塑料件的设计要求及电镀要求
塑料工程技术手册
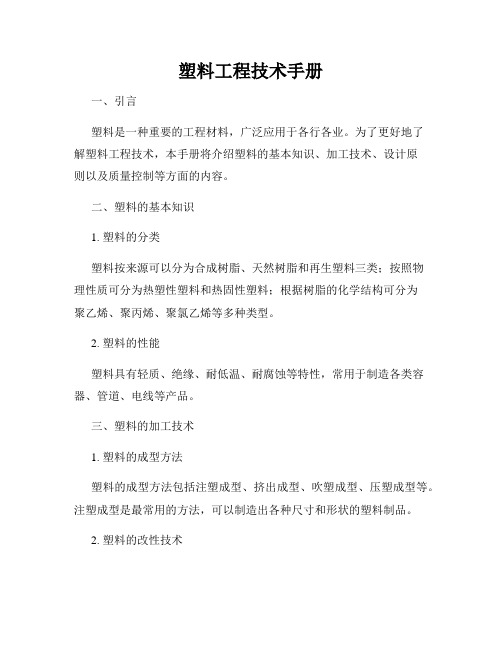
塑料工程技术手册一、引言塑料是一种重要的工程材料,广泛应用于各行各业。
为了更好地了解塑料工程技术,本手册将介绍塑料的基本知识、加工技术、设计原则以及质量控制等方面的内容。
二、塑料的基本知识1. 塑料的分类塑料按来源可以分为合成树脂、天然树脂和再生塑料三类;按照物理性质可分为热塑性塑料和热固性塑料;根据树脂的化学结构可分为聚乙烯、聚丙烯、聚氯乙烯等多种类型。
2. 塑料的性能塑料具有轻质、绝缘、耐低温、耐腐蚀等特性,常用于制造各类容器、管道、电线等产品。
三、塑料的加工技术1. 塑料的成型方法塑料的成型方法包括注塑成型、挤出成型、吹塑成型、压塑成型等。
注塑成型是最常用的方法,可以制造出各种尺寸和形状的塑料制品。
2. 塑料的改性技术塑料的改性技术可以改善塑料的物理性能,常用的改性技术包括填充剂增强、增韧剂掺入、改性剂添加等。
3. 塑料的表面处理技术塑料的表面处理技术可以提高塑料制品的外观质量和耐用性,常用的表面处理技术有喷涂、电镀、印刷等。
四、塑料制品的设计原则1. 强度设计原则塑料制品在设计时需要考虑到其受力情况,合理选择塑料材料和结构设计,确保制品的强度满足要求。
2. 尺寸设计原则塑料制品的尺寸设计需考虑到塑料材料的收缩率,以确保成型后的尺寸符合设计要求。
3. 壳体设计原则塑料制品的壳体设计需要满足结构强度、制造工艺和装配要求,合理选择壳体的厚度和型腔结构。
五、塑料制品的质量控制1. 塑料原料的质量控制塑料原料的质量对最终制品的性能有重要影响,应选用合格的原料并进行严格的质量检测。
2. 加工工艺的质量控制加工工艺的合理控制可以确保塑料制品的尺寸、外观等质量要求,需进行严格的加工工艺检验。
3. 成品质量的控制成品质量的控制包括外观检验、物理性能测试等,确保塑料制品能够满足使用要求。
六、未来发展趋势塑料工程技术在不断发展,未来的趋势包括绿色环保塑料的研发、智能制造技术的应用以及废弃塑料的回收利用等。
七、结论本手册从塑料的基本知识、加工技术、设计原则和质量控制等方面介绍了塑料工程技术的相关内容。
全面的塑料电镀件检验标准
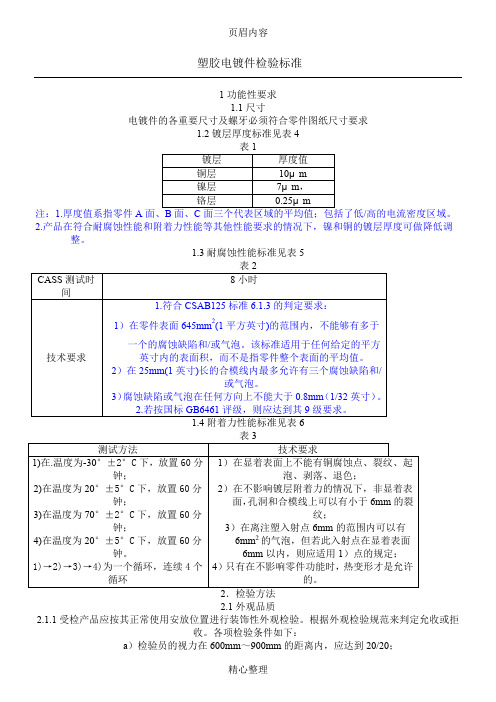
塑胶电镀件检验标准
1功能性要求
1.1尺寸
电镀件的各重要尺寸及螺牙必须符合零件图纸尺寸要求
1.2镀层厚度标准见表4
2.1外观品质
2.1.1受检产品应按其正常使用安放位置进行装饰性外观检验。
根据外观检验规范来判定允收或拒
收。
各项检验条件如下:
a)检验员的视力在600mm~900mm的距离内,应达到20/20;
b)检验灯光应为1600流明,及相当于2支40W的日光灯发出的光,光源于物件距离为
1000mm;
c)物件与检验员眼睛距离应在300mm~400mm范围内。
d)观察时间:A面6s、B面4s、C面2s。
2.1.2
2.1.3拿近物件检验表面其是否存在功能性外观缺陷(如气泡、镀层剥离、镀层毛刺等),如有则拒收该工件。
但是不要拒收发现的装饰性外观缺陷。
拿近发现的装饰性外观缺陷肯定比第一点发现
的装饰性外观缺陷多。
2.2镀层厚度参照GB4955金属覆盖层厚度测定阳极溶解库仑方法进行测试。
2.3耐腐蚀性能参照ASTMB368或GB/T10125方法进行测试。
2.4附着力性能参照EN248方法进行测试。
塑胶表面处理之电镀
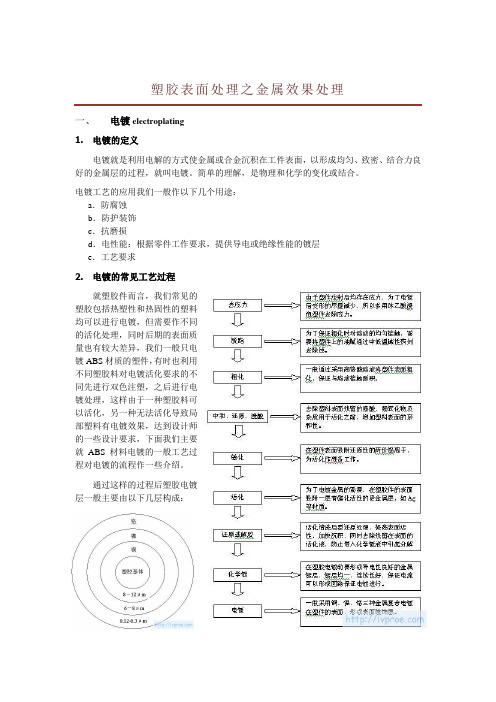
塑胶表面处理之金属效果处理一、电镀electroplating1.电镀的定义电镀就是利用电解的方式使金属或合金沉积在工件表面,以形成均匀、致密、结合力良好的金属层的过程,就叫电镀。
简单的理解,是物理和化学的变化或结合。
电镀工艺的应用我们一般作以下几个用途:a.防腐蚀b.防护装饰c.抗磨损d.电性能:根据零件工作要求,提供导电或绝缘性能的镀层e.工艺要求2.电镀的常见工艺过程就塑胶件而言,我们常见的塑胶包括热塑性和热固性的塑料均可以进行电镀,但需要作不同的活化处理,同时后期的表面质量也有较大差异,我们一般只电镀ABS材质的塑件,有时也利用不同塑胶料对电镀活化要求的不同先进行双色注塑,之后进行电镀处理,这样由于一种塑胶料可以活化,另一种无法活化导致局部塑料有电镀效果,达到设计师的一些设计要求,下面我们主要就ABS材料电镀的一般工艺过程对电镀的流程作一些介绍。
通过这样的过程后塑胶电镀层一般主要由以下几层构成:高光电镀高光电镀的效果的实现通常要求模具表面良好抛光,注射出的塑件采用光铬处理后得到的效果。
亚光电镀亚光电镀的效果的实现通常要求模具表面良好抛光,注射出的塑件采用亚铬处理后得到的效果。
珍珠铬珍珠铬电镀的效果的实现通常要求模具表面良好抛光,注射出的塑件采用珍珠铬处理后得到的效果。
蚀纹电镀蚀纹电镀的效果的实现通常要求模具表面处理出不同效果的蚀纹方式后,注射出的塑件采用光铬处理后得到的效果。
混合电镀在模具处理上既有抛光的部分又有蚀纹的部分,注射出的塑件电镀后出项高光和蚀纹电镀的混合效果,突出某些局部的特征。
混合电镀效果对设计的要求:我们在设计中常常采用高光电镀和蚀纹电镀的效果共同作用在一个制品上得到特殊的设计效果,通常在设计中建议采用较小的蚀纹,这样效果会比较好,但这样的设计时,为了不会使蚀纹的效果被电镀所掩盖,有时会电镀两层后就不进行电镀,这样的后果是电镀第二层的镍会比较容易氧化变色,影响设计的效果。
全面的塑料电镀件检验标准
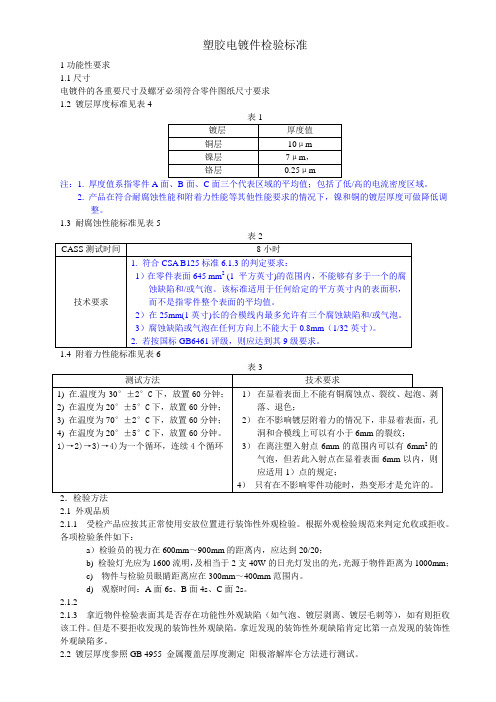
