不良品出库流程图
制程不良品处理流程图
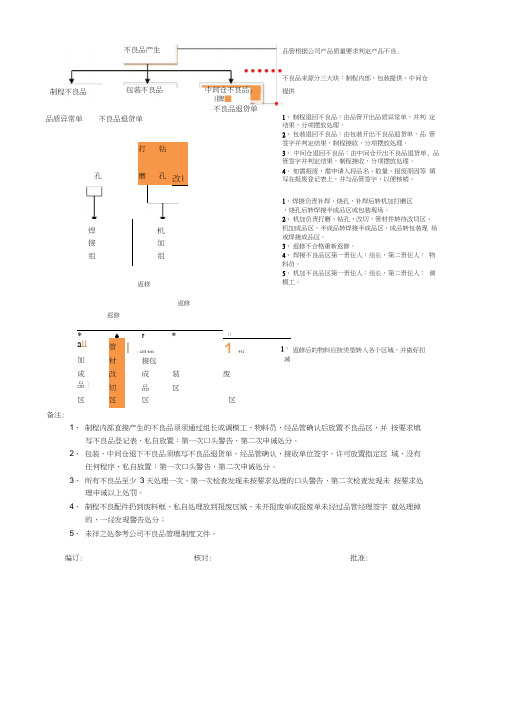
品管根据公司产品质量要求判定产品不良.
包装不良品
制程不良品
不良品退货单
品质异常单
孔
打
磨
钻
孔
改|
焊
机
接
加
组
组
返修
中间仓不良品
|牌■
不良品退货单
不良品来源分三大块:制程内部、包装提供、中间仓
提供
1、制程退回不良品:由品管开出品质异常单,并判 定结果,分项摆放处理。
2、包装退回不良品:由包装开出不良品退货单,品 管签字并判定结果,制程接收,分项摆放处理。
3、中间仓退回不良品:由中间仓开出不良品退货单, 品管签字并判定结果,制程接收,分项摆放处理。
4、如需报废,需申请人将品名、数量、报废原因等 填写在报废登记表上,并与品管签字,以便核销。1、焊接负补焊、烧孔,补焊后转机加打磨区
,烧孔后转焊接半成品区或包装现场。
2、机加负责打磨、钻孔,改切,管材件转待改切区、 机加成品区,半成品转焊接半成品区,成品转包装现 场或焊接成品区。
3、返修不合格重新返修。
4、焊接不良品区第一责任人:组长,第二责任人: 物料员。
5、机加不良品区第一责任人:组长,第二责任人: 调模工。
不良品处理流程图
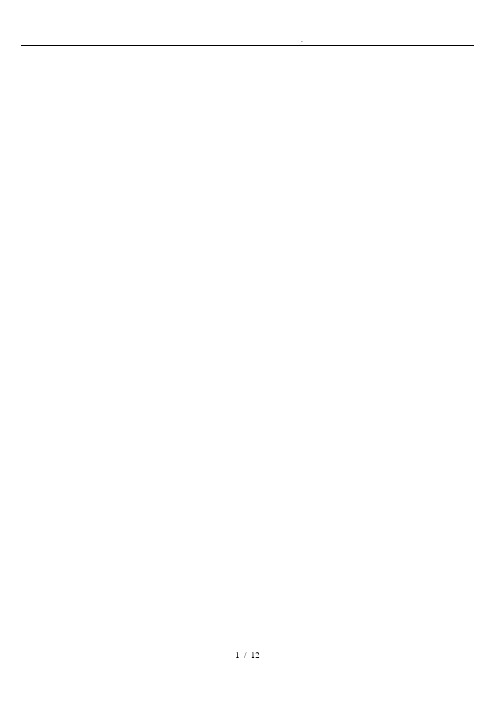
5.10.4IQC收到退料单,在没有急料的情况下须在2个工作小时全检〔在IQC现有设备可完成确
认〕,在全检过程中如检验到制程不良、包装方式不符、标识错误、误判、标识不清晰〔料
号、供给商〔客户〕、数量、不良标识、不良容、不良率〕、拉长/IPQC未签名确认等,
市XXXX
〔三级文件〕
文件名称:不良品处理流程
文件编号:CT-QC-XXXX版 本/次:B/1
制/修日期:2013年7月29日生效日期:2013年7月29
文件会签部门
会 签 人
文件会签部门
会 签 人
□人资部
■电源部
□品管部
□技术部
□市场部
□财务部
■单板生产部
□采购部
■整机生产部
□后勤部
■SMT部
□货仓部
5.9.2每天QC 日报表记录的不良总数量与维修工站的维修日报表统计数量相符。品管IPQC每天稽查此项容。如不相符计缺失项并追踪改善。
5.10 不良品退仓
5.10.1产线在每个投产工位,在上线时挑出的原材料不良,放置规定区域,IPQC与拉长在物料员开单退料前,针对原材料不良全检确认并做好标识,在退料单上签名。
注:所有测试发现的不良品,不可进展第二次测试。
5.2.4外观检验工站发现产品不良现象,用红色箭头标或美纹纸对不良部位进展标识,然后将不良品放入不良区域,并立即在QC 日报表作好相应记录。
5.2.5当检验连续3PCS不良时,应与时反应拉长&IPQC。
5.2.6各工序作业员不可私自维修不良品。
市XXXX
2.适用围:
适用于公司制程不良品、OQC验出不良品和客户检出不良品与不良品维修管制。
不良品分析流程图
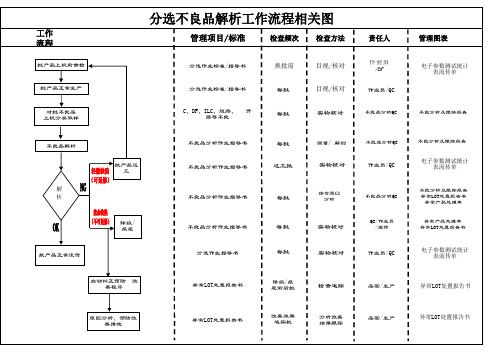
工作流程相关图
批产品上机前首检
管理项目/标准
检查频次
检查方法
责任人
管理图表
分选作业标准/指导书
换批前
目视/核对
作业员/QC
电子参数测试统计
批产品正常生产
分选作业标准/指导书
每批
目视/核对
