用Roll to Roll生产工艺研制精细线路
挠性及刚挠印制电路板
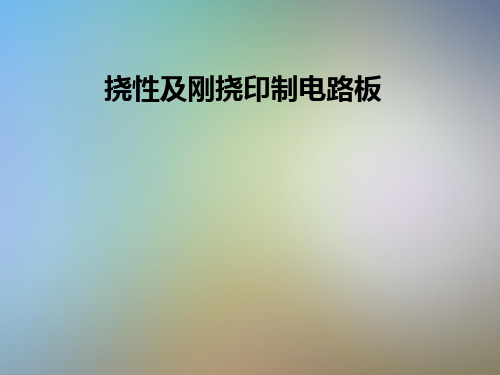
❖11.1.5挠性及刚挠印制电路板的结构形式 挠性印制板与刚挠印制板都是以挠性材料为主体结构
❖ 挠性印制板发展过程可总结如下: 1. 53年美国研制成功挠性印制板。 2. 70年代已开发出刚挠结合板。 3. 80年代,日本取代美国,产能跃居世界第一位。 4. 90年代,韩国、台湾和大陆等地开始批量生产。 ❖ 全球挠性板市场2000年产值达到39亿美元,2004年接近
❖ 3. 加成和半加成加工法 (1) 挠性板制造中采用聚合厚膜技术是种加成法工艺。该 方法采用导电涂料经丝网印制在薄膜基材表面上印刷电 路图形,再经过紫外光或热辐射固化。
(2) 挠性板制造中采用先进的阴极喷镀涂技术,类似于半 加成法工艺。
❖ 4.挠性单面板两面通路(露背)的加工法
该类挠性板是只有一层导体层,因此也是单面板,但 其两个表面都有露出的连接盘(点),可供连接。两面 通路的加工方法有多种,介绍如下。
(7)挠性电路具有优良的电性能、介电性能及耐热性 .
(8)挠性电路有利于热扩散:平面导体比圆形导体有更大 的面积/体积比,另外,挠性电路结构中短的热通道进一 步提高了热的扩散。
❖11.1.4 挠性印制电路板(FPC)的分类
1.按线路层数分 类
❖ (1)挠性单面印制板 (2)挠性双面印制板 (3)挠性多层印制板 (4)挠性开窗板
(2)挠性板基材可弯折挠曲,可用于刚性印制板 无法安装的任意几何形状的设备机体中。
(3)挠性板除能静态挠曲外,还可以动态挠曲.
(4)挠性电路减少了内连所需的硬件具有更高的 装配可靠性和产量
(5) 挠性电路可以向三维空间扩展,提高了电路设计和机 械结构设计的自由度。
方正科技对FPC项目的规划
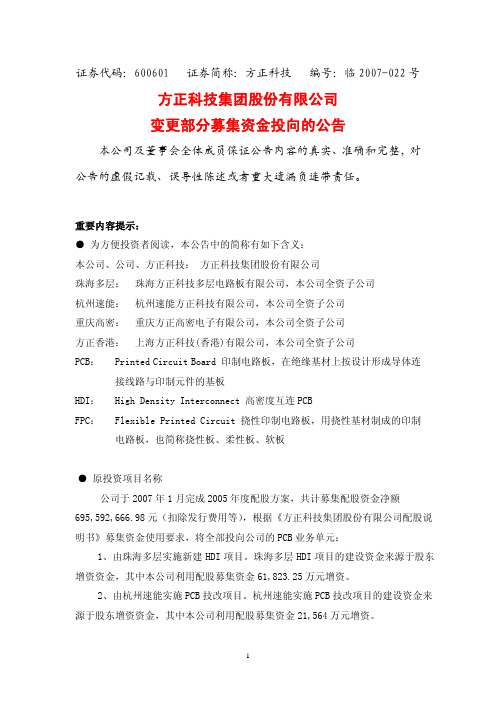
证券代码:600601 证券简称:方正科技 编号:临2007-022号方正科技集团股份有限公司变更部分募集资金投向的公告本公司及董事会全体成员保证公告内容的真实、准确和完整,对公告的虚假记载、误导性陈述或者重大遗漏负连带责任。
重要内容提示:● 为方便投资者阅读,本公告中的简称有如下含义:本公司、公司、方正科技: 方正科技集团股份有限公司珠海多层: 珠海方正科技多层电路板有限公司,本公司全资子公司杭州速能: 杭州速能方正科技有限公司,本公司全资子公司重庆高密: 重庆方正高密电子有限公司,本公司全资子公司方正香港: 上海方正科技(香港)有限公司,本公司全资子公司PCB: Printed Circuit Board 印制电路板,在绝缘基材上按设计形成导体连接线路与印制元件的基板HDI: High Density Interconnect 高密度互连PCBFPC: Flexible Printed Circuit 挠性印制电路板,用挠性基材制成的印制电路板,也简称挠性板、柔性板、软板● 原投资项目名称公司于2007年1月完成2005年度配股方案,共计募集配股资金净额695,592,666.98元(扣除发行费用等),根据《方正科技集团股份有限公司配股说明书》募集资金使用要求,将全部投向公司的PCB业务单元:1、由珠海多层实施新建HDI项目。
珠海多层HDI项目的建设资金来源于股东增资资金,其中本公司利用配股募集资金61,823.25万元增资。
2、由杭州速能实施PCB技改项目。
杭州速能实施PCB技改项目的建设资金来源于股东增资资金,其中本公司利用配股募集资金21,564万元增资。
上述项目募捐资金不足部分,由公司自有资金投入,截止2007年10月20日,本次配股募集资金已按照《配股说明书》计划,向珠海多层和杭州速能分别增资4.8亿元和0.6亿元,目前还剩余配股募集资金1.5559亿元。
● 新投资项目名称,投资总量为使公司PCB业务向纵深发展,实现公司PCB业务高端战略定位,计划利用剩余募集资金对重庆高密增资,补足未到位注册资本1912.407206万美元(汇率按1:7.5计,约为14343.05万元人民币),用于挠性板电路板(FPC)和背板项目生产。
RTR(RolltoRoll)方式制作25um,25umCOF精细线路的参数优化
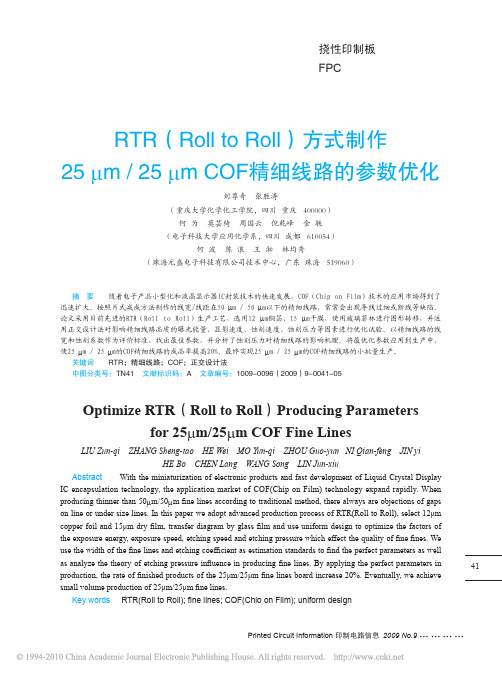
据减成法制作精细线路的经验,铜箔越薄越有利于精
…
于在制作精细线路过程中曝光级数、显影速度、蚀
细线路的制作。薄铜在蚀刻过程中可以有效的减小线
…
刻速度、蚀刻压力这四个因素对线路的质量影响很
路的侧蚀量。基于此,我们选用新日铁12 µm / 20 µm电
…
大。因此,本试验将进行正交分析试验,得到RTR方
解无胶铜箔作为精细线路的基材[3]。
…
图4 蚀刻系数
精细线路优化试验安排及其试验结果如表2所示
…
式中,F——蚀刻系数; H——线路的高度; Wb——线路底部的宽度; Wt——线路顶部的宽度。
(1)
3.1 试验结果
…
由于精细线路过细,在制作的过程中要达到
…
设计线宽和提高蚀刻系数是精细线路的难点,同时
…
线宽和蚀刻系数也是精细线路评价的重要指标。为
素很多,但曝光、显影、蚀刻工艺流程对其影响最 大,在此我们对这几个过程中的曝光级数、显影速
… … … … … Printed Circuit Information 印制电路信息 2009 No.9
…
…
…
…
…
…
…
…
…
…
…
…
…
…
…
…
…
…
…S…um…m…ar…iza…ti…on…&…C…om…mFePnCt …
如图2所示。图2中黑圈所示的区域即是IC和基板键 合的引线区域,也叫做内部引线(Inner Lead)。图3 为图2中黑圈处的放大图,为内部引线的详细图示。 内部引线也是该基板上线宽/线距为25 µm / 25 µm的
制论 且很快成为LCD显示器IC驱动的主流封装技术。在
RFID天线制造方法简介
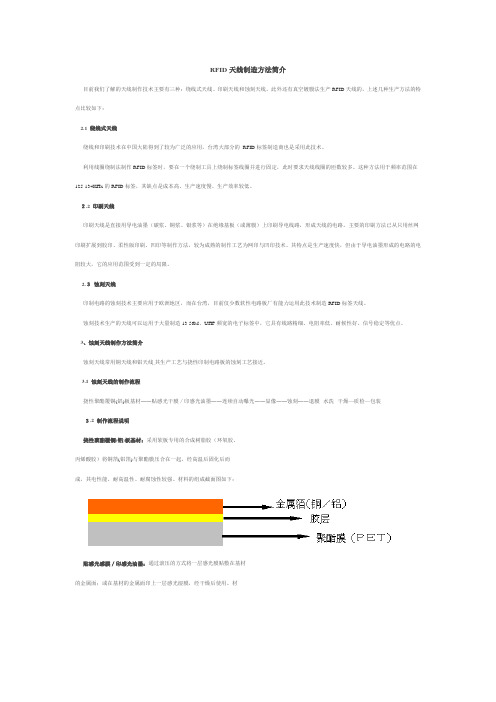
RFID天线制造方法简介目前我们了解的天线制作技术主要有三种:绕线式天线、印刷天线和蚀刻天线。
此外还有真空镀膜法生产RFID天线的,上述几种生产方法的特点比较如下:2.1 绕线式天线绕线和印刷技术在中国大陆得到了较为广泛的应用,台湾大部分的RFID标签制造商也是采用此技术。
利用线圈绕制法制作RFID标签时,要在一个绕制工具上绕制标签线圈并进行固定,此时要求天线线圈的匝数较多。
这种方法用于频率范围在125-134KHz的RFID标签,其缺点是成本高、生产速度慢、生产效率较低。
2.2 印刷天线印刷天线是直接用导电油墨(碳浆、铜浆、银浆等)在绝缘基板(或薄膜)上印刷导电线路,形成天线的电路。
主要的印刷方法已从只用丝网印刷扩展到胶印、柔性版印刷、凹印等制作方法,较为成熟的制作工艺为网印与凹印技术。
其特点是生产速度快,但由于导电油墨形成的电路的电阻较大,它的应用范围受到一定的局限。
2.3蚀刻天线印制电路的蚀刻技术主要应用于欧洲地区,而在台湾,目前仅少数软性电路板厂有能力运用此技术制造RFID标签天线。
蚀刻技术生产的天线可以运用于大量制造13.56M、UHF频宽的电子标签中,它具有线路精细、电阻率低、耐候性好、信号稳定等优点。
3、蚀刻天线制作方法简介蚀刻天线常用铜天线和铝天线,其生产工艺与挠性印制电路板的蚀刻工艺接近。
3.1 蚀刻天线的制作流程挠性聚酯覆铜(铝)板基材――贴感光干膜/印感光油墨――连续自动曝光――显像――蚀刻――退膜--水洗--干燥—质检—包装3.2 制作流程说明挠性聚酯覆铜(铝)板基材:采用软板专用的合成树脂胶(环氧胶、丙烯酸胶)将铜箔(铝箔)与聚酯膜压合在一起,经高温后固化后而成,其电性能、耐高温性、耐腐蚀性较强。
