电磁铸造大板坯凝固过程中热裂纹萌生机理分析
分析铸造热裂缺陷形成的原因及改进对策

分析铸造热裂缺陷形成的原因及改进对策铸造热裂缺陷是铸造过程中常见的一种缺陷形态,会对铸件的性能和质量造成重大影响。
为了解决这一问题,需要深入分析其成因,并制定改进对策。
本文将从铸造热裂缺陷的原因以及改进措施两个方面展开讨论,旨在为铸造工艺提升提供思路和指导。
一、铸造热裂缺陷的形成原因铸造热裂缺陷通常在铸件冷却过程中产生,以下是其形成的主要原因:1. 温度梯度引起的应力集中铸件冷却过程中,由于各部分温度变化不一致,会导致内部产生温度梯度,从而引起局部局部应力集中。
当材料的强度无法承受这种应力时,就会发生热裂缺陷。
2. 晶粒的收缩行为铸件在凝固过程中,晶粒会出现收缩。
若凝固过程中晶粒收缩不一致,就会引起内部应力的不平衡,从而产生热裂。
3. 液态膨胀引起的应力铸造过程中,液态金属体积较大,当其冷却凝固时,体积会缩小,引起内部应力。
若应力超过材料的承载能力,就会发生热裂缺陷。
二、改进对策为了解决铸造热裂缺陷问题,可以采取以下改进对策:1. 优化铸造工艺参数通过调整铸造温度、冷却速度以及铸件尺寸等参数,使得整个铸造过程中的温度分布更加均匀,减小温度梯度和晶粒收缩不一致性,从而减轻应力集中的程度,降低热裂的风险。
2. 控制液态膨胀行为合理控制铸造合金的成分,通过合金设计等方法来调整材料的液态膨胀行为。
降低材料在冷却凝固过程中产生的应力,减少热裂的概率。
3. 采用合适的铸型材料选择合适的铸型材料也是防止铸造热裂缺陷的关键。
材料的导热性能和热传导能力会影响铸件冷却的速度,因此在选择铸型材料时要充分考虑其导热性和热传导性能。
4. 进行合理的余热处理通过对已铸造完成的铸件进行合理的余热处理,使其内部温度均衡分布,减少应力集中和热裂的风险。
此外,适当的余热处理还能改善铸件的织构和力学性能。
5. 严格控制冷却速度合理控制冷却速度是防止铸造热裂缺陷的重要措施之一。
通过对冷却介质的选择以及冷却方式的优化,可以实现对冷却速度的有效控制,降低热裂的风险。
探讨铸造铁热裂缺陷的生成原因及对策
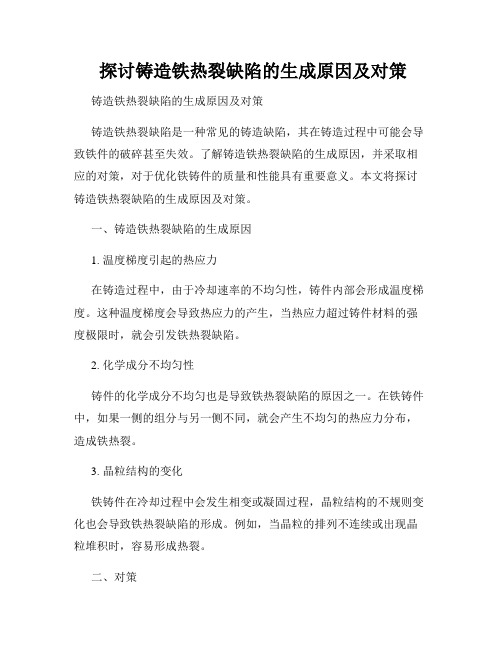
探讨铸造铁热裂缺陷的生成原因及对策铸造铁热裂缺陷的生成原因及对策铸造铁热裂缺陷是一种常见的铸造缺陷,其在铸造过程中可能会导致铁件的破碎甚至失效。
了解铸造铁热裂缺陷的生成原因,并采取相应的对策,对于优化铁铸件的质量和性能具有重要意义。
本文将探讨铸造铁热裂缺陷的生成原因及对策。
一、铸造铁热裂缺陷的生成原因1. 温度梯度引起的热应力在铸造过程中,由于冷却速率的不均匀性,铸件内部会形成温度梯度。
这种温度梯度会导致热应力的产生,当热应力超过铸件材料的强度极限时,就会引发铁热裂缺陷。
2. 化学成分不均匀性铸件的化学成分不均匀也是导致铁热裂缺陷的原因之一。
在铁铸件中,如果一侧的组分与另一侧不同,就会产生不均匀的热应力分布,造成铁热裂。
3. 晶粒结构的变化铁铸件在冷却过程中会发生相变或凝固过程,晶粒结构的不规则变化也会导致铁热裂缺陷的形成。
例如,当晶粒的排列不连续或出现晶粒堆积时,容易形成热裂。
二、对策1. 控制冷却速率为了降低铸造铁热裂缺陷的风险,可以通过控制冷却速率来减少温度梯度。
可以采用快速冷却,或者在铸造过程中采取适当的降温措施,如喷水冷却等。
2. 优化化学成分铸件化学成分不均匀会导致铁热裂缺陷的发生,因此必须对原材料进行严格的化学成分检测和控制。
确保铸造过程中铁铸件的化学成分均匀,可以减少热应力的不均匀分布。
3. 控制晶粒结构通过优化铸造工艺和控制冷却速率,可以实现更均匀的晶粒结构。
采用合适的铸造过程参数,例如浇注温度和浇注速度等,可以避免晶粒结构的变化,减少铁热裂缺陷的风险。
4. 热处理适当的热处理可以有效地解决铸造铁热裂缺陷问题。
通过热处理,可以改善晶粒结构和组织性能,减少内部应力的积累,提高铸件的抗热裂能力。
5. 检测和控制在铸造铁热裂缺陷的预防和控制过程中,必须进行严格的检测和控制。
采用先进的无损检测技术,如超声波检测、X射线检测等,可以及时发现潜在的铁热裂缺陷,并采取相应的措施进行修复或调整。
铸造变形与裂纹的原因分析【全面解析】

铸件在冷却过程中,其固态收缩受到阻碍时,就会在铸件内部产生应力,称为铸造应力,该应力是铸件产生变形、冷裂和热裂等缺陷的主要原因。
1.铸造应力的形成:铸造应力按产生原因的不同可分为热应力、相变应力和收缩应力。