作业员/QC
对批不良品 上机分类取样
C、DF、ILC、短路、
开
每批
实物核对
不良品分析QC
不良分析及跟踪报告
不良品解析 批产品返 工 解 析
不良品分析作业指导书
每批
返工批
测量/ 解剖
不良品分析QC
不良分析及跟踪报告
不良品分析作业指导书
实物核对
作业员/QC
电子参数测试统计
不良品分析作业指导书
每批
综合原因
不良品分析QC
不良分析及跟踪报告 异常LOT处置报告书 异常产品处理单 异常产品处理单 异常LOT处置报告书
降级/ 报废
不良品分析作业指导书
每批
实物核对
QC/作业员
批产品正常流传
分选作业指导书
每批
实物核对
作业员/QC
电子参数测试统计
启动纠正预防 改
异常LOT处置报告书
降级/报
检查追踪ቤተ መጻሕፍቲ ባይዱ
品管/生产
异常LOT处置报告书
原因分析、预防改 善措施
异常LOT处置报告书
改善效果
分析改善 结果跟踪
品管/生产
异常LOT处置报告书
不良品处理流程图

⑤记录日报表 上交报表
返修品集 中一并标 识好,经 过品管 IPQC 全 检确认OK 后重新上 线从第1 站向后工 序流入生 产 所有返修 品砍头后 的料件必 须测量产 品长度。
审核:
编制:阳勤 2016/10/7
不良品处理流程图
维修
②放入到红色胶筐 或不良返修区
不良品发生
①确认(判定)
时间 ①外观检查时 ②外观检查后 ③修正后 ④作业完了后 ⑤作业完了后
责任人 IPQC、检验员 生产主管 IPQC 作业员
报废
②放入到红箱或指定区域
进行维修
④到指定的区域进行废弃
③确认(判 定)
注意事 项:
所有不良 都标识示 出来或在 不良一端 打结,记 录时写上 作业员的 名字或者 编号,把 不良品放 入 红色胶筐 内并记录 在全检记 录表内。
不合格品控制程序及处理流程图
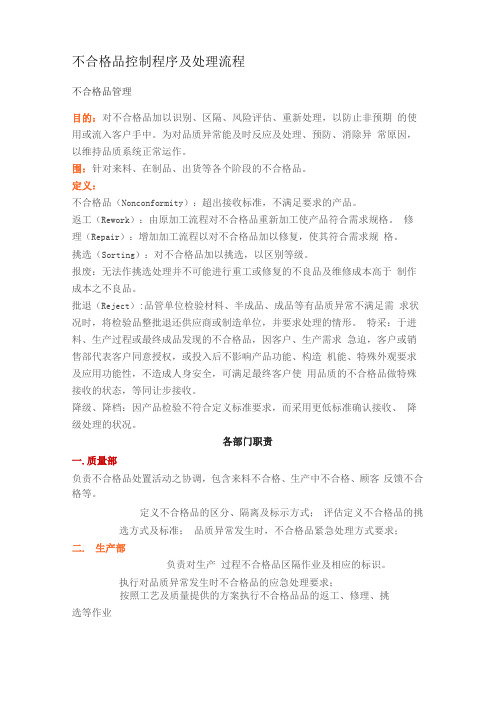
不合格品控制程序及处理流程不合格品管理目的:对不合格品加以识别、区隔、风险评估、重新处理,以防止非预期的使用或流入客户手中。
为对品质异常能及时反应及处理、预防、消除异常原因,以维持品质系统正常运作。
围:针对来料、在制品、出货等各个阶段的不合格品。
定义:不合格品(Nonconformity):超出接收标准,不满足要求的产品。
返工(Rework):由原加工流程对不合格品重新加工使产品符合需求规格。
修理(Repair):增加加工流程以对不合格品加以修复,使其符合需求规格。
挑选(Sorting):对不合格品加以挑选,以区别等级。
报废:无法作挑选处理并不可能进行重工或修复的不良品及维修成本高于制作成本之不良品。
批退(Reject):品管单位检验材料、半成品、成品等有品质异常不满足需求状况时,将检验品整批退还供应商或制造单位,并要求处理的情形。
特采:于进料、生产过程或最终成品发现的不合格品,因客户、生产需求急迫,客户或销售部代表客户同意授权,或投入后不影响产品功能、构造机能、特殊外观要求及应用功能性,不造成人身安全,可满足最终客户使用品质的不合格品做特殊接收的状态,等同让步接收。
降级、降档:因产品检验不符合定义标准要求,而采用更低标准确认接收、降级处理的状况。
各部门职责一.质量部负责不合格品处置活动之协调,包含来料不合格、生产中不合格、顾客反馈不合格等。
