《材料成型金属学》教学资料:Chpt.7-2 冷塑性加工后金属在加热时的组织性能变化
材料成型金属学
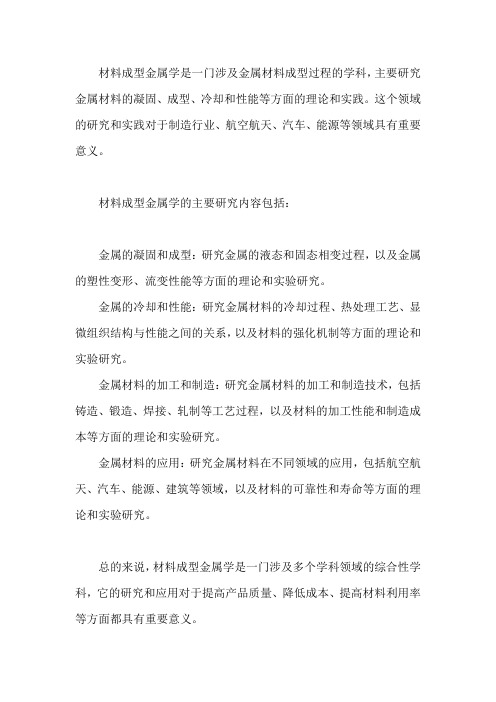
材料成型金属学是一门涉及金属材料成型过程的学科,主要研究金属材料的凝固、成型、冷却和性能等方面的理论和实践。这个领域的研究和实践对于制造行业、航空航天、汽车、能源等领域具有重要意义。
材料成型金属学的主要研究内容包括:
金属的凝固和成型:研究金属的液态和固态相变过程,以及金属的塑性变形、流变性能等方面的理论和实验研究。
金属的冷却和性能:研究金属材料的冷却过程、热处理工艺、显微组织结构与性能之间的关系,以及材料的强化机制等方面的理论和实验研究。
金属材料的加工和制造:研究金属材料的加工和制造技术,包括铸造、锻造、焊接、轧制等工艺过程,以及材料的加工性能和制造成本等方面的理论和实验研究。
金属材料的应用:研究金属材料在不同领域的应用,包括航空航天、汽车、能源、建筑等领域,以及材料的可靠性和寿命等方面的理论和实验研究。
总的来说,材料成型金属学是一门涉及多个学科领域的综合性学科,它的研究和应用对于提高产品质量、降低成本、提高材料利用率等方面都具有重要意义。
金属学与热处理课后答案
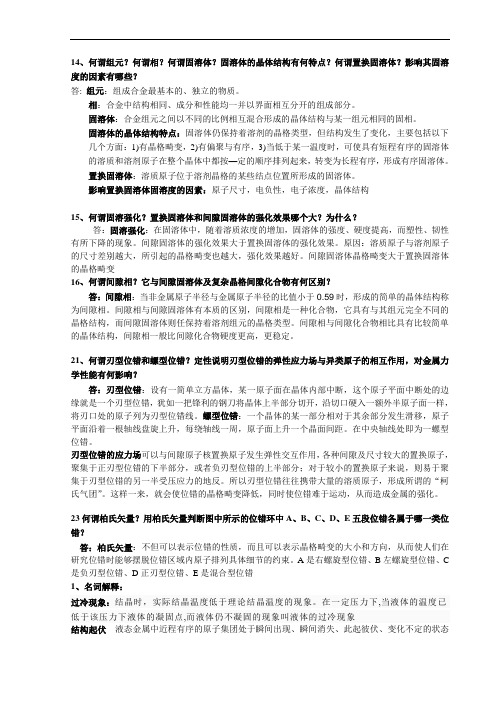
14、何谓组元?何谓相?何谓固溶体?固溶体的晶体结构有何特点?何谓置换固溶体?影响其固溶度的因素有哪些?
答: 组元:组成合金最基本的、独立的物质。
相:合金中结构相同、成分和性能均一并以界面相互分开的组成部分。
固溶体:合金组元之间以不同的比例相互混合形成的晶体结构与某一组元相同的固相。
固溶体的晶体结构特点:固溶体仍保持着溶剂的晶格类型,但结构发生了变化,主要包括以下几个方面:1)有晶格畸变,2)有偏聚与有序,3)当低于某一温度时,可使具有短程有序的固溶体的溶质和溶剂原子在整个晶体中都按—定的顺序排列起来,转变为长程有序,形成有序固溶体。
置换固溶体:溶质原子位于溶剂晶格的某些结点位置所形成的固溶体。
影响置换固溶体固溶度的因素:原子尺寸,电负性,电子浓度,晶体结构
15、何谓固溶强化?置换固溶体和间隙固溶体的强化效果哪个大?为什么?
答:固溶强化:在固溶体中,随着溶质浓度的增加,固溶体的强度、硬度提高,而塑性、韧性有所下降的现象。间隙固溶体的强化效果大于置换固溶体的强化效果。原因:溶质原子与溶剂原子的尺寸差别越大,所引起的晶格畸变也越大,强化效果越好。间隙固溶体晶格畸变大于置换固溶体的晶格畸变
16、何谓间隙相?它与间隙固溶体及复杂晶格间隙化合物有何区别?
