第六章半导体器件工艺学之刻蚀1
半导体刻蚀工艺

半导体刻蚀工艺
半导体刻蚀工艺是一种用于制作半导体器件的技术,目的是把半导体材料削减成特定形状和尺寸,以便制作出各种复杂的集成电路元件,如晶体管、存储器、晶体管级数等。
刻蚀工艺的主要流程是:首先,将半导体块放置在刻蚀槽里,然后使用大量的高压水流来冲刷掉表面的污垢和不需要的部分。
接着,将一种可以溶解或腐蚀半导体材料的化学物质加入到槽内,当这种物质与半导体材料发生反应时,就会持续地将半导体材料腐蚀掉,慢慢地削减出特定的形状和尺寸,以制作出不同的元件。
最后,将由刻蚀工艺制造出的半导体元件放置在晶圆上,然后经过烧蚀、清洗和其他过程,即可完成制作半导体器件的整个工序。
(第六章)刻蚀讲解

End of etch
2. 刻蚀剖面
刻蚀剖面是指被刻蚀图形的侧壁形状 两种基本的刻蚀剖面: 各向同性和各向异性刻蚀剖面
Isotropic etch - etches in all directions at the same rate
Resist
Film Substrate
湿法各向同性化学腐蚀
Anisotropic etch - etches in only one direction
Resist Film Substrate
具有垂直刻蚀剖面的 各向异性刻蚀
湿法刻蚀和干法刻蚀的侧壁剖面
刻蚀类型 侧壁剖面 湿法腐蚀 各向同性
示意图
各向同性(与设备和参数有关)
干法刻蚀
各向异性 (与设备和参数有关) 各向异性– 锥形
第六章 刻蚀
6.1 引 言
刻蚀的概念: 用化学或物理的方法有选择地去除硅片表面层材料的 工艺过程称为刻蚀。
刻蚀示意图:
Photoresist mask
Photoresist
Film
mask
to be etched
Protected film
(a) Photoresist-patterned substrate
干法刻蚀的缺点(与湿法腐蚀比) 1. 对下层材料的刻蚀选择比较差 2. 等离子体诱导损伤 3. 设备昂贵
干法刻蚀过程
1. 刻蚀气体进入反应腔 2. RF电场使反应气体分解电离 3. 高能电子、离子、原子、自由基等结合产生等离子体 4. 反应正离子轰击表面-各向异性刻蚀(物理刻蚀) 5. 反应正离子吸附表面 6. 反应元素(自由基和反应原子团)和表面膜的表面反
③达到一定的负电荷数量后电子会被电极排斥,产生 一个带正离子电荷的暗区(即离子壳层);
半导体制造工艺刻蚀
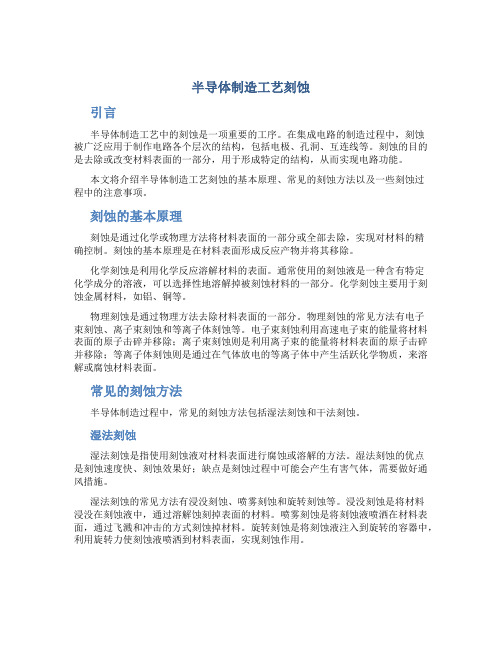
半导体制造工艺刻蚀引言半导体制造工艺中的刻蚀是一项重要的工序。
在集成电路的制造过程中,刻蚀被广泛应用于制作电路各个层次的结构,包括电极、孔洞、互连线等。
刻蚀的目的是去除或改变材料表面的一部分,用于形成特定的结构,从而实现电路功能。
本文将介绍半导体制造工艺刻蚀的基本原理、常见的刻蚀方法以及一些刻蚀过程中的注意事项。
刻蚀的基本原理刻蚀是通过化学或物理方法将材料表面的一部分或全部去除,实现对材料的精确控制。
刻蚀的基本原理是在材料表面形成反应产物并将其移除。
化学刻蚀是利用化学反应溶解材料的表面。
通常使用的刻蚀液是一种含有特定化学成分的溶液,可以选择性地溶解掉被刻蚀材料的一部分。
化学刻蚀主要用于刻蚀金属材料,如铝、铜等。
物理刻蚀是通过物理方法去除材料表面的一部分。
物理刻蚀的常见方法有电子束刻蚀、离子束刻蚀和等离子体刻蚀等。
电子束刻蚀利用高速电子束的能量将材料表面的原子击碎并移除;离子束刻蚀则是利用离子束的能量将材料表面的原子击碎并移除;等离子体刻蚀则是通过在气体放电的等离子体中产生活跃化学物质,来溶解或腐蚀材料表面。
常见的刻蚀方法半导体制造过程中,常见的刻蚀方法包括湿法刻蚀和干法刻蚀。
湿法刻蚀湿法刻蚀是指使用刻蚀液对材料表面进行腐蚀或溶解的方法。
湿法刻蚀的优点是刻蚀速度快、刻蚀效果好;缺点是刻蚀过程中可能会产生有害气体,需要做好通风措施。
湿法刻蚀的常见方法有浸没刻蚀、喷雾刻蚀和旋转刻蚀等。
浸没刻蚀是将材料浸没在刻蚀液中,通过溶解蚀刻掉表面的材料。
喷雾刻蚀是将刻蚀液喷洒在材料表面,通过飞溅和冲击的方式刻蚀掉材料。
旋转刻蚀是将刻蚀液注入到旋转的容器中,利用旋转力使刻蚀液喷洒到材料表面,实现刻蚀作用。
干法刻蚀干法刻蚀是指利用气体等离子体或物理方法对材料表面进行刻蚀的方法。
