弯管标准工艺卡
(完整版)机械加工工艺过程卡片及工序卡片模板
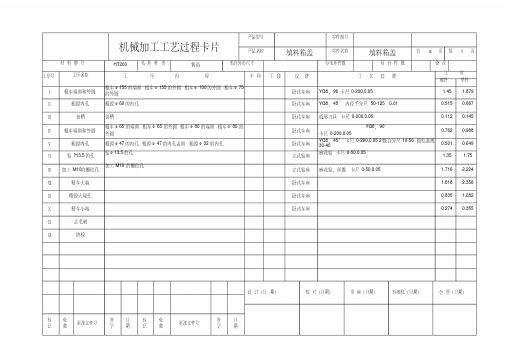
设备名称
卧式车床
夹具编号
设备型号
设备编号
夹具名称
三爪卡盘
工位器具编号
工位器具名称
同时加工件数 切削液
工序工时 (分)
准终
单件
工步号 工
Ⅰ Ⅱ Ⅲ Ⅳ
步
内
粗车Φ 155 的端面
粗车Φ 155 的外圆
粗车Φ 100 的外圆
粗车Φ 75 的外圆
主轴转速 切削速度 进给量 切削深度 进给
工步工时
容
工艺装备
进给 次数
工步工时
基本
0.287
辅助
设 计(日 期) 校 对(日期) 审 核(日期) 标准化(日期) 会 签(日期)
标记 处数 更改文件号 签字 日期 标记 更改文件号 签字 日期
标记 处数 更改文件号 签字 日期 标记 更改文件号 签字 日期
会 签(日期)
机械加工工序卡片
产品型号 产品名称
填料箱盖
车间
毛坯种类
零件图号
零件名称 工序号
填料箱盖
共8
工序名称
Ⅱ
粗镗Φ 60 的内孔
毛坯外形尺寸 每毛坯可制件数
页第 2 页 材 料 牌号
每 台 件数
设备名称
卧式车床
夹具编号
设备型号
设备编号
麻花钻 卡尺 0-50,0.05
0.762 0.501 1.35
0.145 0.988 0.649 1.75
立式钻床 麻花钻,丝锥 卡尺 0-50,0.05
1.716 2.224
Ⅷ
精车大端
卧式车床
1.818 2.356
Ⅸ
精镗大端孔
卧式车床
0.835 1.082
工艺卡片模板100例
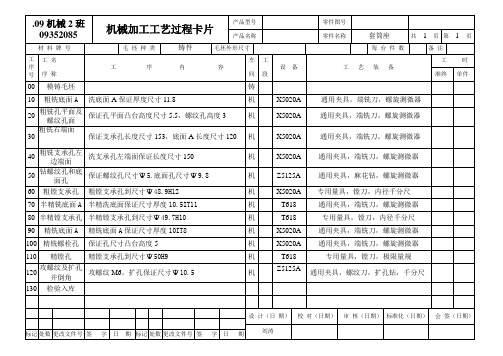
.09机械2班09352085 机械加工工艺过程卡片产品型号零件图号产品名称零件名称套筒座共 1 页第 1 页材料牌号毛坯种类铸件毛坯外形尺寸每台件数备注工序号工名序称工序内容车间工段设备工艺装备工时准终单件00 模铸毛坯铸10 粗铣底面A洗底面A保证厚度尺寸11.8 机X5020A 通用夹具,端铣刀,螺旋测微器20 粗铣孔平面及螺纹孔面保证孔平面凸台高度尺寸5.5,螺纹孔高度3 机X5020A 通用夹具,端铣刀,螺旋测微器30 粗铣右端面保证支承孔长度尺寸153,底面A长度尺寸120 机X5020A 通用夹具,端铣刀,螺旋测微器40 粗铣支承孔左边端面洗支承孔左端面保证长度尺寸150 机X5020A 通用夹具,端铣刀,螺旋测微器50 钻螺纹孔和底面孔保证螺纹孔尺寸ψ5.底面孔尺寸ψ9.8 机Z5125A 通用夹具,麻花钻,螺旋测微器60 粗镗支承孔粗镗支承孔到尺寸ψ48.9H12机X5020A 专用量具,镗刀,内径千分尺70 半精铣底面A半精洗底面保证尺寸厚度10.5IT11机T618 通用夹具,端铣刀,螺旋测微器80 半精镗支承孔半精镗支承孔到尺寸ψ49.7H10机T618专用量具,镗刀,内径千分尺90 精铣底面A精铣底面A保证尺寸厚度10IT8机X5020A 通用夹具,端铣刀,螺旋测微器100 精铣螺栓孔保证孔尺寸凸台高度5 机X5020A 通用夹具,端铣刀,螺旋测微器110 精镗孔精镗支承孔到尺寸ψ50H9机T618 专用量具,镗刀,极限量规120 攻螺纹及扩孔并倒角攻螺纹M6,扩孔保证尺寸ψ10.5机Z5125A通用夹具,螺纹刀,扩孔钻,千分尺130 检验入库设计(日期)校对(日期)审核(日期)标准化(日期)会签(日期)材料牌号毛坯种类毛坯外形尺寸每毛坯件数每台件数备注工序号工名序称工序内容车间工段设备工艺装备工时准终单件设计(日期)校对(日期)审核(日期)标准化(日期)会签(日期)材料牌号毛坯种类毛坯外形尺寸每毛坯件数每台件数备注工序号工名序称工序内容车间工段设备工艺装备工时准终单件设计(日期)校对(日期)审核(日期)标准化(日期)会签(日期)。
弯管工艺卡
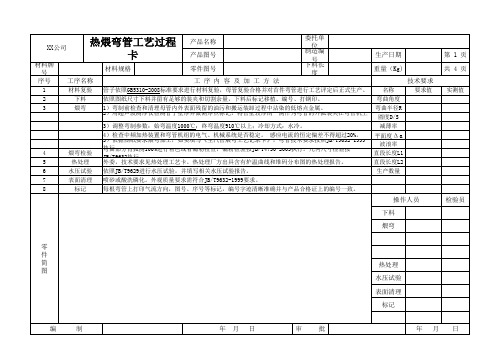
管子依照GB5310-2008标准要求进行材料复验,母管复验合格并对首件弯管进行工艺评定后正式生产。 名称 依照图纸尺寸下料并留有足够的装夹和切割余量,下料后标记移植、编号、打钢印。 弯曲角度 1)弯制前检查和清理母管内外表面残留的油污和搬运装卸过程中沾染的低熔点金属。 弯曲半径R 2)用超声波测厚仪检测管子壁厚并做测厚点标记,将管壁较厚的一侧作为弯管的外弧装夹在弯管机上。 圆度D/S 3)调整弯制参数:始弯温度1000℃;终弯温度910℃以上;冷却方式:水冷。 减薄率 4)检查中频加热装置和弯管机组的电气、机械系统是否稳定。 感应电流的恒定偏差不得超过20%。 平面度Δ a 5)依据图纸要求煨弯加工,如实填写《主汽管煨弯工艺记录卡》,弯管技术要求按照JB/T9632-1999执行。 波浪率 弯曲部分背弧侧100%进行着色或者磁粉检查,磁粉检验按JB/T4730-2005执行。几何尺寸检验按JB/T9632执行。 直段长度L1 外委,技术要求见热处理工艺卡。热处理厂方出具含有炉温曲线和堆码分布图的热处理报告。 直段长度L2 依照JB/T9629进行水压试验,并填写相关水压试验报告。 生产数量 喷砂或酸洗磷化。外观质量要求需符合JB/T9632-1999要求。 每根弯管上打印气流方向,图号、序号等标记,编号字迹清晰准确并与产品合格证上的编号一致。
操作人员 下料பைடு நூலகம்煨弯 零 件 简 图
检验员
热处理 水压试验 表面清理 标记
编
制
年 月
日
审
批
年
月
日
XX公司 材料牌号 序号
1 2 3
热煨弯管工艺过程 卡
材料规格 工序名称
材料复验 下料 煨弯
产品名称 产品图号 零件图号 工 序 内 容 及 加 工 方 法
P11管道焊接工艺卡

标准、型号
制造商牌号
焊丝
R30
CHG-55B2
焊条
E5515-B2
CHH307
保护气体
气体成分及纯度
流速
正面:
Ar 99。95
8—9L/min
背面:
/
L/min
注:不锈钢材料在焊缝厚度≤5mm前不能停止背面气体保护.