材料的组成截面图如下:贴感光感膜/印感光油墨:通过滚压的方式将一层感光膜贴敷在基材的金属面;或在基材的金属面印上一层感光湿膜,经干燥后使用。
材料的组成截面图如下所示:曝光:通过自动连续曝光机,自动对位曝光将菲林上的电路图性转移到感光膜上。
Cu基TP电子薄膜Roll To Roll 加工制程工艺设备技术

二次曝光 掩膜间隙: 15um
其它同覆膜前清洗
工艺条件
压力尽可能小
药液和滤芯要每 天更换一次 脱模长度:3米
Cu基电子薄膜卷对卷加工各工艺槽的工艺条件
工序 覆干膜前清洗 一次显影 作业内容 清洗基材表面 干膜显影 溶液性质 1%浓度碱液 1%浓度碱液 溶液温度 29°C+/-0.5°C 29°C+/-0.5°C 速度 2-3米/分 2-3米/分 长度 1米 2米 槽段数 1 1 作业时间 15秒 60秒 工艺要求 表面清洗 显影 每班更换 备注
湿制程技术
蚀刻精细控制
药液浓度在线补偿精细控制 高精度缓变微喷多段蚀刻 连续换卷与在线监测 非接触式多段干燥 节能环保 实现连续在线监测与换卷 控制干燥速度和温度曲线、加热方式 蚀刻液的密闭、回收与处理
Cu基电子薄膜Roll To Roll湿制程工艺流程与工艺条件
工序 覆膜前清洗 温度:29°C+/-0.5°C 工艺条件 速度:2-3米/分 药液与显影液相同 长度:0.5米 工序 二次蚀刻 (ITO) 药液:HCL+缓释剂 比例:60%:40% 温度:48°C 工艺条件 蚀刻液喷淋压力为 1KG/平方厘米 长度:2米/段 X 2段 工序 三次蚀刻(Cu) 与一次蚀刻工艺同 蚀刻可视区边线 蚀刻区长度:2米 一次覆干膜 厚度7-15um 温度:80-90°C 压力尽可能小 脱干模清洗 滤芯:20um 温度:34°C 压力尽可能小 药液和滤芯要每 天更换一次 药液: 0.5%NaOH 脱模长度:3米 脱干模清洗 滤芯:20um 温度:34°C 覆保护膜 覆50umPE保护膜 收卷 二次覆干膜 厚度:15um 温度:80-90°C 压力尽可能小 一次曝光 掩膜间隙:15um 偏差:+/-1um 一次显影 0.5%NaCO2 其它同覆膜前 清洗 一次蚀刻(Cu) 温度:32°-34°C 速度:1.5米/分 长度:2米 二次显影 1%NaOH
纳米银和金属网格的对比分析

纳米银和金属网格对比分析行业资讯 2014-11-11•一、市场因素的评价关于市场因素决定于产品价格与技术规格,技术规格将于之后再详细讨论。
评价产品价格的变动,包括初期生产价格,例如材料成本、制造成本,IC及其器件的整合成本,假如企业一条龙式地能掌握从原料至器件,甚至IC器件的成本,则有机会端出具有竞争力的产品价格。
第二种系量产价格,当不同材料技术与生产良率仍有提升空间,以及产品的应用领域扩大,因而具备更多压低成本的能力,例如掌握了主要品牌商且成为市场的主流产品,或者进一步扩展到其他应用领域,而造成市占及出货量的扩大。
从原料与制造成本的角度,金属网格材料可为银或铜原子,或银的氧化物,以印刷方式形成金属网格,而该金属网格的线幅超过5μm以上;由于银或铜原料取得并不是问题,原料成本系相对低廉,但超过5μm以上的金属线幅所产生的视觉莫瑞干涉过于明显致规格劣化,因此必须设法降低线幅至3μm以下始为市场所接受,如此,为降低线幅所增加的成本,包括放弃印刷法而改成黄光微影或雷射制作遮罩、良率降低等制造成本增加,就占有很高比重。
相对地,纳米银线油墨包括纳米银线(线径约50nm、线长约23μm)、调制溶液配方等,并非能直接取得,而是购自如纳米银线材料供应商Cambriostechnologies等少数专业厂商,因此原料成本欲降不易,但相对地,纳米银线没有如金属网格的视觉莫瑞干涉现象,不必刻意要求线幅降低,加上可以搭配成本较低的卷对卷印刷方式生产,即能获得符合市场规格的触控面板。
为降低原料与制造成本,主推纳米银线触控面板的触控大厂宸鸿,即于2013宣布与日本写真印刷联手开发纳米银线触控技术,并搭配先前与Cambriostechnologies合资而提供的纳米银线材料。
日本写真擅长塑胶薄膜生产技术与卷轴式(roll-to-roll)生产技术,而Cambriostechnologies系纳米银线材料的少数供应厂商,透过宸鸿专业的触控图案设计及制造技术,三者强强合作将会有不错的价格竞争力,打入高阶产品市场的机会也很高。
光刻胶产品的介绍

光刻胶产品的介绍光刻胶产品主要适用于集成电路产业和平板显示器产业的光刻工艺,以得到精细线路。
文章介绍了高世代平板显示器用光刻胶产品的性能,用途。
标签:光刻胶;性能;用途前言所谓光刻胶(photoresist),是一类利用光化学反应进行精细图形转移的化学品。
应用于集成电路、平板显示器、光伏电池、LED等产业。
文章主要讨论用于高世代平板显示器(FPD)产业的正性光刻胶。
光刻胶隶属于电子化学品,指为电子工业配套的精细化工材料。
工信部指出,“十一五”期,我国必须大力发展电子材料产业,缩小电子材料与国外先进水平的差距,提高国内自主配套能力,为电子信息产业的发展提供有力支撑。
文章讨论的正性光刻胶,利用曝光、显影后,感光部分树脂的溶解度远大于非感光部分树脂的特性,通过光刻工艺(LITHOGRAPHY),得到所需的线路图形,是光刻工艺中使用的关键化学品。
高世代的面板工厂,需建设大面积无尘洁净空间,购置大型的自动化精密机械,投资高昂。
为面板工厂配套的各类电子化学品,需满足面板工厂对大尺寸和精细线路方面的高要求,才能保证产品的正品率,以收回高昂投资。
1 光刻胶的介绍光刻胶,在曝光区域发生化学反应,造成曝光和非曝光部分在碱液中溶解性产生明显的差异,经适当的溶剂处理后,溶去可溶性部分,得到所需图像。
根据其化学反应机理,分负性胶和正性胶两类。
经曝光、显影后,溶解度增加的是“正性胶”,溶解度减小的是“负性胶”。
正性胶有良好的分辨率,但成本较高。
适用于高世代平板显示器产业的光刻胶,一般采用正性光刻胶,以得到良好的分辨率。
FPD工厂所用的曝光光源,一般采用H-line/G-line/I-line的紫外混合光源,光源波长在300nm~450nm范围。
为适应高世代平板显示器尺寸越来越大的趋势,多采用刮涂工艺(SLIT COATING)。
典型的高世代平板显示器产业所用的正性光刻胶,主要成分和作用是:(1)线性酚醛树脂为成膜树脂,通过涂布工艺在喷溅金属的玻璃基材表面形成树脂涂层,利用光刻工艺,在涂层上“印制”线路。
代替ITO的新材料及技术概诉
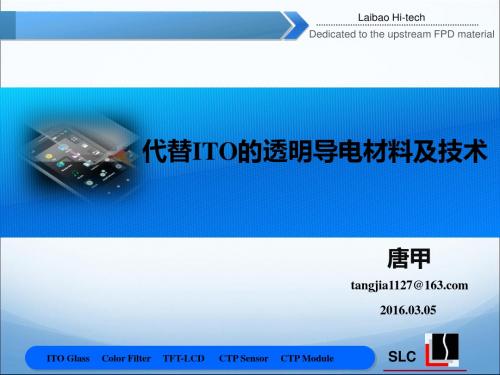
目录
新材料概述 金属网栅
Laibao Hi-tech
Dedicated to the upstream FPD material
纳米银
导电高分子 石墨烯
ITO Glass
Color Filter
TFT-LCD
CTP Sensor
CTP Module
SLC
一 新型透明导电材料概述
Laibao Hi-tech
ITO Glass
Color Filter
TFT-LCD
CTP Sensor
CTP Module
SLC
二. 金属网栅
Laibao Hi-tech
Dedicated to the upstream FPD material
②直接网印技术 印刷油墨内含有许多粒径大小约为数百纳米的银颗粒形 成导电油墨,透过精密遮罩,将线路直接成型,产品面阻 约0.5Ω,线宽约20um,透明度为70%-80%,Gunze公司早 在2009年用该方法制作透明电极膜。
ITO Glass
Color Filter
TFT-LCD
CTP Sensor