干法刻蚀的优点是刻蚀过程中不产生液体,可以避免污染问题;缺点是刻蚀速度较慢。
干法刻蚀的常见方法有等离子体刻蚀、离子束刻蚀和电子束刻蚀等。
等离子体刻蚀是通过在气体放电的等离子体中产生活跃化学物质,来溶解或腐蚀材料表面。
半导体刻蚀工艺简介PPT

除了Cl和F的气体外,溴化氢(HBr)也是一种常用的气 体,因为在小于0.5µm的制程中,栅极氧化层的厚度将小 于10 nm,用HBr等离子体时多晶硅/ SiO2的刻蚀选择比 高于以Cl为主的等离子体。
在本作业中,将介绍现今较为常用的刻蚀设备。
1.反应离子刻蚀机
反应离子刻蚀机系统中包含了一个高真空的反应腔, 腔内有两个呈平行板状的电极,一个电极与腔壁接地,另 一个电极则接在射频产生器上,如图7-2(a)所示。这种刻 蚀系统对离子有加速作用,使离子以一定的速度撞击待刻 薄膜,因此刻蚀过程是物理与化学反应的共同进行。
刻蚀分三步进行:
①刻蚀剂扩散至待刻材料的表面;
②刻蚀剂与待刻材料反应;
③反应产物离开刻蚀表面扩散至溶液当中,随溶液排出。 缺点:湿法刻蚀多是各向同性的,在将图形转移到硅片上 时,刻蚀后会向横向发展,这会造成图形失真,不适合得 到3µm以下的线宽。
要控制湿法刻蚀的速率,通常可通过改变溶液浓度和 反应温度等方法实现。溶液浓度增加会加快湿法刻蚀时反 应物到达及离开被刻蚀薄膜表面的速率,反应温度可以控 制化学反应速率的大小。选择一个湿法刻蚀的工艺,除了 刻蚀溶液的选择外,也应注意掩膜是否适用。
化学性刻蚀
又称等离子体刻蚀,是利用等离子体将刻蚀气体电离 并形成带电离子、分子及反应性很强的原子团,它们扩散 到被刻蚀薄膜表面后与被刻蚀薄膜的表面原子反应生成具 有挥发性的反应产物,并被真空设备抽离反应腔。因这种 反应完全利用化学反应,故称为化学性刻蚀。
第06章 刻蚀

(2)干法腐蚀能达到高的分辨率,湿法腐蚀较差
(3)湿法腐蚀需大量的腐蚀性化学试剂,对人体和环境有害 (4)湿法腐蚀需大量的化学试剂去冲洗腐蚀剂剩余物,不经济
湿法各向同性化学腐蚀
各向同性刻蚀是在各方向上 以同样的速率进行刻蚀 胶
膜
衬底
干法刻蚀
• 干法刻蚀与湿法腐蚀相比的优点 • 刻蚀反应
干法刻蚀与湿法腐蚀相比的优点
7. 不会腐蚀金属.
VLSI/ULSI 技术中的复合金属层
钨的反刻
通孔
SiO2 ILD-2 金属1 复合层 ILD-1
钨
(a) 通孔刻穿 ILD-2 (SiO2)层 钨塞 SiO2 金属2复合层 钨塞
(b) 钨 CVD 通孔填充
(c) 钨反刻
(d) 金属2 淀积
去胶机中氧原子与光刻胶的反应
顺流等离子体 1) O2 分子进入反 应腔
湿法腐蚀需大量的化学试剂去冲洗腐蚀剂剩余物不经济各向同性刻蚀是在各方向上以同样的速率进行刻蚀衬底刻蚀剖面是各向异性具有非常好的侧壁剖面控制cd控制反应正离子轰击表面原子团与表面膜的表面反应副产物的解吸附各向异性刻蚀各向同性刻蚀溅射的表面材料化学刻蚀物理刻蚀衬底刻蚀反应腔电场使反应物分解反应离子吸附在表面反应正离子轰击表面排气气体传送rf发生器副产物电子和原子结合产生等离子体副产物解吸附阴极阳极电场各向异性刻蚀各向同性刻化学干法等离子体刻蚀和物理干法等离子体刻蚀usedprimarilyetchbackoperations
膜
衬底
具有垂直刻蚀剖面的各向异性刻蚀
各向异性刻蚀是仅在一 个方向刻蚀
胶 膜 衬底
湿法腐蚀和干法刻蚀的剖面
刻蚀中的钻蚀和过刻蚀
钻蚀 光刻胶 过刻蚀 膜 衬底
半导体制造工艺刻蚀

成本压力
随着半导体制造工艺的不 断升级,刻蚀技术的成本 也在不断攀升,需要寻找 更经济可行的解决方案。
环保问题
刻蚀过程中会产生废气、 废液等污染物,对环境造 成一定影响,需要加强环 保处理措施。
未来发展方向与趋势
纳米级刻蚀技术
未来刻蚀技术将向纳米级 发展,进一步提高刻和精度,未来将 得到更广泛的应用。
溅射刻蚀原理
物理过程
溅射刻蚀利用高能粒子轰击被刻蚀材料 表面,使表面原子或分子获得足够能量
后以高速溅射出来。
优点
溅射刻蚀具有高刻蚀速率和低损伤特 点。
化学过程
溅射过程中,被刻蚀材料表面原子或 分子与气体反应气体发生化学反应, 生成挥发性物质。
缺点
溅射刻蚀过程中可能会对材料表面造 成损伤,且难以实现高选择性和高分 辨率刻蚀。
04
刻蚀技术应用
微电子领域应用