塑胶电镀件检验标准
1功能性要求
1.1尺寸
电镀件的各重要尺寸及螺牙必须符合零件图纸尺寸要求
1.2 镀层厚度标准见表4
表1
注:1. 厚度值系指零件A面、B面、C面三个代表区域的平均值;包括了低/高的电流密度区域。
2. 产品在符合耐腐蚀性能和附着力性能等其他性能要求的情况下,镍和铜的镀层厚度可做降低调
整。
1.3 耐腐蚀性能标准见表5
表2
2.检验方法
2.1 外观品质
2.1.1 受检产品应按其正常使用安放位置进行装饰性外观检验。
根据外观检验规范来判定允收或拒收。
各项检验条件如下:
a)检验员的视力在600mm~900mm的距离内,应达到20/20;
b) 检验灯光应为1600流明,及相当于2支40W的日光灯发出的光,光源于物件距离为1000mm;
c)物件与检验员眼睛距离应在300mm~400mm范围内。
d)观察时间:A面6s、B面4s、C面2s。
2.1.2
2.1.3 拿近物件检验表面其是否存在功能性外观缺陷(如气泡、镀层剥离、镀层毛刺等),如有则拒收该工件。
但是不要拒收发现的装饰性外观缺陷。
拿近发现的装饰性外观缺陷肯定比第一点发现的装饰性外观缺陷多。
2.2 镀层厚度参照GB 4955 金属覆盖层厚度测定阳极溶解库仑方法进行测试。
2.3 耐腐蚀性能参照ASTM B368或GB/T 10125方法进行测试。
2.4 附着力性能参照EN248方法进行测试。
塑料制品的设计(强行脱模、表面质量)

塑胶制品结构的设计
一.制品结构工艺设计的原则:
1.在保证制品性能和使用要求的情况下,尽量选用价廉、且成型性能好的塑料;
2.力求使制品结构简单,避免侧向凹凸结构,使模具结构简单,易于制造;(内侧凹凸结构有两种情况可不用内行位:碰穿和强行脱模)
•注:关于强行脱模:
1)当侧向凹凸较浅且允许有圆角时,可强行脱模;
2)可强行脱模的塑料有PE、PP、POM和PVC等;
三、制品的表面质量:
1、包括制造质量:型腔省模抛光,一般模具型腔粗糙度为
Ra0.02—1.25um,制品的粗糙度比模具型腔粗糙度低1-2级。
2、注塑质量:水花,蛇纹,熔接痕,顶白变形,黑斑,披锋、
凹痕等。
3、烤柒质量:
4、电镀质量:
5、丝印质量:
6、拉丝质量:
7、抛光质量:
8、汤金质量
9、贴纸质量
10、贴片
四.塑料制品的常见结构设计:
1.脱模斜度:
1).不同塑料的脱模斜度不同,在不影响产品性能的情况下,脱模斜度尽量取较大值;
2).脱模斜度不包括在公差范围之内;
3).晒纹脱模斜度应取较大值,
一般为3°~9°;
4).硬质塑料比软质塑料的脱模斜度大,收缩率大的塑料比收缩率小的脱模斜度大;
5)、制品高度越高,孔越深,为保证精度要求,脱模斜度宜取小一点;
6)、制品形状复杂难脱模时,脱模斜度要大一些;
7)、前模脱模斜度大于后模脱模斜度;
8)、配合精度要求越高,脱模斜度要越小;
9)、壁厚大的制品,脱模斜度可取较大值;机械性能强塑料,自润滑性塑料,脱模斜度可取小一些。
ABS塑料电镀
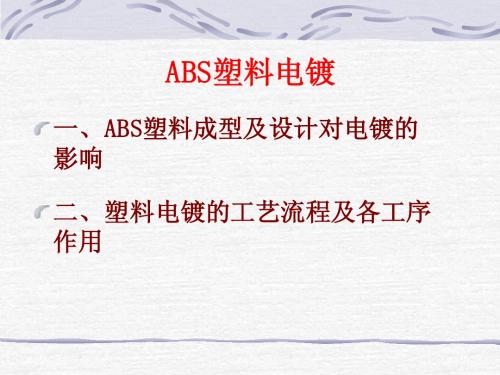
C、制品都应该设计得有足够的强度,壁厚不
要太薄,最好大于3MM,至少为1.5MM。壁厚 不要有突变. D、不应有锐边、尖角及锯齿形,若必须有时, 其边缘应尽量倒圆。 E、尽量避免大面积的平面,因为它不易得到 均匀的光泽。 F、应有足够多的挂具点(因化学镍镀层很薄, 导电比金属件要差得多,最少不得少于三个挂 点),设计挂具点时应选择壁厚部位(预防 变形),如有薄壁要求的应设计辅助挂位, 挂位设计尽可能走左右或上下弹,而不要用 夹的方式。
2、水份的影响 ABS颗粒很易吸水,为了 使其在压注前的水份含量低于0.1%,必须 预先在80℃的热风干燥箱中烘干2~4小时, 同时还必须注意压注的环境,务必保持干 燥,相对湿度不要太高,否则压注后在制 件表面会产生小气泡,电镀后气泡更大。 3、再生料及杂质的影响 要电镀的ABS塑 料,其成份必须一致,不允许混入其他成 份,更不允许掺入其他杂质。对同成分的 再生料也不能用,若一定要用时,应经过 试验并严格控制比例,否则都将得不到良 好的附着力。
ABS塑料电镀
一、ABS塑料成型及设计对电镀的 影响 二、塑料电镀的工艺流程及各工序 作用
一、ABS塑料成型及设计对电镀的影响
(一)ABS塑料成分对电镀的影响
(二)塑料制件电镀对外形设计和 模具设计的要求
(一)ABS塑料成分对电镀的影响
1、丁二烯的含量 ABS塑料是否易 镀,除了制造方法以外,与塑料中 丁二烯的含量关系很大,一般说来, 丁二烯含量高,流动性好,成型容 易,电镀后的镀层附着力好。(丁 二烯含量一般控制在18~23%)
9、焦铜前活化:除去化学镍层表面的氧化 膜,使之后的金属镀层结合力良好。 10、焦铜:化学镍层较薄(0.3um),如直 接进行光亮镀铜,将难以承受如此高的电的 电流密度,故需先预镀一层均匀的延展性良 好的镀层,使之电流承受提高,以方便光铜 的电镀。 11、光铜前活化:除去焦铜表面生成的氧化 膜。 12、光铜:光铜具有较高的光亮度,良好的 填平能力,能淹盖塑胶表面较浅的横纹,现 时工艺可控制厚度在5-20um,镀层内应力小。
塑料件电镀工艺流程
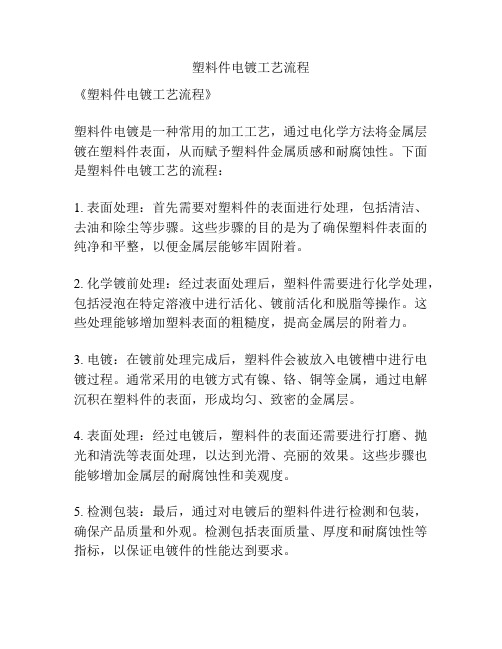
塑料件电镀工艺流程
《塑料件电镀工艺流程》
塑料件电镀是一种常用的加工工艺,通过电化学方法将金属层镀在塑料件表面,从而赋予塑料件金属质感和耐腐蚀性。
下面是塑料件电镀工艺的流程:
1. 表面处理:首先需要对塑料件的表面进行处理,包括清洁、去油和除尘等步骤。