CTP ModuleLeabharlann SLC二. 金属网栅
金属线若是采用上下交叠的正交规 则结构,很容易形成光学干涉,也就是 所谓的莫瑞纹(Moire pattern).在高解 析的显示器上更为显著。 光学干涉的原因: ①来自金属网的规则 网格与下方面板pixel规则图案重叠; ②网格的节点过粗造成的。因此使用金 属网做Touch sensor时,通常会旋转一 个角度来避免图案重叠,同时线径够细 降低节点过粗。
Laibao Hi-tech
Dedicated to the upstream FPD material
COF的生产工艺及技术的发展(中元咨询)

北京中元智盛市场研究有限公司第一节COF制造技术总述 (2)一、COF的问世 (2)二、COF的技术构成 (2)第二节COF挠性基板的生产工艺技术 (3)一、COF挠性基板生产的工艺过程总述及工艺特点 (3)二、挠性基板材料的选择 (5)三、精细线路的制作 (7)第三节IC芯片的安装技术 (9)第四节COF挠性基板的主要性能指标 (11)第一节COF制造技术总述一、COF的问世随着电子、通讯产业的蓬勃发展,液晶及等离子等平板显示器的需求与日剧增,大尺寸如液晶显示器、液晶电视、等离子电视,中小尺寸如手机、数码相机、数码摄像机以及其它3C产品。
这些产品都是以轻薄短小为发展趋势的,这就要求必须有高密度、小体积、能自由安装的新一代封装技术来满足以上需求。
而COF技术正是在这样的背景下迅速发展壮大,成为LCD、PDP等平板显示器的驱动IC的一种主要封装形式,进而成为这些显示模组的重要组成部分。
COF技术已经成为未来平板显示器的驱动IC封装的主流趋势之一。
二、COF的技术构成虽然COF是一种新兴的IC封装技术,但它的工艺制程和传统的FPC及IC安装技术兼容,人们能够用现有的设备生产出COF产品。
包括了浇铸法制无胶FCCL,制作精细线路,涂覆阻焊层,焊盘镀Ni/Au,IC安装,被动元件焊接(回流焊),LCD面板安装等步骤。
其中最关键,也是难度最大的两个工艺步骤为制作精细线路和IC芯片的安装。
图表- 1:COF封装技术工艺流程2第二节COF挠性基板的生产工艺技术一、COF挠性基板生产的工艺过程总述及工艺特点生产流程双面板制开料→钻孔→PTH→电镀→前处理→贴干膜→对位→曝光→显影→图形电镀→脱膜→前处理→贴干膜→对位曝光→显影→蚀刻→脱膜→表面处理→贴覆盖膜→压制→固化→沉镍金→印字符→剪切→电测→冲切→终检→包装→出货单面板制开料→钻孔→贴干膜→对位→曝光→显影→蚀刻→脱膜→表面处理→贴覆盖膜→压制→固化→表面处理→沉镍金→印字符→剪切→电测→冲切→终检→包装→出货1、传统挠性基板制造工艺挠性基板传统制造工艺有连续法(Roll-to-Roll,即卷筒法)和非连续法(片材加工法)。
皮带托滚生产工艺流程

皮带托滚生产工艺流程英文回答:Belt Conveyor Idler Production Process.The production process of belt conveyor idlers involves several stages, each of which plays a crucial role in ensuring the quality and durability of the final product. The key steps in belt conveyor idler production include:1. Design and Engineering:The first stage involves designing the idler based on the specific requirements of the conveyor system. This includes determining the roller diameter, length, material, and bearing type.2. Raw Material Preparation:The next step is preparing the raw materials, whichtypically includes steel tubes and bearings. The steel tubes are cut to the desired length and undergo surface treatment to remove any imperfections. Bearings are cleaned and lubricated to ensure smooth operation.3. Tube Forming and Welding:The steel tubes are formed into a cylindrical shape using a roll forming machine. The ends of the tubes are then welded together to create the roller shell. The welding process is critical in ensuring the strength and durability of the idler.4. End Disc Assembly:End discs are attached to the roller shell using bolts or welding. The end discs provide support for the bearings and prevent them from moving out of place.5. Bearing Installation:Bearings are pressed into the end discs, after whichthey are lubricated and sealed to prevent contamination.The type of bearings used depends on the load capacity and operating conditions of the idler.6. Shaft Installation:The shaft, which supports the roller, is inserted into the bearings. The shaft is typically made of high-strength steel and is machined to precise tolerances.7. Roller Assembly:The roller assembly is completed by attaching theroller to the shaft. This can be done using a press fit, keyway, or other locking mechanism.8. Final Inspection and Testing:Once assembled, the idler undergoes a rigorousinspection and testing process to ensure that it meets the required specifications. This includes checking for defects, dimensional accuracy, and performance under load.9. Painting and Finishing:The idler is painted with a protective coating, typically a powder coating or epoxy paint, to prevent corrosion and enhance its aesthetic appeal.10. Packaging and Shipping:The finished idlers are packaged and shipped to the customer for installation on the conveyor system. Proper packaging ensures that they arrive at the site undamaged.中文回答:皮带托滚生产工艺流程。