(1)热应力:热应力是由于铸件壁厚不均匀,各部分的冷却速度不同,以致在同一时间内,铸件各部分收缩不一致而造成的.通常,热应力使铸件的厚壁处或心部受拉伸,薄壁处或表层受压缩.合金的固态收缩率越高、铸件的壁厚差越大,热应力也越大.预防产生热应力的基本途径是尽量减小铸件各部分的温度差,使铸件均匀地冷却.因此,设计铸件结构时,应尽量使铸件壁厚均匀,避免金属聚集,并在铸造工艺上采取必要的措施,如采取同时凝固原则.(2)相变应力:铸件各部位在不同的时间产生相变而引起的应力称为相变应力.(3)收缩应力:它是铸件收缩受到机械阻碍而形成的应力,因此又称为机械应力.形成机械阻碍的原因很多,如型砂舂得过紧,型砂或芯砂的高温强度太高、退让性差等.这种应力是暂时的,故又称为暂时应力.当机械阻碍的原因一经消失,应力即自行消失.由于铸件高温强度低,当应力超过其高温强度时,在应力集中的部位,容易产生裂纹(热裂).铸造应力是收缩应力、热应力和相变应力的综合.根据铸件的具体情况,三种应力有时互相抵消,有时互相叠加;有时是暂时存在,有时则残留下来.铸件冷却过程中所产生的铸造应力,如超过该温度下合金的屈服强度,则将产生残留变形;如超过其抗拉强度,则将产生裂纹.如在弹性强度范围内,则以残留应力的形式存在铸件内,这样就可能降低其机械强度;E——合金的弹性模量,MPa.测定铸件热处理后应力的消除程度时,可随铸件一起铸出两批应力框,其中一批不经热处理而测定其内应力值(如为σ1);另一批随铸件一起热处理,再测定其内应力值(如为σ2),应力消除的程度就可按下式算出:2.铸件的变形及其防止热应力是铸件产生变形和裂纹的内在原因.铸件的薄壁部分(或外层)冷却较快,残留有压应力,厚壁部分(或内层)冷却较慢,残留有拉应力.具有内应力的铸件处于不稳定状态,能自发地进行变形以减小内应力,使其趋于稳定状态.变形的结果将使铸件产生弯曲.细而长或大而薄的铸件,更易变形.为防止变形,应尽可能使铸件壁厚均匀或使之形状对称.对铸造工艺上应采取措施,力求使其同时凝固.有时,对长而易变形的铸件,在制模时,将木模制成与铸件变形相反的形状,用以抵消铸件产生的变形,这种方法称为反变形法.尽管铸件冷却时发生了一定的变形,但铸造应力仍难以彻底去除.经机械加工后,这些内应力将重新分布.铸件还会逐渐地发生变形,使加工后的零件丧失了应有的精度,严重影响机械产品质量.为此,不允许变形的重要铸件,必须采取自然时效或人工时效方法,将残留的内应力有效地去除.所谓人工时效是将铸件进行低温退火,它比自然时效节省时间,应用广泛.铸件的裂纹及其防止当铸造应力超过金属的强度极限时,铸件则发生裂纹.裂纹是铸件的严重缺陷,必须设法防止.1.热裂热裂是在凝固末期高温下形成的裂缝,其形状特征是裂纹短,缝隙宽,形状曲折,缝内金属呈氧化色(黄紫色).热裂是铸钢和铸铝合金件中常见的缺陷.为防止产生热裂,除了使铸件的结构设计合理外,还应合理地选择型砂或芯砂的黏结剂,以改善其退让性,大的型芯可制成中空的或内部填以焦炭.同时,应严格限制钢和铸铁中的含硫量,因为硫能增加热脆性,使合金的高温强度降低.2.冷裂冷裂是在较低温度下形成的,并常出现在受拉伸的部位,其裂缝细校呈连续直线状,缝内干净,有时呈轻微氧化色.壁厚差别大、形状复杂的铸件,尤其是大而薄的铸件容易发生冷裂.凡是减小铸造内应力或降低合金脆性的因素,均能防止冷裂的形成.钢和铸铁中,磷能显着降低合金的冲击韧性,增加脆性,因此,在熔炼金属过程中,必须对磷加以严格控制.。
分析铸造热裂缺陷形成的机理及改进措施

分析铸造热裂缺陷形成的机理及改进措施铸造热裂缺陷是铸造过程中常见的一种缺陷,它对铸件的质量和性能产生严重的影响。
了解和分析铸造热裂缺陷形成的机理,并采取适当的改进措施,对于提高铸件的质量和性能具有重要意义。
一、铸造热裂缺陷的机理分析铸造热裂缺陷的形成主要与铸造过程中的温度变化和应力积累有关。
具体的机理可以从以下几个方面进行分析:1. 温度梯度引起的热应力在铸造过程中,液态金属流注入型腔中后,由于型腔的温度梯度不均匀,会导致金属在冷却过程中产生温度梯度,从而引起不均匀的热收缩和热应力的积累。
当应力达到材料的承载极限时,就会发生裂纹的形成。
2. 金属的热固性和热收缩不匹配不同金属具有不同的热膨胀系数和热收缩系数,当金属与型腔或其他部件接触时,由于温度变化而引起的热收缩不匹配,也会导致热应力的产生。
3. 相变引起的应力集中在铸造过程中,液态金属在冷却过程中会发生相变,如固态化、固相转变等。
这些相变对金属的体积变化和应力产生有着重要影响。
当相变速率较快时,容易引起应力集中,从而形成裂纹。
二、改进措施为了减少铸造热裂缺陷的发生,可以采取以下改进措施:1. 控制铸造温度和温度梯度合理控制铸造过程中的温度和温度梯度对于减少热应力的产生具有重要作用。
可以通过调整浇注温度、冷却速度等参数来控制温度梯度的变化,减少热应力的积累。
2. 选择合适的金属材料选择具有匹配热膨胀系数和热收缩系数的金属材料,可以减少热收缩不匹配引起的应力积累。
同时,还应选择具有较好耐热性能的材料,以降低温度梯度引起的热应力。
3. 优化铸造工艺合理设计铸造工艺,采用预热、降温等措施,可以有效降低热应力的产生。
此外,还应注意避免温度梯度过大的情况,避免铸件过厚或形状复杂等导致热应力增加的问题。
4. 消除应力集中点铸造热裂缺陷的形成与应力集中有关,因此,要尽量消除或减少应力集中点。
对于已经存在的应力集中点,可以采取修补、改进设计等方式进行处理,以减少裂纹的产生。
铸钢件热裂的产生和防止

铸钢件热裂的产生和防止摘要分析了熔模铸钢件热裂产生的原因和过程,论述了防止热裂的工艺措施,并介绍了自割内浇口转移热裂及其设计方法。
关键词:熔模铸造铸钢热裂热裂是熔模铸钢件常见的缺陷之一。
随着熔模铸造的发展,复杂件、薄壁件越来越多,型壳的强度也得到了很大提高,熔模铸钢件中热裂缺陷的比例也随之上升。
如何防止热裂成了熔模铸造技术工作人员关心和棘手的问题。