这些步骤的目的是为了确保塑料件表面的纯净和平整,以便金属层能够牢固附着。
2. 化学镀前处理:经过表面处理后,塑料件需要进行化学处理,包括浸泡在特定溶液中进行活化、镀前活化和脱脂等操作。
这些处理能够增加塑料表面的粗糙度,提高金属层的附着力。
3. 电镀:在镀前处理完成后,塑料件会被放入电镀槽中进行电镀过程。
通常采用的电镀方式有镍、铬、铜等金属,通过电解沉积在塑料件的表面,形成均匀、致密的金属层。
4. 表面处理:经过电镀后,塑料件的表面还需要进行打磨、抛光和清洗等表面处理,以达到光滑、亮丽的效果。
这些步骤也能够增加金属层的耐腐蚀性和美观度。
5. 检测包装:最后,通过对电镀后的塑料件进行检测和包装,确保产品质量和外观。
检测包括表面质量、厚度和耐腐蚀性等指标,以保证电镀件的性能达到要求。
通过以上工艺流程,塑料件电镀能够赋予塑料产品优良的金属质感和抗腐蚀性能,使其在外观和功能上都得到提升。
同时,合理的工艺流程和严格的质量控制,也能够确保塑料件电镀产品的质量和稳定性。
abs电镀工艺流程
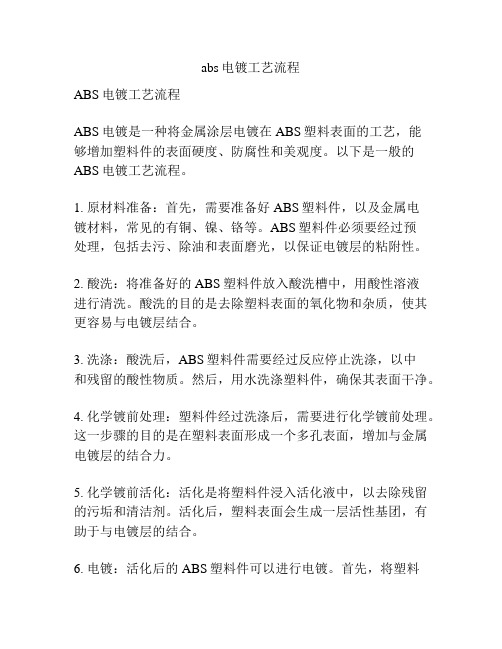
abs电镀工艺流程ABS电镀工艺流程ABS电镀是一种将金属涂层电镀在ABS塑料表面的工艺,能够增加塑料件的表面硬度、防腐性和美观度。
以下是一般的ABS电镀工艺流程。
1. 原材料准备:首先,需要准备好ABS塑料件,以及金属电镀材料,常见的有铜、镍、铬等。
ABS塑料件必须要经过预处理,包括去污、除油和表面磨光,以保证电镀层的粘附性。
2. 酸洗:将准备好的ABS塑料件放入酸洗槽中,用酸性溶液进行清洗。
酸洗的目的是去除塑料表面的氧化物和杂质,使其更容易与电镀层结合。
3. 洗涤:酸洗后,ABS塑料件需要经过反应停止洗涤,以中和残留的酸性物质。
然后,用水洗涤塑料件,确保其表面干净。
4. 化学镀前处理:塑料件经过洗涤后,需要进行化学镀前处理。
这一步骤的目的是在塑料表面形成一个多孔表面,增加与金属电镀层的结合力。
5. 化学镀前活化:活化是将塑料件浸入活化液中,以去除残留的污垢和清洁剂。
活化后,塑料表面会生成一层活性基团,有助于与电镀层的结合。
6. 电镀:活化后的ABS塑料件可以进行电镀。
首先,将塑料件浸入金属电镀液中,确保其完全浸没在液体中。
然后,施加电流,使金属离子在塑料表面析出金属层。
7. 后处理:电镀完成后,金属镀层需要进行后处理以提高其质量和外观。
一般来说,后处理包括冷却、洁净和抛光等步骤。
8. 质检:最后,在电镀完成后,需要对产品进行质量检验。
主要检查电镀层的厚度、附着力和表面质量等。
只有通过质检的产品才会进行包装和出厂。
综上所述,ABS电镀工艺流程包括原材料准备、酸洗、洗涤、化学镀前处理、活化、电镀、后处理和质检等步骤。
每一步骤都非常重要,影响着最终电镀层的质量和性能。
因此,在进行ABS电镀时,需要严格按照工艺规范进行操作,以确保产品能够达到预期的效果。
ABS塑料电镀工艺
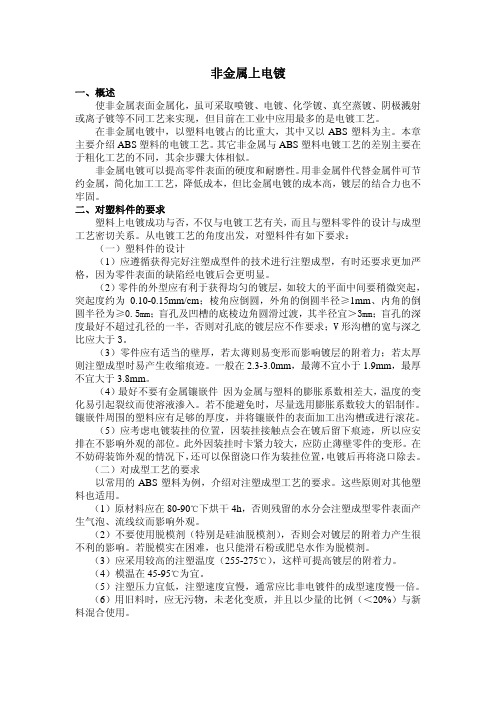
非金属上电镀一、概述使非金属表面金属化,虽可采取喷镀、电镀、化学镀、真空蒸镀、阴极溅射或离子镀等不同工艺来实现,但目前在工业中应用最多的是电镀工艺。
在非金属电镀中,以塑料电镀占的比重大,其中又以ABS塑料为主。
本章主要介绍ABS塑料的电镀工艺。
其它非金属与ABS塑料电镀工艺的差别主要在于粗化工艺的不同,其余步骤大体相似。
非金属电镀可以提高零件表面的硬度和耐磨性。
用非金属件代替金属件可节约金属,简化加工工艺,降低成本,但比金属电镀的成本高,镀层的结合力也不牢固。
二、对塑料件的要求塑料上电镀成功与否,不仅与电镀工艺有关,而且与塑料零件的设计与成型工艺密切关系。
从电镀工艺的角度出发,对塑料件有如下要求:(一)塑料件的设计(1)应遵循获得完好注塑成型件的技术进行注塑成型,有时还要求更加严格,因为零件表面的缺陷经电镀后会更明显。
(2)零件的外型应有利于获得均匀的镀层,如较大的平面中间要稍微突起,突起度约为0.10-0.15mm/cm;棱角应倒圆,外角的倒圆半径≥1mm、内角的倒圆半径为≥0.5mm;盲孔及凹槽的底棱边角圆滑过渡,其半径宜>3mm;盲孔的深度最好不超过孔径的一半,否则对孔底的镀层应不作要求;V形沟槽的宽与深之比应大于3。
(3)零件应有适当的壁厚,若太薄则易变形而影响镀层的附着力;若太厚则注塑成型时易产生收缩痕迹。
一般在2.3-3.0mm,最薄不宜小于1.9mm,最厚不宜大于3.8mm。
(4)最好不要有金属镶嵌件因为金属与塑料的膨胀系数相差大,温度的变化易引起裂纹而使溶液渗入。
若不能避免时,尽量选用膨胀系数较大的铝制作。
镶嵌件周围的塑料应有足够的厚度,并将镶嵌件的表面加工出沟槽或进行滚花。
(5)应考虑电镀装挂的位置,因装挂接触点会在镀后留下痕迹,所以应安排在不影响外观的部位。
此外因装挂时卡紧力较大,应防止薄壁零件的变形。
在不妨碍装饰外观的情况下,还可以保留浇口作为装挂位置,电镀后再将浇口除去。
塑料件的设计要求及电镀要求
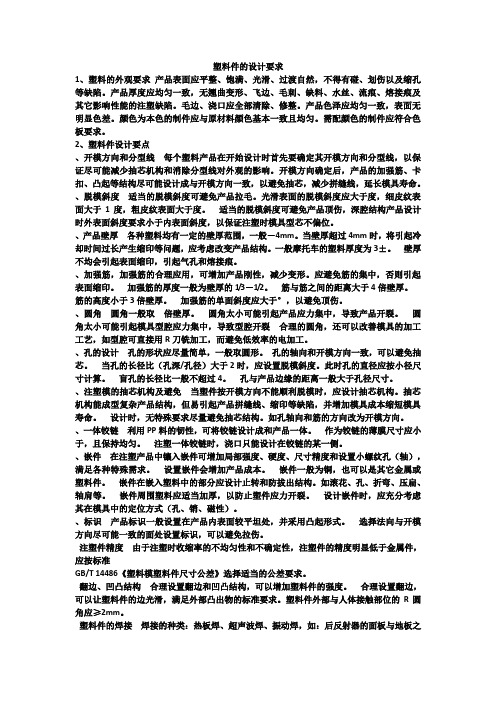
塑料件的设计要求1、塑料的外观要求产品表面应平整、饱满、光滑、过渡自然,不得有碰、划伤以及缩孔等缺陷。
产品厚度应均匀一致,无翘曲变形、飞边、毛刺、缺料、水丝、流痕、熔接痕及其它影响性能的注塑缺陷。
毛边、浇口应全部清除、修整。
产品色泽应均匀一致,表面无明显色差。
颜色为本色的制件应与原材料颜色基本一致且均匀。
需配颜色的制件应符合色板要求。