胶辊生产工艺流程英文介绍

胶辊生产工艺流程英文介绍Rubber Roller Manufacturing Process.The rubber roller manufacturing process is a meticulous series of steps that transform raw materials into precision industrial components. These rollers are widely used in industries such as printing, textile, and packaging, where they play a crucial role in ensuring the efficiency and quality of various operations.1. Material Preparation.The first step in the process is to prepare the raw materials. This involves selecting high-quality rubber compounds that will be used as the base material for the rollers. The compounds are chosen based on their mechanical properties, durability, and resistance to wear and tear. Other additives, such as fillers, stabilizers, and lubricants, may also be incorporated to enhance the performance of the final product.2. Mixing and Compounding.In the mixing stage, the rubber compounds and other additives are combined in a mixer to create a homogeneous mass. This step is crucial as it ensures that the components are evenly distributed throughout the rubber, providing consistent properties throughout the roller. The temperature and duration of mixing are carefully controlled to avoid damaging the rubber's structure.3. Molding.Once the material is mixed, it is ready for molding. This involves pouring the rubber compound into a pre-designed mold, which determines the shape and size of the final roller. The mold is usually made of metal and is precision-engineered to ensure accurate replication of the desired dimensions. The rubber is then pressed orvulcanized to fill the mold cavity and take its final shape.4. Vulcanization.Vulcanization is a crucial step in the rubber roller manufacturing process. It involves heating the molded rubber at high temperatures to trigger a chemical reaction that cross-links the rubber molecules, greatly increasing its strength and durability. This process is typically carried out in a vulcanizer, a specialized oven that provides uniform heating and pressure.5. Post-Vulcanization Processing.After vulcanization, the rollers undergo post-processing steps to achieve the desired surface finish and dimensions. This may include grinding, buffing, or machining to remove any imperfections or excess material. The rollers may also be coated with a protective layer to enhance their wear resistance or provide a specific surface texture for improved ink transfer.6. Quality Control.Quality control is a continuous process throughout themanufacturing cycle. It involves periodic inspections of the rollers to ensure they meet the required specifications in terms of dimensions, hardness, surface finish, and other mechanical properties. Non-conforming rollers are discarded or reworked to ensure that only the highest-quality products leave the factory.7. Packaging and Storage.Once the rollers have passed quality control, they are ready for packaging