微电子领域是刻蚀技术应用最广泛的领域之一。在制造集成电路、微处理器、晶 体管等元器件时,刻蚀技术用于形成电路、隔离区域和电极接触等结构。
刻蚀技术能够精确控制材料的去除过程,实现高精度、高效率的加工,从而提高 电子元器件的性能和可靠性。
纳米科技领域应用
随着纳米科技的不断发展,刻蚀技术也在这一领域发挥着 重要作用。在制造纳米材料、纳米器件和纳米结构时,刻 蚀技术用于形成纳米级别的图案和结构。
其他领域应用
除了上述领域外,刻蚀技术还广泛应 用于太阳能电池、生物医学工程、航 空航天等领域。在这些领域中,刻蚀 技术用于制造特定结构和功能的元件 ,提高产品的性能和可靠性。
VS
随着技术的不断进步和应用领域的拓 展,刻蚀技术的应用前景将更加广阔 。
05
刻蚀技术发展前景与挑战
半导体器件工艺学之刻蚀

下游式刻蚀系统
离子束铣( Ion Milling) 是近年来发展较快的一种离 子剥离技术。该技术主要利用携带能量的离子轰 击靶材料所产生的物理溅射刻蚀效应
离子刻蚀速率表示如下: dh( H) / dt = R( H) / cos(H) = R( H) [ 1 + tan2( H) ]1/2
当离子束入射的角度较大时, 材料表面反射的离子束也增 多。因此, 随着角度H的增大 , 越来越少的离子渗入到材 料的有效表面。为保证离子 的有效渗入, 定义临界角Hc 。 离子束的溅射场与靶材料的 原子数Z 有关, 材料的原子数 Z 越高, 刻蚀速率越高; 反之 则越低。
本产品通过物理与化学相结合的方法,对很细的线条(亚微米以下)进行刻 蚀以形成精细的图形。 主要用于微电子、光电子、通讯、微机械、新材料、能源等领域的器件 研发和制造。
深层反应离子刻蚀(DRIE)
系统己经足以刻蚀深宽比超过50 的深槽硅结构,对于光阻的刻蚀 选择比己超过100:1,刻蚀深度均 匀度也可以控制在±3%以内。
中微发布Primo D-RIE刻蚀设备,面向22 纳米及以下工艺
中微半导体设备(上海)有限公司(以下简称“ 中微”)日前发布面向22纳米及以下芯片生产 的第二代300毫米甚高频去耦合反应离子刻 蚀设备--Primo AD-RIE。 2011年7月
Primo AD-RIE在促进中微第一代刻蚀设备技术创 新的同时,又大大扩大了其自身的加工领域。 该设备的主要部分是一组创新的少量反应台反应 器的簇架构,可以灵活地装置多达三个双反应台 反应器,以达到最佳芯片加工输出量。每个反应 器都可以实现单芯片或双芯片加工。独特的反应 器腔体设计融合了中微专有的等离子体聚焦和喷 淋头技术,确保了芯片加工的质量。Primo ADRIE的一些基本特征使其更具备28纳米以下关键刻 蚀加工的能力
半导体工艺原理--刻蚀工艺
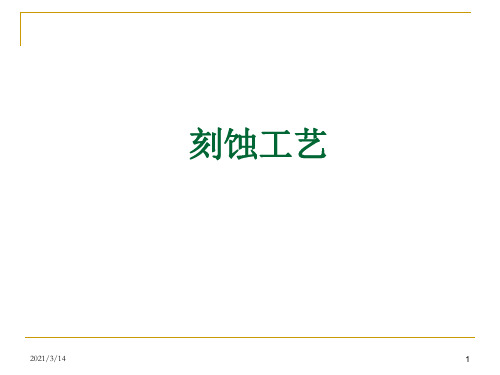
注释
对硅有选择性,对硅腐蚀速率很慢,腐蚀速率依赖于 膜的密度,掺杂等因素
是纯HF腐蚀速率的1/20,腐蚀速率依赖于膜的密度, 掺杂等因素,不像纯HF那样使胶剥离
Si3N4
HF(49%) HPO:HO(沸点:130-150℃)
Al
H3PO4:H2O:HNO3:CH3COOH(16:2:1:
1)
多晶硅 单晶硅
2021/3/14
34
其刻蚀分为两步,首先是要除去未被光刻胶保护 的硅化金属,可以采用CF4、SF6、Cl2、HCl2等都 可以用来作为硅化金属的RIE的反应气体。
对多晶硅的刻蚀采用氟化物将导致等方向性的刻 蚀,而Polycide 的刻蚀必须采用各向异性,因此采 用氯化物较好,有 Si, HCL2, SiCl4等。
2 A l 6 H 3 P O 4 2 A l( H 2 P O 4 ) 3 3 H 2
高锰酸钾腐蚀液的配方为:
K M n O 4 :N a O H :H 2 O 6 g :1 0 g :9 0 m l
高锰酸钾与铝的反应式
N a O H
K M n O 4A l K A lO 2M n O 2
22
湿法刻蚀剖面
2021/3/14
23
SiO2 的腐蚀
SiO24HFSiF42H2O SiF42HFH2(SiF6)
氟化铵在SiO2 腐蚀液中起缓冲剂的作用。这种加有氟化铵 的氢氟酸溶液,习惯上称为HF缓冲液。 常用的配方为:
HF:NH4F:H2O = 3ml:6g:10ml
2021/3/14
24
HNO3:H2O:HF(CH3COOH)(50:20:1)
