26关键限值确定程序
关键限值建立控制程序食品有限公司
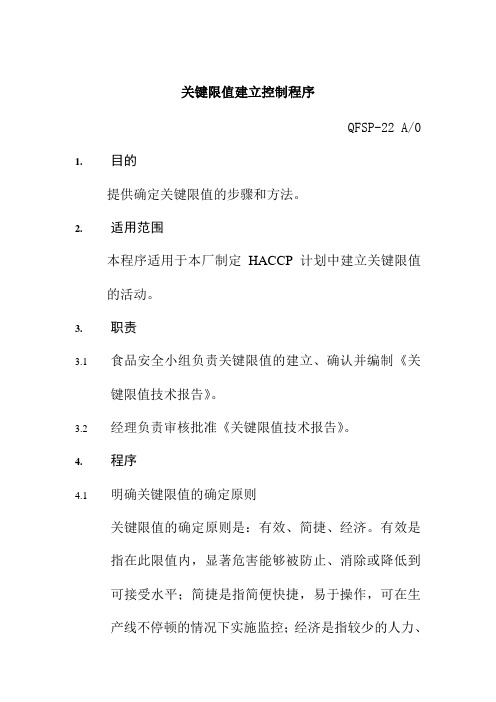
关键限值建立控制程序QFSP-22 A/0 1.目的提供确定关键限值的步骤和方法。
2.适用范围本程序适用于本厂制定HACCP计划中建立关键限值的活动。
3.职责3.1食品安全小组负责关键限值的建立、确认并编制《关键限值技术报告》。
3.2经理负责审核批准《关键限值技术报告》。
4.程序4.1明确关键限值的确定原则关键限值的确定原则是:有效、简捷、经济。
有效是指在此限值内,显著危害能够被防止、消除或降低到可接受水平;简捷是指简便快捷,易于操作,可在生产线不停顿的情况下实施监控;经济是指较少的人力、物力、财力的投入。
4.2建立关键限值的准备在建立各个关键控制点的关键限值之前根据《危害分析工作单》的内容,食品安全小组负责做好以下准备工作:a)明确需建立的HACCP计划列出已确定建立的每个HACCP计划的名称。
b)明确HACCP计划的关键控制点列出每个HACCP计划已确定的关键控制点。
c)明确关键控制点的危害控制组合在每个HACCP计划的每个关键控制点上,列出显著危害与预防控制措施相互对应的危害控制组合。
d)明确控制组合的危害控制原理列出每组危害控制组合的危害控制原理。
4.3建立关键限值食品安全小组根据关键限值的三项确定原则和危害控制原理确定每组危害控制组合的关键限值的种类、载体和数值,并说明确定的依据。
a)确定关键限值的种类根据每组危害控制组合的特性,确定关键限值的种类,如温度、湿度、浓度、时间、水活度、厚度、体积、PH值等,一般尽可能采用物理或化学方法,以便实时监控。
b)确定关键限值的载体关键限值载体的不同影响到三项确定原则的符合程度,需根据具体情况选择。
载体的例子如:精炼各过程的温度是油中心温度还是水/水蒸气的温度,对关键限值确定原则的满足程度是不同的。
c)确定关键限值的数值数值的确定需满足有效性确定原则,根据法规法典和一些权威机构公布的数据(如农残限量)、科学文献、危害控制指南,以及企业自行或委托试验的结论确定关键限值的数值。
关键限值建立程序
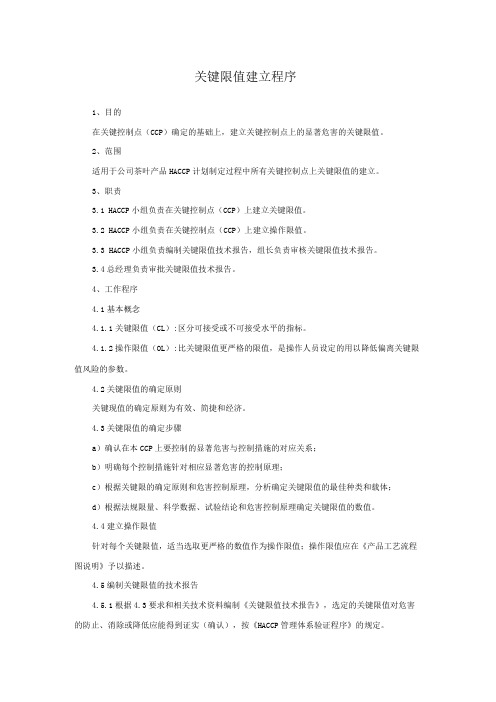
关键限值建立程序1、目的在关键控制点(CCP)确定的基础上,建立关键控制点上的显著危害的关键限值。
2、范围适用于公司茶叶产品HACCP计划制定过程中所有关键控制点上关键限值的建立。
3、职责3.1HACCP小组负责在关键控制点(CCP)上建立关键限值。
3.2HACCP小组负责在关键控制点(CCP)上建立操作限值。
3.3HACCP小组负责编制关键限值技术报告,组长负责审核关键限值技术报告。
3.4总经理负责审批关键限值技术报告。
4、工作程序4.1基本概念4.1.1关键限值(CL):区分可接受或不可接受水平的指标。
4.1.2操作限值(OL):比关键限值更严格的限值,是操作人员设定的用以降低偏离关键限值风险的参数。
4.2关键限值的确定原则关键现值的确定原则为有效、简捷和经济。
4.3关键限值的确定步骤a)确认在本CCP上要控制的显著危害与控制措施的对应关系;b)明确每个控制措施针对相应显著危害的控制原理;c)根据关键限的确定原则和危害控制原理,分析确定关键限值的最佳种类和载体;d)根据法规限量、科学数据、试验结论和危害控制原理确定关键限值的数值。
4.4建立操作限值针对每个关键限值,适当选取更严格的数值作为操作限值;操作限值应在《产品工艺流程图说明》予以描述。
4.5编制关键限值的技术报告4.5.1根据4.3要求和相关技术资料编制《关键限值技术报告》,选定的关键限值对危害的防止、消除或降低应能得到证实(确认),按《HACCP管理体系验证程序》的规定。
4.5.2关键限值技术报告应由HACCP小组组长审核,总经理批准。
经批准的关键限值技术报告归入HACCP计划中。
4.5.3经批准的关键限值有HACCP小组填入《HACCP计划表》的第三栏中。
4.6基于主管信息,如对产品、过程、处理以及等效活动的感观检验确定的关键限值应由指导、规范和(或)人员的能力支持。
5、相关文件《记录控制程序》FTCY-CX-02-2014《HACCP管理体系验证程序》FTCY-CX-11-20146、相关记录《产品工艺流程图说明》FTCY-JL-11-01《关键限制的验证(确认)记录》HFC/QR-11-02。
关键限值一览表
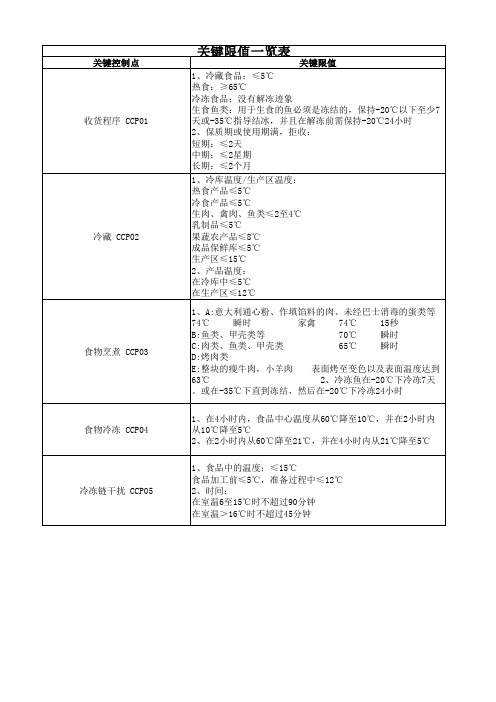