and storage. They are carefully wrapped in protective materials to prevent damage during transport and stored in controlled environments to maintain their integrity until they are ready for use.In summary, the rubber roller manufacturing process is a multi-step operation that requires precise control of materials, processes, and quality assurance measures. It results in the production of high-quality rollers that are essential for various industrial applications, ensuring smooth, efficient, and reliable operations.。
皮带托滚生产工艺流程
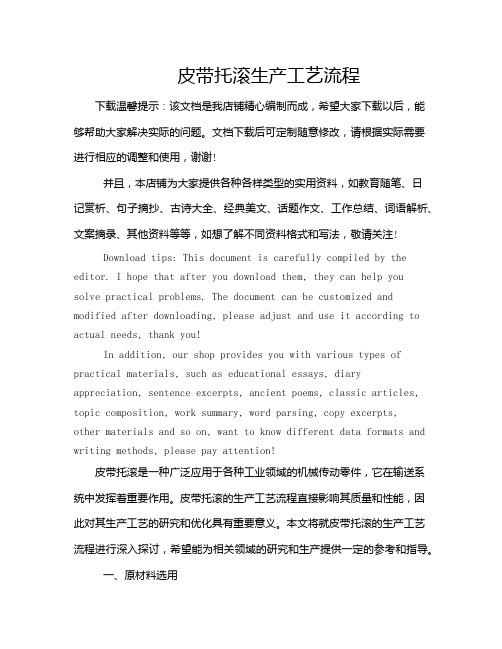
皮带托滚生产工艺流程下载温馨提示:该文档是我店铺精心编制而成,希望大家下载以后,能够帮助大家解决实际的问题。
文档下载后可定制随意修改,请根据实际需要进行相应的调整和使用,谢谢!并且,本店铺为大家提供各种各样类型的实用资料,如教育随笔、日记赏析、句子摘抄、古诗大全、经典美文、话题作文、工作总结、词语解析、文案摘录、其他资料等等,如想了解不同资料格式和写法,敬请关注!Download tips: This document is carefully compiled by the editor. I hope that after you download them, they can help yousolve practical problems. The document can be customized and modified after downloading, please adjust and use it according to actual needs, thank you!In addition, our shop provides you with various types of practical materials, such as educational essays, diary appreciation, sentence excerpts, ancient poems, classic articles, topic composition, work summary, word parsing, copy excerpts,other materials and so on, want to know different data formats and writing methods, please pay attention!皮带托滚是一种广泛应用于各种工业领域的机械传动零件,它在输送系统中发挥着重要作用。
冷轧堆法的工艺流程
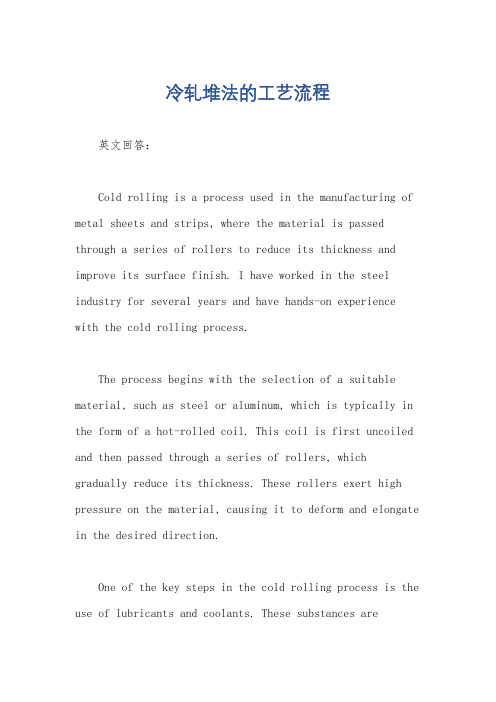
冷轧堆法的工艺流程英文回答:Cold rolling is a process used in the manufacturing of metal sheets and strips, where the material is passed through a series of rollers to reduce its thickness and improve its surface finish. I have worked in the steel industry for several years and have hands-on experience with the cold rolling process.The process begins with the selection of a suitable material, such as steel or aluminum, which is typically in the form of a hot-rolled coil. This coil is first uncoiled and then passed through a series of rollers, which gradually reduce its thickness. These rollers exert high pressure on the material, causing it to deform and elongate in the desired direction.One of the key steps in the cold rolling process is the use of lubricants and coolants. These substances areapplied to the material during the rolling process to reduce friction and heat generation. They also help in improving the surface finish of the final product. For example, in the steel industry, a mixture of oil and water is commonly used as a lubricant and coolant.After each pass through the rollers, the material is annealed to relieve internal stresses and improve its mechanical properties. Annealing involves heating the material to a specific temperature and then allowing it to cool slowly. This process helps in reducing hardness and increasing ductility.The cold rolling process can be repeated multiple times to achieve the desired thickness and surface finish. Each pass through the rollers reduces the thickness of the material by a certain percentage. For example, if theinitial thickness of the material is 10 mm, each pass through the rollers may reduce it by 20%, resulting in a final thickness of 8 mm after five passes.Once the desired thickness is achieved, the material isfurther processed to meet specific requirements, such as cutting it into sheets or coiling it into rolls. Thesefinal products can be used in various industries, including automotive, construction, and packaging.中文回答:冷轧是一种用于制造金属板材和带材的工艺,其中材料通过一系列辊轧机,以减小其厚度并改善其表面光洁度。