答:间隙相:当非金属原子半径与金属原子半径的比值小于0.59时,形成的简单的晶体结构称为间隙相。间隙相与间隙固溶体有本质的区别,间隙相是一种化合物,它具有与其组元完全不同的晶格结构,而间隙固溶体则任保持着溶剂组元的晶格类型。间隙相与间隙化合物相比具有比较简单的晶体结构,间隙相一般比间隙化合物硬度更高,更稳定。
《材料成型原理》教学大纲(金属凝固原理及塑性成形原理部分,基础知识点概括,考研必备)
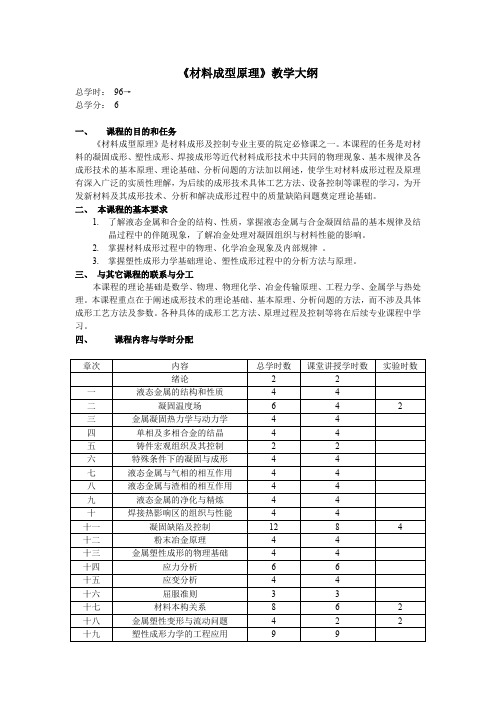
第七章 液态金属与气相的相互作用
在焊接或熔炼过程中, 液态金属会与各种气体发生相互作用, 从而对焊件或铸件的性能 产生影响。本章着重介绍各种气体的来源、气体与金属的相互作用机制、气体对金属质量的 影响以及控制气体的措施等。 § 7-1 气体的来源与产生 焊接区气体的来源与产生;铸造过程中的气体来源:熔炼过程、浇注过程、铸型反应 气相在金属中的溶解
§ 7-3
气体在金属中的析出
气体在金属中的析出的条件 § 7-4 氧化性气体对金属的氧化 金属氧化还原方向的判据:{pO2}>pO2 时,金属被氧化;{pO2}=pO2 时,处于平衡状态; {pO2}<pO2 时,金属被还原。 比较各种金属自由氧化物的分解压高低及稳定性(图 7-14) ,阐明合金元素氧化顺序及 脱氧剂的选用原则 自由氧对金属的氧化; § 7-5 气体的影响与控制
第三章 金属凝固热力学与动力学
本章主要讨论结晶过程的形核及晶体生长热力学与动力学 §3-1 凝固热力学 阐明过冷度Δ T 是影响相变驱动力的决定因素,Δ T 越大,凝固相变驱动力Δ GV 越大; K0 的定义、物理意义及“偏析系数” ∣1- K0∣; §3-2 均质形核 阐明均质形核的临界半径、形核功、形核率等概念,及其相关公式 §3-3 非均质形核 阐明非均质形核形核功;非均质形核形核条件;分析并阐明,通常情况下,接触角 远
渣体结构及碱度:分子理论与离子理论、熔渣的碱度; § 8–3 渣相的物化性质
金属材料成型基础-课件资料
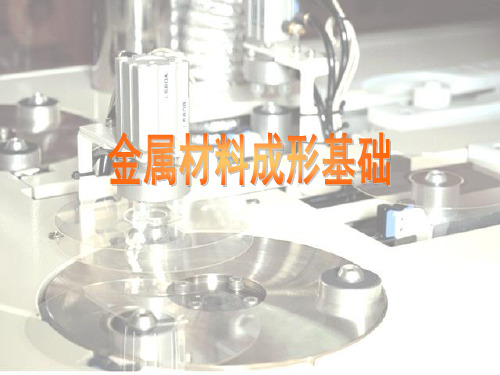
焊接热源:电弧热 溶池保护:焊剂(气、渣)
2. 埋弧自动焊工艺
1)焊前准备 板厚在20~25mm以下的工件可不开坡口;但在实际生产中, 板厚在14~22mm应开Y型坡口,板厚在22~50mm,可开 双Y型 环坡焊口缝或:U焊型丝坡起口弧。点应与环的中心偏离 一定距离a;(a=20~40mm)。直径 小于250mm一般不采用埋弧焊。 2)采取防漏措施 ①双面焊;②手工电弧焊封底;③焊剂 垫;④采用锁底坡口;⑤水冷铜垫板。
第四章 焊 接
概述
一、金属焊接成形
用加热、加压等工艺措施,使两分离表面产生原子间的结 合与扩散作用,从而获得不可拆卸接头的材料成形方法。
二、焊接成形的分类
1.熔化焊: 电弧焊(手工电弧焊、埋弧自动焊、气 体保护焊)、电渣焊、电子束焊、激光 焊、等离子弧焊等
2.压力焊: 电阻焊、摩擦焊、冷压焊、超声波焊、 爆炸焊、高频焊、扩散焊等
一、 焊接热循环
二、 焊接接头金属组织与性能的变化
焊缝区 焊接接头 焊接热影响区 1) 焊缝区 熔池金属冷却结晶所形成的 铸态组织。 2) 焊接热影响区
焊缝两侧的母材,由于焊
接热的作用,其组织和性 能发生变化的区域。
① 熔合区
是焊缝和母材金属的交界区。 (0.1-1mm)
加热温度: T液~T固
金属塑性加工学复习资料
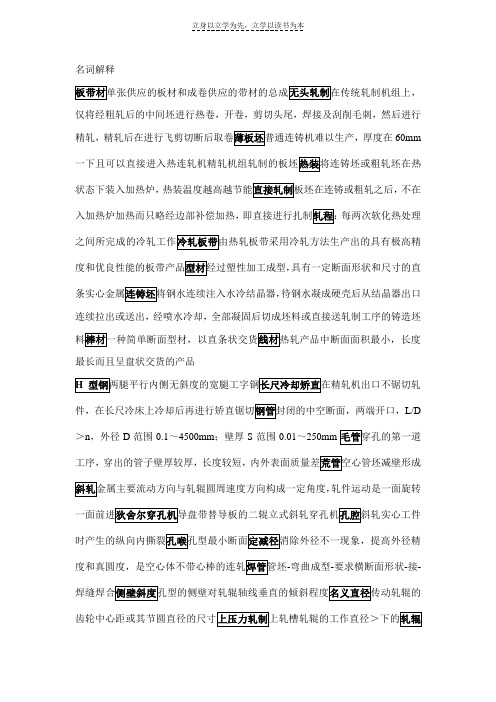
名词解释
仅将经粗轧后的中间坯进行热卷,开卷,剪切头尾,焊接及刮削毛刺,然后进行
精轧,厚度在60mm
状态下装入加热炉,不在
入加热炉加热而只略经边部补偿加热,每两次软化热处理