1 热裂产生的原因当铸件某个部位的应力达到或超过其材质的强度极限时,铸件该部位将会产生裂纹。
铸件的裂纹分为热裂和冷裂两类。
如果裂纹是在凝固过程中形成,则此裂纹称为热裂。
热裂的裂口断面呈氧化色,裂口粗糙,其微观组织为晶间断裂。
如果裂纹是在铸件完全凝固后形成的,则此裂纹称为冷裂。
铸件在凝固时会产生较大的收缩,当此收缩受铸型的阻碍或受铸件其余部分的牵制,则会产生应力。
而铸件材质在凝固阶段的强度极限极低,因此应力很可能达到或超过其强度极限而使铸件局部产生裂纹。
如果裂纹是在凝固前期形成,而此时仍存在着较大比例的液相且具有良好的流动充填性,则裂纹被液相焊合。
但当裂纹在凝固后期形成(一般指固相率>0.7),此时固相骨架已经比较致密,所残余的液相难以充填弥合裂纹,则裂纹将会进一步发展并残留下来,热裂形成点大致在固相线附近。
热裂往往产生在铸件“弱点”部位,所谓“弱点”即铸件凝固过程中结壳最薄部位。
这些“弱点”通常是铸件壁连接的内角或浇注系统引入部位等一些局部过热部位。
热裂的产生过程大致如下:铸件凝固初期,在其平面和圆柱表面部位以及外圆角部位凝固结壳而具有了一定强度和刚度。
之后在内圆角部位也凝固结壳而具有一定强度和刚度。
同时结壳因凝固冷却而产生收缩,此时结壳将受到与其相连的铸型型壁的阻碍而产生应力,特别是铸件的突起部位。
随着凝固的进行,结壳增厚,浇注金属的比强度增大,结壳的总强度也增大。
但是由于铸型型壳受热产生膨胀、烧结而使铸件的收缩受阻增大,引起了凝固结壳中应力增大。
Q345E板坯热送产生的裂纹的形成机理研究

Q345E 板坯热送产生的裂纹的形成机理研究刘伟(天津钢铁集团有限公司技术中心,天津300301)[摘要]采用透射电镜、扫描电镜和能谱分析等方法对Q345E 板坯热送裂纹的形成机理进行了分析,研究了Q345E 铸坯热送热装工艺对板坯裂纹形成的影响,分析了轧制过程中裂纹的形成机理。
结果表明:Q345E 铸坯在热送过程中发生奥氏体向铁素体转变,在奥氏体晶界处形成先共析铁素体膜;Nb 、Ti 的碳氮化物在铁素体中析出并分布在奥氏体晶界处,造成晶界弱化;铸坯在加热炉中受热应力的作用造成Nb 、Ti 的碳氮化物析出相与先共析铁素体脱离,形成孔洞,为板坯热送裂纹的形成提供了条件。
[关键词]微合金化;铸坯;热送;裂纹;析出相Study on mechanism of hot delivery crack formation for Q345E slabLIU Wei(Technology center of Tianjin iron and steel group Co.,Ltd.,TIANJIN 300301)AbstractThe formation mechanism of hot delivery crack of Q345E slab was analyzed by means oftransmission electron microscope,scanning electron microscope and energy spectrum analysis.The effect of hot charging process of Q345E billet on crack formation of slab was studied,and the mechanism of crack formation in rolling process was analyzed.The results show that the transformation of Austenite to Ferrite occurs in Q345E billet during hot delivery,and the pre-eutectic Ferrite film is formed at the Austenite grain boundary,and the carbon nitride of Nb,Ti precipitates in the Ferrite and distributes at the Austenite grain boundary,resulting in the weakening of the grain boundary.The effect of thermal stress on the billet in the heating furnace results in the separation of the carbon and nitride precipitated phase of Nb,Ti from the proeutectic ferrite and the formation of holes,which provides the conditions for the formation of hot delivery cracks in the slab.Key words microalloying,billet,hot delivery,crack,precipitated phaseDOI:10.3969/j.issn.1006-110X.2019.04.0140引言用补热装置,将连铸坯温度保持在1100℃条件下直接送入轧机进行轧制。
