4.车辆铝合金大型材模具的设计与制造工艺研究
汽车铝合金轮毂模具及数控加工工艺设计

毂由于功能上存在一定的局限性, 已经逐渐被取代。 新型的铝合金轮毂因其 自 身质量轻、 散热快、 减震性能好、 轮胎寿命长安全可靠、 尺寸
精确平衡好 以及容易加 工制造等优 点被广泛使 用在现代汽制造行业 中。现代化社会发展产生 巨大的生产需求。 数字化技 术的应 用将会整 体提升 汽车制造行业的进步 , 通过 采用先进 的汽车铝合金轮毂模具及数控加 工工艺 , 全 面改善常规机械制造 中 存 在的不足 , 实现轮毂 整 体 最优化模式的形成。 本 文通过对铝合金轮毂的优点 以及铝合金轮毂模具数控加 工工艺的相关事项进行简要 分析 。 从而强化我国汽车制 造行 业生产 工艺简便 、 快捷 、 可靠的 高效性模 式 , 为我 国经济效益
汽车铝合金轮毂模 具及数控 加工工艺设 计
郭志斌 f 秦皇 岛戴卡兴龙轮毂有限公 司, ; 可北 秦皇 岛 0 6 6 0 0 4 )
摘 要: 自从我 国实行改开放政 策以来, 国家整体经济建设得 到显著提 高, 从 而促使我 国更行业的快速发展 , 其 中对于汽车制造行业 的发展 凸显优越 。 伴 随社会整体不 断进步 , 推 动我 国人们 生活质量水平的提升 , 越 来越 多的人们选择 购买车辆 来方便 出行。 传统的汽车轮
关键词 : 铝 合金 轮 毂 ; 数控加工 ; 模 具
1铝合金轮 毂的优点 ( 2 ) 分析 毛坯在定位安装方面的适应性 ; 传统 的轮毂一般材质都是钢制 , 虽然钢制轮毂在生产 成本上较 ( 3 ) 分析毛坯余量 的大小及均匀性。 不同类 型的零件要选用相应 铝合金材质 的轮毂低 , 但是这种类型 的轮毂一定程度 上存 在着功能 的数控 机床加工 , 以发挥数 控机床的特点和效率 。加工顺序 的安排 结构不足 , 对于铝合金轮毂却是具有很多优点 , 其 中就包括散热快 、 应根据零件 的结构 和毛坯状况 ,以及定位安装 与夹紧 的需 要来考 重量轻 、 强度大 、 舒适 性好 、 效益好 、 安全性好等几方面 的特点 , 非常 虑 , 重点是工件 的刚性不被破坏。 符合现代轿车整体结构需 求 , 铝合金轮 毂将 会因其诸多的优点成为 4轮毂模具底模数控 ̄ m - r - r 艺设计 日 后轻量化发展的必然趋势。 如下对铝合金轮毂上述几方面的优点 在铝轮毂模具的加工方面, 一般是采用进 口 或国产的单轴立式 特性进行详细说 明: 或卧式数控机床, 高精度 C N C加工单元, 切削液冷却。常用的方法主 ( 1 ) 散热快。 一般汽车在道路行驶过程中 , 轮胎与地面都会发 生 要 是在 M V一 6 1 0机 床 S I N U M E R I K 8 1 0 D系统 上进行 数控 铣削 加工 定程度上 的摩擦从而产生相应 的热量 , 同时制动盘和制动 片之 间 的 N C编程及刀路仿真 。 的摩擦作用也会 产生一定 热量 。这样长时间的高热量工作环境下 , 铝轮底模 的加工工 艺流程模具底 模是铝 轮挤压铸 造装 备 的关 轮胎 以及制 动装置就会发生 不同程度 的老化 、 磨损, 不仅影 响汽车 键零件它 的加 工质量不仅决定该 模具的装配质 量还关 系到铝轮 毛 整体制 动效率 , 同时也会增加交 通事故危险 , 例如爆 胎和汽 车刹车 坯生产质量最终影 响到汽车 的安全行驶 。 底模的主要加工技术要求 失灵 问题 。常规 的钢制轮毂散热效果不是非常快 , 造成热量不能及 为底模与侧模 配合处 的尺寸精度 为 h 8 底模工作部分 的表面粗糙 度 时 性地散去 。但是 铝合金轮毂 由于铝 的热容量 大是钢制 的 5 倍之 为 R a 0 . 8 如果挤压 面 的表 面质量要求 较高时其 工作表面可 取 R a 0 . 多, 这样能够将大量热 量散 去 , 降低安全问题 的出现。 0 2 0 . 0 8底模 工作表面不允许 有任何的表面缺 陷如裂纹 、 发裂、 剥落 ( 2 ) 重量轻 。 一般轮毂重量过大的话 , 汽车在进行转动过程中惯 及 各种孔洞底模 导入处端面与柱面 交接 处不允许 有倒角或 圆角 以 量就会随之增 大 , 造 成汽车加速和刹 车功能整体下 降 , 同时汽车 在 免产 生毛刺或合金 液飞溅各 圆柱体 的同轴度要求为 q b 0 . 1 m m尺寸 行驶过程 中也会消 费大量 的能源 。铝合金 轮毂 中铝材 密度 比钢材 精度要 求 为 I T 7全 圆弧 形表面粗糙度 为 R a 3 . 2 a r m且不 能有 明显 的 小, 并且铝合金轮毂 比同尺寸的钢轮毂轻, 这样 采用 铝合金轮毂整体 接刀痕迹底模 在粗加工后最好 进行一次去应 力退火半 精加工后进 改善 了钢轮毂 中存在的不足 , 提升 了汽车使用性 能。 行调质处理 。针对上述 要求 不难看 出该零件的加工难点主要为 : ( 3 ) 强度大。 强度这个问题是在重量一定 的前提下 , 同钢制相 比 ( 1 ) 工件工作表面 比较复杂采用一般方法 很难达到加工要 求而 同等 重量 的轮毂 , 铝合金 轮毂 的强度较钢 轮毂坚 固耐 用 ; 同样相 同 采用数控加工 的方法能保证 加工质量 。 强度 的轮毂 , 铝合金 由于 自身密度低 , 重量也轻于钢制 轮毂 。 ( 2 ) 该模 具需要长期承受高温作用属于难切削加工材料 。 ( 4 ) 舒适性好 。目前进行轮毂设计加工 中通常采用旋 压技 术手 ( 3 ) 模具表面成形后不能再热处 理去除加工应力要求 高 。