具有一定断面形状和尺寸的直
待钢水凝成硬壳后从结晶器出口连续拉出或送出,经喷水冷却,全部凝固后切成坯料或直接送轧制工序的铸造坯
最长而且呈盘状交货的产品
L/D
>n,外径D范围0.1~4500mm;壁厚S范围0.01~250mm
工序,穿出的管子壁厚较厚,长度较短,
轧件运动是一面旋转
-弯曲成型-要求横断面形状-接-
上下轧辊作用于轧件上的力对孔型中某一水平直线的力矩相等,
问答题
加热高温下生成氧化铁皮,不清理会产生麻点等缺陷,除鳞保证优良表面。方法:投入食盐,高温下爆破来破除;粗轧机前设置一台立辊轧机轧制侧边;高压水除
于实现全面计算控制和进行自动化生产;带钢形状简单,可成卷生产,国民经济用量大,能实现高速度的连轧生产;宽厚比和表面积都很大,故生产中轧制压力
自动调节带钢横向延伸;降低轧制压力及能耗;平直厚板型,轧出更薄的产品;调整主电机负荷;传递能量,各机间相互连接
指浪形,瓢曲或旁弯的有无及程度。缺陷:镰刀弯,浪形和瓢曲,肋状皱和眼镜。原因边部延伸
率大产生边浪,
将板卷放置于加热炉内,一边加热保温,一边轧制的方法。优点:减少钢板温降,工艺灵活;可采用钢锭作原料,适于批量不大而品种较多的产品,更适于特殊带钢。缺点:产品质量差;各项消耗高,技术经济指标低;工艺操作复杂
双机座,半连续或连续式。双机座布置:粗轧和精轧分到两个机架上去完成。特
材料学院金属成型原理PPT学习教案
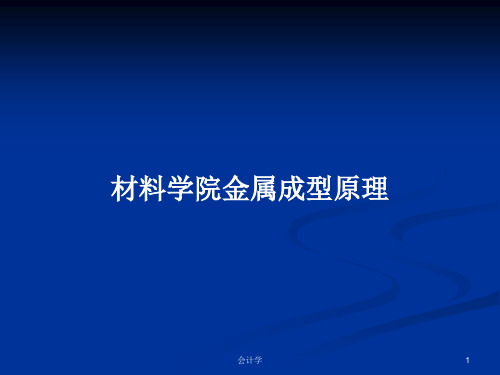
*3、原因其物理化学特性,CO2电弧 具有较 大飞溅 ,采取 各种措 施,只 能减小 其飞溅 ,难以 完全消 除飞溅 。
第2页/共30页
3
§2 CO2焊冶金特点
4
一、合金元素的氧化
CO2高温分解:
CO2
CO
+
1 2
O2
研究热点,但都不很成熟
第19页/共30页
2 0
2)活化焊丝
Cs2CO3、K2CO3,飞溅减少(正极性 ,堆焊 )
3)药芯焊丝 4)防护涂料
药芯焊丝的飞溅率是实芯焊丝的1/3左 右
焊前在工件和喷嘴上刷防护涂料,节 省清理 时间 (60~80%飞溅不会粘连)
5、改进送丝系统
脉动送丝,强制短路过渡,飞溅明显 下降。 (不成 熟)
反应生产物:
ቤተ መጻሕፍቲ ባይዱ合金元素烧损
Fe 浓度最高,氧化较剧烈
1、SiO2、MnO成杂质进入熔渣。
2、CO气体逸出到空气中。 3、FeO 一部分成为熔渣,另部分溶于液态 金属, 可能发 生如下 反应
*1、此反应若发生在熔池深部,CO来 不及逸 出,形 成气孔 。 *2、此反应若发生在熔滴中,CO高温 急剧膨 胀,大 飞溅。
材料学院金属成型原理
会计学
1
材料成型技术基础选择题

材料成形部分复习题
一、液态成形部分
(二)选择
1、形状复杂,尤其是内腔特别复杂的毛坯最适合的生产方式是( B )。
A. 锻造
B.铸造
C. 冲压
D.型材
2.合金的化学成份对流动性的影响主要取决于合金的( B )
A. 凝固点
B.凝固温度区间
C. 熔点
D.过热温度
3.下列因素中,能提高液态合金充型能力的是( C )。
A.采用金属型
B.采用凝固温度范围宽的合金
C.增加充型压力
D.降低浇注温度
4.下列因素中不影响合金的充型能力的因素是( A )
A. 造型方法
B.浇注温度
C. 合金的化学成分
D.铸件结构
5.液态金属浇注温度过高,容易使铸件产生的缺陷是( A )
A. 缩孔
B. 冷隔
C.浇不足
D.砂眼
6.铸件形成缩孔、缩孔的基本原因是由于合金的( D )
A.液态收缩
B.固态收缩
C.凝固收缩
D.液态收缩和凝固收缩
7.铸造合金的液态收缩,凝固收缩大,则铸件易产生( B )
A. 冷隔
B.缩孔、缩松
C. 浇不足
D.内应力