70℃ 瞬时
C:肉类、鱼类、甲壳类
65℃ 瞬时
D:烤肉类
E:整块的瘦牛肉,小羊肉 表面烤至变色以及表面温度达到
63℃
2、冷冻鱼在-20℃下冷冻7天
。或在-35℃下直到冻结,然后在-20℃下冷冻24小时
1、在4小时内,食品中心温度从60℃降至10℃,并在2小时内 从10℃降至5℃ 2、在2小时内从60℃降至21℃,并在4小时内从21℃降至5℃
关键控制点 收货程序 CCP01
冷藏 CCP02
食物烹煮 CCP03 食物冷冻 CCP04 冷冻链干扰 CCP05
关键限值一览表
关键限值
1、冷藏食品:≤5℃ 热食:≥65℃ 冷冻食品:没有解冻迹象 生食鱼类:用于生食的鱼必须是冻结的,保持-20℃以下至少7 天或-35℃指导结冰,并且在解冻前需保持-20℃24小时 2、保质期或使用期满,拒收: 短期:≤2天 中期:≤2星期 长期:≤2个月
1、食品中的温度:≤15℃ 食品加工前≤5℃,准备过程中≤12℃ 2、时间: 在室温6至15℃时不超过90分钟 在室温>16℃时不超过45分钟
1、冷库温度/生产区温度: 热食产品≤5℃ 冷食产品≤5℃ 生肉、禽肉、鱼类≤2至4℃ 乳制品≤5℃ 果蔬农产品≤8℃ 成品保鲜库≤5℃ 生产区≤15℃ 2、产品温度: 在冷库中≤5℃ 在生产区≤12℃
1、A:意大利通心粉、作填馅料的肉、未经巴士消毒的蛋类等
74℃ 瞬时
家禽 74℃ 15秒
B:鱼类、甲Βιβλιοθήκη 类等
关键控制点与关键限值确定控制程序

文件制修订记录1、目的对关键控制点的识别、判断及关键限值的确定过程进行控制,确保关键控制点的确定准确而又科学合理。
2、适用范围适用于本公司用纸张PE、PP料所生产的食品包装盒的生产(含原材料使用储存)、储运、销售以及消费者使用过程中的关键控制点识别判断与关键限值的确定过程。
3、职责3.1危害和风险管理小组3.1.1组织识别判断关键控制点3.1.2负责组织针对关键控制点建立合理的关键限值3.1.3负责对关键控制点的监视进行策划3.2危害和风险管理小组组长负责进行确认批准。
3.3销售、生产、品控、物控等各相关部门配合实施。
4、工作程序4.1关键控制点确定的输入信息危害和风险管理小组根据已确定的《产品描述》、《流程图》以及“危害分析记录”等输入的信息讨论、分析、识别、确定产品生产过程中的关键控制点。
4.2关键控制点识别判断方法—判断树(如下图所示)根据识别的关键控制点由危害和风险管理小组负责整理汇总在“HACCP计划表”中,危害和风险管理小组组长确认后生效。
4.3关键限值的确定危害和风险管理小组根据确认过的“HACCP计划表”,组织相关职能部门/人员针对每一个关键控制点讨论确定关键限值填入“HACCP计划表”中。
同时为了确保关键限值处于有效控制状态,由危害和风险管理小组组长组织相关人员根据关键限值确定操作限值并填入“HACCP计划表”中。
关键控制点的控制策划危害和风险管理小组根据确定的关键控制点以及关键限值、操作限值等对关键控制点的监视进行策划,防止关键控制点偏离,产生用纸张PE、PP料所生产的食品包装袋安全危害或隐患。
4.4关键控制点的更新4.4.1关键控制点每年由危害和风险管理小组组长组织相关人员/职能部门进行评审,必要时予以修订,具体按《文件控制程序》执行。
4.4.2当出现下列情况时,关键控制点应及时更新:a.产品生产加工工艺发生重大变化时b.所用的主要原材料本身发生变化时c.产品生产加工的环境条件发生较大变化时d.产品加工所用的设备类型发生变化时e.生产场所发生变迁f.其他有可能导致产品危害发生变化的情况5、相关文件《文件控制程序》6、相关记录HACCP计划表。
5.4 关键限值的确定及监测控制
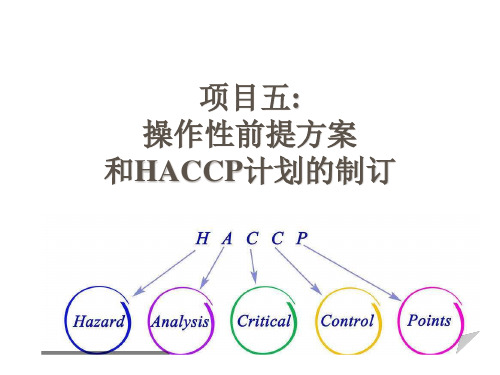
关键限值举例
危害 细菌性病原体 细菌性病原体
CCP 巴氏消毒 干燥
细菌性病原体 酸化
关键限值
≥72℃、t≥15'
干燥温度≥93℃、t≥120' 风温度≤2rpm、水分活度≤0.85
原料量≤4.5kg、浸泡时间≥8h、醋 酸浓度≥3.5%
四、关健控制点的监控
监控什么? 产品加工过程中的CCP情况。通过观察和测量来评估该CCP点是否在关
组织在新产品的开发过程或根据以往的经验最初选用一个保守的CL,然 后再经过确认与验证不断完善。