HNO3:H2O:HF(CH3COOH)(50:20:1) KOH:HO:IPA(23wt%KOH,13wt%IP
半导体工艺第六章

第六章习题6-1 解释欧姆接触,并说明形成欧姆接触的常用方法。
欧姆接触是指金属与半导体之间的电压与电流的关系具有对称和线性关系,而且接触电阻尽可能低,不产生明显的附加阻抗。
常用方法:扩散法和合金法扩散法:是在半导体中先扩散形成重掺杂区以获得N+N或P+P的结构,然后使金属与重掺杂的半导体区接触,形成欧姆接触。
合金法:是利用合金工艺对金属互联线进行热处理,使金属与半导体界面形成一层合金层或化合物层,并通过这一层与表面重掺杂的半导体形成良好的欧姆接触。
6-2 列出并描述集成电路制造中对金属薄膜的要求。
要求:(1)具有高的导电率和纯度(2)与下层衬底(通常是二氧化硅或氮化硅)具有良好的粘附性(3)与半导体材料连接时接触电阻低(4)能够淀积出均匀而且没有“空洞”的薄膜,易于填充通孔(5)易于光刻和刻蚀,容易制备出精细图形(6)很好的耐腐蚀性(7)在处理和应用过程中具有长期的稳定性6-3 列出半导体制造中使用的金属种类,并说明每种金属的用途。
种类:铝、铝铜合金、铜、阻挡层金属、硅化物和钨铝:作为金属互连的材料,以薄膜的形式在硅片中连接不同器件。
铝铜合金:有效解决电迁徙问题。
铜:作为互连线。
阻挡层金属:防止上下层材料相互扩散。
硅化物:减小接触电阻。
钨:填充通孔。
6-4 解释铝已被选择作为微芯片互连金属的原因。
(1)较低的电阻率(2)铝价格低廉(3)工艺兼容性(4)铝膜与下层衬底(通常是硅、二氧化硅或氮化硅)具有良好的粘附性6-5 哪种金属已经成为传统互连金属线?什么是它的取代物?铝已经成为传统互连金属线,铝铜合金是它的取代物6-6 描述结尖刺现象,如何解决结尖刺问题?由于硅在铝中的溶解度比较高,形成合金时,硅会从衬底向铝中溶解,这样就在接触区下层的硅中留下空洞,从而有可能发生尖刺效应。
解决方法:在接触区引入阻挡层金属可阻止上下层材料互相混合。
6-7 描述电迁徙现象,如何解决电迁徙现象?电迁徙现象:在大电流密度的情形下,大量电子对金属原子的持续碰撞,会引起原子逐渐而缓慢的移动。
第六章 光刻与刻蚀工艺
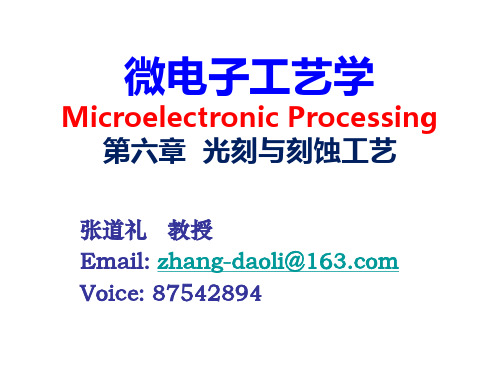
Microelectronic Processing 第六章 光刻与刻蚀工艺
张道礼 教授 Email: zhang-daoli@ Voice: 87542894
6.1 概述
微电子单项工艺
掺杂 薄膜制备 图形转移
扩散掺杂 离子注入掺杂 物理气相淀积 化学气相淀积
外延 光刻 刻蚀
6.1 概述
图形转移(pattern transfer)是微电子工艺的重要基础,其作 用是使器件和电路的设计从图纸或工作站转移到基片上得以实现, 我们可以把它看作是一个在衬底上建立三维图形的过程,包括光刻 和刻蚀两个步骤。
光刻 (lithography,又译图形曝光 ):使用带有某一层设计几 何图形的掩模版(mask),通过光化学反应,经过曝光和显影,使光 敏的光刻胶在衬底上形成三维浮雕图形。将图案转移到覆盖在半导 体晶片上的感光薄膜层上(称为光致光刻胶、光刻胶或光阻,resist, 简称光刻胶)的一种工艺步骤。
正胶 ><
>< 断链
8.2 光刻工艺
负胶是一种含有感光剂的聚合物。曝光时,感光剂将吸收的光 能转变为化学能而引起链反应,聚合物分子间发生交联,形成不 溶于显影液的高分子交联聚合物。显影后,未感光部分的光刻胶 被去除。负胶的主要缺点是显影时吸收显影液溶剂而膨胀,限制 了其分辨率。
负胶
交联
8.2 光刻工艺
刻蚀:在光刻胶掩蔽下,根据需要形成微图形的膜层不同,采 用不同的刻蚀物质和方法在膜层上进行选择性刻蚀。
这样,去掉光刻胶以后,三维设计图形就转移到了衬底的相关 膜层上。图形转移工艺是如此重要,以至一种微电子工艺技术的水 平通常以光刻和刻蚀的图形线宽(特征尺寸)表示。
8.2 光刻工艺
第六章半导体器件工艺学之刻蚀

刻蚀方式: 等离子刻蚀: 等离子刻蚀: 利用放电产生的游离基与材料发生化学反应,形 成挥发物,实现刻蚀。选择性好、对衬底损伤较 小,但各向异性较差 溅射与离子束铣蚀: 溅射与离子束铣蚀: 通过高能惰性气体离子的物理轰击作用刻蚀,各 向异性性好,但选择性较差 反应离子刻蚀(RIE) (RIE): 反应离子刻蚀(RIE): 通过活性离子对衬底的物理轰击和化学反应双重 作用刻蚀。具有溅射刻蚀和等离子刻蚀两者的优 点,同时兼有各向异性和选择性好的优点。目前, RIE已成为VLSI工艺中应用最广泛的主流刻蚀技术。 RIE已成为VLSI工艺中应用最广泛的主流刻蚀技术。