铸件热裂原因
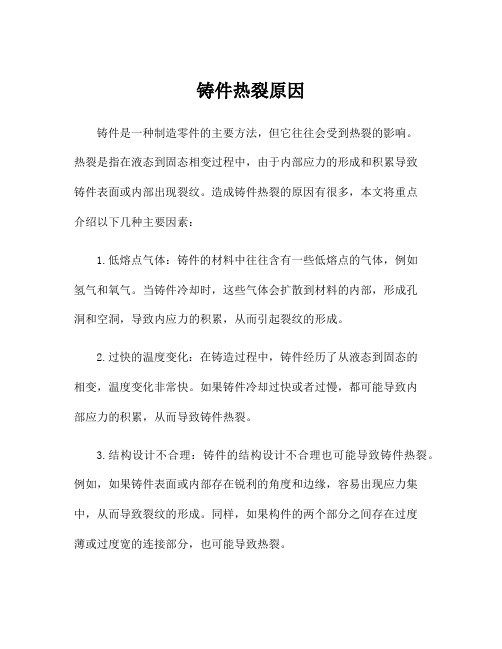
铸件热裂原因
铸件是一种制造零件的主要方法,但它往往会受到热裂的影响。
热裂是指在液态到固态相变过程中,由于内部应力的形成和积累导致
铸件表面或内部出现裂纹。
造成铸件热裂的原因有很多,本文将重点
介绍以下几种主要因素:
1.低熔点气体:铸件的材料中往往含有一些低熔点的气体,例如
氢气和氧气。
当铸件冷却时,这些气体会扩散到材料的内部,形成孔
洞和空洞,导致内应力的积累,从而引起裂纹的形成。
2.过快的温度变化:在铸造过程中,铸件经历了从液态到固态的
相变,温度变化非常快。
如果铸件冷却过快或者过慢,都可能导致内
部应力的积累,从而导致铸件热裂。
3.结构设计不合理:铸件的结构设计不合理也可能导致铸件热裂。
例如,如果铸件表面或内部存在锐利的角度和边缘,容易出现应力集中,从而导致裂纹的形成。
同样,如果构件的两个部分之间存在过度
薄或过度宽的连接部分,也可能导致热裂。
4.金属成分的变化:铸件的金属成分对铸件的热裂性能有很大的影响。
例如,硅、铜、锰等元素的含量过高,会导致内部应力的增加,从而导致铸件热裂。
5.冷却方式不适当:铸造过程中冷却方式不合理也常常是引起热裂的原因之一。
如果冷却过程中所用的冷却剂温度过低或过高,或者冷却的速度过快或过慢,都会导致铸件内部产生应力,从而引起铸件热裂。
综上所述,铸件热裂的原因复杂,需要进行全面的分析和研究。
在铸造中要避免热裂,需要在制作工艺与工作水平的不断提升上进行不断地思考和改进。
板坯内部裂纹的原因与措施
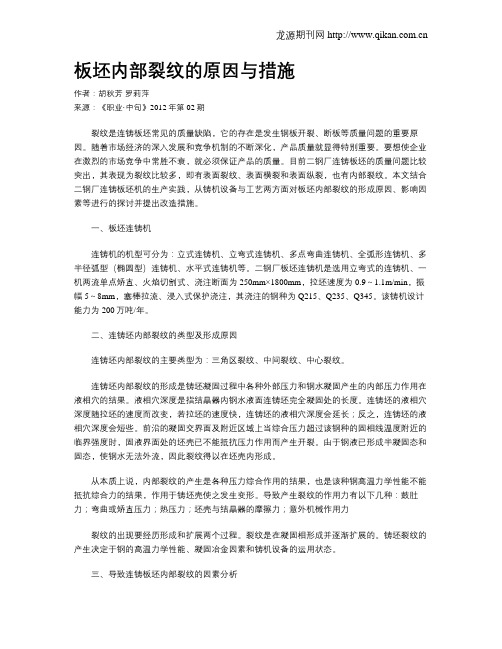
板坯内部裂纹的原因与措施作者:胡秋芳罗莉萍来源:《职业·中旬》2012年第02期裂纹是连铸板坯常见的质量缺陷,它的存在是发生钢板开裂、断板等质量问题的重要原因。
随着市场经济的深入发展和竞争机制的不断深化,产品质量就显得特别重要。
要想使企业在激烈的市场竞争中常胜不衰,就必须保证产品的质量。
目前二钢厂连铸板坯的质量问题比较突出,其表现为裂纹比较多,即有表面裂纹、表面横裂和表面纵裂,也有内部裂纹。
本文结合二钢厂连铸板坯机的生产实践,从铸机设备与工艺两方面对板坯内部裂纹的形成原因、影响因素等进行的探讨并提出改造措施。
一、板坯连铸机连铸机的机型可分为:立式连铸机、立弯式连铸机、多点弯曲连铸机、全弧形连铸机、多半径弧型(椭圆型)连铸机、水平式连铸机等。
二钢厂板坯连铸机是选用立弯式的连铸机、一机两流单点矫直、火焰切割式、浇注断面为250mm×1800mm,拉坯速度为0.9~1.1m/min,振幅5~8mm,塞棒拉流、浸入式保护浇注,其浇注的钢种为Q215、Q235、Q345。
该铸机设计能力为200万吨/年。
二、连铸坯内部裂纹的类型及形成原因连铸坯内部裂纹的主要类型为:三角区裂纹、中间裂纹、中心裂纹。
连铸坯内部裂纹的形成是铸坯凝固过程中各种外部压力和钢水凝固产生的内部压力作用在液相穴的结果。
液相穴深度是指结晶器内钢水液面连铸坯完全凝固处的长度。
连铸坯的液相穴深度随拉坯的速度而改变,若拉坯的速度快,连铸坯的液相穴深度会延长;反之,连铸坯的液相穴深度会短些。
前沿的凝固交界面及附近区域上当综合压力超过该钢种的固相线温度附近的临界强度时,固液界面处的坯壳已不能抵抗压力作用而产生开裂。
由于钢液已形成半凝固态和固态,使钢水无法外流,因此裂纹得以在坯壳内形成。
从本质上说,内部裂纹的产生是各种压力综合作用的结果,也是该种钢高温力学性能不能抵抗综合力的结果,作用于铸坯壳使之发生变形。
导致产生裂纹的作用力有以下几种:鼓肚力;弯曲或矫直压力;热压力;坯壳与结晶器的摩擦力;意外机械作用力裂纹的出现要经历形成和扩展两个过程。
铸造裂纹产生的原因和避免的措施

在所有的铸造缺陷中,对产品质量影响最大的是铸造裂纹,按照其特征可将其分为热裂纹和冷裂纹,它们是不允许存在的缺陷。
(1)热裂纹热裂纹是铸件在凝固末期或凝固结束后不久,铸件尚处于强度和塑性都很低的高温阶段,形成温度在1250~1450℃,因铸件固态收缩受阻而引起的裂纹。
热裂纹的主要特征有:•在晶界萌生并沿晶界扩展,形状粗细不均匀、曲折不规则;•通常呈龟裂的网状;•裂纹的表面呈氧化色,无金属光泽,铸钢件裂纹表面呈近似黑色;•裂纹末端圆钝,两侧有明显的氧化和脱碳,有时有明显的疏松、夹杂、孔洞等缺陷。
按照热裂纹在铸件中的形成位置,又可将其分为外裂纹和内裂纹。
•在铸件表面可以看到的热裂纹为外裂纹,外裂纹常产生在铸件的拐角或局部凝固缓慢、容易产生应力集中的位置,其特征是:表面宽,心部窄,呈撕裂状,有时断口会贯穿整个铸件断面。
•内裂纹一般发生在铸件内部最后凝固的部位,其特征是:形状不规则,裂纹面常伴有树枝晶。
通常情况下,内裂纹不会延伸到铸件表面,内裂纹的一个典型例子是冒口切除后根部所显露的裂纹。
热裂纹的形成原因可归纳为:1.浇铸冷却过程中收缩应力过大;2.铸件在铸型中收缩受阻;3.铸件冷却不均匀;4.铸件结构设计不合理,存在几何尺寸突变;5.有害杂质在晶界富集;6.铸件表面与涂料之间产生了相互作用。
(2)冷裂纹冷裂纹是铸件凝固结束后继续冷却到室温的过程中,因铸件局部受到的拉应力大于铸件本体的破断强度而引起的开裂。