经验的数据也是可以应用的。如某公司将苹果的烂果率控制在10%的时 候都可以保证产品的棒曲霉毒素控制在30ppb以下,历史上发生过超出 30ppb安全限值的情况都是烂果大于10%时生产的产品,为了保险组织可 将关键限值制定在烂果率小于5%。
项目五: 操作性前提方案 和HACCP计划的制订
任务四 关键限值的确定及监测控制
一、关键限值的概述
关键限值CL:与CCP相关的用于区分可接受或不可接受水平的指标。 操作限OL:比关键限值更严格的,由操作者设定的用来减少偏离关键限
值风险的参数。 工序校正:工序应当在超过操作限时进行校正,以避免违反关键限值,这
➢ 操作性强:不测食品中心温度,而是介质的温度。
例如,需对鱼饼进行油炸(CCP),以控制致病菌,油炸肉饼可以有3种 CL的选择方案:
选择1:CL定为“无致病菌检出”; 选择2:CL定为“最低中心温度66℃;最少时间1min”; 选择3:CL定为“最低油温177℃;最大饼厚0.64cm;最少时间1min。 3个方案都能确保产品的质量与卫生安全,哪个为最佳监控方案?
五、关键限值及监控程序示例
监视程序
危害分析与关键控制点(HACCP)体系认证要求(V1

危害分析与关键控制点(HACCP)体系认证要求(V1.0)要求文件和记录条款文件记录备注1.1 总要求过程清单所有过程(包括外包过程)控制程序1.2.2 HACCP 手册、程序文件1.2.3 1文件控制程序1.2.4 2记录控制程序2.2 3合规义务的文件1合规义务的记录2.3 4建立食品安全文化,企业的价值观。
制度和规范2食品安全文化的记录2.5.2.2 5内部报告制度3内部报告的记录2.5.2.3 6外部沟通授权(任命书)4外部沟通的的记录3.1 5前提计划记录3.2 7人力资源管理程序6人员培训等记录3.3 8-25良好卫生规范相关文件18个7环境监测计划对良好卫生规范实施效果的验证记录(系列)3.4 26产品设计和开发程序8产品设计和开发记录3.5 27供方评价、批准和监控程序9合格供方名录10外包过程控制措施实施记录3.6 28、29监视和测量控制程序(产品和设备)11监视和测量记录3.7 30产品标识和可追溯性程序12进货产品追溯及必要关键信息、进货查验记录和产品的发运记录产品可追溯性的验证3.8 31产品放行程序13授权放行人员和产品放行记录3.9 32产品撤回和召回计划14产品撤回和召回计划实施记录3.10 33所有食品生产经营过程及设施的致敏物质管理计划15致敏物质存在的记录致敏物质交叉污染的控制措施确认和验证3.11 34食品防护计划16食品防护记录条款文件记录3.12 35食品欺诈脆弱性评估程序17食品欺诈预防计划18食品欺诈预防计划的评审食品原辅料脆弱性评估表3.13 36应急准备和响应程序19应急预案实施记录4.2.1 HACCP小组的组成20HACCP小组活动的记录4.2.2 产品描述原料、食品添加剂、食品相关产品,终产品4.2.3 预期用途的确定4.2.4 过程描述及流程图的制定4.2.5 流程图的确认确认的流程图4.3.1.1 危害识别21危害识别依据和结果记录4.3.1.2 危害评估22危害评估依据和结果记录4.3.2 37控制措施的制定依据和控制措施文件23控制措施有效性确认的记录4.3.3 危害分析工作单24形成文件的危害分析工作单4.3.4 HACCP计划24关键控制限值确定限定依据和结果记录、监控记录、纠偏记录纠偏人员经适当的培训并经授权4.4 HACCP计划确认25HACCP计划实施前对危害识别、CCP、控制措施、CCP 监控方法和频率、验证的方式和频率以及记录方式等要素的确认记录。
关键限值控制程序

南京来一口食品有限公司
部门标识
制定
审核
批准
受控状态
PG
胡从富
文件名称:关键限值控制程序 文件编号:QP-8.2-02
版本版次: B/0 第 2页 共 3 页
文件状态
1.目的 确定正确、适当的关键控制点关键限值(CL),以确保食品安全危害得到控制,并具有可操作 性,避免关键限值过松或过严的状况发生。 2.适用范围 本公司生产的所有食品。 3.职责 3.1 食品安全小组组织相关部门对食品生产配送过程进行分析和确定关键控制点的关键限值 (CL)。 3.2 品管部负责收集确定关键限值的有关信息。 4.定义 关键限值(CL):是关键控制点的预防性措施必须达到的标准,是每个 CCP 的安全性界线。 操作限值(OL):是由操作者使用的比 CL 更严格的,是用以降低偏离风险的标准,使得操作者 在 CCP 有失控的趋势,但未超过关键限值之前采取措施,而使 CCP 得到控制。 5.工作程序 5.1 关键限值的信息收集 5.1.1 关键限值的信息来源可包括法律、法规标准、操作标准、检验标准和工艺研发、实验,批 量生产等。 5.1.2 生产部收集关键限值的有关信息, 提供食品安全小组讨论。 5.2 关键限值的选择和确定 5.2.1 建立关键限值应做到合理、适宜、适用、可操作性强,能确保食品安全危害得到控制。 5.2.2 合适的关键限值应考虑如下方面: 1) 直观 2) 易于检测 3) 仅基于食品安全 4) 能及时控制 5) 能使只出现少量不合格的食品,即可采取纠偏行动 6) 不是 GMP 和 SSOP 的措施 7)不能违背法规要求