预热后热热处理
预热温度:GTAW100—200℃,SMAW150—250℃(壁厚≥10mm时需预热)
版次:A
编号:
适用范围:汽水管道或联箱封头,汽水取样、仪表等接管座。
焊接标准:DL/T869—2012
焊接工艺评定编号:
焊接方法:GTAW+SMAW
焊接位置:全位置
接头型式:T型
衬垫材料:无
接头型式、坡口和组装尺寸示意图:单位:mm
焊接层道示意图:单位:mm
母材
A侧
B侧
母材材质牌号:
A335—P11
CHH307
Φ3。2
反接
86~149
21~23
50~70
工艺说明
焊前准备、清理和检查:
除去坡口表面及边缘(10~15)mm范围内所有的油、漆、垢、锈等;检查对口尺寸。
施焊注意事项:
单层焊道的厚度不大于所用焊条直径加2mm;单焊道宽度不大于所用焊条直径的4倍。
注意接头和收弧的质量,收弧时应将熔池填满。多层多道焊的接头应错开(15~20)mm。
Φ3.2
反接
75~136
21~23
50~70
3及以上
SMAW
CHH307
Φ4。0
反接
84~161
21~23
02 管道加工工艺示范卡12.22

第2章 管道保温施工工艺示范卡2.1 适用范围本工艺卡适用于火力发电厂各类DN≥100mm,保温厚度δ≥50mm 管道绝热防冻保温工艺,其他口径管道的保温施工工艺可以参照执行。
2.2 施工流程2.3 主要施工工艺质量控制要求2.3.1参数测量(收集数据)保温管道参数测量(数据采集)直接影响到管道保温支撑环制作的尺寸是否准确。
要对实际的管道采用较精确的软皮尺抽样多点测量,然后根据设计院设计的主保温层厚度计算支撑件的个数和长度,进而确定单环与双环的个数。
2.3.2选材(保温材质选择)a) 保温材料的特性将影响管道的传热特性,必须严格按照设计院设计的管道表面温度去确定保温固定件、支撑件等铁件的材质,不可随意替代。
CPIE CBb) 管道保温材料的种类的选材可以根据图2.7中“注1”所示。
2.3.3保温支撑环的制作及安装a) 单环(A 型环)主要用于管道的鳍片间位置;双环(B 型环)主要用于管道的鳍片位置。
两鳍片间距离以3800mm 为优,一般支撑环每3800mm 之间设五个:两个双环(B 型,布置在鳍片位置)和三个单环(A 型,布置在两个鳍片之间),各环间距为(不超过)950mm 为佳。
如图2.5所示。
图2.1 保温支撑环b) 支撑外环的支腿采用与外环尺寸相同的扁钢,支腿与内环的固定采用焊接方式。
c) 支撑件不得设在有附件的位置上,环向应水平设置,各托架筋板之间安装误差不应大于10mm。
支撑件的宽度应小于绝热层的厚度10mm,但最小不得小于20mm 。
C PIECB图2.2 保温支撑环安装d) 直接焊于不锈钢设备上的支撑件,必须采用不锈钢制作。
当支撑件采用碳钢制作时,应加焊不锈钢垫板。
e) 当不允许直接焊于设备上时,应采用抱箍型支撑件。
介质温度大于200℃时,抱箍式固定件与设备之间应设置石棉板等隔垫。
2.3.4 铺设、绑扎保温材料图2.3 保温材料铺设、绑扎CPIE CBa) 一般采用的管材或毯材的长度或宽度宜为950mm,便于施工。
弯管制作工艺

弯管制作1、弯管宜采用壁厚为正公差的管子制作。
弯曲半径与直管壁厚的关系宜符合表1的规定。
表1弯曲半径与直管壁厚的关系弯曲半径R 制作弯管用管子的壁厚R≥6Do 1.06td6Do>R≥5Do 1.08td5Do>R≥4Do 1.14td4Do>R≥3Do 1.25td2、弯管弯曲半径应符合设计文件和国家现行有关标准的规定。
当无规定时,高压钢管的弯曲半径宜大于管子外径的5倍,其他管子的弯曲半径宜大于管子外径的3.5倍。
3、有缝管制作弯管时,焊缝应避开手拉(压)区。
4、金属管应在其材料特性允许范围内进行冷弯或热弯。
5、采用高合金钢管或有色金属管制作弯管时,宜采用机械方法;当允砂制作弯管时,不得用铁锤敲击。
铅管加热制作弯管时,不得允砂。
6、金属管热弯或冷弯后,应按设计文件的规定进行热处理。
当设计文件无规定时,应符合下列规定:1 初制作弯管温度自始至终保持温度在900℃以上的情况外,名义厚度大于19mm的碳素钢管制作弯管后,应按本规范表2表2 管道热处理基本要求母材类别名义厚度t(mm)母材最小规定抗拉强度(Mpa)热处理温度(℃)恒温时间(mim/mm)最短恒温时间(h)碳钢(C)、≤19全部不要求——碳锰钢(C-Mn) >19 全部600~650 2.4 1铬钼合金钢≤19≤490不要求——(C-Mo、Mn-Mo、Cr-Mo) >19 全部600~720 2.4 1Cr≤0.5%全部>490 600~720 2.4 1铬钼合金钢(C-Mo)≤13≤490不要求——0.5%<Cr≤2%>13 全部700~750 2.4 2全部>490 700~750 2.4 2铬钼合金钢(Cr-Mo)≤13全部不要求——2.25%≤Cr≤3%>13 全部700~760 2.4 2铬钼合金钢(Cr-Mo)全部全部700~760 2.4 23%<Cr≤10%马氏体不锈钢全部全部不要求——铁素体不锈钢全部全部不要求——奥氏体不锈钢全部全部不要求——低温镍钢≤19全部不要求——(Ni≤4%)>19 全部600~640 1.2 1注:热处理的加热速率和冷却速率应符合下列规定:1 当加热温度升至400℃时,加热速率不应超过(205×25/t)℃/h,且不得大于205℃/h。
工艺管线管道焊接工艺卡
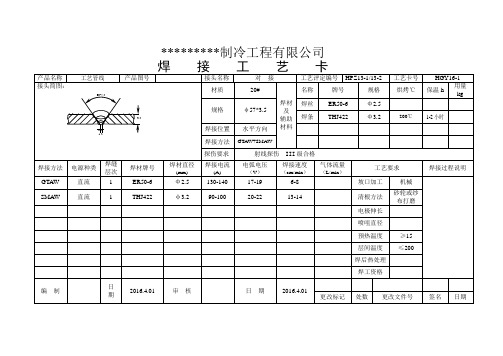