因此 段, 这样精 密度高 同时失 圆度 和不平衡 度也都很 小, 在 使用过程 中 为保证铝轮挤压 铸造模具底模 的加工质量在 实际生产 中须采取特 铝合金的弹性模数 较小 航 振性好, 整体降低 了汽车行驶 过程中车身 殊 的工艺措 施: 粗、 精加工分 开并选择合 理的切 削用量 以减少热 变 振动现象 , 提升了汽车使用舒适度 。 形保证加 工精度和表 面质 量铸 件去应力退火 先进行普通 车床 粗加 ( 5 ) 造型美 , 易加工。 铝合金熔点低 , 在不 同厂商 的设计要求下 , 工, 调质处理 后进行数 控铣削加 工铣削加工采 用球 头刀分粗 、 精 加 能够生产 出不 同形态外观的制成 品, 易于加工处理 。同时铝合金容 工进 行 。精 加工切 削深度不 大于 0 . 0 5 mm粗加 工切削深 度控 制在 易进行切 削加工 , 能够有效地保 障轮毂几何尺寸的精密度。 0 . 2 m m以内。
车用铝合金中铝板冲压的设计及生产的关键技术

车用铝合金中铝板冲压的设计及生产的关键技术随着汽车工业的发展与普及,车用铝合金中铝板冲压技术日渐成熟,成为了汽车制造领域中不可或缺的一部分。
车用铝合金中铝板冲压技术能够大幅度减轻汽车的整体重量,提高车辆的燃油经济性和性能,同时也对汽车的外观设计起到了很大的提升作用。
本文将围绕车用铝合金中铝板冲压的设计及生产的关键技术展开探讨。
一、铝合金中铝板冲压的设计1. 材料选择:在车用铝合金中铝板冲压的设计中,首先需要选择合适的材料。
一般来说,车身冲压零部件所采用的铝合金材料要求具有高强度、高塑性、良好的焊接性、优异的表面质量和成型性能。
目前常用的车用铝合金材料有6系、5系和7系铝合金,其中6系铝合金具有良好的塑性和强度综合性能,被广泛应用于车身冲压零部件的制造。
2. 模具设计:冲压模具是车用铝合金中铝板冲压中至关重要的工艺设备。
模具设计直接影响着产品的成型质量和生产效率。
冲压模具主要包括上模、下模和冲头等部分,其中冲头是决定产品成型质量和表面质量的重要部件。
在车用铝合金中铝板的冲压模具设计中,需要考虑到材料的流动性、成形难度、成形是否均匀等因素,合理设计模具结构和尺寸参数,以确保产品成型质量和生产效率。
3. 工艺流程设计:在车用铝合金中铝板冲压的设计中,需要合理确定冲压的工艺流程。
工艺流程设计需要考虑到产品的结构形状、尺寸精度要求、表面质量要求等因素,以确保产品的成型质量和工艺效率。
1. 强化处理技术:为了提高车用铝合金中铝板的机械性能,常常需要进行强化处理。
强化处理技术主要包括固溶处理和时效处理两种。
固溶处理是指将合金加热到固溶温度,然后经过适当的保温时间后,迅速冷却到室温。
时效处理是指在固溶处理后,通过加热保温一定时间,再经过适当的冷却处理。
通过合理的强化处理技术,可以显著提高车用铝合金中铝板的强度和硬度,满足汽车零部件的使用性能要求。
2. 成形工艺技术:在车用铝合金中铝板的冲压成形过程中,需要考虑到材料的成形性能和成形工艺的合理性。
铝型材模具设计与制造

铝型材模具设计与制造在铝型材生产企业中,模具成本在型材挤压生产成本中占到20%-40%。
模具的好坏以及模具是否能够合理使用和维护,直接决定了企业是否能够正常、合格的生产出型材来。
挤压模具在型材挤压生产中的工作条件是十分恶劣的,既需要在高温、高压下承受剧烈的摩擦、磨损作用,并且还需要承受周期性载荷作用。
这都需要模具具有较高的热稳定性、热疲劳性、热耐磨性和足够的韧性。
为满足以上几项要求,目前在国内普遍采用优质H13合金钢,并采用真空热处理淬火等方式来制作模具,以满足铝型材生产中的各项要求。
由于型材产品结构各种各样,在实际生产中,模具的使用寿命差异也较大,有的无法使用达到预定产量,严重的甚至挤压不到20条棒或上机不到2次就提前报废,致使采用昂贵的模具钢制作的模具远远不能实现其应有的效益。
所以针对不同型材产品,结构的优化,模具的设计至关重要。
1.铝型材模具设计与制造过程:(1)铝型材结构的评审优化,尽量确保截面壁厚均匀,如果是多腔结构,腔体尺寸尽量至少3mm以上。
铝型材断面的设计原则:第一,端面大小的选择。
型材断面大小用外形来衡量,外接圆越大,所需的挤压压力就越大。
一般来说,每台挤压机上能挤压的最大外接圆型材不是固定不变的,与挤压筒直径是有一定关系的,挤压型材的最大外接圆一般比挤压筒直径小25~50mm,挤压空心型材时则应更小一些。
第二,断面形状的复杂性。
根据型材形状主要分成三大类,即实心型材、半空心型材及空心型材。
形状不同,对模具以及工艺都有比较大的影响,。
一般可以通过形状因素指数来初步判断型材挤压的难度,指数F=型材外接圆直径C*型材断面周长/型材断面面积,指数值F越大,则型材就越难挤压。
第三,挤压系数。
合理的挤压系数对于型材能否正常加压是很重要的一个参数。
一般来说,纯铝的挤压系数可达300,6063合金可达200,硬铝可选为20~60。
第四,型材壁厚。
某一特定型材壁厚最小值取决于型材的外接圆直径的大小、合金成分和形状因素等。
大型型材铝合金模具的设计制作和维修

大型铝合金型材的模具设计制作与维修邵莲芬(西南铝业集团有限公司)摘要:介绍了大型铝合金型材的特点,着重讨论各种大型材的模具结构、尺寸设计以及模具制造与修理等方面的关键问题,根据生产实践经验,例举了几种典型复杂模具的设计和试生产情况,有较好的实用价值。
关键词:大型铝合金型材;模具设计;制造;修理;分流孔;阻流随着现代化经济的高速发展,铝合金型材正向着大型化、薄壁扁宽化、尺寸高精度化、形状复杂化的方向发展。