南 京 来 一 口 食 品 有 限 公 司
LAI YI KOU FOOD INDUSTRIAL CO.LTD
文件名称 文件编号 版本版次 B/0 关键限值控制程序 QP-8.2-02 更改履历 新版文件发行版本版次:B/0 第1页 共3页
关键控制点与关键限值判定与控制培训教材

第二章
危害分析 危害评价 显著性危害
CCP控制
SSM方案控制 改进工艺……
第三章:判定关键控制点应考虑的内容
1.产品的预期用途 2.产品的描述 3.产品流程图 4.相关适宜的食品安全法律法规要求 5.组织确定的显著性危害 6.组织的实际情况 7.消费者或顾客的要求 8.已采取的预防性措施
第三章:判定关键控制点应考虑的内容
产品流程图 产品描述内容 组织实际情况
产品预期用途
CCP
相关适宜的法律法规
消费者或顾客的要求
已采取的预防性措施
第四章:关键控制点判断方法
这一步骤是否存在危害?
Y
NO
对已识别的危害是否采取了预防措施
Y
NO
措施能否消除或降低危害至可接受的水平
N
危害是否可能增加到不可接受水平
其关键限值.
第八章:CCP与CL相互之间的关系
关键限值的定义 区分可接收与不可接收的判定值 [思考]: 假如关键限值偏离,后果?对CCP的影响? [思考]: 确定关键限值的目的?
第八章:CCP与CL相互之间的关系
CL的偏离,后果:将产生有潜在危害的食品,即CCP失控 确定CL即是为了确保CCP更好的得到有效控制.
第七章:关键限值确定原则
[练习]: 针对刚才确定的关键控制点任意挑选2~3个结合CL的确定原则
确定其CL。
第八章:CCP与CL相互之间的关系
HACCP原理之三: 为每个关键控制点(CCP)确立关键限值(CL)
CNAB-S152:2004基于HACCP的食品安全管理体系 规范 4.2.4.4对于为每个关键控制点选择的监视参数,组织应确定
第十章:纠正和纠正措施
一般情况下,将CCP验证和纠正及纠正措施都列入 HACCP计划中,便于可操作性
关键控制点与关键限值控制监控程序

1.目的对关键控制点的识别、判断及关键限值的确定过程进行控制,确保关键控制点的确定准确而又科学合理性。
2.适用范围适用于公司用于淀粉糖类产品生产(含原材料使用储存)、储运、销售以及消费者使用过程中的关键控制点识别判断与关键限值的确定过程。
3.职责3.1 HACCP小组3.1.1组织识别判断关键控制点3.1.2负责组织针对关键控制点建立合理的关键限值3.1.3负责对关键控制点的监视进行策划3.2 HACCP组长负责进行确认批准。
3.3 技术、生产、储运、销售、研发等各相关部门配合实施。
4.工作程序4.1关键控制点确定的输入信息HACCP小组根据已确定的《产品描述和流程图说明书》以及“危害分析记录”、“显著危害一览表”等输入的信息讨论分析识别确定淀粉糖生产过程中的关键控制点。
4.2 关键控制点识别判断方法—判断树(如下图所示)根据识别的关键控制点由HACCP小组负责整理汇总形成“HACCP计划一览表”经HACCP 小组组长确认后生效。
4.3 关键限值的确定2HACCP小组根据确认过的“HACCP计划一览表”,组织相关职能部门/人员针对每一个关键控制点讨论确定关键限值填入“HACCP计划一览表”中。
同时为了确保关键限值处于有效控制状态,由HACCP组长组织相关人员根据关键限值确定操作限值并填入“HACCP计划一览表”中。
关键控制点的控制策划HACCP小组根据确定的关键控制点以及关键限值、操作限值等对关键控制点的监视进行策划,防止关键控制点偏离,产生食品安全危害或隐患,具体执行《关键控制点监视和验证控制程序》。
4.4 关键控制点的更新4.4.1 关键控制点每年由HACCP小组组长组织相关人员/职能部门进行评审,必要时予以修订,具体执行《文件控制程序》。