多晶硅栅
在多晶硅栅刻蚀中不期望的微槽
单晶硅槽
三、金属刻蚀
高刻蚀速率(大于1000nm/min) 高刻蚀速率(大于1000nm/min) 对下层的高选择比,对掩膜层(>4 对下层的高选择比,对掩膜层(>4:1)和层 间介质(>20: 间介质(>20:1) 高的均匀性,CD控制很好,没有微负载效应 高的均匀性,CD控制很好,没有微负载效应 没有等离子体诱导充电带来的器件损伤 残留物污染少 不会腐蚀金属
二、硅的刻蚀
主要是制作MOS栅结构的多晶硅栅和制作 主要是制作MOS栅结构的多晶硅栅和制作 器件隔离或DRAM电容结构中的单晶硅槽 器件隔离或DRAM电容结构中的单晶硅槽 多晶硅栅的刻蚀工艺必须对下层栅氧化层 有高的选择比并具有非常好的均匀性和可 重复性,同时要求高度的各向异性 单晶硅刻蚀主要用于制作沟槽,如器件隔 离沟槽或DRAM中高密度的垂直电容的制作。 离沟槽或DRAM中高密度的垂直电容的制作。 在高密度IC中要求数百万个沟槽具有一致 在高密度IC中要求数百万个沟槽具有一致 的光洁度,接近的垂直侧壁,正确的深度 和圆滑的沟槽顶角和底角
半导体刻蚀技术简介终稿

一、等离子体刻蚀技术的产生:在积体电路制造过程中,常需要在晶圆上定义出极细微尺寸的图案,这些图案主要的形成方式,乃是藉由刻蚀技术,将微光刻后所产生的光阻图案忠实地转印至光阻下的材质上,以形成积体电路的复杂架构。
因此蚀刻技术在半导体制造过程中占有极重要的地位。
广义而言,所谓的蚀刻技术,包含了将材质整面均匀移除及图案选择性部份去除的技术。
而其中大略可分为湿式蚀刻与干式蚀刻两种技术。
早期半导体制程中所采用的蚀刻方式为湿式蚀刻,即利用特定的化学溶液将待蚀刻薄膜未被光阻覆盖的部分分解,并转成可溶于此溶液的化合物后加以排除,而达到蚀刻的目的。
湿式蚀刻的进行主要是藉由溶液与待蚀刻材质间的化学反应,因此可藉由调配与选取适当的化学溶液,得到所需的蚀刻速率,以及待蚀刻材料与光阻及下层材质良好的蚀刻选择比(选择性)。
然而,随着积体电路中的元件尺寸越做越小,由于化学反应没有方向性,因而湿式蚀刻是各向同性的,此时,当蚀刻溶液做纵向蚀刻时,侧向的蚀刻将同时发生,进而造成咬边现象,导致图案线宽失真。
因此湿式蚀刻在次微米元件的制程中已被干式蚀刻所取代。
干式蚀刻通常指利用辉光放电方式,产生包含离子,电子等带电粒子及具有高度化学活性的中性原子与分子及自由基的电浆来进行图案转印的蚀刻技术。
由部份解离的气体及等量的带正,负电荷粒子所组成的等离子体被称为电浆。
蚀刻用的电浆中,气体的解离程度很低,其中所含的气体具高度的活性,它是利用外加电场的驱动而形成,并且会产生辉光放电现象。
自1970年代以来元件制造首先开始采用电浆蚀刻技术,对于电浆化学新的了解与认知也就蕴育而生。
在现今的积体电路制造过程中,必须精确的控制各种材料尺寸至次微米大小且具有极高的再制性,而由于电浆蚀刻是现今技术中唯一能极有效率地将此工作在高良率下完成,因此电浆蚀刻便成为积体电路制造过程中的主要技术之一。
影响电浆蚀刻特性好坏的因素包括了:1)电浆蚀刻系统的型态,2)电浆蚀刻的参数; 3)前制程相关参数,如光阻,待蚀刻薄膜之沉积参数条件,待蚀刻薄膜下层薄膜的型态及表面的平整度等。
光刻与刻蚀工艺

张道礼 教授 Email: zhang-daoli@ Voice: 87542894
微电子工艺学
6.1 概述
扩散掺杂 掺 杂 离子注入掺杂 物理气相淀积 微电子单项工艺 薄膜制备 化学气相淀积
外 延
光 图形转移 刻 蚀 刻
6.1 概述
在集成电路制造中,主要的光刻设备是利用紫外光(≈0.2~ 0.4m)的光学仪器。 刻蚀:在光刻胶掩蔽下,根据需要形成微图形的膜层不同,采 用不同的刻蚀物质和方法在膜层上进行选择性刻蚀。 这样,去掉光刻胶以后,三维设计图形就转移到了衬底的相关 膜层上。图形转移工艺是如此重要,以至一种微电子工艺技术的水 平通常以光刻和刻蚀的图形线宽(特征尺寸)表示。
8.2 光刻工艺
光刻胶的性能参数
a. 光学性质:如灵敏度、分辨率、对比度、折射率;