冷裂纹的主要特征有:1.总是发生在承受拉应力的部位,特别是铸件形状、尺寸发生变化的应力集中部位;2.裂纹宽度均匀、细长,呈直线或折线状,穿晶扩展;3.裂纹面比较洁净、平整、细腻,有金属光泽或呈轻度氧化色;4.裂纹末端尖锐,裂纹两侧基本无氧化和脱碳,显微组织与基体的基本相同。
冷裂纹产生的原因,可归纳为:1.铸件结构系统设计不合理,铸件壁厚不均匀会导致铸造应力,有时会产生冷裂纹,刚性结构的铸件,由于其结构的阻碍,温度降低导致的收缩应力容易使铸件产生冷裂纹,薄壁大芯、壁薄均匀的铸件非常容易产生冷裂纹;2.浇冒口系统设计不合理,对于壁厚不均匀的铸件,如果内浇口设置在铸件的厚壁部分时,将使铸件厚壁部分的冷却速度更加缓慢,导致或加剧铸件各部分冷却速度的差别,增大了铸造热应力,容易使铸件产生冷裂纹,浇冒口位置设计不当时,也会直接阻碍铸件收缩,使铸件容易产生冷裂纹;3.型砂或型芯的强度太高,高温退让性差,或舂砂过紧,使铸件收缩受到阻碍,产生很大的拉应力,导致铸件产生冷裂纹;4.钢的化学成分不合格,有害元素磷含量过高,使钢的冷脆性增加,容易产生冷裂纹5.铸件开箱过早,落砂温度过高,或者在清砂时受到碰撞、挤压等都会引起铸件的开裂。
板坯角部裂纹的原因

板坯⻆部裂纹的原因⼀、引⾔板坯⻆部裂纹是⼀种常⻅的冶⾦缺陷,它发⽣在热轧板卷的⻆部位置,呈现出⼀定深度的裂纹。
这种裂纹的产⽣对产品的质量和使⽤性能产⽣了极⼤的影响,不仅影响产品的美观,⽽且降低了产品的使⽤寿命和安全性。
本⽂旨在深⼊探讨板坯⻆部裂纹产⽣的原因,并提出相应的预防措施。
⼆、板坯⻆部裂纹产⽣的原因1.原料质量:原料的化学成分、微观组织结构和冶⾦性能是影响板坯质量的关键因素。
例如,⾼碳钢、合⾦钢等材料的C、Si、Mn等元素的⽐例不当,或者夹杂物含量较⾼,都可能导致板坯⻆部裂纹的产⽣。
2.加热⼯艺:加热温度、加热速度和加热均匀性等加热⼯艺参数对板坯的⻆部裂纹也有重要影响。
如果加热温度过⾼或加热速度过快,可能导致板坯局部过热,造成内部应⼒集中,引发裂纹的产⽣。
此外,加热不均匀也会导致板坯内部应⼒分布不均,进⽽引发裂纹。
3.轧制⼯艺:轧制过程中的各种⼯艺参数,如轧制温度、轧制速度、轧制道次等,都会影响板坯的⻆部裂纹。
如果轧制温度过⾼或轧制速度过快,可能导致板坯在轧制过程中受到的应⼒过⼤,引发裂纹。
此外,轧制道次不合理也会导致板坯内部应⼒的积累,进⽽引发裂纹。
4.冷却⼯艺:冷却⼯艺也是影响板坯⻆部裂纹的重要因素。
如果冷却速度过快或冷却不均匀,可能导致板坯内部应⼒集中,引发裂纹。
5.设备状况:轧机设备的⼯作状态和精度也是影响板坯⻆部裂纹的因素之⼀。
如果轧机设备磨损严重或维护不当,可能导致轧制的板坯质量受到影响,引发裂纹。
三、预防措施针对以上产⽣原因,可以从以下⼏个⽅⾯进⾏预防:1.严格控制原料质量:对原料进⾏全⾯的质量检测,确保其化学成分、微观组织结构和冶⾦性能符合要求。
同时,加强原料的保管和运输,防⽌其受到有害元素的污染。
2.优化加热⼯艺:通过实验和模拟的⽅法,确定合理的加热温度、加热速度和加热均匀性等参数。
在⽣产过程中,加强加热设备的维护和保养,确保其正常⼯作。
3.轧制⼯艺的优化:通过实验和模拟的⽅法,确定合理的轧制温度、轧制速度和轧制道次等参数。
铸造裂纹的产生原因及种类

铸造裂纹的产生原因及种类铸造裂纹是指在铸造过程中,金属在凝固过程中出现的断裂缺陷。
它不仅会降低铸件的质量,还可能导致铸件的完全失效。
由于铸造裂纹的严重性,铸造厂必须采取一系列的措施来预防和控制裂纹的产生。
造成铸造裂纹的原因可以归结为以下几个方面:1.冷却速度过快:当金属液凝固的速度过快时,会导致铸件内部的应力积累,从而引发裂纹的产生。
这种裂纹被称为凝固裂纹。
2.热应力:当金属凝固收缩时,会产生内应力。
如果金属的强度不足以抵抗这种应力,就会发生裂纹。
3.不合理的铸造工艺:铸造过程中,如果温度、压力、冷却速度等参数的控制不当,也会导致铸造裂纹的产生。
4.金属含气量过高:金属中的气体,如氢、氧等,会导致金属的脆性增加,从而促使裂纹的产生。
5.内部缺陷:如果金属液中存在一定数量的夹杂物,如氧化物、硫化物等,也会导致裂纹的产生。
根据裂纹的形态和位置,铸造裂纹可以分为以下几种类型:1.凝固裂纹:凝固裂纹是指在金属凝固过程中形成的裂纹。
这种裂纹通常沿铸件的凝固方向延伸,形成内部裂纹。
2.热裂纹:热裂纹是指在金属冷却过程中形成的裂纹。
它通常发生在冷却速度不均匀的地方,如夹套液化井。
3.收缩裂纹:收缩裂纹是由于金属凝固收缩引起的内部应力积累。
这种裂纹通常发生在壁厚不均匀或设计不当的部位。
4.弯曲裂纹:弯曲裂纹是由于金属内部应力过大,导致铸件变形和裂纹的产生。
5.炸裂:炸裂是指由于金属液中的气体等不可溶性物质在铸件内部聚集形成气泡,而导致持续增大的内部压力,最终引发铸件的炸裂。
为了预防和控制铸造裂纹的产生,铸造厂需要采取一系列的措施:1.优化铸造工艺:合理控制金属的浇注温度、冷却速度等参数,确保金属在凝固过程中的均匀收缩。
2.提高金属质量:通过优化金属的成分和处理工艺,降低金属中的夹杂物和气体含量。
3.设计合理的铸件结构:合理设计铸件的壁厚和几何尺寸,避免出现应力集中的部位。