4.4.2 当出现下列情况时,关键控制点应及时更新:a. 产品生产加工工艺发生重大变化时b. 所用的主要原材料本身发生变化时c. 产品生产加工的环境条件发生较大变化时d.产品加工所用的设备类型发生变化时e.生产场所发生变迁f.其他有可能导致食品危害发生变化的情况5.相关文件5.1 关键控制点监视和验证控制程序5.2文件控制程序5.3产品描述和流程图说明书6.相关记录HACCP计划一览表危害分析记录显著危害一览表3。
以下适合于做关键限值的监视参数

在进行监视参数设定之前,我们首先需要了解什么样的参数适合做关键限值的监视。
关键限值的监视参数需要具备一定的重要性和影响性,能够对系统、进程或产品的正常运行产生较大影响。
以下是一些适合做关键限值的监视参数:1. **系统性能参数:** 系统的性能参数如CPU利用率、内存利用率、磁盘IO等是非常适合做关键限值监视的参数。
这些参数的变化可能会直接影响系统的稳定性和性能。
2. **网络流量参数:** 在网络环境中,网络流量、延迟、丢包率等参数都是非常重要的。
特别是对于一些网络关键设备或关键业务,这些参数的异常变化可能会导致网络服务质量下降,甚至服务中断。
3. **安全事件参数:** 安全事件参数如登入失败次数、异常访问行为等也是非常适合做关键限值监视的参数。
一旦出现异常情况,可能意味着系统或网络受到了攻击或存在安全风险。
4. **业务关键指标:** 对于一些业务系统来说,业务关键指标如订单量、交易金额、用户访问量等是非常重要的。
通过监视这些关键指标的变化,可以及时发现业务异常情况并采取相应措施。
以上提到的参数都是非常适合做关键限值监视的。
在实际操作中,我们可以根据具体的系统、网络或业务情况,设定相应的监视参数,并及时进行监控和报警处理,以保障系统、网络或业务的正常运行。
在监控参数设置时,还需要注意参数的合理性和灵活性,避免过多不必要的监视导致信息过载,影响真正关键参数的监视效果。
以上是我对适合做关键限值监视参数的一些个人观点和理解。
希望这能够帮助您更深入地理解这个主题。
监视参数的设定是保障系统正常运行和预防潜在风险的重要环节。
在实际操作中,为了更好地监控系统、网络或业务的运行状况,我们需要综合考虑各方面的因素,并合理设定关键限值的监视参数。
系统性能参数是非常重要的监控对象。
系统的稳定性和性能直接关系到用户体验和业务持续性。
CPU利用率、内存利用率、磁盘IO等参数的监视可以及时发现系统负载过高、内存泄漏或磁盘故障等问题,从而采取相应措施,保障系统的正常运行。
HACCP体系的7个原则

HACCP体系的7个原则HACCP体系的7个原则HACCP体系必须以NACMCF的7个原则为基础,这7个原则是:(1)危害分析,(2)确定关键控制点,(3)确定关键限值,(4)建立监控程序,(5)矫正措施,(6)记录储存,(7)建立验证程序。
原则1:进行危害分析。
工厂要确定潜在的食品安全危害.并制定预防措施来控制这些危害。
原则2:确定关键控制点。
关键控制点(CCP)是食品加工过程中进行控制的一个点、步骤或是程序,结果可以预防食品安全危害,将其降低到一个可以接受的程度.或是消除它。
食品安全危害是指能导致食品不安全的任何一种生理、化学和物理学性质的危害。
原则3:为每个关键控制点确定关键限值。
确定每个物理、生物和化学危害在关键控制点的大或小值,这种控制可以预防、消除或降低危害到一个可以接受的程度。
原则4:建立关键控制点监控程序。
监控活动必须保证对每个控制点上的过程进行控制。
FSIS要求每个监控程序和频率都符合HACCP体系。
原则5:建立矫正措施。
当监测结果显示关键限值发生偏离时必须要采用这些行动。
如果关键限值不合适,那么终必须要按照工厂的HACCP计划去保证矫正措施的实施。
建立矫正措施目的是保证产品对人们健康的安全性,否则,不合格产品将流人市场。
原则6:建立纪录坚持程序。
HACCP要求所有工厂都要有确定的记录,包括危险性分析和HACCP〔制定〕,同时搞好关键控制点、关键限值、验证活动以及偏差处理等的监测记录。
原则7:建立验证程序。
保证工作按照计划进行;保证生产产品的安全性。
保证HACCP计划的实施.也就是一切按计划运行。
(验证程序包括HACCP计划中的活动记录、CCP记录、关键限值以及微生物的提取和分析)FSIS要求HACCP计划中要有专门的工厂职员进行验证工作。
同时,FSIS检查员也会参加验证工作。
比如,作为验证工作的一部分,FSIS和企业同时〔管理〕微生物测试工作。
20-关键控制点ccp管理制度.