2、塑料件设计要点、开模方向和分型线每个塑料产品在开始设计时首先要确定其开模方向和分型线,以保证尽可能减少抽芯机构和消除分型线对外观的影响。
开模方向确定后,产品的加强筋、卡扣、凸起等结构尽可能设计成与开模方向一致,以避免抽芯,减少拼缝线,延长模具寿命。
、脱模斜度适当的脱模斜度可避免产品拉毛。
光滑表面的脱模斜度应大于度,细皮纹表面大于1度,粗皮纹表面大于度。
适当的脱模斜度可避免产品顶伤,深腔结构产品设计时外表面斜度要求小于内表面斜度,以保证注塑时模具型芯不偏位。
、产品壁厚各种塑料均有一定的壁厚范围,一般-4mm。
当壁厚超过4mm时,将引起冷却时间过长产生缩印等问题,应考虑改变产品结构。
一般摩托车的塑料厚度为3±。
壁厚不均会引起表面缩印,引起气孔和熔接痕。
、加强筋,加强筋的合理应用,可增加产品刚性,减少变形。
应避免筋的集中,否则引起表面缩印。
加强筋的厚度一般为壁厚的1/3-1/2。
筋与筋之间的距离大于4倍壁厚。
筋的高度小于3倍壁厚。
加强筋的单面斜度应大于°,以避免顶伤。
、圆角圆角一般取倍壁厚。
圆角太小可能引起产品应力集中,导致产品开裂。
圆角太小可能引起模具型腔应力集中,导致型腔开裂合理的圆角,还可以改善模具的加工工艺,如型腔可直接用R刀铣加工,而避免低效率的电加工。
、孔的设计孔的形状应尽量简单,一般取圆形。
孔的轴向和开模方向一致,可以避免抽芯。
当孔的长径比(孔深/孔径)大于2时,应设置脱模斜度。
此时孔的直径应按小径尺寸计算。
盲孔的长径比一般不超过4。
电镀标准TL_528
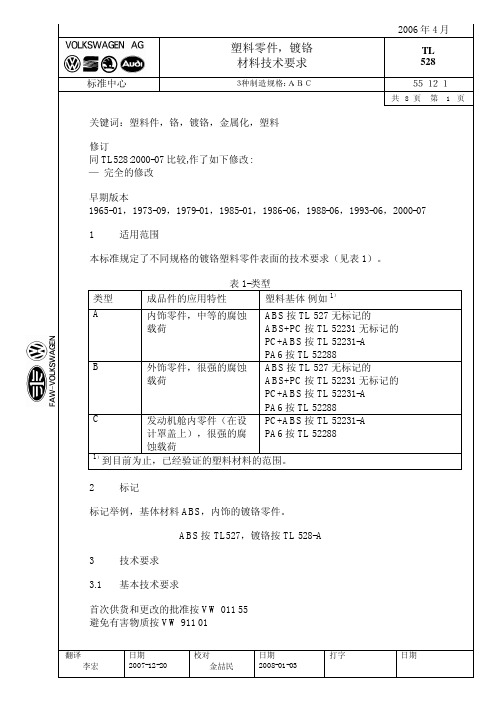
4.3 十字划格
实验的进行与网格切割(见 4.2 条)类似,只是用十字格代替网格。
标准中心
塑料零件,镀铬 材料技术要求
TL 528
共 8页 第 6 页
5 相关参考文献
PV 1058 PV 1063 PV 1065 PV 1200 PV 2005 VW 011 55 VW 911 01 DIN 50021 DIN 50960-1 DIN EN 1403 DIN EN 1464 DIN EN 12540
附件 A (说明) 对电镀的塑料零件批量监控的建议:
标准中心
塑料零件,镀铬 材料技术要求
TL 528
共 8页 第 7 页
要求项目的批量监控是产品专用特性的保障和电镀过程的监控。因为每天生产的大量产 品,无法对每件产品给出单独的反应当时状态的监控,只能按类似的结构(例如,字 标、装饰条等)给产品分组。对各组产品进行连续的批量监控是供应商的一项任务。按 照规则的时间段对一定数量的试样进行检验。实验结果存档。
门协商
无外观变化,在理想照明的条件下,无 60cm 目
视可见的腐蚀。评价前必须将表面残余的盐清
除掉。
气候交变实验存放
96 小时气候交
按 PV1200,
变试验存放, 96 小时气候交变试验存放,然
紧 接 着 进 行 盐 雾 SS- 试 然后进行
后进行 480h ,SS 试验
验,按 DIN 50021
标准中心
塑料零件,镀铬 材料技术要求
TL 528
共 8页 第 2 页
对于一次完整的实验,至少需要 10 件成品件(也按大小)。
所有要实验的零件必须提供下面的信息(见 附件表 B) : a) 零件号 b) 塑料件生产商,地点。 c) 基体材料(塑料类型,制造商,牌号) d) 电镀工厂和电镀设备,地点。 e) 电镀日期 f) 塑料活化/金属化程序的方法(例如,传统胶质镀铬,电离,直接金属化,光亮铬,
汽车塑料件电镀工艺
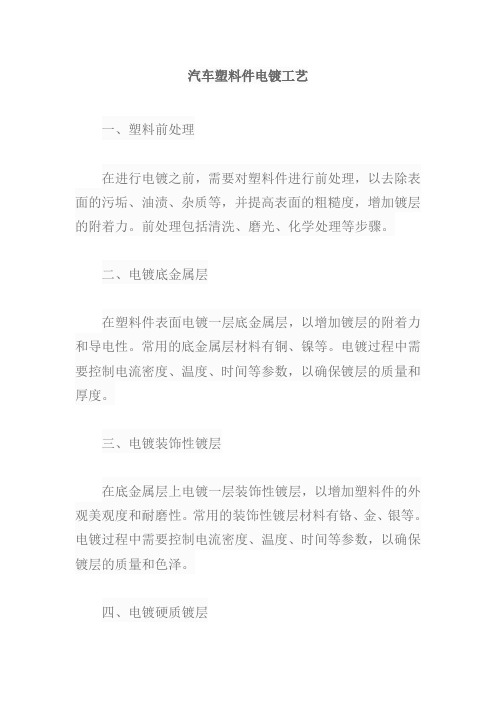
汽车塑料件电镀工艺一、塑料前处理在进行电镀之前,需要对塑料件进行前处理,以去除表面的污垢、油渍、杂质等,并提高表面的粗糙度,增加镀层的附着力。
前处理包括清洗、磨光、化学处理等步骤。
二、电镀底金属层在塑料件表面电镀一层底金属层,以增加镀层的附着力和导电性。
常用的底金属层材料有铜、镍等。
电镀过程中需要控制电流密度、温度、时间等参数,以确保镀层的质量和厚度。
三、电镀装饰性镀层在底金属层上电镀一层装饰性镀层,以增加塑料件的外观美观度和耐磨性。
常用的装饰性镀层材料有铬、金、银等。
电镀过程中需要控制电流密度、温度、时间等参数,以确保镀层的质量和色泽。
四、电镀硬质镀层在底金属层和装饰性镀层之间或表面电镀一层硬质镀层,以增加塑料件的硬度、耐磨性和耐腐蚀性。
常用的硬质镀层材料有镍、铬等。
电镀过程中需要控制电流密度、温度、时间等参数,以确保镀层的质量和厚度。
五、涂清漆在电镀完成后,需要在塑料件表面涂上一层清漆,以增加塑料件的外观美观度和保护电镀层。
清漆的涂装需要在干燥的环境中进行,并控制涂装温度和时间等参数。
六、涂清漆后处理在涂装清漆后,需要进行后处理,以增加清漆的硬度和耐磨性。
常用的后处理方法包括烘烤、硬化等。
后处理过程中需要控制温度和时间等参数,以确保清漆的质量和外观。
七、涂清漆后处理后检验在后处理完成后,需要对塑料件进行检验,以检查清漆的质量和外观是否符合要求。
检验过程中需要使用专业的检测设备和标准进行评估。
八、涂清漆后处理后包装在检验合格后,需要对塑料件进行包装,以保护其在运输和储存过程中的质量和安全性。
包装材料需要根据产品要求和环境条件进行选择和使用。
以上是汽车塑料件电镀工艺的主要步骤和注意事项。
在进行电镀过程中,需要严格控制各项参数和操作流程,以确保产品质量和生产效率。
同时,还需要加强质量管理和监督检查工作,及时发现和解决问题,确保生产的顺利进行。
塑料电镀件标准
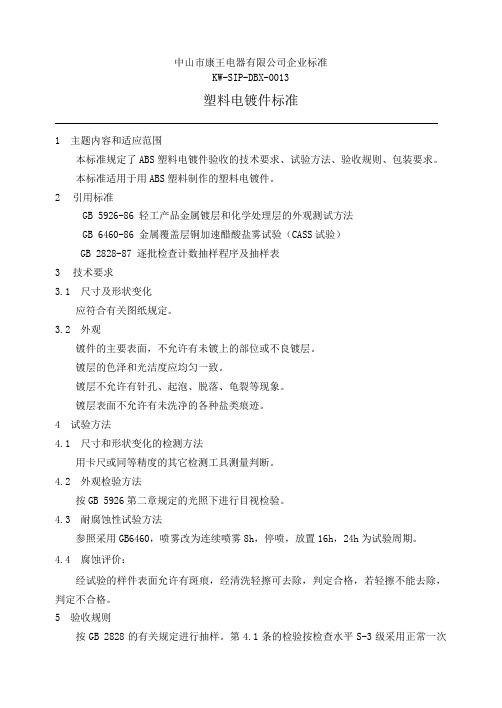