4.使用适当的冷却系统:采用高效的冷却系统,确保金属在冷却过程中获得均匀的温度分布。
分析铸造产生热疲劳开裂的机理及对策

分析铸造产生热疲劳开裂的机理及对策铸造产生热疲劳开裂的机理及对策随着现代工业的发展,铸造技术在各个行业中得到广泛应用。
然而,铸造过程中常常会出现热疲劳开裂的问题,严重影响产品的质量与可靠性。
因此,深入分析铸造产生热疲劳开裂的机理,并提出相应的对策,对于提高铸造产品的质量具有重要意义。
一、机理分析1.热疲劳开裂的概念热疲劳开裂是指在高温下,由于材料内部或表面的热应力积累超过其承受能力而导致的裂纹形成。
其机理可分为两个方面:一是由于局部温度的快速升降导致材料的热应力积累;二是由于材料的热膨胀系数不匹配引起的温度应力。
2.热疲劳开裂的机理热疲劳开裂的机理主要包括以下几个方面:(1)热循环:在铸造过程中,材料会经历连续的加热和冷却过程,热循环导致了材料内部应力的积累。
(2)温度梯度:铸件的不同部位会存在温度梯度,温度梯度会引起材料内部的热应力。
(3)材料热膨胀:高温下,材料发生热膨胀,不同材料的热膨胀系数差异导致温度应力的产生。
(4)晶界滑动:材料中的晶界滑动过程会增加局部应力,导致开裂。
二、对策措施要解决铸造产生热疲劳开裂的问题,可以采取以下对策措施:1.材料选择合适选择合适的铸造材料,可以降低热疲劳开裂的风险。
应选择具有良好的高温强度和抗热疲劳性能的材料,如高温合金等。
2.合理设计减小温度梯度在铸造产品的设计过程中,应尽量减小温度梯度。
可以通过优化产品的结构设计,改变铸件的形状、厚度等参数,减少温度梯度对材料的影响。
3.改善冷却方式改善冷却方式可以有效降低铸造产生热疲劳开裂的风险。
可以采用定向凝固技术、加热均匀性控制技术等方式,控制产品的冷却速率,减少热应力的积累。
4.加强工艺控制严格控制铸造工艺参数,如浇注温度、冷却时间等,可以有效降低热疲劳开裂的风险。
并可通过精细调控生产过程中的热循环和温度梯度,减少热应力的产生。
5.改进材料处理工艺合理的材料处理工艺可以提高铸造产品的抗热疲劳性能,减少开裂的风险。
探讨铸造铁合金热疲劳开裂的生成机理及对策
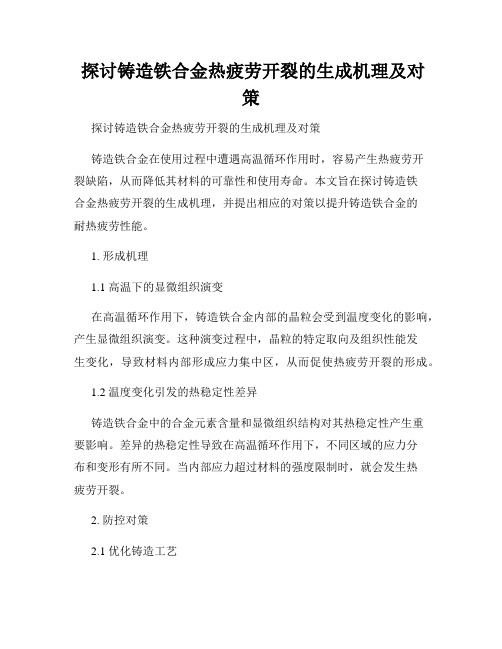
探讨铸造铁合金热疲劳开裂的生成机理及对策探讨铸造铁合金热疲劳开裂的生成机理及对策铸造铁合金在使用过程中遭遇高温循环作用时,容易产生热疲劳开裂缺陷,从而降低其材料的可靠性和使用寿命。
本文旨在探讨铸造铁合金热疲劳开裂的生成机理,并提出相应的对策以提升铸造铁合金的耐热疲劳性能。
1. 形成机理1.1 高温下的显微组织演变在高温循环作用下,铸造铁合金内部的晶粒会受到温度变化的影响,产生显微组织演变。
这种演变过程中,晶粒的特定取向及组织性能发生变化,导致材料内部形成应力集中区,从而促使热疲劳开裂的形成。
1.2 温度变化引发的热稳定性差异铸造铁合金中的合金元素含量和显微组织结构对其热稳定性产生重要影响。
差异的热稳定性导致在高温循环作用下,不同区域的应力分布和变形有所不同。
当内部应力超过材料的强度限制时,就会发生热疲劳开裂。
2. 防控对策2.1 优化铸造工艺通过控制铸造工艺参数,如浇注温度、冷却速率及退火工艺等,可以改善铸造铁合金的显微组织结构并提高热稳定性。
优化工艺有助于降低内部应力集中程度,减少热疲劳开裂的风险。
2.2 淬火过程的改进淬火过程是铸造铁合金制品获得高强度和良好韧性的重要工艺环节。
合理选择淬火介质、温度和时间等参数,可以提高材料的热稳定性和抗热疲劳开裂的能力。
2.3 优化合金设计通过调整合金元素的含量和添加合适的强化相,可以改善铸造铁合金的耐热疲劳性能。
合金设计需要综合考虑材料的显微组织演变特点以及热稳定性等因素,以达到防止热疲劳开裂的目的。
2.4 引入表面处理技术在铸造铁合金制品表面应用适当的涂层或氮化处理等技术,可以提高材料的耐高温循环疲劳的能力。
表面处理可以减轻内部应力集中,阻碍热疲劳开裂的扩展。
3. 结语铸造铁合金热疲劳开裂是一个复杂而严重的问题,对于提高铁合金材料的可靠性和使用寿命具有重要意义。
通过优化铸造工艺、改进淬火过程、优化合金设计以及引入表面处理技术等对策,可以有效预防和减轻铸造铁合金热疲劳开裂的风险,提升材料的耐高温循环疲劳性能。
探讨铸造热裂缺陷的形成原因及预防措施
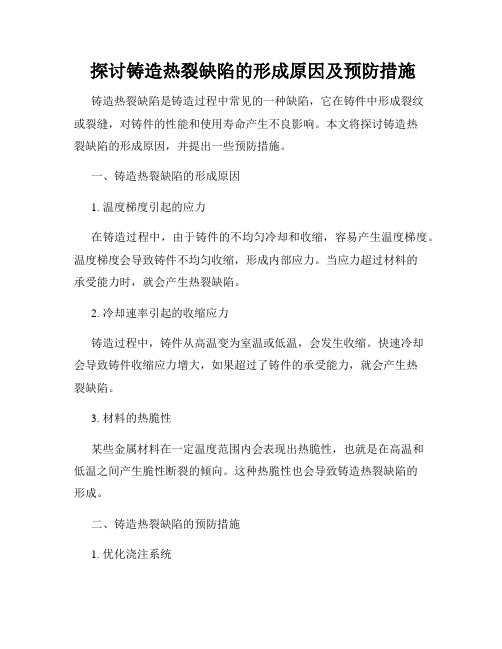
探讨铸造热裂缺陷的形成原因及预防措施铸造热裂缺陷是铸造过程中常见的一种缺陷,它在铸件中形成裂纹或裂缝,对铸件的性能和使用寿命产生不良影响。
本文将探讨铸造热裂缺陷的形成原因,并提出一些预防措施。
一、铸造热裂缺陷的形成原因1. 温度梯度引起的应力在铸造过程中,由于铸件的不均匀冷却和收缩,容易产生温度梯度。
温度梯度会导致铸件不均匀收缩,形成内部应力。
当应力超过材料的承受能力时,就会产生热裂缺陷。
2. 冷却速率引起的收缩应力铸造过程中,铸件从高温变为室温或低温,会发生收缩。
快速冷却会导致铸件收缩应力增大,如果超过了铸件的承受能力,就会产生热裂缺陷。
3. 材料的热脆性某些金属材料在一定温度范围内会表现出热脆性,也就是在高温和低温之间产生脆性断裂的倾向。
这种热脆性也会导致铸造热裂缺陷的形成。