8.铸造合金的固态收缩大,则铸件易产生( B )
A. 冷隔
B.缩孔、缩松
C. 浇不足
D.应力、变形
9.倾向于缩松的合金成分为( B )。
A.纯金属
B.结晶温度范围宽的合金
C.共晶成分
D.逐层凝固的合金
10.糊状凝固的铸造合金缩孔倾向虽小,但极易产生( A )。
A.缩松
B. 裂纹
C.粘砂
D. 夹渣
11.铸件如有什么样的缺陷,承受气压和液压时将会渗漏( B )
A. 浇不足
B.缩松
C. 偏析
D.粘砂
12.防止铸件产生缩孔的有效措施是( A )
A.设置冒口
B. 采用保温铸型
C. 提高浇注温度
D.快速浇注
最新2塑性成型原理热成型解析教学讲义ppt
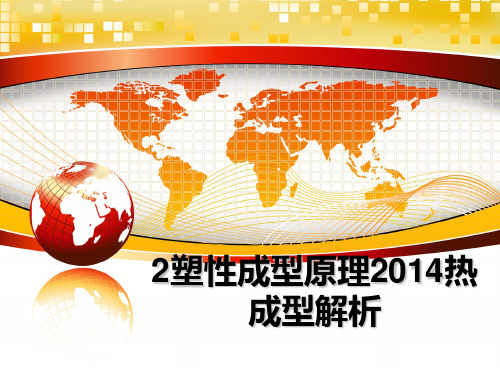
再结晶一般是指较大变形量的金属材料在随后的加热过
程中(回火,再结晶退火),严重变形的晶粒发生回复, 形核长大,形成细小的等轴晶粒,这一过程不会发生相 变,只有应变能的释放。
静态再结晶形核机制
亚晶 聚合
主 要 亚晶 有 长大 三 种
※提高金属组织致密度。 铸态金属中疏松、空隙以及微裂纹等缺陷被压实、锻合,提高 金属致密度。 ※破碎碳化物与非金属夹杂物。 碳化物破碎,均匀分布基体金属中,改善碳化物偏析。 夹杂物变形、破碎,降低其有害作用。 ※热加工产生纤维组织。 金属中存在杂质、夹杂物,沿主变形方向形成纤维组织。
热加工纤维组织
2塑性成型原理2014热 成型解析
第二章 金属塑性变形的物理基础
2.2 金属热塑性变形(一)
思考
(1)回复和再结晶特征及应用 (2)影响再结晶的因素? (3)回复和再结晶的驱动力是什么? (4)冷、热加工的区别(如何判断)?
冷变形组织
加热变形
静态再结晶
※ 进一步提高温度,晶粒的外形将发生变化,从变形的晶粒 中通过形核、长大过程重新形成等轴细晶粒,这些细晶粒 不断向周围变形金属中扩展,直到金属中变形晶粒完全消 失,这个过程称为金属的再结晶过程。
冷加工流线:指随变形度增加,晶 粒将逐渐被沿变形方向拉长,形成 条带状,被称为纤维组织。
材料成型专业练习
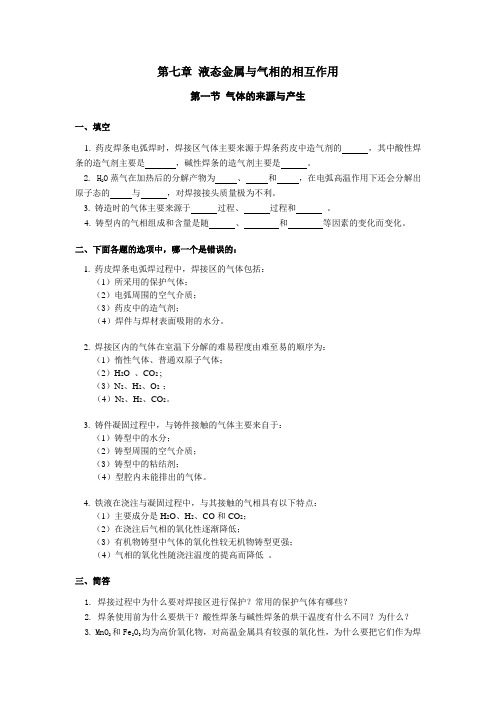
第七章液态金属与气相的相互作用
第一节气体的来源与产生
一、填空
1. 药皮焊条电弧焊时,焊接区气体主要来源于焊条药皮中造气剂的,其中酸性焊条的造气剂主要是,碱性焊条的造气剂主要是。
2. H2O蒸气在加热后的分解产物为、和,在电弧高温作用下还会分解出原子态的与,对焊接接头质量极为不利。
3. 铸造时的气体主要来源于过程、过程和。
4. 铸型内的气相组成和含量是随、和等因素的变化而变化。
二、下面各题的选项中,哪一个是错误的:
1. 药皮焊条电弧焊过程中,焊接区的气体包括:
(1)所采用的保护气体;
(2)电弧周围的空气介质;
(3)药皮中的造气剂;
(4)焊件与焊材表面吸附的水分。
2. 焊接区内的气体在室温下分解的难易程度由难至易的顺序为:
(1)惰性气体、普通双原子气体;
(2)H2O 、CO2 ;
(3)N2、H2、O2 ;
(4)N2、H2、CO2。
3. 铸件凝固过程中,与铸件接触的气体主要来自于:
(1)铸型中的水分;
(2)铸型周围的空气介质;
(3)铸型中的粘结剂;
(4)型腔内未能排出的气体。
4. 铁液在浇注与凝固过程中,与其接触的气相具有以下特点:
(1)主要成分是H2O、H2、CO和CO2;
(2)在浇注后气相的氧化性逐渐降低;
(3)有机物铸型中气体的氧化性较无机物铸型更强;
(4)气相的氧化性随浇注温度的提高而降低。
三、简答
1. 焊接过程中为什么要对焊接区进行保护?常用的保护气体有哪些?
2. 焊条使用前为什么要烘干?酸性焊条与碱性焊条的烘干温度有什么不同?为什么?
