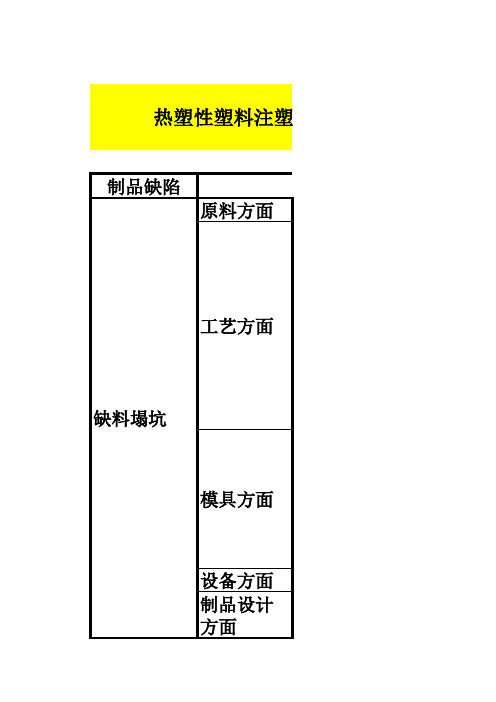
模腔表面光洁度不够,脱模斜度不够、嵌块缝太 大 模具温度过高或过低(过高引起原料降解,过低 带进气体) 模具排气性能不佳 原料收缩率过大 加料量不足 料温过高 注射及保压时间太短 注射压力不足 注射速度过慢,塑胶熔体补缩不足。 脱模时制件过热 流道或浇口尺寸太小、浇口位置不当 模具排气性能不佳
制件壁太厚或壁厚差异太大
原料颗粒不均,新旧料混合比例不当 加料量不稳 料筒和喷嘴温度过高 注射压力低或注射速度慢 冲模时间、保压时间不足 模温不均 成型周期不一致 浇口、流道尺寸不均 模具尺寸不准确 模具定位杆弯曲或磨损 注射机的传感系统不稳定 模温太高 模温不均 脱模是制件温度过高 浇口位置不当、数量不够 顶出杆位置不当 制品厚薄悬殊过大 顶出时制件受力不均 制品中的大分子定向程度太高 脱模剂不均或无效 注射压力太高、注射时间太长 模具温度不合适 卸压太早 浇口尺寸太大或位置、数量不合理
模具方面
设备方面
工艺方面
制品翘曲变 形
模具方面
制品设计 方面
原料方面
工艺方面
制品粘模 模具方面
制品粘模 模具方面
原料方面
制件凹陷 (缩印)
工艺方面
模具方面
制品设计 方面 原料方面
工艺方面 熔接痕、气 纹
模具方面
纹 模具方面
工艺方面 喷纹、蛇纹
模具方面 原料方面
制品表面有 工艺方面 银丝或波纹
模具方面
模具方面
表面光泽不 工艺方面
良
原材料方
面
模具方面 透明度不足 工艺方面
原料方面 工艺方面 制品有冷料 斑、流痕 模具方面
设备方面
原料方面
色差、变色 工艺方面
原料方面
黑条
工艺方面
注塑成型缺陷产生机理及解决办法

注塑成型缺陷产生机理及解决办法概述注塑成型加工过程中是一个涉及模具设计、模具制造、原材料特性和原材料预处理方法、成型工艺、注塑机操作等多方面因素,并与加工环境条件、制品冷却时间、后处理工艺密切相关的复杂加工流程。
因此,制品质量的好环就不单取决于注塑机的注塑精度、计量精度,或是仅仅由模具设计的优劣和模具加工的精度级别决定,通常,它还会受到上述的其他因素的影响和制约。
在如此众多的复合因子约束下,注塑成型制品的缺陷的出现就在所难免,于是,寻求缺陷产生的内在机理以及预测制品可能产生缺陷的位置和种类,并用于指导模具设计和改进、归纳缺陷产生的规律、制订更为合理的工艺操作条件就显得尤为重要。
我们将从影响注塑成型加工过程中的塑料材料特性、模具结构、注塑成型工艺及注塑设备三个主要因素来阐述注塑成型缺陷产生机理及解决办法。
注塑成型制品常见缺陷分类注塑成型加工过程中所用的塑料原料多种多样,模具设计的种类和形式也是五花八门,另外,操作工人对于特定注塑机的熟悉程度以及工人之间的操作技能,实践经验的差异也各不相同,同时,客观环境(如环境温度、湿度、空气洁净程度)也会随着季节变化而不同,这些客观和主观条件共同决定了注塑成型制品缺陷的产生。
一般来说,对于塑料制品性能优劣的评价主要有三个方面:第一、外观质量,包括完整性、颜色、光泽;第二、尺寸和相对位置间的准确性,即尺寸精度和位置精度;第三、与用途相应的力学性能、化学性能、电学性能等,即功能性因而,如果由于上述三个方面中的任何一个环节出现问题,就会导致制品缺陷的产生和扩展。
注塑成型制品常见缺陷分类外观缺陷:•银纹-银纹(Silver Streaks)-缺陷分析及排除方法•变色•熔接痕工艺问题:•飞边性能问题:•翘曲•脆化欠注(Short Shot)-缺陷分析及排除方法什么是欠注(Short Shot)?欠注又叫短射、充填不足、制件不满,俗称欠注,指料流末端出现部分不完整现象或一模多腔中一部分填充不满,特别是薄壁区或流动路径的末端区域。