滚子加工工艺流程

滚子加工工艺流程Roller processing technology is a crucial part of manufacturing in various industries, such as automotive, aerospace, and machinery. 滚子加工技术是汽车、航空航天和机械等各个行业制造中至关重要的一环。
It involves a series of intricate processes to transform raw materialsinto precision-engineered rollers for use in bearings, conveyor systems, and other mechanical components. 它涉及一系列复杂的工艺,将原材料转化为用于轴承、输送系统和其他机械零部件的精密加工滚子。
The first step in the roller processing technology involves the careful selection of the raw material. 滚子加工技术的第一步是仔细选择原材料。
Materials such as steel, aluminum, and titanium are commonly used for manufacturing rollers due to their high strength and durability. 由于其高强度和耐用性,钢铁、铝和钛等材料通常用于制造滚子。
Once the raw material is selected, it undergoes a process of shaping, cutting, and heat treatment to achieve the desired dimensions and mechanical properties. 一旦选定原材料,它就会经历成型、切割和热处理的过程,以达到期望的尺寸和机械性能。
螺旋千斤顶的加工工艺流程

螺旋千斤顶的加工工艺流程英文回答:The manufacturing process of a spiral jack involves several steps to ensure the production of a high-quality and functional product. Here, I will walk you through the process in detail.Step 1: Material selection.First and foremost, the selection of suitable materials is crucial for the production of a spiral jack. Typically, materials such as steel or alloy steel are used due totheir strength and durability. The choice of material depends on the specific requirements and intended use of the jack.Step 2: Cutting and shaping.Once the material is selected, it needs to be cut andshaped according to the design specifications. This can be done through various methods, such as laser cutting or machining. For example, the main body of the jack and the spiral rod are cut and shaped to the desired dimensions.Step 3: Heat treatment.After the initial shaping, the components of the spiral jack undergo heat treatment to improve their mechanical properties. Heat treatment processes like quenching and tempering are commonly used to enhance the strength, hardness, and toughness of the materials. This ensures that the jack can withstand heavy loads and repeated use without deformation or failure.Step 4: Machining and assembly.Next, the components are further machined and prepared for assembly. This includes processes like drilling, milling, and threading to create the necessary holes and threads for the assembly of the jack. Additionally, any surface finishing, such as polishing or coating, may alsobe applied at this stage to enhance the appearance and corrosion resistance of the jack.Step 5: Assembly and testing.Once all the components are ready, they are assembled together to form the complete spiral jack. This involves fitting the spiral rod into the main body, attaching the handle, and ensuring all the parts are securely fastened. After assembly, the jack undergoes rigorous testing to ensure its functionality, safety, and reliability. This may include load testing, durability testing, and performance testing.Step 6: Packaging and quality control.Finally, the finished spiral jacks are packaged and prepared for shipment. Quality control measures are implemented throughout the manufacturing process toidentify and rectify any defects or issues. This ensures that only high-quality products are delivered to the customers.中文回答:螺旋千斤顶的加工工艺流程包括几个步骤,以确保生产出高质量和功能性的产品。