定义不合格品的区分、隔离及标示方式;评估定义不合格品的挑选方式及标准;品质异常发生时,不合格品紧急处理方式要求;二. 生产部负责对生产过程不合格品区隔作业及相应的标识。
执行对品质异常发生时不合格品的应急处理要求;按照工艺及质量提供的方案执行不合格品品的返工、修理、挑选等作业负责生产原因造成品质异常之分析与改善;三. 工艺部品质异常发生时之应急处理方案拟定。
对过程品质异常之分析与改善要求。
对修理、返工作业方式定义。
其他部门负责履行本部门的职责予以协助。
不合格品控制流程一. 进料品质异常控制质量部负责设计抽检方案,按照标准执行检验。
通用不良品处理流程图模板
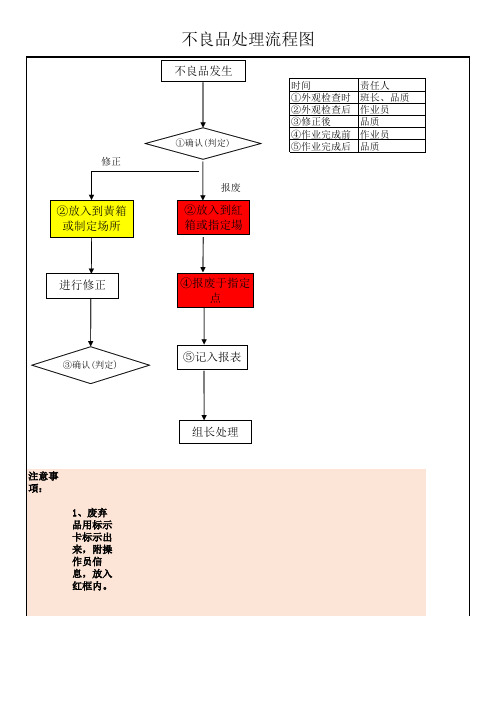
组长处理
2、返修 品/挑选 后用标示 卡标示出 来,放入 黄色胶框 内重新抽 检一遍。
3、机台 蓝色胶 框,产品 待检查。 绿色胶框 为待加工 (机加 工)待檢 查
編制/日 期:
審核/日 期:
修正
②放入到黃箱 或制定场所
不良品处理流程图
不良品发生
①确认(判定)
时间
责任人
①外观检查时 班长、品质
②外观检查后 作业员
③修正後
品质
④作业完成前 作业员
⑤作业完成后 品质
报废
②放入到紅 箱或指定場
进行修正
④报废于指定 点
③确认(判定)
⑤记入报表注意事 項:Fra bibliotek1、废弃 品用标示 卡标示出 来,附操 作员信 息,放入 红框内。
不合格品控制程序及处理流程图
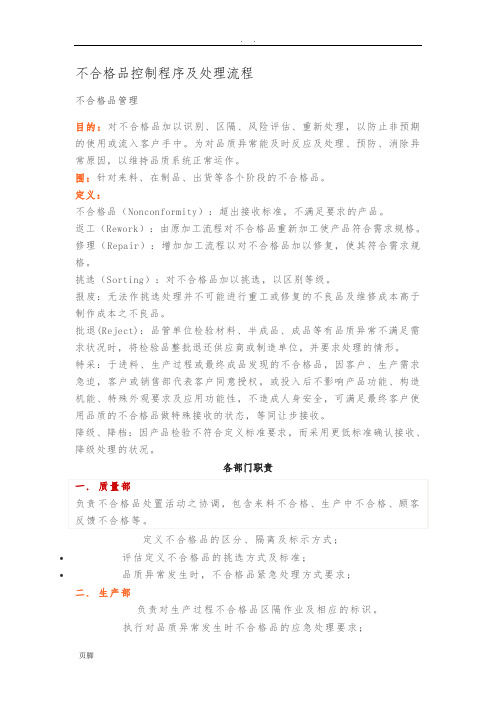
不合格品控制程序及处理流程不合格品管理目的:对不合格品加以识别、区隔、风险评估、重新处理,以防止非预期的使用或流入客户手中。
为对品质异常能及时反应及处理、预防、消除异常原因,以维持品质系统正常运作。
围:针对来料、在制品、出货等各个阶段的不合格品。
定义:不合格品(Nonconformity):超出接收标准,不满足要求的产品。
返工(Rework):由原加工流程对不合格品重新加工使产品符合需求规格。
修理(Repair):增加加工流程以对不合格品加以修复,使其符合需求规格。
挑选(Sorting):对不合格品加以挑选,以区别等级。
报废:无法作挑选处理并不可能进行重工或修复的不良品及维修成本高于制作成本之不良品。
批退(Reject):品管单位检验材料、半成品、成品等有品质异常不满足需求状况时,将检验品整批退还供应商或制造单位,并要求处理的情形。
特采:于进料、生产过程或最终成品发现的不合格品,因客户、生产需求急迫,客户或销售部代表客户同意授权,或投入后不影响产品功能、构造机能、特殊外观要求及应用功能性,不造成人身安全,可满足最终客户使用品质的不合格品做特殊接收的状态,等同让步接收。
降级、降档:因产品检验不符合定义标准要求,而采用更低标准确认接收、降级处理的状况。
各部门职责定义不合格品的区分、隔离及标示方式;•评估定义不合格品的挑选方式及标准;•品质异常发生时,不合格品紧急处理方式要求;二. 生产部负责对生产过程不合格品区隔作业及相应的标识。
执行对品质异常发生时不合格品的应急处理要求;按照工艺及质量提供的方案执行不合格品品的返工、修理、挑选等作业负责生产原因造成品质异常之分析与改善;三. 工艺部品质异常发生时之应急处理方案拟定。