由于铝型材本身具备诸多优点,它的应用范围已拓展到航空航天、交通运输、机械制造和电子电力等各个领域。
也由于大型型材可带来巨大的经济和社会效益,各大铝业公司都先后购进大型挤压机,加大资金投入生产大型铝合金型材。
1 大型铝合金挤压型材的特点界定大型型材一般是根据它的外形尺寸或断面积大小:(1)型材的宽度或外接圆直径大于250 mm;(2)型材的断面积大于2 000 mm2;(3)型材交货长度大于10 m。
诸如薄壁扁宽且宽厚比大于130的型材,见图1a;多孔中空复杂断面型材,见图1b;加强筋高度H>80 mm的中空型材,见图1c;壁厚差较大、中空带实心的大断面型材,见图1d;空心部分位于型材边缘的型材,见图1e等。
类似这些典型型材的模具模腔形状和相关尺寸都相当繁杂、挤压时的温度场、速度场和应力应变场难于控制,所以模具的设计、制作和维修都具有一定的难度。
图1 典型的大型型材断面图2 典型大型材的模具设计2.1 薄壁扁宽型材(图1a)的模具设计2.1.1 薄壁扁宽型材的特点(1)该型材宽厚比W较大:W=360/2.4=160;(2)壁薄(壁厚t0=2.4 mm,按正常规定薄壁扁宽型材,当宽度为360 mm时,t0一般不小于2.8 mm);(3)型材材料为6063合金,选用36 MN挤压机,直径为330 mm挤压筒生产,其挤压比λ=83。
薄壁扁宽型材的模具设计简图见图2。
2.1.2 本例模子设计方案的特点(1)本例型材采用分流焊合挤压法生产。
建筑铝合金模板型材模具的设计制造技术方案浅析

建筑铝合金模板型材模具的设计制造技术方案浅析【摘要】建筑铝合金模板型材模具在建筑行业中起着重要作用,为提高建筑施工效率和质量,设计制造优质的模具至关重要。
本文从建筑铝合金模板型材模具的设计、选择与加工、制造技术方案、使用注意事项以及优劣势分析等方面进行了浅析。
通过对这些关键技术点的研究,总结了建筑铝合金模板型材模具的设计制造技术方案,并对未来的研究展望进行了探讨。
建筑铝合金模板型材模具的设计制造技术方案不仅能够提高建筑施工效率,还能够降低施工成本,是值得深入研究和推广应用的。
【关键词】建筑铝合金模板型材模具, 设计制造技术方案, 铝合金模板型材, 模具制造技术, 模具使用注意事项, 优劣势分析, 研究背景, 研究意义, 结论, 未来研究展望1. 引言1.1 研究背景建筑行业是国民经济的支柱产业之一,在建筑过程中,模板是不可或缺的重要部分。
传统的木质模板存在重量大、易变形、施工效率低等缺点,为了解决这些问题,铝合金模板型材模具应运而生。
铝合金模板型材模具具有重量轻、强度高、耐用性强等优点,已经在建筑施工中得到广泛应用。
目前关于建筑铝合金模板型材模具的设计制造技术方案方面的研究还比较有限。
有必要对建筑铝合金模板型材模具的设计制造技术方案进行深入探讨和分析,以提高建筑施工效率、节约成本、保障施工质量。
本文旨在通过对建筑铝合金模板型材模具的设计制造技术方案进行浅析,探讨其优劣势、使用注意事项,并展望未来的研究方向,为建筑行业的发展和进步提供参考和借鉴。
1.2 研究意义建筑铝合金模板型材模具的设计制造技术方案浅析引言通过深入研究建筑铝合金模板型材模具的设计制造技术方案,可以更好地理解模具的工作原理和运用方法,为施工过程提供更多的便利和支持。
通过优化设计和制造工艺,可以提高模具的使用寿命和稳定性,减少施工中的问题和风险。
研究建筑铝合金模板型材模具的设计制造技术方案具有重要的理论和实践意义,对于推动建筑行业的发展和提高建筑质量具有积极的促进作用。
车用铝合金中铝板冲压的设计及生产的关键技术

车用铝合金中铝板冲压的设计及生产的关键技术随着社会的发展和科技的进步,车用铝合金中铝板冲压技术在汽车制造行业中得到了越来越广泛的应用。
车身板件作为汽车的重要组成部分,其设计制作直接关系到汽车的外观和性能,因此对车用铝合金中铝板冲压的设计及生产的关键技术有着非常高的要求。
一、设计1. 材料选择车用铝合金中铝板冲压的首要任务是选用合适的材料。
在选择材料时需要考虑到铝合金的强度、硬度、延展性等性能指标,以及对汽车整体质量的影响。
常用的铝合金有5052、6061、7075等,设计师需要根据具体的使用场景和要求选择合适的材料。
2. 模具设计模具设计是车用铝合金中铝板冲压中至关重要的一环,直接决定了冲压成型的精度和质量。
在模具设计中需要考虑到产品的结构特点,合理设计模具结构,保证产品的冲压成型质量和生产效率。
3. 工艺设计车用铝合金中铝板冲压的工艺设计包括了冲压过程的工艺路线、冲压工序的顺序、冲压机的选型等内容。
合理的工艺设计能够使得产品的成型过程更加顺畅、精准,提高生产效率和产品质量。
二、生产1. 冲压设备冲压设备是车用铝合金中铝板冲压生产中的关键设备,对产品的成型质量和生产效率有着直接的影响。
目前常用的冲压设备有液压冲床、机械冲床等,工厂需要根据生产需求选择合适的冲压设备。
2. 精密控制在车用铝合金中铝板冲压生产中,需要进行精密的控制来确保产品的质量和精度。
包括对冲压负荷、速度、温度等参数进行准确控制,以及对冲压模具的使用和维护进行严格管理。
3. 质检与改进在整个车用铝合金中铝板冲压的生产过程中需要进行严格的质量检测和控制,及时发现问题并进行改进。
例如采用成型试验来验证模具设计的可行性和合理性,以及对成品进行全面的检查和测试等。
三、关键技术1. 材料成型技术原料的成型质量对最终产品的成形质量有着直接的影响,控制原料的成型技术是车用铝合金中铝板冲压的关键技术之一。
需要对原料的厚度、宽度、形状等进行严格控制,确保原料的均匀性和一致性。