二、铸造热裂缺陷的预防措施1. 优化浇注系统铸造过程中,合理设计浇注系统可以帮助铸件更均匀地冷却,减少温度梯度的产生。
例如,合理设置浇口、冷却器和冷却垫等措施,可以提高铸件的冷却均匀性,降低热裂缺陷的风险。
2. 控制冷却速率合理控制铸件的冷却速率可以减少收缩应力的产生。
通过改变冷却介质或调整冷却周期等方法,可以使铸件的冷却过程更加平缓,降低热裂缺陷的发生概率。
3. 选择适当的材料对于存在热脆性的金属材料,可以选择具有更好耐热性和耐脆性的材料。
例如,添加合适的合金元素,调整材料的成分,改善材料的热稳定性,从而减少热裂缺陷的风险。
4. 加强预热处理在铸造前进行适当的预热处理可以改变铸件的组织结构,提高材料的抗裂性能。
通过加热铸件,可以减轻材料内部的应力,预防热裂缺陷的生成。
5. 控制冷却过程中的应力在铸件冷却过程中,可以采取一些措施来控制应力的产生和释放,避免应力积累导致热裂缺陷。
例如,采用合适的保温措施、调整冷却速率等。
总结:铸造热裂缺陷是铸造过程中常见的一种缺陷,其形成原因主要包括温度梯度引起的应力、冷却速率引起的收缩应力以及材料的热脆性。
铸造裂纹的产生原因及种类

铸造裂纹的产生原因及种类
铸造裂纹的产生原因主要有以下几个方面:
1.材料原因:铸造材料质量不良,有夹杂物或缺陷,导致铸件强度不足,易产生裂纹。
2.工艺原因:铸造工艺控制不当,例如铸造温度不均匀、浇注方式不
正确、冷却速率不协调等都会导致铸件内部应力过大,从而产生裂纹。
3.设计原因:铸件设计不合理、结构形状复杂、壁厚过薄等都是容易
产生裂纹的原因。
铸造裂纹主要有以下几种类型:
1.热裂纹:在铸造过程中,铸件受到热应力的作用,从而产生的裂纹。
2.冷裂纹:指铸件在自然冷却过程中,由于内部应力大、冷却不均等
因素导致的裂纹。
3.拉伸裂纹:在铸件拉伸过程中,由于应力集中导致铸件表面产生的
裂纹。
4.疲劳裂纹:铸件经过长时间的载荷作用,由于应力交替的影响,会
产生裂纹。
5.焊接裂纹:铸造件经焊接后,由于热应力、冷却速率不协调等因素,容易产生的裂纹。
分析铸造Al合金热疲劳开裂的形成机理及对策

分析铸造Al合金热疲劳开裂的形成机理及对策铸造Al合金热疲劳开裂是一种严重的质量问题,对于铸件的可靠性和使用寿命具有重大影响。
本文将分析铸造Al合金热疲劳开裂的形成机理,并提出相应的对策。
一、铸造Al合金热疲劳开裂的形成机理铸造Al合金在高温下容易发生热疲劳开裂,其形成机理主要包括以下几个方面:1.热应力效应:在高温下,铸件内部由于温度梯度和热膨胀不均等原因,会产生较大的热应力,导致铸件出现应力集中区域。
当热应力超过铸件材料的承载能力时,就会引起裂纹的产生和扩展。
2.晶界氧化:在高温下,铸造Al合金晶界处容易发生氧化反应,形成氧化物。
这些氧化物会引起晶界强化和晶界脆化,导致晶界疲劳裂纹的形成和扩展。
3.热疲劳循环加载:在高温下,铸造Al合金受到热循环加载,即温度的周期性升降,这会导致铸件内部的应力不断变化,并最终引起热疲劳开裂。
二、对铸造Al合金热疲劳开裂的对策为了解决铸造Al合金热疲劳开裂的问题,可以采取以下对策措施:1.合理设计铸件结构:在铸件设计过程中,应考虑到热应力的分布情况,避免在铸件中出现应力集中区域。
合理设计铸件结构可以减少热应力的积累,降低开裂的概率。
2.优化铸造工艺参数:在铸造过程中,应优化浇注温度、浇注速度、冷却速率等工艺参数,以减少热应力和晶界氧化的产生。
合理的铸造工艺参数可以改善铸件的热疲劳性能,降低开裂风险。
3.合理选择合金元素:合金元素的添加可以改善铸造Al合金的热疲劳性能。
例如,添加少量的镁元素可以提高铝合金的热塑性和热疲劳强度,降低热疲劳开裂的风险。
4.热处理优化:通过合理的热处理工艺,可以改善铸造Al合金的晶界结构,减少晶界氧化和晶界脆化的发生。
同时,热处理还可以通过调整组织结构,提高材料的抗热疲劳性能。
5.应力消除处理:在铸造Al合金后,可以进行应力消除处理,通过加热和冷却过程调整铸件的内部应力分布,降低开裂的风险。
6.增加铸件表面保护层:在高温环境下,为铸件增加一层保护层,可以减少铸件的氧化反应,延缓晶界氧化的发生。
铸坯中间裂纹诊断模型的开发

铸坯中间裂纹诊断模型的开发随着工业的发展,铸造技术逐渐成为工业生产的重要环节之一。
铸造技术的关键在于铸坯的制造,而铸坯的质量直接影响到最终产品的质量。
因此,如何在铸造过程中及时发现铸坯中的缺陷,尤其是中间裂纹,成为了铸造技术研究的重点之一。
本文将介绍一种铸坯中间裂纹诊断模型的开发。
一、铸坯中间裂纹的形成原因铸坯中间裂纹是指在铸坯的内部形成的裂纹。
铸坯中间裂纹的形成原因有很多,主要包括以下几个方面:1. 温度差异:铸造过程中,铸坯的不同部位温度有所不同,这会导致铸坯内部产生温度差异,从而产生内应力,最终导致中间裂纹的形成。
2. 热应力:铸坯在冷却过程中会产生热应力,如果热应力超过了铸坯材料的强度限制,就会导致中间裂纹的形成。
3. 金属流动不畅:铸坯在铸造过程中,如果金属流动不畅,就会在铸坯内部形成空洞或夹杂物,从而导致中间裂纹的形成。
4. 铸造工艺不合理:铸造工艺不合理也会导致铸坯中间裂纹的形成,例如浇注温度过高或过低、铸造过程中的压力不合适等。