对过程品质异常之分析与改善要求。
对修理、返工作业方式定义。
其他部门负责履行本部门的职责予以协助。
不合格品控制流程一. 进料品质异常控制质量部负责设计抽检方案,按照标准执行检验。
进料品质如发现不合格时,贴不合格标签并依流程执行批退,并将异常反馈给采购部门进行沟通处理。
不合格品流程图

每次 每次 每次 每次
IQC 来料抽验的常规来料在 4 小时 内出结果,急料在 2 小时内出结果,特 急料在 0.5 小时内出结果;
制程检验 制程不合格品 加工包装 品管部/生产部
每次 每次 每次 每次
返 工
报 废
有品质异常时 , 品管部接单后的 4 小时内出结果,分析部门 2 小时,责任部 门 2 小时,原则上是先到现场解决问题, 再写单.
加工包装检验 加工包装不合格品
品管部/生产部
封箱全 检源自特 采返 修每次 每次
出货检验
出货检验不合格品
品管部/生产部
返
特 采
入
库
工
《品质异常处理及改善 对策报告》 《QA 抽验报告》 《特采申请单》
每次 每次
制定:杨礼胜
审核:
批准:
不合格品作业办法
主流程 责任单位或个 人 PMC 部 使用表单 《入库单》 每次 进料检验 作业步 骤 说明事项
原物料不合格品
品管部/采购部
生产制造
退 货
全 检
特 采
《来料送检报告》 《供应商改善通知单》 《特采申请单》 《QC 全检报告》 《不合格标签》 《IPQC 巡检报表》 《品质异常处理及改善 对策报告》 《报废申请单》 《QC 全检报告》 《修理报表》 《IPQC 巡检报表》 《QC 全检报告》 《修理报表》 《品质异常处理及改善 对策报告》
不合格品控制流程图
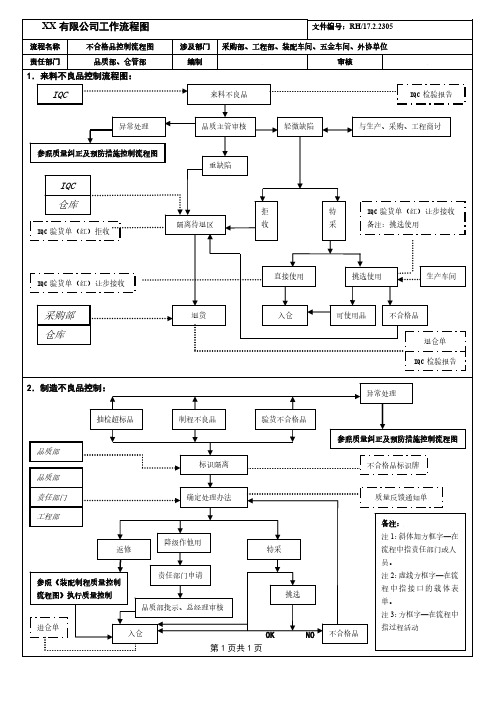
参照质量纠正及预防措施控制流程图 不合格品标识牌
责任部门
确定处理办法
质量反馈通知单
工程部
返修
降级作他用
特采
参照《装配制程质量控制 流程图》执行质量控制
责任部门申请 品质部批示、总经理审核
挑选
进仓单
入仓
OK
NO 不合格品
第 1 页共 1 页
备注: 注 1:斜体加方框字—在 流程中指责任部门或人 员。 注 2:虚线方框字—在流 程中指接口的载体表 单。 注 3:方框字—在流程中 指过程活动
XX 有限公司工作流程图
流程名称
不合格品控制流程图
责任部门
品质部、仓管部
1.来料不良品控制流程图:
IQC
文件编号:RH/17.2.2305
涉及部门 编制
采购部、工程部、装配车间、五金车间、外协单位 审核
来料不良品
IQC 检验报告
异常处理
品质主管审核
轻微缺陷
参照质量纠正及预防措施控制流程图
重缺陷
IQC
仓库
IQC 验货单(红)拒收
拒
特
隔离待退区
收
采
与生产、采购、工程商讨
IQC 验货单(红)让步接收 备注:挑选使用
IQC 验货单(红)让步接收
直接使用
挑选使用
生产车间
采购部 仓库
退货
入仓
可使用品
不合格品 退仓单
IQC 检验报告
2.制造不良品控制:
异常处理
抽检超标品
制程不良品
验货不合格品
品质部 品质部
标识隔离
不良品仓出入库作业规范流程图

单据复核
1.
1. 2. 3