中山市康王电器有限公司企业标准KW-SIP-DBX-0013塑料电镀件标准1 主题内容和适应范围本标准规定了ABS塑料电镀件验收的技术要求、试验方法、验收规则、包装要求。
本标准适用于用ABS塑料制作的塑料电镀件。
2引用标准GB 5926-86 轻工产品金属镀层和化学处理层的外观测试方法GB 6460-86 金属覆盖层铜加速醋酸盐雾试验(CASS试验)GB 2828-87 逐批检查计数抽样程序及抽样表3技术要求3.1 尺寸及形状变化应符合有关图纸规定。
3.2 外观镀件的主要表面,不允许有未镀上的部位或不良镀层。
镀层的色泽和光洁度应均匀一致。
镀层不允许有针孔、起泡、脱落、龟裂等现象。
镀层表面不允许有未洗净的各种盐类痕迹。
4 试验方法4.1 尺寸和形状变化的检测方法用卡尺或同等精度的其它检测工具测量判断。
4.2 外观检验方法按GB 5926第二章规定的光照下进行目视检验。
4.3 耐腐蚀性试验方法参照采用GB6460,喷雾改为连续喷雾8h,停喷,放置16h,24h为试验周期。
4.4 腐蚀评价:经试验的样件表面允许有斑痕,经清洗轻擦可去除,判定合格,若轻擦不能去除,判定不合格。
5 验收规则按GB 2828的有关规定进行抽样。
第4.1条的检验按检查水平S-3级采用正常一次抽样表,AQL=4.0进行取样和判别。
第4.2条的检验按检查水平Ⅱ级,采用正常一次抽样表,AQL=0.4,进行取样和判别。
第4.3条的检验取样,批量在500件以下取3件,批量在500件以上取5件,如检验结果有1件以上不合格,判该批产品不合格。
4.3条试验连续半年合格,可改为型式试验。
除4.1、4.2条以外的试样均不能再用来装配。
6包装用PE充气薄膜袋包装。
塑料件的设计要求及电镀要求
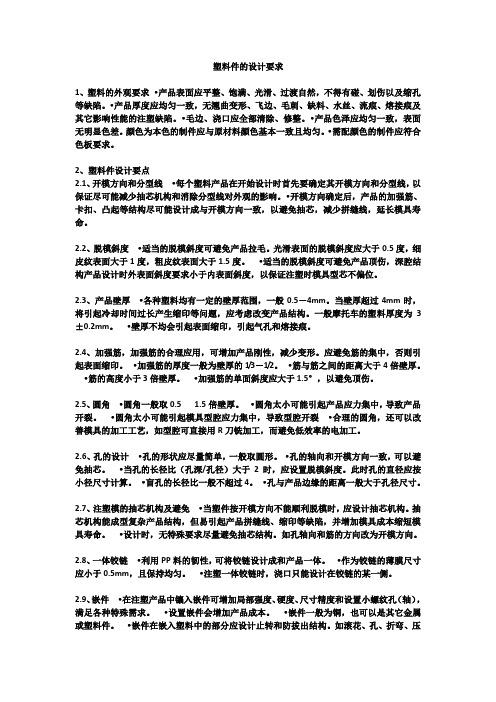
塑料件的设计要求1、塑料的外观要求•产品表面应平整、饱满、光滑、过渡自然,不得有碰、划伤以及缩孔等缺陷。
•产品厚度应均匀一致,无翘曲变形、飞边、毛刺、缺料、水丝、流痕、熔接痕及其它影响性能的注塑缺陷。
•毛边、浇口应全部清除、修整。
•产品色泽应均匀一致,表面无明显色差。
颜色为本色的制件应与原材料颜色基本一致且均匀。
•需配颜色的制件应符合色板要求。
2、塑料件设计要点2.1、开模方向和分型线•每个塑料产品在开始设计时首先要确定其开模方向和分型线,以保证尽可能减少抽芯机构和消除分型线对外观的影响。
•开模方向确定后,产品的加强筋、卡扣、凸起等结构尽可能设计成与开模方向一致,以避免抽芯,减少拼缝线,延长模具寿命。
2.2、脱模斜度•适当的脱模斜度可避免产品拉毛。
光滑表面的脱模斜度应大于0.5度,细皮纹表面大于1度,粗皮纹表面大于1.5度。
•适当的脱模斜度可避免产品顶伤,深腔结构产品设计时外表面斜度要求小于内表面斜度,以保证注塑时模具型芯不偏位。
2.3、产品壁厚•各种塑料均有一定的壁厚范围,一般0.5-4mm。
当壁厚超过4mm时,将引起冷却时间过长产生缩印等问题,应考虑改变产品结构。
一般摩托车的塑料厚度为3±0.2mm。
•壁厚不均会引起表面缩印,引起气孔和熔接痕。
2.4、加强筋,加强筋的合理应用,可增加产品刚性,减少变形。
应避免筋的集中,否则引起表面缩印。
•加强筋的厚度一般为壁厚的1/3-1/2。
•筋与筋之间的距离大于4倍壁厚。
•筋的高度小于3倍壁厚。
•加强筋的单面斜度应大于1.5°,以避免顶伤。
2.5、圆角•圆角一般取0.5 1.5倍壁厚。
•圆角太小可能引起产品应力集中,导致产品开裂。
•圆角太小可能引起模具型腔应力集中,导致型腔开裂•合理的圆角,还可以改善模具的加工工艺,如型腔可直接用R刀铣加工,而避免低效率的电加工。
2.6、孔的设计•孔的形状应尽量简单,一般取圆形。
•孔的轴向和开模方向一致,可以避免抽芯。
塑胶结构设计规范
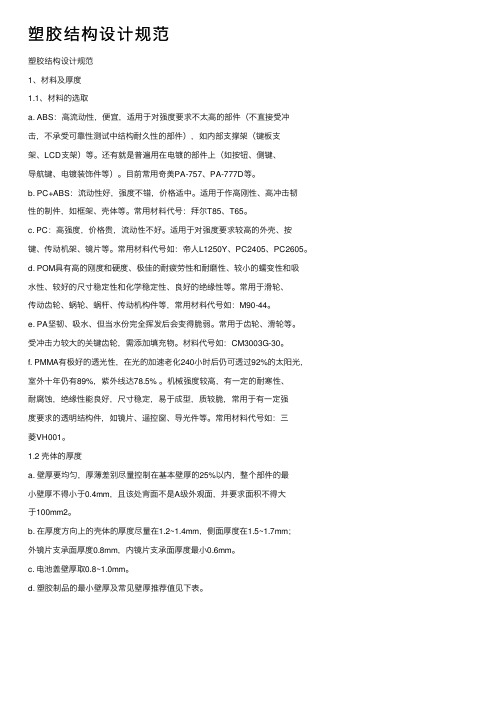
塑胶结构设计规范塑胶结构设计规范1、材料及厚度1.1、材料的选取a. ABS:⾼流动性,便宜,适⽤于对强度要求不太⾼的部件(不直接受冲击,不承受可靠性测试中结构耐久性的部件),如内部⽀撑架(键板⽀架、LCD⽀架)等。
还有就是普遍⽤在电镀的部件上(如按钮、侧键、导航键、电镀装饰件等)。
⽬前常⽤奇美PA-757、PA-777D等。
b. PC+ABS:流动性好,强度不错,价格适中。
适⽤于作⾼刚性、⾼冲击韧性的制件,如框架、壳体等。
常⽤材料代号:拜尔T85、T65。
c. PC:⾼强度,价格贵,流动性不好。
适⽤于对强度要求较⾼的外壳、按键、传动机架、镜⽚等。
常⽤材料代号如:帝⼈L1250Y、PC2405、PC2605。
d. POM具有⾼的刚度和硬度、极佳的耐疲劳性和耐磨性、较⼩的蠕变性和吸⽔性、较好的尺⼨稳定性和化学稳定性、良好的绝缘性等。
常⽤于滑轮、传动齿轮、蜗轮、蜗杆、传动机构件等,常⽤材料代号如:M90-44。
e. PA坚韧、吸⽔、但当⽔份完全挥发后会变得脆弱。
常⽤于齿轮、滑轮等。
受冲击⼒较⼤的关键齿轮,需添加填充物。
材料代号如:CM3003G-30。
f. PMMA有极好的透光性,在光的加速⽼化240⼩时后仍可透过92%的太阳光,室外⼗年仍有89%,紫外线达78.5% 。
机械强度较⾼,有⼀定的耐寒性、耐腐蚀,绝缘性能良好,尺⼨稳定,易于成型,质较脆,常⽤于有⼀定强度要求的透明结构件,如镜⽚、遥控窗、导光件等。
常⽤材料代号如:三菱VH001。
1.2 壳体的厚度a. 壁厚要均匀,厚薄差别尽量控制在基本壁厚的25%以内,整个部件的最⼩壁厚不得⼩于0.4mm,且该处背⾯不是A级外观⾯,并要求⾯积不得⼤于100mm2。