3. MnO2和Fe2O3均为高价氧化物,对高温金属具有较强的氧化性,为什么要把它们作为焊
金属学与热处理课后习题答案
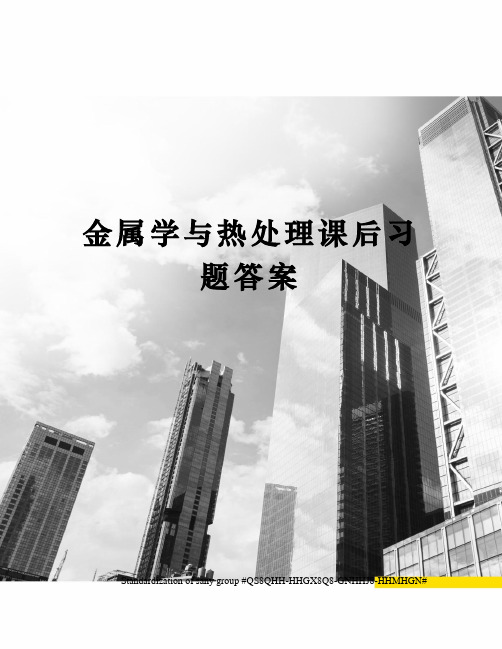
金属学与热处理课后习
题答案
Standardization of sany group #QS8QHH-HHGX8Q8-GNHHJ8-HHMHGN#
第七章金属及合金的回复和再结晶
7-1 用冷拔铜丝线制作导线,冷拔之后应如何如理,为什么
答:
应采取回复退火(去应力退火)处理:即将冷变形金属加热到再结晶温度以下某一温度,并保温足够时间,然后缓慢冷却到室温的热处理工艺。
原因:铜丝冷拔属于再结晶温度以下的冷变形加工,冷塑性变形会使铜丝产生加工硬化和残留内应力,该残留内应力的存在容易导致铜丝在使用过程中断裂。因此,应当采用去应力退火使冷拔铜丝在基本上保持加工硬化的条件下降低其内应力(主要是第一类内应力),改善其塑性和韧性,提高其在使用过程的安全性。
7-2 一块厚纯金属板经冷弯并再结晶退火后,试画出截面上的显微组织示意图。
答:解答此题就是画出金属冷变形后晶粒回复、再结晶和晶粒长大过程示意图(可参考教材P195,图7-1)
7-3 已知W、Fe、Cu的熔点分别为3399℃、1538℃和1083℃,试估算其再结晶温度。
答:
再结晶温度:通常把经过严重冷变形(变形度在70%以上)的金属,在约1h的保温时间内能够完成超过95%再结晶转变量的温度作为再结晶温度。
≈δTm,对于工业纯1、金属的最低再结晶温度与其熔点之间存在一经验关系式:T
再
金属来说:δ值为,取计算。
2、应当指出,为了消除冷塑性变形加工硬化现象,再结晶退火温度通常要比其最低再结晶温度高出100-200℃。
=,可得:
如上所述取T
再
W
=3399×=℃
再
《材料成型技术与基础》全套PPT电子课件教案-第03章 单晶体与多晶体的塑性变形等
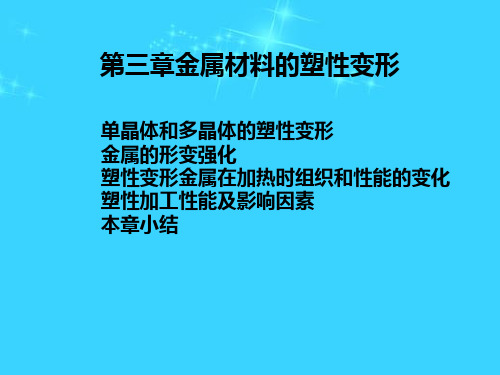
时由于正应力组成的力偶 第三章金属材料的塑性变形 (3)应力状态的影响
(2)金属组织的影响
塑性变形后的 金属加热时会
晶这一过程实质上也是一个形核和长大的过程,
晶粒取向对塑性变形的影响 维组织,具有各向异性。
(1)变形温度的影响
(2)变形速度的影响 因此,多晶体的滑移变形是分期分批进行的;
拉拔时金属应力状态
第三章金属材料的塑性变形
本章小结
锻造、轧制、挤压、冲压等都是塑性变形。这些 塑性变形的目的不仅是为了得到零件的外形和尺寸, 更重要的是为了改善金属的组织和性能。
塑性变形的主要形式是滑移和孪生,是在切应力 的作用下进行的,塑性变形将产生形变强化,形成纤 维组织,具有各向异性。塑性变形后的 金属加热时会 产生回复或再结晶及晶粒长大,其形变强化现象消除。
形变强化金属的回复和再结晶示意图
第三章金属材料的塑性变形
临界变形度 织构
晶粒长大示意图
第三章金属材料的塑性变形
在T再温度以下的塑性变形叫冷加工;T再温度以上的塑性变 形叫热加工.
冷加工产生形变强化,进一步变形困难;热加工消除了形变强 化现象,若对铸锭进行热加工,能使铸锭的气孔及缩松焊合、提高 致密度、并能细化晶粒,还能形成纤维组织.