在 ERP 系统中打印出来《进销存帐》明细上找到对应《物资收发卡》核对双 方的进出存帐是否一致。 先系统帐与物资卡双方的帐目核对,然后系统帐上结存数与实物结存数进行 确认。 如果发现帐物不符:重点确认发料有无多发和少发、丢失和被盗,其次确认 是否有先关单据未复核
仓库/仓管员
仓库/仓管员
减卡发料
1. 2.
领料单据及对应物料都核对清楚后,先在《物资收发卡》上面进行减卡改录: 单据号码、数量、结存数,减好卡后再进行实物的发料动作。 根据先进先出原则、先尾数后整数的发料原则进行发料作业。 所有发料单据统一由发料员在当天下班前自行确认复核完成并交与账务文 员整理归档。
出 料 确 仓库/仓管员 认
页码
1/1
不良品出入库作业流程图
部门
执行部门/人员 作业流程图
1. 收货入库
作业要求
仓管员在收到营销部开出《退货凭单》或产线开出的《退料单》后,仔细核 对实物的规格型号、数量,确认无误后进行签收,将不良品进行分类并将物 料摆放在相应的区域,如果型号及数量不符则要反馈给营销或入库员,要求 其处理。
客 退 品 仓库/仓管员 确 认 及 内 退 确 认 仓库/仓管员
库 存 处 仓库/仓管员 理
安全库存预警及呆 滞物料提报 2.
1.
各自仓库区域“7S”规化整理与维护。 物料的贮存及防护,具体操作见工程部《物料储存管理规定》文件。 管理程序》文件。
库 容 仓库/仓管员 整程中不同环节收、发、存、运输的控制与管理见《仓储 4. 对仓库内储存环境按照相关规定,保持库内合理干湿度,并做好温控记录。
登记入卡
1.
依照签收明细一一对应《物资收发卡》进行上卡记录:产品规格型号、数量、 结存数。
不合格品( HSF)处理流程图ppt课件

工厂内部出现环 境管理物质不合格
负责单位 品保/仓库/制造
库存品的处理
材料向供应商退货替代 合格品/成品直接报废
发生异常
原材料或部件中含 有禁止使用物质 异常连络书的发行
★报告品保部经理/总经理 ★与客户进行联络并报告 ★处理时需注意模向展开其 它料号与追踪上一批物料质 量状况
原因调查
工厂内部混入
纠正预防措施单的发行
ppt课件完整
5
4.0 权责
• 4.1 MRB﹙物料审查委员会﹚:负责不合格 品处理之审核,以决定不合格品之挑选、 返修、重工、退回供应商或予以裁定报废 或特采。
• 4.2不合格品发现/发生部门:负责对不合 格品做适当的识别、隔离及通知。
• 4.3品保:负责产品检验判定及标示区隔, 通知相关单位处置。
从客户反馈环境管理物质不合格信息工厂内部出现环境管理物质不合格供应商提供环境管理物质不合格材料报告品保部经理总经理与客户进行联络并报告处理时需注意模向展开其它料号与追踪上一批物料质量状况原因调查库存品的处理原材料或部件中含有禁止使用物质工厂内部混入异常工序纠正预防措施单的发行异常连络书的发行供应商材料向供应商退货替代合格品成品直接报废不合格对策处理确认会议库存品处理的确认防止再次发生的确认向其它部门或工序的水平推广模向展开标准化对策实施批量产品的进货出货发生异常品保仓库制造负责单位品保品保资料制造供应商业务品保仓库制造品保制造9ppt课件53重工作业流程图此流程不适用于hsf不合格处理流程挑选重工作业重工作业申请批退报废作业流程包装入库保存作业不良状况所费工时记录不合格批产生mrb审查可否重工检验业务
不合格批产生
MRB审查 可否挑选?