车用铝合金中铝板冲压的设计及生产的关键技术
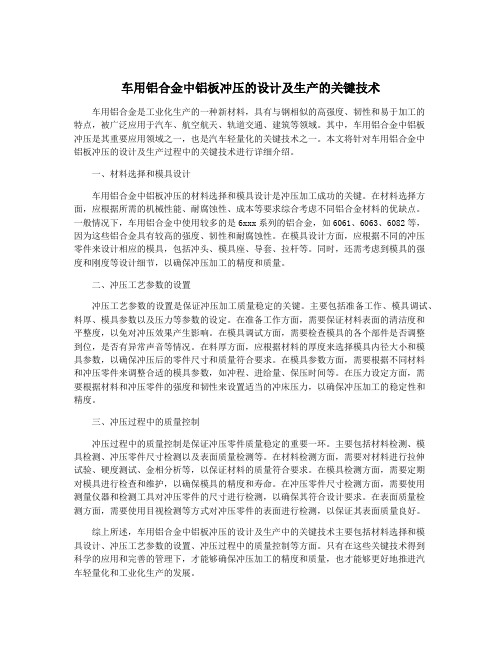
车用铝合金中铝板冲压的设计及生产的关键技术车用铝合金是工业化生产的一种新材料,具有与钢相似的高强度、韧性和易于加工的特点,被广泛应用于汽车、航空航天、轨道交通、建筑等领域。
其中,车用铝合金中铝板冲压是其重要应用领域之一,也是汽车轻量化的关键技术之一。
本文将针对车用铝合金中铝板冲压的设计及生产过程中的关键技术进行详细介绍。
一、材料选择和模具设计车用铝合金中铝板冲压的材料选择和模具设计是冲压加工成功的关键。
在材料选择方面,应根据所需的机械性能、耐腐蚀性、成本等要求综合考虑不同铝合金材料的优缺点。
一般情况下,车用铝合金中使用较多的是6xxx系列的铝合金,如6061、6063、6082等,因为这些铝合金具有较高的强度、韧性和耐腐蚀性。
在模具设计方面,应根据不同的冲压零件来设计相应的模具,包括冲头、模具座、导套、拉杆等。
同时,还需考虑到模具的强度和刚度等设计细节,以确保冲压加工的精度和质量。
二、冲压工艺参数的设置冲压工艺参数的设置是保证冲压加工质量稳定的关键。
主要包括准备工作、模具调试、料厚、模具参数以及压力等参数的设定。
在准备工作方面,需要保证材料表面的清洁度和平整度,以免对冲压效果产生影响。
在模具调试方面,需要检查模具的各个部件是否调整到位,是否有异常声音等情况。
在料厚方面,应根据材料的厚度来选择模具内径大小和模具参数,以确保冲压后的零件尺寸和质量符合要求。
在模具参数方面,需要根据不同材料和冲压零件来调整合适的模具参数,如冲程、进给量、保压时间等。
在压力设定方面,需要根据材料和冲压零件的强度和韧性来设置适当的冲床压力,以确保冲压加工的稳定性和精度。
三、冲压过程中的质量控制冲压过程中的质量控制是保证冲压零件质量稳定的重要一环。
主要包括材料检测、模具检测、冲压零件尺寸检测以及表面质量检测等。
在材料检测方面,需要对材料进行拉伸试验、硬度测试、金相分析等,以保证材料的质量符合要求。
在模具检测方面,需要定期对模具进行检查和维护,以确保模具的精度和寿命。
高铁用大型复杂铝合金铸件的模具设计与制造技术
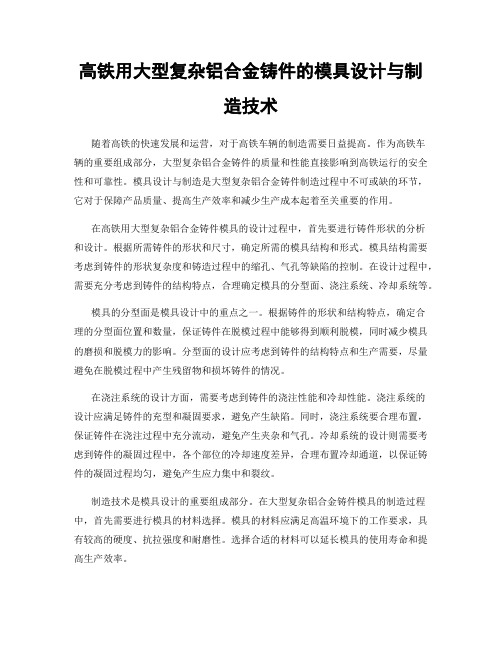
高铁用大型复杂铝合金铸件的模具设计与制造技术随着高铁的快速发展和运营,对于高铁车辆的制造需要日益提高。
作为高铁车辆的重要组成部分,大型复杂铝合金铸件的质量和性能直接影响到高铁运行的安全性和可靠性。
模具设计与制造是大型复杂铝合金铸件制造过程中不可或缺的环节,它对于保障产品质量、提高生产效率和减少生产成本起着至关重要的作用。
在高铁用大型复杂铝合金铸件模具的设计过程中,首先要进行铸件形状的分析和设计。
根据所需铸件的形状和尺寸,确定所需的模具结构和形式。
模具结构需要考虑到铸件的形状复杂度和铸造过程中的缩孔、气孔等缺陷的控制。
在设计过程中,需要充分考虑到铸件的结构特点,合理确定模具的分型面、浇注系统、冷却系统等。
模具的分型面是模具设计中的重点之一。
根据铸件的形状和结构特点,确定合理的分型面位置和数量,保证铸件在脱模过程中能够得到顺利脱模,同时减少模具的磨损和脱模力的影响。
分型面的设计应考虑到铸件的结构特点和生产需要,尽量避免在脱模过程中产生残留物和损坏铸件的情况。
在浇注系统的设计方面,需要考虑到铸件的浇注性能和冷却性能。
浇注系统的设计应满足铸件的充型和凝固要求,避免产生缺陷。
同时,浇注系统要合理布置,保证铸件在浇注过程中充分流动,避免产生夹杂和气孔。
冷却系统的设计则需要考虑到铸件的凝固过程中,各个部位的冷却速度差异,合理布置冷却通道,以保证铸件的凝固过程均匀,避免产生应力集中和裂纹。
制造技术是模具设计的重要组成部分。
在大型复杂铝合金铸件模具的制造过程中,首先需要进行模具的材料选择。
模具的材料应满足高温环境下的工作要求,具有较高的硬度、抗拉强度和耐磨性。
选择合适的材料可以延长模具的使用寿命和提高生产效率。
模具的加工工艺是确保模具质量的关键。
在加工过程中,需要使用先进的数控加工设备和精密的加工工艺,保证模具的加工精度和表面质量。
特别是在大型模具的制造过程中,需要采用多道次的加工工艺,通过精细的修磨和抛光,保证模具的精度和密封性。
车用铝合金中铝板冲压的设计及生产的关键技术

车用铝合金中铝板冲压的设计及生产的关键技术
1. 铝合金板材的选择:铝合金板材具有良好的塑性和可锻性,能够满足复杂形状的
冲压需求。
在车辆制造中常用的铝合金板材有5系、6系和7系。
5系铝合金具有良好的耐腐蚀性和可焊接性,适用于车身外板等部位;6系铝合金具有较高的强度和热处理性能,
适用于车架等高强度部件;7系铝合金具有超高强度和疲劳寿命,适用于重载部件例如承
力梁等。
2. 冲压工艺的设计:冲压工艺的设计是实现车用铝合金中铝板冲压的关键。
首先需
要根据所需的零件形状和尺寸,通过计算和模拟分析确定冲床的压力、速度和行程等参数。
还需要设计合适的冲头和模具,以确保冲压过程中铝板的变形和切削达到预期的要求。
3. 衬板和垫块的应用:在车用铝合金中铝板冲压过程中,为了避免铝板的变形和划伤,常常需要在冲头和模具之间插入衬板和垫块。
衬板通常由聚酰亚胺(PI)或聚四氟乙
烯(PTFE)等材料制成,具有良好的耐磨损和耐高温性能;垫块通常由橡胶或塑料材料制成,能够减小冲压过程中的冲击力和振动。
4. 表面处理技术:车用铝合金中铝板冲压后,常常需要进行表面处理,以提高零件
的耐腐蚀性和装饰效果。