底面*1
特点:不能用热处理方法消除 [111]*2
[110]*3
金属塑性成型复习资料
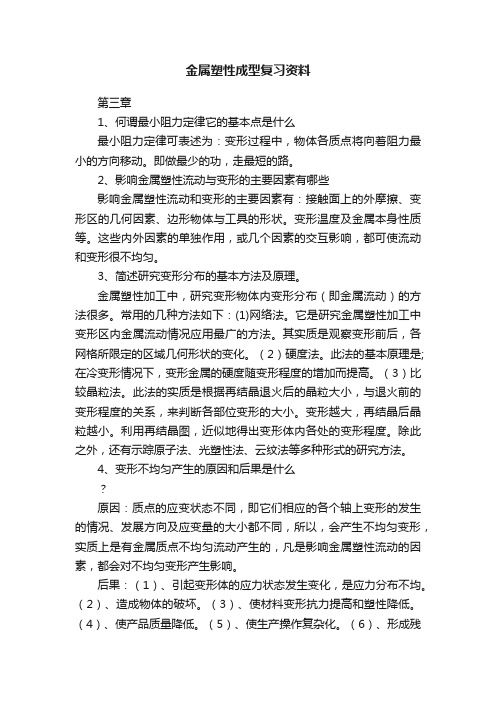
金属塑性成型复习资料
第三章
1、何谓最小阻力定律它的基本点是什么
最小阻力定律可表述为:变形过程中,物体各质点将向着阻力最小的方向移动。即做最少的功,走最短的路。
2、影响金属塑性流动与变形的主要因素有哪些
影响金属塑性流动和变形的主要因素有:接触面上的外摩擦、变形区的几何因素、边形物体与工具的形状。变形温度及金属本身性质等。这些内外因素的单独作用,或几个因素的交互影响,都可使流动和变形很不均匀。
3、简述研究变形分布的基本方法及原理。
金属塑性加工中,研究变形物体内变形分布(即金属流动)的方法很多。常用的几种方法如下:(1)网络法。它是研究金属塑性加工中变形区内金属流动情况应用最广的方法。其实质是观察变形前后,各网格所限定的区域几何形状的变化。(2)硬度法。此法的基本原理是;在冷变形情况下,变形金属的硬度随变形程度的增加而提高。(3)比较晶粒法。此法的实质是根据再结晶退火后的晶粒大小,与退火前的变形程度的关系,来判断各部位变形的大小。变形越大,再结晶后晶粒越小。利用再结晶图,近似地得出变形体内各处的变形程度。除此之外,还有示踪原子法、光塑性法、云纹法等多种形式的研究方法。
4、变形不均匀产生的原因和后果是什么
原因:质点的应变状态不同,即它们相应的各个轴上变形的发生的情况、发展方向及应变量的大小都不同,所以,会产生不均匀变形,实质上是有金属质点不均匀流动产生的,凡是影响金属塑性流动的因素,都会对不均匀变形产生影响。
后果:(1)、引起变形体的应力状态发生变化,是应力分布不均。(2)、造成物体的破坏。(3)、使材料变形抗力提高和塑性降低。(4)、使产品质量降低。(5)、使生产操作复杂化。(6)、形成残
材料成型基础 第四章 金属材料热处理 ppt课件

特点:加热速度快、时间短、 氧化脱碳少、变形小、晶粒细 小、硬度高,表面层具有较大 的残余压应力,可提高疲劳强 度。但设备昂贵。淬火前调质 或正火,淬后需低温回火。
火焰加热表面淬火
4.4钢的回火
处5
处 1 调质
5
感应
理
理
稳定化处理
6
固 7 火焰
3
溶处理;水韧处理
固溶处理和时效 8
续表4.6热处理工艺分类及代号
工艺
工艺 代
名称 代 类型 号
号
表
热
面
处 5热 2
理
处
理
工艺名称 表面淬火和回火 物理气相沉积 化学气相沉积
等离子体化学气相 沉积
代 加热 代 号 方法 号
1 电阻 4
2
3 激光 5
即临界直径D0表示。 淬透性的对应具用体零件要作具体的分析。主要考虑以下几个方面:
其一,对于截面尺寸较大和形状较复杂的重要零件以及要求力 学性能均匀的零件,应选用高淬透性的钢制造。
其二,对于承受弯曲和扭转的轴类、齿轮类零件,可选用低淬 透性的钢制造。
其三,设计和制造零件时,必须考虑钢的热处理尺寸效应。
2.回火后的组织和性能 (1)回火马氏体(250 ℃以下) (2)回火托氏体(350~450 ℃) (3)回火索氏体(500~650 ℃)
金属材料成型加工复习资料(名词解释、简答、论述)
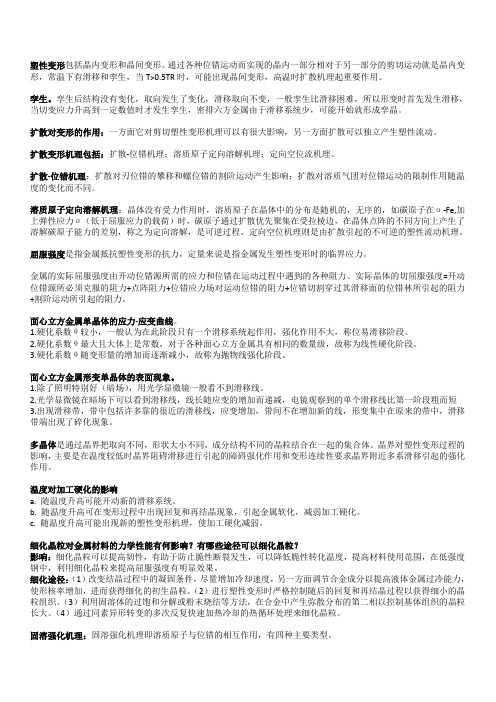
塑性变形包括晶内变形和晶间变形。通过各种位错运动而实现的晶内一部分相对于另一部分的剪切运动就是晶内变形,常温下有滑移和孪生,当T>0.5TR时,可能出现晶间变形,高温时扩散机理起重要作用。
孪生。孪生后结构没有变化,取向发生了变化,滑移取向不变,一般孪生比滑移困难,所以形变时首先发生滑移,当切变应力升高到一定数值时才发生孪生,密排六方金属由于滑移系统少,可能开始就形成孪晶。
扩散对变形的作用:一方面它对剪切塑性变形机理可以有很大影响,另一方面扩散可以独立产生塑性流动。
扩散变形机理包括:扩散-位错机理;溶质原子定向溶解机理;定向空位流机理。
扩散-位错机理:扩散对刃位错的攀移和螺位错的割阶运动产生影响;扩散对溶质气团对位错运动的限制作用随温度的变化而不同。
溶质原子定向溶解机理:晶体没有受力作用时,溶质原子在晶体中的分布是随机的,无序的,如碳原子在α-Fe,加上弹性应力σ(低于屈服应力的载荷)时,碳原子通过扩散优先聚集在受拉棱边,在晶体点阵的不同方向上产生了溶解碳原子能力的差别,称之为定向溶解,是可逆过程。定向空位机理则是由扩散引起的不可逆的塑性流动机理。
屈服强度是指金属抵抗塑性变形的抗力,定量来说是指金属发生塑性变形时的临界应力。
金属的实际屈服强度由开动位错源所需的应力和位错在运动过程中遇到的各种阻力。实际晶体的切屈服强度=开动位错源所必须克服的阻力+点阵阻力+位错应力场对运动位错的阻力+位错切割穿过其滑移面的位错林所引起的阻力+割阶运动所引起的阻力。
面心立方金属单晶体的应力-应变曲线。
1.硬化系数θ较小,一般认为在此阶段只有一个滑移系统起作用,强化作用不大,称位易滑移阶段。
金属塑性成型原理部分课后习题答案