*********制冷工程有限公司焊接工艺卡产品名称工艺管线产品图号接头名称对接工艺评定编号HPZ13-1/13-2 工艺卡号HGY16-1接头简图:材质20#焊材及辅助材料名称牌号规格烘烤℃保温h用量kg规格φ57*3.5 焊丝ER50-6 Φ2.5焊条THJ422 Φ3.2 200℃1-2小时焊接位置水平方向焊接方法GTAW+SMAW探伤要求射线探伤III级合格焊接方法电源种类焊缝层次焊材牌号焊材直径(mm)焊接电流(A)电弧电压(V)焊接速度(cm/min)气体流量(L/min)工艺要求焊接过程说明GTAW 直流 1 ER50-6 Φ2.5 130-140 17-19 6-8 坡口加工机械SMAW 直流 1 THJ422 φ3.2 90-100 20-22 13-14 清根方法砂轮或纱布打磨电极伸长喷咀直径预热温度≥15 层间温度≤200 焊后热处理焊工资格编制日期2016.4.01 审核日期2016.4.01更改标记处数更改文件号签名日期1-2600±53.5******制冷工程有限公司焊接工艺卡产品名称工艺管线产品图号接头名称对接工艺评定编号HPZ13-1/13-2 工艺卡号HGY16-2接头简图:材质20#焊材及辅助材料名称牌号规格烘烤℃保温h用量kg规格Φ76*3.5 焊丝ER50-6 Φ2.5焊条THJ422 Φ3.2 200℃1-2小时焊接位置平焊方向焊接方法GTAW+SMAW探伤要求射线探伤III级合格焊接方法电源极性焊缝层次焊材牌号焊材直径(mm)焊接电流(A)电弧电压(V)焊接速度(cm/min)气体流量(L/min)工艺要求焊接过程说明GTAW 直流 1 ER50-6 Φ2.5 130-140 17-19 6-8 坡口加工机械SMAW 直流 1 THJ422 φ3.2 90-105 20-23 13-14 清根方法砂轮或纱布打磨电极伸长喷咀直径预热温度≥15 层间温度≤200 焊后热处理焊工资格编制日期2016.4.01 审核日期2016.4.01更改标记处数更改文件号签名日期1-2600±54********制冷工程有限公司焊接工艺卡产品名称工艺管线产品图号接头名称对接工艺评定编号HPZ13-1/13-2 工艺卡号HGY16-3接头简图:材质20#焊材及辅助材料名称牌号规格烘烤℃保温h用量kg规格Φ89*4.0 焊丝ER50-6 Φ2.5焊条THJ422 Φ3.2 200℃1-2小时焊接位置平焊方向焊接方法GTAW+SMAW探伤要求射线探伤III级合格焊接方法电源极性焊缝层次焊材牌号焊材直径(mm)焊接电流(A)电弧电压(V)焊接速度(cm/min)气体流量(L/min)工艺要求焊接过程说明GTAW 直流 1 ER50-6 Φ2.5 135-145 18-21 6-8 坡口加工机械SMAW 直流 2 THJ422 φ3.2 95-110 20-23 13-14 清根方法砂轮或纱布打磨电极伸长喷咀直径预热温度≥15 层间温度≤200 焊后热处理焊工资格编制日期2016.4.01 审核日期2016.4.01更改标记处数更改文件号签名日期1-2600±54.5********制冷工程有限公司焊接工艺卡产品名称工艺管线产品图号接头名称对接工艺评定编号HPZ13-1/13-2 工艺卡号HGY16-4接头简图:材质20#焊材及辅助材料名称牌号规格烘烤℃保温h用量kg规格Φ108*4.5 焊丝ER50-6 Φ2.5焊条THJ422 Φ3.2 200℃1-2小时焊接位置平焊方向焊接方法GTAW+SMAW探伤要求射线探伤III级合格焊接方法电源极性焊缝层次焊材牌号焊材直径(mm)焊接电流(A)电弧电压(V)焊接速度(cm/min)气体流量(L/min)工艺要求焊接过程说明GTAW 直流 1 ER50-6 Φ2.5 140-155 19-22 6-8 坡口加工机械SMAW 直流 2 THJ422 φ3.2 100-110 21-23 13-14 清根方法砂轮或纱布打磨电极伸长喷咀直径预热温度≥15 层间温度≤200 焊后热处理焊工资格编制日期2016.4.01 审核日期2016.4.01更改标记处数更改文件号签名日期2~3600±54.5济南*****工程有限公司焊接工艺卡产品名称工艺管线产品图号接头名称对接工艺评定编号HPZ13-1/13-2 工艺卡号HGY16-5接头简图:材质20#焊材及辅助材料名称牌号规格烘烤℃保温h用量kg规格Φ133*5 焊丝ER50-6 Φ2.5焊条THJ422 Φ3.2 200℃1-2小时焊接位置平焊方向焊接方法GTAW+SMAW探伤要求射线探伤III级合格焊接方法电源极性焊缝层次焊材牌号焊材直径(mm)焊接电流(A)电弧电压(V)焊接速度(cm/min)气体流量(L/min)工艺要求焊接过程说明GTAW 直流 1 ER50-6 Φ2.5 145-155 20-23 6-8 坡口加工机械SMAW 直流 2 THJ422 φ3.2 105-120 21-24 13-14 清根方法砂轮或纱布打磨电极伸长喷咀直径预热温度≥15 层间温度≤250 焊后热处理焊工资格编制日期2016.4.01 审核日期2016.4.01更改标记处数更改文件号签名日期2~3600±55济南*****工程有限公司焊接工艺卡产品名称工艺管线产品图号接头名称对接工艺评定编号HPZ13-1/13-2 工艺卡号HGY16-6接头简图:材质20#焊材及辅助材料名称牌号规格烘烤℃保温h用量kg规格Φ159*6 焊丝ER50-6 Φ2.5焊条THJ422 Φ3.2 200℃1-2小时焊接位置平焊方向焊接方法GTAW+SMAW探伤要求射线探伤III级合格焊接方法电源极性焊缝层次焊材牌号焊材直径(mm)焊接电流(A)电弧电压(V)焊接速度(cm/min)气体流量(L/min)工艺要求焊接过程说明GTAW 直流 1 ER50-6 Φ2.5 150-160 21-24 6-8 坡口加工机械SMAW 直流 2 THJ422 φ3.2 110-120 21-25 13-14 清根方法砂轮或纱布打磨电极伸长喷咀直径预热温度≥15 层间温度≤250 焊后热处理焊工资格编制日期2016.4.01 