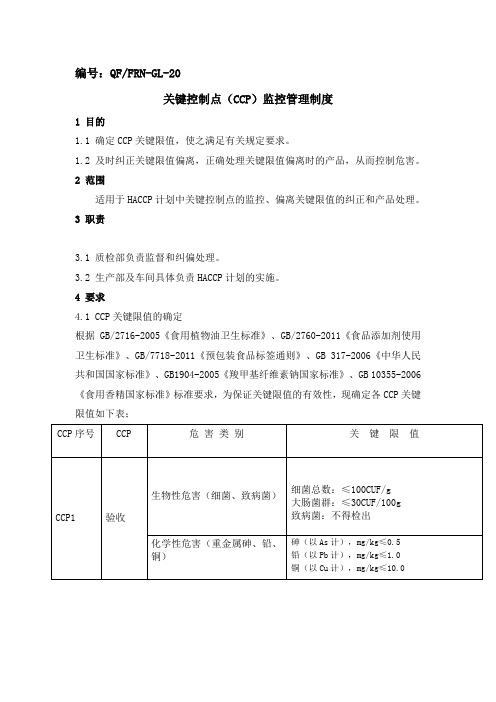
编号:QF/FRN-GL-20关键控制点(CCP)监控管理制度1 目的1.1 确定CCP关键限值,使之满足有关规定要求。
1.2 及时纠正关键限值偏离,正确处理关键限值偏离时的产品,从而控制危害。
2 范围适用于HACCP计划中关键控制点的监控、偏离关键限值的纠正和产品处理。
3 职责3.1 质检部负责监督和纠偏处理。
3.2 生产部及车间具体负责HACCP计划的实施。
4 要求4.1 CCP关键限值的确定根据GB/2716-2005《食用植物油卫生标准》、GB/2760-2011《食品添加剂使用卫生标准》、GB/7718-2011《预包装食品标签通则》、GB 317-2006《中华人民共和国国家标准》、GB1904-2005《羧甲基纤维素钠国家标准》、GB 10355-2006《食用香精国家标准》标准要求,为保证关键限值的有效性,现确定各CCP关键限值如下表;注:微生物、重金属的控制项目按照上述标准中所列的执行。
4.2 CCP的监控4.2.1 通常是连续监控,如不能连续监控,其监控频率或数量必须足以保证CCP 处于受控状态。
对各CCP的监控频率见《固体饮料产品HACCP计划表》。
4.2.2 监控采用感官、物理和化学方法快速进行,CCP-1由质检部负责监控原辅料的微生物检验,CCP-2由生产部负责监视配料的消毒、杀菌实施效果;CCP-3由生产部负责监控混合机混合时间;CCP-4由品控部负责监控包装效果和重量检测;CCP-5由生产部负责监控金属探测仪。
4.3 监控所获得的数据要由生产部负责人、质检部负责人负责评估。
4.4 当监控结果表明CCP的控制有失控趋势时,监控人员要及时通知生产系统对过程进行调整,并追回发生偏离关键限值的产品,重新处理。
4.5 做好以上各项记录。
浅谈如何确定关键控制点关键限值

浅谈如何确定关键控制点的关键限值CQC厦门评审中心陈争HACCP体系由于能有效控制食品中的危害,保证食品的安全,已成为全世界公认的食品安全生产方法。
随着世界各国对食品安全性的关注日益高涨,HACCP体系管理被世界各国认可为一个预防性的食品安全监控系统。
近30年来HACCP体系已经成为国际社会普遍认可和接受的用于确保食品安全的体系。
HACCP体系主要由GMP、SSOP和HACCP计划构成,GMP、SSOP是HACCP 体系的基础,而HACCP计划是HACCP体系的核心。
按照国际食品法典委员会CAC、美国FDA、加拿大HACCP计划通用模式要求,HACCP计划是建立在由五个预先步骤和HACCP的七个原理共十二个步骤组成的一个实施计划。
其中第8个步骤(即原理三):“确定关键限值(CL)”是非常重要的一环,它关系到显著危害能否被控制到安全水平,食品最终使用能否安全卫生的保障。
确定关键限值(CL)应注重三项原则:有效、简捷和经济。
有效是指在此限值内,显著危害能够被防止,消除或降低到可接受水平;简捷是指易于操作,可在生产线不停顿的情况下快速监控;经济是指较少的人力、财力的投入。
好的关键界限应该是直观,易于实际监测,仅基于食品安全角度考虑、允许在较快的规定时间内完成,能使只销毁或处理较少的产品时就采取纠正措施,不打破常规方式,不是GMP或SSOP 措施,不违背法规和标准。
确定关键限值(CL)时应考虑:1、确认在本关键控制点(CCP)上要控制的显著危害与预防控制措施的对应关系;2、分析明确每种预防控制措施针对相应显著危害的控制原理;3、根据关键限值的确定原则和危害控制原理,分析确定关键限值的最佳项目和载体,可考虑的项目包括:温度、时间、湿度、厚度、纯度、粘度、PH值、水份活度、盐度、体积等;4、确定关键限值的数值应根据法规法典和一些权威组织公布的数据(如农、药残限量)、科学文献、危害控制指南以及企业自行或委托试验的结论来确定,而非凭个人的意想、经验随意作决定;5、针对可以通过加严控制,降低偏离风险,而不需要采取纠正措施的关键控制点(CCP),选取适当更严格的数值作为操作限值(OL),通过偏离前的的调整起到经济又确保产品安全的保险杠作用(本文例子中不作阐述)。
附表3烘烤工序关键限值和操作限值的确定依据

烘烤工序关键限值和操作限值的确定依据1、目的:确定烘烤工序的CL值和OL值,保证产品的安全卫生。
2、范围:关键限值的确定依据和试验方法。
3、职责:HACCP小组负责烘烤工序CL值和OL值的确定和有关依据的搜集、整理和归档。
生产部门负责CL值和OL值的控制实施。