NG
报废作业申请
OK
不合格品控制流程图(最完善、最经典)
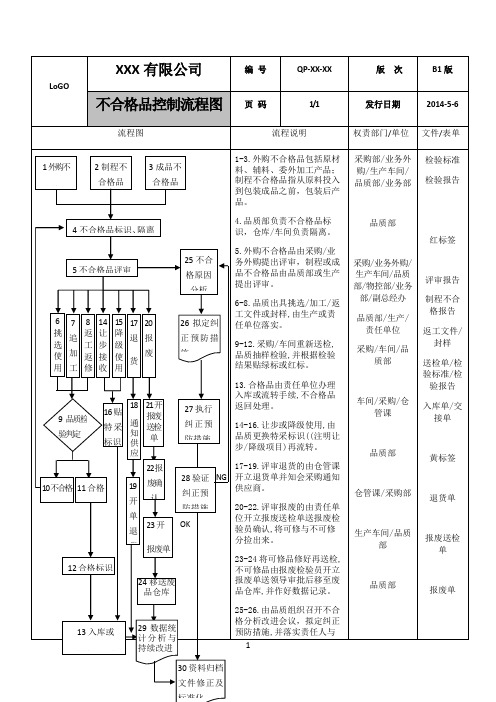
27 执行 纠正预 防措施
28 验证 NG 纠正预 防措施 OK
/审批 24 移送废
品仓库
13.合格品由责任单位办理 入库或流转手续,不合格品 返回处理。
14-16.让步或降级使用,由 品质更换特采标识((注明让 步/降级项目)再流转。
17-19.评审退货的由仓管课 开立退货单并知会采购通知 供应商。
XXX 有限公司
编号
LoGO
不合格品控制流程图 页 码
QP-XX-XX 1/1
版次
B1 版
发行日期
2014-5-6
流程图
流程说明
权责部门/单位 文件/表单
1 外购不 合格品
2 制程不 合格品
3 成品不 合格品
1-3.外购不合格品包括原材 料、辅料、委外加工产品; 制程不合格品指从原料投入 到包装成品之前,包装后产 品。
采购部业务外购生产车间品质部业务部品质部采购业务外购生产车间品质部物控部业务部副总经办品质部生产责任单位采购车间品品质部仓管课采购部生产车间品质品质部品质部生产部技术部物控部业务部副总经办品质部责任单品质部技术部检验标准检验报告红标签评审报告制程不合格报告返工文件送检单检验标准检验报告入库单交接单黄标签退货单报废送检报废单纠正预防措施单品质月周报告相关文件1外购不合格品制程不合格品成品不合格品品质检验判定25不合格原因分析26拟定纠正预防措27执行纠正预防措施28验证纠正预防措施30资料归档文件修正及标准化11合格12合格标识13入库或流转下工序okng16贴标识1824移送废品仓库29数据统计分析与持续改进1921开报废送检10不合格23开报废单审批
质部
车间/采购/仓 管课
品质部
仓管课/采购部
生产车间/品质 部
不合格品控制流程图

生产/ 质量
各部门 担当
生产部/质检部相关人员须做好不合格品的标识记录和追溯管理
整 让返 全 批 步工 数 拒 接返 挑 收 收修 选
1.退货单 3.返工/返修指导书 4.不合格品处理单 5.扣款单
标识记录
OK
NG
检验
1.质量报表
记录归档、产品放行
1.记录清单
不合格品提出
1.不合格品处理单 2.纠正预防措施报告
各部门 担当
1.报废:责任部门提出报废,质检部负责报废品判定,具体流 程见《报废品控制流程图》。 2.让步接受:质量、工程部门、在“不合格品处理单”上注明 意见/建议后报生产副总核准。如有顾客要求,让步接收还需得 到顾客或其代表的批准。 3.返工/返修:对返工/返修的产品,由工程部制定返工返修指 导书,生产部作业,检验员重新检验,合格后方可进入下一流 程。 4.全数挑选:由责任部门实施,挑选后的零件必须重新检验确 认 5.质检部全检组选出的不合格品,每天清理分类别退给生产 部, 生产部每天安排专人维修打磨,第二天随白坯品投入产线返 喷,但须和正常品区分隔离标示,下线后须标示区分,单独存
供
3.返工/返修:技术部制定返工返修指导书,生产部组织对返工
不 合
各部门
责任担当
/返修作业,返修后检验员必须重新检验,合格后方可入库。 4.全数挑选:生产部组织实施,挑选后的产品必须重新提交检