审核日期2016.4.01更改标记处数更改文件号签名日期2~3600±56济南*****工程有限公司焊接工艺卡产品名称工艺管线产品图号接头名称对接工艺评定编号HPZ13-1/13-2 工艺卡号7接头简图:材质20#焊材及辅助材料名称牌号规格烘烤℃保温h用量kg规格Φ219*8 焊丝ER50-6 Φ2.5焊条THJ422 Φ3.2 200℃1-2小时焊接位置平焊方向焊接方法GTAW+SMAW探伤要求射线探伤III级合格焊接方法电源极性焊缝层次焊材牌号焊材直径(mm)焊接电流(A)电弧电压(V)焊接速度(cm/min)气体流量(L/min)工艺要求焊接过程说明GTAW 直流 1 ER50-6 Φ2.5 155-170 21-25 6-8 坡口加工机械SMAW 直流 2 THJ422 φ3.2 115-125 22-25 13-14 清根方法砂轮或纱布打磨电极伸长喷咀直径预热温度≥15 层间温度≤250 焊后热处理焊工资格编制日期2016.4.01 审核日期2016.4.01更改标记处数更改文件号签名日期2~3600±57济南*****工程有限公司焊接工艺卡产品名称工艺管线产品图号接头名称对接工艺评定编号HPZ13-1/13-2 工艺卡号8接头简图:材质20#焊材及辅助材料名称牌号规格烘烤℃保温h用量kg规格Φ273*8 焊丝ER50-6 Φ2.5焊条THJ422 Φ3.2 200℃1-2小时焊接位置平焊方向焊接方法GTAW+SMAW探伤要求射线探伤III级合格焊接方法电源极性焊缝层次焊材牌号焊材直径(mm)焊接电流(A)电弧电压(V)焊接速度(cm/min)气体流量(L/min)工艺要求焊接过程说明GTAW 直流 1 ER50-6 Φ2.5 160-185 22-25 6-8 坡口加工机械SMAW 直流 2 THJ422 φ3.2 120-130 22-25 13-14 清根方法砂轮或纱布打磨电极伸长喷咀直径预热温度≥15 层间温度≤250 焊后热处理焊工资格编制日期2016.4.01 审核日期2016.4.01更改标记处数更改文件号签名日期3-4600±510济南*****工程有限公司焊接工艺卡产品名称工艺管线产品图号接头名称对接工艺评定编号HPZ13-1/13-2 工艺卡号9接头简图:材质20#焊材及辅助材料名称牌号规格烘烤℃保温h用量kg规格Φ325*9 焊丝ER50-6 Φ2.5焊条THJ422 Φ3.2 200℃1-2小时焊接位置平焊方向焊接方法GTAW+SMAW探伤要求射线探伤III级合格焊接方法电源极性焊缝层次焊材牌号焊材直径(mm)焊接电流(A)电弧电压(V)焊接速度(cm/min)气体流量(L/min)工艺要求焊接过程说明GTAW 直流 1 ER50-6 Φ2.5 160-185 22-25 6-8 坡口加工机械SMAW 直流 2 THJ422 φ3.2 120-130 22-25 13-14 清根方法砂轮或纱布打磨电极伸长喷咀直径预热温度≥15 层间温度≤250 焊后热处理焊工资格编制日期2016.4.01 审核日期2016.4.01更改标记处数更改文件号签名日期3-4600±511。
管道焊接施工工艺卡003
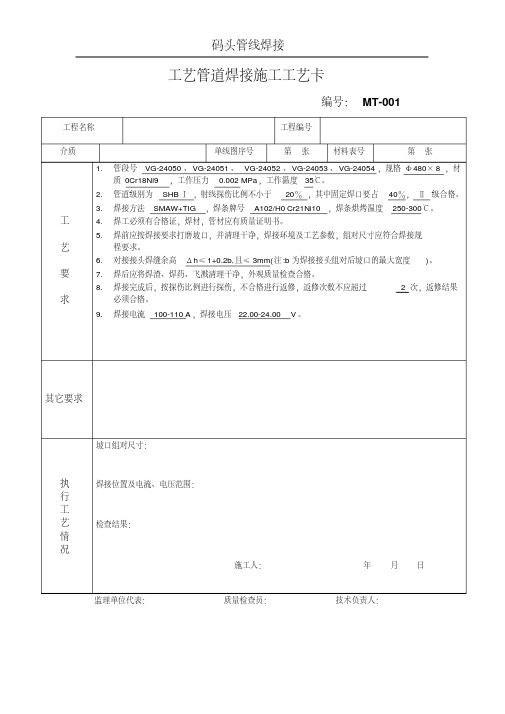
编号:MT-001工程名称工程编号介质单线图序号第张材料表号第张工艺要求1.管段号VG-24050、VG-24051、VG-24052、VG-24053、VG-24054,规格Φ480×8 ,材质0Cr18Ni9,工作压力0.002 MPa,工作温度35℃。
2.管道级别为SHBⅠ,射线探伤比例不小于20%,其中固定焊口要占40%,Ⅱ级合格。
3.焊接方法SMAW+TIG ,焊条牌号A102/H0Cr21Ni10,焊条烘烤温度250-300℃。
4.焊工必须有合格证,焊材,管材应有质量证明书。
5.焊前应按焊接要求打磨坡口,并清理干净,焊接环境及工艺参数,组对尺寸应符合焊接规程要求。
6.对接接头焊缝余高Δh≤1+0.2b,且≤3mm(注:b为焊接接头组对后坡口的最大宽度)。
7.焊后应将焊渣、焊药、飞溅清理干净,外观质量检查合格。
8.焊接完成后,按探伤比例进行探伤,不合格进行返修,返修次数不应超过 2 次,返修结果必须合格。
9.焊接电流100-110 A,焊接电压22.00-24.00 V。
其它要求执行工艺情况坡口组对尺寸:焊接位置及电流、电压范围:检查结果:施工人:年月日监理单位代表:质量检查员:技术负责人:编号:MT-002工程名称工程编号介质PE颗粒+空气单线图序号第张材料表号第张工艺要求1.管段号VG-24057 ,规格Φ480×8 ,材质20#,工作压力0.002 MPa,工作温度350C ℃。
2.管道级别为SHBⅠ,射线探伤比例不小于20%,其中固定焊口要占40%,Ⅱ级合格。
3.焊接方法SMAW+TIG ,焊条牌号J427/H08Mn2Si,焊条烘烤温度250-300 ℃。
4.焊工必须有合格证,焊材,管材应有质量证明书。
5.焊前应按焊接要求打磨坡口,并清理干净,焊接环境及工艺参数,组对尺寸应符合焊接规程要求。
6.对接接头焊缝余高Δh≤1+0.2b,且≤3mm(注:b为焊接接头组对后坡口的最大宽度)。
T管加工检验工艺卡(范例)

套管加工工艺标准卡
规格
代号1
钢级
扣型
执行标准
配带接箍参数
外径
钢级
接箍长度
Ø139.7×7.72
5-1/2〞17LB/FT
J55
LC
API5CT(9th)、
API 5B(15th)
Ø153.67mm
J55
203.2mm(+0.6mm~+1.6mm)
序号
工序名称
工艺参数
1
管端探伤
项目
探伤类型
探伤级别
探伤位置
探伤方向
参数
手提超声
L2
管端450mm内,内外表面
纵向
2
螺纹检查公差
项目
紧密距
螺距
L4长度
牙型角
参数
±2.5mm
0.125"±0.002"
88.9±3.175mm
60°(±11/2°)