二、铸坯中间裂纹的诊断方法铸坯中间裂纹的诊断方法有很多,常用的方法包括:1. 目视检查法:目视检查法是最简单、最直观的一种方法,只需要用肉眼观察铸坯表面是否有裂纹即可。
但是,这种方法只能检测到铸坯表面的裂纹,无法检测到铸坯内部的裂纹。
2. X射线检测法:这种方法可以检测到铸坯内部的裂纹,但是设备昂贵,操作复杂,且对工作环境要求较高。
3. 超声波检测法:超声波检测法是一种非接触式的检测方法,可以检测到铸坯内部的裂纹,且设备价格相对较低,但是对技术人员的要求较高。
三、铸坯中间裂纹诊断模型的开发为了解决以上诊断方法的不足,我们可以开发一种铸坯中间裂纹诊断模型,该模型可以通过铸坯表面的图像信息,预测铸坯内部是否存在裂纹。
该模型的开发步骤如下:1. 数据采集:首先,我们需要采集大量的铸坯表面图像,同时记录每张图像对应的铸坯内部是否存在裂纹的信息。
2. 特征提取:接下来,我们需要从每张图像中提取出一些特征,例如颜色、纹理、边缘等。
锻造和热处理过程中裂纹形成原因分析

锻造和热处理过程中裂纹形成原因分析【摘要】:在进行锻造与热处理的过程中,裂纹的出现是很常见的事情,在所有的锻造与热处理的过程中,不可能不出现裂纹。
这就让裂纹在锻造这个行业中成为了一种讨论的焦点。
构件的尺寸大小,材质质地的不同,裂纹的出现几率也不同,裂纹的出现种类不同,裂纹出现的形状不同。
在本文中主要进行锻造和热处理过程中产生裂纹的原因进行研究。
在本文中通过大量对资料的收集进行了产生裂纹原因的阐述,也进行了防止裂纹产生举措的提出,对于减少构件在锻造和热处理的过程中出现裂纹带来了很大的帮助。
【关键词】:锻造裂纹;折叠裂纹;淬火裂纹引言裂纹是在锻造和热处理过程中产生的常见缺陷之一,也是锻造行业研究讨论的热点、难点。
而大型锻件出现裂纹的概率更高,因而对锻造和热处理过程中产生的裂纹进行研究,分析裂纹产生原因,对于减少产品裂纹具有十分重要的意义。
1.锻造缺陷与热处理缺陷1.1过热、过烧主要特征是晶粒粗大,有明显的魏氏组织。
出现过烧说明加热温度高、断口晶粒粗大,凹凸不平,无金属光泽,晶界周围有氧化脱碳现象。
1.2锻造裂纹常产生于组织粗大,应力集中处或合金元素偏析处,裂纹内部常充满氧化皮。
锻造温度高,或者终端温度低,都容易产生裂纹。
还有一种裂纹是锻造后喷水冷却后形成的。
1.3折叠冲孔、切料、刀板磨损、锻造粗糙等原因造成了表面缺陷,在后续锻造时,将表面氧化皮等缺陷卷入锻件本体内而形成折缝。
在显微镜上观察时,可发现折叠周围有明显脱碳。
1.4淬裂其特点是刚健挺直,呈穿晶分布,起始点较宽,尾部细长曲折。
此种裂纹多产生于马氏体转变之后,故裂纹周围的显微组织与其它区域无明显区别,也无脱碳现象。
1.5软点显微组织有块状或网状屈氏体和未溶铁素体等。
加热不足,保温时间不够,冷却不均匀都会产生软点。
2.实验方法对锻造和热处理裂纹附近的显微组织进行晶相分析,有助于了解裂纹形成的内在原因,也是裂纹鉴别的重要依据。
试验采用实际生产的杆类件作为研究对象,对其裂纹附近组织进行晶相分析。
铸钢件热裂纹的成因与对策分析
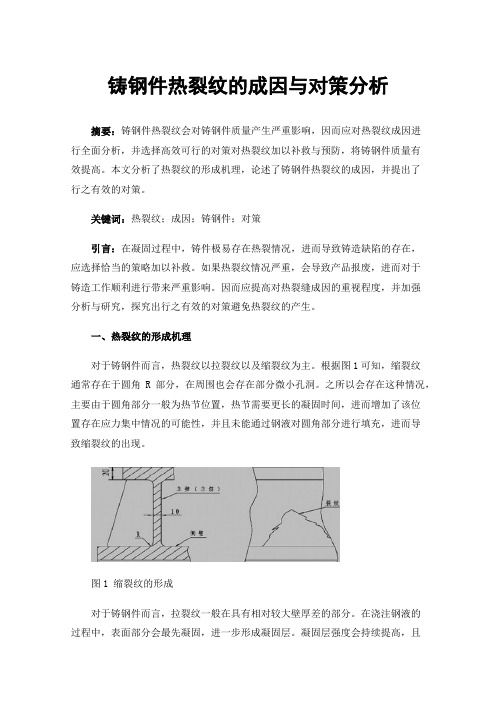
铸钢件热裂纹的成因与对策分析摘要:铸钢件热裂纹会对铸钢件质量产生严重影响,因而应对热裂纹成因进行全面分析,并选择高效可行的对策对热裂纹加以补救与预防,将铸钢件质量有效提高。
本文分析了热裂纹的形成机理,论述了铸钢件热裂纹的成因,并提出了行之有效的对策。
关键词:热裂纹;成因;铸钢件;对策引言:在凝固过程中,铸件极易存在热裂情况,进而导致铸造缺陷的存在,应选择恰当的策略加以补救。
如果热裂纹情况严重,会导致产品报废,进而对于铸造工作顺利进行带来严重影响。
因而应提高对热裂缝成因的重视程度,并加强分析与研究,探究出行之有效的对策避免热裂纹的产生。
一、热裂纹的形成机理对于铸钢件而言,热裂纹以拉裂纹以及缩裂纹为主。
根据图1可知,缩裂纹通常存在于圆角R部分,在周围也会存在部分微小孔洞。
之所以会存在这种情况,主要由于圆角部分一般为热节位置,热节需要更长的凝固时间,进而增加了该位置存在应力集中情况的可能性,并且未能通过钢液对圆角部分进行填充,进而导致缩裂纹的出现。
图1 缩裂纹的形成对于铸钢件而言,拉裂纹一般在具有相对较大壁厚差的部分。
在浇注钢液的过程中,表面部分会最先凝固,进一步形成凝固层。
凝固层强度会持续提高,且逐渐构建出枝晶骨架时,因温度相对较低,会导致骨架存在收缩情况,并且由于铸件有着相对较大的厚薄差值,难以确保各部分收缩的一致性[1]。
与此同时,由于型芯具有一定的阻碍作用,导致在收缩时会形成一定的拉应力。
如果拉应力超过金属断裂强度的时候,就会导致拉裂纹的存在。
二、铸钢件热裂纹的成因铸钢件热裂纹通常在铸件凝固糊状部分,如果液体在即将凝固时会存在应力抵触以及收缩等情况,进而导致热裂纹的存在。
例如,某T型热节如图2所示,a部分为在型腔内浇注钢液时,由于钢液存在收缩与流动现象,进而导致氧化膜存在卷入以及折叠等情况。
b部分为基于高温条件下,因反应形成的气体,再加上夹杂因素而产生界面层。
c部分为凝固环节,因收缩问题导致微小变形,基于阻碍作用下产生的应力超过材料具体断裂强度的时候,会造成微裂纹。