格
验
5.让步接收品:由采购部按次品价格采购。
品
6.外购件由公司返工、全检所产生的费用,由质量部统计、采
购部扣款。
7.客户提供品由我司返工返修,由业务部联络客户确认费用归
属
质量
质检
让步申请如批准,质量部应在“质量报表”上注明,并在标签 上进行标识记号,让步申请未得到批准的,则采用退货方式处
制程不良品处理流程图
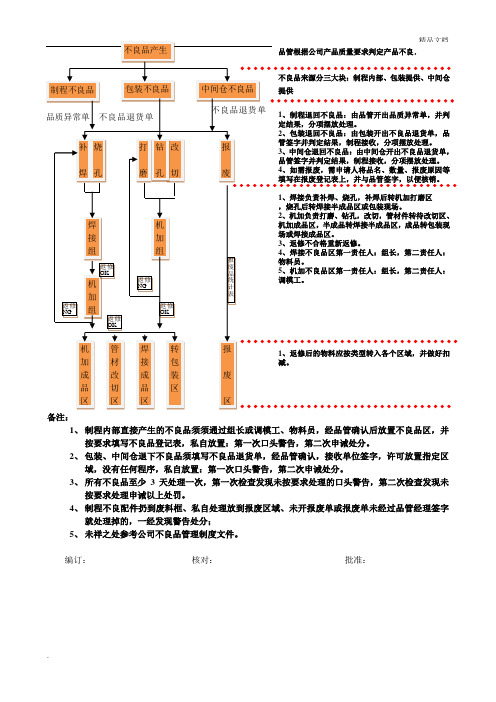
1、制程内部直接产生的不良品须须通过组长或调模工、物料员,经品管确认后放置不良品区,并
按要求填写不良品登记表,私自放置:第一次口头警告,第二次申诫处分。
2、包装、中间仓退下不良品须填写不良品退货单,经品管确认,接收单位签字,许可放置指定区
域,没有任何程序,私自放置:第一次口头警告,第二次申诫处分。
3、所有不良品至少3天处理一次,第一次检查发现未按要求处理的口头警告,第二次检查发现未
按要求处理申诫以上处罚。
4、制程不良配件扔到废料框、私自处理放到报废区域、未开报废单或报废单未经过品管经理签字
就处理掉的,一经发现警告处分;
5、未祥之处参考公司不良品管理制度文件。
编订:核对:批准:
.。
制程不良品处理流程图
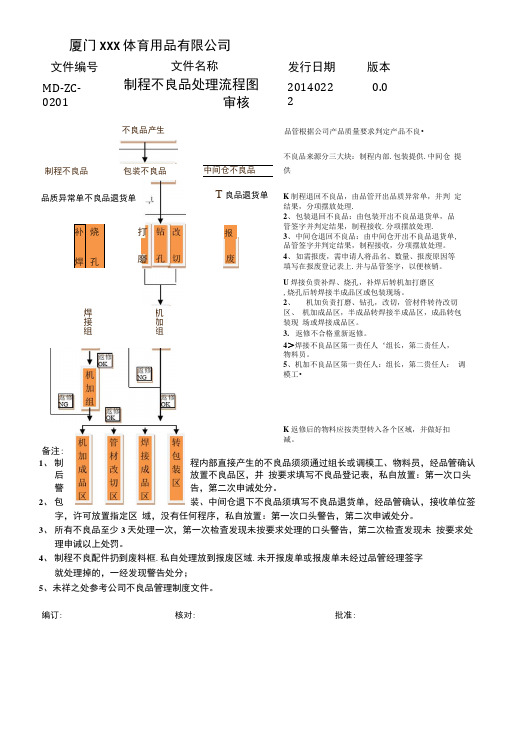
审核K 返修后的物料应按类型转入各个区域,并做好扣 减。
1、 制程内部直接产生的不良品须须通过组长或调模工、物料员,经品管确认后放置不良品区,并 按要求填写不良品登记表,私自放置:第一次口头警告,第二次申诫处分。
2、 包装、中间仓退下不良品须填写不良品退货单,经品管确认,接收单位签字,许可放置指定区 域,没有任何程序,私自放置:第一次口头警告,第二次申诫处分。
3、 所有不良品至少3天处理一次,第一次检査发现未按要求处理的口头警告,第二次检査发现未 按要求处理申诫以上处罚。
4、 制程不良配件扔到废料框.私自处理放到报废区域.未开报废单或报废单未经过品管经理签字就处理掉的,一经发现警告处分;5、未祥之处参考公司不良品管理制度文件。
文件编号 MD-ZC-0201文件名称 制程不良品处理流程图发行日期 20140222版本 0.0品管根据公司产品质量要求判定产品不良•制程不良品 补 烧焊 孔焊接组不良品产生 包装不良品 品质异常单不良品退货单 打 磨中间仓不良品T 良品退货单不良品来源分三大块:制程内部.包装提供.中间仓 提供机加组报K 制程退回不良品,由品管开出品质异常单,并判 定结果,分项摆放处理. 2、 包装退回不良品:由包装开出不良品退货单,品 管签字并判定结果,制程接收.分项摆放处理. 3、 中间仓退回不良品:由中间仓开出不良品退货单, 品管签字并判定结果,制程接收,分项摆放处理。
4、 如需报废,需申请人将品名、数量、报废原因等 填写在报废登记表上.并与品管签字,以便核销。
U 焊接负贵补焊、烧孔,补焊后转机加打磨区 ,烧孔后转焊接半成品区或包装现场。
2、 机加负责打磨、钻孔,改切,管材件转待改切区、 机加成品区,半成品转焊接半成品区,成品转包装现 场或焊接成品区。
3. 返修不合格重新返修。