b. 力学和化学性质 :如固溶度、黏滞度、抗蚀性、热稳定性、流 动性和对环境气氛的敏感度;
c. 其它性质:如纯度、金属含量、可使用范围、有效期和燃点;
一、分辨率 分辨率是指每毫米宽度内能够光刻出可分辨的最多线对数,它 是对光刻工艺可以达到的最小图形尺寸的一种描述。在线宽 L 与 线条间距相等的情况下,分辨率为:R 1 (mm 1 ) ,光刻分辨率受 2L 光刻系统、光刻胶和光刻等多方面因素影响。
+
_ 显影后的理想光刻胶剖面
_
8.2 光刻工艺
Imin
Imax
另一个可以从对比度中得到的光刻胶性能指标是调制传输函 I max I min MTF 数(MTF),它可以用来描述曝光图形的质量: I max I min 其中Imax 和Imin 分别为曝光图形上最大和最小辐照强度。 D D 光刻胶临界调制传输函数(CMTF)为:CMTF D100 D0 100 0 CMTF的典型值约为0.4。如果一个实际光刻图形的MTF小 于所用光刻胶的CMTF,则光刻图形上的最小尺寸线条不能被分 辨。反之,则可能被分辨。 101/ 1 对比度与CMTF的关系为: CMTF 101/ 1 对于曝光系统,如果该系统对各种线条的MTF均已知,则 根据光刻胶对比度可计算出该系统能够形成的最小图形尺寸。
半导体刻蚀 去胶工艺流程

半导体刻蚀去胶工艺流程
半导体刻蚀去胶工艺流程是半导体制造过程中的重要环节之一。
半导体器件的制造通常需要在硅片表面进行图案化处理,而去除胶
层是其中的关键步骤之一。
下面将介绍半导体刻蚀去胶工艺流程的
一般步骤。
1. 初始准备,首先,需要准备一块待处理的硅片。
在进行刻蚀
去胶工艺之前,通常需要对硅片表面进行清洁处理,以确保去胶工
艺的顺利进行。
2. 胶层涂覆,在准备好的硅片上涂覆一层胶层。
这一步骤通常
使用旋涂机或者其他涂覆设备进行,以确保胶层的均匀覆盖。
3. 曝光和显影,接下来,将经过涂覆的硅片放置在曝光机中,
使用光刻胶进行曝光,形成所需的图案。
然后进行显影处理,去除
暴露在光下的胶层部分,留下所需的图案。
4. 刻蚀去胶,将经过曝光和显影处理的硅片放入刻蚀机中,使
用化学溶液或者等离子刻蚀技术,将未被光刻胶保护的区域进行刻蚀,去除胶层。
5. 清洗和检查,最后,对刻蚀去胶后的硅片进行清洗,去除残留的胶层和刻蚀产物。
然后进行表面检查,确保刻蚀去胶工艺的质量和准确度。
总的来说,半导体刻蚀去胶工艺流程是半导体制造中的重要步骤之一,它决定了后续工艺步骤的顺利进行和器件质量的好坏。
因此,精确控制每一个步骤,确保工艺流程的稳定性和可靠性,对于半导体器件制造具有重要意义。
半导体scrubber工作原理 刻蚀工艺

半导体scrubber工作原理刻蚀工艺半导体scrubber是一种用于清洗和去除半导体材料表面污染物和残留物的设备。
它通常使用化学气相刻蚀(CPE)工艺进行清洗。
半导体scrubber的工作原理如下:1. 清洁气体供应:系统中提供一种适当的清洁气体,通常是氨气或氢气。
这种气体被称为携氢气体,其中的氢原子可以与表面的污染物反应,形成可挥发的化合物。
2. 热气供应:系统通过加热方式传递热能到半导体材料的表面。
这有助于提高刻蚀过程的速率,并促使携氢气体与表面污染物反应。
3. 化学反应:清洁气体与被清洁物表面上的污染物发生化学反应。
通常,污染物会被转化为易挥发的化合物,然后通过排气系统从系统中移除。
4. 废气处理:刻蚀过程产生的废气需要经过处理以去除有害物质。
通常,废气会经过气体处理系统,其中包括吸附剂和催化剂等来吸附和催化转化废气中的污染物。
刻蚀工艺是一种用于制造半导体器件的重要工艺。
它通过控制刻蚀过程的条件(如温度、气体浓度、压力等),使半导体器件的表面形状和尺寸得以精确控制。
刻蚀工艺主要分为湿法刻蚀和干法刻蚀两种。
湿法刻蚀是通过将半导体器件浸泡在含有刻蚀液的溶液中,利用化学反应溶解或氧化掉半导体表面的不需要的材料来实现刻蚀的。
常用的刻蚀液有氢氟酸、硝酸、硫酸等。
干法刻蚀是通过在真空环境下,利用化学气相反应实现刻蚀的。
其中包括物理刻蚀和化学刻蚀两种方式。
物理刻蚀是通过粒子的冲击和溅射作用来去除材料,而化学刻蚀则是通过材料与气体之间的化学反应来实现刻蚀。
常用的干法刻蚀工艺包括反应离子刻蚀(RIE)、高密度等离子刻蚀(DRIE)等。