项目
齿高
锥度
最小Lc长度
倒角
参数
0.07125
(-0.002"~+0.004")
0.061~0.066in/in
5
通径
项目
通径位置
通径规直径
通径规长度
参数
接箍拧紧后全长通径
≥121.08mm
≥152mm
6
保护环
项目
保护环品牌及类型
螺纹脂
参数
津英达外钢内塑可吊装保护帽
1、型号:
2、戴保护环前需均匀涂抹,并覆盖裸露丝扣
7
喷标
打印
项目
喷标内容
打印内容
色环
参数
长度MM重量KG TPCOAPI 5CT日期(年季)139.7mm×7.72mmJ S P33.5 LC D炉号批号支号班次号DH
1、弯管工艺卡

检验工具、仪器
检验规则
INSPECT TOOLS、 INSTRUMENT
目测 0-2m 卷尺
INSPECT RULES
自检 首检(可弯管验证),每 200 根抽检 一次,每次不少于 2 根
各种型号铝管落料后做好标识,不能混淆。
标记
MARK
数 量 文件号
QT’S FILE NO.
更改
校审
CHANGE
CHECK
弯管
自动弯管
03
页次 PAGE 003
版次:2009
修订号: 07 状态:有效
本技术文件由江苏常发制冷股份有限公司受控,任何单位、部门、个人未经书面批准同意,严禁私自变更、转借、拍摄、抄袭、复制、外传、外泄。
工 序 简 图 及 技 术 要 求 <PROCESS DRAWING AND TECHNICAL REQUIRMENT>
JIANGSU CHANGFA REFRIGERATION CO.,LTD
检验工具、仪器
检验规则
INSPECT TOOLS、 INSTRUMENT
目测
0—2m 钢卷尺
INSPECT RULES
全检 首检、自检,每 200 件抽检一次,每 次不少于 2 件
273-12Cr1MVG弯管制造工序过程卡

杭 州 航 峰 高 压 管 业 有 限 公 司产品弯管制造工序过程卡弯管规格:12Cr1MoVG ф273×30mm ф245×28mm ф194×22mm 工序号 工序名称 弯 管 加 工 过 程 班组 设备型号工夹具量刃具 责任人 1原材料检验按质保书标准检验原材料钢管的结构尺寸及表面质量。
并且做好检验记录 检验测厚仪、卡尺、盒尺材料质检员 2 理化 硬度检验HB < 200理化试验室 硬度计TH110直尺无损理化质检员3弯制前准备 1) 线圈平面度≤1.5mm ,线圈圆度≤1mm ,线圈宽度25mm ,喷气喷嘴位置在线圈外沿与端面成30度角,每隔5mm 有Φ1.0出气孔。
线圈焊缝不得有裂纹、漏气现象。
2) 冷却气压力0.4Mpa ,气温在5~30℃范围内。
3) 上料时,应避免管子碰壁。
线圈与管子间隙应均匀,管内不应有杂物、水及油污,管表面应去除锈蚀。
成型车间WG460中频加热弯管机角度尺 卡尺 盒尺 直尺 测温仪操作人员4弯制 1) 检查来料尺寸和表面质量,并合理安排用料。
2) 按弯制工序工艺卡要求煨制弯管。
3) 用记号笔把以下标记写在弯管内壁上。
规格:□ □ □ □ □ □A B C D E F A —公称直径mm B —钢管外径mm C —壁厚D —弯曲半径E —弯曲角度F —弯管钢级成型车间WG460中频加热弯管机测温仪 测厚仪 角度尺 卡尺 盒尺操作人员4)工程名称:产品试制(此项写在弯管的外壁)5)原材料的炉批号、管号、施工单位代号6)将原材料的炉批号、管号、弯管编号、弯管规格分别记录在“制造质量检验卡、记录卡上”。
5 整形按弯制工序工艺卡尺寸要求进行整形成型车间液压千斤顶卡尺、盒尺操作人员6 检验1)按《产品技术协议书》的要求对各项指标进行检验,核对弯管标记。
2)将检测记录和原始记录等交档案保存。
检验测厚仪、焊口检测器、角度尺、卡尺、盒尺、直径卷尺质检员7 热处理按热处理工艺卡上的要求进行回火热处理热处理HL-11-01热处理炉热处理人员8 无损检测按JB/T4730-2005对弯管受拉侧中心线上下各45º范围内进行100%磁粉检测,I级合格;对角焊缝采用渗透检测,I级合格;理化试验室CDX-III;着色渗透剂DPT-5型直尺无损理化质检员9 平坡口按工序工艺卡要求平坡口加工车间Q1280坡口机钢盒尺、焊口检测器操作人员10 表面处理按表面处理工序工艺卡要求进行处理, 表面处理车间酸洗池,磷化池, 操作人员11 检验进行成品检验,备好完整的检验资料,质量证明书,产品合格证文件检验质检员12 包装和装运1)弯管管端坡口用管帽保护,保证运输中不脱落。
管道维修工艺卡模板
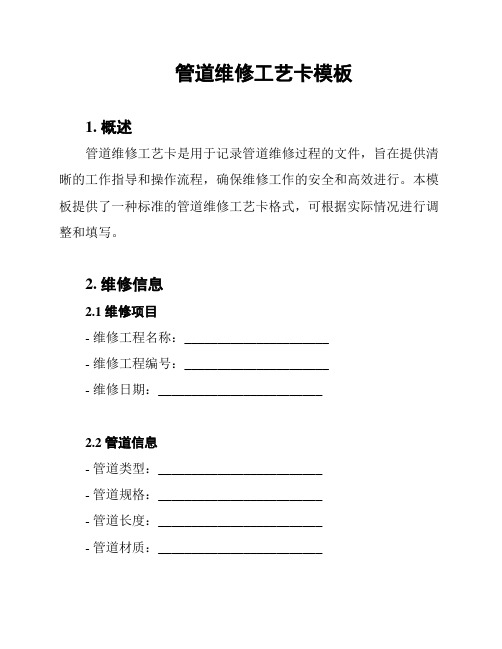
管道维修工艺卡模板1. 概述管道维修工艺卡是用于记录管道维修过程的文件,旨在提供清晰的工作指导和操作流程,确保维修工作的安全和高效进行。
本模板提供了一种标准的管道维修工艺卡格式,可根据实际情况进行调整和填写。
2. 维修信息2.1 维修项目- 维修工程名称:______________________- 维修工程编号:______________________- 维修日期:_________________________2.2 管道信息- 管道类型:_________________________- 管道规格:_________________________- 管道长度:_________________________- 管道材质:_________________________3. 维修工序3.1 准备工作- 清理工作区域,确保安全通道和工作空间。
- 确认维修所需的工具、设备和材料是否齐备。
- 检查管道维修前的工艺参数和安全措施。