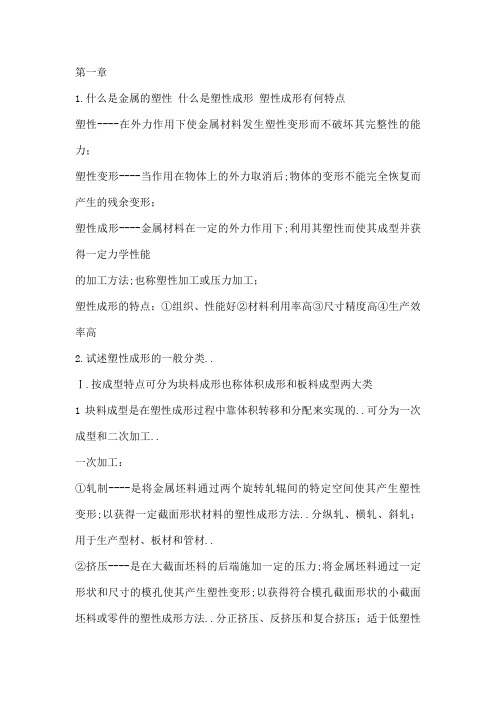
第一章
1.什么是金属的塑性什么是塑性成形塑性成形有何特点
塑性----在外力作用下使金属材料发生塑性变形而不破坏其完整性的能力;
塑性变形----当作用在物体上的外力取消后;物体的变形不能完全恢复而产生的残余变形;
塑性成形----金属材料在一定的外力作用下;利用其塑性而使其成型并获得一定力学性能
的加工方法;也称塑性加工或压力加工;
塑性成形的特点:①组织、性能好②材料利用率高③尺寸精度高④生产效率高
2.试述塑性成形的一般分类..
Ⅰ.按成型特点可分为块料成形也称体积成形和板料成型两大类
1块料成型是在塑性成形过程中靠体积转移和分配来实现的..可分为一次成型和二次加工..
一次加工:
①轧制----是将金属坯料通过两个旋转轧辊间的特定空间使其产生塑性变形;以获得一定截面形状材料的塑性成形方法..分纵轧、横轧、斜轧;用于生产型材、板材和管材..
②挤压----是在大截面坯料的后端施加一定的压力;将金属坯料通过一定形状和尺寸的模孔使其产生塑性变形;以获得符合模孔截面形状的小截面坯料或零件的塑性成形方法..分正挤压、反挤压和复合挤压;适于低塑性
的型材、管材和零件..
③拉拔----是在金属坯料的前端施加一定的拉力;将金属坯料通过一定形状、尺寸的模孔使其产生塑性变形;以获得与模孔形状、尺寸相同的小截面坯料的塑性成形方法..生产棒材、管材和线材..
二次加工:
①自由锻----是在锻锤或水压机上;利用简单的工具将金属锭料或坯料锻成所需的形
状和尺寸的加工方法..精度低;生产率不高;用于单件小批量或大锻件..
②模锻----是将金属坯料放在与成平形状、尺寸相同的模腔中使其产生塑性变形;从
材料成型基础教案-塑性成形

材料成型基础教案-塑性成形
1绪论
教学内容:金属塑性加工的定义、分类、特点、地位;本课程的性质、内容、意义、发展概况。
教学重点:
1对金属塑性加工进行定义及分类
2介绍塑性加工的特点及在国民经济中的地位
3简述了塑性加工理论的发展概况
教学难点:
1重点掌握金属塑性加工的定义
2牢记金属塑性加工的分类
3了解塑性加工在国民经济中的地位及塑性加工原理的发展概况
教学方法:
课堂教学为主,充分利用多媒体素材来表示抽象的概念。
教学要求:
重点掌握金属塑性加工的定义及对其分类,掌握塑性加工的特点及在国民经济中的地位,了解塑性加工理论的概况。
授课内容:
1.1金属塑性成形的特点及分类
1.1.1金属的塑性、塑性成形及其特点
将圆柱形试样进行拉伸实验时,拉力 P与试样伸长Δ l 之间的关系如图所示。如图可看出,当作用力P<Pe(弹性极限载荷)时进行卸载,伸长沿eo方向减小,最后伸长消失,试样恢复原来长度,这种性质称为材料弹性。当作用力
P>Ps(屈服极限载荷),例如加载到c点,然后进行卸载,则伸长随载荷的减小而沿cd方向变化(cd?eo)。卸载后,试样中保留残留变形od,这种残余变形称为塑性变形,即当作用在物体上的外力取消后,物体的变形不能完全恢复而产生的残余变形。在外力作用下使金属材料发生塑性变形而不破坏其完整性的能力称为塑性。
1
塑性材料试样拉伸时拉力与伸长之间的关系图
金属材料在一定的外力作用下,利用其塑性而使其成形并获得一定力学性能的加工方法称为塑性成形,也称塑性加工或压力加工。
金属塑性成形有如下的特点:
(1) 组织、性能好。(2)材料利用率高。(3)尺寸精度高。(4)生产效率高,
- 1、下载文档前请自行甄别文档内容的完整性,平台不提供额外的编辑、内容补充、找答案等附加服务。
- 2、"仅部分预览"的文档,不可在线预览部分如存在完整性等问题,可反馈申请退款(可完整预览的文档不适用该条件!)。
- 3、如文档侵犯您的权益,请联系客服反馈,我们会尽快为您处理(人工客服工作时间:9:00-18:30)。
退火孪晶:大部分是在一次再结晶中形成的
理想状态
⑵异常晶粒长大
二次再结晶 secondary recrystallization
再结晶后继续加热,某些晶粒吞并周围晶 粒长大,出现异常粗大晶粒,称~。
原因:第二相、杂质溶入基体金属中,晶界 迁移长大;或者再结晶织构中,个别晶粒位向 差大,易于迁移 →异常长大。
位错胞
dislocation cells (冷轧)
位错网 dislocation
network (退火初期)
位错墙 dislocation walls
亚晶界 subgrain
boundaries
Low Angle Grain Boundary -小角晶界
大角晶界
high angle boundaries
Prior strain 预应变 Schedule of anneal 退火制度 Prior grain size 初始晶粒尺寸 Impurities 杂质
预应变越大 金属纯度越低 (杂质/合金元素) 原始晶粒越细 加热速度越快 加热时间越短
晶粒细化
Grain refining