4>焊接不良品区第一责任人‘组长,第二责任人, 物料员。
5、机加不良品区第一贵任人:组长,第二贵任人: 调模工•备注: 编订:核对: 批准:。
不合格品处理流程图
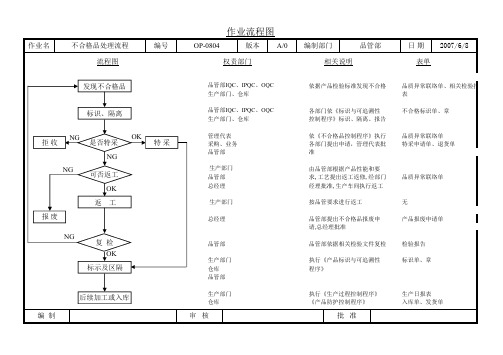
生产日报表 入库单、发货单
品管部IQC、IPQC、OQC 生产部门、仓库
管理代表 采购、业务 品管部
生产部门 品管部 总经理
生产部门
总经理
品管部
生产部门 仓库 品管部
生产部门 仓库
审核
依据产品检验标准发现不合格
品质异常联络单、相关检验报 表
各部门依《标识与可追溯性 控制程序》标识、隔离、报告
不合格标识单、章
依《不合格品控制程序》执行, 各部门提出申请,管理代表批 准
品质异常联络单 特采申请单、退货单
由品管部根据产品性能和要 求,工艺提出返工返修,经部门 经理批准,生产车间执行返工
品质异常联络单
按品管要求进行返工
无
品管部提出不合格品报废申 请,总经理批准
产品报废申
执行《产品标识与可追溯性 程序》
标识单、章
执行《生产过程控制程序》 《产品防护控制程序》
作业名
不合格品处理流程 流程图
编号
作业流程图
OP-0804
版本 A/0
权责部门
编制部门
品管部
相关说明
日 期 2007/6/8 表单
发现不合格品
标识、隔离
拒 收 NG 是否特采
OK 特采
NG NG
可否返工
OK 返工
报废
NG 复检 OK
标示及区隔
编制
后续加工或入库
品管部IQC、IPQC、OQC 生产部门、仓库
不合格品管理流程图

不合格品处理单 纠正预防措施报
品质部负责人
这个时间对处理情况进行验证
告
3.返工或返修后的产品,品质部应进行复 检,复检合格方可流入下序或入库,同 时,对返工后产品应进行特殊标识
返工标识(在标识 卡上用 R 字样标 识)
品质部负责人
1。 品质部对每月不良数据进行统计的 分析,制定改善措施,跟进和验证改 品质月报
类别
三级文件
流程图
不合格品来源
及修订 来 制成 出客 料 程品 货户 检 检检 检退 验 验验 验货
合格
评审/
特采
判定
正 常 使 用
标识
隔离品管理流程图
文件编号 版本版次 页次 生效日期
DOM-880-01 A0
1 /1
2016-12-01
流程说明
输出内容
品质部负责人
1.来料检验时发现不合格品,由 IQC 填 写《不合格品处理单》通知采购处理. 不合格品处理单 可以特采的,由采购组织品质、研发、 生产等部门评审后报总经理批准
IQC 采购负责人 评审小组
2。 制程中首检、自检、巡检时发现的 不合格品,由 IPQC 判定,IPQC 不能 判定时报品质部负责人判定,仍不能
品质部负责人
善结果
审核:
批准:
不合格品处理单
IPQC 品质部负责人
判定,组织生产、研发、销售相关人
评审小组
员评审,并将评审结果报总经理批准
1。不合格品的标识由发现人(可能是 QC 或作业员等)负责,标识的方式可 不合格标识卡 以是用红色标识卡、标识牌或其他易
不合格品发现人
于识别的方式
1.各车间、仓库负责对本区域内的所有不 合格品进行隔离,隔离的方式包括用 红箱盛装、在包装容器内用红卡标识 后移至不合格品放置区等