常见的表面处理技术包括阳极氧化、电泳涂装、喷涂和电镀等。
这些技术能够形成一层保护膜,防止铝板与外界环境发生化学反应,提高零件的使用寿
命。
车用铝合金中铝板冲压的设计及生产需要考虑铝合金板材的选择、冲压工艺的设计、
衬板和垫块的应用以及表面处理技术等关键技术。
通过合理的设计和生产控制,能够实现
高质量和高效率的车用铝合金中铝板冲压生产。
建筑铝合金模板型材模具的设计制造技术方案浅析

建筑铝合金模板型材模具的设计制造技术方案浅析1. 引言1.1 背景介绍建筑铝合金模板在建筑施工中具有重要作用,其质量和效率直接影响着工程进度和质量。
铝合金模板型材模具的设计制造技术在现代建筑领域中得到了广泛应用,其质量和性能直接影响着施工效率和工程质量。
随着建筑行业的不断发展,对铝合金模板型材模具设计制造技术的要求也越来越高。
铝合金模板型材模具设计制造技术的发展离不开科学技术的支持和不断创新。
随着材料科学、机械制造、自动化技术的不断提升,铝合金模板型材模具设计制造技术正在不断完善和升级。
深入研究铝合金模板型材模具的设计制造技术方案,对于提高建筑施工效率和质量具有重要意义。
当前,**建筑铝合金模板型材模具的设计制造技术方案需要进一步探讨和改进,以适应市场需求和技术发展的要求。
**1.2 问题概述建筑行业是我国国民经济的支柱产业之一,而建筑铝合金模板在建筑施工中扮演着非常重要的角色。
在实际应用中,由于铝合金模板型材模具的设计与制造技术存在一定的问题,限制了其在建筑领域的发展和应用。
目前,存在以下几个主要问题:1. 设计不合理:部分铝合金模板型材模具设计不符合实际施工要求,影响施工效率和质量。
2. 制造工艺粗糙:部分铝合金模板型材模具制造工艺简单粗糙,无法满足高质量、大规模施工需求。
3. 成本过高:由于设计制造不规范,导致铝合金模板型材模具的成本偏高,降低了施工企业的竞争力。
针对以上问题,有必要对建筑铝合金模板型材模具的设计制造技术方案进行深入研究和探讨,以提高其设计制造质量和效率,降低成本,更好地满足建筑施工需求。
1.3 研究目的研究目的是为了深入探讨建筑铝合金模板型材模具的设计制造技术,从而提高建筑施工效率和质量,降低成本,推动铝合金模板型材模具行业的发展和进步。
通过对设计原理、制造流程、技术方案分析、关键技术与工艺以及质量控制措施的研究,旨在为铝合金模板型材模具的设计制造提供更科学、高效、可靠的解决方案,为建筑施工行业提供更好的支持和服务。
车用铝合金中铝板冲压的设计及生产的关键技术

车用铝合金中铝板冲压的设计及生产的关键技术随着汽车轻量化的发展趋势,车用铝合金材料在汽车制造中的应用愈发广泛。
而在车身及零部件制造中,铝板冲压技术是一项关键的生产工艺。
本文将重点介绍车用铝合金中铝板冲压的设计及生产的关键技术。
设计阶段在车用铝合金中铝板冲压的设计阶段,需要考虑以下几个关键技术点:1. 材料选择:铝合金材料的选择对于冲压工艺至关重要。
一般而言,汽车中常用的铝合金材料有6系和7系两种。
6系铝合金具有良好的可加工性和韧性,适合用于一般冲压件的制造;而7系铝合金则具有较高的强度和硬度,适合用于制造要求更高的零部件,如车轮等。
2. 零部件设计:在设计车用铝合金中的铝板冲压零部件时,需要考虑其形状复杂度、厚度分布、变形特性等因素。
合理的设计可以降低冲压成本,减小材料浪费,提高产品质量。
3. 模具设计:模具是冲压工艺的关键,直接影响零部件的成型质量。
在设计模具时,需要考虑材料的选择、模具结构、冲压力的传递方式等因素。
生产阶段1. 材料处理:铝合金材料在冲压前需要进行预处理,包括氧化膜清除、表面处理、退火等工艺。
氧化膜的清除对于提高冲压质量至关重要。
2. 冲压工艺:车用铝合金中铝板冲压的工艺包括下料、模具装配、模具调试、冲压成型等环节。
在这个过程中,需要注意工艺参数的设定、模具的调整、冲压速度的控制等关键技术。
3. 质量控制:在冲压过程中,需要通过一系列的质量控制手段来保证产品的质量。
包括对材料的质量把控、对工艺参数的监控、对成品的检测等。
关键技术车用铝合金中铝板冲压的关键技术主要包括材料选择、零部件设计、模具设计、材料处理、冲压工艺、质量控制等方面。
这些技术点的合理运用能够提高产品的质量,降低成本,推动汽车轻量化的发展。
材料选择是车用铝合金中铝板冲压的第一步,选择合适的铝合金材料可以保证产品的成型质量和性能。
合理的零部件设计和模具设计也能够降低生产成本,提高生产效率。
材料处理和冲压工艺则是冲压生产过程中的关键环节,通过合理的处理和控制能够保证产品质量和工艺稳定性。
铝合金车体型材设计的工艺性

铝合金车体型材设计的工艺性【摘要】主要介绍了铝合金车体型材设计中型材断面的设计、筋板的加工工艺,并对筋板的布置方式、筋板角度等进行了分析。
【关键词】铝合金型材;挤压工艺;筋板0 引言铝合金车体结构大部分由铝型材构成,型材断面的设计直接决定了生产过程中的工作量、工作效率和制造难易程度,因此铝合金结构的车体型材的设计应从全局出发,尽最大可能方便后道工序,型材的设计包括了型材的宽与厚设计,筋板的设计,型材滑槽的设计等,本文仅对型材设计的工艺进行分析。
1 型材设计的工艺性1)型材二维空间的工艺性(1)结构设计中要尽量采用宽的型材横断面,减少型材焊接工作量(2)块状、条状结构件应尽量采用型材模具,避免水刀切割工作量(3)型材宽度公差要合理(4)型材四边壁厚要比中间的肋厚0.5~1mm2)筋板的工艺性筋板类零件多采用分体制造后焊接或铸造方式加工,难以满足服役条件,无法达到预期的效果。