刻蚀工艺的选择取决于具体的制造要求和要刻蚀的材料。
不同的材料和工艺会有不同的刻蚀速率和选择性。
因此,在实际应用中需要根据具体情况进行选择和优化。
半导体刻蚀 去胶工艺流程

半导体刻蚀去胶工艺流程
半导体刻蚀是制造集成电路和其他半导体器件的重要工艺步骤
之一。
而在半导体刻蚀过程中,去胶工艺流程也是至关重要的一环。
下面我们将介绍一下半导体刻蚀去胶的工艺流程。
首先,去胶工艺流程是指在半导体器件制作过程中,需要去除
光刻胶以便进行后续的刻蚀工艺。
去胶工艺流程通常包括以下几个
步骤:
1. 粗去胶,在这一步骤中,使用化学溶剂或者氧气等方法,将
覆盖在半导体表面的光刻胶进行粗去除。
这一步骤的目的是去除大
部分的光刻胶,为后续的精细去胶做准备。
2. 清洗,在粗去胶之后,需要对半导体表面进行清洗,以去除
残留的光刻胶和其他杂质。
清洗过程通常采用化学溶剂和超声波清
洗等方法,确保表面干净无尘。
3. 精细去胶,在清洗之后,需要进行精细的去胶工艺,以确保
半导体表面的光刻胶完全去除。
这一步骤通常需要使用等离子刻蚀
工艺,通过氧气等离子对光刻胶进行精细去除。
4. 再清洗,精细去胶之后,需要再次对半导体表面进行清洗,以确保去胶彻底,表面干净。
以上就是半导体刻蚀去胶的工艺流程。
这一流程在半导体器件制造中扮演着至关重要的角色,对于保证器件的性能和可靠性具有重要意义。
随着半导体工艺的不断发展,去胶工艺流程也在不断优化和改进,以适应新材料和新工艺的需求。
蚀刻工艺 半导体
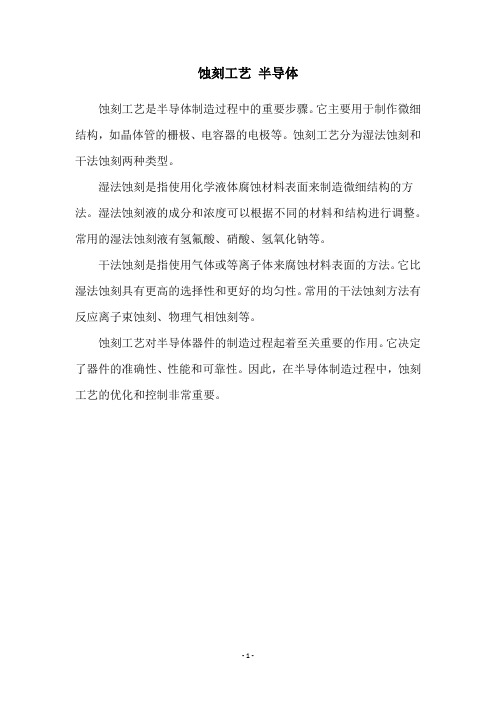
蚀刻工艺半导体
蚀刻工艺是半导体制造过程中的重要步骤。
它主要用于制作微细结构,如晶体管的栅极、电容器的电极等。
蚀刻工艺分为湿法蚀刻和干法蚀刻两种类型。
湿法蚀刻是指使用化学液体腐蚀材料表面来制造微细结构的方法。
湿法蚀刻液的成分和浓度可以根据不同的材料和结构进行调整。
常用的湿法蚀刻液有氢氟酸、硝酸、氢氧化钠等。
干法蚀刻是指使用气体或等离子体来腐蚀材料表面的方法。
它比湿法蚀刻具有更高的选择性和更好的均匀性。
常用的干法蚀刻方法有反应离子束蚀刻、物理气相蚀刻等。
蚀刻工艺对半导体器件的制造过程起着至关重要的作用。
它决定了器件的准确性、性能和可靠性。
因此,在半导体制造过程中,蚀刻工艺的优化和控制非常重要。
- 1 -。
- 1、下载文档前请自行甄别文档内容的完整性,平台不提供额外的编辑、内容补充、找答案等附加服务。
- 2、"仅部分预览"的文档,不可在线预览部分如存在完整性等问题,可反馈申请退款(可完整预览的文档不适用该条件!)。
- 3、如文档侵犯您的权益,请联系客服反馈,我们会尽快为您处理(人工客服工作时间:9:00-18:30)。
高刻蚀速率(大于1000nm/min) 对下层的高选择比,对掩膜层(>4:1)和层 间介质(>20:1) 高的均匀性,CD控制很好,没有微负载效应 没有等离子体诱导充电带来的器件损伤 残留物污染少 不会腐蚀金属
铝和金属复合层刻蚀
钨的刻蚀
湿法去除: 剥离光刻胶是湿法去除光刻胶的一种基本方法
衡量刻蚀工艺在整个硅片上,或整个一批, 或批与批之间刻蚀能力的参数
保持硅片的均匀性是保证制造性能一致的 关键
难点在于在刻蚀具有不同图形密度的硅片 上保持均匀性
(微负载效应)深宽比相关刻蚀:具有高 深宽比硅槽的刻蚀速率要比低深宽比硅槽 的刻蚀速率慢
对于高深宽比的图形窗口,化学刻蚀剂难 以进入,反应生成物难以出来
对于200mm以上的硅片,铜互连采用双层 大马士革技术,层间介质的沟槽刻蚀和低K 介质刻蚀是技术难题 介质刻蚀通常是制作接触孔和通孔,要求 刻蚀出高深宽比的窗口 氧化物的刻蚀困难之一在于难以获得对下 层材料(通常是硅、氮化硅或一层抗反射 涂层)的高选择比 为了防止形成倾斜的侧墙,获得高的氧化 硅/光刻胶的选择比很重要
主要是制作MOS栅结构的多晶硅栅和制作 器件隔离或DRAM电容结构中的单晶硅槽 多晶硅栅的刻蚀工艺必须对下层栅氧化层 有高的选择比并具有非常好的均匀性和可 重复性,同时要求高度的各向异性 单晶硅刻蚀主要用于制作沟槽,如器件隔 离沟槽或DRAM中高密度的垂直电容的制作。 在高密度IC中要求数百万个沟槽具有一致 的光洁度,接近的垂直侧壁,正确的深度 和圆滑的沟槽顶角和底角