b. 在厚度⽅向上的壳体的厚度尽量在1.2~1.4mm,侧⾯厚度在1.5~1.7mm;外镜⽚⽀承⾯厚度0.8mm,内镜⽚⽀承⾯厚度最⼩0.6mm。
c. 电池盖壁厚取0.8~1.0mm。
d. 塑胶制品的最⼩壁厚及常见壁厚推荐值见下表。
塑料件电镀原理

塑料件电镀原理
塑料件电镀是一种常见的表面处理技术,它可以为塑料制品赋予金属外观和性能。
电镀工艺大致分为三个步骤:准备工作、电镀和后处理。
首先,为了确保电镀效果良好,塑料件需要进行准备工作。
这包括清洗、激活和预处理。
清洗能够去除塑料表面的污垢和油脂,以提供充足的附着力。
激活是通过化学方法在塑料表面生成能够与金属起化学反应的活性基团,提高电镀层的附着力。
预处理则是在激活后进行的,通常包括涂覆一层活性剂或底漆,以提高金属层的光滑度和均匀度。
接下来是电镀过程。
电镀是通过使用电解质溶液和电流来在塑料表面沉积金属层。
在电解质溶液中,金属离子会在电极表面还原成金属,形成金属层。
塑料件则作为工作电极,与阳极连接。
通电后,金属离子会受到吸引并沉积到塑料表面,形成金属层。
通常使用的电解质溶液有镀铜、镀镍、镀铬等。
最后是后处理。
电镀后的塑料件需要进行清洗和抛光等处理,以提高表面的光洁度和光亮度。
清洗能够去除电镀过程中产生的残留物和污垢,而抛光则能够进一步提高电镀层的光滑度和亮度。
总的来说,塑料件电镀通过准备工作、电镀和后处理三个步骤,能够使塑料表面形成金属层,从而赋予其金属外观和性能。
这一技术在汽车零部件、家电和装饰品等领域有着广泛的应用。
塑料件的设计要求及电镀要求
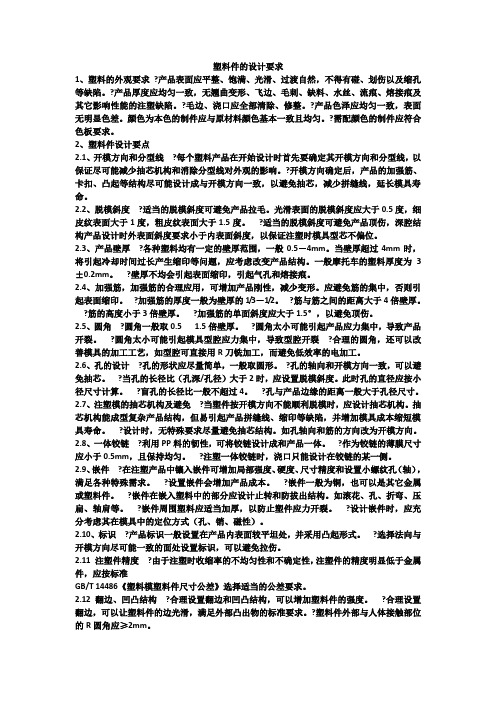
塑料件的设计要求1、塑料的外观要求?产品表面应平整、饱满、光滑、过渡自然,不得有碰、划伤以及缩孔等缺陷。
?产品厚度应均匀一致,无翘曲变形、飞边、毛刺、缺料、水丝、流痕、熔接痕及其它影响性能的注塑缺陷。
?毛边、浇口应全部清除、修整。
?产品色泽应均匀一致,表面无明显色差。
颜色为本色的制件应与原材料颜色基本一致且均匀。
?需配颜色的制件应符合色板要求。
2、塑料件设计要点2.1?每个塑料产品在开始设计时首先要确定其开模方向和分型线,以保证尽可能减少抽芯机构和消除分型线对外观的影响。
?开模方向确定后,产品的加强筋、卡扣、凸起等结构尽可能设计成与开模方向一致,以避免抽芯,减少拼缝线,延长模具寿命。
2.2?适当的脱模斜度可避免产品拉毛。
光滑表面的脱模斜度应大于0.5度,细皮纹表面大于1度,粗皮纹表面大于1.5?适当的脱模斜度可避免产品顶伤,深腔结构产品设计时外表面斜度要求小于内表面斜度,以保证注塑时模具型芯不偏位。
2.3?各种塑料均有一定的壁厚范围,一般0.5-4mm。
当壁厚超过4mm时,将引起冷却时间过长产生缩印等问题,应考虑改变产品结构。
一般摩托车的塑料厚度为3±0.2mm?壁厚不均会引起表面缩印,引起气孔和熔接痕。
2.4、加强筋,加强筋的合理应用,可增加产品刚性,减少变形。
应避免筋的集中,否则引?加强筋的厚度一般为壁厚的1/3-1/2?筋与筋之间的距离大于4倍壁厚。
?筋的高度小于3?加强筋的单面斜度应大于1.5°,以避免顶伤。
2.5?圆角一般取0.5 1.5?圆角太小可能引起产品应力集中,导致产品??合理的圆角,还可以改善模具的加工工艺,如型腔可直接用R刀铣加工,而避免低效率的电加工。
2.6?孔的形状应尽量简单,一般取圆形。
?孔的轴向和开模方向一致,可以避?当孔的长径比(孔深/孔径)大于2时,应设置脱模斜度。
此时孔的直径应按小?盲孔的长径比一般不超过4?孔与产品边缘的距离一般大于孔径尺寸。
电镀塑件模具制作及注塑要点
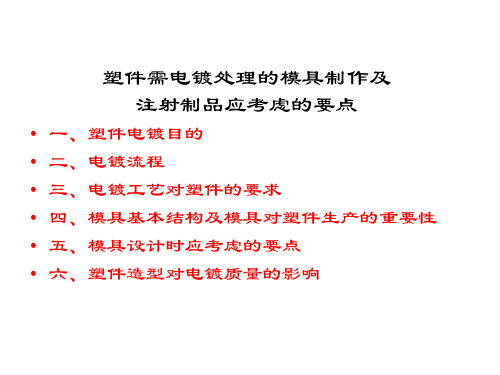
• 9、模具表面光洁度一定要比制品光洁度高1-2级, 应该抛光到镜面光泽。在不要求装饰面上,可以加工 成花纹,有利于提高镀层与基体的结合力和降低模具 的制造成本。 • 10、模具机加磨制完工后,如果有条件的话将模具表 面进行镀铬或化学镀镍磷合金层处理,这样,可以成 倍地提高模具表面的硬度和抵抗腐蚀的能力,复杂的 模具可采用化学镀镍磷合金层。 • 11、电镀上挂,挂具点标准最好采用统一标准,目前 我们的模具在产品排布上,没有形成规范,即制品与 制品之间没有标准距离,这对制作电镀挂具很麻烦, 也就是每电镀一种新制品,就需要制作新挂具,今后 在设计模具时,尽量定好统一标准。
13需要电镀的塑件一定都要有边框且边框上一定要有定位柱没有边框的制品不好用挂具生产且电镀不良14需要电镀的塑件边框上的定位柱一定要足够长各定位柱形状一致并且要设计在和制品表面同方向反之将会影响电镀表面的保护造成表面划伤等不良在塑件生产时也会影响叠放在两片产品叠放时不会接触到制品表面但在搬运过程中只要外力稍大些叠放的制品就会散落如果是电镀好的塑件散落可想而知就会造成表面划伤
• 有些塑料零件,内部有很大的槽位或螺孔,这些狭窄 而细长的孔洞对电镀时的清洗和电解的对流不利。如 果条件允许,应尽可能改成通孔。在塑料零件上,要 安排适当地工艺孔及夹具支撑点,以便于电镀件的装 架上挂。 • 关于平底凹槽、深底凹形槽、双凸棱、拱形凹槽、板 条(间隔切口)、盲孔、肋条、凸形表面圆环方筋、尖 角等奇异形状,都必需在设计时考虑电流分布,以保 证塑料零件电镀后的质量。
• 18、模具设计要考虑电镀液的节省,电镀面积和非电 镀面积(如流道,边框等)的比例应大于3:1,例如 当时我们有开过一套3887672M的模具,产品排布设计 为1出4,同样的模具日本开的产品排布为1出12,我 们1出4的产品外的流道及边框面积大,造成平均单片 的电镀成本远远高于日本模具。 • 19、模具应设计为三板式,这样塑件应力分布均匀, 不会产生电镀后应力变化的镀层脱落情况。