3.2 维修步骤1. 步骤一:____________________________- 描述:____________________________- 工具/设备:________________________2. 步骤二:____________________________- 描述:____________________________- 工具/设备:________________________3. 步骤三:____________________________- 描述:____________________________- 工具/设备:________________________3.3 安全措施- 穿戴个人防护装备,包括安全帽、防护眼镜、手套等。
- 使用正确的工具和设备,确保其正常运作和安全操作。
- 在操作过程中注意周围环境和其他工作人员的安全。
弯管标准化
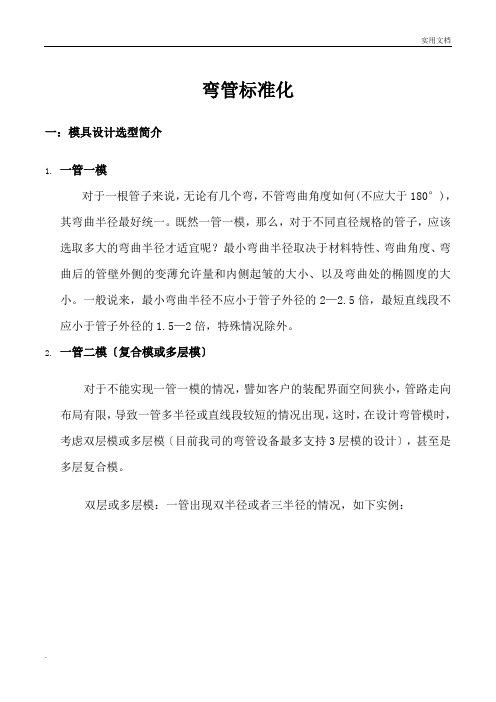
弯管标准化一:模具设计选型简介1.一管一模对于一根管子来说,无论有几个弯,不管弯曲角度如何(不应大于180°),其弯曲半径最好统一。
既然一管一模,那么,对于不同直径规格的管子,应该选取多大的弯曲半径才适宜呢?最小弯曲半径取决于材料特性、弯曲角度、弯曲后的管壁外侧的变薄允许量和内侧起皱的大小、以及弯曲处的椭圆度的大小。
一般说来,最小弯曲半径不应小于管子外径的2—2.5倍,最短直线段不应小于管子外径的1.5—2倍,特殊情况除外。
2.一管二模〔复合模或多层模〕对于不能实现一管一模的情况,譬如客户的装配界面空间狭小,管路走向布局有限,导致一管多半径或直线段较短的情况出现,这时,在设计弯管模时,考虑双层模或多层模〔目前我司的弯管设备最多支持3层模的设计〕,甚至是多层复合模。
双层或多层模:一管出现双半径或者三半径的情况,如下实例:双层或多层复合模:直线段短,不利于夹持的情况,如下实例:3.多管一模我司所用的多管一模,就是同一直径规格的管子应尽量采用同一种弯曲半径。
也就是使用同一套模具弯制不同形状的管件。
这样,才能有利于最大限度地压缩专用工艺设备,减少弯模的制造量,从而降低生产本钱。
在一般情况下,同一直径规格的管子只采用一种弯曲半径不一定能够满足实际位置的装配需要。
因此,相同直径规格的管子可以选取2—4种弯曲半径,以适应实际的需要。
如果弯曲半径取2D(这里D为管子外径),那么2D、2.5D、3D、4D即可。
当然,这种弯曲半径的比例不是固定不变的,应按发动机空间布局的实际情况选定,但是半径不宜选取过大。
而弯曲半径的规格也不宜过多,否那么会失去多管一模所带来的利益。
一根管子上采用同一个弯曲半径(即一管一模)和同规格管子的弯曲半径标准化(多管一模),这是当前国外弯管设计造型的特点和总的趋势,是机械化和自动化代替手工劳动的必然结果,也是设计适应先进的加工工艺和先进的加工工艺促进设计的两者的结合。
二:弯管椭圆度计算弯管机在进行工作运行时,在内压应力作用下,〔内压应力状态参考配管力学〕将使圆形的横截面趋于椭圆,产生短轴及长轴。
机加工艺卡片(折弯 )

锦州天雷电容制造有限公司
机械加工工艺过程卡片
产品型号
零件图号
产品名称
零件名称
共2页
第1页
工序号
工序名称
工序内容
车间
设备名称
设备型号
工艺装备
工时
准终
单件
4
折弯
1.穿戴好劳保用品(工作服、手套、劳保鞋),保证身体不受损伤。
2.检查设备是否工作正常,正常方可进行操作。
3.根据产品的尺寸、板厚、形状要求选择对应的上下模,并进行安装。
4.根据要求调节好பைடு நூலகம்具行程。
5.将与零件一样的板料放在下模上,进行试折弯,尺寸合格方可进行生产。
6.首件附上图纸,上交检验待检
7.折弯结束后,将上模降到下止点,断开电源。
8.整理工具及打扫工作区域卫生。
注意事项:
1.严禁将手或人体其它部位伸入上下模之间,以免机器因误动作而发生人身伤亡事故
2.防止任何物品误碰操作按扭,以免折弯机误动而发生事故。
3.开机前须检查机器运动部件和运动方向有无障碍物,若有应及时予以清理
4.如遇到紧急情况,请立即按下红色的急停按钮,使机器停止。
机
加
车
间
数控液压板料折弯机
WC67K-63-2500
设计(日期)
审核(日期)
标准化(日期)
会签(日期)
标记
处数
更改文件号
签字
日期
标记
处数
更改文件号
签字
日期
描图
描校
底图号
装订号
弯管成型工艺评定记录

下料长度mm
材质
《
φ×8
8
1700
API 5L X42
成型工艺参数
加热温度
工进速度
感应加热功率
感应加热频率
冷却水温度
流速
【
热处理温度
850±50℃
25-60mm/min
60KW
1000HZ
30℃
10m/s
520℃
弯管尺寸和外观检验
椭圆度
>
曲率半径
端面平面度
钝边
直管段直径偏差
762
φ~φ
弯曲角度
操作人:
评定人:
&
评定日期:
《
抚通亿通石油化工设备厂
弯管工艺评定报告
评定记录编号:YT/JL508-04 A/0
№:
工艺编号:YT/JS-14 A/0/NO:
产品名称
规格型号
材质
角度
生产设备
弯曲半径
执行标准
弯管90°5D
φ×
API 5L X42
@
90°
YY-200#弯管机
R=762
ASME
材料
规格
原材料规格/㎜
`
130
137
128
137
126
129
外弧弯曲段
《
127
131
130
133
127
126
其他:磁粉探伤:合格,探伤人员:关少华柳俊江报告编号:140420
:弯管Biblioteka 型工艺评定结论:依据标准的要求,通过对弯管φ×成型工艺试验,经检验完全符合标准要求,
上述检验结果属实,该成型工艺能够支持生产规格 _φ×钢管的生产。
工艺管道规格表

螺柱M24×120 螺柱M24×150 螺柱M24×150 螺柱M24×230 偏心大小头(BW) DN150×125 丝堵 DN20
C23F 4
个
C23F 2
个
C23F 1
个
C23F 3
个
C23F 1