采用焊接加工,焊缝强度低,削弱了承载能力,带筋部位流线不完整,焊接时变形量大,不能满足精度要求;采用铸造加工,铸造状态晶粒尺寸比较大、组织不细密,产品力学性能较差,强度仅能达到350MPa;采用数控加工或化铣加工,不仅材料的利用率低、成本高、环境污染严重,而且加强筋部位的金属流线被切割,使构件的强度大大降低,难以满足构件的使用性能。
挤压工艺生产的零件与其他方法如切削加工生产出来的零件相比,其优点在于保持了金属纤维的完整性,并使其沿零件外形轮廓分布,这样可显著地提高零件的承载能力,另外还可以改善锻件组织,使零件的韧性和塑性同时提高。
根据生产实践,采用挤压工艺生产带有薄腹板的筋类、盘类、梁类、框类等精锻件具有很大的优越性。
该类零件采用挤压方法加工,成形后的内筋不需要再进行切削加工,通过筋板与腔体的整体塑性成形,使金属流线沿零件的几何外形分布,保证了筋部位流线的完整,克服了焊接或锻造强度低的问题,同时提高了产品的内部组织和力学性能,提高了生产率,节约了金属材料。
铝合金模具的生产工艺流程
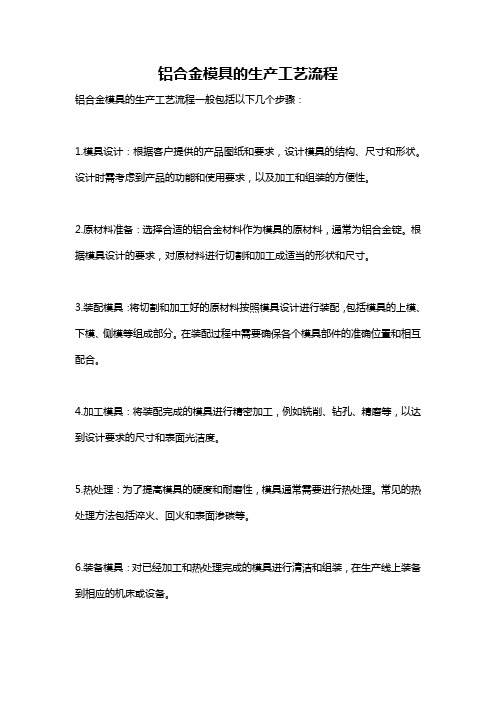
铝合金模具的生产工艺流程
铝合金模具的生产工艺流程一般包括以下几个步骤:
1.模具设计:根据客户提供的产品图纸和要求,设计模具的结构、尺寸和形状。
设计时需考虑到产品的功能和使用要求,以及加工和组装的方便性。
2.原材料准备:选择合适的铝合金材料作为模具的原材料,通常为铝合金锭。
根据模具设计的要求,对原材料进行切割和加工成适当的形状和尺寸。
3.装配模具:将切割和加工好的原材料按照模具设计进行装配,包括模具的上模、下模、侧模等组成部分。
在装配过程中需要确保各个模具部件的准确位置和相互配合。
4.加工模具:将装配完成的模具进行精密加工,例如铣削、钻孔、精磨等,以达到设计要求的尺寸和表面光洁度。
5.热处理:为了提高模具的硬度和耐磨性,模具通常需要进行热处理。
常见的热处理方法包括淬火、回火和表面渗碳等。
6.装备模具:对已经加工和热处理完成的模具进行清洁和组装,在生产线上装备到相应的机床或设备。
7.调试和试产:进行模具的初步调试和试产,确保模具的精度和稳定性。
在试产过程中,检查模具的开合、冷却系统和注塑或压铸过程的效果。
8.维护和保养:模具在使用过程中需要进行定期的保养和维护,包括清洁、润滑和更换磨损部件等。
维护和保养的目的是保证模具的正常使用寿命和生产效率。
以上就是铝合金模具的生产工艺流程的一般步骤,具体的操作和流程可能会因为不同的模具类型和生产要求有所差别,需要根据实际情况进行调整。
铝合金车身加工工艺研究
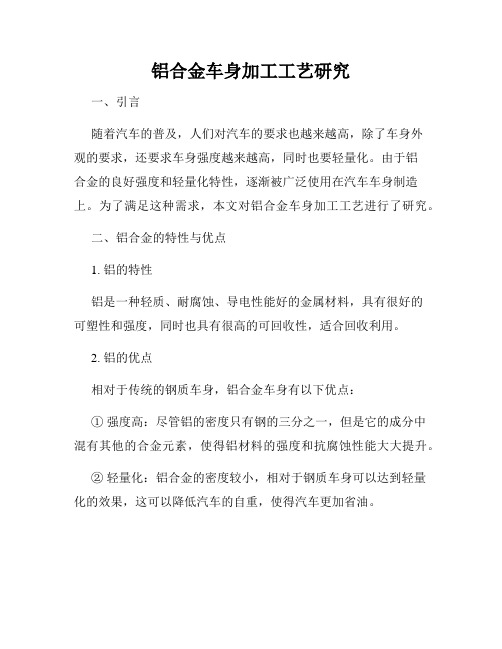
铝合金车身加工工艺研究一、引言随着汽车的普及,人们对汽车的要求也越来越高,除了车身外观的要求,还要求车身强度越来越高,同时也要轻量化。
由于铝合金的良好强度和轻量化特性,逐渐被广泛使用在汽车车身制造上。
为了满足这种需求,本文对铝合金车身加工工艺进行了研究。
二、铝合金的特性与优点1. 铝的特性铝是一种轻质、耐腐蚀、导电性能好的金属材料,具有很好的可塑性和强度,同时也具有很高的可回收性,适合回收利用。
2. 铝的优点相对于传统的钢质车身,铝合金车身有以下优点:①强度高:尽管铝的密度只有钢的三分之一,但是它的成分中混有其他的合金元素,使得铝材料的强度和抗腐蚀性能大大提升。
②轻量化:铝合金的密度较小,相对于钢质车身可以达到轻量化的效果,这可以降低汽车的自重,使得汽车更加省油。
③良好的成形性能:铝具有很好的可加工性,可以很方便地通过压制、铸造等方式制作各种形状,这也为汽车制造厂商提供了更多的设计空间,使得汽车的外形更加多样化。
三、铝合金车身加工工艺铝合金车身加工工艺包括了压铸、锻造、拉伸等多种工艺。
下面分别进行介绍:1. 压铸工艺压铸工艺是一种通过高压力将铝合金液态金属压入模具中,然后将模具加热,使其凝固,从而制成铝合金车身的方法。
这种方法具有成形精度高、生产效率高、耗能低等优点,能够大规模生产。
2. 锻造工艺锻造是将铝合金材料放入锻造机中,经过高温和高压的作用,让材料在短时间内得到定形的方法。
锻造方法可以分为自由锻造和模锻造两种。
自由锻造是通过铜锤将铝合金加热到可挠性状态后,敲打出不同的形状。
模锻造是铝合金材料经过在特殊模具中锤击,完成各种形状的加工方法。
3. 拉伸工艺拉伸工艺是将铝合金材料拉成线状或者条状,并经过加热处理后变成各种形状的方法。
拉伸工艺不仅具有成形能力强、加工效率高的优点,同时也可以提高铝合金车身的强度和硬度。
四、结论本文介绍了铝合金的优点和特性,以及铝合金车身加工的三种方法,包括压铸、锻造、拉伸等。
铝合金汽车零件压铸模具的加工成型技术

铝合金汽车零件压铸模具的加工成型技术摘要:铝合金是工业制造中重要的原材料,特别是在汽车工业领域,铝合金制成的零件占了绝大多数。
但由于材质的特殊性,如何对其进行加工才能达到理想效果,是制造过程中要重点考虑的。
为了得到高质量的汽车铝合金类零件,本文对汽车铝合金类零件的技术特点进行了分析,确定了加工过程中工序设计、刀具、参数等的选择。
关键词:铝合金;零件;加工;刀具;高速铣铝合金作为工业生产中的主要原材料,它的主要成分中的合金元素镁与硅。
铝合金密度低,但强度比较高,接近或超过优质钢,塑性好,可加工成各种型材,具有优良的导电性、导热性和抗蚀性,工业上广泛使用,使用量仅次于钢。
特别是在汽车工业领域,铝合金制成的零件占了绝大多数。
但铝合金加工中容易产生各种变形,因此,铝合金类的零件对加工工艺的要求较高。