- 1、下载文档前请自行甄别文档内容的完整性,平台不提供额外的编辑、内容补充、找答案等附加服务。
- 2、"仅部分预览"的文档,不可在线预览部分如存在完整性等问题,可反馈申请退款(可完整预览的文档不适用该条件!)。
- 3、如文档侵犯您的权益,请联系客服反馈,我们会尽快为您处理(人工客服工作时间:9:00-18:30)。
塑料件的设计要求1、塑料的外观要求•产品表面应平整、饱满、光滑、过渡自然,不得有碰、划伤以及缩孔等缺陷。
•产品厚度应均匀一致,无翘曲变形、飞边、毛刺、缺料、水丝、流痕、熔接痕及其它影响性能的注塑缺陷。
•毛边、浇口应全部清除、修整。
•产品色泽应均匀一致,表面无明显色差。
颜色为本色的制件应与原材料颜色基本一致且均匀。
•需配颜色的制件应符合色板要求。
2、塑料件设计要点2.1、开模方向和分型线•每个塑料产品在开始设计时首先要确定其开模方向和分型线,以保证尽可能减少抽芯机构和消除分型线对外观的影响。
•开模方向确定后,产品的加强筋、卡扣、凸起等结构尽可能设计成与开模方向一致,以避免抽芯,减少拼缝线,延长模具寿命。
2.2、脱模斜度•适当的脱模斜度可避免产品拉毛。
光滑表面的脱模斜度应大于0.5度,细皮纹表面大于1度,粗皮纹表面大于1.5度。
•适当的脱模斜度可避免产品顶伤,深腔结构产品设计时外表面斜度要求小于内表面斜度,以保证注塑时模具型芯不偏位。
2.3、产品壁厚•各种塑料均有一定的壁厚范围,一般0.5-4mm。
当壁厚超过4mm时,将引起冷却时间过长产生缩印等问题,应考虑改变产品结构。
一般摩托车的塑料厚度为3±0.2mm。
•壁厚不均会引起表面缩印,引起气孔和熔接痕。
2.4、加强筋,加强筋的合理应用,可增加产品刚性,减少变形。
应避免筋的集中,否则引起表面缩印。
•加强筋的厚度一般为壁厚的1/3-1/2。
•筋与筋之间的距离大于4倍壁厚。
•筋的高度小于3倍壁厚。
•加强筋的单面斜度应大于1.5°,以避免顶伤。
2.5、圆角•圆角一般取0.5 1.5倍壁厚。
•圆角太小可能引起产品应力集中,导致产品开裂。
•圆角太小可能引起模具型腔应力集中,导致型腔开裂•合理的圆角,还可以改善模具的加工工艺,如型腔可直接用R刀铣加工,而避免低效率的电加工。
2.6、孔的设计•孔的形状应尽量简单,一般取圆形。
•孔的轴向和开模方向一致,可以避免抽芯。
•当孔的长径比(孔深/孔径)大于2时,应设置脱模斜度。
此时孔的直径应按小径尺寸计算。
•盲孔的长径比一般不超过4。
•孔与产品边缘的距离一般大于孔径尺寸。
2.7、注塑模的抽芯机构及避免•当塑件按开模方向不能顺利脱模时,应设计抽芯机构。
抽芯机构能成型复杂产品结构,但易引起产品拼缝线、缩印等缺陷,并增加模具成本缩短模具寿命。
•设计时,无特殊要求尽量避免抽芯结构。
如孔轴向和筋的方向改为开模方向。
2.8、一体铰链•利用PP料的韧性,可将铰链设计成和产品一体。
•作为铰链的薄膜尺寸应小于0.5mm,且保持均匀。
•注塑一体铰链时,浇口只能设计在铰链的某一侧。
2.9、嵌件•在注塑产品中镶入嵌件可增加局部强度、硬度、尺寸精度和设置小螺纹孔(轴),满足各种特殊需求。
•设置嵌件会增加产品成本。
•嵌件一般为铜,也可以是其它金属或塑料件。
•嵌件在嵌入塑料中的部分应设计止转和防拔出结构。
如滚花、孔、折弯、压扁、轴肩等。
•嵌件周围塑料应适当加厚,以防止塑件应力开裂。
•设计嵌件时,应充分考虑其在模具中的定位方式(孔、销、磁性)。
2.10、标识•产品标识一般设置在产品内表面较平坦处,并采用凸起形式。
•选择法向与开模方向尽可能一致的面处设置标识,可以避免拉伤。
2.11 注塑件精度•由于注塑时收缩率的不均匀性和不确定性,注塑件的精度明显低于金属件,应按标准GB/T 14486《塑料模塑料件尺寸公差》选择适当的公差要求。
2.12 翻边、凹凸结构•合理设置翻边和凹凸结构,可以增加塑料件的强度。
•合理设置翻边,可以让塑料件的边光滑,满足外部凸出物的标准要求。
•塑料件外部与人体接触部位的R圆角应≥2mm。
2.13 塑料件的焊接•焊接的种类:热板焊、超声波焊、振动焊,如:后反射器的面板与地板之间采用超声波焊接。
•采用焊接可提高联接强度。
•采用焊接可简化产品设计。
不同材料之间、复杂结构之间都可以采用焊接。
2.14 合理考虑工艺和性能之间的矛盾•设计塑料件时,必须综合考虑产品外观、性能和工艺之间的矛盾。
•有时牺牲部分工艺性,可得到很好的外观或性能。
•设计外观时,也必须充分考虑性能和工艺。
•外观是为性能服务的,不能为了外观而设计外观。
2.15 避免注塑缺陷•结构设计实在无法避免注塑缺陷时,尽可能让缺陷发生在产品的隐蔽部位。
塑料件电镀的要求塑件选材:塑料的种类很多,但并非所有的塑料都可以电镀。
有的塑料与金属层的结合力很差,没有实用价值;有些塑料与金属镀层的某些物理性质如膨胀系数相差过大,在高温差环境中难以保证其使用性能。
目前用于电镀最多的是ABS,其次是PP。
另外PSF、PC、PTFE等也有成功电镀的方法,但难度较大。
塑件造型:在不影响外观和使用的前提下,塑件造型设计时应尽量满足如下要求。
(1) 避免薄壁、不均匀壁厚。
金属光泽会使原有的缩瘪变得更明显,因此要避免制品的壁厚不均匀状况,以免出现缩瘪,而且壁厚要适中,以免壁太薄(小于1.5 mm),否则会造成刚性差,在电镀时易变形,镀层结合力差,使用过程中也易发生变形而使镀层脱落。