- 1、下载文档前请自行甄别文档内容的完整性,平台不提供额外的编辑、内容补充、找答案等附加服务。
- 2、"仅部分预览"的文档,不可在线预览部分如存在完整性等问题,可反馈申请退款(可完整预览的文档不适用该条件!)。
- 3、如文档侵犯您的权益,请联系客服反馈,我们会尽快为您处理(人工客服工作时间:9:00-18:30)。
page 2
正模具的 设计了.其中,最重要的是应注意使 制品壁厚一致.有时,在不得已的情 况下 ,只好通过测量制品的变形,按 相反的方向修整模具,加以校正.故 要求技术工人必须 清楚地知道材料自 身的变形性能.如,收缩率较大的树 脂,一般是结晶性树脂(如聚甲 醛, 尼龙,聚丙烯,聚乙烯及PET树脂等) 比非结晶性树脂(如PMMA树脂,聚氯乙 烯,聚苯 乙烯,ABS树脂及AS树脂等) 的变形大;另外,由于玻璃纤维增强树 脂具有纤维配向性, 变形也变大. 致;(4)定时对注射机的电气,液压 系统进行检修. 白化 白化现象最主要发生在ABS树脂制 品的推出部分,脱模效果不佳是其主 要原因. 可采用降低注射压力,加大 脱模斜度,增加推杆的数量或面积, 减小模具表面粗糙度值 等方法改善, 当然,喷脱模剂也是一种方法,但应 注意不要对后续工序,如烫印,涂装 等产生不良影响. 结 语 通过对热塑性塑料在注射成型过 程中常见缺陷及其产生原因的分析, 我们可以 清楚的知道,对于制品的某 一缺陷有可能是多方面因素综合影 响,我们应当对存在的 问题逐一查找 其原因并耐心纠正;特别是在调整工 艺时,最好一次只改变一个条件,假 如把时间,温度,压力一起调节,则 容易造成混乱和误解. 制品的尺寸不稳定 造成制品尺寸不稳定的因素主要 有: (1)加料量不稳定;(2)塑料 的颗粒大小不 均匀;(3)料筒和喷嘴 的温度太高;(4)注射压力太小; (5)充模和保压的时间不够;(6) 浇 口和流道的尺寸不恰当;(7)模具的设 计尺寸不恰当;(8)模具的设计尺寸不 准确; (9)推杆变形或磨损;(10)注 射机的电气,液压系统不稳定. 解决制品尺寸不稳定现象 ,我们 可以采用如下的方法: (1)控制或调节加料均匀; (2)使用颗粒大小均一的塑料 ,合理 控制混合比例;(3)合理调节温度, 压力,时间,控制型腔各处基本一 廖晓明:男 ,广东河源人,助理 讲师,学士,研究方向为材料成型技 术. 河源职业技术学院 邮编 517000 参考文献 1.黄锐,曾邦禄.塑料成型工艺学[M].北京:中 国轻工业出版社,1997 2.屈华昌. 塑料成型工艺与模具设计[M].北 京:机械工业出版社,1996 3.吴培熙,王组玉,景志坤 .塑料制品生产工 艺手册[M].北京:化学工业出版社,1998 制品翘曲,变形 造成制品发生翘曲,变形的因素 主要有: (1)模具温度太高,冷却时间不 够;(2) 制品厚薄悬殊;(3)浇口 位置不恰当,浇口数量不合适;(4) 推出位置不恰当,且受力不 均;(5) 塑料分子定向作用太大 . 注射制品的翘曲,变形是很棘手 的问题,主要应从模 具设计方面着手 解决,而成型条件的调整效果则是很 有限的.可根据影响因素相应确 定翘 曲,变形的解决方法: (1)由成型条件引起残余应力 造成翘曲,变形时,可通过降 低注射 120 塑料制造 PLASTICS MANUFACTURE 2008年3月刊