一种低噪音轴承滚道超精油石的制备方法

一种低噪音轴承滚道超精油石的制备方法,包括以下步骤:在去离子水中加入固定剂搅拌溶解,在溶液中依次加入78%~82%的CBN磨料和10%~13%β碳化硅,并搅拌,接着加入8%~12%的低温高硼硅玻璃粉,并搅拌,接着加入1%~2%的PMMA微球,并搅拌,制备原材料,然后在原材料中依次加入反应剂和消泡剂,并搅拌,将制得的溶液倒入模具,在室温下静置8小时以上,凝固后得到成型块,将成型块放置在真空干燥箱中干燥,然后烧结并渗透石蜡,切割获得
石蜡具有润滑作用,提高产品表面质量使其表面均匀,确保轴承滚道的粗糙度,降低轴承在转动时的噪音。
数字喷墨打印技术在PCB字符工艺中的应用

数字喷墨打印技术在PCB字符工艺中的应用卢玉蛟;黄哲赟;李宝【摘要】This paper describes the principle and advantage of digital inkjet printing technology for the fabrication of PCB legend. The advantage of fewer production processes, shorter process cycle, and less ink waste shows that digital inkjet printing is a cost-effective method in the PCB fabrication. In addition, inkjet printing is an environmentally friendly method, which meets green ideas. The above demonstrates that digital inkier printer will become a new development direction of the PCB legend manufacturing.%概述了文字喷墨打印技术的原理及其优点。
文字喷印机可明显简化PCB文字工艺流程,提高生产效率,且生产过程中无墨水的浪费,最终体现为生产成本的降低;另外文字喷印机环保无污染,符合绿色环保理念。
以上诸多优点将使其成为未来PCB文字工艺的发展方向。
【期刊名称】《印制电路信息》【年(卷),期】2011(000)012【总页数】5页(P55-59)【关键词】数字喷印;线路板;文字工艺;绿色环保【作者】卢玉蛟;黄哲赟;李宝【作者单位】江苏锐毕利实业有限公司,江苏盐城224056;江苏锐毕利实业有限公司,江苏盐城224056;江苏锐毕利实业有限公司,江苏盐城224056【正文语种】中文【中图分类】TN41数字化文字喷印机的原理是根据从CAD或CAM得到的文件资料将特定的文字墨水喷印到电路板上,并通过紫外灯实现即时固化从而完成字符工艺的过程。
roll to roll

关键词‧滚轮Roller‧软板Web‧可挠性Flexible‧寻边检测Edgedetect‧张力控制Tensioncontrol 摘要光‧电‧与‧半‧导‧体‧设‧备‧技‧术‧专‧辑ToconferthemajortwocontrolledobjectofRoll-to-rollapparatus.Botharetensionintheinternalpartofthe web andthewebisslantedinlateraldirection.Becausethe distribut ion of tension in web is stable or not, itwillinvolve in the dimension of lengthwise direction.Iftensionisnotstable,itwillinfluenceonqualityt hatisnot thesamewithspecificationbeforehand.Whenthe webistransportedinthesurfaceprocess,itwillcauseaserio usdefectiftheweddeviatesfromitsoriginaldirection.前言针对Roll-to-roll设备的两个主要的控制对象做探讨,分别为张力和偏移量,因为软板内部张力值稳定与否,关系到产品生产完成后的纵向尺寸是否与预定的规格一致,而当软板在传送的过程中是否发生横向偏移量,对软板表面加工制程的质量优良与否有着极大的关系。
何谓Roll-to-roll 制程,顾名思义就是指使用滚轮传输结构进行软板、可挠性材料(通常是塑料板材亦可能是金属薄板基材)的相关制程,可挠性材料在此制程中使用滚轮来控制它传输的方向,并保持适当的张力及稳定的传输速度,甚且进行精密的定位传输,它有以下几点特点:1.属于一种连续式的生产方式以生产薄膜制品2.可节省人力因此相对降低生产成本。
- 1、下载文档前请自行甄别文档内容的完整性,平台不提供额外的编辑、内容补充、找答案等附加服务。
- 2、"仅部分预览"的文档,不可在线预览部分如存在完整性等问题,可反馈申请退款(可完整预览的文档不适用该条件!)。
- 3、如文档侵犯您的权益,请联系客服反馈,我们会尽快为您处理(人工客服工作时间:9:00-18:30)。
用Roll to Roll生产工艺研制精细线路2009-6-1 16:04:42 资料来源:PCBcity 作者: 张宣东吴向好何波摘要 | 随着电子技术的蓬勃发展,挠性印制电路板的线路节距正在不断减小。
当常规设备批量生产线宽/线距为0.05mm/0.05mm的精细导线图形时,其合格率也并未因生产条件受到严格控制而得到提高。
本文结合实际阐述了具有自动化程度高、生产效率、合格率高的Roll to Roll生产工艺,并采用Roll to Roll生产工艺对精细线路进行了研制。
一、Roll to Roll生产工艺的出现1898年,英国专利中首次在世界上提出了石蜡纸基板中制作扁平导体电路的发明,几年后,大发明家爱迪生也在实验记录中大胆地设想了在类似薄膜上印刷厚膜电路。
然而直到20世纪70年代初,随着聚酰亚胺树脂合成的工业化,美国PCB业才率先将FPC工业商品化,使得其在军工电子产品中得到使用。
随后,用于FPC制造的FCCL也伴同PI薄膜产品的发展走上先进规模的工业化道路,FPC的制造逐渐在各国PCB业迎来春天,以其轻、薄、短、小、结构灵活的特点牢牢吸引住了各类电子设备生产商的眼光。
随着FPC产品的广泛应用,产品对制作技术的要求日趋提高,片式生产技术已不能满足部分产品的技术需求,尤其是当常规设备批量生产线宽/线距为0.05mm/0.05mm的精细导线图形时,其合格率也并未因生产条件受到严格控制而得到提高。
针对片式生产技术的费时费力、劳动强度大、生产率低、尺寸稳定性(受热、受湿)较难保证,以及对于制造高密度精细线宽/线距的FPC合格率不高,质量亦难保证,而开发的连续传送滚筒(Roll to Roll)生产工艺便成功地解决了上述问题。