干法刻蚀对下层材料没有好的选择比,需 要终点检测来监测刻蚀工艺并停止刻蚀以 减少对下层材料的过度刻蚀 终点检测系统测量一些不同的参数,如刻 蚀速率的变化,产物的类型等
材料刻蚀有:金属刻蚀,介质刻蚀和硅刻蚀 介质刻蚀: (如SiO2)接触孔和通孔制作需要刻蚀介质 硅刻蚀: 如:刻蚀多晶硅晶体管栅和硅槽电容 金属刻蚀: 如:金属层上去除铝合金,制作互连线 光刻胶剥离
§1刻蚀的概念 §2刻蚀工艺 §3刻蚀新技术
(一)基本概念 刻蚀:有选择的去除材料 用化学的或物理的或化学物理结合的方式 有选择的去除(光刻胶开出的窗口) 整体剥离或反刻 被刻蚀的材料:介质 硅 金属 光刻胶
刻蚀速率 刻蚀剖面 刻蚀偏差 选择比 均匀性
刻蚀速率:去除材料的速度 单位:A/min Байду номын сангаас 公式:△T/t
高密度等离子体刻蚀可以在高深宽比图形 中获得各向异性刻蚀
标准等离子体刻蚀,对于0.25μm以下尺寸, 刻蚀基难以进入高深宽比图形,刻蚀生成 物难以从高深宽比图形出来。 解决:低压,以增加气体分子和离子的平 均自由程。但同时由于压力减少而减少了 离子密度,从而降低了刻蚀速率,所以采 用高密度等离子体技术,以产生足够的离 子,从而获得可接受的刻蚀速率 传统等离子体,离化度是在0.01%—0.1%。 而高密度等离子体能产生较大的刻蚀基分 解,获得高达10%的离化率
利用低压放电产生的等离子体中的离子或游离 基(处于激发态的分子、原子及各种原子基团 等)与材料发生化学反应或通过轰击等物理作 用而达到刻蚀的目的 特点:横向钻蚀小,无化学废液,分辨率高, 细线条,操作安全,简便;处理过程未引入污 染;易于实现自动化,表面损伤小。 缺点:成本高,设备复杂。
刻蚀方式: 等离子刻蚀: 利用放电产生的游离基与材料发生化学反应,形 成挥发物,实现刻蚀。选择性好、对衬底损伤较 小,但各向异性较差 溅射与离子束铣蚀: 通过高能惰性气体离子的物理轰击作用刻蚀,各 向异性性好,但选择性较差 反应离子刻蚀(RIE): 通过活性离子对衬底的物理轰击和化学反应双重 作用刻蚀。具有溅射刻蚀和等离子刻蚀两者的优 点,同时兼有各向异性和选择性好的优点。目前, RIE已成为VLSI工艺中应用最广泛的主流刻蚀技术。
刻蚀剖面:刻蚀后图形的侧壁形状 各向同性 各向异性 各向异性对制作亚微米器件很关键 高的各向异性,可以形成88°—89°垂直 度的侧壁
各向异性
各向同性
刻蚀后线宽或关键尺寸间距的变化 通常是由横向钻蚀引起。
选择比:两种材料刻蚀速率的比 公式:S=Ef/Er 高选择比意味着只刻除想要刻去得那层材料。 高选择比对于确保关键尺寸和剖面控制是必需的, 要制造的关键尺寸越小,选择比要求越高
由于化学药品所需的管理和处理,使用湿法去除不 合算 通常干法刻蚀前,光刻胶表面都经过加固处理,使 得光刻胶在大部分湿法去胶液中不溶解,需要干 法等离子体去胶去掉至少上面的一层光刻胶
等离子体去胶:
用氧气来干法去胶,是批量去胶的一种主要 工艺,主要使用下游等离子体反应器 使用O2/N2 ,O2与光刻胶(碳氢聚合物)反 应生成挥发性的气体,这些生成物被真空 系统抽走去除
化学 桶式 下游式 物理 离子束刻蚀 物理和化学 反应离子刻蚀 高密度等离子刻蚀
化学各向同性刻蚀 高选择比 等离子诱导损伤小 用于硅片表面去胶,氧是去胶的主要刻蚀剂
化学各向同性刻蚀 用于去胶或去除非关键层 下游刻蚀的目的是减少或消除等离子体带来的损 伤而使硅片曝露在等离子体中的时间最少
§2 刻蚀工艺 分类 按照刻蚀工艺 湿法刻蚀 干法刻蚀 按照材料 金属刻蚀 介质刻蚀 硅刻蚀
一、湿法刻蚀
液体化学试剂(酸、碱和溶剂等)以化学 方式去除硅片表面材料
反应产物必须是易挥发性的或可溶于刻蚀 剂的物质,否则会成为沉淀,影响刻蚀的 进行
特点: 各向同性 难以精确控制线宽和获得精细图形 安全性 光刻胶脱落 难控制参数 化学试剂处理 高选择性 无离子体损伤 设备简单 方式:浸泡 喷射 应用:通常用于大尺寸刻蚀(> 3μm尺寸 ), 一般用于整体剥离或去除干法刻蚀后的残留物 等
具有强方向性等离子体的一种物理刻蚀机理 小尺寸各向异性 低选择比 低产能 通常用于金,铂和铜等难刻蚀的材料
采用化学反应和物理离子轰击去除硅片表面材料的 技术 具有较好的各向异性侧壁图形 通常用于单晶硅槽的刻蚀
先进的IC技术中刻蚀关键层最主要的刻蚀 方法是采用单片处理的高密度等离子体刻 蚀技术