一、铝合金压铸技术概述1.1压铸工艺原理压铸方法可分为热室压铸和冷室压铸两大类。
热室压铸中,压射系统的压室置于坩埚内,充型时,压射冲头可以直接将坩埚内的金属液推进压室,然后通过压射系统的鹅颈管进入型腔。
冷室压铸中,熔化金属的坩埚和冷室压铸机相分离,冷室压铸生产效率较热室低,但其应用范围较广,铝、锌、镁、铜等有色合金均可使用冷室压铸方法加工。
1.2压铸工艺特点压铸填充压力一般为几兆帕到几十兆帕,最大填充速度能够达到每秒上百米,使整个压铸过程中压射时间极短,体现了压力铸造技术高速高压的优势。
由于充填时有增压过程,得到的压铸件组织致密,能够保证所需要的强度和硬度。
互换性方面,在同一压铸厂,同一型号的零件均由同一副压铸模具成型,所以零件的互换性好。
压铸工艺的以上特点,使其在提高有色金属合金铸件的精度水平、表面质量及生产效率等方面显示出较大优势。
1.3铝合金支架副机组支架是将动力转向泵与水泵等附件固定于汽车副机组发动机上的直接支撑,且负责油道和水道的运输,保障发动机的正常运转。
在汽车行驶过程中,该零件一方面要保持副机组发动机与动力转向泵等附件的固定和平稳,另一方面还需要承受汽车震动时产生的扭力作用。
汽车铝合金板件成形工艺及模具结构设计
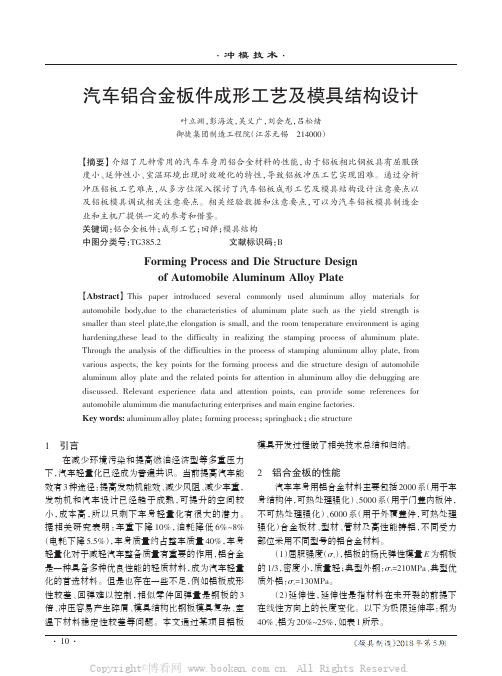
(4)由于铝板密度小,上模容易吸料,冲孔也容易
带料,废料滑出比钢板困难。结构设计时需要注意:
它没有用,铝板自动化生产中,需要在线首设置吹气
①在上模非成形部位加弹顶销,在让空部位及上下模
式分张装置,采用不间断吹气模式,吹气压力至少
周边工艺补充面上加足够多的排气孔,选用顶料型冲
起皱严重致不能压到下死点,解决相关问题后再压
件;成形性调试完成后制件外观应无明显起皱与较大
开裂;④调试完成后,做好相应记录,将调整参数反馈
给相关技术人员。
边间隙(7%~8%)t,铝板修边间隙(5%~7%)t;刀块拼
(4)型面研合:①模具倒装,以成形性调试所得样
缝间隙,钢板模具刀块拼缝间隙+0.04~0.1mm、铝板模
大补偿 5mm
图 1 CAE 数据补偿
图 5 修边碎屑多
图 2 数据补偿后仍回弹
(2)容易开裂:延伸率比钢板小,钢为 40%,铝为
20%~25%,故变形量比钢板小,极易开裂,如图 3、图 4
图 6 翻边有碎屑
《模具制造》2018 年第 5 期
Copyright©博看网 . All Rights Reserved.
系列(6022)的铝合金板材为例:新置材料的屈服强度
为 113.6MPa,存放 3 个月后的屈服强度为 126.5MPa,
所示,成形圆角和拔模角度相比钢板类零件有更高的
要求。
存放 6 个月后的屈服强度为 154.5MPa,如表 2 所示。
如果存放时间超过 6 个月,
将过硬以至于成形困难。
表1
钢板
极限延
加工时方便加垫片;②整形模具设计时要考虑后期整
形镶块后面与底面加垫片的操作可行性。
车用铝合金折弯型材挤压工艺研究
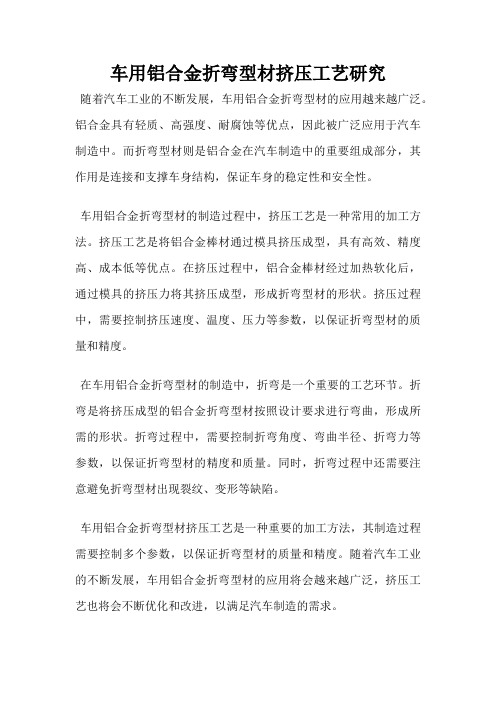
车用铝合金折弯型材挤压工艺研究
随着汽车工业的不断发展,车用铝合金折弯型材的应用越来越广泛。
铝合金具有轻质、高强度、耐腐蚀等优点,因此被广泛应用于汽车制造中。
而折弯型材则是铝合金在汽车制造中的重要组成部分,其作用是连接和支撑车身结构,保证车身的稳定性和安全性。
车用铝合金折弯型材的制造过程中,挤压工艺是一种常用的加工方法。
挤压工艺是将铝合金棒材通过模具挤压成型,具有高效、精度高、成本低等优点。
在挤压过程中,铝合金棒材经过加热软化后,通过模具的挤压力将其挤压成型,形成折弯型材的形状。
挤压过程中,需要控制挤压速度、温度、压力等参数,以保证折弯型材的质量和精度。
在车用铝合金折弯型材的制造中,折弯是一个重要的工艺环节。
折弯是将挤压成型的铝合金折弯型材按照设计要求进行弯曲,形成所需的形状。
折弯过程中,需要控制折弯角度、弯曲半径、折弯力等参数,以保证折弯型材的精度和质量。
同时,折弯过程中还需要注意避免折弯型材出现裂纹、变形等缺陷。
车用铝合金折弯型材挤压工艺是一种重要的加工方法,其制造过程需要控制多个参数,以保证折弯型材的质量和精度。
随着汽车工业的不断发展,车用铝合金折弯型材的应用将会越来越广泛,挤压工艺也将会不断优化和改进,以满足汽车制造的需求。
- 1、下载文档前请自行甄别文档内容的完整性,平台不提供额外的编辑、内容补充、找答案等附加服务。
- 2、"仅部分预览"的文档,不可在线预览部分如存在完整性等问题,可反馈申请退款(可完整预览的文档不适用该条件!)。
- 3、如文档侵犯您的权益,请联系客服反馈,我们会尽快为您处理(人工客服工作时间:9:00-18:30)。
B?FG6I<= :?< :7:IJ=<DK
D6=A@==<D+ &;< :I@C676@C :IIFJ I:?8< =6E< !"#/%% B?FG6I< @=<D GF? >?:67 MFDJ :?< <HB<?6C<7>:IJ B?FD@A<D+
O7+ E.3*;N :I@C676@C :IIFJN I:?8< =6E< <H>?@D678 B?FG6I<=N D6<N BF?>;FI<N C<>:I GIFON D<=687N C:7@G:A>@?678
[ %P(]
最大壁厚为 0* CC , 最小壁厚为 0+* CC 。型材的宽 ! 厚 比也非常大, 最大达 %.. 以上。这些都使得金属的流动 和型材的挤压成形变得非常困难。轨道车辆对型材的 外形尺寸精度和形位公差等的要求很严:要求装配面 侧 平面间隙小于 0 CC ;纵向弯曲全长上不大于 Q CC ; 向弯曲度全长上不大于 , CC ;扭拧度全长上不大于 , 力学性能必须符合表 % 的规定。 这些都给大型材模 CC 。