20世纪80年代,世界上少数大型FPC生产厂家就开始建立了RTR生产线,由于当时所采用的工艺技术尚未成熟,使得RTR生产线上所生产的FPC产品合格率仍然很低。
90年代后期,日本、欧美的连续卷带法生产FPC在生产工艺、设备上都有了很大的进展。
特别是21世纪初,RTR方式生产FPC的技术的发展更体现在了FPC产品制造宽度、高密度布线、孔加工方式、双面板制作上。
二、Roll to Roll生产工艺的特点RTR技术是指挠性覆铜板通过成卷连续的方式进行FPC制作的工艺技术。
采用Roll-to-Roll生产工艺,不仅能提高生产率,而更重要的是提高自动化程度。
这种高自动化的生产明显地减少了人为操作和管理因素,受环境条件(温度、湿度洁净度等)影响变化小,因而具有更均匀一致而稳定的尺寸偏差,从而也易于进行修正和补偿,所以它具有更高的产品合格率、质量和可靠性。
三、Roll to Roll生产工艺的应用我国由于FPC起步较晚,RTR制作技术应用较少。
为了迎合FPC产品市场的需要,提升市场竞争力,国内挠性印制板生产企业也纷纷把目光投入RTR生产技术,开始进行“RTR挠性电路开发与应用”的研究。
为达到高精细线路制作的高良品率和低成本化的工艺水平,我司也于2007年投入到Rol to Roll工艺生产挠性印制板的应用与研究中,旨在解决片式生产高精密线路开短路严重合格率低的问题,同时达到减少人力成本的目的。
本文即通过本司在RTR方式生产FPC板的技术改造对“RTR FPC开发与应用”进行阐述。
3.1 流程确定RTR方式生产FPC的技术改造,首先应根据RTR设备的性能及企业实际生产的FPC产品类型和特点的需要确定整个流程如何分段,或显影、蚀刻、脱膜、后处理一体,或显影与蚀刻、脱膜、后处理分离。
显影与蚀刻分离的作用,在于分离后显影线与蚀刻线可同时进行不同底铜厚度的FPC的生产,可独立调节显影线和蚀刻线的参数多样生产。
考虑到我司1/2oz、1oz底铜使用量都很大的情况最终采用的是分段式(蚀刻与显影分开)双列250mm宽DES线。
综合我司现在的技术能力和对片材生产的熟悉程度及前期投资数量,为达到片材向卷材平稳过渡,我司的RTR工艺流程:3.2 RTR工艺生产FPC的研究在确定对RTR如何分段后, RTR的定位方式、张力控制、传送控制和材料弯曲变形的防止四因素便成了关键。
上世纪80年代,RTR生产线所生产FPC产品的合格率低很大程度上也就正是因为这些技术尚未成熟完善。
各工序中定位和张力、传送控制都与材料平整度的保持直接联系,不恰当的定位方式、传送参数以及放收卷时不适宜的张力都会引起材料的弯曲变形。
为实现RTR 生产工艺的优势,需对各工序的张力、传送等因素进行调整和严格的控制。
以下通过线宽/线距为0.05mm/0.05mm的精细线路的研制分别介绍。
3.2.1 选材高精细线路的制作中,制作方式非常重要,基材的选取也相当关键。
根据以往在制作高精细线路时的经验,减成法制备精细线路时,底铜厚度越薄越易达到预想效果,制备出线宽损失小,蚀刻系数大,侧蚀程度小的线路。
片式生产中当基材厚度较薄时,为防止在开料到压制前操作导致的褶皱,常规的方法是在基材上先贴背胶,而RTR设备生产则不存在这一问题无需背胶。
3.2.2 贴膜贴膜是挠性印制板图形转移的第一步,贴膜品质直接影响整个图形转移的成败。
高品质的贴膜不仅要杜绝因铜面和干膜的不洁引起的板面杂质,而且板面要求平整、无气泡、无皱折,干膜的附着力达标,密合度高。
对于全自动卷式生产,贴膜工序各参数的控制就更为重要,稍有不慎,造成的浪费损失将是巨大的。
虽然RTR设备生产FPC不需背胶解决薄板的褶皱问题,但各工序中仍然要十分注意操作过程中的传送和张力控制防止材料的弯曲变形。
贴膜工序中则重点控制好贴膜的压力、温度和卷材传送的速度,避免不当温度、传送速度造成的针孔、气泡和皱折,使得铜面干膜附着力高。
3.2.3 曝光曝光是挠性印制板线路形成的开始。
精确对位、曝光能量是曝光工序中需特别注意的因素,其中对位精度在RTR自动曝光流程中尤为重要,一旦对位出现偏差而进行返工,将造成整卷干膜等资源的浪费。
近年来,不断有空间对位方面的发明出现,在我们最新的RTR平行曝光机中就自带有寻边器感应卷材传送以及步距控制器调控对位精度,以确保曝光工序线路的形成。
3.2.4 DES曝光完成后,挠性印制板的图形转移便进入湿流程阶段。
卷式流程与片式流程的DES 工序并没有太大的变化,主要区别在于卷式流程中由于薄基材未贴压背胶,卷材在DES的传送过程中传送滚轮将有可能在线路面上造成行轮印,影响导体的外观及性能。
为避免行轮印问题的出现,可选择性地将DES线的传送滚轮替换成实心滚轮。
3.2.5 与片式生产工艺的比较比较片式与卷式工艺生产0.05/0.05mm线宽/线距的结果(见图1,2)。
从上述图片中,我们可以看出,RTR工艺生产的线路的线宽情况和蚀刻系数都与片式相当。
然而尽管片式工艺生产0.05/0.05mm线路时严格控制生产条件,最优化工艺参数,其线路的开短路仍然大量存在,使得产品合格率不高,最佳批量生产合格率也只达75%。
而采用RTR生产工艺时,由于其减少了人为操作和管理因素,受环境条件影响变化小,开短路问题得到了很好的控制,批量生产合格率达到了90%。
与片式生产工艺相比,RTR生产工艺优势不仅在于提高了合格率,还体现在大大提高了生产的自动化程度。
从贴膜曝光到显影蚀刻脱膜,片式生产需12名操作人员,而RTR生产只需4人,大大的节省了劳动力。
3.3 线宽/线距为0.03mm/0.03mm的精细线路的研制3.3.1 选材众所周知,FCCL铜箔的厚度越薄,蚀刻后线条的侧蚀越小,尤其是在制备高精细线路时。
比较了12μm和10μm两种厚度底铜的覆铜板在制备精细线路上的优劣,笔者最终选用底铜为10μm的2L FCCL作为研制线宽/线距为0.03mm/0.03mm的精细线路的基材。
精细线路的研制,所采用干膜的性能也相当关键。
考虑到在实际运用中同系列干膜的厚度越薄其赋形性能解像能力越佳,在线宽/线距达到0.03mm/0.03mm精细线路的研制中将采用15μm厚度的杜邦干膜。
3.3.2 试制在贴膜过程中,由于为提高解像度使用了15μm的干膜,其较常用干膜薄50%,故而对贴膜参数作了轻微调整,适量降低贴膜温度和压力,加快贴膜速度。
曝光过程,经试验证明,对制作0.03mm线宽线距的精细导线时,最佳曝光级数为6级(21级曝光尺)。
0.03mm的线宽无疑是对RTRDES线制程能力的重大挑战,故在DES过程中对显影蚀刻机的各参数调节应相当谨慎。
本试制中,为达到预期的效果,对显影蚀刻机的运行速度与喷淋压力进行了严格的控制。
所得线路见图3。
0.03mm/0.03mm线路的生产,确实很难由片式工艺逾越,而采用在合格率、受环境影响小等较优的RTR技术其结果亦不甚让人满意,线路的开短路虽不严重,但DES的蚀刻速度仍然过快,所得线路间距跟预期比过大。
四、结束语目前国内采用减成法制作0.03mm/0.03mm线宽/线距精密线路仍然是PCB业界的技术难题。
尽管如此,RTR生产工艺的出现大大提高了FPC的生产效率,保证了精细线宽/线距FPC 的合格率,其不仅可应用于FPC的生产,也可应用于FPC后续的封装。
随着电子机械技术地不断发展,较精密较复杂的封装及检测仪器(如自动光学检测AOI、双向非平面软板锡膏印刷机)亦不断地被引入到RTR生产线中,日本的Epson等公司已然拥有从FPC基材形成到最终封装完毕的全RTR生产线。
基于这些优点,RTR生产工艺的应用前景是相当广阔的。
文章摘自《印制电路资讯》09年5月第3期本文资料经作者授权:PCB网城版权所有,转载请注明出处,抄袭必究。