4.确定方法:HACCP小组通过对不同的时间,对其中心温度影响的检测,设定如下的试验方法:产品名称烘烤时间(分钟)烘烤温度(℃)中心温度(℃)白吐司40 平炉:上火:240℃下火:230℃89.5℃45 92.4℃50 97.7℃全麦核桃24转炉温度:175℃86.2℃27 89.9℃30 92.6℃加州葡萄35 平炉:上火:170℃下火:260℃87.4℃38 91.5℃40 95.4℃皇家牛油排包20 平炉:上火:190℃下火:240℃88.2℃24 91.5℃28 94.6℃旺仔小馒头13 平炉:上火:200℃下火:170℃88.9℃15 90.7℃17 92.5℃奶香卷17 平炉:上火:180℃底火:205℃88.7℃19 90.1℃21 93.2℃奶油布洛特21转炉温度:185℃88.4℃24 91.6℃26 97.6℃芝士瓦诺30 平炉:上火:190~200℃下火:190~200℃80.2℃33 85.7℃35 88.4℃瑞士卷16 平炉:上火:200℃下火:170℃84.5℃18 86.2℃20 89.3℃高钙芝士蛋糕52 平炉:上火:220~230℃下火:140~145℃65.4℃60 71.8℃65 78.5℃小元宝蛋糕9 平炉:上火:180~185℃下火:220~230℃75.7℃11 77.5℃13 81.4℃半山蛋糕14 平炉:上火:220~226℃下火:170~175℃85.0℃15 86.2℃16 88.5℃芙蓉黑金砂19 平炉:上火:185~195℃下火:145~150℃81.4℃21 85.2℃23 87.8℃重乳酪68 平炉:上火:230~240℃下火:130℃88.7℃72 90.3℃76 94.1℃蛋糕底21 平炉:上火:200℃下火:185~190℃83.8℃26 88.3℃28 90.7℃毛巾卷14 平炉:上火:200℃下火:160℃83.4℃16 85.2℃18 86.9℃皇冠蛋糕21 平炉:上火:200℃下火:185℃87.7℃26 91.3℃30 96.4℃多轮多10 平炉:上火:200~205℃下火:180℃84.0℃11 87.2℃13 89.8℃和风葡萄14 平炉: 83.2℃16 上火:200~205℃下火:160~165℃85.5℃18 89.4℃玛丽脆皮餐包10 平炉:上火:200℃下火:170℃81.4℃13 87.7℃金砖30 转炉温度:185℃88.5℃34 91.4℃牛奶搭档14 平炉:上火:200~205℃下火:145℃82.1℃16 84.7℃18 88.2℃香浓红豆吐司21 转炉温度:180℃93.8℃25 97.4℃紫薯蜜豆蛋糕23 平炉:上火:200℃下火:180℃91.2℃28 93.5℃夏威夷杯子蛋糕26 平炉:上火:200℃下火:180℃91.3℃28 94.2℃七彩蛋糕34 平炉:上火:200~210℃下火:180~190℃87.0℃37 89.7℃40 90.8℃牛奶清蒸蛋糕16 平炉上火:190~200℃下火:190~200℃80.5 18 84.1 20 87.6抹茶蒸糕30 平炉上火:195~205℃下火:200~210℃77.3 33 80.2 36 84.7铜锣烧3 煎烤:280℃77.6 4 80.6咸蛋糕14 平炉:上火:200~205℃下火:100℃78.2 16 85.7 18 91.4烘烤工序关键限值和操作限值验证报告1、目的:确保烘烤工序的CL值的设置符合《食品微生物学》巴氏杀菌以及高温短时杀菌的原理,等相关要求,保证产品的安全卫生。
HACCP中关键控制点和关键限值确定原则
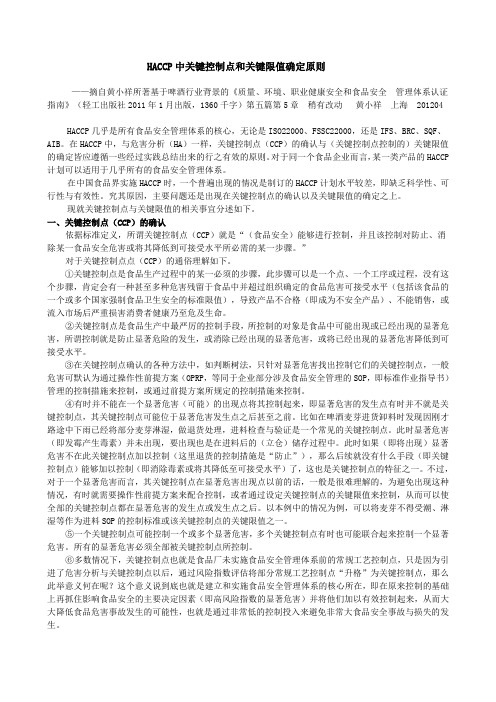
HACCP中关键控制点和关键限值确定原则——摘自黄小祥所著基于啤酒行业背景的《质量、环境、职业健康安全和食品安全管理体系认证指南》(轻工出版社2011年1月出版,1360千字)第五篇第5章稍有改动黄小祥上海 201204HACCP几乎是所有食品安全管理体系的核心,无论是ISO22000、FSSC22000,还是IFS、BRC、SQF、AIB。
在HACCP中,与危害分析(HA)一样,关键控制点(CCP)的确认与(关键控制点控制的)关键限值的确定皆应遵循一些经过实践总结出来的行之有效的原则。
对于同一个食品企业而言,某一类产品的HACCP 计划可以适用于几乎所有的食品安全管理体系。
在中国食品界实施HACCP时,一个普遍出现的情况是制订的HACCP计划水平较差,即缺乏科学性、可行性与有效性。
究其原因,主要问题还是出现在关键控制点的确认以及关键限值的确定之上。
现就关键控制点与关键限值的相关事宜分述如下。
一、关键控制点(CCP)的确认依据标准定义,所谓关键控制点(CCP)就是“(食品安全)能够进行控制,并且该控制对防止、消除某一食品安全危害或将其降低到可接受水平所必需的某一步骤。
”对于关键控制点点(CCP)的通俗理解如下。
①关键控制点是食品生产过程中的某一必须的步骤,此步骤可以是一个点、一个工序或过程,没有这个步骤,肯定会有一种甚至多种危害残留于食品中并超过组织确定的食品危害可接受水平(包括该食品的一个或多个国家强制食品卫生安全的标准限值),导致产品不合格(即成为不安全产品)、不能销售,或流入市场后严重损害消费者健康乃至危及生命。