个
C23F 4
个
C23F
14
米
B23F
25
米
C21F
14
米
C23F 8
米
B21F
C23F 6
个
止回阀(对夹式)H33R—J101 DN200
C23F 1
96
付
C23F 12 付
B23F 2
个
B21F 1
个
A105 D&S:STL STEM:13Cr CL800 SW—NPT API602 BB-BG-OS&Y A105 D&S:STL STEM:13Cr CL800 SW—NPT API602 BB-BG-OS&Y A105 D&S:STL STEM:13Cr CL800 SW—NPT API602 BB-BG-OS&Y A105 图号:PD—00/05 A105 图号:PD—00/05 20# GB/T699 SW SH3410 SCH80 20# GB/T8163 SMLS BE SH3405 SCH40 20# GB/T8163 SMLS BE SH3405 SCH40 20# GB/T8163 SMLS PE SH3405 SCH80 20# GB/T8163 SMLS PE SH3405 SCH80 20# GB/T8163 SMLS PE SH3405 SCH80 20# GB/T8163 SMLS PE SH3405 SCH80 20# GB/T8163 SMLS PE SH3405 SCH80 20# GB/T8163 SMLS PE SH3405 SCH80 20# GB/T8163 SMLS BE SH3405 SCH40 20# GB/T8163 SMLS BE SH3405 SCH40 20# GB/T699 SW HG/T21632 SKT SCH80 20# GB/T699 SW HG/T21632 SKT SCH80 20# GB/T699 SW HG/T21632 SKT SCH80 20# GB/T699 SW HG/T21632 SKT SCH80 20# GB/T8163 PE—NPT 图号 HGS04—04—01—1 SCH80 35CrMoA/35# GB/T3077/GB/T699 等长双头螺柱 带两个II型螺母 35CrMoA/35# GB/T3077/GB/T699 等长双头螺柱 带两个II型螺母 35CrMoA/35# GB/T3077/GB/T699 等长双头螺柱 带两个II型螺母 35CrMoA/35# GB/T3077/GB/T699 等长双头螺柱 带两个II型螺母 35CrMoA/35# GB/T3077/GB/T699 等长双头螺柱 带两个II型螺母SH3404 35CrMoA/35# GB/T3077/GB/T699 等长双头螺柱 带两个II型螺母 35CrMoA/35# GB/T3077/GB/T699 等长双头螺柱 带两个II型螺母
标准的施工工艺卡123
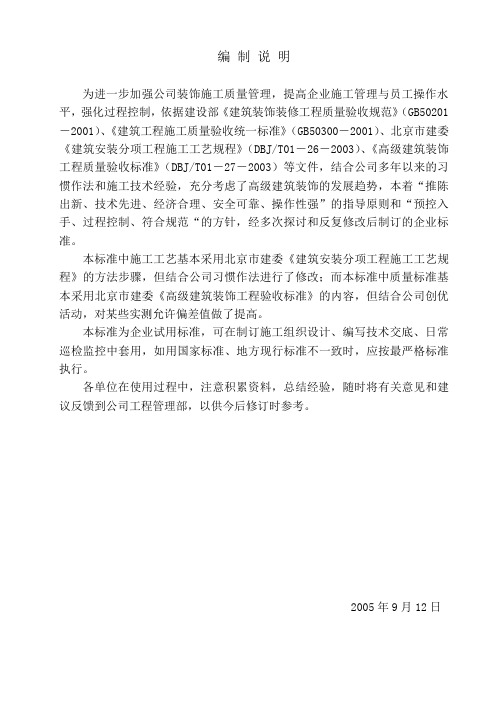
编制说明为进一步加强公司装饰施工质量管理,提高企业施工管理与员工操作水平,强化过程控制,依据建设部《建筑装饰装修工程质量验收规范》(GB50201-2001)、《建筑工程施工质量验收统一标准》(GB50300-2001)、北京市建委《建筑安装分项工程施工工艺规程》(DBJ/T01-26-2003)、《高级建筑装饰工程质量验收标准》(DBJ/T01-27-2003)等文件,结合公司多年以来的习惯作法和施工技术经验,充分考虑了高级建筑装饰的发展趋势,本着“推陈出新、技术先进、经济合理、安全可靠、操作性强”的指导原则和“预控入手、过程控制、符合规范“的方针,经多次探讨和反复修改后制订的企业标准。
本标准中施工工艺基本采用北京市建委《建筑安装分项工程施工工艺规程》的方法步骤,但结合公司习惯作法进行了修改;而本标准中质量标准基本采用北京市建委《高级建筑装饰工程验收标准》的内容,但结合公司创优活动,对某些实测允许偏差值做了提高。
本标准为企业试用标准,可在制订施工组织设计、编写技术交底、日常巡检监控中套用,如用国家标准、地方现行标准不一致时,应按最严格标准执行。
各单位在使用过程中,注意积累资料,总结经验,随时将有关意见和建议反馈到公司工程管理部,以供今后修订时参考。
2005年9月12日目录1 细石砼地面工程.............................. 错误!未定义书签。
2 地面石材铺贴工程............................ 错误!未定义书签。
3 地砖工程.................................... 错误!未定义书签。
4 实木地板安装工程............................ 错误!未定义书签。
5 复合木地板安装工程.......................... 错误!未定义书签。
6 地毯铺设工程................................ 错误!未定义书签。
- 1、下载文档前请自行甄别文档内容的完整性,平台不提供额外的编辑、内容补充、找答案等附加服务。
- 2、"仅部分预览"的文档,不可在线预览部分如存在完整性等问题,可反馈申请退款(可完整预览的文档不适用该条件!)。
- 3、如文档侵犯您的权益,请联系客服反馈,我们会尽快为您处理(人工客服工作时间:9:00-18:30)。
工艺过程卡
项目名称
验收标准
第1页
产品名称
弯管
制造编号
共1页
数量
单重(kg)
材质
材料规格
下料尺寸
序号
工序名称
工作内容、技术要求及施工手段
工时
操作员人
检验员
一
总则
按SY/T5257-2004标准进行生产,首批试验合格后正式生产。
二
弯管基本参数
弯曲半径R(mm):;弯曲角度α:;直管段长度L(mm):
产品名称
弯管
制造编号
共1页
数量
单重(kg)
材质
材料规格
下料尺寸
序号