&;< =>?@A>@?< B:?:C<><?= :7D =6E< D<=687 FG D6< @=<D GF? <H>?@D678 :I@C676@C :IIFJ I:?8< =6E< &;< D6< ?<B:6?678 ><A;7FIF8JL C:7@G:A>@?678 D6< ><A;7FIF8J :7D D6< C:><?6:I :?<
’()*+ ,-.)( /,0)1,2()3405 67280.9.5+ ,0* :7;450 .1 :47 1.3 <=(3)*405 >9)?404)? >99.+ @,357 A3.1497 B;7* 1.3 63,40 C.*+
234 56789:7
D’.)(8E7;( >9)?404)? DF3.)GH I.JK @(*JK I8.05L405 !M#$%&K I840,H >-;(3,2(N
而且是不易充填的斜筋, 斜筋长度达到 %-+ (( 。 上 (( ,
共有 ) 下两个大面的壁厚为 /1’2 $-1& (( 。型材断面复杂,
图!
%&’(## 型材分流模设计图
/1%18
焊合室的确定 焊合室的设计有两种方式,一种是上、下模焊合
个空心孔。 但形状比较对称, 对金属流动有一定的好处。
/
!"# /1%1%
[ 具的设计与制造带来很大的难度
。
因此,国内外都把模具的设计和制造作为重大课题来 进行攻关。目前德国、 意大利、 韩国、 日本等国家的大型 模具技术在世界上处于比较领先的地位。我国大型特 种型材模具技术尚处于起步阶段,模具技术的研制开 发成功, 对地铁和高速列车的国产化具有重要的意义。
,]
。
表#
车辆铝合金型材的力学性能指标
模具设计
模具结构设计 模具规格的确定 由于轨道车辆型材大都是空心型材,因此模具多
室; 另一种为下模焊合室。国外的模具一般采用上、 下 模焊合的方式,即上模的分流桥比桥墩高 %-9/* (( , 形成上焊合室; 下 模 焊 合 腔 深 度 8*97* (( , 与上模一 起形成 7*9&* (( 深的焊合室。 在设计 !"#0%% 型材模具的焊合室时,只在下模 设计焊合室,这样容易加工。因为最大分流桥宽为 ’* 为了有利于金属的焊合及提高焊缝的质量, 焊合 ((, 室的深度设计得比较深, 为 &* (( 。 另外, 为了扩大焊合 室的外侧尺寸,增大两端头部分及两根立筋的金属供 给, 在上模分流孔外侧设计了 +,): 的斜度。
#J%
型材的特点 地 铁 、高 速 列 车 车 辆 型 材 的 品 种 大 致 分 底 板 、 顶
供货长度达 0*P0R CC , 且 R’S 以 宽度为 ,’’PQ,’ CC , 上为多孔异形空心型材。型材的壁厚变化大, 有的型材 收稿日期: 0..(/.)/%*
板、 侧板和转角等类型, 本文仅以 !"#/%% 底板为例进 行讨论。底板型材是国产化地铁型材中很典型的一类
作者简介: 刘静安 ( %1,%/) , 男, 湖南涟源人, 教授级高级工程师。
/**8 , <=>1 8%? @ 3
轻
合
金
加
工
技
术
/&
型 材 ,也 是 车 辆 型 材 生 产 难 度 系 数 很 大 的 一 类 型 材 。
分流比应大于中间的分流比。综合以上分析, !"#$%% 分流模的分流孔共设计为 3 个孔, 如图 / 所示。
0,
轻
合
金
加
工
技
术
0..( , VFI+ (%L W 1
车辆铝合金大型材模具的设计与制造工艺研究
刘静安
( 西南铝业 ( 集团) 有限责任公司, 重庆 !"#$%&)
摘要: 大型材挤压模具设计与制造是现代车辆大型铝合金型材生产的关键技术。以典型的难度较大的底板型材 !"#$ 对大型模具的结构参数和尺寸设计进行了深入分析, 并对模具材料、 热处理工艺、 模具制造工艺和修模等进 %% 为例, 行了讨论。研制出了合格的 !"#$%% 铝合金大型材。 关键词: 铝合金大型材;挤压模具;分流孔;金属流动;设计;制造工艺 中图分类号: &!’()*+,% 文献标识码: 文章编号: ( 0..( ) %..)/)0(* .1$..0,$.,
.+0
合金牌号 供应状态 壁厚 34; * !" "0%* "0.. "01. "# "# "$%
"
%.
!"
Q..*)..*
&Q &*
!* *P0* !,.
"0** "0*. "(*.
"& "& "#
%
#J#
型材的特点及难度分析
轨道车辆型材产品的难度分析 轨道列车车辆型材品种多, 结构复杂, 大多数型材
><A;7FIF8J
大型材模具设计与制造技术是车辆用铝合金大型 材生产的关键技术。地铁、高速列车车辆型材的品种 多, 精度高, 要求性能和焊缝质量好, 扁宽壁薄且形状 复杂, 空腔多且壁厚相差悬殊, 这些都给模具设计与制 造带来了极大的困难。挤压时, 极易造成堵模, 把模具 压裂或压断; 成形不好, 金属流动困难, 焊合不良, 型材 产生波浪、 扭曲、 刀弯等缺陷, 严重影响产品质量
!"#$%% 型材是底板型材之一,属扁宽薄壁空心型材,
宽 &%’ (( , 高 )* ((, 断面积为 +*,-) .( 。型材宽厚比
/
很大, 外形靠近挤压筒边缘, 成形非常困难。图 % 示出 了 !"#0%% 型材的断面图。
图$
%&’(## 型材断面图
!"#$%% 型材的壁厚很小 ,最薄处 厚 度 只有 /1&2 $-1&