②关键控制点是食品生产中最严厉的控制手段,所控制的对象是食品中可能出现或已经出现的显著危害,所谓控制就是防止显著危险的发生,或消除已经出现的显著危害,或将已经出现的显著危害降低到可接受水平。
③在关键控制点确认的各种方法中,如判断树法,只针对显著危害找出控制它们的关键控制点,一般危害可默认为通过操作性前提方案(OPRP,等同于企业部分涉及食品安全管理的SOP,即标准作业指导书)管理的控制措施来控制,或通过前提方案所规定的控制措施来控制。
产品关键控制点的关键限值
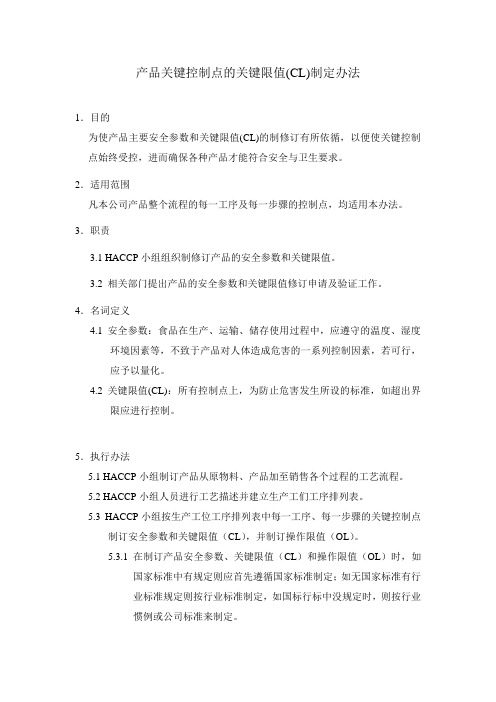
产品关键控制点的关键限值(CL)制定办法1.目的为使产品主要安全参数和关键限值(CL)的制修订有所依循,以便使关键控制点始终受控,进而确保各种产品才能符合安全与卫生要求。
2.适用范围凡本公司产品整个流程的每一工序及每一步骤的控制点,均适用本办法。
3.职责3.1 HACCP小组组织制修订产品的安全参数和关键限值。
3.2 相关部门提出产品的安全参数和关键限值修订申请及验证工作。
4.名词定义4.1 安全参数:食品在生产、运输、储存使用过程中,应遵守的温度、湿度环境因素等,不致于产品对人体造成危害的一系列控制因素,若可行,应予以量化。
4.2 关键限值(CL):所有控制点上,为防止危害发生所设的标准,如超出界限应进行控制。
5.执行办法5.1 HACCP小组制订产品从原物料、产品加至销售各个过程的工艺流程。
5.2 HACCP小组人员进行工艺描述并建立生产工们工序排列表。
5.3 HACCP小组按生产工位工序排列表中每一工序、每一步骤的关键控制点制订安全参数和关键限值(CL),并制订操作限值(OL)。
5.3.1 在制订产品安全参数、关键限值(CL)和操作限值(OL)时,如国家标准中有规定则应首先遵循国家标准制定;如无国家标准有行业标准规定则按行业标准制定,如国标行标中没规定时,则按行业惯例或公司标准来制定。
5.3.2在制订参数及限值时,如用数据来控制时必须要有正负范围或控制范围,如不能用数据控制必须要有比对样本(即标准样本、上限样本、下限样本),如没标准样本就用文字方式清楚明确的叙述。
5.3.3 对按行业惯例或公司标准来制定的限值(CL),和操作限值(OL),HACCP小组组织相关部门进行验证,HACCP小组对验证结果进行讨论分析评估后确认。
5.3.4 经确定限值(CL)、操作限值(OL),列入HACCP计划表或相关操作规程中上报审批。
5.4 建立产品限值(CL)、操作限值(OL)后,相关部门应予以严格执行,当控制超过控制界限时,相关部门应采取措施进行控制,以利于关键控制点始终受控状态。
- 1、下载文档前请自行甄别文档内容的完整性,平台不提供额外的编辑、内容补充、找答案等附加服务。
- 2、"仅部分预览"的文档,不可在线预览部分如存在完整性等问题,可反馈申请退款(可完整预览的文档不适用该条件!)。
- 3、如文档侵犯您的权益,请联系客服反馈,我们会尽快为您处理(人工客服工作时间:9:00-18:30)。
1.0 目的
规范关键控制点的限值确定步骤和权限,保证关键限值的正确性和可行性。
2.0 适用范围
适用于体系中关键控制点的控制限值确定活动。
3.0 职责
3.1 食品安全小组负责分析确定关键限值,必要时提出调整建议。
3.2食品安全小组长负责审核关键限值。
3.3管理者代表负责审批关键限值。
4. 0 定义
关键限值:区分可接受和不可接受的判定值。
5.0 程序
5.1关键限值的初步拟制
5.1.1食品安全小组成员应对每个关键控制点确定标准值,以确保每个关键控制点的
限制在安全值以内。
这些关键限值应尽可能通过各种物理、化学方法进行连续的监控,关键限值常有温度、时间、压力、水分、pH值等。
5.1.2食品安全小组成员根据收集的文献资料、专家意见、试验结果等提出关键限
值。
5.2关键限值的分析
5.2.1对于食品安全小组成员提出的关键限值,是经过确认并具有相关的文献、专家
意见、试验结果的支持。
5.2.2食品安全小组听取关键限值的说明后,应就其符合性和可行性进行讨论,以保
证关键限值符合控制要求、实施现场具有时效性和可操作性。
5.3关键限值的验证:关键限值的正确性需要进行验证,以保证实施的效果。
5.3.1对于通用性的工艺条件或试验参数,有文献资料证明,可以通过对文献的复核作为
验证。
5.3.2对于公司特有的工艺条件参数或试验,应收集相应的工艺试验参数资料或试验
报告,以证明参数和效果的有效性。
5.3.3对于新增的、公司内部无法进行的确认试验可委托外部专业机构进行,通过外
5.4关键限值的确认
关键限值验证完成后,食品安全小组成员将其记录于关键限值一览表。
关键限值一览表经管理者代表审核后作为关键控制点的控制基准。
6.0 相关文件
6.1《前提方案》
6.2《操作性前提方案》
7.0 相关记录
《关键限值一览表》。