(2) 避免盲孔,否则残留在盲孔内的处理液不易清洗干净,会造成下道工序污染,从而影响电镀质量。
(3) 避免锐边、大平面。
电镀中的锐边会引起尖端放电,造成边角镀层隆起、锐边变厚的现象,因此应尽量采用圆角过渡,圆角半径至少0.3 mm 以上。
平板形塑件难电镀,镀件的中心部分镀层薄,越靠边缘镀层越厚,整个镀层呈不均匀状态,应将平面形改为略带圆弧面或用桔皮纹制成亚光面。
电镀的表面积越大,中心部位与边缘的光泽差别也越大,略带抛物面能改善镀面光泽的均匀性。
(4) 塑件上尽量减少凹槽和突出部位。
因为在电镀时深凹部位易露塑,而突出部位易镀焦。
凹槽深度不宜超过槽宽的1/3,底部应呈圆弧。
有格栅时,孔宽应等于梁宽,并小于厚度的1/2。
(5) 镀件上应设计有足够的装挂位置,与挂具的接触面应比金属件大2~3倍。
(6) 塑件的设计要使制件在沉陷时易于脱模,否则强行脱模时会拉伤或扭伤镀件表面,或造成塑件内应力而影响镀层结合力。
(7) 当需要滚花时,滚花方向应与脱模方向一致且成直线式.滚花条纹与条纹的距离应尽量大一些。
(8) 塑件尽量不要用金属镶嵌件,否则在镀前处理时嵌件易被腐蚀。
(9) 塑件表面应保证有一定的表面粗糙度。
模具设计:为了确保塑料镀件表面无缺陷、无明显的定向组织结构与内应力,在设计与制造模具时应满足下面要求。
(1) 模具材料不要用铍青铜合金,宜用高质量真空铸钢制造,型腔表面应沿出模方向抛光到镜面光亮,不平度小于0.2mm,表面最好镀硬铬。
(2) 电镀塑件表面如实反映模腔表面,因此模腔应十分光洁,模腔表面粗糙度应比制件表面表面粗糙度高1~2级。
(3) 分型面、熔接线和型芯镶嵌线不能设计在电镀面上。
(4) 浇口应设计在制件最厚的部位。
为防止熔料充填模腔时冷却过快,浇口应尽量大(约比普通注射模大1O%),最好采用圆形截面的浇口和浇道,浇道长度宜短一些。
(5) 应留有排气孔,以免在制件表面产生气丝、气泡等疵病。
(6) 选择顶出机构时应确保制件顺利脱模。
注射机选用:注射机选用不当,有时会因为压力过高、喷嘴结构不合适或混料使制件产生较大的内应力,从而影响镀层的结合力。
成型工艺:注塑制件由于成型工艺特点不可避免地存在内应力,但工艺条件控制得当就会使塑件内应力降低到最小程度,能够保证制件的正常使用。
相反,如工艺控制不当,就会使制件存在很大的内应力,不仅使制件强度性能下降,而且在储存和使用过程中出现翘曲变形甚至开裂,从而造成镀层的开裂,甚至脱落。
所以工艺参数的控制应使制件内应力尽可能小。
要控制的工艺条件有原材料干燥、模具温度、加工温度、注射速度、注射时间、注射压力、保压压力、保压时间、冷却时间等。
塑型后处理:由于注塑条件、注射机选择、制件造型设计及模具设计的原因,都会使塑件在不同部位不同程度地存在内应力,它会造成局部粗化不足,使活化和金属化困难,最终造成金属化层不耐碰撞和结合力下降。
试验表明,热处理和用整面剂处理都可有效地降低和消除塑件内应力,使镀层结合力提高20~60%。
非导体金属化方法(method of metalizing nonconductors)非导体电镀法须先将非导体表面形成导电化,其过程是将对象用机械或化学方法粗化(roughening)得到内锁表面(interlocking surface),然后披覆上导电镀层,其方法有:(1)青铜处理(bronzing):将金属细粉末,通常是铜粉混合粘结剂(binder),涂在对象上,然后用氰化银溶液浸镀。
(2)石墨化(graphiting):石墨粉涂在腊(wax),橡胶(rubber)及一些聚合物(polymers)上,再用硫酸铜溶液电镀。
(3)金属漆(metallic paints):将银粉与溶剂(flux)涂覆在对象上加以烧结(fire),或用硫酸铜溶液电镀。
(4)金属化(metalizing):系用化学方法形成金属覆层(metallic coating)通常是银镀层。
将硝酸银溶液及还原剂溶液如福尔马林(formaldehyde)或联胺(hydrazine)分别同时喷射在对象上得到银的表面。
从上面四种方法将非导体金属化后可用一般电镀方法做进一步处理。
非导体金属化除了电镀(electroplating)方法外还有如真空电镀(vacuum metalizing)、阴极溅射法(cathode sputtering)及金属喷射法(metal spraying)。
电镀过程和配方:(1)清洁(cleaning):去除塑料成型过程中留下的污物及指纹,可用碱剂洗净再用酸浸中和及水洗干净。
溶剂洗净:不含稀酸的洗净或中性洗净及1~2% 界面活化剂混合以40-65℃浸渍1~2分钟。
(2)溶剂处理(solvent treatment):使塑料表面能湿润(wetting)以便与下一步骤的调节剂(conditioner)作用。
溶剂处理:用丙酮、二醋甲烷,等活性剂。
(3)调节处理(conditioning):将塑料表面粗化成内锁的凹洞以使镀层密着住不易剥离,也称为化学粗化。
即化学粗化、化学刻蚀。
例1:无水铬酸cro3 20 g/l硫酸h2so4 比重1.84 600cc/l液温60℃时间15~30分;例2:无水铬酸cro3 20 g/l磷酸h3po3 100 cc/l硫酸h2so4 500 cc/l液温69℃时间10~20分。
(4)敏感化(sensitization):将还原剂吸附在表面,常用(stannous chloride)或其它锡化合物,就是sn^++离子吸附于塑料表面具有还原性表面。
敏化(sensitizing) :氯化亚锡sncl2 20~40 g/l 盐酸hcl 10~20 cc/l。