工序名称
工作内容、技术要求及施工手段
工时
操作员人
检验员
(Da-Db/ Db)×100%≤1.5%
Da-冷整形后外径,mm;Db -冷整形前外径,mm;
距管端不小于100mm范围内的内、外焊缝余高均应磨削消除,清除后的焊缝余高为0~0.5mm,与管体
三
推制
1、弯制前母管清理的方法及要求
1)检查母管内外表面是否有油污;搬运、装卸过程是否与低熔点金属(Cu、Zn、Sn、Pb等)及不锈钢接触,
材料接触;如发现上述情况,采用砂纸或喷砂进行清除。
2)母管表面应光滑,无尖锐缺口、分层、刻痕、结疤、发裂、折叠、撕裂、裂纹、裂缝等缺陷或缺欠。
采用砂轮进行修磨。修磨处圆滑,满足最小壁厚mm要求,并采用渗透或磁粉进行检测,Ⅰ级合格。
2、使用D12机组推制,使用500KW机组推制,使用250KW机组推制,并对弯管机进行检查评定。
1)感应圈符合设计要求。
2)感应加热的恒定频率偏差不超过±20%。
3)设备控制仪表的检定是否符合要求
4)设备机械、液压、电气系统是否稳定。
5)温度监控系统是否正常运行。
3、下料:推制完成后切割、标识移植、编号,弯管编号具有可追溯性。
材质
材料规格
下料尺寸
序号
工序名称
工作内容、技术要求及施工手段
工时
操作员人
检验员
5、推制参数要求:
1、应按推制参数及工艺规程执行;推制过程中应保证匀速推制,不允许中断,不得有任何振动现象。
2、焊缝位于弯管中性面附近的外弧侧或内弧侧距中性面5°~10°范围内。
3、每根推制的参数值,做好记录。
加热温度:±25℃;推制速度:±2.5mm;中频频率:±Hz;冷却介质及流量:工业洁净水,±2.5m³;
2)、表面硬度检查:≤
七
检验
1、表面预处理:采用喷砂的方式清除表面氧化皮等杂质,弯管外表面达到GB/T8923规定的Sa2级。
2、无损检测:
1)每根弯管焊缝进行100%UT或RT检查,对焊缝的修补处,应进行RT检验。符合GB/T9711的规定。
2)坡口制备后,对整个管口和管口开始的100mm长度的焊缝进行磁粉或渗透检测,Ⅰ级合格。
推制完成后切割、标识移植、编号,弯管编号具有可追溯性。
推制前切割下料、做好记录,推制完成后进行标识移植、编号,弯管编号具有可追溯性。
4、坡口:采用坡口机进行加工,管端坡口形式及尺寸等详见下图所示。
编制
年月日
审批
年月日
弯管加工、制作
工艺过程卡
项目名称
验收标准
第1页
产品名称
弯管
制造编号
共1页
数量
单重(kg)
c、弯曲角度,弯管弧的弯曲角最大偏差为±0.5°。
3)、表面硬度检查:≤
四
首检
取同一推制参数推制的第一和第二根弯管,热处理前和热处理后分别按照SY/T5257-2004标准进行外
观质量及尺寸;表面硬度检验;弯管管体外弧侧(MT或PT);弯管管体(UT)横向缺陷;焊缝UT;
弯管管体外弧侧壁厚;金相及晶粒度检验;拉伸试验;夏比冲击韧性试验,-20℃;维氏硬度检验;
冷却介质温度:±15℃;
6、自检
1)、外观质量:
a、是否存在裂纹、过热、过烧;
b、表面有无硬点;
c、内外表面是否光滑,有尖锐缺口、分层、刻痕、结疤、发裂、折叠、撕裂、裂纹、裂缝等缺陷缺欠。
2)、几何尺寸:
a、外径。
b、圆度,弯管直管段距管端100mm范围内,最大外径减去最小外径应不大于mm。
弯管弯曲段的最大外径减去最小外径应不大于mm。
1)、弯管直管段与弯管弯曲段直径尺寸偏差外径:管端外径允许偏差为+2mm,-1mm。
2)、外弧侧壁厚减薄率:弯管最小壁厚要求10.5mm。
3)、椭圆度:弯管直管段距管端100mm范围内,最大外径减去最小外径应不大于5.6mm。
弯管弯曲段的最大外径减去最小外径应不大于17.5mm。
4)、弯曲角度偏差应不超过±0.5°。弯管弯曲半径为R=5D,极限偏差为±17.7mm。
验收标准
第1页
产品名称
弯管
制造编号
共1页
数量
单重(kg)
材质
材料规格
下料尺寸
序号
工序名称
工作内容、技术要求及施工手段
工时
操作员人
检验员
4)弯管表面不允许有明显折皱。内弧侧起皱高度h应不大于1.32mm,且起皱波浪间距f与起皱高度
h(f/h)之比应大于150。
4、几何尺寸:按照SY/T5257-2004标准进ห้องสมุดไป่ตู้检查。
3)每根弯管管体外弧两侧各90°的弧面进行磁粉或渗透检测,缺欠深度不大于壁厚的5%。
4)每根弯管外弧侧距壁厚基本不变的中性面±45°范围内的管体,采用UT检查横向裂纹缺陷。
5)按SY/T6423.5或SY/T6423.6对弯管进行分层曲线检测,符合GB/T9711的规定。
6)剩磁:按API Spec5L:2000中9.7.7的规定进行检查和消磁,不超过15Gs。
3、外观检查:1)不存在裂纹、过热、过烧;表面无硬点;
2)内外表面是否光滑,有尖锐缺口、分层、刻痕、结疤、发裂、折叠、撕裂、裂纹、裂缝等缺陷缺欠。
3)管体上不允许有深度超过3.15mm的摔坑或焊缝上深度超过1.5mm的摔坑,不允许采用捶击方法修理
凹痕。
编制
年月日
审批
年月日
弯管加工、制作
工艺过程卡
项目名称
弯管管体化学成分,化学元素包括:碳、锰、磷、硫、硅、铌、钒、钛、铜、铬、钼、镍、硼;
五
整形和定径
1、弯制后对弯管不进行再次加热或热定径,超过管材相变温度的整体热处理除外。
2、可采用千斤顶进行冷整形。永久变形量不应大于冷整形前外径的1.5%
编制
年月日
审批
年月日
弯管加工、制作
工艺过程卡
项目名称
验收标准
第1页
表面光滑过渡。不允许用焊接方法把支撑物固定在管子上。
六
热处理
1、热处理前检查热处理炉的各项性能指标是否合格;热电偶是否按规定进行检定,每次使用前经有资
格的检定人员确认。
2、根一炉,分几层放置,热处理后对弯管进行移植
3、按热处理工艺卡执行。
4、自检:
1)、外观检查,表面无裂纹、过热、过烧存在。表面无硬点,无明显褶皱。