⑵再结晶织构的控制 选择适当的工艺和退火制度 适当调整化学成分 危害 :制耳 加工率↑退火温度↑制耳越严重
冷加工变形度对再结晶后晶粒大小的影响
(纯铝片拉伸)
3%
6%
9%
12%
15%
纯铁冷变形
压缩变形
20%变形
40%变形 60%变形
450℃退火
纯铁冷变形+退火
500℃退火
600℃退火
700℃退火
800℃退火
Al-Li合金的再结晶 recrystallization of Al-Li alloy
冷轧 cold rolling + 退火 annealing
形成机理: (1)定向生长
取向有利的晶核迁移快,抑制并吞并其他晶 核,形成再结晶织构。
(2)定向形核 母体具有织构,晶核与母体有一定取向关
系,因此形核长大后也形成织构。
再结晶织构的存在会引起各向异性,织构 越完整,各向异性越明显。
7.2.5 再结晶退火后金属组织 性能的控制
⑴晶粒尺寸的控制. 退火后晶粒大小d取决于: 冷变形量ε/ 退火温度T 常用再结晶图描述三者关系 ·临界变形区 ·二次再结晶区
7.3 金属在热加工中组织性能的变化
7.3.1 热加工的特点 优点 变形抗力↓塑性↑变形量↑
控制 T、ε、V、t →组织性能
缺点 尺寸精度↓表面光洁↓
与冷加工区别: 硬化(work hardening) &软化
(recovery/recrystallization)同时出现。
若相互抵消,无加工硬化效应。
高位错密度晶界迁移,亚晶长大, 成为再结晶的晶核.
变形程度较小时,大角度晶界上有一 小段弓出,晶界扫过的区域储存能释 放,可以作为再结晶晶核而长大。 -晶界弓出
再结晶温度
金属 纯铝
镍 锡
种类 99.999%
99%
合金
99.99%
99.4%
再结晶温度/℃ 85 240
320
370
630 -4
晶粒的反常长大(不均匀长大,或称为二次再结晶secondary recrystallization )
二次再结晶特征: 1. 驱动力来自界面能或表面能的降低。
2. 不需要重新形核,是以一次再结晶后的某些特殊晶粒作 为基础而长大。少数晶粒突发性地迅速发生粗化,使晶 粒间的尺寸差别显著增大。
3. 只有在晶粒正常长大受阻情况下才产生二次再结晶。 4. 也会产生择优取向的晶粒,称之为再结晶织构。
回复机制 Recovery mechanisms
Temp. Low
Intermediate
High
Mechanisms Operating
1.Migration of point defects to sinks (grain boundaries, dislocations, etc) 2.Combination of point defects
再结晶的学习意义
再结晶广泛存在于材料加工成形过程,是材料制 备过程中不可或缺的环节。
再结晶是调整组织结构的有效手段,如细化晶粒 、调整织构。尤其在没有相变的材料如纯铝、纯 镁,再结晶是改善组织的唯一途径。
再结晶形核机制
• 亚晶聚合 伴随着亚晶长大
ABC间位相差很小
A和B合并
ABC合并,形成大位相差界面
1.Rearrangement of dislocations within tangles 2.Annihilation of dislocations 3.Subgrain growth
1.Dislocation climb 2.Subgrain coalescence 3.Polygonization
高纯Fe-3Si箔材于1200℃真空中退火时所 产生的二次再结晶现象
☻粗大晶粒降低材料的力学性能。
☺硅钢片生产中,二次再结晶可获得高斯织构 {110}<001>和立方织构{100}<001>
还可以利用二次再结晶制取单晶体。
7.2.4. 再结晶织构
具有变形织构的冷加工金属,经再结晶退火后, 通常仍具有择优取向,称此为再结晶织构.与原织构 相同/不同。 冷拔铝丝<111>丝织构 500°C以下退火,织构不变 600°C以上退火,变成<112>或<210>织构
铝的再结晶图(熔点660℃)
临界变形区 不均匀变形
二次再结晶区 强烈冷变形+ 高温退火
临界变形度: 金属冷变形后再结晶时晶粒极易长得 粗大,这时所对应的应变量,称为临界变形度。 金 属材料的临界变形度一般为(2~8%)。
晶粒尺寸的控制 control of grain size
Recrystallization offers a means of controlling grain size.
热加工Fra Baidu bibliotek优缺点
优点: (1)金属的塑性好, 断裂倾向小, 可采用较大的变形量; (2)变形抗力低; (3)无需中间退火; (4)可加工室温下不能进行塑性加工的金属; (5)作为开坯, 可改善粗大的铸造组织; (6)可通过控制变形温度/速度/变形程度/冷却速度/道次间隙时间控制
组织性能。 缺点: (1)需要加热,耗能; (2)不如冷加工制品尺寸精确, 表面光洁; (3)尺寸精度不如冷加工。