本文由hasens33贡献 pdf文档可能在WAP端浏览体验不佳。建议您优先选择TXT,或下载源文件到本机 查看。 故障生成与解决Source and Solution of Problems 编者按:从提出问题,分析原因到给予解决方法,去解决生产中的问 题,可谓考虑 周全. 热塑性塑料注射成型时常见 DEFECTS OCCURING IN THE PRODUCTION OF THERMOPLASTIC BY INJECTION MOLD ING AND THEIR SOLUTIONS 缺陷,产生原因及解决措施 文/廖晓明 塑 摘 要:本文介绍了热塑性塑料在注射成型中最为常见的缺 陷,分析了可能产生缺 陷的各种原因,并从改进模具结构,成型 工艺过程控制(包括温度,压力,时间等) 以及 对原料进行预干 燥处理等方面,提出了相关的解决措施. 关键词:热塑性塑料 解决措 施 Abtracts: Various defects may occur in the production of thermoplastic by injection molding,and reasons caused these defects are analyed .Solutio ns by optimizing mold structure, adjusting the condition during shaping pr ocess(including temperature ,pressure, time ,etc.)and pretreating material are put forward. Keywords: Thermoplastic Reason Solution Injection moldin g Product defect 注射成型 制品缺陷 产生原因 料制件在工业中的应用日趋普遍,已成为各 行各业不可或缺的重要材料之一.其 成型 方法有很多:注射成型,压缩成型,压注成 型,挤出成型,气动成型与液压成型,泡沫塑料成型等, 注射成型是塑料制件生产 中最常用的方法之一,主要用于 热塑性塑料的成型,到目前为止,除氟塑料外,几乎所有 的热塑性塑料都可以采用此法成型.为了使热塑性塑料在 注射 成 型 时 获 得 更 好 的 性 能 , 本 文 将 对 热 塑 性 塑 料 在 注射成型中常出现的缺陷及其产生 原因,解决方法作 如下分析. 塑性塑料注射成型缺陷原因分析 在注射成型加工过程中可能由于原料的处理不好, 制品或模具设计不合理,操作 工没有掌握合适的工艺操作 118 塑料制造 PLASTICS MANUFACTURE 2008年3月刊 pingfanmedia 条件,或者因机械方面的原因,常常 使制品产生充填不满,凹陷,飞边, 气泡,尺寸 变化等缺陷.这些制品缺 陷产生的原因主要在于模具设计,制 造精度和磨损等方面,而 生产过程中 成型工艺调节不当也是影响制品质量 和产量的因素之一,由于注射周期很 短,如果工艺条件掌握不好,废品就 会源源不绝. 制品有溢边 产生溢边的主要原因有: (1)料筒,喷嘴及模具温度太 高;(2)注射压力太大,锁模 力太小; (3)模具密合不严,有杂物或模板已变 形;(4)型腔排气不良;(5)塑料的 流动 性太好;(6)加料量过大 . 对于溢边的处理重点应主要放在 模具的改善方面.而在成型 条件上, 则可在降低流动性方面着手.具体可 采用以下几种方法: (1)降低注射压力; (2)降低 树脂温度;(3)选用高粘度等级的材 料;(4)降低模具温度;(5)研磨溢 边发生 的模具面;(6)采用较硬的模 具钢材;(7)提高锁模力;(8)调整 准确模具的结合面等部 位;(9)增加 模具支撑柱,以增加刚性;(10)根据 不同材料确定不同排气槽的尺寸. 融粘度等级高的材料. (2)由于挥发性气体的产生而造 成的气泡,解决的方法主 要有: ① 对材料进行充分地干燥预热; ② 降低树脂温度,避免产生分解气 体. (3)由 于流动性差造成的气泡, 可通过提高树脂及模具的温度,提高 注射速度等方式予以解 决. 常见的制品缺陷及其解 决方法 制品填充不足